Fytech FYMIG5260 User manual

Instruction Manual
Our equipment is approved by the following car manufacturers(China)
FYMIG5260

CONTENTS
1. Safety Precautions Symbols
2. Symbols and Descriptions
3. Installation
3.1 Specifications
3.2 Duty Cycle and Overheating
3.3 Machine Installation
3.4 Selecting a Location
3.5 Installing Gas Supply
3.6 Connecting Input Power
3.7 Threading Welding Wire
3.8 Changing Drive Roll
3.9 Typical MIG Process Connection
3.10 Welding Gun
4. Operation
4.1 Controls
4.2 Holding and Positioning Welding Gun
4.3 Conditions that Affect Weld Bead Shape
4.4 Gun Movement during Welding
4.5 Poor Weld Bead Characteristics
4.6 Good Weld Bead Characteristics
5. Troubleshooting
5.1 Excessive Spatter
5.2 Porosity
5.3 Excess Penetration
5.4 Lack of Penetration
5.5 Incomplete Fusion
5.6 Burn through
5.7 Waviness of Bead
5.8 Distortion
5.9 Other Troubleshooting
1
2
3
4
5
6
7
8
9
10
11
12
13
14
15
16
17
18
19
20
21
22
23
24
25
26
27

Read instructions.
1. Read the manual before using or
servicing unit.
2. Use only manufacturer’s supplied
replacement.
Exploding parts can injure. Always
wear a face shield and long sleeves.
Static can damage PC boards
1.Put on grounded wrist strap before
handing boards or parts。
2. Use proper static-proof bags and
boxes to store, move or ship PC boards.
Fire or explosion hazard.
Do not locate unit on, over, or near combustible
surfaces. Do not install unit near flammables.
1. Wear approved face shield or safety
goggles with side shields.
2. Wear proper body protection to
protect skin.
Do not weld in the height!
Flying metal can injure eyes. Wear safety
glasses with side shields or face shield.
1. Magnetic fields can affect pacemakers.
Pacemaker wearers keep away.
2. Wearers should consult their doctor
before going near plasma arc cutting
operations.
Overuse can cause overheating. Allow
cooling period, follow rated duty cycle
before starting to weld again.
Cylinders can explode if damaged. Gas
cylinders contain gas under high pressure.
If damaged, a cylinder can explode. Be sure
to treat them carefully.
Electric shock can kill:
1. Do not touch live electrical parts.
2. Wear dry, hole-free insulating gloves
and body protection.
3. Do not wrap electrical cable around your body.
4. Ground the workpiece with a good electrical ground.
Keep away from the torch tip.
Remove all flammables of the welding area.
Falling unit can cause injury.
Eye protection for welding:
Current level in amperage / Minimum shade number
30-150A / #8
150-300A / #10
300-500A / #12
The heat from the workpiece can cause serious
burns.
Never cut on pressurized cylinder.
Keep away from moving parts such as fans.
Fumes and gases can be hazardous:
Welding produces fumes and gases. Breathing these
fumes and gases can be hazardous to your health. If
inside, ventilate the area. Do not weld in a confined
space only if it is well ventilated.
Moving parts can cause injury.
To protect yourself and others from injury, read and follow these
precautions before installation and operation.
1. SAFETY PRECAUTIONS SYMBOLS
Page 1
Protect yourself! Warn others! Factory safety! Maintenance regularly!

U1
U0
U2
I2
s1
HZ
A
V
Primary Voltage
Hertz
IP
X
~
1
V
I
O
+-
%
Adjust Air/Gas
Pressure
Gas Input
Gas Output Do Not Switch
While Welding
Amperes
Volts
Gas Metal Arc
Welding (GMAW)
Gun
On Percent
Wire Feed Off Increase
Line Connection
Loose Shield Cup
Protective Earth
(Ground)
Degree of Protection
Rated Welding
Current
No / Do Not Do This
Single Phase
Power Rating, Products
of Voltage and Current
Duty Cycle
Direct Current
Wire Feed
Spool Gun
Input
Constant Current
Voltage Input
Temperature
Rated No Load
Voltage (Average)
Conventional Load
Voltage
Page 2
Description:
Our semi-automatic welder is an all-in-one MIG shielding gases welder (GMAW) with high
efficiency that is an ideal substitute for manual arc welding. Most advanced circuit design
and technology are adopted. Excellent performances, supreme reliability, quality welding
requirements can be satisfied. Spot weld, groove weld, and fillet weld are available. Most
commonly used shielding gases are applicable such as Co2, AR, CO2+AR, CO2+O, etc.
Suitable for welding of various metallic materials such as mild steel, low carbon steel, low
alloy steel, stainless steel, steel, iron, copper, aluminum, nicket, etc. Extensively used in the
welding and field operation of oil pipeline, chemical, car fabrication, shipyard, etc.
2. SYMBOLS AND DESCRIPTIONS
Symbols and Definitions

Page 3
3. INSTALLATION
3.1 Specifications
Model
Input Voltage
(V)
Frequency
(Hz)
FYMIG5320
AC 380
Three Phase
50/60
Rated Input Current
(A)
Rated Output Current
(A)
Output Voltage
(V)
No-load Voltage
(V)
Welding Wire Diameter
(mm)
Duty Cycle
Insulation Class
Dimensions
(mm)
17
320
15.7-33
55
0.6, 0.8, 0.9, 1.0
65%
F
1050*520*930
11
Rated Input Power
(KW)
FYMIG5300
15.7-31
50
0.6, 0.8, 0.9, 1.0
65%
F
1050*520*930
10
FYMIG5260
AC 380
Three Phase
50/60
260
15.7-30
50
0.6, 0.8, 0.9, 1.0
65%
F
1050*520*930
8.0
AC 220
Single Phase
单相
Ac380
Three Phase
单相
50/60
15
300
12

