Fireye E300 User manual

FIREYE®E300
EXPANSION MODULE
For use with the Fireye
FLAME-MONITOR™Control
DESCRIPTION
The FIREYEE300 Expansion Module provides increased interlock supervision capability of the
FLAME-MONITORSystem. The Expansion Module connects to any EB700 FLAME-MONITOR
Chassis by means of a ribbon cable. (P/N E350-3, E350-6).
By wiring any of sixteen interlock switches into the Expansion Module, the FLAME-MONITOR
display automatically acts as a “first-out” annunciator for these interlocks. In addition, a fuel selection
circuit is standard. The E300 is shipped with default messages associated with each set of terminals.
The user has the ability to modify these lockout messages in one of two ways:
1. Use the ED510 display module to select a lockout alarm message for the individual terminals of
the E300 from a library of available messages. Refer to Bulletins E-1101 or ED-5101 (E300
MESSAGE SELECT section).
2. Program a customized message (up to 40 characters in length) for the individual terminals of the
E300 using an IBM compatible PC with the E300 programming software (available at no charge
from Fireye) and the appropriate hardware. On most PC’s Windows Hyperterminal can be used to
program E300 messages.
Note: Modifying the E300 messages requires an EP Programmer with an Engineering code of 28 or
later (Engineering codes are found after the date code, e.g. 9416-28).
The Expansion Module does not interfere with the normal operation of the FLAME-MONITOR
System. It expands the message and diagnostic capability.
The E300 expansion module provides operational information and reduces troubleshooting time and
expense. It expands the standard display messages of the FLAME-MONTOR to identify the specific
limit in the operating control circuit or running interlock circuit which caused the burner shutdown or
lockout. For a detailed description of the FLAME-MONITOR System, see Bulletin E-1101.
APPROVALS
Underwriters Laboratories Inc.: Listing, File #MH10808
Canadian Standards Association: LR7989/17617 Certification Record
Factory Mutual (FM): Approved
SPECIFICATIONS
Supply Voltage:120V (+ 10% - 15%), 50 / 60 Hz
Ambient Temperature Levels: -40F to +125F (-40C to +50C)
Response Time:170 milliseconds Purge/32 milliseconds Run
Weight: 0.5 lb.
Humidity: 85% R.H. non-condensing
E300 CONTROL E350 RIBBON CABLE
E-3001
APRIL 8, 2013
UL
APPROVED
LISTED
CUS

2
DIMENSIONS
ORDERING INFORMATION
PART
NUMBER
DESCRIPTION
E300 Expansion Module used with the EB700 FLAME-MONITOR chassis and 60-1950 wiring base
60-1950 Wiring base
E350-3 3 foot ribbon connector cable
E350-6 6 foot ribbon connector cable
EC485 RS232 to RS485 converter with power supply. Required to customize E300 lockout alarm messages.
ED512-2, -4, -8 Cable with RJ12 connectors on each end. Required to customize E300 lockout alarm messages.
WIRING BASE
MOUNTING HOLES
7 1/4
(184.2)
6
(152.4)
3 1/2
(89)
1/2” KNOCKOUT
CONTROL WITH COVER AND
P/N 60-1950 WIRING BASE
4 7/8
(123.8)
5 11/16
(144.5)
2 7/16
(61.9)
5 1/4
(133)
7
(177.8)
11/16
(17.4)
3/4
(44.4) 25/32
(19.8)
1/4
TYP
(6.35)
390
TYP
(9.9)
KNOCKOUTS FOR
1/2” CONDUIT (7)
1 1/16
(27)
1 3/16
(30.2)
E300 EXPANSION MODULE WITH
MOUNTING SCREW
E350 RIBBON CABLE
(ORDERED SEPARATELY)
WIRING BASE (60-1950)
(ORDERED SEPARATELY)

3
®
OPERATION
The E300 Expansion Module is designed to expand the capability of the FLAME-MONITOR
System by allowing the operator to individually track the operation of three additional recycling
interlocks and thirteen running interlocks. The recycling interlocks are wired between the L1-13
terminals on the FLAME-MONITOR wiring base and the non-recycling interlocks are in the 3-P
circuit.
Referring to the wiring diagram found on page 5, the auxiliary limits 1, 2 and 3 will act as an operat-
ing control to recycle the burner. Whenever one is open and the other limits and operating control are
closed, the message on the display of the FLAME-MONITOR control will say:
STANDBY
AUX LIMIT #1 (or #2, or #3) OPEN (or the appropriate modified message)
Similarly, the interlocks in the 3-P circuit will change the standard running interlock message on the
display from: LOCKOUT 3-P RUN INTERLOCK OPEN to be one which will individually identify
the thirteen interlocks now being monitored by the E300, such as, LOCKOUT 3-P LOW OIL TEM-
PERATURE (or the appropriate modified message). The interlock switch chosen will be selected on
a “first out” basis. The first switch which opens in the string to cause the condition will be displayed.
The 3-P circuit is monitored after ten seconds on a burner start-up.
When a “lockout” condition is manually reset, the display on the FLAME-MONITOR and the
Expansion Module is ready to begin a new burner sequence. Note the section Lockouts in the Bulle-
tin E-1101.
Whenever more than one interlock switch in the L1-13 circuit is open on a start-up, the open inter-
lock switch wired in the sequence closest to the L1 terminal will be displayed.Whenever more than
one interlock switch in the 3-P circuit is open on a startup, the open interlock switch closest to termi-
nal 3 will be displayed.
CAUTION: The E300 messages are stored in the EP Programmer of the FLAME-MONI-
TOR control. The E300 messages shown on page 4, and on the wiring diagram on page 5 rep-
resent the default messages that are shipped with each programmer module. Unless these
default messages are modified via the ED510 display module (Refer to Bulletin ED-5101) or
customized via an IBM PC (Refer to CUSTOMIZING E300 MESSAGES in this bulletin), the
E300 must be wired EXACTLY AS SHOWN, in the sequence as shown in the wiring diagram
on page 5 to ensure proper operation.
The E300 must be connected to the FLAME-MONITOR control to provide access to the additional
lockout messages associated with the E300 Expansion Module.
In operation, the 3 to P and L1 to 13 circuits are checked each half cycle (8 milliseconds) by separate
photo optical couplers in the FLAME-MONITOR system to determine if any interlock is open.
Upon detecting an open interlock, the microprocessor in the FLAME-MONITOR control initiates a
LOCKOUT or HOLD message, then scans its inputs corresponding to terminals 23 through 35 and
20 through 22 (on E300) to determine which of the interlocks closest to terminal 3 (3-P circuit) or
closest to terminal L1 (L1-13 circuit) is open. The microprocessor then selects the corresponding
message from the stored message list and displays it. The E300 messages then become a part of the
historical data which is stored in the FLAME-MONITOR system memory.
Any interlock in the 3-P or in the L1-13 circuit that opens for at least 33-50 ms while the burner is
ON, or for at least 170 ms while the unit is in PURGE will cause the E300 and the FLAME-MONI-
TOR control to respond with the proper message. Interlock contacts that temporarily open for shorter
time periods will be ignored. Refer to the REQUIRED WIRING DIAGRAM on Page 5.

