Reer JANUS 2B TRX Quick start guide

PHOTOELECTRIC
SAFETY BARRIER
JANUS TRX
I
IN
NS
ST
TA
AL
LL
LA
AZ
ZI
IO
ON
NE
E,
,
U
US
SO
O
E
E
M
MA
AN
NU
UT
TE
EN
NZ
ZI
IO
ON
NE
E
I
IN
NS
ST
TA
AL
LL
LA
AT
TI
IO
ON
N,
,
U
US
SE
E
A
AN
ND
D
M
MA
AI
IN
NT
TE
EN
NA
AN
NC
CE
E
I
IN
NS
ST
TA
AL
LL
LA
AT
TI
IO
ON
N,
,
U
UT
TI
IL
LI
IS
SA
AT
TI
IO
ON
N
E
ET
T
M
MA
AI
IN
NT
TE
EN
NA
AN
NC
CE
E
I
IN
NS
ST
TA
AL
LL
LA
AT
TI
IO
ON
N,
,
B
BE
ED
DI
IE
EN
NU
UN
NG
G
U
UN
ND
D
W
WA
AR
RT
TU
UN
NG
G
I
IN
NS
ST
TA
AL
LA
AC
CI
IÓ
ÓN
N,
,
U
US
SO
O
Y
Y
M
MA
AN
NT
TE
EN
NI
IM
MI
IE
EN
NT
TO
O
www.reer.it

8540568 - 12/09/2022 - Rev.6
1
PHOTOELECTRIC
SAFETY
BARRIER
JANUS TRX
INSTALLATION USE AND MAINTENANCE
INDICE
INTRODUCTION ................................................................................................................... 2
PRINCIPLE OF OPERATION ................................................................................................ 3
INSTALLATION ..................................................................................................................... 5
POSITION ......................................................................................................................................6
MULTIPLE SYSTEMS ...................................................................................................................6
SAFETY DISTANCE CALCULATION ............................................................................................7
VERTICAL POSITION OF THE BARRIER ....................................................................................8
ELECTRICAL CONNECTIONS .....................................................................................................8
EXTERNAL CONNECTION ...........................................................................................................9
DISTANCE BETWEEN REFLECTING SURFACES .................................................................. 10
MOUNTING AND OPTICAL ALIGNMENT ................................................................................. 12
OPERATION AND TECHNICAL DATA ................................................................................ 13
LIGHT SIGNALS ......................................................................................................................... 13
CONFIGURATION AND OPERATION MODES ......................................................................... 15
K1/K2 EXTERNAL CONTACTORS CONNECTION ................................................................... 18
OUTPUT STATUS ...................................................................................................................... 18
TECHNICAL SPECIFICATIONS ................................................................................................. 19
DIMENSIONS ...................................................................................................................... 20
CHECKOUTS AND MAINTENANCE ................................................................................... 21
TROUBLESHOOTING ................................................................................................................ 22
SPARE PARTS .................................................................................................................... 24
CE DECLARATION OF CONFORMITY ............................................................................... 25
UKCA DECLARATION OF CONFORMITY .......................................................................... 26
GUARANTEE ...................................................................................................................... 27

2 8540568 - 12/09/2022 - Rev.6
This symbol stands by a very important warning concerning the safety of persons.
Its non-observance can cause a very serious risk for the exposed personnel.
INTRODUCTION
The J TRX safety light curtain is a multi-beam opto-electronic safety system of the Type 4
category of electro-sensitive devices in accordance with IEC61496-1,2 EN61496-1, for the
protection of persons exposed to dangerous machines or plants.
This light curtain consists of an active element J TRX E/R (containing the emitter and the
receiver) and a passive element TRX RR, consisting of pre-aligned reflectors, capable of
reflecting the strip of infrared light (Figure 1, 2 and 3).
2-beams models (distance 500mm), 3-beams models (distance 400mm) and 4-beams
models (distance 300mm) are provided (according to the European Standard ISO 13855).
A diagnostic display available on the active element provides the necessary informations for
a correct use of the device and the valuation of the possible operation failures.
JANUS TRX is ideal for protecting:
Automatic palletizing/depalletizing systems, packing and packaging machines, metal, wood,
marble and glass tool machines, materials handling.
If necessary, for any safety-related problems contact the competent safety
authorities or industrial associations in the country of use.
For applications in the food industry, please contact the manufacturer to ensure that
the barrier contains materials that are compatible with the chemical agents utilized.
The protective function of the optoelectronic devices is not effective in the following cases:
If the machine stopping control cannot be actuated electrically and it is not possible
to stop all dangerous machine movements immediately and at any time during the
operating cycle.
If the machine generates dangerous situations due to material being expelled or
falling from overhead.

