Keba KeDrive D3-DA BG3 User manual

Operation manual
Compact multi-axis system KeDrive D3
KeDrive D3-DA
Axis Controller BG3 and BG4

2
1
Operation Manual KeDrive D3-DA BG3 and BG4
1804.200B.1-01 Date: 03/2023
Overview, KeDrive D3-DA axis controllers
KeDrive D3-DA axis controller BG3 KeDrive D3-DA axis controller BG4
D3-DA 320/x-24xx, D3-DA 320/x-32xx, D3-DA
310/x-45xx, D3-DA 320/x-45xx, D3-DA 310/x-80xx,
D3-DA 310/x-A3xx, D3-DA 310/x-B1xx,
D3-DA310/C-C0xx
Compact multi-axis system KeDrive D3
KeDrive D3-DA axis controller
ID no.: 1804.200B.1-01
Date: 03/2023
Applicable as from: rmware V003.20-04
The German version is the original of this documentation.
Compact multi-axis system KeDrive D3
Consisting of the KeDrive D3-DP supply unit, the DC-powered KeDrive D3-DA axis
controllers and a matching controller KeDrive D3-DU, the compact KeDrive D3 drive
system offers a high degree of solutions expertise and exibility in the range from 2 A to
300 A rated current.
With the aid of the KeDrive D3-DE expansion module, the KeDrive D3-DA axis
controllers BG1 and BG2 can be combined with the KeDrive D3-DA axis controllers BG3
and BG4 without problems.
The addition to the KeDrive D3-DP supply unit BG3 and BG4 of the capacitance module
KeDrive D3-DC makes it possible to operate the axis controllers connected up to the
maximum active power permitted.
Reduction of the wiring and shortening of the installation times are just as easy to
achieve as resource-saving, cost-conscious operation.
Subject to technical change without notice.
The content of our documentation was compiled with the greatest care and attention,
and is based on the latest information available to us.
We should nevertheless point out that this document cannot always be updated
simultaneously with the ongoing technical development of our products.
Information and specications may be subject to change at any time. Please obtain
information about the latest version in our Docu Portal.

3
1 Table of contents
Operation Manual KeDrive D3-DA BG3 and BG4
1804.200B.1-01 Date: 03/2023
Table of contents
3 Mechanical installation ............................................................... 15
3.1 Notes for installation ...............................................................................................15
3.1.1 Order and arrangement............................................................................15
3.2 Mounting clearances ...............................................................................................16
3.3 Cooling of the devices with air cooling ...................................................................17
3.4 Installation of the devices with air cooling................................................................18
3.4.1 Dimensions (housing with heat sink) .......................................................19
3.5 Installation of the devices with liquid cooling ...........................................................20
3.5.1 Dimensions (housing with liquid cooling)..................................................20
3.6 Cooling circuit connection...................................................................................... 22
3.7 KeDrive D3-DA Congurations (examples)...............................................................23
4 Electrical installation ....................................................................25
4.1 Before you start ......................................................................................................25
4.2 Effective EMC installation ........................................................................................25
4.3 Overview of the connections ..................................................................................27
4.3.1 Single-axis controller............................................................................... 30
4.3.2 Double-axis controller ............................................................................. 32
4.4 Protective earth conductor connection................................................................... 35
4.4.1 PE connection according to DIN EN 61800-5-1 ...................................... 35
4.4.2 Connection principle ............................................................................... 36
4.5 Electrical isolation concept..................................................................................... 36
4.6 Connection of the supply voltages ..........................................................................37
4.6.1 24 V control supply.................................................................................. 38
4.6.2 Power supply .......................................................................................... 38
4.6.3 Overview of busbars in the group............................................................ 39
4.7 Control connections ............................................................................................... 39
4.7.1 Digital inputs on X25A (standard functions) ............................................. 40
4.7.2 Digital inputs on X26A (safe digital inputs) ................................................41
Table of contents
1 General ........................................................................................5
1.1 Target group ............................................................................................................ 5
1.2 Prerequisites ............................................................................................................ 5
1.3 Pictograms .............................................................................................................. 5
1.4 Disclaimer................................................................................................................. 5
1.5 Reference documents ............................................................................................. 5
1.6 Order code .............................................................................................................. 6
1.7 Rating plate ............................................................................................................. 6
1.8 Brief description ....................................................................................................... 7
1.9 Scope of supply ....................................................................................................... 8
1.10 Disposal ................................................................................................................... 8
1.11 S up po r t ................................................................................................................... 8
2 Safety ...........................................................................................9
2.1 O v e r v i e w .................................................................................................................. 9
2.2 Measures for your safety .......................................................................................... 9
2.3 General safety instructions and warnings ................................................................10
2.4 Intended use............................................................................................................10
2.4.1 Repair.......................................................................................................10
2.5 Misuse.....................................................................................................................11
2.6 Responsibility ..........................................................................................................11
2.7 Relevant laws, standards and directives applied .....................................................11
2.8 Declaration of conformity.........................................................................................12
2.9 UK Conformity Assessed (UKCA) ............................................................................12
2.9.1 Directives, standards and regulations ......................................................13
2.9.2 UKCA declaration of conformity ...............................................................13

4
1 Table of contents
Operation Manual KeDrive D3-DA BG3 and BG4
1804.200B.1-01 Date: 03/2023
Table of contents
6 Diagnostics .................................................................................63
6.1 Axis status LEDs..................................................................................................... 63
6.1.1 Flashing code.......................................................................................... 63
6.2 Status and error indication in KeStudio DriveManager ........................................... 64
7 Safety design variants .................................................................67
7.1 SD0 model .............................................................................................................67
7.2 SDC model..............................................................................................................67
A Appendix .....................................................................................69
A.1 Technical data, KeDrive D3-DA axis controllers BG3 and BG4 .............................. 69
A.2 Power section current data, 24 A to 210 A controller, air-cooled .............................70
A.3 Power section current data, 24 A to 300 A controller, liquid-cooled ........................72
A.4 Ambient conditions..................................................................................................74
A.5 Power reduction at Tunom ≥ 40 °C ............................................................................75
A.6 Certications............................................................................................................75
A.6.1 CE certication .........................................................................................75
A.6.2 UL certication .........................................................................................75
A.6.3 Load on the mains due to harmonics ......................................................75
A.7 Accessories.............................................................................................................76
A.8 Connection system..................................................................................................76
A.8.1 Encoder cables ........................................................................................76
A.8.2 Motor cable ..............................................................................................76
A.8.3 Connector sets.........................................................................................76
A.8.4 Data cables ..............................................................................................76
A.9 Hydrological data for the liquid cooling ...................................................................77
Glossary.............................................................................................79
4.8 Motor connection ....................................................................................................41
4.8.1 Motor connection diagram .......................................................................42
4.8.2 Motor holding brake monitoring output ................................................... 45
4.8.3 Specication for motor connections........................................................ 45
4.8.4 Switching in the motor cable ................................................................... 46
4.8.5 Electronic overload protection for the motor ........................................... 46
4.9 Encoder connections .............................................................................................47
4.9.1 Allocation of motor/encoder cable to the drive controller ........................47
4.9.2 Connection for high-resolution encoders (X48A and X48C) .................... 48
4.9.3 Connection for additional encoder (X48B and X48D) .............................. 49
4.9.4 Connection of analog sensors (X48B) ..................................................... 49
4.10 Specication ............................................................................. 49
5 Commissioning ...........................................................................53
5.1 Preliminary comment.............................................................................................. 53
5.1.1 Connections for communication ............................................................. 53
5.1.2 EtherCAT® integration............................................................................. 53
5.1.3 Procedure for activating the service/diagnostics mode:.......................... 54
5.1.4 Exiting the service/diagnostics mode:..................................................... 56
5.2 Initial commissioning of the axis controller.............................................................. 58
5.3 Axis controller supply voltage ................................................................................. 58
5.3.1 Commissioning ....................................................................................... 58
5.3.2 Controlling drive using KeStudio DriveManager ..................................... 59
5.3.3 Serial commissioning .............................................................................. 60
5.4 Standard operation on the KeDrive D3-DU controller..............................................61
5.4.1 Conguration of the KeDrive D3-DU controller.........................................61
5.4.2 Conguration of a controller from another manufacturer..........................61

