Ametek Thermox TM2000 User manual

Thermox® TM2000 Oxygen Analyzer
User Manual
Thermox
150 Freeport Road
Pittsburgh, PA 15238
PN 90287VE, Rev. T

ii | Thermox TM2000 Oygen Analyzer
© 2012 AMETEK
This manual is a guide for the use of the Thermox TM 2000 Oxygen Analyzer. Data herein has been veried and validated and is believed
adequate for the intended use of this instrument. If the instrument or procedures are used for purposes over and above the capabilities specied
herein, conrmation of their validity and suitability should be obtained; otherwise, AMETEK does not guarantee results and assumes no obligation
or liability. This publication is not a license to operate under, or a recommendation to infringe upon, any process patents.
OFFICES
USA - Pittsburgh
150 Freeport Road
Pittsburgh, PA 15238
Ph. 412-828-9040
Fax 412-826-0399
CHINA
AMETEK Shanghai (SPL)
Room 408, Metro Tower
#30 Tian Yao Qiao Road
Shanghai 200030
Ph. 86 21 6426 8111
Fax 86 21 6426 7054
USA - Delaware
455 Corporate Blvd.
Newark, DE 19702
Ph. 302-456-4400
Fax 302-456-4444
AMETEK Beijing
CITIC Building, Room 2305
19, Jianguomenwai Dajie
Beijing 100004
Ph. 86 10 8526 2111
Fax 86 10 8526 2141
USA - Texas
4903 West Sam Houston Parkway North
Suite A-400
Houston, TX 77041
Ph. 713-466-4900
Fax 713-849-1924
FRANCE
AMETEK Precision Instruments France
Rond Point de l’épine des champs
Buroplus Bat D
78990 Elanbourt
Ph. 33 1 30 68 89 20
Fax 33 1 30 68 89 29
CANADA
2876 Sunridge Way N.E.
Calgary, AB T1Y 7H9
Ph. 403-235-8400
Fax 403-248-3550
GERMANY
AMETEK GmbH
Rudolf-Diesel-Strasse 16
D-40670 Meerbusch
Ph. 49 21 59 91 36 0
Fax 49 21 59 91 3680
MIDDLE EAST – Dubai
AMETEK
PO Box 17067
Jebel Ali Free Zone
Dubai, UAE
Ph. 971-4-881 2052
Fax 971-4-881 2053
SINGAPORE
AMETEK Singapore Pte. Ltd.
No 43, Changi South Avenue 2, #04-01
Singapore 486164
Ph. 65-64842388
Fax 65-64816588

Thermox TM2000 OxygenAnalyzer | iii
Table ofContents
OFFICES .................................................................................................................ii
Safety Notes ...........................................................................................................v
Electrical Safety......................................................................................................v
Grounding..............................................................................................................v
Warning Labels.....................................................................................................vi
Electromagnetic Compatibility (EMC).............................................................vii
Equipment Used InClass I, Division 2 Hazardous Locations.....................viii
Environmental Information (WEEE) ................................................................ix
CHAPTER 1 OVERVIEW
Sensor...................................................................................................................1-1
Common Operator Errors ................................................................................1-4
Technical Support...............................................................................................1-5
CHAPTER 2 SPECIFICATIONS
CHAPTER 3 INSTALLATION AND START-UP
Unpacking ...........................................................................................................3-1
Mechanical Installation .....................................................................................3-2
Sensor Mounting .........................................................................................3-2
Sample Gas/Calibration Gas Plumbing....................................................3-2
Clean Gas RCU Installation (Optional)....................................................3-8
PPM Measurement Suggestions .............................................................3-12
Control Unit Mounting ...................................................................................3-14
Wiring.................................................................................................................3-17
General Wiring and Conduit Requirements.........................................3-18
Control Unit AC Mains Supply Connections........................................3-19
Sensor Connections...................................................................................3-22
Current Output Connections ..................................................................3-24
Alarm Contact Connections.....................................................................3-26
Remote Calibration Unit Connections...................................................3-28
RS-485 Communications Connections...................................................3-30
Option Card Installation.................................................................................3-34

iv | Thermox TM2000 OygenAnalyzer
CHAPTER 4 CONTROLLER / USER INTERFACE
Series 2000 User Interface .................................................................................4-1
Setup Key.............................................................................................................4-5
Analog Range Key............................................................................................4-19
Alarm Key..........................................................................................................4-27
Service Alarm....................................................................................................4-33
Watchdog Relay................................................................................................4-33
Exception Log ...................................................................................................4-34
CHAPTER 5 CALIBRATION
Definitions...........................................................................................................5-2
Types of Calibrations..........................................................................................5-2
Overview .............................................................................................................5-3
Aborting a Calibration .......................................................................................5-4
Password..............................................................................................................5-5
Initiate Cal ...........................................................................................................5-5
Initiate Verify.....................................................................................................5-10
Cal/Verify Data..................................................................................................5-15
Cal Gas Value ....................................................................................................5-17
Inject Cal Gas ....................................................................................................5-18
Set Cal Timers ...................................................................................................5-20
Configure Verify ...............................................................................................5-25
CHAPTER 6 MAINTENANCE AND TROUBLESHOOTING
System Messages................................................................................................6-2
Error Messages....................................................................................................6-4
Diagnostic Checks..............................................................................................6-8
General Troubleshooting.................................................................................6-17
Leak Check........................................................................................................6-17
Auto Calibration Card LEDs...........................................................................6-18
CHAPTER 7 SERVICE AND PARTS
Thermocouple Replacement ............................................................................7-3
Cell Replacement................................................................................................7-5
Furnace Replacement ........................................................................................7-6
Parts Replacement List ......................................................................................7-7
APPENDIX A SERIAL COMMUNICATIONS
APPENDIX B MENU OPTION CHARTS
APPENDIX C CURRENT OUTPUTS: OTHER APPLICATIONS
APPENDIX D USING SERIES 2000 RCU SIGNALS
APPENDIX E DRAWINGS AND CUSTOM INSTRUCTIONS

