HP 333A User manual

TM 11-6625-1576-15
WARNING
DANGEROUS VOLTAGES
EXIST IN THIS EQUIPMENT
Be careful when working on the power supply and
on the 115-volt ac line connections.
DO NOT TAKE CHANCES
!

This manual contains copyrighted material originally
prcpared by the Hewlett-Packard Co.
TM11-6625-1576-15
TECHNICAL MANUAL
)
HEADQUARTERS
)DEPARTMENT OF THE ARMY
NO. 11-6625-1576-5 )Washington, D.C., 19May1967
Organizational, DS, GS, and Depot Maintenance
DISTORTION ANALYZER, HEWLETT-PACKARD MODELS 333A AND 334A
SectionPage
IGENERAL INFORMATION . . . . . . . . . 1-2.1
1-A.1 Scope . . . . . . . . . . . . . . . . .1-2.1
l-A.2 Index of Publications. . . 1-2.1
l-A.3 Forms and Records . . . . . . . . . . .1-2.1
l-1. Description . . . . . . . .1-3
1-6. Accessory Features . . . . . . . .1-3
1-8. Options Available . . . . . . . . .1-3
1-11. Modifications
. . . . . . . . . . . . . . . . . . . . . . . . 1-3
Section Page
II
INSTALLATION . . . . . . . . . . . . . .2-1
2-1. Introduction . . . . . . . . . . . . . .2-1
2-3. Inspection . . . . . . . . . . . . . . 2-1
2-5. Power Requirements . . . . . . . . . . 2-1
2-7. Three-Conductor Power Cable . . . 2-1
2-10. Installation . . . . . . . . . . . . . . 2-1
2-12. Bench Installation . . . . . . . . . 2-1
2-14. Rack Installation . . . . . . . . . . 2-1
2-16. Repackaging for Shipment . . . . . . 2-1
Section Page
III
OPERATING INSTRUCTIONS . . . . . . . 3-1
3-1. Introduction . . . . . . . . . . . . . 3-1
3-4. Controls and Indicators . . . . . . . 3-1
3-6. Adjustment of Mechanical Zero . . . 3-1
3-8. General Operating Information . . . 3-1
3-9. Input Connections . . . . . . . . . 3-1
3-11. Voltmeter Characteristics . . . . . 3-1
3-14. Use of Output Terminals . . . . . . 3-1
3-16. Operating Procedures . . . . . . . . 3-2
3-18. Distortion Measurement . . . . . . 3-2
Section Page
IV
THEORY OF OPERATION . . . . . . . . . . 4-1
4-1. Overall Description . . . . . . . . 4-1
4-3. Block Diagram Description . . . . . 4-1
4-4. Distortion Measuring Operation . . 4-1
4-6. Distortion Measurement in AM
.
Carriers . . . . . . . . . . . . . 4-1
4-8. Voltmeter Operation . . . . . . . . 4-1
4-10. Schematic Theory . . . . . . . . . . 4-1
4-11. Impedance Converter Circuit . . . 4-1
4-14. Rejection Amplifier Circuit . . . . 4-2
4-36. High Pass Filter . . . . . . . . . . . 4-5
4-38. Meter Circuit . . . . . . . . . . . . 4-5
4-46. Power Supply Circuit . . . . . . . . . . 4-7
4-51. RF Detector Circuit (334A only) . l 4-7
Section Page
VMAINTENANCE. . . . . . . . . . . . . 5-1
5-l. Introduction. . . . . . . . . . . 5-1
5-2. Test Equipment Required . . . . . 5-1
5-5. Performance Checks. . . . . . . . . 5-1
Section V (Cont ‘d)
5-9. Fundamental Rejection Check . .
5-10. Second Harmonic Accuracy Check
5-11. Distortion Introduced by Instru-
ment Check and Automatic
Control Loop Operation . . . .
5-12. Frequency Calibration Accuracy
Check . . . . . . . . . . . .
5-13. Input Resistance Check . . . . . .
5-14. Input Shunt Capacitance Check . .
5-15. Minimum Input Level Check . . .
5-16. DC Isolation Check . . . . . . . .
5-17. Voltmeter Accuracy Check . . . .
5-18. High Pass Filter Check . . . . . .
5-19. Voltmeter Frequency Response
Check . . . . . . . . . . . . . . . .
5-20. Residual Noise Check . . . . . . .
5-21. AM Detector Check (Model 334A
only) . . . . . . . . . . . . . . .
5-22. Adjustment and Calibration
Procedure. . . . . . . . . . . . . . .
5-25. Meter Mechanical Zero Set . . . .
5-27. Power Supply and Bias
Adjustments. . . . . . . . . . .
5-28. A3R16 and A3R30 Distortion
Adjust. . . . . . . . . . . . . .
5-29. Bridge Balance Adjustment (C3) .
5-30. Voltmeter Gain Adjustments . . .
5-31. Voltmeter Frequency Response
Adjustment . . . . . . . . . . .
5-32. Sensitivity Switch Calibration . . .
5-33. Troubleshooting Procedures . . . .
5-39. Bottom Shield Removal . . . . . .
5-41. Servicing Etched Circuit Boards .
5-44.
Servicing Rotary Switches . . . .
Page
5-1
5-2
5-2
5-3
5-4
5-4
5-4
5-4
5-5
5-5
5-6
5-6
5-6
5-7
5-7
5-7
5-9
5-9
5-10
5-10
5-10
5-11
5-11
5-11
5-13
Section
VI
SCHEMATIC DIAGRAMS
6-1. Schematic Diagrams
Page
6-1
6-1
iii


TM 11-6625-1576-15
Section I Model 333A/334A
Table 1-1
Table 1-1. Specifications (Cont ‘d)
1-2

TM 11-6625-1576-15
SECTION I
GENERAL INFORMATION
1-A.1 Scope
This manual includes installation and operation instructions and
covers operator’s, organizational, direct support (DS), general support
(GS), and depot maintenance. It describes Hewlett-Packard (Federal support
Code 80537) Distortion Analyzer Models 333A and 334A (fig. l-l). A
basic issue items list for this equipmnent is not included as part of
this manual.
1-A.2 Index of Publications
Refer to the latest issue of DA Pam 310-4 to determine whether there
are new editions, changes, or additional publications pertaining to the
equipment. DA Pam 310-4 is an index of current technical manuals,
technical bulletins, supply manuals (types 7, 8, and 9), supply bulletins,
lubrication orders, and modification work orders that are available through
publications supply channels. The index lists the individual parts (-10,
-20, - 35P, etc) and the latest changes to and revisions of each equipment
publication.
l-A.3 Forms and Records
a. Reports of Maintenance and UnsatisfactoryEquipment. Use equip-
ment forms and records in accordance with instructions in TM 38-750.
b. Report of Damaged or Improper Shipment. Fill out and forward
DD Form 6 (Report of Damaged or Improper Shipment) as prescribed in
AR 700-58 (Army), NAVSANDA Publication 378 (Navy), and AFR ‘71-4
air Force).
c. Reporting of Equipment Manual Improvements. Report of errors,
omissions, and recommendations for improving this manual by the
individual user is encouraged.Reports should be submitted on DA Form
2028 (Recommended Changes to DA Publications) and forwarded direct
to Commanding General, U. S. Army Electronics Command,
ATTN: AMSEL-MR-NMP-AD, Fort Monmouth, New Jersey 07703.
1-2.1


