MG R7K4FML-6-DC32B User manual

EM-7771-D Rev.2 P. 1 / 8
MG CO., LTD. www.mgco.jp
5-2-55 Minamitsumori, Nishinari-ku, Osaka 557-0063 JAPAN
INSTRUCTION MANUAL
BEFORE USE ....
Thank you for choosing us. Before use, please check con-
tents of the package you received as outlined below.
If you have any problems or questions with the product,
please contact our sales office or representatives.
■PACKAGE INCLUDES:
Discrete output module ......................................................(1)
Mounter slider ....................................................................(2)
■MODEL NO.
Confirm Model No. marking on the product to be exactly
what you ordered.
■INSTRUCTION MANUAL
This manual describes necessary points of caution when
you use this product, including installation, connection and
basic maintenance procedures.
POINTS OF CAUTION
■CONFORMITY WITH EU DIRECTIVES
• The equipment must be mounted inside the instrument
panel of a metal enclosure.
• The actual installation environments such as panel con-
figurations, connected devices, connected wires, may af-
fect the protection level of this unit when it is integrated
in a panel system. The user may have to review the CE
requirements in regard to the whole system and employ
additional protective measures to ensure the CE conform-
ity.
■POWER INPUT RATING & OPERATIONAL RANGE
• Locate the power input rating marked on the product and
confirm its operational range as indicated below:
24V DC rating: 24V ±10%, approx. 60mA
■GENERAL PRECAUTIONS
• Before you remove the unit or mount it, turn off the power
supply and output signal for safety.
• Before you remove the terminal block or mount it, make
sure to turn off the power supply and output signal for
safety.
• DO NOT set the switches on the module while the power
is supplied. The switches are used only for maintenance
without the power.
■ENVIRONMENT
• Indoor use.
• When heavy dust or metal particles are present in the
air, install the unit inside proper housing with sufficient
ventilation.
• Do not install the unit where it is subjected to continuous
vibration. Do not subject the unit to physical impact.
• Environmental temperature must be within 0 to 55°C (32
to 131°F) with relative humidity within 30 to 90% RH in
order to ensure adequate life span and operation.
■WIRING
• Do not install cables close to noise sources (relay drive
cable, high frequency line, etc.).
• Do not bind these cables together with those in which
noises are present. Do not install them in the same duct.
• Be sure to close the terminal cover for safety.
■AND ....
• The unit is designed to function as soon as power is sup-
plied, however, a warm up for 10 minutes is required for
satisfying complete performance described in the data
sheet.
MECHATROLINK I/O MODULE
(PNP transistor output, 32 points, screw terminal block,
MECHATROLINK-I/-II use)
MODEL
R7K4FML-6-DC32B

R7K4FML-6-DC32B
EM-7771-D Rev.2 P. 2 / 8
MG CO., LTD. www.mgco.jp
5-2-55 Minamitsumori, Nishinari-ku, Osaka 557-0063 JAPAN
COMPONENT IDENTIFICATION
4567
123
28 29 30 31
20 21 2219
33 34 35 36
25 26 27
24
32
23
10 11 12 13
2341
15 16 17 18
789
6
14
5
1
×10 ×1
234
ON
STATION ADD.
PWR RDERR
SD
Y0 1234567
Y8 91011 12 13 14 15
Y16171819 20 21 22 23
Y24252627 28 29 30 31
MECHATROLINK
Connector
Station Address Setting
Rotary SW
Status Indicator LED
Operating Mode Setting DIP SW (SW1)
Discrete Output Status Indicator LED
Power Supply Terminals Ouput Terminals
■STATUS INDICATOR LED
ID COLOR FUNCTION
PWR Green Turns on when the internal
power is supplied normally.
ERR Red Turns on in no station ad-
dress setting error.
SD Green Turns on when the module is
transmitting.
RD Green Turns on when the module is
receiving.
■DISCRETE OUTPUT STATUS INDICATOR LED
LED green indicators shows the signal status.
ON : LED ON
OFF : LED OFF
■STATION ADDRESS
Station Address is selected between 60H and 7FH (Simple
I/O) in hexadecimal.