Thermox TM2000 OxygenAnalyzer | v
Safety Notes
WARNINGS, CAUTIONS, and NOTES contained in this manual emphasize critical instructions
as follows:
An operating procedure which, if not strictly observed, may result in personal injury or envi-
ronmental contamination.
An operating procedure which, if not strictly observed, may result in damage to the equipment.
Important information that should not be overlooked.
Electrical Safety
Up to 5 kV may be present in the analyzer housings. Always shut down power source(s) before
performing maintenance or troubleshooting. Only a qualified electrician should make electrical
connections and ground checks.
Any use of the equipment in a manner not specified by the manufacturer may impair the safety
protection originally provided by the equipment.
Grounding
Instrument grounding is mandatory. Performance specifications and safety protection are void
if instrument is operated from an improperly grounded power source.
Verify ground continuity of all equipment before applying power.
NOTE

vi | Thermox TM2000 OygenAnalyzer
PROTECTIVE CONDUCTOR TERMINAL
(BORNIER DE L’ECRAN DE PROTECTION)
Schutzerde
CAUTION - Risk of electric shock
(ATTENTION-RISQUE DE DÉCHARGE ÉLECTRIQUE)
Achtung - Hochspannung Lebensgefahr
CAUTION - (Refer to accompanying documents)
(ATTENTION-SE RÉFERER AUX DOCUMENTS JOINTS)
Achtung (Beachten Sie beiliegende Dokumente)
CAUTION - Hot Surface
(ATTENTION-SURFACE CHAUDE)
Achtung - Heiße Oberäche
Warning Labels
These symbols may appear on the instrument in order to alert you of existing conditions.

Thermox TM2000 OxygenAnalyzer | vii
Electromagnetic Compatibility (EMC)
Read and follow the recommendations in this section to avoid performance variations or
damage to the internal circuits of this equipment when installed in harsh electrical envi-
ronments.
The various configurations of the TM2000 should not produce, or fall victim to, electromagnetic
disturbances as specified in the European Union’s EMC Directive. Strict compliance to the EMC
Directive requires that certain installation techniques and wiring practices are used to prevent or
minimize erratic behavior of the Analyzer or its electronic neighbors. Below are examples of the
techniques and wiring practices to be followed.
In meeting the EMC requirements , the various Analyzer configurations described in this man-
ual rely heavily on the use of metallic shielded cables used to connect to the customer’s equip-
ment and power. Foil and braid shielded I/O and DC power cables are recommended for use in
otherwise unprotected situations. In addition, hard conduit, flexible conduit, and armor around
non-shielded wiring also provides excellent control of radio frequency disturbances. However,
use of these shielding techniques is effective only when the shielding element is connected to
the equipment chassis/earth ground at both ends of the cable run. This may cause ground loop
problems in some cases. These should be treated on a case-by-case basis. Disconnecting one
shield ground may not provide sufficient protection depending on the electronic environment.
Connecting one shield ground via a 0.1 microfarad ceramic capacitor is a technique allowing
high frequency shield bonding while avoiding the AC-ground metal connection. In the case of
shielded cables the drain wire or braid connection must be kept short. A two-inch connection
distance between the shield’s end and the nearest grounded chassis point, ground bar or termi-
nal is highly recommended. An even greater degree of shield performance can be achieved by
using metallic glands for shielded cable entry into metal enclosures. Expose enough of the braid/
foil/drain where it passes through the gland so that the shield materials can be wrapped back-
wards onto the cable jacket and captured inside the gland, and tightened up against the metal
interior.
Inductive loads connected to the low voltage “Alarm Contacts” are not recommended. However,
if this becomes a necessity, adhere to proper techniques and wiring practices. Install an appro-
priate transient voltage suppression device (low voltage MOV, “Transzorb,” or R/C) as close as
possible to the inductive device to reduce the generation of transients. Do not run this type of
signal wiring along with other I/O or DC in the same shielded cable. Inductive load wiring must
be separated from other circuits in conduit by using an additional cable shield on the offending
cable.
In general, for optimum protection against high frequency transients and other disturbances, do
not allow installation of this Analyzer where its unshielded I/O and DC circuits are physically
mixed with AC mains or any other circuit that could induce transients into the Analyzer or the
overall system. Examples of electrical events and devices known for the generation of harmful
electromagnetic disturbances include motors, capacitor bank switching, storm related transients,
RF welding equipment, static, and walkie-talkies.

