FANOX SIL-A User manual

www.fanox.com EN_FANOXTD_GUIDE_SIL_OCEFPrimaryDist_SILA_R002.doc 2 / 36
1...... RECEPTION & INSTALLATION..........................................................................................3
1.1. Relay unpacking.............................................................................................................3
1.2. Relay verification............................................................................................................3
1.3. Powering the relay up....................................................................................................4
1.3.1Keypad & LCD ................................................................................................................ 5
1.3.2Test Menu........................................................................................................................5
1.4. Relay installation............................................................................................................6
1.5. Relay rear part ................................................................................................................ 7
1.6. Connection diagram.......................................................................................................8
2...... USER INTERFACE.............................................................................................................. 8
2.1. Relay front part............................................................................................................... 8
2.2. LED indicators................................................................................................................ 8
2.3. How to install SICOM software ..................................................................................... 9
2.4. Setting-up the session: Password and access levels................................................ 9
3...... FUNCTIONAL DIAGRAM ..................................................................................................10
4...... SELECTION & ORDERING CODES................................................................................. 10
5...... TECHNICAL SPECIFICATIONS........................................................................................10
5.1. IEC60255-151 Curves...................................................................................................11
5.2. IEEE Curves.................................................................................................................. 16
6...... PROGRAMABLE LOGIC CONTROL................................................................................17
7...... FLOWCHART.....................................................................................................................20
7.1. Test menu...................................................................................................................... 20
7.2. Direct Access................................................................................................................21
7.3. Menus............................................................................................................................22
8...... COMMISIONING ................................................................................................................ 30
8.1. Thermal resistance.......................................................................................................31
8.2.Measurements .............................................................................................................. 31
8.3.Protection functions ....................................................................................................32
9...... SILA PROTOCOL..............................................................................................................35

www.fanox.com EN_FANOXTD_GUIDE_SIL_OCEFPrimaryDist_SILA_R002.doc 3 / 36
1. RECEPTION & INSTALLATION
1.1. Relay unpacking
Previously to any handling action, confirm
that relay carton box is in good conditions,
no broken or damaged due to external
manipulation or during storing or moving
process. If packing is correct, proceed to
unpack and you should find following
element:
•SILA Electronic protection relay.
•User Guide.
•Testing protocol.
Testing protocol is a certificate that relay has passed all factory testing process with correct
results.
In case some fault is detected, consider putting into quarantine period the relay and contact
Fanox for further instructions.
1.2. Relay verification
When relay is unpacked, please, take your time to confirm following checking list to be sure that
everything is ok:
•Metallic case not damaged and well
assembled. No loose screws due to
transport or movement conditions
•LCD and front cover not damaged
or scratched.
•Quality sticker and terminal sticker
correctly stuck.
•Rear terminals in good state, being
able to do a good wiring
connection.

www.fanox.com EN_FANOXTD_GUIDE_SIL_OCEFPrimaryDist_SILA_R002.doc 4 / 36
1.3. Powering the relay up
Thanks to the external battery KITCOM the powering and adjusting process of the relay is very
easy and it allows the user to test the relay.
The power comes from two AA batteries (IEC LR06) of 1.5 Volts placed at the bottom of the
kitcom. The equipment has a small Dc/Dc power supply that raises the voltage till the required 5
volts to operate the equipment and that is plugged into the front RS232 communications port
(KITCOM).
The relay is totally maintenance free. This is, there is no need of batteries to log events and
fault reports and there is no need of batteries to maintain date and time.
Besides, the possibility of using external battery power, together with the possibility of activating
the trip contact from the test menu, allows the trip circuit to be tested before the distribution
center is powered up.
The SIL-A is designed to be powered with an auxiliary voltage of 24-230Vac/dc.
The tolerance for the voltage is -20%/+10%. Outside of this range is possible for the relay to
work but is not guaranteed.
Once the relay is powered through the Kitcom, it should be checked:
•Model →Directly, complete model
on top line and phases/neutral
current measurement on bottom
line are displayed. Once “C” key is
pressed the name of phase and
neutral currents (instead the
complete model) is displayed on
the top of LCD Standby screen.
•Serial Number →In “General
Settings” menu serial number of 8
digits can be checked
(OK - ▼- ▼ - ◄ - ▼ - ▼)
•Firmware Version →In “Firmware
Version” menu (HOLD ▲)

www.fanox.com EN_FANOXTD_GUIDE_SIL_OCEFPrimaryDist_SILA_R002.doc 5 / 36
1.3.1.Keypad & LCD
•Use KEYPAD to ensure that all the
push-buttons work correctly (no
difficulties while pushing them,
check out if the relay reacts by
pushing each of the buttons)
•Use KEYPAD to enter in the relay´s menu and make sure that no text is lost while going
from one menu to another.
•Follow the sequence: Left ◄, Down
▼, Right ►, Up ▲, OK, C and
RESET and the following screen
should be displayed:
•If the contrast of the LCD is ot the
correct one, enter to “CONTRAST”
menu by holding “◄” for 3 seconds.
Then, change it by using up and
dwon buttons to increase or
decrease the contrast.
1.3.2.Test menu
NOTE: When performing test menu, protection won´t be available and it will be possible to open
circuit breaker. Only authorized personnel can do this job.
Press ◄,▼,► sequentially and hold OK. The relay will ask for the password “5555” to enter to
the test menu (or customer password if default “5555” has been modified).
LEDs and outputs will be checked to verify
the hardware is OK:
For adaptation C, all LEDs are turned on
when Test Menu is active. Just Outputs can
be activated/deactivated.
For adaptation B, LEDs and Outputs can be
activated/deactivated.
Adaptation C:
Action
Checking
▼, OK
Output 1
Output 1 activated
▼, OK
Output 2
Output 2 activated
▼, OK
Output 3
Output 3 activated
▼, OK
Output 4
Output 4 activated
C
Skip from test menu

