CPS BlackMax 2 Valve Series User manual

BCK®
DIGITAL SERIES
us tent No. 9,3,161
OWNER'S MANUAL (English)
Test Equipment Depot - 800.517.8431 - 99 Washington Street Melrose, MA 02176
TestEquipmentDepot.com







n ,r n
2Er0
[SET]
8
◄-:
SH:
■:
n5.nn
U lJU



,nun
cu-tu
ig
n5.nn
U U
APO
0390
mic
m35
ur
mlc
Vac
[CLR]
Test Equipment Depot - 800.517.8431 - 99 Washington Street Melrose, MA 02176
TestEquipmentDepot.com





16
MD50 2 Valve Manifold [FIG.26] MD100 4 Valve Manifold [FIG.27]
1.) Connect Low (A) and High (B) Service hoses to
service ports (E) and (D) 1.) Connect Low (1) and High (2) Service
hoses to service ports (L) and (H)
2.) Connect hose from tee (C) to Inlet port of
Vacuum Pump. Use the fitting on the tee with the
valve core.
2.) Connect 3/8” hose from port (4) to
Vacuum pump inlet port
3.) Connect another hose from the open port of tee
(C) to the valve of a refrigerant supply tank. Supply
tank valve must be off.
3.) Connect another hose from port (3) to
refrigerant supply tank’s valve. Supply tank
valve must remain off.
4.) Check Low and High Side pressure readings, if zero PSIG or lower continue. If pressure reads
higher than 0 PSIG, run Refrigerant RECOVERY
5.) Once it is determine no refrigerant is present in system, start vacuum pump.
6.) Open low side valve (A) 6.) Open low side valve (A)
Open high side valve (B)
7.) Open high side valve (B) 7.) Open valve (D). Open valve (C), but do
not open supply tank valve.
8.) Note: A Vacuum Gauge (VG200) can be
connected via service tee to equipment to monitor
vacuum pump’s progress.
8.) Note: Optional Vacuum Gauge Accessory
(MDXVG) can be connected via service tee
to the equipment to monitor vacuum pump’s
progress.
9.) Evacuate system according to manufacturer’s specifications; close high and low side hand
knobs.
10.) Disconnect Vacuum Pump hose from valved
port on Tee (C). The valve core will seal when hose is
removed, thus preserving the vacuum.
10.) Close valve (D) once the required
vacuum level is reached. Turn off vacuum
pump.
The unit is now ready for Vacuum Leak test or High Side Charging Procedure.
EVACUATING PROCEDURES
CHARGING PROCEDURE - LOW SIDE
MD50 2 Valve Manifold [FIG.26] MD100 4 Valve Manifold [FIG.27]
1.) The following instructions are to add charge to a pressurized system, known as “topping off”.
2.) Connect Low (A) and High (B) Service hoses to
service ports (E) and (D). All valves should be closed. 2.) Connect Low (1) and High (2) Service hoses
to service ports (L) and (H)
3.) Connect a hose from the open port on tee (C) to
valve fitting on supply tank. 3.) Connect a hose from port (3) to refrigerant
supply tank’s valve.
4.) Open supply tank valve. For blends, turn tank upside down or make sure liquid refrigerant is being
charged.
5.) Push valve core on tee (C) until refrigerant comes
out. This will purge the hose from the supply tank.
5.) Open valve (C). With hose disconnect from
port (4), slightly open valve (D) until
refrigerant comes out. This will purge the hose
from the supply tank.
6.) Turn refrigerant system on. Monitor pressure gauges. Use superheat and subcooling features to help
determine when charge amount is optimal.
7.) Slightly open Low Side Valve (A) to allow liquid refrigerant to flow into low side of equipment. Caution
should be used when charging liquid refrigerant into low side of a refrigeration system.
8.) Close Low Side valve (A) when desired amount of refrigerant has been added. Note the use of a scale
is required.
9.) Let equipment temperatures and pressures stabilize. Check superheat and/or subcooling levels.
Repeat charge if necessary.
10.) Once done, close off supply tank valve and disconnect all hoses. Use Caution as all hose connections
are under pressure.
Once charge is complete, an electronic refrigerant leak detector should be used to confirm leaks do not exist.