viii | Thermox TM2000 OygenAnalyzer
SPECIAL WARNINGS AND INFORMATION
EQUIPMENT USED IN CLASS I, DIVISION 2 HAZARDOUS LOCATIONS
This Equipment is Suitable for Use in Class I, Division 2, Groups ABCD, T4 or Non-Hazardous
Areas Only.
Division 2 stand-alone Analyzer is not supplied with the 24 VDC power supply option.)
Explosion Hazard - Substitution of Components May Impair Suitability for Class I, Division
2.
Risque d’explosion - La substitution de composants peut rendre ce materiel inacceptable pour
les emplacements de Classe I, Division 2.
Explosion Hazard - Do Not Disconnect Equipment Unless Power Has Been Switched Off or
the Area is Known to be Non-Hazardous.
Risque d’explosion - Avant de déconnecter l’équipement, coupez le courant où vous assurez
que l’emplacement est designé non dangereux.
All input and output wiring must be in accordance with Class I, Division 2 wiring methods
(NEC Sec 501.4(b) or CEC 18-152) and in accordance with the authority having jurisdiction.
If the TM2000 is to be powered by a source of 24 VDC other than that supplied by AMETEK, the
power source’s output must be isolated from hazardous mains voltages using double or reinforced
insulation which has a minimum dielectric strength of 2300 VAC. When the TM2000 is used in a
Class I, Division 2 area, this external power source must be located in a general-purpose area or
be Division 2-approved.
The maximum ambient temperature for the Series 2000 control unit is 50° C (122° F).
NOTE

Thermox TM2000 OxygenAnalyzer | ix
Environmental Information (WEEE)
This AMETEK product contains materials that can be reclaimed and recycled. In some cases the
product may contain materials known to be hazardous to the environment or human health. In
order to prevent the release of harmful substances into the environment and to conserve our natu-
ral resources, AMETEK recommends that you arrange to recycle this product when it reached its
“end of life”.
Waste Electrical and Electronic Equipment (WEEE) should never be disposed of in a municipal
waste system (residential trash). The Wheelie Bin marking on this product is a reminder to dis-
pose of the product properly after it has completed its useful life and been removed from service.
Metals, plastics, and other components are recyclable and you can do your part by doing one of
the following steps:
• Whentheequipmentisreadytobedisposedof,takeittoyourlocalorregional
waste collection administration for recycling.
• Insomecases,your“endoflife”productmaybetradedinforcredittowards
the pur-chase of new AMETEK instruments. Contact your dealer to see if this
program is avail-able in your area.
• IfyouneedfurtherassistanceinrecyclingyourAMETEKproduct,contactour
office listed in the front of the instruction manual.

x | Thermox TM2000 OygenAnalyzer
Declaration of Conformity
Manufacturer’s Name: AMETEK/Thermox®
Manufacturer’s Address: Process & Analytical Instruments Division
150 Freeport Road
Pittsburgh, PA 15238
declares that the products:
Product Names: TM2000 Oxygen Analyzer using Series 2000 Controller
PPM RCU
Conform to the following standards:
EMC compliance:
EMC Directive 2004/108/EC:
Immunity:
EN 50082-2:1995 Generic - Heavy Industrial Equipment
EN 50082-1:1997 Generic - Residential, Commercial, Light Industrial Equipment
EN 61326:1997 Measuring Equipment (Heavy Industrial)
EN 61000-6-2:1999 EU Generic Heavy Industrial Equipment
Emissions:
EN 55011:1998 Class A , ISM Equipment
Safety Compliance:
UL 3101-1 UL Listed Inspection and Measuring Electrical Equipment
CAN/CSA 22.2 No. 1010.1-92 cUL Listed Inspection and Measuring Electrical Equipment
Low Voltage Directive 73/23/EEC:
EN 61010-1:1993,
Amendment A2: 1995 Electrical Equipment for Measurement, Controls,
and Laboratory Use
Series 2000 Controller and the PPM RCU also conform to the following safety standarrd:
UL 1604 UL Listed Process Control Equipment for Use in Hazardous Locations
Manufacturer’s Address in Europe:
AMETEK Precision Instruments Europe GmbH
Rudolf-Diesel-Strasse 16
D-40670 Meerbusch, Germany
July 2001
Mark Coppler
Compliance Engineer

