Entes MPR-1 Series User manual

1
Network Analyzer
User Manual
MPR-1X
Series
www.entes.eu

2
SAFETY AND WARNING.............................................................................. 3
Attention.................................................................................................... 3
Safety ....................................................................................................... 3
OPERATING CONDITIONS .......................................................................... 4
INTRODUCTION........................................................................................... 5
General Specications.............................................................................. 5
Applications .............................................................................................. 6
MPR-1 Product Family.............................................................................. 7
Appearance and Interface ........................................................................ 7
Terminal Structures................................................................................... 8
Structure of the MPR-14S Terminal: ......................................................... 8
Structure of the MPR-15S-22 Terminal:.................................................... 9
Structure of the MPR-16S-21 Terminal:.................................................. 10
Structure of the MPR-17S-23 Terminal:...................................................11
CONNECTION TYPES................................................................................ 12
3P4W (Three-Phase Four-Wire) Connection.......................................... 12
3P3W (Three-Phase Three-Wire) Connection........................................ 13
ARON Connection .................................................................................. 13
3P4W BLN
(Three-Phase Four-Wire Balanced)
Connection .................. 14
3P3W BLN (Three-Phase Three-Wire Balanced) Connection................ 14
Communication Line Termination Resistance......................................... 15
Device Communication Settings............................................................. 16
TECHNICAL INFORMATION AND ATTACHMENTS................................... 17
Technical Information.............................................................................. 17
IEC 61557-12 Properties ........................................................................ 18
Compliance with the Standards .............................................................. 19
Index

3
SAFETY AND WARNING
Attention
If the following instructions are not carefully followed, the circumstances which can cause
death and serious injuries might happen.
• The installation of the device must be performed by the qualied and trained personnel.
• Please, cut the whole power while installing the device. Please, use a suitable circuit
breaker on the installation terminal.
• You must connect the power lead-ins of the device by using a current transformer. Do not
apply direct current connection.
• Never, remove the front panel while the device is connected to the mains.
•
Never, clean the device by any solvent or similar material. Only use dry cloth for cleaning it.
• Before, turning on the device, make sure that the connections are correct.
• Please, contact your authorized dealer in case of any problem with your device.
• The device is only for interior panel type assembly. Only the front panel of the device
should be accessible from the switchboard.
• The fuse to be used must be CATIII and F type and the current limit value should be 1A
• Current measurement inputs must be connected with auxiliary current
transformers which have reinforced insulation.
• The power meter shall not be used for primary protection or applications where
its failure can cause harm or death.
• Please de-energize the device before replacing RTC backup battery. It must be Li/MnO2
battery.
The manufacturer rm cannot be held responsible in any way for any circumstance which might
arise if the mentioned precautions are not implemented.
Safety
Please, read the entire operating manual before using the device.
•
Connect a button or a circuit breaker between the mains and the supply inputs of the device.
• The button or circuit breaker to be connected should be close to the device.
• It should be labeled that the button or circuit breaker to be connected will be used for
separating the device from the mains.
• This device is used for analyzing the electricity mains and it must not be used for main
protection function.
Guarantee
The guarantee term of the device is 2 (two) years. In case of any problem, the repair of
the device must be done only by the manufacturer rm; otherwise, the guarantee of the
device becomes invalid.

4
OPERATING CONDITIONS
Operating Conditions Value Range
Operating voltage 95-270 VAC/DC (±%10) ,12-50 VDC
(for MPR-1X-D )
Frequency Range 50 ~ 60 Hz. (Tolerances up to +/-10%)
Maximum Measured Current 6A, Measurement should not be done
without current transformer.
Maximum Measured Voltage 300 VAC (VLN) / 480x VAC (VLL)
Operating Temperature Range -10 ~ +70 ºC
Storage Temperature Range -20 ~ +80 ºC
Maximum Ambient Humidity % 95
Communication Speed 2400 ~ 115200 bps

5
INTRODUCTION
General Specications
• Wide supply voltage range (95 – 270 VAC/DC ±-10%, 12-50 VDC for MPR-1X-D series)
• 3 voltage measurement input
• 3 current measurement input
• 4 different language options
• 4 MB Internal Memory
• Real time clock (RTC)
• Alarm
• Time counters (Operating time and overall time)
• Measured parameters via RS-485 (MODBUS):
o Current
o Neutral current
o Voltage (Phase to Phase, Phase neutral)
o Active, Reactive and Apparent power
o Frequency
o Active Power
o Reactive Power
o Apparent Power
o Cos φ
o Power Factor
o Total Active Power
o Total Reactive Power
o Total Apparent Power
o Total Cos φ
o Total Power Factor
o Total Harmonic Distortion of the Current (% THD-I)
o Total Harmonic Distortion of Phase- Phase Voltages (% THD-VLL)
o Total Harmonic Distortion of Phase-Neutral Voltages (% THD-VLN)
Instant minimum and maximum measured parameters::
o Current
o Phase to Phase Voltage
o Phase Neutral Voltage
o Active Power
o Reactive Power
o Apparent Power
o Frequency
o Total Harmonic Distortion of the Current
o Total Harmonic Distortion of Phase - Phase Voltages (% THD-VLL)
o Total Harmonic Distortion of phase-neutral current (% THD-VLN)

