SICK SIG200 User manual

OPERATING INSTRUCTION
Sensor Integration Gateway - SIG200
PROFINET
Integration Products

Described product
SIG - Sensor integration gateway
SIG200 PROFINET
Manufacturer
SICK AG
Erwin-Sick-Str. 1
79183 Waldkirch
Germany
Production location
SICK PCA
55438 Minneapolis, MN
USA
Legal information
This work is protected by copyright. Any rights derived from the copyright shall be
reserved for SICK AG. Reproduction of this document or parts of this document is
only permissible within the limits of the legal determination of Copyright Law. Any modi‐
fication, abridgment or translation of this document is prohibited without the express
written permission of SICK AG.
The trademarks stated in this document are the property of their respective owner.
© SICK AG. All rights reserved.
Original document
This document is an original document of SICK AG.
E497722
2O P E R A T I N G I N S T R U C T I O N | Sensor Integration Gateway - SIG200 8017853.1D0S/2021-11-04 | SICK
Subject to change without notice

Contents
1 Safety information............................................................................ 4
1.1 General safety notes................................................................................ 4
1.2 Notes on UL approval............................................................................... 4
2 Correct use......................................................................................... 5
3 Product description........................................................................... 6
3.1 Product description.................................................................................. 6
3.2 Operating and status indicators.............................................................. 6
4 Transport and storage....................................................................... 9
4.1 Transport................................................................................................... 9
4.2 Transport inspection................................................................................. 9
4.3 Storage...................................................................................................... 9
5 Mounting............................................................................................. 10
6 Electrical installation........................................................................ 11
6.1 Pin alignment............................................................................................ 11
7 SIG200 configuration....................................................................... 13
7.1 SIG200 PROFINET interface.................................................................... 13
7.2 Operation via Webserver.......................................................................... 42
7.3 Operation via SOPAS ET (USB/Ethernet)................................................. 43
7.4 Configuration via REST API....................................................................... 60
8 Device Functions............................................................................... 102
8.1 Data Storage............................................................................................. 102
8.2 Logic Editor................................................................................................ 102
9 Troubleshooting................................................................................. 122
10 Disassembly and disposal............................................................... 123
11 Maintenance...................................................................................... 124
12 Technical data.................................................................................... 125
12.1 General technical data............................................................................. 125
13 Annex.................................................................................................. 128
13.1 Conformities and certificates................................................................... 128
CONTENTS
8017853.1D0S/2021-11-04 | SICK O P E R A T I N G I N S T R U C T I O N | Sensor Integration Gateway - SIG200 3
Subject to change without notice

1 Safety information
1.1 General safety notes
1.1.1 Safety notes
■Read the operating instructions before commissioning.
■Connection, mounting, and setting may only be performed by trained specialists.
■Not a safety component in accordance with the EU Machinery Directive.
■When commissioning, protect the device from moisture and contamination.
■These operating instructions contain information required during the life cycle of
the gateway.
CAUTION
This equipment is not intended for use in residential environments and may not provide
adequate protection to radio reception in such environments.
1.2 Notes on UL approval
UL Environmental Rating: Enclosure type 1
1 SAFETY INFORMATION
4O P E R A T I N G I N S T R U C T I O N | Sensor Integration Gateway - SIG200 8017853.1D0S/2021-11-04 | SICK
Subject to change without notice

2 Correct use
The SIG200 (hereinafter referred to as "module") is an IO-Link master for connecting
IO-Link devices and standard input signals or output signals.
Intended use requires that the device is used industrially indoors without any spe‐
cific climatic and atmospheric requirements. Operation of the device according to its
intended use and enclosure rating IP 67 are only guaranteed if open male and female
connectors are sealed with blind plugs.
If the product is used for any other purpose or modified in any way, all warranty claims
against SICK AG will be void.
CORRECT USE 2
8017853.1D0S/2021-11-04 | SICK O P E R A T I N G I N S T R U C T I O N | Sensor Integration Gateway - SIG200 5
Subject to change without notice

3 Product description
3.1 Product description
The IO-Link-Master SIG200 is an intelligent gateway to connect IO-Link devices, input
and/or output signals for signal integration via Profinet to a PLC or via REST API to a
network. It was designed for use in industrial environments that require up to an IP67
enclosure rating. There are four IO-Link channels, each on a dedicated Port Type A M12
socket.
In addition, the SIG200 has a powerful user interface that can be accessed either via
USB using the SOPAS ET software from SICK or via Ethernet and any web browser. With
the integrated IODD interpreter, the SIG200 and the connected IO-Link devices can be
parameterized using the IODD file(s). The user interface also has a logic editor that can
be used to parameterize sensor/actuator systems based on the information provided.
3.2 Operating and status indicators
POWER
SF
BF
C/DI/DO1
DI
C/DI/DO1
DI
C/DI/DO1
DI
C/DI/DO
DI
LINK
ACT2
LINK
ACT1
SF
POWER
BF
/DO
DI
/DO
DI
/DO
DI
/DO
DI
LINK
ACT2
LINK
ACT1
SIG200
POWER CONFIG
S1
S2
S3
S4
P2
P1
1
2
á
8
9
ßà
3
4
5
6
7
Figure 1: Dimensional drawing
1POWER IN
2IO-Link Port S1
3IO-Link Port S2
4IO-Link Port S3
5IO-Link Port S4
6Ethernet Port P2
7Ethernet Port P1
8DI: LED for pin 2
9C/DI/DO LED for pin 4
3 PRODUCT DESCRIPTION
6O P E R A T I N G I N S T R U C T I O N | Sensor Integration Gateway - SIG200 8017853.1D0S/2021-11-04 | SICK
Subject to change without notice

