AFINIA LABEL DLP-2000 User manual

Version 1.2
Version 1.2

Print, Laminate, Cut, Remove Matrix
The Afinia Label DLP
vibrant, 1600 DPI, photograph
RotoMetrics cylinder accepts flex
of any shape, including perforations. The DLP
The DLP-
2000 can also convert stock to blank labels, ready for printing. With
possible to run the DLP
ft./min.
The DLP-
2000 Digital Label Press brings the incredible speed, quality and economical low cost
of Memjet
and dies. Finally, labels can be printed, laminated and cut in
DLP
Print, Laminate, Cut, Remove Matrix
The Afinia Label DLP
-
2000 is a digital label press that is powered by
vibrant, 1600 DPI, photograph
RotoMetrics cylinder accepts flex
of any shape, including perforations. The DLP
2000 can also convert stock to blank labels, ready for printing. With
possible to run the DLP
2000 Digital Label Press brings the incredible speed, quality and economical low cost
of Memjet
Technology together with the precision and performance of RotoMetrics magnetic cylinders
and dies. Finally, labels can be printed, laminated and cut in
DLP
-
2000 Digital Label Press
Print, Laminate, Cut, Remove Matrix
2000 is a digital label press that is powered by
vibrant, 1600 DPI, photograph
-
quality color at 6 inches per second
RotoMetrics cylinder accepts flex
ible dies up to 12 inches in length allowing for fast, accurate die cutting
of any shape, including perforations. The DLP
2000 can also convert stock to blank labels, ready for printing. With
possible to run the DLP
-
2000 in full rotary mode which will convert blank labels at a rate of over 140
2000 Digital Label Press brings the incredible speed, quality and economical low cost
Technology together with the precision and performance of RotoMetrics magnetic cylinders
and dies. Finally, labels can be printed, laminated and cut in
2000 Digital Label Press
Print, Laminate, Cut, Remove Matrix
2000 is a digital label press that is powered by
quality color at 6 inches per second
ible dies up to 12 inches in length allowing for fast, accurate die cutting
of any shape, including perforations. The DLP
-
2000 is compatible with your existing RotoMetrics dies.
2000 can also convert stock to blank labels, ready for printing. With
2000 in full rotary mode which will convert blank labels at a rate of over 140
2000 Digital Label Press brings the incredible speed, quality and economical low cost
Technology together with the precision and performance of RotoMetrics magnetic cylinders
and dies. Finally, labels can be printed, laminated and cut in
2
2000 Digital Label Press
2000 is a digital label press that is powered by
quality color at 6 inches per second
ible dies up to 12 inches in length allowing for fast, accurate die cutting
2000 is compatible with your existing RotoMetrics dies.
2000 can also convert stock to blank labels, ready for printing. With
2000 in full rotary mode which will convert blank labels at a rate of over 140
2000 Digital Label Press brings the incredible speed, quality and economical low cost
Technology together with the precision and performance of RotoMetrics magnetic cylinders
and dies. Finally, labels can be printed, laminated and cut in
-
line
2000 Digital Label Press
2000 is a digital label press that is powered by
Memjet
quality color at 6 inches per second
ible dies up to 12 inches in length allowing for fast, accurate die cutting
2000 is compatible with your existing RotoMetrics dies.
2000 can also convert stock to blank labels, ready for printing. With
2000 in full rotary mode which will convert blank labels at a rate of over 140
2000 Digital Label Press brings the incredible speed, quality and economical low cost
Technology together with the precision and performance of RotoMetrics magnetic cylinders
line
.
2000 Digital Label Press
Memjet
. The DLP
quality color at 6 inches per second
and requires no plates. The
ible dies up to 12 inches in length allowing for fast, accurate die cutting
2000 is compatible with your existing RotoMetrics dies.
2000 can also convert stock to blank labels, ready for printing. With
a 14-
inch flexible die, it’s
2000 in full rotary mode which will convert blank labels at a rate of over 140
2000 Digital Label Press brings the incredible speed, quality and economical low cost
Technology together with the precision and performance of RotoMetrics magnetic cylinders
. The DLP
-
2000 prints in
and requires no plates. The
ible dies up to 12 inches in length allowing for fast, accurate die cutting
2000 is compatible with your existing RotoMetrics dies.
inch flexible die, it’s
2000 in full rotary mode which will convert blank labels at a rate of over 140
2000 Digital Label Press brings the incredible speed, quality and economical low cost
-
per
Technology together with the precision and performance of RotoMetrics magnetic cylinders
2000 prints in
and requires no plates. The
ible dies up to 12 inches in length allowing for fast, accurate die cutting
2000 is compatible with your existing RotoMetrics dies.
inch flexible die, it’s
2000 in full rotary mode which will convert blank labels at a rate of over 140
per
-print
Technology together with the precision and performance of RotoMetrics magnetic cylinders

3
Contents
Features ........................................................................................................................................................ 5
Specifications ................................................................................................................................................ 6
Installation .................................................................................................................................................... 7
Unpacking ................................................................................................................................................. 7
Adjusting Pinch Rollers.............................................................................................................................. 8
Components.................................................................................................................................................. 9
Identifying major components.................................................................................................................. 9
Safely Features........................................................................................................................................10
Connecting power...................................................................................................................................11
Overview .....................................................................................................................................................12
Menu Review ..........................................................................................................................................12
Jump1..................................................................................................................................................12
Jump2..................................................................................................................................................12
Jump3..................................................................................................................................................12
Jump4..................................................................................................................................................12
Jump5..................................................................................................................................................12
Jump6..................................................................................................................................................12
Loading media.........................................................................................................................................13
Printer media ..........................................................................................................................................14
System Settings Review ..........................................................................................................................15
System settings when converting printed labels from the printer:....................................................15
System settings when converting blank labels – reciprocating mode:...............................................15
System settings when converting blank labels – full rotary mode: ....................................................15
Enable or disable the loop sensor...........................................................................................................16
Opening the die lids ................................................................................................................................17
Using the splicing table ...........................................................................................................................18
Adjusting media ......................................................................................................................................19
Adjusting mark sensor position ..............................................................................................................20
Teaching the Mark Sensor ......................................................................................................................21
The Encoder ............................................................................................................................................22
Running blank labels ...............................................................................................................................23
Reciprocating Mode............................................................................................................................23
Full Rotary Mode.................................................................................................................................24