6
Demand and Maximum Demand parameters measured by integration time:
o Current
o Active Power
o Apparent Power
• Insulated Digital Input and Output, Relay and Analog Output
• Saving 256 event logs
• DIN4 type rack assembly
• Measurement by 5 different connections: 3-phase 4-wire, 3-phase 3-wire, 3-phase
Aron, 3-phase 4-wire balanced, 3-phase 3-wire balanced
• Adjustable Demand time
• Summer-Winter time application
Applications
This is a MPR-1 series 3-phase mains analyzer. It is a microprocessor based device which
is designed for measuring all parameters of an electricity main; calculate consumptions and
transferring desired parameters with Modbus and I/O outputs.
Thanks to the RTC clock chip and ash memory of the device, the operations performed by
the operator such as interruption records, time and setting changes, reset operations are
recorded in real time. These records can be remotely read and monitored with Modbus RTU
protocol over RS-485 communication line.
The current connection is made by connecting it to a 1A or 5A secondary current
transformer.

7
MPR-1 Product Family
Appearance and Interface
The appearance of the device’s front is as below:
Product Code
3xV, 3xl, Frequency, W
VAr, VA,SP, SQ,SS, kWh,
kVArh, Demand,
Max, Min, Cosj, I nötr
95-270 VAC/DC Besleme
MPR-14S DIN4 128 4MB
MPR-15S-22 DIN4 2 2 128 4MB
MPR-16S-21 DIN4 51 2 1 128 4MB
MPR-17S-23 DIN4 51 2 2 1 128 4MB
12-50 VDC Besleme
MPR-14S-D DIN4 128 4MB
MPR-15S-22-D DIN4 2 128 4MB
MPR-16S-21-D DIN4 51 2 2 1 128 4MB
MPR-17S-23-D DIN4 51 2 2 1 128 4MB
% THD I
Dimensions
% THD V
AyrıAyrı
Number of Samples
Current-Voltage
95-270
RS-485
Digital Input
Digital Output
Analog Output
Harmonics
Relay Output
In one Period
Unbalances
VAC/DC
Memory
X/5,X/1
12-50 VDC

8
Terminal Structures
The terminal structures according to the models are described in this section:
Structure of the MPR-14S Terminal:
Current Terminals: K1, L1, K2, L2, K3, L3
An external current transformer must be used for the 3-phase system connection to these terminals
where the current up to 5A can be input.
Supply Terminals: A1, A2
Please, apply 95-270 VAC/DC (12-50 VDC for MPR-1X-D series) supply connection through
these terminals.
Voltage Terminals: N, L1, L2, L3
Please, apply 3-phase voltage connection through these terminals.
Communication Terminals: A(+), B(-), GND, TR
RS-485 communication terminals are used for Modbus RTU communication connection. A (+)
and B (-) terminals are connected in parallel between devices.
When the communication distance exceeds 10 meters and there are more than one device on
the line, communication instability may occur. In this case;
• A 120 Ohm connection resistor from the device box is installed between the A (+) terminal and
the B (-) terminal,
• Short circuit between the TR terminal and the A (+) terminal.
In this way, line balancing is done.
A(+) B(-)

9
Structure of the MPR-15S-22 Terminal:
DOC terminals is referred to digital output common, digital output reference connection is done
with this terminal.DO1 and DO2 is also referred to 1st and 2nd digital output terminals.
INC terminal is referred to Input Common and it is the digital input reference. IN1 and IN2 are also
referred 1st and 2nd digital input terminals.
Digital Input Terminals: INC, IN1, IN2
As the INC terminal will be the joint point (reference), the IN1 and IN2 inputs are used
as digital inputs between 5-30V. Inputs have 1kV insulation level.
Digital Output Terminals: OC, O1, O2
As the OC terminal will be the joint point (reference), the O1 and O2 terminals are used
as insulated outputs. As it can be seen from the following gure, these Open Collector
outputs should be fed by an external supply for operation.
5-30 VDC
MPR-1X
OC
O1
O2
Relay Coil

10
Structure of the MPR-16S-21 Terminal:
Different from the MPR-16S-21’den these terminals which are used for relay output are the
terminals next to the voltage terminals. They are indicated with the key symbol on the front view.
The terminal structure of the MPR16S-21 model is as in the following:
Digital Input Terminals: INC, IN1, IN2
As the INC terminal will be the joint point (reference), the IN1 and IN2 inputs are used
as digital inputs between 5-30V. Inputs have 1kV insulation level.

11
Structure of the MPR-17S-23 Terminal:
As the AOC terminal will be the joint point (reference), the analogue current or voltage output is
ensured respectively through the AIO and AVO terminals. Only one of the AVO and AIO terminals
are used at the same time.
Analog Output Terminals: AOC, AVO, AIO
AOC terminal is the common point (reference), and analog current or voltage output is provided
from the AIO and AVO terminals, respectively. Only one of the AVO and AIO terminals is used at
the same time.
Digital Input Terminals: INC, IN1, IN2
As the INC terminal will be the joint point (reference), the IN1 and IN2 inputs are used
as digital inputs between 5-30V. Inputs have 1kV insulation level.
Digital Output Terminals: OC, O1, O2
As the OC terminal will be the joint point (reference), the O1 and O2 terminals are used
as insulated outputs. As it can be seen from the following gure, these Open Collector
outputs should be fed by an external supply for operation.

