Bahco TAWM Series User manual

1
Original Instructions
TAWM SERIES
STANDARD AND SLIM
ELECTRONIC TORQUE-ANGLE WRENCH
WITH MEMORY

3
TAWM SERIES
HEAD TYPE
Square drive 48 teeth
9x12, 14x18 & 24x32 receivers for interchange-
able head
DISPLAY
• DISPLAY TYPE:
Dot Matrix LCD (192 x 65 Resolution) STD
Dot Matrix LCD (168 x 48 Resolution) SLIM
• VIEWING DIRECTION: 6:00
• BACKLIGHT: WHITE (LED)
SEALED BUTTON PAD
POWER - ON/OFF and torque and angle
re-zero
ENTER - measurement mode select and
menu entry
UP – increments torque and angle settings
and menu navigation
DOWN - decrements torque and angle set-
tings and menu navigation
UNITS - units select: ft-lbs, in-lbs, in-oz
(depending on range); kgm, kg-cm, dNm,
cNm (depending on range) and enter PSET
(preset) menu
LCD BACKLIGHT – Illuminates all screens
and last peak torque or angle recall
FUNCTIONS
• Set - torque or angle target
• Track - real time display of torque or accumu-
lated angular rotation with progress lights
• Peak Hold - 5 sec. ashing of peak torque or
alternating peak torque/angle on release of
torque
• Peak Recall - display last peak torque or peak
torque/angle on button press
• Memory - display of last 1500 peak torque or
peak torque/angle readings
ACCURACY
• Temperature: 22°C (72°F)
• Angle: ±1% of reading ±1º angular velocity
> 10º/sec < 180º/sec
STD CW CCW
±2% ±3% of reading, 20% to 100%
of full scale
Torque: ±4% ±6% of reading, 10% to 19%
(unexed) offullscale
±8% ±10% of reading, 5% to 9%
of full scale
SLIM CW CCW
±2% ±3% of reading, 20% to 100%
Torque: of full scale
(unexed) ±4% ±6% of reading, 5% to 19%
of full scale
OPERATING TEMPERATURE
0°F - 130°F (-18°C - 54°C)
STORAGE TEMPERATURE
0°F to 130°F (-18°C to 54°C)
MEASUREMENT DRIFT
ANGLE: -0.12 Angular Degrees per Degree C
TORQUE: +0.01% of reading per Degree C
HUMIDITY
Up to 90% non-condensing
BATTERY
SLIM: Single “AA” Alkaline Cell
STD: Three “AA” Alkaline Cells
Alkaline or rechargeable NiMH batteries ex-
ceeds ASME battery life requirement of 10 hours
continuous operation.
DEFAULT AUTO SHUT-OFF
After 2 minutes idle –
(Adjustable, see Advanced Settings)
WARNING.
RISK OF FLYING PARTICLES.
Over-torquing can cause breakage.
Force against ex stops on ex
head can cause head breakage. An
out of calibration angle wrench can
cause part or tool breakage. Broken
hand tools, sockets or accessories
can cause injury. Excess force can
cause crowfoot or are nut wrench
slippage.
• Read this manual completely before
using ELECTRONIC WRENCH.
• To insure accuracy, work must not
move in angle mode.
• For personal safety and to avoid
wrench damage, follow good profes-
sional tool and fastener installation
practices.
• Periodic recalibration is necessary to
maintain accuracy.
• Wear safety goggles, user and
bystanders.
• Be sure all components, including
all adaptors, extensions, drivers
and sockets are rated to match or
exceed torque being applied.
• Observe all equipment, system and
manufacturer’s warnings, cautions and
procedures when using this wrench.
• Use correct size socket for fastener.
• Do not use sockets showing wear or
cracks.
• Replace fasteners with rounded
corners.
• To avoid damaging wrench: Never
use wrench with power off. Always
turn ON wrench so applied torque is
being measured.
• Do not press POWER while torque is
applied or while wrench is in motion.
• Never use this wrench to break
fasteners loose.
• Do not use extensions, such as a
pipe, on handle of wrench.
• Check that wrench capacity matches
or exceeds each application before
proceeding.
• When using negative offsets, verify
maximum targets are not exceeded
(see tables on page 6).
• Verify calibration if dropped.
• Make sure ratchet direction lever is
fully engaged in correct position.
• Verify calibration of wrench if you
know or suspect its capacity has
been exceeded.
• Do not force head of ex head drives
against stops.
• Always adjust your stance to prevent
a possible fall should something give
while using wrench.
• Do not attempt to recharge Alkaline
cells.
• Store wrench in dry place.
• Remove batteries when storing
wrench used for periods longer than
3 months.
WARNING.
Electrical Shock Hazard.
Electrical shock can cause injury.
Metal handle is not isolated.
Do not use on live electrical circuits.
SAVE THESE INSTRUCTIONS
DISCLAIMER
Operation of the wrench is not warranted in an
EU member state if operating instructions are
not in that State’s language.
Contact BAHCO if a translation is needed.
SPECIFICATIONSIMPORTANT SAFETY INSTRUCTIONS

5
TAWM SERIES
Install fresh Alkaline “AA” cells into handle of wrench.
WRENCH POWER ON SEQUENCE
Note: Do not turn on wrench while torque is applied, otherwise torque zero offset will be incorrect
and wrench will indicate a torque reading when torque is released. If this occurs, re-zero wrench by
momentarily pressing POWER button while wrench is on a stable surface with no torque applied.
1. Turn On Wrench.
While holding wrench still, press POWER button. BAHCO logo will be displayed followed by torque and
angle re-zeroing screens (if angle mode has been previously selected). If real-time-clock has not been
set, date and time entry screens are displayed (see Advanced Conguration section for entering date
and time). After entering date and time or if time has been previously set, target TORQUE or ANGLE
screen will now be displayed (depending on previous measurement mode selected).
2. Select Measurement Mode.
Toggle between target TORQUE and ANGLE screens by repeatedly pressing ENTER button.
STD
USER INSTRUCTIONS
SLIM
Note: When date and time is set for rst time, In-Service date is also set and is used for calculating
initial calibration interval (see “Setting Calibration Interval” in Advanced Conguration section).
Note: If wrench is powered up in torque only measurement mode, angle is not zeroed until mode is
changed to angle measurement mode, at which time torque and angle zeroing begins automatically
after 2 seconds. Wrench should be placed on a stable surface with no torque applied.
Note: Pressing ENTER button while angle is zeroing will abort zeroing function to allow user to
select another measurement mode.
TORQUE MODE
1. Set Target.
Use UP/DOWN buttons to change TORQUE target value.
2. Select Units of Measure.
Repeatedly press UNITS button while on target TORQUE screen until desired units are displayed.
3. Apply TORQUE.
Grasp center of handle and slowly apply torque to fastener until progress lights display green and a
½ second audible alert and handle vibration alerts you to stop.
4. Release TORQUE.
Note peak TORQUE reading ashing on LCD display for 5 seconds. Pressing BACKLIGHT button
while peak torque is ashing will continue to display value until button is released. Momentarily
pressing UP/DOWN, ENTER or UNITS button will immediately return to target TORQUE screen.
Reapplying TORQUE will immediately start another TORQUE measurement cycle.
5. Recall Peak TORQUE Reading.
To recall last peak TORQUE measurement, press and hold BACKLIGHT button for approximately 3
seconds. Peak TORQUE will ash for 5 seconds.
ANGLE MODE
Note: When angle measurement mode is selected for rst time following a power on, “ANGLE
ZERO REQUIRED” message is displayed. After two seconds angle zero process begins and
FIGURE 1
BATTERY
CONDITION
DATA STORAGE
ALERT
USB
CONNECTOR
PROGRESS
LIGHTS
PROGRESS
LIGHTS
TORQUE AND/OR
ANGLE DISPLAY
MODE
COUNT
ON/OFF AND
RE-ZERO BUTTON
UNITS AND PRESET
ENTRY BUTTON
INCREMENT
BUTTON
DECREMENT
BUTTON
MODE SELECT AND
MENU ENTRY BUTTON
LCD BACKLIGHT
AND PEAK
TORQUE/ANGLE
RECALL BUTTON
AUDIBLE
ALERT
PROGRESS LIGHTS
Yellow:
First light indicates 40% of
target torque or angle reached,
Second indicates 60% of
target reached,
Third indicates 80% of
target reached.
Green:
Indicates target torque or angle
reached.
Red:
Indicatesexceededtorqueor
angle target plus 4% or
exceededmaximumPreset
target.

7
TAWM SERIES
wrench must be placed on a stable surface. If ENTER button is pressed before two seconds to
change to torque only mode, angle zero process is skipped.
1. Set target. Use UP/DOWN buttons to change target ANGLE value.
2. Apply Torque and Rotate Wrench. Grasp center of handle and slowly apply torque to fastener and
rotate wrench at a moderate consistent speed until progress lights display green and a ½ second
audible alert and handle vibration alerts you to stop.
3. Release torque. Note alternating peak TORQUE and ANGLE readings ashing on LCD display for 5
seconds. Pressing BACKLIGHT button while peak values are ashing will continue to display values
until button is released. Momentarily pressing UP/DOWN, ENTER or UNITS button will immediately
return to target ANGLE screen. Reapplying torque (ratcheting) before target screen is displayed will
continue ANGLE accumulation as wrench is rotated.
4. Recall Peak ANGLE Reading. To recall last peak ANGLE measurement, press and hold BACKLIGHT
button for approximately 3 seconds. Peak TORQUE and ANGLE will be displayed alternately for 5
seconds.
MODE CYCLE COUNT
Mode cycle count feature is used to indicate number of times wrench has reached target torque in
torque measurement mode or target angle in angle measurement mode.
STD / SLIM
TORQUE AND ANGLE MODE CYCLE COUNTING
1. Numerical counter located in top right of target torque or target angle screen will increment after each
torque or angle cycle if applied torque or angle has reached target value.
2. When toggling between torque mode or angle mode using ENTER button or if target is changed,
numerical counter will reset back to 00. counter WILL NOT reset when re-zeroing, on menu entry/
exit or power down.
3. Memory icon will turn on indicating at least one torque or angle cycle data has been stored in memory.
DATA DOWNLOAD
Torque and Angle data in memory can be downloaded to a computer via USB port.
Note: When downloading data from a wrench that has previous downloaded data, rename
previous le or move it to a different directory to prevent overwrite. However, Windows®will
notify user of duplicate le names and allow user to skip download, overwrite existing le or
save new le as a second copy.
1. Connect supplied USB cable from computer to wrench.
2. Computer will display “AutoPlay” window showing TORQLOG as a disk drive with option of using
Windows Explorer to view les:
3. Click “Open Folder” selection to display TORQLOG Character Separated Value (.csv) le.
Note: If “AutoPlay” does not start automatically, use Explorer to display TORQLOG drive contents.
4. Open le using Microsoft Excel by double clicking on le name (Example: “1213590002.CSV”) or
“drag and drop” le to computer.
5. Data on wrench can be cleared by deleting le on the TORQLOG drive.
Note: Wrench Serial Number and Calibration Date are included in rst line of downloaded .csv le.
Example:

9
TAWM SERIES
MAIN MENU
Main menu displays wrench operational information.
1. From target torque or angle screen, press and hold ENTER button for 3 seconds.
2. Use UP/DOWN buttons to highlight menu selection then press ENTER button.
Menu Selections:
EXIT - Exits Main menu and returns to target screen.
LANGUAGE - Displays language selection menu.
SET HEAD LENGTH - Displays wrench head length entry screen.
SHOW DATA - Displays stored torque and angle data.
CLEAR DATA - Clears stored torque and angle data.
CYCLE COUNT - Displays torque/angle cycle count screen.
SETTINGS - Displays advanced settings menu (see Advanced Settings Section).
CONFIGURE - Displays advanced conguration menu (see Advanced Conguration Section).
SETTING HEAD LENGTH
Note: If wrench has an interchangeable head or an adapter or extension is added, length of
head, adapter and/or extension being used can be entered to correct for a different length
without requiring re-calibration.
1. To enter a head length, from target torque or angle screen, press and hold ENTER button for 3
seconds.
2. With SET HEAD LENGTH menu selection highlighted, momentarily press ENTER button.
3. Set Head Length screen is displayed next. Default head length is length of head at calibration
(zero for xed head wrench) and is displayed with most-signicant digit highlighted. Use UP/
DOWN buttons to increment/decrement head length. Pressing and holding UP/DOWN buttons will
progressively increment/decrement value faster.
4. Press ENTER button to accept digit and highlight next-signicant digit.
5. Default units of length is in inches. Press UNITS button to change to millimeters.
6. Pressing ENTER button after least-signicant digit is set returns to main menu. If length is changed
from default, «OFFSET IN USE» message will be displayed on target screen (on STD wrenches),
the target torque is highlighted in black (on SLIM wrenches).
Note: If UP/DOWN buttons are pressed simultaneously while on the Set Head Length screen,
displayed head length resets to zero or calibration head length for interchangeable head
wrenches.
Note: For a xed length head, head length entered is offset length measured from center of
drive to center of fastener.
Note: For an interchangeable head, head length is measured from locking pin to center of drive.
SET HEAD LENGTH is set during calibration. If a different length head is used, enter new head
length and offset is calculated automatically.
Note: For an interchangeable head with an adapter, head length entered is sum of head length
and offset length.
USE OF NEGATIVE OFFSETS
Note: Enter a negative value for offset when used in reverse direction with ex head or when
calculating sum of interchangeable head and offset lengths.
Offset
Offset

11
TAWM SERIES
800 Nm wrench:
Maximum Target Torque = offset *7,6 + 800
Offset (cm) Max Target (Nm)
-1 792
-2 785
-3 777
-4 770
When length of an offset (or sum of head minus offset for interchangeable head) is negative, maximum
fastener target is limited by following formulas:
STD
SLIM
Note: When using a negative offset, entering a target torque greater than maximum values
above may cause an overtorque error before reaching fastener target torque and possibly
damage wrench.
VIEWING STORED TORQUE AND ANGLE DATA
Torque data is stored in memory after each torque cycle if applied torque has reached target value.
Torque and angle data is stored in memory after each angle cycle if applied angle has reached target
value. Memory Indicator is displayed when data is stored in non-volatile memory.
1. To view stored torque and angle data, from target torque or angle screen, press and hold ENTER
button for 3 seconds.
2. Highlight SHOW DATA menu selection by pressing UP/DOWN buttons then press ENTER button to
display Show Data screen.
3. In Show Data screen, scroll through each stored data record by pressing UP/DOWN buttons.
Example:
0002 = Show Data List Counter: TQ = Peak torque value
0001 = Show Data List Counter: TQ = Peak torque value: ANG = Peak angle value
4. Pressing ENTER button while on Show Data screen returns to main menu.
STD
SLIM
Note: A maximum of 1500 data records can be stored. Memory full icon will be displayed when
full and no more data is stored until memory is cleared (on STD wrenches only).
Note: A maximum of 1500 data records can be stored in memory. Memory full icon will be
displayed when full. When full, a new data record will become record number 1500 and all older
data is shifted down one record number. Record 0002 becomes 0001 and old 0001 is dropped.
DELETING STORED TORQUE AND ANGLE DATA
1. From target torque or angle screen, press and hold ENTER button for 3 seconds.
2. Highlight CLEAR DATA menu selection using UP/DOWN buttons then press ENTER button to
display CLEAR ALL DATA screen.
3. In CLEAR ALL DATA screen, highlight YES menu selection to delete all stored data, or NO menu
selection to exit without deleting data.
4. Press ENTER button after making selection.
340 Nm wrench:
Maximum Target Torque = offset *6,1 + 340
Offset (cm) Max Target (Nm)
-1 334
-2 328
-3 322
-4 316
135 Nm wrench:
Maximum Target Torque = offset *4,1 + 135
Offset (cm) Max Target (Nm)
-1 131
-2 127
-3 123
-4 119
10 Nm wrench:
Maximum Target Torque = offset * 0.435 + 10
Offset (cm) Max Target (Nm)
-1 9.57
-2 9.13
-3 8.70
-4 8.26
30 Nm wrench:
Maximum Target Torque = offset * 1.3 + 30
Offset (cm) Max Target (Nm)
-1 28.70
-2 27.40
-3 26.10
-4 24.80

13
TAWM SERIES
Note: If wrench is Locked (see Preset Lock in Advanced section), Clear Data function is disabled.
STD
SLIM
VIEWING AND CLEARING WRENCH CYCLE COUNTER
Each time torque or angle target is reached, wrench cycle counter is incremented. Maximum cycle
count is 999999.
1. From target torque or angle screen, press and hold ENTER button for 3 seconds.
2. Highlight CYCLE COUNT menu selection using UP/DOWN buttons.
3. Press ENTER button to display CYCLE COUNT screen.
4. To exit CYCLE COUNT screen without clearing count, press ENTER button while EXIT menu
selection is highlighted.
5. To reset wrench cycle count to 0, highlight CLEAR menu selection then press ENTER button.
6. EXIT menu selection is automatically highlighted after count is cleared. Press ENTER button to
return to main menu.
STD
SLIM
Note: If wrench is Locked (see Preset Lock in Advanced section) Clear count function is disabled.
LANGUAGE
1. To select the language menu, press the ENTER button while LANGUAGE is highlighted then
highlight the desired language and press the ENTER button.
2. Decimal Mark selection menu is displayed. Decimal separator can be a comma or decimal point.
Use UP/DOWN buttons to select the decimal separator then press the ENTER button.
Note: The decimal separator will affect the formatting of the downloaded data when opened by
Excel depending on Windows®regional settings.
STD
SLIM
3. To exit Main menu and return to target torque or angle screen, press ENTER button while EXIT
menu selection is highlighted.
TARGET PRESETS (PSET)
PSET function gives user ability to congure 50 preset target torque or target angle settings, each with
a target, minimum, maximum (over range) and batch count value. PSETs are stored in non-volatile
memory so that they are retained while power is off.
Note: After adding a Preset (see below), navigate between manual target torque, angle mode
and PSET screen by repeatedly pressing ENTER button. While PSET screen is displayed, press
UP/DOWN buttons to select additional congured PSETs.

15
TAWM SERIES
6. MAXIMUM TORQUE screen is displayed next. MAXIMUM TORQUE is torque value above which
red progress lights turn on. Initial MAXIMUM TORQUE value will be TARGET TORQUE value plus
positive torque tolerance (default 4%, see MODE SETUP in Advanced Conguration section).
Maximum torque value can be set greater than TARGET TORQUE value to 10% above wrench
maximum range by pressing UP/DOWN buttons. Once desired maximum torque value has been set,
press ENTER button.
7. BATCH COUNT screen is displayed next. Default value is zero. Batch count range is 0 to 99. Press
UP/DOWN buttons to increment/decrement batch count. Mode Count increments each time target
torque is reached if a batch count of zero is entered. Mode Count decrements if a non-zero batch
count is entered and resets to batch count value when count reaches zero. Once desired batch
count value has been set, press ENTER button.
8. PSET target screen is displayed labeled with next available PSET number from 01 to 50.
9. To enter additional torque presets, repeatedly press ENTER button until target torque screen is dis-
played and repeat steps above.
STD
SLIM
ADDING AN ANGLE PRESET
1. From manual target angle screen, press and hold UNITS button for 3 seconds.
2. ADD PRESET conrmation screen is displayed. Highlight YES menu selection using UP/DOWN buttons
then press ENTER button. NO menu selection returns to main menu without adding a PSET.
3. TARGET ANGLE screen is displayed. TARGET ANGLE is fastener rotational angle target value. Initial
TARGET ANGLE value is value from target angle screen. TARGET ANGLE can be set from 0 to 360° by
pressing UP/DOWN buttons. Once desired target angle value has been set, press ENTER button.
4. MINIMUM ANGLE screen is displayed. MINIMUM ANGLE is value at which green progress lights, au-
dible alert and vibrator turn on. Initial MINIMUM ANGLE value is TARGET ANGLE minus negative angle
STD
SLIM
ADDING A TORQUE PRESET
1. From manual target torque screen, select units of measure.
2. Press and hold UNITS button for 3 seconds.
3. ADD PRESET conrmation screen is displayed. Highlight YES menu selection using UP/DOWN
buttons then press ENTER button. NO menu selection returns to main menu without adding a PSET.
4. TARGETTORQUE screen is displayed. TARGET TORQUE is target value of fastener. Initial TARGET
TORQUE value is value from target torque screen. TARGET TORQUE can be set to any value within
wrench torque range by pressing UP/DOWN buttons. Once desired target torque value has been
set, press ENTER button.
5. MINIMUM TORQUE screen is displayed. MINIMUM TORQUE is value at which green progress
lights, audible alert and vibrator turn on. Initial MINIMUM TORQUE value is TARGET TORQUE value
minus negative torque tolerance (default 0%, see MODE SETUP in Advanced Conguration section).
MINIMUM TORQUE can be set to any value from TARGET TORQUE to wrench minimum torque range
by pressing UP/DOWN buttons. Once desired minimum torque value has been set, press ENTER button.