0
15
A
Page 4
3. INSTALLATION
3.2 Duty Cycle and Overheating
1. Overheat protection is installed on the aluminium board of main transformer
and rectifier. The unit products heat while welding.
2. If unit overheats, output stops, and cooling fan runs.
3. Wait fifteen minutes for unit to cool. Reduce amperage or voltage, or duty
cycle before welding.
Weld againOverheating Stop working Wait 15 minutes
for unit to cool
Reduce amperage or
reduce duty cycle

Page 5
3. INSTALLATION
3.3 Machine Installation
1. Open the package and find out the Manual.
2. Check the details of accessories according to packing list that attached to this
manual.
3. Properly install this equipment as following diagram. Inspect the unit for any
damage. If so, contact your local distributor or service agency.
4. The unit should not be located under sunshine. The worksite should be in low
humidity and without dust.
5. Operating Temperature range: -10°C to +40°C.
6. Storage Temperature range: -25°C to +56°C.
7. At least 20cm of space for airflow, 30cm of space for two units located side by
side.
8. Use tent to protect the machine from stormy weather when operate outdoor.
9. Welding produces fumes and gases, breathing these fumes and gases can be
3
hazardous to your health. If inside, less than 300m , Ventilate the area.
10. Properly ground this equipment.
11. The input power cord gradient should not more than 15°.

Page 6
3. INSTALLATION
3.4 Selecting a Location
1. Select a correct location to place the unit.
2. Determine input power cord length according to its actual operation
requirement. Input power cord must have a minimum inside diameter of 6mm2.
3. Do not move or operate unit where it could tip.
4. Use cart or unit handle to move unit. Do not pull the cords to move unit.
5. Moving gas cylinder and main unit to hight sparaely.Use lifting eye to lift unit
only, not running gear, gas cylinders, or any other accessories.
6. Optional order for individual wire feeder is available. The wire fe eder and
welding gun divide from the main unit.It is more convenient to operate.

ON
OFF
CO2
Page 7
3. INSTALLATION
3.5 Installing Gas Supply
1. Cap
2. Cylinder valve (Remove cap, stand to side of valve, and open valve slightly. Gas
flow blows dust and dirt from vavle. Close vavle.)
3. Cylinder
4. Regulator/Flowmeter (Make sure the surface is vertical while installing.)
5. Flow Adjust (Typical pressure is 0.05-0.15MPa.)
6. Hose
7. Hose Connection (Connect gas hose between regulator/flowmeter and the
unit.)
8. Regulator/Flowmeter heating socket (For low temperature worksite, please
plug the regulator/flowmeter to the socket for heating.
DO NOT use other gases regulater/flowmeter
2
with CO shielding gas.
Rear Panel
1
2
3
4
5
6
7
8

ON
OFF
CO2
Page 8
3. INSTALLATION
3.6 Connecting Input Power
2
1. Input power cord (not less than 6mm
copper cord).
2. Over-current protection.
3. Disconnect device line terminals.
4. Ground wire L1/L2 input conductors.
Installation must meet all National and Local
Codes. Only qualified persons
are allowed to make this installation.
Disconnect and lockout/tagout input power
before connecting input conductors from unit.
Select type and size of over-current protection.
Close and secure door on disconnect device.
Remove lockout/tagout device, and place
switch in the "on" position.
2
L1 L2
2
1
4

2
3
4
Page 9
3. INSTALLATION
3.7 Threading Welding Wire
1. Wire spool spindle
2. Welding wire
3. Pressure adjustment knob
1
2
3
1. Open wire spool spindle; install wire spool; release pressure adjustment knob;
pull and hold wire.
Push wire thru guides into drive roll. Close wire spool spindle tightly to prevent
slipping (Feed wire to check wire spool installation).
2. Set a desired drive roll pressure, close and tighten pressure adjustment knob.
3. Press gun trigger and let go of wire.
4. Remove gun nozzle and contact tip.
5. Press gun trigger until wire comes out of gun. Reinstall contact tip and nozzle.
6. Feed wire to check drive roll pressure, tighten knob enough to prevent slipping.
7. Cut off wire if welding wire extends too far beyond nozzle.

1. Drive roll securing nut
2. Drive roll
3. Pressure adjustment knob
4. Press device
2
1
3
4
Changing Drive roll:
1. Release pressure adjustment knob. Press wire device springs open.
2. Loosen securing nut, Remove drive roll.
3. The drive roll consists of two different sized grooves. Reinstall the desired wire
sized groove close to the motor shaft.
4. Tighten securing nut.
5. Replace press wire device, and set a desired pressure.
6. Make sure drive roll groove lines up with wire guide.
Page 10
3. INSTALLATION
3.8 Changing Drive Roll

ON
OFF
CO2
2
3
4
Regulator/Flowmeter
Wire feeder Hose
Shielding gas
Gun
Work clamp and workpiece
Weld current can damage electronic parts in vehicles. Disconnect both battery
cables before welding on a vehicle. Place work clamp as close to the weld as
possible.
Page 11
3. INSTALLATION
3.9 Typical MIG Process Connection

1. Shield cup C012
2. Contact tip C004
3. Front adaptor C010
4. Gooseneck (15/24AK) C020/C018
5. Trigger
6. Spanner
1234
65
Page 12
3. INSTALLATION
3.10 Welding Gun