4
SPECIAL NOTES ON OPERATION
After any recycle (L1-13) or running interlock (3-P) limit opens, the control will display a POST
PURGE message for 15 seconds before displaying the appropriate message.
On recycle type programmers (e.g. EP260, EP270 or EP380, EP390 set for recycle operation), if a
running interlock (3-P) limit opens, the control will shutdown, and then try to restart. The control
will hold for ten (10) minutes during purge waiting for the limit to close. If a second running inter-
lock opens during this “hold” period, the message may change to reflect the new interlock.
If auxiliary limit #1, #2 or #3 opens during a firing cycle, the control will initiate a 15 second post
purge and then go to a standby message. The FLAME-MONITOR will wait for the L1-13 circuit to
close to begin a new cycle.
If multiple interlocks in the 3-P circuit are opened within the first 10 seconds of purge, the first inter-
lock in the following sequence will be displayed:
Table 2: E300 MESSAGES (E110 Interlock System)
Important: If a particular interlock is not used in your system, a jumper must be installed on the ter-
minals of the Expansion-Module wiring base which corresponds to that interlock message. For
example: If your system has no high temperature switch and no need for auxiliary limits 5 and 6, a
jumper should be placed between terminals 31 and 32, 33 and 34, 34 and 35.
Important: When a single fuel burner is used, the fuel selector switch is not necessary. However, the
appropriate terminals to determine fuel type should be jumpered. For gas only: terminals 24 and 25.
For oil only: Terminals 24 and 26.
When the fuel selector switch is on the GAS position, the 3 oil interlocks are ignored by the
FLAME-MONITOR control. When the switch is in the OIL position, the 2 gas interlocks are
ignored.
CAUTION: E300 wiring should not interfere with the safety function of the operation inter-
lock. Check each interlock for proper operation after wiring the E300.
OIL MODE GAS MODE
Terminal Message Terminal Message
Recycling Limits
20 20
21 L1-13 Aux #1 Open 21 L1-13 Aux #1 Open
22 L1-13 Aux #2 Open 22 L1-13 Aux #2 Open
13 L1-13 Aux #3 Open 13 L1-13 Aux #3 Open
Non-Recycling Limits
23 High Water 23 High Water
24 Low Water 24 Low Water
26 No Fuel Selected 25 No Fuel Selected
28 Low Oil Pressure 27 High Gas Pressure
29 Low Oil Temperature
30 Low Atomizing Media 30 Low Gas Pressure
31 High Pressure 31 High Pressure
32 High Temperature 32 High Temperature
33 Auxiliary Limit #4 33 Auxiliary Limit #4
34 Auxiliary Limit #5 34 Auxiliary Limit #5
35 Auxiliary Limit #6 35 Auxiliary Limit #6
PAir Flow PAir Flow

5
®
WIRING DIAGRAM FOR DEFAULT MESSAGES
24 26 28
25 27 29
LOW OIL
TEMP
LOW OIL
PRESS
LOW ATOMIZER
MEDIA
LOW GAS
PRESSURE
HIGH GAS
PRESSURE
L1
3P
GAS
OIL
31 33 35
30 32 34
HIGH
PRESS
AIR
FLOW
AUX
LIMIT
HIGH
TEMP
AUX
LIMIT AUX
LIMIT
#4 #5 #6
23
LOW
WATER
HIGH
WATER
13
AUX
LIMIT
#1
AUX
LIMIT
#3
AUX
LIMIT
#2
20 22
21
OPERATOR
CONTROL
L2
TO L2 ON E110
L2
TO L2 TERMINAL ON 60-1950 WIRING BASE NOTE: All existing wiring on terminals not shown
will be undisturbed when the E300 is installed.
60-1950 WIRING BASE
60-1386-2 or 60-1466-2 WIRING BASE
FOR FLAME MONITOR
FUEL VALVE
END SWITCH

6
SPECIAL NOTES ON OPERATION
An important safety feature of the FLAME-MONITOR system is its ability to remember the proper
timed operation of critical terminals such as fuel valve terminals 5, 6 & 7. Jumpering these terminals
could cause the control to sense an unusual condition and lock out.
When changing fuels on combination burners where direct spark ignition is used, it is normal to
jumper terminal 6 to 7. To assure that burner operation is not interrupted in this situation, you must
do one of the following:
•Momentarily interrupt the power to L1 when changing fuels, before the initial burner cycle with
the new fuel, or
•Install a time delay relay as shown in the diagram; this procedure can only be done with CODE
12 or higher programmers.
FLAME-MONITOR TERMINALS
TIME DELAY RELAY (ON DELAY)
3 SEC. (MINIMUM) DELAY
L2
57
6

7
®
INSTALLATION AND WIRING
CAUTION: Remove all power from the FLAME-MONITOR control and the E300 Module
before proceeding.
1. Remove cover by loosening screw 1/4 turn. 2. Pull bottom out and lift up from top of
clip.
3. Mounting screw is used to attach the control
to its wiring base (60-1950). Mounting screw
is supplied with the E300.
4. Caution: Route the ribbon cable
so that it is not in contact or close
proximity to line voltage wiring.
Secure ribbon cable to double sided
tape provided.
5. Remove the connector board cover at the bot-
tom of the EB700 chassis and insert the end of
the E350 ribbon cable into the circuit board
cable connector on the bottom left side of the
EB700 as shown.
6. Drape the ribbon cable down the front
of the control as shown. Reinstall the
connector board cover.

