Enerpac PID Series User manual

Operation and Maintenance Manual
To reduce the risk of injury, user must read and understand this document before use.
Document Number: L4523
Document Revision: A
Issue Date: October, 2021
Language: English EN
PID Series
Hydraulic Oil-to-Oil Intensifiers
PIDxxxA PIDMxxx
PIDHxxx PIDVxxxA
PIDVHxxx

2L4523_a
ABOUT US
Enerpac is a global market leader in high pressure hydraulic
tools, controlled force products, portable machining, on-
site services and solutions for precise positioning of heavy
loads. As a leading innovator with over a 100 year legacy,
Enerpac has helped move and maintain some of the largest
structures on earth. When safety and precision matters,
elite professionals in industries such as aerospace,
infrastructure, manufacturing, mining, oil & gas and power
generation rely on Enerpac for quality tools, services and
solutions. For additional information, visit www.enerpac.
com.
WARRANTY
Refer to the Enerpac Global Warranty document for terms
and conditions of the product warranty. Such warranty
information can be found at www.enerpac.com.
PRODUCT MARKINGS
Refer to markings on intensifier housing for the model
number, date code and other applicable information.
Markings shown in graphic at right are typical, but will
vary depending on model.
AVAILABLE LANGUAGES
An electronic copy of this document is available online in multiple languages:
•
EN
English - For other languages, visit www.enerpac.com.
•
DE
Deutsch - Weitere Sprachen finden Sie unter www.enerpac.com.
•
ES
Español - Para otros idiomas visite www.enerpac.com.
•
FR
Français - Pour toutes les autres langues, rendez-vous sur www.enerpac.com.
•
IT
Italiano - Per altre lingue visitate il sito www.enerpac.com.
•
JA
日本語-その他の言語はwww.enerpac.comでご覧 いた だ けます。
•
NL
Nederlands - Ga voor de overige talen naar www.enerpac.com.
•
PT
Português - Para outros idiomas consulte www.enerpac.com.
•
ZH
中文-如需其他语言,请前往www.enerpac.com.
Model Number
Serial Number
www.facebook.com/enerpac
www.youtube.com/enerpac
www.linkedin.com/company/enerpac
www.twitter.com/enerpac

L4523_a 3
1.0 SAFETY...................................................................................................................................................... 4
2.0 SPECIFICATIONS AND PRODUCT DATA ................................................................................................ 6
3.0 DESCRIPTION......................................................................................................................................... 12
4.0 PRINCIPLES OF OPERATION ................................................................................................................ 12
5.0 INSTALLATION AND SETUP................................................................................................................... 12
6.0 OPERATION............................................................................................................................................. 15
7.0 SERVICE .................................................................................................................................................. 18
8.0 TROUBLESHOOTING ............................................................................................................................. 18
9.0 REPLACEMENT PARTS.......................................................................................................................... 20
CONTENTS PAGE

4L4523_a
• Verify that all appropriate safety measures have
been taken to avoid the risk of injury and property
damage from your application or system.
• Be sure that all personnel involved with operating
or servicing the workholding devices read and
understand the information contained in the
manuals included with these devices. Observe
and follow all safety instructions and precautions
contained in the manuals.
• Design the control units of power operated
clamping systems to avoid inadvertent or
unauthorized activation.
• Be sure that clamping cylinders and other similar
workholding devices are properly positioned
before clamping forces are applied.
• Maintain a safe distance from clamping elements
and workpiece to avoid personal injury. Stay clear
of pinch points. Keep your hands, feet and body
away from the clamping area.
• Use mechanical devices and not fingers to hold
a part in place until the clamping hydraulics are
activated. Do not remove or disable the pressure
relief valve.
NOTICE
Hydraulic equipment must only be serviced
by a qualified hydraulic technician. For repair service,
contact the Enerpac authorized service center in your
area.
1.1.2 Hydraulic Intensifier Safety
Precautions (All PID Series Models)
WARNING
Failure to observe and comply with the
following precautions could result in death or serious
personal injury. Property damage could also occur.
• Be sure that the hydraulic pump or system hydraulic
power unit is turned off and disconnected from
power source before beginning any work. Lockout
and tag controls to prevent accidental startup as
installation is being performed.
• Be sure that any hydraulic pressure in the circuit is
completely relieved before loosening any hydraulic
fittings or removing any hoses or components. All
gauges must indicate zero (0) psi/bar. Be certain
that no hydraulic hoses are stiff and that there are
no other indications of trapped pressure within the
system.
• Work with clean tools in clean surroundings, free
of dust or dirt.
• Ensure that the intensifier installation is performed
only by trained and qualified personnel, familiar with
the setup and installation of hydraulic equipment.
• If unsure about safety, installation or adjustment
procedures described in this manual, consult
an experienced hydraulic systems engineer or
technician, and if needed, the Enerpac Technical
Service Department.
• Never exceed the maximum rated operating
pressure of the intensifier. Never exceed the
maximum pressure rating of other devices in
the circuit. Refer to the tables in Section 2.0 of
this manual for intensifier maximum operating
pressures.
1.0 SAFETY
Read all instructions carefully. Follow all recommended
safety precautions to avoid personal injury as well as
damage to the product and/or damage to other property.
Enerpac cannot be responsible for any damage or injury
from unsafe use, lack of maintenance, or incorrect
operation. Do not remove warning labels, tags, or
decals. In the event that any questions or concerns
arise, contact Enerpac or a local Enerpac distributor for
clarification.
Save these instructions for future use.
Appropriate training in the safe use of workholding
hydraulic systems and components is required prior to
the installation and operation of the intensifier. If training
is needed, contact your local Enerpac distributor or
authorized service center for information about an
Enerpac hydraulic safety training course.
This manual follows a system of safety alert symbols,
signals, words, and safety messages to warn the user of
specific hazards. Failure to comply with these warnings
could result in death or serious personal injury, as well
as damage to the equipment or other property.
The Safety Alert Symbol appears throughout
this manual. It is used to alert you to potential
physical injury hazards. Pay close attention
to Safety Alert Symbols and obey all safety
messages that follow this symbol to avoid the possibility
of death or serious injury.
Safety Alert Symbols are used in conjunction with certain
Signal Words that call attention to safety messages or
property damage messages and designate a degree or
level of hazard seriousness. The Signal Words used in
this manual are WARNING, CAUTION and NOTICE.
WARNING
Indicates a hazardous situation that, if not
avoided, could result in death or serious personal injury.
CAUTION
Indicates a hazardous situation that, if not
avoided, could result in minor or moderate personal
injury.
NOTICE
Indicates information considered important,
but not hazard related (e.g. messages related to property
damage). Please note that the Safety Alert Symbol will
not be used with the signal word.
1.1 Hydraulic Safety Precautions
1.1.1 General Workholding Safety
Precautions
WARNING
Failure to observe and comply with the
following precautions could result in death or serious
personal injury. Property damage could also occur.
• Although hydraulic operation moves the control of
the clamping fixture to an area of greater safety,
operators must still remain alert and use common
sense practises during their work.
• Use care when selecting components for the
workholding application so that safe operation
is ensured. Be certain that all components and
devices are of adequate rated capacity to perform
their intended functions. Do not exceed equipment
ratings.

L4523_a 5
• Some PID Series intensifier models are capable
of providing a maximum pressure above 5000 psi
[350 bar]. Operation at pressures above 5000 psi
[350 bar] requires the use of high pressure fittings.
Contact Enerpac for additional details.
• Read, understand and follow all communicated
safety precautions and related information included
on the following pages of this manual.
1.2 Labels
Product information (decals, labels, symbols etc.) may
be affixed to or printed on the intensifier housing. In some
instances, these labels may advise the user of potentially
hazardous situations. Always completely follow the
communicated precautions and/or instructions.