095 0.412 M/M
Page 13
4.OPERATION
4.1 Controls
14
15
16
17
11
12
13
10
9
8
7
6
5
1
2
3
4
1. LCD panel
2. Inductance display
3/4. Inductance adjustment
5. Time display
6/7. Time adjustment
8. Current adjustment
9. Wire feeding speed adjustment
10/11. Thickness adjustment
12. Device information
13. Pulse welding
14. Aluminium
15. Iron
16. Copper
17. Alloy
1. Current display
2. Material thickness
3. Wire feeding speed
4. Pulse welding
5. Regular
Setting Instructions
12 3
4
5
1.Operation Panel
NO.13
(1). LCD panel
(2) .Inductance display
(3)/(4) .Inductance adjustment
(Default setting, do not adjust
unless necessary. Remember that
the higher the inductance, the
deeper the fusion.)
(5) .Time display
(6)/(7) .Time adjustment
(8). Current adjustment
(9) .Wire feeding speed adjustment
(10)/(11) .Thickness adjustment
(12) .Equipment information
(13). Pulse / Regular
(14) .Welding materials
Attention!
1.Generally only need to adjust (10) and (11). Do not need adjust other preset parameters.
2.According to actual situations, sometimes can fine tune (8) and (9) to achieve the best welding effect.
3.Restore factory default settings:
Press (12), LCD panel (1) shows equipment information. Then press and hold (3) and (6) at the same time for
about 10s. Turn off the machine then turn it on.
4.Regular and pulse switching: The machine is preset as regular mode as ⑤ in the figure. Press (13) to switch
the mode to pulse welding indicated by a highlighted black box over the program icon as ④ in the figure. Then
(9) is used to adjust the pulse frequency instead of wire feeding speed. Press (13) again, switch to regular
welding mode again.
5.Spot welding time adjustment: The defualt setting is FFF -- manual mode. It will switch to aoto mode if adjust
(6) and (7). For example spot welding time 0.1 means 0.1s, which means that when you press and release the
trigger once, the machine will stop after feeding wire 0.1s (welding only 0.1s even if you press and hold the
trigger all the time).
2.Setting Screen
095 0.412 M/M
(1)
(2)
(3)
(4)
(11)
(12)
(13)
(10)
(9)
(8)
(7)
(6)
(5)
Welding materials(14)
①.Current display
②.Material thickness
③.Wire feeding speed
④.Pulse welding
⑤.Regular welding (it is regular
welding as shown in the figure)
① ② ③
④
⑤
Operation

1. Hold gun and control gun trigger
2. Workpiece
3. Work clamp
4. Electrode extension (stickout)
5. Cradle gun and rest hand on workpiece
1
2
3
4
5
End view of work angle
End view of work angle
Side view of gun angle
Side view of gun angle
45°
45°
90° 90° 0°-15°
0°-15°
GROOVE WELDS
FILLET WELDS
Welding wire is energized when gun trigger is pressed. Before lowering helmet and
pressing trigger, be sure wire size is correct to past end of contact tip, and tip of
wire is positioned correctly on seam.
Page 14
4.OPERATION
4.2 Holding and Positioning Welding Gun

Weld bead shape depends on gun angle ,direction of travel, electrode extension
(stickout), travel speed, thickness of base metal, wire feed speed (weld current),
and voltage.
Push
Perpendicular
Short
Short
Slow
Normal
Normal
Normal
Drag
Long
Long
Fast
10°
10°
GUN ANGLES AND WELD BEAD PROFILES
ELECTRODE EXTENSIONS (STICKOUT)
FILLET WELD ELECTRODE EXTENSIONS (STICKOUT)
GUN TRAVEL SPEED
Page 15
4.OPERATION
4.3 Conditions that Affect Weld Bead Shape

1. Stringer Bead
Steady movement along seam
2. Weave Bead
Side to side movement along seam
3. Weave Patterns
Use weave patterns to cover a wide
area in one pass of the electrode
Page 16
4.OPERATION
4.4 Gun Movement during Welding
1
2
3

1. Large Spatter Deposits
2. Rough, Uneven Bead
3. Slight Crater during Welding
4. Bad Overlap
5. Poor Penetration
Page 17
4.OPERATION
4.5 Poor Weld Bead Characteristics
1
23
4
5