TM 11-6625-1576-15
Model 333A/334A
Section I
Paragraphs l-l to l-13
1-1. DESCRIPTION.
1-2. The Hewlett-Packard Models
Distortion Analyzers are solid state 333A and 334A
instruments for
measuring distortion and ac voltages. The Models
333A and 334A include two control loops that auto-
matically tune both legs of a bridge circuit which re -
jects the fundamental when the rejection circuit is
initially set within the range of the loops. A high im -
pedance detector which operates from 500 Kc to greater
than 65 Mc provides the capability” of monitoring the
distortion of the amplitude modulation on an rf carrier.
1-3. Distortion levels of O. 1% to 1OO% full scale are
measured in seven ranges for any fundamental fre -
quency of 5 cps to 600 Kc.
Harmonics are indicated up
to 3Mc. The high sensitivity of these instruments re-
quires only O. 3 v rms for the 100% set level reference.
The distortion characteristics can be monitored at the
OUTPUT connectors with an oscilloscope, a true rms
voltmeter, or a wave analyzer. The instruments are
capable of an isolation voltage of 400 volts above chassis
ground.
1-4. The voltmeter can be used separately for general
purpose voltage and gain measurements. It has a fre -
quency range of 5 cps to 3 Mc (20 cps to 500 Kc for 300
pv range) and a voltage range of 300 pv to 300 v rms
full scale.
1-5. The AM detector included in the Model 334A is
a broadband dc restoring peak detector consisting of a
semiconductor diode and filter circuit. AM distortion
levels as low as O. 3% can be measured on a 3 v to 8 v
rms carrier modulated 30% in the standard broadcast
band, and lower than 1% distortion can be measured
at the same level of the carrier up to 65 Mc.
1-6. ACCESSORY FEATURES.
1-7. The accessory available with the 333A and 334A
Distortion Analyzers is a voltage divider probe, -hp-
Model No. 1000lA. The features of the probe are:
a. 10 megohms shunted by 10 pf, giving 10:1
attenuation.
b. DC to 30 Mc bandwidth.
c. 2% division accuracy.
d. 600 v peak input.
e. 5 ns rise-time.
1-8. OPTION.
1-9. Option 0l is a standard -hp- Model 333A or 334A
with a special meter and meter amplifier, compen-
sated to permit response to VU (volume units)
characteristics.
1-11. Modifications
1-12, Specification C10-334A is a standard
334A Distortion Analyzer modified by placing
the INPUT and OUTPUT terminals on the rear
panel of the instrument. The rear terminals
are binding post connectors and are in
parallel with the front panel terminals.
Due to the rear terminal leads, the shunt
capacitance of the instrument is increased
by 20pF .
1-3


TM 11-6625-1576-15
Model333A/334A Section II
Paragraphs 2-1 to 2-19
2-1. INTRODUCTION.
SECTION II
INSTALLATION
2-2. This section contains information and instruc-
tions necessary for the installation and shipping of the
Models 333A/334A Distortion Analyzers. Included
are initial inspection procedures, power and grounding
requirements,installation information, and instruc -
tions for repackaging for shipment.
2-3. INSPECTION.
2-4. This instrument was carefully inspected both
mechanically and electrically before shipment. It
should be physically free of mars or scratches and in
perfect electrical order upon receipt. To confirm
this, the instrument should be inspected for physical
damage in transit. Also check for supplied accessories,
and test the electrical performance of the instrument
using the procedure outlined in Paragraph 5-5.
2-5. POWER REQUIREMENTS.
2-6. The Model 333A/334A can be operated from any
ac source of 115 or 230 volts (+10%), at 50- 1000 cps.
With the instrument disconnected from the ac power
source, move the slide (located on the rear panel) un-
til the desired line voltage appears. The instrument
can be battery operated by connecting two 28-50 V
batteries (rated 80 milliamperes) to the battery ter-
minal on the rear panel. Power dissipation is 10 watts
maximum.
2-7. THREE-CONDUCTOR POWER CABLE.
2-8. To protect operating personnel, the National
Electrical Manufacturers’ Association (NEMA) recom-
mends that the instrument panel and cabinet be grounded.
All Hewlett-Packard instruments are equipped with a
three -conductor power cable, which when plugged in-
to an appropriate receptacle, grounds the instrument
The offset pin on the power cable three-prong connec-
tor is the ground wire.
2-9. To preserve the protection feature when operat-
ing the instrument from a two-contact outlet, use a
three-prong to two-prong adapter and connect the
green pigtail on the adapter to ground.
2-10. INSTALLATION.
2-11 The Model 333A/334A is fully transistorized;
therefore, no special cooling is required. However,
the instrument should not be operated where the am-
bient temperature exceeds 55 C (191 F).
2-12. BENCH INSTALLATION.
2-1% The Model 333A/34A is shipped with plastic
feet and tilt stand in place, ready for use as a bench
instrument.
2-14. RACK INSTALLATION.
2-15. The Model 333A/334A may be rack mounted by
using the 5“ RackMount Kit (-hp- Part No. 5060-0775).
Instructions for the conversion are included with the
kit. The rack mount for the Model 333A/334A is an
ELA standard width of 19 inches. when mounted in a
rack using the rack mount kit, additional support at
the rear of the instrument should be provided if vibra
tion or similar stress is likely.
2-16. REPACKAGING FOR SHIPMENT.
2-17. The following paragraphs contain a general guide
for repackaging of the instrument for shipment. Refer
to Paragraph 2-18 if the original container is to be
used; 2-19 if it is not.
2-18. If original container is to be used, proceed as
follows:
a. Place instrument in original container if avail-
able.
b. Ensure that container is well sealed with strong
tape or metal bands.
2-19. If original container is not to be used, proceed
as follows:
a. Wrap instrument in heavy paper or plastic be-
fore placing in an inner container.
b. Place packing material around all sides of in-
strument and protect panel face with cardboard strips.
c. Place instrument and inner container in a heavy
carton or wooden box and seal with strong tape or
metal bands.
d. Mark shipping container with “DELICATE
INSTRUMENT," "“RAGILE,” etc.
2-1

