Cembre LD-41PY User manual

1
RAIL DRILL
TYPE
LD-41PY
ENGLISH
OPERATION AND MAINTENANCE
MANUAL
4-CYCLE
HONDA ENGINE
08 M 076 U
Cerfied Environmental
Management System
Cerfied Occupaonal
Health & Safety
Management System
Cerfied Quality
Management System

2
WARNINGS
LD-41PNY
basic drill
LD-41PY
(LD–41PN + DBG-Y)
basic drill complete with
railweb clamping device
– Before using the drill, carefully read the instructions contained in this manual.
SAVETHESEINSTRUCTIONS:thismanualcontainsimportantsafetyandoperating
instructions for the drill.
– During operation keep your hands outside the danger area.
– Always wear protective glasses and work gloves.
– Avoid wearing clothes which may present a risk to personal safety.
– Always check combustion engine oil level before operation!

3
GENERAL CHARACTERISTICS
The Cembre LD-41PNY drill powered by HONDA 4-cycle engine can be stored and continuously op-
erated in full 360° inclination, thanks to the rotary-slinger pumping lubrication system.
– Drilling capacity:...................................................................................................................... Ø 9/40" to 1 9/16"
(with special twist drill bits: hole diameters of 9/32" to 1-1/8" on rails up to 3 1/2" thick)
(with broach cutters: hole diameters of 3/4" to 1-1/2" on rails up to 2 3/4" thick)
– Speed without load:.............................................................................................................................n° 230 rpm
– Gear sump:
– Recommended oil:................................................ SHELL SPIRAX S4 TXM or
...................................................................................... MOBIL SUPER MULTIGRADE 10-30-SAE or equivalents
– Weight: (LD-41PNY) .....................................................................................................................................35.9 lbs
– Weight: (LD-41PY) ...........................................................................................................................................43 lbs
– Combustion engine (EPA/CARB compliant):
– Type:............................................................................................4-cycle, overhead camshaft, single cylinder
– Model:.....................................................................................................................................Honda GX35NT STSC
– Operating angle:.............................................................................................................................................infinite
–Displacement:....................................................................................................................... 2.18 cu-in (35,8 cm3)
– Power (SAE J1349):..................................................................................................1,0 kW (1,3 HP) / 7000 rpm
– Fuel tank capacity: ............................................................................................................0.16 US gal (0,63 litre)
– Clutch:................................................................................................centrifugal with automatic intervention
– Start: ..........................................................................................................................................................by rope pull
– Ignition:............................................................................................................................. transistorized magneto
– Spark plug:.............................................................................................NGK CM5H or CMR5H or equivalents
– Fuel: .............................................................................................unleaded regular grade gasoline ( see § 12)
– Recommended oil:..................................................................................................SAE 10W-30, API SJ or later
– Acoustic Noise (Directive 2006/42/EC, annexe 1, point 1.7.4.2 letter u)
–The continuous equivalent weighted level (A)
of noise pressure at the working place LpA is equal to .............................................................. 96,2 dB (A)
– The maximum value of instantaneous weighted noise
pressure C at the working place LpCPeak is......................................................................................< 130 dB (C)
– The level of noise force produced by the machine LWA
is equal to................................................................................................................................................101,9 dB (A)
– Risks due to vibration (Directive 2006/42/EC, annexe 1, point 2.2.1.1.)
Tests carried out in compliance with the indications contained in EN ISO 5349-1/2 and UNI EN 28662-1
Standards, and under operating conditions much more severe
than those normally found, certify
that the weightedrootmeansquare infrequency
of the acceleration the upper limbs are exposed
is 2,69 m/sec
2
.
1. RAIL DRILL TYPE LD-41PNY

4
2.1) Pilot bits for controlling the cooling system:
for use with short broach cutters (7/8 " depth of cut)
– 1 pc PPC 2
for use with long broach cutters (2 " depth of cut)
– 1 pc PPL 2
2.2) Spacer, type DPE, for use with spiral bits and APE adaptor
for controlling the cooling system.
2.3) Adaptor, type ARE, for external cooling, to be used with the
SR5000 cooling unit.
2.4) Grub screw, M8x10
– 4 pcs for clamping cutters or bits onto spindle shaft.
2.5) Socket head cap screws, M6x16
– 4 pcs for securing positioning shoes to front plate.
2.6) Socket head cap screws, M6x25
– 4 pcs for securing special positioning shoes to front plate.
2.7) Range of tools:
– 1 pc 5 mm allen key
– 1 pc 6 mm allen key
– 1 pc 4 mm allen key with handle
– 1 pc spark plug key
– 1 pc brush
2.8) 3.4 fl oz (100 ml) oil bottle
for gear sump
(Accessories from pos. 2.1 to pos. 2.8 are included
in the “Kit of accessories for LD-41PNY” having
the code 6002682)
2.9) Type SR5000 cooling unit
2. ACCESSORIES SUPPLIED WITH THE DRILL

5
3.1) "DBG-Y" device with moving arm for clamping the drill
to the rail web and track fittings, complete with the TDB 6
termination.
Always supplied with drilling machine ref. LD-41PY
3.1.2) "DBG-GR" device for clamping the drill in correspondance
of guard rail.
Always supplied with drilling machine ref. LD-41PYGR
3. OPTIONAL ACCESSORIES (to be ordered separately)
3.1.1) "DBG-LY" device specific for clamping the drill to the girder
rails (for example 128 GR or GGR 118).With the specific shoes allows
the positioning on both sides of the rails, complete with theTDB 3
termination.
3.2) "TST50" two stage template (to be used with
specific DBG-AY clamping device)
This device enables the drilling of 150 lb and
aluminium composite contact rails from one side.
Restart of work stroke: 1,97”
Typical application:
– Aluminium composite rail.
– 150 lbs contact rail.