1
23
4
5
1. Fine Spatter
2. Uniform Bead
3. Moderate Crater during Welding
4. No Overlap
5. Good Penetration into Base Metal
Page 18
4.OPERATION
4.6 Good Weld Bead Characteristics
Table of contents
Other Fytech Welding System manuals
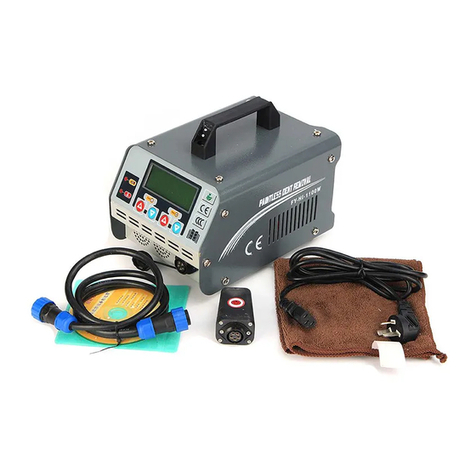
Fytech
Fytech FY-HI-1100W User manual
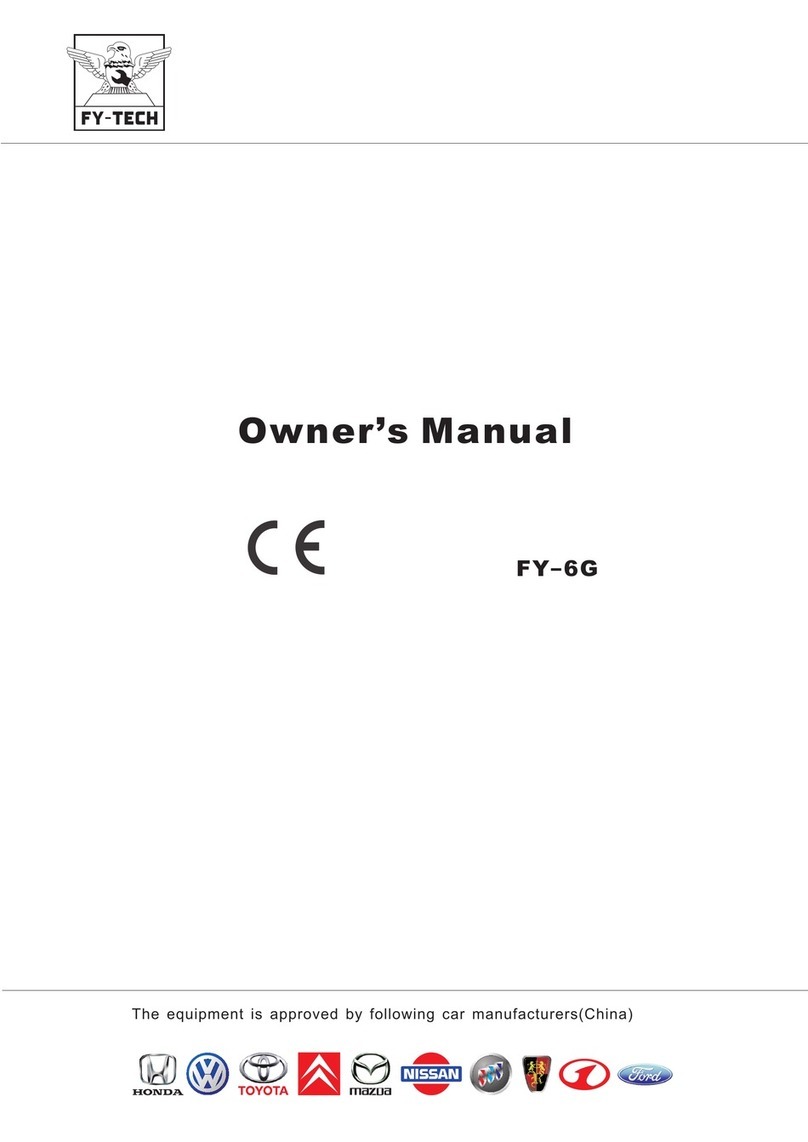
Fytech
Fytech FY-6G User manual
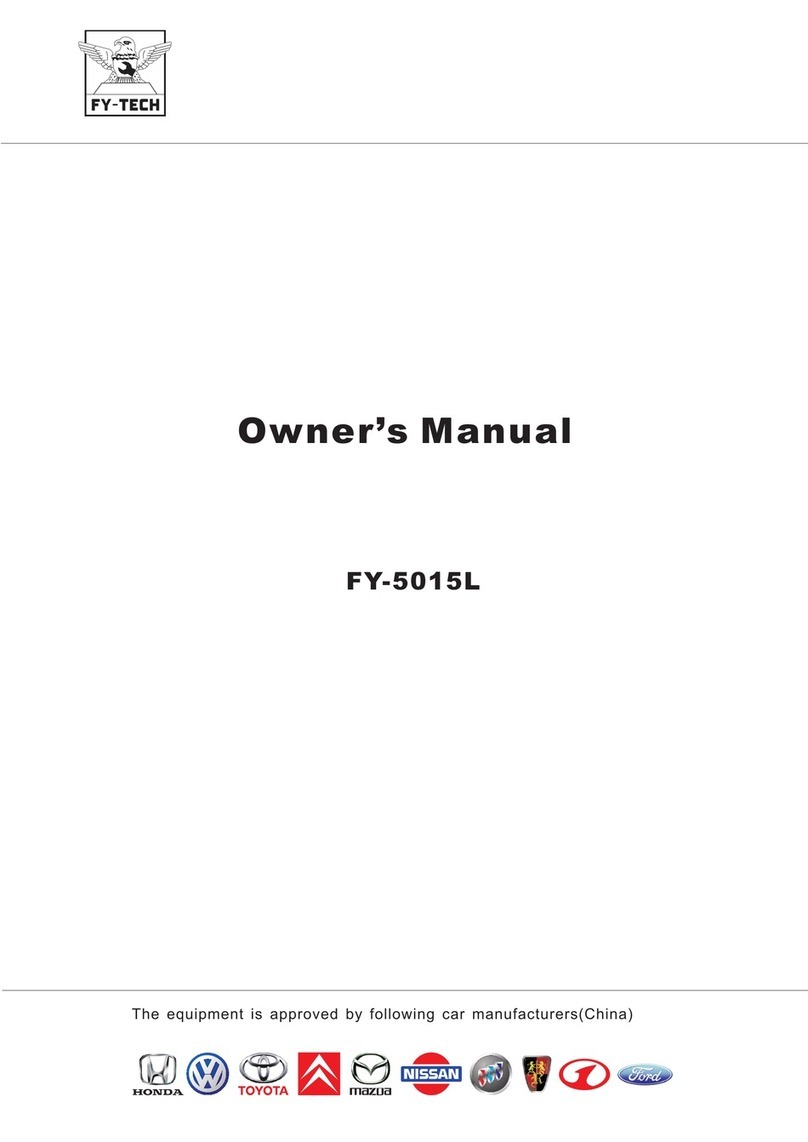
Fytech
Fytech FY-5015L User manual

Fytech
Fytech FYMIG270X User manual
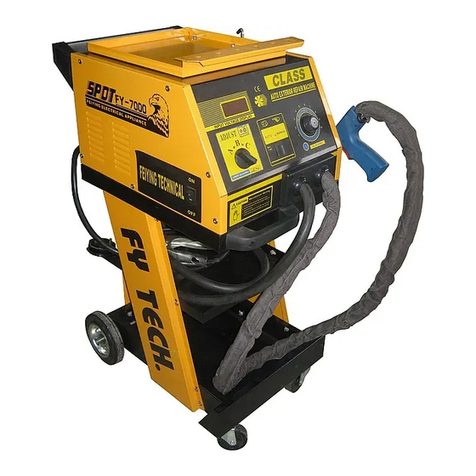
Fytech
Fytech FY-7000 User manual

