Bender ISOMETER isoMIL425HV User manual

Manual
EN
Insulation monitoring device for unearthed
AC, AC/DC and DC systems (IT systems)
for military applications up to 3(N)AC, AC 690 V, DC 1000 V
Software version: D0460 V1.xx
ISOMETER® isoMIL425HV
with coupling device AGH421
isoMIL425HV_D00204_05_M_XXEN/02.2021

Bender GmbH & Co. KG
Londorfer Str. 65 • 35305 Grünberg • Germany
PO box 1161 • 35301 Grünberg • Germany
Tel.: +49 6401 807-0
Fax: +49 6401 807-259
E-mail: [email protected]
Web: https://www.bender.de
©Bender GmbH & Co. KG
All rights reserved.
Reprinting and duplicating
only with permission
of the publisher.
Photos: Bender archives.

Table of Contents
3
isoMIL425HV_D00204_05_M_XXEN/02.2021
1. Important information .................................................................................... 6
1.1 How to use this manual ................................................................................. 6
1.2 Technical support: Service and support .................................................. 7
1.2.1 First level support ............................................................................................. 7
1.2.2 Repair service ..................................................................................................... 7
1.2.3 Field service ........................................................................................................ 8
1.3 Training courses ................................................................................................ 8
1.4 Delivery conditions .......................................................................................... 9
1.5 Inspection, transport and storage .............................................................. 9
1.6 Warranty and liability ...................................................................................... 9
1.7 Disposal ............................................................................................................ 10
2. Safety instructions ......................................................................................... 11
2.1 General safety instructions ........................................................................ 11
2.2 Work activities on electrical installations ............................................. 11
2.3 Intended use ................................................................................................... 12
3. Function ........................................................................................................... 13
3.1 Device features .............................................................................................. 13
3.2 Functional description ................................................................................ 14
3.2.1 Monitoring the insulation resistance ..................................................... 15
3.2.2 Undervoltage/overvoltage monitoring ................................................ 16
3.2.3 Self test/error codes ..................................................................................... 16
3.2.4 Malfunction ..................................................................................................... 19
3.2.5 Signalling assignment of the alarm relays K1/K2 .............................. 19
3.2.6 Measuring and response times ................................................................ 20
3.2.7 Password protection (on, OFF) ................................................................. 21
3.2.8 Factory settings FAC .................................................................................... 21
3.2.9 External stop switch ..................................................................................... 21

Table of Contents
4isoMIL425HV_D00204_05_M_XXEN/02.2021
3.2.10 Fault memory .................................................................................................. 22
3.2.11 History memory HiS ...................................................................................... 22
3.2.12 Interface/protocols ...................................................................................... 22
4. Installation, connection and commissioning ........................................... 24
4.1 Installation ....................................................................................................... 24
4.2 Wiring diagram .............................................................................................. 26
4.3 Commissioning .............................................................................................. 28
5. Operation of the device ............................................................................... 29
5.1 Display elements ........................................................................................... 30
5.2 Menu structure ............................................................................................... 31
5.3 "AL" menu ........................................................................................................ 32
5.3.1 Response value setting ............................................................................... 32
5.4 "out" menu ....................................................................................................... 33
5.4.1 Configuration of the relay operating mode ........................................ 33
5.4.2 Relay signalling assignment "r1" and "r2" and LED assignment .. 33
5.4.3 Fault memory configuration .................................................................... 34
5.4.4 Interface configuration .............................................................................. 35
5.5 "t" menu ............................................................................................................ 36
5.5.1 Time configuration ....................................................................................... 36
5.6 "SEt" menu ....................................................................................................... 36
5.6.1 Function configuration ............................................................................... 36
5.7 Measured value display and history memory ..................................... 37
6. Data access using the BMS protocol .......................................................... 39

Table of Contents
5
isoMIL425HV_D00204_05_M_XXEN/02.2021
7. Data access using the Modbus RTU protocol ........................................... 40
7.1 Reading out the Modbus register from the ISOMETER® ................. 40
7.1.1 Command of the master to the ISOMETER® ........................................ 40
7.1.2 The ISOMETER® answers the master ...................................................... 41
7.2 Writing the Modbus register (parameter setting) ............................. 41
7.2.1 Command of the master to the ISOMETER® ........................................ 41
7.2.2 The ISOMETER® answers the master ...................................................... 42
7.3 Exception code ............................................................................................... 42
7.3.1 Structure of the exception code .............................................................. 42
8. Modbus register assignment of the ISOMETER® ...................................... 43
8.1 Device-specific data type of the ISOMETER® ....................................... 49
8.1.1 Device name ................................................................................................... 49
8.1.2 Measured values ............................................................................................ 49
8.1.2.1 Float = Floating point value of the channels .............................. 50
8.1.2.2 AT&T = Alarm type and test type (internal/external) .............. 51
8.1.2.3 R&U = Range and unit ......................................................................... 52
8.1.3 Alarm assignment of the relays ................................................................ 53
8.2 Channel descriptions ................................................................................... 54
9. IsoData data string ........................................................................................ 56
10. Technical data .............................................................................................. 58
10.1 Tabular representation ................................................................................ 58
10.2 Standards, approvals and certifications ................................................ 64
10.3 Ordering details ............................................................................................. 65
10.4 Revision history .............................................................................................. 65