8
CUSTOMIZING E300 MESSAGES
The user can customize the lockout alarm message associated with each pair of terminals of the E300
Expansion Module. Each customized message can be up to 40 characters in length.
Note: Messages longer than 16 characters in length will scroll across the ED510 display. Messages
longer than 8 characters will scroll across the ED500 display.
The following equipment is required:
•An IBM compatible PC with E300 programming software (available on the E700 or E720 soft-
ware programs).
•An RS232 to RS485 converter (P/N EC485 - includes a power supply).
•An ED512-2, -4, or -8 cable.
•EP programmer with an Engineering code of 28 or later.
1. Connect the EC485 converter to the serial COMMunication port of the IBM PC using a straight
through cable. The cable should be configured as follows:
A 9 pin to 25 pin converter may be required if the serial COMMunication port on the IBM PC has a
DB-9 connector. (See above for pin out connections).
2. Connect the RJ12 female connector (provided with the EC485) to terminals TD(A), TD (B),
RD(A), and RD(B) on the EC485. The pins on the RJ12 connector will line up with the termi-
nals on the EC485 converter.
3. Set the jumpers on the EC485 converter to SD and ECHO OFF. See diagram below.
4. Plug on end of the ED512-2, -4, -8 cable into the RJ12 jack on the EC485 converter, and the
other end into either of the RJ12 jacks on the EP programmer.
5. The Flame-Monitor control must be powered, and the operating control (L1-13) should be open.
11
22
33
44
55
66
77
88
20 20
DB25 Serial
Com Port
of IBM PC
EC485
Converter
DB 9
18
23
32
420
57
66
74
85
922
DB 25
DB9 to DB 25 Converter
CABLE CONNECTIONS
RS-485
RS-232
FR. GRD
SHLD
TD (A)
TD (B)
RD (A)
RD (B)
+12VDC
GND
ECHO
ON
OFF
RTS SD
CONTROL
TD RD
POWER
SUPPLY 120VAC
ED512, -2, -4, -8
TO RJ12 CONNECTOR
ON EP PROGRAMMER
TO SERIAL
COMM PORT
ON IBM PC 12VDC
White Stripe

9
®
E300 Software
1. Insert the E300 software into the appropriate disk drive on an IBM PC and at the A: prompt (or
B: prompt), type E300 and press RETURN.
2. The screen will display the available serial COMMunication ports on the IBM PC. Use the UP
or DOWN cursor position keys or Mouse to highlight the serial COMMunication port where the
RS485/RS232 converter is connected.
Note: Pressing the F1 key will display Help information pertaining to each screen.
3. Press RETURN (or double click the Mouse) and the screen will display four baud rate selec-
tions (300, 1200, 4800, and 9600). Use the Up or Down cursor position keys or Mouse to high-
light the selection: 4800, N, 8, 1 - E300 Programming
4. Press RETURN (or double click the Mouse) and the screen will display a blank programing
screen. The E300 software program is ready to type in the customized messages.
5. Type in password &Z*
IMPORTANT: Before the user can type in any customized message, the following characters
MUST INITIALLY BE TYPED IN: & Z * (followed by RETURN). The second character
must be an upper case Z (not a lower case). These characters WILL NOT appear on the
screen when they are typed.
Type in the appropriate command associated with the set of terminals whose message will be modi-
fied. All commands must begin with a period. See the table below.
PROGRAMMING THE E300 MESSAGES - EXAMPLE:
1. To change the message associated with the first limit in the 3-P running interlock circuit (termi-
nal 3 of the EB700 or E110 and terminal 23 of the E300), type in .T23 and press RETURN. The
screen will display:
NONE STORED (If no customized message has been programmed for these terminals.
CHANGE MESSAGE Y/N
IMPORTANT: The user must first type in the characters & Z * one time before typing in the
command. These characters WILL NOT appear on the screen when they are typed.
Command Terminals Default Message
.T21 20 - 21 AUX LIMIT #1
.T22 21 - 22 AUX LIMIT #2
.T13 22 - 13 (On EB700 or E110) AUX LIMIT #3
.TP 35 - P (On EB700 or E110) AIR FLOW
.T35 34 - 35 AUX LIMIT #6
.T34 33 - 34 AUX LIMIT #5
.T33 32 - 33 AUX LIMIT #4
.T32 31 - 32 HIGH TEMPERATURE
.T31 30 - 31 HIGH PRESSURE
.TO30 29 - 30 1LOW ATOMIZING MEDIA
.T29 28 - 29 1LOW OIL TEMPERATURE
.T28 26 - 28 1LOW OIL PRESSURE
.TG30 27- 30 2LOW GAS PRESSURE
.T27 25 - 27 2HIGH GAS PRESSURE
.T24 23 - 24 LOW WATER
.T23 23 - 3 (On EB700 or E110) HIGH WATER
1When the fuel selector switch is on the GAS position (terminals 24-25), these messages are ignored.
2When the fuel selector switch is on the OIL position (terminals 24-26), these messages are ignored.

10
2. Type in Yto change the message. The screen will display: * (The asterisk indicates a ready
prompt)
3. Type in the customized message (up to 40 characters in length) and press RETURN.
4. To verify the programmed message, type in the command again (e.g..T23) and press RETURN.
The screen will display:
.T23
HIGH STACK TEMP (or customized message)
CHANGE MESSAGE Y/N
5. Type in N
REVIEW CUSTOMIZED MESSAGES
The E300 software will store the last 32,000 bytes of data in RAM memory on the computer. The
user can scroll backward or forward through previously entered commands and customized mes-
sages by using the Page Up/Page Down/Up Arrow/Down Arrow keys.
Note: Quitting the E300 software program deletes the commands and messages from RAM memory.
THE ONLY WAY TO DISPLAY THE CUSTOMIZED MESSAGES ON THE ED510 DIS-
PLAY IS TO OPEN THE SAFETY LIMIT WIRED BETWEEN THE APPROPRIATE TER-
MINALS.
The Sub-Menu “E300 MSG SELECT” on the ED510 Display Module will not display the custom-
ized messages, but only display the available lockout messages from its library of messages. (Refer
to Bulletin ED-5101).
IMPORTANT: The E500 Communication Interface will only display the E300 default
messages. The E500 will not display the messages from the available library of messages
or any customized messages.

