Reer VISION MXL Quick start guide

Dichiarazione CE di conformità
EC declaration of conformity
Torino, 1/1/2010
REER SpA
via Carcano 32
10153 – Torino
Italy
dichiara che le barriere fotoelettriche VISION VXL / VISION MXL sono Dispositivi Elettrosensibili di
Sicurezza (ESPE) di :
Tipo 2 (secondo la Norma CEI EN 61496-1:2005; CEI EN 61496-2:2007)
SIL 2 (secondo la Norma CEI EN 61508:2002)
SILCL 2 (secondo la Norma CEI EN 62061:2005 + CEI EN 62061/EC2:2008)
PL d (secondo la Norma UNI EN ISO 13849-1:2008)
declares that the VISION VXL / VISION MXL photoelectric safety barriers are :
Type 2 (according the Standard IEC 61496-1:2004; IEC 61496-2:2006)
SIL 2 (according the Standard IEC 61508:1998)
SILCL 2 (according the Standard IEC 62061:2005)
PL d (according the Standard ISO 13849-1:2006)
Electro-sensitive Protective Equipments (ESPE)
realizzati in conformità alle seguenti Direttive Europee:
complying with the following European Directives:
2006/42/CE "Direttiva Macchine"
"Machine Directive"
2004/108/CE "Direttiva Compatibilità Elettromagnetica"
"Electromagnetic Compatibility Directive"
2006/95/CE "Direttiva Bassa Tensione"
"Low Voltage Directive"
e sono identiche all'esemplare esaminato ed approvato con esame di tipo CE da:
and are identical to the specimen examined and approved with a CE - type approval by:
TÜV SÜD Rail GmbH – Ridlerstrasse 65 – D-80339 – Muenchen – Germany
Carlo Pautasso Giancarlo Scaravelli
DirettoreTecnico Presidente
Technical Director President

8540687 • 29/03/2010 • Rev.10 1
PHOTOELECTRIC
SAFETY
LIGHT CURTAIN
VISION MXL
INSTALLATION USE AND MAINTENANCE
SUMMARY
INTRODUCTION...........................................................................................................................2
OPERATION.................................................................................................................................3
INSTALLATION.............................................................................................................................4
MUTING FUNCTION...........................................................................................................................5
POSITIONING.....................................................................................................................................9
SAFETY DISTANCE CALCULATION...............................................................................................10
VERTICAL POSITION OF THE LIGHT CURTAIN ...........................................................................11
MULTIPLE SYSTEMS.......................................................................................................................12
DISTANCE BETWEEN REFLECTING SURFACES.........................................................................12
MECHANICAL ASSEMBLY AND OPTICAL ALIGNMENT...............................................................14
ELECTRICAL CONNECTIONS ........................................................................................................15
EMITTER CONNECTIONS...............................................................................................................15
RECEIVER CONNECTIONS............................................................................................................16
WARNINGS REGARDING THE CONNECTION CABLES...............................................................16
CONFIGURATION AND MODE OF OPERATIONS.........................................................................18
OPERATION AND TECHNICAL DATA.......................................................................................22
SIGNALS...........................................................................................................................................22
TEST FUNCTION..............................................................................................................................23
MUTING LAMP .................................................................................................................................23
MUTING ENABLE COMMAND.........................................................................................................23
OUTPUT STATUS ............................................................................................................................24
TECHNICAL SPECIFICATIONS.......................................................................................................25
DIMENSIONS (mm)....................................................................................................................27
CHECKOUTS AND MAINTENANCE..........................................................................................30
VERIFICATION OF LIGHT CURTAIN EFFICIENCY........................................................................30
TROUBLESHOOTING......................................................................................................................31
SPARE PARTS...........................................................................................................................33
GUARANTEE..............................................................................................................................34

VISION MXL
2 8540687 • 29/03/2010 • Rev.10
This symbol stands by a very important warning concerning the safety of persons. Its
non-observance can cause a very serious risk for the exposed personnel.
INTRODUCTION
VISION MXL light curtain is a multibeam optical-electronic safety system belonging to the
category of Type 2 electro-sensitive devices, and is equipped with a MUTING function to protect
people exposed to dangerous machines or equipment, according to norms IEC 61496-1,2 and
EN 61496-1.
VISION MXL is composed of Emitter plus Receiver, with added functions such as Muting,
feedback control of eventual external contactors, and manual/automatic function management.
A series of warning LEDs located on the Emitter and the Receiver display the information
necessary for the correct use of the device and to evaluate eventual functioning anomalies.
Thanks to an automatic self-monitoring system, VISION MXL light curtain is able to
autonomously detect any dangerous fault in a maximum of 0,5 seconds. This detection system
is permanently active and does not need any external command.
VISION MXL is ideal for protecting:
•automatic palletizing/depalletizing systems
•materials handling and storage systems;
•packing and packaging machines;
•assembly lines;
•industrial automatic warehouses;
•AGV transit openings;
•metal, wood, marble and glass tool machines.
Carefully consider the risk analysis of the application and the legislation of the light
curtain application within the Country to establish if the application is compatible with the
safety category 2.
If necessary, for any safety-related problems contact the competent safety authorities or
industrial associations in the country of use.
For applications in the food industry, please contact REER to ensure that the light curtain
contains materials that are compatible with the chemical agents utilized.
The protective function of the optoelectronic devices is not effective in the following case:
If the machine stopping control cannot be actuated electrically and it is not possible to
stop all dangerous machine movements immediately and at any time during the operating
cycle.
If the machine generates dangerous situations due to material being expelled or falling
from overhead.