6
3.5) "MPAU" UNIVERSAL RAIL SHOE for rail or for special appli-
cationssuchas drilling #20 high speed switchpoints (positioning
not automatic).
3.5.1) "MPAU10" UNIVERSAL SHORT RAIL SHOE for rail or for
special applications (positioning not automatic).
3.4) “VAL MPA” suitable for storage of rail shoes, cutters
and accessories
• 15 1/2” (L) x 13 3/4” (W) x 2 1/4” (H)
3.2) “VAL P24” plastic carrying case for storing the drill complete with the device with moving
arm and accessories.
Also available VAL P24-CS plastic carrying case with folding handle and wheels.
3.2.1) “VAL LD-L” metal case for storing the drill complete with the DBG-LF2 device, and
VAL MPA tool case.
VAL P24-CS VAL LD-L

7
3.5.2) "MPAF..." SPECIFIC RAIL SHOES
Suitable for positioning the drill on running and guard rails
Enable the automatic position of the machine onthe drilling axis (H) of
each specific rail.
•Note: Please contact Cembrefor other types of rail.
RAIL SHOES DRILLING ON GUARD RAILS
RAIL SHOES DRILLING ON RUNNING RAILS
RAIL SHOES DRILLING ON GIRDER RAILS
H
H
(*) to be used with PFA 1 arbour extension and PPL5 Pilot Bit.
100 LB ARA-B 2 1/4”
112/115/119 LB RE 2 5/8”
115 LB-RE-3132 3 1/32”
132 LB RE 3 9/32”
136 LB RE 3 1/4”
MPAF 100 LB ARA-B GR
MPAF 115/119 LB RE GR
MPAF 115 LB-RE-3132
MPAF 132 LB-RE-3932
MPAF 136 LB-RE-314
RAIL SHOE
(Using DBG-GR clamp)
TYPE OF
RAIL
H
inches
128/149 LB 3”
128/149 LB 2 3/4”
149 LB 2 3/4”
GGR 118 2 3/8”
RI60/RI60N 2.87”
NP4A/NP4AM 2.87”
180-105 LB 2.87”
MPAF 128/149 LB GR
MPAF 128/149 LB GR 234
MPAF 149 LB GR 234
MPAF GGR 118
MPAF RI 60 N
MPAF NP4AM
MPAF BA9101
TYPE OF
RAIL
H
inches
RAIL SHOE
(Using DBG-LY clamp
and 2” depth cutters)
40 LB ASCE 3 1/16"
60 LB ASCE 3 1/16"
80 LB ASCE 2 3/16”
85 LB ASCE 2 17/64”
85 LB PRR 2 1/16”
85 LB PS 2 15/64”
90 LB ARA-A 2 9/16”
90 LB ASCE 2 45/128”
100 LB ARA-A 2 3/4”
100 LB ARA-B 2 65/128”
100 LB ASCE 2 65/128”
100 LB DY 2 5/8”
100 LB NYNH&H 2 39/64”
100 LB RE 2 45/64”
100 LB RE-HF 2 45/64”
100 LB PRR 2 9/32”
100 LB PS 2 31/64”
105 LB DY/110 LB RE
2 43/64”
112/115/119 LB RE 2 7/8”
122 CB 2 7/8”
127 LB DY 3 1/8”
130 LB RE/HF-A 2 3/4”
130 LB RE-HF 3 1/16"
130 LB HF-B 3 3/8”
130 LB PS 2 3/4”
131 LB RE 3 1/2”
132 LB RE 3 3/32”
133 LB RE 3”
136 LB RE 3 3/32”
136 LB LE VAL 3 1/16”
140 LB RE/140 PS
3”
141 LB AB/ 141 LB RE
3 3/32”
152 LB PS 3 3/4”
155 LB PS rail 3 3/8”
MPAF 40 LB ASCE
MPAF 60 LB ASCE
MPAF 80 LB ASCE
MPAF 85 LB ASCE
MPAF 85 LB PRR
MPAF 85 LB PS
MPAF 90 LB ARA-A
MPAF 90 LB ASCE
MPAF 100 LB ARA-A
MPAF 100 LB ARA-B
MPAF 100 LB ASCE
MPAF 100 LB DY
MPAF 100 LB NH
MPAF 100 LB RE
MPAF 100 LB RE-HF
MPAF 100 LB PRR
MPAF 100 LB PS
MPAF 105 LB DY
MPAF 115/119 LB RE
MPAF 122 CB
MPAF 127 LB DYM
MPAF 130 LB RE
MPAF 130 LB RE-HF
MPAF 130 LB HF-B
MPAF 130 LB PS
MPAF 131 LB RE
MPAF 132 LB RE
MPAF 133 LB RE
MPAF 136 LB RE
MPAF 136 LB LVM
MPAF 140 LB RE
MPAF 141 LB AB
MPAF 152 LB PS *
MPAF 155 LB PS *
TYPE OF
RAIL
H
inch
RAIL
SHOE

8
POSITIONING
GAUGE A B C
MRF Y10: suitable for drilling the following rails 100 ARA-B, 115 and 119 LB RE
MRF Y11: suitable for drilling the following rails 100 ARA-B, 105 DL&W
MRF Y12: suitable for drilling the following rails 115, 119, 132, 136, 140 LB RE, 130 and 155 PS
MRF Y13: suitable for drilling the following rails 80, 90 LB ASCE and 100 ARA-A
MRF Y14: suitable for drilling the 85 LB ASCE rail
MRF Y15: suitable for drilling the 130 LB RE and 136 LE.VAL rails
MRF Y: universal positioning gauge for all rail sizes
•Note: other positioning gauge sizes available upon request.
HOLES DISTANCES (inch)
2 21/32" 7 1/4" 5 1/2"
3 1/2" 6" 6"
2 21/32" 7 1/4" 5 1/2"
3 1/2" 4 3/4" 4 3/4"
2 23/32" 6" 7"
3 1/2" 6" 6"
3" 6" -
2 7/16" 5" -
2 7/16" 7" -
2 3/8" 7" -
2 3/4" 6 3/4" 6 3/4"
2 11/16" 5 1/2" 5 1/2"
3 1/2" 6" 6"
MRF Y10
MRF Y11
MRF Y12
MRF Y13
MRF Y14
MRF Y15
MRF Y16C
A C
RAIL END
B
3.6) JOINT BAR POSITIONING GAUGES
Positioning gauges MRF-Y... for drilling
joint bar holes at pre-defined
distances between rail end and
holes center lines.
A
IL
END
G
ES
ng

