AKO AKO-16524A User manual

AKO-16524A AKO-16525A
Advanced temperature controller for cold rooms
User manual
GB 1652H4A02 Ed.09

2
Index
AKO Electromecánica thanks and congratulates you for purchasing our product, in whose development and manufacture the most innovative
technology has been used, as well as strict production and quality control processes.
Our commitment to satisfy our customers and our continuous efforts to improve every day can be seen in the various quality certifications we
have obtained.
This is a high performance, high technology product. The operation and final performance of the equipment depend on proper planning,
installation, configuration and commissioning. Read this manual carefully before installation, and always follow its instructions.
Only qualified personnel should install or perform technical assistance on this product.
This product is designed to be used in the applications described in the product manual. AKO Electromecánica gives no guarantee of its
operation in any use not foreseen in the manual, and is not responsible for any damage resulting from improper use, configuration,
installation or commissioning.
It is the responsibility of the installer and the customer to comply with and ensure others comply with all regulations applicable to
installations incorporating our products. AKO Electromecánica is not responsible for any damage caused by non-compliance with regulations.
Follow strictly the instructions given in this manual.
To maximise the service life of our equipment, these recommendations should be followed:
Do not expose electronic equipment to dust, dirt, water, rain, humidity, high temperatures, chemicals or corrosive substances of any sort.
Do not submit the equipment to blows or vibrations nor try to manipulate it differently from shown in the manual.
Never exceed the specifications and limitations indicated in the manual.
Always respect the specified ambient working and storage conditions.
During and after installation, avoid leaving loose, broken, unprotected or damaged wiring, since they might constitute a risk for the
equipment and its users.
AKO Electromecánica reserves the right to make any non-metrology modification to the documentation or the equipment without previous
notice
Page
Presentation ........................................................................................................................................3
Warnings.............................................................................................................................................3
Maintenance ........................................................................................................................................3
Description ...........................................................................................................................................4
Installation ...........................................................................................................................................6
Wiring ..........................................................................................................................................7
Installation of the probes ...............................................................................................................8
Installation of the CAMM AKO-58500 module included.....................................................................9
Link with the AKO CAMM Tool / AKO CAMM Fit application..............................................................9
Initial configuration (wizard) ..............................................................................................................10
Operation..........................................................................................................................................11
Messages...................................................................................................................................11
SELFDRIVE mode........................................................................................................................13
Cold regulation ..........................................................................................................................14
Door management .....................................................................................................................18
Defrost.......................................................................................................................................19
Evaporator fans ..........................................................................................................................24
Alarms .......................................................................................................................................25
Alerts.........................................................................................................................................27
..................................................................................................28Operation of the auxiliary relays
Core Index .................................................................................................................................29
Dashboard .................................................................................................................................29
Configuration ....................................................................................................................................30
Connectivity ......................................................................................................................................36
Technical specifications 37......................................................................................................................
Troubleshooting.................................................................................................................................39
1652H4A02 Ed.09

3
AKO-16524A / AKO-16525A
Warnings
-If the equipment is used without adhering to the manufacturer's instructions, the device safety
requirements could be compromised. Only probes supplied by AKO must be used for the unit to operate
correctly.
2
-From -40 ºC to +20 °C, if the NTC probe is extended to 1000 m with at least a 0.5 mm cable, the maximum
deviation will be 0.25 ºC (cable for probe extension ref. AKO-15586. Earth the cable mesh at one end only).
-Only NTC type probes supplied by AKO must be used for the appliance to operate correctly.
-It must be installed in a place protected from vibrations, water and corrosive gases, where the ambient
temperature does not exceed the value indicated in the technical data.
-For the reading to be correct, the probe must be used in a place without thermal influences apart from the
temperature you want to measure or control.
-IP65 protection degree is only valid with the protection cover closed.
-The IP65 protection degree is only valid if the cables enter the device through a tube for electric conduits +
gland with IP65 or above. The size of the glands must be suitable for the diameter of the tube used.
-Do not spray the unit directly with high-pressure hoses, as this could damage it.
Maintenance
Clean the surface of the unit with a soft cloth, water and soap.
Do not use abrasive detergents, petrol, alcohol or solvents, as this might damage the unit.
Presentation
The AKO-16524A / 16525A advanced controller for cold
room stores has a SELFDRIVE operating mode that
automatically controls (without parametrisation) the fans
and adaptively minimises defrosts to optimise the
performance of the cold room store: maximising time in set
point and minimising costs linked to energy consumption
and wear of components.
In order to evaluate the performance of the refrigeration
facility in detail, the CAMM (AKO-58500) module and the
applications for the AKO CAMM Tool and AKO CAMM Fit
mobile devices (available in App Store and in Google Play)
are included with the AKO-16524A controller . These applications provide several indicators on the actual operation
of the cold room that allow diagnosing possible design, usage or maintenance problems in the installation.
1652H4A02 Ed.09