12
CONNECTION TYPES
As there are shunts at the current measurement inputs of the device, it is mandatory to use
a current transformer except for the connections of current inputs. If, the device will be used
on the same current line by means of analyzers with other shunts, it is recommended that the
device is located at the extreme point.
The device has 5 different connection types. These connection types are described in the
following schemes:
3P4W (Three-Phase Four-Wire) Connection
As it is seen below, four voltage and three current connections including the neutral line are
established in this connection type.

13
3P3W (Three-Phase Three-Wire) Connection
As it is seen below, three voltage and three current connections are established in this
connection type.
ARON Connection
Three voltage and two current connections are established in this connection type. As it is
seen in the following gure, the current connections are established with the 1st and 3rd
phases.

14
3P4W BLN
(Three-Phase Four-Wire Balanced)
Connection
Four voltages and one current connection are established in this connection type. The
device displays the value measured at the current input connected to the rst phase on its
screen for other phases in the same value.
3P3W BLN (Three-Phase Three-Wire Balanced) Connection
Three voltage and one current connection are established in this connection type. As it is
seen below, the device displays the value measured at the current input connected to the
rst phase on its screen for other phases in the same value.

15
Communication Line Termination Resistance
RS-485 communication terminals are used for Modbus RTU communication connection. A
(+) and B (-) terminals are connected in parallel between devices. When the communication
distance exceeds 10 meters and there are more than one device on the line, communication
instability may occur. In this case;
• 120 Ohm line coming out of the device box between A (+) terminal and B (-) terminal.
termination resistor installed,
• Short circuit between the TR terminal and the A (+) terminal.
In this way, line balancing is done.

16
Device Communication Settings
Device communication address and baud rate settings are adjustable from the DIP switches
located at the device’s front panel. Devices communication address settings can be done, as
shown at the below table.
Number written to the Modbus 17124 address and the DIP switch’s 1st and 5th positions
determines the devices communication address. Factory settings for Modbus address is 1.
Number writ-
ten to Modbus
17124 address
DIP switch
setting
Address
1 10000 1
1 01000 2
… … …
111111 31
32 00000 32
32 10000 33
… … …
32 11111 63
… … …
64 00000 64
64 10000 65
64 01000 66
… … …
200 00000 192
200 10000 193
232 00000 224
… … …
232 11101 247
Baud rate is determined from DIP switch’s 6th, 7th and 8th pins as shown at the below.
Baud rate
000:2400
100:4800
010:9600
110:19200
001:38400
101:57600
011:115200
111:115200

17
TECHNICAL INFORMATION AND ATTACHMENTS
Technical Information
Technical properties Value
Dimensions DIN 4
Voltage measurement range 10~300 VAC(VLN) 10~480 VAC(VLL)
Measurement range with transformer 10V~999 kV
Accuracy %0.5 ± 1 digit
Input Impedance 1.8 MΩ
Burden (Input Load) < 0.5 VA
Current measurement accuracy %0.5 ± 1 digit
Nominal Current 1A, 5A
Lowest current 5 mA
Current measurement range 50 mA ~ 5,5A (Do not use without current transformer)
Measurement range with transformer 50 mA ~ 10 kA
Burden (Input Load) < 1 VA
Active power accuracy %1 ± 1 digit
Reactive power accuracy %1 ± 1 digit
Active energy measurement accuracy Class 1
Reactive energy measurement accuracy Class 2
Active power measurement range 0 ~ 1 GW
Reactive power measurement range 0 ~ 1 GVAr
Apparent power measurement range 0 ~ 1 GVA
Power consumption < 4 VA
Active energy measurement ceiling 9 999 999.9 kWh
Reactive energy measurement ceiling 9 999 999.9 kVArh
Operating voltage 95 - 270 VAC/VDC ,12 – 50 VDC (MPR-1X-D)
(Tolerances up to ± 10%)
Operating frequency 45 - 65 Hz.
Max. Voltage / Max. Current (For Relay) 250 VAC / 5A
Digital input processing voltage 5 ~ 30 VDC
Digital input switching current Max 50 mA
Minimum pulse time 100 ms pulse period, 80 ms pulse width
Operating Temperature Range -10 ~ +70 ºC
Storage Temperature Range -20 ~ +80 ºC
Maximum operating humidity 95 %
Assembly Assembled to the wall box from the front.
Connection terminals Screw terminal
Connection types 3 phase without neutral (3P3W)
3 phase + neutral (3P4W)
3 phase without neutral (3P3W) balanced
3 phase + neutral (3P4W) balanced
3 phase Aron
Communication Protocol RS-485 / MODBUS RTU
Communication Speed 2400 ~ 115200 bps

