Basler BE1-DFPR User manual

+05647%6+10/#07#.
(14
&+564+$76+10(''&'4
2416'%6+104'.#;
$'&(24
7PKV4GXKUKQP4#PF5WDUGSWGPV
2WD KECVKQP
4GXKUKQP #

i
W A R N I N G !
To avoid personal injury or equipment damage, only
qualified personnel should perform the procedures
presented in this manual.
+0641&7%6+10
This manual provides information concerning the operation and
installation of the BE1-DFPR, Distribution Feeder Protection Relay,
Unit Revision R and subsequent. BE1-DFPR Relays, Unit Revision Q
and previous require Instruction Manual 9 2315 00 990. To
accomplish these goals, the following information is provided.
Specifications
Functional description
Mounting information
Setting procedure/example.

ii
CONFIDENTIAL INFORMATION
OF BASLER ELECTRIC COMPANY, HIGHLAND, IL. IT IS LOANED FOR
CONFIDENTIAL USE, SUBJECT TO RETURN ON REQUEST, AND WITH THE
MUTUAL UNDERSTANDING THAT IT WILL NOT BE USED IN ANY MANNER
DETRIMENTAL TO THE INTEREST OF BASLER ELECTRIC COMPANY.
First Printing: December 1995
Printed in USA
© 1995, 1996, 1997 Basler Electric Co., Highland, IL 62249
September 1997
It is not the intention of this manual to cover all details and variations
in equipment, nor does this manual provide data for every possible
contingency regarding installation or operation. The availability and
design of all features and options are subject to modification without
notice. Should further information be required, contact Basler
Electric Company, Highland, Illinois.
BASLER ELECTRIC, BOX 269 HIGHLAND, IL 62249 USA
PHONE 618-654-2341 FAX 618-654-2351

iii
$$#
SECTION 1 GENERAL INFORMATION 1-1
Description ........................................ 1-1
Functions ......................................... 1-1
Protection ..................................... 1-1
Control ........................................ 1-1
Data Processing ................................ 1-1
Communication ................................. 1-1
Set-up and Test Provisions ........................ 1-1
Features .......................................... 1-2
Protection Features .............................. 1-2
Control Features ................................ 1-2
Data Processing Features ......................... 1-2
Communication Features .......................... 1-2
Set-up and Test Provisions Features ................. 1-3
Application ........................................ 1-5
Improving Protection Schemes ..................... 1-5
Implementing Adaptive Schemes ................... 1-5
Providing Maintenance Information .................. 1-5
Specifications ...................................... 1-6
General Specifications .............................. 1-11
Standard Accessories .............................. 1-13
Model and Style Number Description ................... 1-13
General ...................................... 1-13
Sample Style Number ........................... 1-13
Style Number Identification Chart .................. 1-14
Time Overcurrent Characteristic Curves ............. 1-15
SECTION 2 CONTROLS AND INDICATORS 2-2
Location Of Controls And Indicators .................... 2-1
Control module ..................................... 2-3
Contact Sense Module ............................... 2-4
Magnetics Module .................................. 2-5
SECTION 3 FUNCTIONAL DESCRIPTION 3-1
General .......................................... 3-1
Block Diagram Analysis .............................. 3-1
General ....................................... 3-1
Current Inputs .................................. 3-1
Voltage Inputs .................................. 3-1
Trip Outputs .................................... 3-1
Close Outputs .................................. 3-3
Control Inputs .................................. 3-3
User Programmable Inputs ........................ 3-3
Control Outputs ................................. 3-4
Target Outputs .................................. 3-4
Alarm Outputs .................................. 3-5
Trip Circuit Sense ............................... 3-5
Control Power .................................. 3-5
Communications ................................ 3-5

iv
%106'065 - Continued
SECTION 3 FUNCTIONAL DESCRIPTION (continued)
Modes of Operation .................................3-6
Settings Mode ..................................3-6
Status Mode ....................................3-8
Auxiliary Settings ...................................3-8
Auxiliary Setting 1 (CLP) ..........................3-8
Auxiliary Setting 2 (EP) 3, And 4 ....................3-9
Overcurrent Protection ...............................3-9
Sensing Configurations ...........................3-9
Time Overcurrent (51, 51N) ........................3-9
Instantaneous Overcurrent (50, 50N) .................3-9
Fixed Time Overcurrent (50T, 50TN) .................3-9
Frequency Tripping and Restoration ....................3-10
Undervoltage Tripping ...............................3-10
Tripping Logic .....................................3-10
Automatic Reclosing ................................3-11
Zone Sequence Coordination .........................3-12
Contact Sensing Inputs ..............................3-12
Reclose Initiate (RI) .............................3-12
Reclose Disable (RDS) ...........................3-13
Reclose Enable (REN) ...........................3-13
Drive To Lockout (DTL) ..........................3-13
Reclose Logic .....................................3-13
Control Functions ..................................3-13
Supervisory Trip/Supervisory Close (Trip/Close) .......3-13
Block Load Tap Changer (BLTC) ...................3-13
System Diagnostics and Alarm Outputs .................3-14
Relay Trouble ..................................3-14
Target Repeat Contacts ..........................3-14
Breaker Fail Alarm ..............................3-14
Lockout Alarm .................................3-14
Programmable Alarms ...........................3-14
Instrumentation ....................................3-15
Real Time Values ...............................3-15
Demand Values ................................3-15
Status Conditions ...............................3-15
Data Collection and Storage .......................3-15
Fault Data .....................................3-15
Communications ...................................3-16
General .......................................3-16
RS 232-C Format ...............................3-17
Serial Port Connections and Configurations ...........3-17
Serial Communication ...........................3-19
Starting Communication ..........................3-19
Downloading And Uploading Settings ...............3-19
Capturing Data To A File .........................3-22
SECTION 4 INSTALLATION 4-1
General ...........................................4-1
Operating Precautions ...............................4-1