Thermox TM2000 OxygenAnalyzer | xi
WARRANTY AND CLAIMS
We warrant that any equipment of our own manufacture or manufactured for us pursuant to our
specifications which shall not be, at the time of shipment thereof by or for us, free from defects
in material or workmanship under normal use and service will be repaired or replaced (at our
option) by us free of charge, provided that written notice of such defect is received by us within
twelve (12) months from date of shipment of portable analyzers or within eighteen (18) months
from date of shipment or twelve (12) months from date of installation of permanent equipment,
whichever period is shorter. All equipment requiring repair or replacement under the warranty
shall be returned to us at our factory, or at such other location as we may designate, transporta-
tion prepaid. We shall examine such returned equipment, and if it is found to be defective as a
result of defective materials or workmanship, it shall be repaired or replaced as aforesaid. Our
obligation does not include the cost of furnishing any labor in connection with the installation of
such repaired or replaced equipment or parts thereof, nor does it include the responsibility or cost
of transportation. In addition, instead of repairing or replacing the equipment returned to us as
aforesaid, we may, at our option, take back the defective equipment, and refund in full settlement
the purchase price thereof paid by Buyer.
The warranty shall not apply to any equipment (or part thereof) which has been tampered with or
altered after leaving our control or which has been replaced by anyone except us, or which has been
subject to misuse, neglect, abuse or improper use. Misuse or abuse of the equipment, or any part
thereof, shall be construed to include, but shall not be limited to, damage by negligence, accident,
fire or force of the elements. Improper use or misapplications shall be construed to include improper
or inadequate protection against shock, vibration, high or low temperature, overpressure, excess
voltage and the like, or operating the equipment with or in a corrosive, explosive or combustible
medium, unless the equipment is specifically designed for such service, or exposure to any other
service or environment of greater severity than that for which the equipment was designed.
The warranty does not apply to used or secondhand equipment nor extend to anyone other than
the original purchaser from us.
THISWARRANTYISGIVENANDACCEPTEDINLIEUOFALLOTHERWARRANTIES,WHETHER
EXPRESS OR IMPLIED, INCLUDING WITHOUT LIMITATION AND WARRANTIES OF FITNESS
OR OF MERCHANTABILITY OTHER THAN AS EXPRESSLY SET FORTH HEREIN, AND OF ALL
OTHER OBLIGATIONS OR LIABILITIES ON OUR PART. IN NO EVENT SHALL WE BE LIABLE
UNDER THIS WARRANTY OR ANY OTHER PROVISION OF THIS AGREEMENT FOR ANY
ANTICIPATED OR LOST PROFITS, INCIDENTAL DAMAGES, CONSEQUENTIAL DAMAGES,
TIME CHANGES OR ANY OTHER LOSSES INCURRED BY THE ORIGINAL PURCHASER OR
ANY THIRD PARTY IN CONNECTION WITH THE PURCHASE, INSTALLATION, REPAIR OR
OPERATION OF EQUIPMENT, OR ANY PART THEREOF COVERED BY THIS WARRANTY OR
OTHERWISE. WE MAKE NO WARRANTY, EXPRESS OR IMPLIED, INCLUDING WITHOUT
LIMITATION ANY WARRANTIES OF FITNESS OR OF MERCHANTABILITY, AS TO ANY OTHER
MANUFACTURER’SEQUIPMENT,WHETHERSOLDSEPARATELYORINCONJUNCTIONWITH
EQUIPMENT OF OUR MANUFACTURE. WE DO NOT AUTHORIZE ANY REPRESENTATIVE OR
OTHER PERSON TO ASSUME FOR US ANY LIABILITY IN CONNECTION WITH EQUIPMENT,
OR ANY PART THEREOF, COVERED BY THIS WARRANTY.

xii | Thermox TM2000 OygenAnalyzer
This page intentionally left blank.

Overview | 1-1
OVERVIEW
Sensor
The TM2000 has no operator-serviceable components. An operator
should never attempt to open the sensor or controller covers. Refer all
servicing to qualified service personnel.
Basic Elements of the Sensor
The TM2000 analyzer consists of the following basic systems:
• The Plumbing: Flow control valve, all inlet and outlet tubing, the sens-
ing cell and the sensing cell fitting.
• The Measuring System: Sensing cell, sensor board, interconnecting
wiring and the control unit.
• The Temperature System: Electrical cell heater (furnace), the type “K”
thermocouple (monitors furnace operating temperature), and the
sensor board containing cold junction thermocouple compensation,
interconnect wiring and the control unit. The temperature system
keeps the sensing cell at a constant temperature.
NOTE

1-2 | Thermox TM2000 OxygenAnalyzer
The Oxygen Measuring Cell
The sensing element itself is a closed-end tube or disk made from ceramic
zirconium oxide stabilized with an oxide of yttrium or calcium. Porous
platinum coatings on the inside and outside serve as a catalyst and as
electrodes. At high temperatures (generally above 1200°F/650°C), oxygen
molecules coming in contact with the platinum electrodes near the sensor
become ionic. As long as the oxygen partial pressures on either side of the
cell are equal, the movement is random and no net flow of ions occurs.
If, however, gases having different oxygen partial pressures are on either
side of the cell, a potentiometric voltage is produced (See Figure 1-1).
The magnitude of this voltage is a function of the ratio of the two oxygen
partial pressures. If the oxygen partial pressure of one gas is known, the
voltage produced by the cell indicates the oxygen content of the other gas.
A reference gas, usually air (20.9% O2), is used for one of the gases.
Figure 1-1.
Zirconium oxide cell
principle of operation.
Since the voltage of the cell is temperature dependent, the cell is main-
tained at a constant temperature. Some newer high temperature insitu
models use the heat from the process to heat the sensor, and the process
temperature is continuously measured and used in the software calcula-
tion. The oxygen content is then determined from the Nernst equation:
E = In
RT
4F
O1
O2

