SICK EtherNet/IP SIG350 User manual

OPERATING INSTRUCTIONS
Sensor Integration Gateway - SIG350
EtherNet/IPTM
Integration Products

Described product
SIG – Sensor Integration Gateway
SIG350 - EtherNetIP
Manufacturer
SICK AG
Erwin-Sick-Str. 1
79183 Waldkirch
Germany
Legal information
This work is protected by copyright. Any rights derived from the copyright shall be
reserved for SICK AG. Reproduction of this document or parts of this document is
only permissible within the limits of the legal determination of Copyright Law. Any modi‐
fication, abridgment or translation of this document is prohibited without the express
written permission of SICK AG.
The trademarks stated in this document are the property of their respective owner.
© SICK AG. All rights reserved.
Original document
This document is an original document of SICK AG.
54PM
2006/42/EC
NO
SAFETY
2O P E R A T I N G I N S T R U C T I O N S | Sensor Integration Gateway - SIG350 8027834./2022-06-10 | SICK
Subject to change without notice

Contents
1 About this document........................................................................ 5
1.1 Further information................................................................................... 5
1.2 Explanation of symbols............................................................................ 5
2 Safety information............................................................................ 6
2.1 Intended use............................................................................................. 6
2.2 Improper use............................................................................................. 6
2.3 General safety notes................................................................................ 7
2.4 Notes on UL approval............................................................................... 7
3 Product description........................................................................... 8
3.1 General information.................................................................................. 8
3.2 Operating elements and status indicators.............................................. 11
4 Transport and storage....................................................................... 15
4.1 Transport................................................................................................... 15
4.2 Transport inspection................................................................................. 15
4.3 Storage...................................................................................................... 15
5 Mounting............................................................................................. 16
5.1 Prerequisites............................................................................................. 16
5.2 Module mounting...................................................................................... 16
5.3 Mounting of functional earth................................................................... 17
5.4 Rotary switch cover................................................................................... 18
5.5 Scope of delivery....................................................................................... 19
6 Electrical installation........................................................................ 20
6.1 Electrical installation................................................................................ 20
6.2 Pin assignment......................................................................................... 20
6.3 Supply concept......................................................................................... 22
6.4 Derating..................................................................................................... 23
7 Commissioning.................................................................................. 24
7.1 IP address................................................................................................. 24
7.2 MAC address............................................................................................. 25
7.3 Rotary switch............................................................................................. 25
7.4 Data security............................................................................................. 26
8 Operation............................................................................................ 27
8.1 EtherNet/IP integration............................................................................ 27
8.2 Dual Talk.................................................................................................... 43
8.3 Web interface............................................................................................ 60
8.4 SOPAS Engineering Tool........................................................................... 70
9 Troubleshooting................................................................................. 73
CONTENTS
8027834./2022-06-10 | SICK O P E R A T I N G I N S T R U C T I O N S | Sensor Integration Gateway - SIG350 3
Subject to change without notice

9.1 Reset to factory settings.......................................................................... 73
9.2 Device restart............................................................................................ 73
9.3 Updating firmware.................................................................................... 73
9.4 Fault diagnosis.......................................................................................... 74
10 Disassembly and disposal............................................................... 75
11 Maintenance...................................................................................... 76
12 Technical data.................................................................................... 77
12.1 General technical data............................................................................. 77
13 Annex.................................................................................................. 80
CONTENTS
4O P E R A T I N G I N S T R U C T I O N S | Sensor Integration Gateway - SIG350 8027834./2022-06-10 | SICK
Subject to change without notice

1 About this document
1.1 Further information
NOTE
All the documentation available for the device can be found on the online product page
at:
bwww.sick.de/SIG350
The following information is available for download from this page:
•Type-specific online data sheets for device variants, containing technical data and
dimensional drawings
•EU declaration of conformity for the product family
•Dimensional drawings and 3D CAD dimension models in various electronic for‐
mats
•These operating instructions, available in English and German, and in other lan‐
guages if necessary
•Other publications related to the devices described here
•Publications dealing with accessories
•IO-Link driver files and IO-Link Technical Information v1.1
1.2 Explanation of symbols
Warnings and important information in this document are labeled with symbols. The
warnings are introduced by signal words that indicate the extent of the danger. These
warnings must be observed at all times and care must be taken to avoid accidents,
personal injury, and material damage.
DANGER
…indicates a situation of imminent danger, which will lead to a fatality or serious
injuries if not prevented.
WARNING
…indicates a potentially dangerous situation, which may lead to a fatality or serious
injuries if not prevented.
CAUTION
…indicates a potentially dangerous situation, which may lead to minor/slight injuries if
not prevented.
NOTICE
…indicates a potentially harmful situation, which may lead to material damage if not
prevented.
NOTE
…highlights useful tips and recommendations as well as information for efficient and
trouble-free operation.
ABOUT THIS DOCUMENT 1
8027834./2022-06-10 | SICK O P E R A T I N G I N S T R U C T I O N S | Sensor Integration Gateway - SIG350 5
Subject to change without notice

2 Safety information
2.1 Intended use
The SIG350 is a remote IO-Link input and output module for connecting a EtherNET/IP
network.
Intended use requires that the device is used industrially indoors without any spe‐
cific climatic and atmospheric requirements. Operation of the device according to its
intended use and enclosure rating IP 67 are only guaranteed if open male and female
connectors are sealed with blind plugs. Intended use also includes EMC-compliant
electrical installation.
If the product is used for any other purpose or modified in any way, all warranty claims
against SICK AG will be void.
NOTE
This document is aimed at the trained specialist personnel. Qualified specialist person‐
nel are persons who are familiar with work such as the installation and operation of the
product, and who have the necessary qualifications for this activity. All claims against
the manufacturer in respect of warranty and liability shall be invalidated in the event of
damage resulting from unauthorized manipulation or incorrect use. The operating entity
is responsible for ensuring that the work safety regulations and accident prevention
regulations applicable in the specific individual case are observed.
2.2 Improper use
•The device does not constitute a safety-relevant device according to the EC Machi‐
nery Directive (2006/42/EC).
•The device must not be used in explosion-hazardous areas.
•Any other use that is not described as intended use is prohibited.
•Any use of accessories not specifically approved by SICK AG is at your own risk.
The device is not suitable for the following applications (this list is not exhaustive):
•As a safety device to protect persons, their hands, or other body parts
•Underwater
•In explosion-hazardous areas
•Outdoors, without additional protection
NOTICE
Danger due to improper use!
Any improper use can result in dangerous situations.
Therefore, observe the following information:
bThe device should be used only in line with intended use specifications.
bAll information in these operating instructions must be strictly complied with.
2 SAFETY INFORMATION
6O P E R A T I N G I N S T R U C T I O N S | Sensor Integration Gateway - SIG350 8027834./2022-06-10 | SICK
Subject to change without notice