Fytech
Fytech FYMIG200L-3 User manual
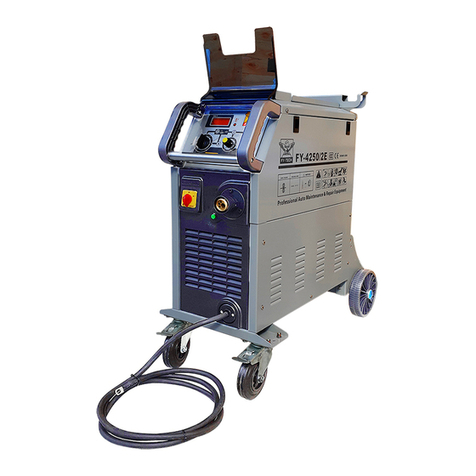
Fytech
Fytech FY-4250/2E User manual

Fytech
Fytech FY-2012S User manual
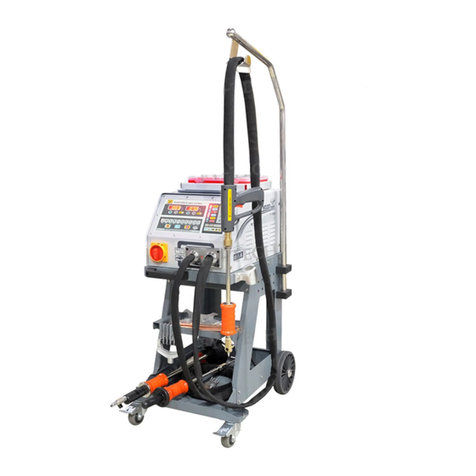
Fytech
Fytech FY-9000 User manual
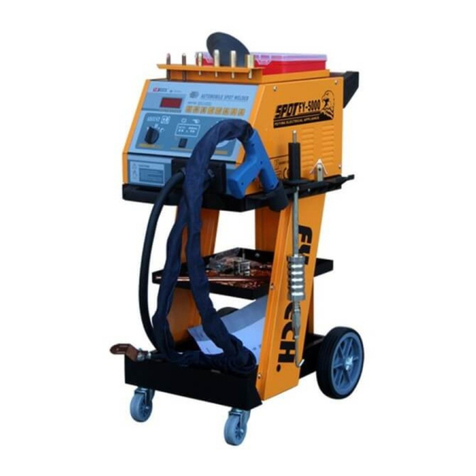