VISION MXL
8540687 • 29/03/2010 • Rev.10 3
OPERATION
If the protected area is clear, the two outputs on the Receiver are active and enable the
machine to which they are connected to operate normally.
Each time that an object bigger than or equal in size to the resolution of the system intercepts
the optical path of one or more beams, the Receiver deactivates the outputs.
This condition enables hazardous machine movements to be stopped (by means of an
adequate machine emergency stop circuit).
The resolution is the minimum dimensions that an object must have so that, on crossing
the protected area, it will certainly intercept at least one of the optical beams generated by
the light curtain (Figure 1).
Figure 1
The resolution is constant irrespectively of work conditions, as it only depends on the geometric
characteristics of the lenses and the distance between the centres of two adjacent lenses.
The height of the protected area is the height that is actually protected by the safety light
curtain. If the latter is placed horizontally, this value refers to the depth of the protected area.
The working range is the maximum operative distance that can exist between the Emitter and
the Receiver.
VISION MXL is available with the following resolutions:
–30 mm (protected height from 150 mm to 1200 mm)
PROTECTION OF HANDS
–40 mm (protected height from 300 mm to 1200 mm)
PROTECTION OF HANDS
VISION MXL is available also in the 2, 3, 4 beams configuration with the following lens pitch:
–500mm (2 beams), 400mm (3 beams), 300mm (4 beams).
PROTECTION OF BODY
P = Pitch between two lenses
D = Diameter of one lens
R = Resolution = P+D

VISION MXL
4 8540687 • 29/03/2010 • Rev.10
INSTALLATION
Before installing the VISION MXL safety system, make sure that:
The safety system is only used as a stopping device and not as a machine control device.
The machine control can be actuated electrically.
All dangerous machine movements can be interrupted immediately. In particular, the
machine stopping times must be known and, if necessary, measured.
The machine does not generate dangerous situations due to materials projecting or
falling from overhead; if that is not the case, additional mechanical guards must be
installed.
The minimum dimensions of the object that must be detected are greater than or equal to
the resolution of the specific model.
Knowledge of the shape and dimensions of the dangerous area enables the width and height of
the relative access area to be calculated.
Compare these dimensions with the maximum working range and the height of the
protected area in relation to the specific model.
The general instructions set out below must be taken into consideration before placing the
safety device in position.
Make sure that the temperature of the environment in which the system is to be installed
is compatible with the temperature parameters contained in the technical data sheet.
Do not install the Emitter and Receiver close to bright or high-intensity flashing light
sources.
Certain environmental conditions may affect the monitoring capacity of the photoelectric
devices. In order to assure correct operation of equipment in places that may be subject
to fog, rain, smoke or dust, the appropriate correction factors Cf should be applied to the
maximum working range values. In these cases:
where Pu and Pm are, respectively, the working and maximum range in meters.
The recommended Cf factors are shown in the table below:
ENVIRONMENTAL CONDITION CORRECTION FACTOR Cf
Fog 0.25
Steam 0.50
Dust 0.50
Dense fumes 0.25
If the device is installed in places that are subject to sudden changes in temperature, the
appropriate precautions must be taken in order to prevent the formation of condensation
on the lenses, which could have an adverse effect on monitoring.
Pu = Pm x Cf

VISION MXL
8540687 • 29/03/2010 • Rev.10 5
MUTING FUNCTION
The Muting function is a temporary suspension of the safety light curtain’s protective
function. Carefully check your risk analysis in order to assess whether the Muting function
is compatible with your application and what additional measures have to be taken.
The Muting function is capable of generating a temporary and automatic suspension of the light
curtain functioning in order to guarantee the normal flow of material through the protected passage. The
muting function takes place with 2 events:
•Interruption of beams from the two muting sensors, in a maximum time of 4 seconds.
•MUTING ENABLE signal (pin C) at +24DC.
The activation of the Muting function depends not only on the consent obtained by activating the MUTING
ENABLE signal, but also on the system’s acknowledgement of the object interrupting the guarded
passage. In other words, whenever the system acknowledges the material and distinguishes it from an
eventual operator (in a potentially dangerous situation), it is enabled to temporarily exclude the curtain, so
that the material can cross the passage. The Muting sensors are the detection system which decides
whether to activate or not the Muting function. Only a correct sequence of beam interruption of the
Muting sensors can consent the disabling of dangerous passage control.
Remember that muting is a temporary automatic suspension of the safety function. This
means that a time limit is always mandatory. If a time out limit of 90min is a too short time for
a particular machine cycle, the configuration without time monitoring (t =
∞
) can be selected.
In this case alternative solutions or additional measures shall be implemented to detected the
condition of a muting function permanently active caused by accumulation of faults or by the
muting sensors activated all the time. For example for the application of guarding the
openings of a conveyor system (palletizers) by monitoring appropriate signals generated by
the transport system to determinate if and when a pallet is in the detection zone.
MUTING TYPES
MXL uses 2 sensors, to be connected to the M16 connector located on the receiver. These sensors can
be of different types (proximity, optical, capacity), with PNP or electro-mechanic outputs and with DARK-
ON change-over switching, i.e. active output in presence of material.
CONNECTION FOR TWO-WAY MUTING
This connection is useful to protect the passages with pallet output and input.
The meeting point of the two sensors must be located inside the dangerous area, to avoid
undesired and dangerous activations of the Muting function.
The activation of the Muting function takes place after sensors S1 and S2 are interrupted at the same time
(within max 4 sec). The Muting function will remain activated for as long as both sensors are occupied, and is
disabled as soon as the first of the two sensors is free. Maximum Muting duration (timeout) can be selected as
30 seconds, 90 minutes or Infinite.
Figure 2 - Two-way openings with pallet entrance/exit.
DANGEROUS
AREA