5
1 General
Operation Manual KeDrive D3-DA BG3 and BG4
1804.200B.1-01 Date: 03/2023
General
1 General
The document set from KEBA Industrial Automation Germany GmbH contains the
complete documentation for the related product range. The documentation for a product
range includes the operation manual (hardware description), device help (software
description) as well as further user manuals (e.g. eld bus description) and specications.
The documents are available in PDF format.
1.1 Target group
Dear user,
The documentation forms part of the device and contains important information about
operation and service. It is aimed at all persons who undertake mounting, installation,
commissioning and servicing work on the product.
1.2 Prerequisites
Prerequisites for usage of the devices from KEBA:
yThe documentation on the devices is to be stored so it is legible, accessible at
all times and for the entire life of the product.
yThe user must read and understand the documentation on the device.
yQualication: to prevent injury or damage, personnel may only work on the
device if they have electrical engineering qualications.
yKnowledge required:
− National accident prevention regulations (e.g. DGUVV3 in Germany)
− Mounting, installation, commissioning and operation of the device
Work in other areas, for example transport, storage and disposal is only allowed to be
undertaken by trained personnel.
1.3 Pictograms
To help the user, in this document we use the following pictograms:
NOTE
Useful information for the user.
Reference to other documents.
You will nd the "safety instructions and warnings" used in this operation manual in
chapter 2 Safety.
1.4 Disclaimer
Following the documentation on the devices from KEBA is a prerequisite:
yFor safe operation.
yTo obtain stated performance features and product characteristics.
KEBA does not accept any liability for injuries, damage or nancial losses that result from
the failure to follow the documentation.
1.5 Reference documents
NOTE:
You will nd all reference documents for this device on our web site in the
DOCU Portal: www.keba.com

6
1 General
Operation Manual KeDrive D3-DA BG3 and BG4
1804.200B.1-01 Date: 03/2023
General
1.6 Order code
The article designation provides information about the related variant.
D3 - DA 3 2 0 / A - 4 5 1 1 - 2 1 0 0 - 0 0 0 0
Module type Axis module
Product line
Number of
axes
1: Single-axis
2: Double-axis module
Supply 0: DC voltage
Cooling A: Heat sink
C: Liquid cooling
Rated current
24: 24 A BG3 (2 axes)
32: 32 A BG3 (2 axes)
45: 45 A BG3 (1 + 2 axes)
80: 80 A BG3 (1 axis)
A3: 130 A / 150 A1) BG4 (1 axis)
B1: 210 A / 250 A1) BG4 (1 axis)
C0: 300 A BG4 (1 axis)
Encoder
interface
0: None
1: Multi-encoder interface
2: Hiperface DSL® (one-cable solution)
3: HIPERFACE DSL® (one-cable solution) + multi-encoder
interface solution
Safety
function
1: SD0 (STO and SBC)2)
2: SDC (encoder version SinCos + HDSL®)3)
3: SDC (encoder version SinCos + EnDat2.2)4)
4: SDC (encoder version Resolver + HDSL®)3)
5: SDC (encoder version Resolver + EnDat2.2)4)
7: SDC (encoder version SinCos + HDSL®) + FW
V3.0.0.82) 3)
8: SDC (encoder version Resolver + HDSL®) + FW
V3.0.0.82) 3)
Options
0: None
1: With protective coating
2: Output frequency limiting < 600 Hz2)
3: Output frequency limiting < 600 Hz, with protective coating
Version 0: First version
1: New eld bus controller2)
1) second gure applies to liquid-cooled variant, 2) preferred option, 3) hardware version 0 only, 4) on request, 5) discontinued
D3 - DA 3 2 0 / A - 4 5 1 1 - 2 1 0 0 - 0 0 0 0
Model
00: Standard variant2)
01: With document set5)
02: With connector sets inside device packaging
03: With connector sets, with document set5)
Field bus
0: EtherCAT
1: Powerlink
2: PROFINET3)
Reserved
1) second gure applies to liquid-cooled variant, 2) preferred option, 3) hardware version 0 only, 4) on request, 5) discontinued
1.7 Rating plate
On the rating plate for the KeDrive D3-DA BG3 and BG4 you will nd the serial number.
You can identify the date of manufacture based on the following key.
Mac Adr.:
SW:
FS SW1:
SN:
SN:
FS SW2:
*)
KEBA Industrial Automation Germany GmbH
Gewerbestr. 5-9, 35633 Lahnau, www.keba.com
Multiple rated equipment. See instruction manual
In:
Out:
Year:
T1
T
D3-DA 320/A-4511-0000-0000
JJWWSXXXX
325 V - 678 V DC
20XX
110 A
2 x (0-480 V 3ph 0-400 Hz 45 A)
JJWWSXXXX
MACADR
D3-DA 320/A-4511-0000-0000
Serial no. key:
- JJ (YY) = Prod. year
- WW = Calendar week (CW)
- S = Production site
- XXXX = Sequential no. (per CW)
*) = Revision state (e.g. F)
Figure 1.1 Hardware rating plate KeDrive D3-DA BG3 and BG4 (example)

