AimTTi LCR400 User manual

LCR400
Precision LCR Bridge INSTRUCTION MANUAL

1
Table of Contents
Introduction 1
Specification 2
Safety 4
Installation 5
Connections 6
Operation 7
Measurement Principles 9
Component Sorting 13
Remote Operation 17
Remote Commands 18
Maintenance 21
Instructions en Francais 22
Bedienungsanleitung auf Deutsch 43
Istruzioni in Italiano 65
Instrucciones en Español 86
Introduction
The LCR 400 Precision Bridge provides a fast, convenient and accurate means of measuring the
inductance, capacitance, resistance, D and Q of components with a basic accuracy of 0.1%. The
major and minor parameters of the component are displayed simultaneously.
The microprocessor controlled unit provides fully automatic mode and range selection for a wide
range of components. Control is by front panel keyboard or by RS232 link to a PC which can be
used to set up all measurement functions.
The LCR400 can be programmed to sort a range of components into bins according to value.
Multiple bins can be set to sort different tolerances of the same value or different values.
Up to nine measurement set-ups can be stored in the instrument in non-volatile memory and
called up for re-use with a few keystrokes.
Connections to the components are made via the built in four–terminal test fixture or plug–in axial
adaptor providing true contact resistance free measurements for low impedance components.
The capacitance (up to 100pf) introduced by an external test fixture can be cancelled out
permitting high impedance measurements to be made with confidence.

2
Specification
Specifications apply for 18ºC −28ºC ambient after 30 minute warm-up.
Functions
Parameters Measured:
R, L, C, D & Q.
Measurement Modes:
Series or parallel equivalent circuit.
Measurement Functions: Fully autoranging including selection between L, C and R. The Zero C
function nulls out up to 100pF of stray capacitance in the test fixture.
Measurement Frequency: User selectable to be 100Hz, 1kHz or 10kHz; frequency accuracy
± 0.01%. 120Hz instead of 100Hz by factory option for 60Hz operation.
Measurement Ranges
and Resolution:
Parameter
Range
R
0.1mΩ−990MΩ
L 0.001µH −9900H
C
0.001pF −99000µF
D
0.001 −999
Q
0.001 −999
Measurement Accuracy:
100/120Hz
1kHz
10kHz
R (Q<0·1) 0.1% ± 1 digit
0.5% ± 1 digit
2% ± 1 digit
2Ω−1MΩ
0.4Ω−5MΩ
0.1Ω−20MΩ
2Ω − 500kΩ
0.4Ω − 2MΩ
0.1Ω−10MΩ
2Ω − 50kΩ
0.4Ω − 200kΩ
0.1Ω – 500kΩ
L (Q>10) 0.1% ± 1 digit
0.5% ± 1 digit
2% ± 1 digit
4mH – 500H
800µH – 2500H
200µH
−
9900H
400µH −50H
80µH – 250H
20µH −1000H
40µH −5H
8µH – 25H
2µH −100H
C (D<0.1) 0.1% ± 1 digit
0.5% ± 1 digit
2% ± 1 digit
10nF −1000µF
2nF −5000µF
500pF −20000µF
1nF −100µF
200pF −500µF
50pF −2000µF
100pF −10µF
20pF −50µF
5pF −200µF
Q & D 0.25% ± 1 digit 0.25 −4.0
for C = 40nF – 100µF
or L = 10mH – 50H
0.25 −4.0
for C = 10nF – 10µF
or L = 1mH – 2.5H
0.25 −4.0
for C = 1nF – 1µF
or L = 100µH – 250mH
Capacitance accuracies apply after null.
Measurement Update Rate:
2.5 readings per second.
Limits Comparator (Sort Mode)
Type:
Comparison with multiple limits set up from the keyboard or PC via RS232 interface.
Binning:
Up to 8 Pass bins for the major parameter, plus minor parameter Fail and general Fail bins.

3
Display
Display Type: Dual 5-digit 0·56” LEDs with range and function indication.
Maximum display count 50,000.
Display Functions: Simultaneous display of R + Q, L + Q, C + D, or C + R in normal
measurement modes.
Prompts to change frequency or mode to improve accuracy.
Simultaneous display of Pass/Fail status with Bin No. in Sort mode.
Inputs
Component Connection:
4-terminal connection for both radial and axial devices.
Maximum Voltage on
Component:
0·3Vrms.
Bias Voltage:
Switchable 2V polarising voltage for measuring electrolytic capacitors.
Input Protection: The instrument has been designed to withstand direct connection of
capacitors charged up to 50V DC with up to 1 Joule ( ½ CV 2 ) of stored
energy.
Interfaces
RS232: Serial link to PC permitting range/function control, limits setting and
results data-logging on the PC.
General
Keyboard:
Full numeric keyboard for entry of limits data.
Non-Volatile Memory:
Up to 9 complete set ups stored in non-volatile memory.
Power: 220V-240V AC or 110V-120V AC ±10%, 50/60Hz, adjustable internally;
25VA max. Installation Category II.
Operating Range:
+5ºC to 40ºC, 20-80% RH.
Storage Range:
–40ºC to 70ºC.
Environmental:
Indoor use at altitudes up to 2000m, Pollution Degree 2.
Safety & EMC: Complies with EN61010-1 & EN61326-1.
For details, request the EU Declaration of Conformity for this instrument
via http://www.aimtti.com/support (serial no. needed).
Size:
365 x 240 x 95 mm, including feet.
Weight:
2.9 kg.
Options: Remote 4–terminal measurement interface.
4–terminal surface mount tweezers.
Kelvin Clip set.
PC logging software.

4
Safety
This instrument is Safety Class I according to IEC classification and has been designed to meet
the requirements of EN61010−1 (Safety Requirements for Electrical Equipment for
Measurement, Control and Laboratory Use). It is an Installation Category II instrument intended
for operation from a normal single phase supply.
This instrument has been tested in accordance with EN61010−1 and has been supplied in a safe
condition. This instruction manual contains some information and warnings which have to be
followed by the user to ensure safe operation and to retain the instrument in a safe condition.
This instrument has been designed for indoor use in a Pollution Degree 2 environment in the
temperature range 5°C to 40°C, 20% −80% RH (non−condensing). It may occasionally be
subjected to temperatures between +5° and −10°C without degradation of its safety. Do not
operate while condensation is present.
Use of this instrument in a manner not specified by these instructions may impair the safety
protection provided. Do not operate the instrument outside its rated supply voltages or
environmental range.
WARNING! THIS INSTRUMENT MUST BE EARTHED
Any interruption of the mains earth conductor inside or outside the instrument will make the
instrument dangerous. Intentional interruption is prohibited. The protective action must not be
negated by the use of an extension cord without a protective conductor.
When the instrument is connected to its supply, terminals may be live and opening the covers or
removal of parts (except those to which access can be gained by hand) is likely to expose live
parts. The apparatus shall be disconnected from all voltage sources before it is opened for any
adjustment, replacement, maintenance or repair.
Any adjustment, maintenance and repair of the opened instrument under voltage shall be
avoided as far as possible and, if inevitable, shall be carried out only by a skilled person who is
aware of the hazard involved.
If the instrument is clearly defective, has been subject to mechanical damage, excessive
moisture or chemical corrosion the safety protection may be impaired and the apparatus should
be withdrawn from use and returned for checking and repair.
Make sure that only fuses with the required rated current and of the specified type are used for
replacement. The use of makeshift fuses and the short−circuiting of fuse holders is prohibited.
Do not wet the instrument when cleaning it.
The following symbols are used on the instrument and in this manual:−
Caution −refer to the accompanying documentation,
incorrect operation may damage the instrument.
alternating current.

