SICK Flexi Gateway GCAN1 User manual

OPERATING INSTRUCTIONS
Flexi Gateway GCAN1
Expansion module - gateway

Described product
Flexi Gateway GCAN1
Manufacturer
SICK AG
Erwin-Sick-Str. 1
79183 Waldkirch
Germany
Legal information
This work is protected by copyright. Any rights derived from the copyright shall be
reserved for SICK AG. Reproduction of this document or parts of this document is
only permissible within the limits of the legal determination of Copyright Law. Any modi‐
fication, abridgment or translation of this document is prohibited without the express
written permission of SICK AG.
The trademarks stated in this document are the property of their respective owner.
© SICK AG. All rights reserved.
Original document
This document is an original document of SICK AG.
CANopen®
CANopen® is a registered trademark, licensed by CiA - CAN in Automation e.V., Ger‐
many.
2O P E R A T I N G I N S T R U C T I O N S | Flexi Gateway GCAN1 8024587/1CUS/2022-09-23 | SICK
Subject to change without notice

Contents
1 About this document........................................................................ 5
1.1 Purpose of this document........................................................................ 5
1.2 Scope......................................................................................................... 5
1.3 Target groups and structure of these operating instructions................ 6
1.4 Further information................................................................................... 6
1.5 Symbols and document conventions...................................................... 6
2 Safety information............................................................................ 8
2.1 General safety notes................................................................................ 8
2.2 Intended use............................................................................................. 8
2.3 Improper use............................................................................................. 8
2.4 Cybersecurity............................................................................................ 9
2.5 Requirements for the qualification of personnel.................................... 9
3 Product description........................................................................... 10
3.1 Configuration of the safety controller...................................................... 10
3.2 Overview of the module............................................................................ 11
3.3 Design and function of the module......................................................... 11
3.4 Status indicators....................................................................................... 12
4 Project planning................................................................................ 13
4.1 Design........................................................................................................ 13
4.2 Integration into the network..................................................................... 13
4.2.1 Network services and ports.................................................... 13
4.2.2 Integration via the fieldbus interface..................................... 14
5 Mounting............................................................................................. 15
5.1 Mounting procedure................................................................................. 15
5.2 Module exchange...................................................................................... 15
6 Electrical installation........................................................................ 16
6.1 Connecting................................................................................................ 16
6.1.1 CAN connection....................................................................... 16
7 Configuration..................................................................................... 17
7.1 Delivery state............................................................................................ 17
7.2 Overview.................................................................................................... 17
7.3 Offline, online and security configuration............................................... 17
7.4 Configuring the network interfaces......................................................... 18
7.4.1 Configuring the higher-level controller.................................... 18
7.4.2 Enabling emergency messages.............................................. 19
7.4.3 Configuring the output data (routing to CPU)......................... 19
7.4.4 Configuring the input data (routing to network)..................... 19
7.4.5 Configuring CAN listen mode and associated output data... 20
CONTENTS
8024587/1CUS/2022-09-23 | SICK O P E R A T I N G I N S T R U C T I O N S | Flexi Gateway GCAN1 3
Subject to change without notice

8 Commissioning.................................................................................. 22
8.1 Check during commissioning and modifications.................................... 22
9 Operation............................................................................................ 23
9.1 Operation of the display........................................................................... 23
9.2 Display menu............................................................................................ 23
9.3 Status indicators....................................................................................... 23
9.4 Regular thorough check........................................................................... 26
10 Maintenance...................................................................................... 27
10.1 Regular thorough check........................................................................... 27
11 Troubleshooting................................................................................. 28
11.1 Possible faults........................................................................................... 28
12 Decommissioning............................................................................. 29
12.1 Disposal..................................................................................................... 29
13 Technical data.................................................................................... 30
13.1 Data sheet................................................................................................. 30
13.2 Data exchange in the network................................................................. 31
13.2.1 CANopen................................................................................... 31
13.3 Dimensional drawings.............................................................................. 39
14 Ordering information........................................................................ 40
14.1 Scope of delivery....................................................................................... 40
14.2 Ordering information for main module.................................................... 40
14.3 Ordering information for expansion module........................................... 40
14.4 Ordering information for accessories...................................................... 40
15 Annex.................................................................................................. 42
15.1 Conformities and certificates................................................................... 42
15.1.1 EU declaration of conformity................................................... 42
15.1.2 UK declaration of conformity.................................................. 42
16 List of figures..................................................................................... 43
17 List of tables....................................................................................... 44
CONTENTS
4O P E R A T I N G I N S T R U C T I O N S | Flexi Gateway GCAN1 8024587/1CUS/2022-09-23 | SICK
Subject to change without notice