9
All the broach cutters allow automatic cooling by means of the SR5000 unit supplied with the drills.
15128
15130
15132
15234
TSC 1 1/8"
15138
TSC 1 1/4"
TSC 1 5/16"
15144
15146
TSC 1 1/2"
TSC 3/4"
01354
01355
01356
01357
01358
01359
01360
01361
01362
01363
01364
12218
3-12224
3-12226
3-12228
3-12230
3-12232
3-12236
BROACH
CUTTER
PILOT
BIT
HOLE
DIAMETER
(inch)
7/8"
15/16"
1"
1 1/16"
1 1/8"
1 3/16"
1 1/4"
1 5/16"
1 3/8"
1 7/16"
1 1/2"
3/4"
7/8"
15/16“
1“
1 1/16"
1 1/8"
1 3/16“
1 1/4"
1 5/16“
1 3/8"
1 7/16"
1 1/2"
9/16"
3/4"
13/16"
7/8"
15/16"
1"
1 1/8"
MAX.
DEPTH OF CUT
(inches)
Ref. PPC 2
Ref. PPL 2
3-10528
2 "
7/8 "
3 "
3.7) BROACH CUTTERS
These cutters rapidly produce high quality, accurate holes in a
single pass.The automatic lubrocooling system reduces friction
and eliminates heat build up during the drilling operation. Un-
der standard conditions a broach cutter can drill 40-50 holes,
depending on the hardness of the rail.

10
with adapter
3.8) SPECIAL SPIRAL TWIST BITS
Using these bits guarantees optimum performance during the drilling operations. As a rule, under
normal conditions, a spiral bit can drill 70-100 holes, depending on the hardness of the rail.
For tools of other types, check the dimensional compatibility (particularly the size of the attachment and the length).
APED...
Diam.
3.9) "LR2" LUBROCOOLERCONCENTRATE,1 or 5 gallons foroptimum operation
of both the broach cutters and the spiral bits.
Thisproduct ofvegetableorigin,tobe watereddowninthepercentage95%water,
5% oil, will provide a white colour mixture very effective for the drilling operations
resulting in no heating at the rail or the drilling machines.
3.10) "LR3" ANTIFREEZE CONCENTRATE of 1 or 5 gallons added to the lubro-
cooling mixture with the right percentage will maintain the lubrocooling mixture
fluid in negative temperature consitions.
LR 3
LR 2
PE70
PE95 C
PE130
PE160
PE190
PE220
PE130L-AR
PE3/4”-L1-AR
PE7/8”-L1-AR
PE1”-L1-AR
PE1-1/8”-L1-AR
PE1-1/4”-L1-AR
SPIRAL
BIT ADAPTER
HOLE
DIAMETER
(inch)
9/32”
3/8”
1/2”
5/8”
3/4”
7/8”
1/2”
3/4”
7/8”
1”
1 1/8”
1 1/4”
SPACER
APED70
APED 3/8 Y
APED 130
APED135/165
without adapter
without adapter
APED 130
without adapter
without adapter
without adapter
without adapter
without adapter
included in the APED 70
included in the APED 3/8 Y
included in the APED 130
included in the APED
135/165
DPE
DPE
included in the APED 130
DPE
DPE
DPE
DPE
not required
not required
not required
not required
not required
not required
TST50 + DBG-AY
TST50 + DBG-AY
TST50 + DBG-AY
TST50 + DBG-AY
TST50 + DBG-AY
TST50 + DBG-AY
ADDITIONAL
ACCESSORIES
without adapter
Diam.

11
02
17
35
03
01
Detail of the
max pressure valve
FIG. 3 – COOLANT UNIT
The type SR5000 coolant unit (01) consists of a tank complete with tube and maximum pressure
valve, fitted with a pump device for pressurisation, which must be connected to the attachment
(35) on the drill by means of its quick-coupling (03).
The delivery and shut-off of the lubrocoolant are controlled automatically, when drilling with
a broach cutter, by the guide bit; when drilling with a spiral bit, delivery and shut-off of the
fluid must be effected manually by operating the tap (02). The use of the lubrocoolant supplied
by Cembre, in the recommended concentrations, guarantees optimum use of the drilling tools.
Consumption of the lubrocoolant depends both on the variable degree of opening of the tap (02)
and the inner pressure of the tank: it is therefore advisable to open the tap a little when the tank is
at maximum pressure, while it must be fully opened when the pressure in the tank is low.
When using the coolant system, pay careful attention to the instructions on the tank label.
Warning:
•When the tank is not under pressure, check that the bush on the maximum pressure valve is
screwed right down.
•To fill tank with lubrocoolant, turn handle anticlockwise approximately 2 turns to release
handle locking mechanism. Remove handle/piston assembly from tank.
01 – Tank complete with hose
and max. pressure valve
02 – Tap
03 – Quick-coupling
17 – Vent valve
35 – Attachment valve
4. SR5000 COOLANT UNIT (Ref. to Fig. 3)