The left switch and the right switch determine the MSD
and the LSD of the address, respectively.
(Factory setting: 61H)
Certain numbers may not be selectable depending on the
master types.
Refer to the instruction manual of the master unit for de-
tail.
Station Address Setting (×1)
Station Address Setting (×10)
0
1
2
3
4
5
6
7
8
9
A
B
C
D
E
F
0
1
2
3
4
5
6
7
8
9
A
B
C
D
E
F
■OPERATING MODE
• MECHATROLINK mode: SW1-1, 1-2
Choose MECHATROLINK-I or -II, and the data size.
SW1-1 and SW1-2 are used.
SW1-1 SW1-2 MECHATROLINK MODE
OFF OFF MECHATROLINK-II (32 byte mode) (*)
ON OFF MECHATROLINK-II (17 byte mode)
ON ON MECHATROLINK-I (17 byte mode)
(*) Factory setting
Note: Be sure to set unused SW1-3 and 1-4 to OFF.
4
NC
567
123
NC
+
24V
0V
NC NC FE
1. NC
2. NC
3. FE
4. NC
5. NC
6. +24V
7. 0V
-
-
Functional earth
-
-
Power supply (24V DC)
Power supply (0V)
■POWER SUPPLY TERMINAL ASSIGNMENT

R7K4FML-6-DC32B
EM-7771-D Rev.2 P. 3 / 8
MG CO., LTD. www.mgco.jp
5-2-55 Minamitsumori, Nishinari-ku, Osaka 557-0063 JAPAN
■OUTPUT TERMINAL ASSIGNMENT
14
56
Y7
Y6 Y8
15
Y9
16 17 18
789
Y11 Y13 Y15
Y10 Y12
10
12
V
+
V
-
Y0
11
Y1
12 13
34
Y3 Y5
Y2 Y4 Y14
32
23 24
Y23
Y22 Y24
33
Y25
34 35 36
25 26 27
Y27 Y29 Y31
Y26 Y28
28
19 20
V+
V
-
Y16
29
Y17
30 31
21 22
Y19 Y21
Y18 Y20 Y30
NO. ID FUNCTION NO. ID FUNCTION
1 V– Out. Common 10 V+ External excitation
2 Y0 Output 0 11 Y1 Output 1
3 Y2 Output 2 12 Y3 Output 3
4 Y4 Output 4 13 Y5 Output 5
5 Y6 Output 6 14 Y7 Output 7
6 Y8 Output 8 15 Y9 Output 9
7 Y10 Output 10 16 Y11 Output 11
8 Y12 Output 12 17 Y13 Output 13
9 Y14 Output 14 18 Y15 Output 15
NO. ID FUNCTION NO. ID FUNCTION
19 V– Out. Common 28 V+ External excitation
20 Y16 Output 16 29 Y17 Output 17
21 Y18 Output 18 30 Y19 Output 19
22 Y20 Output 20 31 Y21 Output 21
23 Y22 Output 22 32 Y23 Output 23
24 Y24 Output 24 33 Y25 Output 25
25 Y26 Output 26 34 Y27 Output 27
26 Y28 Output 28 35 Y29 Output 29
27 Y30 Output 30 36 Y31 Output 31
MOUNTING INSTRUCTIONS
■DIN RAIL MOUNTING
• Mounting
1) Set the upper hook at the rear side of the unit on the DIN
rail.
2) Push in the lower.
1
2
• Dismounting
1) Push down the DIN rail mounter slider with tip of a mi-
nus screwdriver.
2) Pull the lower of the unit.
3) Remove the upper hook of the unit from the DIN rail.
1
1
2
3
■SURFACE MOUNTING
1) Insert the two DIN rail mounter sliders until it clicks
once, as shown below.
1
1
2) Mount the unit with M4 screws referring the Mounting
Requirements. (Torque: 1.4 N·m)

R7K4FML-6-DC32B
EM-7771-D Rev.2 P. 4 / 8
MG CO., LTD. www.mgco.jp
5-2-55 Minamitsumori, Nishinari-ku, Osaka 557-0063 JAPAN
TERMINAL CONNECTIONS
Connect the unit as in the diagram below.