17
CHARGING PROCEDURE - HIGH SIDE
MD50 2 Valve Manifold [FIG.26] MD100 4 Valve Manifold [FIG.27]
1.) A scale should be used to weigh in the charge. Place tank on scale so liquid refrigerant is supplied.
2.) Open Supply tank valve to fill manifold with liquid refrigerant.
3.) Set scale to record charge amount.
4.) Open High Side Valve (B). Monitor weight reading.
5.) Once desired charge amount has been reached, close High Side Valve (B) and supply tank valve.
6.) Start refrigeration system. Open Low Side valve (A) to allow all remaining refrigerant in manifold and
service hoses to charge into system.
7.) Close Low Side Valve (A). 7.) Close Low Side Valve (A) and Valve (C).
8.) Monitor Low and High Side pressures. Superheat and subcooling features of manifold can be used at this time.
9.) Disconnect service hoses from equipment. Use Caution as all hoses are under pressure.
Once charge is complete, an electronic refrigerant leak detector should be used to confirm leaks do not exist.
High Side Charging should be done on a completely evacuated system.
APPENDIX A (MANIFOLD SPECIFICATIONS)
High side pressure range -14.7 to 800.0 PSIG (-1.0 to 55 bar)
Low side pressure range -14.7 to 800.0 PSIG (-1.0 to 55 bar)
Pressure reading accuracy +/- 1% of reading or +/- 0.5 PSIG (+/- 0.05 bar)
Pressure reading resolution 0.5 PSIG (0.05 bar)
High and low side burst pressure 1500.0 PSIG (103.4 bar)
High side temperature range -58.0 °F to 302 °F (-50 °C to 150°C)
Low side temperature range -58.0 °F to 302 °F (-50 °C to 150°C)
Temperature reading accuracy +/- 0.36 °F (+/- 0.2°C)
Vacuum indication accuracy +/- 10 microns (requires MDXVG accessory)
SH, SC and saturation temperature accuracy +/- 0.5°F (+/- 0.3°C)
Instrument working temperature -4.0 °F to 122°F (-20°C to 50°C)
Instrument working RH range 0% to 100% non-condensing
Total number of stored refrigerants 93
APO (Automatic Power Off) 10 minutes. Can be disabled by user.
MD100 size (L x H x W) 8.1” x 3.5” x 7.0” (20.5 cm x 8 9 cm x 17.8cm)
MD50 size (L x H x W) 8.1” x 2.5” x 7.0” (20.5 cm x 6.4 cm x 17.8cm)
MD100 weight 3.3 lb. (1.5 kg)
MD50 weight 3.0 lb. (1.4 kg)
Display Life (Using 4 industrial
alkaline AA batteries (included)
Backlight full ON: 25+ hrs. continuous duty
Backlight full OFF: 60+ hrs. continuous duty
Display Life Using 4 Rechargeable
NiMH AA batteries (not included):
Backlight full ON: 20+ hrs. continuous duty from full charge
Backlight full OFF: 50+ hrs. continuous duty from full charge
APPENDIX B (MDXVG VACUUM GAUGE ACCESSORY SPECIFICATIONS)
Sensor Type Self - heated thermistor bridge with integral temperature compensation from
0 to 50 °C (32 to 122 °F).
Display Pressure Range
AUTO-RANGING SCALES:
0 to 99 microns 1 micron resolution
100 to 990 microns 10 micron resolution
1000 to 9900 microns 20 micron resolution
10000 to 25000 microns 50 micron resolution
above 25000 microns Will display low side pressure reading, in
selected unit.
Accuracy +/- 10% of reading or +/- 10 microns, whichever is greater
Operating Temperature Range
Compensated (accuracy as stated): 0°C TO 50°C (32°F TO 122°F)
Non-compensated (add +/- 0.5% of reading error for every °C outside
compensated range): -10 to 0°C (14 to 32°F)
Operating and Storage Humidity 0 to 95%, non-condensing
Storage Temperature -40 to 85°C (-40 to 185°F)