2.3 General safety notes
2.3.1 Safety notes
■Read the operating instructions before commissioning.
■
Connection, mounting, and setting may only be performed by skilled per‐
son.
■
2006/42/EC
NO
SAFETY
Not a safety component in accordance with the EU Machinery Directive.
■
When commissioning, protect the device from moisture and contamination.
■These operating instructions contain information required during the life cycle of
the sensor.
2.4 Notes on UL approval
UL Environmental Rating: Enclosure type 1
SAFETY INFORMATION 2
8027834./2022-06-10 | SICK O P E R A T I N G I N S T R U C T I O N S | Sensor Integration Gateway - SIG350 7
Subject to change without notice

3 Product description
3.1 General information
The SIG350 IO-Link Master is a gateway for connecting IO-Link devices as well input
and/or output signals for data integration into a PLC via EtherNet/IP . Parallel to the
fieldbus communication, the data can also be transmitted to a network via the inte‐
grated IIOT interfaces (REST API, MQTT or OPC UA). It is intended for use in industrial
environments that require enclosure rating up to IP67.
The module has eight IO-Link Master channels and eight universal digital channels
(PNP). The device is connected to an M12 female connector that can be operated
either in the Class A or Class B connection type.
In addition, the SIG350 has a powerful user interface that can be accessed either using
the SOPAS ET software from SICK or directly via the web interface. This is used to
parameterize the SIG350 and the connected devices.
The SIG350 can be commissioned using the following methods
•Engineering tool of the PLC manufacturer
•Integrated web interface
•SICK SOPAS Engineering Tool application
•Dual Talk interface
Parameterization
•Parameterization via EtherNet/IP is performed using the engineering tool of the
PLC manufacturer to access the SIG350 directly. Depending on which type of
PLC engineering tool is used, parameterization of the SIG350 and the connected
devices is done in different ways.
•The integrated web interface of the SIG350 provides direct access for parameter‐
ization via a suitable web interface on devices connected to the same Ethernet
network as the SIG350.
•It is also possible to connect the SIG350 to the SOPAS Engineering Tool from SICK
via Ethernet for parameterization. The SOPAS Engineering Tool application can be
downloaded at www.sick.com.
•The SIG350 also has different IIoT interfaces (Dual Talk) that provide direct access
for higher-level automation operations.
3.1.1 EtherNet/IP
The Profinet technology was developed by Siemens and the member companies of the
Profibus user organization. EtherNet/IP based on Ethernet-TCP/IP. Profinet can be used
to implement solutions for manufacturing technology, process automation, building
automation as well as for the entire spectrum of drive technology up to synchronous
motion control applications. Profinet is an open communication protocol according to
IEC 61784.
The SIG350 supports PROFINET specification 2.41 and follows the guideline “IO-Link
Integration – Edition 2 Specification for PROFINET Version 1.1 – February 2020 Order
No.: 2.832.”
Requested Packet Interval (RPI)
The PROFINET concept has a modular structure. Data is exchanged between the con‐
troller, also called the IO controller, and the connected participants, the IO devices, by
means of Ethernet telegrams. The devices exchange data cyclically according to the pro‐
vider-consumer principle. The devices operate simultaneously as receiver (consumer)
3 PRODUCT DESCRIPTION
8O P E R A T I N G I N S T R U C T I O N S | Sensor Integration Gateway - SIG350 8027834./2022-06-10 | SICK
Subject to change without notice

and sender (provider). The IO-devices send input data to the controller and receive
output data from it. Other components of the communication protocol are telegrams in
the form of acyclic communication for the transmission of parameters.
Device level ring (DLR)
The communication of the SIG350 is based on a full-duplex Ethernet network with 100
Mbit/s. Auto negotiation is supported.
3.1.2 IO-Link
IO-Link is a standard (IEC 61131-9) that can be used to connect intelligent devices at
the sensor and actuator level to an automation system.
The SIG350 complies with IO-Link specification V1.1.3.
Communication
Communication takes place between a master and a device. An IO-Link Master con‐
tains one or more ports. One device can be connected per port, which means that
IO-Link is point-to-point communication and not a fieldbus. The IO-Link Master forms
the interface between the higher-level fieldbus level and the IO-Link system.
IO-Link is functional and enables advanced diagnostics of sensors and actuators or
simple and fast parameterization through bidirectional communication. The IO-Link
devices are connected to the master via unshielded 3-, 4- or 5-wire standard cables of
a maximum length of 20 m.
The SIG350 supports IO-Link communication at the following speeds:
•COM 1 → 4,800 baud
•COM 2 → 28,400 baud
•COM 3 → 230,400 baud
The module automatically selects the communication speed that matches the IO-Link
device.
IO-Link modus (IOL)
IO-Link communication (C/Q) is activated at pin 4, so an IO-Link device can be con‐
nected.
ISDU (Indexed Service Data Unit) access
The acyclic data allows the device parameters to be written by an IO-Link device or
parameters, measured values and diagnostic data to be read by an IO-Link device.
The following tasks can be performed: • Parameterization/Configuration of an IO-Link
device during operation. • Diagnosis of an IO-Link device by reading out diagnostic
parameters. • Execution of IO-Link port functions. • Saving/Restoring of IO-Link device
parameters. The data on the IO-Link device is uniquely addressed with index and
subindex.
Data storage mode
The data storage mode allows IO-Link devices to be exchanged without any configura‐
tion in the event of service. Both the IO-Link Master and the IO-Link device store the
device parameters. During data storage, these different parameter data memories are
synchronized.
In the event of device replacement, the master writes the stored device parameters
to the new device. The application can be restarted without further intervention via a
configuration tool or the like.
PRODUCT DESCRIPTION 3
8027834./2022-06-10 | SICK O P E R A T I N G I N S T R U C T I O N S | Sensor Integration Gateway - SIG350 9
Subject to change without notice