12
•The drill is equipped with a coolant attachment valve (35) and a vent valve (17) which are located
as shown (Fig. 3).
If under certain operating circumstances they need to be interchanged, proceed as follows:
– Using a 17 mm hexagonal spanner unscrew the vent valve from its seat.
– Using the 4 mm allen key provided with the drill, remove the appropriate coolant valve from its seat
and fit into the vent valve seat.
– Fit the vent valve into the into the vacant coolant valve seat.
•When temperatures fall below 32° F (0° C) the lubrocoolant
may freeze which could cause damage to the seals
contained in the drill coolant system.
It is therefore advisable, when storing the drilling
machine, to empty the lubrocoolant system
completely.
Proceed as follows (Fig. 4):
– Disconnect the quick coupling (03) from the
coolant attachment (35) on the drilling machine.
– Tilt the machine so that the coolant attachment is
at its lowest point allowing for natural drainage.
– Operate the advancing lever (36) to advance and
retract the drilling spindle.
– Gently shake the machine to expel all fluid.
ARE adaptor
FIG. 5 – ARE ADAPTOR
4.1) ARE adaptor
For use with type SR5000 coolant unit. The ARE adaptor is inserted in the quick-coupling of the
tank tube (Ref. to Fig. 5), it may be used to provide manual external cooling when cutters are
used to enlarge existing holes, or when using spiral bits not designed for automatic cooling.
If necessary the ARE adaptor can also be used to clean various parts of the drill, by means of the
lubrocoolant pressure jet, e.g. parts such as the tool clamping seat in the spindle shaft, seats for
the jig fixing screws, etc.
FIG. 4
35
36
03

13
FIG. 6
FIG. 7
The spindle is advanced by moving the lever
(36) (See Fig. 6 a). The lever is fitted with a
release pawl (39) which, when pressed, ren-
ders it independent of the hub and hence
the spindle; the operator can therefore easily
vary the angular position of the lever without
movement of the spindle (Fig.6).
6c - With the hub released, moving the lever towards the
operator produces a corresponding advance of this
spindle.
6a - Moving the lever (36) towards the operator produces
a corresponding advance of the spindle.
5.1) Adjustment of the advance lever
Themovementofthe levermustneverbe loose,
for adjustment proceed to tighten it by loading
the cup springs by means of the associated
self-locking nut, after removing the protective
cap (see Fig. 7).
6b - Withthe releasepawl(39)pressed,theleveris released
fromitshubandcan repeattheprevioustravelwithout
the spindle moving.
36
5. SPINDLE ADVANCE LEVER (Ref. to Fig. 6)

14
07
18 Pilot bit PP...
Pilot bit PPL ...
6.1) Assembling broach cutters (Ref. to Figs. 8-11).
6.1.1) Insert the pilot bit in the cutter from the side of the spigot.
6.1.2) Using the lever (36), position the spindle shaft (07) so that both grub screws (18) become
accessible and sufficient space is provided to insert the cutter; if necessary rotate the spindle
shaft manually and sufficiently by inserting the 4 mm male hexagon key in the appropriate
intermediate gear housing (33) in the crankcase of the drill corresponding to the feed handle
(71) (see Fig. 11).
6.1.3) Insert the cutter in the spindle shaft so that the two engaging dogs on the cutter spigot line
up with the grub screws (18).
6.1.4) Clamp the cutter by fully tightening the grub screws by means of the 4 mm male hexagon
key.
6.1.5) Check that the guide bit slides freely by applying slight pressure on it.
6.2) Assembling spiral bits (Ref. to Figs. 9 - 11)
6.2.1) Using the advance lever, position the spindle shaft so that both grub screws become acces-
sible and sufficient space is provided to insert the spiral bit; if necessary rotate the spindle
shaft manually and sufficiently by inserting the 4 mm male hexagon key in the appropriate
intermediate gear housing in the crankcase of the drill corresponding to the feed handle
(see Fig. 11).
FIG. 8 – ASSEMBLING BROACH CUTTERS
Short type broach cutter
Maximum drilling thickness: 1 inch
Long type broach cutter
Maximumdrillingthickness:2inches
Engaging dogs
6. PREPARING THE DRILL

15
33
71
6.2.2) Insert into the spindle shaft, the DPE spacer required to activate the coolant system.
If it necessary to use an APE... adaptor, the bit must first be fitted into the corresponding
APE adaptor and locked with the appropriate grub screw, then the DPE spacer inserted.
Note: Adaptors type APED… (e.g. APED 135/165) do not require use of DPE spacer.
6.2.3) Insert the bit-spacer unit in the spindle shaft so that the two engaging dogs on the bit spigot
line up with the grub screws. Press the bit-spacer unit home against the inner seat of the
spindle: this will enable the DPE spacer to open the coolant circuit (see Fig. 10).
6.2.4) Clamp the bit by fully tightening the two grub screws(18) using the 4 mm male allen key.
FIG. 10 – ASSEMBLING THE
BIT-SPACER UNIT
FIG. 9 – ASSEMBLING SPIRAL BITS
FIG. 11 – MANUAL SPINDLE ROTATION
07
18
DPE *
DPE
Bits PE ... (e.g. PE70)
Bits PE ... (e.g. PE 190)
APE ...
* use only for APE, not required for APED

16
7. RAIL DRILL TYPE LD-41PY
FIG. 12 – DRILL WITH DBG-Y CLAMPING DEVICE
reference
rod
TDB 6
M 8x25 screws
and spring washers
Ref. LD-41PY consist of the LD-41PNY basic drill (see page 2) complete with the DBG-Y moving arm
device for clamping to the rail web and the track fittings (Refer to Fig. 12).
The DBG-Y clamping device consists of:
– Clamping unit
– Type TDB6 standard termination.
– Socket head cap screws M8x25 (2 pcs).
– Spring washers (4 pcs).
– Reference rod.