6L4523_a
2.0 SPECIFICATIONS AND PRODUCT DATA
2.1 Specifications (imperial)
Model No. Mounting
Style
Max Hyd.
Pressure
at Outlet *
Pressure
Intensification
Ratio
Inlet
Pressure
Range
Maximum
Inlet
Flow
Maximum
Outlet
Flow
Weight Port Sizes
psi in3/min in3/min lb Inlet &
Return Outlet
psi
PID321A Inline 5000 3.2:1 290-1563 915 153 2.2 #4 SAE #6 SAE
PID401A Inline 5000 4.0:1 290-1250 854 122 2.2 #4 SAE #6 SAE
PID501A Inline 5000 5.0:1 290-1000 854 98 2.2 #4 SAE #6 SAE
PID661A Inline 5000 6.6:1 290-758 793 79 2.2 #4 SAE #6 SAE
PID322A Inline 9600* 3.2:1 290-3000 915 153 2.2 G1/4" G1/4"
PID402A Inline 11600* 4.0:1 290-2900 854 122 2.2 G1/4" G1/4"
PID502A Inline 11600* 5.0:1 290-2321 854 98 2.2 G1/4" G1/4"
PID662A Inline 11600* 6.6:1 290-1758 793 79 2.2 G1/4" G1/4"
PIDH322 Inline 5000 3.2:1 290-1563 2136 305 8.14 G3/8" G1/2"
PIDH432 Inline 5000 4.0:1 290-1163 2136 244 8.14 G3/8" G1/2"
PIDH512 Inline 5000 5.0:1 290-980 2136 214 8.14 G3/8" G1/2"
PIDH632 Inline 5000 6.6:1 290-794 2136 153 8.14 G3/8" G1/2"
PIDV322A D03/CETOP 3 5000 3.2:1 290-1563 915 153 5.5 - - - - - -
PIDV402A D03/CETOP 3 5000 4.0:1 290-1250 855 122 5.5 - - - - - -
PIDV502A D03/CETOP 3 5000 5.0:1 290-1000 855 98 5.5 - - - - - -
PIDV662A D03/CETOP 3 5000 6.6:1 290-758 795 79 5.5 - - - - - -
PIDVH322 D03/CETOP 3 5000 3.2:1 290-1563 2449 397 13.2 - - - - - -
PIDVH432 D03/CETOP 3 5000 4.3:1 290-1163 2449 305 13.2 - - - - - -
PIDVH512 D03/CETOP 3 5000 5.1:1 290-980 2449 250 13.2 - - - - - -
PIDVH632 D03/CETOP 3 5000 6.3:1 290-794 2449 208 13.2 - - - - - -
PIDM322 Face Manifold 5000 3.2:1 290-1563 924 153 3.85 - - - - - -
PIDM402 Face Manifold 5000 4.0:1 290-1250 855 122 3.85 - - - - - -
PIDM502 Face Manifold 5000 5.0:1 290-1000 855 98 3.85 - - - - - -
PIDM662 Face Manifold 5000 6.6:1 290-758 785 79 3.85 - - - - - -
*Operating pressures above 5000 psi [350 bar] require high pressure fittings. Contact Enerpac for details.

L4523_a 7
2.2 Specifications (metric)
Model No. Mounting
Style
Max Hyd.
Pressure
at Outlet *
Pressure
Intensification
Ratio
Inlet
Pressure
Range
Maximum
Inlet
Flow
Maximum
Outlet
Flow
Weight Port Sizes
bar lpm lpm Kg Inlet &
Return Outlet
bar
PID321A Inline 350 3.2:1 20-109 15 2.5 1.0 #4 SAE #6 SAE
PID401A Inline 350 4.0:1 20-87 14 2.0 1.0 #4 SAE #6 SAE
PID501A Inline 350 5.0:1 20-70 14 1.6 1.0 #4 SAE #6 SAE
PID661A Inline 350 6.6:1 20-53 13 1.3 1.0 #4 SAE #6 SAE
PID322A Inline 662* 3.2:1 20-207 15 2.5 1.0 G1/4" G1/4"
PID402A Inline 800* 4.0:1 20-200 14 2.0 1.0 G1/4" G1/4"
PID502A Inline 800* 5.0:1 20-160 14 1.6 1.0 G1/4" G1/4"
PID662A Inline 800* 6.6:1 20-121 13 1.3 1.0 G1/4" G1/4"
PIDH322 Inline 350 3.2:1 20-109 35 5.0 3.7 G3/8" G1/2"
PIDH432 Inline 350 4.0:1 20-81 35 4.0 3.7 G3/8" G1/2"
PIDH512 Inline 350 5.0:1 20-69 35 3.5 3.7 G3/8" G1/2"
PIDH632 Inline 350 6.6:1 20-56 35 2.5 3.7 G3/8" G1/2"
PIDV322A D03/CETOP 3 350 3.2:1 20-109 15 2.5 2.5 - - - - - -
PIDV402A D03/CETOP 3 350 4.0:1 20-87 14 2.0 2.5 - - - - - -
PIDV502A D03/CETOP 3 350 5.0:1 20-70 14 1.6 2.5 - - - - - -
PIDV662A D03/CETOP 3 350 6.6:1 20-53 13 1.3 2.5 - - - - - -
PIDVH322 D03/CETOP 3 350 3.2:1 20-109 40 6.5 6.0 - - - - - -
PIDVH432 D03/CETOP 3 350 4.3:1 20-81 40 5.0 6.0 - - - - - -
PIDVH512 D03/CETOP 3 350 5.1:1 20-69 40 4.1 6.0 - - - - - -
PIDVH632 D03/CETOP 3 350 6.3:1 20-56 40 3.4 6.0 - - - - - -
PIDM322 Face Manifold 350 3.2:1 20-109 15 2.5 1.75 - - - - - -
PIDM402 Face Manifold 350 4.0:1 20-87 14 2.0 1.75 - - - - - -
PIDM502 Face Manifold 350 5.0:1 20-70 14 1.6 1.75 - - - - - -
PIDM662 Face Manifold 350 6.6:1 20-53 13 1.3 1.75 - - - - - -
*Operating pressures above 350 bar [5000 psi] require high pressure fittings. Contact Enerpac for details.

