SPENCE D Series User manual

www.SpenceValve.com
Spence D Series Pressure Reducing Pilot
▲ WARNING
Failure to follow these instructions or
to properly install and maintain this
equipment could result in an explosion,
fire and/or chemical contamination
causing property damage and personal
injury or death.
Emerson regulator must be installed,
operated and maintained in accordance
with federal, state and local codes, rules
and regulations and Emerson Process
Management Regulator Technologies,
Inc. (Emerson) instructions.
If the regulator vents gas or a leak
develops in the system, service to
the unit may be required. Failure
to correct trouble could result in a
hazardous condition.
Installation, operation and maintenance
procedures performed by unqualified
personnel may result in improper
adjustment and unsafe operation. Either
condition may result in equipment
damage or personal injury. Only a
qualified person shall install or service
the Type D.
▲ WARNING
CALIFORNIA PROPOSITION 65
This product can expose you to
chemicals including lead and nickel
which is known to the State of
California to cause cancer, birth
defects or other reproductive
harm. For more information, go to
www.P65Warnings.ca.gov.
Introduction
Scope of the Manual
This manual provides instructions for installation,
maintenance and parts information for the D Series
pressure reducing pilots.
Product Description
Spence Pressure Regulator is a combination of
D Series pilot and a Type E main valve. This regulator
reduces a steady or varying initial pressure to a
constant, adjustable delivery pressure.
Figure 1. D Series
Instruction Manual
VCIMD-14966 D Series
August 2022

Specications
The Specications section gives some general specications for the D Series pilot. The nameplates give detailed
information for a specic pilot as built in the factory.
Available Configurations
Type D: For ±1 psi / 0.07 bar control of delivery
pressures between 3 and 150 psi / 0.21
and 10.3 bar.
Type D2: For control of delivery pressures
between 100 and 300 psi / 6.90 and
20.7 bar.
Type D5: For ±1/2 psi / 0.03 bar control of delivery
pressures between 1 and 25 psi / 0.07
and 1.72 bar.
Type D120: Fast response controlling delivery
pressures between 5 and
300 psi / 0.35 and 20.7 bar. Used on
large Type E main valves.
Maximum Inlet Temperature(1)
Cast Iron: 450°F / 232°C
Steel: 750°F / 400°C
Maximum Inlet Pressure(1)
Cast Iron: 250 psig / 17.2 bar
Steel: 600 psig / 41.4 bar
Pressure Ranges(1)
Type D: 3 to 150 psig / 0.21 to 10.3 bar
Type D2: 100 to 300 psig / 6.90 to 20.7 bar
Type D5: 1 to 25 psig / 0.07 to 1.72 bar
Type D120: 5 to 300 psig / 0.35 to 20.7 bar
Construction Materials
Body: Cast Iron, Steel
Stem, Disk, Seat and Diaphragm: Stainless steel
Gasket: Grafoil
Spring: Inconel®
Approximate Weights
Type D: 7 lbs / 3.2 kg
Type D2: 10 lbs / 4.5 kg
Type D5: 14 lbs / 6.4 kg
Type D120: 16 lbs / 7.3 kg
Optional Accessories
Spring Chamber
Adjusting Handwheel
Wall Bracket
Locking Device
Composition Disk
Integral Mount Body
Vacuum Spring Assembly
1. The pressure/temperature limits in this Instruction Manual or any applicable standard limitation should not be exceeded.
TYPE PRESSURE RANGE,
psig / bar
ADJUSTING SPRING
Wire Diameter, In. / mm Part Number Color
D
3 to 20 / 0.21 to 1.38(1) 3/16 / 4.76 WAL05-05007-00 Aluminum
5 to 50 / 0.35 to 3.45(1) 1/4 / 6.35 WAL05-05003-00 Orange
10 to 100 / 0.69 to 6.89 5/16 / 7.94 WAL05-05005-00 Green
20 to 150 / 1.38 to 10.3 11/32 / 8.73 WAL05-05012-00 Black
D2 100 to 300 / 6.89 to 20.7 7/16 / 11.1 WAL05-04990-00 Aluminum
D5 1 to 10 / 0.07 to 0.69 3/16 / 4.76 WAL05-05007-00 Aluminum
5 to 25 / 0.35 to 1.72 1/4 / 6.35 WAL05-05003-00 Orange
D120
5 to 25 / 0.35 to 1.72 7/32 / 5.56 WAL05-05016-00 Not Specified on
Purchasing Specification,
Item Details or Drawing.
10 to 75 / 0.69 to 5.17 5/16 / 7.94 WAL05-05028-00
40 to 150 / 2.76 to 10.3 3/8 / 9.53 WAL05-05030-00
100 to 300 / 6.89 to 20.7 7/16 / 11.1 WAL05-04990-00 Aluminum
1. Vacuum Spring Assembly, minimum range is 30 in. Hg / 1.02 bar; maximum is reduced by 15 psig / 1.03 bar.
Table 1. D Series Spring Pressure Ranges
Inconel®is a mark owned by Special Metals Corporation.
2
D Series

SIDE MOUNTED
INTEGRALLY MOUNTED
VALVE IS TAPPED SO THAT
PILOT MAY BE MOUNTED ON
EITHER SIDE.
Figure 2. Typical Type ED Installation
3
D Series

