IFM DP2200 User manual

Operating instructions
Analogue threshold display
DP2200
11470257 / 0009 / 2022
GB

DP2200 Analogue threshold display
2
Contents
1 Preliminary note ............................................................. 4
1.1 Symbols used.......................................................... 4
1.2 Warnings used ......................................................... 4
2 Safety instructions............................................................ 5
3 Intended use................................................................ 6
3.1 Block diagram.......................................................... 6
4 Function ................................................................... 7
4.1 Use as a stand-alone device without IO-Link . . . . . . . . . . . . . . . . . . . . . . . . . . . . . . . . . . 7
4.2 Application as an IO-Link device............................................ 7
4.2.1 General information.................................................. 7
4.2.2 Application example ................................................. 8
4.2.3 Functionality....................................................... 8
4.2.4 IO Device Description (IODD).......................................... 8
5 Installation.................................................................. 9
6 Electrical connection.......................................................... 10
6.1 Removing the connector with vibration protection . . . . . . . . . . . . . . . . . . . . . . . . . . . . . . . 11
6.2 Cable length........................................................... 11
7 Operating and display elements................................................. 12
7.1 Push rings (pushbuttons) ................................................. 12
7.2 LEDs................................................................. 12
7.3 Display ............................................................... 12
7.3.1 Representation of the measured current value . . . . . . . . . . . . . . . . . . . . . . . . . . . . . 13
8 Menu...................................................................... 14
8.1 General............................................................... 14
8.2 Menu structure ......................................................... 15
8.3 Parameters of the main menu.............................................. 15
8.3.1 SP1/rP1 ─ set point/reset point OUT1. . . . . . . . . . . . . . . . . . . . . . . . . . . . . . . . . . . . 15
8.3.2 FH1/FL1 ─ min/max switching limits for window function . . . . . . . . . . . . . . . . . . . . . 16
8.3.3 EF ─ extended functions.............................................. 16
8.4 Parameters of the extended functions (EF) . . . . . . . . . . . . . . . . . . . . . . . . . . . . . . . . . . . . 16
8.4.1 rES ─ restore factory setting........................................... 16
8.4.2 A.Trm ─ analogue termination for OUT2 . . . . . . . . . . . . . . . . . . . . . . . . . . . . . . . . . . 16
8.4.3 ou1 ─ output function for OUT1......................................... 16
8.4.4 dS1/dr1 ─ switching delay/switch-off delay for OUT1 . . . . . . . . . . . . . . . . . . . . . . . . 17
8.4.5 ScAL ─ scaling of the displayed value. . . . . . . . . . . . . . . . . . . . . . . . . . . . . . . . . . . . 17
8.4.6 C.ASP/C.AEP - customer-specific analogue start/end point . . . . . . . . . . . . . . . . . . . 17
8.4.7 coLr ─ display colours and colour changes . . . . . . . . . . . . . . . . . . . . . . . . . . . . . . . . 18
8.4.8 cFH/cFL ─ upper/lower value for colour change . . . . . . . . . . . . . . . . . . . . . . . . . . . . 18
8.4.9 diS ─ refresh rate of the displayed measured value . . . . . . . . . . . . . . . . . . . . . . . . . 19
8.4.10 Lo/Hi ─ min/max measured input values . . . . . . . . . . . . . . . . . . . . . . . . . . . . . . . . . . 19
8.4.11 dAP ─ damping..................................................... 19
8.4.12 Reset [Hi] and [Lo] memory............................................ 19
8.5 Parameters adjustable via IO-Link .......................................... 19
8.5.1 C.uni – customer-specific unit.......................................... 19
8.5.2 S.Loc – software locking.............................................. 20
8.5.3 Application-specific tag............................................... 20
9 Parameter setting............................................................ 21
9.1 Parameter setting in general............................................... 21
9.2 Example [ou1] ─ output function for OUT1 . . . . . . . . . . . . . . . . . . . . . . . . . . . . . . . . . . . . 21
9.3 Notes on programming................................................... 22
9.3.1 Locking / unlocking.................................................. 22
9.3.2 Timeout........................................................... 22
9.3.3 Numerical entries with [▼] or [▲] . . . . . . . . . . . . . . . . . . . . . . . . . . . . . . . . . . . . . . . 22
10 Operation .................................................................. 23
10.1 Functions output 1 ...................................................... 23

Analogue threshold display DP2200
3
10.2 Functions output 2 ...................................................... 23
11 Troubleshooting ............................................................. 24
12 Maintenance, repair and disposal................................................ 25
13 Factory settings.............................................................. 26

DP2200 Analogue threshold display
4
1 Preliminary note
You will find instructions, technical data, approvals and further information using the QR code on the
unit / packaging or at www.ifm.com.
1.1 Symbols used
Requirement
Instructions
Reaction, result
[...] Designation of keys, buttons or indications
Cross-reference
Important note
Non-compliance may result in malfunction or interference.
Information
Supplementary note
1.2 Warnings used
CAUTION
Warning of personal injury
wSlight reversible injuries may result.

Analogue threshold display DP2200
5
2 Safety instructions
• The unit described is a subcomponent for integration into a system.
– The system architect is responsible for the safety of the system.
– The system architect undertakes to perform a risk assessment and to create documentation in
accordance with legal and normative requirements to be provided to the operator and user of
the system. This documentation must contain all necessary information and safety instructions
for the operator, the user and, if applicable, for any service personnel authorised by the
architect of the system.
• Read this document before setting up the product and keep it during the entire service life.
• The product must be suitable for the corresponding applications and environmental conditions
without any restrictions.
• Only use the product for its intended purpose (Ò Intended use).
• If the operating instructions or the technical data are not adhered to, personal injury and/or damage
to property may occur.
• The manufacturer assumes no liability or warranty for any consequences caused by tampering with
the product or incorrect use by the operator.
• Installation, electrical connection, set-up, programming, configuration, operation and maintenance
of the product must be carried out by personnel qualified and authorised for the respective activity.
• Protect units and cables against damage.
• Replace damaged units, otherwise the technical data and safety will be impaired.
• Observe applicable documents.