8540568 - 12/09/2022 - Rev.6 3
PRINCIPLE OF OPERATION
Figure 1 shows the MI/ML/MT TRX way of operation :
The active element M TRX E/R contains the emitter and the receiver units; the emitted
infrared beam, correctly reflected by the pre-aligned deflection mirrors of the passive
element TRX RR, is received by the receiver of the M TRX E/R.
With the protected area clear, the two PNP outputs of the active elements are in ON
condition (24VDC) and guarantee the normal operation of the connected machine.
When an object interrupts the infrared beams, the TRX PNP outputs are de-energized (OFF
condition - 0VDC). This condition permits to stop the moving body of the machine (thanks to
a specific stopping circuit).
ACTIVE ELEMENT
EMITTER
RECEIVER
Figure 1 - J TRX with 2 beams
PASSIVE ELEMENT
1° MIRROR
2° MIRROR
ACTIVE ELEMENT
RECEIVER1
EMITTER1
EMITTER2
RECEIVER2
Figure 2 - J TRX with 3 beams
PASSIVE ELEMENT
1° MIRROR
2° MIRROR
3° MIRROR
4° MIRROR

4 8540568 - 12/09/2022 - Rev.6
ACTIVE ELEMENT
RECEIVER1
EMITTER1
EMITTER2
RECEIVER2
Figure 3 - J TRX con 4 raggi
PASSIVE ELEMENT
MIRROR1
MIRROR2
MIRROR3
MIRROR4

8540568 - 12/09/2022 - Rev.6 5
INSTALLATION
Before installing the JANUS TRX safety system, make sure that:
The safety system is only used as a stopping device and not as a machine control
device.
The machine control can be actuated electrically.
All dangerous machine movements can be interrupted immediately. In particular, the
machine stopping times must be known and, if necessary, measured.
The machine does not generate dangerous situations due to materials projecting or
falling from overhead; if that is not the case, additional mechanical guards must be
installed.
The minimum dimensions of the object that must be intercepted are greater than or
equal to the resolution of the JANUS TRX.
Knowledge of the shape and dimensions of the dangerous area enables the width and height
of the relative access area to be calculated.
Compare these dimensions with the maximum working range and the height of the
protected area in relation to the JANUS TRX.
The general instructions set out below must be taken into consideration before placing the
safety device in position.
Make sure that the temperature of the environment in which the system is to be
installed is compatible with the temperature parameters contained in the technical
data sheet.
Do not install the active unit close to bright or high-intensity flashing light sources.
Certain environmental conditions may affect the monitoring capacity of the
photoelectric devices. In order to assure correct operation of equipment in places
that may be subject to fog, rain, smoke or dust, the appropriate correction factors Cf
should be applied to the maximum working range values. In these cases:
where Pu and Pm are, respectively, the working and maximum range in meters.
Pu = Pm x Cf

6 8540568 - 12/09/2022 - Rev.6
The recommended Cf factors are shown in the table below:
ENVIRONMENTAL CONDITION
CORRECTION FACTOR Cf
Fog
0.25
Steam
0.50
Dust
0.50
Dense fumes
0.25
If the device is installed in places that are subject to sudden changes in temperature,
the appropriate precautions must be taken in order to prevent the formation of
condensation on the lenses, which could have an adverse effect on monitoring.
POSITION
The active J TRX E/R and passive elements J TRX RR must be positioned in such a way
that the access to the dangerous zone from overhead, bottom and from the opposite sides is
impossible without intercepting at least one of the two optical beams.
Figure 4
MULTIPLE SYSTEMS
JANUS TRX is composed of one active and one reflecting element; when more than
one JANUS TRX system is used, precaution must be taken to avoid optical interference
between them.
We recommend to interpose between two adjacent systems, opportune NOT
TRANSPARENT surfaces to stop the passage of the infrared beam.
WARNING
To reach the perfect JANUS TRX
installation, position both the
units as showed in Figure 4
(REER labels in the same side)
FRONT WINDOW
JANUS
JANUS

8540568 - 12/09/2022 - Rev.6 7
SAFETY DISTANCE CALCULATION
The barrier must be installed at a distance that is greater than or equal to the minimum
safety distance S, so that a dangerous point can only be reached after all hazardous
machine movements have stopped (Figure 3).
According to European standard EN999, the minimum safety distance S must be calculated
using the following formula:
S = K (t1+ t2) + C
where:
S
minimum safety distance
mm
K
approach speed of object to the dangerous area
mm/sec
t1
response time of the safety barrier in seconds
sec
t2
machine response time, in seconds, meaning the time
required for the machine to interrupt the dangerous movement
following transmission of the stop signal
sec
c
additional distance
mm
The non-observance of the correct safety distance reduces or cancels the protective
action of the light curtain.
If the position of the barrier does not prevent the operator from having access to the
dangerous area without being detected, additional mechanical guards must be
installed to complete the system.
S=Safety distance
Figure 5
HAZARDOUS
MACHINE
S
PASSIVE
ELEMENT
ACTIVE
ELEMENT
MECHANICAL
PROTECTIONS