VISION MXL
6 8540687 • 29/03/2010 • Rev.10
SERIES "MXL T" - KIT OF MXL LIGHT CURTAIN AND SENSOR ELEMENT “MXLT SI” AND “MXLT SE”
Integrated Muting sensors – for two-way openings with pallet entrance/exit.
In this model, the Muting sensors are the first on one side
and the second on the other in relation to the vertical light
curtain (Figure 3). This model is therefore two-way and is
useful for protecting pallet entrance/exit openings.
The point of intersection of the two muting sensors (Figure
3) must be INSIDE the dangerous area in order to avoid
accidental actuation of the Muting function.
The Muting function is activated following concurrent
interruption (within max. 4 sec) of sensors S1 and S2.
The Muting function remains active as long as both
sensors remain occupied.
When the first of the two sensors is cleared, the Muting
function is disabled. Also for this model, the maximum
duration of the Muting condition (timeout) can be set to 30
seconds or 90 minutes.
Figure 3
CONNECTION FOR ONE-WAY MUTING (MXL "U")
This connection is useful to protect passages with pallet output.
In applications that involve access by personnel (full body or parts of body) to the dangerous area, the MXL or
MXL "T" models (and not MXL "L" and "U") must be used.
The MXL "L" and "U" models must be used only for applications involving One-way movements of materials
exiting the dangerous area (e.g. pallet output) and only in manual restart mode (guaranteed by suitable setting of
the light curtain or by an on-board machine safety control).
The activation of the Muting function takes place after sensors S1 and S2 are interrupted at the same
time (within max 4 sec). The Muting function will remain activated for as long as both sensors are
occupied. When the first of the 2 sensors is free, the material will still have 4 seconds available to
abandon the guarded area limited by the curtain. The Muting condition will be disabled as soon as the
guarded area is free. At the end of the 4 seconds, if the curtain is still occupied the OSSD outputs will be
disabled, interrupting machine function. For this model the maximum duration of the Muting condition
(timeout) can be selected as 30 seconds, 90 minutes or Infinite.
ÎIt is absolutely necessary to complete a Muting sequence (freeing the guarded area) in order to
guarantee the correct activation of the next sequence.
In case the selected timeout is Infinite, please refer to the precautions section of page 5.
In order to work safely with the MXL equipped with One-way Muting, the muting sensors must absolutely be
positioned inside the dangerous area (in dashed lines in Figures 4 and 5).
Figure 4 - Crossed sensors (one way muting)
Figure 5 - Parallel sensors (one way muting)
Emitter
Receiver
Sensor 1
Sensor 2
D
DA
AN
NG
GE
ER
RO
OU
US
S
A
AR
RE
EA
A

VISION MXL
8540687 • 29/03/2010 • Rev.10 7
Figure 6 - Muting cycle closed by the light curtain
SERIES "MXL L" - KIT OF MXL LIGHT CURTAIN AND SENSOR ELEMENT “MXLL S”
Integrated Muting sensors – only for one-way openings with pallet exit.
In this model, the sensors 1 and 2 are on the same side of
the vertical light curtain and are placed in front of the
guarded opening (Figure 7).
This model is one-way and is useful for protecting pallet exit
openings.
In applications that involve access by personnel (full body or
parts of body) to the dangerous area, the MXL or MXL "T"
models (and not MXL "L" and "U") must be used.
The MXL "L" and "U" models must be used only for
applications involving One-way movements of materials
exiting the dangerous area (e.g. pallet output) and only in
manual restart mode (guaranteed by suitable setting of the
light curtain or by an on-board machine safety control).The
Muting function is activated following concurrent interruption
(within max. 4 sec) of sensors S1 and S2. The Muting function
remains active as long as both sensors remain occupied.
When the first of the 2 sensors is cleared, the material has
four seconds to abandon the guarded area delimited by the
light curtain. The Muting condition will be disabled as soon
as the protected area is cleared.
After 4 seconds, if the light curtain is still occupied, the
OSSD outputs are disabled, interrupting functioning of the
machine. For this model, the maximum duration of the
Muting condition (timeout) can be set to 30 seconds or 90
minutes.
Figure 7
To guarantee the safety operation of the MXL L series, the horizontal muting sensor must be mounted INSIDE the
dangerous area (dashed on Figure 7).
When using a MXL L series, the minimum distance between two consecutive pallets must be less than 10cm or
more than 32cm.
Muting enable
Sensor1
Sensor2
Curtain free Curtain intercepted
Receiver
Emitter
Sensor 1
Sensor 2
D
DA
AN
NG
GE
ER
RO
OU
US
S
A
AR
RE
EA
A

VISION MXL
8 8540687 • 29/03/2010 • Rev.10
POSITIONING OF THE MUTING SENSORS
The Emitter and Receiver of the light curtain must be positioned so as to permit access to the
dangerous area from above, from below and from the sides without first of all intercepting at
least one of the optical beams.
Indications for correct positioning of the light curtain are provided in the figure below:
Figure 8
For correct positioning of sensors 1 and 2, i.e. those that manage enabling and disabling of the
Muting function, take into account the following:
•the two beams must be crossed and pass diagonally through the zone guarded by
the light curtain;
•the point of intersection of the two beams must be in the dangerous area
beyond the light curtain;
•the angle between the two Muting beams must be calculated according to the size
of the pallet and its speed, taking into account that the Muting function is activated
only if the interception delay between the two sensors is less than 4 seconds;
•the pallet must interrupt the two beams before intercepting the light curtain;
•the two beams must be interrupted continuously by the pallet for the entire period
during which the pallet passes between the sensors;
•make sure that the two beams are effectively intercepted by the material on the
pallet and not by the empty pallet;
•the zone identified by the points of interception and clearing of the beams of
sensors 1 and 2 by pallet must be limited as far as possible (or suitably
protected) so as to avoid the possibility of accidental passing through the light
curtain with Muting active (Figure 9).
Figure 9
S1 = Sensor 1
S2 = Sensor 2
R1 = Reflector 1 (or Receiver 1)
R2 = Reflector 2 (or Receiver 2)
B = Light curtain
Material
Dangerous area
Dimension to be reduced to a minimum
Mechanical guards
Material
DANGEROUS
AREA