1652H4A02 Ed.09
4
Description
Display
Keypad
Indicators
Constant: Stand-By Mode activated.
Regulation is paused.
Flashing: Controlled stop process for the
regulation in progress.
Constant: Cold room door open.
Flashing: The door has been open for a longer
time than defined in parameter A12.
There is an active alarm, but not an active
HACCP alarm.
Constant: HACCP alarm active.
Flashing: HACCP alarm recorded and
unconfirmed. Press the key to confirm an MUT
HACCP alarm.
Constant: The SELFDRIVE mode is active.
Flashing: An error has been detected in the
SELFDRIVE mode.
Constant: Evaporator fans active.
Flashing: The evaporator fans should be active
but a delay is preventing this.
Constant: The cold solenoid is active.
Flashing: The solenoid should be active but a
delay or protection is preventing this.
Constant: Compressor active.
Flashing: The compressor should be active but a
delay or protection is preventing this.
Defrost relay active.
Continuous cycle mode active.
Cold room light active.
Alarm in progress muted.
Temperature displayed in ° Fahrenheit /
º Centigrade.
Programming mode active.
Constant: CAMM module in operation.
Flashing: Malfunction in CAMM module.
Bluetooth activated (only with CAMM module).

1652H4A02 Ed.09
5
Keypad
Pressing it for 3 seconds activates/deactivates the Stand-By mode. In this mode, regulation is paused and
the m icon is displayed.
In the programming menu, it exits the parameter without saving changes, returns to the previous level or
exits programming.
Pressing once without holding displays the temperature of probe S2 for 2 seconds (if it is enabled).
Pressing it for 3 seconds starts/stops the defrost.
In the programming menu, it allows scrolling through the different levels, or during the setting of a
parameter, changing its value.
A brief press shows the SELFDRIVE mode operating alerts.
Pressing it for 3 seconds activates/deactivates the continuous cycle mode.
In the programming menu, it allows scrolling through the different levels, or during the setting of a
parameter, changing its value.
Pressing once without holding activates/deactivates the cold room light.
Pressing it for 3 seconds accesses the condensed programming menu.
Pressing it for 6 seconds accesses the expanded programming menu.
In the programming menu, it accesses the level shown on the display or, during the setting of a parameter,
accepts the new value.
Pressing once without holding displays the current effective value of the Set Point, taking into
consideration temporary modifications by other parameters (C10 or C12).
When an alarm is in progress, pressing once without holding mutes the acoustic alarm.
Pressing for 3 seconds accesses the Set Point setting.
STAND-BY
If the regulation cannot be instantly stopped due to its configuration, a controlled stop process starts
and the m icon flashes. To stop the controlled stop process and force the step to Stand-by, press the
Stand-by key again for 3 seconds.

6
Installation
-Remove the bezels (1)
-Make a 1/4 turn of the screws (2) anti-clockwise and
open the door (3).
-Install the necessary glands (4 / 5) by drilling holes in the
points indicated on the box.
-Mark and make the holes in the wall with the aid of the
template included.
-Fix the device to the wall. If it is a brick wall, use the screws and plugs supplied; if the wall is made of sheet
metal (cold room store), use the screws provided without plugs (6).
-Wire the device by following the recommendations indicated on p. 7.
-Close the cover (3), tighten the screws (2) and replace the bezels (1).
1
2
3
6
4Ø Max. 25 mm
5Ø Max. 20 mm
1652H4A02 Ed.09

1652H4A02 Ed.09
7
Wiring
Always disconnect the power supply to do the wiring.
The probes and their cables must NEVER be installed in a conduit together with power, control or power
supply cables.
For disconnection, the power supply circuit must be equipped with at least a 2 A, 230 V switch, located near
the device. The power supply cable shall be of the H05VV-F or NYM 1x16/3 type. The cross-section to be used
2
will depend on the local regulations in force, but must never be less than 1.5 mm .
2
Cables for relay or contactor outputs must have a cross-section of 2.5 mm and allow working temperatures equal
to or over 70 °C and must be installed with as little bending as possible.
The 120/230 V~ wiring area must be kept clear of any other external element.
The wiring to be undertaken depends on the option selected in the initial configuration wizard (see
p. 10). Use the appropriate diagram based on the option selected.
Check the available options on the diagram sheet included with your device.
The AKO-16523D model has a contactor which allows for the connection of three-phase defrost resistors, a three-
phase compressor or three-phase fans, according to your installation’s requirements. Check how to connect it on
the diagram sheet included with your device.
IMPORTANT:
ŸThe AUXILIARY relays are programmable, and their operation depends on the configuration.
ŸThe function of the digital inputs depends on the configuration.
ŸThe recommended currents and powers are the maximum working currents and powers.