18
IEC 61557-12 Properties
CONFORMITY IEC 61557-12 Edition 2
PMD SPECIFICATIONS
Type of Specication Examples of possible
specication values
Other additional
specications
Supply quality evaluation
function (option)
/ /
PMD Classication SD /
Set point K55 /
Humidity + Altitude / /
Operating performance class for
active power or active energy (if
function available)
0,5 /
Symbol for
functions
Measurement
range
Operating
performance class,
according to CEU
61557-12
according to KI
Other additional
specications
P10% to 120% In 0,5
Qa, Qv 10% to 120% In 1
Sa, Sv 10% to 120% In 1
Ea 0 to 99999999 kW/h 0,5
Era, Erv 0 to 99999999 kVar/h 1
Eapa 0 to 99999999 kVA/h 0,5
f45 to 65 Hz 0,02
I10% to 120% In 0,2
In, Inc 10% to 120% In 0,2
U10 to 520Vac ph/ph 0,2
Pfa, Pfv 0,5 ind to 0,8 cap 0,5
Udip, Uswl Unavailable function
Utr Unavailable function
Uint Unavailable function
Unba, Unb Unavailable function
Uh Unavailable function
THDu Fn=50Hz - range 1 to 50
Fn=60Hz - range 1 to 50 1
THD-Ru Unavailable function
Ih Unavailable function
THDi Fn=50Hz - range 1 to 50
Fn=60Hz - range 1 to 50 1
THD-Ri Unavailable function
Msv Unavailable function

19
Compliance with the Standards
Standard Year Title
IEC 61557-12 2008 Electrical safety in low voltage distribution systems up to
1kV (a.a.) and 1,5kV DC(d.a.) – Equipment for testing,
measuring or monitoring of protective measures - Part 10:
Performance measuring and monitoring arrangements
IEC 61326-1 2005 Electrical equipment for measurement, control and
laboratory use - EMC requirements - Part 1: General
conditions
EN 61000-6-2 2005 Electromagnetic compatibility (EMC) - Part 6-2: General
standards - Immunity for industrial environments
IEC
60050(161)
2011 International Electro-technical Vocabulary Chapter 161-
Electromagnetic Compatibility
EN 62053-21 2003 Electricity measurement equipment (a.a.) - Special rules
- Chapter 21: Static meters for active energy (class 1 and
class 2)
EN 62053-23 2003 Electricity measurement equipment (a.a.) - Special rules -
Chapter 23: Static meters - Reactive energy (class 2 and
class 3)
EN 61000-4-2 1995 Electromagnetic compatibility (EMC) - Part 4-2: Test and
measurement techniques - Electrostatic discharge immu-
nity test
EN 61000-4-3 2006 Electromagnetic compatibility (EMC) - Part 4-3: Test and
measurement techniques-Radiated, radio- frequency,
electromagnetic eld immunity test
EN 61000-4-4 2004 Electromagnetic compatibility (EMC) - Part 4-4: Test and
measurement techniques - Electrical fast transient/burst
immunity test
EN 61000-4-5 2006 Electromagnetic compatibility (EMC) - Part 4-5: Test and
measurement techniques - Surge immunity test
EN 61000-4-6 2007 Electromagnetic compatibility (EMC) - Part 4-6: Test and
measurement techniques - Immunity to conducted distur-
bances, induced by radio-frequency elds
EN 61000-4-8 2010 Electromagnetic compatibility (EMC) - Part 4-8: Test and
measurement techniques-Power Frequency Magnetic
Field Immunity Test
EN 61000-4-11 2004 Electromagnetic compatibility (EMC) - Part 4-11: Test
and measurement techniques - Voltage dips, short
interruptions and voltage variations immunity tests