5
Installation
Mains Operating Voltage
The operating voltage of the instrument is shown on the rear panel. Should it be necessary to
change the operating voltage from 230V to 115V or vice-versa, proceed as follows:
1. Disconnect the instrument from all voltage sources.
2. Remove the 6 screws which hold the case upper to the chassis and lift off, noting the flat
cable connector positions.
3. Remove the 4 screws securing the power supply pcb to the chassis and lift the pcb free.
4. Change the appropriate zero-ohm links beside the transformer on the pcb:
Link LK4 only for 230V operation
Link LK3 and LK5 only for 115V operation
Note that, if the change of operating voltage is accompanied by a change of supply
frequency, optimum common mode rejection of the mains will be achieved by setting the
internal 100/120Hz selection to 100Hz for 50Hz supply and 120Hz for a 60Hz supply.
This is set by the status of link LK2 which is situated immediately below the oscillator
module on the main circuit board. With no shorting link fitted to the pins the frequency is
set to 100Hz; if a shorting link is fitted it is set to 120Hz. The factory setting for 230V
operation is 100Hz and for 115V operation is 120Hz. If LK2 is changed from the factory
setting the unit will need to be recalibrated at the new frequency setting (calibration
settings for 100Hz and 120Hz cannot be held simultaneously).
5. Refit the pcb to the chassis, ensuring all connections (especially safety earth) are remade
as before, and refit the case upper.
6. To comply with safety standard requirements the operating voltage marked on the rear
panel must be changed to clearly show the new voltage setting.
7. Change the fuse to suit the new operating voltage, see below.
Fuse
The correct time-lag fuse must be fitted for the selected operating voltage.
For 230V operation use 125mA (T) 250V HBC.
For 115V operation use 250mA (T) 250V HBC.
Make sure that only fuses with the required rated current and of the specified type are used for
replacement. The use of makeshift fuses and the short-circuiting of fuse holders are prohibited.
Mains Lead
Connect the instrument to the AC supply using the mains lead provided. Should a mains plug be
required for a different mains outlet socket, a suitably rated and approved mains lead set should
be used which is fitted with the required wall plug and an IEC60320 C13 connector for the
instrument end. To determine the minimum current rating of the lead-set for the intended AC
supply, refer to the power rating information on the equipment or in the Specification.
WARNING! THIS INSTRUMENT MUST BE EARTHED
Any interruption of the mains earth conductor inside or outside the instrument will make the
instrument dangerous. Intentional interruption is prohibited.

6
Connections
Component Connections
The leads of the Device Under Test (DUT) are inserted in the Kelvin connectors on the top of the
instrument. Axial components can be inserted into the adaptors supplied, which themselves are
inserted into the Kelvin connectors. Both forms of connection provide true four–terminal contact
to the DUT to ensure accurate measurement of low impedance components.
The leads of radial components can be pushed directly into the spring–loaded connectors.
Alternatively, for delicate leads, the connectors can be opened by pressing down on the
connector actuators.
Similarly, the axial adaptors can be inserted by pushing directly into the main connectors; adjust
the position of the adaptors to suit the lead and body length of the axial DUT.
Ensure the contact surfaces of the Kelvin connectors are free from contamination. If in doubt,
refer to the Maintenance section.
Surface Mount Components
Plug the interface module of the optional surface mount tweezers into the Kelvin connectors.
True four–terminal connection is maintained at the tweezers.
Remote Connections
A remote test jig can be connected via the BNC connectors on the optional interface module
which inserts into the Kelvin connectors on the top of the instrument. The connectors are labelled
High Drive, High Sense, Low Sense and Low Drive. The screens of the Drive coax cables should
be connected together at the remote end and connected to the screen and case of the external
jig. The screens of the Sense leads should be isolated both from each other and from the jig
screen.
Whilst leads of up to 1 metre are unlikely to present problems, the leads to an external jig should
be kept as short as possible and the accuracy of measurements checked at all test frequencies
and over the range of values being measured before being relied upon.
RS232
9–pin D–connector for PC remote control with the following connections:
Pin
Name
Description
1
DCD
Linked to pins 4 and 6
2
TXD
Transmitted data from instrument
3
RXD
Received data to instrument
4
DTR
Linked to pins 1 and 6
5
GND
Signal ground
6
DSR
Linked to pins 1 and 4
7
RTS
Linked to pin 8
8
CTS
Linked to pin 7
9
–
No internal connection
Connect to a PC with a cable which has pins 2, 3 and 5 wired plus pins 1, 4 & 6 and pins 7 & 8
linked at the PC end. Alternatively, since the links are made within the instrument, a fully–wired
1–to–1 cable may be used.

7
Operation
This section covers general use of the instrument. Although the basic capabilities are largely
obvious from the keypad functions, users requiring full performance and accuracy are advised to
read this and the Measurement Principles sections in full.
Switching On
Switch on the instrument using the ON/OFF switch on the rear panel.
At switch on the instrument runs a short internal self test procedure, displays the software
version, and then waits in Auto mode for a component to measure. If it is switched on with a
component connected it will automatically detect and measure that component.
To fully disconnect from the AC supply unplug the mains cord from the back of the instrument or
switch off at the AC supply outlet; make sure that the means of disconnection is readily
accessible. Disconnect from the AC supply when not in use.
Display
In normal use the left–hand 5–digit display shows the value of the major parameter (L, C or R)
and the right–hand display shows the value of the minor parameter (Q, D or R). The parameters
being displayed are indicated above their respective numeric values and the units of the
parameter are shown to the right of the value itself. A display test which lights all the indicators
can be carried out by holding down any key while the instrument is switched on.
Basic measurement accuracy is 0.1% and, for the impedance range for which this accuracy is
guaranteed (see Specification) the instrument will autorange to give typically between 5,000 and
50,000 counts of display resolution. If the measured value is outside the range within which
0.1% accuracy is guaranteed (at the measurement frequency selected) the units indicator (kΩ,
pF, etc.) will flash to show this. If the frequency indicator is also flashing, changing the frequency
range may bring the component being measured within the range of the instruments 0.1%
accuracy specification. For example, measuring 680pF at the default Auto frequency of 1kHz will
cause both the units indicator (pF) and frequency range lamp to flash; changing the frequency to
10kHz brings 680pF within the instrument’s 0.1% specification and both lamps will stop flashing.
During the set–up and use of the sort facility the displays have other uses; these are fully
explained in the Component Sorting section.

8
Measurement Keys and Indicators
Frequency
Pressing the Freq key sets the test frequency for the measurement to 100/120Hz, 1kHz or
10kHz.
Note: For a 50Hz supply the lowest test frequency will generally be 100Hz, for a 60Hz supply it
will generally be 120Hz, see Installation section.
Pressing the key changes the frequency from 100/120Hz to 1kHz to 10kHz and back to
100/120Hz. The lamp indicates the setting being used. If the lamp flashes it is a warning that
another frequency may give a more accurate measurement for a component of that type and
value.
Mode Selects either series or parallel mode equivalent circuit values to be displayed, see Measurement
Principles section. If the lamp flashes it is a warning that the other mode is the more usual
selection for a component of that type and value. If Auto mode has been selected the Mode
cannot be changed without first selecting L, C or R mode.
Bias This applies 2 Volts DC across the test terminals to polarise electrolytic capacitors according to
the polarity marked on the Kelvin connectors. Note that applying bias to resistors or inductors
may cause a measurement error because of internal overload. Bias voltages up to 50V DC can
be applied externally, see the External Bias section of the Measurement Principles chapter.
Zero C
When measuring capacitors, pressing this button prior to inserting the component under test
zeroes the capacitance reading thereby eliminating the capacitance of the test jig. Up to 100pF of
stray capacitance may be zeroed out in this way. The correction factor is lost when the bridge is
turned off. Zero C can only be used when capacitance is being measured; if any other function is
selected the display will show not C for 2 seconds and the command will be ignored.
R+Q, L+Q, C+D, C+R
Sets the instrument to show the major parameter in the left–hand display and the corresponding
minor parameter on the right.
Auto In Auto mode the instrument automatically detects whether the component being measured is a
resistor, capacitor or inductor and sets the instrument to display the parameters of the test
component automatically. Note that ‘imperfect’ components, e.g. inductors with a high series
resistance, may be incorrectly detected in Auto mode and will need to have the correct function
set manually. In Auto mode the measurement frequency can be changed (by pressing the Freq
key) but the Series/Parallel mode selection is held at the default selection for that component
type, see Measurement Principles section. To change from series to parallel mode, or
vice–versa, it is first necessary to exit Auto mode by selecting the appropriate function
(R+Q, L+Q, etc.); the mode can then be changed with the Mode key.
Range Hold
Holds the measurement range at that in use when the button is pressed. This disables the auto–
ranging and minimises the settling time between measurements of similar value components.
Note that DUT voltage and current measurement are individually auto–ranged for optimum
accuracy and resolution; the processor then determines the measurement uncertainty and sets
an appropriate display resolution. Range Hold fixes all of these ranges. If a component with a
significantly different value is measured, causing any of these ranges to be exceeded, the display
will show or (out of range) and Range Hold will need to be turned off to get a true reading.
Sorting Keys and Store/Recall Keys
The keys used to set up sorting and binning, and to store and recall complete sorting set–ups,
are described in the Component Sorting section.

