Koehler K2269X Guide

Operation and Instruction Manual
REV B
Koehler Instrument Company, Inc.
1595 Sycamore Avenue • Bohemia, New York 11716-1796 • USA
Toll Free: 1-800-878-9070 (US only) • Tel: +1 631 589 3800 • Fax: +1 631 589 3815
http://www.koehlerinstrument.com • e-mail: info@koehlerinstrument.com
Petroleum Testing & Analysis Instrumentation • Custom Design & Manufacturing
K2269X
Low Temperature Pressure Viscometer


CERTIFICATE OF CONFORMANCE
Low Temperature Pressure Viscometer
K2269X
This certificate verifies that part number K2269X, Low Temperature Pressure
Viscometer, was manufactured in conformance with the applicable standards set
forth in this certification.
Specifications: ASTM D1092
This unit is tested before it leaves the factory, to ensure total functionality and
compliance to the above specifications and ASTM standards. Test and inspection
records are on file for verification.
Jesse Kelly
Application Engineer
Koehler Instrument Company


K2269X Low Temperature Pressure Viscometer
Operation and Instruction Manual
K2269X-Manual -1-
Table of Contents
1Introduction ...................................................................................................................2
1.1 Koehler’s Commitment to Our Customers .............................................................................................2
1.2 Recommended Resources and Publications.........................................................................................2
1.3 Instrument Specifications.......................................................................................................................2
2Safety Information and Warnings ................................................................................3
3Getting Started...............................................................................................................3
3.1 Packing List............................................................................................................................................3
3.2 Unpacking ..............................................................................................................................................4
3.3 Setup......................................................................................................................................................4
4Description.....................................................................................................................5
4.1 Instrument Descriptions .........................................................................................................................5
4.2 Top Assembly Description .....................................................................................................................5
4.3 Control Box Descriptions........................................................................................................................6
4.4 Gear Box and Motor Descriptions..........................................................................................................7
4.5 Temperature Controller Descriptions.....................................................................................................7
5Operation .......................................................................................................................9
5.1 Refrigerated Test Chamber....................................................................................................................9
5.2 Power.....................................................................................................................................................9
5.3 Calibrate Hydraulic System....................................................................................................................9
5.4 Loading Grease Cylinder .....................................................................................................................11
5.5 Testing Procedure................................................................................................................................12
6Maintenance.................................................................................................................13
6.1 Routine Maintenance...........................................................................................................................13
6.2 Instrument Cleaning.............................................................................................................................13
6.3 Replacement Parts...............................................................................................................................14
7Wiring Diagrams..........................................................................................................15
7.1 220-240V 50Hz Unit Wiring (K22695)..................................................................................................15
8Service..........................................................................................................................16
9Storage.........................................................................................................................16
10 Warranty.......................................................................................................................16
11 Returned Goods Policy...............................................................................................16
Notes..................................................................................................................................17

K2269X Low Temperature Pressure Viscometer
Operation and Instruction Manual
K2269X-Manual -2-
1 Introduction
The Koehler K2269X Low Temperature
Pressure Viscometer is designed to determine the
apparent viscosity of lubricating greases,
adhesives, sealants and other semi-solid products
at low temperatures according to the ASTM D1092
test method.
The pressure viscometer uses a gear pump-
driven hydraulic system to force a sample through
a capillary. The resulting pressure in the system is
measured, and the “apparent viscosity is then
calculated from the flow rate and pressure. Eight
different capillaries and two pump speeds allow for
apparent viscosity determinations at up to sixteen
different shear rates.
This manual provides important information
regarding safety, technical reference, installation
requirements, operating condition specifications,
user facility resource requirements, and operating
instructions for the Pressure Viscometer. This
manual should also be used in conjunction with
applicable published laboratory procedures.
Information on these procedures is given in
section 1.2.
1.1 Koehler’s Commitment to Our
Customers
Providing quality testing instrumentation and
technical support services for research and testing
laboratories has been our specialty for more than
50 years. At Koehler, the primary focus of our
business is providing you with the full support of
your laboratory testing needs. Our products are
backed by our staff of technically knowledgeable,
trained specialists who are experienced in both
petroleum products testing and instrument service
to better understand your requirements and
provide you with the best solutions. You can
depend on Koehler for a full range of accurate and
reliable instrumentation as well as support for your
laboratory testing programs. Please do not
hesitate to contact us at any time with your
inquiries about equipment, tests, or technical
support.
Toll Free: 1-800-878-9070 (US only)
Tel: +1 631 589 3800
Fax: +1 631 589 3815
http://www.koehlerinstrument.com
1.2 Recommended Resources and
Publications
1. American Society for Testing and Materials
(ASTM)
100 Barr Harbor Drive
West Conshohocken, Pennsylvania 19428-
2959, USA
Tel: +1 610 832 9500
Fax: +1 610 832 9555
http://www.astm.org
ASTM Publication:
ASTM D1092: Standard Test Method for
Measuring Apparent Viscosity of
Lubricating Greases
1.3 Instrument Specifications
Models:
K22690
K22695
K22696
Electrical
Requirements:
115V 60Hz
220-240V 50Hz
220-240V 60Hz
Operating Range:
Performs apparent viscosity
determinations at sixteen
different shear rates
Temperature
Range:
Ambient to -65°F (-54°C)
Temperature
Control Precision:
±0.5°F (0.3°C) throughout
the operating range
Test Chamber
Medium:
Dry Denatured Alcohol
Test Chamber
Volume:
20 Gallons (75.71 Liters)
Net Weight:
640 lbs (290.3 kg)
Shipping Weight:
900 lbs (408.2 kg)
Dimensions
(lxwxh,in.(cm)):
43¼ x 30¾ x 66¼
(110x78x168)
Shipping
Dimensions:
89.8 Cu. ft.