1652H4A02 Ed.09
8
Installation of the probes
To achieve maximum performance from the advanced controller, the correct installation of the probes is key, as
they are responsible for calculating the evaporator’s thermal transfer coefficient, evaluating the start and end of the
defrosts and diagnosing problems in the evaporator.
Material included
-4 mm hermetic evaporator probe, 1.5 m of cable.
-Ambient probe
-1 mounting clip for 10-13 mm coil
-1 mounting clip for 14-18 mm coil
-1 mounting clip for 19-21 mm coil
-1 mounting clip for 22-25 mm coil
Location of the ambient probe
The probe should be located in a place that does not directly receive the flow of cold air from the evaporator.
Preferably in its air aspiration area.
Location of the evaporator probe
The probe must be located as near as possible to the inlet of refrigerant from the evaporator (close to the
expansion valve) in the finned area.
In certain evaporators, for example cubic ones, this inlet may be located on the front part of the battery, just behind
the fan.
If defrost is done by electric heat, the probe must be located far away from them and, if possible, in the area of the
evaporator where defrosting is slower, in other words, in the last area to defrost.
If the two conditions are not possible, the best possible compromise must be looked for.
Select the appropriate clip
depending on the size of its
evaporator pipe.
Attach the probe to the pipe
using the clip, making sure that
its end is in direct contact with
the tube.
Bend the fins of both ends of the
probe to increase the fixing and
contact surface.

1652H4A02 Ed.09
9
Installation of the CAMM AKO-58500 module included
In combination with the application for AKO CAM Tool mobile devices, the CAM module provides the device with
multiple functions:
- Data logging - Activity summaries
- Logging of configuration changes - Logging of events and alerts
- Remote configuration - Remote control of functions
- Clock functions in real time - Energy efficiency indicators
Link with the AKO CAMM Tool / AKO CAMM Fit application
The use of both applications requires logging in with a valid email.
After 1 minute without activity between the application and the CAMM module, communication is
disconnected, to re-establish it, return to screen “Device list” and press the button.REF
Insert the CAM AKO-58500 module in the
pre-installed base as shown in the picture.
Open app AKO CAMM Tool /
AKO CAMM Fit in your mobile and
enter the access data.
The app makes a device search
and displays the results on screen.
Choose the device you want, in a
few seconds the app requests the
Bluetooth link code (by default
123456).
After a few seconds, the app
displays the screen of the device
chosen, communication has been
established correctly.
12 3
Some Android devices, during the linking process, may tell the user to access settings / Bluetooth and
link from there, looking for the device via its serial number.

10
Initial configuration (wizard)
The first time the unit receives the power supply, it will enter into
ASSISTANT mode. The display will show the message In{ flashing at 0.
Step 1:
Select the most suitable InI option based on the type of installation to be
carried out and press SET. The available options will be shown in the
following table:
If options 2, 5, or 7 are chosen, check the configuration of parameter I11 according to the pressure
switch type used. (See diagram included with the device).
Step 2:
Use keys N and Q to enter the desired Set Point value and press SET.
The configuration wizard has finished. The unit will begin to regulate the
temperature.
If this is not the first time you run the wizard, after completing the last
step the display will show the message dFp (default parameters). You
may choose between two options:
0: Only change the parameters which affect the wizard. The other
parameters will remain the same.
1: All parameters return to their factory setting except those
which have been modified by the wizard.
The configuration wizard will not reactivate. To reactivate it, activate the Stand-By mode (by pressing the m
key for 3 seconds) and wait until the unit completely halts regulation (the m indicator will light up
permanently) and press in this order the following keys (one after the other, not at the same time) N, Q and
SET .
STAND-BY
If the regulation cannot be instantly stopped due to its configuration, a controlled stop process starts
and the m icon flashes. To stop the controlled stop process and force the step to Stand-by, press the
Stand-by key again for 3 seconds.
In{
Type of installation
Parameters
Diagram
to be
used
Cold
regulation
Pump
Down
Defrost
Evaporator
fans
Pd
o00
I00
I10
I11
I20
I21
d1
d7
F3
0
Demo mode: it displays the temperature but does not regulate the temperature or activate relays.
1
Solenoid
No
Electric
Yes
0
*
2
0
0
0
0
20
0
0
A
2
Solenoid + compressor
Yes
Electric
Yes
1
1
2
7
1
0
0
20
0
0
B
3
Solenoid + compressor
No
Electric
Yes
0
1
2
0
0
0
0
20
0
0
B
4
Solenoid
No
Air
Yes
0
*
1
0
0
0
0
20
1
1
A
5
Solenoid + compressor
Yes
Air
Yes
1
1
1
7
1
0
0
20
1
1
B
6
Solenoid + compressor
No
Air
Yes
0
1
1
0
0
0
0
20
1
1
B
7
Solenoid + compressor
Yes
Hot gas
Yes
1
1
2
7
1
9
1
5
2
0
C
8
Solenoid + compressor
No
Hot gas
Yes
0
1
2
0
0
9
1
5
2
0
C
* o00=2 in AKO-16523 / 16520, o00=0 in AKO-16523P / 16520P / 16523D.
CORECORE
CORECORE
CORECORE
CORECORE
1
2
1652H4A02 Ed.09