www.fanox.com EN_FANOXTD_GUIDE_SIL_OCEFPrimaryDist_SILA_R002.doc 6 / 36
Adaptation B:
Action
Checking
OK, OK
Led1
Led1 activated
▼, OK
Led2
Led2 activated
▼, OK
Led3
Led3 activated
▼, OK
Led4
Led4 activated
▼, OK
Led5
Led5 activated
▼, OK
Led6
Led6 activated
▼, OK
Led-52
Led-52 activated
▼, OK
Led-79
Led-79 activated
▼, OK
Output 1
Output 1 activated
▼, OK
Output 2
Output 2 activated
▼, OK
Output 3
Output 3 activated
▼, OK
Output 4
Output 4 activated
C
Skip from test menu
1.4. Relay installation
To fix the relay to the switchgear, use default holes in front of relay with appropriate fixing
system. Do not manipulate relay to fix it on the switchgear.
Failure to follow these instructions can result in death, serious injury, or equipment damage.

www.fanox.com EN_FANOXTD_GUIDE_SIL_OCEFPrimaryDist_SILA_R002.doc 7 / 36
1.5. Relay rear part
Consider the wiring of the switchgear and connect relay properly:
D1
+ RS485 Modbus RTU, DNP3.0 Serial or
IEC60870-103 depending on model (*)
D14
NO digital output 2
D2
–RS485 Modbus RTU, DNP3.0 Serial or
IEC60870-103 depending on model (*)
D15
NC digital output 2
D3
Digital input 1
D16
Digital 2 common output
D4
Digital input 2
D17-D18
NO digital output 3
D5
Common inputs 1 and 2
D19-D20
NO digital output 4
D6
Digital input 3
D21
+Auxiliary voltage.
D7
Digital input 4
D22
-Auxiliary voltage.
D8
Digital input 5
A1-A2
Phase A current measurement
D9
Digital input 6
A3-A4
Phase B current measurement
D10
Common digital inputs 3, 4, 5 and 6
A5-A6
Phase C current measurement
D11
NO digital output 1
A7-A8
Neutral current measurement
D12
NC digital output 1
E
IEC 61850, DNP3.0 TCP/IP, IEC60870-104 or
Modbus TCP/IP depending on model (*)
D13
Digital 1 common output

www.fanox.com EN_FANOXTD_GUIDE_SIL_OCEFPrimaryDist_SILA_R002.doc 8 / 36
1.6. Connection diagram
2. USER INTERFACE
2.1. Relay front part
2.2. LED indicators
The SILA front panel has 8 LEDs. The operation of the LED indicators can be checked from the
test menu.
The user can change the configuration of the LEDs depending on its requirements.

www.fanox.com EN_FANOXTD_GUIDE_SIL_OCEFPrimaryDist_SILA_R002.doc 9 / 36
2.3. How to install SICOM software
To install the SICom it is necessary the following link:
http://fanox.blob.core.windows.net/sicom/publish.htm
The link will open the next screen, where button “install” must be pressed:
The necessary drivers depending on the operative system can be downloaded from this page.
The update of the software does not require any user´s action, this is, if the computer is
connected to Internet, SICom updates itself when it is started.
2.4. Setting-up the session: Password and access levels
Users must identify themselves with a password to start communications and to change the
equipment settings or configuration using the HMI. Depending on the access level, it may or
may not be possible to perform the operations shown on the table below.
ACCESS
LEVEL
Read-only
permission:
Status and
measurements
Settings
Configuration
Events/DFR
Permission to:
Change settings
Permission to:
Delete Events
Delete DFR
Permission to:
Execute
Commands
Set Counters
Permission to:
Change
Configuration
Permission to
Change
Protected
Settings
2
YES
YES
YES
NO
NO
NO
3
YES
NO
NO
YES
NO
NO
4
YES
YES
YES
YES
NO
NO
5
YES
YES
YES
YES
YES
NO
Four passwords and their associated levels of access are set up when the equipment is
configured using the SIcom program. By default, the equipment is programmed with the
following passwords and their associated levels:
PASSWORD
ACCESS LEVEL
2222
2
3333
3
4444
4
5555
5