1 About this document
1.1 Purpose of this document
These operating instructions contain the information required during the life cycle of the
safety controller.
Operating instructions of the safety controller must be made available to all people who
work with the device.
1.2 Scope
Product
This document applies to the following products:
•Product code: Flexi Gateway GCAN1
•“Operating instructions” type label entry: 8024572
Document identification
Document part number:
•This document: 8024587
•Available language versions of this document: 8024572
You can find the current version of all documents at www.sick.com.
Other documents relevant for the product
Table 1: Available documents
Document Title Part number
Operating instructions Flexi Compact safety control‐
ler
8024573
Operating instructions FLX3-XTDI1
Expansion module for safety
controllers
8024571
Operating instructions FLX3-XTDO1
Expansion module for safety
controllers
8024570
Operating instructions FLX0-GPNT1
Expansion module for safety
controllers
8024567
Operating instructions FLX0-GETC1
Expansion module for safety
controllers
8024566
Operating instructions FLX0-GCAN1
Expansion module for safety
controllers
8024572
Operating instructions Flexi Loop Safe Series Con‐
nection Hardware
8015834
Operating instructions Flexi Loop in the Safety
Designer Software
8018174
Competence brochure Guide for Safe Machinery 8008007
ABOUT THIS DOCUMENT 1
8024587/1CUS/2022-09-23 | SICK O P E R A T I N G I N S T R U C T I O N S | Flexi Gateway GCAN1 5
Subject to change without notice

1.3 Target groups and structure of these operating instructions
These operating instructions are intended for the following target groups:project devel‐
opers (planners, developers, designers), installers, electricians, safety experts (such as
CE authorized representatives, compliance officers, people who test and approve the
application), operators, and maintenance personnel.
These operating instructions are organized by the life phases of the device: project
planning, mounting, electrical installation, commissioning, operation and maintenance.
The table below shows the target groups and how – for many applications – these are
typically divided up between the manufacturer and the entity operating the machine in
which the device is to be integrated:
Area of responsibility Target group Specific chapters of these operating instruc‐
tions 1)
Manufacturer Project developers
(planners, developers,
designers)
Project planning, page 13
Technical data, page 30
Installers Mounting, page 15
Electricians Electrical installation, page 16
Safety experts Project planning, page 13
Commissioning, page 22
Technical data, page 30
Operating entity Operators Troubleshooting, page 28
Maintenance staff Troubleshooting, page 28
Ordering information, page 40
1) Chapters not listed here are intended for all target groups. All target groups must follow all of the safety
and warning instructions in all chapters of the operating instructions!
In other applications, the operating organization is also the manufacturer of the equip‐
ment with the corresponding allocation of the target groups.
1.4 Further information
www.sick.com
The following information is available via the Internet:
•Data sheets and application examples
•CAD files and dimensional drawings
•Certificates (such as the EU declaration of conformity)
•Guide for Safe Machinery. Six steps to a safe machine
•Safety Designer (software for configuring safety solutions made by SICK AG)
1.5 Symbols and document conventions
The following symbols and conventions are used in this document:
Safety notes and other notes
DANGER
Indicates a situation presenting imminent danger, which will lead to death or serious
injuries if not prevented.
1 ABOUT THIS DOCUMENT
6O P E R A T I N G I N S T R U C T I O N S | Flexi Gateway GCAN1 8024587/1CUS/2022-09-23 | SICK
Subject to change without notice

WARNING
Indicates a situation presenting possible danger, which may lead to death or serious
injuries if not prevented.
CAUTION
Indicates a situation presenting possible danger, which may lead to moderate or minor
injuries if not prevented.
NOTICE
Indicates a situation presenting possible danger, which may lead to property damage if
not prevented.
NOTE
Indicates useful tips and recommendations.
Instructions to action
bThe arrow denotes instructions to action.
1. The sequence of instructions for action is numbered.
2. Follow the order in which the numbered instructions are given.
✓The check mark denotes the result of an instruction.
ABOUT THIS DOCUMENT 1
8024587/1CUS/2022-09-23 | SICK O P E R A T I N G I N S T R U C T I O N S | Flexi Gateway GCAN1 7
Subject to change without notice

2 Safety information
2.1 General safety notes
Product integration
DANGER
The product can not offer the expected protection if it is integrated incorrectly.
bPlan the integration of the product in accordance with the machine requirements
(project planning).
bImplement the integration of the product in accordance with the project planning.
Mounting and electrical installation
DANGER
Death or severe injury due to electrical voltage and/or an unexpected startup of the
machine
bMake sure that the machine is (and remains) disconnected from the voltage
supply during mounting and electrical installation.
bMake sure that the dangerous state of the machine is and remains switched off.
Repairs and modifications
DANGER
Improper work on the product
A modified product may not offer the expected protection if it is integrated incorrectly.
bApart from the procedures described in this document, do not repair, open, manip‐
ulate or otherwise modify the product.
2.2 Intended use
The Flexi Compact safety controller is a freely configurable control for safety applica‐
tions.
Sensors and switching elements (e.g. light curtains, laser scanners, switches, sensors,
encoders, emergency stop pushbuttons) are connected to the safety controller and
are linked logically. The corresponding actuators of the machines or systems can be
switched off safely via the switching outputs of the safety controller.
The gateway is an extension module of the safety controller. The gateway module ena‐
bles a safety controller to send data to a network for control and diagnostic purposes,
and to receive data from the network.
Incorrect use, improper modification or manipulation of the product will invalidate any
warranty from SICK; in addition, any responsibility and liability of SICK for damage and
secondary damage caused by this is excluded.
The product is only suitable for use in industrial environments.
2.3 Improper use
Among others, the safety controller is not suitable for the following applications:
•Outdoors
•Underwater
2 SAFETY INFORMATION
8O P E R A T I N G I N S T R U C T I O N S | Flexi Gateway GCAN1 8024587/1CUS/2022-09-23 | SICK
Subject to change without notice