ßMounting hole for front mounting
àMounting hole for side mounting
áRemovable user defined port labels
âUSB Port (M8) for configuration with SOPAS ET
LEDs on the fieldbus module
SF
BF
SIG200
POWER CONFIG
1
2
3
LINK
ACT2
LINK
ACT1
P2
P1
Table 1: LED status indicators
LED Display Meaning
Supply volt‐
age
green OPower on
Off oPower off
Flashing
green
ÖA serious error has occurred. Please contact your SICK
service partner.
MS (Module
status)
dark oThe module has no power
red / green alter‐
nately
Ö
Self-test when switching on
green ODevice in operation
green blink‐
ing
ÖDevice in standby, no IP address assigned
red OError (device not in operation)
red blinking ÖWarning (but device in operation)
NS (Network
status)
dark oNo voltage or IP address
red / green alter‐
nately
Ö
Self-test when switching on
green OValid IP address and CIP connection
green blink‐
ing
ÖValid IP address, no connection
red OIP address assigned to a different device
red blinking ÖConnection timeout
LINK ACT 1
(Link / Activ‐
ity 1)
dark oNo network connection on port 1
green ONetwork connection on port 1
LINK ACT 2
(Link / Activ‐
ity 2)
dark oNo network connection on port 2
green ONetwork connection on port 2
PRODUCT DESCRIPTION 3
8017853.1D0S/2021-11-04 | SICK O P E R A T I N G I N S T R U C T I O N | Sensor Integration Gateway - SIG200 7
Subject to change without notice

IO-Link Port LEDs (Port S1-S4)
/DO
DI
SIG200
S1
8
9
Legend LED Indication Meaning
8DI: LED for pin 2 amber Additional DI on pin 2
Off No additional DI on
pin 2
9C/DI/DO LED for pin 4 green Pin 4 - IO-Link commu‐
nication active
green blinking Pin 4 - no IO-Link com‐
munication active
3 PRODUCT DESCRIPTION
8O P E R A T I N G I N S T R U C T I O N | Sensor Integration Gateway - SIG200 8017853.1D0S/2021-11-04 | SICK
Subject to change without notice

4 Transport and storage
4.1 Transport
For your own safety, please read and observe the following notes:
NOTE
Damage to the device due to improper transport.
■The device must be packaged for transport with protection against shock and
moisture.
■Recommendation: Use the original packaging as it provides the best protection.
■Transport should be performed by specialist staff only.
■The utmost care and attention is required at all times during unloading and
transportation on company premises.
■Note the symbols on the packaging.
■Do not remove packaging until immediately before you start mounting.
4.2 Transport inspection
Immediately upon receipt at the receiving work station, check the delivery for complete‐
ness and for any damage that may have occurred in transit. In the case of transit
damage that is visible externally, proceed as follows:
■Do not accept the delivery or only do so conditionally.
■Note the scope of damage on the transport documents or on the transport compa‐
ny’s delivery note.
■File a complaint.
NOTE
Complaints regarding defects should be filed as soon as these are detected. Damage
claims are only valid before the applicable complaint deadlines.
4.3 Storage
Store the device under the following conditions:
■Recommendation: Use the original packaging.
■Do not store outdoors.
■Store in a dry area that is protected from dust.
■So that any residual damp can evaporate, do not package in airtight containers.
■Do not expose to any aggressive substances.
■Protect from sunlight.
■Avoid mechanical shocks.
■Storage temperature: see "Technical data", page 125.
■Relative humidity: see "Technical data", page 125.
■For storage periods of longer than 3 months, check the general condition of all
components and packaging on a regular basis.
TRANSPORT AND STORAGE 4
8017853.1D0S/2021-11-04 | SICK O P E R A T I N G I N S T R U C T I O N | Sensor Integration Gateway - SIG200 9
Subject to change without notice

5 Mounting
The SIG200 is mounted with two screws, maximum M6, and two flat washers.
Observe the maximum permissible tightening torque of 0.8 Nm.
2 x M6
< 0.8 Nm
Figure 2: Mounting
Scope of delivery:
•SIG200
•5 blind plugs (on Port CONFIG, S2, S3, S4, P1)
•Quickstart instruction
•20 labels for the label pocket
To ensure proper ground connection to the housing, the coating on the housing around
the mounting screws must be removed.
NOTE
There can be several SIG200 mounted side by side without observing a minimum
distance between each IO-Link Master.
NOTE
There are no blind plugs at ports P1, S1 and Power.
NOTE
There are no screws inlcuded in the scope of delivery.
5 MOUNTING
10 O P E R A T I N G I N S T R U C T I O N | Sensor Integration Gateway - SIG200 8017853.1D0S/2021-11-04 | SICK
Subject to change without notice

6 Electrical installation
The SIG200 power and IO-Link cables must be connected in a voltage-free state (UV =
0 V). The following information must be observed, depending on the connection type:
Even if the wiring is looped through, the total current of the module must not exceed
3 A.
NOTICE DAMAGE OF EQUIPMENT
Equipment damage due to incorrect supply voltage! Please note the instructions for
electrical installation.
An incorrect supply voltage may result in damage to the equipment. Operation in
short-circuit protected network max. 8 A is allowed.
Only apply voltage/switch on the voltage supply (UV > 0 V) once all electrical connec‐
tions have been established.
Male and female connectors that are not used must be sealed with blind caps so that
the enclosure rating of IP 67 is assured.
Explanation of the connection diagrams:
DI = Digital input
DO = Digital output
FE = functional ground
IO-Link = IO-Link communication (C)
n. c. = not connected
Rx+ = Receiver +
Rx- = Receiver -
Tx+ = Transmitter +
Tx- = Transmitter +
6.1 Pin alignment
UB: 10 ... 30 V DC
Table 2: Power Port, M12 A-coded
Pin Signal Description
1+ (L+) + 24 V DC nominal
2n.c. not connected
3M 0 V
4n.c. not connected
12
4 3
IN = 4 A
ELECTRICAL INSTALLATION 6
8017853.1D0S/2021-11-04 | SICK O P E R A T I N G I N S T R U C T I O N | Sensor Integration Gateway - SIG200 11
Subject to change without notice

Table 3: USB Port (for configuration), M8
Pin Signal Description
1+ (L+) + 5 V DC nominal
2- Data
3+ Data 0 V (logic ground)
4M
4
3
2
1
Table 4: Profinet Port (P1/P2), M12 D-coded
Pin Signal Description
1Tx+ Sender +
2Rx+ Receiver +
3Tx- Sender -
4Rx- Receiver -
43
12
Table 5: IO-Link Ports (S1-S4) M12, A-coded, (Port Class A)
Pin Signal Description
1+ (L+) + 24 V DC nominal
2DI Configurable as Digital Input
3M 0 V (logic ground)
4DI / DO or IO-Link Configurable as Digital Input or
Digital Output or IO-Link
5n. c.
21
5
3 4
6 ELECTRICAL INSTALLATION
12 O P E R A T I N G I N S T R U C T I O N | Sensor Integration Gateway - SIG200 8017853.1D0S/2021-11-04 | SICK
Subject to change without notice