17
7.2) Assembly of the DBG-Y clamping device on the drill
The DBG-Y clamping device is fitted to the front plate of the drill, centred by means of the refer-
ence pin supplied and secured with the two socket head cap screws M8x25 (35) also supplied. The
assembly is illustrated in Fig. 14.
FIG. 13 – ASSEMBLY OF THE TERMINATION
7.1) Assembling of the termination of the DBG-Y device with moving arm for clamping the drill
to the rail web and track fittings.
The termination TDB 6 of the DBG-Y device, with moving arm, have been designed for adaptation to
the different operating conditions on the rails and track fittings; their assembly is shown in Fig. 13.
• When disassembling the TDB 6 termination ensure that, after removing the pivot, the complete
assembly is slid away downward without acting on the holding plate.
holding plate

18
FIG. 14 – ASSEMBLY OF DBG-Y
CLAMPING DEVICE
DBG-Y Clamping device
Rail drill front plate
35
FIG. 15 – ASSEMBLY OF POSITIONING SHOES
7.3) Assembly of positioning shoes (Ref. to Fig. 15)
7.3.1) The type MPAF.. and MPAU positioning shoes are secured to the front plate (22) of the drill
by means of the two socket head cap screws M 6x16 supplied.
screws M6x16
MPAF...
MPAU
reference pin
22

19
FIG. 16 – POSITIONING OF THE DRILL
11
03
36
07
18
7.4) Clamping to the rail web (Ref. to Fig. 16)
The special shape of the positioning shoes, each corresponding to the type of rail, enables the drill
to be positioned quickly, accurately and safely on the element to be drilled.
To position the drill, complete with the clamping termination (§ 7.1) and the positioning shoe (§
7.3) suitable for the type of rail to be drilled, proceed as follows:
7.4.1) Withdraw the spindle shaft (07) completely by means of the lever (36).
7.4.2) Bring the moving arm (03) of the clamping device into the fully open position by means of
the handwheel (11).
7.4.3) Place the drill on the rail at the point where the drilling is to be carried out, and clamp it by
tightening the handwheel (11) right down: the positioning shoe will automatically position
the cutter or spiral bit in line with the desired axis; if accurate positioning relative to the
longitudinal axis of the rail is required, use the reference rod (18).

