Delta DTV Series User manual

1
Introduction
Thank you for choosing this product. This manual provides users with instructions on how to safely
operate a robot and information on Delta 6-axis industrial robot series.
This product is intended for
•Standard 6-axis robots equipped with electric control box DCV-2J00-AA
•EU 6-axis robots equipped with electric control box DCV-2J00-CA

2
General Precautions
For your safety, please read this manual carefully before operating the robot. This manual includes:
•HMI operation functions and descriptions.
•Inspection and maintenance.
•Troubleshooting.
For safety reasons, we conduct specialized personnel training according to different robot applications,
and this manual is intended for the following users:
•System integration designers.
•Installation workers.
•Personnel conducting test run and tuning.
•Maintenance or inspection workers.
•Equipment operators.
Before using this product, please read this manual carefully to ensure correct use. Also, please keep it
in a safe place for future reference. Be sure to observe the following points before you finish reading
this manual:
•The installation environment must be free of moisture, corrosive and flammable gases.
•Do not disassemble the teach pendant or change its internal wiring when powered on.
•Before powering on, please check that the emergency stop device of the teach pendant is ready to
activate at all times.
If you have any other questions, please consult the distributor or Delta Customer Service Center.

3
Safety Precautions
Delta robots can be controlled by a computer via the DRAStudio software or the handheld HMI DTS-
2xM series by operating the drive to control the robot. The robot uses the latest control architecture,
including a controller with high-speed computing capability, to control the robot more precisely for
precise robot actions. The handheld HMI cannot be operated separately from the drive. For your
safety, please pay attention to the safety of the working environment and set up protective fences
around the robot to ensure user safety during operation. Delta robots can be used in industrial
applications and should be installed in the wiring (electric) box specified in the user manual (drives,
cables, and motors must be installed in accordance with UL Environment Class 1 minimum installation
environment requirements). During acceptance inspection, installation, wiring, operation, maintenance
and inspection, please observe the following safety precautions at all times.
Meaning of “DANGER”, “WARNING” and “STOP” signs:
Please use the servo drive and the servo motor according to the specified method,
otherwise it may cause fire or equipment failure.
Indicates potential hazards that may cause moderate personal injury, serious
product damage, or even failure.
Indicates absolutely prohibited actions that may cause product damage or even
failure.
Acceptance Inspection
Please use the robot according to the specified method, otherwise it may cause fire
or equipment failure.
Installation Notes Do not expose this product to moisture, corrosive and flammable gases, etc.,
otherwise it may cause electric shock or fire.

4
Operation Notes Please read this manual carefully before using to ensure correct usage and
maintenance worker safety.
Do not wear loose clothes, ties, rings, or bracelets and ensure to wear the hairnet to
prevent them from getting caught in the machine by accident and cause injury or
danger during operation.
To stop using the robot, please turn off the power and isolate the energy source until
the robot stops completely before leaving.
Make sure that there is no one inside the fences before operating the robot.
Do not chat with each other when operating the robot. Otherwise, it may cause
dangers such as robot collisions or personal injury.
When teaching the robot for the first time, do not stand within the robot's motion
range to avoid danger due to being unfamiliar with the operation.
Use slow speed operation when operating the robot manually for the first time,
otherwise it may cause damage to the robot or dangers such as personal injury.
To remove the teach pendant cable on the controller, please do so when it is
completely powered off, otherwise it may cause damage to the teach pendant.
Adjust the parameter settings before operating the robot. If not adjusted correctly,
the robot may be out of control or malfunctioning. Make sure that the emergency
stop device can be activated at any time before operating the robot. When powering
on, make sure that the robot remains stationary and does not move due to inertia or
other reasons.
Do not touch any rotating parts when the robot is operating, otherwise it may cause
personal injury.
Do not change any parts on the handheld teach pendant, including the emergency
stop and the enable switch. Doing so may lower the safety performance and level or
even lose safety protection.
Do not short-circuit the safety protection signal on the controller in any way. We shall
not be liable for any occupational accident.
When operating the robot, do not allow anyone to approach or stand within the
working range of the robot, otherwise it may cause personal injury.
Do not unplug any cables on the controller while the robot is operating, otherwise it
may cause damage to the controller.
To prevent accidents, please separate the jigs of the robot before the first
commissioning. If an operation error occurs after the servo motor and the robot are
running, it may cause damage to the robot as well as personal injury. It is strongly
recommended to test if the robot is working normally without any load before
connecting loads to avoid unnecessary hazards.
Do not touch the control box during operation, otherwise it may cause burns or
electric shocks due to high temperature.
Do not touch the controller and the inside of the robot, otherwise it may cause
electric shocks. Do not remove the handheld HMI when the power is on,
otherwise it may cause electric shocks and damage to the handheld HMI. Do
not touch the wiring terminals within 30 minutes after turning off the power as
residual voltage may cause electric shocks. Do not modify the wiring while the
power is on, otherwise it may cause electric shocks or personal injuries. The
installation, wiring, repair, and maintenance of this robot must be performed
by trained and qualified electricians only.
Maintenance
and Inspection

5
Circuit Wiring Remove the terminal block from the servo drive when performing wiring. Insert
only one wire into the wire socket of the terminal block. When inserting wires, do
not short-circuit the core wires and adjacent wires. Check whether the wiring is
correct before powering on.
Do not turn the power on and off frequently. If you need to switch the power
continuously, please do so once every minute or longer.

6
Basic Inspection
Inspection Item
Inspection Content
General inspection
•Regularly check the connection between the HMI and the
equipment for loose screws.
•Protect the HMI from hazardous gas or dust if they are present.
Pre-operation Inspection
(control power not
supplied)
•The wiring should be correct, otherwise abnormalities may occur.
•Check the inside of the HMI for conductive objects such as
screws or metal sheets, or flammable objects.
•When an electronic instrument used near the HMI is subject to
electromagnetic interference, use instruments for adjustment to
reduce the electromagnetic interference.
•Make sure that the supply voltage level of the HMI is correct.
Pre-run Inspection
(control power supplied)
•Check if the power indicator lights up. Check if the robot
operates normally.
•If abnormalities occur to the HMI, please contact your dealer or
Delta Customer Service Center.