9
Measurement Principles
Circuit models
Resistors, capacitors and inductors can all be represented at a given frequency by a simple
series or parallel equivalent circuit. It must be stressed that this is a simple equivalent circuit and
as such will only be representative over a limited frequency range. The effects of a wide
frequency range are discussed later.
The Models used by the LCR400 are as follows:
Lpj
Rp LpRpj
Zp
Lsj
RsZs
ω
ω
ω
+
=
+
=
Rs
Ls
Lp
Rp
Q
ω
ω
=
=
Lp
Q
Q
Ls 2
2
1+
=
Q
L
Rs s
ω
=
LpQRp
ω
=
Cs
jRsZs
ω
1
−=
RpCpjRp
Zp
ω
+
=1
RpCp
RsCsD
ω
ω
1
==
Q
D1
=
(D is also known as tan
δ
)
CpDCs )1
(
2
+
=
Rp
D
D
Rs
2
2
1+
=
where
ω =
2πf
Resistors
All resistors have parasitic impedances, both inductance and capacitance and distributed effects
of both. Fortunately, however, in normal use these parasitic effects are usually very small
compared with the resistance.
The LCR 400 provides the opportunity to evaluate the series and parallel components of resistors
at 100Hz and 1kHz and 10kHz.
Some types of resistor have more prominent parasitic effects than others. Wire wound resistors,
unless they are specially wound, have more inductance than their carbon and metal film
equivalents. Even carbon film resistors have inductance due to the inductance of the leads and
the spiral cut used to trim the resistance. There is also always capacitance between the end cap
connections - on metal film resistors it is typically around 0.25pF. This usually only becomes
significant on high value resistors or/and at high frequencies. Bifilar wound resistors may have
low inductance but the close proximity of the windings can introduce significant capacitance –
distributed along the resistance. To predict the performance of such a component at high

10
frequencies requires a more complex equivalent circuit than the simple two component series or
parallel circuits discussed here. In practice the solution is to select component types to match
the frequency range of the application.
For the majority of resistors, where inductive and capacitive parasitics are minimal, both series
and parallel circuits will give identical results for resistance.
For resistors where inductance is the significant parasitic, the series equivalent circuit will give
the value which matches the manufacturer’s data-sheet. For high value devices, capacitance can
start to be significant and the parallel equivalent circuit may be more appropriate.
Normally R+Q should be selected for resistors; the Q of a resistor will usually be very low –
especially at the low measurement frequencies used. However if the series and parallel
resistances at 10kHz differ significantly to those at 100Hz or 1kHz, the Q will be significant. Either
the inductance or capacitance of the resistor is producing an effect. Selecting either C+R or L+Q
will quantify the parasitic capacitance or inductance.
Low value resistors can be measured at any of the three LCR400 test frequencies but high value
resistors (>100kΩ) are best measured on the 100Hz range. The instrument warns if a
measurement is outside its maximum accuracy range by flashing the units annunciator; if
accuracy can be improved by changing the measurement frequency the frequency annunciator
will also flash, see Display section.
Capacitors
All capacitors have parasitic inductance and resistance in addition to their intended capacitance.
The leads of a capacitor can add significant inductance at high frequencies. Spiral wound metal
film capacitors can have significant parasitic inductance, which is why they are not used for
decoupling high frequencies. Some types of ceramic capacitors can provide excellent de-
coupling, i.e. have high capacitance with low series resistance and inductance, but can be very
lossy. Large value electrolytic capacitors can have significant inductance – this inductance can
even resonate with the capacitance at the measurement frequencies of the LCR400. This has the
effect of showing a known high value capacitor to have either negative capacitance or
inductance.
Capacitors have two main types of parasitic resistance. Firstly there is the physical resistance of
the dielectric and dielectric losses; this is normally specified in terms of the Dissipation Factor ‘D’
or loss tangent and is frequency dependent. Secondly, there is the physical resistance of the
leads and the connections to the electrodes on the dielectric. The lead and connection resistance
are usually negligible, but on high value electrolytics, used to smooth power supplies, it can be
very important. The series resistance of such devices is often a manufacturers specified
parameter.
For most capacitors, other than high value electrolytics, the parallel equivalent circuit will give the
capacitance that matches the manufacturers data sheet. For low loss capacitors the series and
parallel equivalent capacitances will be the same.
Electrolytic capacitors are polarity sensitive and should be connected to the instrument correctly
and bias applied. For very high value electrolytics, for which the manufacturer specifies
Equivalent Series Resistance (ESR) the series equivalent circuit should be used.
The LCR 400 provides the means to investigate the losses of capacitors either in terms of
dissipation factor (C+D) or in terms of equivalent series or parallel resistance (C+R).
To get maximum resolution and accuracy, low values of capacitance, (<4nF) are best measured
on the LCR 400 at 10kHz after zeroing the capacitance with no component connected. Higher
values, (>10µF) should be measured at 100Hz. The instrument warns if a measurement is
outside its maximum accuracy range by flashing the units annunciator; if accuracy can be
improved by changing the measurement frequency the frequency annunciator will also flash, see
Display section.

11
External Bias
The 2 Volt DC bias available internally (see the Measurement Keys and Indicators section) is
usually adequate for polarizing electrolytic capacitors. However, it is possible to externally
connect a fully floating power supply (or battery) to give a bias voltage of up to 50 Volts DC.
The external DC bias must be connected to the LCR400 and DUT as shown in the diagram. The
High Drive, High Sense, Low Drive and Low Sense connections to the LCR400 are made using
the optional interface module which inserts into the Kelvin connectors on the top of the
instrument.
The BNC connectors on the interface module are marked with the signal names. Connect to the
power supply and DUT using screened cables, e.g. miniature coaxial cable, but leave the
screens unconnected at the remote end.
CAUTION. Always observe the correct polarity when connecting capacitors; failure to do so
may result in damage to the DUT and possible user injury.
Always discharge capacitors after making measurements with a DC bias, especially at high bias
voltages; failure to do so may result in possible user injury and damage to the LCR400 if the
charged capacitor is subsequently connected directly to the Kelvin connectors. The LCR400
has been designed to withstand the direct connection of capacitors charged up to 50V DC with
up to 1 Joule of stored energy ( ½ CV 2 ); it should not, however, be used to routinely discharge
such capacitors. Higher voltage or higher energy may result in damage to the instrument.
Inductors
All inductors have resistive losses, parasitic capacitance and an external coupled magnetic field.
The resistive losses are the resistance equivalent to losses in the core and the resistance of the
conductive wire making up the turns of the inductor. There is capacitance between each turn of
conductor and every other turn. The magnetic field of an inductor can extend outside the physical
package of the component.
In its simplest form the resistance can be represented as a resistor in series with the inductance,
and the capacitance as a capacitor in parallel. The effect of an inductor’s self capacitance and
inductance at any given frequency combine to produce net inductance below the resonant
frequency or capacitance above the resonant frequency.

12
On high value inductors, such as transformers designed to work at 50/60Hz, the self resonant
frequency can be below the higher test frequencies of the LCR 400. Above the self-resonant
frequency these inductors will appear as a lossy capacitor. Due to the distributed nature of these
parasitics, the equivalent values of the resistance and capacitance change with frequency.
The leaked magnetic field, whilst usually negligible in the case of torroids, laminated core
inductors and pot core inductors, can be significant with axial inductors like RF chokes and ferrite
rod antennae. This means that the inductance of a device with a ‘leaky’ magnetic field can vary
considerably depending upon the characteristics of any conducting or magnetic material close to
the device. Any conductive material within the device’s field will contain induced currents that can
in turn have the effect of reducing the apparent inductance of the component. Conversely any
ferro-magnetic material in the immediate area of the component can have the effect of increasing
the apparent inductance. In extreme cases the inductance of a component can appear to vary
depending upon its distance above the connectors and steel case of the LCR400.
Low value inductors (<100uH) are best measured at 10kHz whilst high values >25H should be
measured at 100Hz. The instrument warns if a measurement is outside its maximum accuracy
range by flashing the units annunciator; if accuracy can be improved by changing the
measurement frequency the frequency annunciator will also flash, see Display section.
Series / Parallel connection
The LCR400 provides the capability of measuring the series or parallel equivalent circuit
parameters of resistors, capacitors and inductors.
In Auto mode the bridge uses the following models.
Resistor
Series
Inductor
Series
Capacitor <1µF
Parallel
Capacitor >1µF
Series
These will provide the parameters that will match data sheet values for most components.