TM 11-6625-1576-15
Model 333A/334A
Section III
Paragraphs-3-l to 3-15
SECTION III
OPERATING INSTRUCTIONS
3-1. INTRODUCTION.
3-2. The Models 333A and 334A Distortion Analyzers
measure total harmonic distortion from 5 cps to 600
Kc. Harmonics up to 3 Mc are included. The sharp
elimination characteristics, >80 db, the low level of
instrument induced distortion, and the meter accuracy
of the 333A and the 334A result in accurate measure-
ment of low level harmonic content in the input signal.
3-3. An RMS voltmeter is inherent in the 333A and
334A, The voltmeter provides a full scale sensitivity
of 300 u volts rms (residual noise <25 u volts). The
voltmeter frequency range is from 5 cps to 3 Mc ex-
cept on the 0. 0003 volt range, which is from 20 cps to
500 Kc.
3-4. CONTROLS AND INDICATORS.
3-5. Figure 3-1 illustrates and describes the function
of all front and rear panel controls, connectors, and
indlcators. The description of each component is
keyed to a drawing included within the figure.
3-6. ADJUSTMENTS OF MECHANICAL ZERO.
3-7. The procedure for adjustment of mechanical
zero is given in Section V, Paragraph 5-25.
3-8. GENERAL OPERATING INFORMATION.
3-9. INPUT CONNECTIONS.
3-10. Signal source can be connected to the 333A and
334A through twisted pair leads or a shielded cable
with banana plug connectors. Keep all test leads as
short as possible to avoid extraneous pickup from
stray ac fields, When measuring low-level signals,
battery operation is recommended to avoid ground
loops.
Another method for avoiding ground loops is
by connecting only one instrument in a test setup
directly to power line ground through a NEMA (three-
prong) connector, Connect all other instruments to
the power source through a three-prong to two-prong
adapter and leave the pigtail disconnected. Both the
333A and 334A have a dc isolation of ±400 vdc from
the external chassis with the shorting bar, (item 16 ,
Figure 3-1), disconnected.
3-11. VOLTMETER CHARACTERISTICS.
9-12. The RMS VOLTS markings on the meter face are
based on the ratio between the average and effective
(rms) values of a pure sine wave. The ratio of aver-
age to effective values in a true sine wave is approxi-
mately O. 9 to 1.When the meter is used to measure
complex waves,the voltage indicated may not be the
rms value of the signal applied. This deviation of
meter indication exists because the ratios of average
to effective values are usually not the same in a com -
plexwave as in a sine wave. The amount of deviation
depends on magnitude and phase relation between
harmonics and fundamental frequency of the signal
applied. Table 3-1 shows the deviation of the meter
indication of a sine wave partly distorted by harmonic..
As indicated in the table, harmonic content of less
than approximately 10% results in very small errors.
Table 3-1
Effect of Harmonics on Voltage Measurements
Input Voltage True Meter
Characteristic
RMS Value
Indication
Fundamental = 100
100 100
Fundamental +10% 100. s
100
2nd harmonic
Fundamental +20%
102
100-102
2nd harmonic
Fundamental +50%
112
100-110
2nd harmonic
Fundamental +10% 100.5 96-104
3rd harmonic
Fundamental +20%
102
94-108
3rd harmonic
Fundamental +50%
112
90-116
3rd harmonic
NOTE
This chart is universal in application
since time errors are inherent in
all average-responding type voltage-
measuring instruments.
3-13. In distortion measurements where the fundamen-
tal frequency is suppressed and the remainder of the
signal is measured, the reading obtained on an average-
responding meter may deviate from the true total rms
value. When residual wave contains many inharmoni-
cally related sinusoids, the maximum error in the dis-
tortion reading is about 11% low for distorilon levels
below 10%.
Measured Maximum Error Total
Distortion In Meter Indication Distortion
2. 5%
+0. 11 X O. 025 =
0.025 +0. 0027 =
0.00027
0.0277 or 2.8%
This example represents the maximum possible error,
and in most cases the error is less. In distortion
measurements, the reading of an average-responding
meter is sufficiently close to the rms value to be
satisfactory under most measurement conditions.
3-14. USE OF OUTPUT TERMINALS.
3-15. The OUTPUT terminals provide a O. 1 v rms
output for full scale meter deflection These ter-
minals can be used to monitor the output signal with
an oscilloscope,a true rms voltmeter, or a wave
analyzer. The combination of the distortion meter
and oscilloscope provides more significant information
3-l

3-18. DISTORTION MEASUREMENT.
TM 11-6625-1576-15
Section III
Paragraphs 3-16 to 3-22
about the device under test than the expression of dis-
tortion magnitude alone. Information obtained from
the oscilloscope pattern is specific and reveals the
nature of the distortion that sometimes occurs at such
low levels that it is difficult to detect in the presence
of hum and noise. The impedance at the OUTPUT
terminals is 2000 ohms, therefore, capacitive loads
greater than 50 pf should ‘be avoided to maintain the
accuracy of meter readings.
3-16. OPERATING PROCEDURES.
3-17. The 333A and 334A Distortion Analyzers can be
operated from an ac power source ( 115/230 volt) or a
dc power source (+28 to +50 and -28 to -50 volt source).
If a dc source is used, check the -25 v output. If
necessary, adjust the power supply according to the
procedures in Paragraph 5-27.
3- 19. DISTORTION MEASUREMENT IN PERCENT,
AUTOMATIC MODE.
a. Position FUNCTION selector to SET LEVEL.
b. Position MODE switch to MANUAL.
c. If fundamental frequency is 1 Kc or greater,
position HIGH PASS FILTER SWITCH to IN.
d. Rotate SENSITIVITY selector to MIN position.
NOTE
The bandwith of the SENSITIVITY se-
lector is reduced in the two extreme
CCW positions (positions used with an
input signal greater than 30 v).
e. Position METER RANGE selector to SET LEVEL
100%).
f. Connect test leads from device under test to
INPUT terminals.
REMOVE SHORTING STRAP BETWEEN
FLOATING GROUND ~ AND CHASSIS
GROUND (+) TERMINALS ON FRONT
PANEL INPUT TERMINALS WHEN
MEASURING DISTORTION BETWEEN
TWO POINTS WHICH ARE BOTH ABOVE
GROUND POTENTIAL.
g. With SENSITIVITY VERNIER control max. CCW,
position SENSITIVITY selector for meter indication
greater than 1/3 full scale.
NOTE
If unable to adjust for full scale deflec-
tion which indicates input signal is be-
low O. 3 volts, use manual mode and
position METER RANGE selector down-
scale. Use this new position as the 100%
SET LEVEL position, thus making the
next range 30%, etc.
h. Adjust SENSITIVITY VENIER control for full
scale deflection.
j. Position FRIQUENCY RANGE selector and
frequency dial to fundamental frequency of input signal.
3-2
Model 333A/334A
k. Position FUNCTION selector to DISTORTION,
m. Adjust METER RANGE selector and frequency
dial vernier control for minimum meter indication.
n. Adjust COARSE and FINE BALANCE controls
for further reduction of meter indication. Meter indi-
cation must be less than 10%of SET LEVEL indication.
p. Position MODE switch to AUTOMATIC.
r. Observe percentage of distortion indicated on
meter. Meter indication is in conjunction with METER
RANGE selector. For example, if meter indicates
.4 and METER RANGE selector is on 1% position,
distortion measured is 0.4%.
3-20.
a.
b.
NOTE
RMS voltage of input signal being ana-
lyzed for distortion can be measured
by positioning FUNCTION selector to
VOLTMETER position.
DISTORTION MEASUREMENT IN PERCENT,
MANUAL MODE.
NOTE
In MANUAL mode the accuracy of dis -
tortion measurements is affected by
frequency stability of the input signal.
An inaccuracy in distortion indications
occure when the frequency drift of the in-
put signal exceeds the bandwidth of the
rejection curve.
Perform steps a through n in Paragraph 3-19.
Repeat steps m and n until no further reduction
in meter- indication can be obtained.
c. Observe percentage of distortion indicated on
meter.
3-21. DISTORTION MEASUREMENT IN DB,
AUTOMATIC MODE .
a. Perform steps a through g of Paragraph 3-19.
b. Adjust SENSITIVITY VERNIER control for 0 db
meter indication.
c. Perform steps j through 3-19.
d. Observe meter indication for distortion in db.
NOTE
Distortion in db is obtained by alge-
braically adding meter indication to
db indicated by METER RANGE se-
lector: for example, If meter indi-
cates -2 and METER RANGE selec-
tor is on -20 db position, distortion
measured is -22 db.
3-22. DISTORTION MEASUREMENT IN DB, MANUAL
MODE .
NOTE
Notes in Paragraphs 3-20 and 3-21
apply.
a. Perform steps a through g of Paragraph 3-19.
b. Adjust SENSITIVITY VERNIER control for O db
meter indication.