K2269X Low Temperature Pressure Viscometer
Operation and Instruction Manual
K2269X-Manual -3-
2 Safety Information and Warnings
Safety Considerations. The use of this
equipment may involve hazardous materials and
operations. This manual does not purport to
address all of the safety problems associated with
the use of this equipment. It is the responsibility of
any user of this equipment to investigate,
research, and establish appropriate safety and
health practices and determine the applicability of
regulatory limitations prior to use.
Equipment Modifications and Replacement
Parts. Any modification or alteration of this
equipment from that of factory specifications is not
recommended voids the manufacturer warranty,
product safety, performance specifications, and/or
certifications whether specified or implied, and
may result in personal injury and/or property loss.
Replacement parts must be O.E.M. exact
replacement equipment.
Unit Design. This equipment is specifically
designed for use in accordance with the applicable
standard test methods listed in section 1.2 of this
manual. The use of this equipment in accordance
with any other test procedures, or for any other
purpose, is not recommended and may be
extremely hazardous.
Chemical Reagents Information. Chemicals and
reagents used in performing the test may exhibit
potential hazards. Any user must be familiarized
with the possible dangers before use. We also
recommend consulting the Material Data and
Safety Sheet (MSDS) on each chemical reagent
for additional information. MSDS information can
be easily located on the internet at
http://siri.uvm.edu or http://www.sigma-
aldrich.com.
3 Getting Started
The instructions for preparing the equipment
assume that the user is aware of the contents of
this document, which lists the warranty conditions
and important precautions.
3.1 Packing List
K2269X Low Temperature Pressure Viscometer
K2269X-Manual Operation and Instruction
Manual
Refer to Figure 1 for an illustration of the included
accessories below:
Set of Interchangeable Pressure Gauges (A)
Consisting of:
- 311-060-005 Pressure Gauge 0-60 psi
- 311-100-004 Pressure Gauge 0-100 psi
- 311-600-004 Pressure Gauge 0-600 psi
- 311-503-001 Pressure Gauge 0-5000 psi
K226-0-22 Set of S/S Capillary No. 1-8 (B)
Consisting of:
- K226-0-22/1 Capillary, #1
- K226-0-22/2 Capillary, #2
- K226-0-22/3 Capillary, #3
- K226-0-22/4 Capillary, #4
- K226-0-22/5 Capillary, #5
- K226-0-22/6 Capillary, #6
- K226-0-22/7 Capillary, #7
- K226-0-22/8 Capillary, #8
K226-0-21 Copper Gasket (Qty 8) (D)
265-000-001 Thermocouple (Qty 3) (E)
K22690-0-27 Grease Cylinder Assembly
(Qty 3) (F)
Includes:
- K22690-0-8 Grease Cylinder Piston
(Qty 3) Packed Separately (C)
K22690-23150 Calibration Pipe Assembly (G)
K22690-23151 Standard Pipe Assembly (H)
K22690-03100 Cylinder Holder Removal Tool (I)
Set of Wrenches and Tools (7 Pieces) (J)
Figure 1. Packing List

K2269X Low Temperature Pressure Viscometer
Operation and Instruction Manual
K2269X-Manual -4-
3.2 Unpacking
1. The K2269X Low Temperature Pressure
Viscometer will ship and arrive in two large
packages:
- Wooden Crate
- Cardboard Box
2. To open the Wooden Crate, a crowbar or
prybar and a hammer will be required. Use the
crowbar and hammer to first open the top of
the crate.
3. Once the entire top piece is removed, observe
inside the crate for the instruments orientation.
Locate the front of the instrument and remove
the corresponding front panel of the wooden
crate.
4. Once the top and front panels of the crate
have been removed it will be easy to remove
the 2x4 supports.
5. Extract the instrument from the crate. The
instrument is equipped for four wheels for
ease of transportation to the work area.
WARNING: Be sure two or more individuals
are available for extracting and lifting instrument
from box to cart and from cart to bench.
Individuals must lift in accordance to proper
technique. See Figure below.
6. Before opening the Cardboard Box, check the
Shock Watch Label on the Box for indication
of rough handling and possible damage.
7. Check labeling for correct orientation of
instrument. (e.g. This Side Up)
8. Carefully open top of box with box cutter and
remove packing foam.
9. Ensure that all parts listed on the packing list
are present. Inspect the unit and all
accessories for damage. If any damage is
found, keep all packing materials and
immediately report the damage to the carrier.
We will assist you with your claim, if
requested. When submitting a claim for
shipping damage, request that the carrier
inspect the shipping container and equipment.
Do not return goods to Koehler without written
authorization.
3.3 Setup
Equipment Placement. Transport the instrument
to a work area with sufficient space to allow for
ease of operation by the user. This unit comes
basically fully assembled, except for the assembly
of the different gauges, pipe assemblies,
capillaries and grease cylinders.
Environmental Conditions: The instrument
environment must comply with the following
conditions for proper setup:
No / Low Dust
No direct sunlight
Not near heating or AC ventilation ducts
No Vibrations
Clearance from other instruments
Temperature Range: 5 to 40°C
Elevation to 2000 meters
Relative Humidity: < 80%
Bath Medium. Fill the refrigerated test chamber
with 20 gallons (75 Liters) of Denatured Ethanol.
Hydraulic Oil. Fill the hydraulic oil reservoir
(Figure 3, item 7) with hydraulic oil to
approximately ¾ of its entire volume.
Power. Connect the line cords to properly fused
and grounded receptacles with the correct voltage
as indicated in section 1.3 or on the back of the
unit.
WARNING: For safety, disconnect the
power when performing any maintenance and/or
cleaning. Do NOT turn the power on unless the
bath is filled with the proper medium; otherwise,
damage may occur to the unit and the warranty
will be void.

K2269X Low Temperature Pressure Viscometer
Operation and Instruction Manual
K2269X-Manual -5-
4 Description
4.1 Instrument Descriptions
Figure 2. Instrument Descriptions_Front
1. Top Assembly. The top assembly of the
apparatus consists of the chamber lid,
Standard Needle Valve, Calibration Needle
Valve, Hydraulic Fluid Cylinder and Grease
Cylinder Chamber. Refer to section 4.2 for
detailed descriptions on this section of the
apparatus.
2. Refrigerated Test Chamber. Provides
environment for apparent viscosity test to be
performed at low temperatures down to -54°C.
3. Receiver Chamber. For collecting grease
sample after being forced through cylinder.
Thermocouple port located here for
connection to RTD probe to measure grease
sample temperature inside cylinder. Chamber
has sufficient work space for interchanging
grease capillaries during testing.
4. Control Box. For control of the refrigeration
and hydraulic system of the apparatus. Refer
to section 4.3 for detailed descriptions.
5. Gear Box and Motor Assembly. This section
of the apparatus contains the gear pump,
gears, drive motor required to power the
hydraulic system. Refer to section 4.4 for
detailed descriptions on this section of the
apparatus.
4.2 Top Assembly Description
Figure 3. Instrument Descriptions_Top
6. Pressure Gauge: Displays pressure required
for hydraulic system to dispense grease or
other sample through capillary. Gauges are
easily interchangeable for pressure
measurements of various magnitudes.
7. Hydraulic Oil Reservoir: For filling,
replenishing or changing hydraulic oil.
Reservoir has clear viewing window that
allows the user to observe the flow of oil
during testing. The top of the reservoir
chamber can be removed easily to fill or
remove hydraulic oil.
8. Left-Hand Needle Valve Knob: Part of dual
valve hydraulic system designed for
continuous flow of hydraulic fluid. Turning left-
hand knob counter-clockwise opens valve and
allows for fluid to flow through the open loop
system. Closing Left-Hand Valve by turning
knob clockwise closes the system loop and
forces the fluid to pressurize grease cylinder.
NOTE: The two valve system (Left and Right-
hand Knobs) must be used in opposition.
When one valve is open, the other must be
closed, and vice-versa.
WARNING: Never close both valves at
the same time as this will result in pressure