11
®
MESSAGES
The following is a list of default messages which appear on the ED510 display when it is connected
to an E300. The user also can modify the message associated with each set of terminals in one of two
ways:
1. Use the ED510 display module to select a lockout alarm message for the individual terminals
of the E300 from a library of available messages. Refer to Bulletins E-1101 or ED-5101 (E300
MESSAGE SELECT section).
2. Program a customized message (up to 40 characters in length) for the individual terminals of the
E300 using an IBM compatible PC with the E300 programming software.
The default messages below also list in the description the associated terminal on the E300 wiring
base. When the message is modified for a set of terminals (see above), the modified message will be
displayed when the interlock wired to those terminals opens.
Note: Modifying the E300 messages requires an EP Programmer with an Engineering code of 28 or
later (Engineering codes are found after the date code, e.g. 9416-28).
The various messages (default or modified) correspond to the terminals on the E300 wiring base (60-
1950). For example, if the interlock switch wired between terminals 23 and 24 opens, the FLAME-
MONITOR control will display LOW WATER (default message) or the appropriate modified mes-
sage.
If the E300 wiring terminals for a particular interlock are not used in your system, a jumper must be
installed across those terminals.
The FLAME-MONITOR control is compatible with two types of display modules (ED510 and
ED500). The ED500 was the predecessor of the ED510 display and uses an older design. It does not
have the features of the ED510 display. The following messages are associated with the ED510 dis-
play. These messages may differ slightly with the ED500 display.
HOLD MESSAGES1,2DESCRIPTION
The air flow switch has opened and the control is waiting until the con-
dition corrects itself. 3(Terminal P on FLAME-MONITOR wiring
base.)
The auxiliary #4 switch has opened and the control is waiting until the
condition corrects itself. 2 (Terminal 33).
The auxiliary #5 limit switch has opened and the control is waiting until
the condition corrects itself 2 (Terminal 34).
TheAuxiliary#6limitswitch hasopened andthe controlis waitinguntil
the condition corrects itself. 2 (Terminal 35).
1. Messages more than 16 characters in length will scroll from right to left on the bottom line of the display.
2. HOLD messages only apply to recycle-type programmers i.e. EP260 or EP380, EP390 set for recycle operation.
3. This condition will hold for 10 minutes on an EP260, EP270, EP380, EP390 series programmer before a lockout will occur.
HOLD PURGE
3-P AIR FLOW OPEN
HOLD PURGE
3-P AUX. #4 LIMIT OPEN
HOLD PURGE
3-P AUX. #5 LIMIT OPEN
HOLD PURGE
3-P AUX. #6 OPEN

12
The high gas pressure switch has opened and the control is waiting until
the condition corrects itself. 2(Terminal 27)
HOLD MESSAGES12DESCRIPTION
The high temperature switch has opened and the control is waiting until
the condition corrects itself. (Terminal 32).
The high pressure switch has opened and the control is waiting until the
condition corrects itself. 2(Terminal 31).
The high water cutoff circuit has opened and the control is in a hold con-
dition until it close.2(Terminal 23). *
Thelowatomizingmedia switchhas openedand thecontrolis waitinguntil
the condition corrects itself. 3(Terminal 30)
The low gas pressure switch has opened and the control is waiting until the
condition corrects itself. 2(Terminal 30)
The low oil pressure switch has opened and the control is waiting until the
condition corrects itself. 2(Terminal 28)
The low oil temperature switch has opened and the control is waiting until
the condition corrects itself. 2(Terminal 29)
The low water cutoff circuit has opened and the control is waiting until the
condition corrects itself. 2(Terminal 24)
The fuel selection switch was opened during, or at the beginning of an
operating cycle. 2(Terminal 25 or 26)
1. Messages more than 16 characters in length will scroll from right to left on the bottom line of the display.
2. HOLD messages only apply to recycle-type programmers i.e. EP260 or EP380, EP390 set for recycle operation.
3. This condition will hold for 10 minutes on an EP260, EP270, EP380, EP390 series programmer before a lockout will occur.
HOLD PURGE
3-P HIGH GAS PRESSURE
HOLD PURGE
3-P HIGH TEMPERATURE
HOLD PURGE
3-P HIGH PRESSURE
HOLD PURGE
3-P HIGH WATER
HOLD PURGE
3-P LOW ATOMIZING MEDIA
HOLD PURGE
3-P LOW GAS PRESSURE
HOLD PURGE
3-P LOW OIL PRESSURE
HOLD PURGE
3-P LOW OIL TEMPERATURE
HOLD PURGE
3-P LOW WATER
HOLD PURGE
3-P FUEL SELECTED