Fytech
Fytech FY-5000 User manual
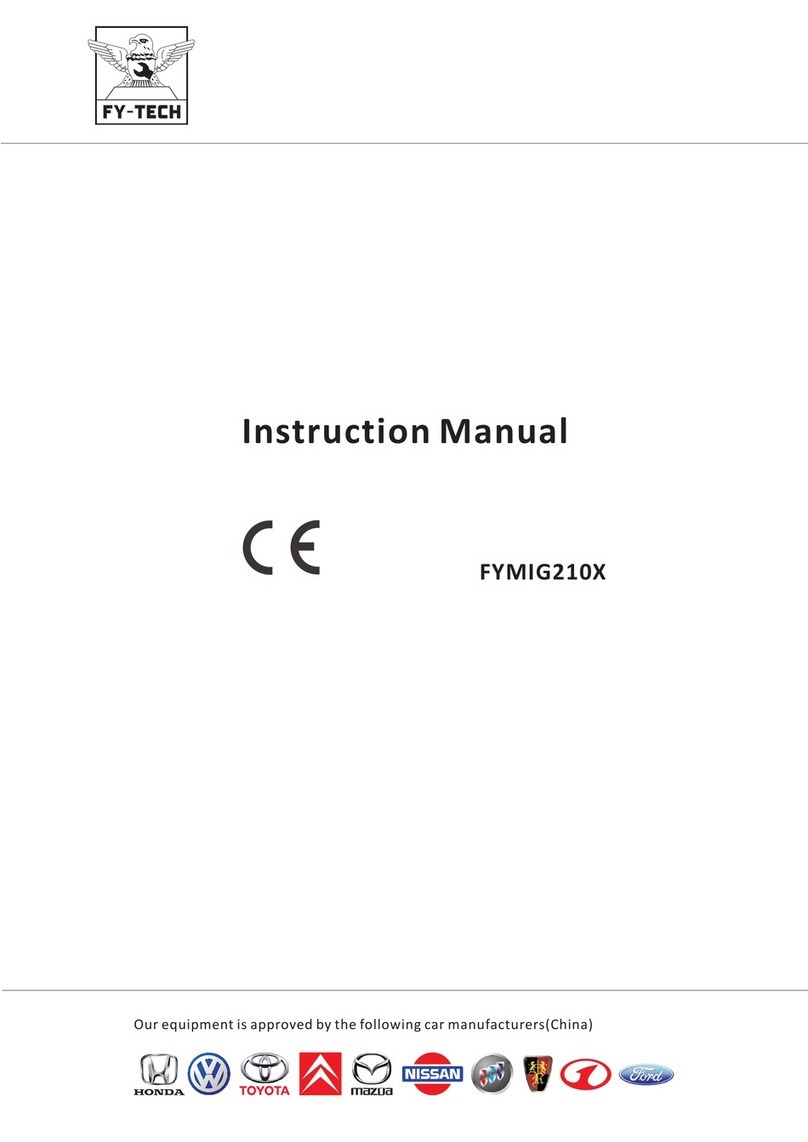
Fytech
Fytech FYMIG210X User manual
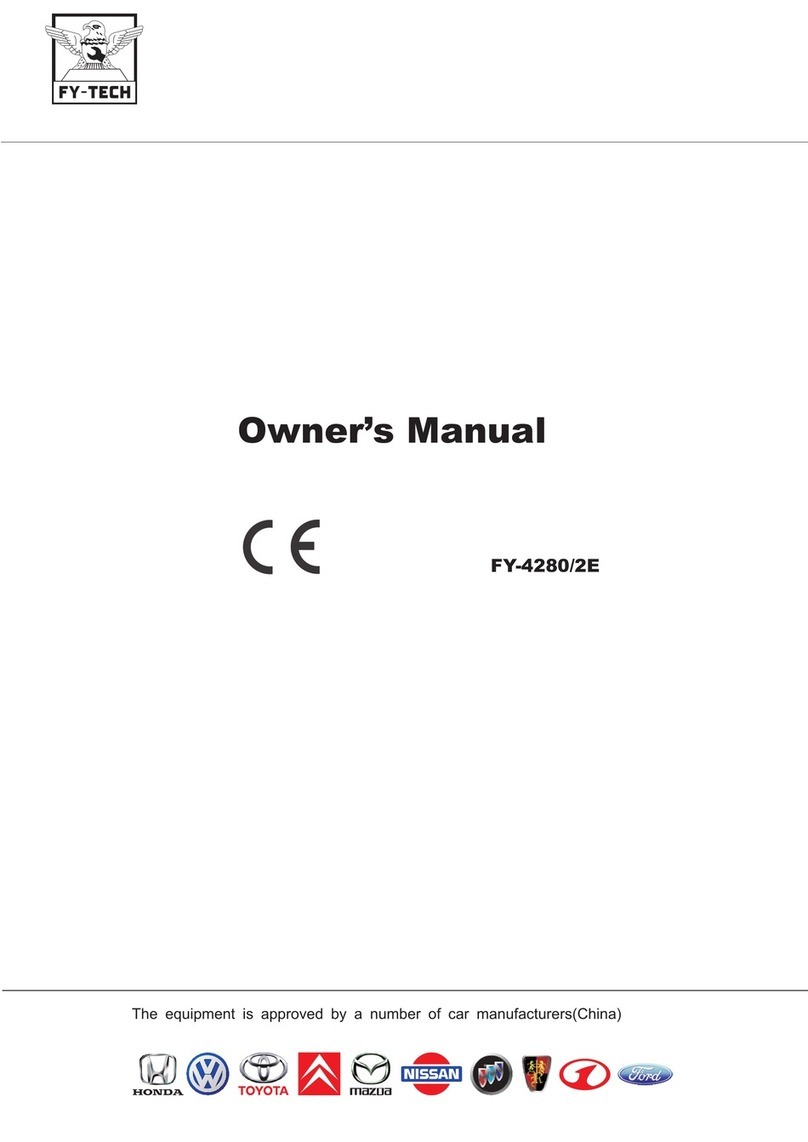
Fytech
Fytech FY-4280/2E User manual
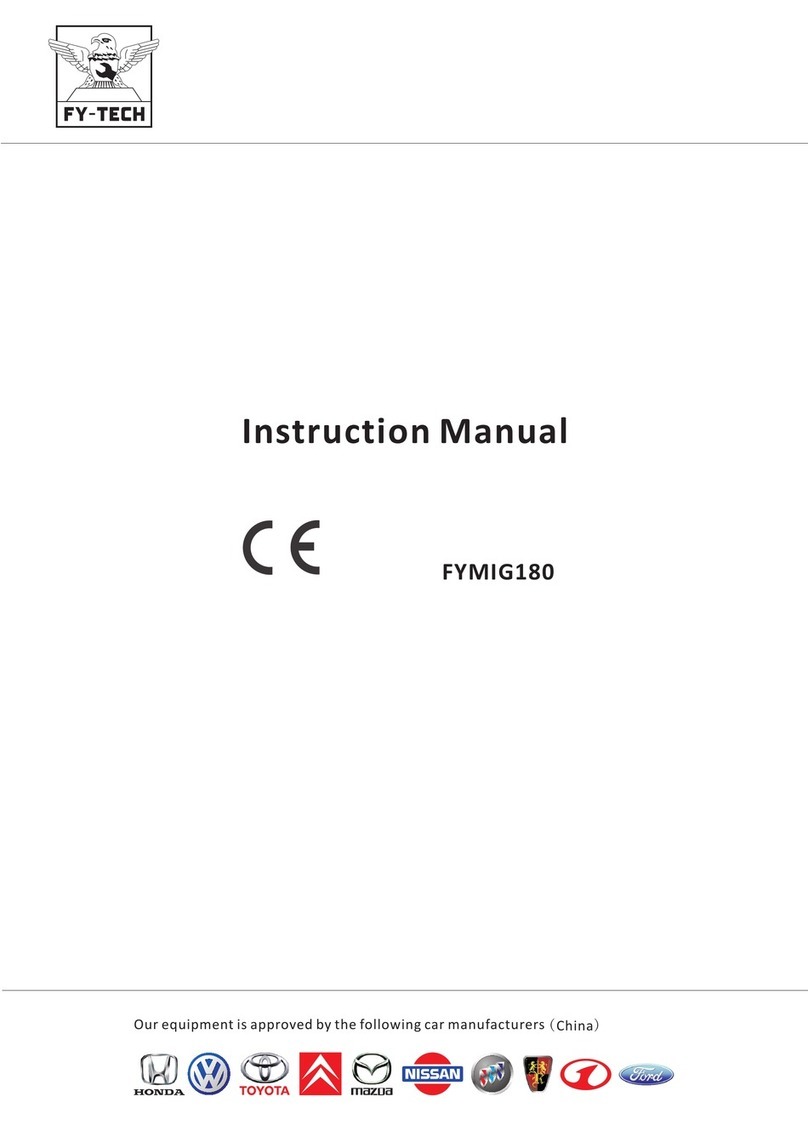
Fytech
Fytech FYMIG180 User manual