6isoMIL425HV_D00204_05_M_XXEN/02.2021
1 Important information
1.1 How to use this manual
Always keep this manual within easy reach for future reference.
To make it easier for you to understand and revisit certain sections in this man-
ual, we have used symbols to identify important instructions and information.
The meaning of these symbols is explained below:
This manual is intended for electrically skilled
persons working in electrical engineering and electro-
nics.
DANGER
This signal word indicates that there is a high risk of danger
that will result in death or serious injury if not avoided.
WARNING
This signal word indicates a medium risk of danger that
can lead to death or serious injury if not avoided.
CAUTION
This signal word indicates a low level risk that can result in
minor or moderate injury or damage to property if not
avoided.

Important information
7
isoMIL425HV_D00204_05_M_XXEN/02.2021
1.2 Technical support: Service and support
For commissioning and troubleshooting Bender offers you:
1.2.1 First level support
Technical support by phone or e-mail for all Bender products
Questions concerning specific customer applications
Commissioning
Troubleshooting
Telephone: +49 6401 807-760*
Fax: +49 6401 807-259
In Germany only: 0700BenderHelp (Tel. and Fax)
E-Mail: [email protected]
1.2.2 Repair service
Repair, calibration, update and replacement service for Bender prod-
ucts
Repairing, calibrating, testing and analysing Bender products
Hardware and software update for Bender devices
Delivery of replacement devices in the event of faulty or incorrectly
delivered Bender devices
Extended warranty for Bender devices with in-house repair service or
replacement device at no extra cost
This symbol denotes information intended to assist the user
in making optimum use of the product.

Important information
8isoMIL425HV_D00204_05_M_XXEN/02.2021
Telephone: +49 6401 807-780* (technical issues)*
+49 6401 807-784**, -785** (sales)
Fax: +49 6401 807-789
E-Mail: [email protected]e
1.2.3 Field service
On-site service for all Bender products
Commissioning, parameter setting, maintenance, troubleshooting for
Bender products
Analysis of the electrical installation in the building (power quality test,
EMC test, thermography)
Training courses for customers
Telephone: +49 6401 807-752**, -762 **(technical issues)
+49 6401 807-753** (sales)
Fax: +49 6401 807-759
E-Mail: fieldservice@bender.de
Internet: www.bender.de
*Available from 7.00 a.m. to 8.00 p.m. 365 days a year (CET/UTC+1)
**Mon-Thurs 7.00 a.m. - 8.00 p.m., Fr 7.00 a.m. - 13.00 p.m.
1.3 Training courses
Bender is happy to provide training regarding the use of test equipment.
The dates of training courses and workshops can be found on the Internet at
www.bender.de -> Know-how -> Seminars.

Important information
9
isoMIL425HV_D00204_05_M_XXEN/02.2021
1.4 Delivery conditions
Bender sale and delivery conditions apply. For software products, the "Soft-
wareklausel zur Überlassung von Standard-Software als Teil von Lieferungen,
Ergänzung und Änderung der Allgemeinen Lieferbedingungen für Erzeug-
nisse und Leistungen der Elektroindustrie" (software clause in respect of the
licensing of standard software as part of deliveries, modifications and changes
to general delivery conditions for products and services in the electrical indus-
try) set out by the ZVEI (Zentralverband Elektrotechnik- und Elektronikindus-
trie e.V.) (German Electrical and Electronic Manufacturers' Association) also
applies.
Sale and delivery conditions can be obtained from Bender in printed or
electronic format.
1.5 Inspection, transport and storage
Inspect the dispatch and equipment packaging for damage, and compare the
contents of the package with the delivery documents. In the event of damage
in transit, please contact Bender immediately.
The devices must only be stored in areas where they are protected from dust,
damp, and spray and dripping water, and in which the specified storage tem-
peratures can be ensured.
1.6 Warranty and liability
Warranty and liability claims in the event of injury to persons or damage to
property are excluded if they can be attributed to one or more of the follow-
ing causes:
Improper use of the device.
Incorrect mounting, commissioning, operation and maintenance of the
device.
Failure to observe the instructions in this operating manual regarding
transport, commissioning, operation and maintenance of the device.
Unauthorised changes to the device made by parties other than the
manufacturer.

Important information
10 isoMIL425HV_D00204_05_M_XXEN/02.2021
Non-observance of technical data.
Repairs carried out incorrectly and the use of replacement parts or
accessories not approved by the manufacturer.
Catastrophes caused by external influences and force majeure.
Mounting and installation with device combinations not recom-
mended by the manufacturer.
This operating manual, especially the safety instructions, must be observed by
all personnel working on the device. Furthermore, the rules and regulations
that apply for accident prevention at the place of use must be observed.
1.7 Disposal
Abide by the national regulations and laws governing the disposal of this de-
vice. Ask your supplier if you are not sure how to dispose of the old equip-
ment.
The directive on waste electrical and electronic equipment (WEEE directive)
and the directive on the restriction of certain hazardous substances in electri-
cal and electronic equipment (RoHS directive) apply in the European Commu-
nity. In Germany, these policies are implemented through the "Electrical and
Electronic Equipment Act" (ElektroG). According to this, the following applies:
Electrical and electronic equipment are not part of household waste.
Batteries and accumulators are not part of household waste and must
be disposed of in accordance with the regulations.
Old electrical and electronic equipment from users other than private
households which was introduced to the market after 13th August
2005 must be taken back by the manufacturer and disposed of prop-
erly.
For more information on the disposal of Bender devices, refer to our
homepage at www.bender.de -> Service & support.