Overview | 1-3
where R and F are constants, T is absolute temperature, and O1and O2
are the oxygen partial pressures on either side of the cell.
For measuring oxygen in non-combustibles gases, the calibration of an
analyzer is obtained from the formula:
Where Ais a constant, Tis the cell temperature on an absolute scale (°C +
273) and O2 Unk% is the unknown oxygen concentration of the gas to be
analyzed, and which is calculated by the analyzer.
The cell produces zero voltage when the same amount of oxygen is on
both sides, and the voltage increases as the oxygen concentration of the
sample decreases. The voltage created by the difference in the sample gas
and the reference air is carried by a cable to the microprocessor control
unit, where it is linearized to an output signal.
Because of the high operating temperature of the cell, combustible
gases that are present may burn. When this occurs, the cell will gener-
ate high millivolts and cause the display to indicate less oxygen than
is actually in the gas (net oxygen content).
Hydrocarbons
When hydrocarbons are present in the gas sample, a combustion process
occurs when this gas sample is exposed to the high temperature of the
zirconia cell. An indication that hydrocarbons may be present in the gas
sample is that the oxygen reading will be lower than expected. For exam-
ple, if a calibration gas cylinder has an oxygen value of 20 PPM and 5 PPM
of hydrogen (balance nitrogen), the oxygen analyzer will read 17.5 PPM
oxygen. The reduction of oxygen is due to the combustion process where
5 PPM of hydrogen will combine with 2.5 PPM of oxygen to form water.
Thus, the oxygen analyzer will read 17.5 PPM rather than the actual 20
PPM oxygen.
The amount of oxygen reduction is dependent on the type of hydrocar-
bons present in the sample gas.
NOTE
AT = 44.0 at 615°C
E = A*T*Log 20.9%
O2Unk%
NOTE

1-4 | Thermox TM2000 OxygenAnalyzer
Common Operator Errors
There are some common errors to avoid. If they are avoided, your ana-
lyzer will operate with a minimum of maintenance and troubleshooting.
• Do not use pipe dope or any other contaminant that gives off com-
bustible vapor that can cause erroneous measurements on any joints
of the sample tubing.
• Do not use calibration gases if they contain a mixture of oxygen and
combustibles.
• Always introduce calibration gases at the recommended flow rate.
• When working on the plumbing inside the sensor cabinet, turn
the power off. The heater has exposed windings and a short to the
plumbing will blow the fuse and could damage the furnace or ther-
mocouple.
• Do not handle the cell excessively. Do not try to clean the cell except
by rinsing.
• Do not remove a cell or type “K” thermocouple that you may want to
use again when the inside of the furnace is still hot. Severe thermal
shock can be destructive to both of them.
• Always replace the viton O-ring when replacing the oxygen cell.
• Allow at least one hour after closing the sensor door for readings to
stabilize. Allow more time after a cold start-up.
• If calibrating in the PPM range, calibration gas should be in cylinders
made of aluminum, not carbon steel.

Overview | 1-5
Technical Support
AMETEK/Thermox is committed to providing the best technical support
in the industry. If you need service or application assistance, please call
AMETEK at (412) 828-9040, or your local AMETEK/Thermox representa-
tive.
Before you call the factory for technical support, run test gases and record
the following values (you may be asked by the factory to provide this
information when receiving service):
• Cellmillivolts
• Thermocouplemillivolts
• Celltemperature
See the “Display” section in the Controller / User Interface chapter for
help on how to display this information on your Series 2000 control unit.
If you need to return equipment, you will be asked to provide the follow-
ing information before obtaining a Return Material Authorization (RMA)
number.
• Billingandshippingaddress
• Modelnumber
• Serialnumber
• Purchaseordernumber
• Telephonenumber
Before returning material, you must get an RMA number from the
factory.
NOTE

1-6 | Thermox TM2000 OxygenAnalyzer
This page intentionally left blank.

Specications | 2-1
4 line x 20 character vacuum fluorescent. Displays combinations of oxygen
(0.1 PPM O2 to 100%, auto-ranging), time and date, cell temperature, user
programmable text, thermocouple mV or cell mV. Password protection,
programmable pressure compensation and context-sensitive help are also
provided.
Two isolated linear current outputs. Select O2, cell temperature, thermo-
couple mV or cell mV. Each output can be 4-20 mA, 0-20 mA, 20-4 mA or
20-0 mA, and is fully scalable. Hold or track during calibration and select
degree of damping. Maximum load 1200 ohms.
Two independent oxygen alarms, each high or low selectable. One alarm
can be assigned as oxygen, calibrate or verify. Set relays to energize or de-
energize on alarm.
0.5A, 30V, 10VA max. noninductive load, AC or DC