v
$$# - Continued
SECTION 4 INSTALLATION (continued)
Dielectric Test ..................................... 4-1
Mounting ......................................... 4-1
Outline Dimensions (Rack Mounting) .................... 4-2
Outline Dimensions (Panel Mounting) ................... 4-3
Connections ....................................... 4-4
DC Control Connections (Typical) ...................... 4-4
Connection Diagram ................................ 4-5
BE1-DFPR Rear View ............................... 4-6
Communications Interface ............................ 4-7
RS-232 Connection Diagram For IBM Type Computers ..... 4-8
RS-232 Interconnection Diagram For PRT ............... 4-9
RS-232 Interconnection Diagram For RFL 9660 Switch ..... 4-9
SECTION 5 TESTING 5-1
General .......................................... 5-1
Testing ........................................... 5-1
Operational Test Procedure ........................... 5-1
Preliminary Setup Procedure ....................... 5-1
Entering Time and Date Settings .................... 5-1
BE1-DFPR Test Simulator, Front View ............... 5-2
BE1-DFPR Test Simulator, Rear View ............... 5-3
BE1-DFPR Test Simulator, Schematic Diagram ........ 5-4
Test Setup Diagram .............................. 5-6
Entering Settings ................................ 5-7
Pickup Verification ............................... 5-7
Timing Verification .............................. 5-11
Breaker Duty Timers ............................ 5-14
Control Inputs ................................. 5-15
Outputs ...................................... 5-17
Self Test ......................................... 5-19
Trip Test ......................................... 5-21
Loading Factory Default Settings ...................... 5-22
Normal, AUX1, AUX2, AUX3, And AUX4 Settings ..... 5-22
Installation Settings ............................. 5-22
Other Parameters .............................. 5-23
Load Default Settings ........................... 5-23
Resetting Demand Values ........................... 5-24
SECTION 6 MAINTENANCE 6-1
General .......................................... 6-1
In-House Repair .................................... 6-1
Storage .......................................... 6-1
SECTION 7 MANUAL CHANGE INFORMATION 7-1

1-1
SECTION 1
GENERAL INFORMATION
DESCRIPTION
BE1-DFPR Distribution Feeder Protection Relays are microprocessor controlled devices with
communications that provide complete real time protection, monitoring, control, and instrumentation for
distribution circuits. In summary, it is an integrated feeder supervision system. DFPR relay communication
provides for collection of real time operational data on both protected distribution circuits and controlled
circuit breakers. Communication also provides fault data and distribution circuit status to a local or remote
location, and allows the user to change the settings or select relay predefined conditional settings to meet
existing operating system conditions as they occur.
FUNCTIONS
DFPR relay multiple functions provide protection, control, data processing, communication, set-up
provisions, and test provisions. These functions are expanded and listed in the following paragraphs.
Protection
Three-phase and neutral overcurrent.
Breaker failure.
Undervoltage and Overvoltage for each phase.
Frequency tripping/restoration.
Control
Multiple shot reclosing (4-shot).
Reclosing may be controlled with external inputs.
Accepts breaker, trip and close inputs.
Protection may be adapted to system conditions.
Data Processing
Measures watts, var, voltamperes, power factor, frequency, volts, or amperes.
Calculates present and stores minimum and maximum demand values.
Measures energy accumulation in watt hours and var hours.
Accumulates data on breaker duty.
Stores fault/event reports.
Output contacts provide status information for SCADA.
Communications
Menu driven operation.
Front and rear panel RS-232 ports.
Uses terminal or PC with off-the-shelf software.
Optional RS-485 rear port supporting special application protocols.
Set-up and Test Provisions
Standard connection/test plugs for testing in the case.
Test module for control inputs (option).
Test unit is available to simplify testing.
Built-in self-checking capabilities.

BE1-DFPR General Information
1-2
Built-in breaker trip circuit monitor.
FEATURES
Each DFPR relay function has many different features. These features are also listed in the following
paragraphs and elaborate on the expanded functions.
Protection Features
Programmable integrating reset characteristics available for 51 functions.
Current and voltage sensing elements attenuate offsets and harmonics.
Different time overcurrent curves may be selected for phase and neutral.
Instantaneous overcurrent elements are provided for phase and neutral.
Fixed time overcurrent elements are provided for phase and neutral.
Tripping elements and the response of the reclosing section may be set for normal, AUX 1 (cold
load), AUX 2 (emergency), AUX 3 and AUX 4 settings by control inputs.
Inadditiontothemaintrippingoutputs,anindependenttripoutputmaybeprogrammedtooperate
on any of the protective functions.
Control inputs are provided to block all fixed time overcurrent elements and/or the neutral fixed
time and neutral time overcurrent elements.
The breaker failure element may be initiated by any protective tripping function or a supervisory
trip.
Abreakerfailalarm contact isprovidedtoindicatebreakerproblems that occurbeforethebreaker
fail function is actually caused to operate.
Zone sequence coordination provided.
Control Features
The reclosing function includes two programmable close outputs, inputs for initiate, drive-to-
lockout, and enabling or disabling reclosing.
The reclosing section of the relay is deactivated to prevent pumping when the breaker is tripped
or closed through one of the control inputs.
An output is provided to block the load tap changer on the substation transformer or voltage
regulator during a fault clearing or restoration process.
Overcurrent protective functions may be adapted through BT1 and BT2 control inputs.
Programmable inputs available for control features.
Data Processing Features
Data is formatted to display information in logical groups on computer or terminal.
Demand values are calculated for phase currents, watts, var, and voltamperes for intervals from
one to sixty minutes.
Energy accumulation in watt hours, var hours, and the number of hours since last reset are
calculated and stored.
Data stored on breaker duty includes number of operations and the sum of the I2or I values
interrupted.
Fault/event data is stored for up to 40 breaker operations.
Parameters being measured and/or stored may be displayed on the front panel.
Status outputs are provided for targets and reclose functions.
Battery backed-up clock provides date and time for reports.
Programmable alarm outputs available for alarm functions.
Communications Features
Front RS-232 port for observing menus and groups of data or set-up parameters via a portable

BE1-DFPR General Information
1-3
computer terminal.
Rear RS-232 port for connection to a communications link.
Communications provides access to set-up parameters, real time data, and stored information.
Settings upload and download.
Set-up and Test Provision Features
Access to the connection/test plugs is achieved by removing the left section of the front panel.
The optional test module provides the means to disconnect control inputs and apply test signals
through the test points.
Front panel display for reading data and setting parameters.
Menu driven procedures are user friendly.
Figure1-1 illustrates the path throughthe menu structureand therequired keystrokes toenter andexit each
screen. AMAINMENUprovidesselectionsforthemainactivities. REVIEW/EDITSETTINGSMENUallows
the user to select a complete group of settings. When the activity of the selected screen is complete, the
user is returned to the menu for another activity selection.