7
Structure of this manual
Chapter 1 HMI Basic Operation Interface
This chapter explains the connection precautions and methods of the teach pendant and the buttons
and switches required for operation.
Chapter 2 Tab Operations and Function Instructions
This chapter describes how to use the operating functions of the teach pendant.

8
Table of Contents
Handheld Teach Pendant DTV Series··································0
Introduction ··································································································· 0
General Precautions························································································ 2
Safety Precautions·························································································· 3
Basic Inspection ····························································································· 6
Structure of this manual ··················································································· 7
1HMI Basic Operation Interface ··································· 12
1.1 Hardware Interface·················································································13
1.2 Brief Introduction to the Operating Environment············································14
1.3 Teach Pendant Hardware Button Functions·················································15
1.4 Touch screen ························································································18
2Tab Operation and Function Instructions···················· 24
2.1 Main ····································································································25
2.2 Edit/RL·································································································27
2.2.1 Create a New Project···································································29
2.2.2 Opening an Old Project ································································31
2.2.3 Editing Programs ········································································32
2.3 Execution (Exe) ·····················································································35
2.4 Points ··································································································36
2.4.1 Global Point···············································································37
2.4.2 Local Point·················································································38
2.4.3 User Frame Settings····································································39
2.4.4 Tool Frame Settings ····································································43
2.4.5 Work Space Settings ···································································47
2.5 JOG Settings·························································································49
2.6 IO Monitor (I/O)······················································································50
2.7 Info······································································································51
2.7.1 Alarm Info··················································································51
2.7.2 Controller Info·············································································52
2.7.3 Modbus Info···············································································52
2.8 System·································································································55
2.8.1 Home························································································55
2.8.2 Controller IP···············································································56
2.8.3 Other························································································57
2.9 Servo Setting·························································································61
2.10 External Axis·······················································································63
2.10.1 External Axis Information······························································63
2.10.2 External Axis Jog ········································································64
2.10.3 External Axis Servo Switch ···························································65
2.10.4 External Axis Point Teaching·························································66

9
(This page is intentionally left blank.)

10
List of Figures
Figure 1-1 Electric control box T1 simple wiring diagram ·········································· 14
Figure 1-2 Startup screen·················································································· 17
Figure 1-3 Back of the handheld teach pendant······················································ 17
Figure 1-4 SD card slot of the handheld teach pendant············································ 18
Figure 1-5 Touch screen structure······································································· 18
Figure 2-1 Main screen - not logged in ·································································25
Figure 2-2 Main screen - enter privilege password·················································· 26
Figure 2-3 Main screen - logged in (robot operation mode: T1, TP operation mode: Enable)
············································································································· 26
Figure 2-4 Edit/RL - before opening a project························································· 27
Figure 2-5 Edit/RL - after opening a project··························································· 27
Figure 2-6 Edit/RL - add a new project ·································································29
Figure 2-7 Edit/RL - enter the project name··························································· 30
Figure 2-8 Edit/RL - new project created······························································· 30
Figure 2-9 Edit/RL - open a project······································································ 31
Figure 2-10 Edit/RL - project opened ··································································· 31
Figure 2-11 Edit/RL - select the input field····························································· 32
Figure 2-12 Edit/RL - manual editing···································································· 33
Figure 2-13 Edit/RL - write programs by selecting commands···································· 34
Figure 2-14 Edit/RL - use Cancel, Replace, or Insert ··············································· 34
Figure 2-15 Edit/RL - delete a command line························································· 35
Figure 2-16 Execution (Exe) ·············································································· 35
Figure 2-17 Points··························································································· 36
Figure 2-18 Points - specify global points······························································ 37
Figure 2-19 Points - local points of the project test·················································· 38
Figure 2-20 Points - setting the local point parameters············································· 39
Figure 2-21 Points - user frame origin setting························································· 40
Figure 2-22 Points - user frame +X direction point setting········································· 41
Figure 2-23 Points - user frame XY plane point setting (determine +Y direction) ············ 41
Figure 2-24 Points - page for entering teaching points ············································· 42
Figure 2-25 Points - entering point data respectively ··············································· 42
Figure 2-26 Tool size: height, width, and angle······················································· 44
Figure 2-27 Points - tool frame setting·································································· 44
Figure 2-28 Points - tool size calibration ······························································· 44
Figure 2-29 Select the tool frame ID with the points taught in the JOG screen··············· 45
Figure 2-30 Points - point teaching demonstration ·················································· 45
Figure 2-31 Points - tool frame orientation calibration ·············································· 46
Figure 2-32 Points - tool orientation calibration setting············································· 46
Figure 2-33 Points - WorkSpace setting (cylinder range teaching) ······························ 48
Figure 2-34 Points - WorkSpace setting (rectangular range teaching)·························· 48
Figure 2-35 Jog settings ··················································································· 49
Figure 2-36 IO monitoring - System IO·································································50
Figure 2-37 IO monitoring - User IO····································································· 50
Figure 2-38 Alarm Info······················································································ 51
Figure 2-39 Alarm Info - alarm information ···························································· 51
Figure 2-40 Controller Info················································································· 52
Figure 2-41 Modbus Info - default screen······························································ 52
Figure 2-42 Modbus Info - writing Modbus address information·································· 53
Figure 2-43 Modbus Info - reading Modbus address information ································ 53
Figure 2-44 Modbus Info - Modbus address information (read only)···························· 54
Figure 2-45 System - GoHome··········································································· 55
Figure 2-46 System settings - Controller IP ··························································· 56
Figure 2-47 System settings - obtain controller IP··················································· 56
Figure 2-48 System settings - set controller IP ······················································· 57
Figure 2-49 System settings - Other ···································································· 57
Figure 2-50 Rotation axis rotation count ······························································· 58
Figure 2-51 End axis rotation count····································································· 58