11
Operation
MESSAGES
Pump down malfunction error (stop), the time configured in parameter C20 has been exceeded
(see p. 17).
Only displayed on screen.
Pump down malfunction error (start-up), the time configured in parameter C19 has been
exceeded (see p. 17).
Only displayed on screen.
Probe 1/2/3 failure (open circuit, crossed circuit or temperature outside the limits of the probe)
(Equivalent limits in °F).
Only E2 and E3: Damp evaporator probe (see p. 25).
Activates the alarm relay and the audible alarm.
Flashing with temperature: Probe error 1/2/3 in SELFDRIVE mode.
Flashing with CAL: Probe error 1/2/3 during the calibration.
Open door alarm. Only if the door remains open for a longer time than defined in parameter
A12 (see p. 26).
Activates the alarm relay and the audible alarm.
Maximum temperature in control probe alarm. The temperature value programmed in A1 has
been reached (see p. 25).
Activates the alarm relay and the audible alarm.
Minimum temperature in control probe alarm. The temperature value programmed in A2 has
been reached (see p. 25).
Activates the alarm relay and the audible alarm.
External alarm activated (by digital input) (see p. 25).
Activates the alarm relay and the audible alarm.
Severe external alarm activated (by digital input) (see p. 25).
Activates the alarm relay and the audible alarm.
Alarm for defrost completed due to time-out. The time set in d1 has been exceeded (see p. 27).
Activates the alarm relay and the audible alarm.
HACCP alarm. The temperature has reached the value of parameter h1 during a longer period
than established in h2 (see p. 26).
Activates the alarm relay and the audible alarm.
HACCP alarm due to a power supply failure. The temperature established in h1 has been
reached, following a power supply failure (see p. 26).
Activates the alarm relay and the audible alarm.
Indicates that a defrost is being performed (see p. 20).
Only displayed on screen.
Password request. See parameters b10 and PAS (see p. 27).
Only displayed on screen.
Shown sequentially with the temperature: The controller is in demo mode, the
configuration has not been made.
1652H4A02 Ed.09

12
1652H4A02 Ed.09
MESSAGES
Calibration ongoing, therefore, avoid, as far as possible, opening the cold room during the
process. For further information, see page 13.
Flashing with temperature: Configuration has been changed from 1 to 2 evaporators or vice
versa.
SELFDRIVE MODE ALERT MESSAGES (Only shown pressing the Q key)
Defrost end error in 1/2 evaporator during the calibration, defrost has not ended due to
temperature.
Error during calibration in 1/2 evaporator. There is not enough difference in temperature
between the cold room probe and the evaporator probe.
It has not been possible to carry out the calibration due to a lack of stability in the system
(Excessive door opening, excessive oscillations in the lower pressure, etc.).
Error during normal operation (SELFDRIVE Mode active) in 1/2 evaporator. There is not enough
difference in temperature between the cold room probe and the evaporator probe.
A lack of stability has been detected in the system (Excessive door opening, excessive oscillations in
the low pressure, etc.) during normal operation (SELFDRIVE Mode active).
The persistent lack of stability has led to the deactivation of the SELFDRIVE mode.
Excessive door openings have been detected during calibration and it has not been possible to
calibrate.
Excessive door openings have been detected and the device cannot regulate in SELFDRIVE mode.

13
1652H4A02 Ed.09
SELFDRIVE mode
SELFDRIVE modeIf the SELFDRIVE mode is activated (default configuration), the device periodically
evaluates the evaporator’s heat transfer, managing the available resources to maximise it.
The defrosts are minimised, adapting to the changing conditions of the cold room, reducing heat input
into the refrigerated space, thermal stress in the evaporator and energy consumption.
Operation of the evaporate fans is optimised taking into account the compressor status, evaporate temperature,
frost level, opening of the door, etc.
The control function of the drainage resistor minimises its activation (moments before starting a defrost), thereby
reducing energy consumption.
To achieve correct operation of the SELFDRIVE mode, it is very important for the probes to be correctly installed, as
described on page 8.
Calibration
During the first hours of operation, the device performs two calibrations automatically, during
which the display shows the CAL.message.
Calibration may take several hours and include several refrigeration and defrost cycles.
IMPORTANT:
During the calibration processes, the following should be avoided:
Opening the cold room door
Turning the controller off or putting it on stand-by
Changing controller parameters, including the set point
While the calibration process is active:
-Manual defrost cannot be activated (H key)
-The continuous cycle cannot be activated
-The set point change function cannot be activated
If calibration cannot be performed, or if an important part of the installation is replaced (compressor, evaporator,
etc.) it is advisable to perform a manual calibration.
It is also recommended (not essential) to perform a manual calibration, once the installation has completed its
commissioning, with a load inside it and when its operating temperature has been stabilised, after several days of
operation, in this way calibration is optimal.
In the event of changing the set point or hysteresis, the device performs a calibration again automatically, except if
the set point change is made using the “set point change mode” function (see page 16).
To perform a manual calibration, access the parameter menu (see page 31) and follow the sequence indicated
below:
-Access parameter b30
-A security code is requested, enter code 63
--Using keys N and Q, select option 1 and press SET