BE1-DFPR General Information
1-4
Figure 1-1. Terminal Screens Flow Diagram (Sheet 1 Of 2)

BE1-DFPR General Information
1-5

BE1-DFPR General Information
1-6
Figure 1-2. Terminal Screens Flow Diagram (Sheet 2 Of 2)

BE1-DFPR General Information
1-7
APPLICATION
Distribution feeders represent the majority of circuits in a utility system. These circuits are typically radial,
three-phase, and operate over the range of 2.4 to 35 kV. In the majority of distribution substations, circuit
breakers are used to interrupt these circuits, with fuses and sectionalizers providing fault isolation
downstream. Because the substations are usually in remote areas, it is desirable to be able to control the
breakerfromacentraldispatchoffice.Totalautomationofthesedistributionsystems,includingrealtimeload
and demand data collection for each feeder, is also desirable. BE1-DFPR Distribution Feeder Protection
Relays provide both protection and data collection.
Improving Protection Schemes
Quantity of data and status information that can be collected is limited by the space available to mount
discrete devices and the capability of SCADA terminals to collect and process data. BE1-DFPR relays are
multi-phase, multi-function devices in economical, standard 19-inch rack units and require less space than
the equivalent electromechanical overcurrent relays.
Overcurrent elements in DFPR relays are tuned to the fundamental frequency (50 or60 hertz) and, thereby,
rejects offsets and harmonics. This provides the means to achieve more sensitive neutral overcurrent
protection in feeders with high harmonic content. In addition to overcurrent protection, DFPR relays include
undervoltage elements that may be used for undervoltage load-shedding applications.
DFPR relays also include a complete multiple shot reclosing unit with four shot capabilities. By integrating
this function along with the protective functions, it is possible to program the reclosing system to respond
in a specified manner to operations of the various tripping elements. This makes it possible to implement
improved logic in the reclosing scheme.
DFPR relays have the means to selectively trip individual feeders on underfrequency conditions and to
automatically restore them at selected frequencies.
Breakerfail outputs (BFO) may be used toactivatebreakerfailureschemes. Thisinvolvestrippingabreaker
or breakers upstream from the one that failed.
Implementing Adaptive Schemes
One adaptive capability of DFPR relays is to revert to normal, auxiliary one (cold load pickup), auxiliary two
(emergency), auxiliary three, or auxiliary four setting groups in accordance with the control inputs applied
to the relay. DFPR relays can, if desired, automatically revert to auxiliary one (cold load pickup) settings if
the feeder has been dead for a preset time. Normal settings are restored if automatic entrance to the
auxiliary one settings has occurred and the feeder has been energized for ten minutes.
DFPRrelays include acontrolinputfor blocking allfixed timeovercurrent elements. Italso includesa control
input for blocking neutral fixed time and neutral time overcurrent elements. Control inputs are also provided
for enabling or disabling the reclose function.
Providing Maintenance Information
DFPR target and reclose function status output contacts may be interfaced with a SCADA system to give
the operator additional information about what occurred on a feeder that tripped. This information is used
to help guide maintenance personnel.
Through communications, DFPR relays provide information about the type of fault. This information is
obtained from the fault report under REVIEW EVENT SCREEN. The report lists fault currents, voltages,
targets, breaker operate time, reclose status, and general information. By interpreting the fault information,
the fault location can be estimated.

BE1-DFPR General Information
1-8
Information is also provided by the DFPR to schedule breaker maintenance. Available is the number of
breakeroperationsandarccumulatedcontactwear. Thisinformationisaccessiblethroughcommunications
under REVIEW/RESET MAINTENANCE VALUES SCREEN.
DFPR relays store minimum and maximum demand values. This information can be retrieved periodically
to keep track of load peaks and growth for planning purposes.
SPECIFICATIONS
BE1-DFPR relays are available with the following features and capabilities.
Accuracies of Measured Currents Refer to Table 1-1 for accuracies of front panel
instrumentation measured currents.
Table 1-1. Accuracies of Instrumentation Currents
For 5 A CT For 1 A CT Accuracy
0.1 to 0.5 A 0.02 to 0.1 A ±5% or ±15 mA
0.5 to 2.0 A 0.1 to 0.4 A ±3%
2.0 to 7.5 A 0.4 to 1.5 A ±2%
Accuracies of Measured Voltages Refer to Table 1-2 for accuracies of front panel
instrumentation measured voltages.
Table 1-2. Accuracies of Instrumentation Voltages
Voltage Accuracy
40 to 130 ±2%
Calculated Values and Accuracy
Present values: W, var, VA, pf
Demand values: A, W, var, VA
Accuracy: Better than ±4% for all values
Demand intervals: 1 to 60 min.
Date And Time Clock
Accuracy: 3 seconds per day at 25(C
Resolution: 10 milliseconds
Backup battery: Lithium carbon monofluoride
Battery life: 20 years
Date and time setting provisions: Front panel and communications port
Recognition Time On Contact Inputs 8 ms.
AC Response Characteristics Rejects harmonics higher than second by 12 db or more.
Rejects dc offsets
50 Hz range: 40 to 55 Hz
60 Hz range: 50 to 65 Hz

BE1-DFPR General Information
1-9

BE1-DFPR General Information
1-10
T
AD
MN
C
BD
K
Current Pickup For Phase and Neutral Dropout/pickup ratio: 95% or higher
Time Elements (51, 51N)
5 Ampere CT Range 0.5 to 12 A
Increments 0.1 A
Pickup accuracy ±2% or 50 mA
1 Ampere CT Range 0.1 to 2.4 A
Increments 0.02 A
Time Characteristic Curves Refer to Table 1-3. Timing accuracy within 5% or 40 milli-
(FOR51,51NELEMENTS) seconds,whicheverisgreaterfortime dial settings greater
than 0.1 and multiples of 2 to 40 times pickup setting.
Eleven inverse time functions and one fixed time function
canbeselected. Characteristic curves fortheinverseand
definite time functions are defined by the trip and
integrating reset characteristic equations and shown
graphically in Figures 1-5 through 1-16.
Table 1-3. 51, 51N Characteristic Curves
Type Curve Name Figure
Number
S Short Inverse Figure 1-5
L Long Inverse Figure 1-6
D Definite Time or IDMT Figure 1-7
M Moderately Inverse Figure 1-8
I Inverse Time Figure 1-9
V Very Inverse Figure 1-10
E Extremely Inverse Figure 1-11
A BS142 Standard Inverse Figure 1-12
B BS142 Very Inverse (It) Figure 1-13
C BS142 Extremely Inverse (I2t) Figure 1-14
G BS142-Longtime Inverse Figure 1-15
F Fixed Time Figure 1-16
Trip Characteristic Characteristic curves for the inverse and definite time
functions are defined by the following equation.
Where:
D = TIME DIAL setting
M = Multiple of PICKUP setting
A, B, C, N, K = Constants for the particular curve