8 8540568 - 12/09/2022 - Rev.6
VERTICAL POSITION OF THE BARRIER
These models are suitable for the protection of
the entire body and must not be used to protect
arms or legs.
The minimum safety distance S is calculated
according to the following formula:
S = 1600 (t1+ t2) + 850
➔The recommended height H from the
reference surface G (ground) is as follows:
Figure 6
MODEL
BEAMS
Reccomended Height H (mm)
J 2B TRX E/R
J 3B TRX E/R
J 4B TRX E/R
2
3
4
400 – 900
300 – 700 – 1100
300 – 600 – 900 - 1200
ELECTRICAL CONNECTIONS
WARNINGS
Before making the electrical connections, make sure that the supply voltage complies with
the one specified in the technical data sheet.
Janus TRX must be supplied with 24Vdc±20% power supply that guarantee safe
isolation from main voltage (PELV).
The external power supply must comply with the standard EN 60204-1 (Chapter 6.4).
The electrical connections must be made according to the diagrams in this manual. In
particular, do not connect other devices to the connectors of the active unit.
To guarantee reliability of operation, when using a diode jumper supply unit, its output
capacity must be at least 2000µF for each absorbed A.
safety
barrier
point of
danger
direction
of
approach
reference plane

8540568 - 12/09/2022 - Rev.6 9
Connector pins.
Figure 7
EXTERNAL CONNECTION
PIN
COLOR
NAME
TYPE
DESCRIPTION
OPERATION
2
Brown
24VDC
-
24VDC power supply
-
7
Blue
0VDC
-
0VDC
-
8
Red
PE
-
Ground connection
-
1
White
OSSD1
OUTPUT
Safety static outputs
PNP active high
3
Green
OSSD2
OUTPUT
5
Grey
EXT_SEL_A
INPUT
Barrier
configuration
According the normative
EN61131-2
(ref. Table 2 and Table 3)
6
Pink
EXT_SEL_B
INPUT
4
Yellow
EXT_K1_K2
INPUT
Feedback external
contactors
Table 1
Warnings regarding the connection cables
• For connections over 50m long, use cables with a cross-section area of
1 mm2.
• The power supply to the barrier should be kept separate from that to other
electric power equipment (electric motors, inverters, frequency converters) or
other sources of disturbance.
• Connect the active element to the ground output.
• The connection cables must follow a different route to that of the other
power cables.

10 8540568 - 12/09/2022 - Rev.6
DISTANCE BETWEEN REFLECTING SURFACES
The presence of reflecting surfaces in proximity of the photoelectric barrier may generate
spurious reflections that prevent monitoring. With reference to Figure 8, object A is not
detected because surface S reflects the beam and closes the optical path between the active
and passive elements.
A minimum distance d must therefore be maintained between any reflecting surfaces and
the protected area. The minimum distance d must be calculated according to the distance l
between the active and passive unit, considering that the angle of projection and
reception is 4°.
Figure 8
Figure 9 illustrates the values for the minimum distance d that must be maintained when the
distance l between the active and passive elements is changed.

8540568 - 12/09/2022 - Rev.6 11
Figure 9
After installing the system, check whether any reflecting surfaces intercept the beams, first in
the centre and then in the vicinity of the active unit.
During these operations, the red LED on the active elements should never, for any reason,
switch off.

12 8540568 - 12/09/2022 - Rev.6
MOUNTING AND OPTICAL ALIGNMENT
The active element J TRX E/R and the the passive element J TRX RR must be mounted the
first in front of the other with the same (or less) distance showed in the technical data.
Using the fastening brackets and inserts (available on request) fix the active element
J TRX E/R and the passive element J TRX RR aligned and parallel.
The fastening inserts can be located in the rear or in the side spline of the units, depending
on the dimensions and shape of the machine rest (Figure 10). The bracket supplied with
the barrier must be fixed in the vertical center of the columns.
The perfect alignment between the two units is essential for the correct barrier operation; the
control of the signal leds makes this function easier.
Figure 10
• Place the optical axis of the photoemitter and photoreceiver on the same axis
of the reflecting mirrors of the passive element.
• Hold the passive element and move J TRX E/R to find the area within which
the green led stays on, then position the first beam (the one close to the
indicator leds) in the centre of this area.
• Lock the two units in place.
During these operations it may be useful to check the orange weak signal LED on the
passive element. Upon completion of alignment, this LED must be off.
If the active element is assembled in areas that are subject to strong vibrations, the use of
vibration-damping supports is recommended, in order to prevent circuit malfunctions.