1652H4A02 Ed.09
14
Cold regulation
Solenoid control (COOL Relay)
Cold production is regulated by means of opening /
closing the solenoid valve.
When the temperature in probe S1 reaches the set
point (SP) value plus the probe's differential (C1), the
solenoid opens and causes the temperature to drop.
Once the set point (SP) value is reached, the solenoid
closes.
Compressor control (Relay AUX 1)
With Pump Down (Inl: 2, 5, 7)
Requires the connection of a low pressure
switch in digital input 1.
When the temperature in probe S1 reaches the set
point (SP) value plus the probe’s differential (C1), the
solenoid opens, causing the pressure in the evaporator
to increase and, therefore, the low pressure switch
deactivates and the compressor starts up.
Once the set point (SP) value is reached, the solenoid
closes, causing the pressure in the evaporator to
decrease, triggering the low pressure switch and
stopping the compressor.
For further details of the process, see the next page.
Without Pump Down (Inl: 3, 6, 8,)
The compressor operates simultaneously with the solenoid valve, starting up when the latter opens and stopping
when it closes.
Operation in the event of a fault in probe S1
If probe S1 fails (fault, disconnection, etc. ), compressor behaviour will depend on parameter C6, with one of 3
options available:
C6=0: The compressor is stopped until probe S1 begins to operate again.
C6=1: The compressor is started-up until probe S1 begins to operate again
C6=2: The compressor operates in line with the average operation during the 24 hours prior to the error,
taking into account the number of start-ups and stops and the average time in each state (stop-start).
If 24 hours have not elapsed without a probe error, the device moves to C6=3 mode.
C6=3: C6=3: The compressor operates in line with the times programmed in C7 (ON) and C8 (OFF).
SP+C1
SP+C1
SP
SP
Solenoid
Solenoid
Low
pressure
switch
Compressor
Compressor
ON
ON
ON
ON
ON ON
C7 C7C8
S1
S1

1652H4A02 Ed.09
15
Regulation of cold with two temperature probes (S1 + S3)
This requires configuration of digital input 2 as cold room temperature (I20=10).
The device regulates the temperature of the cold room taking into account the reading of both probes. Using
parameter C25, the influence of probe S3 is determined in the regulation.
Examples: C25=0 (S1: 100 % S3: 0 %) C25=75 (S1: 25 % S3: 75 %)
C25=60 (S1: 40 % S3: 60 %) C25=95 (S1: 5 % S3: 95 %)
This mode is particularly useful in large volume cold room stores, where there may be significant variations of
temperature.
In the event of an error in probe 3 (E3), the controller only uses the reading of probe 1. If both probes break (E1 +
E3), the controller acts according to parameter C6.
Continuous cycle mode
This is used to quickly cool the cold room stores
before products are loaded and is activated by
pressing the key for 3 seconds.CIC
Upon activating this mode, the compressor begins to
operate until the temperature in probe S1 reaches the
set point value, minus the variation indicated in
parameter C10. The value of C10 is always negative,
unless it is 0.
The unit will immediately return to normal operation.
Should it not be possible to reach this point, the
device will return to normal operation once the time
configured in C9 has elapsed, or by pressing the CIC
key again for 5 seconds.
Calibration of probe 1
Parameter C0 allows for correction of the temperature detected by probe 1; this is particularly useful when the
probe cannot be located in the ideal place.
Set Point locking
Parameters C2 and C3 allow for an upper and lower limit to be established for the set point (SP), to protect the
product or installation from Set Point manipulation.
Product temperature
This function allows using a temperature probe to display the product temperature.To activate it, input 2 must be
configured as “Product temperature” (I20=11), and the display of all the probes activated sequentially (C21=0).
SP
SP+C10
Solenoid ON ON
SP+C1
S1

16
Set Point change mode
This allows for quick alternation between two working temperatures in the cold room store, modifying the Set
Point in line with the value indicated in parameter C12. The aforementioned value may be negative or positive,
which allows for the Set Point to be reduced or increased. If it is configured in 0, the mode is disabled.
It is activated in three possible ways:
ŸBy means of an external switch connected to one of the digital inputs. The digital input should be configured
as “Set Point change (I10 or I20=4). Activation through this method cancels any other activation and can
only be deactivated using the same method.
ŸBy means of the AKONet application. This requires the device to be connected to a Modbus network (see p. 36).
ŸBy means of the CAMM module and the AKO CAMM tool application.
EXAMPLE:
If the SELFDRIVE mode is active:
It is recommended for calibration to be performed with the lowest set point value.
It is recommended that the difference between set points is not greater than 5 ºC in negative cold
rooms and 2 ºC in positive cold rooms.
Compressor protection timing
Parameter C4 allows for selection of the type of timing to be applied to protect the compressor. These delays
prevent continuous compressor starts and stops.
These timings affect the COOL and AUX 1 relays (if o00=1)
OFF-ON (C4=0): Minimum time in OFF mode before each start-up.
OFF-ON / ON-OFF (C4=1): Minimum time in ON and OFF mode for each cycle.
The delay time is defined by means of parameter C5; if C5=0, timing is disabled.
SP
SP+C12
Solenoid
D1
ON ON
SP+C1
(SP+C12)+C1
Gnd
D2 / S3
D1
Cambio
Set Point
DIG. IN
Configuration
I10: 4
I11: 0
D1= OND1= OFF
S1
ON ON
OFF-ON (C4=0) OFF-ON / ON-OFF (C4=1)
SP SPSP+C1 SP+C1
C5 C5C5
OFF OFF
COOL COOL
1652H4A02 Ed.09