Model 333A/334A
c. Perform steps j through n of Paragraph 3-19.
d. Repeat steps m and n until no further reduction
n meter indication can be obtained.
e. Observe meter indication for distortion in db.
3-23. DISTORTION MEASUREMENT OF AM RF
CARRIERS. (334A Only)
a. Set NORM - RF SET selector to RF SET.
OBSERVE MAXIMUM INPUT VOLTAGES
AS INDICATED ON REAR PANEL.
b. Connect Input to RF INPUT on rear panel.
c. Adjust SENSITIVITY VERNIER control for O db
meter indication.
d. Perform steps j through n of Paragraph 3-19.
e. Refer to Paragraph 3-20 for manual measure-
ment in percent.
f. Refer to Paragraph 3-21 and 3-22 for automatic
and manual measurement in db.
-24. VOLTMETER MODE.
NOTE
If DBM measurements are to be made,
the DB markings on the METER RANGE
switch must each be lowered by 10.
That is, the DB marking for the O. 3 v
range becomes-10 DBM, 1 v range be-
comes O DBM, 3 v range becomes +10
DBM etc. If the other DB markings are
used, the DBM readings will be 10 DBM
high.
TM 11-6625-1576-15
Section III
Paragraphs 3-23 to 3-27
3-25. The 333A and 334A perform as general purpose
AC Voltmeters when the FUNCTION selector is set
to VOLTMETER position.
NOTE
With the FUNCTION selector in VOLT-
METER position, the SENSITIVITY se-
lector is disabled.
a, Position METER RANGE selector to a range
exceeding the value of the signal to be measured.
b. Connect signal to INPUT terminals.
c. Select a METER RANGE to give a reading as
close to full scale as possible and observe meter
indication.
3-26. OUTPUT TERMINALS.
3-27. In VOLTMETER or SET LEVEL position ofthe
FUNCTION selector, the 333A/334A can be used as a
low distortion, high gain, wideband preamplifier. A
portion of the meter input (O. 1 v RMS output for full
scale meter deflection) is provided at the OUTPUT
terminal J2. In the DISTORTION position, the distor-
tion is provided for monitoring purposes.
DO NOT EXCEED THE VOLTAGES
LISTED BELOW TO PREVENT BLOWING
FUSE F2:
VOLTMETER.= -1 V RANGE
AND BELOW, AND DISTORTION
ANALYZER, MODE-MAXIMUM
SENSITIVITY.
1. 300 V ABOVE 100 CPS
2. 50 V ABOVE 1 KC
IF LOW FREQUENCIES ARE NOT TO
BE MEASURED, Cl MAY BE REPLACED
WITH A SMALLER CAPACITOR, AND
THE VOLTAGE LIMITS OF F2 MAY BE
RAISED ACCORDINGLY.
3-3

TM 11-6625-1576-15
Model 333A/334A Section IV
paragraphs 4-1 to 4-12
SECTION IV
THEORY OF
4-1. OVERALL DESCRIPTION.
4-2. Models 333A and 334A Distortion Analyzers in-
clude an impedance converter, a rejection amplifier,
a metering circuit, and a power supply, The Model
334A also contains an AM detector. A block diagram
of the instruments is shown in Figure 4-1. The im -
pedance converter provides a low noise input circuit
with a high input impedance independent of source
impedance placed at the INPUT terminals. The re-
jection amplifier rejects the fundamental frequency of
an input signal and passes the remaining frequency
components on to the metering circuit for measuring
distortion. The metering circuit provides visual
indications of distortion and voltage levels on the front
panel meter, M 1. The AM detector (Model 334A only)
detects the modulating signal from the RF carrier and
filters any RF components from the modulating signal
before it is applied to the impedance converter circuit.
4-3. BLOCK DIAGRAM DESCRIPTION.
4-4. DISTORTION MEASURING OPERATION.
4-5. For distortion measurement, the input signal is
applied to the impedance converter, Assembly A2,
through the FUNCTION selector, S1, and the one meg-
ohm attenuator, The one megohm attenuator, a voltage
divider network provides 50 db attenuation in 10 db
steps. The desired level of attenuation is selected by
the SENSITIVITY selector, S2. The impedance con-
verter provides an impedance conversion and unity
gain between the instrument INPUT terminals and the
input of the rejection amplifier. The rejection ampli-
fier consists of a preamplifier, a Wien bridge, and a
bridge amplifier. The SENSITIVITY VERNIER control,
at the input of the preamplifier, provides a set level
signal to obtain a full scale reading on the meter for
any voltage level at the input of the instrument. With
the FUNCTION selector in the SET LEVEL position, a
ground is applied in the Wien bridge circuit to allow
a signal reference level to be set up on the meter.
With the FUNCTION selector in the DISTORTION posi-
tion, the Wien bridge is used as an interstate coupling
network between the preamplifier and bridge amplifier.
The Wien bridge is tuned and balanced to reject the
fundamental frequency of the applied input signal. Two
automatic control loops consisting of two phase detec -
tors, lamp drivers, lamps, and photocells provide fine
tuning and balance in the AUTOMATIC MODE. The
remaining frequency components are applied to the
bridge amplifier and are measured as distortion by
the metering circuit. Negative feedback from the
bridge amplifier to the preamplifier narrows the re-
jection response of the Wien bridge. The output of
the rejection amplifier is applied to the metering cir -
cuit through the post-attenuator. The post-attenuator
is used to limit the input signal level applied to the
metering circuit to 1 mv for full scale deflectlon.
The metering circuit sensitivity is increased to 300
uV for full scale deflection on the 300 pv range. The
metering circuit provides a visual indication of the
OPERATION
distortion level of the input signal. In addition to the
visual indication provided by the meter, the OUTPUT
terminals provide a means of monitoring the distortion
components.
4-6. DISTORTION MEASUREMENT IN AM
CARRIERS.
4-7. The Model 334A Distortion Analyzer contains an
AM detector circuit for measuring envelope distortion
in AM carriers.The input signal is applied to the in-
put of the AM detector circuit where the modulating
signal is recovered from the RF carrier. The signal
is then applied to the impedance converter circuit
through the one megohm attenuator and then through
the same circuits previously described in the distor-
tion measuring mode operation.
4-8. VOLTMETER OPERATION.
4-9. In the voltmeter mode of operation, the input
signal is applied to the impedance converter circuit
through the 1:1 and 1000:1 attenuator. The 1:1 atten-
uation ratio is used in the .0003 to .3 VOLTS position
of the METER RANGE selector S3, and the 1000:1
attenuation ratio is used in the 1 to 300 VOLTS posi-
t ions.
With the FUNCTION selector in the VOLT-
METER position, the output of the impedance converter
bypasses the rejection amplifier and is applied to the
metering circuit through the post-attenuator (METER
RANGE selector).Metering circuit sensitivity is in-
creased from 1 mv for full scale deflection to 300 uv
on the 300 uv range, as it was in the distortion mea-
suring operation.The function of the post-attenuator
and metering circuit is the same for voltmeter opera-
tion as for the distortion measuring operation.
4-10. SCHEMATIC THEORY.
4-11. IMPEDANCE CONVERTER CIRCUIT.
4-12. The input signal to the distortion analyzer is
applied to the impedance converter circuit (refer to
Figure 6-2) through the 1:1 and 1000:1 attenuator
S3R12 in the voltmeter mode of operation and through
the one megohm attenuator S2R1 through S2R6 in the
distortion mode of operation. Capacitive dividers
S2C10 through S2C 10 in the attenuator keep the frequency
response flat. The impedance converter is a low
distortion, high input impedance amplifier circuit
wit h gain independent of the source impedance placed
at the INPUT terminals. Instrument induced distor-
tion of the signal being measured is minimized by
keeping the input impedance and the gain of the imped-
ance converter linear. The input impedance is kept
linear by use of local positive feedback from the source
of A2Ql to the gate of A2Q1 and to the protective diodes
A2CR2 and A2CR3. Thus signals with large source
impedance can be measured accurately. Overall in-
duced distortion is further minimized by a high open
loop gain and 100% negative feedback. The high open
loop gain is achieved by local positive feedback from
4-1