20
EN 61000-6-3 2007 Electromagnetic compatibility (EMC) - Chapter 6-3: Gen-
eral standards - Emission Standard for residential, Com-
mercial and light-industrial environments
EN 61000-3-2 2010 Electromagnetic compatibility (EMC) - Part 3-2: Limit
values - limits for harmonic current emissions (equipment
input current ≤ 16 A per phase)
EN 61000-3-3 2011 Electromagnetic compatibility (EMC) - Part 3-3: Limits -
Limitation of voltage uctuations and icker in low- voltage
supply systems for equipment with rated current kleiner 16
A
EN 55016-2-1 2009 Specication for radio disturbance and immunity meas-
uring apparatus and methods - Chapter 2-1: Methods of
measurement of disturbances and immunity - Conducted
disturbance measurements
EN 60068-2-2 2008 Basic environmental testing procedures Part 2:tests-Test
B: Dry heat
EN 60068-2-6 2007 Environment test - Chapter 2-6: Tests - Fc tests: Vibration
(sinus formed)
EN 60068-2-
30
2008 Environmental testing -- Part 2-30: Tests - test db: Damp
heat, cyclic (12 h + 12 h cycle)
EN 60068-2-
31
2010 Environmental testing -- Part 2-31: Tests - test ec: Rough
handling shocks, primarily for equipment-type specimens
EN 60068-2-
75
1997 Basic Environmental Testing Procedures Part 2: Tests -
test eh: Hammer tests
BS EN 61010-
1
2010 Safety requirements for electrical equipment for measure-
ment, control and laboratory use-Part 1:General require-
ments
EN 61010-2-
030
2010 Safety requirements for electrical equipment for measure-
ment, control and laboratory use-Part 2-030: Specic rules
for test and measurement of circuits
EN 62262 2010 Degrees of protection provided by enclosures for electrical
equipment against external mechanical impacts (IK code)
/ Note: Includes Corrigendum of July 2002 (EN 50120 +
A1 are renumbered as EN 62262:2002)
This manual suits for next models
8
Table of contents
Other Entes Measuring Instrument manuals
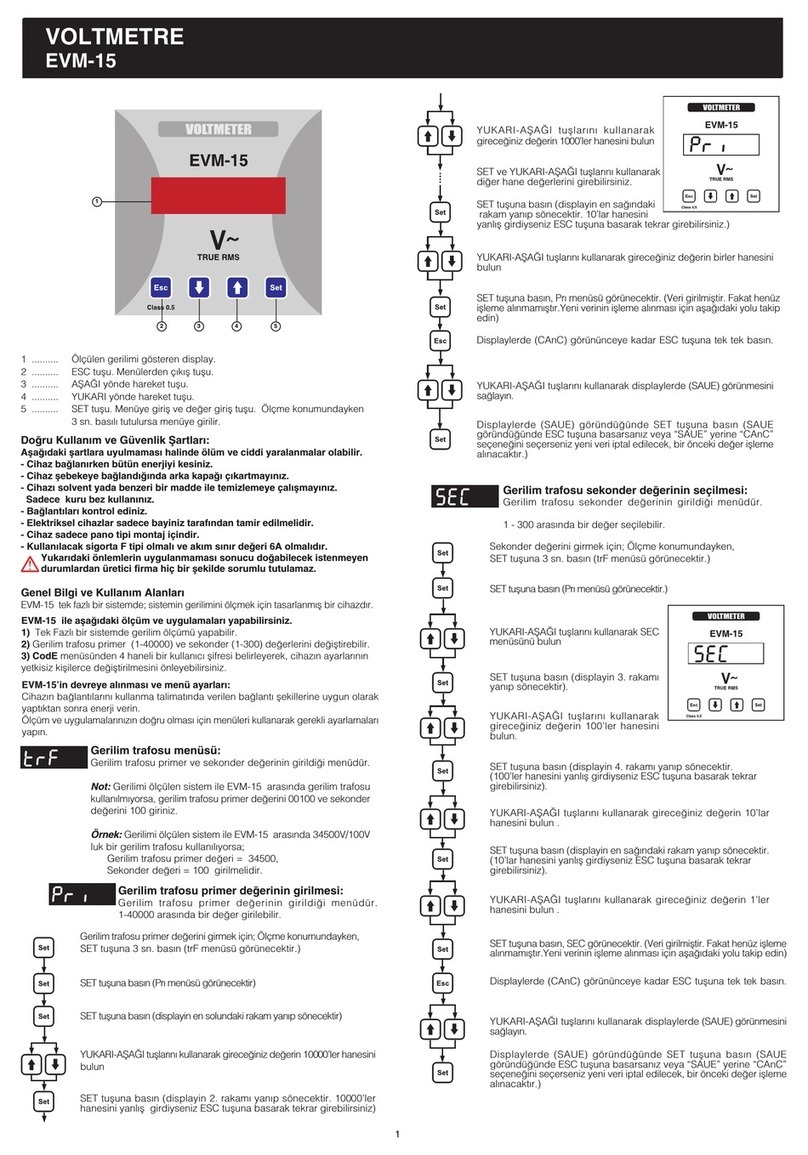
Entes
Entes EVM-15 User manual
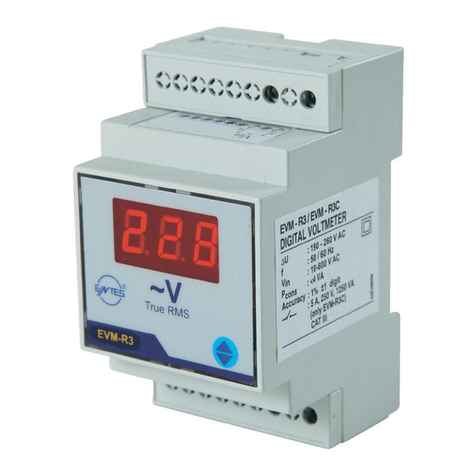
Entes
Entes EVM-R3 User manual
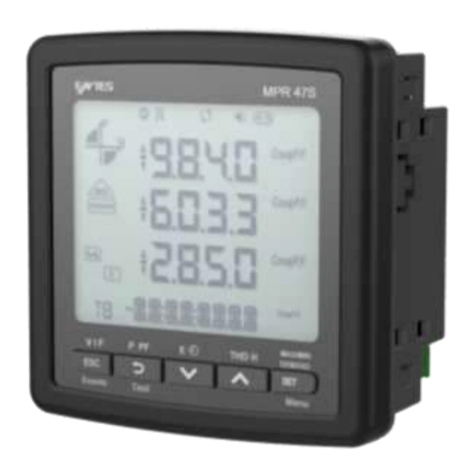
Entes
Entes MPR-4 Series User manual