17
Pump down function
This function foresees problems in the compressor caused by movements of coolant, using a stop/start technique
for the installation, controlled via the liquid solenoid, the low pressure switch and the compressor itself.
This function is only available for In{ options 2, 5 and 7 and requires the connection of a low pressure switch in
digital input 1. (I10=7)
STOP
When the temperature in probe S1 reaches the set point (SP) value, the COOL relay deactivates, closing the liquid
solenoid.
Because the compressor continues to operate, pressure in the evaporator quickly drops. Upon reaching a given
value, the low pressure switch activates, changing the status of digital input 1, which stops the compressor (relay
AUX 1).
This manoeuvre isolates all of the coolant in the high-pressure line, far from the compressor crankcase, preventing
serious faults upon start-up.
Should the low pressure switch fail, the controller stops the compressor once the safety interval defined in C20 has
elapsed, displaying the message “Pd” (an informative message that does not affect the unit's operation).
If C20 time is 0 (default value), the compressor will not stop until the low pressure switch is activated, but it will
display the “Pd” message after 15 minutes.
START
When the temperature in probe S1 reaches the set point value plus the differential (SP+C1), the COOL relay
activates, opening the liquid solenoid. This increases the pressure in the evaporator, deactivating the low pressure
switch, which turns the compressor on.
If, some time (determined by C19) after the liquid solenoid is opened (COOL relay set to ON), the low pressure
switch does not deactivate, the controller will once again close the solenoid (COOL relay set to OFF) and the “LP”
message will be displayed. This manoeuvre will be repeated every 2 minutes, indefinitely, until the pressure switch
is deactivated and the installation reverts to its normal operation.
If C19 time is 0 (default value), the solenoid will remain open until the low pressure switch deactivates, but it will
display the “LP” message after 5 minutes.
STAND-BY
If the pump down function is active, a certain amount of time may elapse between starting the stand-
by function and the controller stopping; this is because certain installation control phases cannot be
interrupted.
To force the stop of the controller, press the Stand-by key again for 3 seconds.
ON
Liquid solenoid
Low pressure
switch
Pressure
switch fault
Pressure
switch fault
Compressor
Pressure in
evaporator
ON
ON
+
C20 C19
OFF
OFF
OFF
COOL
D1
AUX 1
SP SPSP+C1 SP+C1
1652H4A02 Ed.09

1652H4A02 Ed.09
18
Door management
Door management requires configuring one of the digital inputs as “Door contact” (I10 ó I20=1).
Standard operating mode (CE=0)
Door management allows for the installation's behaviour to be controlled, should the cold room door open
through parameters C22 and C23.
Parameter C22 defines whether cold production should be stopped if the door opens. If C22=1, when the door
opens, the fans stop and, 15 seconds later, the solenoid closes (COOL relay).
Parameter C23 defines the maximum time, in minutes, that the installation can remain without producing cold
whilst the door is open. If C23=0, cold is not produced with the door open.
SELFDRIVE operating mode (CE=1)
If the SELFDRIVE mode is active, in the case of opening the door, the fans stop, or do not stop, depending on
parameter C22. If the door does not close, when the time set in parameter C24 has passed, cold production stops
and does not activate again until the time set in C23 has passed.
If, when the door is opened, cold is not being produced, only parameter C23 is
taken into account.
Management of door frame resistor
If the Set Point is equal to or below -4°C and the relay AUX 2 has been
configured as “door frame resistor” (o10=4), the resistor is activated
(relay ON) when the temperature of the cold room drops below -3°C, and
is deactivated (relay OFF) when 0°C is reached.
SP
Door
C23
COOL
Open
ON ON
SP+C1
Configuration:
C22: 1
C23: 5
S1
Door frame
resistor
CNC
AUX 2
NO
N L
100-240 V~
50/60 Hz