7 SIG200 configuration
The SIG200 PROFINET can be configured via following different methods:
1 PROFINET (Fieldbus/PLC Engineering Tool)
2 Ethernet (Webserver)
3 USB (with SOPAS ET)
4 Ethernet (with SOPAS ET)
5 Ethernet (via REST API)
Parameterization via PROFINET (1) is performed using the engineering tool of the PLC
manufacturer to access the SIG200 directly. Depending on which type of PLC engineer‐
ing tool is used, parameterization of the SIG200 and the connected devices is done in
different ways.
The integrated web server (2) of the SIG200 provides direct access for parameteriza‐
tion via a suitable web browser on devices connected to the same Ethernet network as
the SIG200.
In addition, the SIG200 can be done via USB (3) using the SOPAS engineering tool
application from SICK. The required cable (M8, USB) must be ordered separately. It is
also possible to connect the SIG200 to SOPAS ET via Ethernet (4) for parameterization.
The SOPAS engineering tool application can be downloaded from www.sick.com.
The SIG200 also has a REST API interface that provides direct access for higher-level
automation operations. A REST API is a programming interface that defines functions
for making requests and receiving responses via HTTP protocols such as GET and POST
(REST = Representational State Transfer, API = Application Programming Interface).
7.1 SIG200 PROFINET interface
The SIG200 can be parameterized with a suitable PLC and PROFINET software tools.
This also includes addressing and parameterization. The system integration and param‐
eterization described in the following shows a good example of how the SIG200 is used
together with the TIA Portal V13 project planning software from Siemens. If you use
other controllers and project planning software, observe the corresponding documenta‐
tion.
GSDML file
The device data required for project planning are saved in GSDML files. The GSDML file
makes the possible data module available with input or output of different data widths.
•Call up the PLC/PROFINET engineering tool.
•At www.sick.com, download the current GSDML file for the device.
•Install the GSDML file in the engineering tool.
7.1.1 Configuration via PROFINET
7.1.1.1 Integration of SIG200
The hardware catalog can be used to search for devices. Select the desired product.
Drag and drop into the topology or network view.
SIG200 CONFIGURATION 7
8017853.1D0S/2021-11-04 | SICK O P E R A T I N G I N S T R U C T I O N | Sensor Integration Gateway - SIG200 13
Subject to change without notice

Figure 3: Hardware catalog
7.1.1.2 Device Model
PROFINET devices are designed as a modular system. The system is composed of a top
module and several data modules. To configure the IO-Link Master, the relevant data
modules are assigned to a slot or subslot. The project planning software represents
the data modules broken down according to the slots. Within SIG200 the slots are
structured in the following way:
7 SIG200 CONFIGURATION
14 O P E R A T I N G I N S T R U C T I O N | Sensor Integration Gateway - SIG200 8017853.1D0S/2021-11-04 | SICK
Subject to change without notice

NOTE
The HW ID for the SICK device and IOL call module is assigned to slot 2.1 of the hardware
configuration.
NOTE
Fixed modules/submodules cannot be changed by the user. Plugged modules/submod‐
ules are pre-parameterized by default, but can be removed by the user.
There is no standard assignment for subslots 2 to 5 in the IO-Link master module and
subslot 2 of the global function module. They must be configured during installation.
7.1.1.3 Device Name and PROFINET address
The communication parameters of the IO-Link Master are displayed by double-clicking
on SIG200 in the “Device overview” window.
SIG200 CONFIGURATION 7
8017853.1D0S/2021-11-04 | SICK O P E R A T I N G I N S T R U C T I O N | Sensor Integration Gateway - SIG200 15
Subject to change without notice

Figure 4: Device overview
Here, device name and PROFINET address (IP) can be configured.
Figure 5: PROFINET address
Right-click on the selected module. Then click on Assign device name .
7 SIG200 CONFIGURATION
16 O P E R A T I N G I N S T R U C T I O N | Sensor Integration Gateway - SIG200 8017853.1D0S/2021-11-04 | SICK
Subject to change without notice

Figure 6: Assign device name
7.1.1.4 Allocating device names
Select the desired device name. Assign the device name to the found marked device
using the Assign name command. The device name must correspond to the names
previously configured under Properties. The identification is done via the MAC address or
via the flash test. The MAC address is indicated on the label on the side of the SIG200.
Figure 7: Device names
SIG200 CONFIGURATION 7
8017853.1D0S/2021-11-04 | SICK O P E R A T I N G I N S T R U C T I O N | Sensor Integration Gateway - SIG200 17
Subject to change without notice

Next, the various subslots (2 to 5, corresponding to IO-Link ports 1 to 4, to which
IO-Link or standard I/O devices are connected) must be configured. In the catalog on
the right, select a suitable IO-Link submodule according to the process data length of
the IO-Link device. Drag and drop to the appropriate subslot (2 to 5).
Subslot 2.2. is linked to SIG200 Port S1.
Subslot 2.3 is linked to SIG200 Port S2.
Subslot 2.4 is linked to SIG200 Port S3.
Subslot 2.5 is linked to SIG200 Port S4.
Refer to the documentation for the IO-Link device for the required process data lengths
of the IO-Link device.
NOTE
When using the IO-Link device in SIO mode, use a digital input or digital output module
at the corresponding subslot.
NOTE
There is no parameterization for pin 2. Pin 2 is always 0 if there is no physical connec‐
tion. If a physical connection exists, the signal is automatically transmitted without
further parameterization and access can be made via SIG200-IO-Link master subslot
2.1.
NOTE
In order to get valid process data for the logic editor submodule 1.1, the Profinet input
and output process data in the logic editor must be connected (see "Device Model ",
page 14).
Figure 8: Device overview
7.1.1.5 Addressing modules
The I/O addresses can be selected and changed by selecting the IO-Link modules.
7 SIG200 CONFIGURATION
18 O P E R A T I N G I N S T R U C T I O N | Sensor Integration Gateway - SIG200 8017853.1D0S/2021-11-04 | SICK
Subject to change without notice