4
Removing Waste .....................................................................................................................................25
Loading laminate.....................................................................................................................................26
Laminate Adjustments ............................................................................................................................27
Attaching plates ......................................................................................................................................28
Removing plates......................................................................................................................................29
Sitting ......................................................................................................................................................30
Designing labels ......................................................................................................................................31
Screen Functions.....................................................................................................................................32
Adjusting die travel .................................................................................................................................33
Entering Label Counts .............................................................................................................................34
Time-out safety setting ...........................................................................................................................35
Changing the electronic black mark........................................................................................................36
Troubleshooting..........................................................................................................................................37
Media problems......................................................................................................................................37
Registration problems.............................................................................................................................38
Cutting problems ....................................................................................................................................38
Electrical problems..................................................................................................................................39
Maintenance ...............................................................................................................................................41
Maintenance Schedules ..........................................................................................................................41
Buying cutting plates...................................................................................................................................42
What and how to order ..........................................................................................................................42
Magnetic Cylinder Information...............................................................................................................43

Features
If you need to laminate and convert pre
complete solution.
It may be used as a stand
labels with a black registration mark and this remarkable machine makes laminating and die cutting look
easy. The DLP
board, screen and keyboard to ensure an amazing +/
Die cutting is handled by our unique full rotary reciprocating head. This system uses a full rotary cutting
action,
with a geared reciprocating cylinder carriage. It uses economical flexible steel cutting plates, for
very high precision and long die life.
The use of a high quality PCB for logic control ensures the DLP
custom applicati
attachments, the DLP
Visit our website at
Features
If you need to laminate and convert pre
complete solution.
It may be used as a stand
labels with a black registration mark and this remarkable machine makes laminating and die cutting look
easy. The DLP
-
2000 uses a combination of an
board, screen and keyboard to ensure an amazing +/
Die cutting is handled by our unique full rotary reciprocating head. This system uses a full rotary cutting
with a geared reciprocating cylinder carriage. It uses economical flexible steel cutting plates, for
very high precision and long die life.
The use of a high quality PCB for logic control ensures the DLP
custom applicati
ons, such as bar code verification. When combined with optional slitting and sheeting
attachments, the DLP
-
2000 is the complete solution to your laminating and die
Visit our website at
www.a
If you need to laminate and convert pre
It may be used as a stand
-
alone unit or in
labels with a black registration mark and this remarkable machine makes laminating and die cutting look
2000 uses a combination of an
board, screen and keyboard to ensure an amazing +/
Die cutting is handled by our unique full rotary reciprocating head. This system uses a full rotary cutting
with a geared reciprocating cylinder carriage. It uses economical flexible steel cutting plates, for
very high precision and long die life.
The use of a high quality PCB for logic control ensures the DLP
ons, such as bar code verification. When combined with optional slitting and sheeting
2000 is the complete solution to your laminating and die
www.a
finialabel.com
If you need to laminate and convert pre
-
printed continuous material, the Afinia DLP
alone unit or in
-
line with the Afinia L801 printer. Simply print your continuous
labels with a black registration mark and this remarkable machine makes laminating and die cutting look
2000 uses a combination of an
electronic mark sensor together with a printed
board, screen and keyboard to ensure an amazing +/
Die cutting is handled by our unique full rotary reciprocating head. This system uses a full rotary cutting
with a geared reciprocating cylinder carriage. It uses economical flexible steel cutting plates, for
very high precision and long die life.
The use of a high quality PCB for logic control ensures the DLP
ons, such as bar code verification. When combined with optional slitting and sheeting
2000 is the complete solution to your laminating and die
finialabel.com
for detailed information and downloads.
5
printed continuous material, the Afinia DLP
line with the Afinia L801 printer. Simply print your continuous
labels with a black registration mark and this remarkable machine makes laminating and die cutting look
electronic mark sensor together with a printed
board, screen and keyboard to ensure an amazing +/
-
0.3mm registration accuracy.
Die cutting is handled by our unique full rotary reciprocating head. This system uses a full rotary cutting
with a geared reciprocating cylinder carriage. It uses economical flexible steel cutting plates, for
The use of a high quality PCB for logic control ensures the DLP
ons, such as bar code verification. When combined with optional slitting and sheeting
2000 is the complete solution to your laminating and die
for detailed information and downloads.
printed continuous material, the Afinia DLP
line with the Afinia L801 printer. Simply print your continuous
labels with a black registration mark and this remarkable machine makes laminating and die cutting look
electronic mark sensor together with a printed
0.3mm registration accuracy.
Die cutting is handled by our unique full rotary reciprocating head. This system uses a full rotary cutting
with a geared reciprocating cylinder carriage. It uses economical flexible steel cutting plates, for
The use of a high quality PCB for logic control ensures the DLP
-
2000 can be modified to suite most
ons, such as bar code verification. When combined with optional slitting and sheeting
2000 is the complete solution to your laminating and die
for detailed information and downloads.
printed continuous material, the Afinia DLP
-
2000 offers the
line with the Afinia L801 printer. Simply print your continuous
labels with a black registration mark and this remarkable machine makes laminating and die cutting look
electronic mark sensor together with a printed
0.3mm registration accuracy.
Die cutting is handled by our unique full rotary reciprocating head. This system uses a full rotary cutting
with a geared reciprocating cylinder carriage. It uses economical flexible steel cutting plates, for
2000 can be modified to suite most
ons, such as bar code verification. When combined with optional slitting and sheeting
2000 is the complete solution to your laminating and die
-
cutting requirements.
for detailed information and downloads.
2000 offers the
line with the Afinia L801 printer. Simply print your continuous
labels with a black registration mark and this remarkable machine makes laminating and die cutting look
electronic mark sensor together with a printed
circuit
Die cutting is handled by our unique full rotary reciprocating head. This system uses a full rotary cutting
with a geared reciprocating cylinder carriage. It uses economical flexible steel cutting plates, for
2000 can be modified to suite most
ons, such as bar code verification. When combined with optional slitting and sheeting
cutting requirements.
2000 offers the
line with the Afinia L801 printer. Simply print your continuous
labels with a black registration mark and this remarkable machine makes laminating and die cutting look
circuit
Die cutting is handled by our unique full rotary reciprocating head. This system uses a full rotary cutting
with a geared reciprocating cylinder carriage. It uses economical flexible steel cutting plates, for
ons, such as bar code verification. When combined with optional slitting and sheeting
cutting requirements.