Entes
Entes EMG Series User manual
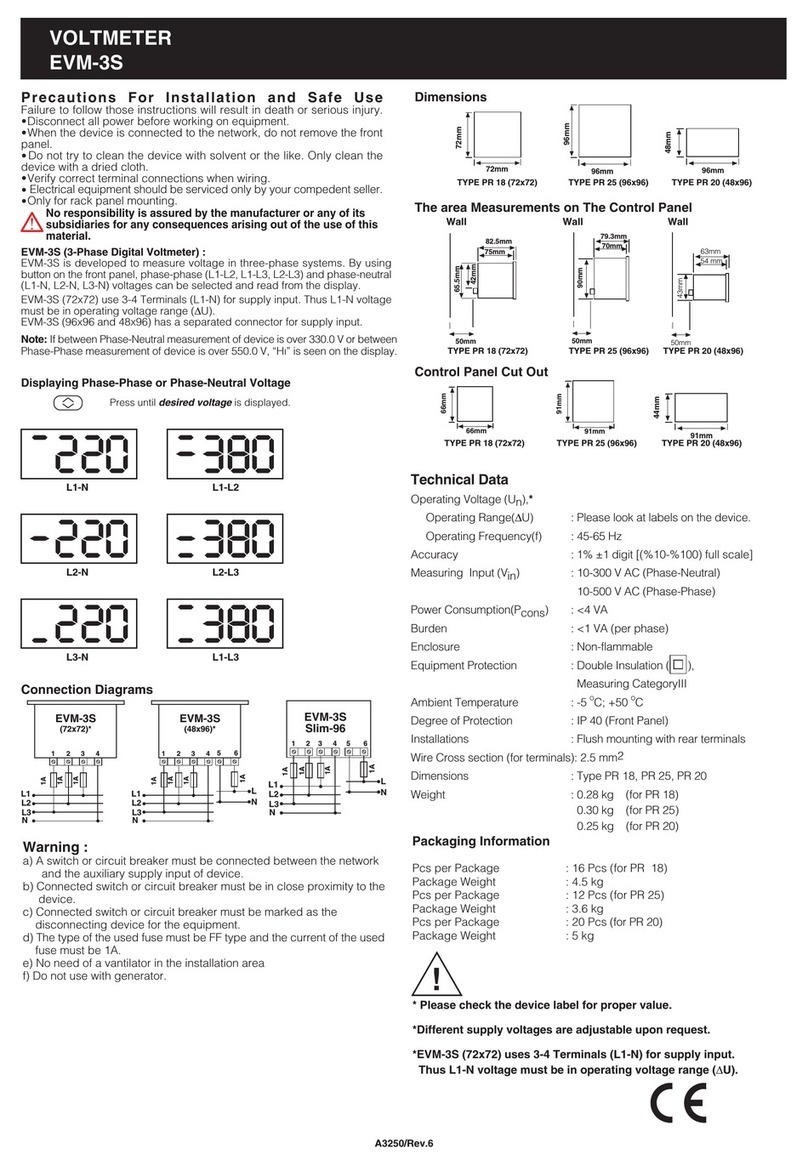
Entes
Entes EVM-3S User manual
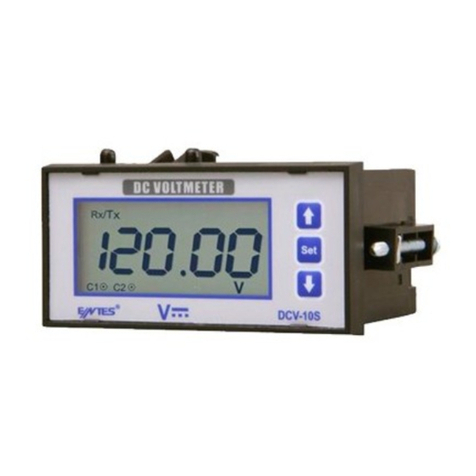
Entes
Entes DCV-10 User manual
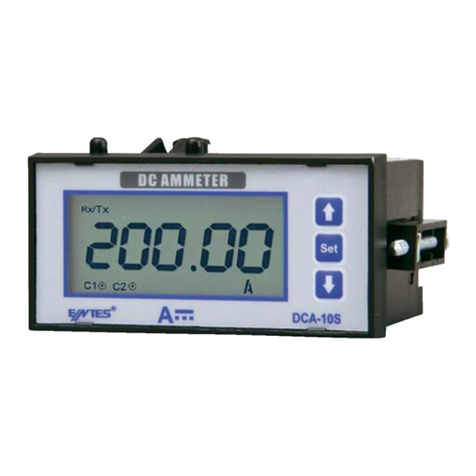
Entes
Entes DCA-10 User manual
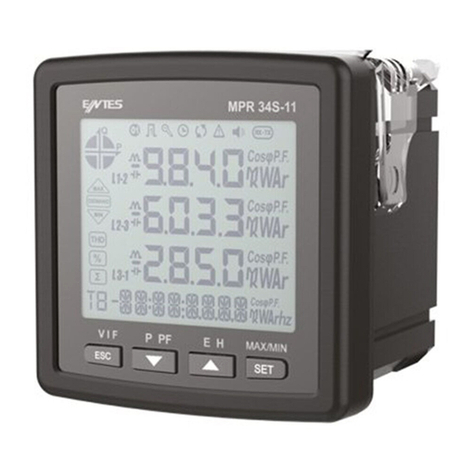
Entes
Entes MPR-32 User manual