13
®
STANDBY MESSAGES DESCRIPTION
The auxiliary limit switch #1 in the operating control circuit has opened
andthecontrol iswaitinguntil the conditioncorrectsitself.2Thecontrol
will hold this message indefinitely. (Terminal 21)
The auxiliary limit switch #2 in the operating control circuit has opened
and the control is waiting until the condition corrects itself. The control
will hold this message indefinitely. (Terminal 22)
The auxiliary limit switch #3 in the operating control circuit has opened
and the control is waiting until the condition corrects itself. The control
will hold this message indefinitely. (Terminal 13 on the FLAME-MON-
ITOR wiring base.)
LOCKOUT MESSAGES1DESCRIPTION
The air flow switch has opened and caused the control to lockout. (Ter-
minal P on the FLAME-MONITOR wiring base).2
The auxiliary #4 limit switch has opened and caused the control to lock-
out. (Terminal 33).2
The auxiliary #5 limit switch has opened and caused the control to lock-
out. (Terminal 34).2
The auxiliary #6 limit switch has opened and caused the control to lock-
out. (Terminal 35.)2
With gas selected, the high gas pressure switch has opened and caused
the control to lockout. (Terminal 27).2
The high pressure switch has opened and caused the control to lockout.
(Terminal 31).2
The high temperature switch has opened and caused the control to lock-
out (Terminal 32).2
1. Messages more than 16 characters in length will scroll from right to left on the bottom line of the display.
2. The point in the operating sequence in which the lockout occurred will appear in the upper right hand corner of the display
(e.g. PURGE, PTFI, MTFI, or AUTO). On recycle-type programmers (e.g. EP260, EP270, or EP380, EP390 set for recycle
operation), the display will always indicate the LOCKOUT occurred during PURGE, even though the interlock could have
opened during Purge, PTFI, MTFI, or AUTO and failed to close within the first 10 minutes of purge following the recycle.
STANDBY
L1-13 AUX. #1 OPEN
STANDBY
L1-13 AUX. #2 OPEN
STANDBY
L1-13 AUX. #3 OPEN
LOCKOUT PURGE 2
3-P AIR FLOW OPEN
LOCKOUT PURGE 2
3-P AUX #4 OPEN
LOCKOUT PURGE 2
3-P AUX #5 OPEN
LOCKOUT PURGE 2
3-P AUX #6 OPEN
LOCKOUT PURGE 2
3-P HIGH GAS PRESSURE
LOCKOUT PURGE 2
3-P HIGH PRESSURE
LOCKOUT PURGE 2
3-P HIGH TEMPERATURE

14
The high water cutoff circuit has opened and caused the control to lock-
out (Terminal 23). 2
Withoilselected,thelowatomizingmediaswitchhasopenedandcaused
the control to lockout. (Terminal 30). 2
With gas selected, the low gas pressure switch has opened and caused
the control to lockout (Terminal 30). 2
Thelowoil pressure switchhas openedandcausedthe control tolockout
(Terminal 28). 2
The low oil temperature switch has opened and caused the control to
lockout (Terminal 29). 2
Thelowwatercutoffcircuithasopenedandcausedthecontroltolockout
(Terminal 24).2
The fuel selection switch was opened during or at the beginning of an
operation cycle. (Terminal 25 or 26).2
The Flame-Monitor programmer has detected an error in attempting to
read the E300 Expansion Module.
LOCKOUT PURGE 2
3-P HIGH WATER
LOCKOUT PURGE 2
3-P LOW ATOMIZING MEDIA
LOCKOUT PURGE 2
3-P LOW GAS PRESSURE
LOCKOUT PURGE 2
3-P LOW OIL PRESSURE
LOCKOUT PURGE 2
3-P LOW OIL TEMPERATURE
LOCKOUT PURGE 2
3-P LOW WATER
LOCKOUT PURGE 2
3-P FUEL SELECTED
LOCKOUT PURGE 2
EXPANSION MODULE

15
®

16
NOTICE
When Fireye products are combined with equipment manufactured by others and/or integrated into
systems designed or manufactured by others, the Fireye warranty, as stated in its General Terms and
Conditions of Sale, pertains only to the Fireye products and not to any other equipment or to the
combined system or its overall performance.
WARRANTIES
FIREYE guarantees for one year from the date of installation or 18 months from date of manufacture
of its products to replace, or, at its option, to repair any product or part thereof (except lamps, elec-
tronic tubes and photocells) which is found defective in material or workmanship or which otherwise
fails to conform to the description of the product on the face of its sales order. THE FOREGOING
IS IN LIEU OF ALL OTHER WARRANTIES AND FIREYE MAKES NO WARRANTY OF
MERCHANTABILITY OR ANY OTHER WARRANTY, EXPRESS OR IMPLIED. Except as
specifically stated in these general terms and conditions of sale, remedies with respect to any product
or part number manufactured or sold by Fireye shall be limited exclusively to the right to replace-
ment or repair as above provided. In no event shall Fireye be liable for consequential or special dam-
ages of any nature that may arise in connection with such product or part.
FIREYE E-3001
3 Manchester Road APRIL 8, 2013
Derry, New Hampshire 03038 USA Supersedes November 8 2005
www.fireye.com
Table of contents
Other Fireye Control Unit manuals