■EXTERNAL DIMENSIONS unit: mm (inch)
DIN RAIL
35mm wide
[4 (.16)]
50 (1.97)
3.5 (.14)5(.2)
210 (8.27)
220 (8.66)
235 (9.25)
47 (1.85)
45 (1.77)
6
36−M3 SCREW
TERMINALS FOR OUTPUT
4567
123
6
7−M3 SCREW
TERMINALS FOR POWER
28 29 30 31
20 21 2219
33 34 35 36
25 26 27
24
32
23
10 11 12 13
2341
15 16 17 18
789
6
14
5
2
-
4.3 dia.
4 deep
(2
-
1.17 dia.
.16 deep)

R7K4FML-6-DC32B
EM-7771-D Rev.2 P. 5 / 8
MG CO., LTD. www.mgco.jp
5-2-55 Minamitsumori, Nishinari-ku, Osaka 557-0063 JAPAN
■CONNECTION DIAGRAM
Note: In order to improve EMC performance, bond the FE
terminal to ground.
Caution: FE terminal is NOT a protective conductor terminal.
10
36
19
2
V+
28
V+
V–
1
V–
Y31
■ Output Connection Examples
*MECHATROLINK connectors are internally connected.
The network cable can be connected to either one.
Y0
−+
1
5
10
2
6
4
7
13
8
9
14
12
15
11
16
17
18
V–
V+
Y2
Y4
Y6
Y8
Y10
Y12
Y14
Y1
Y15
Y3
Y5
Y7
Y9
Y11
Y13
Y0
3
19
23
28
20
24
22
25
31
26
27
32
30
33
29
34
35
36
21
6
7
24V DC
0V
3
FE
V–
V+
Y18
Y20
Y22
Y24
Y26
Y28
Y30
Y17
Y31
Y19
Y21
Y23
Y25
Y27
Y29
Y16
*
MECHATROLINK
CONNECTOR
*
MECHATROLINK
CONNECTOR
MOUNTING REQUIREMENTS unit: mm (inch)
220 (8.66)
2–M4
WIRING INSTRUCTIONS
■TORQUE
Wiring screw for separable terminal: 0.5 N∙m
Fixing screw for separable terminal: 0.5 N∙m
■SOLDERLESS TERMINAL
Refer to the drawing below for recommended ring tongue
terminal size. Spade tongue type is also applicable.
Applicable wire size: 0.25 to 1.65 mm2(AWG 22 to 16)
Recommended manufacturer: Japan Solderless Terminal
MFG. Co., Ltd, Nichifu Co., Ltd
6 (.24) max
3.3 (.13) max
mm (inch)
■HOW TO UNMOUNT THE SEPARABLE TERMINAL
The separable terminal of the unit is 2 piece constructions.
It is possible to remove the terminal by loosening two screws
of terminal alternately.

R7K4FML-6-DC32B
EM-7771-D Rev.2 P. 6 / 8
MG CO., LTD. www.mgco.jp
5-2-55 Minamitsumori, Nishinari-ku, Osaka 557-0063 JAPAN
COMMUNICATION CABLE CONNECTIONS
■MECHATROLINK CONNECTION
SRD
+
SRD
–
SLD
Master
termi-
nator
termi-
nator
* Terminator
Be sure to connect the terminating resistors to the unit at both ends of transmission line.
Use the terminating resistor dedicated for MECHATROLINK: Model JEPMC-W6022, Yaskawa Controls Co., Ltd.
Certain types of Master units may have incorporated terminating resistors. Consult the instruction manual for the Master.
SRD
+
SRD
–
SLD
SRD
+
SRD
–
SLD
Slave
SRD
+
SRD
–
SLD
SRD
+
SRD
–
SLD
Slave
SRD
+
SRD
–
SLD
MECHATROLINK
Cable
MECHATROLINK
Cable
* *
MECHATROLINK COMMUNICATION
■MECHATROLINK-I
Baud rate: 4 Mbps
Transmission distance: 50 m max.
Distance between stations: 30 cm min.