BE1-DFPR General Information
1-11
Tr
ArD
M
21
Trip Characteristic Refer to Table 1-4 for the time characteristic curve con-
Continued stants. Constants havebeen selected to
conform to the characteristics of electromechanical relays
over a range of pickup multiples from 1.3 to 40. Values of
the constants are available for use in computer relay
setting programs.
The fixed time characteristic (curve type F) provides
delaysof0.0 to9.9 seconds correspondingto thetimedial
setting. The time set is constant over a range of pickup
multiples from 1.0 to 40.
Integrating Reset Characteristic
Front panel selectable for 51P, 51N, or 51P and 51N using the 51 RESET setting. The integrating reset
characteristic curves are defined by the following equation.
Where:
D = TIME DIAL setting
M = Multiple of PICKUP setting
Ar=Constantfortheparticularcurve(Table1-4)
Table 1-4. 51 And 51N Time Characteristic Curve Constants
Curve Type
Characteristic Constants
Trip Reset
ABC NKA
r
S 0.2663 0.03393 1.000 1.2969 0.028 0.500
L 5.6143 2.18592 1.000 1.000 0.028 15.75
D 0.4797 0.21359 1.000 1.5625 0.028 0.875
M 0.3022 0.12840 1.000 0.5000 0.028 1.750
I 8.9341 0.17966 1.000 2.0938 0.028 09.00
V 5.4678 0.10814 1.000 2.0469 0.028 05.50
E 7.7624 0.02758 1.000 2.0938 0.028 07.75
A 0.01414 0.00000 1.000 0.0200 0.028 02.00
B 1.4636 0.00000 1.000 1.0469 0.028 03.25
C 8.2506 0.00000 1.000 2.0469 0.028 08.00
G 12.1212 0.00000 1.000 1.000 0.028 29.00
F 0.0000 1.00000 0.000 0.0000 0.000 0.000
Curve Type:
S = Short Inverse L = Long Inverse D = Definite Time
M = Moderately Inverse I = Inverse V = Very Inverse
E = Extremely Inverse A = BS142 Standard Inverse B = BS142 Very Inverse
C = BS142 Extremely Inverse G = BS142 Long Time Inverse F = Fixed Time
Curves A, B, C, and G are defined in British Standard BS142.

BE1-DFPR General Information
1-12
Fixed Time Parameters
(For 50T, 50TN Elements)
Characteristic: Fixed time for any current exceeding pickup
Time Range: 30 to 5000 ms
Time Increments: 10 ms
Reset: Reset is instantaneous
Timing accuracy: ±5% or 15 ms, whichever is greater
Current Pickup For Phase And Neutral Dropout/Pickup ratio: 90%.
Fixed Time Elements (50T, 50TN) Pickup accuracy: ±5%
5 Ampere CT Range 0.5 to 150 A
Increments 0.1 A
1 Ampere CT Range 0.1 to 30 A
Increments 0.02 A
Instantaneous Response Characteristics
(For 50, 50N Elements)
Characteristic: Refer to Figure 1-3 for the instantaneous response range.
Figure 1-3. Instantaneous Response Characteristics (50, 50N Elements)
Current Pickup For Phase And Neutral Dropout/Pickup ratio: 90%.
Instantaneous Elements (50, 50N) Pickup accuracy: ±5%
5 Ampere CT Range 0.5 to 150 A
Increment 1.0 A

BE1-DFPR General Information
1-13
NOTE
A time dial (time range) setting of 0.0 inhibits the 59 function.
CAUTION
The 59 pickup element must not be set lower than the 27 pickup element. Doing so
will cause a trip condition.
NOTE
A time dial (time range) setting of 0.0 inhibits the 27 function.
CAUTION
The 27 pickup element must not be set higher than the 59 pickup element. Doing so
will cause a trip condition.
Current Pickup (50, 50N) - Continued
1 Ampere CT Range 0.1 to 30 A
Increment 0.2 A
Overvoltage Response characteristic
(For 59 Element)
Characteristic: Fixed time
Time range: 0.0 to 100 seconds
Setting increments: 0.1 second
Reset 16 ms or less
Timing accuracy: ±5% for settings greater than 5 seconds
Overvoltage Pickup Setting
(For 59 Element)
Setting range: 50 to 150 volts
Setting increments: 1.0 volt
Pickup accuracy: ±2%
Dropout/Pickup ratio: 90%
Acceptable Setting Example: If 27 = 100, then 59 must be 100
Undervoltage Response Characteristic
(For 27 Element)
Characteristic: Fixed time
Time range: 1 to 1000 seconds
Setting increments: 1 seconds
Reset: 16 ms or less
Timing accuracy: ±5% for settings greater than 5 seconds.
Undervoltage Pickup Setting
(For 27 Element)
Setting range: 50 to 100% of nominal input
Setting increment: 1 V
Pickup accuracy: ±2%
Dropout/Pickup ratio: 110% or higher

BE1-DFPR General Information
1-14
Acceptable Setting Example: If 59 = 120, then 27 must be 120
Underfrequency Response Characteristics
(For 81 Element)
Characteristic: Fixed time
Time range: 100 to 500 ms
Setting increments: 10 ms
Reset: Two cycles or less
Timing accuracy: 10% or 50 ms, whichever is greater
Underfrequency Pickup Setting (81)
Voltage supervision range: 40 to 120 V
Setting range: Nominal frequency +5 Hz, -10 Hz
Setting increment: 0.01 Hz
Pickup accuracy: 0.01 Hz
Restoration-Frequency Response
Characteristic (For 81 Element)
Conditional requirement: Underfrequency trip has occurred
Characteristic: Definite time
Time range: 1 to 1000 seconds
Time increment: 1 seconds
Timing accuracy: ±5% or 200 ms, whichever is greater
Restoration-Frequency Pickup
Setting (81)
Voltage supervision range: 40 to 120 V
Setting range: Nominal frequency +5 Hz, -10 Hz
Setting increment: 0.01 Hz
Pickup accuracy: 0.01 Hz
Reclosing Relay Timers
(For 79 Element)
Reclosing delays (4): 0.00 to 100 seconds (0 = inhibit)
Reset time range: 1 to 200 seconds
Maximum cycle time: 0 to 999 seconds (0 = inhibit)
Fail to reclose timer: 0.0 to 9.9 seconds (0 = inhibit)
Timing Accuracy 5% or 30 ms whichever is greater
Breaker Fail Timer
(For 50BF Element)
Delay range: 30 to 500 ms
Setting increment: 10 ms
Reset time: 16 ms or less
Timing Accuracy 5% or 8 ms whichever is greater
GENERAL SPECIFICATIONS
AC Voltage Inputs At 50 Hz
Nominal: 100, 173 or 192 V phase-to-phase
Continuous: 133 V phase-to-neutral
One second rating: 260 V
Burden: Less than 1.0 VA at 100 V phase-to-neutral
AC Voltage Inputs At 60 Hz
Nominal: 120, 208 or 230 V phase-to-phase
Continuous: 160 V phase-to-neutral
Table of contents
Other Basler Relay manuals