6
Specifications
Print Speed: 30 ft/min.
Print Quality: 1600 DPI full-color output
Max. Web Width: 9.65″ (245 mm)
Max. Diecutting Width 9″ (230 mm)
Max. Diecutting Length 12″ (304.8 mm)
Cutting Dies Flexible steel – any size from 0.2″ (5 mm) to 12″ (304.8 mm) repeat
Max. Laminate OD 11″ (280 mm)
Max. Finished Label Rewind 11″ (280 mm)
Max. Waste Matrix Rewind 11.8″ (300 mm)
Razor Slitter Assembly 6 knives
Razor Slitter Lateral Adjustment 0.47″ (12 mm)
Unwind 15.75″ (400 mm) max. outside diameter
Registration Sensor Laser
Registration Sensor Adjustment 9″ (230 mm) x 12″ (304.8 mm)
Sensor Mark 0.2″ x 0.2″ (5 mm x 5 mm)
Lateral Paper Adjustment 0.5″ (12 mm)
Laminate Economical, self-wound and supported laminate (on a liner). Liner
removal included for use with high quality,liner-supported laminate
Core Sizes 3″ (76 mm)
Dimensions 65″ (1650 mm) x 41.33″ (1050 mm) x 33″ (840 mm)
Frame 0.4″ (10 mm) solid aluminum
Safety Sensors Magnetic lid x2
Loop Photoelectric distance sensor
Power 110V– 240Vadjustable, 7 Amps
Registration +/-0.01″ (+/- 0.3mm)
Speed Max 7.87″/sec (200 mm/sec) re-registering or 140 ft/min full rotary for
blank labels
Speed Control Variable
Weight 420 lbs (190 kg)
Motors 2, 400 W / 90 W
Control PCB. Inverter, Encoder

7
Installation
Unpacking
Once you are ready to uncrate your DLP-2000, you will first need to remove the top panel, followed by
the 4 side panels, leaving the machine accessible for examination and detachment from the base panel.
View from underneath the crate
After removing the top and side panels, remove the 4 bolds holding the DLP to the base panel. The
DLP-2000 is supplied ready to use. Once you have removed the outer part of the crate, you will only
need to position the machine with a forklift, where it is to be used and plug it in.
Caution:
This machine is extremely heavy. Do not attempt to move the crate or machine
without suitable lifting equipment. Failure to follow these instructions may result in
serious back injury.
Caution:
Use a forklift t
o remove the DLP
-
2000 from its crate and to place
your machine into its final working position. Do not carry the machine.

8
Adjusting Pinch Rollers
The DLP-2000 is fitted with silicone rubber nip rollers. Do not use a knife on these rollers and clean with
a mild solvent if required.
The DLP
-
2000 is supplied with pre
-
set maximum roller settings. If the machine is supplied
with no nip pressure, simply turn the adjustment knob down unit it stops. Do not use
excessive force.
PINCH ROLLER ADJUSTERS
The laminating roller pressure is set
and should not need to be changed.
Wind the pressure adjusters down
until they stop. Do not use
excessive force.

9
Components
Identifying major components
Caution: Do
not proceed until you have a good understanding of the major components
of your machine and their locations. Do not attempt to start or run the DLP-2000 before
reading the instructions detailed on the following pages.

10
Safely Features
Following is an outline of the main safety features included with the DLP-2000. Please ensure that you
are familiar with all of the safety features before proceeding.
EMERGENCY STOP: Note the location of the emergency stop switch. The switch is designed to
immediately stop the machine and apply the motor brakes. After a few seconds, the motor
brakes are automatically released.
ELECTRICAL CABINET: The cabinet is secured by 4 – 8mm bolts which should be kept tight at all
times and removed by authorized technicians only.
DRIVE BELT: Ensure that hands, hair or clothing do not overhang the machine and cannot be
caught in the drive belt. These are inside the back cover and underneath the die cylinder.
NIP ROLLERS: These rollers are driven by powerful motors. Never under any circumstances
place fingers, hair or clothing near the nip rollers while the machine is running.
WARNING LABELS: These labels indicate important safety considerations for your machine.
Never remove, damage or obscure warning labels.
DIE ACCESS LID: Never open the die access lid while the DLP is operating. The die access lid is
protected by a safety switch. Never remove, disable or disconnect the switch and do not
continue to operate the DLP with a defective switch. Always open and close the lid slowly and
carefully using the handles provided ONLY.
Caution: The safety features included with your machine are for your protection. Never
remove warning labels or disable cut out switches. Be aware of your emergency stop
location and use common safety precautions and care at all times.

11
Connecting power
Follow these steps listed to attach power.
Locate the position of the power socket
The DLP-2000 power socket is switchable and you must check that the correct voltage has been
selected for your local power source. Note that the voltage indicator 1will indicate either 110-
120V or 220-240V. The text next to the voltage indicator arrow that points downwards is the
current setting. If the voltage text is not correct you must contact your distributor immediately.
DO NOT attempt to start the DLP-2000 with the wrong voltage selected.
Attach a power cable to the DLP-2000 machine. Connect the cable plug to a standard protective
earth electrical socket of the correct voltage. You will need a standard computer power cable
with the correct power socket for your country
Caution: Do not proceed until you have a good understanding of the major components
of your machine and their locations. Do not attempt to start or run the DLP-2000 before
reading the instructions detailed on the following pages.

12
Overview
Menu Review
Jump1
Die Length: Length of die + 20mm.
Stroke: This is the drive pulley teeth count. The value is set automatically by converter.
Rotary Mode (M): Sets the length of stock to be run when in full rotary mode.
METERS REM (M): Displays the number of meters remaining in the job, when in full rotary mode.
Jump2
Labels Required: Enter number of labels to convert, noting that one label will include the number of
labels on the die. Example, die contains 6 labels. If 100 is entered in label count, 600 blank labels will be
produced.
Label Count: Number of labels produced. Press CLR to reset label count. Same rule applies, stated
above.
Count: 1 is on, 0 is off.
Jump3
Unwinder: Does not apply. Should be 0
Loop Sensor: 1 is enabled, 0 is disabled. Enabled when printing in line. Disabled when not using printer.
Cutter Qty: Does not apply. Should be 0001
(Page 2 settings in Jump3 are the same as in Jump5)
Jump4
Encoder Read: The amount the encoder has currently read in its cycle. This value cannot be changed.
CAL: This value is preset at the factory. Do not change.
Encoder Mark: 1/3 of the distance of the die length
ENC. Fast: Value of zero.
ENC O/Run: Value of 000.8
Index T/Out: Distance the converter will run before stopping because the black mark was not
detected. Set this value to 1.5 times the repeat value
Jump5
Encoder Indexing: Always set to 1. Do not change.
Repeat: distance from the middle of one black mark to the next (pitch)
Sense: distance the laser starts to look for the next black mark. Set to 0 if making blanks in
reciprocating mode.
Jump6
Dig-IN: 10001000
ADIG-IN: 10010000
These are used for troubleshooting. These values indicate that a low voltage part is working. If you
trigger a sensor, i.e.; move the encoder, hold a metal object in front of a proximity switch, cause the
laser sensor to see something by lighting up (or turning off its light) or making the loop sensor "see"
something and you get no value change on the screen in any digit, then you know that the sensor is
faulty or not being recognized by the machine. It is a simple way of narrowing down an unexpected
fault to a particular device. Not all digits are used.

13
Loading media
Caution: Ensure that the power is disconnected before you begin to load your media for
the first time or until you have a good understanding of the general operating
procedures.