www.fanox.com EN_FANOXTD_GUIDE_SIL_OCEFPrimaryDist_SILA_R002.doc 11 / 36
5. TECHNICAL SPECIFICATIONS
50_1
50_2 (*)
Function Enable: Yes/No/SHB(*)
Current Tap: 0.10 to 30 xIn (step 0.01)
Time Delay: 0.00(*) to 300 s (step 0.01 s)
Activation level 100%
Deactivation level 95%
Instantaneous deactivation
Timing accuracy:
If Time Delay 0.00 to 0.02 s: ± 50 ms or ± 0.5% (greater of both).
If Time Delay 0.02 to 300 s: ± 30 ms or ± 0.5% (greater of both).
50N/G_1
50N/G_2 (*)
Function Enable: Yes/No/SHB(*)
Current Tap: 0.05(*) to 30 xIn (step 0.01)
Time Delay: 0.00(*) to 300 s (step 0.01 s)
Activation level 100%
Deactivation level 95%
Instantaneous deactivation
Timing accuracy:
If Time Delay 0.00 to 0.02 s: ± 50 ms or ± 0.5% (greater of both).
If Time Delay 0.02 to 300 s: ± 30 ms or ± 0.5% (greater of both).
50/51
Function Enable: Yes/No/SHB(*)
Current Tap: 0.10 to 7 xIn (step 0.01)
Curves IEC 60255-151 and IEEE
Curve Type: IEC Inverse curve, IEC very inverse curve, IEC extremely inverse curve IEC long time
inverse, IEEE Inverse curve, IEEE very inverse curve, IEEE extremely inverse curve, Defined Time.
Time Delay: 0.00(*) to 300 s (step 0.01 s)
Time Dial (TMS): 0.02 to 2.20 (step 0.01)
Curve, activation level 110%
Curve, deactivation level 100%
Defined time, activation level 100%
Defined time, deactivation level 95%
Instantaneous deactivation
Timing accuracy for IEC and IEEE curves selection:
± 30 ms or ± 5% (greater of both).
Timing accuracy for defined time curve selection:
If Time Delay 0.00 to 0.02 s: ± 50 ms or ± 0.5% (greater of both).
If Time Delay 0.02 to 300 s: ± 30 ms or ± 0.5% (greater of both).
50/51N/G
Function Enable: Yes/No/SHB(*)
Current tap: 0.05(*) to 7 xIn (step 0.01)
Curves IEC 60255-151 and IEEE
Curve Type: IEC Inverse curve, IEC very inverse curve, IEC extremely inverse curve IEC long time
inverse, IEEE Inverse curve, IEEE very inverse curve, IEEE extremely inverse curve, Defined Time.
Time Delay: 0.00(*) to 300 s (step 0.01 s)
Time Dial (TMS): 0.02 to 2.20 (step 0.01)
Curve, activation level 110%
Curve, deactivation level 100%

www.fanox.com EN_FANOXTD_GUIDE_SIL_OCEFPrimaryDist_SILA_R002.doc 12 / 36
Defined time, activation level 100%
Defined time, deactivation level 95%
Instantaneous deactivation
Timing accuracy for IEC and IEEE curves selection:
± 30 ms or ± 5% (greater of both).
Timing accuracy for defined time curve selection:
If Time Delay 0.00 to 0.02 s: ± 50 ms or ± 0.5% (greater of both).
If Time Delay 0.02 to 300 s: ± 30 ms or ± 0.5% (greater of both).
46
Function Enable: Yes/No/SHB(*)
Current Tap: 0.10 to 7.00 xIn (step 0.01)
Curves IEC 60255-151 and IEEE
Curve Type: IEC Inverse curve, IEC very inverse curve, IEC extremely inverse curve IEC long time
inverse, IEEE Inverse curve, IEEE very inverse curve, IEEE extremely inverse curve, Defined Time.
Time Delay: 0.00(*) to 300 s (step 0.01 s)
Time Dial (TMS): 0.02 to 2.20 (step 0.01)
Curve, activation level 110%
Curve, deactivation level 100%
Defined time, activation level 100%
Defined time, deactivation level 95%
Instantaneous deactivation
Timing accuracy for IEC and IEEE curves selection:
± 30 ms or ± 5% (greater of both).
Timing accuracy for defined time curve selection:
If Time Delay 0.00 to 0.02 s: ± 50 ms or ± 0.5% (greater of both).
If Time Delay 0.02 to 300 s: ± 30 ms or ± 0.5% (greater of both).
Circuit breaker
monitoring
Maximum number of openings: 1 to 10,000 (step 1)
Maximum accumulated amperes: 0 to 100,000 (M(A²)) (step 1)
Opening time: 0.02 to 30 s (step 0.01 s)
Closing time: 0.02 to 30 s (step 0.01 s)
Excessive repeated openings: 1 to 10,000 (step 1)
Repetitive openings/Time: 1 to 300 min (step 1 min)
Open circuit breaker activation threshold: 8% In
Open circuit breaker reset threshold: 10% In
79
Function Enable: Yes/No
Hold Enable: Yes/No/No Time
Number of reclosings: 1 to 5
Reclose time 1, 2, 3, 4, 5: 0.02 to 300 s (step 0.01 s)
Hold time: 0.02 to 300 s (step 0.01 s)
Reset time: 0.02 to 300 s (step 0.01 s)
Safe time: 0.02 to 300 s (step 0.01 s)
Locking possibilities: pulse inputs, level inputs, commands.
50BF (*)
Function Enable: Yes/No
Time Delay: 0.02 to 1.00 s (step 0.01 s)
Open circuit breaker activation threshold: 8% In

