HPC Tiger SHARK User manual

Touch Screen-Controlled
Computerized Code Machine
No. 123TSHARK
091416 36123_100_00
Exploded View
&
Parts List Inside


1
Index
1.1 Introduction
1.2 Accessories Checklist
1.3 Parts Designation
1.4 Preparing to use the Tiger SHARK™
1.5 Touch Screen
2.1 Cutter Wheel Descriptions
2.2 Replacing Cutters
2.3 Changing Cutters
3.1 Loading Key Blanks
3.2 Gauging Methods
3.3 4-Way Jaws
4.1 Cutting by DSD
4.2 Cutting by Code
4.3 Cutting Specialty Keys
5.1 Edit DSD Presets
5.2 DSD Specific Adjustments
5.2.1 Cut Styles
5.3 Custom DSDs
5.4 Machine Adjustments
5.5 Decode a Key
5.6 Special Function
5.7 Security
6.1 Replacement of Deburring Brush
6.2 Replacement of Cutter Belt
6.3 Replacement of Drive Belt
7. Troubleshooting
8. Exploded View and Parts List
9. Warranty, Maintenance, Cleaning, and Repair
4
5
6
7
9
12
12
13
16
16
17
20
21
26
30
32
34
35
39
42
46
47
50
51
56
58
59
60

2
Find out more about the entire line of HPC
Key Machines,
Software,
Key Cabinets,
Lock Picks,
Car Opening Kits,
Locksmithing Tools,
and much more at:
www.hpcworld.com

3
Tiger SHARK™
1.1 Introduction
1.2 Accessories Checklist
1.3 Parts Designations
1.4 Preparing to use the Tiger SHARK™
1.5 Touch Screen
INTRODUCTION & FEATURES

4
Thank you for purchasing the Tiger SHARK™computerized code machine.
We appreciate your business. We are confident your investment in this
machine will pay off in increased productivity and in the ability to better serve
your customers.
The Tiger SHARK™is the culmination of thousands of hours of research and
development. This machine combines a state of the art, computer controlled
code cutting key machine with the most extensive key code database ever
compiled, plus the touch screen user interface. In addition, HPC’s master
keying (MasterKing®) and key management (KeyTrail®) software programs will
download key cutting data to the Tiger SHARK™, providing a comprehensive
computerized solution to key control. Please complete and return the enclosed
registration card. It is imperative to register your machine with HPC.
As a registered owner of the Tiger SHARK™, you will receive notices of updates
and upgrades to the machine, as well as access to our technical support.
If you have any questions about your Tiger SHARK™, please contact our
Customer Service Department at:
TM
This manual and the internal software and data of theTiger SHARK™described in this manual are
copyrighted by: HPC, a Hudson Lock Company, Hudson, MA 01749 USA
The internal software and data is a work fully protected by the United States Copyright Laws.
Federal Law: This manual or the internal software of the Tiger SHARK™may not be copied,
translated, photocopied, microfilmed, or reproduced in any form (in whole or in part), without the
express written consent of the copyright holder.
HPC, a Hudson Lock Company
Hudson, MA, USA
© Copyright 2015
1.1 Introduction

5
1.2 Accessories Checklist
HPC Cutter Wheel HPC Cutter Wheel HPC Cutter Wheel
(CW-14MC) (CW-1011) (CW-20FM)
HPC Cutter Wheel HPC Cutter Wheel HPC Cutter Wheel
)2101-WC()CM09-WC()CM74-WC(
Decoder Plate
No. SHARK-18
Stylus
No. SHARK-14
Bolt Down Brackets (set of 4)
No. SHARK-25
Calibration Disc
No. CMB-CKDISC
Manual
Calibration Key
No. SHARK-21
3/32” Allen Wrench
No. WRENCH-4
Restore & Update Card
(installed in rear slot)
No. SHARK-xx-MMC
Cutter Nut Wrench
No. WRENCH-7
Serial Cable
No. CABLE-25S
Cutter Nut
No. CM-1039A
Tiger SHARK™
Manual
Softie™ Brush Wrench
No. WRENCH-8
Auto-Calibration Card
No. SHARK-32
(installed)

6
1.3 Parts Designation
Touch Screen
Shaft-Lock Button
Shoulder Gauge Handle
Quick Nut
Cutter
Wing Nut
Tip Gauge
Top Jaw
Bottom Jaw
Stylus
Stylus Holder
Platform
Deburring Brush
Tip Gauge Handle
Shoulder Gauge
Touch Screen Angle
Adjustment Knob
Decoder Plate SD Card
Serial Port
FUSE
Fuse