14
Printer media
Load the printer with the desired media.
Once though the printer, use the printer to either feed or print media until you have enough media to
feed through the DLP-2000 convert as shown below.
To use the inline method of production, the printer must not have an automatic cut off or sheeting
mechanism active when the printer is paused. To stop and start the converting process, the printer is in
control of both sections of the machine. Simply pause or stop the printer to stop the unwind and the
DLP-2000 converter.
It is also important that the speed of the printer not exceed the speed of the DLP-2000 converter or
media will reach the floor. When the printer is slower than the converter, the converter will stop and
start automatically, keeping the loops at a constant level.
Caution: Ensure that the power is disconnected before you begin to load your media for
the first time or until you have a good understanding of the general operating
procedures.

15
System Settings Review
System settings when converting printed labels from the printer:
Die length: Length of die + 20mm – Set in Jump 1
Loop sensor: 1 (on) – Set in Jump 3
Encoder mark (ramp down): Set to 1/3 of the die length – Set in Jump 4
Repeat: Distance from center of one black mark to the next black mark – Set in Jump 5
Sense: Distance the laser will start to look for the black mark, set to 10mm – Set in Jump 5
System settings when converting blank labels – reciprocating mode:
Die length: Length of die + 20mm – Set in Jump 1
Loop sensor: 0 (off) – Set in Jump 3
Encoder mark (ramp down): Set to 1/3 of the die length – Set in Jump 4
Repeat: Distance of the pitch of the die plus the label gap – Set in Jump 5
Sense: Set to 0. This causes the system not to use the laser – Set in Jump 5
System settings when converting blank labels – full rotary mode:
Change the position of the cylinder to full rotary mode. See page 24.
Die length: Length of die – does not apply
Loop sensor: 0 (off) – Set in Jump 3
Rotary Mode setting – enter length (in meters) of the length to convert. Once that length is reached,
the system stops – Set in Jump 1
Encoder mark (ramp down): Do not need to change. This function is not used in full rotary mode.
Repeat: Does not apply– Set in Jump 5
Sense: Does not apply – Set in Jump 5

16
Enable or disable the loop sensor
To access the menu to enable or disable the loop sensor, press the JUMP key, followed by the
number 3 key
Use the arrow key to scroll to the Loop Sensor setting. Disable the sensor by changing the loop
sensor setting to 0 by entering 0 and pressing the Enter key
Enable the sensor by changing the loop sensor setting to 1 by entering 1 and pressing the Enter
key
Press the HOME key to return to the front screen
If the need
arises where the loop sensor needs to be turned off, use these instructions to
enable or disable the DLP-2000 loop sensor.

17
Opening the die lids
Use these instructions to open and close the die access lids.
Do not use the die access lids to top the machine. Use the STOP key or the EMERGENCY STOP
button. If the die access lids are raised during the operation of the DLP-2000 the operator must
press the Emergency Stop button and then the RESET button to re-home the cutting die. Failure
to follow these instructions could result in a web break.
When cleaning the die lids, use a window cleaning detergent only. The use of strong solvents or
chemicals will destroy the transparency of the lids.
The DLP-2000 lids can be opened partly or fully, depending on the access required. OPEN ONE
LID AT A TIME USING THE HANDLES PROVIDED.
Caution: Ensure that the printer is stopped before opening the die access lid. Close and
open doors carefully, using the handles only.

18
Using the splicing table
When the current roll of media is finished, stop the DLP-2000 or the loop sensor will stop the
machine when it sees no media. Push the Emergency Stop button.
Load the new roll of media into the printer or unwind mandrel, making sure the new roll is in
the same position as the previous roll. Enter the new roll of media into the splicing table and
align it with the previous media.
Lower and lock the top section of the splicing table. Using a sharp knife, cut through both pieces
of media, in the slot on the splicing table.
Using tape, join the underside of the new media to the underside of the previous roll, making
sure to align them as perfectly as possible. Undo and lift the top section of the splicing table,
remove the unwanted cut pieces of media and place another piece of tape across the top of the
media at the join. If laminate is being applied, the top tape is not required.
Using scissors or a sharp knife, cut the excess tape on each side of the media, as close to the
media as possible. Release the Emergency stop and press the reset button. You are now ready
to begin running a job.
The splicing table enables the user to join rolls of media together neatly
and correctly, to
allow smooth passage through the die cutting, stripping and slitting processes. Follow
the instructions below on the use of the DLP-2000 splicing table.