11
isoMIL425HV_D00204_05_M_XXEN/02.2021
2 Safety instructions
2.1 General safety instructions
Part of the device documentation in addition to this manual is the enclosed
"Safety instructions for Bender products".
2.2 Work activities on electrical installations
If the device is used outside the Federal Republic of Germany, the applicable
local standards and regulations must be complied with. The European stand-
ard EN 50110 can be used as a guide.
Only skilled persons are permitted to carry out the
work necessary to install, commission and run a de-
vice or system.
DANGER
Risk of electrocution due to electric shock!
Touching live parts of the system carries the risk of:
An electric shock
Damage to the electrical installation
Destruction of the device
Before installing and connecting the device, make sure that
the installation has been de-energised. Observe the rules for
working on electrical installations.

Safety instructions
12 isoMIL425HV_D00204_05_M_XXEN/02.2021
2.3 Intended use
The ISOMETER® of the isoMIL425HV series monitors the insulation resistance
RFof unearthed AC/DC main circuits (IT systems) with nominal system
voltages of 3(N)AC, AC/DC 0 … 690 V or DC 0 …1000 V, 15…460 Hz.
DC components existing in 3(N)AC, AC/DC systems do not influence the
operating characteristics when a minimum load current of DC 10 mA flows. A
separate supply voltage Usallows de-energised systems to be monitored, too.
The maximum permissible system leakage capacitance Ceis 700 µF.
The ISOMETER® is always used in conjunction with the coupling device
AGH421.
Any use other than that described in this manual is regarded as improper.
To ensure that the ISOMETER® functions correctly, an internal
resistance of
≤
1 kΩ must exist between L1/+ and L2/- via the
source (e.g. the transformer) or the load.

13
isoMIL425HV_D00204_05_M_XXEN/02.2021
3 Function
3.1 Device features
Monitoring of the insulation resistance RFfor unearthed 3(N)AC, AC
and DC systems with galvanically connected rectifiers or inverters
Measurement of the nominal system voltage Un(True RMS) with und-
ervoltage and overvoltage detection
Measurement of residual voltages system to earth (L+/PE and L-/PE)
Automatic adaptation to the system leakage capacitance Ceup to
700 F
Automatic device self test with connection monitoring
Selectable start-up delay, response delay and delay on release
Two separately adjustable response value ranges of 1…500 k
(Alarm 1, Alarm 2)
Alarm signalling via LEDs ("AL1", "AL2"), a display and alarm relays ("K1",
"K2")
N/C operation or N/O operation of the relays selectable
Measured value indication via multi-functional LC display
Fault memory can be activated
RS-485 (galvanically isolated) including the following protocols:
– BMS interface (Bender measuring device interface) for data
exchange with other Bender components
– Modbus RTU
– IsoData (for continuous data output)
Password protection to prevent unauthorised parameter changes

Function
14 isoMIL425HV_D00204_05_M_XXEN/02.2021
3.2 Functional description
The ISOMETER® measures the insulation resistance RFand the system leakage
capacitance Cebetween the system to be monitored (L1/+, L2/-) and earth
(PE). The RMS value of the nominal system voltage Unbetween L1/+ and L2/-
as well as the residual voltages UL1e (between L1/+ and earth) and UL2e
(between L2/- and earth) are also measured.
From a minimum value of the nominal system voltage, the ISOMETER® deter-
mines the faulty conductor "R %", which shows the distribution of the insula-
tion resistance between conductors L1/+ and L2/-. The distribution is
indicated by a positive or negative sign preceding the insulation resistance
measurement. The value range of the faulty conductor is ±100 %:
The partial resistances can be calculated from the total insulation resistance RF
and the faulty conductor (R %) using the following formula:
Also from a minimum value of the nominal system voltage, the ISOMETER® de-
termines the insulation resistance RUGF from the residual voltages UL1e and
UL2e. It is an approximate value for one-sided insulation faults and can be used
as a trend indicator in cases where the ISOMETER® has to adapt to an RFand
Cerelation that varies considerably.
It is possible to assign the detected fault or the faulty conductor to an alarm
relay via the menu. If the values RFor Unviolate the response values activated
in the "AL" menu, this will be indicated by the LEDs and relays "K1" and "K2"
according to the signalling assignment set in the "out" menu. In addition, the
operation of the relay (n.c./n.o.) can be set and the fault memory "M", activat-
ed.
Indication Meaning
-100 % one-sided fault at conductor L2/-
0 % symmetrical fault
+100 % one-sided fault at conductor L1/+
Fault at conductor L1/+ RL1F = (200 % * RF)/(100 % + R %)
Fault at conductor L2/- RL2F = (200 % * RF)/(100 % – R %)