TM11-6625-1576-15
Section IV
Paragraphs 4-13 to 4-25 and Figure 4-2
the emitter of A2Q3 to the collector of A2Q2. Overall
negative feedback from the emitter circuit of A2Q4 to
the source of A2Q1 results in unity gain from the im-
pedance converter.
4-13. The bias points of the transistors in the imped-
ance converter are selected to minimize instrument
induced distortion. A2Q 1, an extremely low noise,
high impedance field effect transistor, is the major
component that makes linearity of the Impedance con-
verter independent of the signal source impedance.
4-14. REJECTION AMPLIFIER CIRCUIT.
4-15. The rejection amplifier circuit (see Figures 6-3
and 6-6) consists of the preamplifier (A3Q1) thru A3Q3),
the Wien bridge resistive leg and auto control loop
(A5Q1 thru A5Q9 with associated lamp and photocell),
the reactive leg and auto control loop (A5Q10 thru
A5Q 18 with associated lamp and photocell), and the
bridge amplifier (A3Q4 thru A3Q6).
4-16. PREAMPLIFIER CIRCUIT.
4-17. The signal from the impedance converter is ap-
plied to the preamplifier, which is used during SET
LEVEL and DISTORTION measuring operations. Neg-
ative feedback from the junction of A3R1O and A3R11 is
applied to the junction of A3R2 and A3C2 to establish
the operating point for A3Q1. Negative feedback from
the emitter of A3Q3 is applied to the emitter of A3Q1
to stabilize the preamplifier. The preamplifier, like
the impedance converter, is designed for high open
loop gain and low closed loop gain to minimize instru-
ment induced distortion.
4-18. WIEN BRIDGE CIRCUIT.
4-19. In the distortion measuring operation the Wien
bridge circuit is used as a rejection filter for the
fundamental frequency of the input signal. With the
FUNCTION selector, S1, in the DISTORTION position,
the Wien bridge is connected as an interstage coupling
network between the preamplifier circuit and the bridge
amplifier circuit. The bridge is tuned to the fundamen-
tal frequency of the input signal by setting the FRE-
QUENCY RANGE selector, S4, for the applicable fre-
quency range, and tuning the capacitors C4A through
C4D. The bridge circuit is balanced by adjusting the
COARSE balance control, R4, and the FINE balance
control, R5.
In the AUTOMATIC MODE fine tuning
and balancing are accomplished by photoelectric cells
which are in the resistive and reactive legs of the
Wien bridge. The error signals for driving the photo-
cells are derived by detecting the bridge output using
the input signal as a reference.
4-20. When the Wien bridge is not tuned exactly to the
frequency to be nulled, a portion of the fundamental
frequency will appear at the bridge output. The phase
of this signal depends on which leg of the bridge is not
tuned, or on the relative errors in tuning if neither is
set correctly. The magnitude of the signal is propor-
tional to the magnitude of the tuning error of either or
both legs of the bridge.
4-2
Model 333A/334A
Figure 4-2. Bridge Waveforms
4-21. Figure 4-2a is a sinusoid input to the Wien bridge.
If the resistive leg of the bridge iS slightly unbalanced,
the output of the bridge is very small, but has the
waveform shown in Figure 4-2b and is in phase with
the input. As the resistive leg is tuned, the signal
approaches zeroamplitude at null and then becomes
larger, but 180° out of phase, if the null position is
passed. When the resistive leg is correctly tuned
and the reactive leg is tuned through null, a similar
waveform is produced, Figure 4-2c. The only differ-
ence is that the reactive signal is 90° out of phase with
the resistive signal.
4-22. When the bridge output is detected using the
input signal as the reference, the error signals in
phase or 180° out of phase with the reference develop
a voltage which is used to vary the resistance in the
resistive leg of the bridge, to tune it to the correct
null position, Signals of the form in Figure 4-2c do
not develop any voltage as the resistive detector is
insensitive to input differing from the reference by 90° .
4-23. In an independent, but similar control loop, the
bridge input signal is shifted 90° and used as the
reference signal for the detector. This detector
develops control voltages to null the reactive leg of
the bridge, but is insensitive to signals of the form
in Figure 4-2b which are caused by small tuning
errors of the resistive branch.
4-24. The result is that the two control loops derive
information from a common source and develop two
independent control signals for nulling the two legs
of the bridge. These control voltages are used to
vary the brilliance of lamps, which in turn causes
resistance changes in photocells which form part of
the Wien bridge.
4-25. Refer to Figure 4-3 for the phase relationship
of the bridge error signal and reference voltage at the
base of A5Q4. The shaded portions of the error sig-
nals (b and c) indicate that part of the error signal
which contributes to the dc lamp control voltage. As
indicated in d, any error signal that is 90° out of
phase with the reference does not affect the dc lamp
control voltage.