20
<>
Check engine oil level before operation (see § 13.2.4)
Switch on the cooling system before starting the drill (see § 4)
8.1) Drill fitted with “short” type broach cutter (for drilling thicknesses of up to 1").
The drilling sequence may be started with the drill fitted with the broach cutter (§ 6.1), clamping
termination (§ 7.1), positioning shoe (§ 7.3), the drill being clamped to the rail
(§ 7.4), as follows:
8.1.1) Connect the female quick-coupling of the SR5000 coolant unit to the male coupling (35)
on the drill.
8.1.2) Open the tap (02) fitted on the coolant unit hose.
8.1.3) Using the lever (36) bring the guide bit
almostincontactwith therail(Fig.17a);
keeping the release pawl (39) pressed,
releasetheleverfromitscupand return
intotheinitial position(Fig.17b),which
will enable the travel of the lever (36)
to be used in the most advantageous
way.
FIG. 17 – DRILLING
Fig. 17c
Fig. 17a
Fig. 17b
36
39
8. DRILLING (Ref. to Figs. 17-18)
Table of contents
Other Cembre Drill manuals
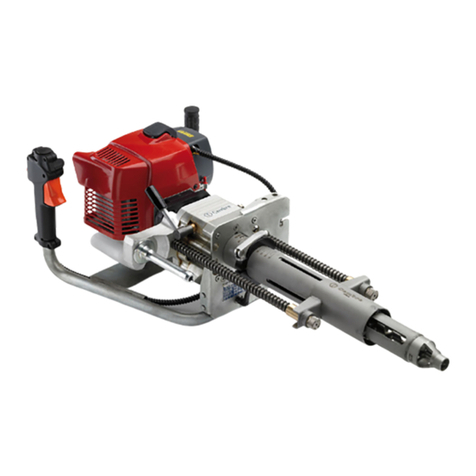
Cembre
Cembre SD-9P-ECO User manual
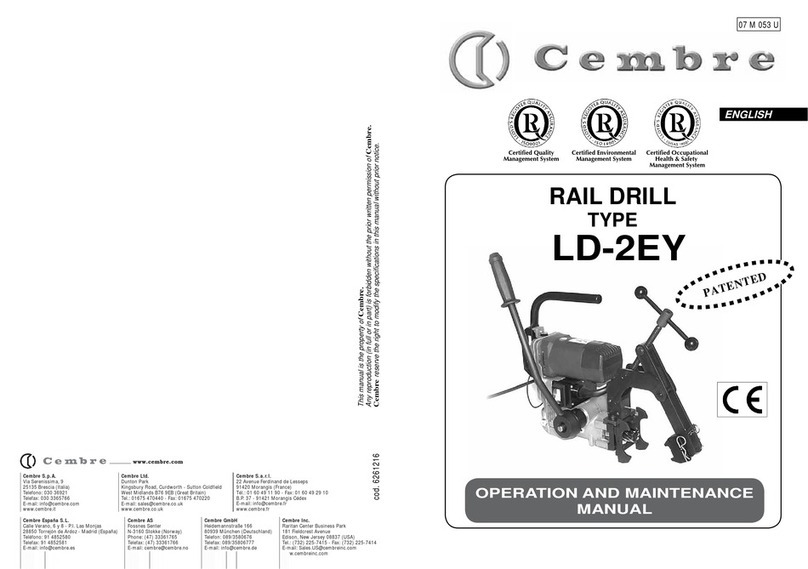
Cembre
Cembre LD-2EY User manual
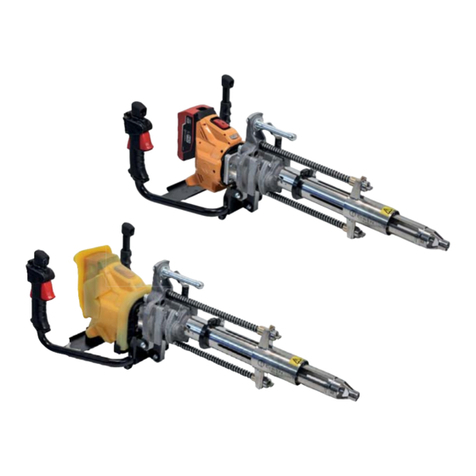
Cembre
Cembre SD-19BR User manual
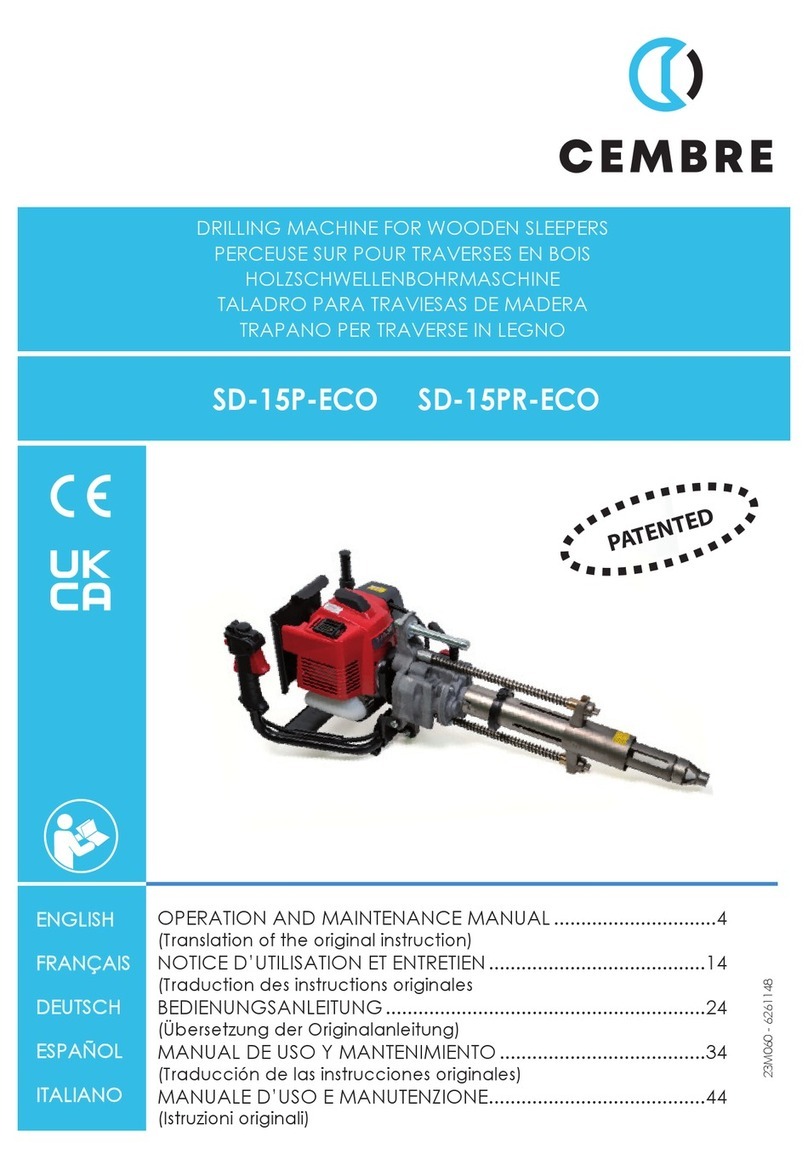
Cembre
Cembre SD-15P-ECO User manual
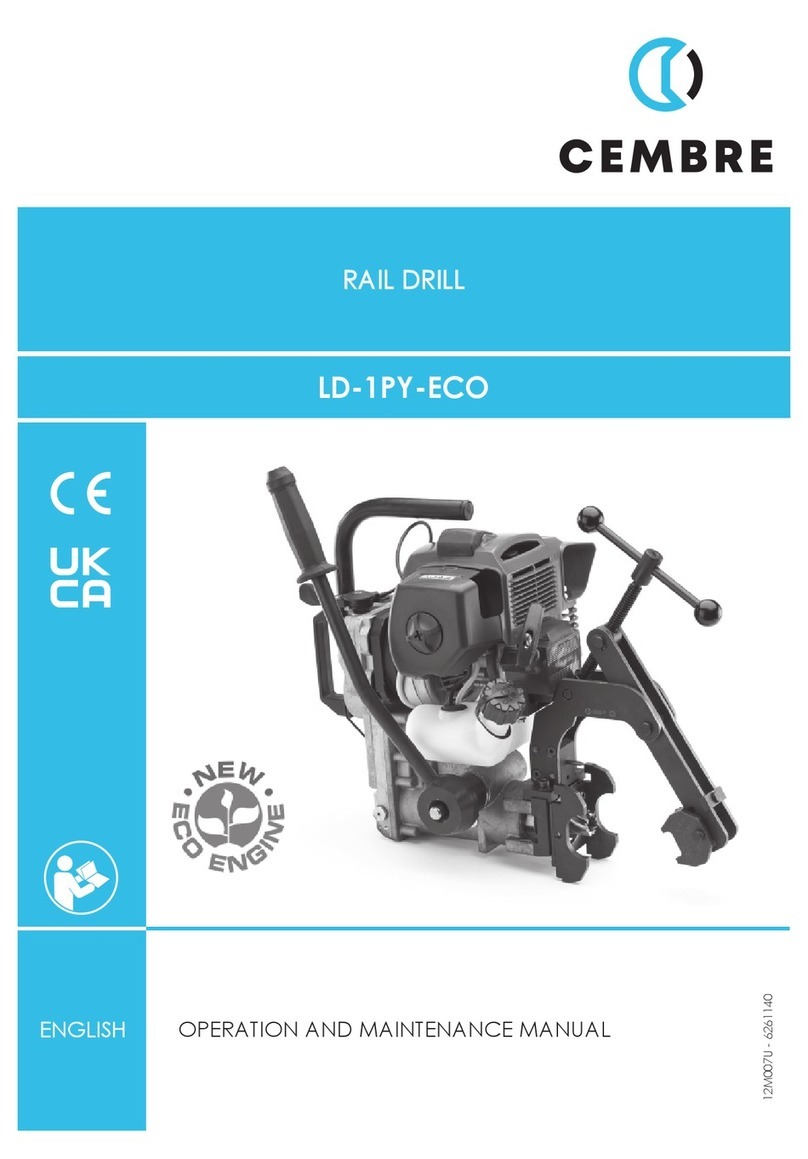
Cembre
Cembre LD-1PY-ECO User manual