Function
15
isoMIL425HV_D00204_05_M_XXEN/02.2021
If the values RFor Undo not violate their release value (response value plus
hysteresis) for the period toff without interruption, the alarm relays will switch
back to their initial position and the alarm LEDs "AL1"/"AL2" stop lighting.
The ISOMETER® features a stop switch. When the stop switch is closed, the
ISOMETER® is in operation. If the stop switch is opened, the ISOMETER® enters
stop mode, i.e. a high-resistance connection (approx. 20 M) is established
between the coupling L1/+ and L2/- and the system to be monitored. In stop
mode, if the memory function "M" is activated (reset function), the fault
memory is cleared. The stop function can also be triggered via an interface
command and in this case it can only be reset via the interface. When starting
the device or leaving the stop mode, no device test is run.
Parameters are assigned to the device via the LCD and the control buttons on
the front panel; this function can be password-protected. Parameterisation is
also possible via the BMS bus, for example by using the BMS Ethernet gateway
(COM465IP) or the Modbus RTU.
3.2.1 Monitoring the insulation resistance
The two parameters that monitor the insulation resistance, "R1" and "R2", can
be found in the menu "AL" (see table in chapter 5.3). The value R1 can only be
set higher than the value R2. If the insulation resistance RFreaches or falls be-
low the activated values R1 or R2, an alarm message will be signalled. If RFex-
ceeds the values R1 or R2 plus the hysteresis value (see table in chapter 5.3),
the alarm will be cleared.

Function
16 isoMIL425HV_D00204_05_M_XXEN/02.2021
3.2.2 Undervoltage/overvoltage monitoring
In the menu "AL" (see chapter 5.3), the parameters ("U <" and "U >") for
monitoring the mains voltage can be activated or deactivated. The maximum
undervoltage value is limited by the overvoltage value.
The RMS value of the mains voltage is monitored. If the mains voltage Un
reaches, falls below or exceeds the limit values ("U <" or "U >"), an alarm will
be signalled. If the maximum permissible system leakage capacitance set for
the ISOMETER® is exceeded, an alarm will be triggered even if the overvoltage
limit value has been deactivated. The alarm will be deleted when the limit
values plus hysteresis (see chapter 5.3) are no longer violated.
3.2.3 Self test/error codes
The integrated self test function checks the function of the insulation moni-
toring device and the connection monitoring checks the connections to the
system to be monitored. The alarm relays are not switched during the self test.
This can be changed using the parameter "test" in the signalling assignment
("out" menu, chapter 5.4.2). During the test, the display indicates "tES".
When malfunctions are detected or connections are missing, the LEDs "ON"/
"AL1"/"AL2" flash. The respective error codes ("E.xx") will be indicated on the
display and the relay "K2" switches.
The relays can be assigned to a device error with the parameter "Err" in the
"out" menu in the alarm assignment.

Function
17
isoMIL425HV_D00204_05_M_XXEN/02.2021
Error codes
If, contrary to expectations, a device error should occur, error codes will ap-
pear on the display. Some of these are described below:
Internal device errors "E.xx" can be caused by external disturbances or inter-
nal hardware errors. If the error message occurs again after restarting the
device or after a reset to factory settings (menu item "FAC") , the device must
be repaired.
Error code Description
E.01
PE connection fault
The connections "E" or "KE" to earth are interrupted.
Action:
Check connection, eliminate fault. The error code will be
erased automatically once the fault has been eliminated.
E.02
Connection fault system (L1/+ , L2/-),
The internal resistance of the system is too high, the con-
nection "L1/+" or "L2/-" to the system is interrupted or the
DC system being monitored has the wrong polarity at
Un> 100 V .
Action:
Check connection, eliminate fault. The error code will be
erased automatically once the fault has been eliminated.
E.05 Measurement technique error/calibration invalid
For the current software version
E.07
The maximum permissible system leakage capacitance
Ceis exceeded
Action:
Device not suitable for the existing system leakage capaci-
tance Ce: Uninstall device.
E.08
Calibration error during device test
Action:
If the error continues to exist after checking the device con-
nections, there is an error inside the device.

Function
18 isoMIL425HV_D00204_05_M_XXEN/02.2021
After eliminating the fault, the alarm relays switch back automatically or by
pressing the reset button.
The self test can take a few minutes. The self test can be suppressed for the du-
ration of the device start by setting the parameter in the menu "SEt" to
"S.Ct = off". This allows the ISOMETER® to enter measurement mode quickly af-
ter connecting the supply voltage Us.
Automatic self test
The device runs a self test after connecting the supply voltage Usand later
every 24 h (selectable: off, 1 h, 24 h).
Manual self test
A self test is initiated by pressing the test button for more than 1.5 s. While
pressing the internal test button "T", all display elements available for this de-
vice are shown.
Connection monitoring
The connection monitoring activated by the self test checks the connections
of the terminals "E" and "KE" to the protective earth conductor (PE). When an
error is detected, the message device error ("Err") will be signalled and the er-
ror code "E.01" appears on the display.
The system connection monitoring is used to check the terminal connections
"L1/+" and "L2/-" to the system to be monitored. When an interruption or a
high-resistance connection between L1/+ and L2/- is detected via the internal
resistance of the system, the device error ("Err") will be signalled and the error
code "E.02" appears on the display. Since a test of the system connection may
take considerable time due to system disturbances or may even provide in-
correct results, the system connection monitoring can be disconnected using
the parameter "nEt" in the "SEt" menu.