7
1 General
Operation Manual KeDrive D3-DA BG3 and BG4
1804.200B.1-01 Date: 03/2023
General
Allocation of number of axes, rated current and sizes
Axis
controller
with ...
Cooling Size 3 (BG3)
Rated current Irated, eff [A]
Size 4 (BG4)
Rated current Irated, eff [A]
1 axis Air – – 45 80 130 210 –
1 axis Liquid – – 45 80 150 250 300
2 axes Air 2x24 2x32 2x45 – – – –
2 axes Liquid 2x24 2x32 2x45 – – – –
The table below shows the type, device and short designations. All three designations
can be used in the operation manual in different contexts with the same meaning.
Type designation Device designation Short designation
KeDrive D3-DA Axis controller D3 DA
KeDrive D3-DP Supply unit D3 DP
KeDrive D3-DC Capacitance module D3 DC
KeDrive D3-DE Expansion module D3 DE
- Single model D3 DE Single
- Dual model D3 DE Dual
- Dual End model D3 DE Dual End
- Size (BG) 1 and size (BG) 2 BG1 and BG2
- Size (BG) 3 and size (BG) 4 BG3 and BG4
NOTE:
The axis controllers KeDrive D3-DA BG3 and BG4 are DC-powered
devices that are only allowed to be operated on a supply unit (type D3-DP
300/x-45xx-xx to D3-DP 300/x-A2xx-xx) in the KeDrive D3 drive system.
T
T1
Figure 1.2 Position of rating plate (T) Figure 1.3 Position of rating plate (T1)
The rating plate T is on the left side of the KeDrive D3-DA axis controller. A second rating
plate (T1) is on the top of the busbar cover. In this way the rating plate data can also be
seen if the devices are installed in a row.
1.8 Brief description
NOTE
Only the KeDrive D3-DA BG3 and BG4 are described in this operation manual.
You will nd information about the other components of the KeDrive D3 drive
system in the related operation manuals.

8
1 General
Operation Manual KeDrive D3-DA BG3 and BG4
1804.200B.1-01 Date: 03/2023
General
1.9 Scope of supply
The scope of supply includes:
yKeDrive D3-DA axis controllers BG3 and BG4
yReady-made connection cable for EtherCAT
yReady-made busbar elements for 24 V control supply
yBusbar elements for DC link supply in separate accessory kit
yOptional document set (depending on the version ordered)
1.10 Disposal
Follow the current national regulations! If necessary, dispose of individual parts,
depending on their characteristics and existing national regulations, e.g. as:
yElectrical waste
yPlastic
yMetal
Or engage a certied disposal organisation with scrapping
1.11 Support
Address: KEBA Industrial Automation Germany GmbH
Gewerbestrasse 5-9
35633 Lahnau
Control engineering:
Phone: +43 732 7090 23222
E-Mail: [email protected]
Drive engineering:
Phone: +49 6441 966 180
E-Mail: [email protected]
You can reach us Monday to Thursday between 8:00 am and 5:00 pm, Friday between
8:00 am and 4:00 pm.
NOTE:
You will nd detailed information about our services on our web site under
Technical support

9
1 Safety
Operation Manual KeDrive D3-DA BG3 and BG4
1804.200B.1-01 Date: 03/2023
Safety
2 Safety
2.1 Overview
Our devices are state-of-the-art and comply with recognised safety regulations,
nevertheless hazards can arise. In this chapter:
yWe provide information about residual risks and hazards that can emanate from
our devices if used as intended.
yWe warn about the foreseeable misuse of our devices.
yWe refer to the necessary care and measures to be taken to prevent risks.
2.2 Measures for your safety
NOTE
Your device is only allowed to be installed and placed in operation taking into
account the documentation for the related device family!
Our devices are quick and safe to operate. For your own safety and for the safe function
of your machine, please be sure to observe the following points:
1. Follow safety instructions for the devices:
Follow all safety instructions and warnings in the entire documentation related to the device range.
2.
Electrical drives are dangerous:
• Due to electrical voltages up to 480V AC and up to 800V DC
• Even 10min. after switching off the mains supply, dangerously high voltages of ≥50V may still
be present (capacitor charge). Therefore check there is no electrical power in the device! See
also the warning label on the front panel on the device.
• Rotating parts
• Automatically starting drives.
• Hot components and surfaces
3.
Protection against magnetic and/or electromagnetic elds during
installation and operation.
Persons tted with heart pacemakers, metallic implants or hearing aids, etc. must not be allowed
access to the following areas:
• Areas in the immediate vicinity of electrical equipment!
• Areas where electronic components and drive controllers are installed,
repaired and operated!
• Areas where motors are installed, repaired and operated!
Motors with permanent magnets pose particular hazards.
4.
During installation observe the following:
• Comply with connection conditions and technical data as per the documentation and the rating
plate!
• Comply with standards and directives on electrical installation, such as cable cross-section,
shielding, etc.!
• Do not touch electronic components or contacts!
Electrostatic discharge can harm people and destroy components!
• Take protection measures and use protection devices as per the applicable regulations
(e.g. EN 60204 or EN 61800-5-1)!
• Take protection measures against electric shock according to IEC 60364-4-41:2005/AMD1:-
section 411.3. As a protection measure, use additional protective equipotential bonding as
described in appendix D of IEC 60364-4-41.
• Take "device earthing" protection measure!
5.
Ambient conditions
• Pay attention to the information about the transport, storage and correct operation of the
devices stated in the operation manual in "A Appendix".

10
1 Safety
Operation Manual KeDrive D3-DA BG3 and BG4
1804.200B.1-01 Date: 03/2023
Safety
2.3 General safety instructions and warnings
DANGER! Risk of injury due to electrical power!
• Carelessness will result in serious injuries or death.
Follow safety instructions and warnings in this document and on the device.
WARNING! Risk of injury due to electrical power!
• Carelessness may result in serious injuries or death.
Follow safety instructions and warnings in this document and on the device.
CAUTION! Risk of injury or damage to the device due to incorrect operation!
• Carelessness may result in minor injuries or damage.
Follow safety instructions and warnings in this document and on the device.
WARNING! Risk of injury due to hot surfaces and components!
• Carelessness may result in serious burns.
Electronic components may become hot during operation!
Follow safety instructions and warnings in this document and on the device!
Caution! Damage due to electrostatic discharge!
• Electrostatic discharge can destroy components.
Do not touch electronic components or contacts!
Follow safety instructions and warnings in this document and on the device!
DANGER! Risk of injury due to rotating parts on the motor!
• Carelessness will result in serious injuries or death.
Follow safety instructions and warnings in this document.
Pay attention to special safety instructions and warnings that are given here in the document before a
specic action and that warn the user about a specic hazard!
NOTE:
The pictograms may also be used on their own with the signal word, e.g.
in the connection diagrams, however they have the same function as in the
complete warning.
DANGER WARNING CAUTION
2.4 Intended use
Our devices are components intended for stationary electrical systems and machines in
the industrial and commercial sector.
The KeDrive D3-DA axis controllers BG3 and BG4 conform to the
Machinery Directive 2006/42/EC
Tested and certied in accordance with applicable standards (see declaration of conformity in
chap. 2.8).
If installed in machines it is prohibited to start up intended operation until it has been
ascertained that the completed machine fully complies with the provisions of the
Machinery Directive (2006/42/EC); compliance with EN 60204 is mandatory.
Starting intended operation incl. all accessories such as mains lters and mains chokes
is only permitted while complying with the EMC Directive 2014/30/EU.
The devices meet the requirements of the harmonised product standard EN 61800-5-1.
You will nd information about the installation of your device in chapter "3 Mechanical
installation".
2.4.1 Repair
Only have repairs undertaken by authorised repair workshops. Unauthorised repairs
could lead to death, injury or damage (see previous sections). The warranty provided by
KEBA will be rendered void.