11
Figure 2-52 DRV model rotation axis ··································································· 58
Figure 2-53 System settings - select axis rotation operation mode······························ 59
Figure 2-54 System settings - displays axis rotation operation mode··························· 59
Figure 2-55 Joint Rotation Count function mode 0 uses User Frame to teach points······· 59
Figure 2-56 Joint Rotation Count function mode 0 does not use User Frame to teach points
············································································································· 59
Figure 2-57 Joint Rotation Count function mode 1··················································· 60
Figure 2-58 Joint Rotation Count function mode 2··················································· 60
Figure 2-59 Joint Rotation Count function mode 3··················································· 60
Figure 2-60 Servo Setting - All Axes Servo Off······················································· 61
Figure 2-61 Servo Setting - All Axes Servo On······················································· 61
Figure 2-62 Servo Setting - First Axis Servo On ····················································· 62
Figure 2-63 Servo Setting - First Axis Servo Off ····················································· 62
Figure 2-64 External Axis option········································································· 63
Figure 2-65 External axis information··································································· 63
Figure 2-66 Jog setting for the external axis ·························································· 64
Figure 2-67 External Axis Servo Switch (Ext. Servo on/off) ······································· 65
Figure 2-68 External Axis Servo Switch - External Axis 1 Servo On ···························· 65
Figure 2-69 External axis points - point table (1)····················································· 66
Figure 2-70 External axis points - point table (2)····················································· 66
Figure 2-71 External axis points - point table (3)····················································· 67

12
Handheld Teach Pendant DTV Series User Manual
1 HMI Basic Operation Interface
1.1 Hardware Interface··············································································13
1.2 Brief Introduction to the Operating Environment ········································14
1.3 Teach Pendant Hardware Button Functions··············································14
1.4 Touch Screen·····················································································18

13
1. HMI
1.1 Hardware Interface
Item
Specification
Display
Panel Type
7" TFT LCD (65535 colors)
Resolution
800 x 480 pixels
Display Area
154.08 x 85.92 mm
Auxiliary Key
21 Function Keys
Operating Temperature
0 - 40°C (32 - 104°F)
Storage Temperature
-10 to +60°C (14 - 140°F)
Dimensions
W x H x D (mm)
257.4 x 170.3 x 71.8 (including the protruding emergency stop and hook
parts)
Weight
750 g (not including cables)
Note:
1. Definition of the half-life period of the backlight module: Half-life period is the time during which the
brightness of the backlight reduces to half of the maximum brightness under maximum drive current.
The life-time indicated is an estimated value under a working environment at the room temperature of
25°C (77°F) with ambient humidity.
2. Isolation circuit withstand specifications: Able to withstand 1500V high-voltage surges for 1 minute.
3. Certifications for some models are being applied. Consult regional agents for details on certified models.

14
Handheld Teach Pendant DTV Series User Manual
1.2 Brief Introduction to the Operating Environment
This section provides a brief description for the teach pendant only. For a complete description of the
operating environment, please refer to the control box manual.
•The safety connector uses two sets of NC contacts for the emergency stop button, with the first set of
NC contacts connected to Pin 1 and Pin 2, and the second set of NC contacts connected to Pin 3 and
Pin 4. If the user has connected the safety gate signals to Pin 5, Pin 6, Pin 7, and Pin 8, functions
such as Jog, Goto, GoHome, and project program execution can be performed without pressing the
enable switch on the back of the teach pendant when the safety gate is closed. To perform teaching
with the teach pendant when the safety gate is open, the enable switch on the back of the teach
pendant must be pressed.
•To create a simple jig for T1 mode, input 0V (connect the 0V pin of DC Output) for System DI/O Pin 1
and Pin 3. Please refer to the control box manual for details.
Figure 1-1 Electric control box T1 simple wiring diagram

15
1. HMI
1.3 Teach Pendant Hardware Button Functions
The hardware interface structure of the handheld teach pendant is mainly divided into the touch screen
and physical buttons, as shown in Figure 1-2, Figure 1-3, and Figure 1-4.
•Touch screen functions include robot arm operating status, connection status, robot language editing,
point information display / teaching, system related parameter settings, system information display,
etc., as shown in Figure 1-2.
•Physical button functions include JOG (jog operation), RUN (auto execution), PAUSE / RESUME,
STOP, page switch button, selection / adjustment knob, emergency stop (E-STOP), and teach
pendant power indicator.
Physical
Button
Function Description
Executable
Page
Press and hold this button and the second position of the three-position
operating button simultaneously for 2 seconds to automatically execute
the currently running project.
Edit/RL
Press and hold this button and the second position of the three-position
operating button simultaneously to pause or resume the currently
running project.
Edit/RL
Press and hold this button and the second position of the three-position
operating button simultaneously to stop the currently running project.
Edit/RL
Press and hold this button and the second position of the three-position
operating button to move the axis in the positive direction.
All pages
Press and hold this button and the second position of the three-position
operating button to move the axis in the negative direction.
All pages
Press this button to go to the previous page You can use it in the point
page, project directory page, and RL editing page.
Edit/RL,
Points
Press this button to go to the next page. You can use it in the point page,
project directory page, and RL editing page.
Edit/RL,
Points