Basler
Basler BE1-87G User manual
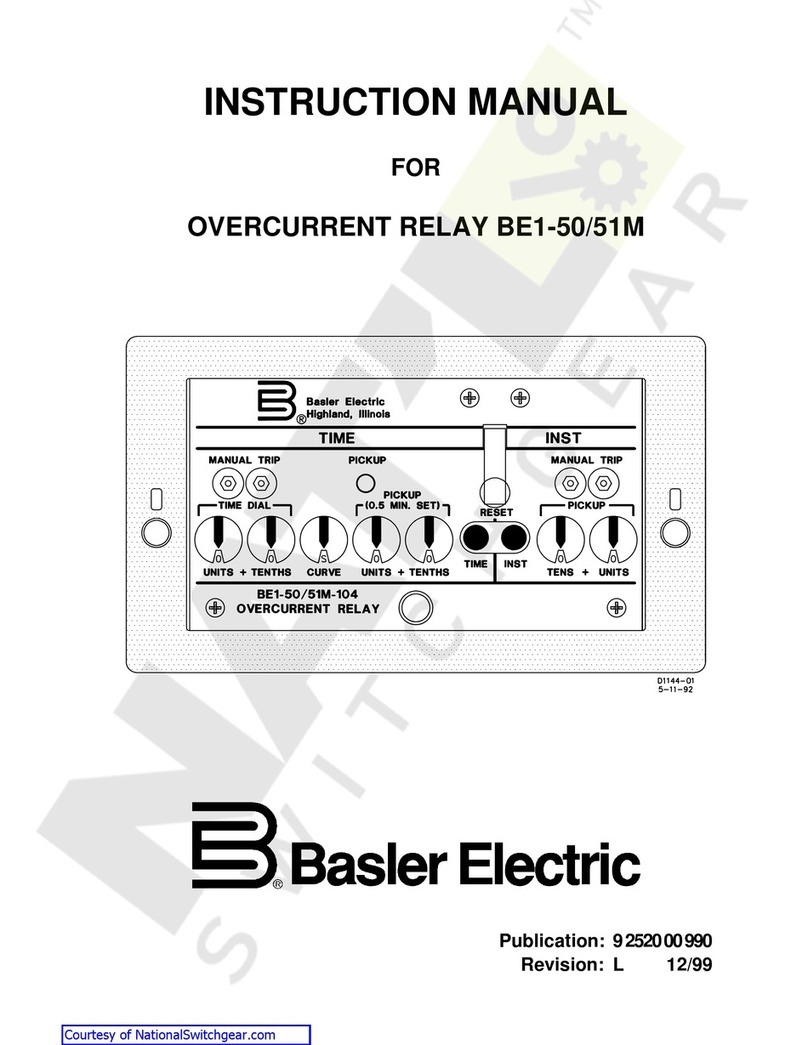
Basler
Basler BE1-50M User manual
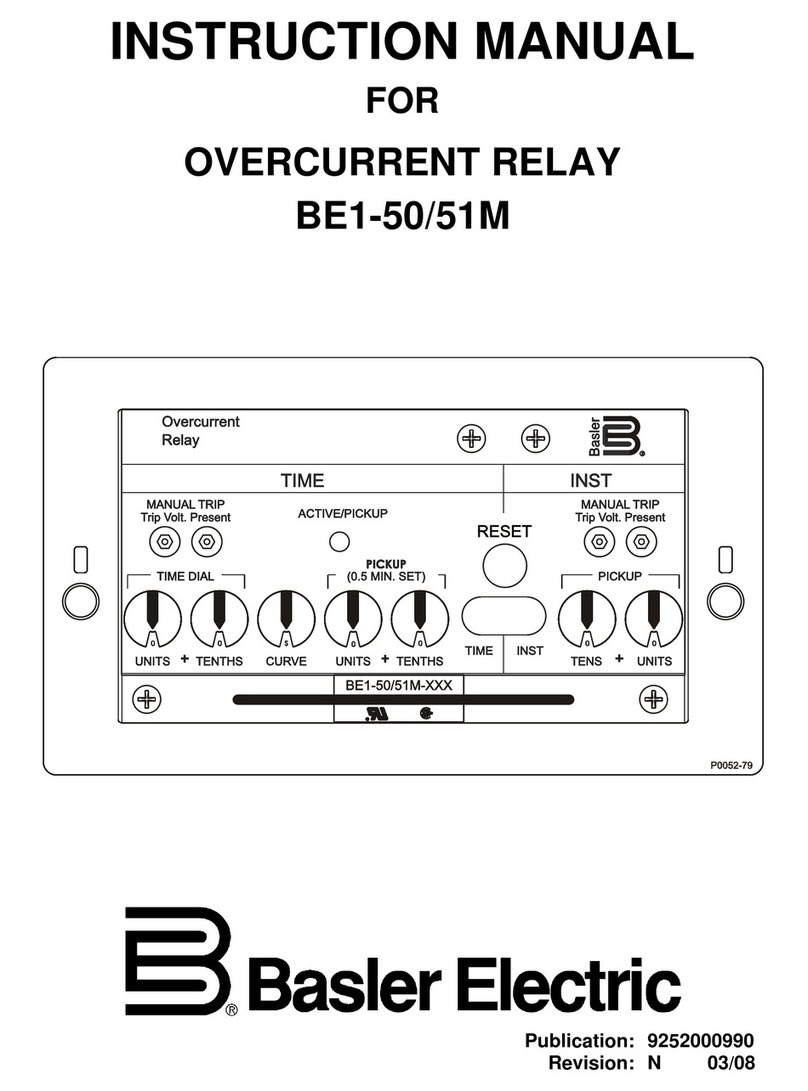
Basler
Basler BE1-51M User manual
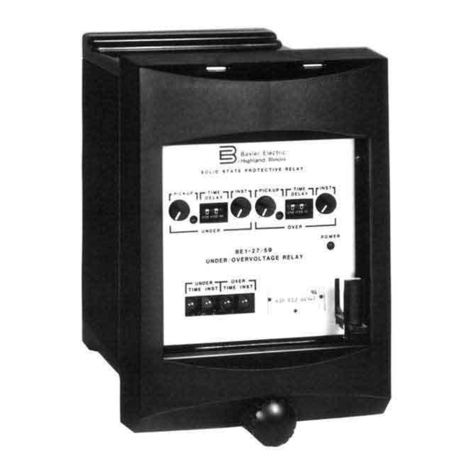
Basler
Basler BE1-27 User manual
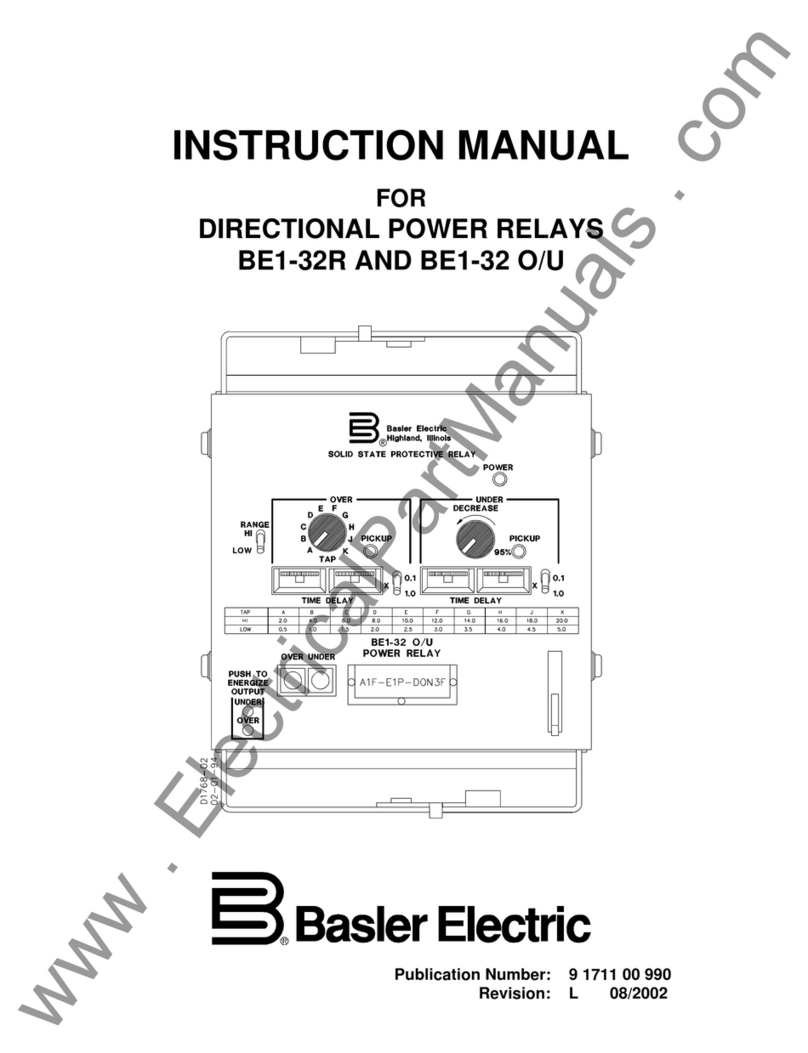
Basler
Basler BE1-32R User manual