•In explosion-hazardous areas
•In residential areas
2.4 Cybersecurity
Overview
To protect against cybersecurity threats, it is necessary to continuously monitor and
maintain a comprehensive cybersecurity concept. A suitable concept consists of organi‐
zational, technical, procedural, electronic, and physical levels of defense and considers
suitable measures for different types of risks. The measures implemented in this
product can only support protection against cybersecurity threats if the product is used
as part of such a concept.
You will find further information at www.sick.com/psirt, e.g.:
•General information on cybersecurity
•Contact option for reporting vulnerabilities
•Information on known vulnerabilities (security advisories)
Further topics
•"Network services and ports", page 13
2.5 Requirements for the qualification of personnel
The product must be configured, installed, connected, commissioned, and serviced by
qualified safety personnel only.
Project planning
You need safety expertise to implement safety functions and select suitable products
for that purpose. You need expert knowledge of the applicable standards and regula‐
tions.
Mounting, electrical installation and commissioning
You need suitable expertise and experience. You must be able to assess if the machine
is operating safely.
Configuration
You need suitable expertise and experience. You must be able to assess if the machine
is operating safely.
Operation and maintenance
You need suitable expertise and experience. You must be instructed in machine oper‐
ation by the machine operator. For maintenance, you must be able to assess if the
machine is operating safely.
SAFETY INFORMATION 2
8024587/1CUS/2022-09-23 | SICK O P E R A T I N G I N S T R U C T I O N S | Flexi Gateway GCAN1 9
Subject to change without notice

3 Product description
3.1 Configuration of the safety controller
Configuration of the safety controller
A safety controller comprises the following components:
•A main module
•Up to 12 optional expansion modules (excluding maximum 1 gateway)
I3
I5
Q1
Q7
I4
I6
Q2
Q8
A2
I7
Q3
Q5
A1
I8
Q4
Q6
I2
PWR
I1
I3
I5
Q1
Q7
I4
I6
Q2
Q8
A2
I7
Q3
Q5
A1
I8
Q4
Q6
I2
PWR
I1
I3
I5
Q1
Q7
I4
I6
Q2
Q8
A2
I7
Q3
Q5
A1
I8
Q4
Q6
I2
PWR
I1
I3
I5
Q1
Q7
I4
I6
Q2
Q8
A2
I7
Q3
Q5
A1
I8
Q4
Q6
I2
PWR
I1
I3
I5
Q1
Q7
I4
I6
Q2
Q8
A2
I7
Q3
Q5
A1
I8
Q4
Q6
I2
PWR
I1
I3
I5
Q1
Q7
I4
I6
Q2
Q8
A2
I7
Q3
Q5
A1
I8
Q4
Q6
I2
PWR
I1
I3
I5
Q1
Q7
I4
I6
Q2
Q8
A2
I7
Q3
Q5
A1
I8
Q4
Q6
I2
PWR
I1
I3
I5
Q1
Q7
I4
I6
Q2
Q8
A2
I7
Q3
Q5
A1
I8
Q4
Q6
I2
PWR
I1
I3
I5
Q1
Q7
I4
I6
Q2
Q8
A2
I7
Q3
Q5
A1
I8
Q4
Q6
I2
PWR
I1
I3
I5
Q1
Q7
I4
I6
Q2
Q8
A2
I7
Q3
Q5
A1
I8
Q4
Q6
I2
PWR
I1
I3
I5
Q1
Q7
I4
I6
Q2
Q8
A2
I7
Q3
Q5
A1
I8
Q4
Q6
I2
PWR
I1
1
2
3
FLEXIcompact
CV
I1
I3
I7
X1
I2
I4
I8
X2
X4
I5
I9
I11
X3
I6
I10
I12
I15
I17
X5
Q3
I16
I18
X6
Q4
A2
I19
X7
Q1
A1
I20
X8
Q2
I14
PWR
I13
Figure 1: Example maximum configuration
1Main module
2Expansion module - gateway
3IO expansion module
Complementary information
•The gateway and IO expansion modules can be arranged arbitrarily.
3 PRODUCT DESCRIPTION
10 O P E R A T I N G I N S T R U C T I O N S | Flexi Gateway GCAN1 8024587/1CUS/2022-09-23 | SICK
Subject to change without notice

3.2 Overview of the module
1
2
3
4
Figure 2: Gateway expansion module
1Release element of the module
2Display
3D-Sub male connector
4Backplane bus
3.3 Design and function of the module
Prerequisites
•The module can only be operated with a main module.
Configuration
Table 2: Interfaces of the module
Description Quantity
CAN (D-SUB male connector) 1
Function
The module enables a safety controller to send data to a network for control and
diagnostic purposes, and to receive data from the network.
The module offers the following functions:
•Integration into a CANopen network
•CAN listen mode
Complementary information
•Voltage is supplied to the module via the backplane bus. Communication with the
main module of the safety controller also occurs via the backplane bus.
PRODUCT DESCRIPTION 3
8024587/1CUS/2022-09-23 | SICK O P E R A T I N G I N S T R U C T I O N S | Flexi Gateway GCAN1 11
Subject to change without notice