Cembre
Cembre LD-1P-ECO User manual
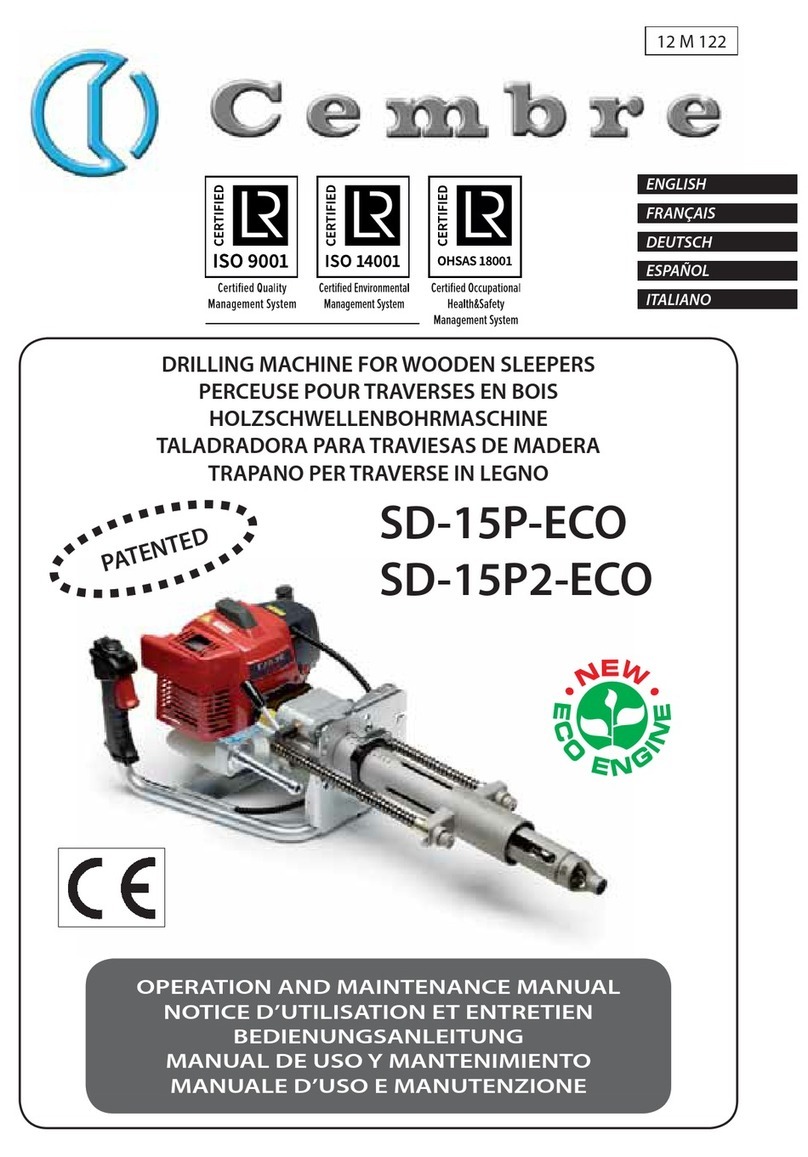
Cembre
Cembre SD-15P-ECO User manual

Cembre
Cembre LD-16B Manual

Cembre
Cembre SD-9P-ECO User manual
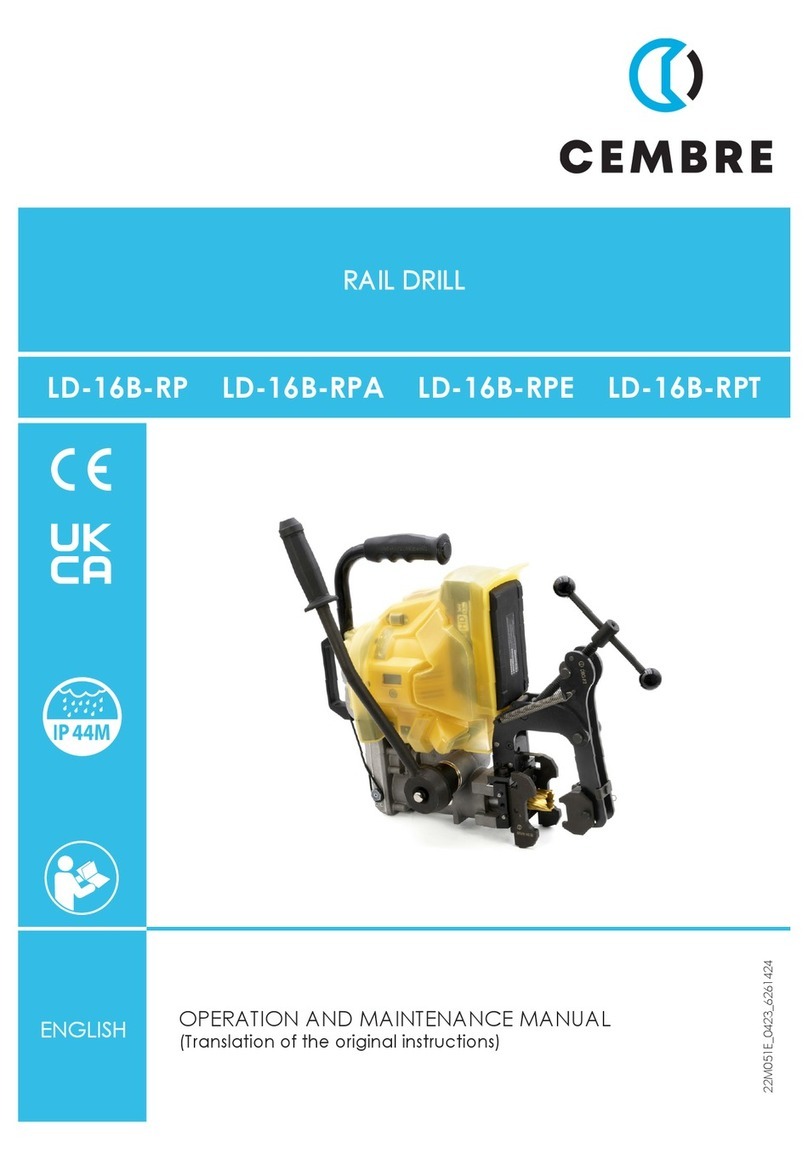
Cembre
Cembre LD-16B-RP User manual
Popular Drill manuals by other brands