Adjusting media
Before beginning the following it is important to have the back plates of the DLP
lined up squarely with each other.
When loading the media onto the unwind mandrel it is
recommended but not essential, to keep the paper to
a constant
allows for faster changes in web width as only the near
side paper guides will need to be moved.
It is important to set the 2 lower paper guides first. After
inching
the paper for a few feet you can set the paper
guides. Make sure that the guides are set against the
media so as not to allow for any lateral movement.
It is easier to nip the paper guides up only a little so
that they can be moved by hand if requir
Once through the machine attach the media to a core
on one of the rewind mandrels. If the job requires more
than one roll to be rewound, take note of the position of
the first roll on the mandrel ruler, as it winds up on the
mandrel. This will
easier.
Use the lateral web adjuster to move the web across the
machine if needed. This can be done while the machine
is running. Wait for a few impressions before moving it
again to see how much movement you ha
to begin a job with this adjustment in the center of travel
to insure movement in either direcions, if required.
The correct line of the paper is important to the lateral registration. Follow the
instructions below as a guide to setting the line of paper up correctly to ensure a
consistently straight web path.
Adjusting media
Before beginning the following it is important to have the back plates of the DLP
lined up squarely with each other.
When loading the media onto the unwind mandrel it is
recommended but not essential, to keep the paper to
a constant
position to the back of the machine. This
allows for faster changes in web width as only the near
side paper guides will need to be moved.
It is important to set the 2 lower paper guides first. After
the paper for a few feet you can set the paper
guides. Make sure that the guides are set against the
media so as not to allow for any lateral movement.
It is easier to nip the paper guides up only a little so
that they can be moved by hand if requir
Once through the machine attach the media to a core
on one of the rewind mandrels. If the job requires more
than one roll to be rewound, take note of the position of
the first roll on the mandrel ruler, as it winds up on the
mandrel. This will
make the repositioning of new cores
Use the lateral web adjuster to move the web across the
machine if needed. This can be done while the machine
is running. Wait for a few impressions before moving it
again to see how much movement you ha
to begin a job with this adjustment in the center of travel
to insure movement in either direcions, if required.
The correct line of the paper is important to the lateral registration. Follow the
instructions below as a guide to setting the line of paper up correctly to ensure a
consistently straight web path.
Before beginning the following it is important to have the back plates of the DLP
lined up squarely with each other.
When loading the media onto the unwind mandrel it is
recommended but not essential, to keep the paper to
position to the back of the machine. This
allows for faster changes in web width as only the near
side paper guides will need to be moved.
It is important to set the 2 lower paper guides first. After
the paper for a few feet you can set the paper
guides. Make sure that the guides are set against the
media so as not to allow for any lateral movement.
It is easier to nip the paper guides up only a little so
that they can be moved by hand if requir
Once through the machine attach the media to a core
on one of the rewind mandrels. If the job requires more
than one roll to be rewound, take note of the position of
the first roll on the mandrel ruler, as it winds up on the
make the repositioning of new cores
Use the lateral web adjuster to move the web across the
machine if needed. This can be done while the machine
is running. Wait for a few impressions before moving it
again to see how much movement you ha
to begin a job with this adjustment in the center of travel
to insure movement in either direcions, if required.
The correct line of the paper is important to the lateral registration. Follow the
instructions below as a guide to setting the line of paper up correctly to ensure a
consistently straight web path.
Before beginning the following it is important to have the back plates of the DLP
When loading the media onto the unwind mandrel it is
recommended but not essential, to keep the paper to
position to the back of the machine. This
allows for faster changes in web width as only the near
side paper guides will need to be moved.
It is important to set the 2 lower paper guides first. After
the paper for a few feet you can set the paper
guides. Make sure that the guides are set against the
media so as not to allow for any lateral movement.
It is easier to nip the paper guides up only a little so
that they can be moved by hand if requir
ed.
Once through the machine attach the media to a core
on one of the rewind mandrels. If the job requires more
than one roll to be rewound, take note of the position of
the first roll on the mandrel ruler, as it winds up on the
make the repositioning of new cores
Use the lateral web adjuster to move the web across the
machine if needed. This can be done while the machine
is running. Wait for a few impressions before moving it
again to see how much movement you ha
ve made. Try
to begin a job with this adjustment in the center of travel
to insure movement in either direcions, if required.
The correct line of the paper is important to the lateral registration. Follow the
instructions below as a guide to setting the line of paper up correctly to ensure a
19
Before beginning the following it is important to have the back plates of the DLP
When loading the media onto the unwind mandrel it is
recommended but not essential, to keep the paper to
position to the back of the machine. This
allows for faster changes in web width as only the near
It is important to set the 2 lower paper guides first. After
the paper for a few feet you can set the paper
guides. Make sure that the guides are set against the
media so as not to allow for any lateral movement.
It is easier to nip the paper guides up only a little so
Once through the machine attach the media to a core
on one of the rewind mandrels. If the job requires more
than one roll to be rewound, take note of the position of
the first roll on the mandrel ruler, as it winds up on the
make the repositioning of new cores
Use the lateral web adjuster to move the web across the
machine if needed. This can be done while the machine
is running. Wait for a few impressions before moving it
ve made. Try
to begin a job with this adjustment in the center of travel
to insure movement in either direcions, if required.
The correct line of the paper is important to the lateral registration. Follow the
instructions below as a guide to setting the line of paper up correctly to ensure a
Before beginning the following it is important to have the back plates of the DLP
The correct line of the paper is important to the lateral registration. Follow the
instructions below as a guide to setting the line of paper up correctly to ensure a
Before beginning the following it is important to have the back plates of the DLP
-
2000 and the unwind
The correct line of the paper is important to the lateral registration. Follow the
instructions below as a guide to setting the line of paper up correctly to ensure a
2000 and the unwind
The correct line of the paper is important to the lateral registration. Follow the
instructions below as a guide to setting the line of paper up correctly to ensure a
2000 and the unwind