17
TAWM SERIES
tolerance (default 0%, see MODE SETUP in Advanced Conguration section). MINIMUM ANGLE can be
set from 0 to TARGET ANGLE by pressing UP/DOWN buttons. Once desired minimum angle value has
been set, press ENTER button.
5. MAXMUM ANGLE screen is displayed next. MAXIMUM ANGLE is angle value above which red progress
lights turn on. Initial MAXIMUM ANGLE value will be TARGET ANGLE plus positive angle tolerance (de-
fault 4%, see MODE SETUP in Advanced Conguration section). MAXIMUM ANGLE value can be set to
any value greater than TARGET ANGLE by pressing UP/DOWN buttons. Once desired value has been
set, press ENTER button.
6. BATCH COUNT screen is displayed next. Default value is zero. Batch count range is 0 to 99. Press UP/
DOWN buttons to increment/decrement batch count. Mode Count increments each time target angle is
reached if a batch count of zero is entered. Mode Count decrements if a non-zero batch count is entered
and resets to batch count value when count reaches zero. Once desired batch count value has been set,
press ENTER button.
7. PSET target screen is displayed labeled with next available PSET number from 01 to 50.
8. To enter additional angle presets, repeatedly press ENTER button until target angle screen is displayed and
repeat steps above.
STD
SLIM
EDITING A PRESET
Edit PSET function gives user ability to edit stored PSETS on wrench.
1. From Preset screen to be edited, press and hold UNITS button for 3 seconds.
2. CHANGE PRESET screen is displayed.
3. Highlight EDIT selection using UP/DOWN buttons then press ENTER button.
4. TARGET TORQUE or TARGET ANGLE screen is displayed. Value can be changed by pressing UP/
DOWN buttons. Once desired target torque or angle value has been set, press ENTER button.
5. MINIMUM TORQUE or MINIMUM ANGLE screen is displayed. Value can be changed by pressing
UP/DOWN buttons. Once desired torque or angle value has been set, press ENTER button.
6. MAXMUM TORQUE or MAXIMUM ANGLE screen is displayed next. Value can be changed by
pressing UP/DOWN buttons. Once desired torque or angle value has been set, press ENTER button.
7. BATCH COUNT screen is displayed next. Value can be changed by pressing UP/DOWN buttons.
Once desired batch count value has been set, press ENTER button.
8. PSET target screen is displayed labeled with same PSET number.
STD
SLIM
Note: Pressing ENTER button while EXIT menu selection is highlighted will exit without editing
PSET.
DELETING A PRESET
Delete PSET function allows user to remove stored presets from wrench
1. From Preset screen to be deleted, press and hold UNITS button for 3 seconds.
2. CHANGE PRESET screen is displayed.
3. Highlight DELETE menu selection using UP/DOWN buttons and press ENTER button.
4. Target screen is displayed and deleted PSET is no longer available for selection.

19
TAWM SERIES
Note: Pressing ENTER button while EXIT menu selection is highlighted will exit without deleting PSET.
Note: When a PSET is deleted, all other stored PSET’s will retain their original PSET numbers.
When a new PSET is entered, it will be assigned rst available PSET number in sequence.
STD SLIM
SLIM
Note: All user congurable settings are stored in non-volatile memory and are retained while
power is off.
SHOW INFO
Show Info menu selection displays wrench operational information.
1. From Settings menu, press ENTER button while SHOW INFO selection is highlighted.
2. SHOW INFO screen is displayed.
3. UP/DOWN buttons are used to scroll screen.
Operational Information:
SN: Serial number assigned to wrench.
CAL: Date of last wrench calibration.
ISD: In-Service Date.
TCF: Torque Calibration Factor.
ACF: Angle Calibration Factor.
VER: Software version.
OVR CNT: Overtorque Counter tracks how many times an over-torque event occurred on wrench
(torque >125% of full scale).
AZZ: Angle Z-Axis Zero Offset (only on SLIM wrenches).
AZX: Angle X-axis Zero Offset (only on SLIM wrenches).
AZO: Angle Zero Offset at full scale torque (only on SLIM wrenches).
TFS: Torque full scale value (only on SLIM wrenches).
Copyright (only on SLIM wrenches).
TQZ: Torque Zero Offset.
ANZ: Angle Zero Offset (only on SLIM wrenches).
4. Pressing ENTER button exits Show Info screen and returns to Settings menu.
STD SLIM
ADVANCED SETTINGS
Advanced settings are accessed from SETTINGS menu selection on main menu.
1. From target torque or angle screen, press and hold ENTER button for 3 seconds.
2. Highlight SETTINGS menu selection using UP/DOWN buttons.
3. Press ENTER button to display Settings menu.
Menu Selections:
EXIT - Exits Settings menu and returns to target screen.
SHOW INFO - Displays wrench operational information.
SLEEP TIME - Displays power down interval setup screen.
LCD CONTRAST - Displays LCD contrast setup screen.
KEY BEEP - Displays button press beep enable/disable setup screen.
TARGET BEEP - Displays target beep enable/disable setup screen (only on SLIM wrenches).
AUTO BACKLIGHT - Displays auto backlight enable/disable screen to turn on backlight during
measurement.
TOGGLE BACKLGHT - Displays BACKLIGHT button toggle or timeout enable/disable screen.
VIBRATOR CONFIG - Displays vibrator ON/OFF conguration for when target reached.
BATTERY TYPE - Displays the battery type selection screen (only on SLIM wrenches).
4. To exit Settings menu and return to target torque or angle screen, press ENTER button while EXIT
menu selection is highlighted.
STD

21
TAWM SERIES
SETTING SLEEP TIME
This function will allow user to set interval wrench enters power-down state following last applied
torque or button press.
1. From Settings menu, use UP/DOWN buttons to highlight SLEEP TIME selection then press
ENTER button.
2. SLEEP TIME screen is displayed.
3. Use UP/DOWN buttons to select sleep interval.
Selectable Intervals: 2 MIN (factory default); 5 MIN; 10 MIN; 30 MIN; 1 HR; 2 HR; 8 HR
4. Press ENTER button to accept selection and exit to Settings menu.
STD SLIM
SETTING LCD CONTRAST
This function will allow user to set LCD contrast for optimal viewing.
1. From Settings menu, use UP/DOWN buttons to highlight LCD CONTRAST selection then press
ENTER button.
2. CONTRAST screen is displayed.
3. Use UP/DOWN buttons while viewing display to change contrast to desired level.
Selectable levels: 20 to 80 in increments of 5 (factory default = 40).
4. Press ENTER button to accept selection and exit to Settings menu.
STD SLIM
KEY BEEP SETUP
This function will allow user to enable or disable audio feedback when a button is pressed.
1. From Settings menu, use UP/DOWN buttons to highlight KEY BEEP selection then press ENTER
button.
2. KEY BEEP screen is displayed.
3. Use UP/DOWN buttons to highlight ENABLE (factory default) or DISABLE selection.
4. Press ENTER button to accept selection and exit to Settings menu.
STD SLIM
TARGET BEEP SETUP (ONLY ON SLIM WRENCHES)
This function will allow user to enable or disable audio feedback when target is reached.
1. From Settings menu, use UP/DOWN buttons to highlight TARGET BEEP selection then press
ENTER button.
2. TARGET BEEP screen is displayed.
3. Use UP/DOWN buttons to highlight ENABLE (factory default) or DISABLE selection.
4. Press ENTER button to accept selection and exit to Settings menu.
AUTO BACKLIGHT SETUP
This function will allow user to enable or disable backlight from turning on during torque or angle measurement.
1. From Settings menu, use UP/DOWN buttons to highlight AUTO BACKLIGHT selection then press
ENTER button.

23
TAWM SERIES
2. AUTO BACKLIGHT screen is displayed.
3. Use UP/DOWN buttons to highlight ENABLE (factory default) or DISABLE selection.
4. Press ENTER button to accept selection and exit to Settings menu.
STD SLIM
TOGGLE BACKLIGHT SETUP
This function will allow user to enable or disable backlight toggle function. If toggle mode is disabled,
BACKLIGHT button turns on backlight and it automatically turns off after ve seconds following any
last button press. If toggle mode is enabled, a BACKLIGHT button press will turn on backlight and it will
remain on until next BACKLIGHT button press.
1. From Settings menu, use UP/DOWN buttons to highlight TOGGLE BACKLGHT selection then press
ENTER button.
2. TOGGLE BACKLGHT screen is displayed.
3. Use UP/DOWN buttons to highlight ENABLE or DISABLE (factory default) selection.
4. Press ENTER button to accept selection and exit to Settings menu.
Note: Backlight will turn off when wrench powers down either by POWER button press or sleep time.
Note: If toggle backlight is enabled and backlight is on, backlight will remain on during and after
applying torque.
STD SLIM
VIBRATOR CONFIGURATION
This function will allow user to congure vibrator for On or Off when target is reached for preference
and/or battery power savings.
1. From Settings menu, use UP /DOWN buttons to highlight VIBRATOR CONFIG selection, then
press ENTER button.
2. VIBRATOR CONFIG screen is displayed.
3. Use UP /DOWN buttons to toggle ON or OFF selection.
4. Press ENTER button to accept selection and exit to Settings menu.
STD SLIM
BATTERY TYPE SELECTION (ONLY ON SLIM WRENCHES)
This function will allow user to congure the battery discharge thresholds for the type of battery used.
1. From Settings menu, use UP /DOWN buttons to highlight BATTERY TYPE selection then press
ENTER button.
2. BATTERY TYPE screen is displayed.
3. Use UP /DOWN buttons to select the type of battery being used.
4. Press ENTER button to accept selection and exit to Settings menu.
Note: Wrench is congured for Alkaline battery shipped from factory. If Alkaline battery is replaced
with rechargeable Nickel-Metal Hydride (NIMH) or lithium, battery type should be changed so battery
level icon and LOW battery warnings function optimally. Battery life (REPLACE) will not be impacted,
however 50% and Low will be optimized to show most accurate linear discharge time.

25
TAWM SERIES
Advanced conguration is accessed from CONFIGURE menu selection on main menu.
Note: If wrench has been locked (see Preset Lock and Job Mode), a password entry is required
to enter Congure menu.
1. From target torque or angle screen, press and hold ENTER button for 3 seconds.
2. Highlight CONFIGURE menu selection using UP/DOWN buttons.
3. Press ENTER button to display Congure menu.
Menu Selections:
EXIT - Exits Congure menu and returns to target torque or angle screen.
MODE SETUP - Displays wrench mode setup menu.
PRESET LOCK - Displays Preset lock menu.
DELETE PRESETS - Displays delete all presets menu.
JOB MODE - Displays Job mode menu.
CALIBRATION - Displays wrench calibration menu (password protected).
SET DATE/TIME - Displays clock date and time entry screens.
SET CAL INTRVAL - Displays calibration interval setup screen (requires clock date and time setup).
CAL COUNT DOWN - Displays calibration needed countdown setup screen (requires clock date and
time setup and calibration interval setup) (only on SLIM wrenches).
CHANGE PASSWD - Displays change password menu.
ASSET # - Displays user congurable 15-character string (only on SLIM wrenches).
4. To exit Congure menu and return to target torque or angle screen, press ENTER button while
EXIT menu selection is highlighted.
STD SLIM
Note: All user congurable settings are stored in non-volatile memory and are retained while
power is off.
MODE SETUP
Mode setup menu allows user congure target torque and angle minus and plus tolerances and enable/
disable Torque THEN Angle mode and Torque AND angle mode.
1. From Congure menu, press ENTER button while MODE SETUP selection is highlighted.
2. Mode Setup menu is displayed.
Menu Selections:
EXIT - Exits Mode setup menu and returns to Congure menu screen.
TQ-% SETUP - Displays target torque minus tolerance entry screen.
TQ+% SETUP - Displays target torque plus tolerance entry screen.
ANG-% SETUP - Displays target torque minus tolerance entry screen.
ANG+% SETUP - Displays target torque plus tolerance entry screen.
THEN DISABLED - Displays THEN Mode enable/disable screen.
AND DISABLED - Displays AND Mode enable/disable screen.
3. Use UP/DOWN buttons to highlight menu selections.
4. Press ENTER button while EXIT menu selection is highlighted to return to Congure menu.
STD SLIM
SETTING TARGET TOLERANCES
This function will allow user to set plus and minus tolerances for torque and angle targets.
Note: These tolerances are used for manual modes only. Preset tolerances are dened by Mini-
mum and Maximum values.
1. From Mode Setup menu, use UP/DOWN buttons to highlight tolerance selection to setup (TQ-%,
TQ+%, ANG-% ANG+%) then press ENTER button.
2. Tolerance screen is displayed.
3. Use UP/DOWN buttons to change tolerance value. Range is 0 to 10% ( factory default for minus
tolerance is 0% and 4% for plus tolerance).
4. Press ENTER button to accept selection and exit to Mode Setup menu.
STD SLIM
Note: Green progress lights turn on at target minus -% TOL.
Note: Red progress lights turn on above target plus +% TOL.
Note: Plus tolerance is added to minimum Preset value to dene initial maximum value when a
Preset is rst added.
ENABLE/DISABLE TORQUE THEN ANGLE MODE
This function will allow user to enable or disable Torque THEN Angle Mode.
1. From Mode Setup menu, use UP/DOWN buttons to highlight THEN DISABLED (factory default)
selection then press ENTER button.
2. TQ THEN ANGLE enable/disable screen is displayed.
3. Use UP/DOWN buttons to select ENABLE or DISABLE selection.
4. Press ENTER button to accept selection and exit to Mode Setup menu.
ADVANCED CONFIGURATION