www.fanox.com EN_FANOXTD_GUIDE_SIL_OCEFPrimaryDist_SILA_R002.doc 13 / 36
Open circuit breaker reset threshold: 10% In
Configurable function pickup
74TCS
Function Enable: Yes/No
Time Delay: 0.02 to 300 s (step 0.01 s)
Continuity in circuits A and B
Dedicated inputs
CLP
Function Enable: Yes/No
Settings group: 1 to 4 (step 1)
No load Time: 0.02 to 300 s (step 0.01 s)
Cold load Time: 0.02 to 300 s (step 0.01 s)
CLP activation threshold: 8% In
CLP reset threshold: 10% In
PGC
OR4, OR4_LATCH, OR4_PULSES, OR4_TIMERUP, OR4_PULSE, NOR4, NOR4_LATCH,
NOR4_TIMERUP, NOR4_PULSE, AND4, AND4_PULSES, AND4_TIMERUP, AND4_PULSE,
NAND4, NAND4_TIMERUP, NAND4_PULSE
86
Allows to latch (lock out) the contact trip due to programmable logic (PGC: LATCH).
49T
Available through configurable inputs thanks to the programmable logic
74CT (*)
Function Enable: Yes/No
Time Delay: 0.02 to 300 s (step 0.01 s)
Timing accuracy: ±30 ms or ±0.5% (greater of both)
37 (*)
Function Enable: Yes/No
Current Tap: 0.10 to 30 xIn (step 0.01)
Time Delay: 0.02 to 300 s (step 0.01 s)
Activation level: 100%
Deactivation level: 105%
Instantaneous reset
Timing accuracy: ±30 ms or ±0.5% (greater of both)
49 (*)
Function Enable: Yes/No
Current Tap: 0.1 to 2.4 xIn (step 0.01)
ζheating: 3 to 600 min (step 1 min)
ζcooling: 1 to 6 ζheating (step 1)
Alarm: 20 to 99 % (step 1%)
Trip level: 100%
Deactivation level: 95% of alarm level
Trip time accuracy: ± 5% over the theoretical value
Trip time curves are valid under 20 times the adjusted tap. With currents higher than 20 times the
adjusted tap, trip time and thermal image value are truncated to 20 times the adjusted tap.
46BC (*)
Function Enable: Yes/No
Current tap: 15 to 100% (step 1%)
Time Delay: 0.02 to 300 s (step 0.01 s)
Timing accuracy: ±30 ms or ±0.5% (greater of both)
SHB (*)
Function Enable: Yes/No

www.fanox.com EN_FANOXTD_GUIDE_SIL_OCEFPrimaryDist_SILA_R002.doc 14 / 36
Current tap: 5 to 50 % (step 1%)
Reset time: 0.00 to 300 (step 0.01s)
Block Threshold: 0.1 to 30 xIn (step 0.01)
TB (*)
Function Enable: Yes/No
Current Tap: 1.5 to 20 x In (step 0.01)
68
ZSI available through configurable inputs and outputs thanks to programmable logic
Settings Groupss
4 settings groups
Activated by inputs or by general settings.
Events
200 events
Disturbance fault
recording (DFR)
16 samples/cycle
Fault start configurable
20 fault reports with 24 events each one
5 COMTRADE records of 100 cycles: 3 prefault and 97 postfault cycles
COMTRADE IEEE C37.111-1991
4 analog channels and up to 48 digital channels
Load Data Profiling
(LDP)
Demand of current with the following characteristics:
•Number of records: 168
•Recording mode circular
•Sampling rate (interval): configurable through communications: 1 –60 min
•Record format:
Date/Time
IMAX (in interval)
IMAX (actual)
IA
IB
IC
IN
Inputs
Same voltage as the auxiliary power supply
Up to 6 configurable inputs (*)
Outputs
250 Vac –8 A
30 Vdc –5 A
4 configurable outputs
•Output 1 and Output 2: NC + NO
•Output 3 and Output 4: NO
Frequency
50/60 Hz selectable by general settings
Current
measurement
Phase current (IA, IB, IC), neutral (IN), positive sequence (I1), negative sequence (I2), phase
second harmonic current (IA-2H, IB-2H and IC-2H), maximum current (Imax) and thermal image (TI)
(*)
Fundamental values (DFT)
Sampling: 16 samples/cycle
±2% Accuracy over a band of ±20% over the nominal current and ±4% or ±5 mA (greater of both)
over the rest of the range
Saturation limit: 30 times rated current
Communications
LOCAL COMMUNICATION
1 Local port RS232: ModBus RTU
REMOTE COMMUNICATION (*)
1 remote port with the following options:

www.fanox.com EN_FANOXTD_GUIDE_SIL_OCEFPrimaryDist_SILA_R002.doc 15 / 36
•1 Remote port RS485: ModBus RTU, IEC 60870-5-103 or DNP3.0 Serial (by general
settings)
•1 Remote port RJ45: IEC 61850, DNP3.0 TCP/IP, Modbus TCP/IP or IEC 60870-5-104
(depending on model)
Auxiliary power
24-230 Vac/dc (-20%/+10%)
Environmental
conditions
Operating temperature: -10 to 70ºC
Storage temperature: -20 to 80ºC
Relative humidity: 95%
Transformers (*)
Measurement 3 or 4 CT /5 or /1
Measurement 3 LPCT (current transformers with voltage output)
Mechanical
Characteristics
Metallic box
Panel mounted.
Height x Width: 177 x 107 (mm)
Depth: 122.1 mm
Weight: 1.5 Kg
IP-54 on pannel
(*) Depending on model
(1) LPCT model→50N/G, 50/51N: calculated neutral;
Standard model→50N/G, 50/51N/G: measured neutral
5.1. IEC60255-151 Curves
The SIL-A relay complies with the curves shown in standard IEC 60255-151:
•Inverse Curve
•Very Inverse Curve
•Extremely Inverse Curve
•Long time Inverse Curve
There is a general mathematical equation that defines the time in seconds as a function of the
current:
KDB
QV DA
tP++
−
=
adjusted
II
V=
Parameters
A
P
Q
B
K
Long time Inverse
120
1
1
0
0
Ext. Inverse
80
2
1
0
0
Very Inverse
13,5
1
1
0
0
Inverse
0,14
0,02
1
0
0
The curve can move from its axis using the D time selection device, which the user can adjust.
Iadjusted is the initial operating current, set by the user.