7
Auto-Calibrate
1. Place the Calibration Key in Jaw A and align with the shoulder gauge (Fig. 1). After
aligning the Calibration Key, lower the shoulder gauge to the rest position. And press
“Continue”.
The carriage will slowly move in toward the Calibration Disk. The disk will make contact
at a number of points on the Calibration Key. This phase of the program takes about 60
seconds. When this phase is completed the Tiger SHARK™ will stop and beep 3 times
while changing screens.
2. The screen will read “*Set tool for tip adjustment*”. Remove the Calibration Key, turn
it around, and gauge it with the tip gauge (Fig. 2). Press the “DO TIP” button. The
machine will continue to self-calibrate by repeating the touch off routines it did for the
shoulder gauge. This phase will take about 30 seconds. After it finishes the machine will
beep 4 times to tell you it has completed the self-calibration. When prompted, click
“Confirm”. The screen will change to the main Auto-Calibrate menu.
3. Remove the Calibration Key and Calibration Disk. Install the No. CW-14MC cutter
and a standard shoulder gauge key blank (eg. Schlage SC1). On the menu, click DSD,
then type in “Schlage” or DSD number 60. Follow the instructions on screen, and cut
5-depths in all positions. If a Schlage key blank is not available, select another standard
shoulder gauge key blank, and use the appropriate DSD number and cutter.
4. Use a key micrometer (such as the HPC Ultimate Micrometer, No. SKM-2D) to
measure the depths of each cut. Compare the depths obtained to the depths listed in
HPC’s CodeSource® program, or other reliable source. All cuts should be within
.002-inch (.05mm) of the manufacturer’s specification (.260-inch for a Schlage 5-depth).
In most cases no further adjustments will be needed. If the cuts are not within the
.002-inch tolerance, then run the Auto Calibration again and cut 5-depths on a new key
blank.
Fig. 1
Fig. 2
1.4 Preparing To Use The Tiger SHARK™
Power Requirements: 120 VAC, 60 hz, 4 amps OR 240 VAC, 50hz, 4 amps
Before using the Tiger SHARK™key machine, read this manual in order to gain a thorough understanding of all of its
capabilities. You will receive peak performance and efficiency from your machine by fully comprehending all of its functions.
Make sure that the power outlet that the Tiger SHARK™will attach to is properly wired, i.e., grounded with correct hot and
neutral leads. If the outlet is not wired properly or power from the available outlet is not regular (i.e., you experience frequent
power brownouts), it may cause the Tiger SHARK™to malfunction. While the Tiger SHARK™contains an internal surge
protector, it is recommended that you use a surge/brownout protector when operating the Tiger SHARK™.

8
MINUS (-) ARROW
.001" / .01mm.
PLUS (+) ARROW
.001" / .01mm.
If, after the 2nd calibration, the machine is still off by more than .002-inch (or you
need even tighter tolerances), then use the Machine Adjustments function to make
small adjustments in the depths. Click on “TOOLS”, then “Machine Adjustments”.
Refer to section 5.4 for complete instructions.
The Tiger SHARK™is supplied with Bolt Down Brackets. If you
prefer to bolt down the machine to your work bench or counter,
simply align the brackets to screw locations located on the side
panels of the machine. Remove side panel screws, place
slotted side of bracket against panel and thread screws in to
place but do not tighten. Make sure bracket is flush with surface
of counter. Tighten brackets down using your own bolts
(suitable for the type and thickness of your workbench). Next,
tighten screws on bracket sides to secure machine to bench.
5. After the Auto Calibration process has been completed, the Operating
Program must be installed using the Update Card that is installed in the
machine.
A. Click “TOOLS”
B. Click “SPECIAL FUNCTION”.
C. Click “UPDATE FROM MMC CARD”, then “CONFIRM”.
The screen will turn white for about 10 minutes, then turn black for about
3 minutes. Do not switch off the machine during this procedure.
When the machine beeps and the main screen is restored, the Tiger
SHARK™ is ready for use.
Auto-Calibrate
Tools
Auto-Calibrate
CALIBRATE
Securing The Tiger SHARK™To Your Work Bench

9
1.5 Touch Screen
The Tiger SHARK™is equipped with a state of the art touch-sensitive display screen. Use the stylus provided in
much the same way as you would use a mouse to navigate and select objects on your PC. You can also use
your fingertip. However, it is recommended to use the stylus for the greatest accuracy and to keep the screen
cleaner.
The machine is programmed to dim the screen after approximately 10 minutes of non-use. Simply tap or touch the
screen to reactivate it. This auto-dimming feature cannot be modified.
To clean the screen use a commercial glass cleaner sprayed on a soft cloth. Do not spray the touch screen
directly.
Avoid prolonged exposure to direct sun light. Excessive exposure to direct sunlight can cause the screen to go
dark. This is a normal occurrence with LCD screens, and is not permanent.
The screen has been calibrated during production of the machine. However, if you notice that the accuracy of
your stylus taps have diminished (you do not get the results expected from a particular key), this indicates the
screen requires re-calibration to align the image on the screen with the touch-sensitive coating. Please refer to the
Tools section 5.6 for instructions.
WORK AREA: It is important to maintain a clean work surface, free from key dust debris and dirt.
A hand vacuum or small brush is recommended.