Basler
Basler BE1-67N User manual
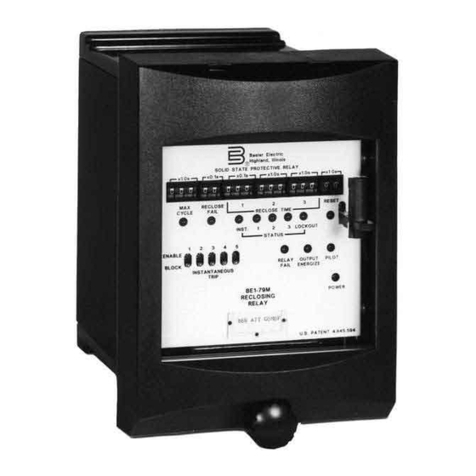
Basler
Basler BE1-79M User manual

Basler
Basler BE1-50 User manual
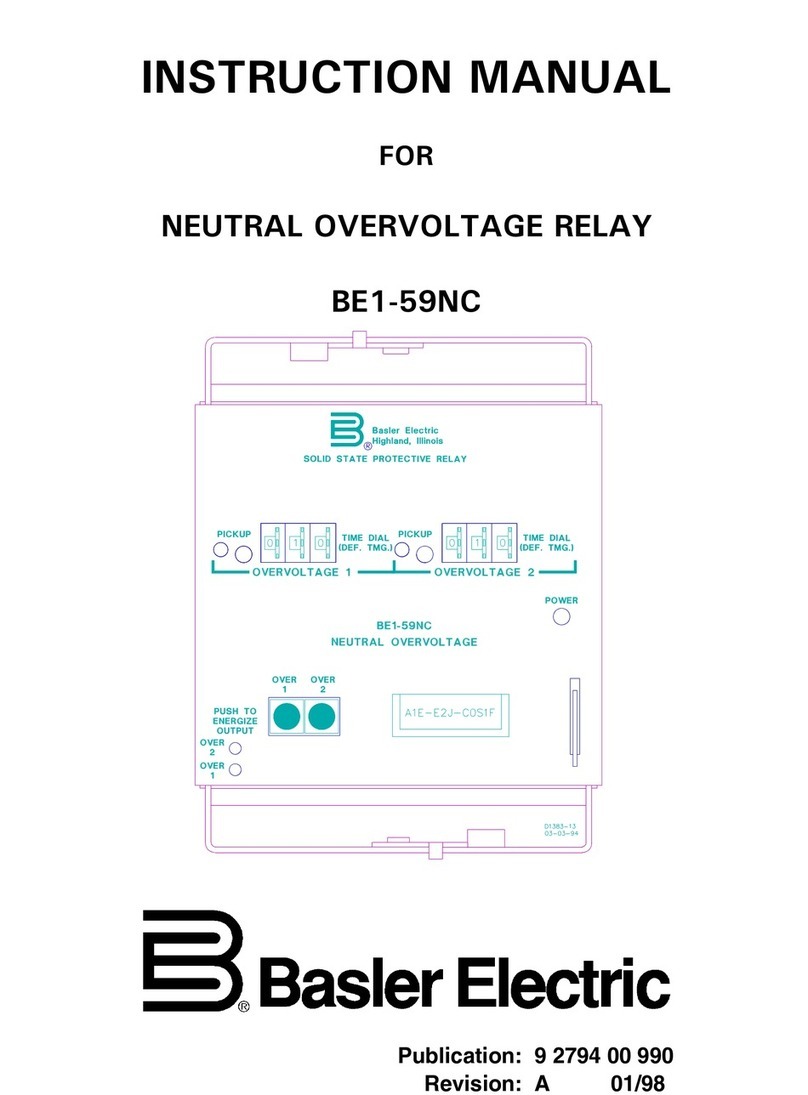
Basler
Basler BE1-59NC User manual
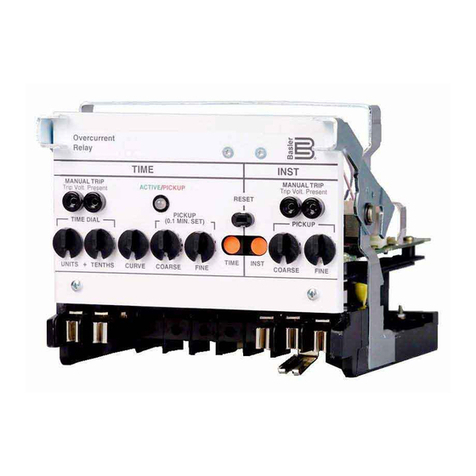
Basler
Basler BE1-50/51B-218 User manual
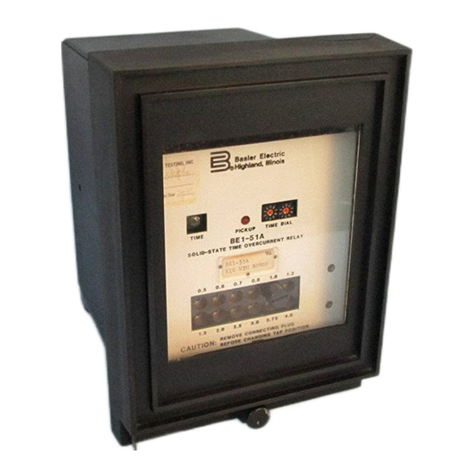
Basler
Basler BE1-51A User manual