VISION MXL
8540687 • 29/03/2010 • Rev.10 9
POSITIONING
The position of the MXLE Emitter and the MXLR Receiver must prevent access to the danger
zone from above, below and from the sides, unless at least one of the optical beams has been
intercepted. Some useful information regarding the correct position of the light curtain is shown
in the figure below.
Incorrect positioning of light curtain
Correct positioning of light curtain
Figure 10

VISION MXL
10 8540687 • 29/03/2010 • Rev.10
SAFETY DISTANCE CALCULATION
The light curtain must be installed at a distance that is greater than or equal to the minimum
safety distance S, so that a dangerous point can only be reached after all hazardous machine
movements have stopped (Figure 11).
According to European standard EN999, the minimum safety distance Smust be calculated
using the following formula:
S = K (t1+ t2) + C
where:
S minimum safety distance mm
K approach speed of object to the dangerous area mm/sec
t1response time of the safety light curtain in seconds sec
t2machine response time, in seconds, meaning the time
required for the machine to interrupt the dangerous movement
following transmission of the stop signal sec
c additional distance mm
The non-observance of the correct safety distance reduces or cancels the protective
action of the light curtain.
If the position of the light curtain does not prevent the operator from having access to the
dangerous area without being detected, additional mechanical guards must be installed
to complete the system.
“S”=Safety distance
Figure 11
HAZARDOUS
MACHINE
S

VISION MXL
8540687 • 29/03/2010 • Rev.10 11
VERTICAL POSITION OF THE LIGHT CURTAIN
30 mm and 40 mm resolution models.
These models are suitable for the protection of
hands.
The minimum safety distance Sis calculated
according to the following formula:
S = 2000(t1+ t2) + 8(D-14)
D=resolution (mm)
This formula is valid for distances Sbetween 100
and 500 mm. If this formula results in Sbeing
greater than 500 mm, the distance can be reduced
to a minimum of 500 mm by means of the following
formula:
S = 1600(t1+ t2) + 8(D-14)
If, due to the specific configuration of the machine,
the dangerous area can be accessed from above,
the highest beam of the light curtain must be at a
height Hof at least 1800 mm from the base Gof the
machine.
Figure 12
2, 3, 4 beams Models.
These models are suitable for the protection of
the entire body and must not be used to protect
arms or legs.
The minimum safety distance Sis calculated
according to the following formula:
S = 1600 (t1+ t2) + 850
ÎThe recommended height Hfrom the base
(G) must be the following:
Figure 13
MODEL BEAMS Reccomended Height H (mm)
MXL 2B
MXL 3B
MXL 4B
2
3
4
400 – 900
300 – 700 – 1100
300 – 600 – 900 - 1200
safety light
curtain
point of
dan
g
e
r
direction
of
approach
reference plane
safety light
curtain point of
dan
g
e
r
direction
of
approach
reference plane

VISION MXL
12 8540687 • 29/03/2010 • Rev.10
MULTIPLE SYSTEMS
When more than one VISION MXL system is used, precautions must be taken to avoid optical
interference between them: install units so that the beam emitted by the Emitter of one system
can only be received by the relative Receiver.
Figure 14 illustrates some examples of correct positioning when two photoelectric systems are
installed. Incorrect positioning could generate interference, and may result in malfunctioning.
Figure 14
DISTANCE BETWEEN REFLECTING SURFACES
The presence of reflecting surfaces in proximity of the photoelectric light curtain may generate
spurious reflections that prevent monitoring. With reference to Figure 15, object Ais not
detected because surface Sreflects the beam and closes the optical path between the Emitter
and Receiver. A minimum distance dmust therefore be maintained between any reflecting
surfaces and the protected area. The minimum distance dmust be calculated according to the
distance lbetween the Emitter and the Receiver, considering that the angle of projection and
reception is 5°.
Figure 15
Figure 16 illustrates the values for the minimum distance dthat must be maintained when the
distance lbetween the Emitter and Receiver is changed.
Systems installed alongside each other:
A
Installation of two adjacent Emitters
Overlapping systems: B
L-shaped installation: C
Crossed positioning of Emitters and Receivers

VISION MXL
8540687 • 29/03/2010 • Rev.10 13
Figure 16
After installing the system, check whether any reflecting surfaces intercept the beams, first in
the centre and then in the vicinity of the Emitter and Receiver. During these operations, the red
LED on the Receiver should never, for any reason switch off.