13
Component Sorting
The LCR 400 provides comprehensive facilities for sorting components into ‘bins’ according to
value. The parameters for each bin can be defined from the keyboard or from a PC via the
RS232 interface. Binning parameters are stored with the instrument set–up; up to 9 complete
set–ups can be stored.
Bin limits are set up as percentages around nominal values and can be overlapping or sequential
(with the same nominal) or can be percentages around quite different nominals; the bins must,
however, apply to the same parameter (R, L or C).
If only one bin is set up, all components outside the range are fails. Up to 8 bins (0–7) can be
used to sort on the basis of the major parameter; bin 8 can be used to set limits for the minor
parameter only (D, Q or R) and bin 9 is the general fail bin.
Sorting Keys
The following keys are associated with sorting; they are described more fully in the sections that
follow.
Sort
Turns the sorting function on and off.
Bin No.
Used for setting each of up to eight bin values.
Nominal
Used to set the nominal value for a bin and the limit for minor parameter (bin 8).
Limit
Used to set the limits for a bin, in percentages.
Numeric keys 0-9, •and ±
Used to enter the bin numbers, program store numbers, nominal values and percentage limits.
ΩµH pF
Used when entering nominal component values to set the appropriate multiplier.
kΩmH nF
Used when entering nominal component values to set the appropriate multiplier.
MΩH µF
Used when entering nominal component values to set the appropriate multiplier.
Enter
Used to confirm a numerical entry (value, bin number or program store number).
Store/Recall Keys
The following keys are used to store and recall set–ups:
Store
Stores the complete set–up, including the set binning values, in non volatile memory.
Recall
Recalls up to nine previously stored set–ups.

14
Simple Pass / Fail Sorting
To set up simple pass/fail sorting, first select the measurement type to be made, i.e. R+Q, L+Q,
C+D or C+R. Set the measurement frequency and select series or parallel measurement as
required.
Note: Binning cannot be set with the bridge in Auto mode.
Bin Selection
Press the Bin No. key to enter set–up mode. Successive presses of the Bin No. key will step
the display through the options of binX (where Xis the bin number), CLEAr? (clear the
selected bin), CLEAR ALL? (clear all bins) and End? (exit bin set–up mode). The first
press of Bin No. will enter the option sequence where it was last exited; it may be necessary to
press the key several times to get to the desired option.
If any previous binning information needs to be cleared select CLEAr? with the Bin No. key
and press Enter; the display should show the message CLEAr donE and then binX in
the right–hand display, ready for the next step. If all bins are to be cleared select CLEAr ALL?
and follow a similar procedure.
For simple pass/fail sorting, bin 0 must be used. The other bins (1 to 7 inclusive) should be
‘closed’ by setting their limits to zero; alternatively, and easier, all the bins can be cleared by
using CLEAr ALL? before bin 0 is set. Bin 8 can be used to set limits for the minor
parameter (Q, D, or R); parts that fail these limits fall into bin 8. Parts that fall into neither bin 0
nor bin 8 fall into bin 9, the general fail bin.
Press Bin No. until binX shows in the display. Press 0to select bin 0; bin0 should show in
the right–hand display.
Setting Nominal Value
With bin0 displayed, press the Nominal key; the left–hand display now shows six dashes and
NOM above them.
Enter the nominal value required, followed by the appropriate units key (kΩ, µF, etc.). Press
Enter to save the value; the left–hand display now shows the value entered.
To edit an entered value simply enter a new value and press Enter again.
Setting Limits
With bin0 displayed, press the Limit key; the left–hand display now shows six dashes and
+LIM above them. The units indicator changes to %.
Enter the upper limit of deviation from the nominal allowed for a pass component, as a
percentage, and press Enter. Note that the minimum value that can be entered is 0.1% and the
resolution is 0.1%. The left–hand display again shows the value entered. To change an entered
value simply enter a new value and press Enter again.
Press the Limit key again; the left–hand display shows six dashes but now with –LIM above
them. Enter the lower limit of deviation from the nominal allowed for a pass component, as a
percentage, and press Enter. Note that for a limit below the nominal value it is necessary to
enter a minus value using the ±key. Note also that the limits need not be symmetrical and can
even both be above the nominal or both below the nominal. If no –LIM limit is entered the limits
are assumed to be symmetrical about the nominal value, i.e. if the upper limit has been set to
+0.5%, the lower limit automatically defaults to –0.5%.
The lower limit (–LIM) can be set above the upper limit (+LIM) but exiting set–up mode and
selecting Sort will give Err bin0.

15
Minor Parameter Limits
To set the minor parameter limit (Q, D or R) select bin 8; do this by using the Bin No. key until
BinX is shown, then enter 8. bin8 will now show in the left–hand side of the display.
To enter the limit press Nominal; the minor parameter indicator (Q, D or R) will show in the
right–hand side of the display and the limit value should then be entered from the keyboard.
Press Enter to confirm the limit.
Parts that fail the minor parameter limit of bin 8 will fall into bin 8 regardless of whether the major
parameter passes the bin 0 limits. Use of bin 8 is optional; it is not necessary to set a limit and if
the limit is left ‘closed’ (the default state, indicated by dashes) bin 8 will be ignored.
Fail Bin
Parts that do not fall into bin 0 or bin 8 are assigned to bin 9, the general fail bin.
Using Sort
Having set up bin 0, press Bin No. until End? is shown in the display then press Enter to exit
the set–up mode.
Press Sort to turn on the sort facility. Parts that pass the major parameter percentage limits will
be indicated by PASS bin0 in the display; parts that fail the minor term limits of bin 8 (if set)
will be indicated by FAIL bin8, parts that do not fall into either bin 0 or bin 8 will be indicated
by FAIL bin9.
Storing Sort Set–ups
To store a Sort set–up press the Store key; the display shows StorE?. Press a key 1to 9
followed by Enter; after a few seconds the right–hand display shows donE to indicate that the
set–up has been stored. The binning nominal and limits are stored, together with the Function,
Frequency, Mode, etc. used for the Sort set–up.
To recall a Sort set–up press Recall, the store number (1to 9), and Enter. The display shows
rcl donE when the set–up has been reloaded from non–volatile memory.
Note that memory 0 contains the factory default settings; these can be loaded by pressing,
Recall, 0, Enter. Memory 0 cannot be overwritten by pressing Store, 0, Enter and cannot
therefore be used to store binning information.
Multiple Bin Sorting
The LCR400 supports two different schemes for multiple bin sorting, overlap and sequential.
Overlapping (or nested) bins have one nominal value and progressively larger symmetrical
limits. Sequential bins can also have one nominal value but asymmetric limits (e.g. –5% to –2%,
–2% to +2%, +2% to 5%) or can have different nominal values, each with their own percentage
limits.
As with simple pass/fail sorting, bin 8 is the failure bin for the appropriate minor parameter and
bin 9 is the general fail bin.
Multiple bin sort schemes can be quite complicated; it is therefore a good idea to write down the
binning set–up before programming is started and to save the set–up once programming is
complete.