Entes
Entes MPR-53S User manual
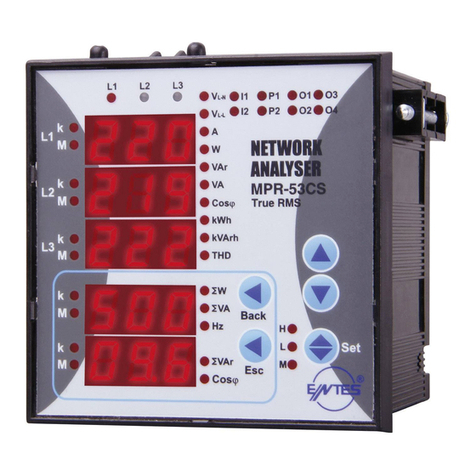
Entes
Entes MPR-53CS User manual
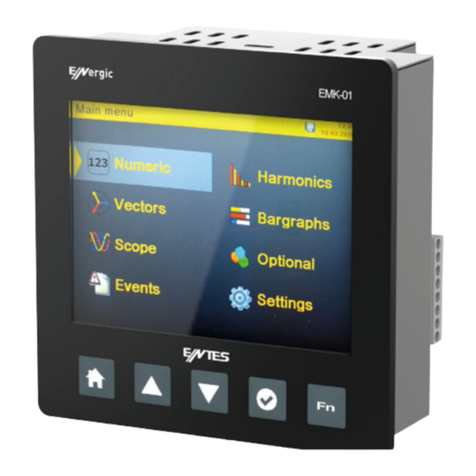
Entes
Entes EMK-01 User manual
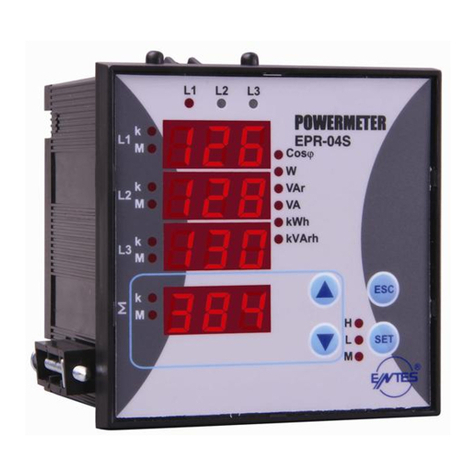
Entes
Entes EPR-04 Instruction manual
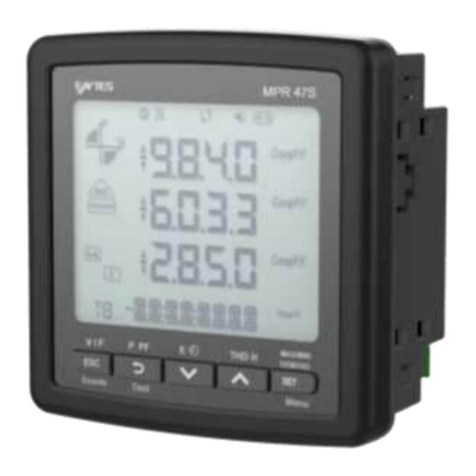
Entes
Entes MPR-4 Series User manual
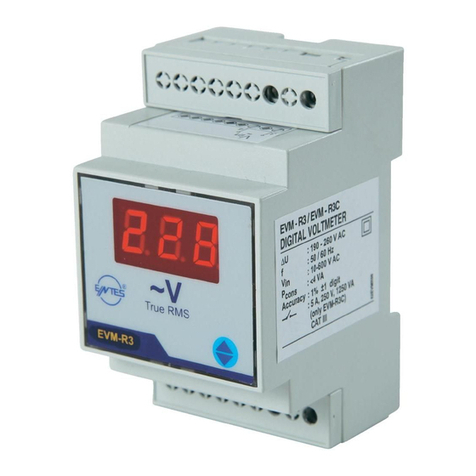
Entes
Entes EVM-R3 User manual