3.4 Status indicators
Status indicators
Figure 3: Status indicators, CAN listen mode
deactivated
Figure 4: Status indicators, CAN listen mode
activated
Status indicator
Table 3: Status indicator
Labeling Color Function
PWR (power) Green/Red Device status
RUN Green CANopen operational status
ERR Red CANopen error state
P1 1) Green/yellow/red/white Status D-SUB male connector
ID –
(text field)
CANopen node ID
LMS 2) Green/Red CAN listen mode: Status
CAN 2) Green/Red CAN listen mode: CAN control‐
ler error state
1 … 16 2) Green/red/gray CAN listen mode: Instances
1) Status display only appears when CAN listen mode is not activated.
2) Status display only appears when CAN listen mode is activated.
Further topics
•"Status indicators", page 23
•"Troubleshooting", page 28
•"Operation", page 23
3 PRODUCT DESCRIPTION
12 O P E R A T I N G I N S T R U C T I O N S | Flexi Gateway GCAN1 8024587/1CUS/2022-09-23 | SICK
Subject to change without notice

4 Project planning
4.1 Design
Installation site
•The safety controller must be protected against condensation and conductive
contamination, e.g. in an IP54 control cabinet.
•Mounting on a 35mm × 7.5mm mounting rail in accordance with IEC60715.
•The mounting rail is connected to the functional earth.
•Mounting rail is mounted on a mounting plate.
•Mounting plate is connected to functional earth.
•Mounting in a vertical orientation (on a horizontal mounting rail).
•Take suitable ESD protection measures.
Air circulation
To ensure sufficient air circulation and cooling, sufficient distance must be kept in the
control cabinet above and below the module.
Provide an adequate clearance in front of the module (front side) for the connected
cables.
≥ 30≥ 30
≥ 25
Figure 5: Clearances for adequate air circulation
Recommended distance:
•Above and below the module: ≥30mm
•In front of the module: ≥25mm
4.2 Integration into the network
4.2.1 Network services and ports
Network services:
•CANopen
•EtherCAT® (backplane bus)
PROJECT PLANNING 4
8024587/1CUS/2022-09-23 | SICK O P E R A T I N G I N S T R U C T I O N S | Flexi Gateway GCAN1 13
Subject to change without notice

4.2.2 Integration via the fieldbus interface
Prerequisites
•EDS file (device description file) is installed in the hardware catalog of the higher-
level controller.
Parameters to be configured
Parameter:
•Valid node ID (CANopen address)
•Correct data transmission rate
You can configure the parameters via the following interfaces:
•Safety Designer
•Configuration software for the relevant fieldbus network
•CANopen server
•Display on the gateway
Changes to the Node ID and baud rate only take effect after a restart.
Complementary information
You can find the required device description file and the device symbol for integration
into a higher-level controller in the following locations:
•On the Internet on the gateway product page at www.sick.com
4 PROJECT PLANNING
14 O P E R A T I N G I N S T R U C T I O N S | Flexi Gateway GCAN1 8024587/1CUS/2022-09-23 | SICK
Subject to change without notice

5 Mounting
5.1 Mounting procedure
For information on the mounting process, please see the operating instructions:
•“Flexi Compact” (SICK part number 8024573)
5.2 Module exchange
Approach
1. Disconnect the module and the connected components from all voltage sources.
2. Remove the module.
3. Mount the new module.
MOUNTING 5
8024587/1CUS/2022-09-23 | SICK O P E R A T I N G I N S T R U C T I O N S | Flexi Gateway GCAN1 15
Subject to change without notice

6 Electrical installation
6.1 Connecting
Prerequisites
•Mounting is completed.
•Electrical installation is carried out according to the project planning.
•Dangerous condition of the machine is and remains off during the electrical instal‐
lation.
•The outputs of the safety controller do not affect the machine during electrical
installation.
6.1.1 CAN connection
Prerequisites
Network cable requirement:
•Cable with D-SUB male connector, 9-pin
•Maximum length 1,000m in accordance with EN50173
•Shielded cables
Pin assignment
12345
6789
Figure 6: Male connector, D-Sub, 9-pin
Table 4: Pin assignment for D-SUB male connector
PIN Designation Description
1 NC Not assigned
2 CAN_L CAN signal
3 CAN_GND GND voltage supply
4 NC Not assigned
5 NC Not assigned
6 CAN_GND GND voltage supply
7 CAN_H CAN signal
8 NC Not assigned
9 NC Not assigned
Male connector CAN_SHIELD Shielding
Further topics
•"CANopen fieldbus data", page 30
6 ELECTRICAL INSTALLATION
16 O P E R A T I N G I N S T R U C T I O N S | Flexi Gateway GCAN1 8024587/1CUS/2022-09-23 | SICK
Subject to change without notice