10

11
Tiger SHARK™
2.1 Cutter Wheel Descriptions
2.2 Replacing Cutter Wheels
2.3 Changing Cutter Wheels
CUTTER WHEELS

12
The Tiger SHARK™is supplied with 6 standard cutter wheels.
CW-1011: used for cabinet, padlock, and most vehicle applications
CW-14MC : used for most standard cylinder keys
CW-90MC: similar to the CW-14MC, but makes cuts with a steeper slope for special applications
CW-20FM: 76 degree cutter used for Sargent keys
CW-47MC: 87 degree cutter used for certain automotive keys
CW-1012: for Medeco® keys
Flat Steel cutters, the Emhart cutter (CW-1013), the ASSA Cutter (CW-32MC), as well as others,
are optional cutter wheels that are available for use with the Tiger SHARK™.
Refer to the HPC website, www.hpcworld.com for a complete list of cutters and applications.
2.2 Replacing Cutter Wheels
Cutter wheels eventually wear out and become dull. The life expectancy of a cutter wheel
is dependent on the quantity and types of keys you are cutting and the composition of your key
blanks.
HPC does not recommend sharpening cutter wheels. Each time a cutter is sharpened, a
small amount of material is removed and the diameter is slightly reduced. This reduction in diam-
eter will result in cuts shallower then the manufacturer’s specifications.
2.1 Cutter Wheel Descriptions

13
2.3 Changing Cutter Wheels
The Tiger SHARK™is equipped with the HPC Quick Nut; tools are not required to change
cutters. The following procedure is recommended when changing cutter wheels:
1. Turn the Tiger SHARK™off. Hold the cutter head assembly and press down the shaft-lock button.
2. Turn the Quick Nut clockwise (toward the front of the machine) and remove it.
NOTE: The locknut is reverse thread.
3. Remove the cutter. Slide the new cutter onto the shaft. IMPORTANT NOTE: Be sure
the cutter is installed for a clockwise rotation, with the arrow facing the outside, so it
can be seen.
4. Reinstall the Quick Nut, turning counterclockwise (toward the rear of the machine)
onto the cutter shaft.
5. Hold the cutter head assembly securely and press down the shaft-lock button.
6. Tighten the Quick Nut. Note: Do not overtighten the nut.
NOTE: A special wrench has been included in
case the Cutter Nut has been inadvertently
overtightened.

14

15
Tiger SHARK™
3.1 Loading Key Blanks
3.2 Gauging Methods
3.3 4-Way jaws
LOADING / GAUGING KEYS

16
3.1 Loading Key Blanks
The Tiger SHARK™is equipped with 4-way jaws and integral shoulder and tip gauges. The choice of using the
shoulder or tip gauge is mandated by the type of key being cut. If in doubt of the gauge point, refer to the informa-
tion on the CUT SCREEN for the key to be cut (see 4.1 “Cutting by DSD”, step 6 in this manual for information on
the CUT SCREEN).
Important: The shoulder and tip gauges have safety switches. The cutter motor will not power on until the gauges
are lowered to their rest position. The Touch Screen will indicate to lower the gauges if necessary
Loosen the wing nut and place the key blank between the top and bottom jaw. The bottom of the key blank should
be against the back of the bottom jaw. Make sure that the key is level in the jaw.
3.2 Gauging Methods
INCORRECT INCORRECT CORRECT
Bow is not flush
with back of Jaw.
Tip is not flush
with back of Jaw.
Typical shoulder gauging for standard keys.
Typical tip gauging.
SIDE VIEW
SIDE VIEW
SIDE VIEW

17
Special Best style tip gauging.
3.3 4-Way Jaws
The Tiger SHARK™is equipped with state of the art 4-way jaws. These jaws are expertly machined to insure
secure holding of virtually all keys. The 4 sides are marked as follows:
The A-side is for most standard size keys.
The B-side is for most small size keys.
The CUT SCREEN or BITTING SCREEN will indicate which side to use for the particular key to be cut.
The sides marked and are for use with double sided keys. The indicates the holding ridge is on the
bottom jaw, pointing up. The indicates the holding ridge is on the top jaw, pointing down.
These holding ridges will allow you to clamp on the grooves in the keyway. When you use
these sides of the jaw you are not gauging from the back of the jaw, as you do on the A-side
and B-side.
To change sides:
D. Tighten wing nut.C. Swivel to another side.B. Grasp bottom jaw
and lift upwards.
A. Loosen the wing nut.