Function
19
isoMIL425HV_D00204_05_M_XXEN/02.2021
3.2.4 Malfunction
In addition to the self test described above, several functions in the insulation
monitoring device are continuously checked during operation. If a fault is de-
tected, the device error ("Err") will be signalled, the error code "E.xx" appears
on the display as an identifier for the error type xx and the LEDs "ON"/"AL1"/
"AL2" will flash.
If the error occurs again after restarting the device or after restoring the facto-
ry settings, please contact Bender Service.
3.2.5 Signalling assignment of the alarm relays K1/K2
The messages "device error", "insulation fault", "insulation impedance fault",
"undervoltage/overvoltage fault", "device test" or "device start can be as-
signed to the alarm relays" via the "out" menu. An insulation fault is indicated
by the messages "+R1", "-R1", "+R2" and "-R2". Messages "+R1" and "+R2" indi-
cate an insulation fault assigned to conductor L1/+, and messages "-R1" and
"-R2" indicate an insulation fault assigned to conductor L2/-. If an assignment
is not possible, for example in the event of a symmetrical insulation fault, the
messages corresponding to + and - are shown together.
The message "test" indicates a self test.
The message "S.AL" indicates a so-called "device start with alarm". After con-
necting to the supply voltage and setting the parameter value to "S.AL = on",
the ISOMETER® starts with the insulation measurement value RF= 0 and sets
all activated alarms. The alarms will be cleared only when the measured val-
ues are up-to-date and no thresholds are exceeded. In the factory setting
"S.AL = off", the ISOMETER® starts without an alarm.
It is recommended that the value set for the "S.AL" parameter value is identical
for both relays.

Function
20 isoMIL425HV_D00204_05_M_XXEN/02.2021
3.2.6 Measuring and response times
The measuring time is the period essential for the detection of the measured
value. The measuring time is reflected in the operating time tae .
The measuring time for the insulation resistance value is mainly determined
by the required measuring pulse duration, which depends on the insulation
resistance RFand system leakage capacitance Ceof the system to be moni-
tored. The measuring pulse is produced by the measuring pulse generator in-
tegrated in the ISOMETER®. The measuring times for Ce, UL1e, UL2e and R % are
synchronous. System disturbances may lead to extended measuring times. In
contrast, the time for the system voltage measurement Unis independent and
considerably shorter.
Operating time tae
The operating time tae is the time required by the ISOMETER® to determine
the measured value. The insulation resistance measured value depends on
the insulation resistance RFand the system leakage capacitance Ce.
High system leakage capacitances and system interferences lead to longer
operating times.
Response delay ton
The response delay ton is set uniformly for all messages in the menu "t" using
the parameter "ton". This delay time can be used for interference suppression
in the case of short measuring times.
An alarm will only be signalled when a threshold value of the respective meas-
uring value is violated for the period of ton without interruption. Every time
the threshold value is violated within the time ton, the response delay "ton" re-
starts once again.
Every alarm message listed in the alarm assignment has its own timer for ton.
Total response time tan
The total response time tan is the sum of the operating time tae and the re-
sponse delay time ton.
Other manuals for ISOMETER isoMIL425HV
2
Table of contents
Other Bender Controllers manuals
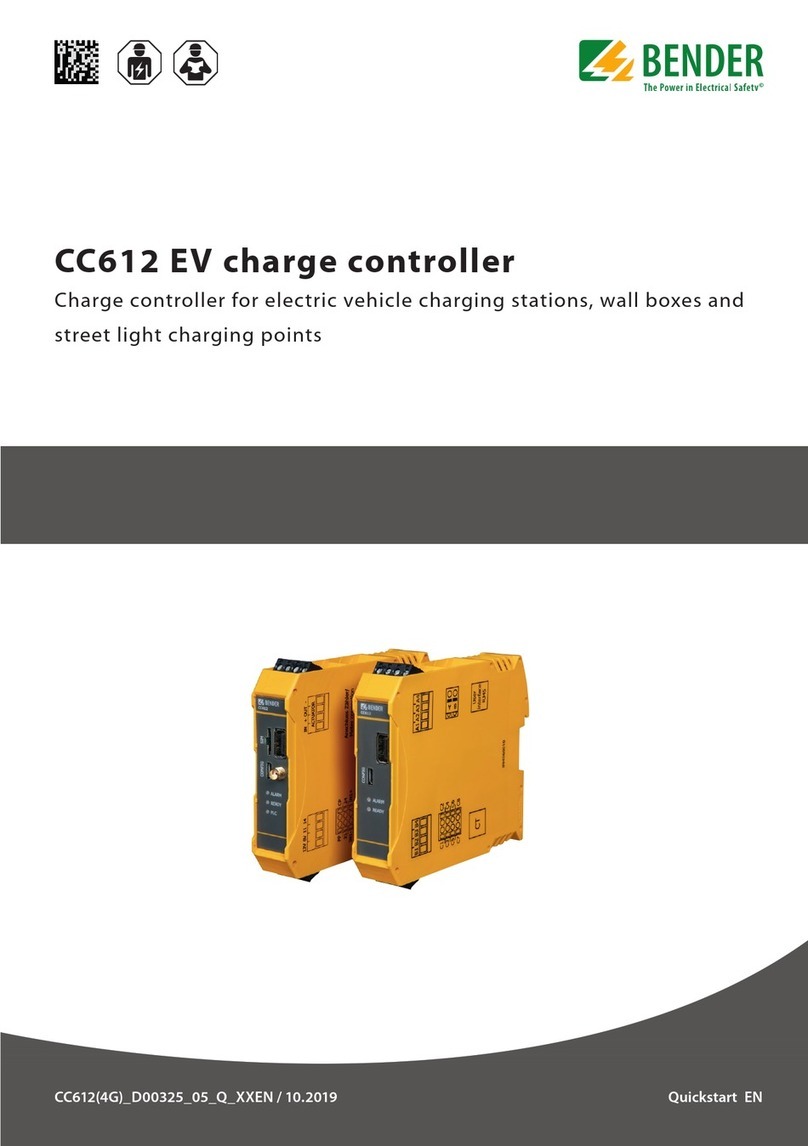
Bender
Bender CC612 EV User manual

