Fireye M4RT1 User manual

1
®
FIREYE
M4RT1
FLAME SAFEGUARD CONTROLS
WARNING: Selection of this control for a particular application should be made by a com-
petentprofessional,licensedbyastateorothergovernmentagency.Inappropriateapplication
of this product could result in an unsafe condition hazardous to life and property.
DESCRIPTION
The Fireye® M4RT1 Flame Safeguard Control is a compact burner management system. It is
designed to provide automatic ignition and continuous flame monitoring for commercial sizes of
heating and process burners that use gaseous fuels.
Flame monitoring is accomplished by a Flame Rod detector, the built in amplifier and programmer.
Control functions and timing are factory set with onboard jumpers. Functions such as recycle/non-
recycle, purge timing, and pilot trial for ignition (P.T.F.I.) time are determined by the jumpers. Flame
Failure Response Time (F.F.R.T.) is fixed at three seconds. LED indicator lights indicate the operat-
ing status of the control.
In the event of ignition failure, or following a safety shutdown, the unit locks out, activating an
alarm circuit. Cycling the power OFF and back on will reset the control. A manual reset option can
be special ordered. Remote reset (via remote pushbutton) is also available as a special order option.
A detailed description of the programmer sequence is found later in this document. Test jacks are
provided to permit flame signal measurement during operation.
The M4RT1 control incorporates a safety checking circuit that is operative on each start. If flame
(real or simulated) is detected prior to a start or during the purge, the fuel valves will not be ener-
gized, and the unit will lock out.
All M4RT1 controls do not require a wiring base due to the terminals included on the relay board.
See INSTALLATION OF CONTROL, SCANNERS, AND FLAME DETECTORS (page 2) for tem-
perature and wiring requirements.
M-4000
APRIL 16, 2013

2
SPECIFICATIONS
Supply:
120V (min. 102, max. 132) 60 Hz
Table 1: AMBIENT TEMPERATURE LIMITS
Power Consumption: 12 VA (Operating)
Shipping Weight (Approx.): 2.2 lbs. (1.4kg)
Table 2: LOAD RATINGS
APPROVALS
Underwriters Laboratories Inc.
Recognized Components Guide MCCZ2
File MP1537
FM Approvals
FM7610
ORDERING INFORMATION
CONTROL:
M4RT1 120 VAC (min.102, max 132) Supply, 60 Hz.
FLAME DETECTORS:
69ND1-1000K4 12 inch flame rod, 1/2NPT connector
69ND1 -1000K6 18 inch flame rod, 1/2NPT connector
69ND1-1000K8 24 inch flame rod, 1/2NPT connector
MAXIMUM MINIMUM
Control 125F(52C) - 40F(- 40C)
Flame Rod
(Tip 2460 F)
1500F(816C) - 40F(- 40C)
Fireye Terminal Typical Load Maximum Rating & 120V 60 Hz
3 or 4
Individual or combined
Pilot valve(s)
Solenoid valve
Ignition Transformer
125 VA pilot duty (solenoid valve) plus
250 VA (Transformer)
5Main Fuel Valve(s)
125 VA pilot duty (solenoid) or
25 VA pilot duty (solenoid) and
400 VA (opening) motorized
8Motor or contactor
Motor normally energized and de-energized by the
operating control whose rating must be suitable. Termi-
nal 8 rated to de-energize 9.8 FLA, 58.8 LRA, on safety
lockout.
AAlarm 50 VA, pilot duty
Minimum load requirement = 100mA

3
®
INSTALLATION OF CONTROL, SCANNERS, AND FLAME DETECTORS
Wiring Base
Mount the control in an enclosure/burner panel that provides the proper protection for the control.
The location should be free from moisture, excessive vibration and within the specified ambient tem-
perature rating. The control may be mounted in any angular position.
All wiring should comply with applicable electrical codes, regulations, and local ordinances. Use
moisture resistant wire suitable for at least 90 degrees C. Circuit recommendations are found on
pages 10 through 11. Consult the factory for assistance with non-standard applications.
WARNING: Installer must be trained and qualified. Follow the burner manufacturer's in-
structions, if supplied. Otherwise, proceed as follows.
WARNING: Controls require safety limits utilizing isolated mechanical contacts. Solid state
limit switches are not acceptable and should not be used due to their high leakage currents.
WARNING: Remove power from the control before proceeding.
Replaceable Fuse
The M4RT1 is designed with a field replaceable fuse. The fuse is located on the printed circuit
board. The fuse will blow as a result of an overload condition on Terminals 3, 4 or 5. To replace the
fuse, remove power from the system. Using a small screwdriver or similar tool, remove the fuse
from its holder. Install a Fireye replacement fuse (P/N 23-176) or equivalent 8 amp fuse (e.g. Little-
fuse 225008P, 8 amp, 125V).
WARNING: Turn off the power when installing or removing the control.
INSTALLATION - 69ND1 FLAME ROD
The 69ND1 flame rod proves a gas pilot flame and/or main gas flame. It is a spark plug type unit
consisting of 1/2NPT mount, a KANTHAL flame rod, a glazed porcelain insulating rod holder and
a spark plug connector for making electrical connections. The 69ND1 is available in 12,18or 24
lengths.
The flame rod may be located to monitor only the gas pilot flame or both the gas pilot and main gas
flames. It is mounted on a 1/2NPT coupling.
The following instructions should be observed:
1. Keep flame rod as short as possible.
2. Keep flame rod at least 1/2from any refractory.
3. Flame rod should enter the pilot flame from the side so as to safely prove an adequate pilot
flame under all draft conditions.
4. If the flame is nonluminous (air and gas mixed before burning), the electrode tip should extend
at least 1/2into the flame, but not more than halfway through.
WRONG POSITION
OF ROD
INADEQUATE FLAME
PILOT BURNER
CORRECT POSITION
OF PILOT FLAME
CORRECT
POSITION
OF ROD