Transmission media: MECHATROLINK cable (Model JEPMC-W6003-x-E, Yaskawa Controls Co., Ltd.)
Max. number of slaves: 15 (The maximum number of slaves might change depending on the master unit. Refer to the
manual of the master unit.)
Transmission cycle: 2 msec. (fixed)
Data length: 17 byte
■MECHATROLINK-II
Baud rate: 10 Mbps
Transmission distance: 50 m max.
Distance between stations: 50 cm min.
Transmission media: MECHATROLINK cable (Model JEPMC-W6003-x-E, Yaskawa Controls Co., Ltd.)
Max. number of slaves: 30 (The maximum number of slaves might change depending on the master unit. Refer to the
manual of the master unit.)
Transmission cycle: 0.25 msec., 0.5 msec., 1 msec., 1.5 msec., 2 msec., 4 msec., 8 msec.
Data length: 17 bytes / 32 bytes selectable (Must choose identical data size for all stations on the same network)

R7K4FML-6-DC32B
EM-7771-D Rev.2 P. 7 / 8
MG CO., LTD. www.mgco.jp
5-2-55 Minamitsumori, Nishinari-ku, Osaka 557-0063 JAPAN
MECHATROLINK RELATED COMMANDS
R7K4FML (Simple I/O) communicates with I/O service with no processor, therefore it uses a connectionless communication
protocol. There is no application layer either; the R7K4FML interchanges I/O data via data link layer.
■MECHATROLINK DATA LINK LAYER COMMAND DESCRIPTIONS
The following tables explain the two Commands supported by the R7K4FML.
• MDS Command (04H) Data Format
BYTE COMMAND RESPONSE REMARKS
0 MDS (04H) S(0) (90H) Message Data Search (MDS) Command: Read the ID from slave station(s)
S(0): Response to MDS
1 0 ID
2 0
3 0 0 All 0
4 0 0
5 0 0
6 0 0
7 0 0
8 0 0
9 0 0
10 0 0
11 0 0
12 0 0
13 0 0
14 0 0
15 0 0
16 0 0
17
:
31
0
:
0
0
:
0
Byte 17 through 31 are always 0 in the 32-byte mode.
These bytes are unavailable for MECHATROLINK-I and
MECHATROLINK-II in the 17-byte mode.
• CDRW Command (03H) Data Format
BYTE COMMAND RESPONSE REMARKS
0 CDRW (03H) ACK (01H) Cyclic Data Read/Write (CDRW) Command: Link transmission
Acknowledge (ACK): Positive response to CDRW
1 Out Data: Lowest In Data: Lowest Order of data: Little Endian
2
3
4
5
6
7
8
9
10
11
12
13
14
15
16 Out Data: Highest In Data: Highest
17
:
31 (Out Data: Highest) (In Data: Highest)
Byte 17 through 31 are unavailable for MECHATROLINK-I and
MECHATROLINK-II in the 17-byte mode.
(Only available for MECHATROLINK-II in the 32-byte mode)

R7K4FML-6-DC32B
EM-7771-D Rev.2 P. 8 / 8
MG CO., LTD. www.mgco.jp
5-2-55 Minamitsumori, Nishinari-ku, Osaka 557-0063 JAPAN
I/O DATA DESCRIPTIONS
■17-BYTE MODE
• 32 points output data (Out Data)
Byte Bit7 Bit6 Bit5 Bit4 Bit3 Bit2 Bit1 Bit0
100000000
200000000
300000000
400000000
500000000
:
:00000000
1200000000
13 Out7 Out6 Out5 Out4 Out3 Out2 Out1 Out0
14 Out15 Out14 Out13 Out12 Out11 Out10 Out9 Out8
15 Out23 Out22 Out21 Out20 Out19 Out18 Out17 Out16
16 Out31 Out30 Out29 Out28 Out27 Out26 Out25 Out24
■32-BYTE MODE
• 32 points output data (Out Data)
Byte Bit7 Bit6 Bit5 Bit4 Bit3 Bit2 Bit1 Bit0
100000000
200000000
300000000
400000000
500000000
:
:00000000
2800000000
29 Out7 Out6 Out5 Out4 Out3 Out2 Out1 Out0
30 Out15 Out14 Out13 Out12 Out11 Out10 Out9 Out8
31 Out23 Out22 Out21 Out20 Out19 Out18 Out17 Out16
32 Out31 Out30 Out29 Out28 Out27 Out26 Out25 Out24
0: OFF, 1: ON
At the loss of communication, output is hold (last data correctly received is hold).