8540568 - 12/09/2022 - Rev.6 13
OPERATION AND TECHNICAL DATA
LIGHT SIGNALS
ACTIVE ELEMENT SIGNALS
At power-on, for a period of 5 seconds, the display will show the number "8" and all the leds
will be ON. In the next 10 seconds, the display and the leds will show the configuration
selected. At initial power-on after installation, always check the accuracy of these settings
very carefully. This check is also indispensable in all cases of malfunctioning (ref.
"TROUBLESHOOTING").
During display of the configuration, the display will show the letter "C" while during normal
operation, a hyphen "-" will be displayed (ref. Figure 11).
Initial display
Figure 11
LED
NORMAL OPERATION
COLOR
(LED ON)
(LED OFF)
Weak (1)
-
-
ORANGE
Break (2)
OSSD outputs set to OFF
-
RED
Guard (3)
-
-
GREEN
Clear (4) CLEAR
-
-
YELLOW
MAN/AUTO
Manual functioning
mode enabled
Automatic functioning mode
enabled
YELLOW
EN EDM
Control of feedback external relays
enabled
Control of feedback external
relays disabled
YELLOW
(1) Weak signal from the emitter
(2) Barrier occupied - output disabled
(3) Barrier free - output enabled
(4) Barrier free - output disabled - Waiting for restart
➔The flashing led together with the C and F letters indicates the incorrect type of
configuration.
2
1
3
4

14 8540568 - 12/09/2022 - Rev.6
Normal display
LED
NORMAL OPERATION
COLOR
(LED ON)
(LED OFF)
Weak (1)
Weak signal received
Signal received OK
ORANGE
Break (2)
Light curtain occupied,
OSSD outputs set OFF
-
RED
Guard (3)
Light curtain clear,
OSSD outputs set ON
-
GREEN
Clear (4) CLEAR
Light curtain clear, OSSD outputs set
OFF (the receiver is waiting for a
Restart signal)
-
YELLOW
(1) Weak signal from the emitter
(2) Barrier occupied - output disabled
(3) Barrier free - output enabled
(4) Barrier free - output disabled - Waiting for restart
➔In case of fault, only the red led will remain ON and the display will show a flashing "C" or
“F” followed by the fault code (ref. TROUBLESHOOTING paragraph).

8540568 - 12/09/2022 - Rev.6 15
CONFIGURATION AND OPERATION MODES
The JANUS TRX operation mode is selected realizing appropriate connections on the M12
8 poles of the active element (Table 1 and Table 2).
AUTOMATICO MODE
In this operation mode the OSSD1 and OSSD2 safety outputs follow the barrier status :
• with proteceted area clear, the safety outputs are active.
• with proteceted area intercepted, the safety outputs are disabled.
CONNECTION
OPERATION MODE
EXT_SEL_A (PIN 5)
connected to :
ext_OSSD1 (PIN 1)
EXT_SEL_B (PIN 6)
connected to :
ext_OSSD2 (PIN 3)
EXT_K1_K2 (PIN 4)
connected to :
0VDC
AUTOMATIC without
K1-K2 feedback
EXT_SEL_A (PIN 5)
connected to :
ext_OSSD2 (PIN 3)
EXT_SEL_B (PIN 6)
connected to :
ext_OSSD1 (PIN 1)
EXT_K1_K2 (PIN 4)
connected to : 24VDC
(through series of contatcts
N.C. of external relays)
AUTOMATIC with
K1-K2 feedback
Table 2
Figure 12
Example of connection of TRX barrier in AUTOMATIC mode with feedback K1K2

16 8540568 - 12/09/2022 - Rev.6
Figure 13
Example of connection of TRX barrier in AUTOMATIC mode without feedback K1K2
MANUAL MODE
In this operating mode the safety outputs OSSD1 and OSSD2 are activated (+24VDC) only if
the protected area is free and after the reception of the RESTART signal, using a push
button or thank to an appropriate control on the SEL_A or SEL_B input (ref.Table 3).
After an interception of the protected area, the safety outputs will be de-activated.
To re-activate them it will be necessary to repeat the sequence described above.
The RESTART command is active with a voltage of +24VDC.
The minimum duration of the RESTART command is 400ms.
Use of manual mode (start/restart interlock activated) is compulsory if the safety
device controls an opening to protect a danger area and a person, after passing
through the opening, may remain in the danger area without being detected (use as
'trip device' according to IEC 61496). Failure to comply with this rule may result in
very serious hazards for the persons exposed.
CONNECTION
OPERATION MODE
EXT_SEL_A (PIN 5)
connected to :
24VDC (PIN 2)
EXT_SEL_B (PIN 6)
connected to :
24VDC (PIN 2)
(through the RESTART
pushbutton)
EXT_K1_K2 (PIN 4)
connected to :
0VDC
MANUALE senza
feedback K1-K2
EXT_SEL_A (PIN 5)
connected to :
24VDC (PIN 2)
(through the RESTART
pushbutton)
EXT_SEL_B (PIN 6)
connected to :
24VDC (PIN 2)
EXT_K1_K2 (PIN 4)
connected to : 24VDC
(through series of contatcts
N.C. of external relays)
MANUALE con
feedback K1-K2
Table 3