2-2 | Thermox TM2000 Oxygen Analyzer
Diagnostics
Watchdog timer and service alarms. System test for A/D, RAM, EEPROM
and keypad. Display line 4 reserved for full-text error and diagnostic
messages. Twenty-entry exception log for automatically detected system
events.
Communications
RS-485, 2-way addressable.
Environment
Ambient Temp: 14 to 122°F (-10 to 50°C)
Relative Humidity: 0% to 80%, non-condensing
Max. Altitude: 2000 meters
IEC Installation Category II
IEC Pollution Degree 2
Enclosure
Standard weatherproof NEMA 4 (IP56) wall/pannel mount. Optional GP
(General Purpose) wall mount, GP 19” rack mount, GP panel mount, or
stainless steel weatherproof NEMA 4X (IP 56) wall/panel mount. All are
UL Listed for NEC Class I, Division 2 areas. Purged and explosion-proof
versions available.
Calibration
Store last calibration and verification data. Selectable calibration gas run
time and process recovery time. Timed automatic calibration with option-
al remote calibration unit. Oxygen cell lifetime extender. Single gas verify
that analyzer is within calibration limits.
Power Requirements
Nominal 115-230 VAC ±10%, 47-63 Hz. max., 75 VA max.
Table of contents
Other Ametek Analytical Instrument manuals
