Samson foundation 3787 Service manual




















Other manuals for foundation 3787
1
Other Samson Controllers manuals
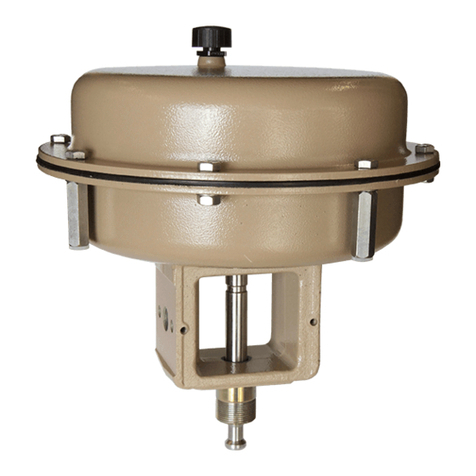
Samson
Samson 3271 Service manual
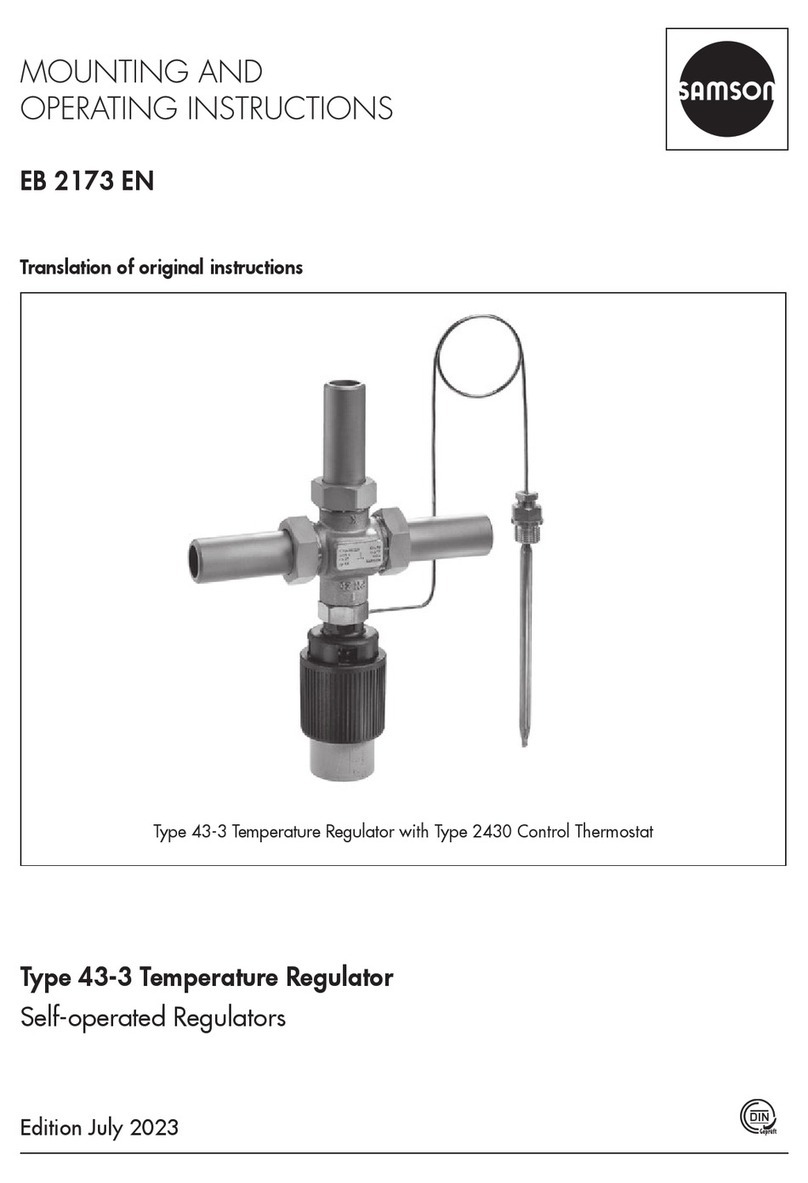
Samson
Samson 43-3 Service manual