1652H4A02 Ed.09
19
Defrost
Types of defrost
There are 3 possible defrost types, depending on the option selected in the wizard (Inl):
Electric (InI=1, 2 and 3) (d7=0)
Defrost is performed through electrical resistors, supplying the evaporator with heat. The operation of fans in this
mode depends on parameter F3; the compressor and solenoid are stopped.
By air (InI=4, 5 and 6) (d7=1)
Usually used in positive cold rooms (> 3°C), since the inside temperature of the cold room is sufficient to melt
evaporator ice. By default, the fans are activated so that air may circulate through the evaporator; to stop them,
change parameter F3 to 0. The compressor and solenoid are stopped.
Hot gas (InI=7 and 8) (d7=2)
The hot gas from compressor discharge is used to melt evaporator ice and, to this end, two valves are necessary:
one at the condenser input (A) (SSV relay) and another between the compressor output and the evaporator input
(B) (DEF relay).
During the process, the liquid solenoid valve (C) and the condenser input valve are closed and the evaporator input
valve is opened, forcing hot gas to pass through the latter and melting the ice.
Optionally, a high pressure switch (D) can be added to control the solenoid valve (digital input D2, l20=9) during
the defrost process using hot gas. If the pressure decreases, the solenoid opens to allow liquid into the tank; when
the pressure rises again, the solenoid closes.
Gnd
D2 / S3
D1
DIG. IN
COND.
EVAP.
A
D
BC
CNC
AUX 2
NO NC NO C NO CNO C NC NO C
DEF.COOL
FAN AUX 1

1652H4A02 Ed.09
20
Control of defrost in standard mode (CE=0)
Defrost start
Defrost will start if:
-The time programmed in parameter d0 has elapsed since the start of the last defrost.
-We press the H key for 3 seconds.
-By means of an external push-button (I10 / I11=5).
-Through the app or through AKONet.
Defrost completion
Defrost will complete if:
-The temperature programmed in parameter d4 has been reached in probe 2. This requires a 2nd probe
(l00=2) to be available, located in the evaporator.
-The time configured in parameter d1 has elapsed (maximum defrost duration).
-We press the H key for 5 seconds.
-By means of an external push-button (I10 / I11=5).
-Through the app or through AKONet.
DEFROST
COLD REGULATION
COLD REGULATION
F4
Máx. d1 d3d9
d0
SP
SP+C1
d4
DEFROST
DRIP TIME FAN START-UP
DELAY
"DEF” MESSAGE
S1
Other manuals for AKO-16524A
2
This manual suits for next models
1
Table of contents
Other AKO Temperature Controllers manuals
Popular Temperature Controllers manuals by other brands
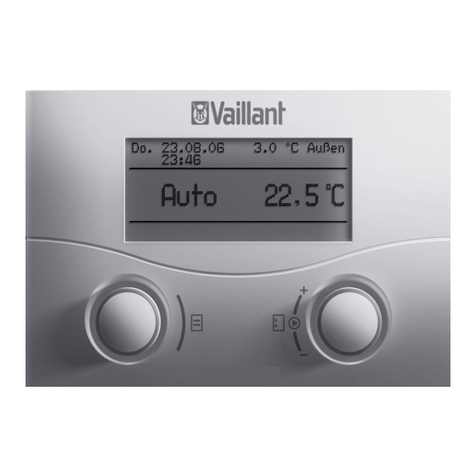
Vaillant
Vaillant VRC 430f OPERATING AND INSTALLATION Manual
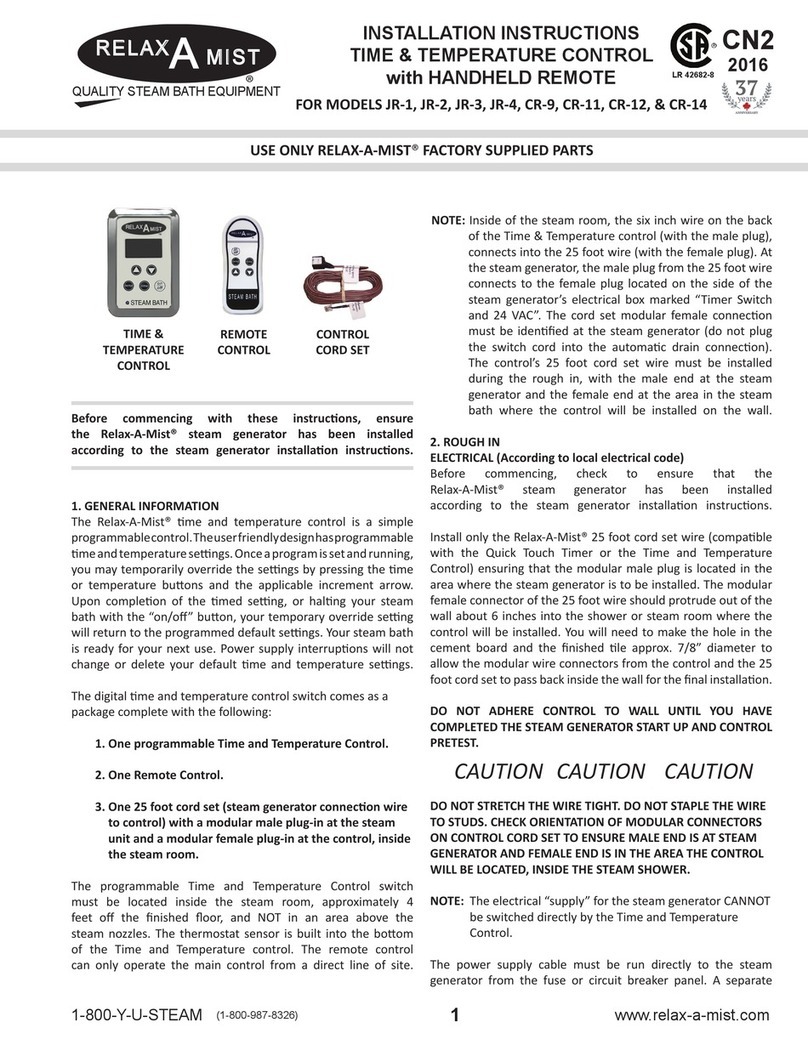
RELAX-A-MIST
RELAX-A-MIST CR-9 installation instructions