16
Emergency stop switch: Located at the top front of the handheld teach pendant (Figure 1-2). The safety
switch when operating the robot arm.
•When an emergency occurs, press the emergency stop button on the handheld teach pendant in
any operation mode to stop the robot.
Three-position operating button (Enable Switch): Located on the back of the handheld teach pendant
(Figure 1-3). The safety switch when operating the robot arm.
•The three-position operating button is divided into the following 3 statuses according to the force
applied when pressing the switch. If accidents happen, the operator will not be pressing within the
normal range.
Pressing Status
Operating
Status
Robot Status
Pressed with normal force (second position)
On
Can be operated manually
Not pressed or pressed with a force that is weaker
and less than the normal pressing force
Off
Stopped and cannot be operated
Pressed with excessive force
Off
Stopped and cannot be operated
•The functions of the three-position operating button vary depending on the operation mode and
whether a safety equipment is set (Note 1 and Note 2), as listed below:
1. In Auto mode: The handheld teach pendant only displays information but cannot be operated, and
the three-position operating button has no function.
2. In T1 and T2 modes:
a. Without safety equipment: Release or fully press the three-position operating button to stop
the robot.
b. With safety equipment: When the safety equipment is disconnected, the user must press and
hold the three-position operating button at the second position to operate the robot. Releasing or
fully pressing the three-position operating button will stop the robot immediately with a warning
displayed. On the other hand, when the safety equipment is activated normally, the three-position
operating button has no function.
Note: When workers are adjusting the robot in the safety equipment, please place a warning sign or
notification board to notify workers outside that the robot arm is being adjusted and that workers outside
must not operate the robot or its peripheral equipment. That way, the workers inside the safety equipment
will not be in danger of getting stuck.
Note 1: Safety equipment refers to safety fences, safety grating, or other safety facilities.
Note 2: Safety equipment is connected to the control box via the safety connector. For details, refer to the control
box manual.

17
Handheld Teach Pendant DTV Series User Manual
•SD card slot: Located at the bottom of the handheld teach pendant (Figure 1-4) and used for teach
pendant firmware update. Please use a 16G, Class 10 SD card which supports SDHC.
Figure 1-2 Startup screen
Figure 1-3 Back of the handheld teach pendant

18
1. HMI
Figure 1-4 SD card slot of the handheld teach pendant
1.4 Touch screen
The touch screen structure is divided into the menu bar on the left, the robot state monitoring on the top,
the jog information monitoring on the right, and the content of the corresponding tab. The functions are as
follows:
Figure 1-5 Touch screen structure

19
Handheld Teach Pendant DTV Series User Manual
•Menu Bar:
Displays tab switch buttons, including Edit/RL, Exe (Execution), Points, JOG, I/O (DI/O), Servo,
Info, and System.
Component
Appearance
Function Description
Tap this component to switch to the main screen and switch the menu bar to
the first page. The component will be highlighted in black when switching is
complete.
Tap this component to switch the menu bar to the next page.
Tap this component to switch the menu bar to the previous page.
Tap this component to switch to the Edit/RL screen. The component will be
highlighted in black when switching is complete.
Tap this component to switch to the Execution screen. The component will be highlighted
in black when switching is complete.
Tap this component to switch to the Points screen. The component will be highlighted in
black when switching is complete.
Tap this component to switch to the Jog setting screen. The component will be highlighted
in black when switching is complete.
Tap this component to switch to the I/O monitoring screen. The component will be
highlighted in black when switching is complete.
Tap this component to switch to the Servo ON/OFF screen. The component will be
highlighted in black when switching is complete.
Tap this component to switch to the information display screen. The component will be
highlighted in black when switching is complete.
Tap this component to switch to the system setting screen. The component will be
highlighted in black when switching is complete.
Tap this component to switch to the external axis screen. The component will be
highlighted in black when switching is complete.
Table of contents
Other Delta Controllers manuals
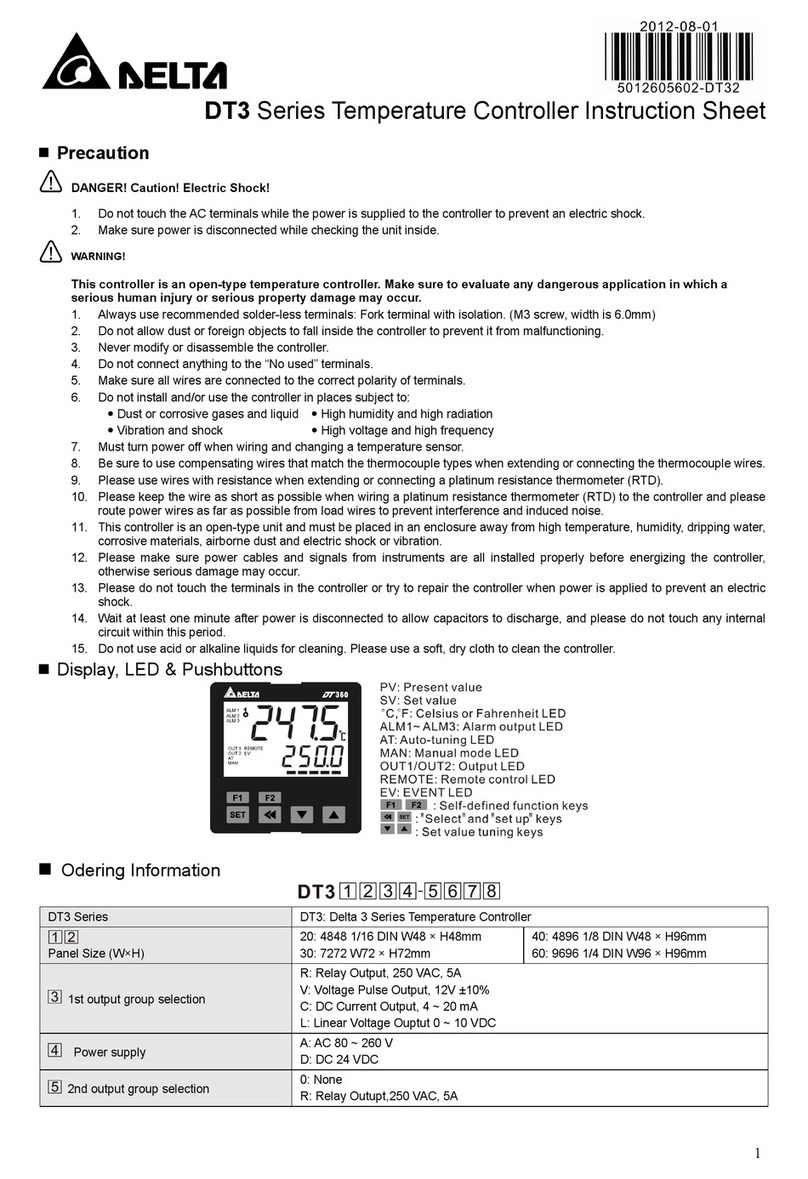
Delta
Delta DT3 Series User manual