19
APPENDIX F (LIMITED WARRANTY)
APPENDIX G (REFRIGERANTS STORED IN MEMORY)
BLACKMAX digital manifolds are covered by a CPS Products, Inc. LIMITED WARRANTY.
CPS Products, Inc. warrants, to the original purchaser, that its BLACKMAX line of digital
manifolds and accessories are free from defects in assembly, materials and workmanship for
1 year from the date of purchase, or 15 months from the date of manufacture, whichever is sooner. If any
BLACKMAX product is believed to be defective it must be returned to CPS Products. If the product is found to be
defective, CPS will repair or replace the item(s), at our option, at no charge.
This warranty does not apply to products or accessories that have been altered, misused, submerged, exposed
to extreme heat or cold, lightning str kes, or electrical voltage exceeding published product specifications. This
warranty also does not apply to products that are simply in need of routine field service maintenance.
To assure your BLACKMAX purchase is on file with CPS Products, please fill in a
Product Registration form and mail to CPS within 15 days from the date of purchase, along with a copy of the
original sales receipt. Return of the registration form is not required to be covered by the Limited Product Warranty.
To process a warranty claim, please contact CPS USA at 1-800-277-3808 or CPS Products
N.V. (Belgium) at (32) 3 281 30 40; or CPS Australia at 08 8340 7055, within 15 days of
discovering defects in assembly, materials, or workmanship. CPS will provide a return
authorization number (RGA #). Do not attempt to repair BLACKMAX products. CPS has the sole right to determine
if a claim is valid and if compensation is justified.
THE FOREGOING WARRANTY IS IN LIEU OF ALL OTHER EXPRESS WARRANTIES. TO THE EXTENT ALLOWED
BY LAW, ANY IMPLIED WARRANTIES OF MERCHANTABILITY OR FITNESS FOR A PARTICULAR PURPOSE
ARE LIMITED TO THE DURATION OF THE LIMITED PRODUCT WARRANTY. IN NO CASE SHALL CPS
PRODUCTS INC. HAVE ANY LIABILITY FOR SPECIAL, INCIDENTAL OR CONSEQUENTIAL DAMAGES OF ANY
KIND, INCLUDING BUT NOT LIMITED TO: THE LOSS OF THE USE OF THE PRODUCT OR ANY ASSOCIATED
EQUIPMENT, COST OF ANY SUBSTITUTED EQUIPMENT, FACILITIES OR SERVICES, DOWNTIME, THE
CLAIMS OF THIRD PARTIES, DAMAGE TO PROPERTY OR PERSONAL INJURY. SOME JURISDICTIONS DO
NOT ALLOW LIMITS ON WARRANTIES OR ON REMEDIES FOR BREACH IN CERTAIN TRANSACTIONS. IN
SUCH JURISDICTIONS, THE LIMITS IN THIS PARAGRAPH MAY NOT APPLY.
THIS WARRANTY GIVES YOU SPECIFIC LEGAL RIGHTS, AND YOU MAY ALSO HAVE OTHER RIGHTS WHICH
VARY FROM JURISDICTION TO JURISDICTION.
R11 R13B1 R290 R407D R416A R424A R504
R113 R141B R32 R407F R417A / M059 R425A R507A
R114 R142B R401A R408A R426A R508A
R115 R143 R401B R409A R418A R427A /
M089 /
FX100
R508B
R116 R143A R401C R41 R419A R509A
R12 R152A R402A R410A R420A
R123 R176 R402B R410B R421A R428A R600
R123A R21 R403A R411A R421B R434A R600A
R1234YF R218 R403B R411B R422A / M079 R437A /
M049PLUS
R601
R124 R22 R404A R412A R601A
R125 R23 R405A R413A /
M049 R422B R438A /
M099
R744
(Sub-critical
range only)
R1270 R236ea R406A R422C R500
R13 R236FA R407A R414A R422D / M029 R501
R134 R245ca R407B R414B R502
R134A R245fa R407C R415A R423A / 39TC R503
MD50 and MD100 manifold series are pre-loaded with 93 of the most common refrigerants.