If the IO-Link Master is replaced, the new master reads the IO-Device parameters from
the device and saves them. The “Save and Restore” data storage function must be
activated for this purpose. The application can also be restarted here without further
intervention via a configuration tool or the like.
The data retention mode is only available for devices that comply with IO-Link version
V1.1 and higher.
3.1.3 Dual Talk (IIoT interfaces)
The SIG350 features Dual Talk functionality, which allows the user to address the
module from IT networks and integrate it into Internet-of-Things applications.
The SIG350 contains the following interfaces:
•MQTT JSON
•REST API JSON
•OPC UA
REST API
The Representational State Transfer – Application Programming Interface (REST API) is
a programmable interface that uses HTTP requests for GET and POST data. This allows
access to detailed device information. The format is JSON.
The REST API interface of the SIG350 complies with the JSON Integration for IO-Link
standard version V1.0.0 published by the IO-Link community.
MQTT
The MQTT (Message Queuing Telemetry Transport) protocol is an open network protocol
for machine-to-machine communication that enables the transmission of telemetric
data between devices.
An MQTT client is integrated in the SIG350, which enables the device to publish certain
information to an MQTT broker. The format is JSON.
The publication of messages can either take place periodically or be triggered man‐
ually.
The MQTT interface of the SIG350 complies with the JSON Integration for IO-Link
standard version V1.0.0 published by the IO-Link community.
OPC UA
OPC United Architecture (OPC UA) is a platform-independent standard with a service-
oriented architecture for communication in and with industrial automation systems.
The OPC UA standard is based on the client-server principle and enables machines
and devices to communicate horizontally with each other and vertically with the ERP
system or the cloud, regardless of the preferred fieldbus. The SIG350 provides an OPC
UA server at field device level, to which an OPC UA client can connect to exchange
information securely. The interface complies with the IO-Link Companion specification
(version V1.0).
3.1.4 Web interface
The SIG350 has an integrated web interface that provides functions for device configu‐
ration and the display of status and diagnostic information via a web interface. The web
interface provides an overview of the configuration and status of the device.
The graphical user interface ensures fast and intuitive operation.
The prerequisite for using the web interface is the existence of a valid IP address. This
can be set via the rotary switches directly on the device or via the DCP tool. SICK also
offers the SOPAS ET engineering tool, which can be used to configure the SIG350.
3 PRODUCT DESCRIPTION
10 O P E R A T I N G I N S T R U C T I O N S | Sensor Integration Gateway - SIG350 8027834./2022-06-10 | SICK
Subject to change without notice

In the SIG350, IP addressing is preconfigured to BootP in the delivery state.
After assigning the IP address, enter http:// followed by the IP address, e.g. http://
192.168.0.1, in the address bar of your web browser to access the web interface. If the
device status page is not displayed, check your browser and firewall settings.
3.2 Operating elements and status indicators
3.2.1 Model structure
SIG350
S4 S8
0 01 1
S3 S7
0 01 1
S2 S6
0 01 1
S1 S5
0 01 1
BF SF LNK1 ST LNK2 UA US
ACT1 ACT2 POWER
PWR1 PWR2
x100 x10 x1
P1 P2
1
2
3
4
5
6
7
8
9
Figure 1: Model structure
1Sensor/Actuator connection (8x): IO-Link port S1 – S8
2LED status indicators for bus and device status
3Voltage supply (2x): Voltage input (PWR1) and output (PWR2)
4Rotary switch
5Ethernet connection (2x): Ethernet Port P1 – P2
6Mounting opening
7LED display for IO-Link port S1 – S8 (2x per port)
8Marking labels (removable)
9Connection for functional earth
3.2.2 Status indicators
PRODUCT DESCRIPTION 3
8027834./2022-06-10 | SICK O P E R A T I N G I N S T R U C T I O N S | Sensor Integration Gateway - SIG350 11
Subject to change without notice

S4 S8
0 01 1
S3 S7
0 01 1
S2 S6
0 01 1
S1 S5
0 01 1
BF SF LNK1 ST LNK2 UA US
ACT1 ACT2 POWER
1
2
Figure 2: Status indicators
1LED status indicator for IO-Link port S1 – S8:
Each input and output is assigned its own status display:
- Channel 0 corresponds to pin 4
- Channel 1 corresponds to pin 2
2Status indicator for bus and device status
- LED MS = Module status
- LED NS = Network status
- LED LNK1 = Link 1
- LED ACT1 = Activity 1
- LED ST = Status
- LED LNK2 = Link 2
- LED ACT2 = Activity 2
- LED POWER UA = Supply voltage actuator
- LED POWER US = Supply voltage sensor
Table 1: LEDs for IO-Link port S1 – S8
LED Display Description
0 Off Pin 4 is not used/deactivated
Green Pin 4 is configured as IO-Link.
Communication active.
Flashing green
(1Hz)
Pin 4 is configured as IO-Link.
No communication.
Flashing green
(10Hz)
Pin 4 is configured as IO-Link, but is in Pre-Operate mode. e.g.
discrepancy DeviceID
Yellow Pin 4 is configured as a binary signal: 24V
- DI visible in process data
- DO can be switched via process data
Red Pin 4 is configured as DO:
Overload/Short-circuit on pin 4
Flashing red
(1Hz)
Pin 4 is configured as DI or DO:
Overload/Sensor supply short-circuit
Flashing red
(2Hz)
Pin 4 is configured as IO-Link:
- Data storage error
3 PRODUCT DESCRIPTION
12 O P E R A T I N G I N S T R U C T I O N S | Sensor Integration Gateway - SIG350 8027834./2022-06-10 | SICK
Subject to change without notice