DP2200 Analogue threshold display
6
3 Intended use
The device is used for the evaluation of an analogue signal (4...20 mA) from a connected sensor or
another device with analogue output (4...20 mA). The device has one analogue current input and two
outputs: output 1 (digital) and optionally output 2 (analogue current output).
The unit is not suited for environments with particular requirements on mechanical stability (e.g.
shock/vibration).
The unit is intended for indoor use only.
uObserve the operating conditions (Ò Technical data at www.ifm.com).
3.1 Block diagram
2
3
1
Input (analogue) I
IN
OUT2 (analogue)
OUT1 (SIO / IO-Link)
DP2200
A.Trm
*) **)
Fig.1: inputs/outputs of the device
1: IN (analogue input IIN) A.Trm: analogue termination OUT2
2: OUT1 (digital output SIO / IO-Link) *) switchable internal load
3: OUT2 (analogue output IOUT = IIN) **) external load (optional)
Current rating: max. 50 mA for each output
The current loop of the analogue input must be terminated. Only one load may be connected,
either an internal or an external load.
See:
A.Trm ─ analogue termination for OUT2 (Ò/16)
Troubleshooting (Ò/24)

Analogue threshold display DP2200
7
4 Function
There are basically two modes in which the device can be operated:
• As stand-alone device
The device compares the measured current value with the set parameters and switches its output
according to the selected parameters. This mode is without IO-Link functionality. The parameters
can, however, also be set with an IO-Link tool.
• As IO-Link device
The device operates as an “analogue/IO-Link converter”. The evaluation of the measured current
value depends on the parameters which are set with IO-Link tools or a PLC via IO-Link
communication or directly on the device.
In some points parameter setting via IO-Link tools or PLC is different from parameter setting via
the menu (Ò Parameter setting).
4.1 Use as a stand-alone device without IO-Link
The device compares the measured current value with the set parameters and switches its output
according to the selected function (Ò Operation).
The measured value is shown on the alphanumerical display. The displayed value can be scaled by
the user (2-point scaling).
3
4
5
6
bar
4...20 mA
24 V DC
24 V DC 4...20 mA
M
OUT1
2
1
Fig.2: Application example without IO-Link master
1: Sensor with analogue output (e.g. pressure sensor) 2: Threshold display
3: Digital output 4: Looping through an analogue input signal
5: Switching amplifiers 6: Relay output for switching of
electric motors,
valves etc.
4.2 Application as an IO-Link device
4.2.1 General information
The unit has an IO-Link communication interface which requires an IO-Link capable module (IO-Link
master).
The IO-Link interface allows direct access to the process and diagnostic data and enables setting of
the parameters of the unit during operation.
You will find further information about IO-Link and all the necessary information about the required IO-
Link hardware and software at:
www.io-link.ifm

DP2200 Analogue threshold display
8
4.2.2 Application example
2
3
4
5
6
7
bar
4...20 mA
24 V DC
Fieldbus
4...20 mA
1
Fig.3: Application example with IO-Link master
1: Analogue sensor (e.g. pressure sensor) 2: Threshold display
3: Fully bidirectional IO-Link communication
• Remote display: reading and displaying the measured
current
• Remote parameter setting: reading and changing the
parameter setting
4: Looping through an analogue input signal
5: IO-Link master 6: Fieldbus (e.g. Profibus, Profinet etc.)
7: PLC
4.2.3 Functionality
In the IO-Link SIO mode, the device has the same functionality as a stand-alone device. The
measured value is also displayed.
Additionally, the device converts the measured current and transmits the value via IO-Link connection
to the PLC.
4.2.4 IO Device Description (IODD)
You will find the IODDs required for configuration of the IO-Link device as well as detailed information
about the process data structure, diagnostic information and parameter addresses at
documentation.ifm.com

Analogue threshold display DP2200
9
5 Installation
uInstall the device so that the M12 connection parts and the device are protected from mechanical
stress such as shock and vibration.
uIf necessary, fix the device with a mounting clip. Use M4 screw or cable tie for this purpose.
uDuring installation, ensure that the pollution degree is 2 or better.
Fig.4: Mounting clip Fig.5: Mounting clip with attached unit
The mounting clip is not supplied with the device. More information about available accessories
at www.ifm.com.