16
Overlap Sorting
Overlap sorting is used when components are to be sorted into bins according to their deviation
from a nominal value, for example sorting a particular resistor value into ± 0.1%, ± 0.5% and
± 1% selections.
To set up this type of binning first select the measurement type to be made, e.g. R + Q, set the
measurement frequency and select series or parallel mode as required.
Select bin 0 and set the nominal value and tightest tolerance to be selected (i.e. 0.1% in the case
of the example) using the Nominal and Limit keys exactly as described for simple pass/fail
testing. Note that, since the limits are symmetrical, it is only necessary to set +LIM to 0.1%; if
–LIM is ‘closed’ (dashes shown in the display) the lower limit is automatically –0.1%.
Next select bin 1 in a similar way to bin 0 and set its limits to the next tightest tolerance (i.e. 0.5%
for the example). In the same way as for bin 0 it is only necessary to set +LIM to 0.5%;
–LIM will default to –0.5% if no limit is set. Also note that it is not necessary to set a nominal
for bin 1 (and any successive bins that use the same nominal); if the nominal is left ‘closed’
(dashes shown in the display) the nominal of the next lower bin, in this case bin 0, is
automatically used. Note that if bin 0 does not have a nominal value and limits, selecting Sort will
cause the display to show the message Err bin0.
Set the +LIM limit of bin 2 to 1% to complete the example given.
Set the minor term limit (Q in the case of R + Q measurements) in bin 8 if required; bin 8 is
ignored if the limit is ‘closed’ (dashes shown in the display).
Parts that fall into more than one bin are assigned to the lower numbered bin, Thus the tightest
tolerances should be assigned to the lowest bin number, as in the example.
Unused bins should be ‘closed’ (indicated by dashes) by using the clear bin function.
Parts that do not fall into the pass bins or bin 8 are assigned to bin 9, the general fail bin.
Sequential Sorting
Sequential sorting with the same nominal can be set up in essentially the same way as for
overlap sorting, with a nominal value only defined for bin 0. However, every bin will need both
upper (+LIM) and lower (–LIM) limits defined. For example, to sort a particular resistor into
the bands –2% to –1%, ± 1%, and +1% to +2%, bin 0 has its NOM set to the nominal resistor
value, +LIM set to –1% and –LIM set to –2%; bin 1 has no NOM value and its +LIM is
set to +1% and its –LIM to –1%; bin 2 has no NOM either, its +LIM is set to +2% and its
–LIM is set to +1%.
Sequential sorting with different nominals can again be set up in essentially the same way but
this time every bin has NOM set to its respective nominal. If the limits associated with each
nominal are symmetric then only +LIM need be set, but if they are asymmetric then –LIM
will also need to be set.
In both schemes bin 8 can be set with the limit for the minor term, if required, exactly as
described previously.
Any parts that do not fall into the pass bins or bin 8, including any ‘gaps’ between the limits of the
sequential bins are assigned to bin 9, the general failure bin.
Storing and Recalling Sort Set–ups
Set–ups for multi–bin sorting are stored and recalled from non–volatile memory exactly as
described for simple pass/fail sorting.

17
Remote Operation
General
The instrument can be remotely controlled via its RS232 interface.
At power-on the instrument will be in the local state with the REMote indicator off. When a
command is received the remote state will be entered and the REMote indicator will be turned on.
The keyboard is not locked out and the instrument may be returned to the local state by pressing
any key; however, the effect of this action will only remain until the instrument receives another
character from the interface, when the remote state will once again be entered.
Remote command format and the remote commands themselves are detailed in the Remote
Commands chapter.
RS232 Connector
The 9-way D-type serial interface connector is located on the instrument rear panel. The pin
connections are as shown below:
Pin
Name
Description
1
DCD
Linked to pins 4 and 6
2
TXD
Transmitted data from instrument
3
RXD
Received data to instrument
4
DTR
Linked to pins 1 and 6
5
GND
Signal ground
6
DSR
Linked to pins 1 and 4
7
RTS
Linked to pin 8
8
CTS
Linked to pin 7
9
-
No internal connection
Connect to a PC with a cable which has pins 2, 3, 5, wired plus pins 1, 4, 6 and pins 7 and 8,
linked at the PC end, see diagram. Alternatively, since the links are also made at the instrument
end, a fully-wired 1-to-1 cable may be used.
The interface parameters are fixed as follows:
Baud Rate:
9600
Start Bits: 1
Parity: None
Data Bits: 8
Stop Bits: 1
RS232 Character Set
Any ASCII code can be used. Bit 7 of ASCII codes is ignored, i.e. assumed to be low. No
distinction is made between upper and lower case characters in command mnemonics and they
may be freely mixed. The ASCII control codes between 00H and 31H are ignored, except for 0AH
(Line Feed, LF) which is used as a command terminator.

18
Remote Commands
RS232 Remote Command Formats
Serial input to the instrument is buffered in an input queue which is filled, under interrupt, in a
manner transparent to all other instrument operations. This queue contains raw (un-parsed)
command data which is taken, by the parser, as required. Commands (and queries) are executed
in order and the parser will not start a new command until any previous command or query is
complete.
Commands (and queries) must be sent as specified in the command list and must be terminated
with the command terminator code 0AH (Line Feed, LF). Note that parameters are separated
from the command header by one space (20H) and multiple parameters are separated by
commas (2CH).
Responses to commands or queries are sent immediately; there is no output queue. The
controller must wait for the response to a command or query before the next command or query
is sent.
The instrument responds to the controller after every command either with ‘OK’ if the command
was completed successfully, or with ‘ERRnn’ if the command was not accepted; nn is the error
number, see list at the end of this section. The instrument responds to the controller after every
query as specified in the commands list. In all cases each response is terminated by 0DH
(Carriage Return, CR) followed by 0AH (Line Feed, LF).
<WHITE SPACE> is defined as character codes 00H to 20H inclusive. <WHITE SPACE> is ignored
except in command identifiers. e.g. '*C LS' is not equivalent to '*CLS'.
The high bit of all characters is ignored.
The commands are case insensitive.
Command List
This section lists all commands and queries implemented in this instrument. The commands are
listed in alphabetical order within the function groups.
The following nomenclature is used:
<rmt>
<RESPONSE MESSAGE TERMINATOR>, CR followed by LF
<nrf> A number in any format. e.g. 12, 12·00, 1·2 e1 and 120 e-1 are all
accepted as the number 12. Any number, when received, is converted to
the required precision consistent with the use then rounded up to obtain
the value of the command.
<nr1>
A number with no fractional part, i.e. an integer.
Measurement Set-up Commands
BIASOFF
Sets internal bias off.
BIASON
Sets internal bias on.
FREQ <nr1> Sets the frequency as follows:
<1> sets 100Hz or 120Hz as determined by internal hardware link.
<2> sets 1kHz.
<3> sets 10kHz.
FUNC <nr1> Sets the measurement function as follows:
<0> sets Auto
<1> sets R + Q
<2> sets L + Q
<3> sets C + D
<4> sets C + R