LED Display Description
1 Off Pin 2 is not used/deactivated
Yellow Pin 2 is configured as a binary signal: 24V
- DI visible in process data
- DO can be switched via process data
Red Pin 2 is configured as DO:
Overload/Short-circuit on pin
Flashing red
(1Hz)
Overload/Sensor supply short-circuit
Table 2: LEDs for bus system and status
LED Display Description
MF Off Module is switched off
Red System error
Flashing red
(1Hz)
Error in configuration or inconsistent configuration
Flashing green
(1Hz)
No data exchange standby – module not configured
Green Module in operation
NS Off Module is switched off
Red System error IP address already in use
Flashing red
(1Hz)
DCP signal service is initiated via bus. At least one connection has
timed out.
Flashing green
(1Hz)
No connection to the master
Green Connection to master present
ST Green Module operating without errors
Flashing green
(4Hz)
The operation requested by the position of the rotary switch is
performed. Do not switch off the device
.
Flashing red
(1Hz)
Invalid rotary switch position. System does not start.
Red Initialization error:
•Rotary switch operation failed etc.
•Hardware problem
•No valid configuration
Table 3: LEDs for Ethernet communication
LED Display Description
LNK1 +
LNK2
Off No connection to network
à Check cable connections
Green Connection to network present
ACT1 +
ACT2
Off Module is not sending/receiving Ethernet frames
à Check cable connections
Yellow flashing Module is sending/receiving Ethernet frames
PRODUCT DESCRIPTION 3
8027834./2022-06-10 | SICK O P E R A T I N G I N S T R U C T I O N S | Sensor Integration Gateway - SIG350 13
Subject to change without notice

Table 4: LEDs for supply voltage
LED Display Description
UA Off No voltage: UA <11V
Green Module operating without errors: 18V ≤ UA ≤30V
Red Undervoltage: 11V ≤ UA <18V
Flashing red
(4Hz)
Overvoltage: UA >30V
US Off No voltage: US <11V
Green Module operating without errors: 18V ≤ US ≤30V
Red Undervoltage: 11V ≤ US <18V
Flashing red
(4Hz)
Overvoltage: US >30V
3 PRODUCT DESCRIPTION
14 O P E R A T I N G I N S T R U C T I O N S | Sensor Integration Gateway - SIG350 8027834./2022-06-10 | SICK
Subject to change without notice

4 Transport and storage
4.1 Transport
For your own safety, please read and observe the following notes:
NOTE
Damage to the device due to improper transport.
■The device must be packaged for transport with protection against shock and
moisture.
■Recommendation: Use the original packaging as it provides the best protection.
■Transport should be performed by specialist staff only.
■The utmost care and attention is required at all times during unloading and
transportation on company premises.
■Note the symbols on the packaging.
■Do not remove packaging until immediately before you start mounting.
4.2 Transport inspection
Immediately upon receipt at the receiving work station, check the delivery for complete‐
ness and for any damage that may have occurred in transit. In the case of transit
damage that is visible externally, proceed as follows:
■Do not accept the delivery or only do so conditionally.
■Note the scope of damage on the transport documents or on the transport compa‐
ny’s delivery note.
■File a complaint.
NOTE
Complaints regarding defects should be filed as soon as these are detected. Damage
claims are only valid before the applicable complaint deadlines.
4.3 Storage
Store the device under the following conditions:
■Recommendation: Use the original packaging.
■Do not store outdoors.
■Store in a dry, dust-protected place.
■To allow any residual dampness to evaporate, do not package in airtight contain‐
ers.
■Do not expose to aggressive substances.
■Protect from sunlight.
■Avoid mechanical shocks.
■Storage temperature: see "Technical data", page 77.
■Relative humidity: see "Technical data", page 77.
■For storage periods longer than 3 months, regularly check the general condition of
all components and the packaging.
TRANSPORT AND STORAGE 4
8027834./2022-06-10 | SICK O P E R A T I N G I N S T R U C T I O N S | Sensor Integration Gateway - SIG350 15
Subject to change without notice

5 Mounting
5.1 Prerequisites
The following requirements must be met when mounting the SIG350:
•Level mounting surface free of mechanical stress.
•Provide suitable earthing.
•Select suitable mounting location with regard to vibration and impact load, temper‐
ature and humidity see "General technical data", page 77.
•Protected to prevent the connecting cables from being torn off by personnel or the
device.
•For proper installation and improved heat dissipation, keeping a minimum dis‐
tance of 3mm between two modules is recommended.
•When using angled plug connectors, a minimum distance of 50mm must be
maintained between two modules.
•Mount modules in such a way that they cannot be used as climbing aids.
NOTE
To ensure IP 67 protection, all unused connections must be covered with sealing
caps. These are not included in the scope of delivery and must be ordered separately.
Suitable sealing caps can be found at SICK.com (part number 5309189). In addition,
connected cables and sealing caps must be fastened with the appropriate torque (see
manufacturer’s specifications).
5.2 Module mounting
The SIG350 is mounted using two screws (max. M6) and two washers.
The fixing screws and tightening torques depend on the substrate of the mounting
location. Always tighten the screws carefully and observe the maximum permissible
tightening torque of 3Nm.
5 MOUNTING
16 O P E R A T I N G I N S T R U C T I O N S | Sensor Integration Gateway - SIG350 8027834./2022-06-10 | SICK
Subject to change without notice

Figure 3: Mounting the module
Mounting
•Position M6 screw in the upper mounting opening and tighten lightly.
•Align housing
•Position another M6 screw in the lower mounting opening and tighten lightly.
•Tighten both screws with a max. tightening torque of 3Nm.
•Ground module: see "Mounting of functional earth", page 17.
5.3 Mounting of functional earth
The module must be grounded to a metal base via a ground strap. To ensure functional
earth, the module must be mounted with conductive screws. The fixing screws and
tightening torques depend on the substrate of the mounting location. Always tighten the
screws carefully and observe the maximum permissible tightening torque of 1.2Nm.
NOTE
The ground strap and the associated screws for the functional earth are not included
with delivery. This set is available as an accessory (part number 5346121).
MOUNTING 5
8027834./2022-06-10 | SICK O P E R A T I N G I N S T R U C T I O N S | Sensor Integration Gateway - SIG350 17
Subject to change without notice

Mounting
Figure 4: Mounting the ground strap
•Place the ground strap in the opening provided in the housing for functional earth.
•Position washer on ground strap and fasten to module with M4 screw.
•Observe the tightening torque of 1.2Nm.
•Align ground strap
•Tighten the lower end of the ground strap with another M4 screw and two washers
at the mounting location, observing the tightening torque.
5.4 Rotary switch cover
The rotary switches are provided with a cover to ensure IP protection. To operate the
rotary switches, the cover must be removed. The cover must then be refitted.
The rotary switch cover is fastened with two M3 screws. The permitted tightening torque
is 0.8Nm.
5 MOUNTING
18 O P E R A T I N G I N S T R U C T I O N S | Sensor Integration Gateway - SIG350 8027834./2022-06-10 | SICK
Subject to change without notice