DP2200 Analogue threshold display
10
6 Electrical connection
The unit must be connected by a qualified electrician.
Observe the national and international regulations for the installation of electrical equipment.
Voltage supply according to SELV, PELV.
The circuit is insulated from device surfaces that could be touched with basic insulation according to
IEC 61010-1 (secondary circuit with max. 32 V DC, supplied from the mains circuit up to 300 V of
overvoltage category II).
The external wiring has to be carried out in a way that ensures the required separation from other
circuits.
CAUTION
Input current is not limited.
wNo fire protection.
uProtect circuits.
Potential M12 connector ①Fuse
L+ / supply voltage Pin 1 ≤ 2 A
Required tripping characteristic of the fuses:
Tfuse ≤ 120 s at max. 6.25 A (fire protection)
uAlternatively supply the device via a limited energy circuit according to IEC61010-1 or class 2
according to UL1310.
uDisconnect power.
uConnect the unit as follows:
2
1
43
2 1
3
1 2
4
5
Fig.6: Electrical connection
1: 4-pole M12 connector
(Output side)
• Pin 1: L+ / supply voltage
• Pin 2: OUT2 (analogue output)
• Pin 3: L- / supply voltage
• Pin 4: OUT1 (digital output SIO / IO-Link)
2: 5-pole M12 female connector
(Input side)
• Pin 1: L+ / sensor supply
• Pin 2: Analogue input (4...20 mA)
• Pin 3: L- / sensor supply
• Pin 4: Not used
• Pin 5: Not used
The threaded connections in the device correspond to the M12 standard. To ensure compliance with
the specified protection rating, only cables that comply with this standard may be used. In the case of
self-assembled cables, the system manufacturer is responsible for the protection rating.
uUse connectors with gold-plated contacts.
uDuring installation, place the connectors vertically so that the coupling nut will not damage the
thread.
uObserve the coding of the connectors during installation.
uTighten the cable sockets according to the torque specifications indicated by the cable
manufacturer. Maximum permissible tightening torque: 1.3 ± 0.1Nm

Analogue threshold display DP2200
11
uTighten the cable plug using 1.8 ± 0.1Nm.
uProvide all outgoing cables with suitable strain relief after a maximum of 200mm. Observe the
minimum bending radius of the cables (Ò information from the cable manufacturer).
2-wire sensors can also be connected to the device.
uExternal interference suppression of inductive loads is required.
Always use the provided connection cables to connect other devices.
See also application examples (Ò Function)
6.1 Removing the connector with vibration protection
uPress the connector against the unit and simultaneously loosen the coupling nut.
6.2 Cable length
• Without IO-Link communication: 30 m on each side
• With IO-Link communication: 20 m on the master side

DP2200 Analogue threshold display
12
7 Operating and display elements
2
3
1
7.1 Push rings (pushbuttons)
To execute an [esc], [●], [▼] or [▲] command, press the corresponding corner of a push ring.
Button Function
[esc] Escape Return to the previous menu. Exit parameter setting without saving the new value.
[●] Enter Open menu mode.
Selection of the parameter and acknowledgement of a parameter value.
[▼] Down Selection of a parameter. Setting a parameter value (scrolling by holding down, incremen-
tally by pressing repeatedly).
[▲] Up
To ensure correct operation of the push rings (buttons), do not install or place the unit directly
on a metal surface.
For the installation use the mounting clip Ò Installation.
7.2 LEDs
LED Colour Status Designation
I OUT1 yellow on Output 1 switched.
Power green on Voltage supply OK.
Device in operating mode.
off No voltage supply.
Device switched off.
II OUT2 yellow on Output 2 switched.
Error signals and diagnostics: Troubleshooting
7.3 Display
Colour Designation
Red/green 7-segment LED display, 4 digits, with colour change

Analogue threshold display DP2200
13
Error signals and diagnosis: Troubleshooting
In the operating mode the input current value is displayed. The scaling depends on the parameter
ScAL ─ scaling of the displayed value (Ò/17).
7.3.1 Representation of the measured current value
21 [mA]3.83.60.30.20 20.5
nPrb UL OL
Input current
Silent
events
3600-21000 μA
Process
data-32760 3276032764
3.60...21.00 mA
"UL" "OL""nPrb"
IO-Link
2 3
4
1
1: No measured data nPrb: No sensor
2: Input current below the range (-) UL: Process value too low
3: Input current above the range (+) OL: Process value too high
4: Displayed message or value.
The input current is not displayed scaled here.
Hysteresis range

DP2200 Analogue threshold display
14
8 Menu
8.1 General
Irrespective of the operating mode (standard IO mode or IO-Link device) there are two options to set
the parameters of the unit:
• directly on the device via the menu (Ò Parameter setting)
• or via an IO-Link tool
Access via an IO-Link tool has a higher priority than parameter setting via the menu.
Parameter cloning and parameter setting backup is possible with an IO-Link tool.
Some parameters can only be set via the IO-Link interface:
Parameters adjustable via IO-Link.
If the device was locked via IO-Link, it can also only be unlocked via the IO-Link interface:
Locking / unlocking (Ò/22).
The scaling parameter [ScAL] only influences the display and not the transferred process data or the
actual switching threshold values.
Via IO-Link, the current value is always transmitted in μA → Representation of the measured current
value (Ò/13). The switching thresholds can be set in steps of 0.01 mA.
If a scaling is set, the menu settings of the switching thresholds (SP, rP etc.) are also scaled.
Via IO-Link, however, the settings continue to be displayed and executed in steps of 0.01 mA
(resolution 10 bits).

Analogue threshold display DP2200
15
8.2 Menu structure
FH1 4.10...20.00
FL1 4.00...19.90
SP1 4.10...20.00
rP1 4.00...19.90
rESEF ---
A.trm On OFF
ou1 Hno Hnc Fno Fnc
dS1 0.0...50.0
dr1 0.0...50.0
ScAL OFF cccc ccc.c cc.cc c.ccc
C.ASP -746...9745
C.AEP -366...9366
coLr rEd GrEn r1ou G1ou r-cF G-cF
cFH 4.10...20.00
cFL 4.00...19.90
diS d1 d2 d3 OFF
Lo ---
Hi ---
dAP 0.000...4.000
1234
mA
3
12
1: Operating mode: Operation (Ò/23)
2: Main menu: Parameters of the main menu (Ò/15)
3: Extended functions: Parameters of the extended functions (EF) (Ò/16)
Factory settings (Ò/26)
8.3 Parameters of the main menu
8.3.1 SP1/rP1 ─ set point/reset point OUT1
Upper/lower limit for measuring current at which OUT1 switches with hysteresis setting. Only
displayed if the hysteresis function [Hno] or [Hnc] is set in [ou1].
Hno
Hnc
HY
SP1
1
0
1
0
rP1
OUT1
I [mA]
t
Fig.7: Hysteresis functions
SP: Switch point
rP: Reset point
HY: Hysteresis
Hno: Hysteresis function normally open
Hnc: Hysteresis function normally closed
uSelect [SP1] and set the value at which output OUT1 switches.
uSelect [rP1] and set the value at which output OUT1 switches off.
[rP1] is always smaller than [SP1]. The device only accepts values which are lower than the
value for [SP1].