8L4523_a
2.3 External Dimensions & Port Locations - PIDxxxA Models
A B I
172
ACL-22A
RA-1061
B-171
V-66
SURS-52
Activator wand and booster
Shown: RA-1061, B-81
Contamination resistant closed hydraulic system
• No-leak palletized system, eliminates oil loss at connection point
• Closed design prevents machining chips and coolant from
entering the hydraulic circuit
• Booster can be mounted in either horizontal or vertical
position for design.
B and RA-series
Mechanical energy transfer system
uses external cylinder to operate
receiver booster.
❚ A manually placed Wand and
Booster system is used to clamp
the castings in this machining
fixture.
Hydraulic system schematics
The Activator Wand RA-1061 is placed into the receiver booster B-81 or B-171.
The mechanical transfer of force from the activator wand plunger to the booster
piston provides oil to the system.
Product selection
Pressure Oil flow Oil Stroke Model Operating
ratio ratio volume number area pressure
per
stroke
cm
3
mm cm
2
bar kg
▼ Receiver booster
▼ Activator wand
Hydraulic
Accumulator
Bleeder
Valve
Bleeder
Valve
Pressure Gauge
Activator Wand
Hydraulic hose
Pump
valve
Receiver booster
Swing Cylinders
G-series
H700 series
PED-1001E
Collet-Lok
®
products
Swing clamps
Work SupportsLinear Cylinders
Power SourcesValvesPallet Components
2 : 1 1,75 : 1 132,7 51,8 B-81 25,7 30 - 350 5,7
2 : 1 1,75 : 1 280,2 109,2 B-171 25,7 30 - 350 7,1
– – 162,2 112,7 RA-1061 14,4 60 - 700 5,1
D
E
F
GH
C
Item Dimension or Port Size Item Dimension or Port Size
inch mm inch mm
Aø 1.17-1.18 ø 29.8-30.0 G4.32-4.34 109.8-110.2
BM24 x 1.5 H1.61 40.9
C0.74-0.76 18.8-19.2 I1.09-1.10 27.8-28.0
D0.09-0.11 2.3-2.7 Outlet Port
A B I
172
ACL-22A
RA-1061
B-171
V-66
SURS-52
Activator wand and booster
Shown: RA-1061, B-81
Contamination resistant closed hydraulic system
• No-leak palletized system, eliminates oil loss at connection point
• Closed design prevents machining chips and coolant from
entering the hydraulic circuit
• Booster can be mounted in either horizontal or vertical
position for design.
B and RA-series
Mechanical energy transfer system
uses external cylinder to operate
receiver booster.
❚ A manually placed Wand and
Booster system is used to clamp
the castings in this machining
fixture.
Hydraulic system schematics
The Activator Wand RA-1061 is placed into the receiver booster B-81 or B-171.
The mechanical transfer of force from the activator wand plunger to the booster
piston provides oil to the system.
Product selection
Pressure Oil flow Oil Stroke Model Operating
ratio ratio volume number area pressure
per
stroke
cm
3
mm cm
2
bar kg
▼ Receiver booster
▼ Activator wand
Hydraulic
Accumulator
Bleeder
Valve
Bleeder
Valve
Pressure Gauge
Activator Wand
Hydraulic hose
Pump
valve
Receiver booster
Swing Cylinders
G-series
H700 series
PED-1001E
Collet-Lok
®
products
Swing clamps
Work SupportsLinear Cylinders
Power SourcesValvesPallet Components
2 : 1 1,75 : 1 132,7 51,8 B-81 25,7 30 - 350 5,7
2 : 1 1,75 : 1 280,2 109,2 B-171 25,7 30 - 350 7,1
– – 162,2 112,7 RA-1061 14,4 60 - 700 5,1
D
E
F
GH
C
A
B
C
D
#4 SAE or G-1/4" (varies by model)
E1.97-1.97 49.9-50.0 Inlet Port
A B I
172
ACL-22A
RA-1061
B-171
V-66
SURS-52
Activator wand and booster
Shown: RA-1061, B-81
Contamination resistant closed hydraulic system
• No-leak palletized system, eliminates oil loss at connection point
• Closed design prevents machining chips and coolant from
entering the hydraulic circuit
• Booster can be mounted in either horizontal or vertical
position for design.
B and RA-series
Mechanical energy transfer system
uses external cylinder to operate
receiver booster.
❚ A manually placed Wand and
Booster system is used to clamp
the castings in this machining
fixture.
Hydraulic system schematics
The Activator Wand RA-1061 is placed into the receiver booster B-81 or B-171.
The mechanical transfer of force from the activator wand plunger to the booster
piston provides oil to the system.
Product selection
Pressure Oil flow Oil Stroke Model Operating
ratio ratio volume number area pressure
per
stroke
cm
3
mm cm
2
bar kg
▼ Receiver booster
▼ Activator wand
Hydraulic
Accumulator
Bleeder
Valve
Bleeder
Valve
Pressure Gauge
Activator Wand
Hydraulic hose
Pump
valve
Receiver booster
Swing Cylinders
G-series
H700 series
PED-1001E
Collet-Lok
®
products
Swing clamps
Work SupportsLinear Cylinders
Power SourcesValvesPallet Components
2 : 1 1,75 : 1 132,7 51,8 B-81 25,7 30 - 350 5,7
2 : 1 1,75 : 1 280,2 109,2 B-171 25,7 30 - 350 7,1
– – 162,2 112,7 RA-1061 14,4 60 - 700 5,1
D
E
F
GH
C
A
B
C
D
#4 SAE or G-1/4" (varies by model)
F3.34-3.35 84.8-85.2 Return Port
A B I
172
ACL-22A
RA-1061
B-171
V-66
SURS-52
Activator wand and booster
Shown: RA-1061, B-81
Contamination resistant closed hydraulic system
• No-leak palletized system, eliminates oil loss at connection point
• Closed design prevents machining chips and coolant from
entering the hydraulic circuit
• Booster can be mounted in either horizontal or vertical
position for design.
B and RA-series
Mechanical energy transfer system
uses external cylinder to operate
receiver booster.
❚ A manually placed Wand and
Booster system is used to clamp
the castings in this machining
fixture.
Hydraulic system schematics
The Activator Wand RA-1061 is placed into the receiver booster B-81 or B-171.
The mechanical transfer of force from the activator wand plunger to the booster
piston provides oil to the system.
Product selection
Pressure Oil flow Oil Stroke Model Operating
ratio ratio volume number area pressure
per
stroke
cm
3
mm cm
2
bar kg
▼ Receiver booster
▼ Activator wand
Hydraulic
Accumulator
Bleeder
Valve
Bleeder
Valve
Pressure Gauge
Activator Wand
Hydraulic hose
Pump
valve
Receiver booster
Swing Cylinders
G-series
H700 series
PED-1001E
Collet-Lok
®
products
Swing clamps
Work SupportsLinear Cylinders
Power SourcesValvesPallet Components
2 : 1 1,75 : 1 132,7 51,8 B-81 25,7 30 - 350 5,7
2 : 1 1,75 : 1 280,2 109,2 B-171 25,7 30 - 350 7,1
– – 162,2 112,7 RA-1061 14,4 60 - 700 5,1
D
E
F
GH
C
A
B
C
D
#6 SAE or G1/4" (varies by model)
2.4 External Dimensions & Port Locations - PIDHxxx Models
A
B
C
D
Item Dimension Item Port Size
inch mm
A2.36 60.0 Outlet Port
A B I
172
ACL-22A
RA-1061
B-171
V-66
SURS-52
Activator wand and booster
Shown: RA-1061, B-81
Contamination resistant closed hydraulic system
• No-leak palletized system, eliminates oil loss at connection point
• Closed design prevents machining chips and coolant from
entering the hydraulic circuit
• Booster can be mounted in either horizontal or vertical
position for design.
B and RA-series
Mechanical energy transfer system
uses external cylinder to operate
receiver booster.
❚ A manually placed Wand and
Booster system is used to clamp
the castings in this machining
fixture.
Hydraulic system schematics
The Activator Wand RA-1061 is placed into the receiver booster B-81 or B-171.
The mechanical transfer of force from the activator wand plunger to the booster
piston provides oil
to the system.
Product selection
Pressure Oil flow Oil Stroke Model Operating
ratio ratio volume number area pressure
per
stroke
cm
3
mm cm
2
bar kg
▼ Receiver booster
▼ Activator wand
Hydraulic
Accumulator
Bleeder
Valve
Bleeder
Valve
Pressure Gauge
Activator Wand
Hydraulic hose
Pump
valve
Receiver booster
Swing Cylinders
G-series
H700 series
PED-1001E
Collet-Lok
®
products
Swing clamps
Work SupportsLinear Cylinders
Power SourcesValvesPallet Components
2 : 1 1,75 : 1 132,7 51,8 B-81 25,7 30 - 350 5,7
2 : 1 1,75 : 1 280,2 109,2 B-171 25,7 30 - 350 7,1
– – 162,2 112,7 RA-1061 14,4 60 - 700 5,1
D
E
F
GH
C
A
B
C
D
G-1/2"
B5.93 150.5 Inlet Port
A B I
172
ACL-22A
RA-1061
B-171
V-66
SURS-52
Activator wand and booster
Shown: RA-1061, B-81
Contamination resistant closed hydraulic system
• No-leak palletized system, eliminates oil loss at connection point
• Closed design prevents machining chips and coolant from
entering the hydraulic circuit
• Booster can be mounted in either horizontal or vertical
position for design.
B and RA-series
Mechanical energy transfer system
uses external cylinder to operate
receiver booster.
❚ A manually placed Wand and
Booster system is used to clamp
the castings in this machining
fixture.
Hydraulic system schematics
The Activator Wand RA-1061 is placed into the receiver booster B-81 or B-171.
The mechanical transfer of force from the activator wand plunger to the booster
piston provides oil to the system.
Product selection
Pressure Oil flow Oil Stroke Model Operating
ratio ratio volume number area pressure
per
stroke
cm
3
mm cm
2
bar kg
▼ Receiver booster
▼ Activator wand
Hydraulic
Accumulator
Bleeder
Valve
Bleeder
Valve
Pressure Gauge
Activator Wand
Hydraulic hose
Pump
valve
Receiver booster
Swing Cylinders
G-series
H700 series
PED-1001E
Collet-Lok
®
products
Swing clamps
Work SupportsLinear Cylinders
Power SourcesValvesPallet Components
2 : 1 1,75 : 1 132,7 51,8 B-81 25,7 30 - 350 5,7
2 : 1 1,75 : 1 280,2 109,2 B-171 25,7 30 - 350 7,1
– – 162,2 112,7 RA-1061 14,4 60 - 700 5,1
D
E
F
GH
C
A
B
C
D
G-3/8"
C1.73 44.0 Return Port
A B I
172
ACL-22A
RA-1061
B-171
V-66
SURS-52
Activator wand and booster
Shown: RA-1061, B-81
Contamination resistant closed hydraulic system
• No-leak palletized system, eliminates oil loss at connection point
• Closed design prevents machining chips and coolant from
entering the hydraulic circuit
• Booster can be mounted in either horizontal or vertical
position for design.
B and RA-series
Mechanical energy transfer system
uses external cylinder to operate
receiver booster.
❚ A manually placed Wand and
Booster system is used to clamp
the castings in this machining
fixture.
Hydraulic system schematics
The Activator Wand RA-1061 is placed into the receiver booster B-81 or B-171.
The mechanical transfer of force from the activator wand plunger to the booster
piston provides oil to the system.
Product selection
Pressure Oil flow Oil Stroke Model Operating
ratio ratio volume number area pressure
per
stroke
cm
3
mm cm
2
bar kg
▼ Receiver booster
▼ Activator wand
Hydraulic
Accumulator
Bleeder
Valve
Bleeder
Valve
Pressure Gauge
Activator Wand
Hydraulic hose
Pump
valve
Receiver booster
Swing Cylinders
G-series
H700 series
PED-1001E
Collet-Lok
®
products
Swing clamps
Work SupportsLinear Cylinders
Power SourcesValvesPallet Components
2 : 1 1,75 : 1 132,7 51,8 B-81 25,7 30 - 350 5,7
2 : 1 1,75 : 1 280,2 109,2 B-171 25,7 30 - 350 7,1
– – 162,2 112,7 RA-1061 14,4 60 - 700 5,1
D
E
F
GH
C
A
B
C
D
G-3/8"
Dø 2.76 ø 70.0
Outlet Port
Return Port
Inlet Port
Outlet Port Return Port
Inlet Port

L4523_a 9
2.5 External Dimensions & Port Locations - PIDVxxxA Models
A
B
C
D
E
F
G
B
TP
A
B
PT
A
D03/CETOP 3 VALVE MOUNTING
Item Dimension Item Dimension
inch mm inch mm
Aø 1.97 ø 50.0 E2.36 60.0
B6.64 168.7 F0.34 8.8
C2.72 69.0 G0.41 10.5
D1.97 50.0 Ports: A (advance), B (retract), P (pump) and T (reservoir)