Figure 5: Mounting of rotary switch cover
5.5 Scope of delivery
Included in the scope of delivery of the SIG350:
•SIG350 IO-Link Master module
•Quickstart instructions
•20 marking labels
NOTE
No screws are included in the scope of delivery.
MOUNTING 5
8027834./2022-06-10 | SICK O P E R A T I N G I N S T R U C T I O N S | Sensor Integration Gateway - SIG350 19
Subject to change without notice

6 Electrical installation
6.1 Electrical installation
The SIG350 is used in electrical installations. When working on the module or the plant,
the safety rules of electrical engineering must be observed.
The following information must be observed, depending on the connection type:
•Switch off the power supply to the device before starting work on it.
•The connection of the network and IO-Link cable of the SIG350 must be voltage-
free (UB = 0V). Only apply voltage/switch on the voltage supply (UB >0V) once all
electrical connections have been established.
•All unused male and female connectors must be sealed with sealing caps to
ensure enclosure rating IP 67.
•If possible, each of the sensor/bus and actuator power supplies should be drawn
from different sources. The total current of the module must not exceed 16A.
•In case of separate actuator and sensor supply, always switch on the sensor
voltage first and then the actuator voltage to ensure error-free function of the
digital inputs and outputs.
•An incorrect supply voltage may result in damage to the device.
•Cables and/or modules damaged by short-circuits can overheat and cause fires.
Provide sensible current monitoring or fuse. The fuse protection must be designed
for max. 16A.
•During operation of the module, the device surface may heat up. If necessary,
wear suitable thermal gloves.
•Only install cables and accessories that comply with the requirements and regu‐
lations for safety, electromagnetic compatibility and, if applicable, telecommunica‐
tions terminal equipment and the specification requirements.
•Observe the derating when using the product. The ambient temperature and the
current have an influence on the heating of the product (see "Derating", page 23)
NOTE
Only operate the product with DC 24V PELV (Protective Extra-Low Voltage) or SELV
(Safety Extra-Low Voltage) voltage sources.
There is a risk of electric shock if this is not observed.
Only use a power supply unit that allows max. 60V DC or 25V AC in the event of a
fault.
6.2 Pin assignment
NOTE
You will find a large selection of connection cables at www.sick.com
Explanation of the connection diagrams
•DI = Digital input
•DO = Digital output
•FE = Functional earth
•n. c. = Not connected
•Rx+ = Receiver +
•Rx- = Receiver -
•Tx+ = Sender +
•Tx- = Sender –
•US = Sensor voltage
•UA = Actuator voltage
6 ELECTRICAL INSTALLATION
20 O P E R A T I N G I N S T R U C T I O N S | Sensor Integration Gateway - SIG350 8027834./2022-06-10 | SICK
Subject to change without notice
Other SICK Gateway manuals
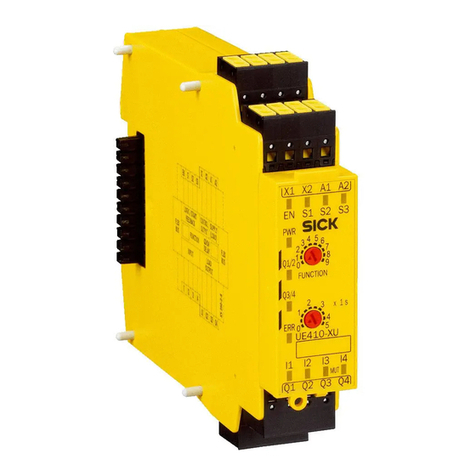
SICK
SICK Flexi Classic User manual