www.fanox.com EN_FANOXTD_GUIDE_SIL_OCEFPrimaryDist_SILA_R002.doc 16 / 36
5.2. IEEE Curves
The SIL-A relay complies with the curves shown in standard IEEE:
•Inverse Curve
•Very Inverse Curve
•Extremely Inverse Curve
There is a general mathematical equation that defines the time in seconds as a function of the
current:
( )
+
−
= B
VA
TDtP1
adjusted
II
V=
Which relate to the parameters figuring in the following table:
Parameters
A
P
B
Ext. Inverse
28,2
2
0,1217
Very Inverse
19,61
2
0,491
Inverse
0,0515
0,02
0,114
The curve can move from its axis using the TD time selection device, which the user can adjust.
Iadjusted is the initial operating current, set by the user.

www.fanox.com EN_FANOXTD_GUIDE_SIL_OCEFPrimaryDist_SILA_R002.doc 17 / 36
6. PROGRAMABLE LOGIC CONTROL
Firstly, it is defined the concept of physical input, physical output and logical signal.
Physical inputs are the real inputs of the device. SIL-A device has physical inputs (6 inputs).
These inputs are translated to internal binary states which later, can be assigned to logical
signal to get a specific operation.
Physical outputs are the real outputs of the Device. SIL-A has 4 outputs and up to 8
configurable leds, which receive the same treatment as the physical outputs, some working on
output relays and others working on led diodes.
Logical signals are internal binary states resulting from control programmable logic. Each logical
signal has a specific meaning and is intended to be used by the functions of the device.
SIL-A Adaptation B
SIL-A Adaptation C
LEDs
LED 1
LEDs
LED 1
LED 2
LED 2
LED 3
LED 3
LED 4
LED 4
LED 5
LED 5
LED 6
LED 6
LED 52
LED 52
LED 79
LED 79
PHYSICAL OUTPUTS
Output 1
PHYSICAL OUTPUTS
Output 1
Output 2
Output 2
Output 3
Output 3
Output 4
Output 4
LOGICAL SIGNALS
52a
LOGICAL SIGNALS
52a
52b
52b
External Trip
External Trip
50BF Start (*)
50/51 Block
DFR Start
50/51N/G Block
79 Start
Settings group 1
79 Enable
Settings group 2
79 Level Block
Reset
79 Block
79 Start
79 Unblock
79 Enable
Block 50/51
79 Level Block
Block 50/51N/G
79 Block
Reset
79 Unblock
Settings group 1
DFR Start
Settings group 2
74TCS Continuity A
74TCS Continuity B
Logic Signal 1
Logic Signal 2
For each output, there is a LOGICAL GATE. It can perform a logical operation up to 4 binary
states to obtain other binary result. In V3 of the PLC the LOGICAL GATES that are supported
by SIL-A are:

www.fanox.com EN_FANOXTD_GUIDE_SIL_OCEFPrimaryDist_SILA_R002.doc 18 / 36
NOTE: As it is described above, the options NOR4_LATCH and NAND4_LATCH are not
available in the relay. Although, using SICOM software allows the user to configure these
options, the relay will not recognize them, and it will not work properly.
By default, configuration is:
OUTPUT
LOGICAL GATE
BINARY STATES (Adaptation B)
BINARY STATES (Adaptation C)
LEDs
LED 1
OR4_PULSES
•Ready
•Ready
LED 2
OR4_LATCH
•50-1 Trip
•50-2 Trip
•51 Trip
•50-1 Trip
•51 Trip
LED 3
OR4_LACTH
•50G1 Trip
•50G2 Trip
•51G Trip
•50G1 Trip
•51G Trip
LED 4
OR4_LACTH
•50BF Trip
•SHB
LED 5
OR4_LACTH
•46 Trip
•46 Trip
LED 6
OR4_LACTH
•74TCS Alarm
•74TCS Alarm
LED 52
OR4
•52 Closed
•52 Closed
LED 79
OR4
•79 Standby
•79 Standby
PHYSICAL
OUTPUTS
Output 1
OR4
•Ready
•Ready
Output 2
OR4
•50BF Trip
•46 Trip
•46BC Trip
Output 3
OR4
•79 Close time
•Local close breaker
•Remote Modbus close
breaker
•Remote protocol close
breaker
•79 Closing time
•Local close breaker
•Remote modbus close
breaker
•Remote DNP3.0 close
breaker
Output 4
OR4
•General trip
•Local open breaker
•General trip
•Local open breaker
LOGICAL GATE
HMI SYMBOL
OR4
+
NOR4
OR4_LACTH
Ю
AND4_LACTH
Φ
OR4_PULSES
⌠
AND4
&
NAND4
§
AND4_PULSES
$
OR4_TIMER_UP
O
NOR4_TIMER_UP
P
AND4_TIMER_UP
Q
NAND4_TIMER_UP
R
OR4_PULSE
o
NOR4_PULSE
p
AND4_PULSE
q
NAND4_PULSE
r
NOR4_PULSES
t