7 Configuration
7.1 Delivery state
The device is not configured in the delivery state.
7.2 Overview
For more information on configuring the safety controller, see the operating instruc‐
tions:
•“Flexi Compact” (SICK part number 8024573)
7.3 Offline, online and security configuration
Overview
All configuration parameters are assigned to a configuration group. The configuration
groups differ, for example, when transmitting and saving the configuration.
The following configuration groups are available
•Offline configuration
•Online configuration
•Security configuration
Offline configuration
All offline configuration parameters are written to the safety controller using the Transfer
to device function. The offline configuration includes, for example, all parameters of the
hardware configuration.
These parameters can only be configured in the configuration software.
To configure the parameters, no connection to the safety controller must exist. Only
establish a connection to the safety controller when you want to transfer the configura‐
tion.
The application is stopped while the configuration is transferred to the safety controller.
The offline configuration is stored in the SmartPlug. A (defective) module can be
replaced with a compatible module without having to reconfigure the device. The offline
configuration must be compatible with the physical safety controller.
Within the offlline configuration, a distinction is made between the following configura‐
tion data.
Configuration data:
•Safety configuration
Configuration data that affect the safety function of a device, e.g., configuration of
safety capable inputs, safety outputs, logic, …
•Standard configuration
Configuration data that affect the non-safety function of a device, e.g., configura‐
tion of test outputs, configuration of non-safe modules.
•Non-functional configuration
Configuration data that have no effect on the functioning of the device, e.g. tag
names, comments in the logic, project information of the user
Online configuration
Each of the online configuration parameters have their own transfer option and can
be individually written to the safety controller. The online configuration includes, for
example, the parameters relating to the network settings.
CONFIGURATION 7
8024587/1CUS/2022-09-23 | SICK O P E R A T I N G I N S T R U C T I O N S | Flexi Gateway GCAN1 17
Subject to change without notice

These parameters can be configured in the configuration software or via a module with
a display.
To configure the parameters using the configuration software, a connection to the
safety controller must exist.
The application does not need to be stopped while the configuration is transferred to
the safety controller.
The online configuration is saved in and read back from the SmartPlug using the mod‐
ule position and the module type. If the module position is maintained, a (defective)
module can be replaced with a compatible module without having to reconfigure the
device. If the module position is changed, the saved parameters will not work. If, for
example, the module position of a gateway is changed, the connection parameters
need to be reconfigured before a connection to the safety controller can be established.
The old module positions are corrected when writing an offline configuration.
If online configuration parameters are configured without a SmartPlug inserted, these
settings will only apply temporarily until the safety controller is restarted or a SmartPlug
is inserted.
Security configuration
The security configuration includes the following parameters:
•Passwords for user groups
These parameters can only be configured in the configuration software.
The application does not need to be stopped while the configuration is transferred to
the safety controller.
The security configuration is saved in the SmartPlug. A (defective) module can be
replaced with a compatible module without having to reconfigure the device.
Further topics
•"Display menu", page 23
7.4 Configuring the network interfaces
7.4.1 Configuring the higher-level controller
Approach
1. Load the device description file into the configuration software of the higher-level
controller. To do so, follow the instructions in the online help or in the user manual
of the configuration tool of the fieldbus.
2. Add the gateway to the CANopen network.
3. Select and configure the process data objects (PDOs). Process data are transmit‐
ted using RPDO1…4 and TPDO1…4.
Complementary information
You can find the device description file and device symbol on the gateway product page
at www.sick.com.
It is recommended to use the heartbeat mechanism to monitor the integrity of the
process data. You should only configure nodes as a heartbeat consumer, however, if
they are a heartbeat producer and send process data to the gateway.
This could otherwise produce many error messages that will overwrite the other warning
and error messages. The "Data valid network→ Gateway" status bit could also change to
0 even though the PDOs are actually valid.
7 CONFIGURATION
18 O P E R A T I N G I N S T R U C T I O N S | Flexi Gateway GCAN1 8024587/1CUS/2022-09-23 | SICK
Subject to change without notice

Further topics
•"Configuring the output data (routing to CPU)", page 19
•"Configuring the input data (routing to network)", page 19
7.4.2 Enabling emergency messages
Approach
1. In the main navigation pane, click Configuration.
2. In the navigation pane under GCAN1, select the CANopen alarms menu item.
3. Select the All activated option.
✓The emergency messages are transmitted to the higher-level control system.
7.4.3 Configuring the output data (routing to CPU)
Overview
The gateway can receive 4process data objects (PDO), each with 8bytes of output
data, from a higher-level controller. The actual data volume and contents depends on
how the output data are configured in the higher-level control system.
The configuration of the output data includes the following points:
•Specifying the routing
•Optional: Enter the tag names for the data received from the network
Approach
1. In the main navigation pane, click Configuration.
2. In the navigation tree of the required module, select Routing to CPU.
3. Select a routing template and drag it onto a single byte or several bytes of the
output data block.
✓The bits, bytes or data formats are available as inputs in the logic editor.
✓Each bit, byte or data format inherits a default tag name from the routing.
4. If required, edit the default tag name in the Properties tab.
Complementary information
Table 5: Colors of the bytes and bits of a record
Color Meaning
Light blue The byte or the bit is empty.
Blue The byte or the bit is occupied. The relevant module, input or
output is configured in the hardware configuration of the safety
controller.
Gray The byte or the bit is occupied. The relevant module, input or
output is not yet configured in the hardware configuration of the
safety controller.
You can monitor the status of the communication with the network. A status bit for the
receipt of data from the network is provided for this. If the gateway detects a fault in the
communication, it sets the contents of the output records and the associated status bit
to Null.
7.4.4 Configuring the input data (routing to network)
Overview
The gateway can send 4process data objects (PDO), each with 8bytes of input data, to
a higher-level controller.
The input data can comprise the statuses of the inputs and outputs, the logic results, or
diagnostic data.
CONFIGURATION 7
8024587/1CUS/2022-09-23 | SICK O P E R A T I N G I N S T R U C T I O N S | Flexi Gateway GCAN1 19
Subject to change without notice