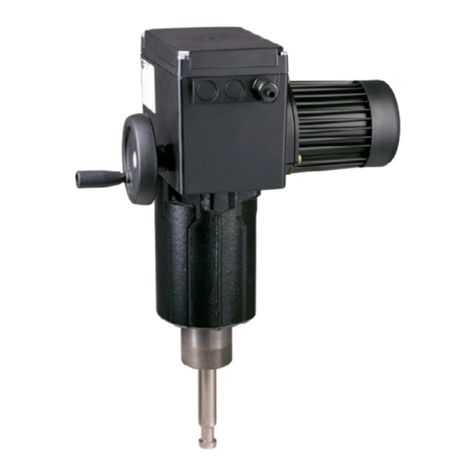
Samson
Samson 3375-10 Setup guide

Samson
Samson 41-23 Series Service manual

Samson
Samson Trovis 6400 Service manual

Samson
Samson TROVIS 5433 Service manual
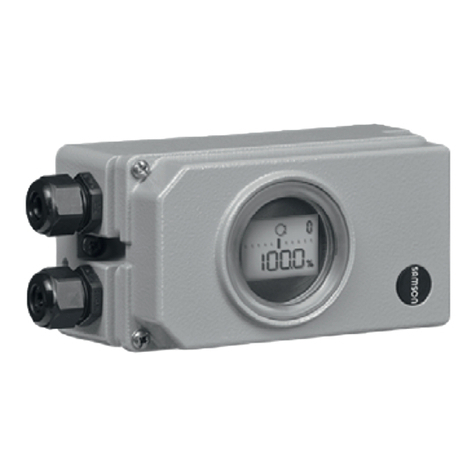
Samson
Samson 3730 Series Service manual