www.fanox.com EN_FANOXTD_GUIDE_SIL_OCEFPrimaryDist_SILA_R002.doc 19 / 36
•Remote Modbus open
breaker
•Remote protocol open
breaker
•Remote Modbus open
breaker
•Remote DNP3.0 open
breaker
LOGICAL
SIGNALS
52a
No configured
-
-
52b
OR4
•Input 1
•Input 1
External
Trip
No configured
-
-
50BF start
OR4
•General trip
na
DFR start
OR4
•General trip
•
50/51
block
Not configured
-
-
50/51N/G
block
Not configured
-
-
Reset
OR4_PULSE
•Local reset
•Remote Modbus reset
•Remote protocol reset
•Local reset
•Remote Modbus reset
•Remote DNP3.0 reset
Settings
group 1
Not configured
-
-
Settings
group 2
Not configured
-
-
79 Start
OR4
•General trip
•General trip
79 Enable
Not configured
-
-
79 Level
Block
Not configured
-
-
79 Block
Not configured
-
-
79
Unblock
Not configured
-
-
74TCS
Continuity
A (*)
Not configured
-
na
74TCS
Continuity
B
Not configured
-
na
Logical
signal 1
Not configured
-
na
Logical
signal 2
Not configured
-
na

www.fanox.com EN_FANOXTD_GUIDE_SIL_OCEFPrimaryDist_SILA_R002.doc 20 / 36
7. FLOWCHART
7.1. Test menu
From standby screen, press ◄,▼,► sequentially and hold OK until the ‘Test menu’ appears on
the display. The relay will ask for the password ‘5555’ to be entered in the test menu (or other if
the customer password by default is ‘5555’ has been modified). The test menu is accessed by
pressing the ‘OK’ key again, and the ‘▲’ and ‘▼’ keys can be used to navigate through the
different menu items. Each item can be activated or deactivated by pressing ‘OK’ on it (if the
item is deactivated, it is activated by pressing OK; if the item is activated, it is deactivated by
pressing ‘OK’). Press the ‘C’ key to exit the test menu.
Once “Led1” appears, by pressing “OK” the led is activated and by pressing “OK” again, it is
deactivated.
To go through all options, press “▼”. To activate and deactivate the options follow the same
steps as in case of LED 1.
On adaptation C all the LEDs will be activated simultaneously when entering on Test Menu. In
case of the outputs, they will be activated or deactivated by pressing OK key.
Other manuals for SIL-A
1
Table of contents
Other FANOX Relay manuals

FANOX
FANOX SIL B User manual

FANOX
FANOX SIA D User manual
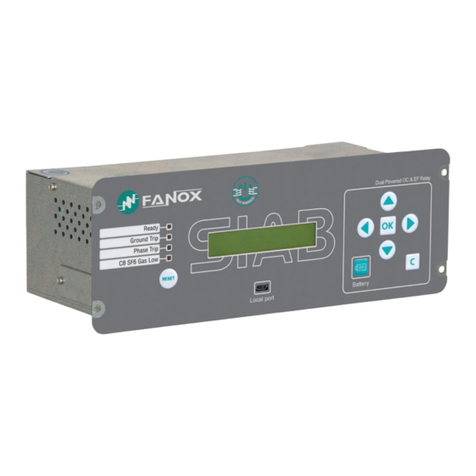
FANOX
FANOX SIA-B Standard Series User manual
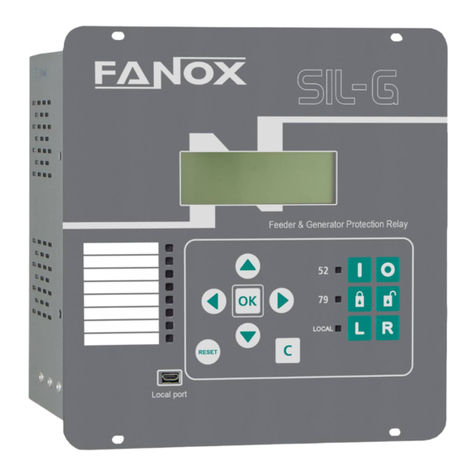
FANOX
FANOX SIL-G User manual
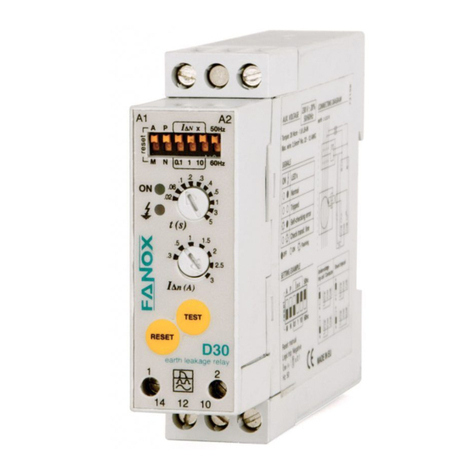
FANOX
FANOX D30 User manual
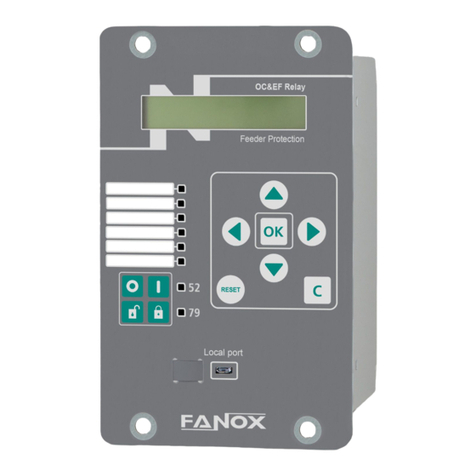
FANOX
FANOX SIL-A A Series User manual
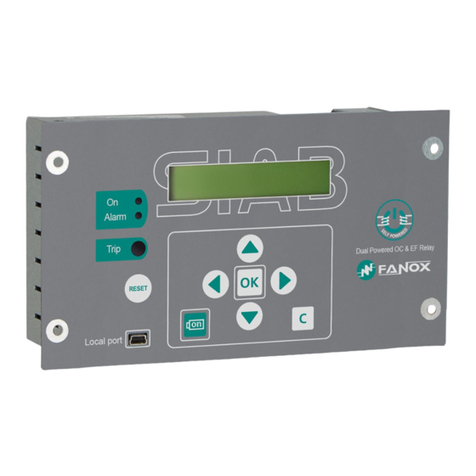
FANOX
FANOX SIA-B User manual
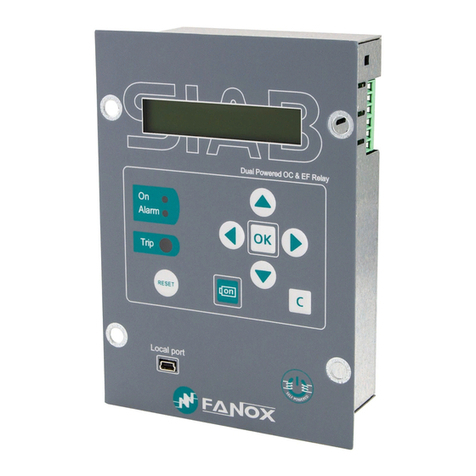
FANOX
FANOX SIA-B User manual