Fireye
Fireye EP160 User manual
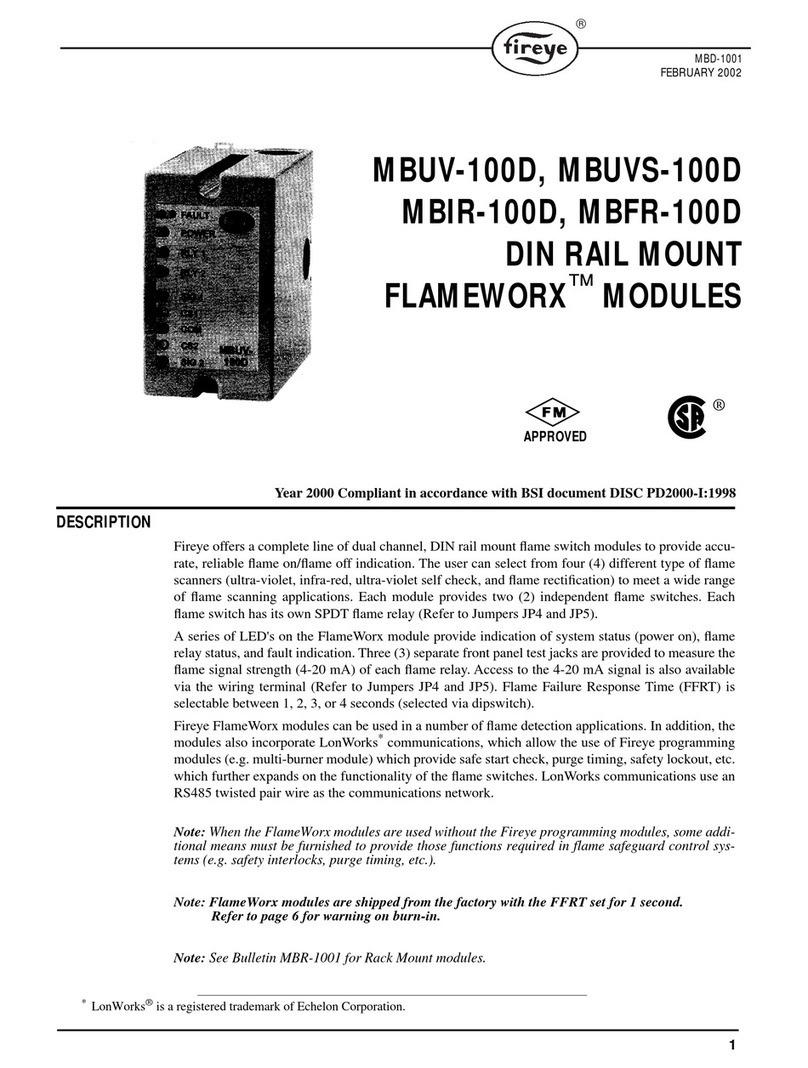
Fireye
Fireye FlameWorx MBUV-100D User manual
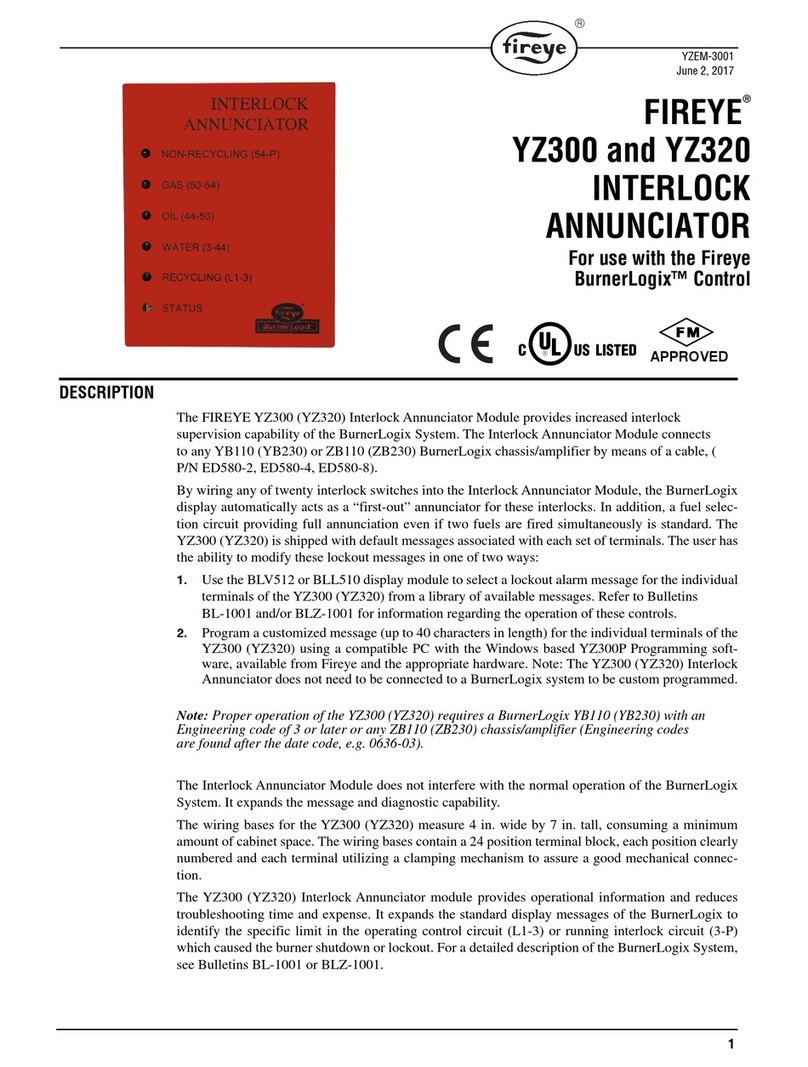
Fireye
Fireye YZ300 User manual
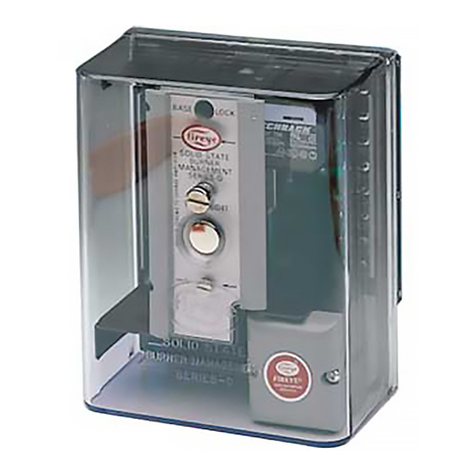
Fireye
Fireye D30 Series User manual
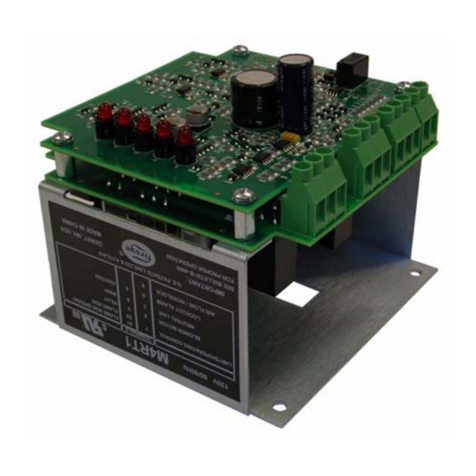
Fireye
Fireye M4RT1 User manual