Basler
Basler BE1-51 User manual

Basler
Basler BE1-50BF User manual
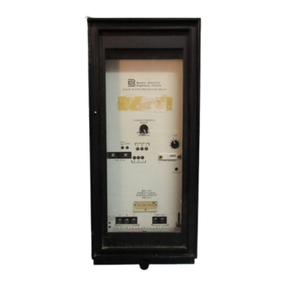
Basler
Basler BE1-67 User manual
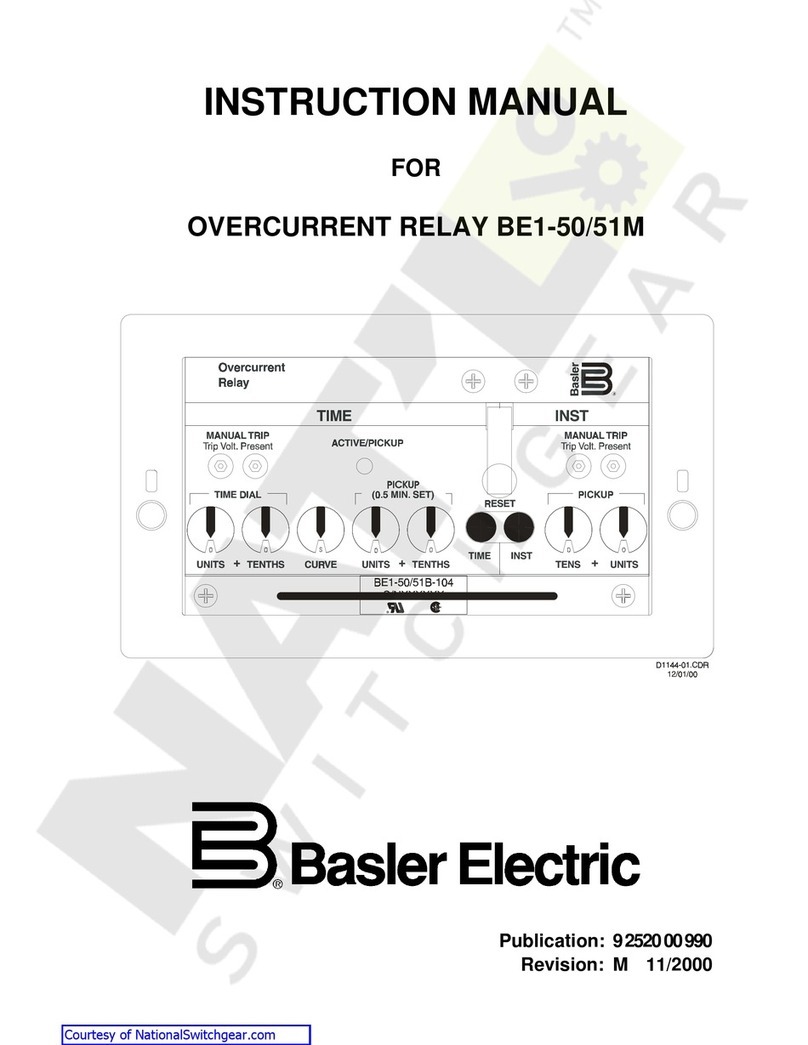
Basler
Basler BE1-50/51M-100 Series User manual
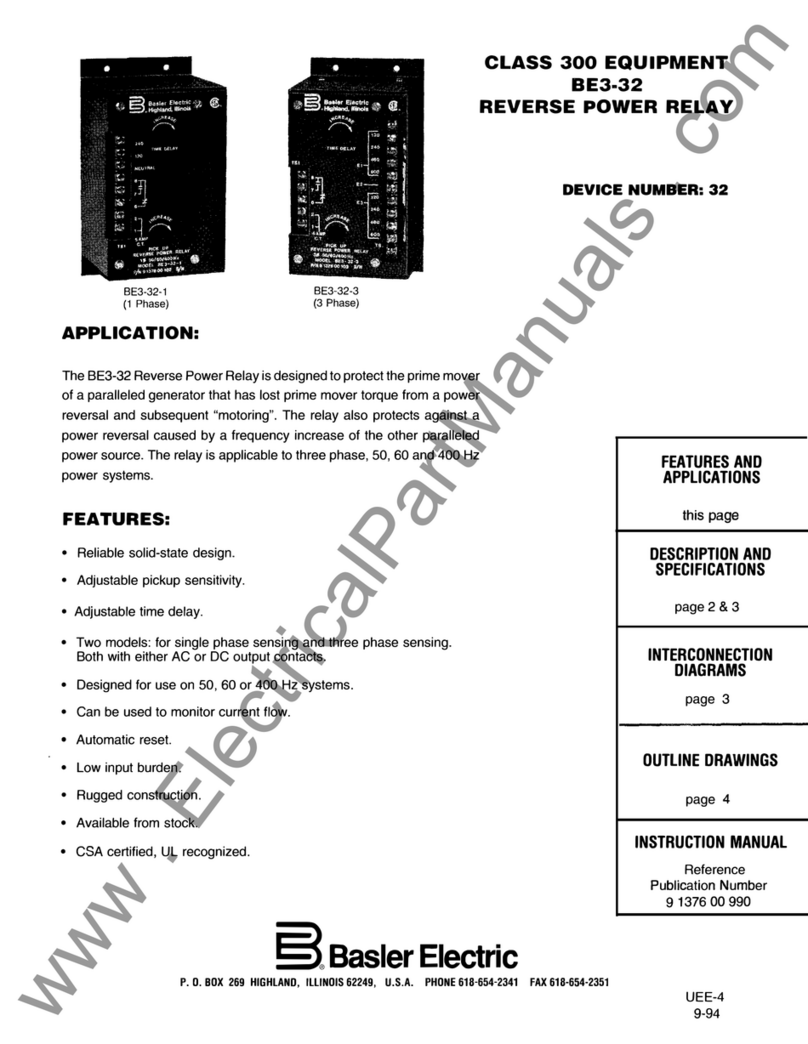
Basler
Basler Class 300 User manual