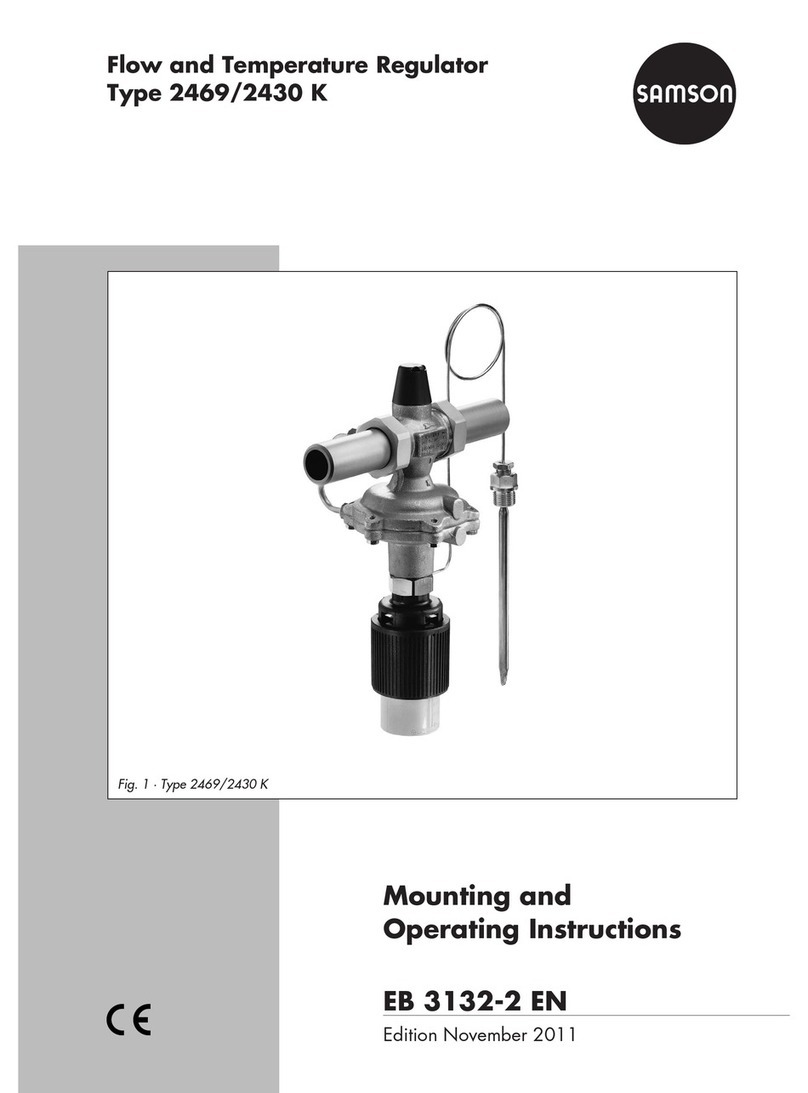
Samson
Samson 2469 Service manual

Samson
Samson 1060 Operating manual
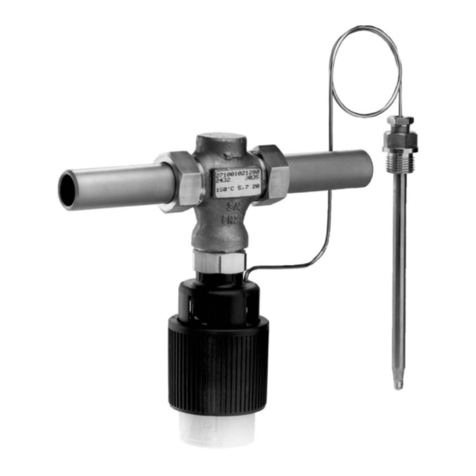
Samson
Samson 43-1 Service manual
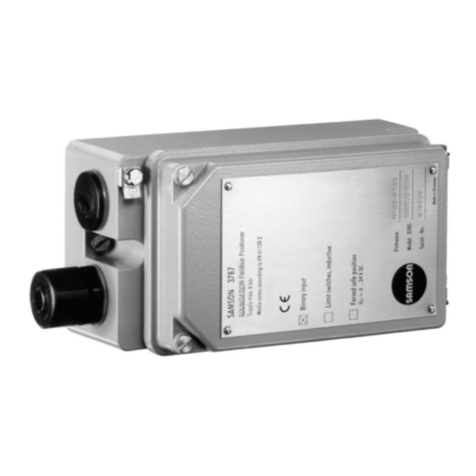
Samson
Samson foundation 3787 Service manual