11
1 Safety
Operation Manual KeDrive D3-DA BG3 and BG4
1804.200B.1-01 Date: 03/2023
Safety
yThe emergency stop function (as per EN 60204-1:2006) shuts down the supply
of power to a machine, which results in the drives coasting down in an uncon-
trolled manner. To avert hazards, check whether it is appropriate:
− To keep individual drives in operation
− To initiate specic safety procedures
− To incorporate a Safe Torque Off function (Safe Torque Off: movement stop
by "switching off the electrical supply" or STO)
2.7 Relevant laws, standards and directives
applied
For information about laws, standards and directives applied by KEBA, refer to the
declaration of conformity.
NOTE:
Depending on the specic application for the devices, other laws, standards
and directives with provisions about "safety" may apply. If necessary, contact
the machine or system manufacturer.
NOTE:
Due to possible output frequencies >600Hz, the following variants of the
drive controllers fall under Dual Use Regulation (EU) no. 1382/2014 dated
22 October 2014 item 3A225:
D3-DA 3xx/x-xxxx-Yxxx-xxxx, Y = 0 and Y = 1
Export authorisation is therefore required for non-EU countries. Please note
the information in the delivery documents.
NOTE:
The KEBA drive controllers described here do not fall under the Ecodesign
Regulation (EU)2019/1781 (efciency class IE2) because at least one of the
following points applies if used as intended:
yOperation exclusively for servomotors with speed/position feedback
ySupply with DC voltage
ySupply with single-phase AC voltage
ySupply with low voltage <100 V
2.5 Misuse
Our devices are:
yNot intended for installation in vehicles. Deployment of the device in mobile
equipment is classed as non-standard ambient conditions and is permissible
only by special agreement.
yNot intended for installation in environments with harmful oils, acids, gases,
vapours, dusts, radiation, etc.
yNot approved for usage in special applications (e.g. in potentially explosive
atmospheres or areas in which there is a risk of re).
yNot approved for usage outside a switch cabinet.
yNot approved for the generation of high-frequency onboard
networks for which the devices are not designed.
NOTE:
The use of devices in warehouse storage and retrieval systems operated
inside and outside the rack aisle on rails is allowed provided the vibration does
not exceed the maximum standard values 3M1 as per DINEN60721-3-3.
2.6 Responsibility
Electronic devices are not fail-safe. The installer and/or organisation operating a
complete machine or system is responsible:
yFor ensuring the drive is rendered safe if the device fails.
yFor ensuring the safety of personnel and machinery
yFor ensuring the complete machine is in correct working order
yFor the risk assessment on the complete machine or system according to
DIN EN 12100:2011 and EN ISO 13849-1
In EN 60204-1:2006 "Safety of machinery", pay attention to:
yThe topic of "Electrical equipment of machines". The safety requirements on
electrical machines specied there are intended to protect personnel and ma-
chinery or systems.

12
1 Safety
Operation Manual KeDrive D3-DA BG3 and BG4
1804.200B.1-01 Date: 03/2023
Safety
2.8 Declaration of conformity
2.9 UK Conformity Assessed (UKCA)
UKCA (UKCA = UK Conformity Assessed) is the British product marking required for
certain products placed on the market in Great Britain (England, Wales and Scotland).
Authorised representative is:
KEBA Ltd.
Aston Court
Frederick Place
Kingsmead Business Park
High Wycombe
HP11 1JU
Authorised person to compile the technical le is Ian Hanton, KEBA Ltd.

13
1 Safety
Operation Manual KeDrive D3-DA BG3 and BG4
1804.200B.1-01 Date: 03/2023
Safety
2.9.1 Directives, standards and regulations
The following table provides a comparison of the EU directives met and the regulations
applicable in Great Britain.
European Union (EU) Great Britain (UK)
2006/42/EC - Machinery Supply of Machinery (Safety) Regulations 2008
2014/30/EU - Electromagnetic Compatibility Electromagnetic Compatibility Regulations 2016
2011/65/EU - Restriction of Hazardous Substances in
Electrical and Electronic Equipment
The Restriction of the Use of Certain Hazardous
Substances in Electrical and Electronic Equipment
Regulations 2012
2.9.2 UKCA declaration of conformity
The declaration of conformity for the product can be requested from KEBA Industrial
Automation Germany GmbH.

14
1 Safety
Operation Manual KeDrive D3-DA BG3 and BG4
1804.200B.1-01 Date: 03/2023
Safety