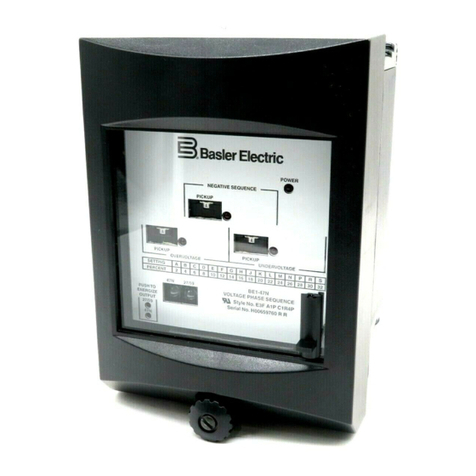
Basler
Basler BE1-47N User manual
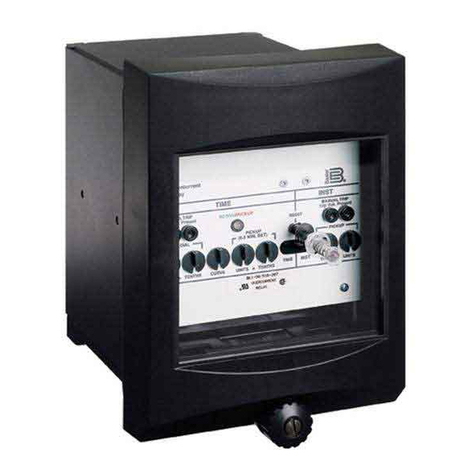
Basler
Basler BE1-50/51B-229 User manual
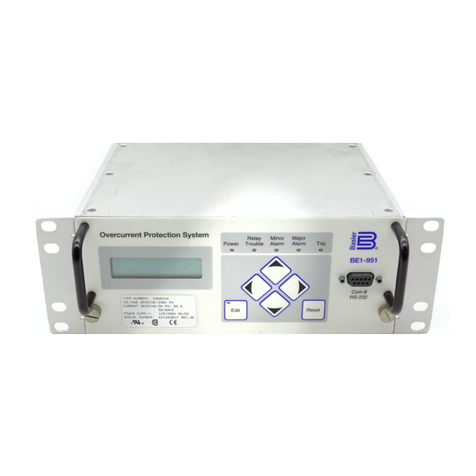
Basler
Basler BE1-951 User manual
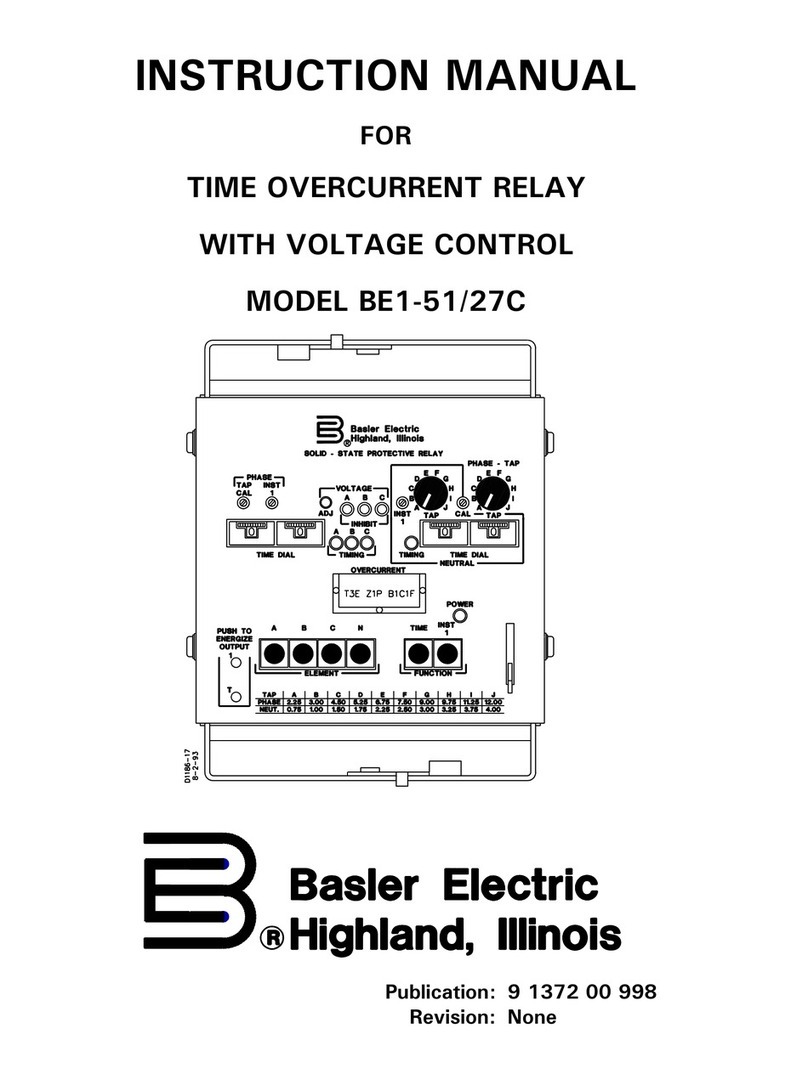
Basler
Basler BE-51/27C User manual