Fytech
Fytech FYMIG306L User manual
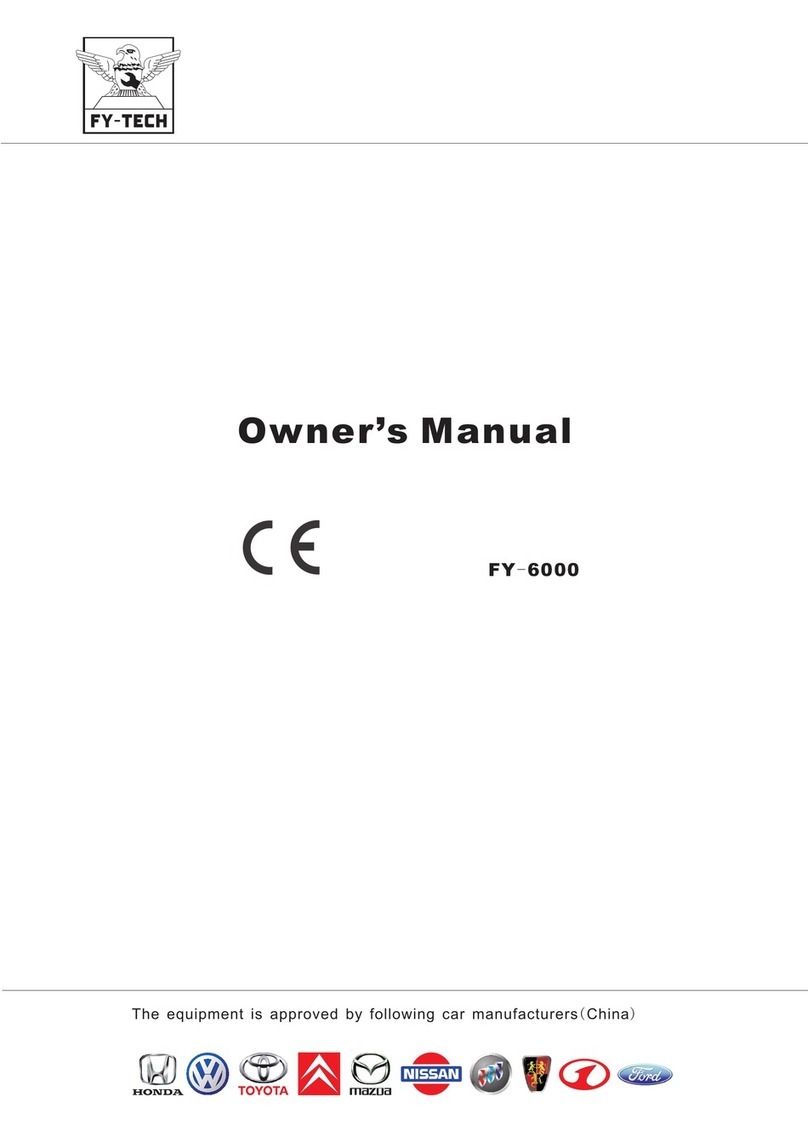
Fytech
Fytech FY-6000 User manual
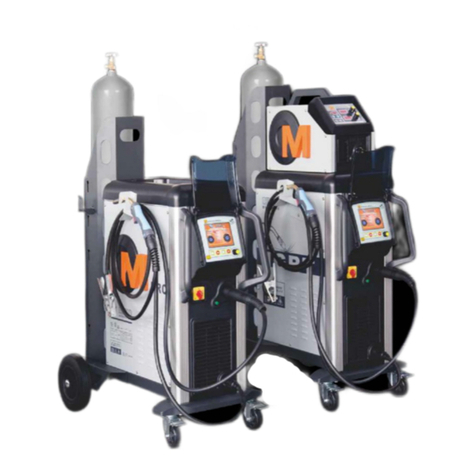
Fytech
Fytech FYMIG307 User manual
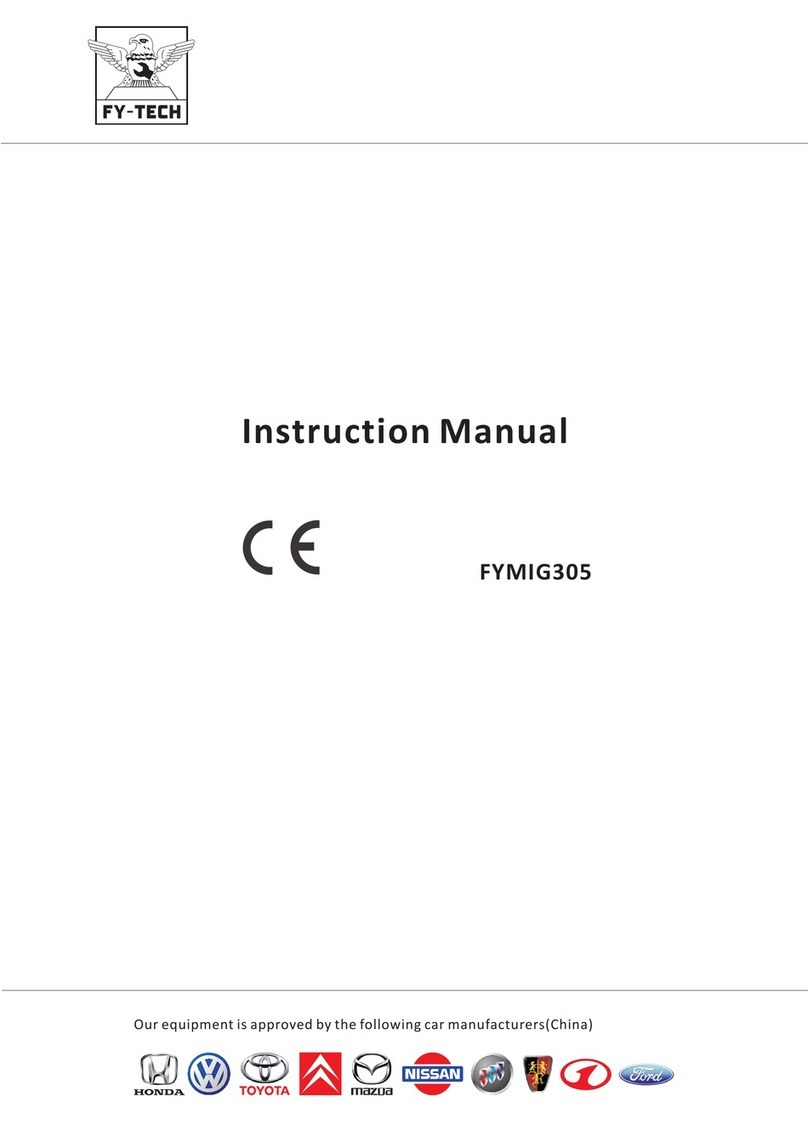
Fytech