19
HOLDOFF
Sets Range Hold off.
HOLDON
Sets Range Hold on.
MODE <nr1> Sets the equivalent circuit mode as follows:
<1> sets Series mode.
<2> sets Parallel mode.
ZEROCON ‘Nulls out’ residual capacitance (up to 100pF) at the measurement
terminals; the measured value is subtracted from all subsequent C + D or
C + R readings until Zero C is turned off. Can only be used with a
capacitance function already selected.
ZEROCOFF
Turns off Zero C function.
Measurement Reading Commands
READALL? Returns the values of the major parameter, minor parameter and bin
number of the reading completed immediately after the command has
been passed.
The syntax of the response is <ASCII data><rmt>, where <ASCII data>
consists of the three values separated by commas.
The major and minor values are returned as a character string of the form
X=n.nnnnE±nn where X = R, L, C, Q or D and n is a decimal number. The
units are Ohms for R, Henrys for L and Farads for C.
For example:
R=2.0000E+3 is 2kΩ
L=1.5000E-6 is 1.5µH
C=18.000E-12 is 18pF
Q=2.56 is Q = 2.56
D=0.015 is D = 0.015
The bin number is returned in the form BIN=n, where n is a decimal
number. When binning is not active, NOBIN is returned.
Examples of complete responses are:
L=1.5000E-6,Q=2.18,NOBIN<rmt>
C=186.97E-6,R=0.2015,BIN=2<rmt>
R=384.30E-3,Q=0.0004,BIN=1<rmt>
READMAJ? Returns the value of the major parameter only, in the format described
above for READALL?
READMIN? Returns the value of the minor parameter only, in the format described
above for READALL?
READBIN? Returns the value of the bin number only in the format described above for
READALL?
Table of contents
Languages:
Other AimTTi Measuring Instrument manuals
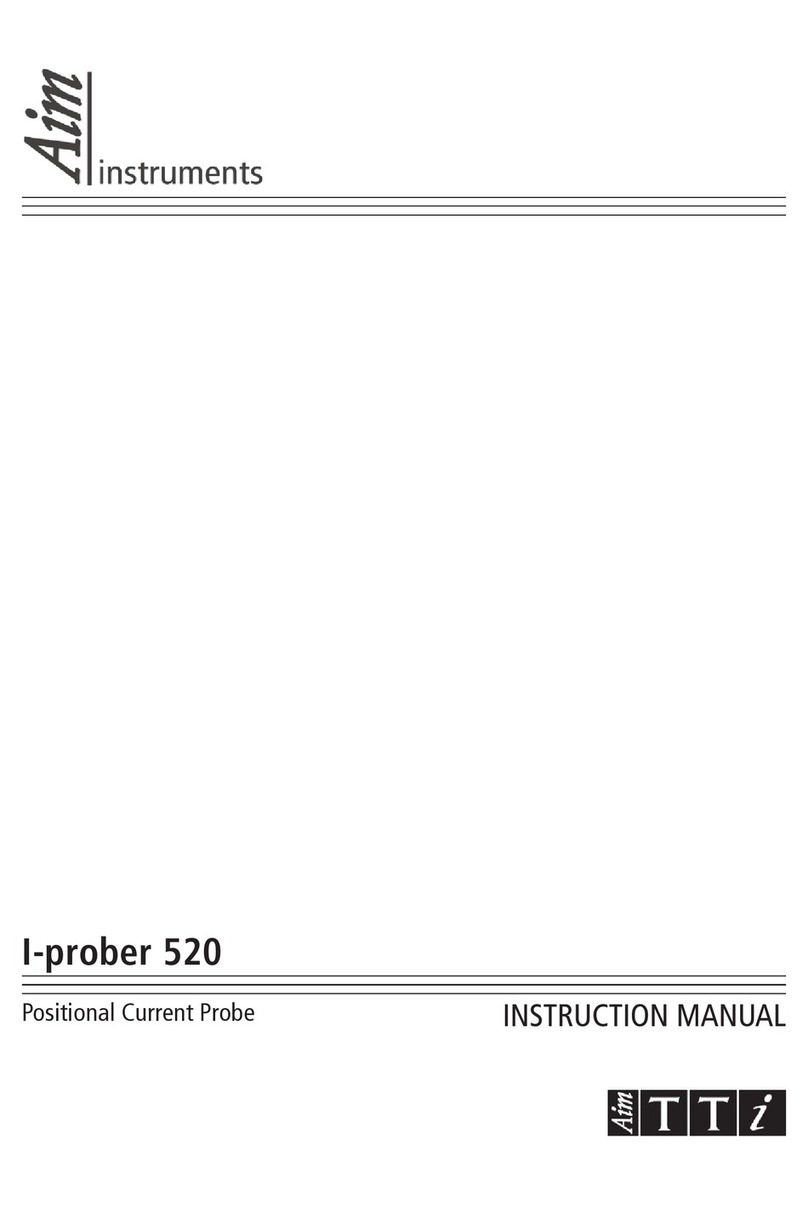
AimTTi
AimTTi I-prober 520 User manual
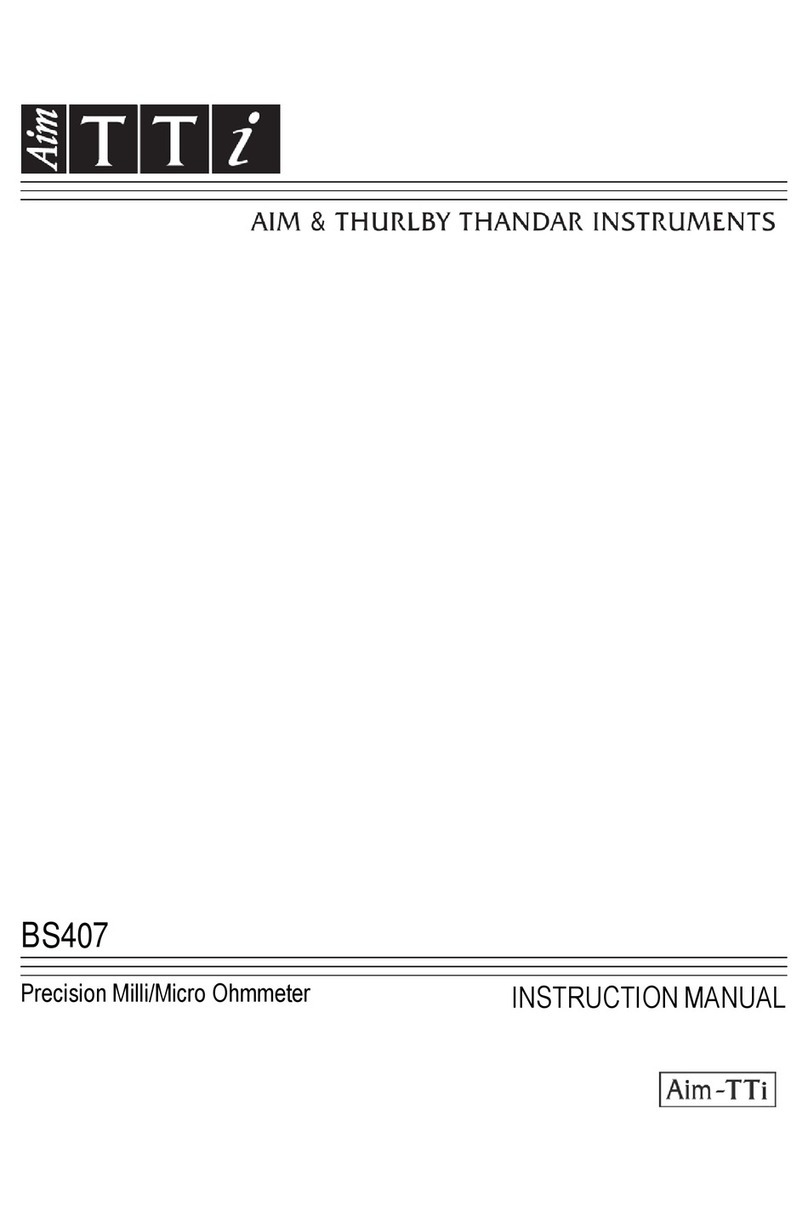
AimTTi
AimTTi BS407 User manual

AimTTi
AimTTi SMU4000 Series User manual
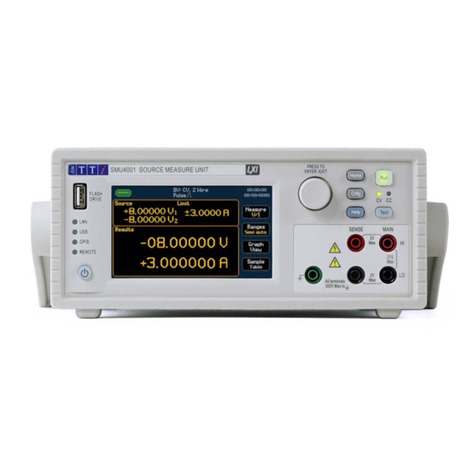
AimTTi
AimTTi SMU4001 User manual