VISION MXL
14 8540687 • 29/03/2010 • Rev.10
MECHANICAL ASSEMBLY AND OPTICAL ALIGNMENT
The Emitter and the Receiver must be assembled opposite each other (at a distance specified
in the technical data sheet). Use the fastening brackets and inserts supplied with the system
to place the Emitter and the Receiver so that these are aligned and parallel to each other and
with the connectors facing the same way.
Depending on the dimensions and the shape of the support on which they are to be installed,
the Emitter and Receiver must be assembled with the fastening inserts at the back, or else by
fitting these in the side groove (Figure 17).
Perfect alignment of the Emitter and Receiver is essential in order to assure correct light curtain
operation. The indicator LEDs on the Emitter and Receiver facilitate this operation.
ÎTo perform an easier alignment the use of SFB circular brackets is necessary. These are
available on request (ordering code 1330974).
Figure 17
•Position the optical axis of the first and last beam of the Emitter on the same axis as
that of the corresponding beams on the Receiver.
•Move the Emitter in order to find the area within which the green LED on the Receiver
stays on, then position the first beam of the Emitter (the one close to the indicator
LEDs) in the centre of this area.
•Using this beam as a pivot, effect small sideways movements of the opposite end to
move to the protected area clear condition. The green LED on the Receiver will
indicate this condition.
•Lock the Emitter and Receiver in place.
ÎIn case the Emitter and the Receiver are assembled in areas subject to strong
vibration, in order to prevent damages to the equipment it is necessary to use anti-
vibration devices (code SAV-3 1200088, code SAV-4 1200089).

VISION MXL
8540687 • 29/03/2010 • Rev.10 15
ELECTRICAL CONNECTIONS
WARNINGS
Before making the electrical connections, make sure that the supply voltage complies with that
specified in the technical data sheet.
Emitter and Receiver units must be supplied with 24Vdc±20% power supply that
guarantee safe isolation from main voltage.
The external power supply must comply with the standard EN 60204-1 (Chapter 6.4).
The electrical connections must be made according to the diagrams in this manual. In particular,
do not connect other devices to the connectors of the Emitter and Receiver.
For reliability of operation, when a diode jumper supply unit is used, its output capacity must be
at least 2000µF for each absorbed A.
EMITTER CONNECTIONS
MXL L / MXL T MXL / MXL U
5 poles M12 connector
PIN COLOR NAME TYPE DESCRIPTION FUNCTIONING
1 BROWN 24VDC +24VDC power
supply -
3 BLUE 0VDC 0VDC power supply -
5 GREY FE Ground connection -
2 WHITE TEST
INPUT
TEST request - Operation without TEST (+24VDC)
- TEST request (Transition
+24VDC -> 0VDC or open circuit)
4 BLACK N.C. - N.C. -
Table 1 - Emitter connections
M12 - 5 poles
(To the sensors
connector) M12 - 5 poles

VISION MXL
16 8540687 • 29/03/2010 • Rev.10
RECEIVER CONNECTIONS
MXL L / MXL T MXL / MXL U
12 poles M16 connector
PIN COLOR NAME TYPE DESCRIPTION FUNCTIONING
D GREY SUPPLY_A - Supply A
SUPPLY_A : 0Vdc
SUPPLY_B : 24Vdc MANUAL
(see Table 4)
B GREEN SUPPLY_B - Supply B
SUPPLY_A : 24Vdc
SUPPLY_B : 0Vdc AUTOMATIC
(see Table 3)
H PURPLE FE - Ground connection -
A GREY-PINK OSSD1 OUTPUT
K YELLOW OSSD2 OUTPUT Static safety outputs PNP active high
L BROWN SENSOR1 INPUT
M BLUE SENSOR2 INPUT Muting sensors
< 5VDC (with <3mA) :
sensor free
11÷30 VDC (with 6
÷
30mA):
sensor occupied
J RED-BLUE FBK_K1K2/
RESTART INPUT External contactors
feedback +
RESTART input
F RED OVERRIDE INPUT Override request
C WHITE MUTING
ENABLE INPUT Muting enabling
request
E PINK TIMEOUT INPUT Timeout Selection
< 5VDC (I <3mA) : OFF
11÷30 VDC (I = 6
÷
30mA): ON
G BLACK MUT_LAMP OUTPUT Muting lamp output PNP active high
Table 2 - Receiver connections
5 poles M12 connector
This connector must be wired to the 5 poles M12 male connector connected to the muting arms.
WARNINGS REGARDING THE CONNECTION CABLES
•For connections over 50m long, use cables with a cross-section area of 1 mm2.
•The power supply to the light curtain should be kept separate from that to other electric power
equipment (electric motors, inverters, frequency converters) or other sources of disturbance.
•Connect the Emitter and the Receiver to the ground outlet.
•The connection cables must follow a different route to that of the other power cables.
M12 - 5 poles
(To the sensors
connector) M16 - 12 poles

VISION MXL
8540687 • 29/03/2010 • Rev.10 17
Example of connection in MANUAL mode of operation with feedback of K1K2
external contactors, pulse OVERRIDE and MUTING timeout = 30 s
Figure 18
Example of connection in AUTOMATIC mode of operation with feedback of K1K2 external
contactors, OVERRIDE with continuous action and MUTING timeout = 90 min
Figure 19
ÎIf the TEST function is not required by the application, connect pin 2 of the emitter to
+24Vdc.