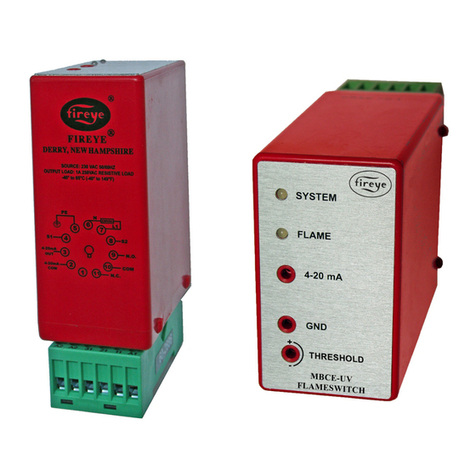
Fireye
Fireye MBCE-110UV Series User manual
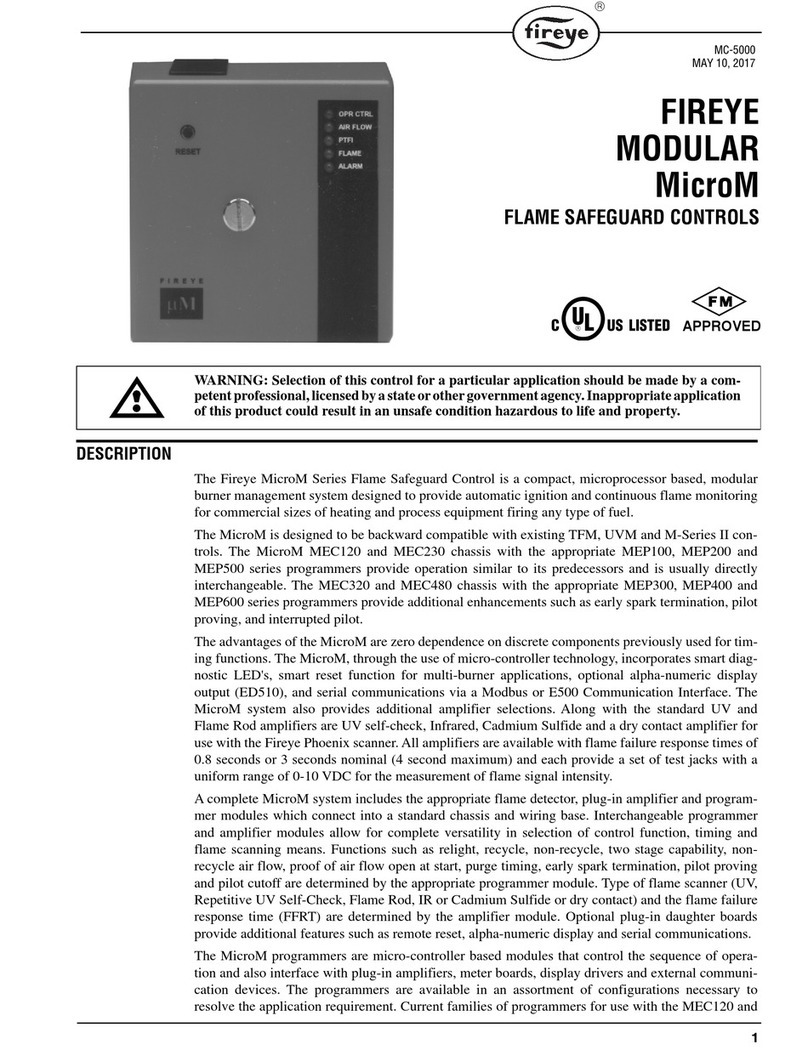
Fireye
Fireye MicroM Series User manual
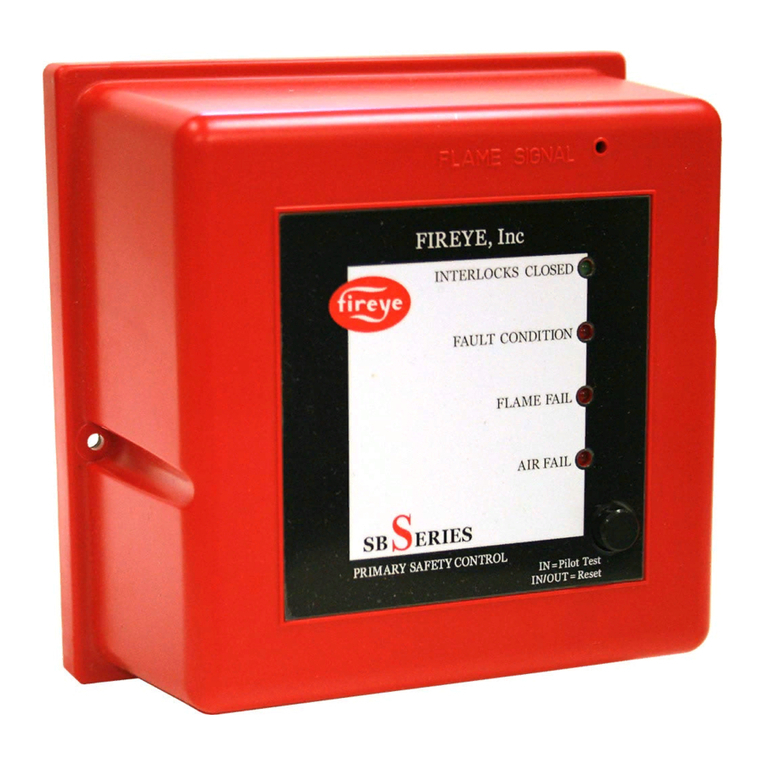
Fireye
Fireye SB Series User manual
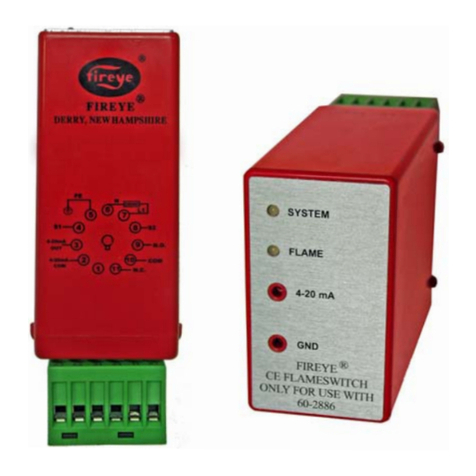
Fireye
Fireye MBCE-110FR User manual