Bender
Bender CC611 User manual
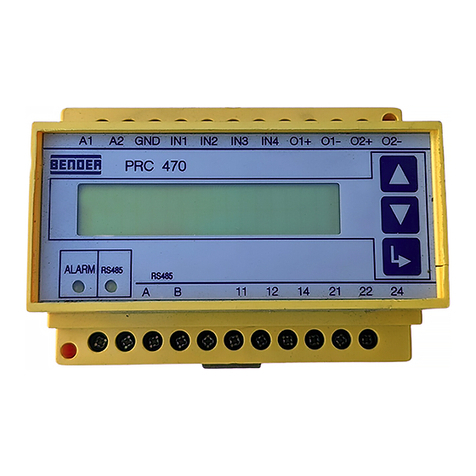
Bender
Bender PRC470 Series User manual
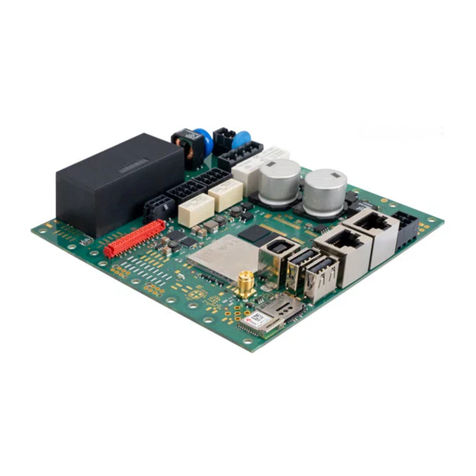
Bender
Bender ICC1324 User manual
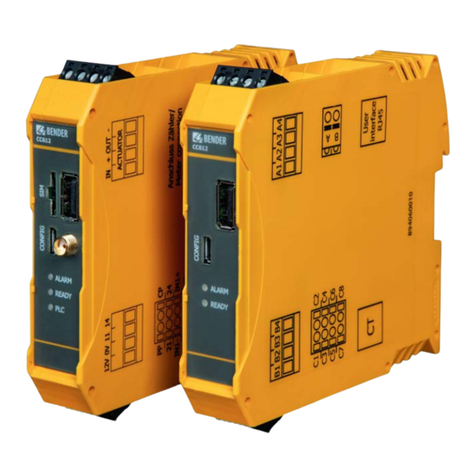
Bender
Bender CC612 User manual
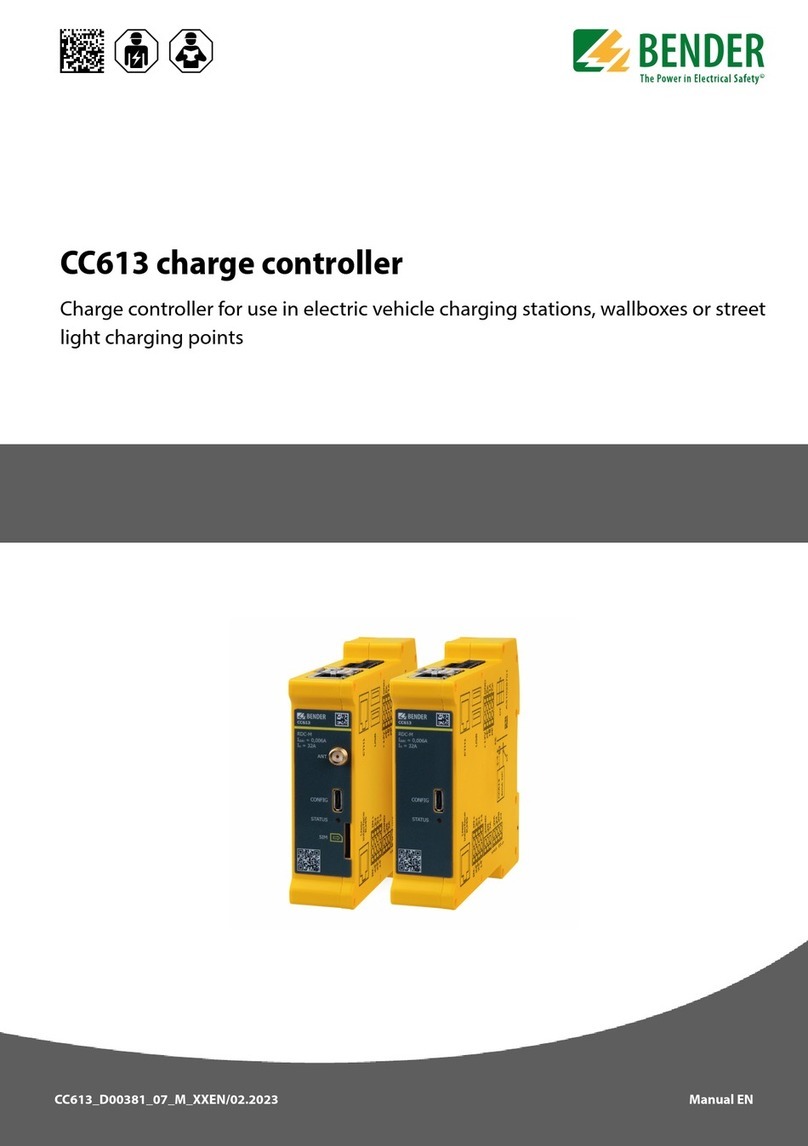
Bender
Bender CC613 User manual
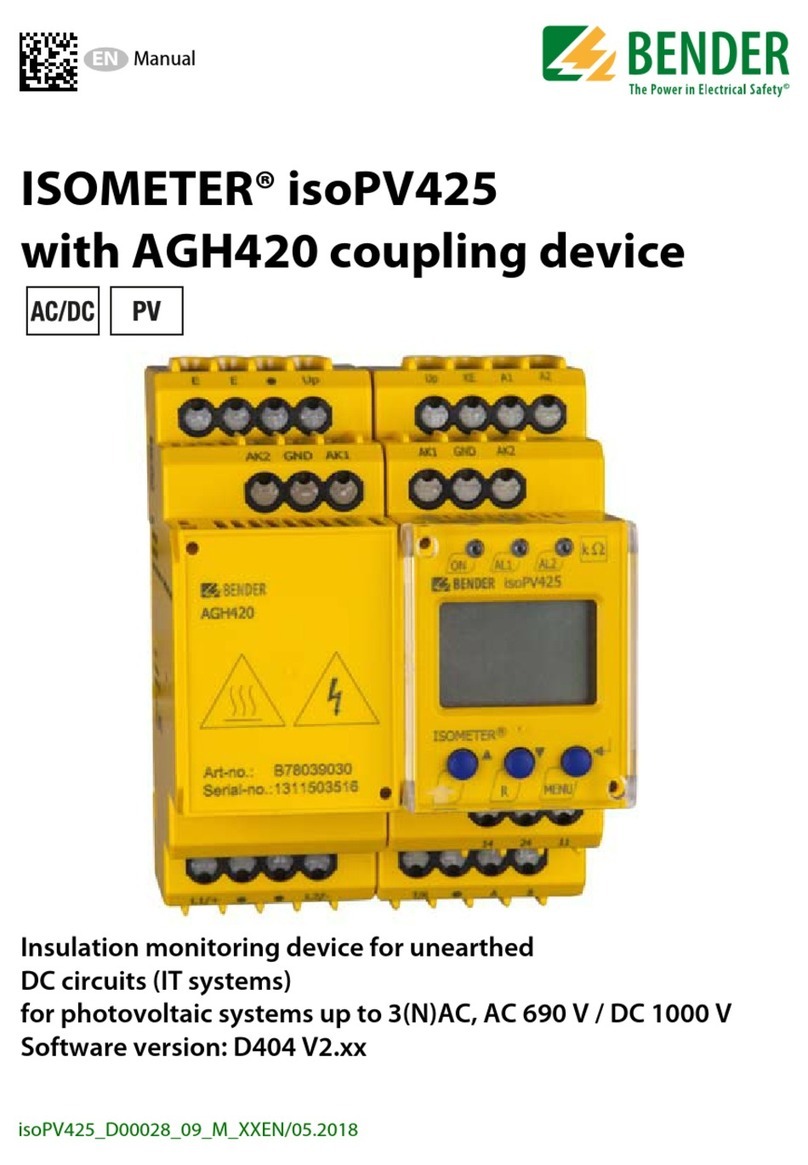
Bender