While selecting the IO-Link module, the IO-Link parameters of the corresponding port
can be changed via the Module parameters menu item. Example: Validation and backup.
NOTE
In IOL Autoconfig mode, the Device Check (validation) and Backup and Restore functions are
not possible.
Figure 9: Module parameters
7.1.1.6 Ending configuration
Click on Compile and download the parameterization.
Figure 10: Compile
7.1.2 Operation via PROFINET
The SIG200 can exchange process data and parameters via PROFINET. For this pur‐
pose, the IO-Link master must be connected to a suitable programmable logic control‐
ler (PLC).
The PROFINET interface of the SIG200 has the following features:
Properties Values
Transmission rate 100 Mbit/s
Maximum distance between nodes 100 m
SIG200 CONFIGURATION 7
8017853.1D0S/2021-11-04 | SICK O P E R A T I N G I N S T R U C T I O N | Sensor Integration Gateway - SIG200 19
Subject to change without notice

Properties Values
Process data Max. 257 bytes at input and 257 bytes at output
Minimum cycle time: 1 ms
Asynchronous data Are supported, see "Acyclic data", page 28
Observed standard IEEE802.3u (100Base-Tx)
Conformity class Class B
NetLoad class II
Ethernet ports 2
PROFINET features Media redundancy (MRP), network diagnostics (MIB/
SNMP), topology detection, connection diagnostics (for‐
ward/backward), link diagnostics (link length measure‐
ment), I&M0...3, automatic device replacement, gear
reduction, OpenVAS tested
GSDML file Available in V2.2, V2.32, V2.33, V2.34
For the integration of the SIG200 into a PROFINET PLC, the corresponding GSDML file
(General Station Description Markup Language) must be used.
Download the GSDML file at www.sick.com. Different versions are available for differ‐
ent engineering tools.
7.1.2.1 Device model
SIG200 PROFINET represents process data and acyclic data in the following slots:
The PROFINET slots have the following functions:
Slot Subslot Name Function
0 SIG200-0A0412200 Device Access Point (DAP): Main module
X1 PN-IO PROFINET functions
X1 P1 Port 1 – M12 Ethernet port functions
X1 P2 Port 2 – M12
7 SIG200 CONFIGURATION
20 O P E R A T I N G I N S T R U C T I O N | Sensor Integration Gateway - SIG200 8017853.1D0S/2021-11-04 | SICK
Subject to change without notice
Other manuals for SIG200
3
This manual suits for next models
1
Table of contents
Other SICK Gateway manuals
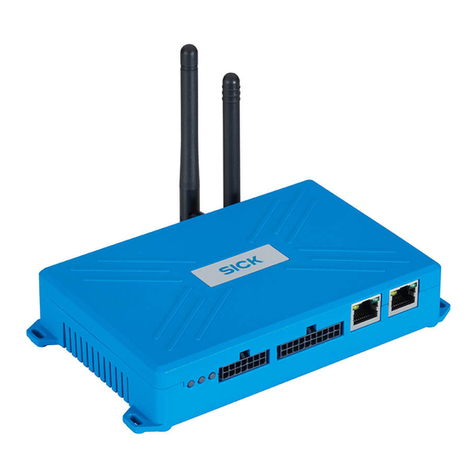
SICK
SICK TDC-E User manual
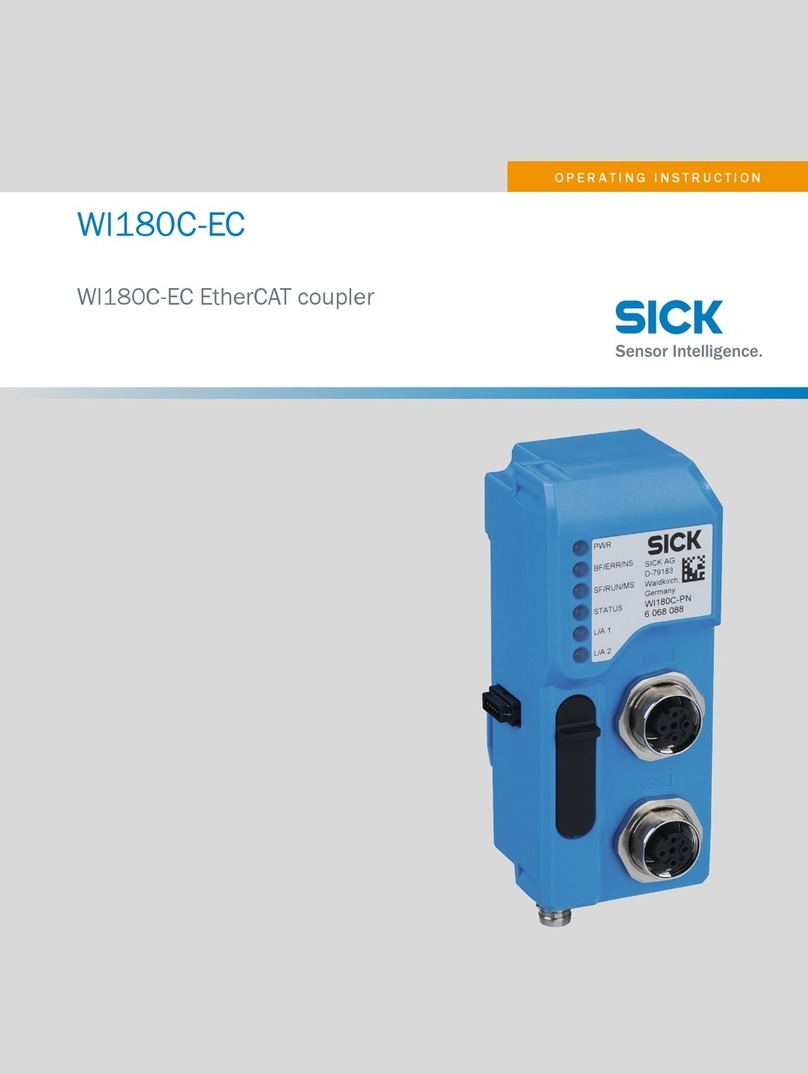
SICK
SICK WI180C-EC User manual