SICK
SICK UE4740 User manual

SICK
SICK Flexi Gateway GETC1 User manual
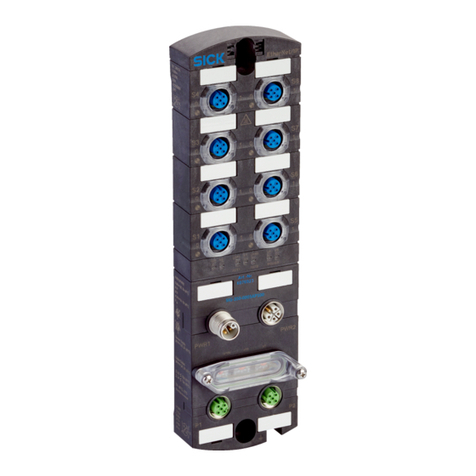
SICK
SICK EtherCAT SIG350 User manual
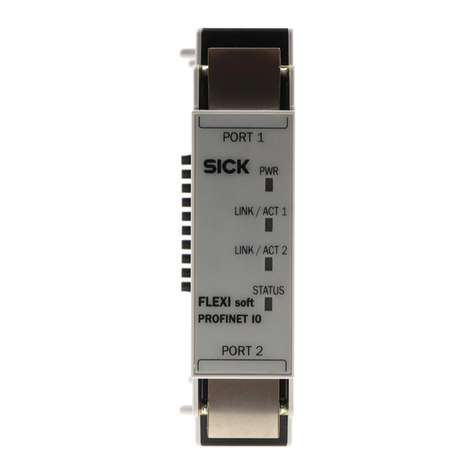
SICK
SICK Flexi Soft User manual
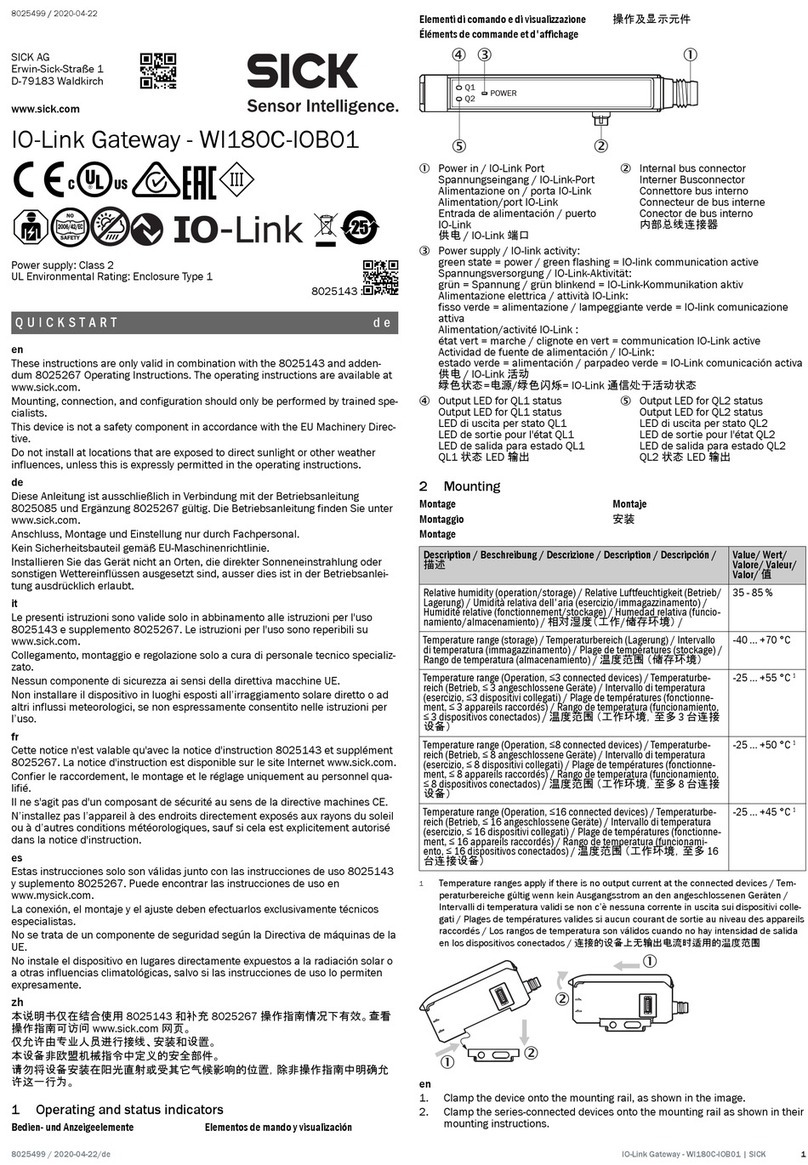
SICK
SICK WI180C-IOB01 User manual
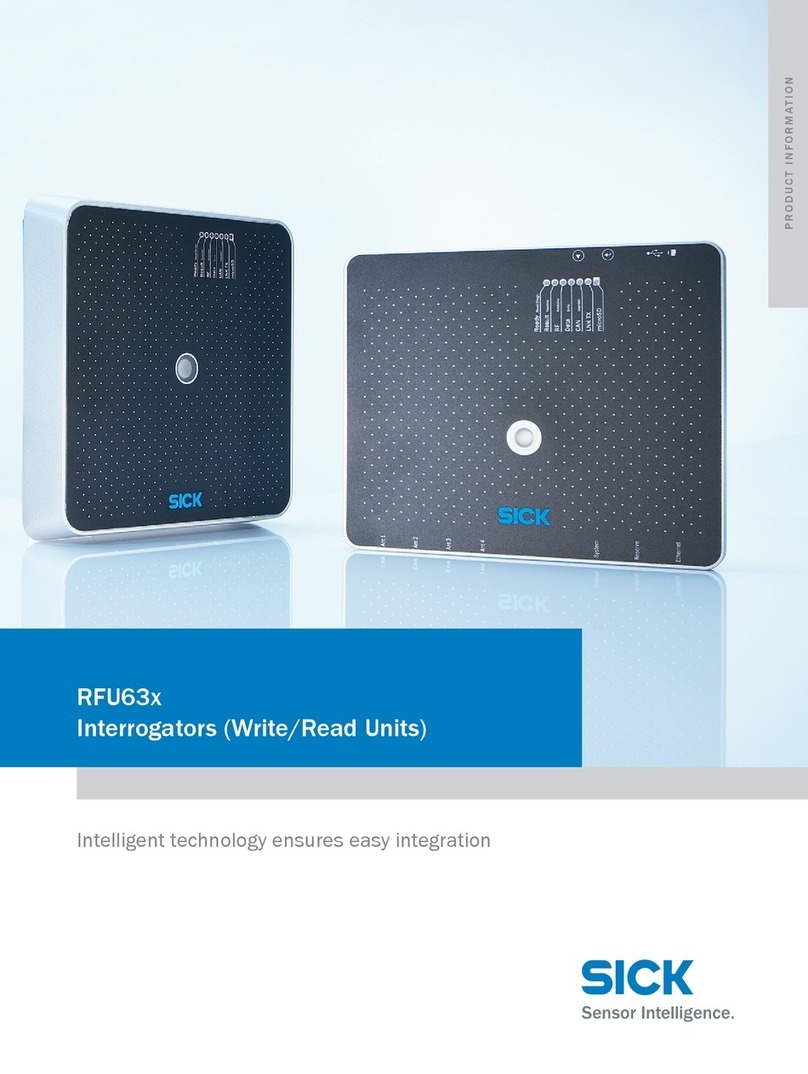
SICK
SICK RFU63x User manual