Bender ISOMETER isoPV425 with AGH420 User manual
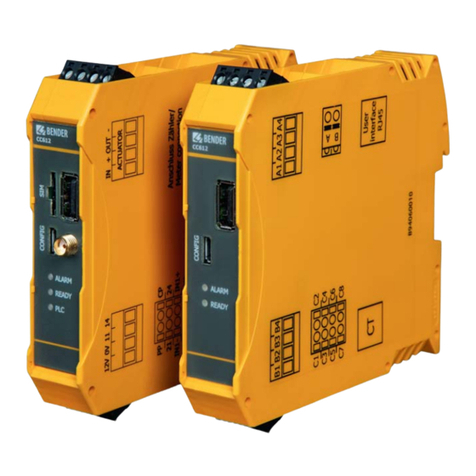
Bender
Bender CC612 User manual
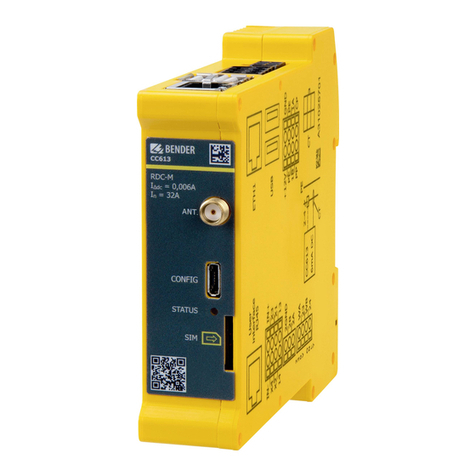
Bender
Bender CC613 User manual
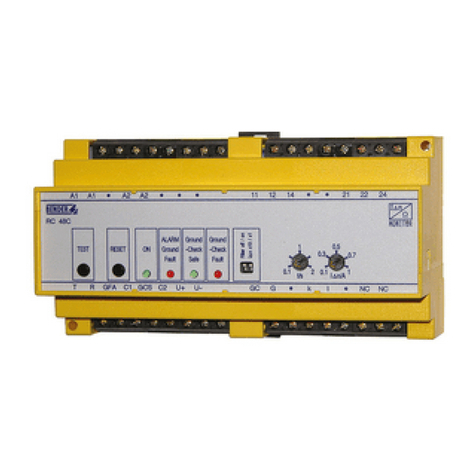
Bender
Bender RC48C User manual
Popular Controllers manuals by other brands
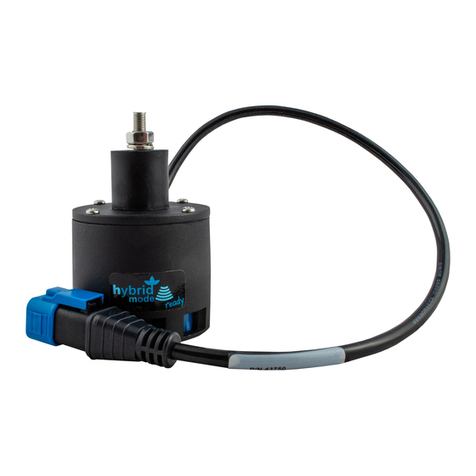
Norac
Norac UC5 Topcon X30 installation manual