K2269X Low Temperature Pressure Viscometer
Operation and Instruction Manual
K2269X-Manual -6-
build-up of the system and rupturing of the
over-pressure emergency valve. Always make
sure opposing valve is in the open position
prior to closing a valve.
9. Refrigerated Chamber Lid. Keep lid in
closed position to maintain temperature
uniformity of the refrigerated chamber.
Remove lid when inserting and removing the
grease cylinder.
10. Right-Hand Needle Valve Knob: Part of dual
valve hydraulic system designed for
continuous flow of hydraulic fluid. Turning
Right-Hand knob counter-clockwise opens
valve and allows for fluid flow to pressurize the
grease cylinder. Closing Right-Hand valve by
turning knob clockwise closes the path to the
grease cylinder and forces the fluid to flow
through the continuous system loop.
NOTE: The two valve system (Left and Right-
hand Knobs) must be used in opposition.
When one valve is open, the other must be
closed, and vice-versa.
WARNING: Never close both valves at
the same time as this will result in pressure
build-up of the system and rupturing of the
over-pressure emergency valve. Always make
sure opposing valve is in the open position
prior to closing a valve.
11. Hydraulic System Connection Port: For
connection to hydraulic system. Quick connect
coupling allows the user to easily connect the
grease cylinder to the hydraulic system. This
port is also used as the main connection point
for the hydraulic system calibration by utilizing
the Calibration Pipe Assembly, See Figure 1,
Item G.
4.3 Control Box Descriptions
Figure 4. Instrument Descriptions_Control Box
12. Compressor Switch. Controls power to
refrigeration system. Turning on the switch will
also power on the lamp in the receiver
chamber as well as the Chamber Temperature
Controller (16) and Sample Temperature
Display (17).
NOTE: When power to the compressor is
turned off, the user must wait for a period of
30 minutes prior to turning the power back on.
This is to prevent any damage to the
compressor.
13. Drive Motor / Circulating Pump Switch.
Turns on both the drive motor which powers
the hydraulic / gear pump as well as the
circulating pump which pushes refrigerant to
the hydraulic / gear pump.
NOTE: It is not necessary to switch on the
Drive Motor / Circulating Pump until the
instrument has reached the proper test
temperature.
14. Reset Button. The gear box cover is
equipped with a safety switch that shuts off
the Drive Motor / Circulating Pump when
opened. If the gear box cover is opened for an
extended period of time the Drive Motor /
Circulating Pump may not automatically be
switched back on when the cover is closed. In
this case, pressing the Reset Button will turn
the Drive Motor / Circulating Pump back on.
15. Gear Switch. Allows for changing drive motor
speed to simulate flow rates attained by 40-
tooth gear and 64-tooth gear as per ASTM
D1092.

K2269X Low Temperature Pressure Viscometer
Operation and Instruction Manual
K2269X-Manual -7-
16. Chamber Temperature Controller. The
temperature controller regulates the chamber
temperature for the test procedure. Set point
temperature is in green and actual
temperature of the chamber is displayed in
red. Refer to Section 4.5 for full operational
details.
17. Sample Temperature Display. For displaying
the sample temperature of the grease during
testing.
4.4 Gear Box and Motor Descriptions
Figure 5. Instrument Descriptions_Gear Box and Motor
18. Gear Box Cover. Protects user from rotating
gears. Lift gear box to access gears for
removal of ice / frost build-up. When gear box
cover is lifted, drive motor will automatically
stop and gears will stop rotating. Upon closing
gear box cover, drive motor and gears should
start up automatically. In the event the system
does not restart, press the red Reset button
located on the control box, See Figure 4, Item
14.
19. Speed Reducer: 200 to 1 ratio speed reducer
is coupled to the drive motor to obtain desired
speed for gears used to power the hydraulic
pump system.
20. Variable Speed Drive Motor: 1/8-hp, 3000
rpm motor is powered on by pressing the
Drive Motor / Circulating Pump switch to the
ON position. See Figure 4, item 13. Variable
Speed Motor is coupled to the speed reducer
and is capable of operating at two speeds
required to simulate flow rates attained by 40-
tooth gear and 64-tooth gear as per ASTM
D1092. Therefore, it is not required to
physically switch gear from 40-tooth to 64-
tooth type and vice-versa.
21. Refrigerant Circulation Piping. Circulating
Pump located in the Refrigerated Test
Chamber pushes refrigerant through the
refrigerant circulating piping, cooling the
hydraulic fluid and gear pump, and flows back
into the Refrigerated Test Chamber.
22. Over-Pressure Valve. In the event, the
pressure of the hydraulic system becomes too
high, the over-pressure valve will burst and
safely release the pressure inside the system.
23. Gear Pump. Pushes hydraulic fluid through
the system. Gear pump is insulated to prevent
loss of cooling from the refrigeration system.
The gear pump must be as close to thermal
equilibrium with the refrigeration system as
possible to properly pump the hydraulic fluid
throughout the system.
24. Gear. Dual gear set is fixed to the speed
reducer and gear pump to provide the proper
flow rate of the hydraulic fluid through the
system. It is not necessary to remove the gear
at any time. The two fluid flow rates required
by the ASTM test method can be obtained by
flipping the Gear Switch on the control box.
See Figure 4, Item 15.
4.5 Temperature Controller Descriptions
Figure 4. Temperature Controller