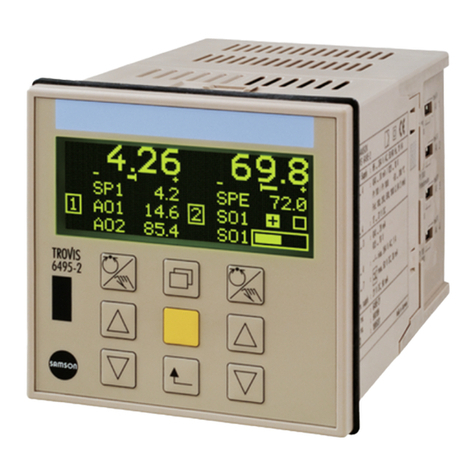
Samson
Samson TROVIS 6495 Series Service manual
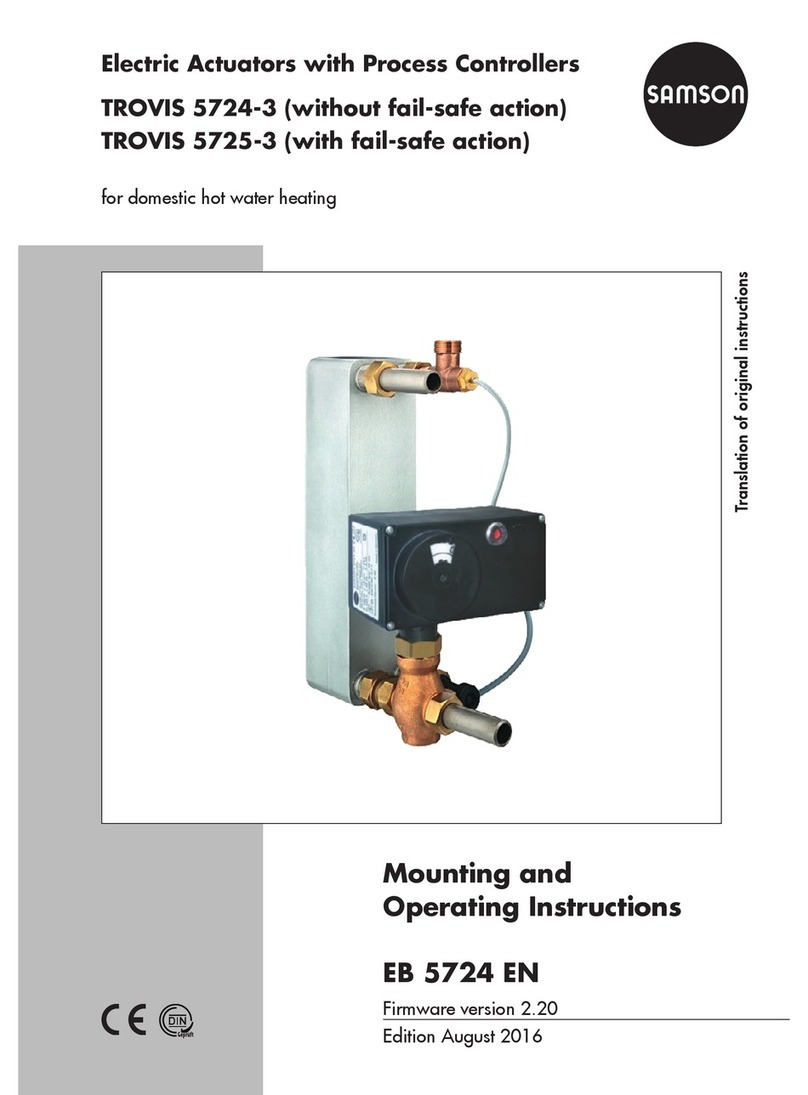
Samson
Samson TROVIS 5724-3 Service manual

Samson
Samson 42-37 Service manual
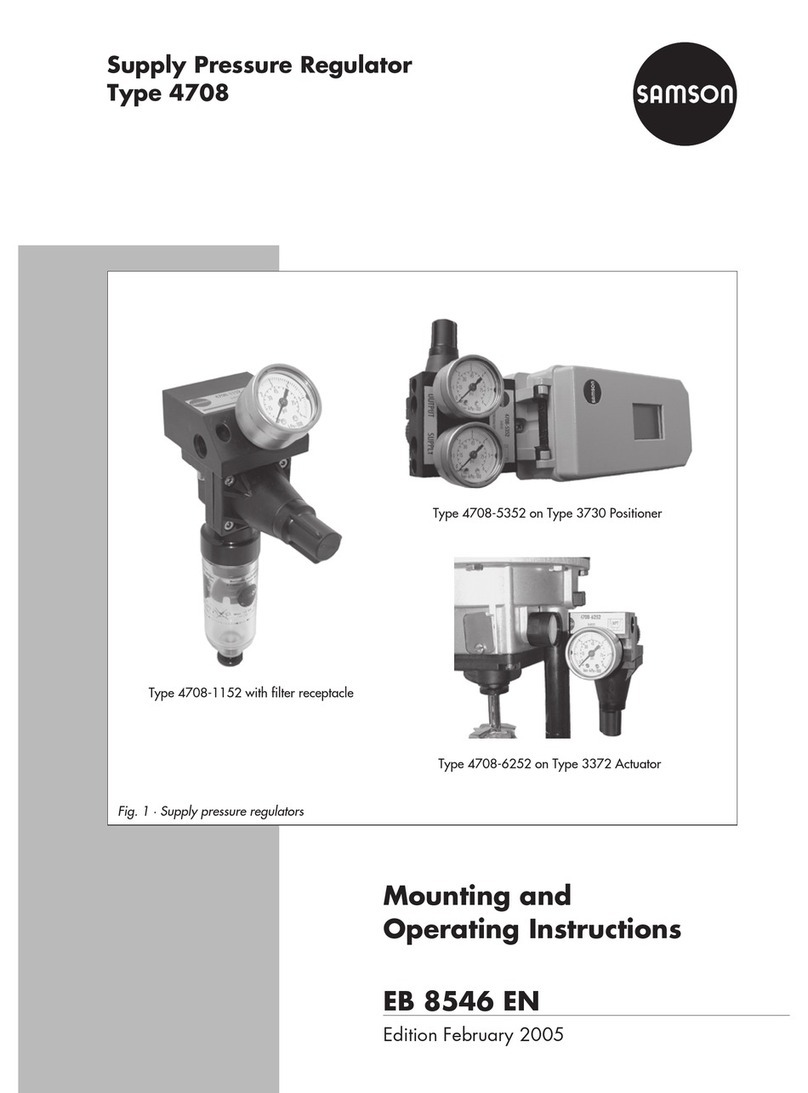
Samson