TM 11-6625-1576-15
Model 333A/334A Section IV
Paragraphs 4-26 to 4-27 and Figure 4-3
4-26. The operation of the reactive branch control loop
is similar to that of the resistive branch. The phase
delay circuit (Figure 6-6), A5Q15, A5Q16, S4AF and
S4C1 through S4C5, shifts the reference voltage 90º,
as shown in Figure 4-3f. This makes the detector
A5Q12 sensitive to components of the bridge error
signal that are 90° out of phase (g and h). The output
of the lamp driver, Q14, controls the brilliance of
A6DS2, which varies the resistance of A6V2 through
A6V5 to tune the branches of the reactive leg. Deck
AR of the FREQUENCY RANGE switch, S4, switches
A5R56 in parallel with A5R55 on the top three frequency
ranges. A6DS2 will become brighter, and lower the
resistance of A6V2 through A6V5, making variation
in resistance less than on the two lower ranges.
However, less variation in resistance is needed to
tune the leg, because the impedance in the reactive leg
becomes progressively less as the higher frequency
ranges are selected.
4-27. Any error signal that is not an integral multiple
of 90 is the result of the reactive leg of the bridge
being detuned, and the resistive leg being unbalanced.
.
For example, an error signal that is 45º out of phase
(Figure 4-3e and j) will result in outputs from both
detectors to tune the bridge and reject the fundamental.
Figure 4-3. Reference and Error Phase Relationship
4-3

TM 11-6625-1576-15
Section IV
Paragraphs 4-28 to 4-35 and Figures 4-4 to 4-5
Figure 4-4. Wien Bridge Circuit and Rejection Characteristics
4-28. When the bridge circuit is tuned and balanced,
the voltage and phase of the fundamental, which appears
at junction of the series reactive leg (S4R1, 3, 5, 7,
or 9 and C4A/B) and the shunt reactive leg (S4R11,
13, 15, 17, or 19, and C4C/D), is the same as at the
midpoint of the resistive leg (A3R12 and A3R14). When
these two voltages are equal and in phase, the funda-
mental frequency will not appear at the drain of the
field effect transistor A3Q4. For frequencies other
than the fundamental,the reactive leg of the Wien
bridge offers various degrees of attenuation and phase
shift which cause a voltage at the output points of the
bridge. This difference voltage between the reactive
leg and resistive leg is amplified by A3Q4, A3Q5, and
A3Q6.
Figure 4-4 illustrates a typical Wien bridge
circuit and the rejection characteristics for it.
4-29. The Wien bridge circuit is designed to cover a
continuous frequency range of over a decade for each
position of the FREQUENCY RANGE selector, S4. S4
provides course tuning of the reactive leg by changing
the bridge circuit constants in five steps at 1 decade
per step. For the automatic control loop, the reference
voltage is taken from R6 at the input to the rejection
amplifier and applied to the buffer amplifier A5Q7.
The reference voltage is amplified and clipped by A5Q8
and A5Q9 and coupled to the detector A5Q4. The output
of the metering circuit, which contains the fundamental
frequency if either leg of the bridge is untuned, is ap-
plied to the buffer amplifier A5Q1. It is amplified by
A5Q2 and A5Q3 and coupled to the detector A5Q4.
4-30. Refer to Figure 4-5 simplified partial schematic
for detector operation. The discussion is applicable
to both resistive and reactive detector circuits.
4-31. The signals from the error amplifier, (A5Q2
and A5Q3) will be equal and of opposite phase, and will
cancel out each other when the detector, A5Q4 is off.
However,
when the positive half of the reference
square wave gates A5Q4 on, the signal from the col-
lector of A5Q3 will be shorted to ground. Thus the
signal from the collector of A5Q2 will be coupled
through the filter network to the base of AQ5. If the
signal from A5Q2 is in phase with the reference, the
4-4
positive half of the signal will be passed, and if it is
out of phase, the negative half will be passed.
4-32. The normal working voltage at TP3 is between
0 and -1 volt. The dc output of the filter network
causes the voltage at TP3 to go in a positive direction
(toward zero) for in phase error signals, and in a
negative direction (toward-1 v) for out of phase error
signals. The change in base voltage is then amplified
by A5Q5 and lamp driver A5Q6. This will change the
brilliance of lamp A6DS1, which will vary the resis-
tance of A6V1 in the direction necessary to balance
the resistive leg of the bridge.
Figure 4-5. Auto Control Loop Detector
4-33. When the FUNCTION selector is set to the VOLT-
METER or SET LEVEL position, the junction of the
series and shunt reactive branches of the Wien bridge
is connected to circuit ground through R19 by S1BF
which disables the frequency rejection characteristic
of the bridge circuit. With the bridge circuit disabled,
the rejection amplifier circuit provides one db of gain
for the fundamental frequency and the harmonics. In
the SET LEVEL operation, this signal is used to es-
tablish the SET LEVEL reference.
4-34. BRIDGE AMPLIFIER CIRCUIT.
4-35. The bridge amplifier circuit consists of three
stages of amplification, A3Q4 through A3Q6. The
Other manuals for 333A
3
This manual suits for next models
1
Table of contents
Other HP Measuring Instrument manuals
Popular Measuring Instrument manuals by other brands
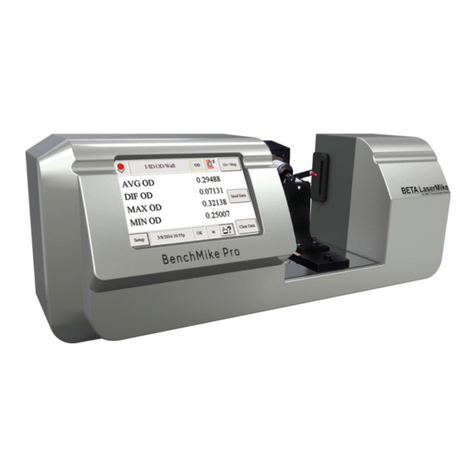
Beta LaserMike
Beta LaserMike BenchMike Pro Addendum
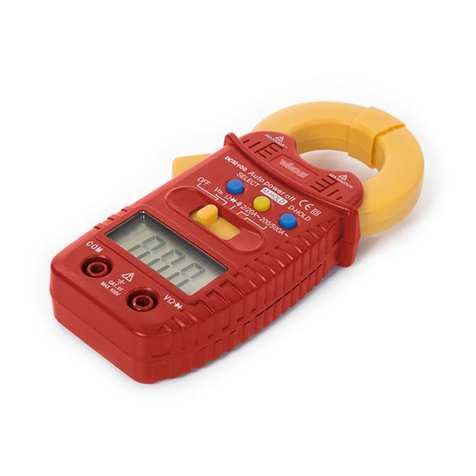
Velleman
Velleman DCM100 user manual
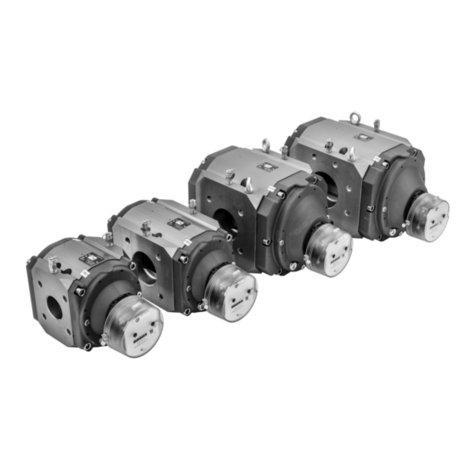
Elster Instromet
Elster Instromet RABO G65 instruction manual