Table of contents
Other MG Control Unit manuals
Popular Control Unit manuals by other brands
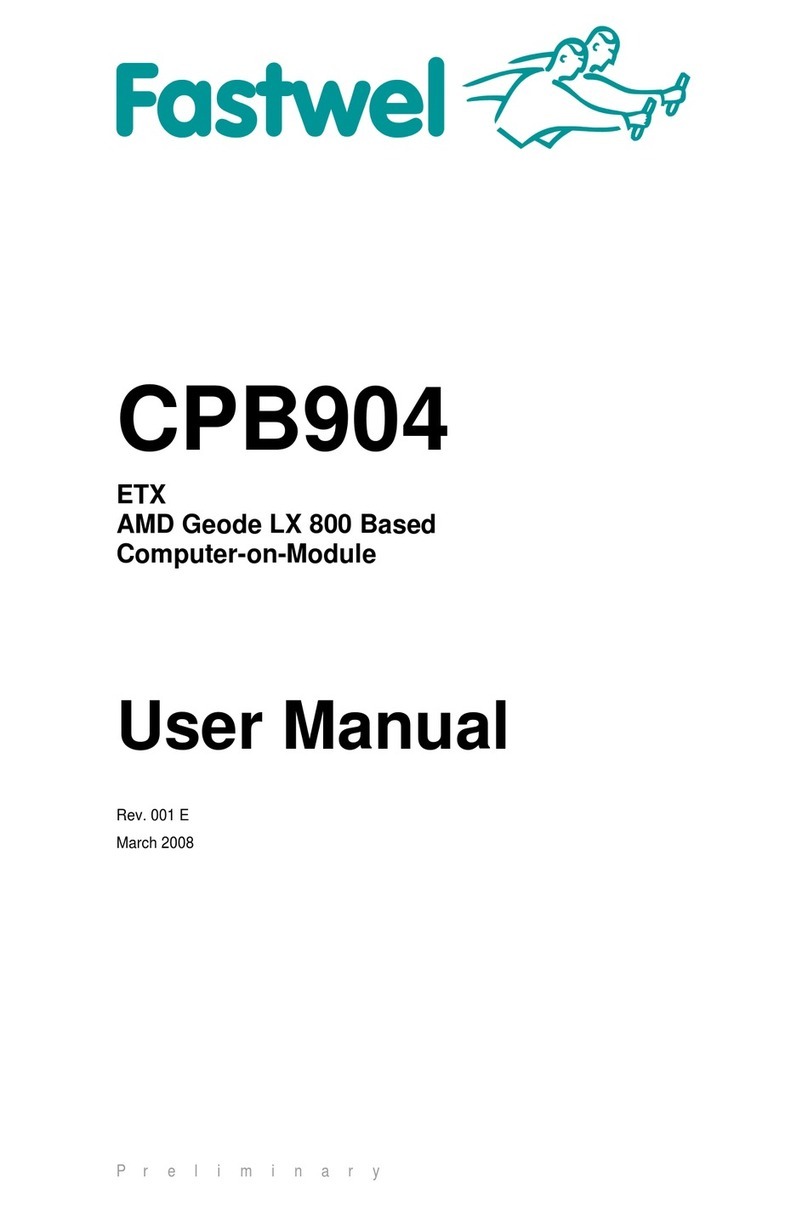
Fastwel
Fastwel CPB904 user manual
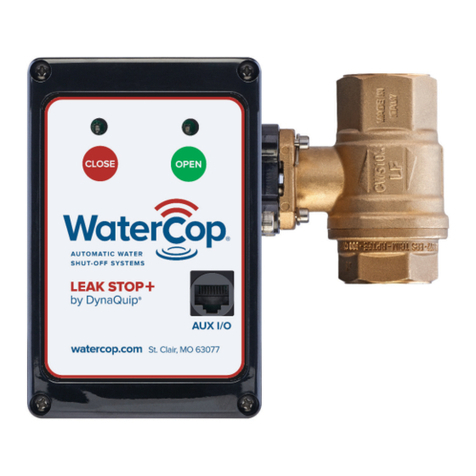
DynaQuip