Samson Type 4708 Service manual
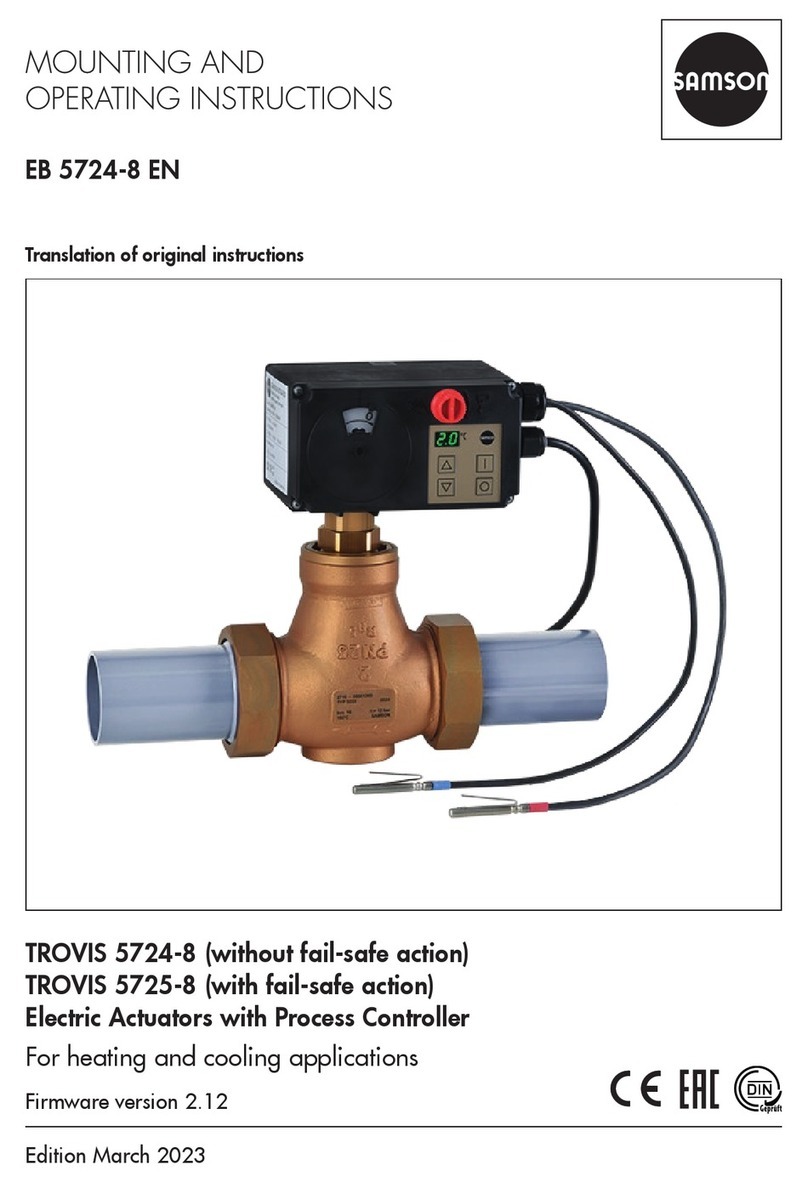
Samson
Samson TROVIS 5724-8 Service manual
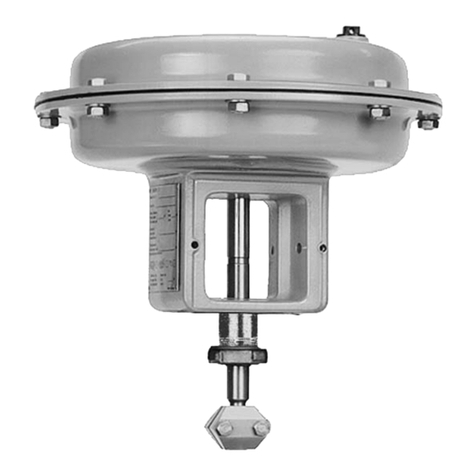
Samson
Samson 3277 Service manual

Samson
Samson TROVIS 5757-3 Instruction sheet
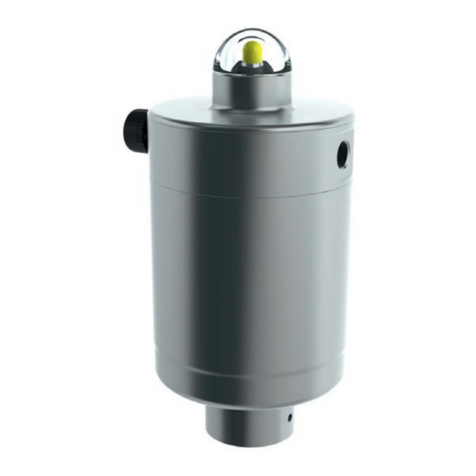