Adjusting mark sensor position
The DLP-
2000 machine is fitted with an amplified laser black mark sensor. It can be moved
within the die cutting area however to reduce set up time for each job and minimize any settings, follow
these instructions.
Adjust the sensor so that it points to the mark approximately in line with the zero line on the sensor
ruler. The s
setting up your digital print, always place the black mark
The adjuster for along the web registration is used to adv
position of the cutting die. Anti
machine. If the above instructions are followed very little movement will be required for registration
If the user keeps the paper guides at the back of the machine, in a constant fixed position, there will also
be very little adjustment required for the sensor, across the web. If it is required, with the lids
hold both ends of the sensor
up with the black mark. Gently lock the sensor bar position using the grub screws in both ends of the
sensor bar.
Adjusting mark sensor position
2000 machine is fitted with an amplified laser black mark sensor. It can be moved
within the die cutting area however to reduce set up time for each job and minimize any settings, follow
these instructions.
Adjust the sensor so that it points to the mark approximately in line with the zero line on the sensor
ruler. The s
ensor is deliberately set on an angle to avoid excess reflection on glossy materials. When
setting up your digital print, always place the black mark
The adjuster for along the web registration is used to adv
position of the cutting die. Anti
machine. If the above instructions are followed very little movement will be required for registration
If the user keeps the paper guides at the back of the machine, in a constant fixed position, there will also
be very little adjustment required for the sensor, across the web. If it is required, with the lids
hold both ends of the sensor
up with the black mark. Gently lock the sensor bar position using the grub screws in both ends of the
sensor bar.
Adjusting mark sensor position
2000 machine is fitted with an amplified laser black mark sensor. It can be moved
within the die cutting area however to reduce set up time for each job and minimize any settings, follow
Adjust the sensor so that it points to the mark approximately in line with the zero line on the sensor
ensor is deliberately set on an angle to avoid excess reflection on glossy materials. When
setting up your digital print, always place the black mark
The adjuster for along the web registration is used to adv
position of the cutting die. Anti
-
clockwise turning will advance the print towards the slitting end of the
machine. If the above instructions are followed very little movement will be required for registration
If the user keeps the paper guides at the back of the machine, in a constant fixed position, there will also
be very little adjustment required for the sensor, across the web. If it is required, with the lids
hold both ends of the sensor
bar and gently pull forward or push back to the required position, for lining
up with the black mark. Gently lock the sensor bar position using the grub screws in both ends of the
Adjusting mark sensor position
2000 machine is fitted with an amplified laser black mark sensor. It can be moved
within the die cutting area however to reduce set up time for each job and minimize any settings, follow
Adjust the sensor so that it points to the mark approximately in line with the zero line on the sensor
ensor is deliberately set on an angle to avoid excess reflection on glossy materials. When
setting up your digital print, always place the black mark
The adjuster for along the web registration is used to adv
clockwise turning will advance the print towards the slitting end of the
machine. If the above instructions are followed very little movement will be required for registration
If the user keeps the paper guides at the back of the machine, in a constant fixed position, there will also
be very little adjustment required for the sensor, across the web. If it is required, with the lids
bar and gently pull forward or push back to the required position, for lining
up with the black mark. Gently lock the sensor bar position using the grub screws in both ends of the
20
2000 machine is fitted with an amplified laser black mark sensor. It can be moved
within the die cutting area however to reduce set up time for each job and minimize any settings, follow
Adjust the sensor so that it points to the mark approximately in line with the zero line on the sensor
ensor is deliberately set on an angle to avoid excess reflection on glossy materials. When
setting up your digital print, always place the black mark
in the center
The adjuster for along the web registration is used to adv
ance or retard the print, in relation to the