10 L4523_a
2.6 External Dimensions & Port Locations - PIDVHxxx Models
A
B
C
D
F
E
G
B
TP
A
B
TP
A
D03/CETOP 3 VALVE MOUNTING
Item Dimension Item Dimension
inch mm inch mm
Aø 2.76 ø 70.0 E2.83 72.0
B8.53 216.7 F0.74 18.8
C3.15 80.0 G0.41 10.5
D2.76 70.0 Ports: A (advance), B (retract), P (pump) and T (reservoir)

L4523_a 11
2.7 External Dimensions & Port Locations - PIDMxxx Models
A
B
C
D
E
L
M
F
G
H
I
J
K
Item Dimension Item Dimension
inch mm inch mm
Aø 1.97 ø 50.0 I0.73 18.5
B4.79 121.7 J1.97 50.0
C0.87 22.0 K1.22 31.0
D2.72 69.0 L0.28 7.0
Eø 0.24 ø 6.2 M2.17 55.0
F0.37 9.5 Outlet Port
A B I
172
ACL-22A
RA-1061
B-171
V-66
SURS-52
Activator wand and booster
Shown: RA-1061, B-81
Contamination resistant closed hydraulic system
• No-leak palletized system, eliminates oil loss at connection point
• Closed design prevents machining chips and coolant from
entering the hydraulic circuit
• Booster can be mounted in either horizontal or vertical
position for design.
B and RA-series
Mechanical energy transfer system
uses external cylinder to operate
receiver booster.
❚ A manually placed Wand and
Booster system is used to clamp
the castings in this machining
fixture.
Hydraulic system schematics
The Activator Wand RA-1061 is placed into the receiver booster B-81 or B-171.
The mechanical transfer of force from the activator wand plunger to the booster
piston provides oil to the system.
Product selection
Pressure Oil flow Oil Stroke Model Operating
ratio ratio volume number area pressure
per
stroke
cm
3
mm cm
2
bar kg
▼ Receiver booster
▼ Activator wand
Hydraulic
Accumulator
Bleeder
Valve
Bleeder
Valve
Pressure Gauge
Activator Wand
Hydraulic hose
Pump
valve
Receiver booster
Swing Cylinders
G-series
H700 series
PED-1001E
Collet-Lok
®
products
Swing clamps
Work SupportsLinear Cylinders
Power SourcesValvesPallet Components
2 : 1 1,75 : 1 132,7 51,8 B-81 25,7 30 - 350 5,7
2 : 1 1,75 : 1 280,2 109,2 B-171 25,7 30 - 350 7,1
– – 162,2 112,7 RA-1061 14,4 60 - 700 5,1
D
E
F
GH
C
A
B
C
D
Maximum ø 0.236 Maximum ø 6
G0.63 16.0 Inlet Port
A B I
172
ACL-22A
RA-1061
B-171
V-66
SURS-52
Activator wand and booster
Shown: RA-1061, B-81
Contamination resistant closed hydraulic system
• No-leak palletized system, eliminates oil loss at connection point
• Closed design prevents machining chips and coolant from
entering the hydraulic circuit
• Booster can be mounted in either horizontal or vertical
position for design.
B and RA-series
Mechanical energy transfer system
uses external cylinder to operate
receiver booster.
❚ A manually placed Wand and
Booster system is used to clamp
the castings in this machining
fixture.
Hydraulic system schematics
The Activator Wand RA-1061 is placed into the receiver booster B-81 or B-171.
The mechanical transfer of force from the activator wand plunger to the booster
piston provides oil to the system.
Product selection
Pressure Oil flow Oil Stroke Model Operating
ratio ratio volume number area pressure
per
stroke
cm
3
mm cm
2
bar kg
▼ Receiver booster
▼ Activator wand
Hydraulic
Accumulator
Bleeder
Valve
Bleeder
Valve
Pressure Gauge
Activator Wand
Hydraulic hose
Pump
valve
Receiver booster
Swing Cylinders
G-series
H700 series
PED-1001E
Collet-Lok
®
products
Swing clamps
Work SupportsLinear Cylinders
Power SourcesValvesPallet Components
2 : 1 1,75 : 1 132,7 51,8 B-81 25,7 30 - 350 5,7
2 : 1 1,75 : 1 280,2 109,2 B-171 25,7 30 - 350 7,1
– – 162,2 112,7 RA-1061 14,4 60 - 700 5,1
D
E
F
GH
C
A
B
C
D
Maximum ø 0.236 Maximum ø 6
H0.63 16.0 Return Port
A B I
172
ACL-22A
RA-1061
B-171
V-66
SURS-52
Activator wand and booster
Shown: RA-1061, B-81
Contamination resistant closed hydraulic system
• No-leak palletized system, eliminates oil loss at connection point
• Closed design prevents machining chips and coolant from
entering the hydraulic circuit
• Booster can be mounted in either horizontal or vertical
position for design.
B and RA-series
Mechanical energy transfer system
uses external cylinder to operate
receiver booster.
❚ A manually placed Wand and
Booster system is used to clamp
the castings in this machining
fixture.
Hydraulic system schematics
The Activator Wand RA-1061 is placed into the receiver booster B-81 or B-171.
The mechanical transfer of force from the activator wand plunger to the booster
piston provides oil to the system.
Product selection
Pressure Oil flow Oil Stroke Model Operating
ratio ratio volume number area pressure
per
stroke
cm
3
mm cm
2
bar kg
▼ Receiver booster
▼ Activator wand
Hydraulic
Accumulator
Bleeder
Valve
Bleeder
Valve
Pressure Gauge
Activator Wand
Hydraulic hose
Pump
valve
Receiver booster
Swing Cylinders
G-series
H700 series
PED-1001E
Collet-Lok
®
products
Swing clamps
Work SupportsLinear Cylinders
Power SourcesValvesPallet Components
2 : 1 1,75 : 1 132,7 51,8 B-81 25,7 30 - 350 5,7
2 : 1 1,75 : 1 280,2 109,2 B-171 25,7 30 - 350 7,1
– – 162,2 112,7 RA-1061 14,4 60 - 700 5,1
D
E
F
GH
C
A
B
C
D
Maximum ø 0.236 Maximum ø 6
FACE MOUNTING

12 L4523_a
3.0 DESCRIPTION
The Enerpac PID Series oil-to-oil intensifier increases
hydraulic system output pressure as needed, allowing
the system to power a cylinder or other device which
requires a higher inlet pressure.
The self-contained device boosts inlet pressure by up
to a 6.6:1 ratio (depending on model selected) without
the use of external power. The intensifier also maintains
high pressure and automatically compensates for the
consumption of hydraulic oil on the high pressure side.
Key features and benefits include:
• Compact and self-contained design allows for
ease of installation.
• Internal bypass valving helps ensure high output
flow rates.
• Available in a wide range of intensification ratios to
suit various operating pressure requirements.
• Integral dump valve eliminates the need for an
external pilot check valve.
• Internal filter screens located in the ports protect
the intensifier from debris. An internal flow metering
orifice prevents damage from excessive flow.
• Precision fit of all internal components helps
provide long operating life.
4.0 PRINCIPLES OF
OPERATION
When hydraulic pressure from an existing power source
is limited, the intensifier increases the output pressure
to satisfy the required application.
• When oil is supplied to the inlet port, it flows
freely past the check valves and the dump valve,
advancing the cylinder.
• As the inlet pressure increases, the intensifier’s
built-in oscillating pump automatically increases
the outlet pressure by a specific intensification
ratio. This ratio will vary depending on intensifier
model number.
• The intensifier's oscillating pump will make a soft
“ticking” sound as it oscillates, indicating that
pressure is building.
• When the maximum pressure is reached, the
oscillation frequency lowers and balances at the
maximum pressure. At this point, the intensifier’s
oscillating pump stops oscillating or oscillates very
slowly.
• Free flow from the cylinder back to the tank occurs
when the directional control valve is shifted to
supply flow to the return port.
Refer to Section 6.0 for additional model-specific
intensifier operation information.
5.0 INSTALLATION AND
SETUP
5.1 Receiving Instructions
Visually inspect all components for shipping damage.
Shipping damage is not covered by warranty. If shipping
damage is found, notify carrier at once. The carrier is
responsible for all repair and replacement costs resulting
from damage in shipment.
5.2 Description of Models & Porting
PIDxxxA and PIDHxxx models are inline mounted units
designed to be installed in a hydraulic circuit using
threaded SAE or BSPP fittings and either tubing or
hoses. PIDxxxA models have a mounting nut at the
outlet port which can be used to secure the intensifier
to a bracket.
PIDVxxxA and PIDHVxxx models are designed to
mount on a D03 (CETOP3) valve manifold, and require
a directional control valve to control the oil flow through
the Intensifier.
PIDMxxx models are designed to face mount on a
custom manifold block, allowing the intensifier to be
integrated into a circuit.
5.3 Installation
• Refer to hydraulic pressure specifications in
Section 2.0. Do not exceed the maximum pressure
limits for your intensifier model. Also refer to
additional information in Section 5.5.
• In order to prevent damage to the intensifier,
the inlet oil flow must not exceed the maximum
allowable flow rate for your intensifier model. Refer
to maximum flow specifications in Section 2.0.
• Do not place the intensifier into operation unless
you are certain the machine or system into which it
is installed complies with all applicable regulations
and directives required by local and regional
authorities.
• For PIDxxxA and PIDHxxx models, refer to the
tables in Section 2.0 for SAE and BSPP port sizes.
5.4 System Design
• All current production PID Series intensifier models
include a built-in filter screen at each port to block
large particles such as metal chips. In addition, a
flow control orifice located in the inlet port limits
the flow rate into the intensifier. Separate external
filters and flow control valves are not required.
• During installation, make sure that there are no
restrictions downstream of the return port, which
could create back pressure in the return line. The
outlet pressure from the intensifier is based on
the differential between the Inlet and return port
pressure. Any backpressure on the return port will
proportionally reduce the outlet pressure.