18
Table of contents
Other HPC Lathe manuals
Popular Lathe manuals by other brands
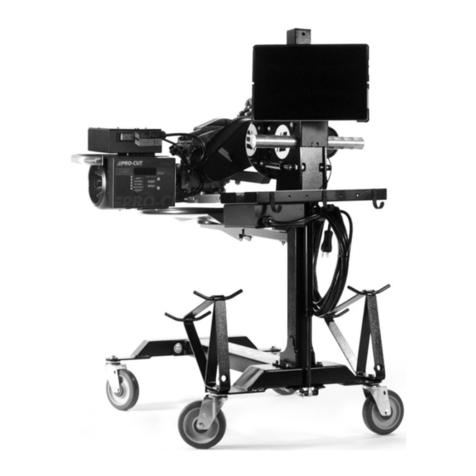
Pro-Cut
Pro-Cut X9 Technical manual

Bolton Tools
Bolton Tools CEB Operation manual
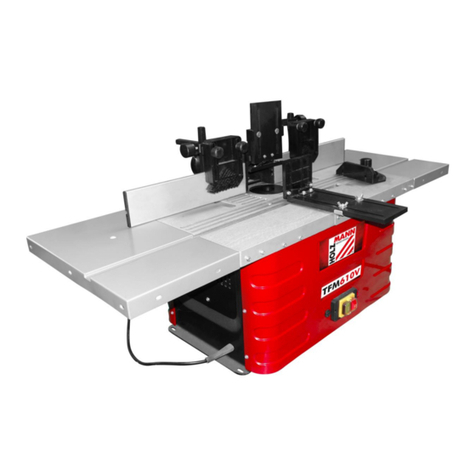
HOLZMANN MASCHINEN
HOLZMANN MASCHINEN TFM610V operating manual
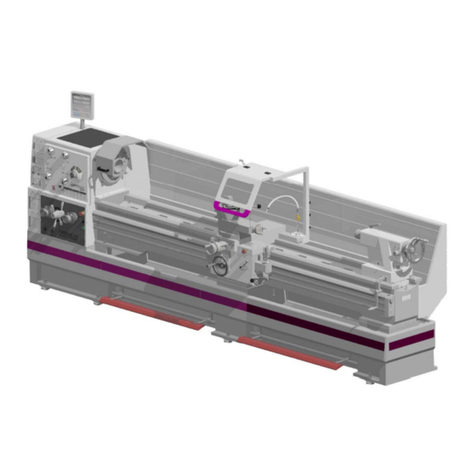
Optimum
Optimum OptiTurn TH 6620D operating instructions
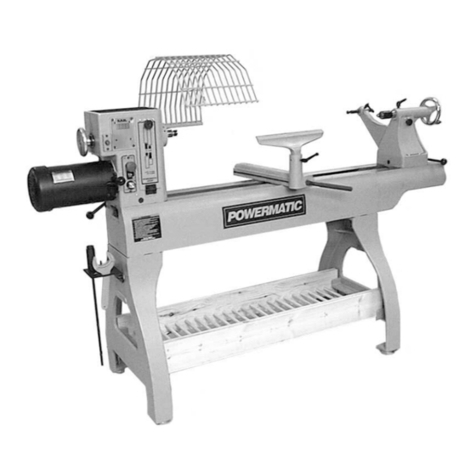
Powermatic
Powermatic 3520B Operating instructions and parts manual
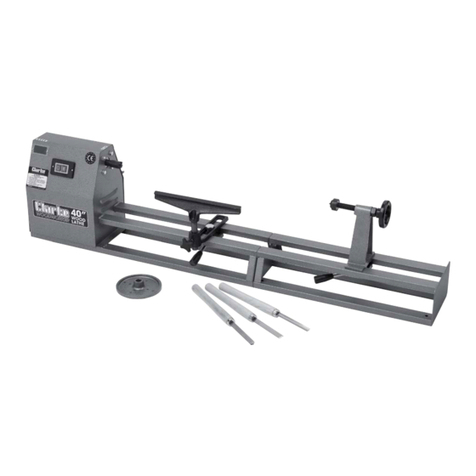
Clarke
Clarke Woodworker CWL1000 Operating & maintenance instructions