27
TAWM SERIES
STD
SLIM
Note: Menu selection indicates current conguration (ENABLED or DISABLED).
TORQUE THEN ANGLE MODE
Torque THEN Angle mode is setup by rst setting a target torque and units then a target angle before
selecting Torque THEN Angle mode. In Torque THEN Angle mode, when applied torque reaches target
torque, wrench automatically switches to angle mode for angle measurement. Progress lights indicate
applied torque progress while torque is measured and angle when angle is measured. If torque is below
target torque when angle reaches target angle, green progress lights will not turn on and if angle exceeds
maximum angle, red progress lights turn on indicating a potential problem with fastener.
1. From target torque screen, use UP/DOWN buttons to set target torque and UNITS button to select
torque measurement units then press ENTER button.
2. Angle target screen is displayed. Use UP/DOWN buttons to set target angle then press ENTER button.
3. Torque THEN Angle mode screen is displayed.
4. Apply torque until target is reached then rotate wrench to target angle.
STD
SLIM
Note: UNITS button can be used to select torque units while on Torque THEN Angle screen.
Note: Torque cycle is not recorded in memory unless both torque and angle reach targets.
Note: Red progress lights turn on if torque exceeds 110% of wrench full scale or if angle exceeds
target + plus tolerance while in manual mode.
Note: Torque THEN Angle Presets are entered by pressing and holding Units button while on
Torque THEN Angle screen. MAXIMUM TORQUE defaults to full range plus 10%. Refer to “Adding
a Torque Preset” and “Adding an Angle Preset” in Basic section for parameter entry.
ENABLE/DISABLE TORQUE AND ANGLE MODE
This function will allow user to enable or disable Torque AND Mode.
1. From Mode Setup menu, use UP/DOWN buttons to highlight AND DISABLED (factory default)
selection then press ENTER button.
2. TQ AND ANGLE enable/disable screen is displayed.
3. Use UP/DOWN buttons to select ENABLE or DISABLE selection.
4. Press ENTER button to accept selection and exit to Mode Setup menu.
STD
SLIM
Note: Menu selection indicates current conguration (ENABLED or DISABLED).
TORQUE AND ANGLE MODE
Torque AND Angle mode is setup by rst setting a target torque and units then a target angle before selecting
Torque AND Angle mode. In Torque AND Angle mode, torque and angle are measured simultaneously.
Yellow progress lights track torque measurement. When both torque and angle reach their targets, green
progress lights turn on and torque and angle data record is stored. If either of measurements exceed their
upper tolerance, red progress lights turn on.

29
TAWM SERIES
1. From target torque screen, use UP/DOWN buttons to set target torque and UNITS button to select
torque measurement units then press ENTER button.
2. Angle target screen is displayed. Use UP/DOWN buttons to set target angle then press ENTER
button until Torque AND Angle mode screen is displayed.
3. Apply torque and rotate wrench until both targets are reached.
STD
SLIM
Note: UNITS button can be used to select torque units while on Torque AND Angle screen.
Note: Torque THEN Angle Presets are entered by pressing and holding Units button while on
Torque THEN Angle screen. Refer to “Adding a Torque Preset” and “Adding an Angle Preset” in
Basic section for parameter entry.
Note: Torque cycle is not recorded in memory unless both torque and angle reach targets.
Note: Red progress lights turn on if torque exceeds target + plus tolerance or if angle exceeds
target + plus tolerance while in manual mode.
Note: Red progress lights turn on if torque exceeds maximum torque or if angle exceeds maxi-
mum angle in Preset mode.
PRESET LOCK
Preset Lock function allows user to lock wrench so that only congured presets are accessible. No other
presets can be congured and manual target torque and angle modes are not accessible when locked.
Note: Password entry is required to enable Preset Lock. When locked, password entry is required
to re-enter Congure menu (Refer to Calibration Manual regarding Congure password).
1. From Congure menu, use UP/DOWN buttons to highlight PRESET LOCK selection then press
ENTER button.
2. Preset Lock enable/disable screen is displayed.
3. Use UP/DOWN buttons to select LOCK or UNLOCK selection.
4. Press ENTER button to accept selection and exit to Congure menu.
STD
SLIM
Note: If LOCK is selected without a Preset congured, following screen is displayed:
STD SLIM
Note: When Preset Lock is enabled, Clear Memory function is disabled and displays following
Locked message if attempted:
STD SLIM
Note: When Preset Lock is enabled, Clear Cycle count function is disabled and displays Locked
message if attempted.
PRESET UNLOCK
When Preset Lock is enabled, a password is required to access Congure menu. Refer to Calibration
Manual for Congure password.
1. From target torque or angle screen, press and hold ENTER button for 3 seconds.
2. Highlight CONFIGURE menu selection using UP/DOWN buttons.
3. Press ENTER button to display Password screen.
4. Follow password entry procedure found in Calibration manual.
STD

31
TAWM SERIES
SLIM
DELETE PRESETS
Delete Presets function allows user to delete all presets at once.
1. From Congure menu, use UP/DOWN buttons to highlight DELETE PRESETS selection then
press ENTER button.
2. Delete Presets conrmation screen is displayed.
3. Use UP/DOWN buttons to select YES or NO selection.
4. Press ENTER button to accept selection and exit to Congure menu.
STD SLIM
Note: If Delete Presets is selected without a Preset congured, following screen is displayed:
STD SLIM
JOB MODE
Job Mode function allows user to enable or disable wrench preset Job mode. When in Job mode,
wrench executes presets in order congured and automatically switches to next preset when batch
count reaches zero. When in Job mode wrench is locked and Preset lock icon is displayed.
Note: Password entry is required to enable Job Mode. When enabled, password entry is re-
quired to re-enter Congure menu (Refer to Calibration Manual for Congure password).
1. From Congure menu, use UP/DOWN buttons to highlight JOB MODE selection then press ENTER button.
2. Job Mode enable/disable screen is displayed.
3. Use UP/DOWN buttons to select ENABLE or DISABLE.
4. Press ENTER button to accept selection and exit to Congure menu.
STD
SLIM
Note: Text “JOB” is displayed between PSET number and batch count when enabled.
CALIBRATION
Calibration menu is password protected. Refer to Calibration Manual.
STD SLIM
SETTING DATE AND TIME
Set Date/Time function allows user to set real-time-clock date and time for time stamping data records,
recording last calibration date and notifying user of an expired calibration interval.
Note: When date and time is set for rst time, In-Service date is also set and is used for calculating
initial calibration interval (see “Setting Calibration Interval” in Advanced Conguration section).

33
TAWM SERIES
1. From Congure menu, use UP/DOWN buttons to highlight SET DATE/TIME selection then press
ENTER button.
2. SET DATE screen is displayed with year highlighted.
3. Use UP/DOWN buttons to set year then press ENTER button to highlight month.
4. Use UP/DOWN buttons to set month then press ENTER button to highlight day.
5. Use UP/DOWN buttons to set day then press ENTER button.
6. SET TIME screen is displayed with hour highlighted.
7. Use UP/DOWN buttons to set hour then press ENTER button to highlight minutes.
8. Use UP/DOWN buttons to set minutes then press ENTER button to highlight seconds.
9. Use UP/DOWN buttons to set seconds then press ENTER button.
10. Clock is set and Congure menu is displayed.
STD
SLIM
Note: Year selection will scroll up from 2013. Month selection will scroll from 1 to 12. Day selection will
scroll from 1 to 31.
Note: Hour selection will scroll through 0 to 23. Minute and Second selections will scroll through 0 to 59.
Note: If batteries are removed from wrench for longer than 20 minutes, clock will revert to default set-
tings and must be re-entered at power on.
SETTING CALIBRATION INTERVAL
This function will allow user to set calibration interval for when “CAL NEEDED” message will be displayed.
1. From Congure menu, use UP/DOWN buttons to highlight SET CAL INTRVAL selection then press
ENTER button.
2. CAL INTERVAL screen is displayed.
3. Use UP/DOWN buttons to change calibration interval.
Selectable Intervals: 12 MON (factory default); 6 MON; 3 MON; DISABLED
4. Press ENTER button to accept selection and exit to Congure menu.
STD SLIM
Note: Clock Date and Time must be set before calibration interval will function. If batteries are
removed from wrench for longer than 20 minutes, clock will revert to default settings and must
be re-entered at power on.
Note: Calibration interval is calculated from either IN-Service Date or last Calibration date (see
SHOW INFO menu) depending on which is more recent date. When clock Date is greater than
IN-Service or Last Calibration date, plus Cal Interval, “CAL NEEDED” message will be displayed
on power up and after a re-zero. Pressing ENTER button will continue to target menu. Applying
torque while “CAL NEEDED” message is displayed will immediately display torque or angle
measurement and return to target menu when released.
Note: As an alternative to calibration interval, a Calibration Cycle Counter is provided in Calibration
menu (Refer to Calibration Manual regarding Calibration menu). Each time a measurement cycle
reaches target torque, calibration cycle counter is incremented. When torque is recalibrated,
calibration counter is automatically reset to zero. User can disable calibration interval check and
use number of cycles since last calibration to decide when to recalibrate.
Note: If an invalid date is entered and Calibration interval is enabled, an unintended “CAL NEEDED”
message may be displayed. Either disable the calibration interval or enter a correct date.
SETTING CALIBRATION NEEDED COUNTDOWN (ONLY ON SLIM WRENCHES).
This function will allow user to set number of days when “CAL NEEDED” message will be displayed along
with days remaining before a wrench lock out occurs due to Cal interval expiring.
1. From Congure menu, use UP/DOWN buttons to highlight CAL COUNTDOWN selection then press
ENTER button.
2. CAL COUNTDOWN screen is displayed.
3. Use UP/DOWN buttons to change calibration countdown.
Range: 0 to 10 days.
4. Press ENTER button to accept selection and exit to Congure menu.