L4523_a 13
Ports Hydraulic Connection Size and Type Maximum Tightening Torque
lb-ft Nm
Inlet (IN)
Return (R)
Outlet (H)
G-1/4" Threaded with steel washer 29.5 40
G-1/4" Threaded with aluminium washer 22.0 30
G-1/4" Threaded with cutting edge 29.5 40
Figure 1: Torque Specifications, PIDxxxA Models
Ports Hydraulic Connection Size and Type Maximum Tightening Torque
lb-ft Nm
Inlet (IN)
Return (R)
G-3/8" Threaded with steel washer 44.3 50
G-3/8" Threaded with aluminium washer 29.5 40
G-3/8" Threaded with cutting edge 44.3 60
Outlet (H) G-1/2" Threaded with steel washer 95.9 130
G-1/2" Threaded with cutting edge 95.9 130
Figure 2: Torque Specifications, PIDHxxx Models
Mounting Bolt Size Maximum Tightening Torque
lb-ft Nm
M6 x 25 12.9 - DIN 912 2.8 18
Note: PIDMxxx models are supplied with four mounting bolts and four 6.4 mm
washers. Place washers under the bolt heads prior to tightening.
Figure 3: Torque Specifications, PIDMxxx Models
• The intensifier is designed to automatically
compensate for downstream pressure losses.
However, a sufficient inlet flow rate of approximately
79 in³/min [1.3 lpm] is required to maintain this
capability.
5.5 Hydraulic Pressure
CAUTION
Failure to observe maximum pressure
ratings could result in personal injury, improper
operation, equipment failure and/or property damage.
• Refer to the tables in Section 2.0 for intensifier
maximum pressure ratings.
• All models except PID322A, PID402A, PID502A
and PID663A: The maximum hydraulic pressure
at the intensifier outlet ports “A”, “B” or “H” (as
applicable for your intensifier model) must not
exceed 5000 psi [350 bar].
• Models PID402A, PID502A and PID663A: The
maximum hydraulic pressure at the intensifier
outlet port “H” must not exceed 11,600 psi [800
bar].
• Model PID322A: The maximum hydraulic pressure
at the intensifier outlet port “H” must not exceed
9,600 psi [662 bar].
NOTICE
Special high pressure fittings must be used in
systems with pressures exceeding 5000 psi [350 bar].
Contact Enerpac for additional information.
• Minimum hydraulic pressure at the inlet port for all
models is approximately 290 psi [20 bar]. Intensifier
may not function if flow rate is too low.
5.6 Torque Specifications
• Observe proper torque values when installing
hydraulic fittings in the ports of PIDxxxA and
PIDHxxx Series hydraulic intensifiers. These units
use threaded SAE or BSPP ports.
• Mounting hardware is supplied with PIDMxxx
models only. Refer to Figure 3 for mounting bolt
torque specifications.
• Mounting bolts and other hardware (as needed)
is to be supplied by the user for other intensifier
models.

14 L4523_a
5.7 Directional Control Valve Recommendations
• To prevent hydraulic oil leakage from occurring, it is strongly recommended that an open center control valve
be used with the intensifier. See Figure 4, upper view.
• Use of a closed center control valve is not recommended. See Figure 4, lower view.
NOTICE
If a closed center control valve is used, contaminated hydraulic oil can cause the internal check valves
of the intensifier to leak high‐pressure oil back to the inlet (IN) and return (R) connection. In addition, on PIDVxxxA,
PIDVHxxx and PIDMxxx models, if high pressure (> 3,000 psi [> 207 bar]) becomes trapped between the intensifier
and the directional control valve, the connecting bolts can be stretched, resulting in possible external oil leakage.
not recommended
recommended
or
or
Open center valve
Closed center valve
Figure 4: Open Center Control Valve Recommended
5.8 Oil Filtration Requirements
Oil filtration must be in accordance with the ISO 44306 standard or the equivalent standard applicable in your
region or country.
Ensure that the hydraulic oil is clean. Filtration must meet the ISO target levels and micron ratings shown in the
table in Figure 5.
0 to 2,000 psi
[0 to 140 bar]
2,000 to 3,000 psi
[141 to 207 bar]
Media ISO Target
Levels
Micron
Ratings
ISO Target
Levels
Micron
Ratings
Oil >5cSt 19/17/14 10 20-109 15
Water/Water Glycol <5cSt 18/16/13 5 20-87 14
Figure 5: Oil Filtration Requirements

L4523_a 15
6.0 OPERATION
6.1 PIDxxxA and PIDHxxx Models
When hydraulic oil enters the inlet (IN) port, it freely flows through the check valves (KV1, KV2) to the cylinder. The
cylinder then advances.
When cylinder pressure reaches the supply pressure, the intensifier oscillating pump (OP) automatically starts
oscillating and begins to increase the pressure in the cylinder by the designated intensification factor (varies by
intensifier model).
Once the desired pressure is reached, the oscillation frequency drops to a level that provides only enough flow to
maintain maximum pressure in the cylinder. If no additional flow is required, pump oscillation stops.
Adjusting the inlet pressure also adjusts the outlet pressure. The outlet pressure is directly proportional to the
inlet pressure. For example, in a model PID321 intensifier, with a 3.2:1 ratio, 100 psi [6.9 bar] of supply pressure
adjustment raises or lowers the outlet pressure by 321 psi [22.1 bar].
To allow cylinder retraction, dump valve (DV) is pilot operated to open when the control valve (CV) is shifted to the
retract position. This allows the oil from the advance side of the cylinder to flow back through the inlet (IN) port to
the valve and back to the pump reservoir.
Note that if a double-acting cylinder is used, a secondary circuit from the cylinder retract port must be connected
to allow retraction of the cylinder.
OP
CV
Key:
IN Inlet Port
R Return Port
H Outlet Port
CV Control Valve
IN
R
DV
KV1 KV2 H
Cylinder (Double-Acting)
Cylinder (Single-Acting)
KV1 Check Valve (inlet)
KV2 Check Valve (outlet)
OP Oscillating Pump
DV Dump Valve
CV
IN
R
DV
KV1
KV2 H
Cylinder (Double-Acting)
Cylinder (Single-Acting)
OP
PIDxxxA Models
PIDHxxx Models
Figure 6: Hydraulic Schematic, PIDxxxA and PIDHxxx Models

16 L4523_a
6.2 PIDVxxxA and PIDVHxxx Models
The PIDVxxxA and PIDVHxxx models function in the same manner as the PIDxxxA models (refer to Section 6.1).
However, for the PIDVxxxA, the intensifier is integrated into a D03 (CETOP 3) ported manifold block. A control valve
is required and must be mounted above the intensifier in a valve stack on a D03 (CETOP 3) valve manifold.
The high pressure advance flow is directed to port A on the valve manifold and retract flow is directed to port B. This
allows the cylinder to be plumbed from the valve manifold in a typical circuit.
OP
Control Valve
Cylinder
Intensifier
Connection Plate
P T B A
P T B A
P T B A
B A
DV KV1 IN
R
KV2
Inlet Pressure (low pressure)
Outlet Pressure (high pressure)
Key:
A Advance Port
B Retract Port
P Inlet (pump) Port
T Tank (return) Port
KV1 Check Valve
KV2 Check Valve
OP Oscillating Pump
DV Dump Valve
Figure 7: Hydraulic Schematic, PIDVxxxA and PIDVHxxx Models

L4523_a 17
6.3 PIDMxxx Models
The PIDMxxx models function in the same manner as the PIDxxxA models (refer to Section 6.1). However for the
PIDMxxx, the intensifier is integrated into a flange mount manifold block that is designed to face-mount to a custom
manifold block. This allows the user to integrate the intensifier into a block with other components, such as a
pressure gauge, cartridge directional valve, pressure reducing valve or pressure switch/transducer.
X
X
Cylinder
Connection Plate
A
B
IN
H
R
KV2
DV
KV1
OP
PT
CV
Key:
A Advance Port
B Retract Port
P Inlet (pump) Port
T Tank (return) Port
H Outlet Port
CV Control Valve
OP Oscillating Pump
DV Dump Valve
KV1 Check Valve (inlet)
KV2 Check Valve (outlet)
Figure 8: Hydraulic Schematic, PIDMxxx Models