DynaQuip WaterCop LEAK STOP+ Owner's manual and installation guide
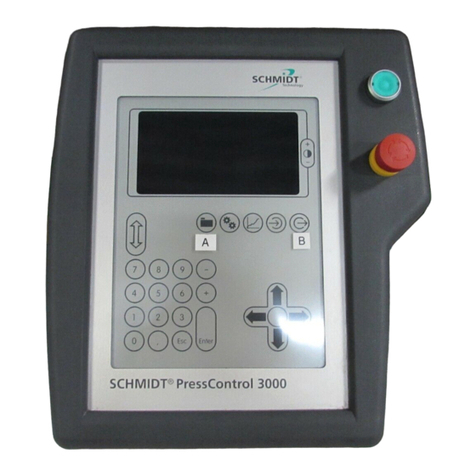
Schmidt
Schmidt PressControl 3000 Operator's manual
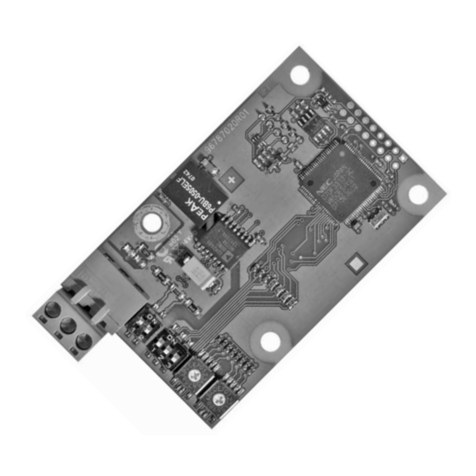
Grundfos