SICK
SICK Flexi Gateway GETC1 User manual
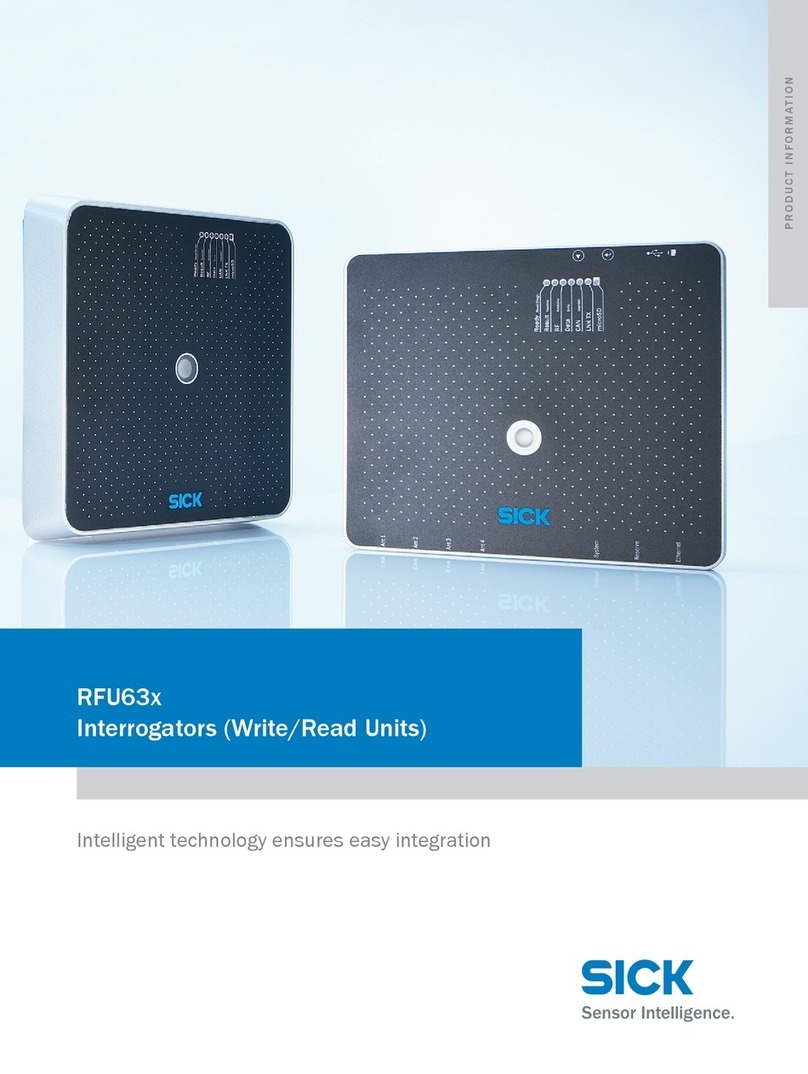
SICK
SICK RFU63x User manual
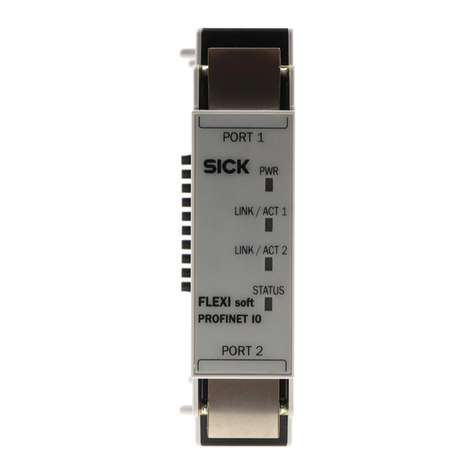
SICK
SICK Flexi Soft User manual
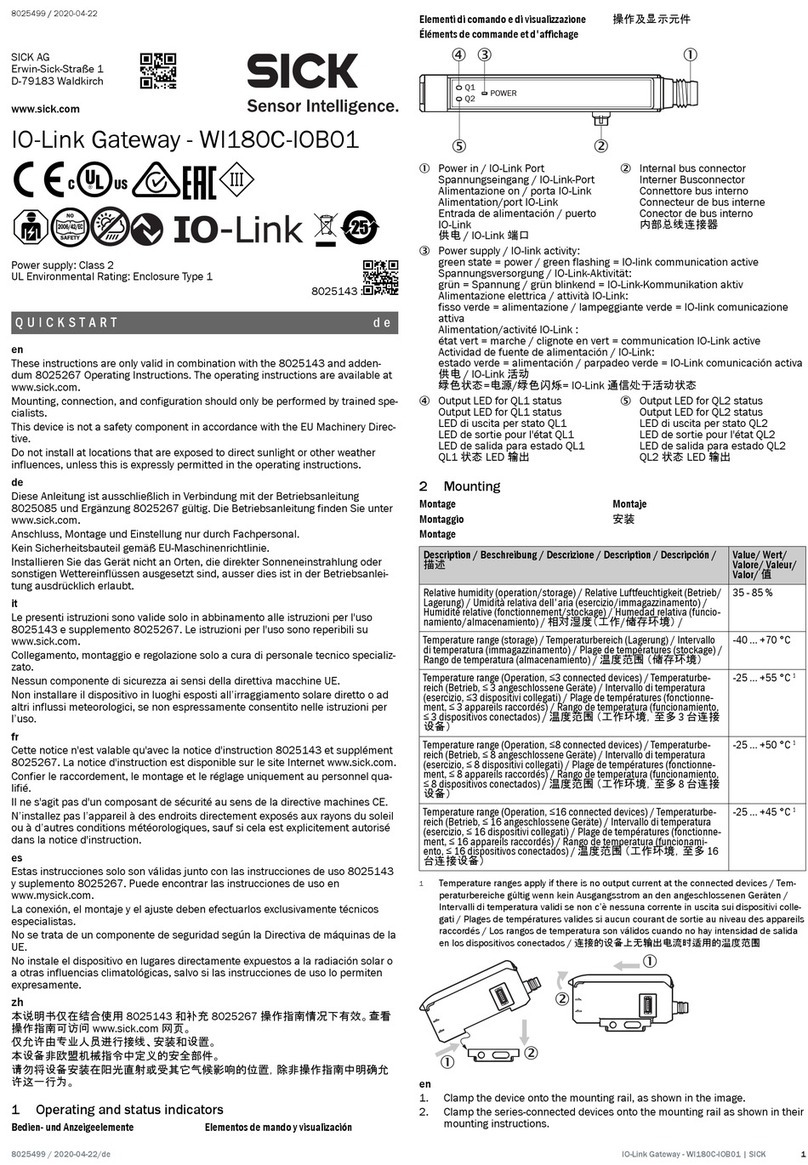
SICK
SICK WI180C-IOB01 User manual