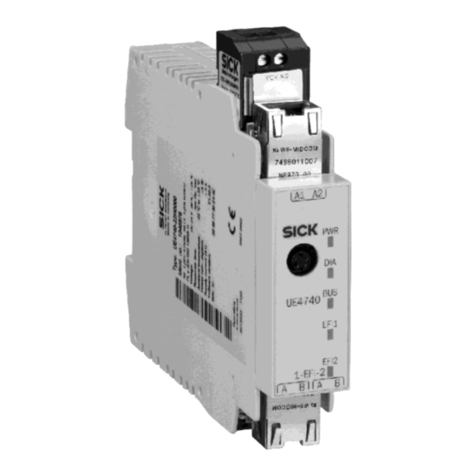
SICK
SICK UE4740 User manual
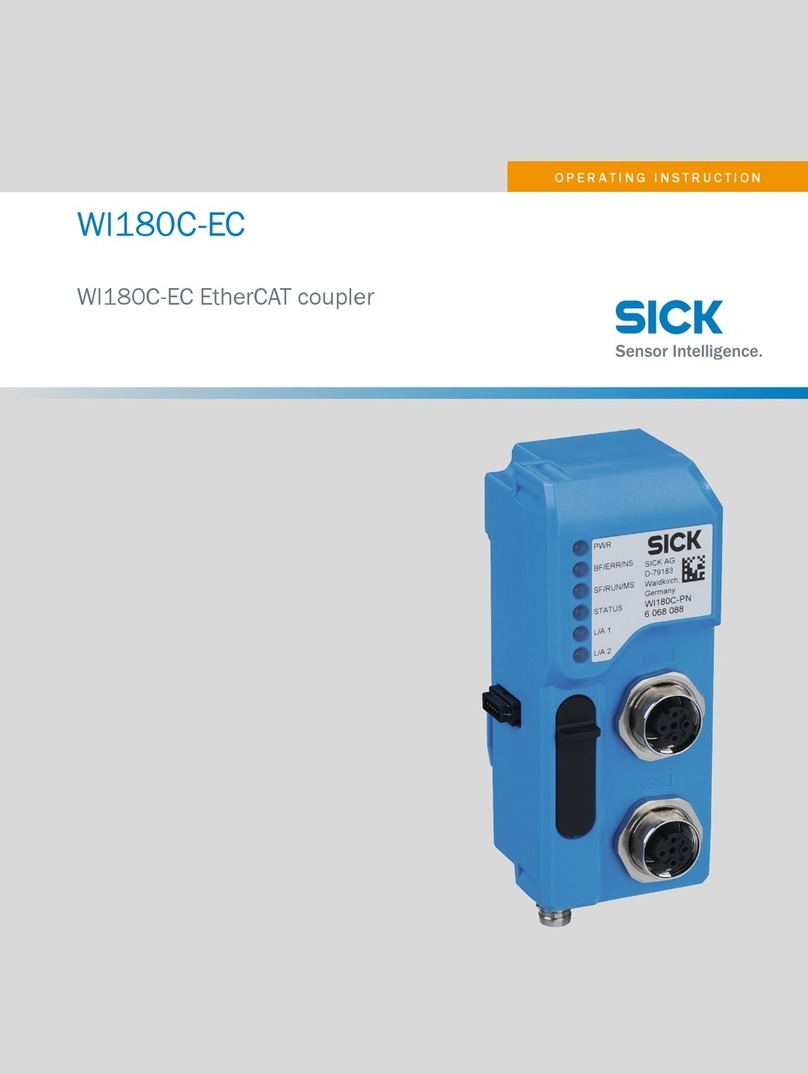
SICK
SICK WI180C-EC User manual
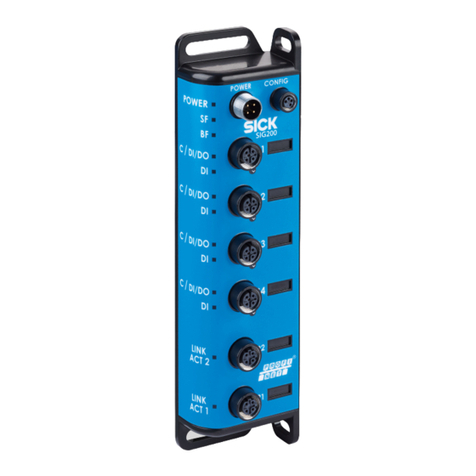
SICK
SICK SIG200 User manual
Popular Gateway manuals by other brands
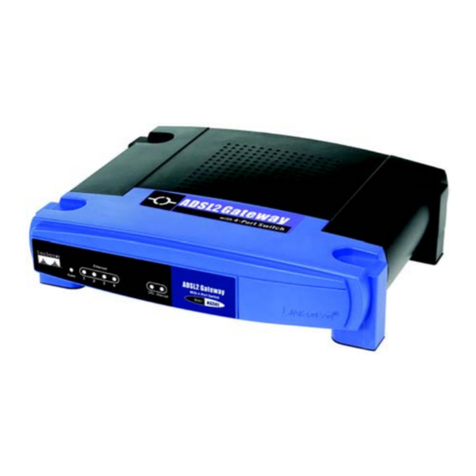
Linksys
Linksys AG241 Product data
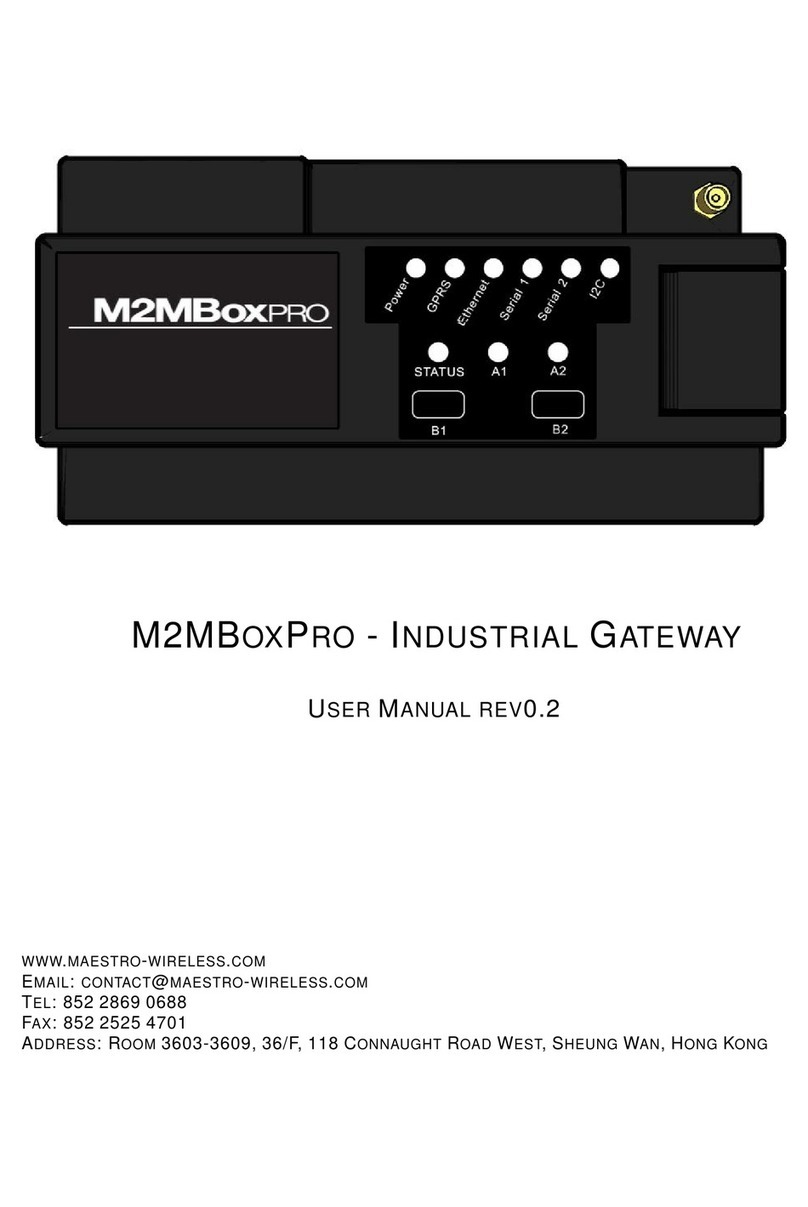
Maestro Wireless Solutions