Delta
Delta DVP-20PM User manual
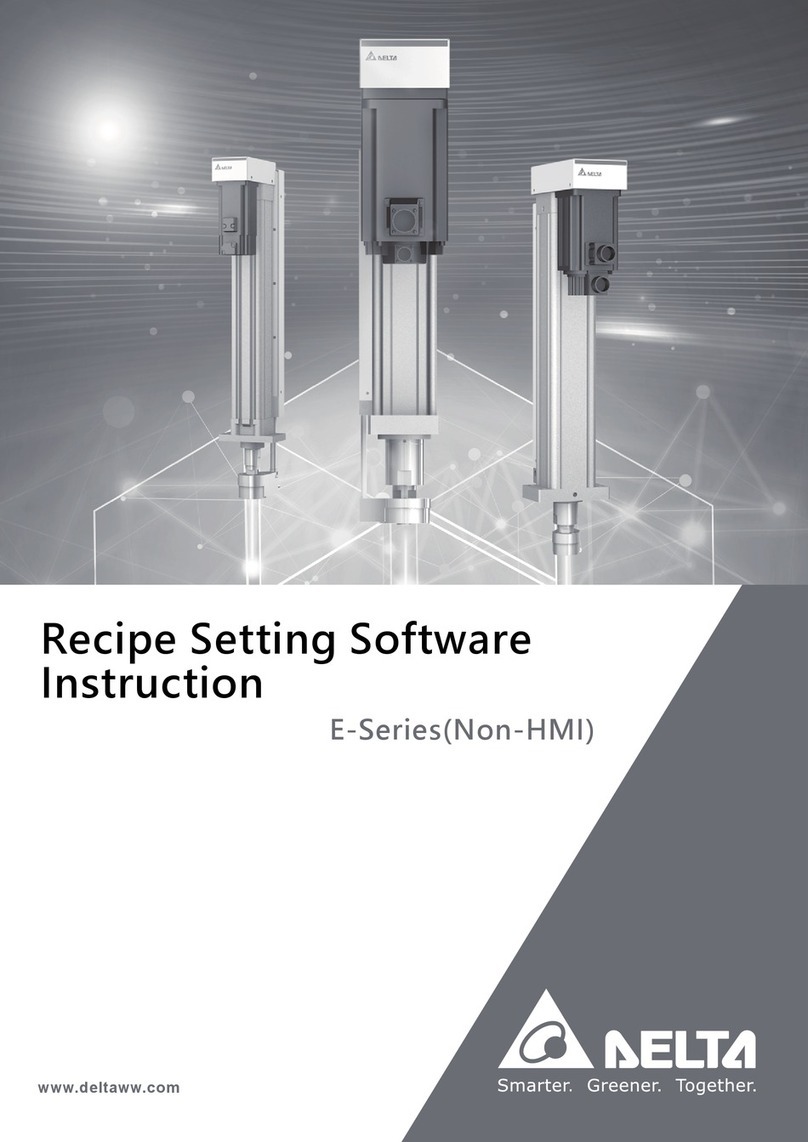
Delta
Delta E Series Mounting instructions