18 L4523_a
7.0 SERVICE
Except for a few maintenance oriented items, the PID Series intensifiers contain no user-replaceable parts.
Maintaining the proper filtration and flow rate of the inlet oil will help provide trouble-free operation. Service kits
containing replacement filters, O-rings and orifices are available from your Enerpac distributor or authorized service
center. Refer to the parts lists and diagram for your intensifier model in Section 9.0.
If an internal malfunction is suspected, have the intensifier inspected by an Enerpac authorized service center.
WARNING
Shut down hydraulic power source before performing any service or maintenance activities. Be sure
that hydraulic pressure is completely relieved before loosening intensifier fittings or mounting hardware. Failure
to observe this precaution could result in the release of pressurized hydraulic oil and possible skin penetration.
Serious personal injury could result.
8.0 TROUBLESHOOTING
Only qualified hydraulic technicians should troubleshoot the intensifier and related system components.
Refer to the schematic diagrams in figures 6, 7and 8for descriptions of intensifier components referenced in the
troubleshooting guide.
A system failure may or may not be the result of an intensifier malfunction. To determine the cause of the problem, the
complete system must be included in any diagnostic procedure.
The following troubleshooting guide is intended to be used only as an aid in determining if a problem exists. For repair
service, contact an Enerpac authorized service center.
Troubleshooting Guide
Problem Possible Cause Corrective Action
1. Intensifier does not
oscillate and pressure does
not increase.
a. inlet pressure too low. Increase pressure. Refer to the
tables in Section 2.0 for the minimum
pressure for your intensifier model.
b. Dirt or metal chips in KV1 valve
or DV valve. Oil contamination.
Clean or replace intensifier filter
screens and orifice as required. Refer
to Section 9.0 for parts information.
Change oil in hydraulic system.
2. Intensifier does not
reach maximum intensified
pressure.
Dirt or metal chips in KV1 valve.
Oil contamination.
Clean or replace intensifier filter
screens and orifice as required. Refer
to Section 9.0 for parts information.
Change oil in hydraulic system.
3. Intensifier operates
continuously (does not stop
oscillating).
Dirt or metal chips in KV1 valve or
DV valve. Oil contamination.
Clean or replace intensifier filter
screens and orifice as required. Refer
to Section 9.0 for parts information.
Change oil in hydraulic system.
4. Intensifier loses pressure
when hydraulic oil is hot.
Damaged high pressure piston
due to oil contamination.
See authorized service center. Change
oil in hydraulic system.
NOTICE
If corrective actions fail to restore proper operation, take the intensifier to an Enerpac authorized service
center for diagnosis. Intensifier is not user-repairable.
(continued on next page)

L4523_a 19
Troubleshooting Guide (continued)
Problem Possible Cause Corrective Action
5. Oil leakage between
top and middle portions of
intensifier.
Stretched bolts.
a. Inlet pressure too high. Reduce inlet pressure. Refer to the
tables in Section 2.0 for the maximum
allowable inlet pressure for your
intensifier model.
b. Inlet flow rate too high. Reduce inlet flow rate. Refer to the
tables in Section 2.0 for the maximum
allowable inlet flow rate for your
intensifier model.
c. Closed center control valve
being used.
Replace closed center control valve
with open center control valve.
Refer to Section 5.7 for additional
information.
6. Intensifier will not sustain
high pressure.
Dirt or metal chips in KV2 valve or
DV valve. Oil contamination.
Clean or replace intensifier filter
screens and orifice as required. Refer
to Section 9.0 for parts information.
Change oil in hydraulic system.
7. Intensifier dump (DV) valve
will not relieve pressure.
Inlet pressure too low. Raise inlet pressure.
8. Outlet port pressure
fluctuates.
Pressure peaks at the inlet port. Check hydraulic system for pressure
fluctuations.
NOTICE
If corrective actions fail to restore proper operation, take the intensifier to an Enerpac authorized service
center for diagnosis. Intensifier is not user-repairable.

20 L4523_a
9.0 REPLACEMENT PARTS
Replacement parts are shown in the following parts lists (sections 9.1 through 9.5). Refer to the parts list for your
intensifier model.
9.1 Parts List for PIDxxxA Models
12
23
Item Description Qty
1Filter Screen, Outlet (H) Port 1
2Filter Screen, Inlet (IN) and Return (R) Ports 2
3Orifice, 1.6 mm, Inlet (IN) Port 1
Items included in Parts Kit, PIDK1.
9.2 Parts List for PIDHxxx Models
12
2
3
Item Description Qty
1Filter Screen, Outlet (H) Port 1
2Filter Screen, Inlet (IN) and Return (R) Ports 2
3Orifice, 2.5 mm, Inlet (IN) Port 1
Items included in Parts Kit, PIDHK1.
Item 3: Apply anti-seize compound to threads. Torque to
7.4 lb-ft [10 Nm]. Use 4 mm hex wrench.
Item 2: Apply anti-seize compound to threads. Torque to
3.7 lb-ft [5 Nm]. Use 2.5 mm hex wrench.
Table of contents
Other Enerpac Control Unit manuals

Enerpac
Enerpac VE33 User manual
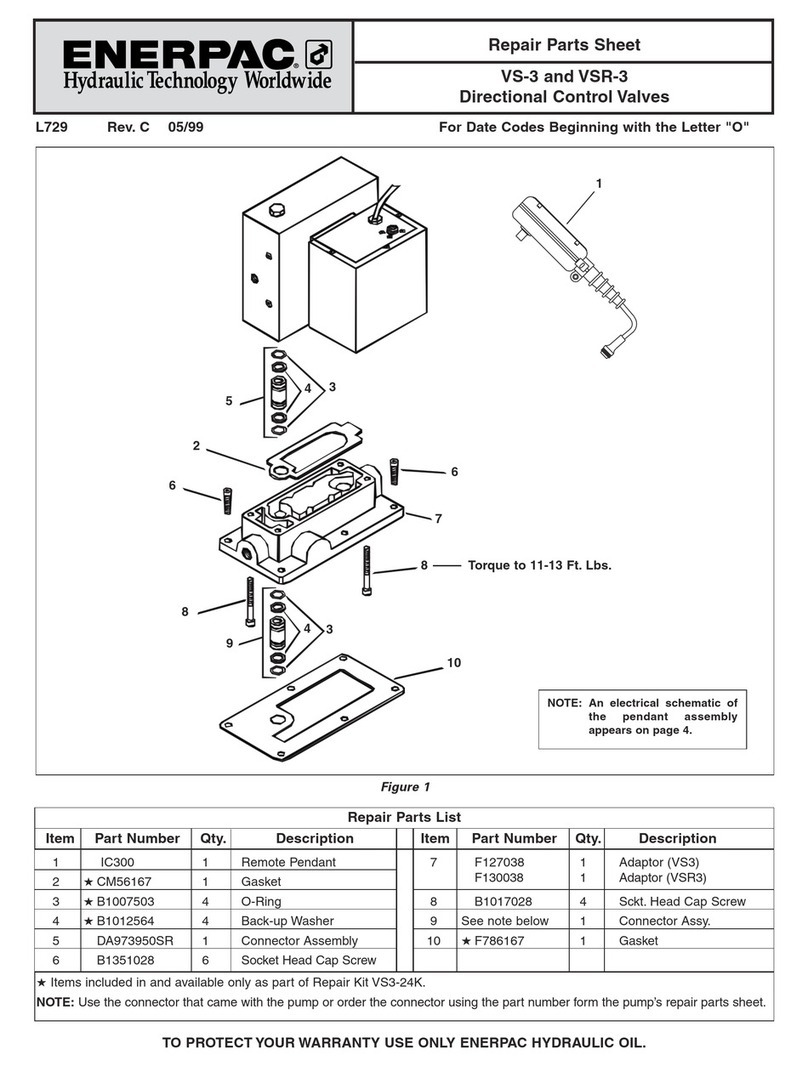
Enerpac
Enerpac VS-3 Use and care manual