FANOX
FANOX SIA-F User manual

FANOX
FANOX D30 User manual
Popular Relay manuals by other brands
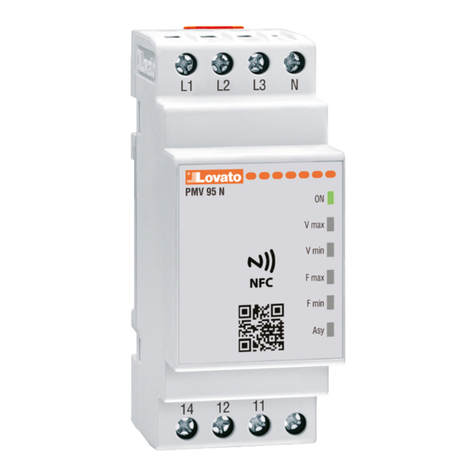
LOVATO ELECTRIC
LOVATO ELECTRIC PMV95N***NFC Series user manual
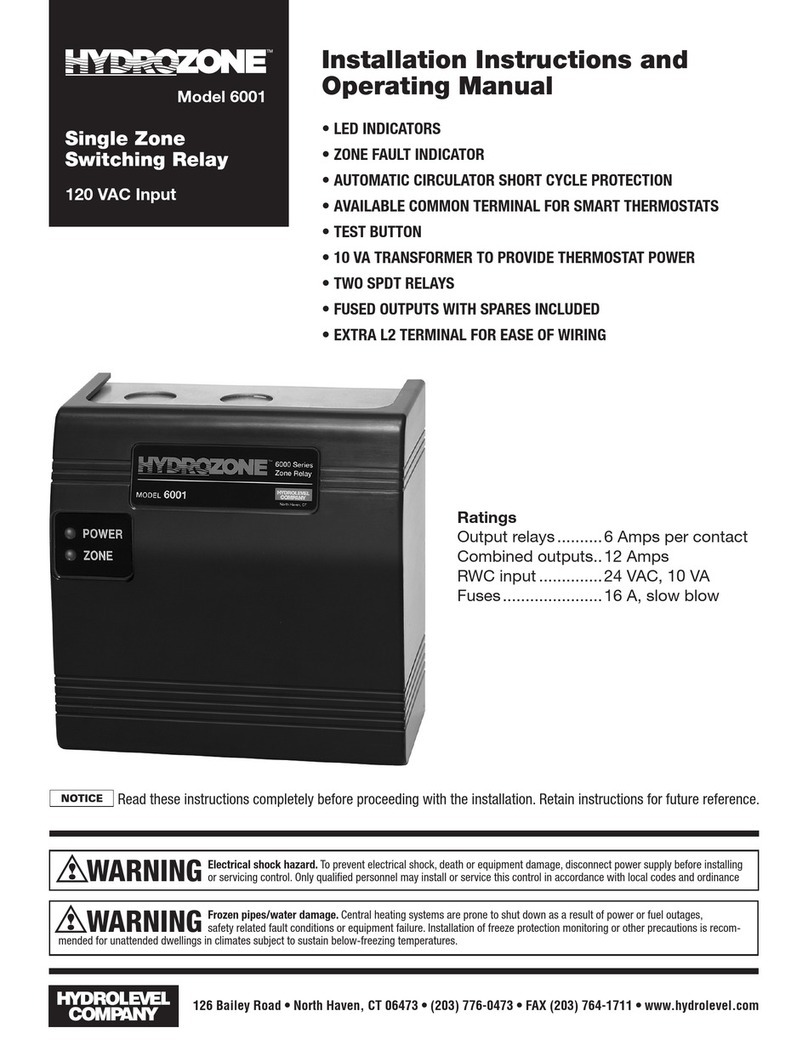
Hydrolevel Company
Hydrolevel Company HYDROZONE 6000 Series Installation instructions and operating manual