Maestro Wireless Solutions M2MBOXPRO user manual
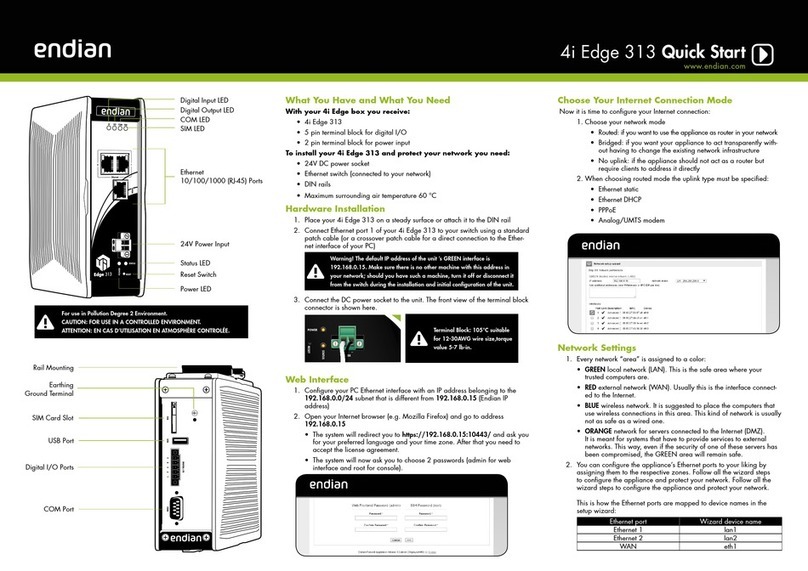
ENDIAN
ENDIAN 4i Edge 313 quick start
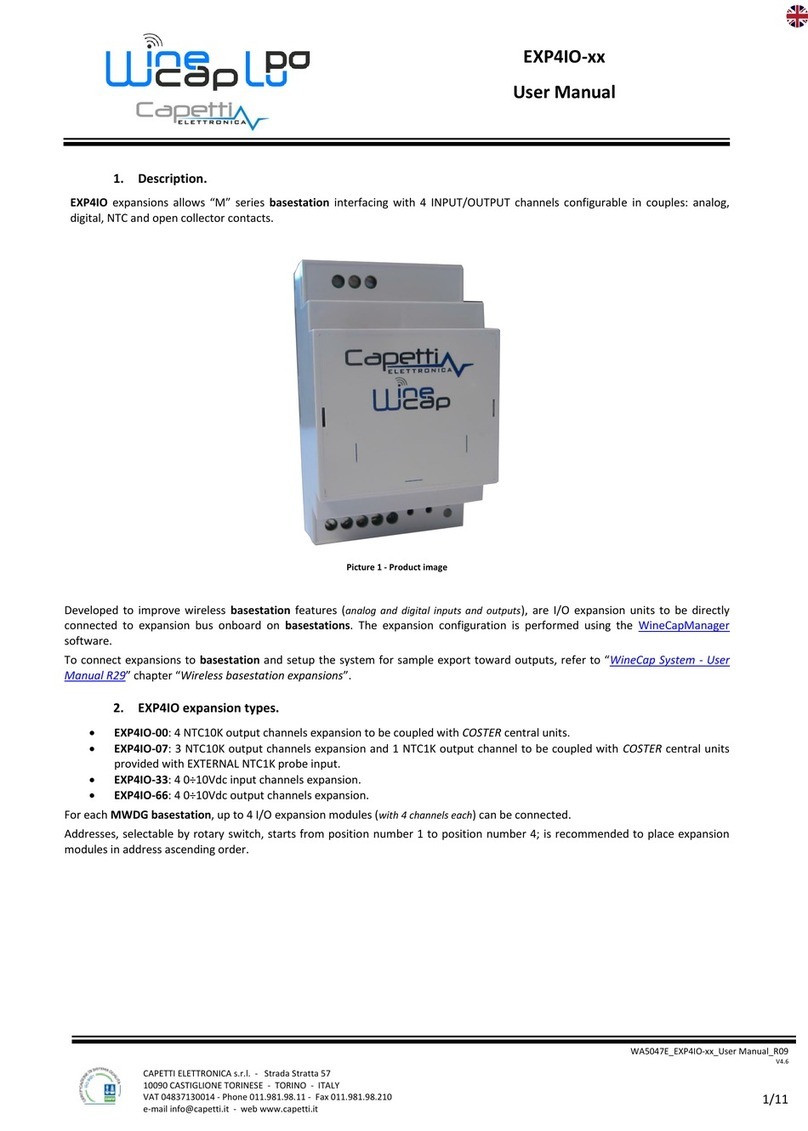
Capetti Elettronica
Capetti Elettronica Winecap EXP4IO Series user manual
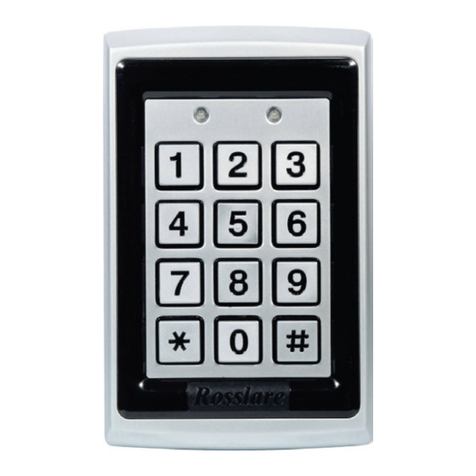
Rosslare
Rosslare AY-Q64 Installation and programming manual

Dinstar
Dinstar MMTG200 user manual