8540568 - 12/09/2022 - Rev.6 17
Figure 14
Example of connection of TRX barrier in MANUAL mode with feedback K1K2
Figure 15
Example of connection of TRX barrier in MANUAL mode without feedback K1K2

18 8540568 - 12/09/2022 - Rev.6
K1/K2 EXTERNAL CONTACTORS CONNECTION
In every operating mode is activable the K1/K2 external contactors feedback.
If you want to use this check, connect the pin 4 of 8 poles M12 connector with the power
supply (+24VDC) through the series of N.C. contacts (feedback) of external contactors.
OUTPUT STATUS
Janus TRX features two static PNP outputs on the active element, the status of which
depends on the condition of the protected area.
The maximum load allowed is 500mA at 24VDC, which corresponds to a resistive load of
48. Maxim load capacity corresponds to 2.2F. The meaning of the status of outputs is
defined in the table below. Any short circuit between outputs or between outputs and 24VDC
or 0VDC power supplies is detected by the barrier.
NAME OF SIGNAL
CONDITION
MEANING
OSSD1
24VDC
Condizione di barriera libera.
OSSD2
OSSD1
0VDC
Condizione di barriera occupata
o guasto riscontrato
OSSD2
Table 4
In the protected area clear condition, the active element supplies a voltage of 24 VDC
on both outputs. The required load must therefore be connected between the output
terminals and the 0DVC (Figure 16).
Figure 16