Enerpac
Enerpac PUJ-1201B Operating instructions
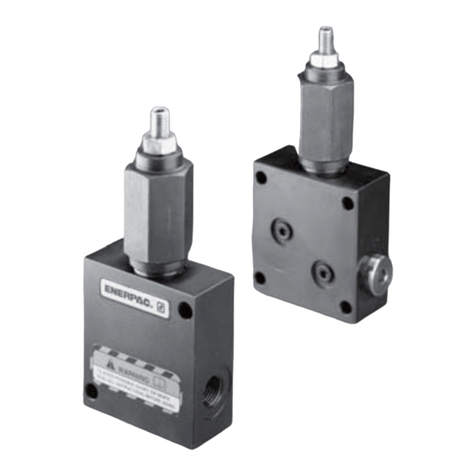
Enerpac
Enerpac MVP-5 User manual
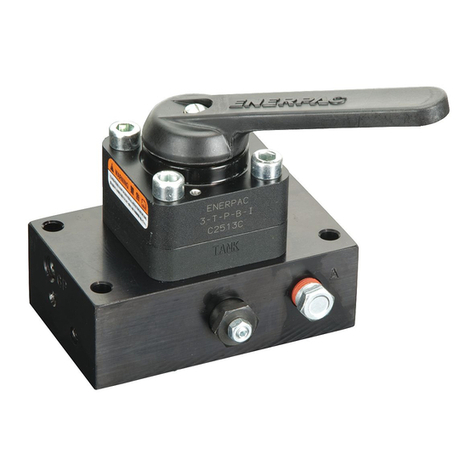
Enerpac
Enerpac VM33 Use and care manual
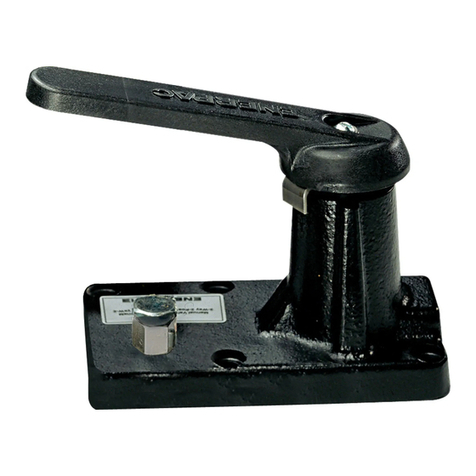
Enerpac
Enerpac VM2 User manual

Enerpac
Enerpac VM2 User manual
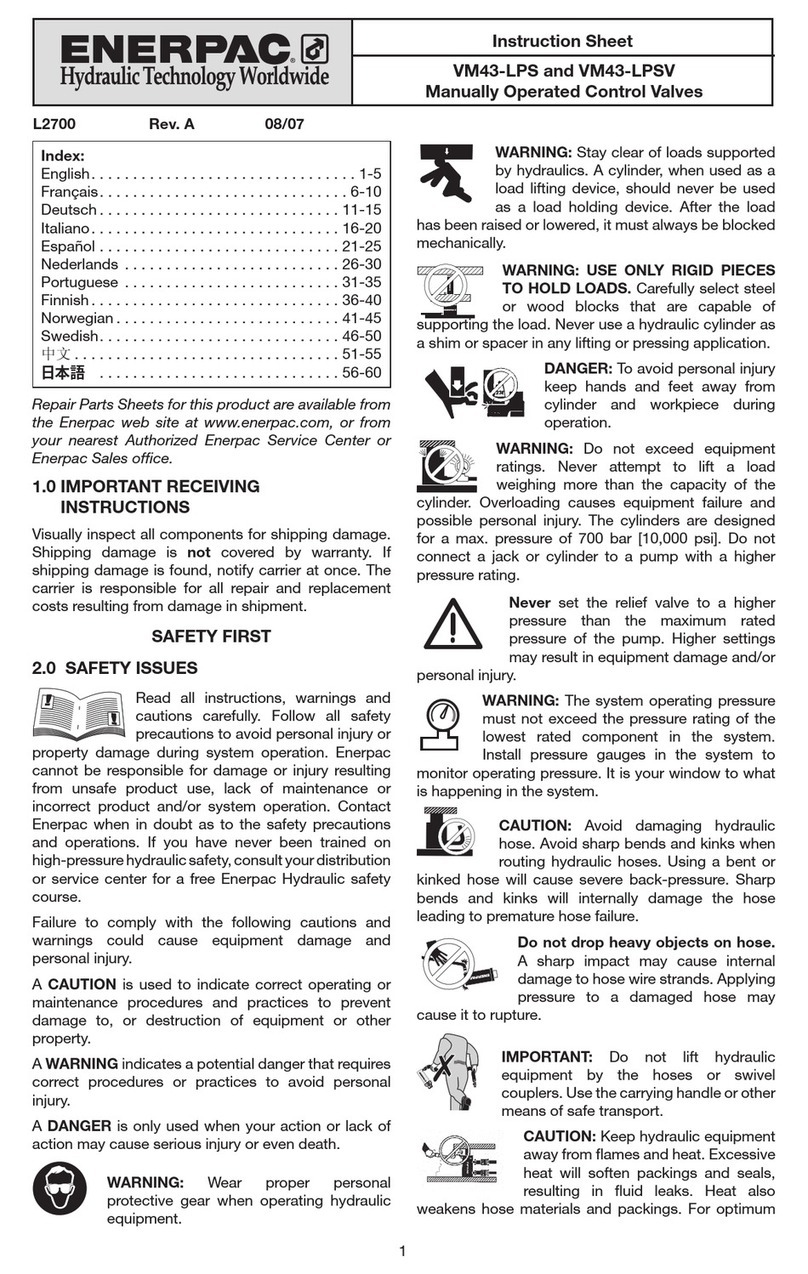
Enerpac
Enerpac VM43-LPS User manual
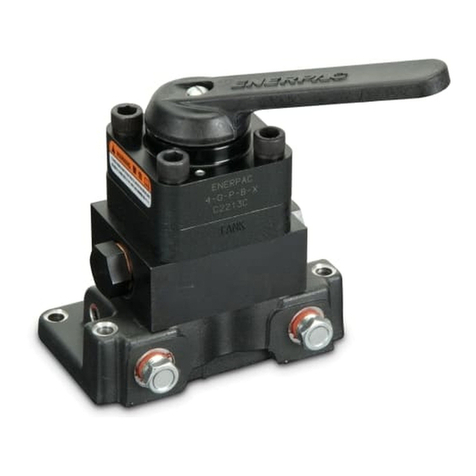
Enerpac
Enerpac VM3 User manual