clockwise turning will advance the print towards the slitting end of the
machine. If the above instructions are followed very little movement will be required for registration
If the user keeps the paper guides at the back of the machine, in a constant fixed position, there will also
be very little adjustment required for the sensor, across the web. If it is required, with the lids
bar and gently pull forward or push back to the required position, for lining
up with the black mark. Gently lock the sensor bar position using the grub screws in both ends of the
2000 machine is fitted with an amplified laser black mark sensor. It can be moved
within the die cutting area however to reduce set up time for each job and minimize any settings, follow
Adjust the sensor so that it points to the mark approximately in line with the zero line on the sensor
ensor is deliberately set on an angle to avoid excess reflection on glossy materials. When
in the center
of the image(s) to be cut.
ance or retard the print, in relation to the
clockwise turning will advance the print towards the slitting end of the
machine. If the above instructions are followed very little movement will be required for registration
If the user keeps the paper guides at the back of the machine, in a constant fixed position, there will also
be very little adjustment required for the sensor, across the web. If it is required, with the lids
bar and gently pull forward or push back to the required position, for lining
up with the black mark. Gently lock the sensor bar position using the grub screws in both ends of the
2000 machine is fitted with an amplified laser black mark sensor. It can be moved
within the die cutting area however to reduce set up time for each job and minimize any settings, follow
Adjust the sensor so that it points to the mark approximately in line with the zero line on the sensor
ensor is deliberately set on an angle to avoid excess reflection on glossy materials. When
of the image(s) to be cut.
ance or retard the print, in relation to the
clockwise turning will advance the print towards the slitting end of the
machine. If the above instructions are followed very little movement will be required for registration
If the user keeps the paper guides at the back of the machine, in a constant fixed position, there will also
be very little adjustment required for the sensor, across the web. If it is required, with the lids
bar and gently pull forward or push back to the required position, for lining
up with the black mark. Gently lock the sensor bar position using the grub screws in both ends of the
2000 machine is fitted with an amplified laser black mark sensor. It can be moved
anywhere
within the die cutting area however to reduce set up time for each job and minimize any settings, follow
Adjust the sensor so that it points to the mark approximately in line with the zero line on the sensor
ensor is deliberately set on an angle to avoid excess reflection on glossy materials. When
of the image(s) to be cut.
ance or retard the print, in relation to the
clockwise turning will advance the print towards the slitting end of the
machine. If the above instructions are followed very little movement will be required for registration
If the user keeps the paper guides at the back of the machine, in a constant fixed position, there will also
be very little adjustment required for the sensor, across the web. If it is required, with the lids
closed
bar and gently pull forward or push back to the required position, for lining
up with the black mark. Gently lock the sensor bar position using the grub screws in both ends of the
anywhere
within the die cutting area however to reduce set up time for each job and minimize any settings, follow
Adjust the sensor so that it points to the mark approximately in line with the zero line on the sensor
ensor is deliberately set on an angle to avoid excess reflection on glossy materials. When
ance or retard the print, in relation to the
clockwise turning will advance the print towards the slitting end of the
machine. If the above instructions are followed very little movement will be required for registration
.
If the user keeps the paper guides at the back of the machine, in a constant fixed position, there will also
closed
,
bar and gently pull forward or push back to the required position, for lining
up with the black mark. Gently lock the sensor bar position using the grub screws in both ends of the
Table of contents
Other AFINIA LABEL Label Maker manuals
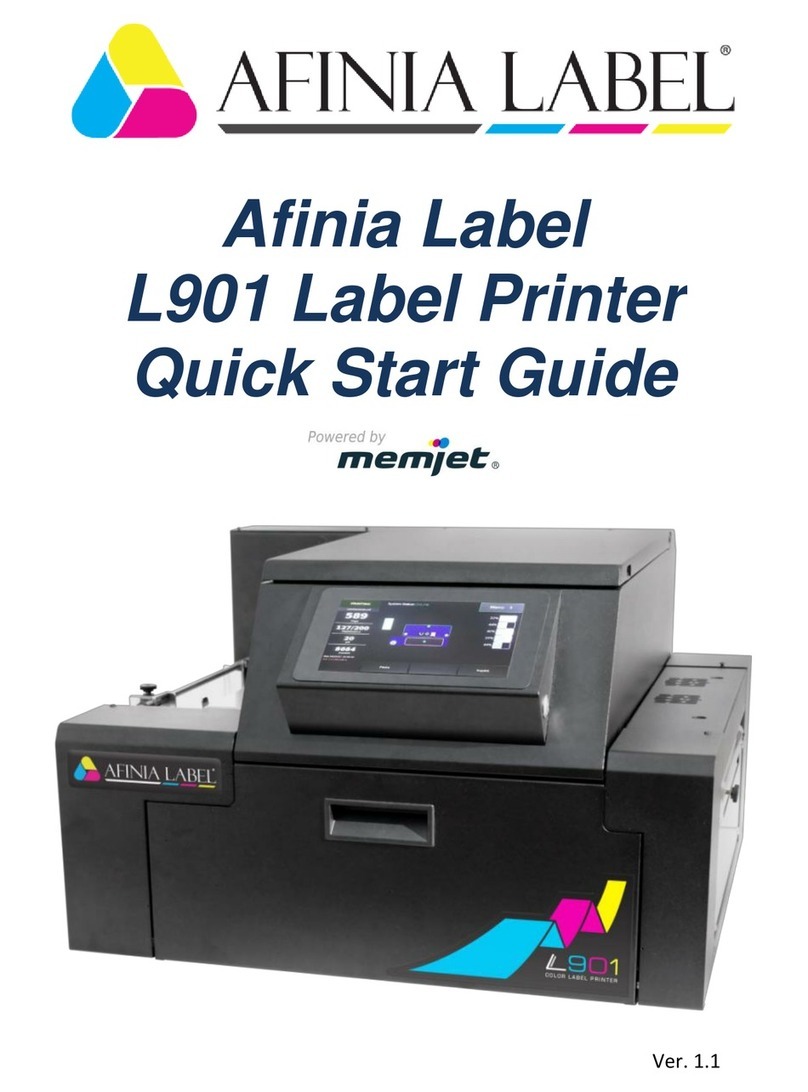
AFINIA LABEL
AFINIA LABEL L901 User manual
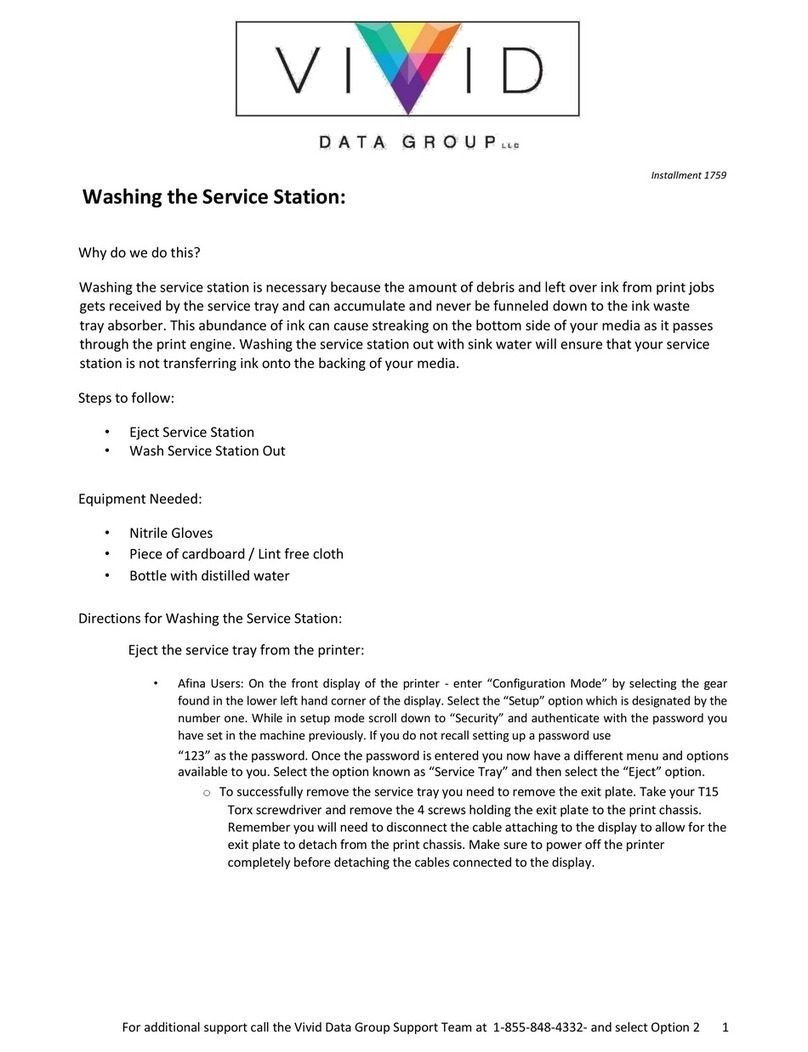
AFINIA LABEL
AFINIA LABEL L801 User manual
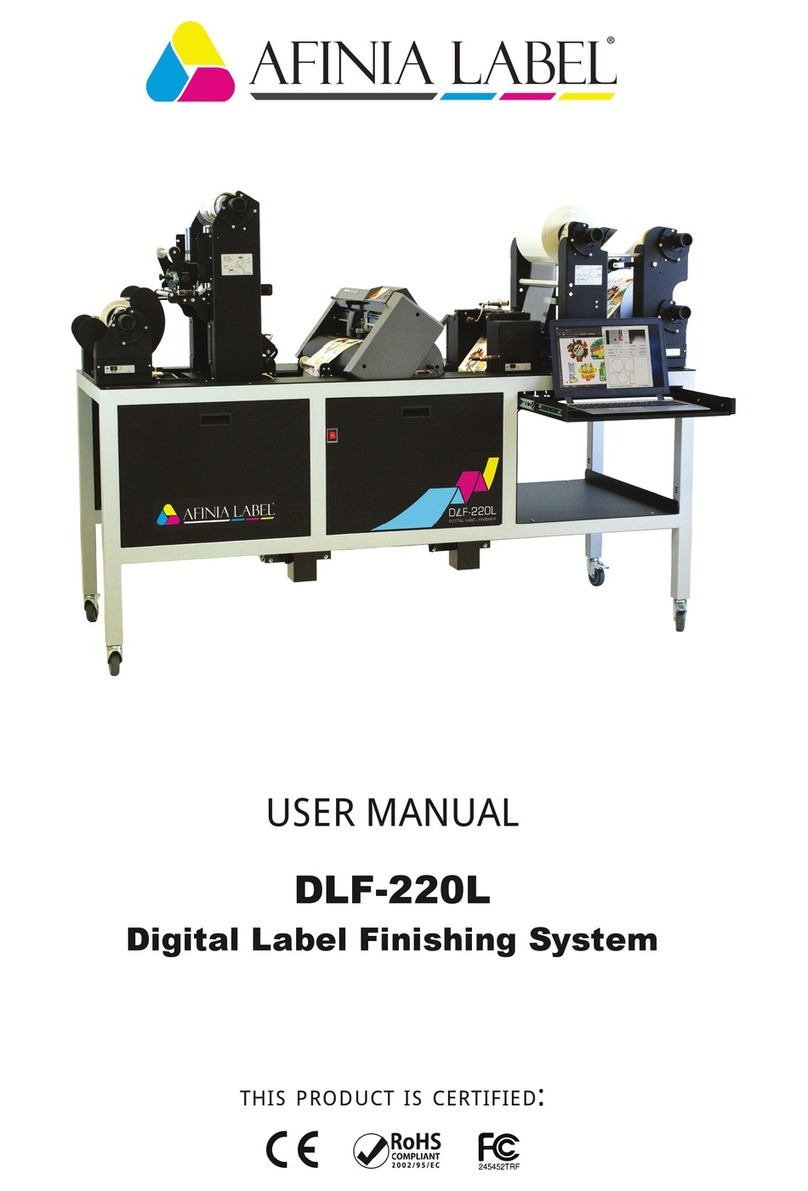
AFINIA LABEL
AFINIA LABEL DLF-220L User manual
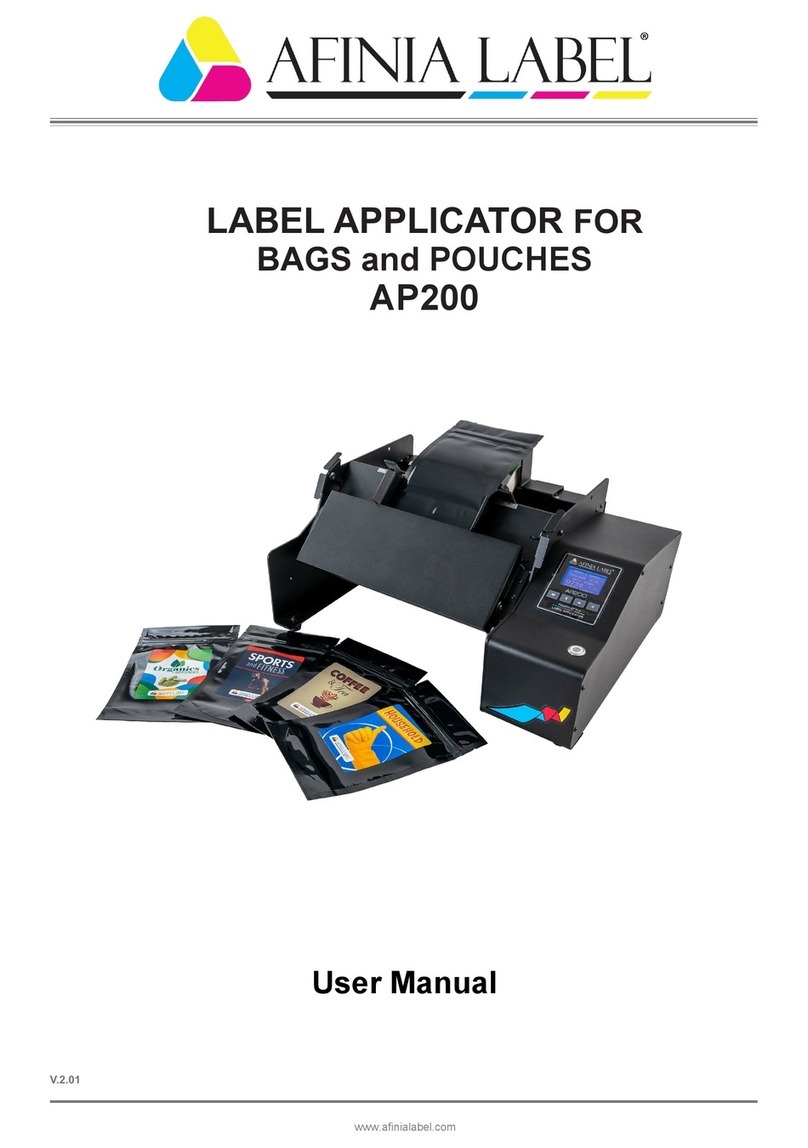
AFINIA LABEL
AFINIA LABEL AP200 User manual