APPENDIX H {ERROR INDICATOR SCREENS)
BCK ®
20 73-154 REV B
Test Equipment Depot - 800.517.8431 - 99 Washington Street Melrose, MA 02176
TestEquipmentDepot.com
This manual suits for next models
7
Table of contents
Other CPS Measuring Instrument manuals
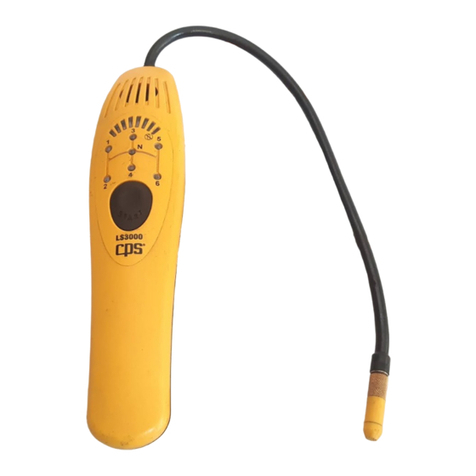
CPS
CPS ELIMINATOR LS3000 User manual

CPS
CPS IAQPRO SmartAir User manual

CPS
CPS HVP-252 User manual

CPS
CPS IAQPRO SmartAir User manual
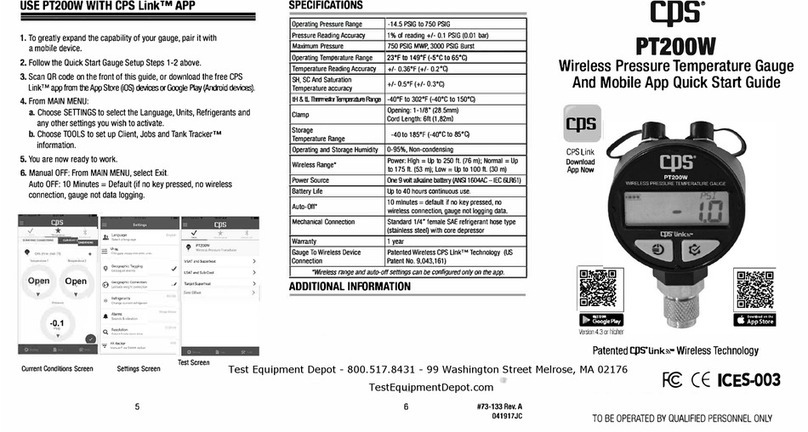
CPS
CPS PT200W User manual

CPS
CPS FlexOM-PP User manual

CPS
CPS Leak-Seeker LSCG User manual
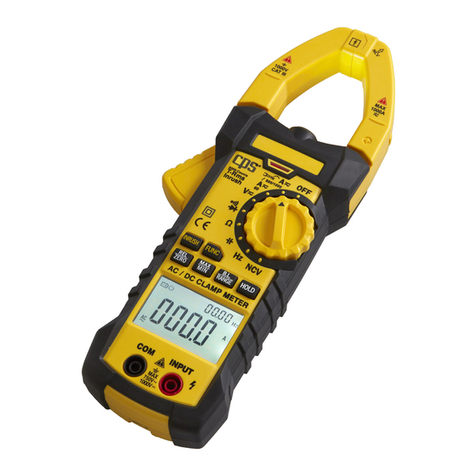
CPS
CPS AC750 User manual
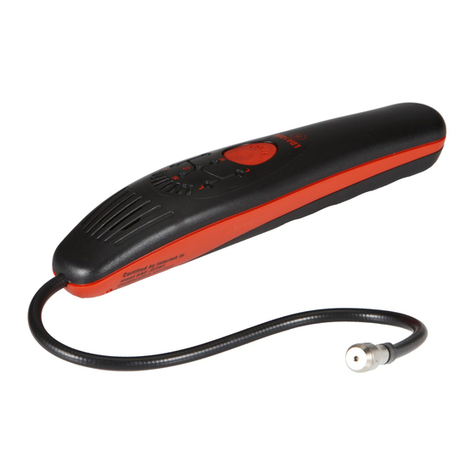
CPS
CPS Pro-Set LDA1000H User manual

CPS
CPS AC750 User manual