Delta
Delta ASDA-A2 Series User manual
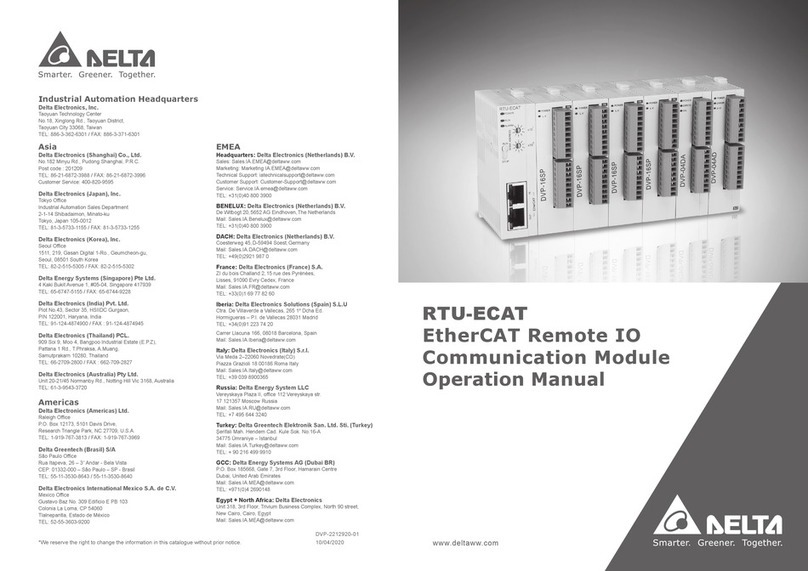
Delta
Delta RTU-ECAT User manual
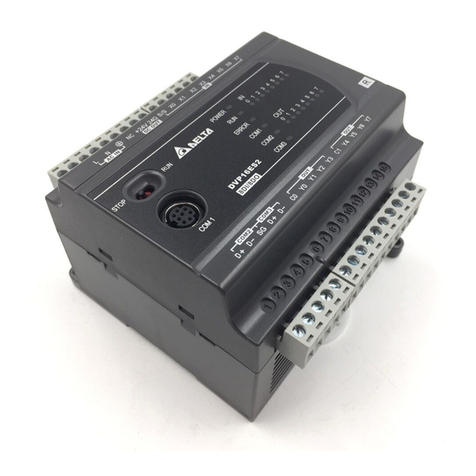
Delta
Delta DVP-ES2 User manual
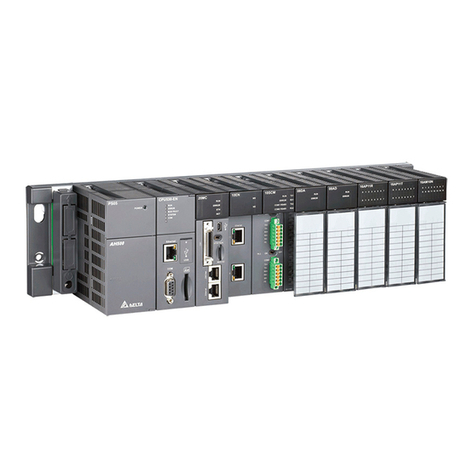
Delta
Delta AH500 series User manual
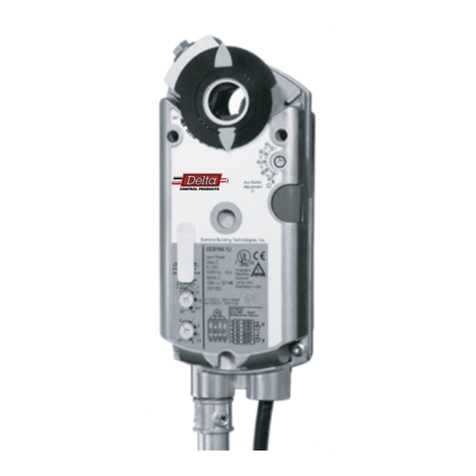
Delta
Delta DC-132 Series User manual
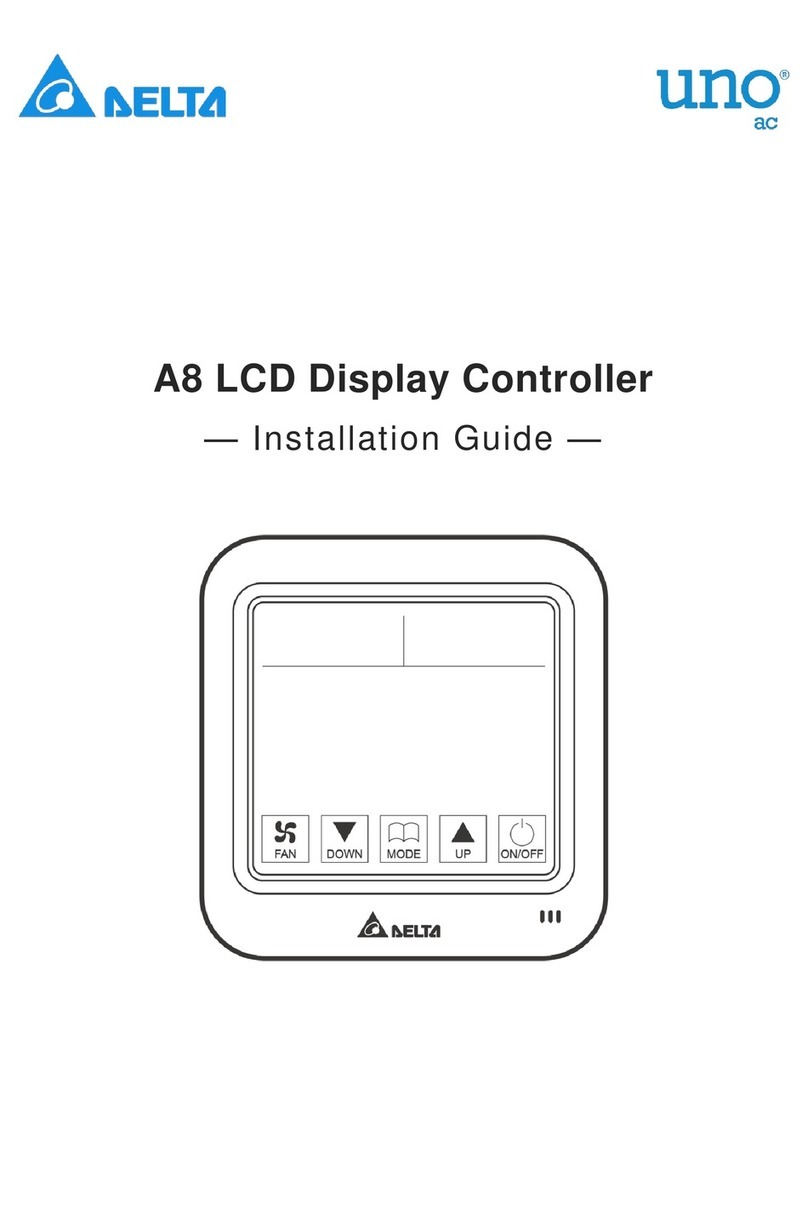
Delta
Delta UNOac A8 User manual