3 Mechanical installation
3.1 Notes for installation
During the installation work it is imperative you avoid ...
− Drill chippings, screws or other foreign objects falling into the device
− Moisture entering the device
Switch cabinet
− The device is designed only for installation in a stationary switch cabinet. The switch cabinet
must as a minimum provide the degree of protection IP4X. According to ENISO13849-2 the
switch cabinet must have degree of protection IP54 or higher when using the safety functions
(STO and SBC) in the axis controller.
Environment
− The axis controllers must not be installed in areas where they would be permanently exposed
to vibration. You will nd more information in the appendix A.4
Soiling
− Maximum pollution degree 2 in accordance with EN60664-1. You will nd further information
about ambient conditions in the appendix A.4
Effective EMC installation
− To obtain the best result for effective EMC installation you should use a conductive, well-
earthed, chromated or galvanised backing plate.
− If backing plates are varnished, remove the coating from the contact area! The devices
themselves have a chromated zinc frame.
NOTE:
If the axis controller is installed in the axis group it is imperative the operation
manuals for the other devices (supply unit, controller, etc.) are also followed.
3.1.1 Order and arrangement
The following basic guidelines apply to the arrangement and installation of the axis
controller or supply unit:
Butt mounting and alignment
yThe devices can be mounted directly beside each other without any spacing.
They are fastened to the backing plate using screw joints.
yThe 24 V DC control supply must be provided by an external power supply
unit. All devices in the axis group are connected together using the 24 V
busbars. Given the same cooling concept, these connections can be made
without additional compensation measures in relation to device depth.
yDC link busbars are available for the power supply.
yThe devices must be mounted in the stipulated order and one against the
other, see Figure 3.1. A different order is not allowed, as otherwise there
will be problems with the busbars and the thermal interaction between the
devices.
NOTE:
A maximum of 8 communication bus users can be connected to and operated
on a supply unit. A communication group is allowed to consist of a maximum
of 9 bus users.
NOTE:
In the overall axis group, the following DC link capacitance, referred to the total
active power, must be provided:
− 3 x 400 V: ≥ 100 μF/kW
− 3 x 480 V: ≥ 85 μF/kW
− 3 x 230 V: ≥ 170 μF/kW
− 1 x 230 V: ≥ 900 μF/kW
The DC link capacitance is determined by adding together the capacitances
of the supply unit, capacitance module and DC-supplied axis controllers
(see Table A.1). The root mean square of the active power for a load cycle is
dened as the total active power.
15
1 Mechanical installation
Operation Manual KeDrive D3-DA BG3 and BG4
1804.200B.1-01 Date: 03/2023
Mechanical installation

126
7
4
35
1.) KeDrive D3-DU controller
2.) KeDrive D3-DP supply unit BG3
3.) KeDrive D3-DC capacitance module (optional)
4.) KeDrive D3-DA BG4
5.) KeDrive D3-DA BG3
6.) KeDrive D3-DE expansion module
7.) Possible connection of KeDrive D3-DA BG1 and BG2
Figure 3.1 Butt mounting sequence
WARNING! Risk of injury due to hot surfaces on the device (heat sink)!
Carelessness may result in serious burns or damage.
• The device heats up very signicantly during operation and can reach temperatures
of up to 100°C. If touched there is a risk of burns to the skin. For this reason provide
protection against touching.
• Please maintain a sufcient distance from neighbouring assemblies, particularly above
the heat sink.
3.2 Mounting clearances
CAUTION! Damage to the device due to incorrect installation conditions!
The device may suffer irreparable damage if the conditions are not
met.
• The minimum clearances stated in the gure below apply to all devices (KeDrive D3-DU,
KeDrive D3-DP BG3 and BG4 and KeDrive D3-DA BG3 and BG4).
• The clearance above the devices is important to prevent the build-up of heat. The
clearance underneath and at the front is necessary to permit correct cable laying.
≥130
≥250*)
D3-DP BG3 D3-DA BG3
≥300
*) The bending radius of the connection cables must also be taken into account:
Figure 3.2 Mounting clearances, KeDrive D3-DA BG3
16
1 Mechanical installation
Operation Manual KeDrive D3-DA BG3 and BG4
1804.200B.1-01 Date: 03/2023
Mechanical installation

≥130
≥250 *)
≥300
D3-DP BG4 D3-DA BG4
*) The bending radius of the connection cables must also be taken into account
Example:
Motor cable 4 x 70 mm2
-> D = 42 mm (for D3-DA 310/x-A3xx)
(D = outside Ø of the motor cable)
Bending radius (acc. to EN 60332-1-2):
For xed laying 5 x D = approx. 210 mm
to 7 x D = approx. 292 mm
depending on the cable type
Figure 3.3 Mounting clearances, KeDrive D3-DA BG4
NOTE:
It is imperative the min. mounting clearances above and below are met for
thermal reasons. Depending on the connection cables used (mains cable/
motor cable), the mounting clearances may increase signicantly due to the
bending radii necessary.
3.3 Cooling of the devices with air cooling
Cooling air must be able to ow through the device (interior and heat sink) without
restriction. If a thermal cut-out occurs, the cooling conditions must be improved.
Note:
Due to the compact design, the
KeDrive D3 DA axis controllers
are equipped with internal fans for
optimal heat dissipation. The speed
of these fans is set as a function of
the heat sink temperature. The fan
noise may therefore vary depending
on the load.
Figure 3.4 Cooling air ows unhindered through the device
17
1 Mechanical installation
Operation Manual KeDrive D3-DA BG3 and BG4
1804.200B.1-01 Date: 03/2023
Mechanical installation

3.4 Installation of the devices with air cooling
Step Action Comment
1.
Arrange the devices on the backing plate as per Figure
3.1.
Please also provide enough space to the left of the
supply unit for the controller.
Align all devices in a multi-axis group in a line along
the top edge of the devices.
This action is necessary to be able to
couple the DC link using the busbars.
2.
Mark out the position of the tapped holes on the
backing plate.
Drill holes in the backing plate and cut a thread for
each xing screw in the backing plate.
Pay attention to the bending radius of the
connection cables!
For hole spacing and dimensional
drawings see Table 3.1, Figure 3.5 and
Figure 3.6
3. Install the axis controllers vertically and butt mounted
with the supply unit in a row on the backing plate.
The contact surface must be bare metal
and conductive.
You will nd the next steps for the electrical installation
in chapter 4.
18
1 Mechanical installation
Operation Manual KeDrive D3-DA BG3 and BG4
1804.200B.1-01 Date: 03/2023
Mechanical installation

3.4.1 Dimensions (housing with heat sink)
KeDrive D3-DA BG3 BG4
Type
D3-DA 320/A-24xx
D3-DA 320/A-32xx
D3-DA 310/A-45xx
D3-DA 320/A-45xx
D3-DA 310/A-80xx
D3-DA 310/A-A3xx
D3-DA 310/A-B1xx
Mounting method Vertical mounting with unhindered air ow
Side clearance Direct butt mounting
Weight approx. Approx. 13 kg Approx. 20 kg
B (width) 164 274
H (height) 430 430
T/T1 (depth) 251 / 2221) 251 / 2221)
Mounting holes
A 27 27
A1 110 220
C 4.8 4.8
D 80 80
E 98 -
H1 378 378
H2 6 6
H3 390 390
Screws 4 x M4 4 x M4
All dimensions in mm
1) Without terminals and connectors
Table 3.1 Table of dimensions KeDrive D3-DA BG3 and BG4 wall mounting
Dimensional drawings
T
T1
D
H
B
H3
C
A A1
H2H1
E
M10 M6
Figure 3.5 Dimensional drawing, KeDrive D3-DA BG3 (example 1 x 45 A)
C
D
H
B
A1
H3
A
H2H1
T
T1
M10 M6
Figure 3.6 Dimensional drawing, KeDrive D3-DA BG4 (example 1x 210 A)
19
1 Mechanical installation
Operation Manual KeDrive D3-DA BG3 and BG4
1804.200B.1-01 Date: 03/2023
Mechanical installation