DP2200 Analogue threshold display
16
[rP1] follows the changes of [SP1] and keeps the set hysteresis.
8.3.2 FH1/FL1 ─ min/max switching limits for window function
Upper/lower limit for measuring current at which OUT1 switches within the window setting. The
parameters are only displayed if the window function [Fno] or [Fnc] is set in [ou1].
Fno
Fnc
FE
1
0
1
0
FH1
OUT1
I [mA]
FL1
t
Fig.8: Window functions
FH: Window upper threshold
FL: Window lower threshold
FE: Window
Fno: Window function normally open
Fnc: Window function normally closed
uSelect [FH1] and set the upper limit.
uSelect [FL1] and set the lower limit.
[FL1] is always smaller than [FH1]. The device only accepts values which are lower than the
value for [FH1].
[FL1] follows the changes of [FH1] and keeps the set hysteresis.
8.3.3 EF ─ extended functions
EF ─ extended functions: Parameters of the extended functions (EF) (Ò/16)
8.4 Parameters of the extended functions (EF)
8.4.1 rES ─ restore factory setting
Resets all parameters to the Factory settings.
uSelect [rES].
uPress [●].
uPress and hold [▲] or [▼] until [----] is displayed.
uBriefly press [●].
8.4.2 A.Trm ─ analogue termination for OUT2
• [OFF] = OUT2 is externally connected, e.g. to the analogue input of another device.
• [On] = OUT2 is not connected and the current path is terminated internally.
Note the following for proper current measurement and evaluation:
If the internal analogue termination is set to [On], output OUT2 must not be connected.
8.4.3 ou1 ─ output function for OUT1
Switching signal for the current limits.
• [Hno] = hysteresis function / normally open

Analogue threshold display DP2200
17
• [Hnc] = hysteresis function / normally closed
• [Fno] = window function / normally open
• [Fnc] = window function / normally closed
See also:
SP1/rP1 ─ set point/reset point OUT1 (Ò/15)
FH1/FL1 ─ min/max switching limits for window function (Ò/16)
8.4.4 dS1/dr1 ─ switching delay/switch-off delay for OUT1
Value: 0.0...50.0 s (0.0 = delay time is not active)
8.4.5 ScAL ─ scaling of the displayed value
The setting acts like a multiplier for the parameters [C.ASP]/[C.AEP].
• [OFF] = measured current value is not scaled.
• [cccc] = scaling without decimal place (x 0001).
• [ccc.c] = scaling with 1 decimal place (x 000.1).
• [cc.cc] = scaling with 2 decimal places (x 00.01).
• [c.ccc] = scaling with 3 decimal places (x 0.001).
8.4.6 C.ASP/C.AEP - customer-specific analogue start/end point
Settings for scaled display values.
The parameters are only displayed if [ScAL] is set to [cccc], [ccc.c], [cc.cc] or
[c.ccc].
C.ASP value: -746 ... 9745 corresponds to 4 mA.
C.AEP value: -366 ... 9366 corresponds to 20 mA.
If a scaling is set via [ScAL], the C.AEP value also has to be adapted accordingly:
With [ScAL] = [ccc.c] → C.AEP value x 10
With [ScAL] = [cc.cc] → C.AEP value x 100
With [ScAL] = [c.ccc] → C.AEP value x 1000
All displayed current values are interpolated based on a 2-point approximation ([SP1]+[rP1],
[FH1]+[FL1], [cFH]+[cFL], [Lo]+[Hi]).
IO-Link process data and parameters are not affected by the scaling.
~ 9999
C.AEP
~ 999
C.ASP
[mA]4 20
21
3.6
9366
-746
~ 9999
C.ASP
~ 999
C.AEP
[mA]4 20
21
3.6
9745
-366

DP2200 Analogue threshold display
18
[mA]4 20
100.0
10
0.0
Fig.9: Example with scaled display value
Menu setting example
ScAL ccc.c
C.ASP 0.0
C.AEP 100.0
Input 10 mA
Display 37.5
8.4.7 coLr ─ display colours and colour changes
Assignment of the display colours "red" and "green" within the measuring range.
• [rEd] = continuously red (independent of the measured value).
• [GrEn] = continuously green (independent of the measured value).
• [r1ou] = red when OUT1 switches.
• [G1ou] = green when OUT1 switches.
OUT1
gn
rd
4 mA 20 mA
Fig.10: Hysteresis function with [r1ou]
OUT1
rd
gn
4 mA 20 mA
Fig.11: Hysteresis function with [G1ou]
FL1
FH1
gn gn
rd
4 mA 20 mA
Fig.12: Window function with [r1ou]
FL1
FH1
rd rd
gn
4 mA 20 mA
Fig.13: Window function with [G1ou]
[r-cF] = red when the measured value is between the values [cFL] and [cFH].
[G-cF] = green when the measured value is between the values [cFL] and [cFH].
8.4.8 cFH/cFL ─ upper/lower value for colour change
When setting [coLr] to [r-cF] or [G-cF]:
uSelect [cFH] and set the upper limit.
Setting range corresponds to the measured values. The lowest setting value is [cFL].
Select [cFL] and set the lower limit value.
Setting range corresponds to the measured values. The highest setting value is [cFH].