Approach
1. In the main navigation pane, click Configuration.
2. In the navigation tree of the required module, select Routing to network.
3. Select the required input data and drag it onto a single byte or several bytes of the
input data block.
The following input data are available:
°Routing Templates contains templates for the routing of data from the logic
editor.
°Inputs contain the input values of the modules.
°Outputs contain the output values of the modules as well as the logic results
from the logic editor.
°Diagnostics contains the checksums and status information of the modules.
✓The bits, bytes or data formats are available as individual outputs in the logic
editor.
✓Each bit, byte or data format inherits a default tag name from the routing.
4. If required, edit the default tag name in the Properties tab.
Complementary information
Table 6: Colors of the bytes and bits of a record
Color Meaning
Light blue The byte or the bit is empty.
Blue The byte or the bit is occupied. The relevant module, input or
output is configured in the hardware configuration of the safety
controller.
Gray The byte or the bit is occupied. The relevant module, input or
output is not yet configured in the hardware configuration of the
safety controller.
The status of the communication with the network can be monitored. A status bit for
the sending of data to the network is provided for this. If the gateway detects a fault in
the communication, it sets the contents of the input records and the associated status
bit to Null. The bit also switches to Null if the gateway is not ready for operation or the
safety controller was stopped via the configuration software.
7.4.5 Configuring CAN listen mode and associated output data
Overview
The module can use CAN listen mode to listen to the messages sent from other
communication nodes in the CAN network, e.g., an encoder. You can configure up to
16instances. Using these instances, the module can capture specific CAN contents
and forward them to the main module.
CAN listen mode can be used not only in a CANopen network, but also when using
other CAN protocols.
This is where you configure the parameters of the instances, and which data the
instance forwards to the main module.
The following routing data are available:
•8bytes CAN data (payload)
•4bytes time stamp
•1bit status
•1bit data valid
Approach
Configuring CAN listen mode
1. In the main navigation pane, click Configuration.
7 CONFIGURATION
20 O P E R A T I N G I N S T R U C T I O N S | Flexi Gateway GCAN1 8024587/1CUS/2022-09-23 | SICK
Subject to change without notice
Table of contents
Other SICK Gateway manuals
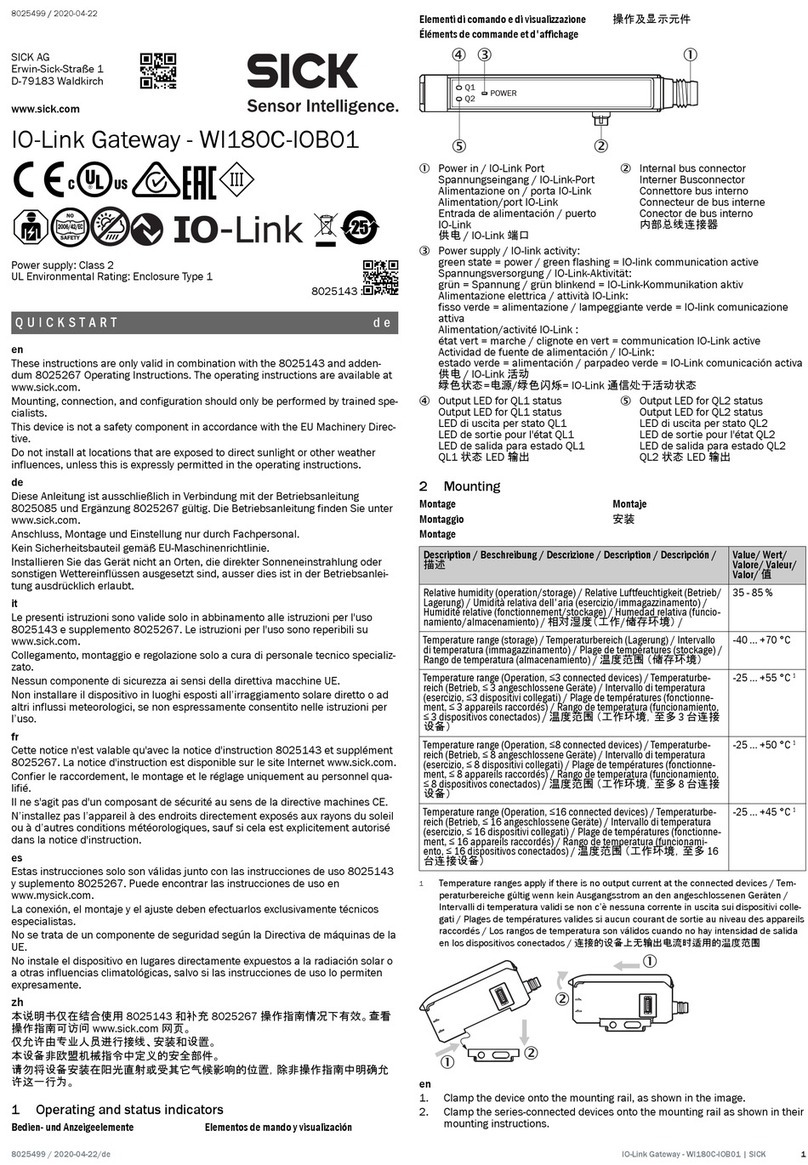
SICK
SICK WI180C-IOB01 User manual