K2269X Low Temperature Pressure Viscometer
Operation and Instruction Manual
K2269X-Manual -8-
1. Process Temperature Display. The
upper red LED display shows the process
temperature as read from the RTD probe.
2. Set Point Temperature Display. The
lower green LED display shows the set
point temperature of the controller.
3. Programming Key. Permits scrolling
through controller menu parameters. One
Level Forward
4. Down Key. Used to decrease the set
point temperature and to decrease or
change parameter values when
programming the temperature controller.
5. Up Key. Used to increase the set point
temperature and to increase or change
parameter values when programming the
temperature controller.
6. Exit / Function Key. This key is used to
exit or leave a level. One level backward
IMPORTANT NOTE: The digital
temperature controller for the unit comes
pre-programmed from the Koehler factory.
Please do NOT attempt to re-program the
digital temperature controller as this will
void the product warranty. If assistance is
required, please do not hesitate to contact
the Koehler technical service department.
Setting the Temperature. Set the desired
operating temperature by adjusting the set
point with the up and down keys. The set point
will be displayed in the lower green Set Point
LED display and the actual temperature will be
displayed in the upper red Process LED
display. Please allow the instrument to fully
equilibrate before proceeding with any testing.
Temperature Calibration. This routine allows the
digital temperature controller to be calibrated
to a certified thermometer.
a. Use a certified calibrated measuring
device to acquire the temperature.
Calculate the difference between the
measuring device and the Process value
displayed on the controller.
b. Press the program key two times until PCt
is displayed in the lower green LED
display. Press the DOWN key. CAL will
display on the lower green display. If there
is a value observed in the upper red LED
display, add it to the calculated difference
obtained in the previous step. This is the
offset value.
c. Press the Program Key. The lower green
display will flash. Use the up or down keys
to adjust to the new calibration offset
value on the upper red display calculated
in the previous step. When the value has
been entered, the controller will
automatically store the value. The lower
green display will stop flashing. If further
adjustments are necessary, press the
Program Key again. Resume regular
operations by pressing the Exit / Function
key two times. Verify if the new calibration
is correct by observing the upper red
display and comparing the value with the
calibrated reference device.
Auto Tune. This routine allows the digital
temperature control to learn the heating
parameters needed for any particular set point
temperature. This operation should be done
when installing a new unit, after replacing or
changing the bath medium type, or utilizing a
different temperature set point 20% different
from the previously used set point
temperature.
a. Set the operating temperature to the
desired setting.
b. Press the up and down arrow buttons
simultaneously for about 5 seconds. When
Auto Tune is active, the lower green LED
display will blink TUNE. Auto Tune will
automatically toggle off when the set point
temperature is reached. Auto tune can be
terminated by pressing the up & down
buttons simultaneously again.

K2269X Low Temperature Pressure Viscometer
Operation and Instruction Manual
K2269X-Manual -9-
5 Operation
5.1 Refrigerated Test Chamber
Remove the Chamber lid (Figure 3, Item 9) and
fill the test chamber with Dry Denatured Ethanol
as specified in section 1.3. Fill the bath with the
medium to within about 1” (2.54cm) from the top of
the grease cylinder sleeve. Approximately 20
Gallons or 75.71 Liters will be required. Additional
medium may need to be added as fluid is cooled
to appropriate test temperature.
NOTE: Do not attempt moving the bath
when filled with fluid medium. Drain all fluid before
moving or relocating the instrument. Sudden
starting and stopping could result in cold bath fluid
being forcefully ejected from the bath.
5.2 Power
Press on the compressor switch, See Figure 4,
Item 12. This turns on the refrigeration system of
the instrument.
WARNING: Do NOT turn the compressor on
unless the bath is filled with the proper medium;
otherwise, damage may occur to the unit and the
warranty would be void.
Set Chamber Temperature Controller (Figure 4,
Item 16) to desired testing temperature. The
scope of ASTM D1092 covers a testing range
down to -54°C. Refer to section 4.5 for detailed
operation instructions for the temperature
controller.
NOTE: Allow for the test chamber to cool
and come to temperature equilibrium prior to
turning on Drive Motor / Recirculating Pump (See
Figure 4, Item 13). It may take approximately 8
hours for temperature equilibrium at -54°C and
having the gear pump and operating during this
time will only cause unnecessary wear to its
components.
5.3 Calibrate Hydraulic System
Prior to calibrating the hydraulic system, check
and confirm that the hydraulic oil reservoir is filled
with hydraulic oil at least ¾ of its entire volume.
The hydraulic oil in the reservoir will come to
temperature equilibrium with the chamber
temperature during the cooling period.
If the reservoir is not filled with hydraulic oil, fill
the reservoir with the appropriate amount of oil
(3/4 of the reservoir cylinder volume) and allow for
sufficient time for the oil to come to equilibrium
with the chamber temperature.
After the test chamber medium and hydraulic oil
has obtained equilibrium at the desired test
temperature, the hydraulic system must be
calibrated at that temperature.
1. To calibrate the hydraulic system, first connect
the Calibration Piping Assembly (Figure 1,
Item G) to the Hydraulic System Connection
Port (Figure 3, Item 11) using the quick
connect coupling. Refer to Figures 7 and 8
below.
Figure 7. Hydraulic System Connection Port
Figure 8. Calibration Pipe Quick Coupling