AimTTi
AimTTi HA1600A User manual

AimTTi
AimTTi PSA3605 User manual
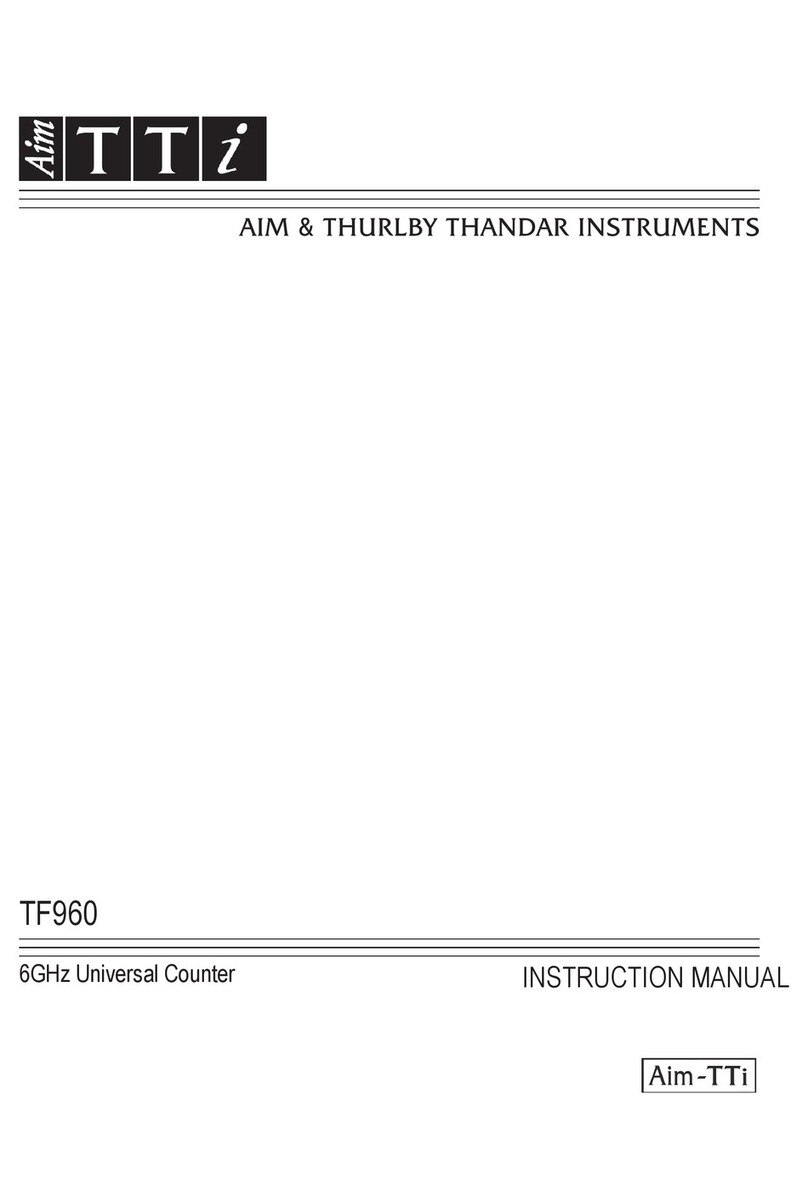
AimTTi
AimTTi TF960 User manual
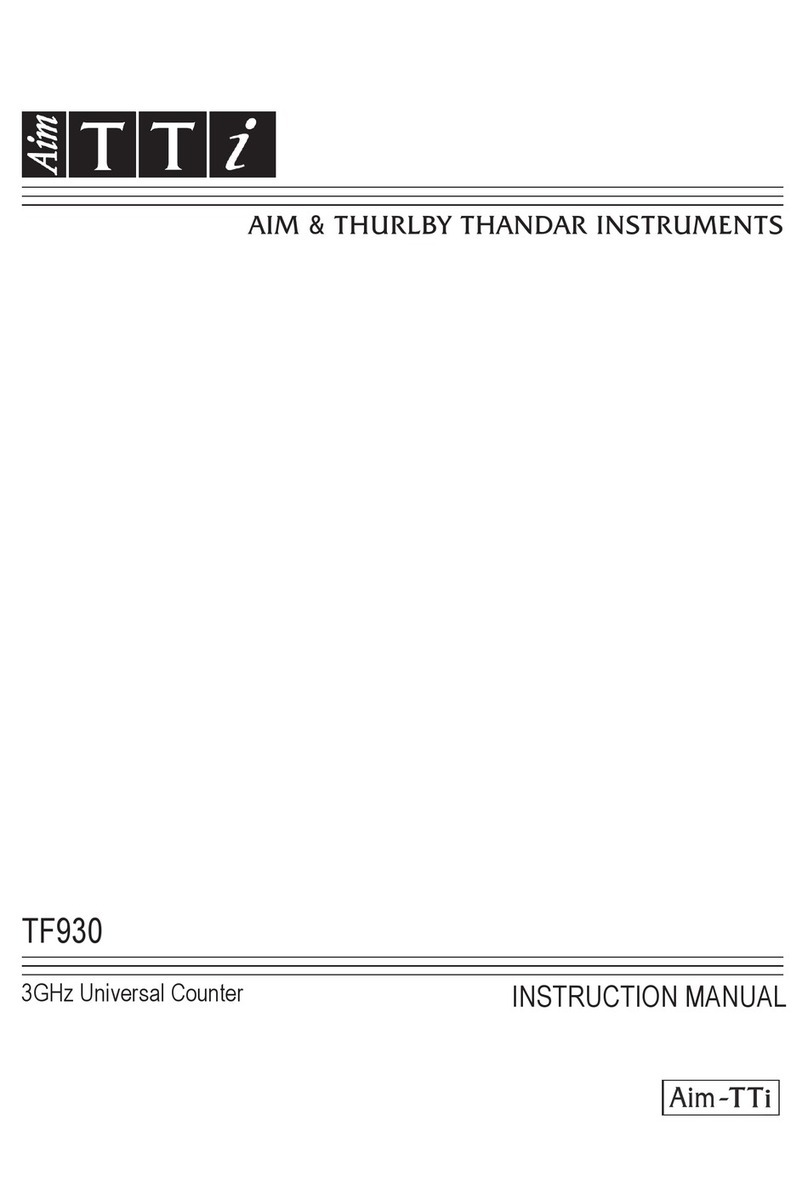
AimTTi
AimTTi tf930 User manual
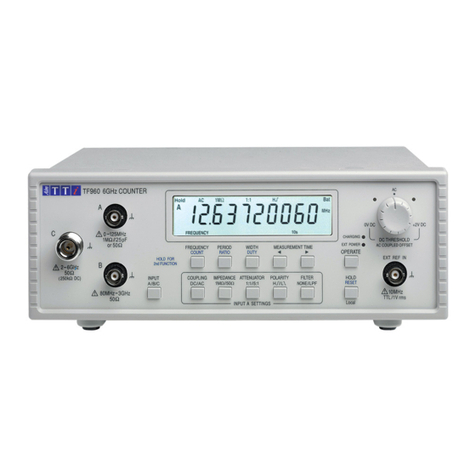
AimTTi
AimTTi TF960 User manual