Samson
Samson EB 8315 EN User manual

Samson
Samson TROVIS 5575 Service manual
Popular Controllers manuals by other brands
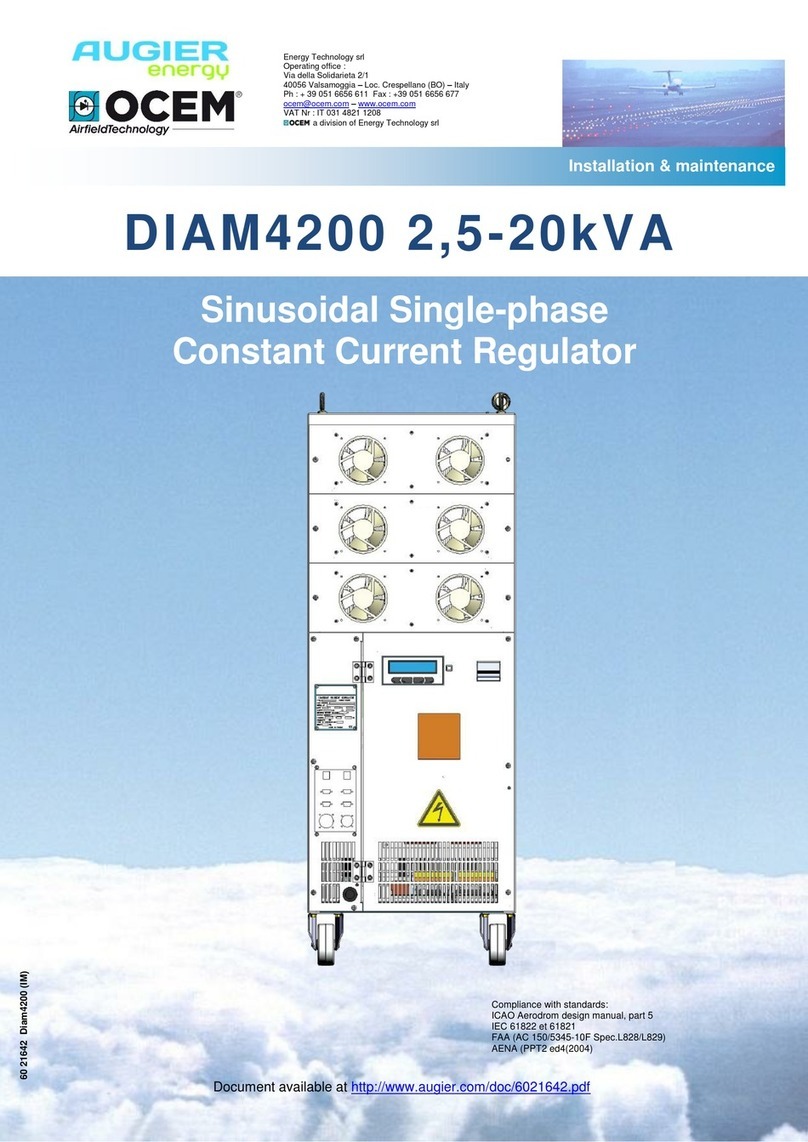
Energy Technology
Energy Technology OCEM AUGIER DIAM4200 Series Installation & maintenance
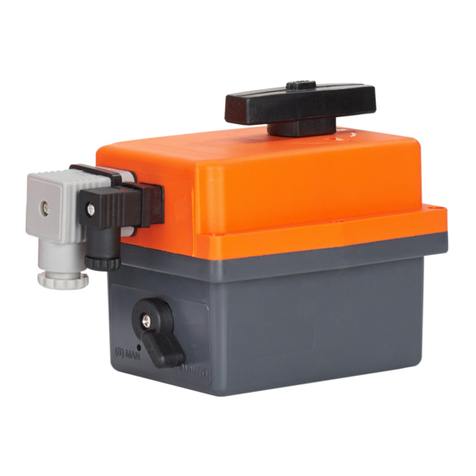