35
TAWM SERIES
Note: Clock Date and Time must be set and Cal interval enabled before calibration countdown
will function (see Setting Date and Time and Setting Calibration Interval).
Note: Calibration Countdown is number of days before wrench is locked out from use following
an expired Cal interval. Countdown number of days before lockout is displayed below “CAL
NEEDED” message:
Note: “CAL NEEDED” message will be displayed on power up and after a re-zero. Applying
torque while countdown is remaining, torque or angle is immediately displayed. Red LEDs and
buzzer turn on if Cal interval has expired. Pressing ENTER button after Cal interval has expired
will display Password Entry screen (Refer to TAWM Calibration manual).
Note: An entered Cal Countdown value of 0 days will disable calibration countdown and if Cal
interval is enabled, wrench does not lock when CAL NEEDED” message is displayed.
CHANGE PASSWORD
Change Password function allows user to change password to a new password. Default password is
required to initially change the password (Refer to Calibration Manual for Congure password).
1. From Congure menu, use UP/DOWN buttons to highlight CHANGE PASSWD selection then press
ENTER button.
2. Initial password entry screen is displayed.
3. Enter default password if changing for rst time, otherwise enter current user password using UP/
DOWN buttons to change each digit followed by ENTER button.
4. Change password entry screen is displayed.
5. Enter new password using UP/DOWN buttons to change each digit followed by ENTER button.
6. Conrm password entry screen is displayed.
7. Re-enter new password using UP/DOWN buttons to change each digit followed by ENTER button.
STD
SLIM
Note: Pressing POWER button at any time aborts password change sequence.
Note: If an invalid password is entered during the conrmation step, Invalid Password Match
screen is displayed and new password is not accepted.
STD SLIM
ASSET # (ONLY ON SLIM WRENCHES)
This function displays a USB congurable 15-character string. When congured, Asset # string is down-
load data le name and is included in rst row of.csv data le.
1. From Congure menu, use UP/DOWN buttons to highlight ASSET # selection then press ENTER
button.
2. ASSET # screen is displayed.
3. Use Windows program to congure Asset # via USB (Contact factory for software).
4. Press ENTER button to accept selection and exit to Congure menu.
Note: While Asset # is being displayed, number can be congured via USB.
Note: Available characters for Asset #: 0-9, A-Z, space # _ % ‘ ( ) + , - .
Note: If Asset # is blank, wrench serial number is used for .csv le name and included in data.

37
TAWM SERIES
Note: If any of following issues persist, return wrench to a SNA Europe/Bahco repair center.
TROUBLESHOOTING
ISSUE POSSIBLE CAUSE RESOLUTION
Wrench does not turn on when
POWER button pressed.
Dead/No batteries Replace batteries
Software glitch Cycle power using end-cap
Torque reading out of spec.
Calibration required Recalibrate
Incorrect head length entered Enter correct offset head length
Wrench did not retain settings
while batteries were removed.
Batteries removed before setting were
saved in non-volatile memory.
Clear data, re-enter settings and press
and hold POWER button to power down
wrench before removing batteries.
Low battery Press ENTER button to continue using
wrench and replace batteries soon.
Dead battery Press POWER button to turn off wrench
and replace batteries.
Torque applied while zeroing Remove torque and re-zero
Wrench over torqued Recalibrate
Wrench improperly calibrated Recalibrate
Torque sensor failure Return to Factory
Wrench moving during zeroing Place wrench on stable surface
Gyro unstable Return to Factory
ENTER button pressed during angle
zeroing (Aborted zeroing to access
menus)
Press POWER button to re-zero
Over 125% of full scale torque applied Cycle power using POWER button and
recalibrate
Wrench rotated too fast during angle
measurement Press POWER button to re-zero
Calibration interval exceeded or invalid
date entered with calibration interval
enabled
Calibrate wrench or press ENTER to
continue. Disable calibration interval if
not required.
Memory error Clear data memory
Torque uncalibrated Calibrate torque
Angle uncalibrated Calibrate angle
LOW BATTERY
REPLACE BATTERY
TORQUE ZERO
ERROR
ANGLE ZERO
ERROR
ANGLE
ERROR
CALL
NEEDED
torque ucal
angle ucal
OVERTORQUE
ANGLE ZEROING
--
SET STILL
USE OF ADAPTORS, EXTENSIONS AND
UNIVERSALS
Anytime an adaptor, extension or universal is used
with a torque wrench in such a way that fastener
distance is different than torque wrench square drive
distance at calibration, an adjustment to head length
is required to get a proper fastener torque reading.
When using wobble extension or a universal, do
not exceed more than 15 degrees of offset from
perpendicular drive. Do not use a long extension
with ex-drive at full ex.
CALIBRATION
Contact your Bahco sales representative for
calibration services or refer to Calibration Manual.
CERTIFICATION
This torque-angle wrench was calibrated at factory
using angular displacement and torque measure-
ment instruments that are traceable to National
Institute of Standards and Technology (N.I.S.T.).
Torque parameters comply with ISO 6789:2003 and
ASME B107:300-2010 (B107.29). Note: no U.S. or
International Standards exist for angle wrenches.
Angle calibration was performed on an angle gage
with ±1 degree accuracy at each 45 degree in-
dexing point throughout 180 degrees of rotation.
MAINTENANCE / SERVICE
Clean wrench by wiping with a damp cloth. DO
NOT use solvents, thinners or carburetor cleaners.
DO NOT immerse in anything.
Service and repairs are to be done by SNA
Europe/Bahco Service Center only. Contact your
Bahco Torque Products representative.
Ratchet head repair kits can be ordered from a
Bahco Representative.
NOTES:
- If display shows persistent “TORQUE ZERO
ERROR” at power on, wrench is damaged
and must be returned for repair.
- If display shows “ANGLE ERROR” in angle
mode, fastener rotation speed has exceeded
capacity of wrench.
- Wrench must be held still during angle
zeroing. Motion is indicated by alternating
dashes “- -” on display
- Remove battery when stored for extended
periods (Note: clock will revert to default set-
tings).
BATTERY REPLACEMENT
Note: When replacing batteries, real-time-clock
will maintain date and time for 20 minutes.
Note: Turn end cap counter-clockwise to unscrew.
Batteries should be installed in carrier prior to car-
rier installation into wrench. Battery negative con-
tacts should be oriented with carrier springs.
Replace SLIM models with one single “AA” cell only
Replace STD models with three “AA” cells only.
Note: When Replace Battery screen is displayed
wrench will no longer operate until batteries are
replaced. Only POWER button functions which
immediately turns off wrench.
MEMORY INDICATORS
IMPORTANT INFORMATION
IMPORTANT!
Calibration events are recorded in wrench
memory which provides evidence to void factory
certication.
MEMORY FULL
1500 torque or angle records stored in memory.
New records will not be recorded until memory is cleared
(on STD wrenches only).
New data will replace oldest record until memory is
cleared (on SLIM wrenches only)
DATA IN MEMORY
Less than 1500 torque and angle records
stored in memory.
MEMORY ERROR
Memory read or write error.
Unscrew end cap. Insert new cells
Positive (+) end into handle rst
Unscrew end cap. Insert new cell
Negative (-) end Into end cap
100% BATTERY LEVEL
50% BATTERY LEVEL
LOW BATTERY
REPLACE BATTERY
LOW BATTERY
REPLACE BATTERY