8540568 - 12/09/2022 - Rev.6 19
TECHNICAL SPECIFICATIONS
GENERAL DATA
Safety category
4
Reset
automatic or manual selectable
Power supply
Vcc
24 20%
Connections
M12 – 8 poles (male)
Protection rating
IP 65
Max. length of
electrical connections
m
100
Dimensions light
curtain section
mm
50 x 60
Operating temperature
°C
Storage temperature
°C
Max operative humidity
%
95
Safety outputs
2 PNP auto-controlled – 500 mA @ 24 Vdc
with short-circuit, overload, reversal of polarity protection
Max. output current
mA
500
System Status signal current
mA
100
Max. capacitive load
F
2,2
Max. off-state voltage
V
< 1
Max. resistance of
connections between OSSDs
and the loads
Ohm
< 25
Light curtain lifetime
20 years
Safety level
Type 4
IEC 61496-1:2004
IEC 61496-2:2006
SIL 3
IEC 61508:1998
SILCL 3
IEC 62061:2005
PL e - Cat. 4
ISO 13849-1 : 2006
*IEC 61508
# ISO 13849-1
J TRX
Number of beams of light curtains for
detection of body in access control
2 – 3 – 4
Operating range
m
0 ÷ 6
2B
3B
4B
Number of beams
2
3
4
Distance between beams mm
500
400
300
Response time ms
10
10,5
10,5
Overall barrier ht. mm
741
1041
1141
PFHd *
4,83E-09
4,92E-09
5,01E-09
DCavg #
98,14%
98,16%
98,19%
MTTFd #years
100
CCF #
80%
0...55
-20...70
This manual suits for next models
2
Table of contents
Other Reer Security Sensor manuals
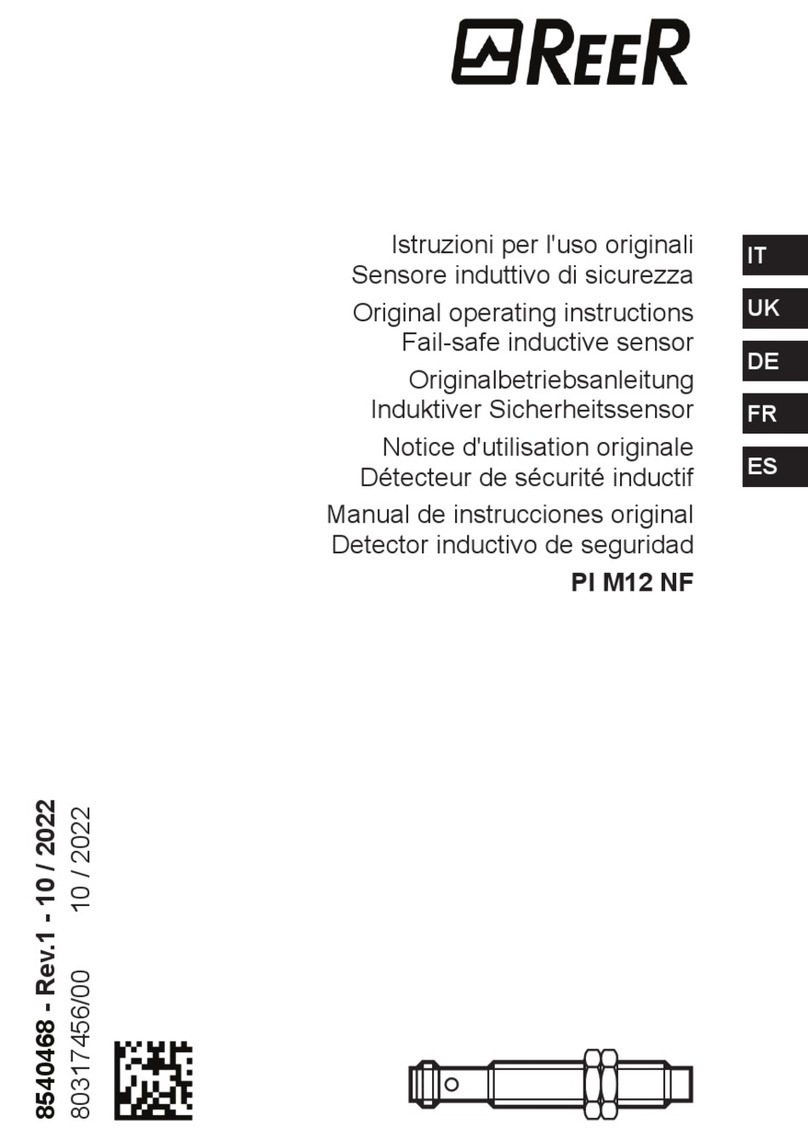
Reer
Reer PI M12 NF User manual
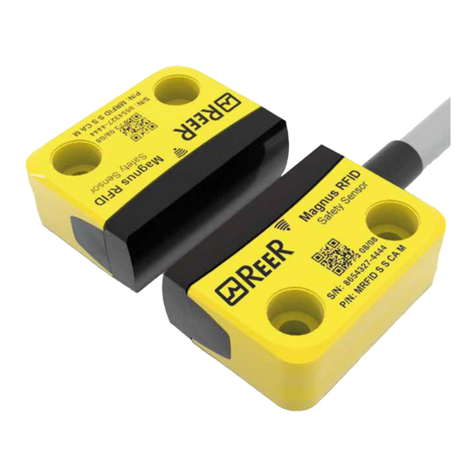
Reer
Reer Magnus RFID S Series Quick start guide
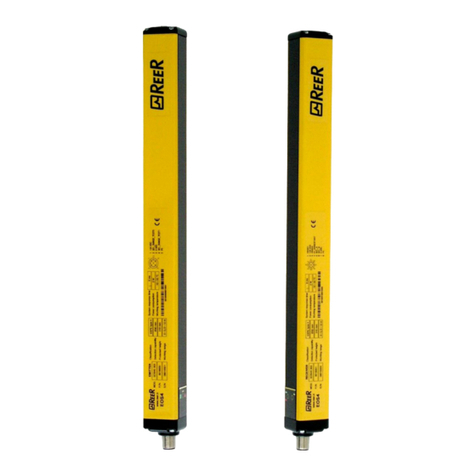
Reer
Reer EOS4 Series Quick start guide
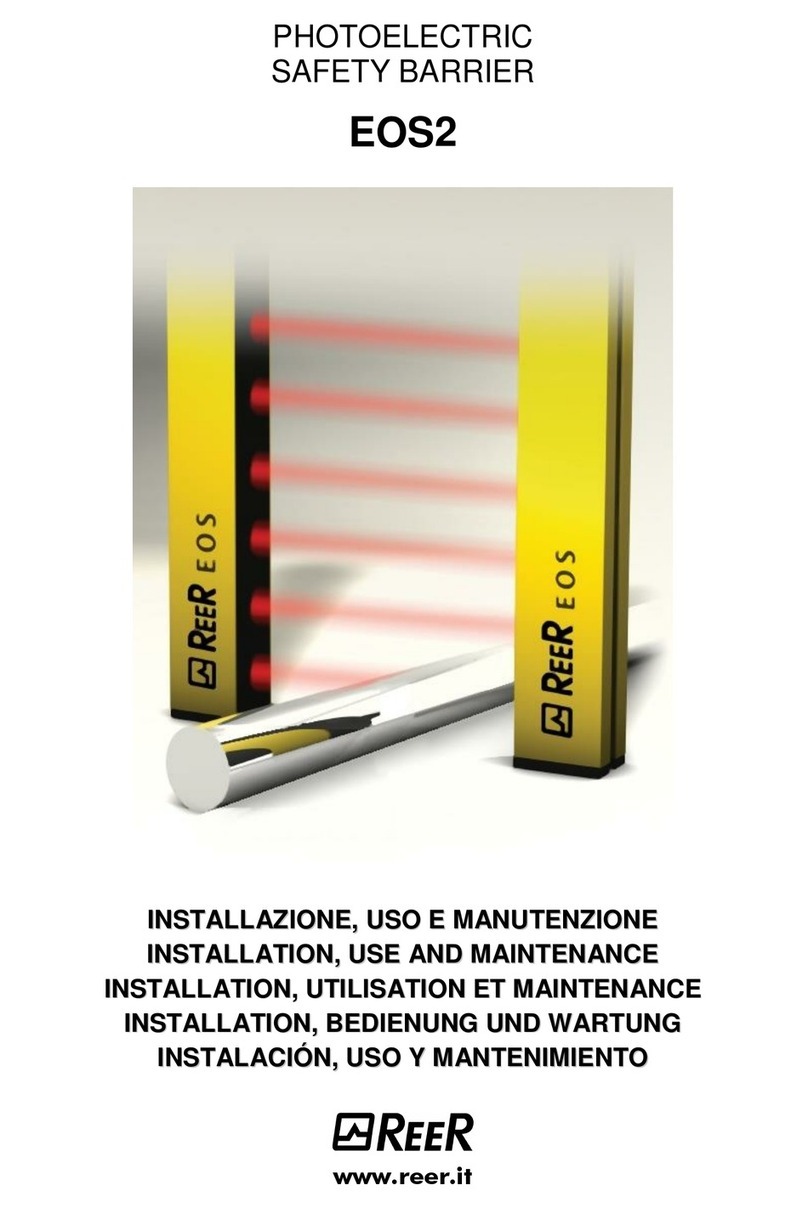
Reer
Reer EOS2 Quick start guide