GF
GF EA 04 operating instructions
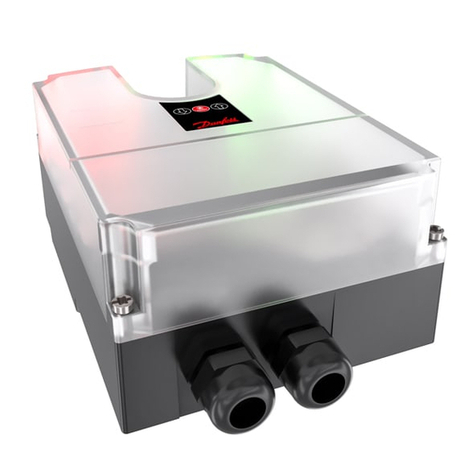
Danfoss
Danfoss AMEi 6 iNET operating guide

Siemens
Siemens SIMATIC EM 300 manual
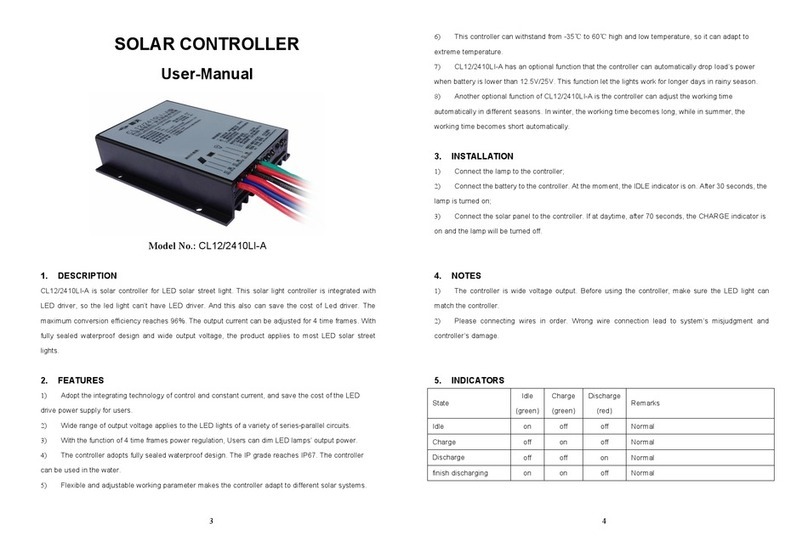
Nanjing Putian Datang Information Electronics Co., Ltd.