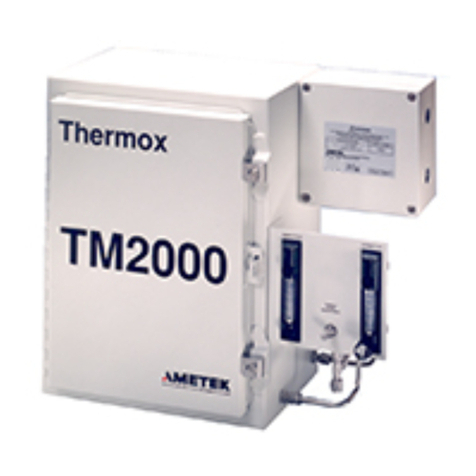
Ametek
Ametek TM2000 Pro User manual
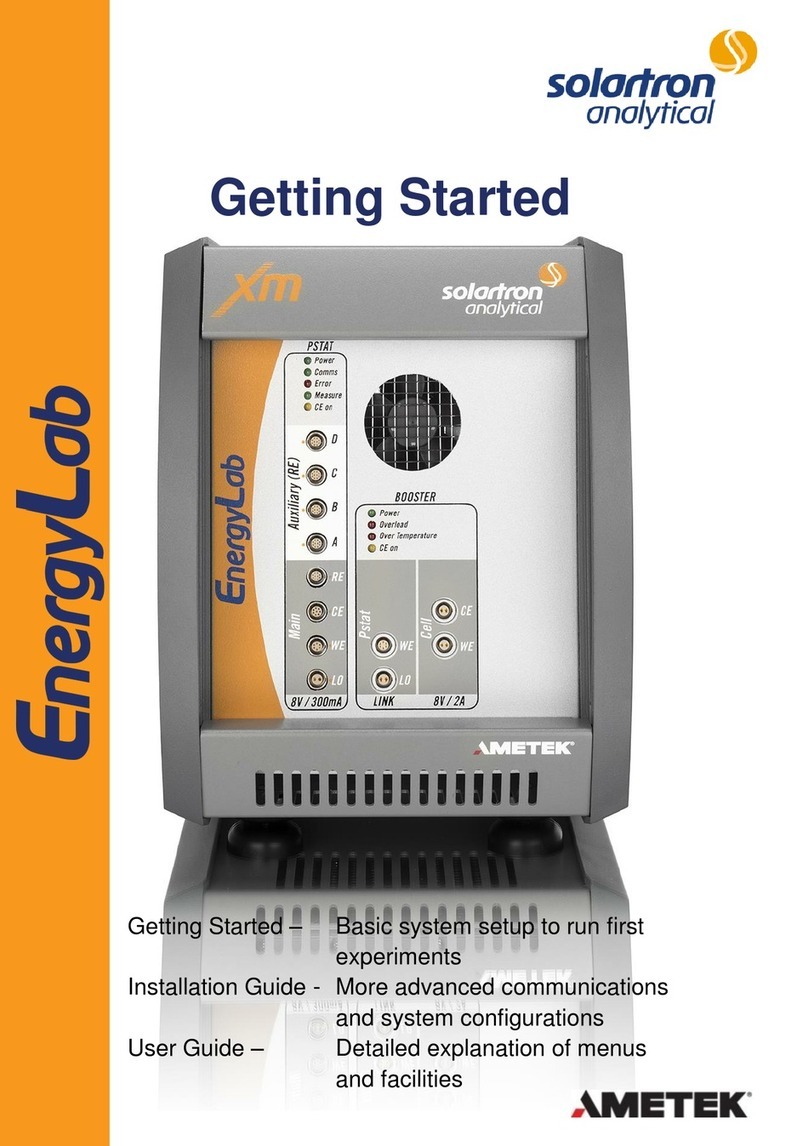
Ametek
Ametek Solatron Analytical EnergyLab XM User manual
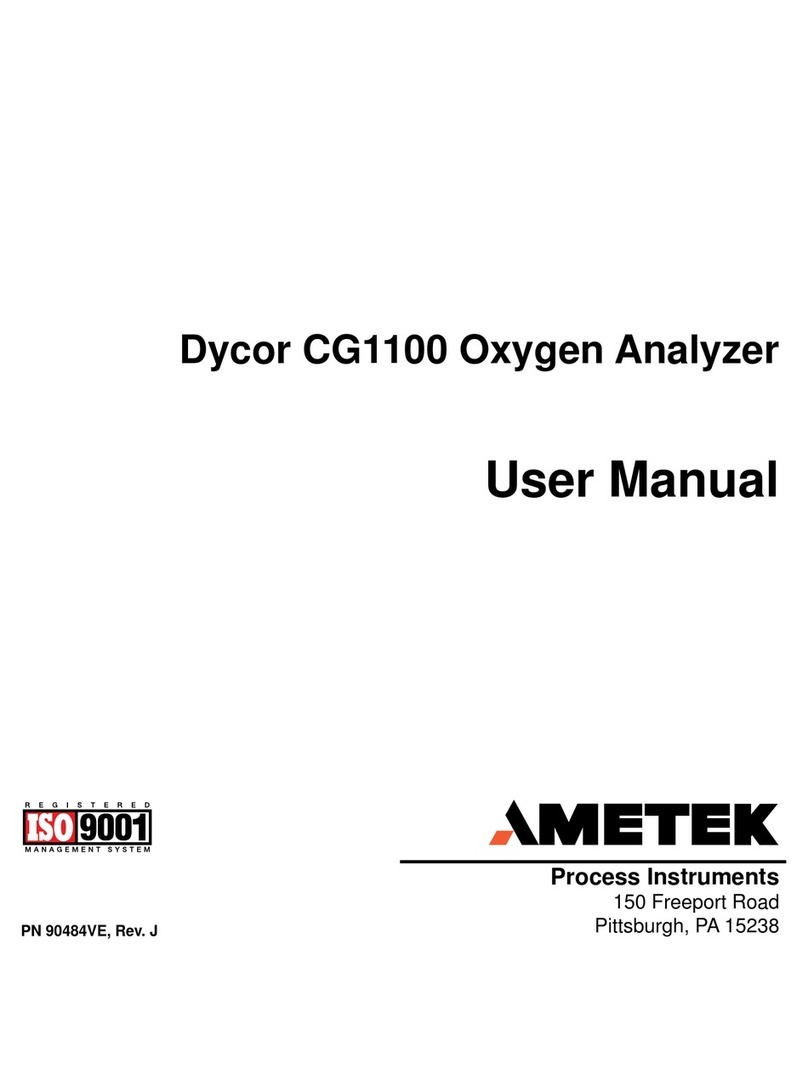
Ametek
Ametek Dycor CG1100 Series User manual
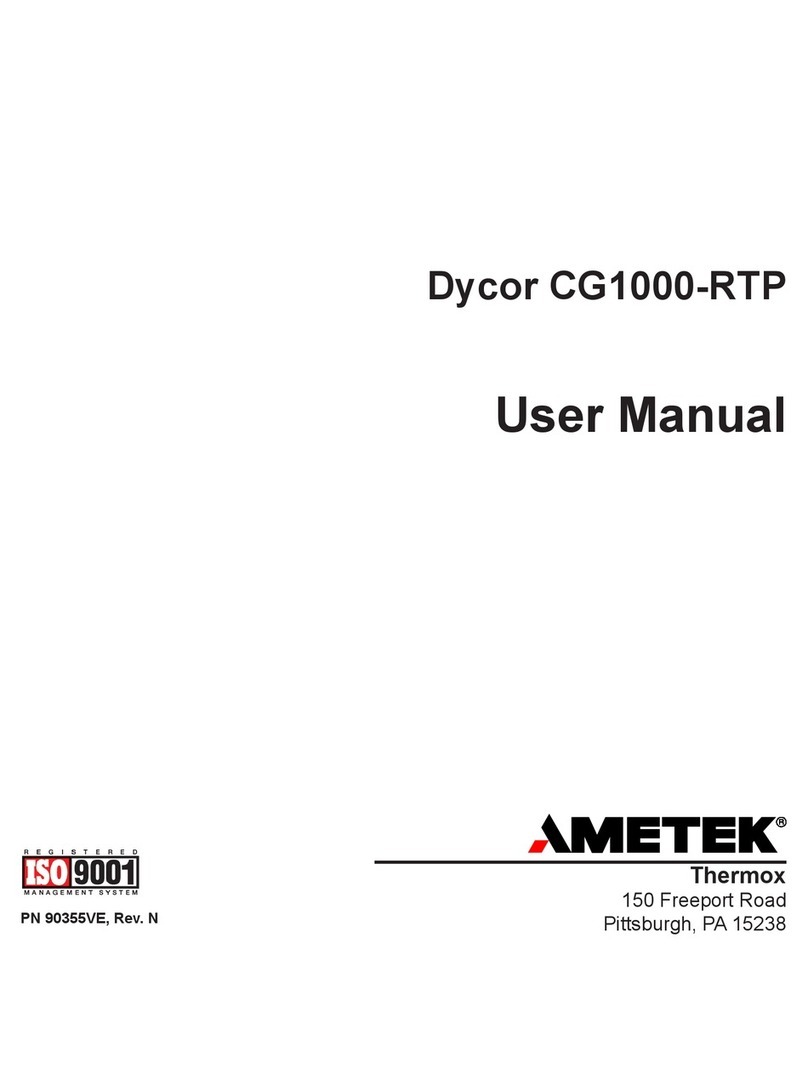
Ametek
Ametek Dycor CG1000-RTP User manual
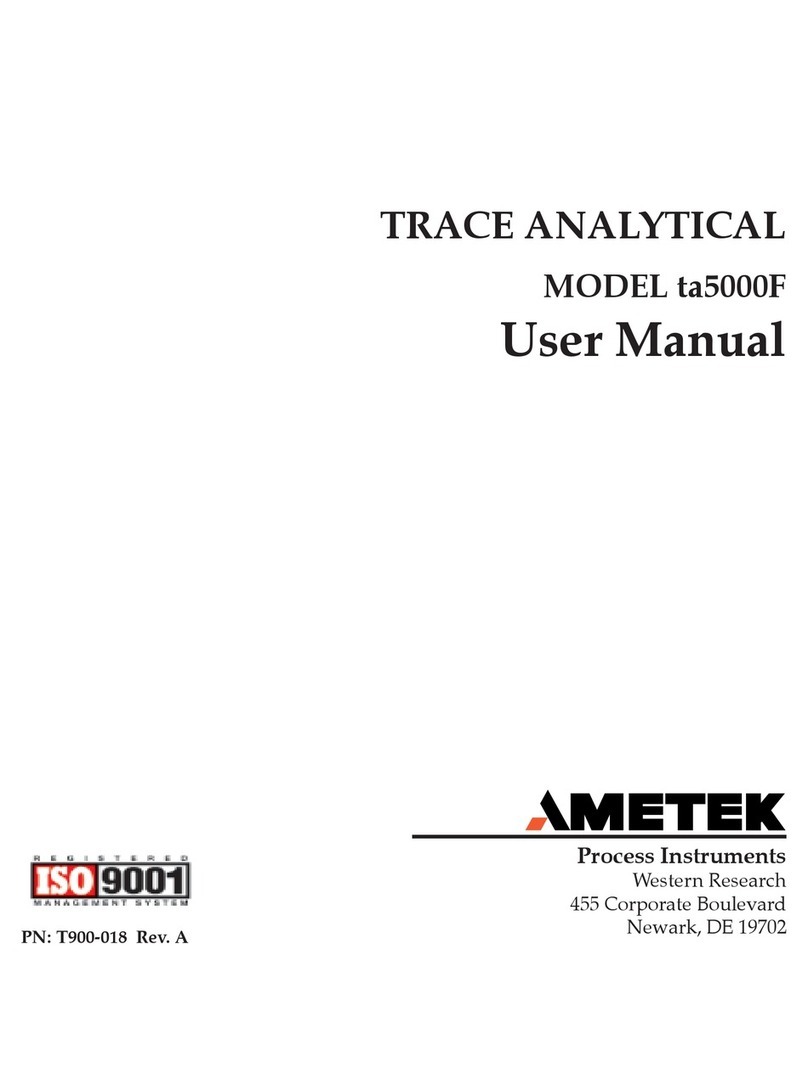
Ametek
Ametek TRACE ANALYTICAL TA5000F User manual
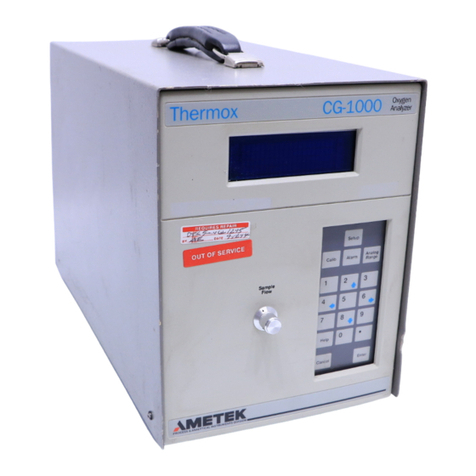
Ametek
Ametek Thermox CG1000 User manual
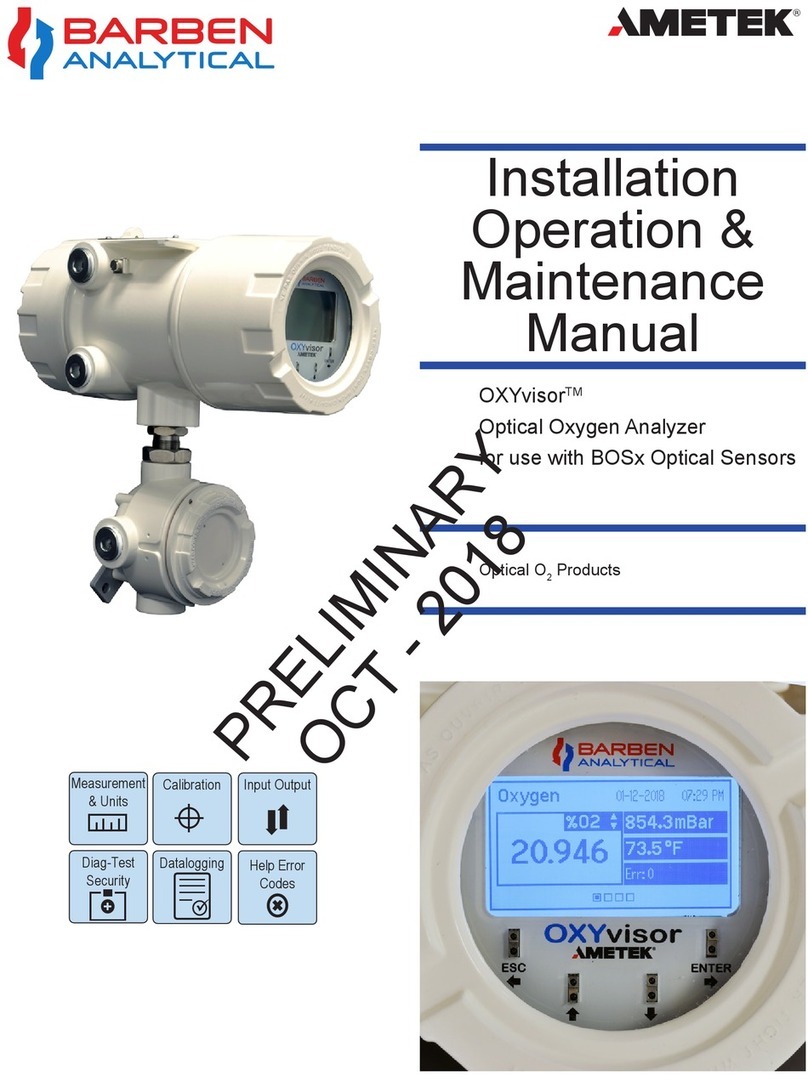
Ametek
Ametek OXYvisor Instruction manual