Entes
Entes EPM-4A User manual
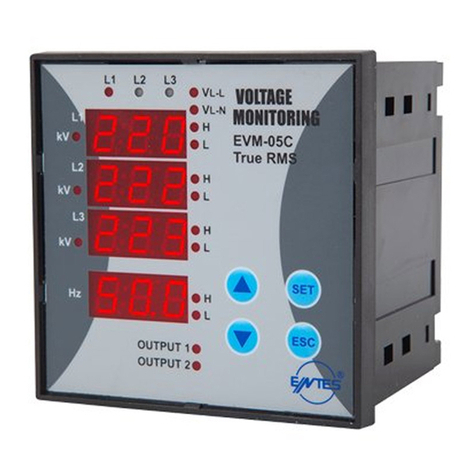
Entes
Entes EVM-05C User manual
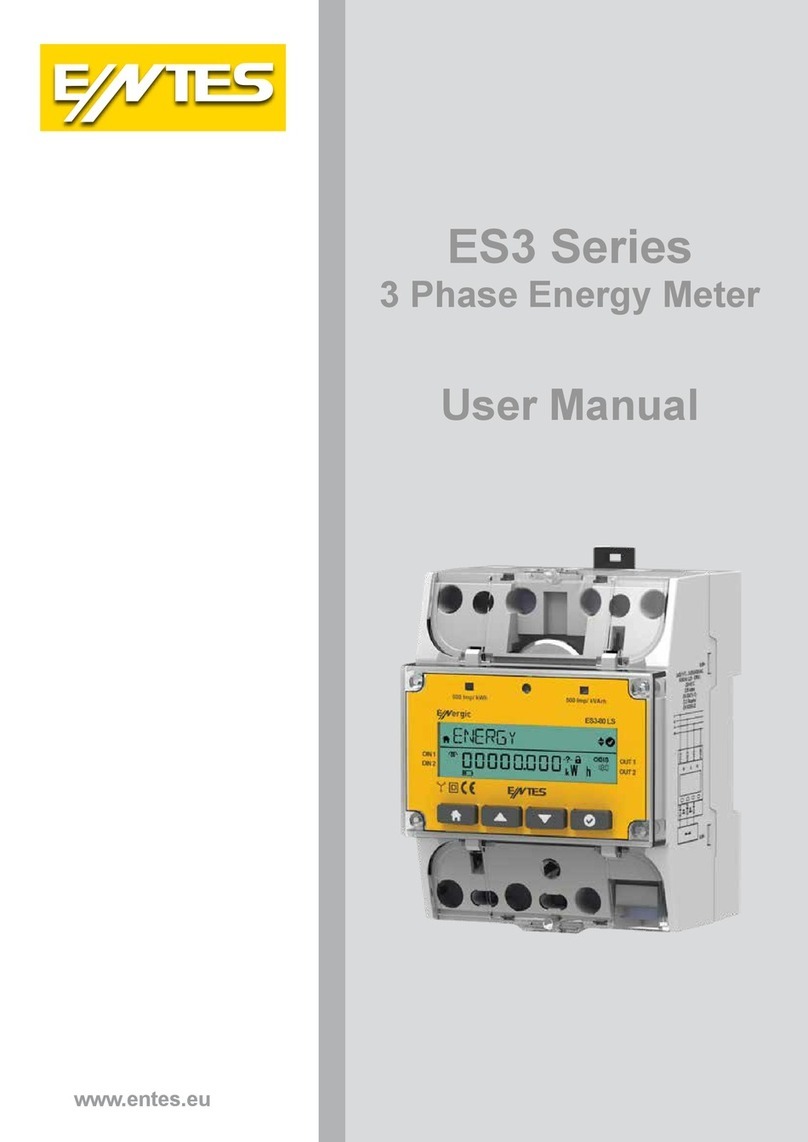
Entes
Entes ES3 Series User manual
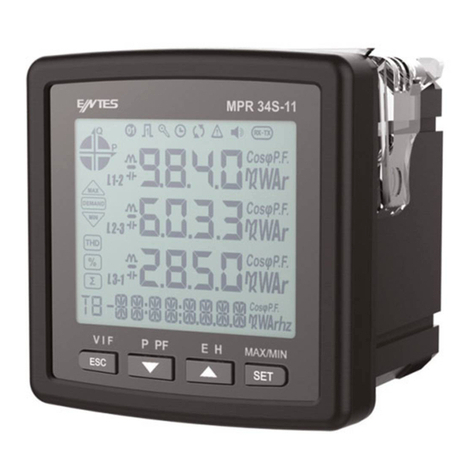
Entes
Entes MPR-3 Series User manual
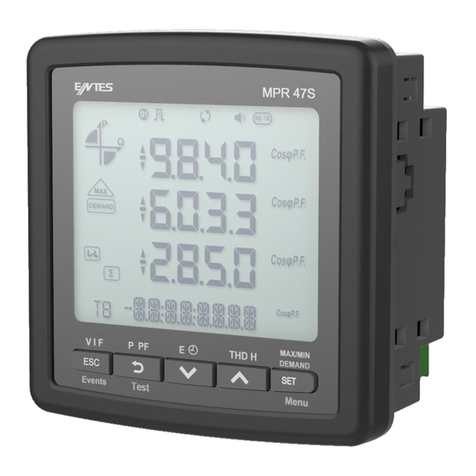
Entes
Entes MPR-45 User manual
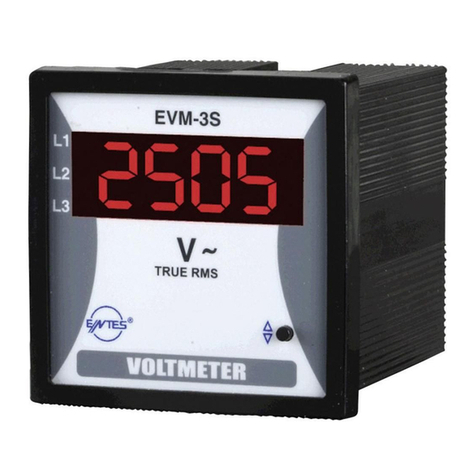
Entes
Entes EVM-3 Instruction manual