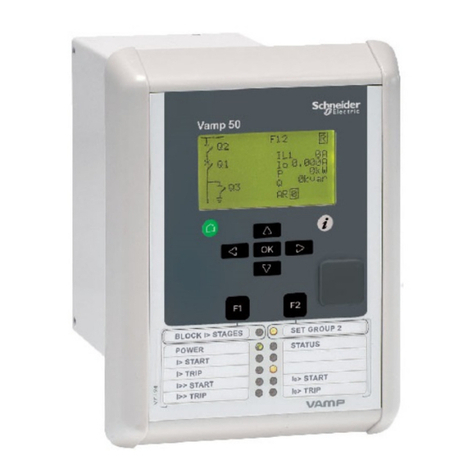
VAMP
VAMP 50 Operation and Configuration
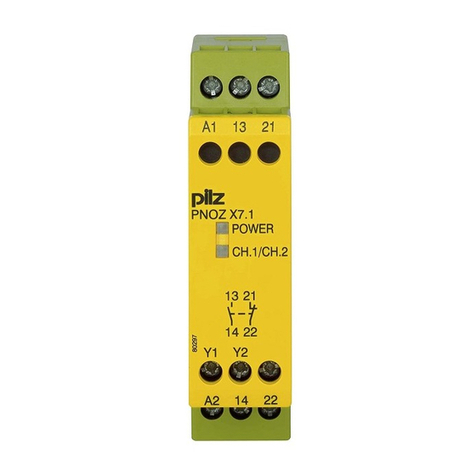
Pilz
Pilz PNOZ X7.1 operating instructions
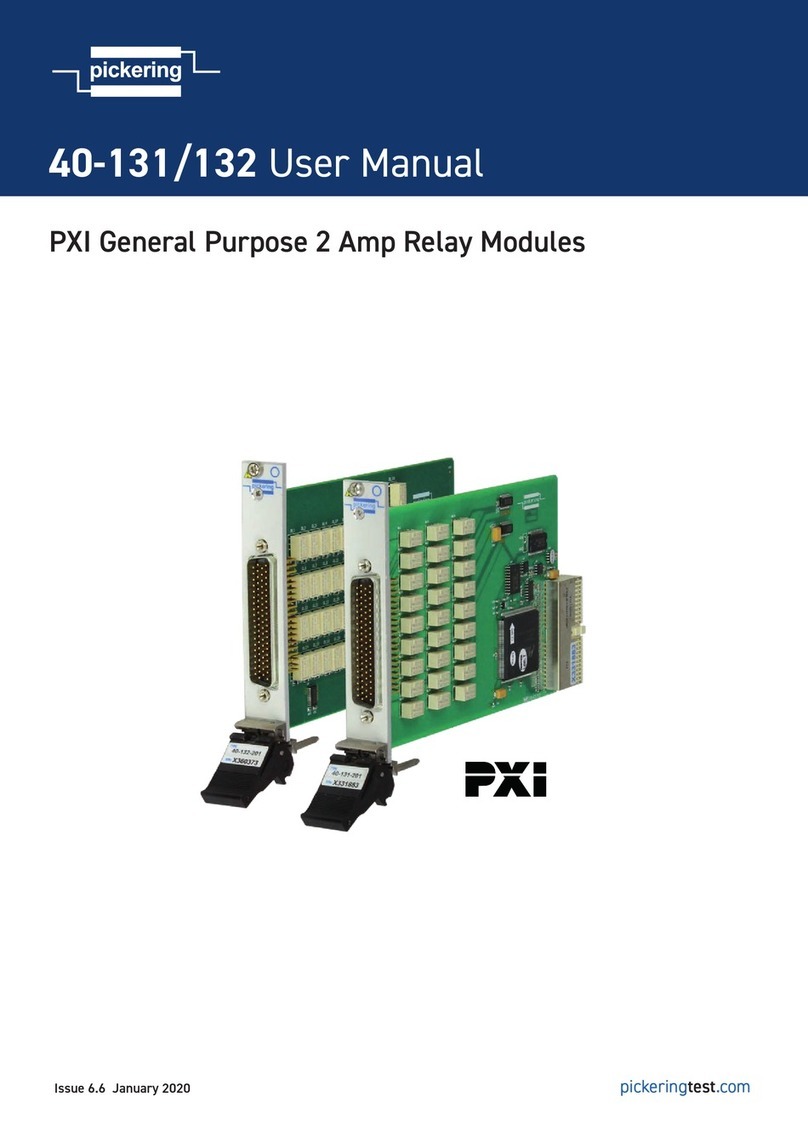
Pickering
Pickering PXI 40-131 user manual

Leviton
Leviton EZ-MAX H Series quick start guide