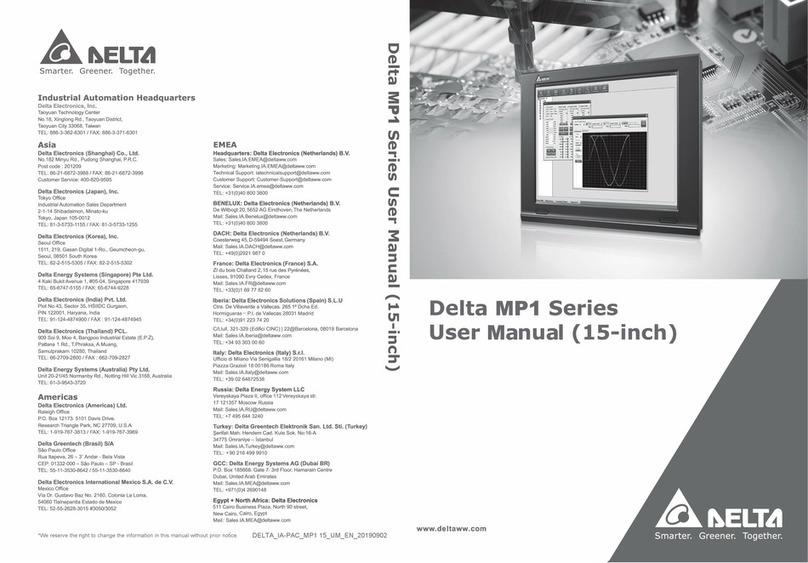
Delta
Delta MP1 Series User manual
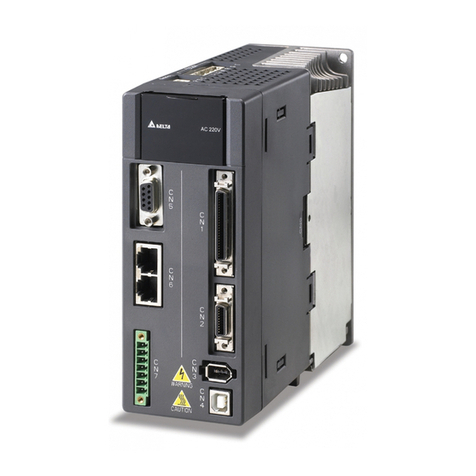
Delta
Delta ASDA-A2 Series User manual
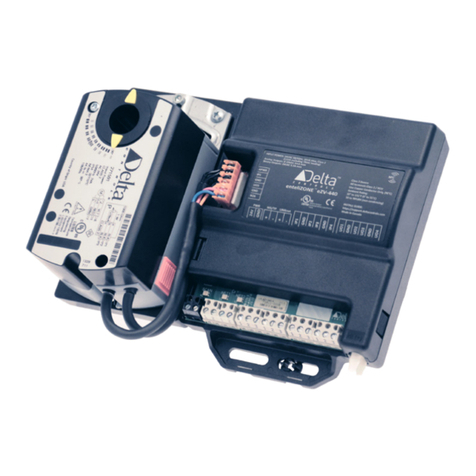
Delta
Delta eZV-440 User guide
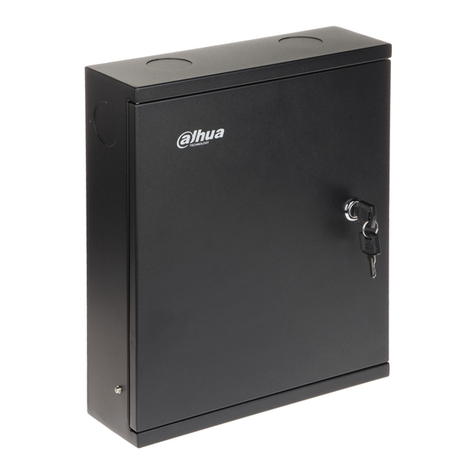
Delta
Delta ASC2204C-H User manual
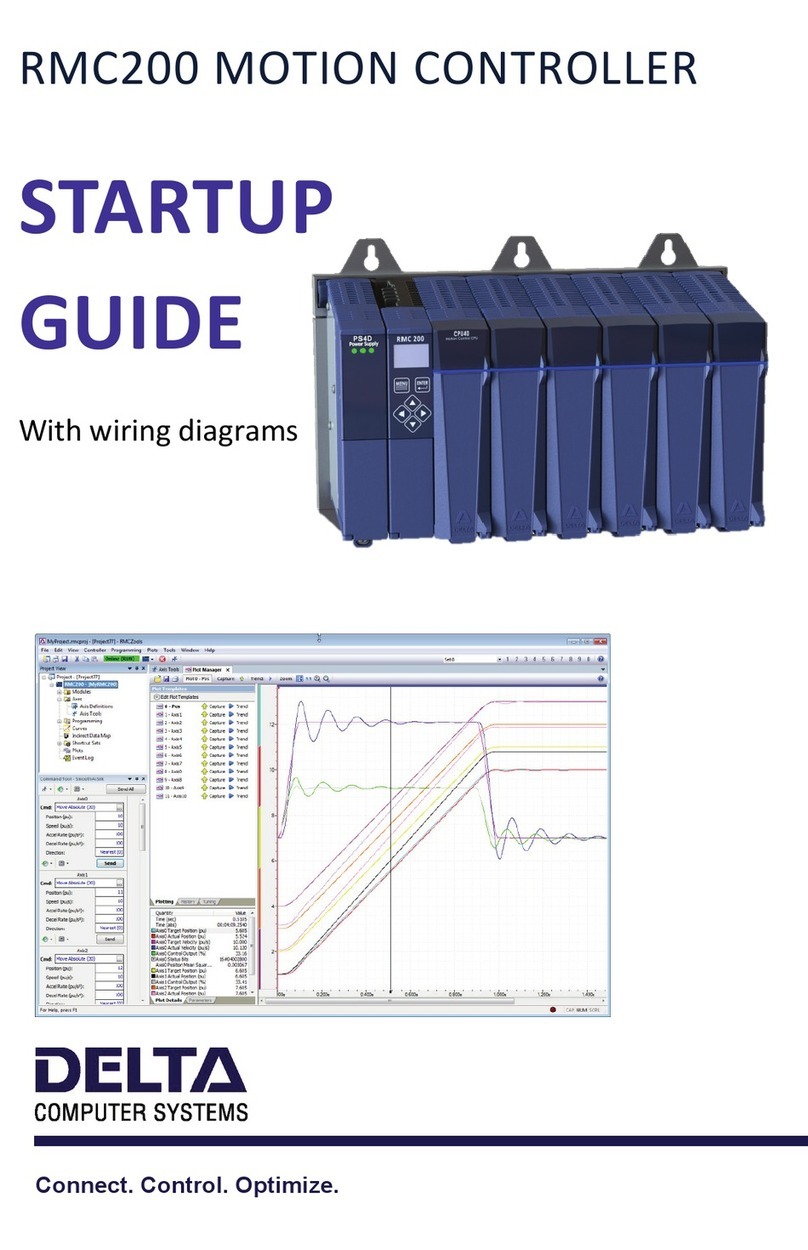
Delta
Delta RMC200 User guide
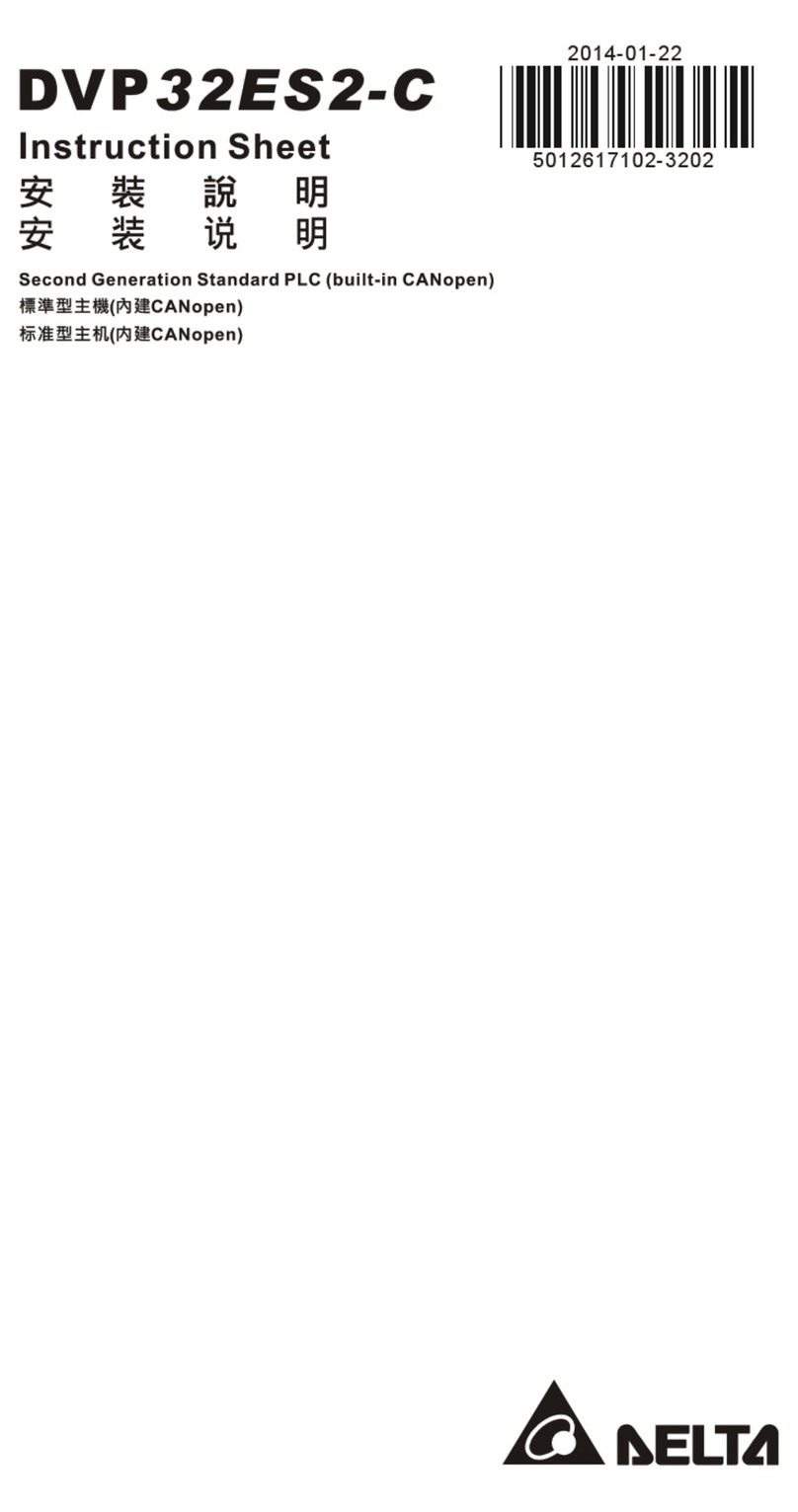
Delta
Delta DVP32ES200RC User manual