SICK
SICK UE4740 User manual

SICK
SICK Flexi Gateway GETC1 User manual
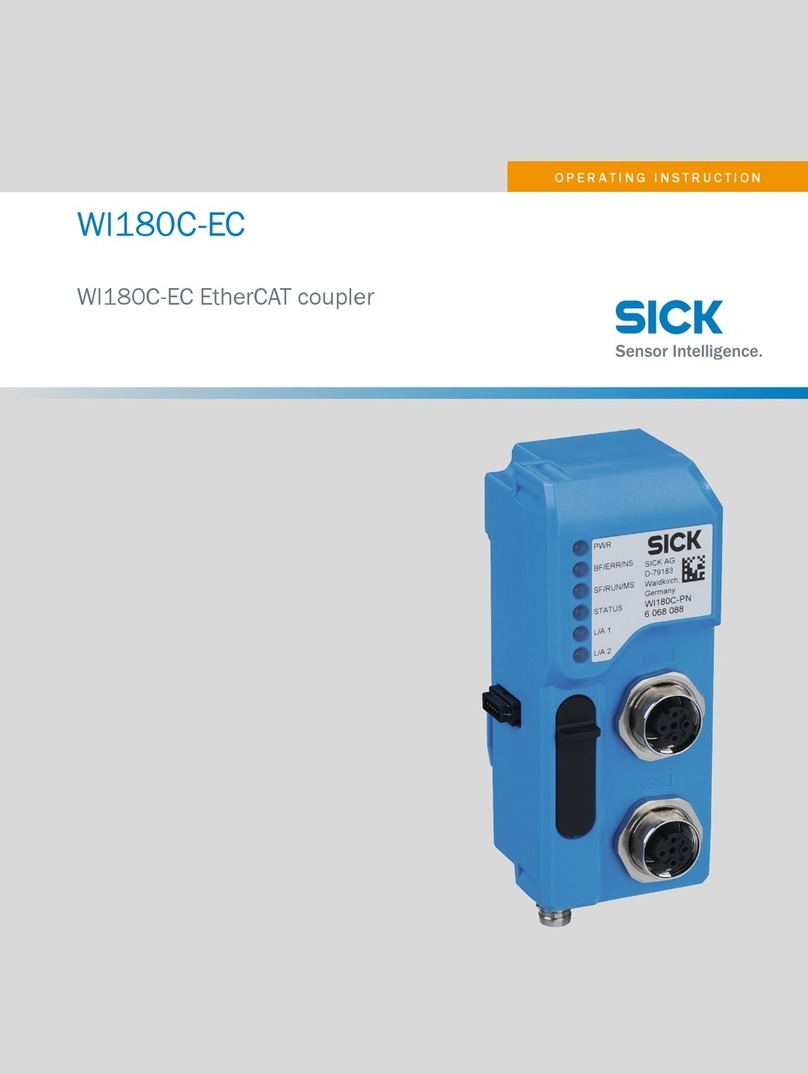
SICK
SICK WI180C-EC User manual

SICK
SICK EFI Manual
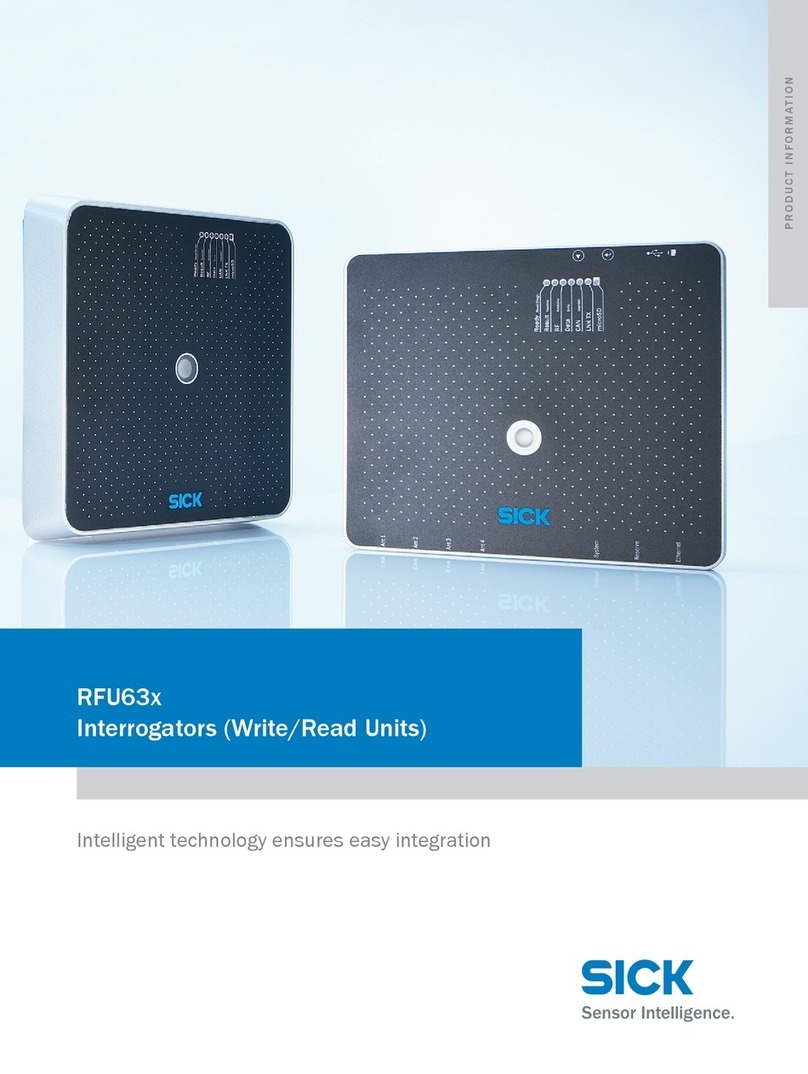
SICK
SICK RFU63x User manual
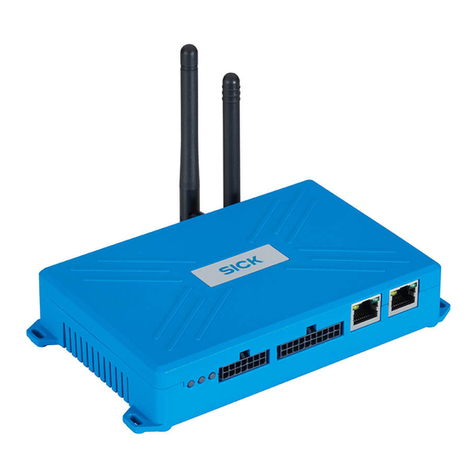
SICK
SICK TDC-E User manual