VISION MXL
18 8540687 • 29/03/2010 • Rev.10
CONFIGURATION AND MODE OF OPERATIONS
The mode of operation of VISION MXL curtain is set thanks to connections to be carried out on
connector 12 poles M16 of the Receiver (Table 3 and Table 4).
AUTOMATIC MODE
The VISION MXL light curtain does not dispose of a start/restart interlock circuit in
automatic mode. In most applications this safety function is necessary. Please consider
the risk-analysis of your application about this matter.
In AUTOMATIC operation mode, the two static outputs OSSD1 and OSSD2 follow the status of
the guarded opening.
•with the area guarded clear, the outputs will supply +24VDC
•with the area occupied they will supply 0VDC.
OPERATION MODE CONNECTIONS
AUTOMATIC without K1-K2
feedback control
AUTOMATIC with
K1-K2 feedback control
Table 3 - Automatic mode
MANUAL MODE
Use of manual mode (start/restart interlock activated) is compulsory if the safety device
controls an opening to protect a danger area and a person, after passing through the
opening, may remain in the danger area without being detected (use as 'trip device'
according to IEC 61496). Failure to comply with this rule may result in very serious
hazards for the persons exposed.
In this operating mode the safety outputs OSSD1 and OSSD2 are activated (+24VDC) only if
the protected area is free and after the reception of the RESTART signal, using a push
button (ref.Table 4).
The series of control contacts of external relays and RESTART button guarantees that
the curtain is rearmed only if K1K2 external relays are not excited (control contacts
closed).
After an interception of the protected area, the safety outputs will be de-activated. To re-activate
them it will be necessary to repeat the sequence described above. The RESTART command is
active with a voltage of +24VDC. The minimum duration of the RESTART command is 100ms.

VISION MXL
8540687 • 29/03/2010 • Rev.10 19
OPERATION MODE CONNECTIONS
MANUAL without K1-K2
feedback control
MANUAL with K1-K2
feedback control
Table 4 - Manual Mode
SELECTING THE MAXIMUM DURATION OF MUTING AND OVERRIDE TYPE
MXL receiver inputs allow to configure the maximum duration of Muting condition (timeout) and
the Override type to be adopted.
At start up it is necessary to correctly connect the various inputs in order to achieve correct
operation, as indicated below.
SELECTED
MUTING
TIMEOUT
OVERRIDE
TYPE CONNECTION
Continuous action
command
30sec
Pulse command
Table of contents
Other Reer Security Sensor manuals

Reer
Reer JANUS Quick start guide
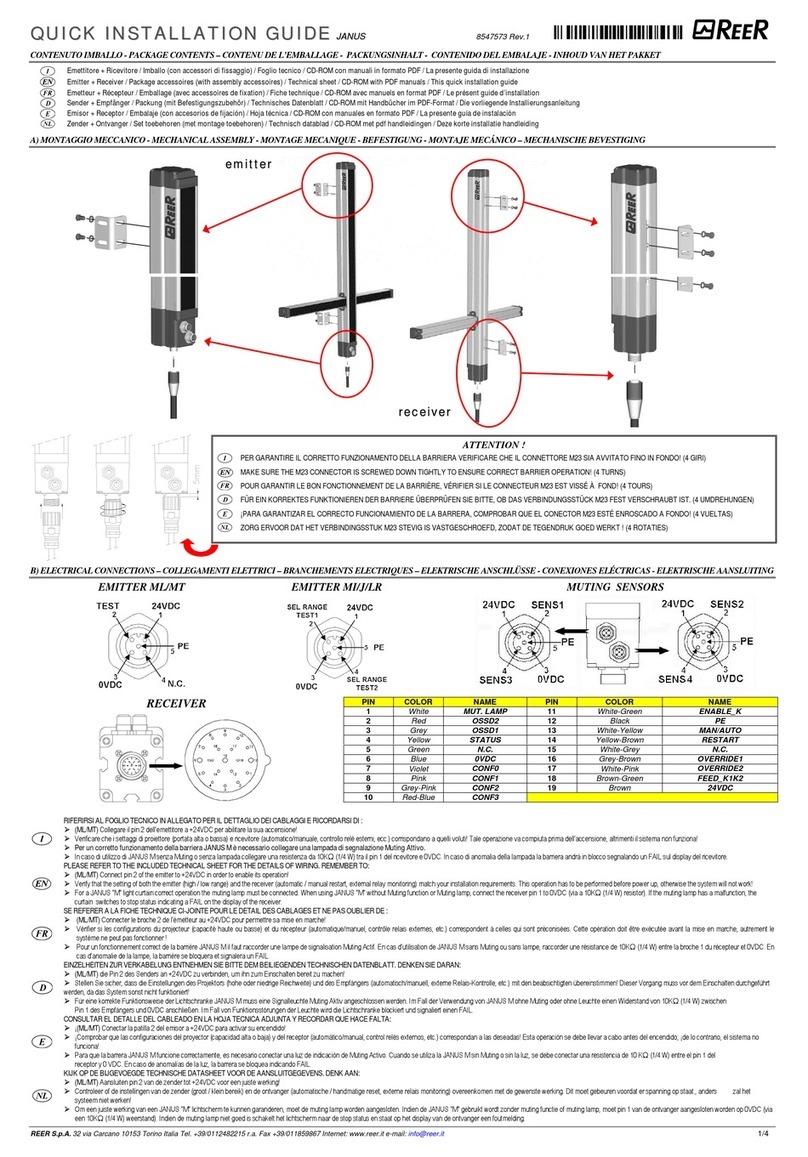
Reer
Reer JANUS User manual