Nanjing Putian Datang Information Electronics Co., Ltd. CL12/2410LI-A user manual
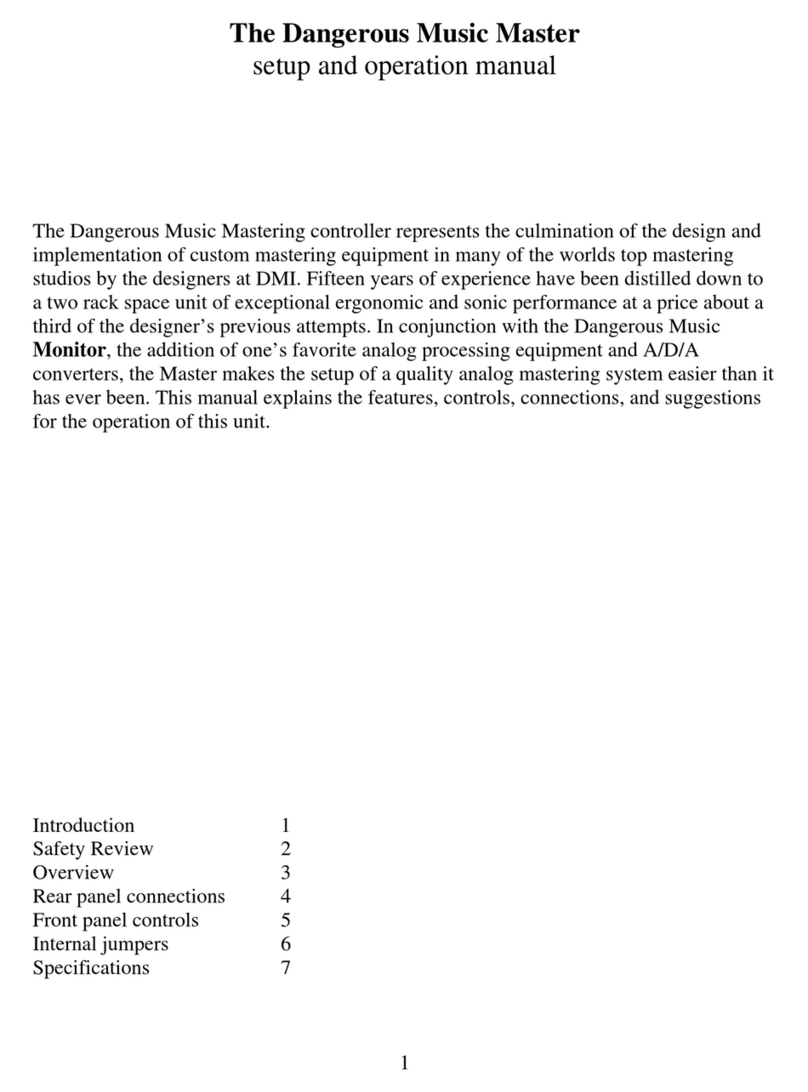
Dangerous Music
Dangerous Music Master Setup and operation manual