SICK
SICK WI180C-IOA00 User manual
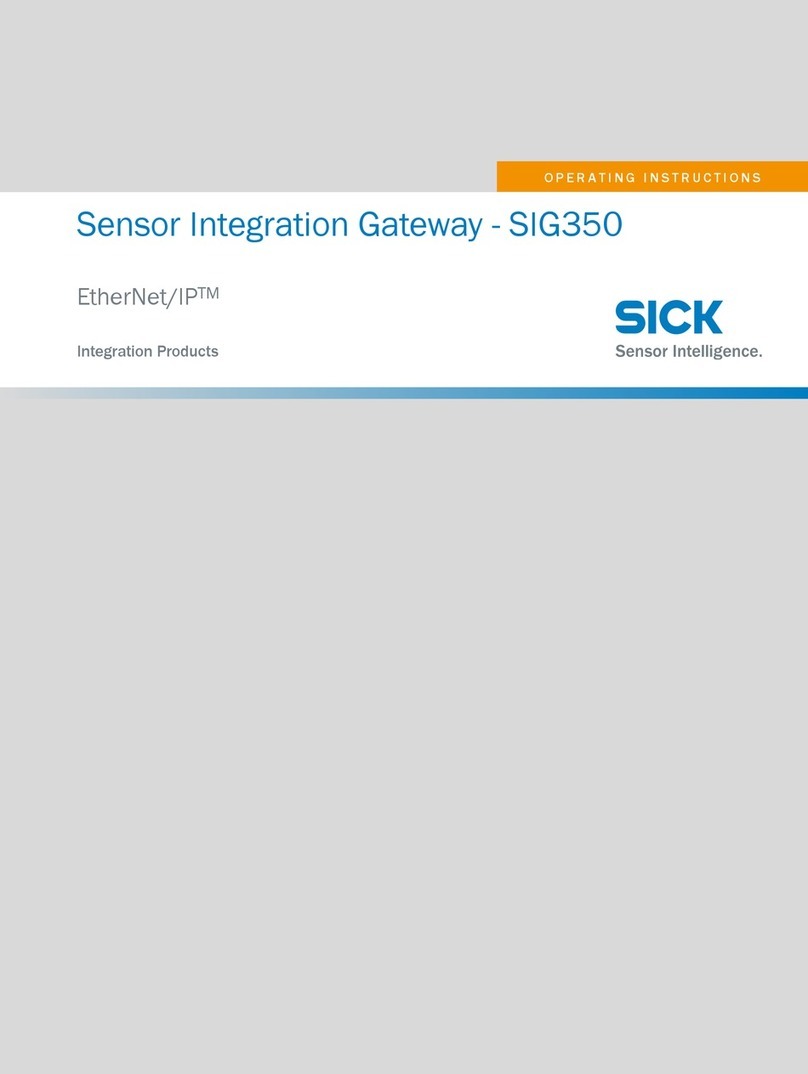
SICK
SICK EtherNet/IP SIG350 User manual
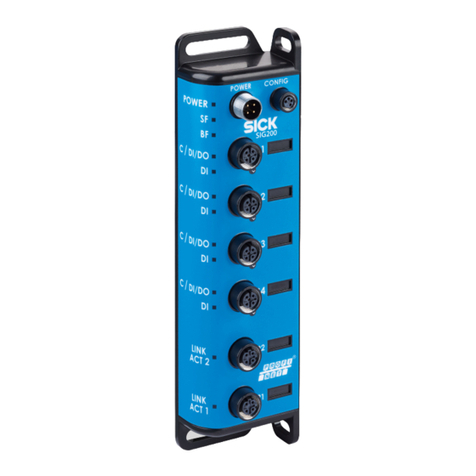
SICK
SICK SIG200 User manual