Delta
Delta 5CN-220T Series User manual
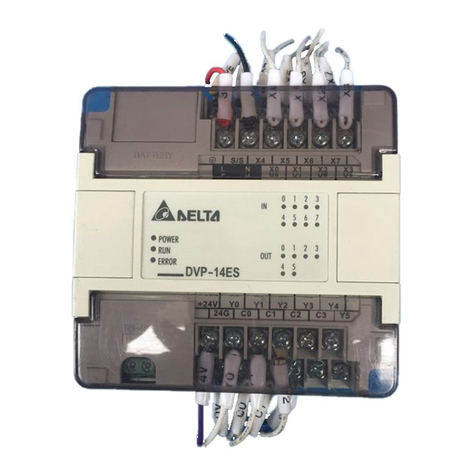
Delta
Delta DVP14ES00R2 User manual
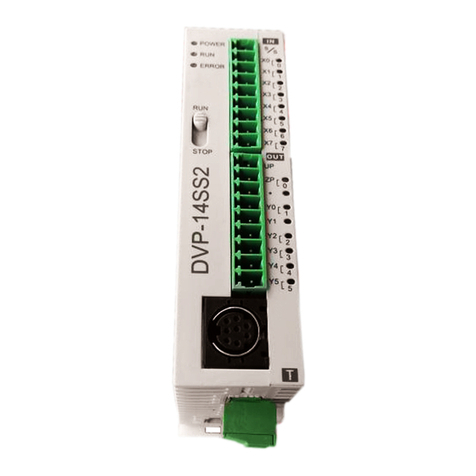
Delta
Delta DVP-SS2 User manual
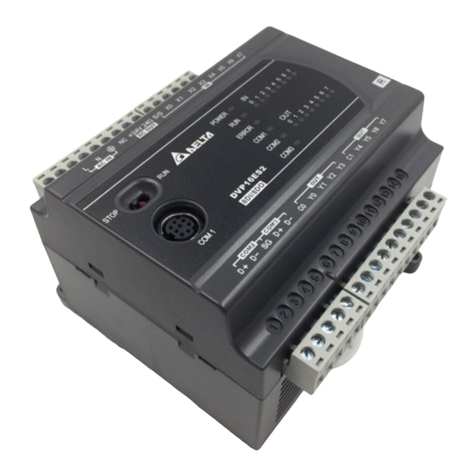
Delta
Delta DVP-ES2 User manual

Delta
Delta AH500 series User manual