4
5. If the flame is partly luminous, the electrode tip should extend only to the edge of the flame. It is
not necessary to maintain absolutely uninterrupted contact with the flame.
6. It is preferable to angle the rod downward to minimize the effect of sagging and to prevent it
from coming in contact with any object.
7. An adequate grounding surface for the flame must be provided. The grounding surface in actual
contact with the flame must be at least four times greater than the area of the portion of the
flame rod in contact with the flame. It is essential to adjust the flame rod and ground area ratio
to provide a minimum signal reading of 6.0 VDC.
Note: Interference from the ignition spark can alter the true signal reading by adding to, or subtract-
ing from it. This trend sometimes may be reversed by interchanging the primary wires (line voltage)
to the ignition transformer. This interference can also be reduced by the addition of grounded shield-
ing between the flame rod and ignition spark.
8. Proven types of flame grounding adapters, as shown below, may be used to provide adequate
grounding surface. High temperature stainless steel should be used to minimize the effect of
metal oxidation. This assembly may be welded directly over the pilot or main burner nozzle.
WIRING OF FLAME RODS
For proper operation of flame rectification systems, it is necessary to maintain at least 20 megohms
insulating resistance in the flame rectification circuit.
1. The scanner should be wired using metal cable or rigid conduit.
2. High voltage wiring must not be installed in the same conduit with scanner wiring.
Selection of Scanner Wire
1. Use #14, 16, or 18 gauge wire with 90 C, 600 volt insulation for up to 20 feet distance.
2. The type of insulation used with flame rectification is important, since it must protect against
current leakage resistance to ground. Use Belden 8254-RG62 Coaxial Cable (or equal) for runs
greater than 20 feet. Maximum wiring run not to exceed 100 feet.
MAINTENANCE
Type 69ND1 Flame Rod
The flame rod and its insulator should be kept clean by washing routinely with soap and water. Rods
should be routinely replaced as they oxidize.
Flame Signal Strength
Routine observation of the flame signal strength will forewarn any deterioration in the capability of
the flame detector or its application.
Periodic Safety Check
It is recommended that a procedure be established to test the complete flame safeguard system at
least once a month. This test should verify the proper operation of all limit switches and safety inter-
locks as well as flame failure protection and fuel safety shutoff valve tightness.
BOMB FIN
GROUNDING
ASSEMBLY
THREADED ROD
ASSEMBLY

5
®
RESET
In the event of a lockout condition, the M4RT1 can be reset via a minimum one second power inter-
ruption to terminal 7.
RESET OPTIONS (Special Order)
1. Optional M4RT1 reset push button. When this optional reset pushbutton is installed, the M4RT1
can be reset by depressing this button for a minimum of one second.
2. Remote reset option. With this option, the M4RT1 is provided with two additional screw termi-
nals. Using those terminals, a remote, dry contact pushbutton switch can be connected. The
maximum wire length is 100 feet (no.18 AWG wire size is recommended).
CAUTION: Remote reset is recommended only on a control solely for proved ignition pro-
gramming (pilot ignited burner)or a control for use only with appliances in which unburned
fuel cannot accumulate and that is intended for installation in inaccessible locations such as
open-flame, ceiling-suspended gas heaters.
WARNING: SelectionofthePurgetimeandRecycle/ Non-Recycleoperation foraparticular
application, by changes to the factory default jumpers described below, should only be per-
formed by a competent professional, licensed by a state or other government agency. Inap-
propriate selection of these safety critical parameters could result in an unsafe condition
hazardous to life and property.
PROGRAMMER JUMPER SETTINGS
The M4RT1 has a series of 8 jumpers that are used to configure the Purge timing, Pilot Trial for Igni-
tion (PTFI) timing, and recycle or non-recycle operation.
Purge Timing
Jumpers JP1 through JP5 are used to select the Purge timing for the M4RT1. The available Purge
timing selections are 5, 7, 30, 60, and 240 seconds and any additive combination of those times.
Selecting two or more Purge timing jumpers will result in a Purge time period equal to the sum of the
jumpers selected. Selection of a Purge time is accomplished by cutting or not installing the associ-
ated jumper. The factory set, default Purge time of 5 seconds (JP1 not installed) is always selected.
The Table below lists all available Purge times and how to select those by cutting jumpers JP2
through JP5.
Purge Time (seconds) JP2 JP3 JP4 JP5
5 Installed Installed Installed Installed
12 Cut Installed Installed Installed
35 Installed Cut Installed Installed
42 Cut Cut Installed Installed
65 Installed Installed Cut Installed
72 Cut Installed Cut Installed
95 Installed Cut Cut Installed
102 Cut Cut Cut Installed
245 Installed Installed Installed Cut
252 Cut Installed Installed Cut
275 Installed Cut Installed Cut
282 Cut Cut Installed Cut
305 Installed Installed Cut Cut
312 Cut Installed Cut Cut
335 Installed Cut Cut Cut
342 Cut Cut Cut Cut

6
Pilot Trial for Ignition
Jumpers JP6 and JP7 are used by the factory only to select the PTFI for the M4RT1. The available
PTFI timing selections are 5 and 10 seconds. The factory set, default PTFI time is 10 seconds (JP6
installed, JP7 not installed). The PTFI time may only be set by the factory.
Recycle/Non-recycle Operation
Jumper JP8 is used to select either Recycle or Non-Recycle operation of the M4RT1. The factory
set, default is Recycle operation (JP8 installed). To select Non-Recycle operation, cut jumper JP8.
LED INDICATOR LIGHTS
The M4RT1 has 5 LED lights to indicate the operating status of the control. The function of these
lights are:
Opr Ctrl (Operating Control): This LED is lighted whenever input terminal 7 is energized. The
burner system safety interlocks and operating control should be wired in series and connected to the
M4RT1 terminal 7.
Air Flow: This LED is lighted whenever all of these conditions exist:
— Input terminal 7 is energized (operating control and safety interlocks closed).
— Input terminal 6 is energized (proof of airflow switch is closed).
— Output terminal 8 is energized (blower motor).
PTFI: This LED is energized only during the Pilot Trial For Ignition Period.
Flame: This LED is lighted whenever an adequate flame signal is detected between the M4RT1
terminals S1 & S2.
Alarm: This LED is energized whenever a safety lockout occurs. (See APPLICATION AND
FUNCTION section).
NOTE: The M4RT1 is not powered until the user’s operating control is energized.
APPLICATION AND FUNCTION
The M4RT1 provides prepurge, ignition and flame safeguard for heating and process gas fired burn-
ers. The “recycle” or “non-recycle” operation is determined by the #8 jumper on the top PCB. Purge
timing, as well as trial for ignition timing is also set by the jumpers. See JUMPER SETTINGS on
page 5.
The M4RT1 amplifier circuitry is designed to utilize a flame rod for flame detection. The Flame Fail-
ure Response Time (F.F.R.T.) is fixed at 3 seconds.
Pilot Ignited Burners - “Recycle” Operation
With jumper #8 in the “recycle” position, the typical wiring arrangement illustrated on page 10 for
pilot ignited burners provides the following function:
1. With power applied to Terminal 7 (Opr Ctrl LED lighted), the burner motor circuit (Terminal 8)
is energized. The control then waits for the proof of airflow input (Terminal 6) to be energized
2. The Pre-Purge timing starts when terminal 6 is energized.
3. Following the prepurge period (as determined by jumpers #1 through #5), KL-1 closes, ener-
gizing Terminal 3 which powers the pilot gas valve and Terminal 4 which powers the spark igni-
tion. A five or ten sec. (as determined by jumpers #6 or #7) trial for ignition is initiated (PTFI
LED lit).
4. When pilot flame is detected (Flame LED lit), KF-1 closes, energizing Terminal 5 which powers
the main fuel valve, KF-2 opens de-energizing Terminal 4 which shuts off the spark ignition.
5. When the operating control opens its circuit, or if a power failure occurs, the entire system is de-
energized. Power interruptions in the millisecond range do not affect the operation of the con-
trol. Power interruptions of longer duration will cause the control to recycle.