iNels
iNels RFSTI-11B installation manual
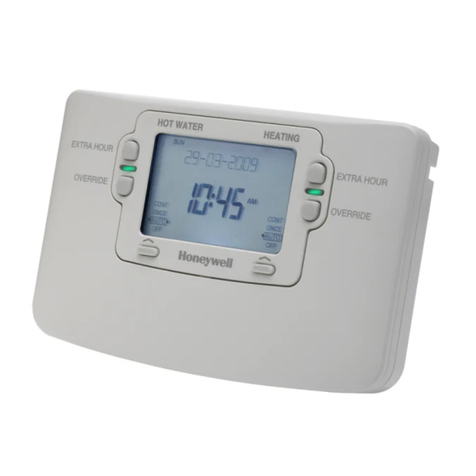
Honeywell
Honeywell ST9400S user guide
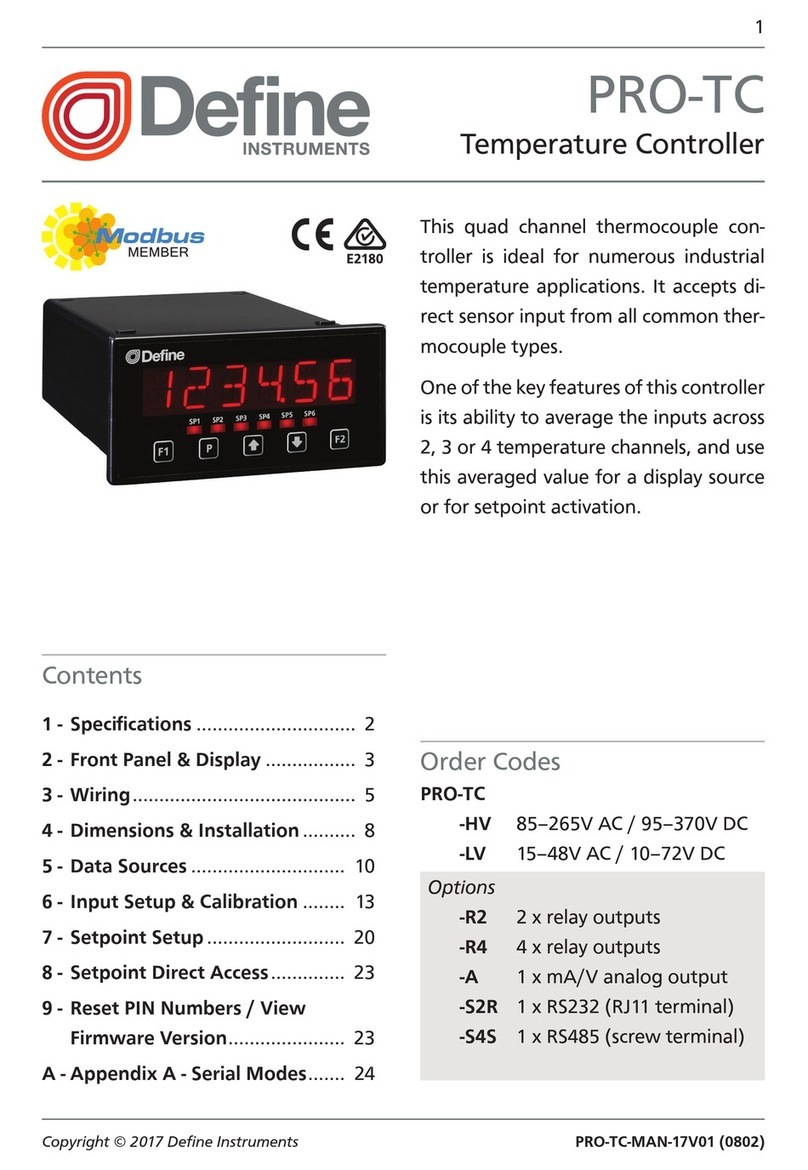
Define Instruments
Define Instruments PRO-TC-LV manual

GreenTech
GreenTech pureComfort YEAR-ROUND owner's manual