Enerpac
Enerpac VE33VAC User manual
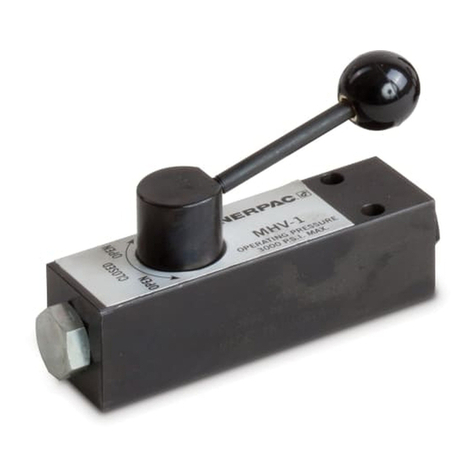
Enerpac
Enerpac MHV-1 User manual
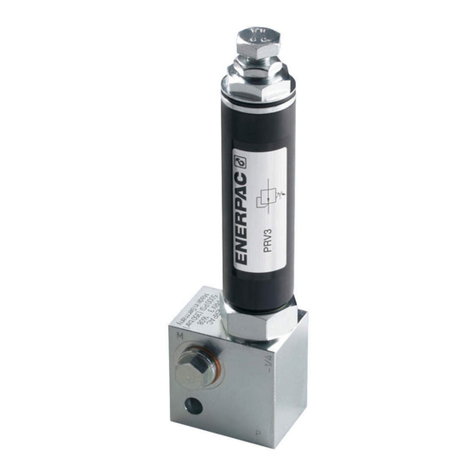
Enerpac
Enerpac PRV2 User manual
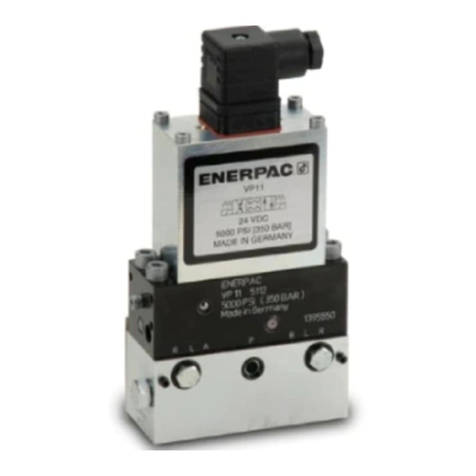
Enerpac
Enerpac VP Series User manual
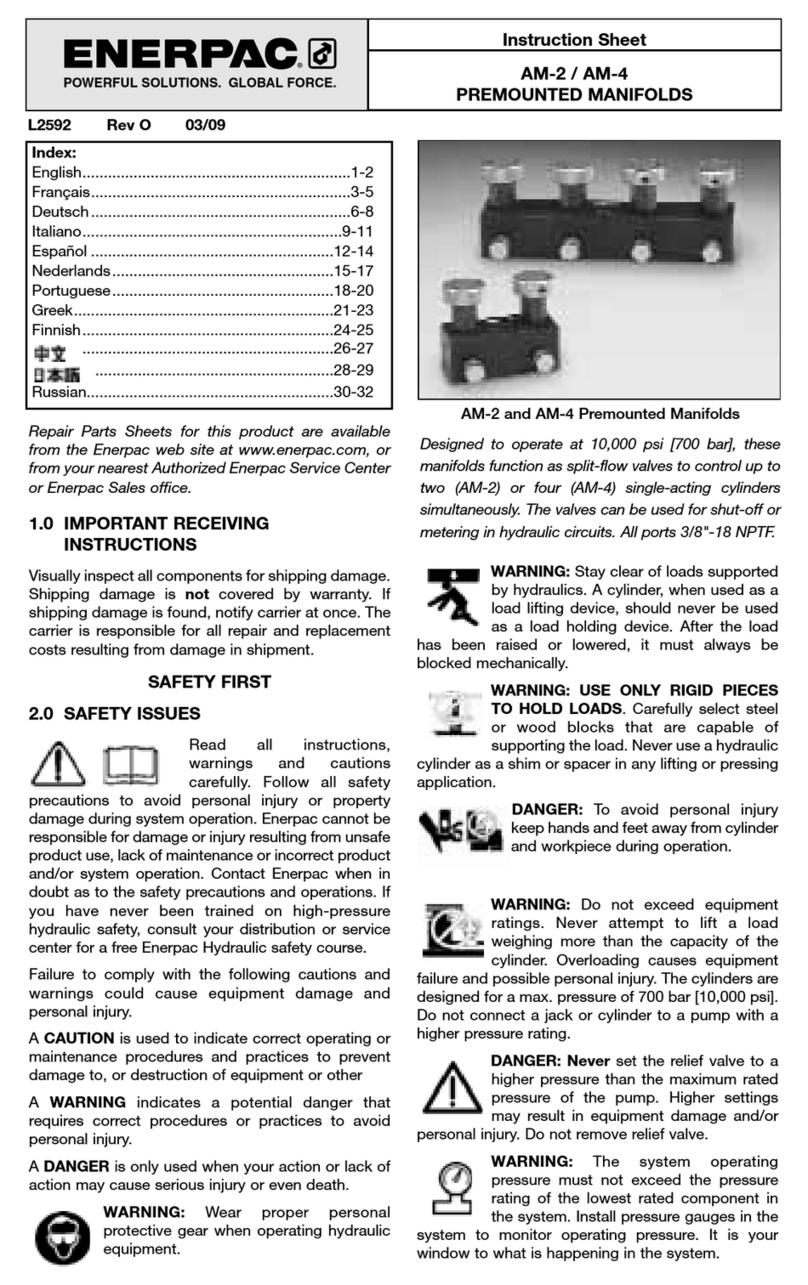
Enerpac
Enerpac AM Series User manual
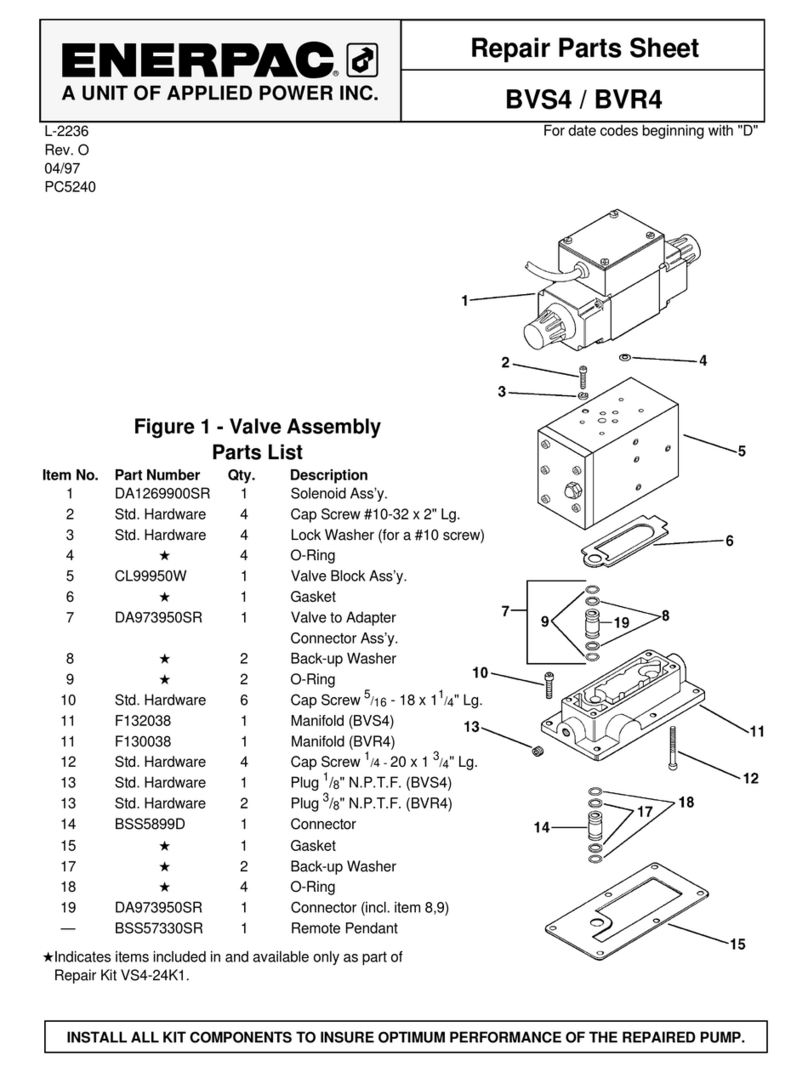
Enerpac
Enerpac BVS4 Use and care manual
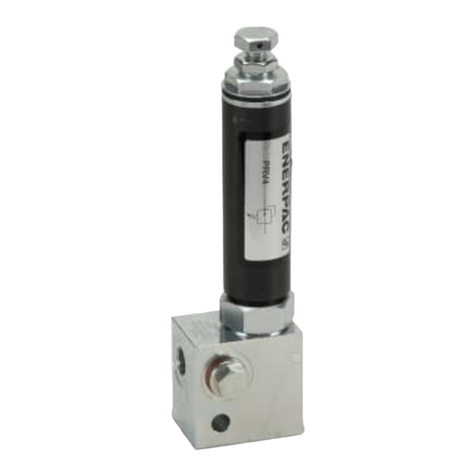
Enerpac
Enerpac PRV-8 User manual
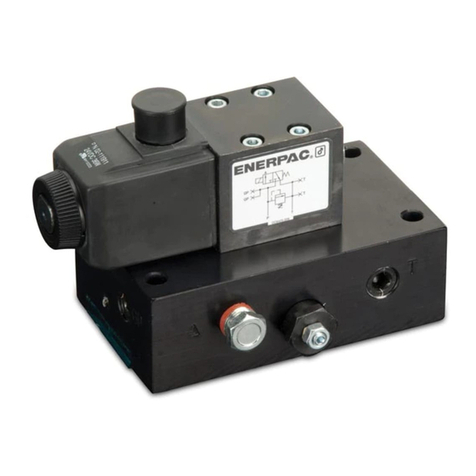
Enerpac
Enerpac VE32 Use and care manual
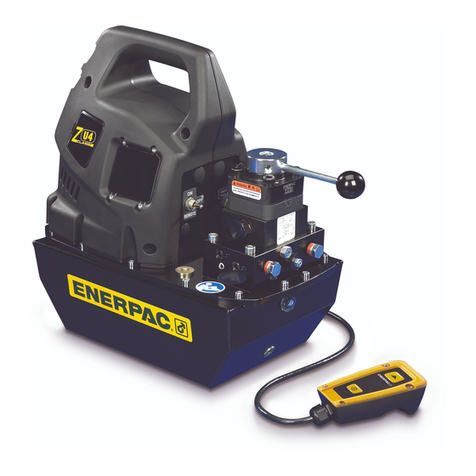
Enerpac
Enerpac VM43-LPS Use and care manual
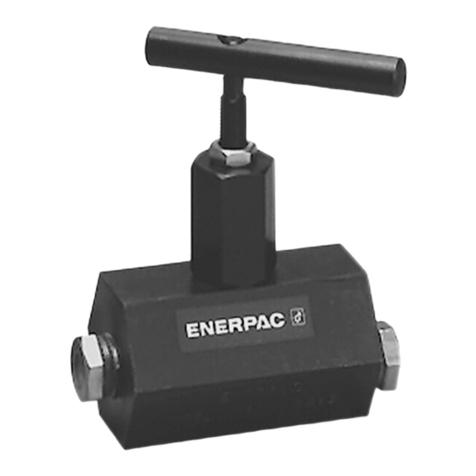
Enerpac
Enerpac V-161 User manual
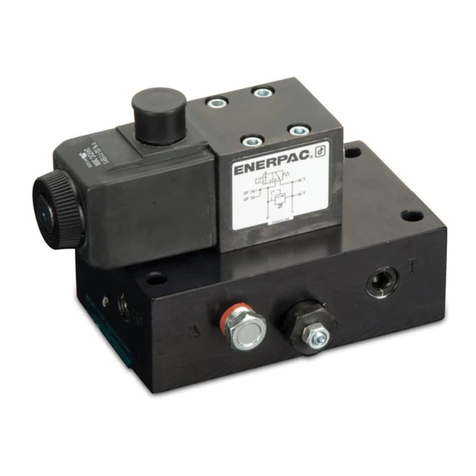
Enerpac
Enerpac VE32 User manual