K2269X Low Temperature Pressure Viscometer
Operation and Instruction Manual
K2269X-Manual -10-
2. Connect the 5000psi maximum pressure
gauge to the upper connection of the
Calibration Piping Assembly using the quick
connect coupling assembly. See Figure 9:
NOTE: Each of the four pressure gauges
that come equipped with the apparatus are
equipped with quick connect couplings for user
friendly connection and disconnect.
Figure 9. Pressure Gauge Quick Coupling
3. Close Right-Hand Needle Valve. Refer to
Figure 3, Item 10.
4. Open Left-Hand Needle Valve. Refer to
Figure 3, Item 8.
5. Press Gear Switch (Figure 4, Item 15) to
simulate a 40-tooth flow rate.
6. Turn on Drive Motor / Circulating Pump
Switch. Refer to Figure 4, Item 13. The
hydraulic oil will begin circulating through the
system.
NOTE: During operation and while hydraulic oil
is flowing throughout the system the reservoir
volume should be at least ¼ filled with oil.
7. Wait for a period of at least 25-30 minutes for
the oil to completely circulate throughout the
system at the test temperature.
8. Open Right-Hand Needle Valve. Refer to
Figure 3, Item 10.
9. Close Left-Hand Needle Valve. Refer to
Figure 3, Item 8.
10. Observe the hydraulic oil flow as it drips from
the Calibration Piping Assembly exit port. See
Figure 10, Item 26.
NOTE: It is recommended to place a
small collection beaker or towel underneath
the exit port while the hydraulic system is
being primed.
11. Once a steady flow or constant drip rate is
observed, the hydraulic system is primed and
free of air bubbles.
12. Using the relief valve at the right-hand side of
the calibration piping assembly (Figure 10,
Item 25), turn counter-clockwise to completely
open the valve. This allows the system to flow
at atmospheric pressure and will serve as the
reference value (100% free flow delivery) of
the calibration curve vs. pressure, psi.
13. Place a 60-mL Saybolt Receiving Flask
(Figure 10, Item 27) or other receiving device
capable of collecting 60-mL of oil, under the
exit port and start a timer.
14. Determine the delivery time for 60-mL of
hydraulic oil to flow and calculate the flow rate
in cubic centimeters per second assuming 1
mL equal to 1 cm3. Again, this calculated flow
rate is the 100% free flow delivery value on
the calibration curve vs pressure.
15. To obtain additional points for the curve
perform the 60-mL timing observation
sequence at 500, 1000, 1500 psi and at
sufficient pressures above 1500 psi.
16. Turn the relief valve clockwise to increase the
pressure to 500psi, place the 60-mL flask
under the exit port and measure the delivery
time for 60-mL of hydraulic oil to collect.
17. Repeat this procedure for 1000psi, 1500psi
and pressures above to develop a sufficient
calibration curve.
18. Finally, repeat the entire procedure for the
same pressures using the 64-tooth flow rate
by pressing the Gear Switch (Figure 4, Item
15).
19. When Calibration Curve is determined and
sufficient for use, open the Left-Hand Needle
Valve (Figure 3, Item 8) and close the Right-
Hand Needle Valve (Figure 3, Item 10).

K2269X Low Temperature Pressure Viscometer
Operation and Instruction Manual
K2269X-Manual -11-
20. Disconnect the Calibration Piping Assembly
from the Hydraulic System Connection Port
(Figure 3, Item 11).
Figure 10. Calibration Assembly Set up
5.4 Loading Grease Cylinder
During grease cylinder loading procedure
ensure that hydraulic fluid is flowing through the
open system of the apparatus. For this state, the
Left-hand Needle Valve (Figure 3, Item 8) must
be open and the Right-Hand Needle Valve (Figure
3, Item 10) must be closed.
1. Components for assembling and loading the
grease cylinder include:
- Grease Cylinder (F)
- Grease Cylinder Piston (C)
- Thermocouple and Ferrule (E)
- Capillary (B)
- Standard Pipe Assembly (H)
- Pressure Gauge (A)
- Set of Wrenches and Tools (J)
(Refer to Figure 1 for letter designations)
2. Attach Thermocouple Ferrule (E) to bottom
cap of Grease Cylinder (F).
NOTE: Thermocouple Ferrule may
already be attached to grease cylinder bottom
cap for testing purposes. If not attached,
ferrule will be in thermocouple packaging.
3. Remove bottom cap from Grease Cylinder (F).
4. Invert grease cylinder and place Grease
Cylinder Piston (C) inside Grease Cylinder (F).
5. Fill Grease Cylinder with approximately one-
half pound of the grease to be tested in a
manner as to minimize the inclusion of air.
Soft greases may be poured into the cylinder
and heavy samples must be hand packed.
NOTE: Soft greases may also be drawn
up by vacuum. Refer to ASTM D1092, Section
9.1 for details on vacuum procedure.
6. Replace bottom cap with copper gaskets and
tighten with wrenches supplied (J).
7. Attach Standard Pipe Assembly (H) to the top
of the Grease Cylinder (F) and tighten using
the supplied wrench (J).
8. Remove Chamber Lid (Figure 4, Item 9) and
place loaded Grease Cylinder and Standard
Pipe Assembly in sleeve located inside the
refrigerated test chamber. See Figure 11.
Figure 11. Grease Cylinder Placement
9. Replace Refrigerated Chamber Lid
10. Using the quick connect coupling, connect the
Standard Piping Assembly to the Hydraulic
System Connection Port. Refer to Figures 12
and 13.
Figure 12. Standard Piping Connection_1

K2269X Low Temperature Pressure Viscometer
Operation and Instruction Manual
K2269X-Manual -12-
Figure 13. Standard Piping Connection_2
11. Using the quick connect coupling that comes
attached to the pressure gauge, connect a
pressure gauge to the top of the standard
piping assembly. Refer to Figure 9.
NOTE: The proper gauge to be used
depends on the equilibrium pressure
determined by the type of grease during
testing. Generally, it is recommended to begin
with the 5000psi maximum gauge when the
theoretical pressure is unknown so as not to
damage smaller range gauges.
12. Access the Receiver Chamber (Figure 2, Item
3) and insert a thermocouple into the grease
sample through the thermocouple ferrule at
the bottom of the grease cylinder.
13. Connect the Thermocouple port to the Sample
Temperature Display input located in the
Receiver chamber. See Figures 14 and 15.
Once this connection is established the
Sample Temperature Display on the Control
Box will display the grease sample
temperature.
Figure 14. Thermocouple Connection
Figure 15. Thermocouple Connection_Close Up
14. The grease cylinder loading procedure is now
complete. Before attaching a capillary,
changing the flow of the hydraulic fluid and
starting a test, the sample grease must attain
temperature equilibrium with the test chamber.
The time to attain temperature varies with the
grease being tested, however the user should
expect a wait time of approximately 2 hours
prior to equilibrium and start a test.
5.5 Testing Procedure
1. Prior to performing the testing procedure,
confirm that the grease sample temperature
has come to equilibrium with the chamber
temperature.
2. Attach Capillary No. 1 (Figure 1, Item B) to
the bottom of the grease cylinder via the
receiving chamber (Figure 2, Item 3) and
tighten using a wrench provided.
3. Press the Gear Switch (Figure 4, Item 15) to
simulate the 40-tooth gear speed.
4. With the Grease Cylinder properly connected
to the hydraulic system connection point and a
pressure gauge connected to the grease
cylinder assembly the flowing hydraulic fluid
can be redirected to the grease cylinder to
build pressure for testing.
5. Open Right-Hand Needle Valve (Figure 3,
Item 10).
6. Close Left-Hand Needle Valve. (Figure 3,
Item 8).
7. Observe the pressure gauge connected to the
grease cylinder. Pressure will begin to
increase until an equilibrium pressure is
obtained. Record the pressure.