Reer
Reer ADMIRAL Quick start guide
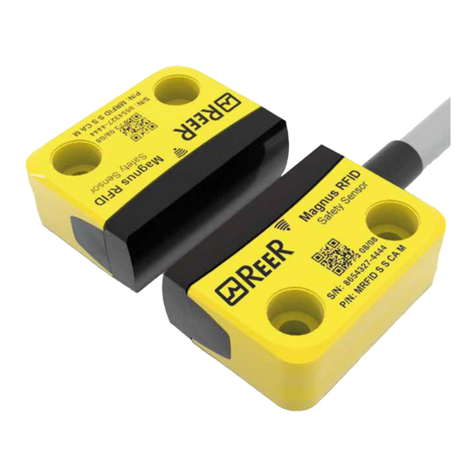
Reer
Reer Magnus RFID S Series Quick start guide
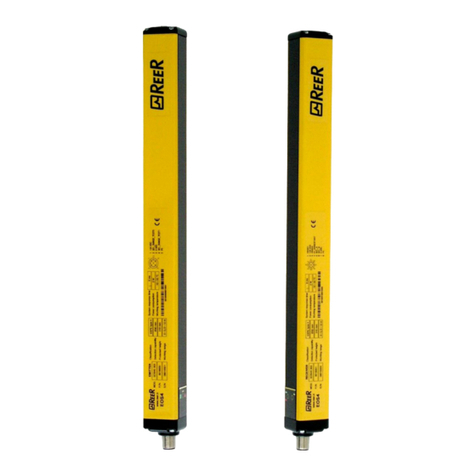
Reer
Reer EOS4 Series Quick start guide