Analogue threshold display DP2200
19
cFL cFH
gn gn
rd
4 mA 20 mA
Fig.14: Function [r-cF]
cFL cFH
rd rd
gn
4 mA 20 mA
Fig.15: Function [G-cF]
For b/w printouts: gn = green, rd = red
8.4.9 diS ─ refresh rate of the displayed measured value
• [OFF][ = The measured value display is deactivated in the operating mode.]
• [d1] = update of the measured values every 50 ms.
• [d2] = update of the measured values every 200 ms.
• [d3] = update of the measured values every 600 ms.
Even with an unsteady input value, [d1] provides optimum readability.
8.4.10 Lo/Hi ─ min/max measured input values
[Lo] = lowest measured value
[Hi] = highest measured value
Delete memory:
uSelect [Hi] or [Lo].
uPress and hold [▲] or [▼] until [----] is displayed.
uBriefly press [●].
8.4.11 dAP ─ damping
Damping of the measured analogue value.
Setting also influences the set point, the IO-Link process data and the display.
Value: 0.000...4.000 s (T value: 63 %).
At 0.000 damping is not active.
8.4.12 Reset [Hi] and [Lo] memory
Reset of both memories: Reset [Hi] and [Lo] memory
8.5 Parameters adjustable via IO-Link
The following functions or parameters are only available via IO-Link tools.
8.5.1 C.uni – customer-specific unit
Customer-specific unit with max. 4 characters.

DP2200 Analogue threshold display
20
8.5.2 S.Loc – software locking
Value: ON/OFF
With ON, the device is locked for local menu settings.
Unlocking only via IO-Link.
8.5.3 Application-specific tag
Customer-specific application description, max. 32 characters long.
Default value: “ *** ” / can be freely defined by the customer
Table of contents
Other IFM Monitor manuals