Makita
Makita DF001GZ01 instruction manual

HIKOKI
HIKOKI DS14DSDL Handling instructions

Campbell Hausfeld
Campbell Hausfeld DG190600CK S Operating instructions and parts manual
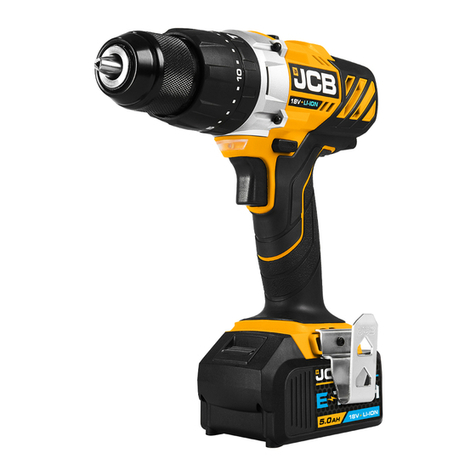
jcb
jcb JCB-18CD Instructions & user's manual
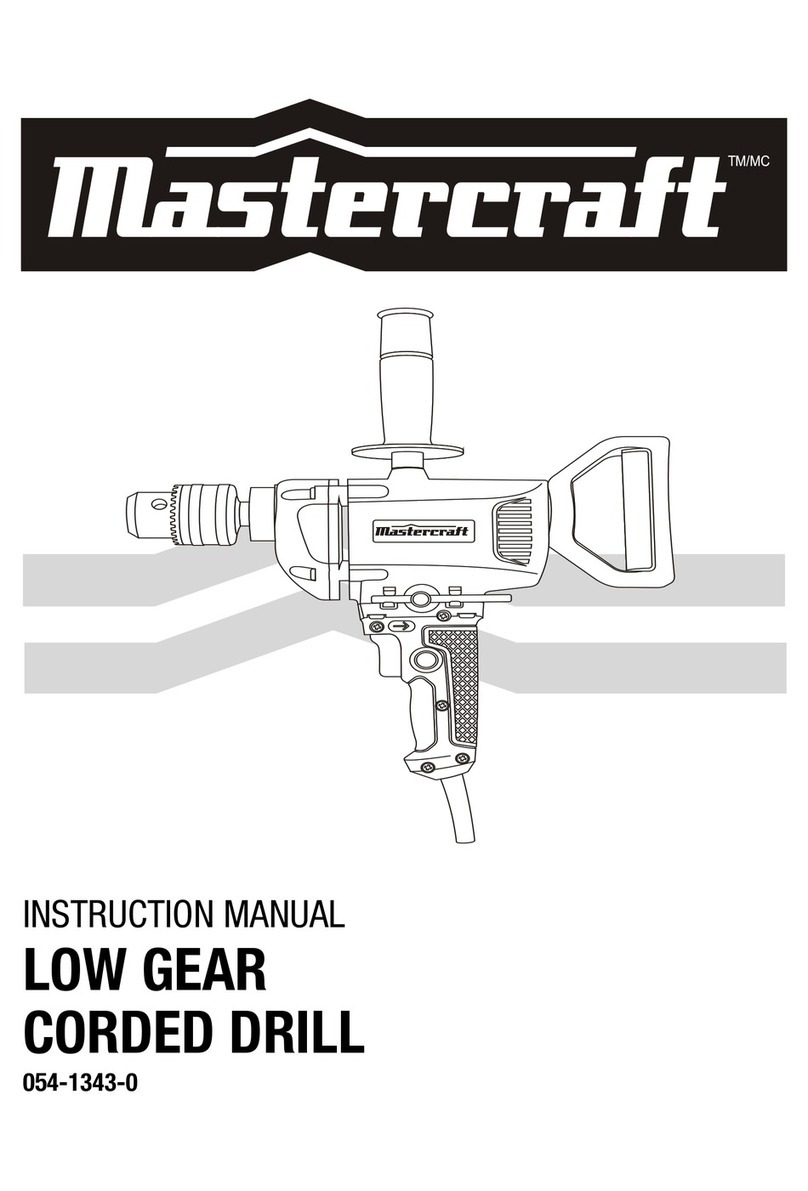
MasterCraft
MasterCraft 054-1343-0 instruction manual

Black & Decker
Black & Decker TP550 manual