Reer
Reer JANUS Quick start guide

Reer
Reer ADMIRAL Quick start guide
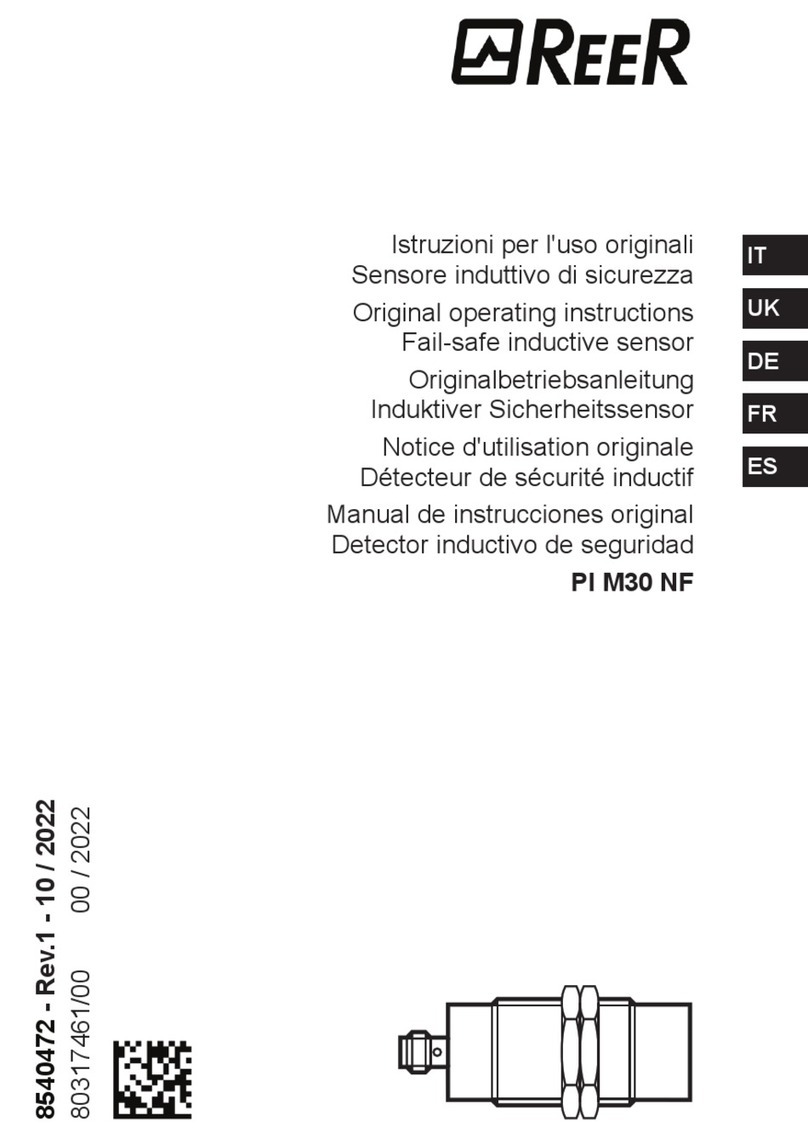
Reer
Reer PI M30 NF K User manual