Fireye
Fireye D40 Series User manual
Popular Control Unit manuals by other brands
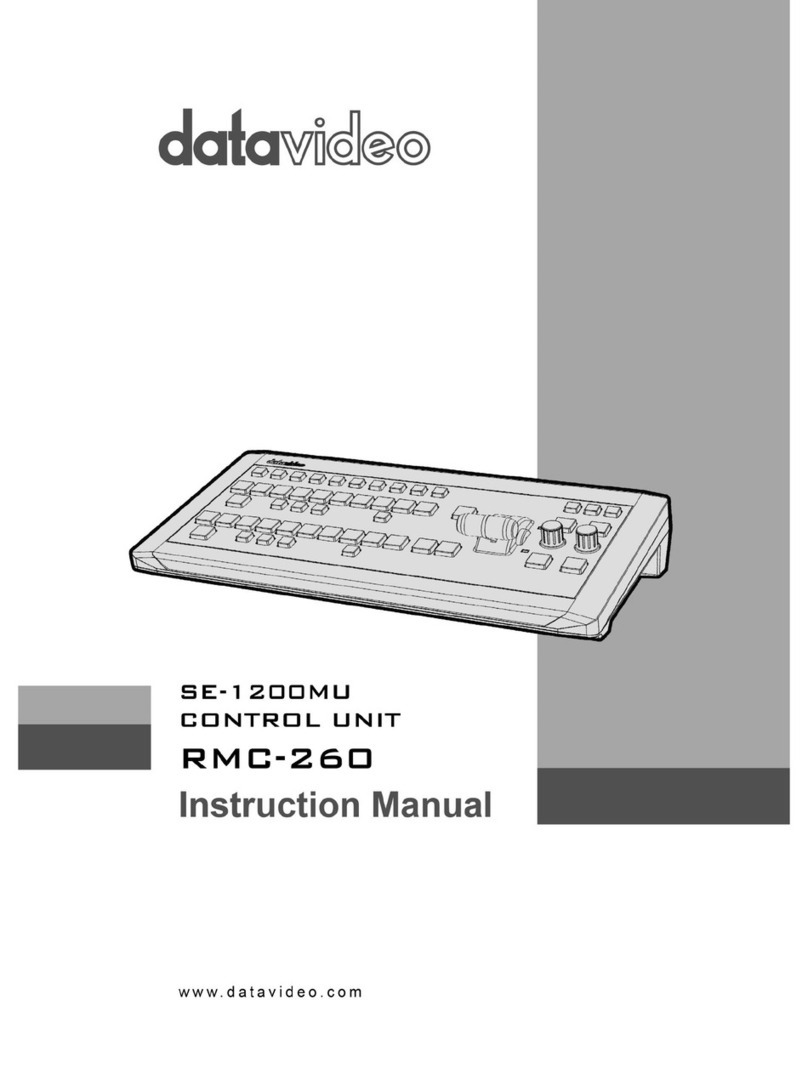
Data Video
Data Video RMC-260 instruction manual
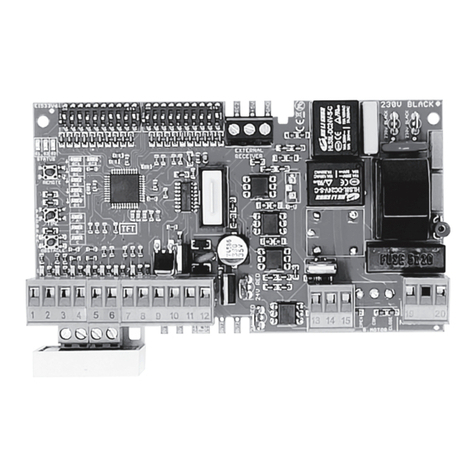
Tecnoautomazione
Tecnoautomazione T182S user manual
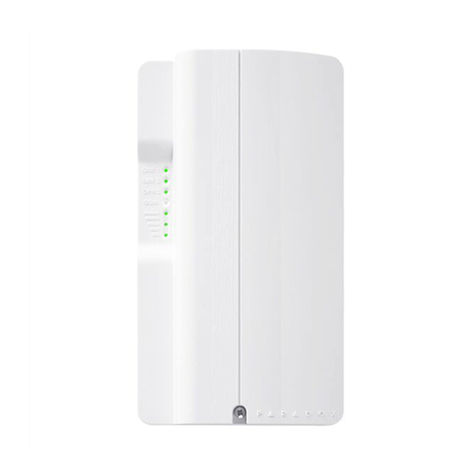
Paradox
Paradox PCS250G Installation and programming guide
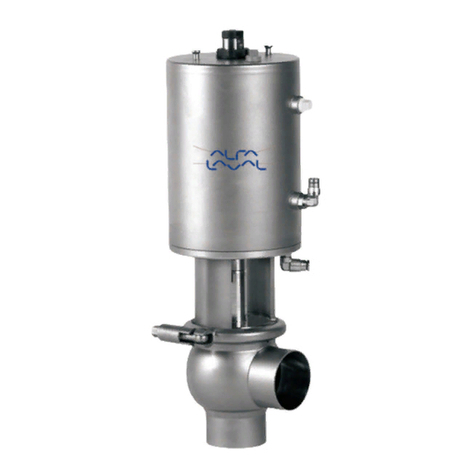
Alfalaval
Alfalaval Unique SSV PN10 instruction manual
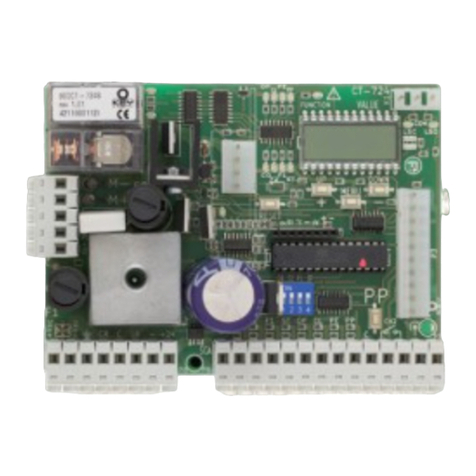
Keyautomation
Keyautomation CT-724 Series Instructions and warnings for installation and use
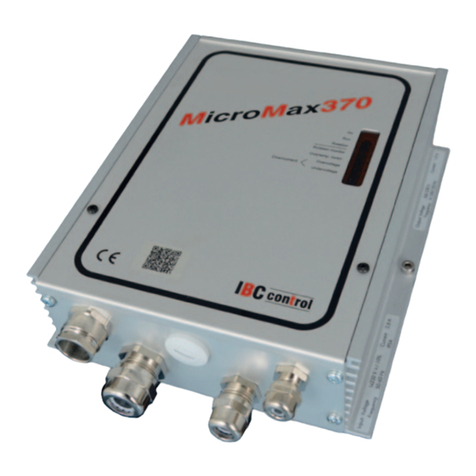
IBC control
IBC control MicroMax370 manual