7
®
6. In the event the pilot flame is not detected by the end of trial for ignition period (PTFI), the pilot
gas valve (Terminal 3) and spark ignition (Terminal 4) are de-energized. A safety shutdown
occurs followed in approximately 30 seconds by a safety lockout that de-energizes the blower
motor (Terminal 8) and energizes the lockout alarm circuit (Alarm LED lighted).
7. In the event of a flame failure during a firing period, the pilot and main fuel valves are de-ener-
gized. Following the prepurge period (as determined by jumpers #1 through #5), with proven air
flow (Air Flow LED lit), the pilot gas valve and spark ignition are re-energized and a five or ten
sec. (as determined by jumpers #6 or #7) trial for ignition is initiated (PTFI LED lit). If pilot
flame is detected (Flame LED lit), the main fuel valve is energized, the spark ignition is de-ener-
gized. In the event the pilot flame is not detected by the end of trial for ignition period (PTFI),
the pilot gas valve (Terminal 3) and spark ignition (Terminal 4) are de-energized. A safety shut-
down occurs followed in approximately 30 seconds by a safety lockout that de-energizes the
blower motor (Terminal 8) and energizes the lockout alarm circuit (Alarm LED lighted).
8. Manual Reset (supply power cycled off/on) is required following any safety lockout.
NOTE: Wait 10 seconds after lockout before restarting the control.
Pilot Ignited Burners - “Non-recycle” Operation
The function of “non-recycle” pilot ignited burners is the same as described for the “recycle” con-
trols, except that the “non-recycle” operation will lock out following any flame failure. “Recycle” or
“non-recycle” operation is determined by the position of jumper #8. See Programmer jumper set-
tings on page 5.
Direct Spark Ignited Burners - “Recycle” Operation
With jumper #8 in the “recycle” position, the typical wiring arrangement illustrated on pages 10 and
11 for direct spark ignited burners provides the following function:
1. With power applied to Terminal 7 (Opr Ctrl LED lighted), the burner motor circuit (Terminal 8)
is energized. The control then waits for the proof of airflow input (Terminal 6) to be energized.
2. The Pre-Purge timing starts when terminal 6 is energized.
3. Following the selected prepurge period (as determined by jumper #1 through #5), KL-1 closes,
energizing Terminal 3 which powers the primary main fuel valve, and Terminal 4 which powers
the spark ignition. A five or ten second (as determined by jumper #6 and #7) trial for ignition is
initiated (PTFI LED lit).
4. When pilot flame is detected (Flame LED lit), KF-1 closes, energizing Terminal 5 which pow-
ers the secondary main fuel valve, and KF-2 opens, de-energizing Terminal 4 which shuts off
the spark ignition.
5. When the operating control opens its circuit, or if a power failure occurs, the control is de-ener-
gized. Power interruptions in the millisecond range do not affect the operation of the control.
Power interruptions at longer duration will cause the control to recycle.
6. In the event the pilot flame is not detected by the end of trial for ignition period (PTFI), the pilot
gas valve (Terminal 3) and spark ignition (Terminal 4) are de-energized. A safety shutdown
occurs followed in approximately 30 seconds by a safety lockout that de-energizes the blower
motor (Terminal 8) and energizes the lockout alarm circuit (Alarm LED lighted).
Direct Spark Ignited Burners - “Non-recycle” Operation
The function of “non-recycle” direct spark ignited burners is the same as described for the “recycle”
controls, except that the “non-recycle” operation will lock out following any flame failure. “Recy-
cle” or “non-recycle” operation is determined by the position of jumper #8. See Programmer Jumper
Settings on page 5.

8
TIMING CHART
Selectable Recycle/Non-Recycle operation on loss of flame after Terminal 5 energized. Recycle on
loss of air flow after flame proven.
INSTALLATION TESTING
Use of Test Meter
Testing the Fireye M4RT1 Control requires the use of a test AC-DC multimeter, with a 1,000 ohm/
volt DC rating or greater, or a digital meter with 500K input impedance or greater.
With the test meter on the DC scale, and the test meter leads inserted into the test jacks. A steady DC
voltage reading of 6 to 18 volts should be obtained when the control is detecting flame, and zero
volts when no flame is present.
With the test meter on the AC scale, line and load voltages may be measured at the identified test
points on the chassis.
On the M4RT1 control, a micro-ammeter may be connected in series with the wire to Terminal S2.
Normal flame will produce a meter reading between 4 and 10 micro-amps.
Flame Signal Testing
1. Manually shut off the main fuel valve for a pilot ignited burner, or the secondary fuel valve for a
direct spark ignited burner.
2. Set the test meter on the DC scale and insert the test leads into the test jacks on the amplifier
module. (If the meter reads backwards, reverse the meter leads). Red - Plus, Black - Negative.
3. Initiate a normal startup.
4. When flame is established, the test reading should be normal: a steady DC voltage reading of 6
to 18 volts.
5. Inadequate flame signal may be improved by:
a Assuring that the flame detector and wiring installations have followed the instructions on
pages 3 and 4.
b Assuring that the flame detector is clean and within the ambient temperature limits.
c Assuring that the flame is sufficiently large to detect.
d Assuring that the flame quality (fuel to air ratio, combustion air velocity) is satisfactory.
PROGRAMMING SEQUENCE
7
ON
PURGE
COMPLETE
FIRING
PERIOD 7
OFF
SELECTABLE PTFI
5 OR10 SEC
SELECTABLE
PURGE
8
T
E
R
M
I
N
A
L
S
3
4
5
AIR
FLOW
PROVEN