IFM
IFM E30430 User manual
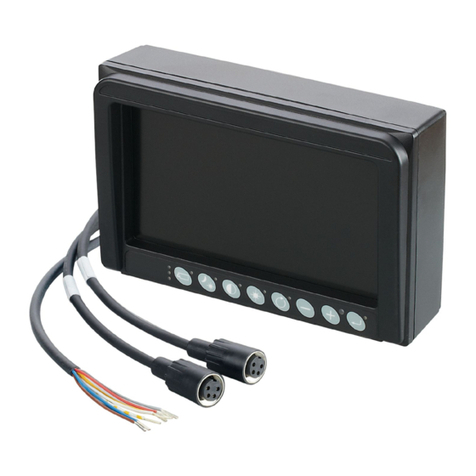
IFM
IFM E2M231 User manual
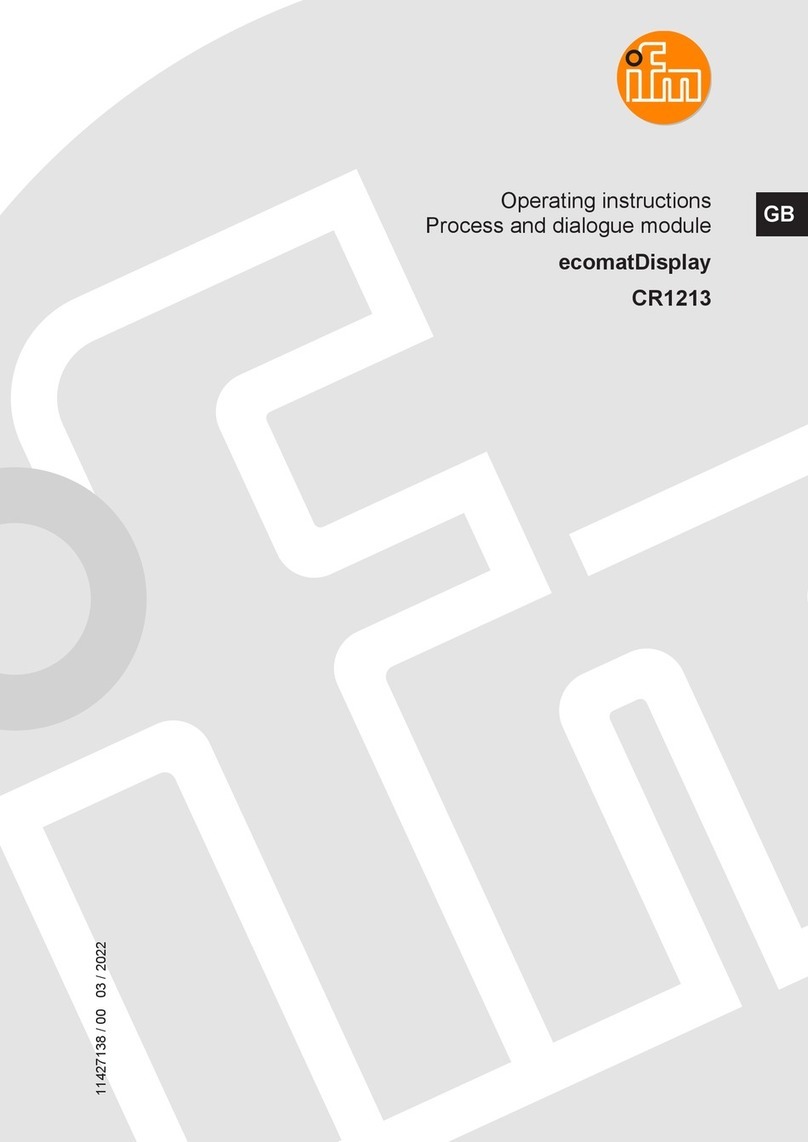
IFM
IFM ecomatDisplay CR1213 User manual
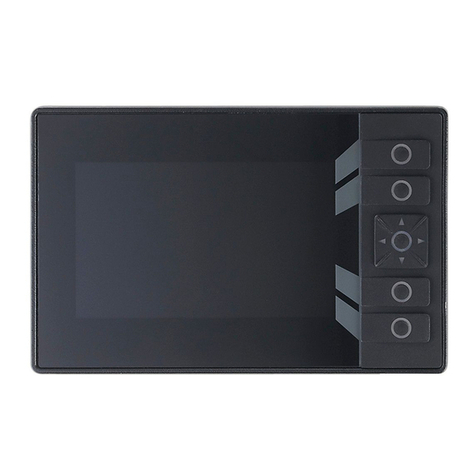
IFM
IFM ecomatDisplay CR1058 User manual
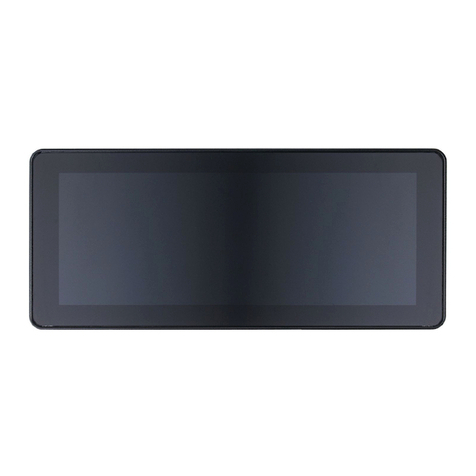
IFM
IFM ecomatDisplay CR1203 User manual
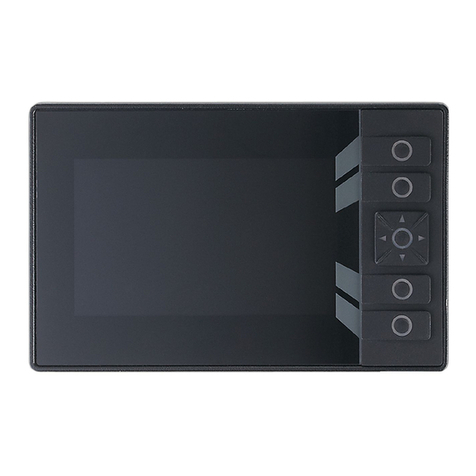
IFM
IFM ecomatDisplay CR1150 User manual
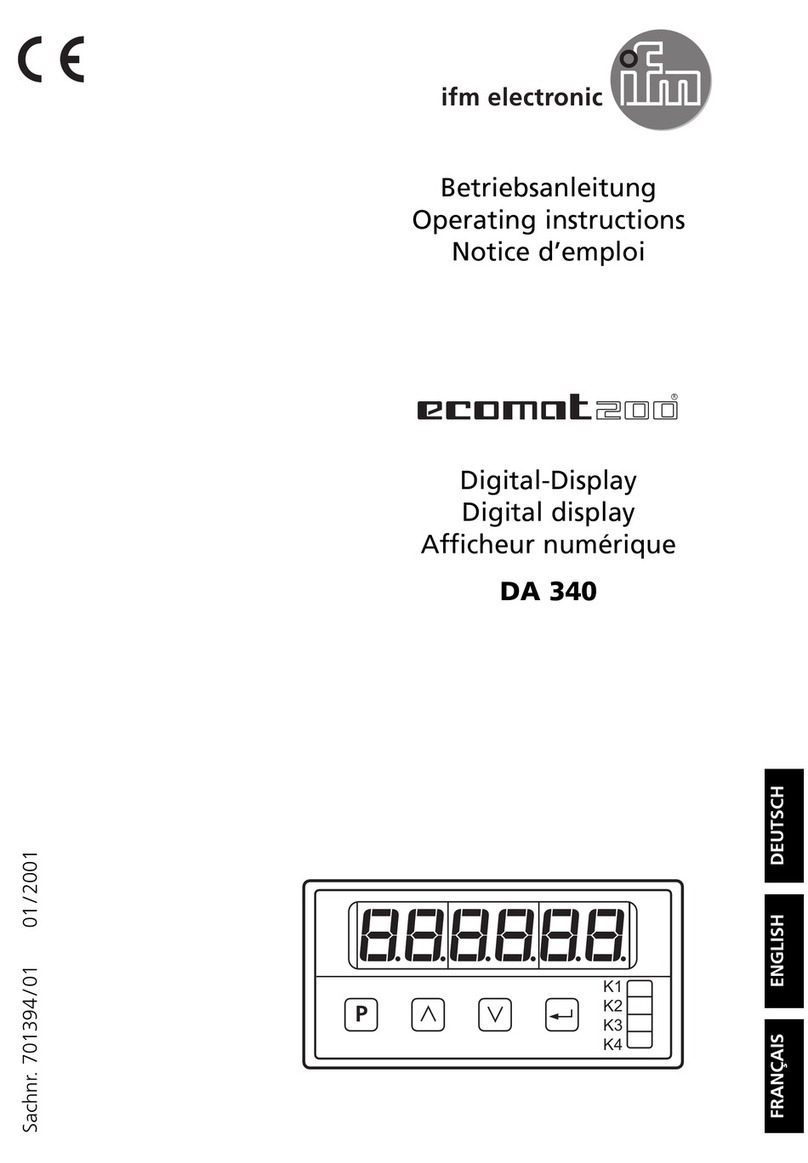
IFM
IFM Ecomat 200 DA 340 User manual
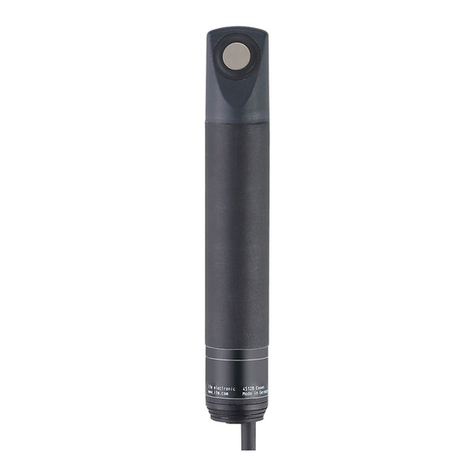
IFM
IFM SL5105 User manual