SICK
SICK UE4740 User manual
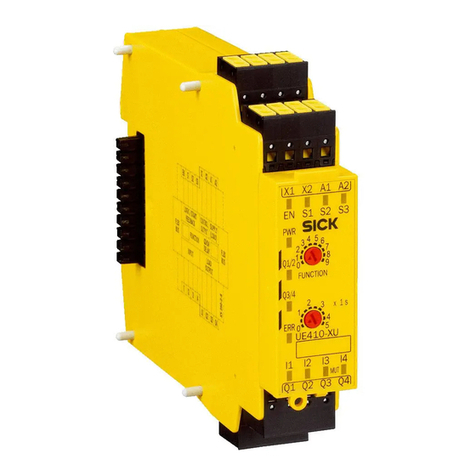
SICK
SICK Flexi Classic User manual
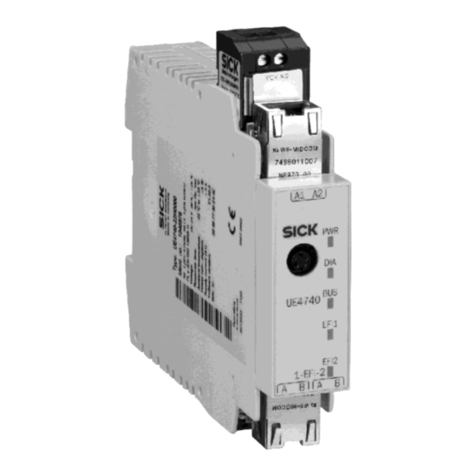
SICK
SICK UE4740 User manual
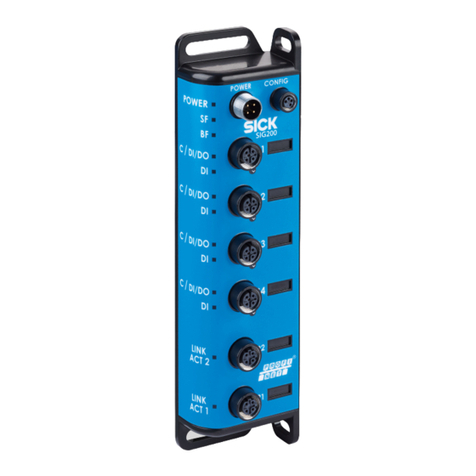
SICK
SICK SIG200 User manual
Popular Gateway manuals by other brands