Landis+Gyr
Landis+Gyr Ultracold T550 operating instructions
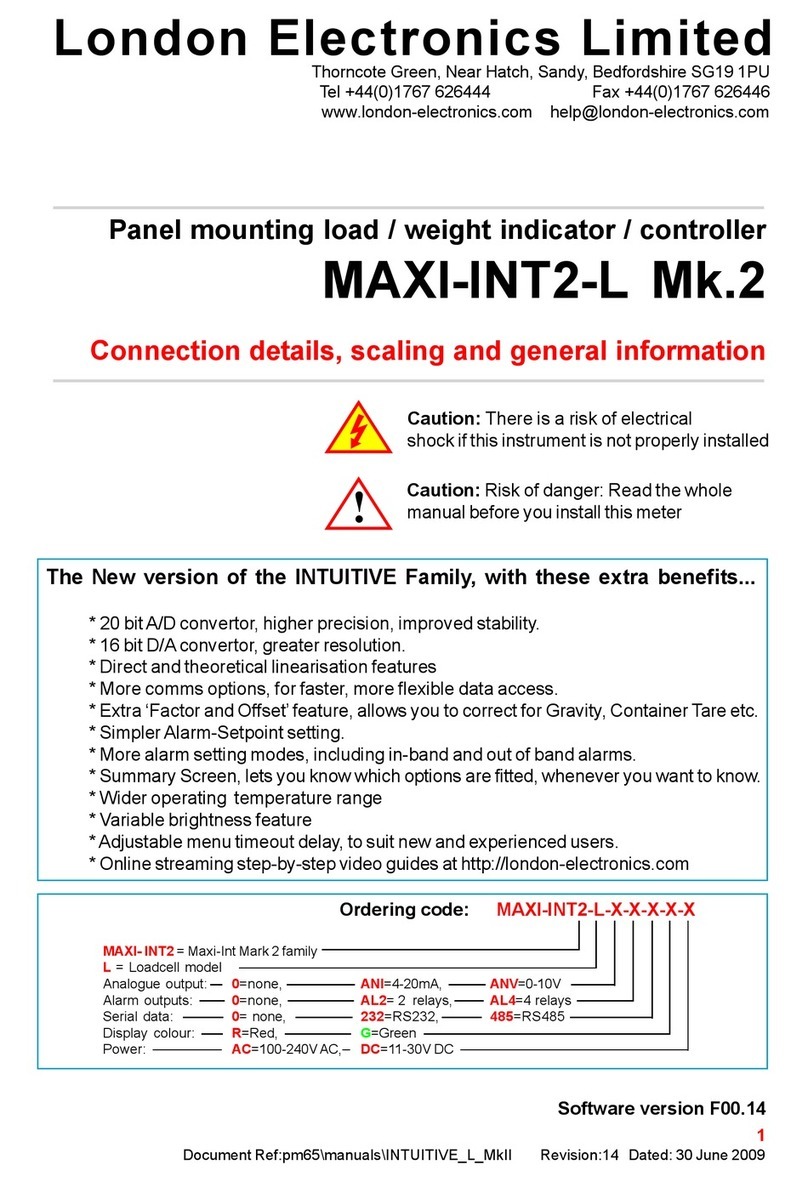
London Electronics
London Electronics MAXI-INT2-L Mk.2 manual
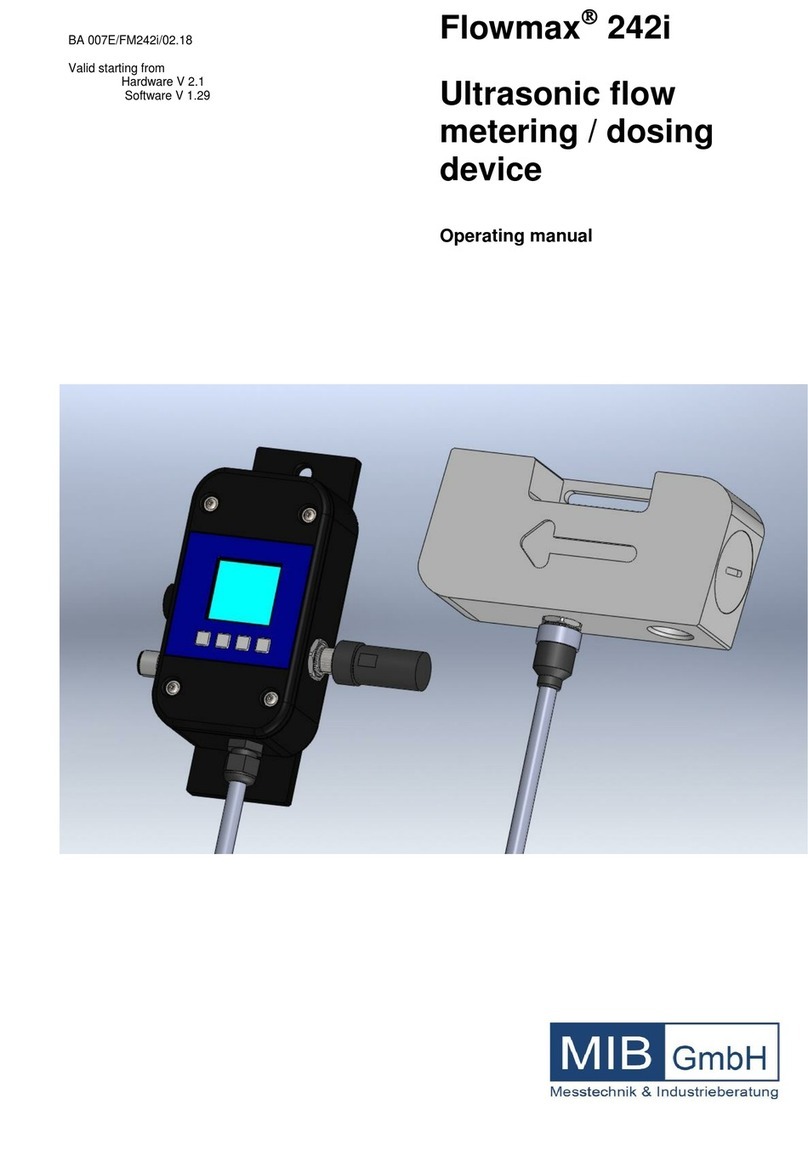
MIB
MIB Flowmax 242i operating manual