9
®
Minimum Pilot Test
This test insures that the flame detector will not sense a pilot flame too small to light the main flame
reliably. It must be made on every new installation as well as following the repositioning of the flame
detector. This procedure should not be used on a direct spark ignited burner.
1. Manually shut off the fuel to the main burner.
2. Connect a test meter to the test jacks.
3. Initiate a normal startup.
4. Reduce the fuel to the pilot until the DC voltmeter reads approximately 6 volts or when the pilot
is at the minimum to provide a reliable main flame light-off. See WARNING below. This is the
minimum pilot.
5. Slowly turn on the main fuel and insure that the main flame lights off promptly and normally.
WARNING: If light off is delayed, shut off the power to the installation. Realign the flame
detector so that pilot flame detection requires a larger pilot flame. Repeat this test until the
main flame lights reliably with minimum pilot.
WARNING:Theminimumpilottestmust be accomplishedbyatrainedandqualifiedburner
technician.
6. After the minimum pilot test is completed satisfactorily, increase the pilot flame to normal size,
and observe that the main flame is properly established during a normal cycle ("Run-Check"
switch in the "Run" position).
Flame Failure Test
1. Temporarily connect spark ignition and pilot valve to Terminal #3.
2. Initiate a normal startup.
3. Manually shut off all fuel and observe the loss of flame signal on the test meter.
4. If flame signal does not reduce to zero within the flame failure response time of the control, a
grounded metallic shield may need to be inserted between the flame rod and spark ignition to
prevent interference.
5. IMPORTANT: When the test is completed, reconnect the spark ignition to Terminal #4.

10
FIGURE 1. TYPICAL WIRING ARRANGEMENT FOR PILOT IGNITED BURNER.
Use moisture resistant wire suitable for at least 90C.
CAUTION: When powered, 260 VAC across S1, S2.
FIGURE 2. TYPICAL WIRING ARRANGEMENT FOR DIRECT SPARK IGNITED BURNER
Use moisture resistant wire suitable for at least 90C.
CAUTION: When powered, 260 VAC across S1, S2.
CAUTION: Control wiring procedures which deviate fromthose shown in the diagrams may
bypass safety functions designed in the control. Check with the Fireye Representative before
deviating from the recommended wiring diagrams.
LIMIT
SWITCHES
OPERATING
CONTROL
FUEL
INTERLOCKS
7
BURNER MOTOR
OR
CONTACTOR 8
2
A
6
LOCKOUT
ALARM
KB
KA
AIR FLOW
SWITCH
ELECTRONIC
CIRCUIT
KL KF
S1
S2
3
5
4
FLAME
AMPLIFIER
KL-1
KF-1
KF-2
PILOT
MAIN
SPARK
BURNER
CONTROL
SWITCH
H
N
120V (MC120))
60 Hz
SUPPLY
DISCONNECT MEANS
& OVERLOAD
PROTECTION REQUIRED
FLAME ROD
FUEL VALVE
IGNITION
GAS VALVE
LIMIT
SWITCHES
OPERATING
CONTROL
FUEL
INTERLOCKS
7
BURNER MOTOR
OR
CONTACTOR 8
2
A
6
LOCKOUT
ALARM
KB
KA
AIR FLOW
SWITCH
ELECTRONIC
CIRCUIT
KL KF
S1
S2
3
5
4
FLAME
AMPLIFIER
KL-1
KF-1
KF-2
PRIMARY MAIN
BURNER
CONTROL
SWITCH
H
N
120V (MC120)
60 Hz
SUPPLY
DISCONNECT MEANS
& OVERLOAD
PROTECTION REQUIRED
FLAME ROD
FUEL VALVE
SECONDARY
SPARK
MAIN FUEL
VALVE (IF USED)
IGNITION
FOR INTERMITTENT IGNITION, CONNECT
TO TERMINAL 3

11
®
FIGURE 3. ALTERNATE WIRING ARRANGEMENT
Use moisture resistant wire suitable for at least 90C.
CAUTION: Control wiring procedures which deviate from those shown in the diagrams may
bypass safety functions designed in the control. Check with the Fireye Representative before
deviating from the recommended wiring diagrams.
S2
3
5
4
MAIN
IGNITION
7
8
2
A
6
STOP
PILOT
S1
START
LIMIT SW
FUEL VALVE
ALARM
ON-OFF
HOT
NEUTRAL
LR-1
LR-2
LATCH
AIR FLOW
SWITCH
MOTOR
A. FOR MANUAL START
A START-STOP STATION MAY BE ADDED TO REQUIRE
OPERATOR START-UP EACH TIME THE BURNER FIRES.
S2
3
5
4IGNITION
7
8
2
A
6
PILOT
S1
B. MULTIPLE BURNER SYSTEMS
S2
3
5
4IGNITION
7
8
2
A
6
PILOT
S1
LIMIT
R
MANUAL RESET
MAIN GAS VALVE
ALARM
S.P.D.T.
RA
ALARM SILENCE
SWITCH
G
R
STOP START
LR-1
AIR FLOW
COIL OF MOTOR
CONTACTOR LATCH
HOTNEUTRAL
MULTIPLE BURNER SYSTEMS UTILIZING SEMI-AUTOMATIC OPERATION INCORPORATE THE FIREYE
MODULAR M-SERIES II CONTROLS IN A CASCADING SEQUENCE WHEN PILOT #1 IS PROVEN. TRIAL
FOR IGNITION FOR PILOT #2 BEGINS. WHEN ALL PILOTS ARE PROVEN THE SAFETY SHUTOFF VALVE
MAY BE MANUALLY OPENED. FLAME FAILURE OF ANY BURNER WILL TRIP THE MAIN FUEL VALVE AND
SOUND ALARM.
THE TOTAL CONNECTED LOAD MUST NOT EXCEED THE RATING OF THE FIRST CONTROL.
VALVE
RELAY COIL
MAIN GAS VALVE
GAS VALVE
RELAY
GAS VALVE
SWITCH
SWITCH
HOT