Fytech FYMIG305 User manual
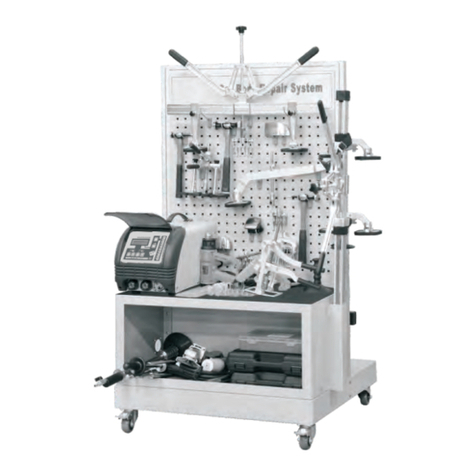
Fytech
Fytech FY-9028 User manual
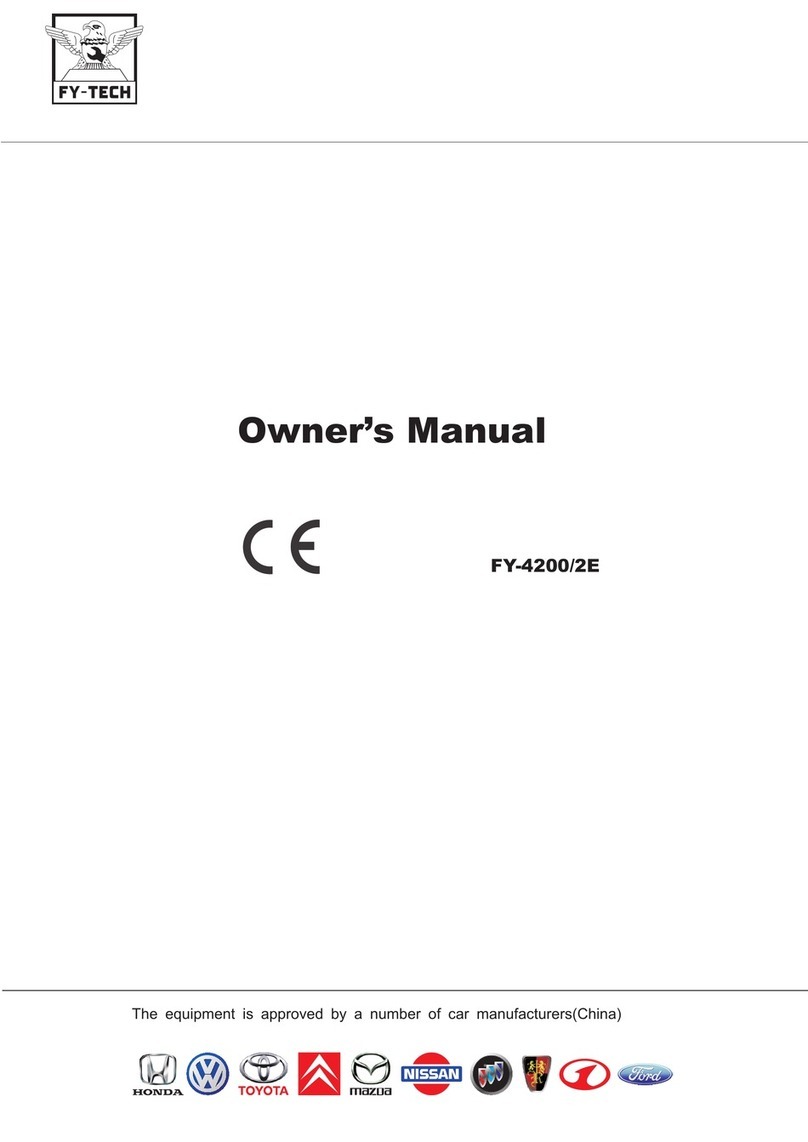
Fytech
Fytech FY-4200/2E User manual
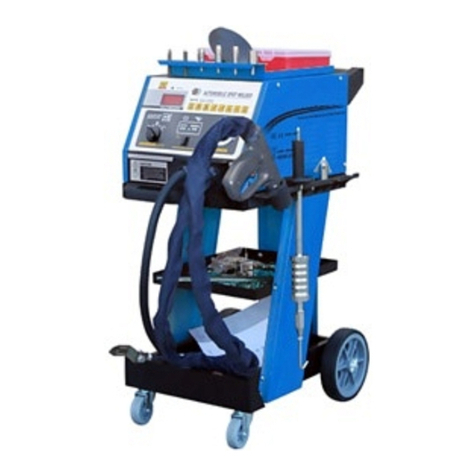
Fytech
Fytech FY-4500 User manual