BOS
BOS BS-DET2000BT manual
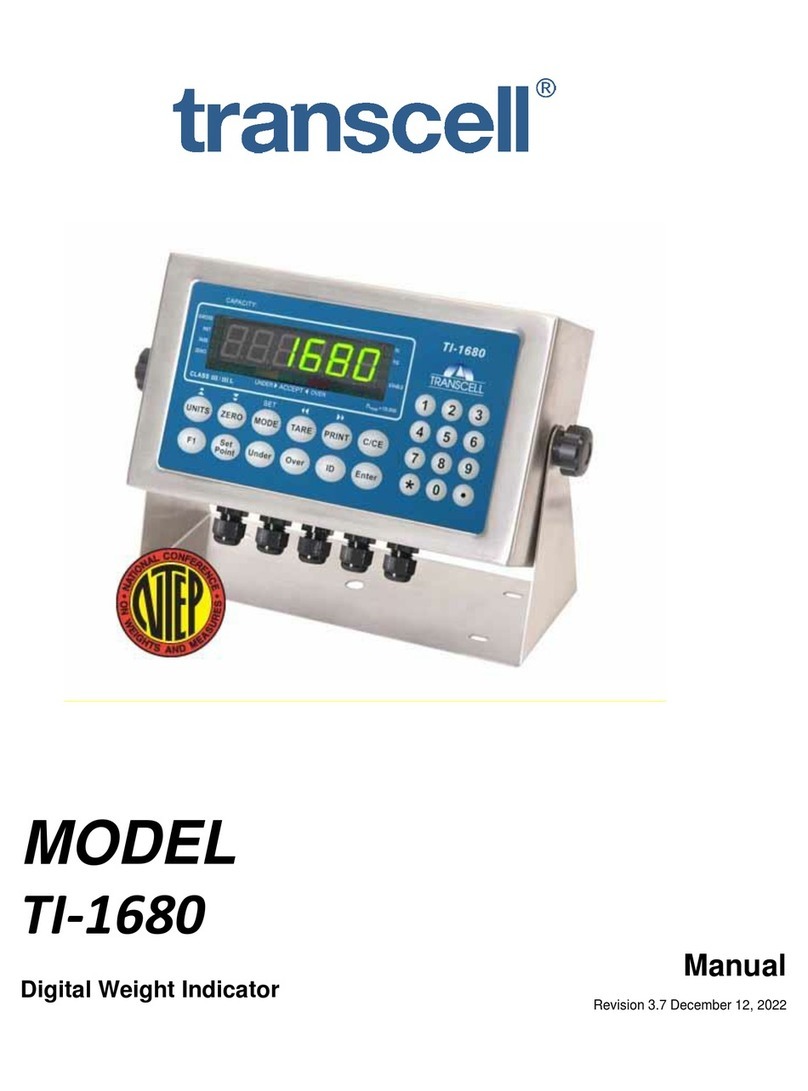
Transcell Technology
Transcell Technology TI-1680 manual
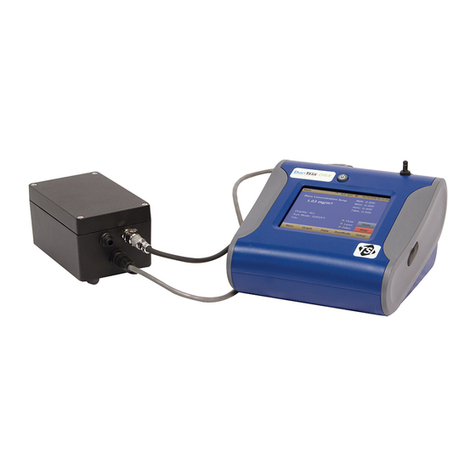
TSI Incorporated
TSI Incorporated DUSTTRAK DRX 8533 Operation and service manual
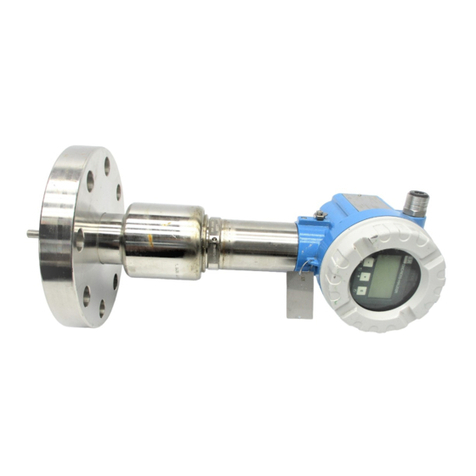
Endress+Hauser
Endress+Hauser Levelflex M FMP45 operating instructions

Topcon
Topcon BM-9A instruction manual
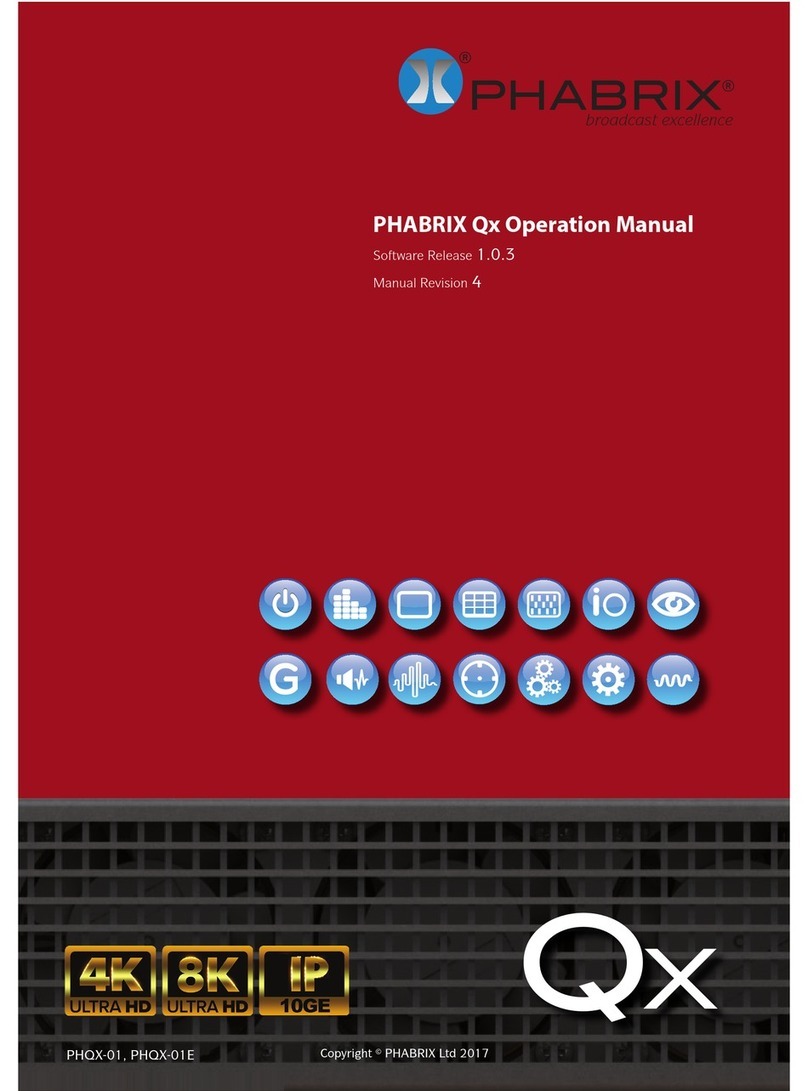
Phabrix
Phabrix PHQX-01E Operation manual