12
NOTICE
When Fireye products are combined with equipment manufactured by others and/or integrated into
systems designed or manufactured by others, the Fireye warranty, as stated in its General Terms and
Conditions of Sale, pertains only to the Fireye products and not to any other equipment or to the
combined system or its overall performance.
WARRANTIES
FIREYE guarantees for one year from the date of installation or 18 months from date of manufacture
of its products to replace, or, at its option, to repair any product or part thereof (except lamps, elec-
tronic tubes and photocells) which is found defective in material or workmanship or which otherwise
fails to conform to the description of the product on the face of its sales order. THE FOREGOING
IS IN LIEU OF ALL OTHER WARRANTIES AND FIREYE MAKES NO WARRANTY OF
MERCHANTABILITY OR ANY OTHER WARRANTY, EXPRESS OR IMPLIED. Except as
specifically stated in these general terms and conditions of sale, remedies with respect to any product
or part number manufactured or sold by Fireye shall be limited exclusively to the right to replace-
ment or repair as above provided. In no event shall Fireye be liable for consequential or special dam-
ages of any nature that may arise in connection with such product or part.
FIREYE M-4000
3 Manchester Road APRIL 16, 2013
Derry, New Hampshire 03038 Supersedes July 15, 2011
www.fireye.com
Table of contents
Other Fireye Control Unit manuals
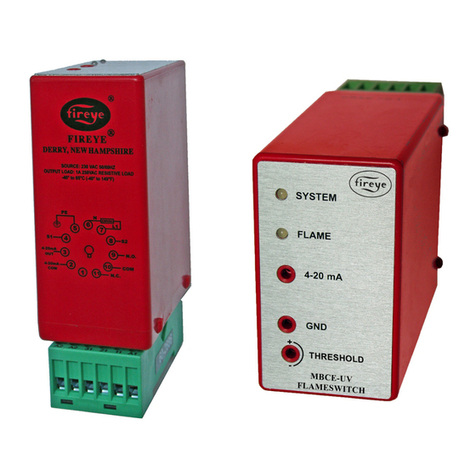
Fireye
Fireye MBCE-110UV Series User manual
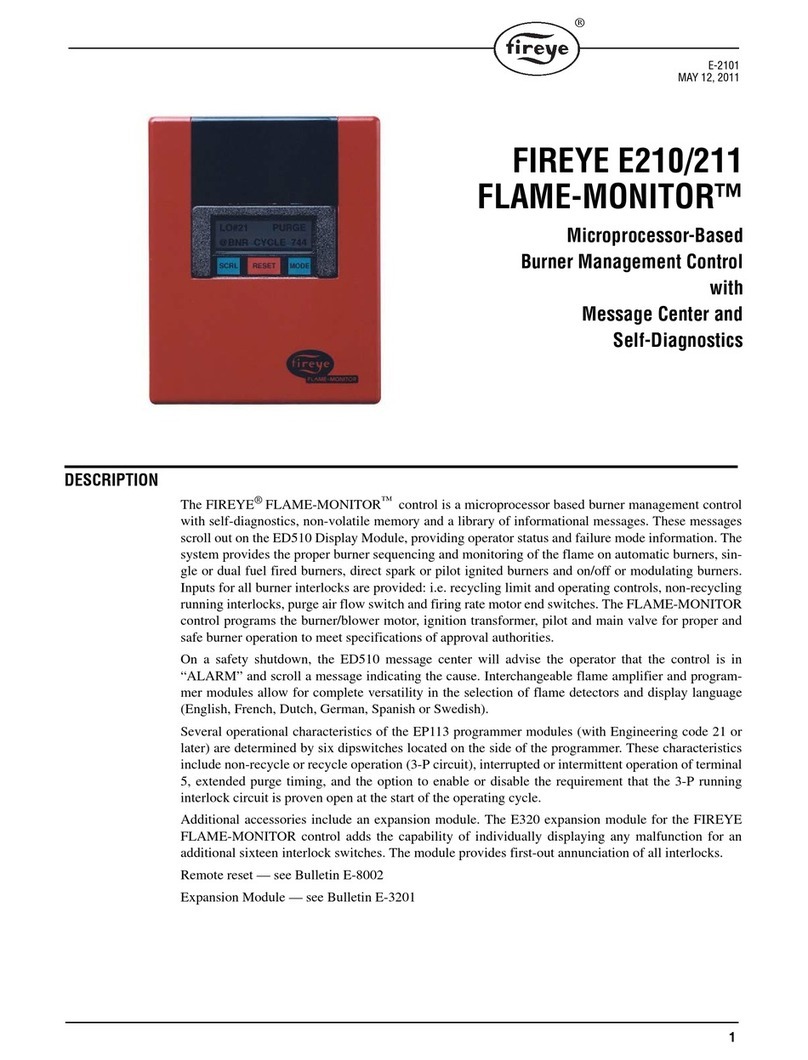
Fireye
Fireye FLAME-MONITOR E210 User manual
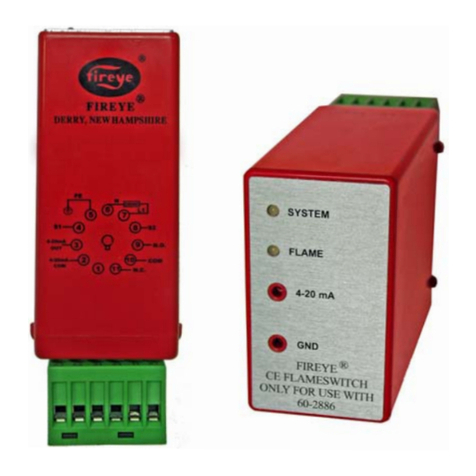
Fireye
Fireye MBCE-110FR User manual
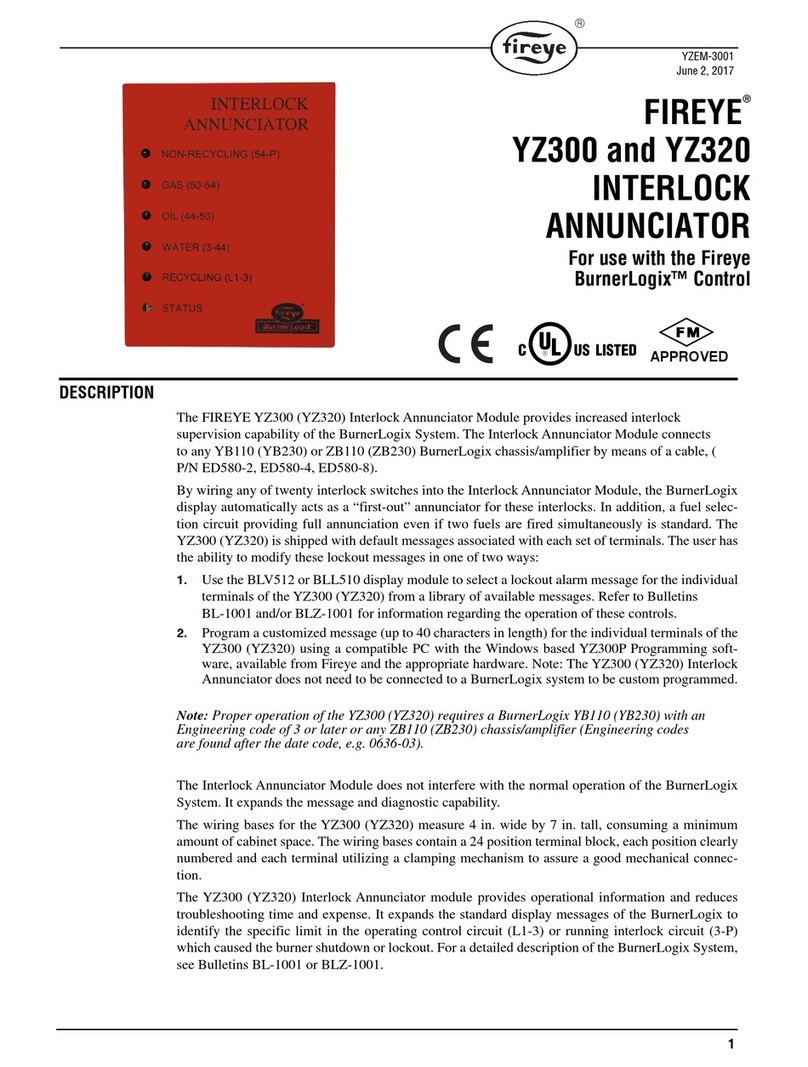
Fireye
Fireye YZ300 User manual
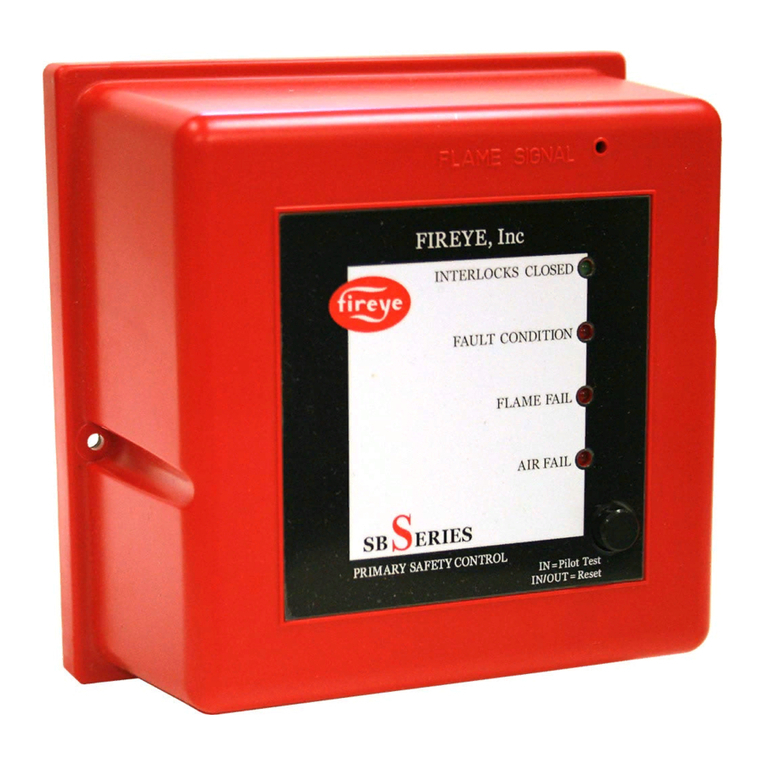
Fireye
Fireye SB Series User manual
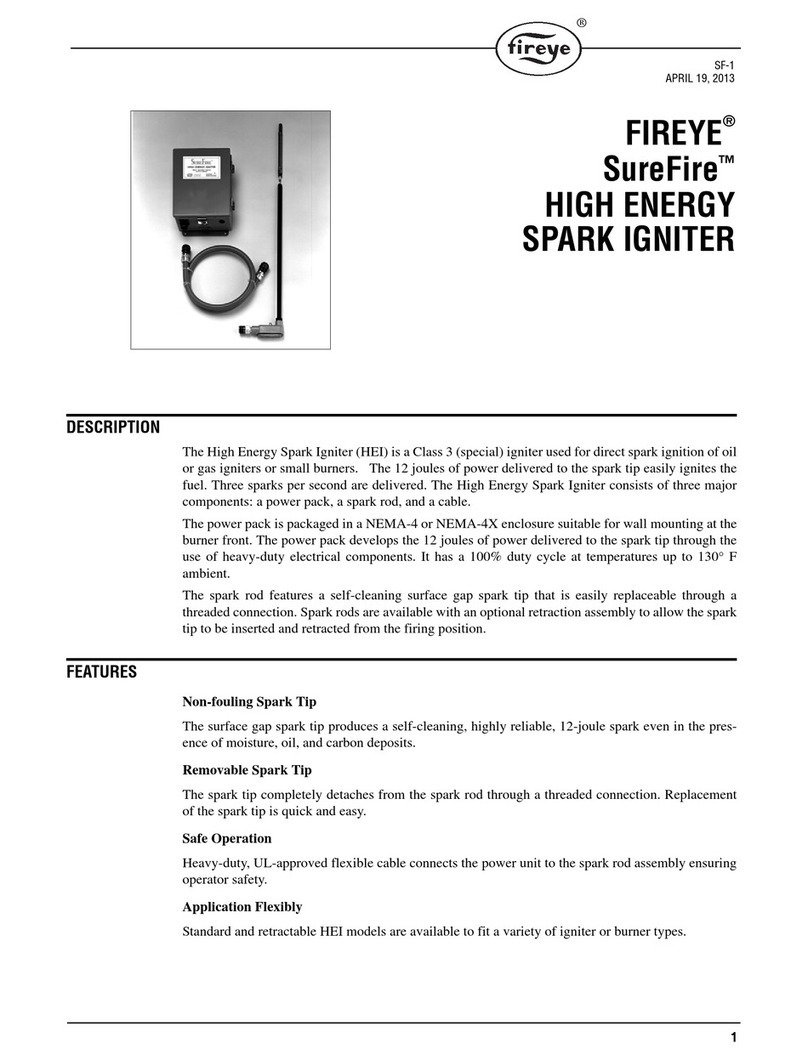
Fireye
Fireye SureFire User manual