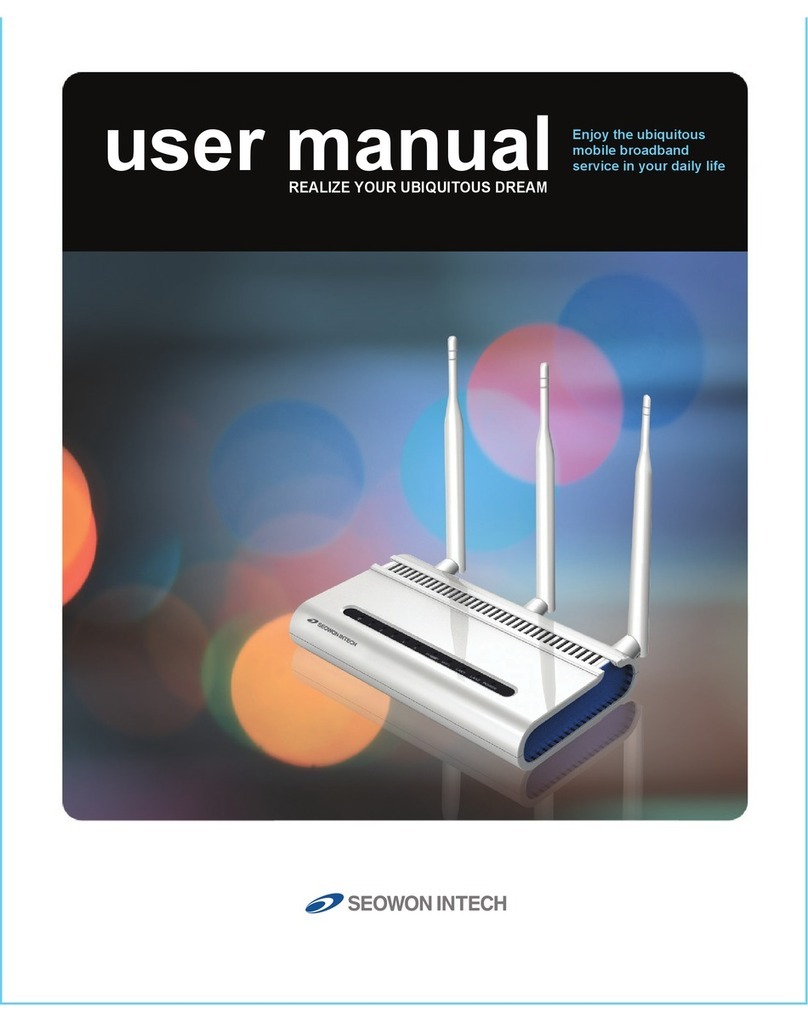
SEOWON INTECH
SEOWON INTECH SWC-5x00W series user manual
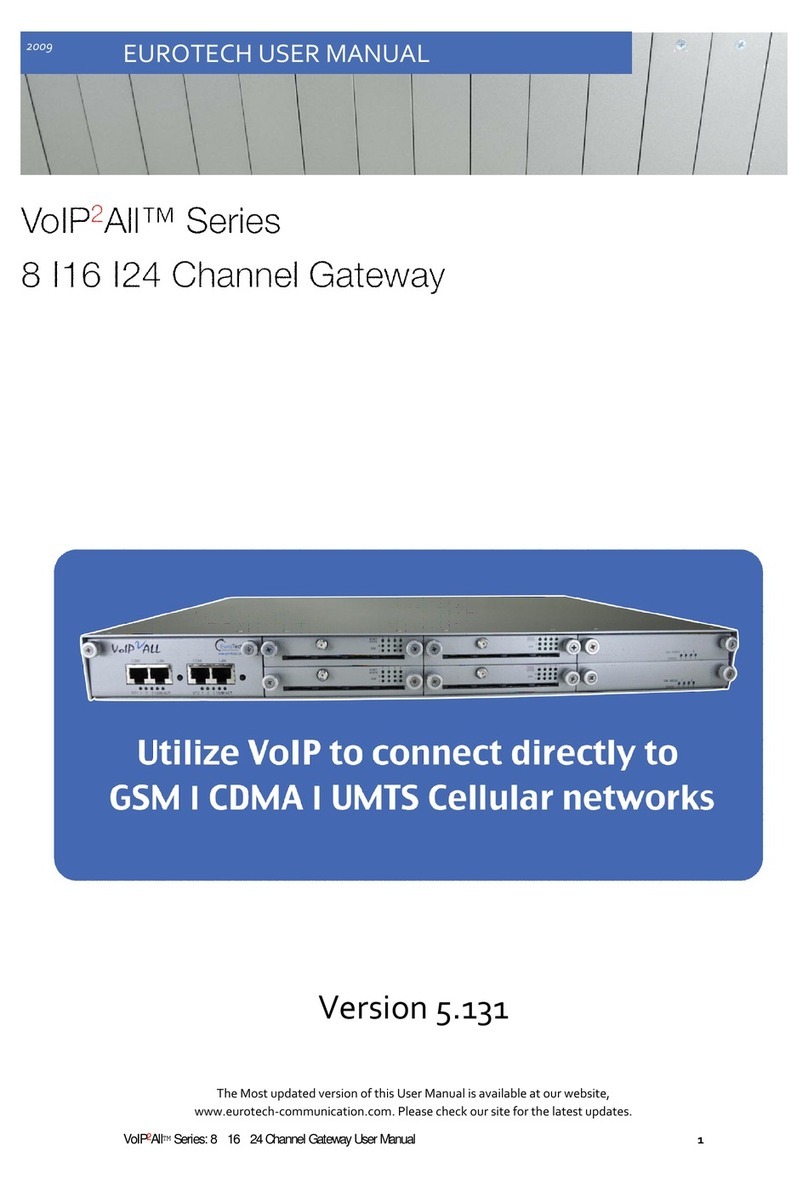
Eurotech
Eurotech VoIP2 AII Series user manual
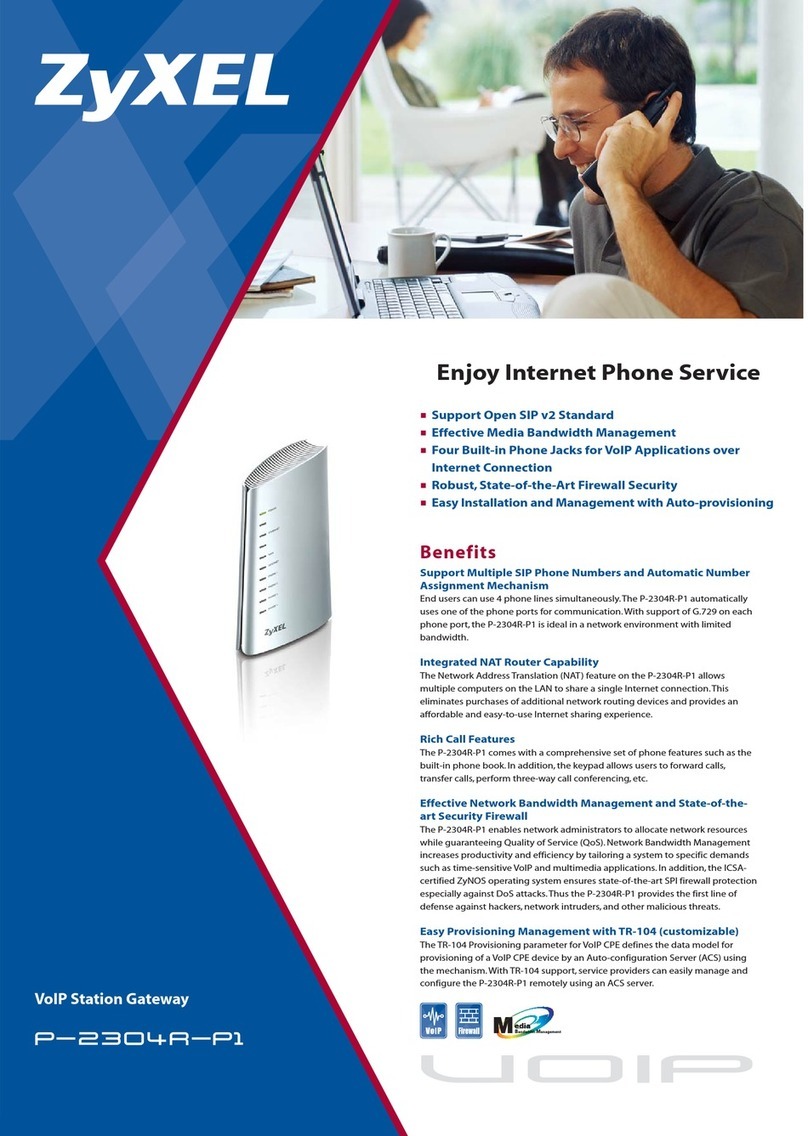
ZyXEL Communications
ZyXEL Communications P-2304R-P1 Series Specifications