3.5 Installation of the devices with liquid
cooling
Step Action Comment
1.
Arrange the devices on the backing plate as per Figure
3.1. Pay attention to the routing of the connections for
the cooling circuit at the rear.
Please also provide enough space to the left of the
supply unit for the controller (KeDrive D3-DU).
Align all devices in a multi-axis group in a line along
the top edge of the devices.
Pay attention to the information in the
chapter "Cooling circuit connection".
This is necessary to be able to supply the
controller with 24 V DC.
This action is necessary for the busbars
for the 24 V DC and the DC link coupling.
2.
Mark out the position of the tapped holes and the pipe
ttings on the backing plate.
Drill holes in the backing plate and cut a thread for
each xing screw in the backing plate.
Pay attention to the bending radius of the
connection cables!
For hole spacing and dimensional
drawings see Table 3.2, Figure 3.7 and
Figure 3.8.
3.
Install the axis controllers vertically and butt mounted
with the supply unit in a row on the backing plate.
While screwing the hose connections (not included in
the scope of supply) into the pipe ttings, lock the pipe
ttings using a 22 mm open-ended wrench to prevent
damage due to the application of torque to the device.
The contact surface must be bare metal
and conductive.
4.
Pay attention to a perfectly sealed connection without
leaks (e.g. using Teon sealing tape).
You will nd further notes on the liquid cooling in
chap. A.9.
You will nd the next steps for the electrical installation
in “4 Electrical installation”.
3.5.1 Dimensions (housing with liquid cooling)
KeDrive D3-DA BG3 BG4
Type
D3-DA 320/C-24xx
D3-DA 320/C-32xx
D3-DA 310/C-45xx
D3-DA 320/C-45xx
D3-DA 310/C-80xx
D3-DA 310/C-A3xx
D3-DA 310/C-B1xx
D3-DA 310/C-C0xx
Mounting method Vertical mounting with unhindered air ow (interior)
Side clearance Direct butt mounting
Weight approx. Approx. 13 kg Approx. 20 kg / 25 kg
B (width) 164 274
H (height) 430 430
T/T1 (depth) 251 / 75.2 251 / 75.2
Mounting holes
A 27 27
A1/ A2 110/ 55 220/ 110
H2/ H3 6/ 378 6/ 378
C diameter 4.8 4.8
D 80 80
D1 35 (bore for pipe tting) 35 (bore for pipe tting)
E 247 247
F 70 70
G 47 102
H1 390 390
Screws 5 x M4 9 x M4
All dimensions in mm
Table 3.2 Table of dimensions KeDrive D3-DA BG3 and BG4 liquid cooling
20
1 Mechanical installation
Operation Manual KeDrive D3-DA BG3 and BG4
1804.200B.1-01 Date: 03/2023
Mechanical installation
This manual suits for next models
1
Table of contents
Other Keba Controllers manuals
Popular Controllers manuals by other brands
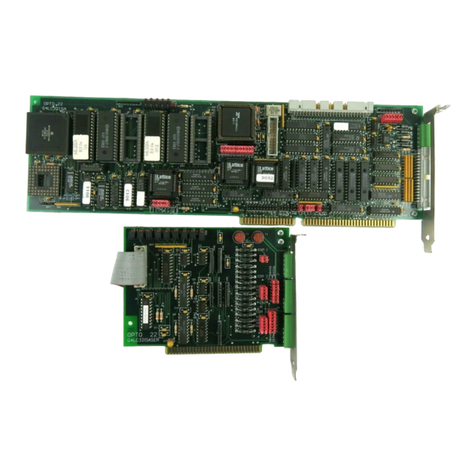
OPTO 22
OPTO 22 G4LC32ISA-LT user guide
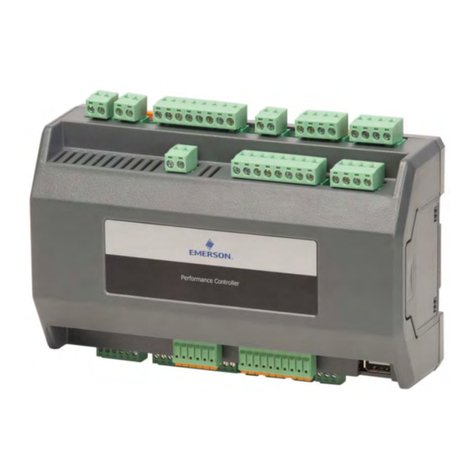
Emerson
Emerson PeC C100 Hardware Implementation Guidelines
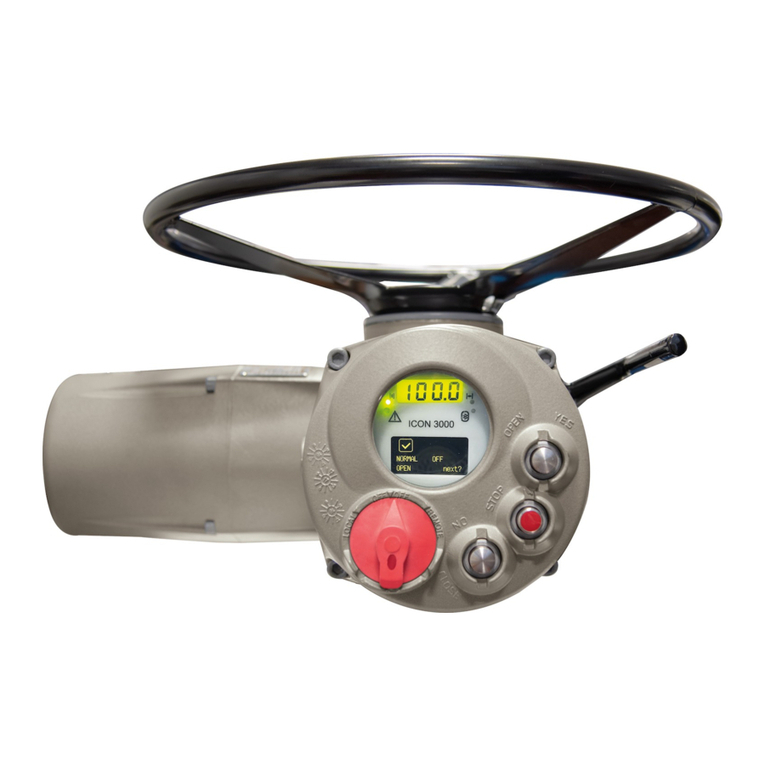
BIFFI
BIFFI ICON3000 Series Advanced Maintenance Instructions
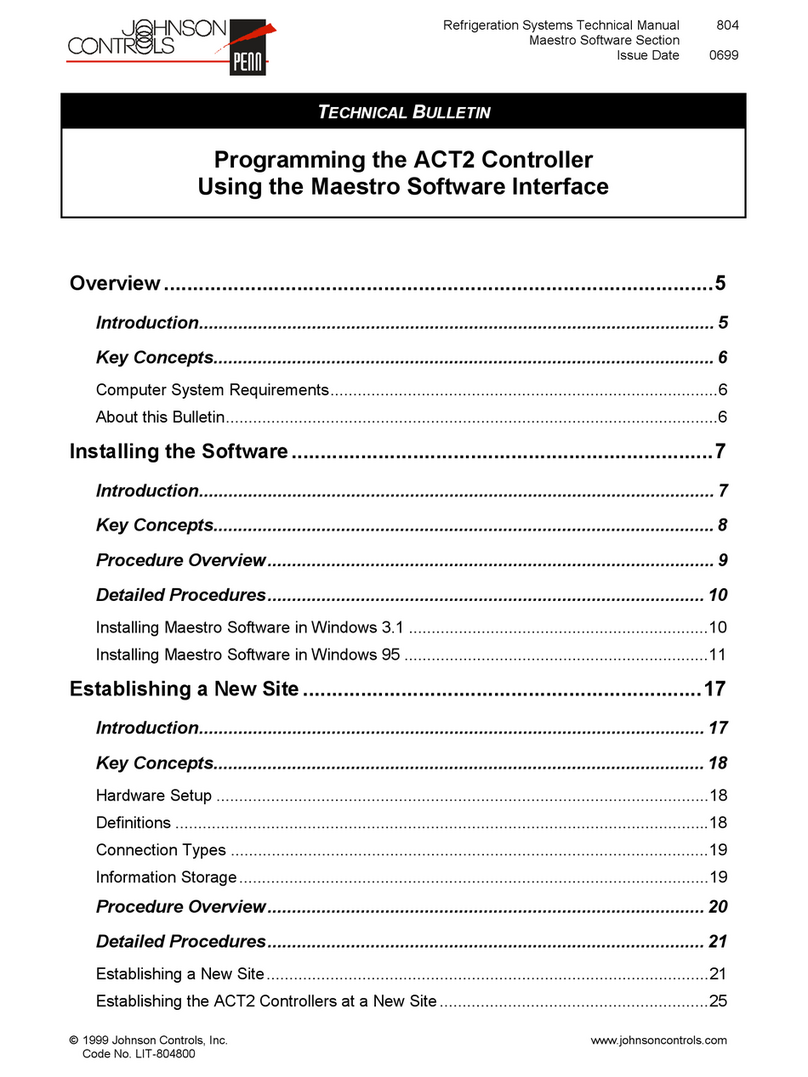
Johnson Controls
Johnson Controls PENN ACT2 Technical bulletin