IFM
IFM FX460 User manual
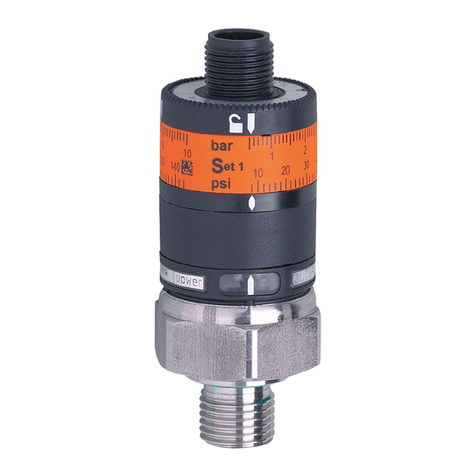
IFM
IFM PK55 Series User manual
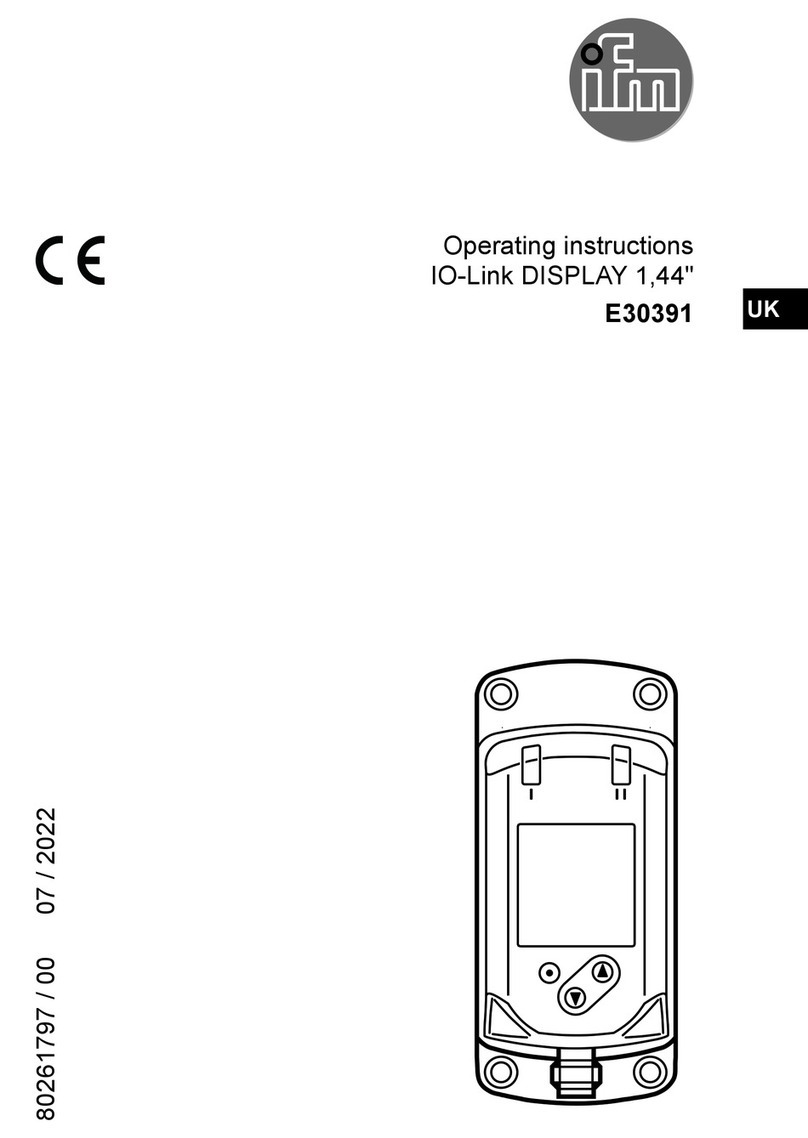
IFM
IFM E30391 User manual
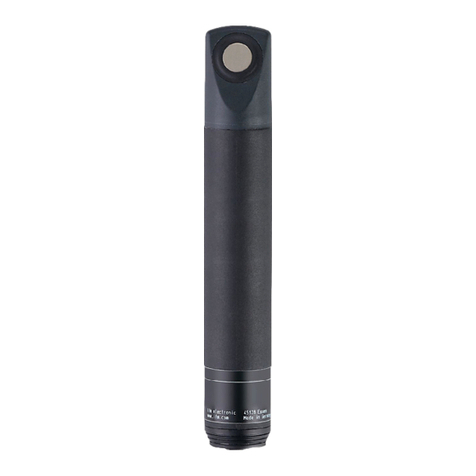
IFM
IFM Efector 300 SL5105 User manual
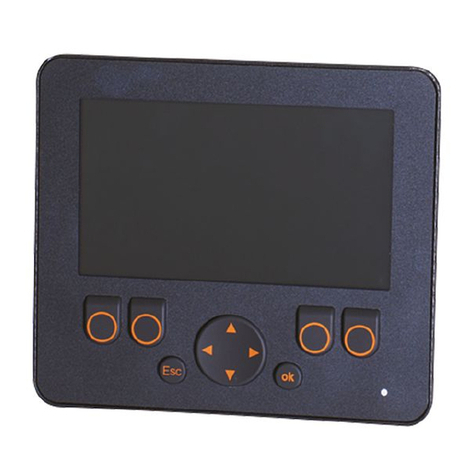
IFM
IFM CR0452 Owner's manual