TAWM SERIES
(ENG) EC DECLARATION OF CONFORMITY
(FRA) DÉCLARATION DE CONFORMITÉ CE
(ESP) DECLARACIÓN DE CONFORMIDAD DE LA CE
(POR) DECLARAÇÃO DE CONFORMIDADE EC
(ITA) DICHIARAZIONE DI CONFORMITA’ CE
(GER) EG-KONFORMITÄTSERKLÄRUNG
(NED) EG- VERKLARING VAN OVEREENSTEMMING
(POL) EC DEKLARACJA ZGODNOŚCI
(SWE) CE DEKLARATION
(DEN) EF-VERENSSTEMMELSESERKLÆRING
(NOR) ECSAMSVERKLARING
(FIN) EY-VAATIMUSTENMUKAISUUSVAKUUTUS
(RUS) Декларация о соответствии EC
(TUR) CE STANDARDİZASYON BEYANI
(CZE) PROHLÁŠENÍ O SHODĚ
(SVK) PREHLÁSENIE O ZHODE
(GRE) ΔΗΛΩΣΗ ΣΥΜΜΟΡΦΩΣΗΣ ΜΕ ΕΕ
(ENG) Herebydeclaresthat:/Thedevice:
(FRA) Déclareparlaprésenteque:/L´appareil:
(ESP) Declaroque:/Elaparato:
(POR) Vimosporestemeiodeclarar:/Oaparéelo:
(ITA) Conlapresentedichiaroche:/Dispositivo:
(GER) Hiermitwirderklärt,dass:/DiefolgendenErzeugnisse:
(NED) Hierbijverklaartdat:/Hetapperaat:
(POL) Niniejszymoświadcza,że:/Urządzenia:
(SWE) Härmeddeklarerasatt:/Enheten:
(DEN) Erklærerhervedat:/enheten:
(NOR) Erklærerhervedat:/enheten:
(FIN) Vakuutammetäten:/Ettätuote:
(RUS) Настоящимзаявляем,что:/Устройство:
(TUR) Beyanederizki:/Cihaz:
(CZE) Nížeprohlašujeme,že:/výrobek:
(SVK) Týmtoprehlasujeme,že:/Výrobok:
(GRE) Δηλώνειότι:/Ησυσκευή:
(ENG) Wasmanufacturedinconformitywiththeprovisionsinthe:
(FRA) Aétéfabriquéenconformitéaveclesdispositionsdes:
(ESP) Estáfabricadasegúnlasdisposicionesde:
(POR) Foifabricadoemconformidadecomospressupostos:
(ITA) Prodottoinconformitàconledisposizioni:
(GER) InÜbereinstimmungmitdenBestimmungender:
(NED) Isvervaardigdinovereenstemmingmetdebepalingeninde:
(POL) Zostałwyprodukowanyzgodniezprzepisami:
(SWE) Produceratsenligtbestämmelsernaiföljandedirektiv:
(DEN) Produsertisamsvarmedbestemmelsenei:
(NOR) Produsertisamsvarmedbestemmelsenei:
(FIN) Onvalmistettunoudattaensäännöksiä:
(RUS) Былопроизведеновсоответствиисположениями:
(TUR) AşağıdakiStandartlarauygunüretilmiştir:
(CZE) Bylvyrobenveshoděspředpisy:
(SVK) Bolvyrobenývzhodespredpismi:
(GRE)Κατασκευάστηκεσύμφωναμετιςδιατάξειςτου:
(ENG)Type(s)
(FRA)Type(s)
(ESP)Tipo(s)
(POR)Tipo
(ITA)Tipo
(GER)Type(s)
(NED)Typen
(POL)Typ
(SWE)Typ
(DEN)Typ
(NOR)Typ
(FIN)Tyyppi
(RUS)Тип
(TUR)Tip
(CZE)Typ
(SVK)Typ
(GRE)Τύπος:
TAWM912M
TAWM930M
TAWM9135
TAWM14340
TAWM24800
TAW1412M
TAW1430M
TAW38135
TAW12340
TAW34800
(ENG)Personauthorizedtocompilethetechnicalle(TCF):
(FRA)Personneautoriséeàconstituerledossiertechnique:
(SPA)Personafacultadaparaelaborarelexpedientetécnico:
(POR)Pessoaautorizadaparaelaborarodossiertécnico:
(ITA)Personaautorizzataacompilarelapraticatecnica
(GER)Bevollmächtigte(r)zumZusammenstellentechnischerUnterlagen:
(NLD)Persoondieisgemachtigdhettechnischdossiersamentestellen
(POL)Osobaodpowiedzialnazazestawianieplikutechnicznego
(SWE)Personsomärbehörigattsammanställadentekniskadokumentationen:
(DAN)Personbemyndigettilatudarbejdetekniskebeskrivelser:
(NOR)Autorisertpersonforutarbeidelseavdentekniskelen:
(FIN)Henkilöonvaltuutettukokoamaanteknisentiedoston
(TUR)Teknikdosyayıdüzenlemeyeyetkilikişi:
(RUS)Лицо,уполномоченноенасоставлениетехническойдокументации:
(CZE)Autorizovanáosobaprosestavenítechnickéhospisu:
(SLO)Osobazodpovednázavypracovanietechnickejdokumentácie:
(GRE)Άτομοεξουσιοδοτημένονακαταρτίσειτοντεχνικόφάκελο
Sergio
Calvo
Antigua ctra. Altube Km 5,5 - 01196 Arangiz, SPAIN
(ENG)Year
(FRA)Année
(ESP)Año
(POR)Ano
(ITA)Anno
(GER)Baujahr
(NED)Jaar
(POL)Rok
(SWE)År
(DEN)År
(NOR)År
(FIN)Vuosi
(RUS)Год
(TUR)Sene
(CZE)Rok
(SVK)Rok
(GRE)Χρόνος:
2018
2018/11/5
SNA EUROPE – 16 Allé Rosa Luxemburg, Eragny-sur-Oise, 95610 Cergy Pontoise Cedex, France – Phone: +33 1 39099868 – Fax : +33 1 39099881