Beckhoff
Beckhoff KS2791 Documentation
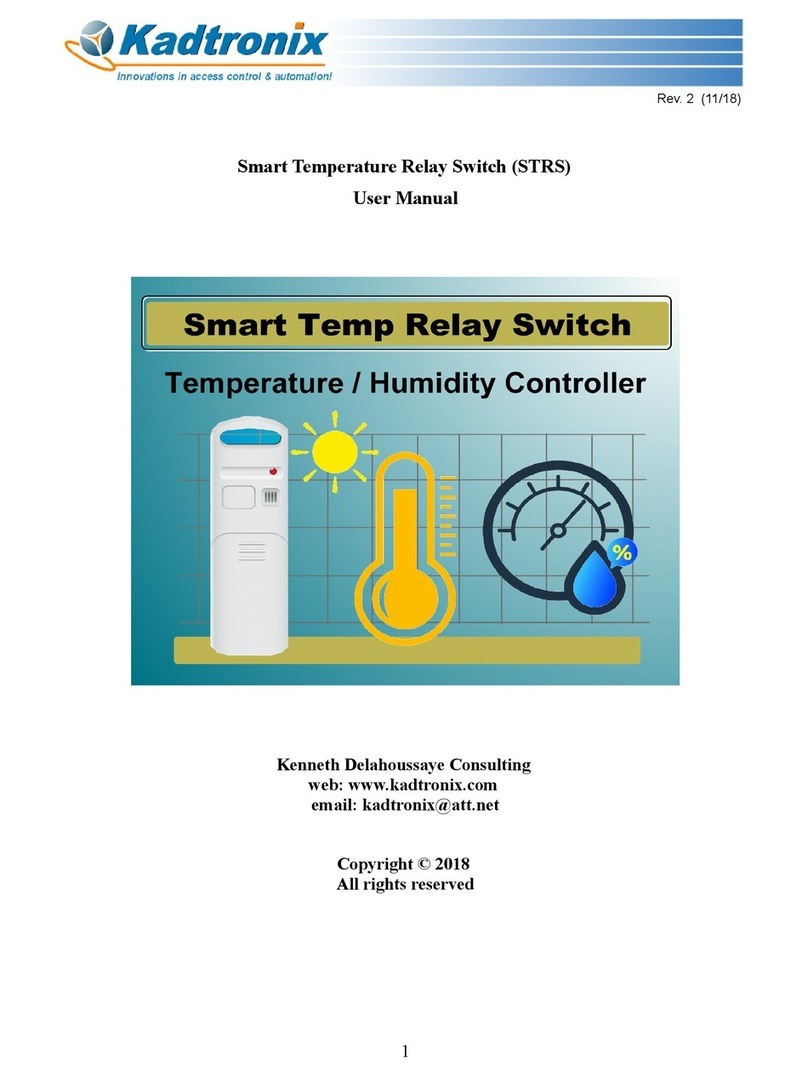
Kadtronix
Kadtronix Smart Temperature Relay Switch user manual