Reer
Reer SAFEGATE S Installation and operating instructions
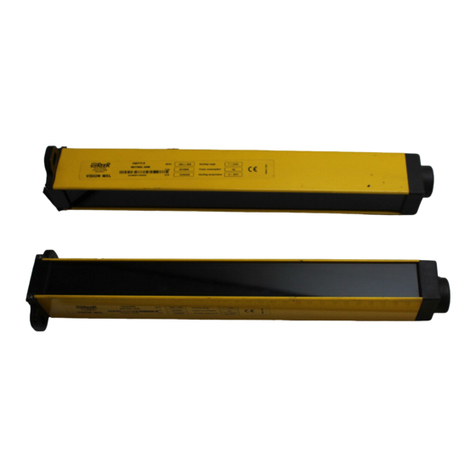
Reer
Reer VISION MXL Quick start guide
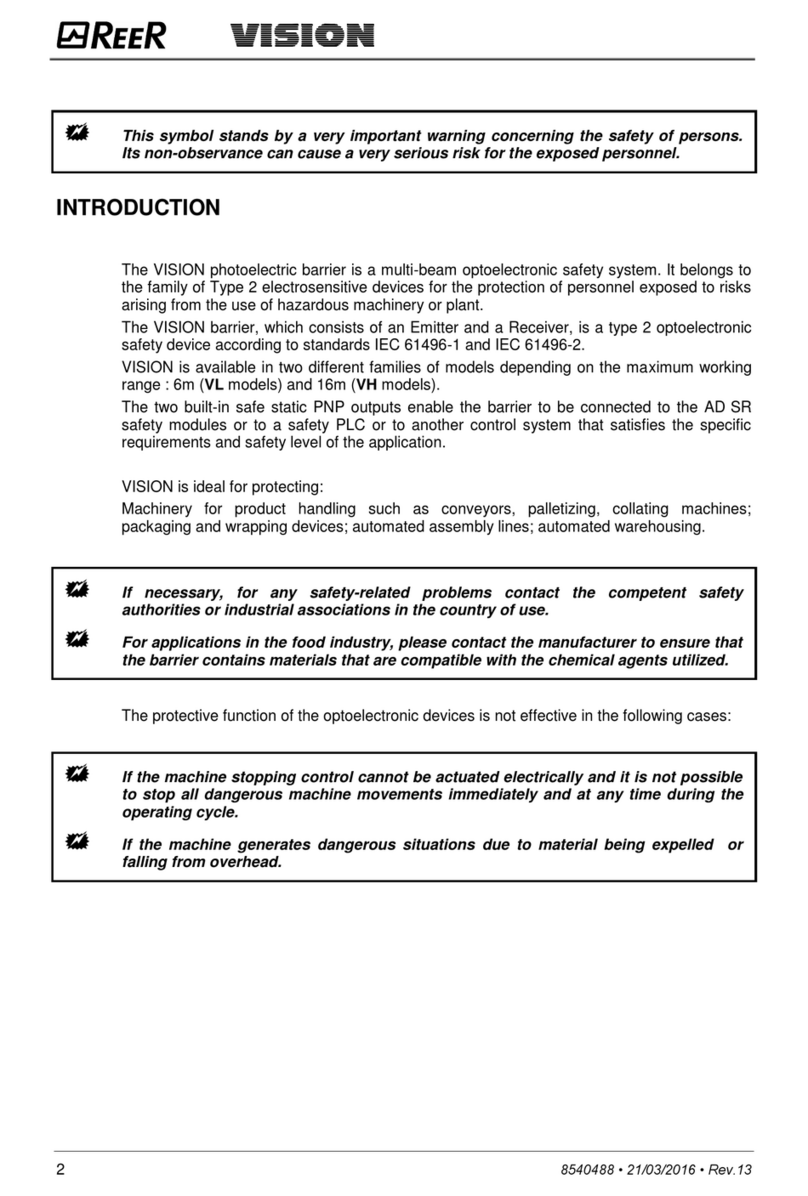
Reer
Reer VISION V3BL User manual