IFM
IFM SL020 Series User manual
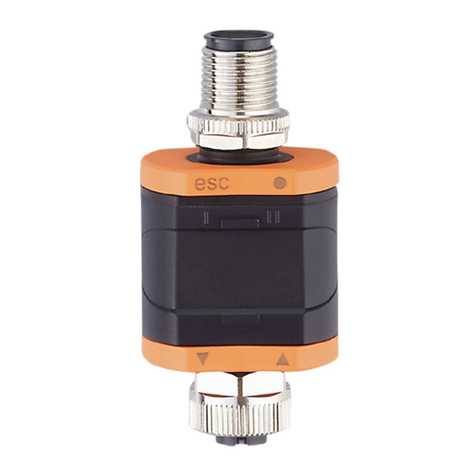
IFM
IFM DP2122 User manual

IFM
IFM ecomatDisplay CR1152 User manual
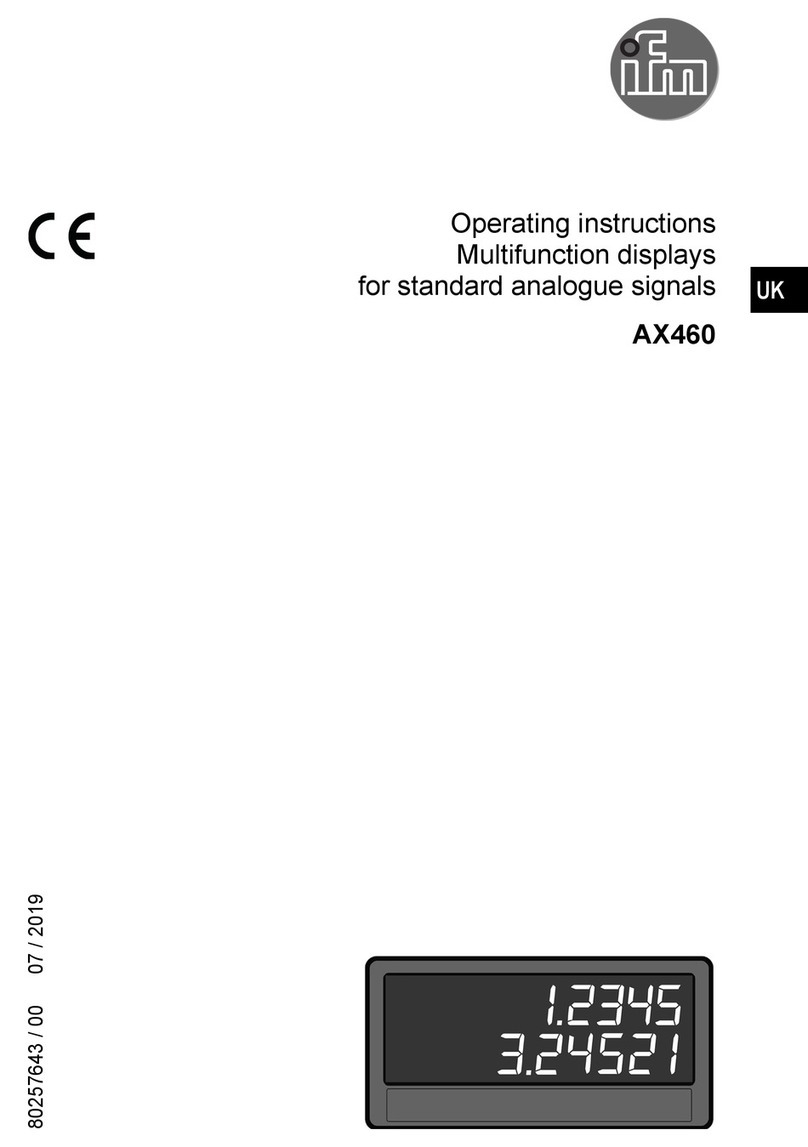
IFM
IFM AX460 User manual
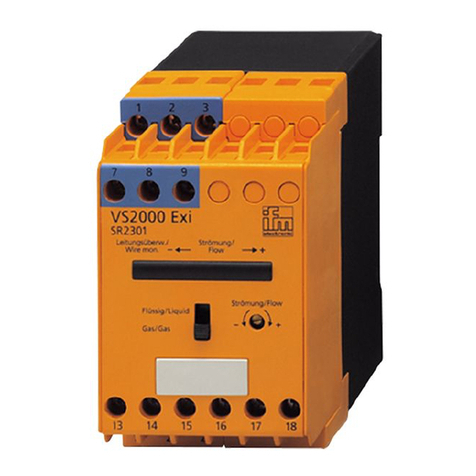
IFM
IFM Efector 300 VS2000 Exi User manual

IFM
IFM DX1063 User manual

IFM
IFM efector 300 SID User manual