K2269X Low Temperature Pressure Viscometer
Operation and Instruction Manual
K2269X-Manual -13-
NOTE: Dependent on the equilibrium
pressure obtained, it may be necessary to
switch the pressure gauge to a smaller range
for a more accurate reading
8. Press the Gear Switch (Figure 4, Item 15) to
simulate the 64-tooth gear speed.
9. Observe the pressure once again until
equilibrium is established. Record the
pressure.
10. Relieve the pressure to the grease cylinder by
opening the Left-Hand Needle Valve (Figure
3, Item 8) and closing the Right-Hand Needle
Valve (Figure 3, Item 10).
11. Replace the No. 1 capillary with subsequent
ones, No. 2 thru No. 8, and repeat this
procedure until tests have been run with all
capillaries at both flow rates.
NOTE: With some soft or hard greases,
it cannot be practical to use all of the
capillaries.
NOTE: It may be necessary to refill the
cylinder with fresh grease when all 16
determinations are to be made
12. Calculate the apparent viscosity using the
formulas given in the ASTM D1092 test
method.
6 Maintenance
WARNING: Disconnect power to the unit
before servicing to avoid exposure to high
voltages and/or temperatures which may result in
personal injury or death. If you have any questions
about maintaining your equipment, then please do
not hesitate to contact the Koehler technical
service department.
6.1 Routine Maintenance
The K2269X Low Temperature Pressure
Viscometer requires little routine maintenance to
provide many years of continuous service.
However, over the course of time, some
instrument parts may need to be replaced. When
ordering replacement part(s), please provide the
model number, serial number, and product
shipment date of your equipment so that we can
ensure you will receive the proper replacement
part(s).
6.2 Instrument Cleaning
To clean the instrument’s exterior, which
includes all painted surfaces, either a solution
of soap and water or laboratory grade
detergent may be used.
Apply cleaner to clean wipe or cloth, not to the
instrument directly. Wipe surface clean.
Do Not clean bath exterior with organic
chemicals such as Acetone, Toluene, Hexane,
etc.
For more difficult cleaning of finished surfaces,
a dilute solution or isopropanol in water may
be used.
It is not recommended that more aggressive
solvents be used on painted surfaces since
paint color will tarnish or be stripped from the
instrument.
Stainless Steel surfaces, such as the
refrigerated test chamber, may be cleaned
using a more aggressive solvent such as a
stainless steel cleaner.

K2269X Low Temperature Pressure Viscometer
Operation and Instruction Manual
K2269X-Manual -14-
6.3 Replacement Parts
Part Number
Description
091-032-001
Relay, Solid State, 4-32VDC, 20A
278-001-002
Fuse, 1A, Slo-Blo, 5 X 20 MM
278-020-004
Fuse, 20A, 600VAC, Time Delay
278-104-002
Fuse,.25A Slo-Blo 5X20 M.M.
220-240-013
Cartridge Heater, 500W, 240V
265-500-001
RTD Temperature Probe ¼” x 12”
275-103-044
Temperature Controller,100-240V
288-230-018
Motor, 208-230V, 3 Phase
288-230-020
Motor, 230V, 1/8HP,3000RPM
356-001-003
Gear Pump
360-230-007
Motor Controller, 220V Var. Freq.
K226-0-13
Gear Reducer
K226-0-8A
Gear, 40-Tooth (60Hz)
K226-0-8B
Gear, 64-Tooth (60Hz)
K22690-0-6
Filter Screen
K22690-0-7
Hydraulic Fluid Reservoir
K22752-03024
Stirrer Shaft

K2269X Low Temperature Pressure Viscometer
Operation and Instruction Manual
K2269X-Manual -15-
7 Wiring Diagrams
7.1 220-240V 50Hz Unit Wiring (K22695)