Arbor Technology
Arbor Technology ELIT-1270 user manual
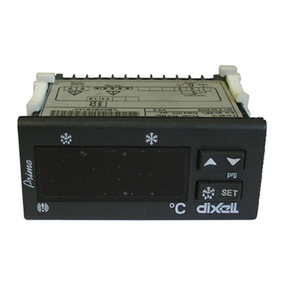
dixell
dixell XR20C Installing and operating instructions
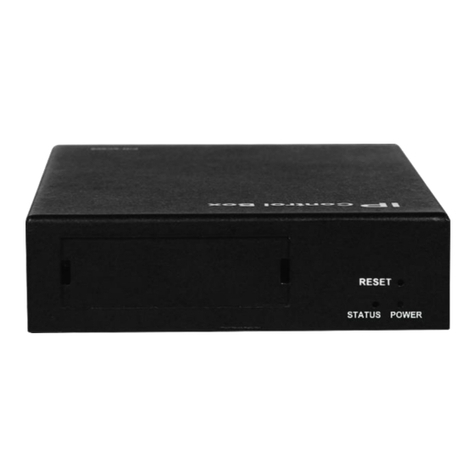
Zenty
Zenty ZT-IP100C user manual
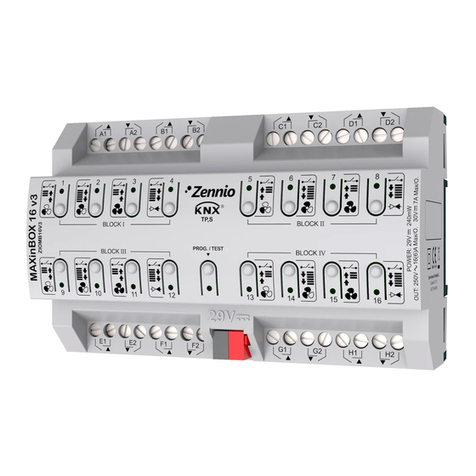
Zennio
Zennio MAXinBOX 16 Plus Technical documentation
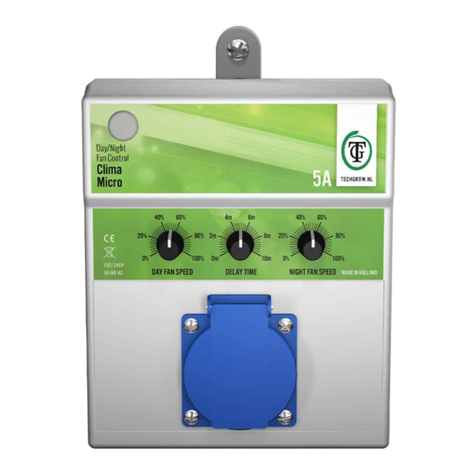
TechGrow
TechGrow Clima Micro Day/Night Fan Control user manual