Reer
Reer SAFEGATE S Installation and operating instructions
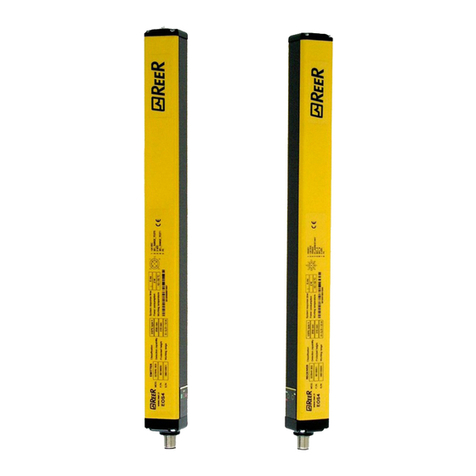
Reer
Reer EOS2 A User manual
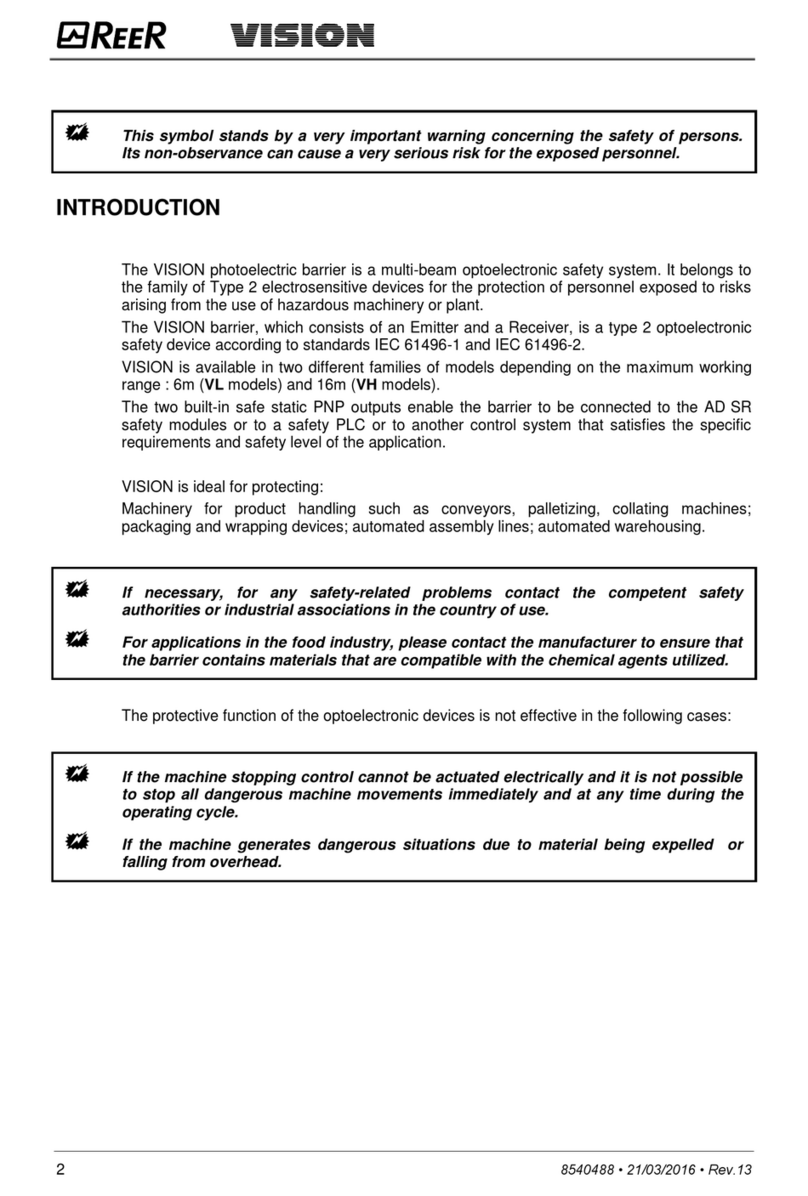
Reer
Reer VISION V3BL User manual
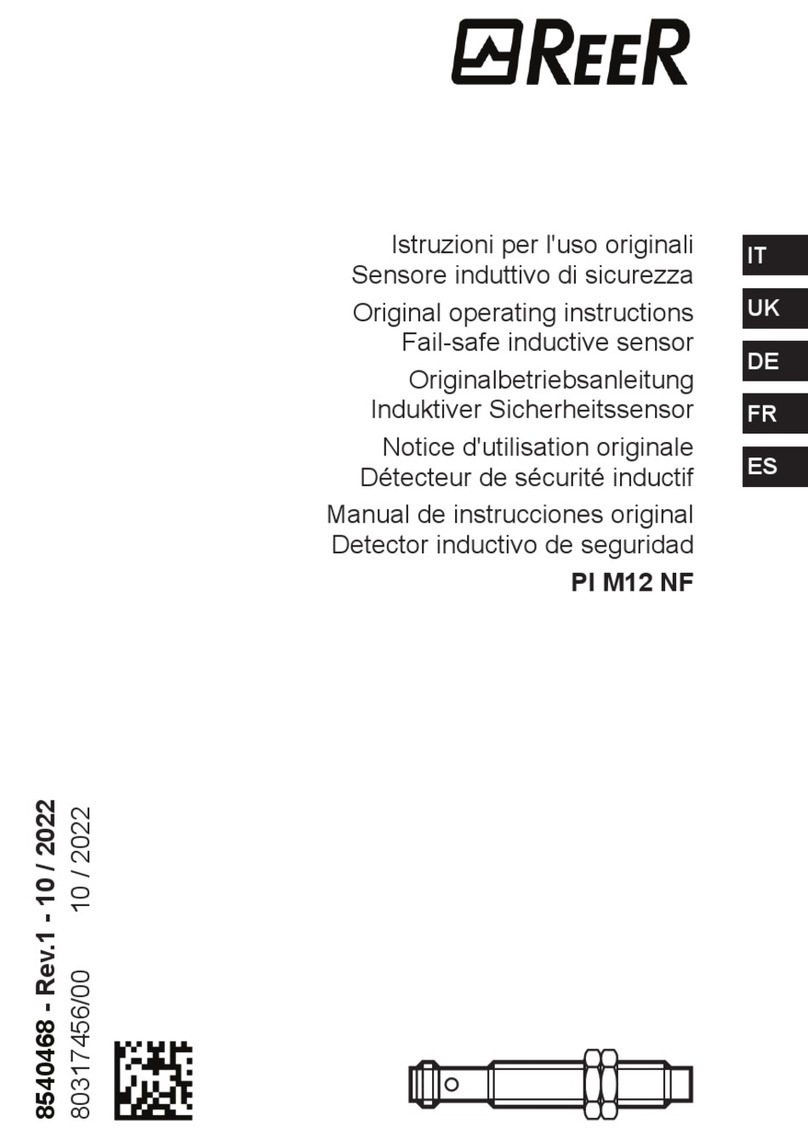
Reer
Reer PI M12 NF User manual
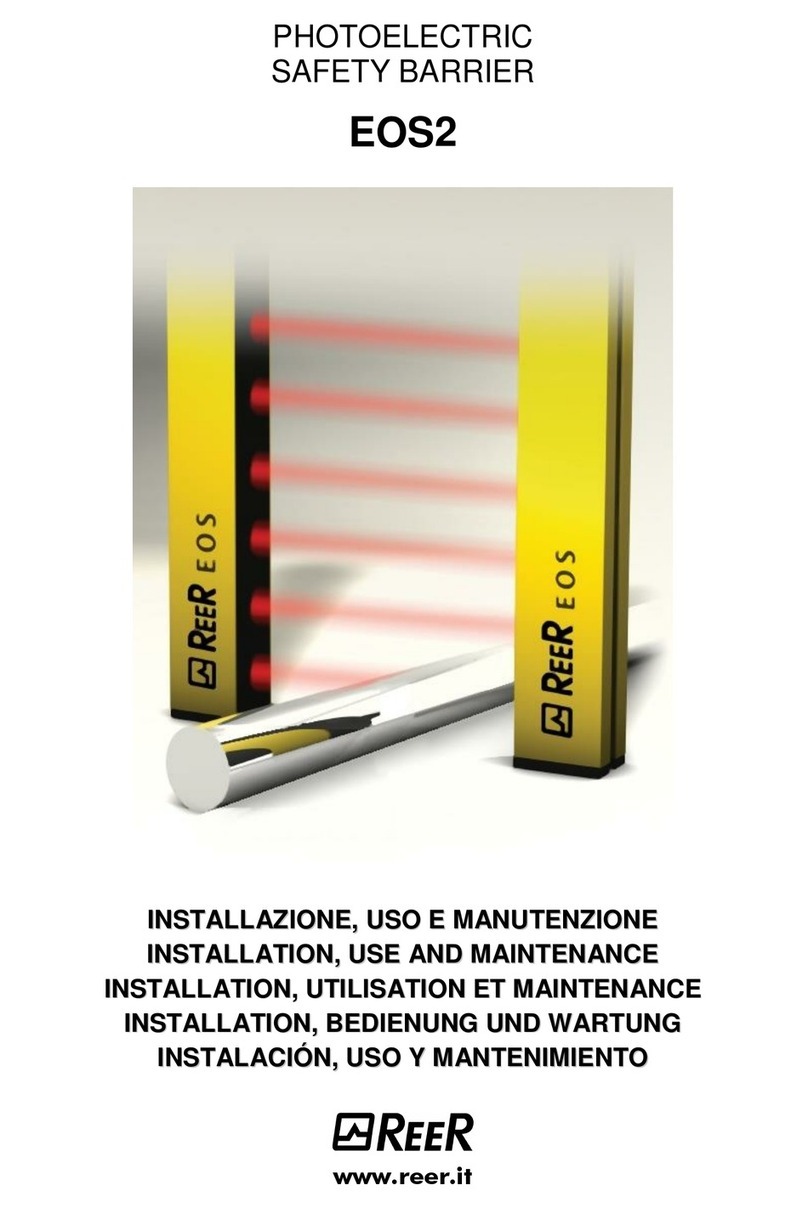
Reer
Reer EOS2 Quick start guide