K2269X Low Temperature Pressure Viscometer
Operation and Instruction Manual
K2269X-Manual -16-
8 Service
Under normal operating conditions and with
routine maintenance, the K2269X Low
Temperature Pressure Viscometer should not
require service. Any service problem can be
quickly resolved by contacting Koehler’s technical
service department either by letter, phone, fax, or
email. In order to assure the fastest possible
service, please provide us with the following
information.
Model Number:
Serial Number:
Date of Shipment:
9 Storage
This laboratory test instrument is equipped with
electrical components. Storage facilities should be
consistent with an indoor laboratory environment.
This testing equipment should not be subjected to
extremes of temperature and/or moisture.
This equipment was shipped from the factory in
a corrugated cardboard container. If long term
storage is anticipated, re-packing the instrument in
a water-resistant container is recommended to
ensure equipment safety and longevity.
10 Warranty
We, at Koehler, would like to thank you for your
equipment purchase, which is protected by the
following warranty. If within one (1) year from the
date of receipt, but no longer than fifteen (15)
months from the date of shipment, Koehler
equipment fails to perform properly because of
defects in materials or workmanship, Koehler
Instrument Company, Inc. will repair or, at its sole
discretion, replace the equipment without charge
F.O.B. its plant, provided the equipment has been
properly installed, operated, and maintained.
Koehler Instrument Company must be advised in
writing of the malfunction and authorize the return
of the product to the factory. The sole
responsibility of Koehler Instrument Company and
the purchaser’s exclusive remedy for any claim
arising out of the purchase of any product is the
repair or replacement of the product. In no event
shall the cost of the purchaser’s remedy exceed
the purchase price, nor shall Koehler Instrument
Company be liable for any special, indirect,
incidental, consequential, or exemplary damages.