Fireye
Fireye BurnerLogiX YB110 User manual
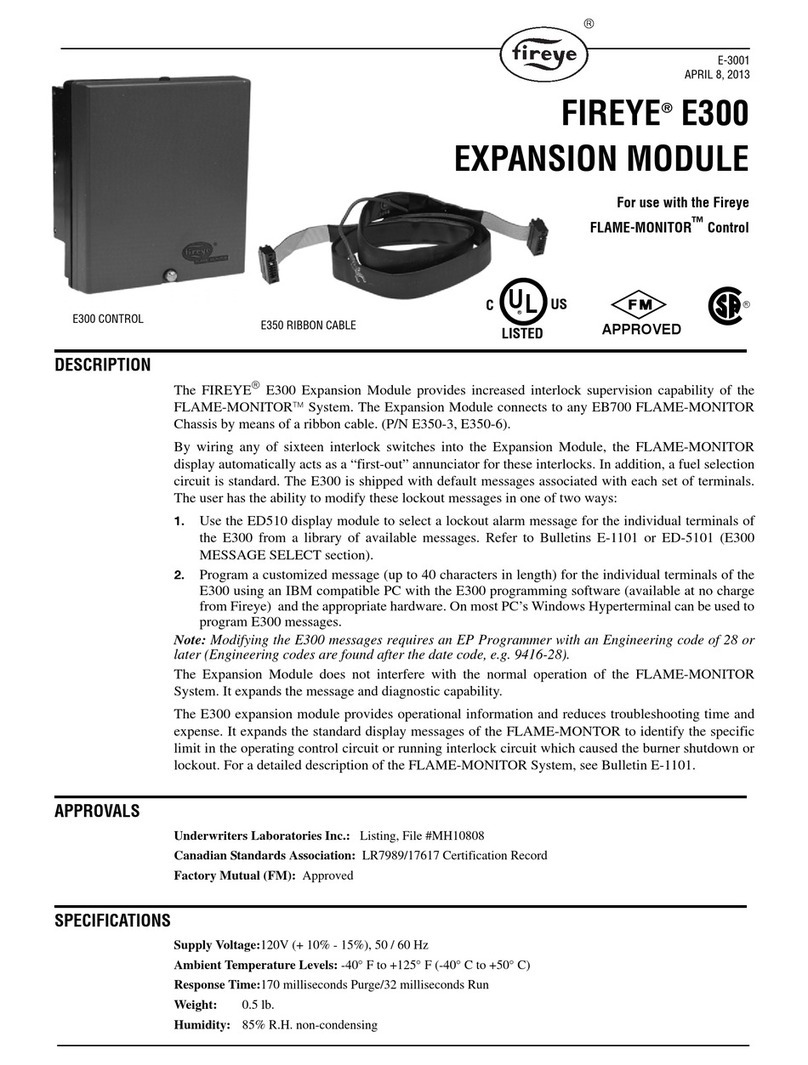
Fireye
Fireye E300 User manual