AFINIA LABEL
AFINIA LABEL Mini DLF Series User manual
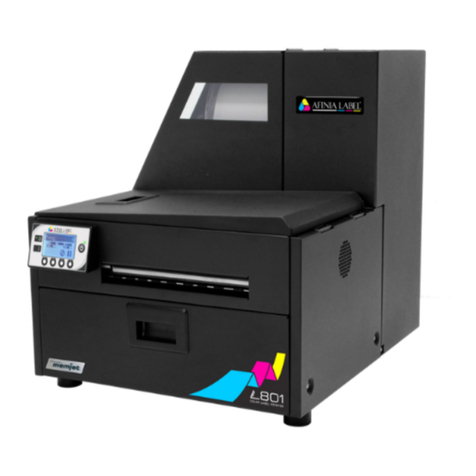
AFINIA LABEL
AFINIA LABEL L801 Reference manual
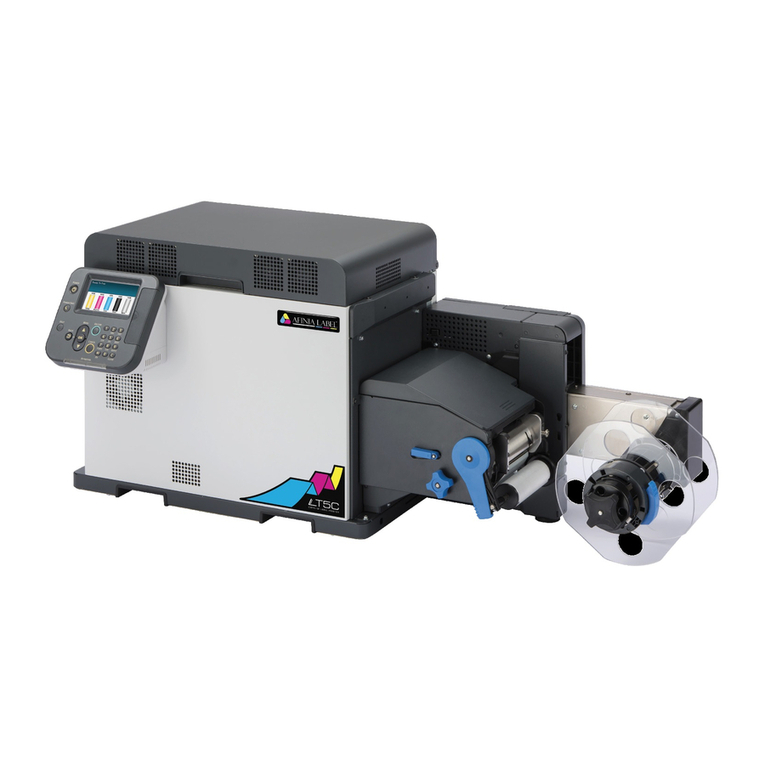
AFINIA LABEL
AFINIA LABEL LT5C User manual
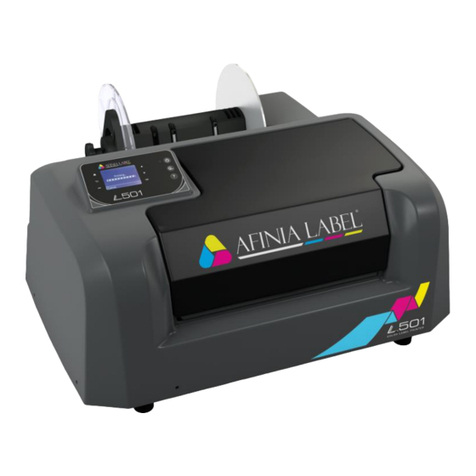
AFINIA LABEL
AFINIA LABEL Afinia L501 Specification sheet
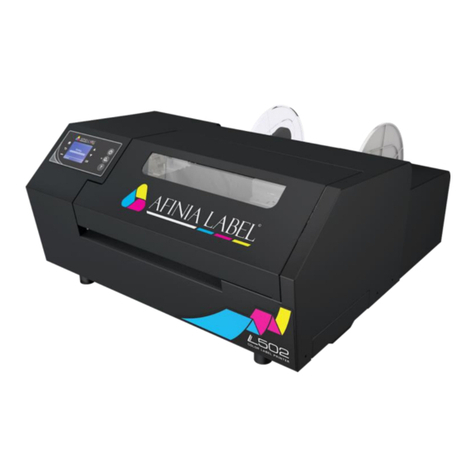
AFINIA LABEL
AFINIA LABEL Afinia 502 Specification sheet

AFINIA LABEL
AFINIA LABEL L301 Specification sheet