KOEHLER INSTRUMENT COMPANY, INC.
DISCLAIMS ALL OTHER WARRANTIES,
EXPRESSED OR IMPLIED, INCLUDING ANY
IMPLIED WARRANTIES OF FITNESS FOR A
PARTICULAR PURPOSE. Please save the
shipping carton in the event the equipment needs
to be returned to the factory for warranty repair. If
the carton is discarded, it will be the purchaser’s
responsibility to provide an appropriate shipping
carton.
11 Returned Goods Policy
To return products for credit or replacement,
please contact Koehler Customer Service with
your purchase order number, our packing
list/invoice number, the item(s) to be returned and
the reason for the return. You will be issued a
Returned Authorization (RA) number, which must
be prominently displayed on the shipping
container when you return the material to our
plant. Shipping containers without an RA number
prominently displayed with be returned to the
sender. Goods must be returned freight prepaid.
Returns will be subject to a restocking charge, the
application of which will depend upon the
circumstances necessitating the return. Some
returns cannot be authorized, including certain
products purchased from outside vendors for the
convenience of the customer, products
manufactured on special order, products shipped
from the factory past ninety (90) days, and
products which have been used or modified in
such a way that they cannot be returned to stock
for future sale.
Table of contents
Other Koehler Measuring Instrument manuals
Popular Measuring Instrument manuals by other brands
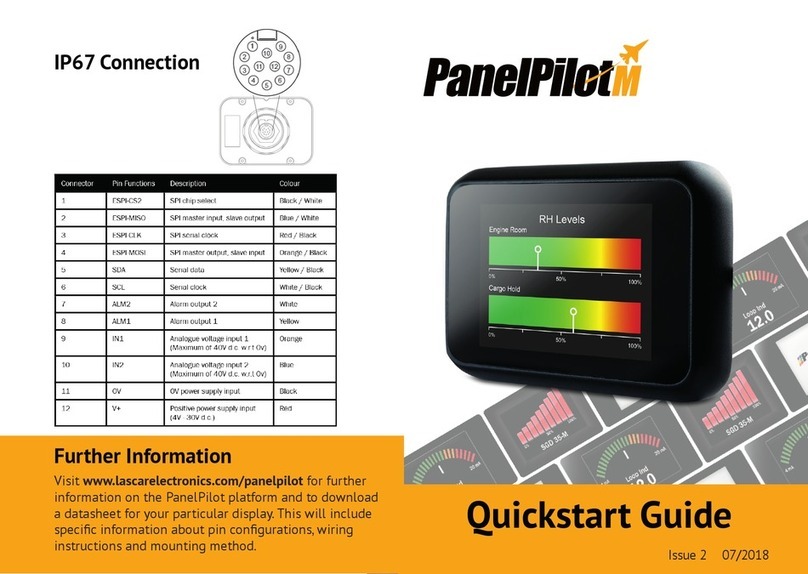
Lascar Electronics
Lascar Electronics PanelPilot SGD 24-M-IP quick start guide
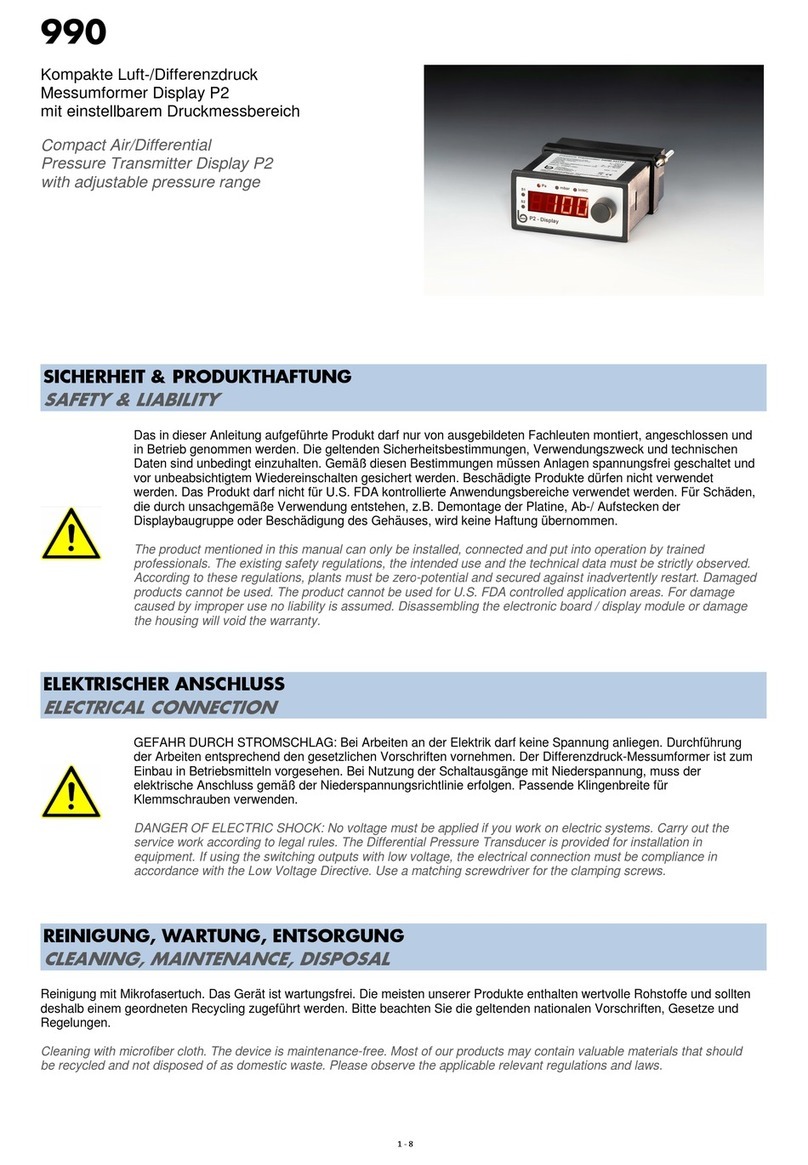
Beck
Beck 990 Series manual
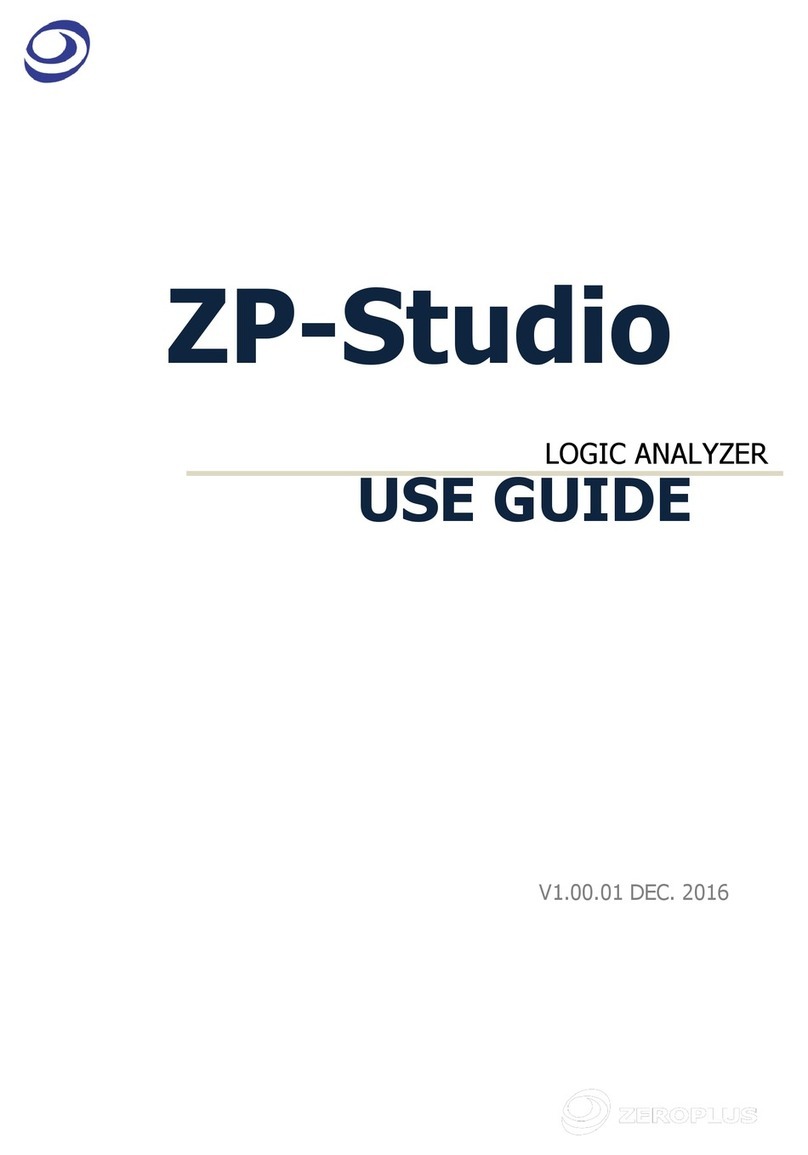
Zeroplus
Zeroplus ZP-Studio user guide
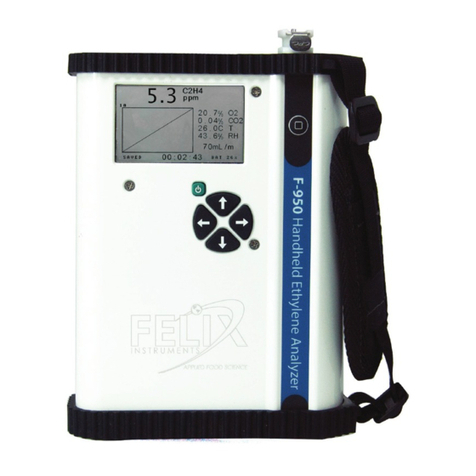
Felix Storch
Felix Storch F-950 Operation manual
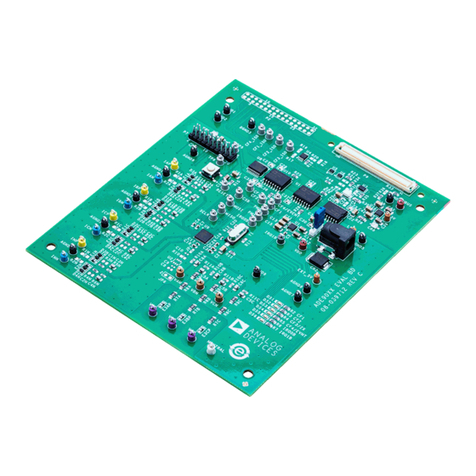
Analog Devices
Analog Devices ADE9000 Technical reference manual
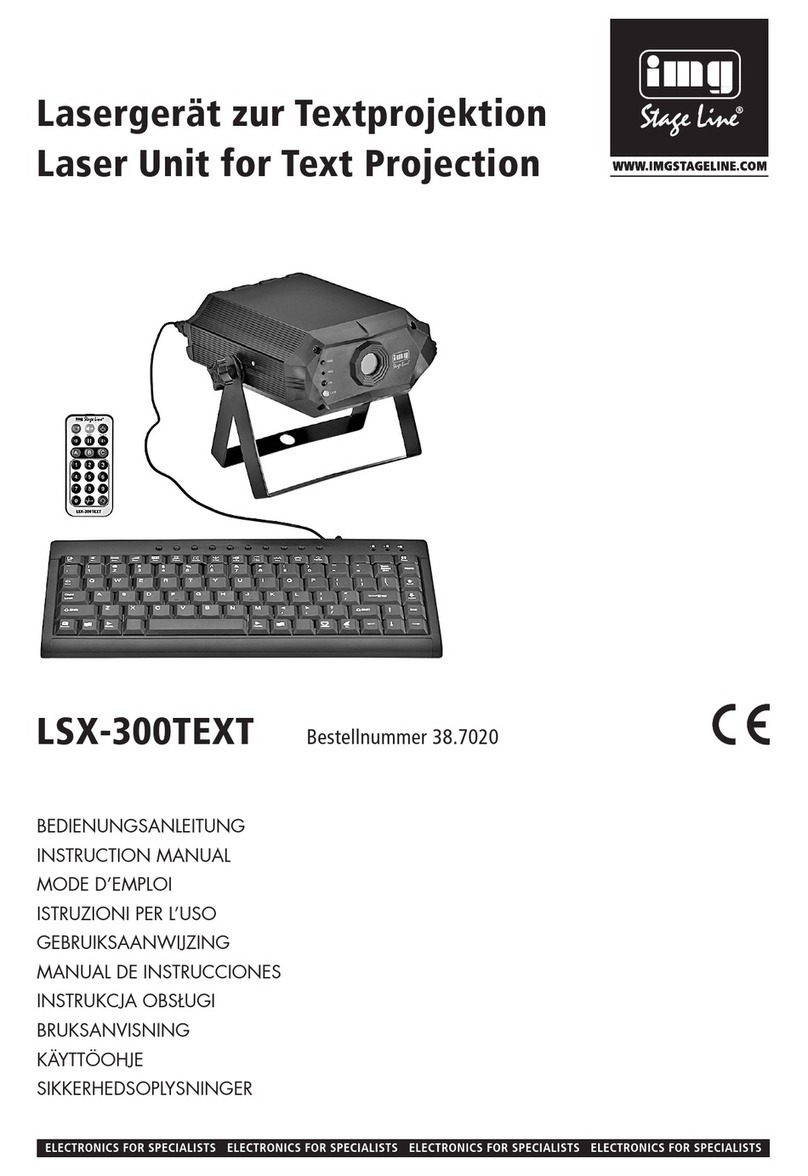
IMG STAGE LINE
IMG STAGE LINE LSX-300TEXT instruction manual