Jandy
Jandy Infinite WaterColors R0979800 installation manual
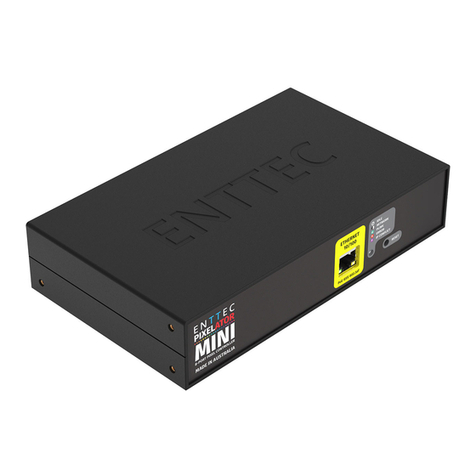
Enttec
Enttec PIXELATOR MINI user manual
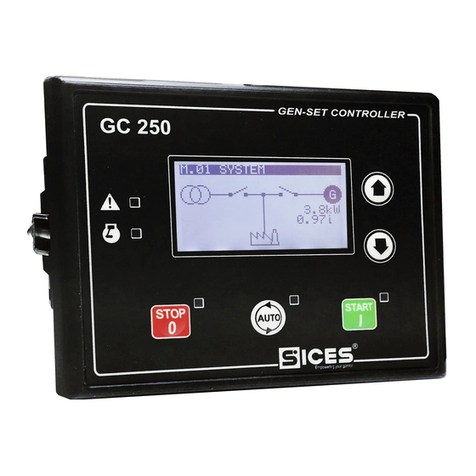
Sices
Sices GC250 Technical manual
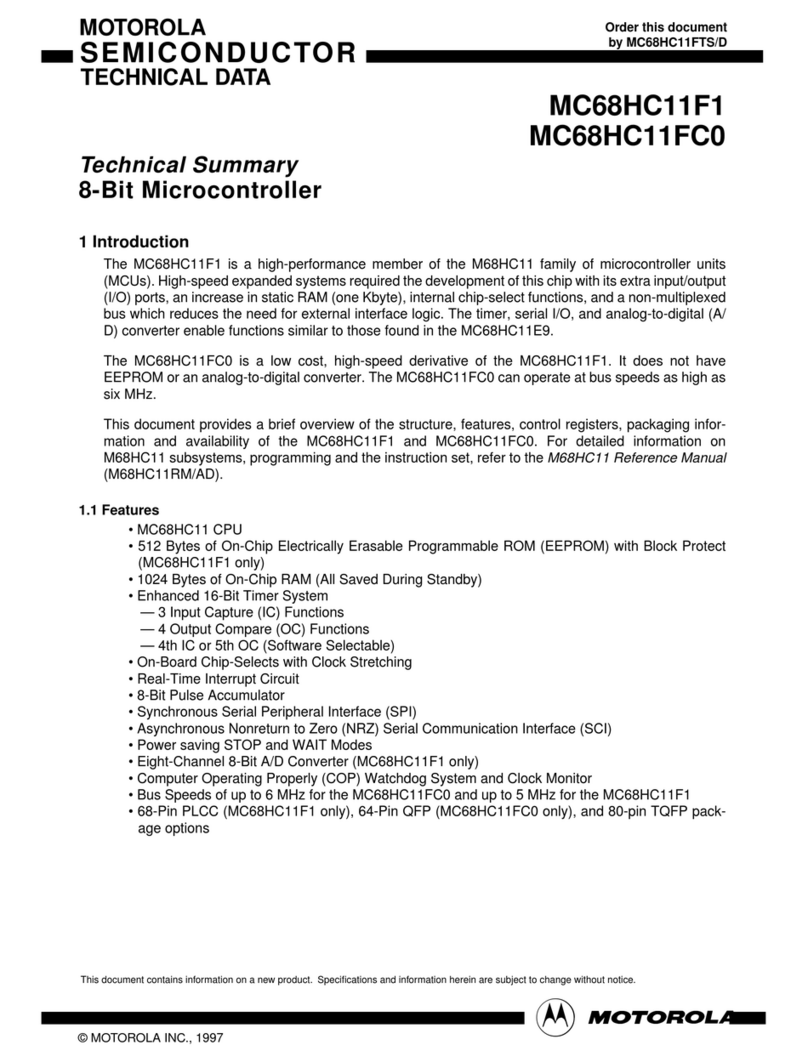
Motorola
Motorola Semiconductor MC68HC11F1 Technical manual

Elsner
Elsner KNX eTR Sunblind Series Installation and adjustment
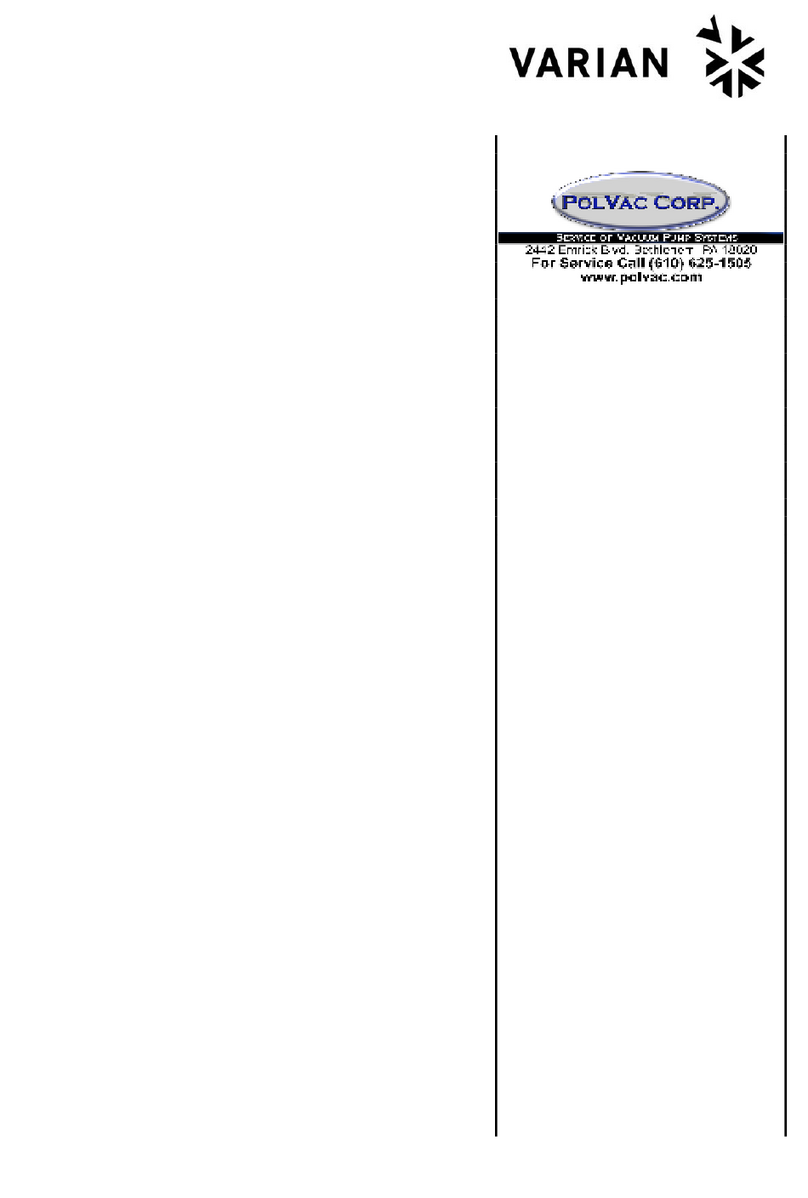
Varian
Varian Turbo-V 300 75 Vdc instruction manual