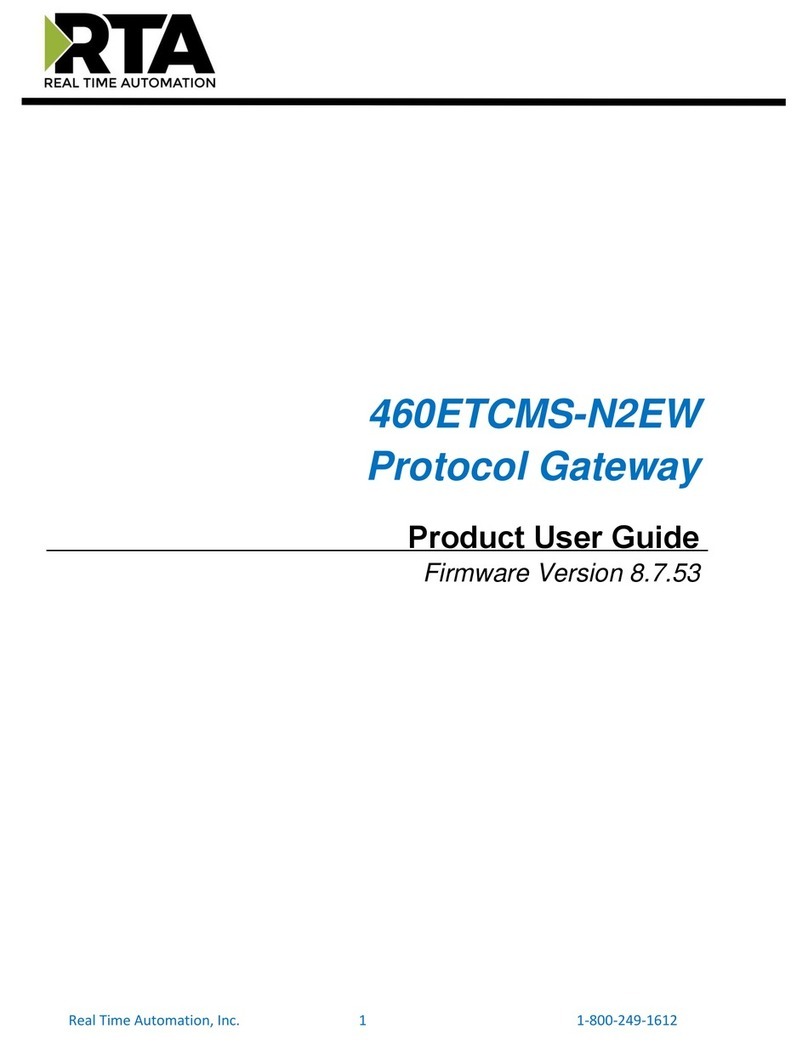
RTA
RTA 460ETCMS-N2EW Product user guide
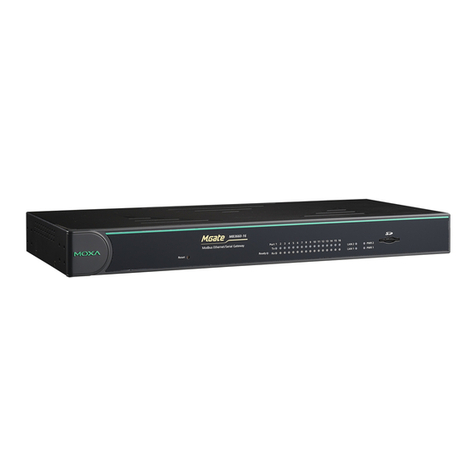
Moxa Technologies
Moxa Technologies Mgate MB3660 user manual
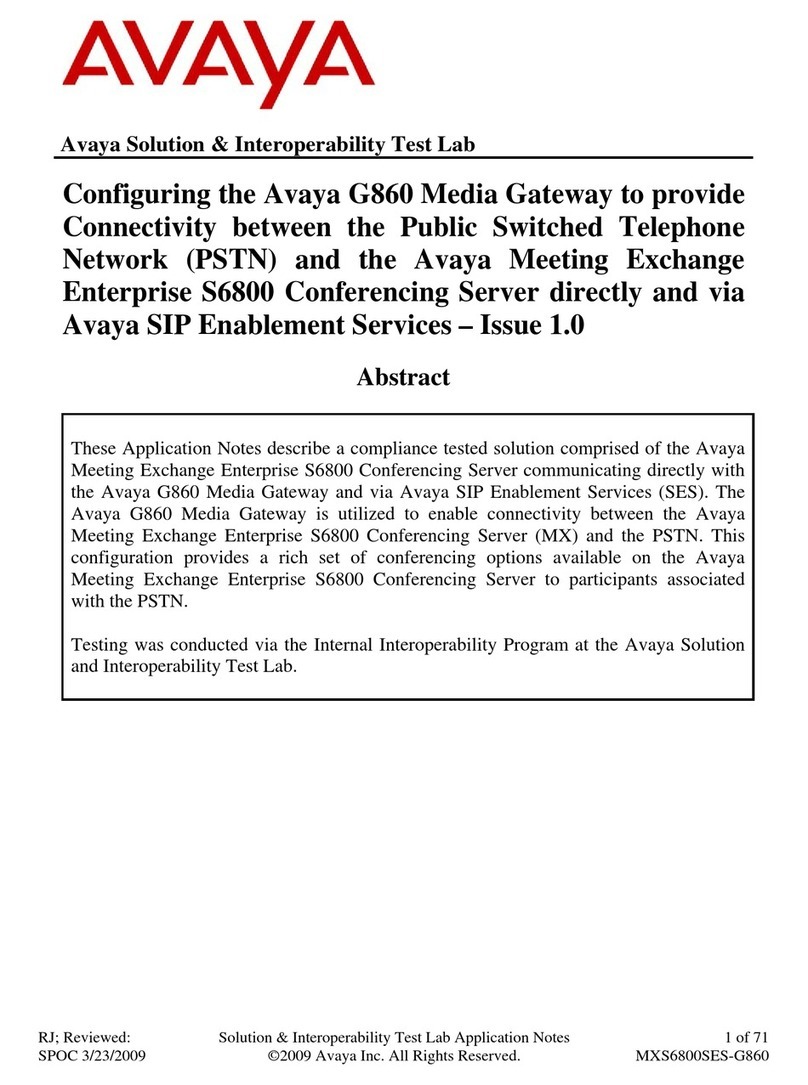
Avaya
Avaya G860 Configuring guide