AimTTi
AimTTi PSA1303 User manual
Popular Measuring Instrument manuals by other brands
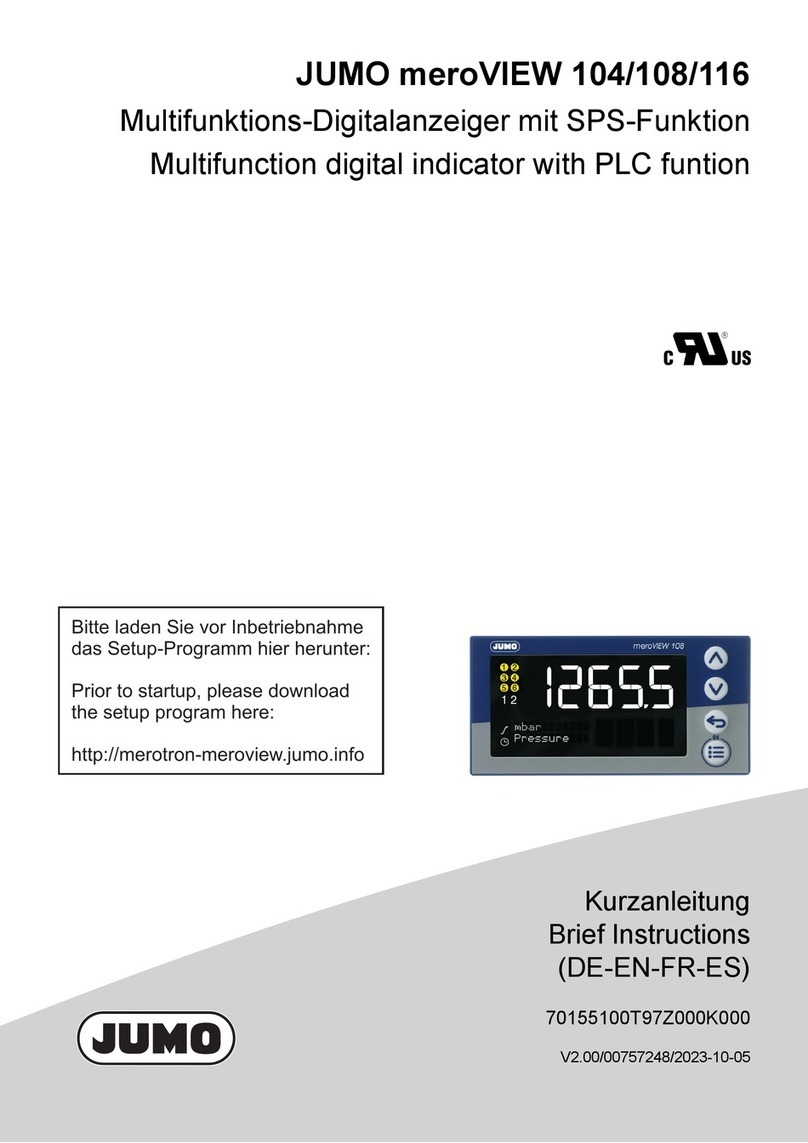
JUMO
JUMO meroVIEW 104 Brief instructions
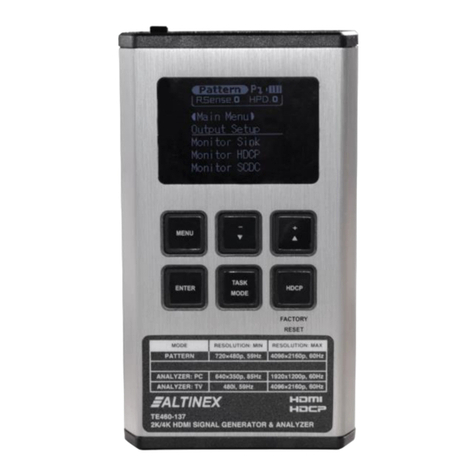
Altinex
Altinex SIGNAL MANAGEMENT SOLUTIONS TE460-137 user guide
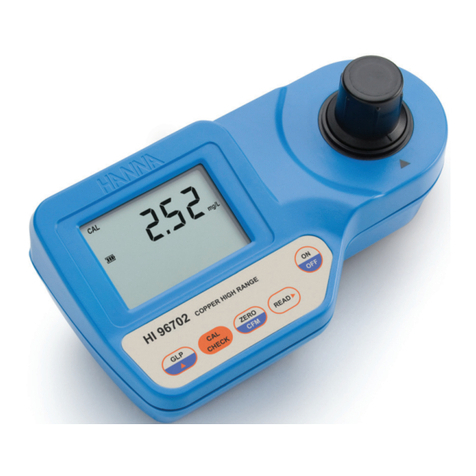
Hanna Instruments
Hanna Instruments HI96702C instruction manual
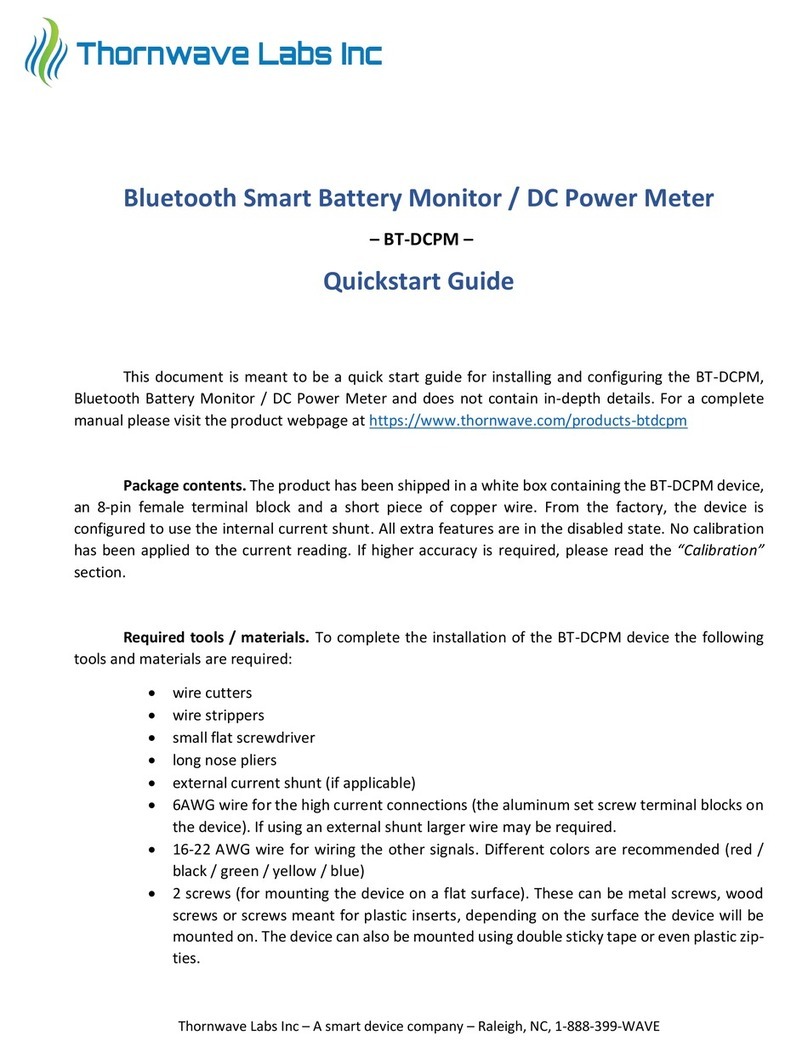
Thornwave Labs
Thornwave Labs BT-DCPM quick start guide
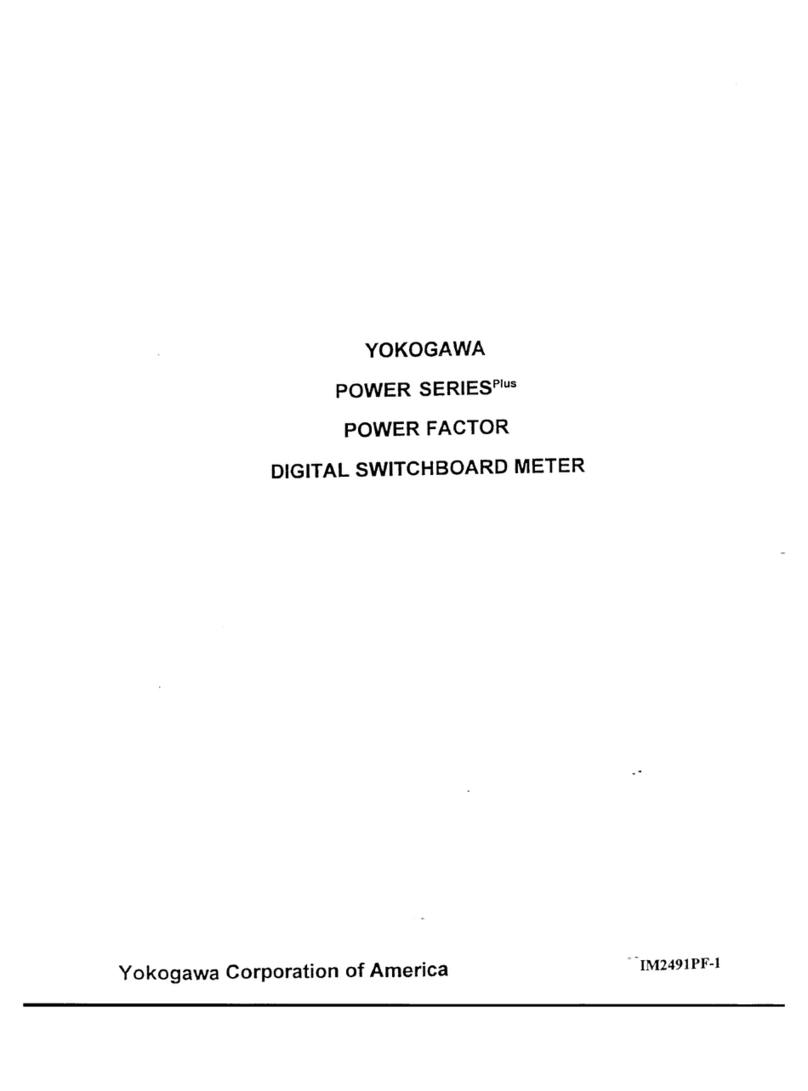
YOKOGAWA
YOKOGAWA Power Series Plus instruction manual

Endress+Hauser
Endress+Hauser Prothermo NMT81 Brief operating instructions