Fireye
Fireye EP160 User manual

Fireye
Fireye D40 Series User manual
Popular Control Unit manuals by other brands
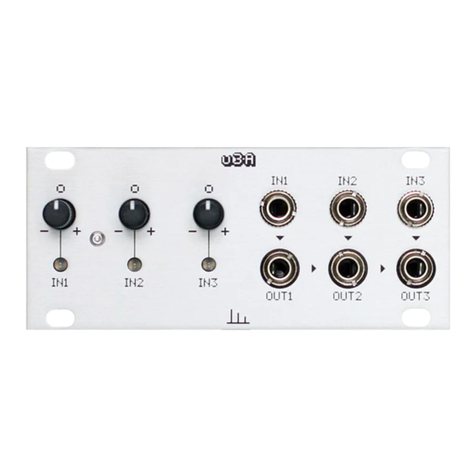
Transient Modules
Transient Modules u3A Build manual
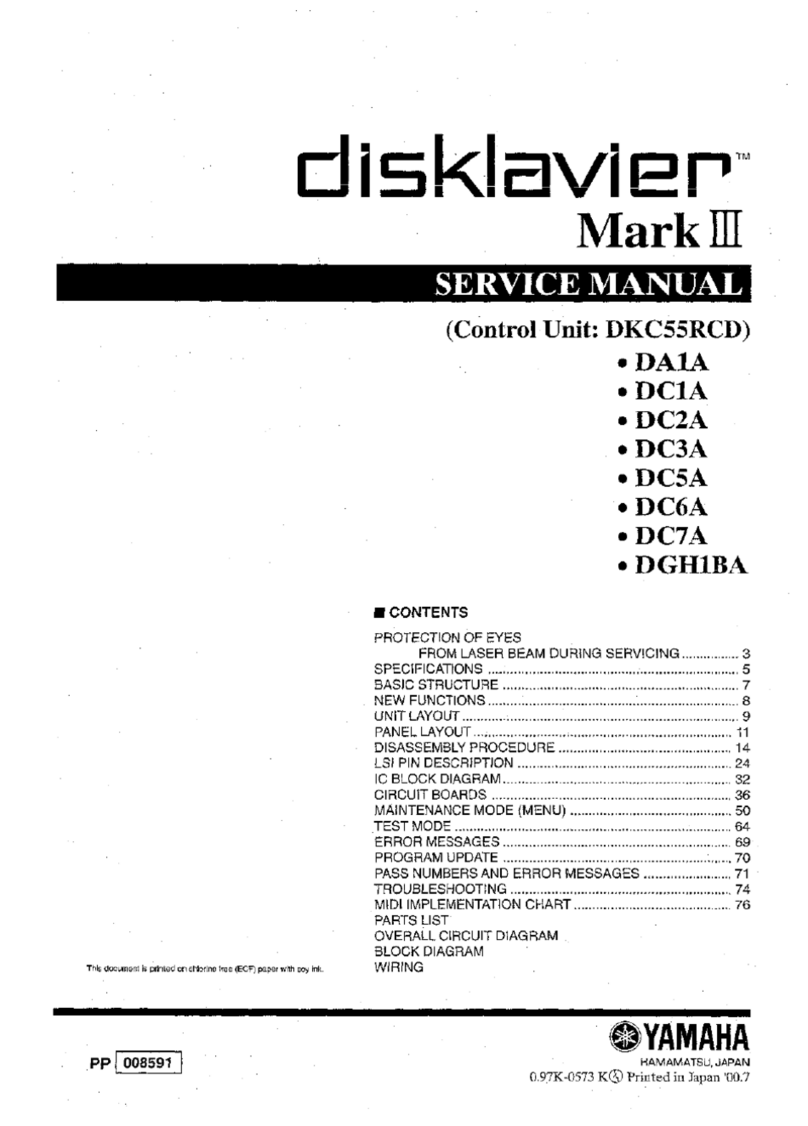
Yamaha
Yamaha Disklavier DKC55RCD XG Mark III Service manual
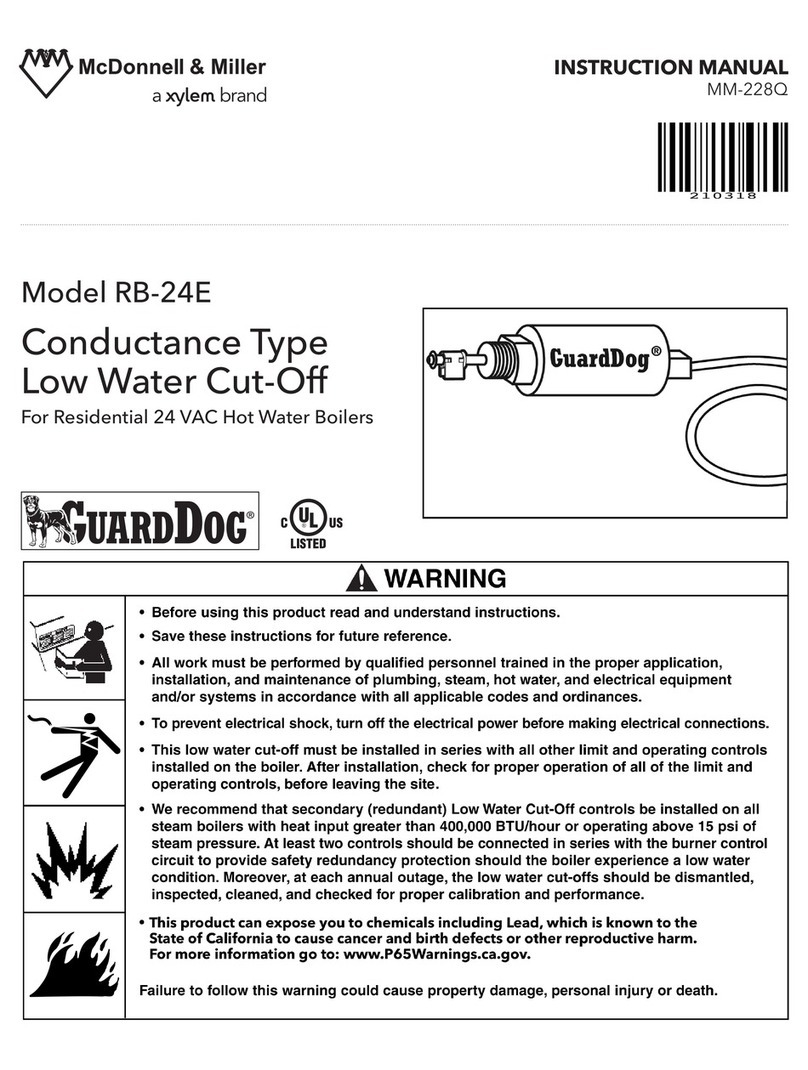
Xylem
Xylem McDonnell & Miller RB-24E instruction manual
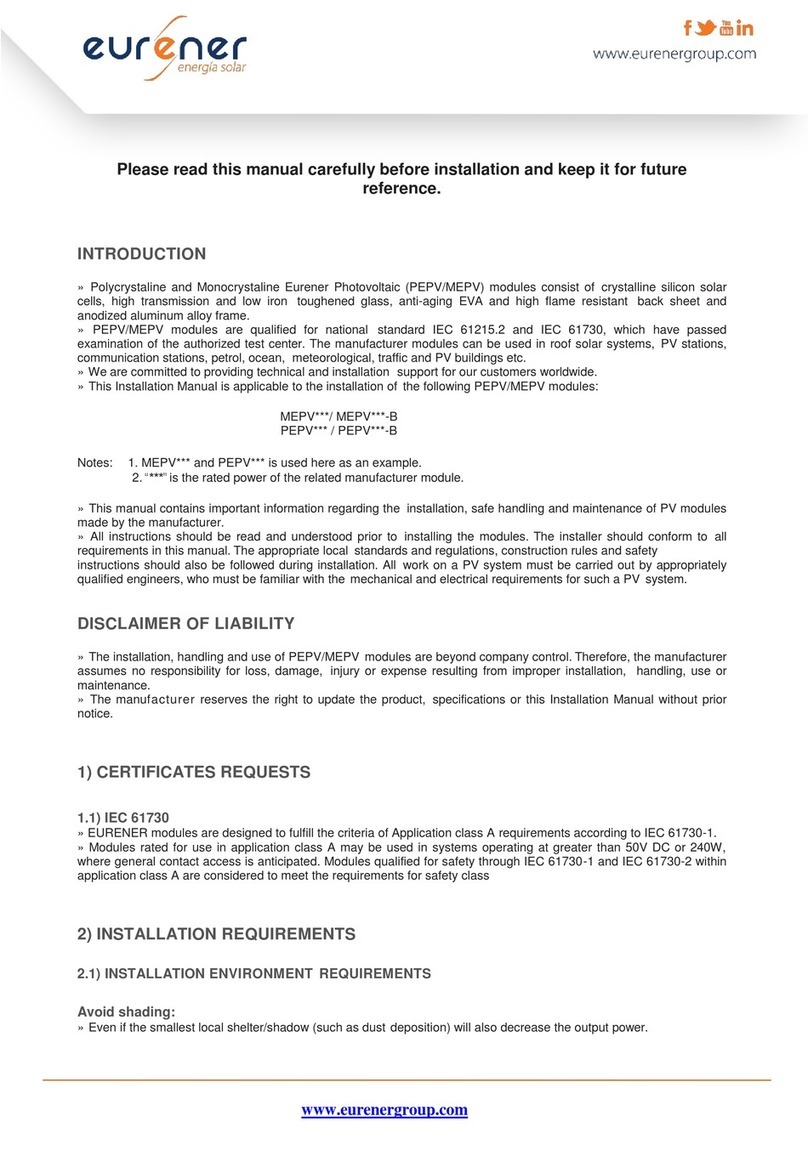
Eurener
Eurener PEPV Series installation manual

Danfoss
Danfoss AKD 5001 manual
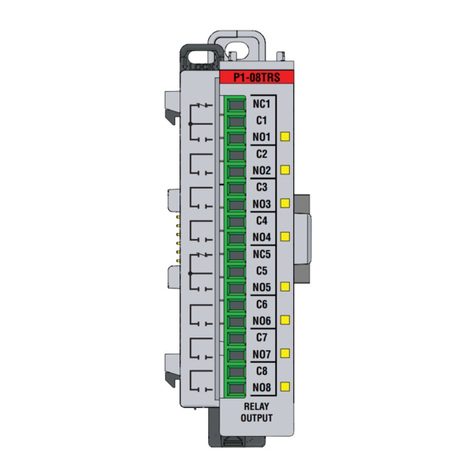
Automationdirect.com
Automationdirect.com Productivity 1000 P1-08TRS manual