Grundfos CIM 3 Series Installation and operating instructions
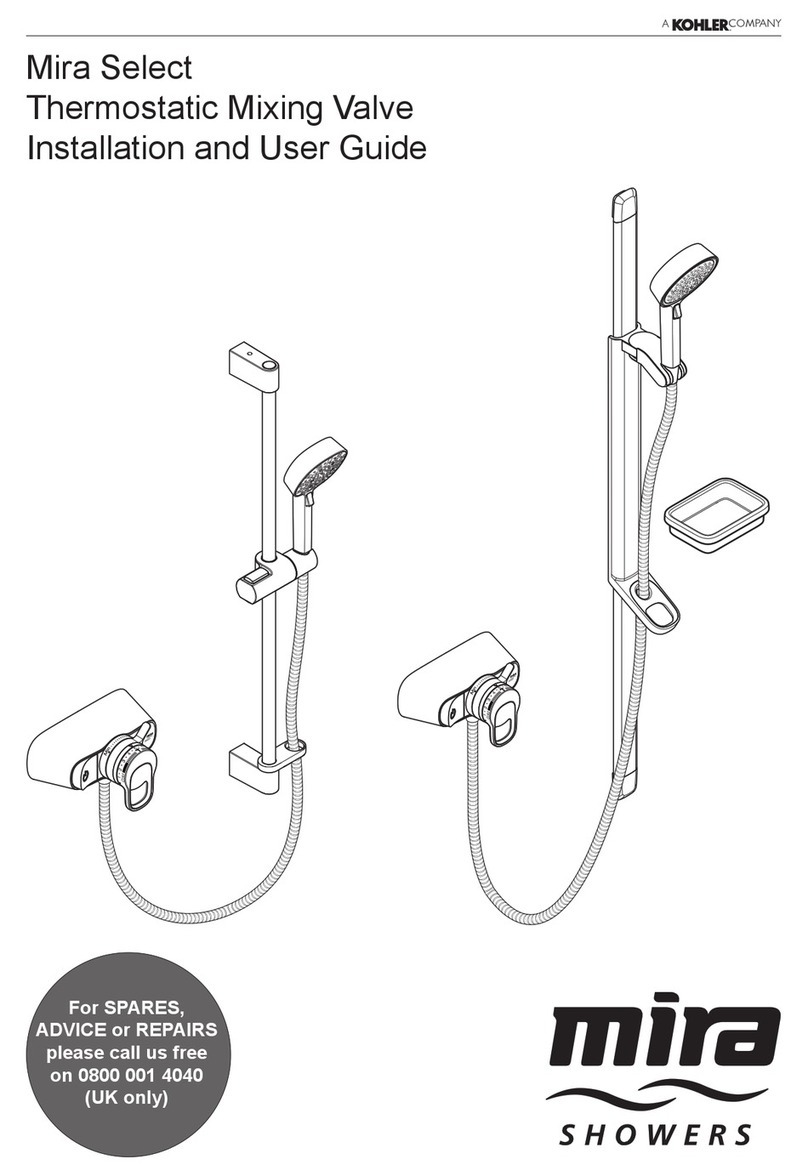
Kohler
Kohler Mira Select B14C Installation and user guide
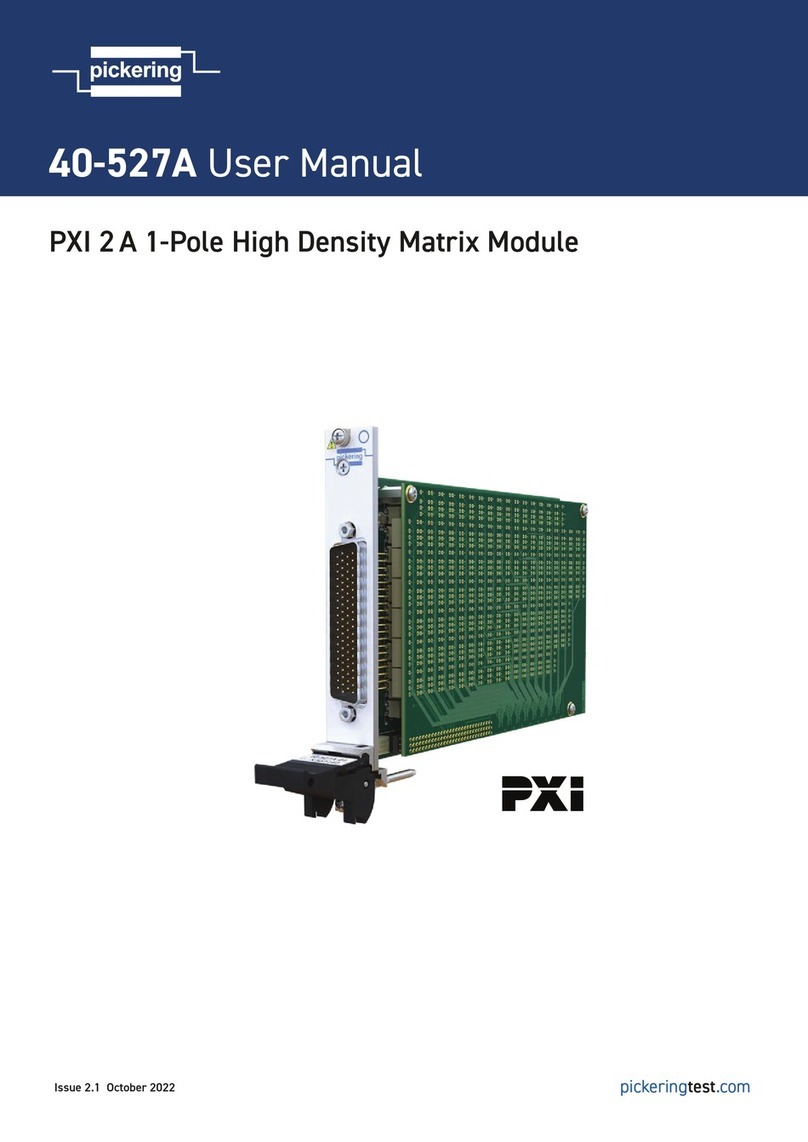
Pickering
Pickering 40-527A user manual