2004/108/EC
EN 61326-1:2006, EN 55011:2006, EN 61000-4-2, EN 61000-4-3, EN 61000-4-8
(ENG)Product
(FRA)Produit
(ESP)Producto
(POR)Produto
(ITA)Prodotto
(GER)Produkt
(NED)Product
(POL)Produkt
(SWE)Produkten
(DEN)Produktet
(NOR)Produktet
(FIN)Tuotteen
(RUS)Изделие
(TUR)Ürün
(CZE)Výrobek
(SVK)Výrobok
(GRE)Προιόν:
Electronic Torque and angle Wrench
ClédynamométriqueCoupleetAngle
Llavedinamométricadeparyángulo
Chavedinamométricatorçãoeângulo
Chiavedinamometricacoppia/angolo
Drehwinkel-Drehmomentschlüssel
Momentsleutelmethoekmeting
Kluczdynamometrycznykątowy
ElektroniskMomentnyckel
Elektroniskmomentnøgle
Momentnøkkel,momentoggrader
Momenttiavain
ElektronikAçılıTorkAnahtarı
Elektronickýmomentovýklíčsúhlovýmměřením
Elektronickémomentovéuhlovékľúče
Ηλεκτρονικόκλειδίροπήςκαιγωνίας
Электронныйдинамометрическийключсфункцией
предустановкиуглазатягивания
Antigua ctra. Altube Km 5,5
01196 Arangiz, SPAIN
This manual suits for next models
10
Table of contents
Other Bahco Power Tools manuals
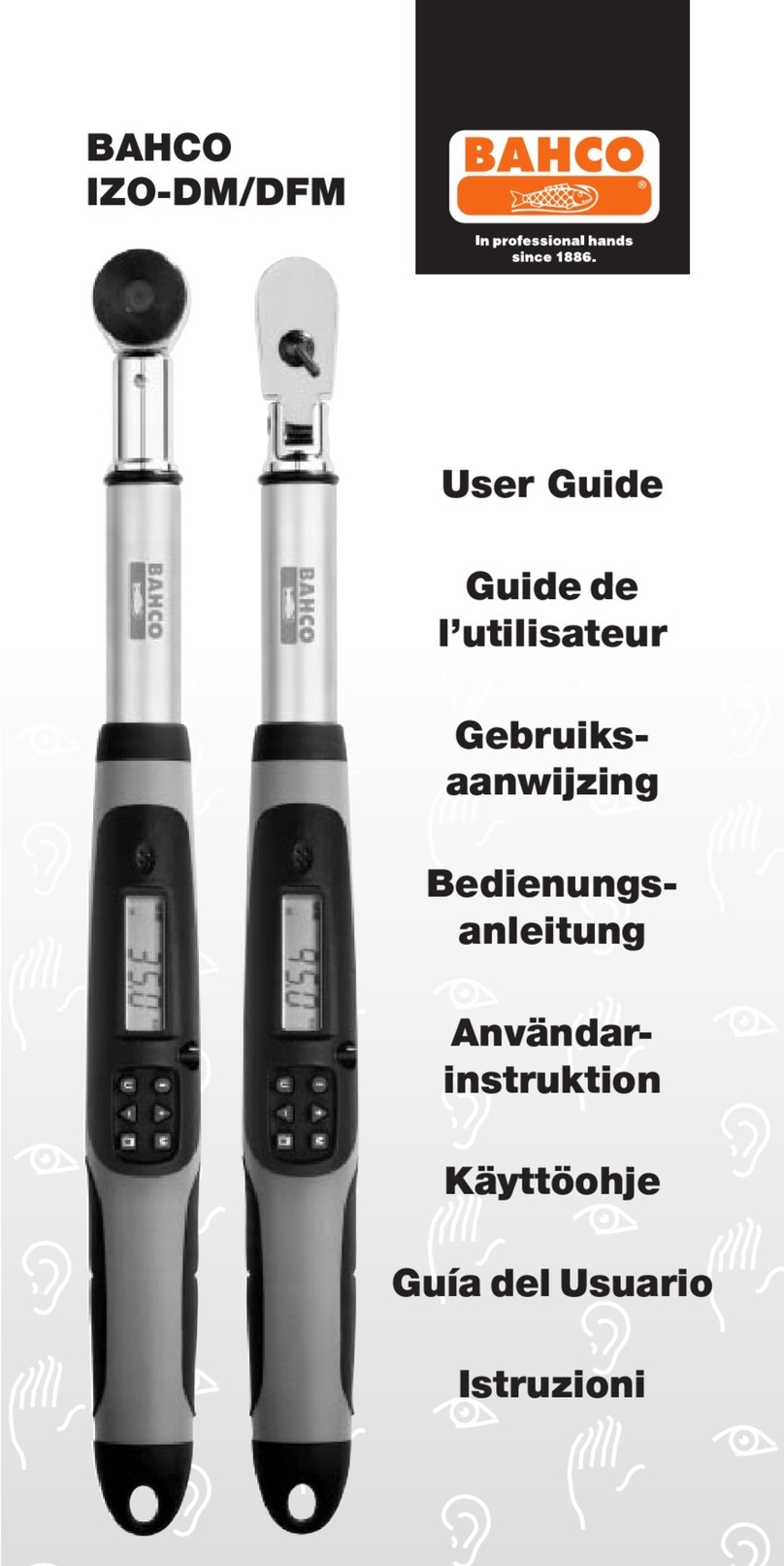
Bahco
Bahco IZO-DM User manual
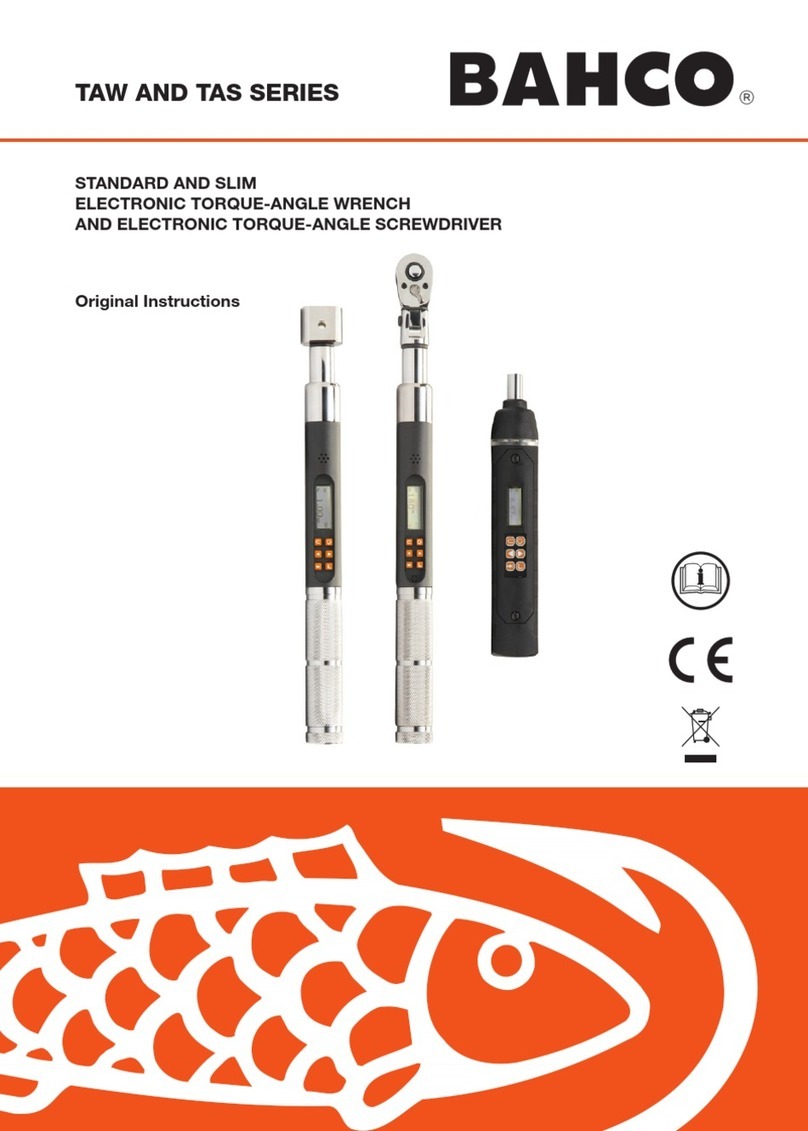
Bahco
Bahco TAW Series User manual
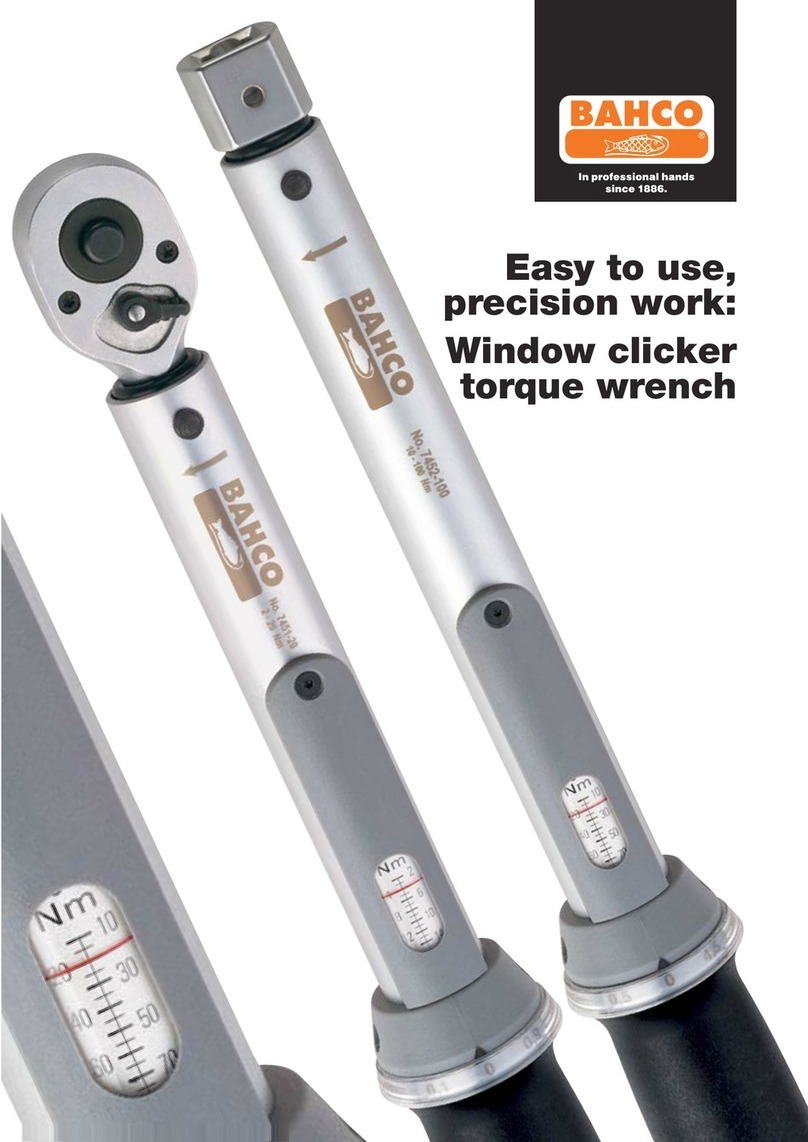
Bahco
Bahco Torque Wrench User manual
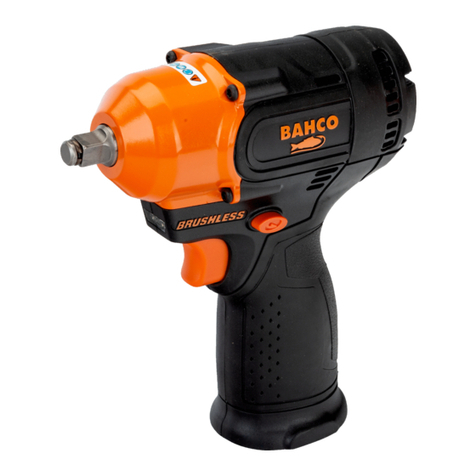
Bahco
Bahco BCL32IW1 User manual
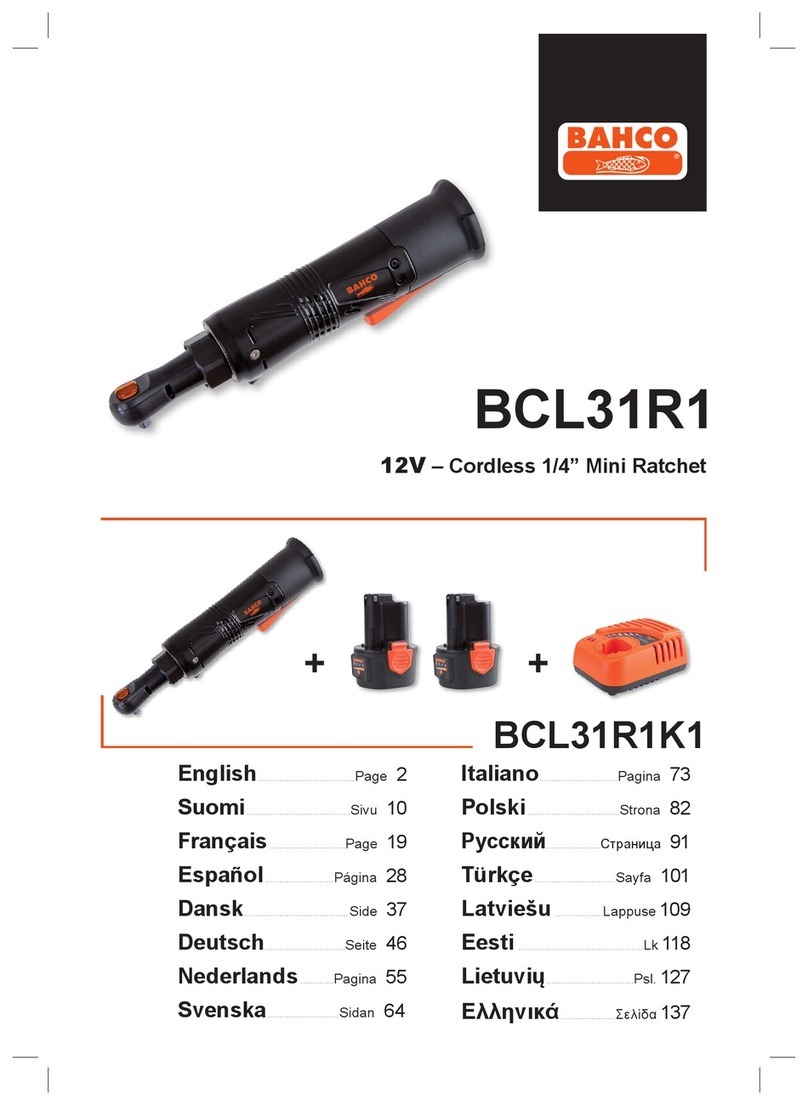
Bahco
Bahco BCL31R1 User manual
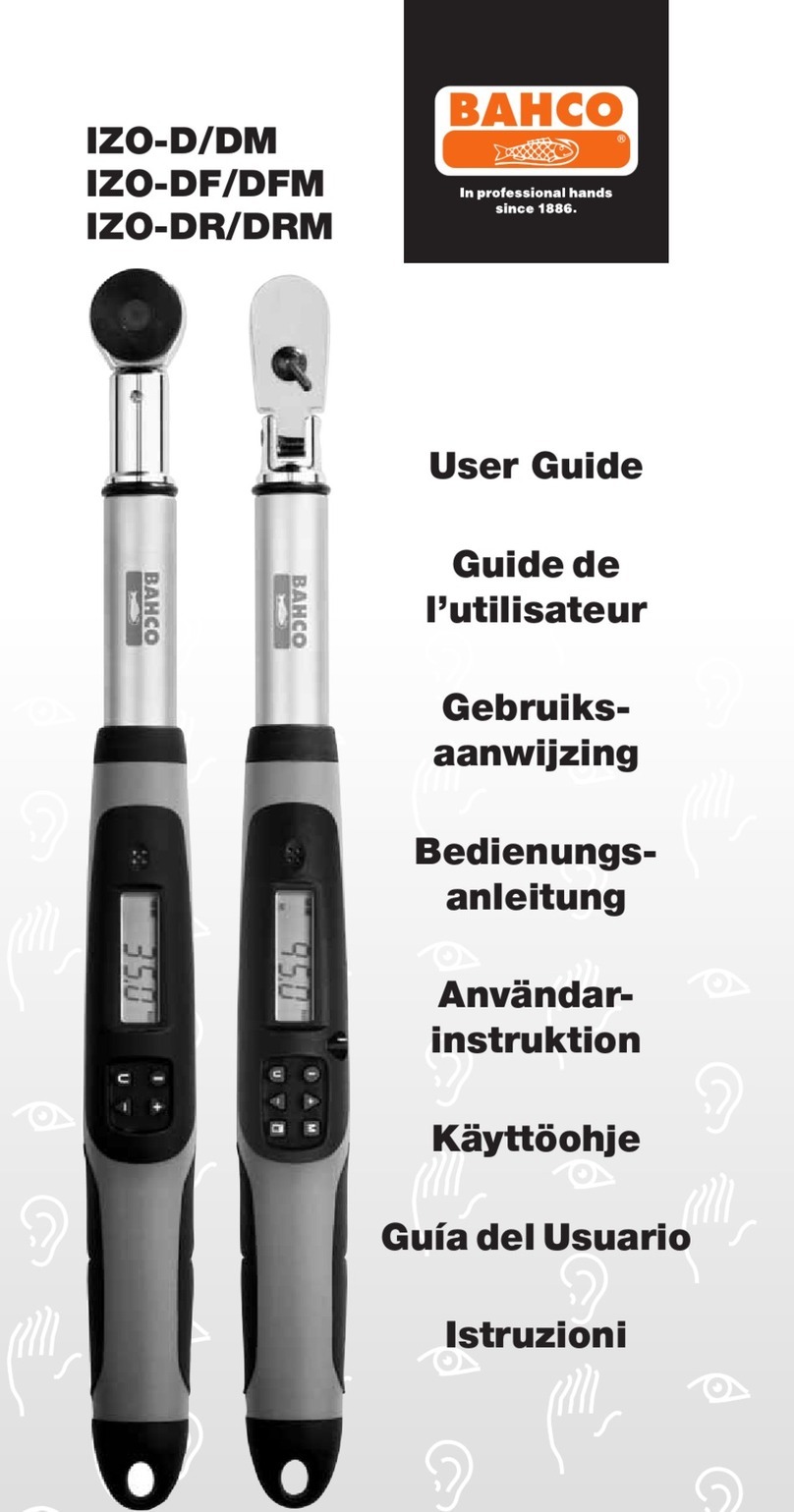
Bahco
Bahco IZO-D User manual
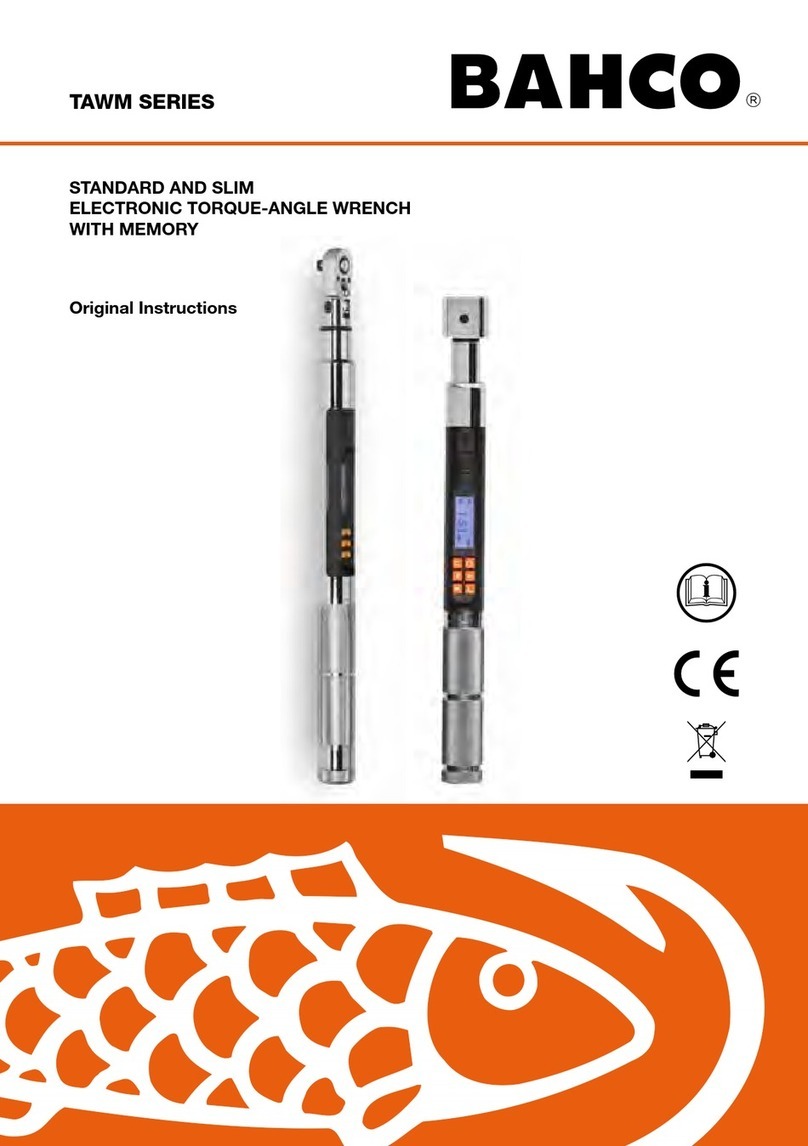
Bahco
Bahco TAWM1412M User manual
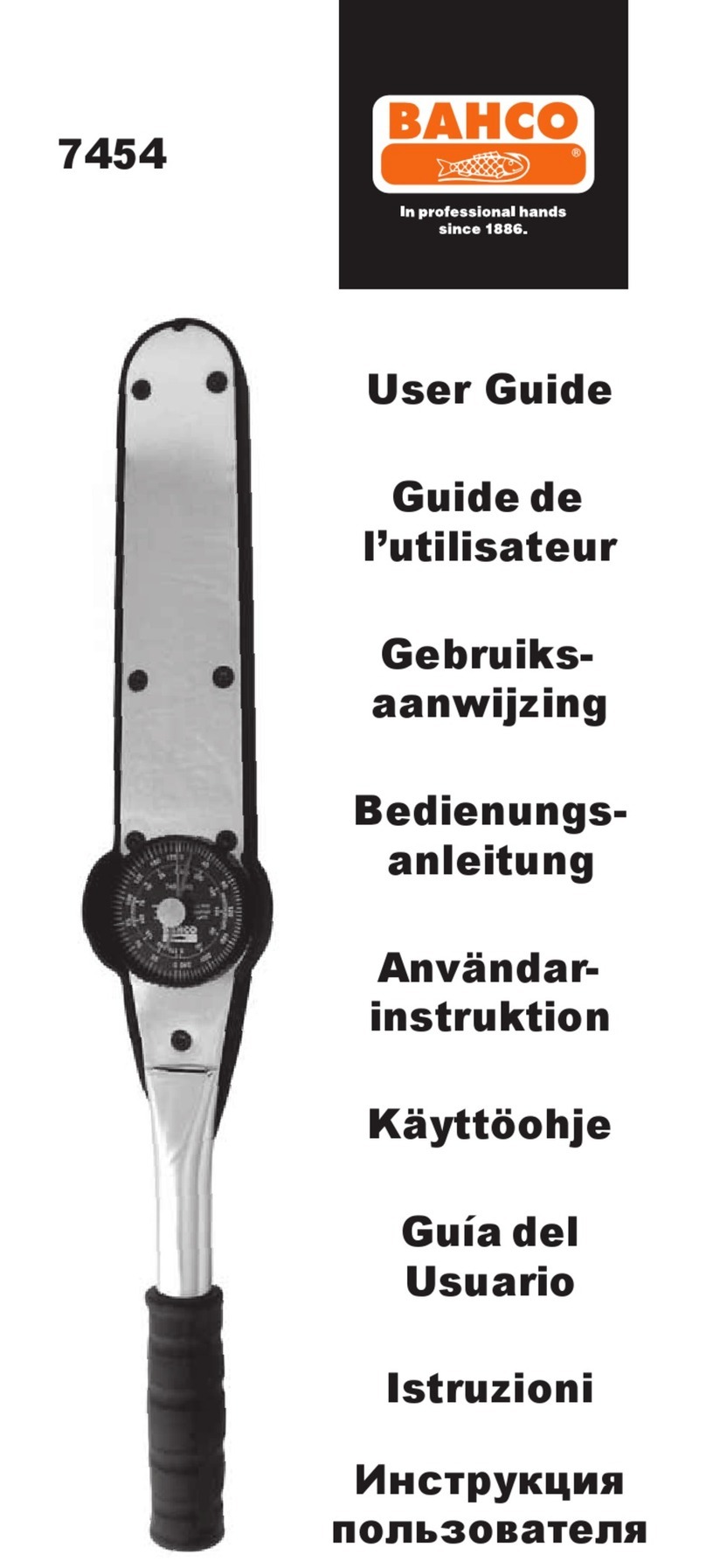
Bahco
Bahco 7454 User manual
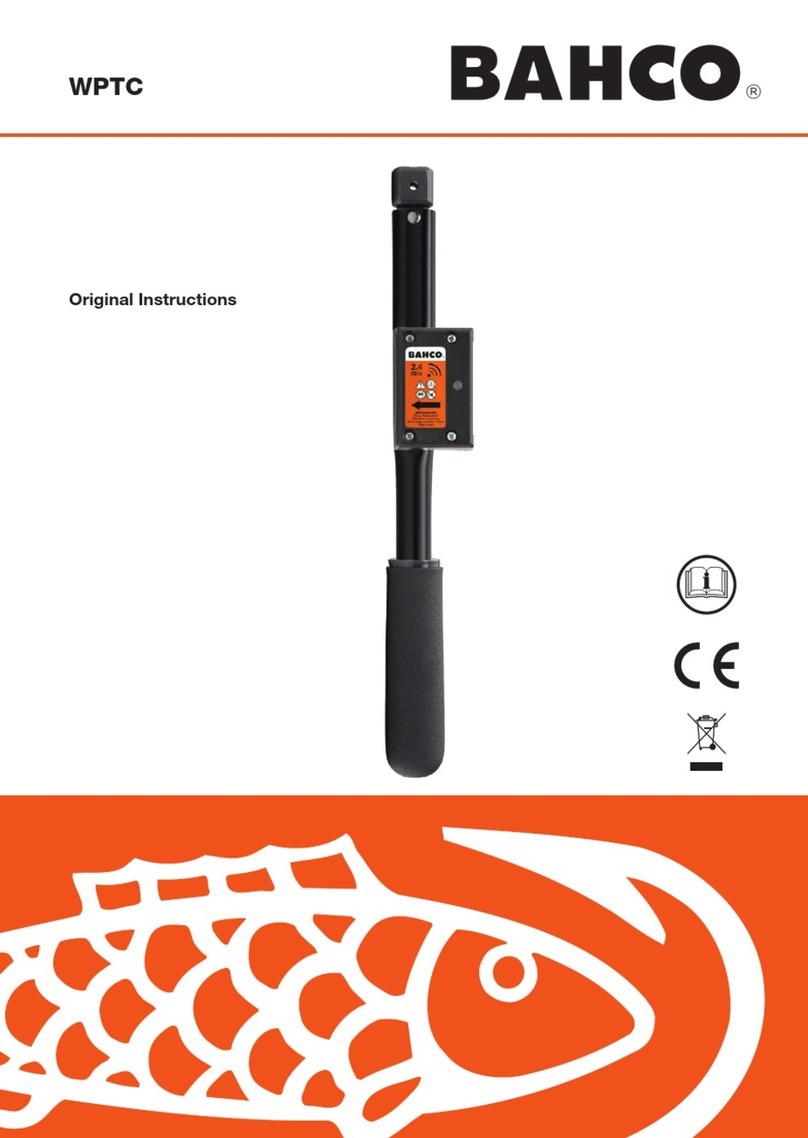
Bahco
Bahco WPTC Series User manual
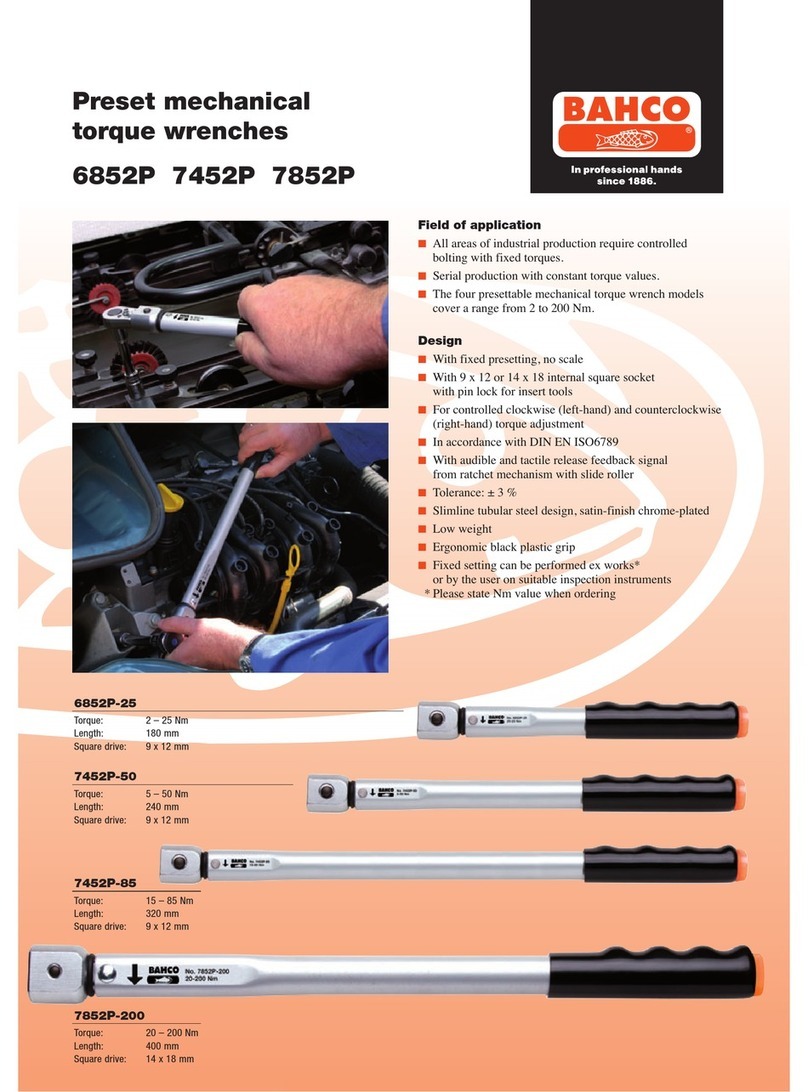
Bahco
Bahco 6852P User manual