Principle of Operation
The regulator is operated by initial steam or fluid
pressure. It is normally closed, being held so by initial
pressure on the disk and by an internal main spring.
When the pilot is opened, initial pressure flows through
the pilot to the 8B tee. Bleedport 4A restricts the flow
and pressure builds under the diaphragm and opens
the main valve. The 5A restriction elbow steadies the
operation of the regulator.
Delivery pressure feeds back through the control pipe
to the pilot diaphragm. As this pressure approaches a
balance with the air loading signal, the pilot throttles
the loading pressure. In turn, the main valve takes
a position established by the loading pressure
where just enough steam flows to maintain the set
delivery pressure.
Installation
▲ WARNING
Personal injury or system damage may
result if this pilot is installed, without
appropriate overpressure protection,
where service conditions could exceed
the limits given in the Specifications
section and/or pilot nameplate.
Additionally, physical damage to the
pilot may result in personal injury or
property damage due to escaping
of accumulated gas. To avoid such
injury and damage, install the pilot in a
safe location.
All pressure equipment should be
installed in a non-seismic area;
should not be exposed to fire; and
should be protected from thunderbolt
(lightning) strikes.
△ CAUTION
The piping system must be
adequately designed and supported
to prevent extraordinary loads to the
pressure equipment.
Planning
1. Locate the regulator in a horizontal pipe.
2. Provide a trap ahead of the regulator to prevent
water hammer and erratic operation.
3. Use strainer to protect the regulator and avoid
damaging effects of scale and dirt in pipelines.
4. Provide a three valve bypass to facilitate
inspection of the regulator without
interrupting service.
Main Valve
1. Flush the main piping system thoroughly to clear it
from welding beads, scale, sand, etc.
2. Mount main valve with diaphragm chamber down
and arrow on body pointing in the direction of flow.
Screwed end valve should be mounted in unions.
Pilot
1. Mount the pilot on either side of the main valve
by means of a 1/4 in. / 6.35 mm nipple and
union provided Make this connection to the
1/4 in. / 6.35 mm pipe tap on the inlet of the
main valve.
2. Screw 4A bleedport fitting into 1/8 in. / 3.18 mm
pipe tap on the outlet of the main valve body.
Note
Bleed orifice in this fitting is vital to
operation of regulator.
3. Screw 8B tee into 1/8 in. / 3.18 mm pipe tap in
pilot. Select tap facing downstream.
4. Screw 5A elbow containing restriction orifice into
1/8 in. / 3.18 mm pipe tap on underside of main
valve diaphragm chamber. If initial pressure or
pressure drop is less than 15 psi / 1.03 bar, a 5B
open elbow without orifice is used.
5. Connect tubing bends as illustrated in Figure 2.
Maintenance
▲ WARNING
To avoid personal injury, property
damage or equipment damage caused
by sudden release of pressure or
explosion of accumulated gas, do
not attempt any maintenance or
disassembly without first isolating the
pilot from system pressure and relieving
all internal pressure from the pilot.
Pilots that have been disassembled
for repair must be tested for proper
4
D Series

operation before being returned to
service. Only parts manufactured by
Emerson should be used for repairing
this pilot.
Due to normal wear or damage that may
occur from external sources, this pilot
should be inspected and maintained
periodically. The frequency of inspection
and replacement of parts depends upon
the severity of service conditions or the
requirement of local, state and federal
rules and regulations.
Disassembly
1. Release adjusting spring (key 4) compression by
loosening adjusting nuts (key 1). Remove nuts,
yoke (key 2), adjusting spring and spring button
(key 5).
2. Remove diaphragm nuts (key 15) and lift off cowl
(key 6). Lift out diaphragm assembly (keys 7, 16
and 17).
3. Disassemble diaphragm assembly by removing
diaphragm screw (key 7) from pressure plate
(key 16).
Note
This step is not necessary if installing
a new diaphragm assembly (included in
repair kit).
4. Remove blind flange bolts (key 23) and take off
blind flange (key 14). Remove screen (key 20) and
gasket (key 13).
5. Hold the pusher plate (key 8) and remove stem
nuts (key 22). Lift out stem assembly (keys 8 and
19) and valve spring (key 9). The disk (key 21)
will drop off. If the disk is not easily removed from
the stem, or the stem does not easily move in the
bushing (key 10) is difficult to remove, inspect
stem, seat ring (key 11) and disk carefully for
notches, scratches or bending.
6. Remove the seat ring (key 11) from the pilot body
(key 12) using a socket wrench. Do not remove
the seat ring unless replacing the stem assembly
(keys 8 and 19) and disk (key 21).
Inspection
1. Examine the seat ring (key 11) and disk (key 21)
sealing surfaces for nicks or other signs of
damage by pipeline debris. Slight imperfections
may be removed by lapping the surfaces.
Otherwise, replace the seat ring and disk.
2. Examine the stem (key 19) for a build-up of
pipeline contaminants or erosion. Remove any
build-up with a wire brush and polish with a very
fine crocus cloth. Work carefully to avoid bending
the stem.
3. Inspect the pilot body (key 12) and its ports for
corrosion. Some rust is normal, but if corrosion
debris is readily separated from the body, clean
body with wire brush and remove debris.
Lapping Operations
Lap sparingly using 500 grit lapping compound and
light pressure. Heavy grinding may cause galling, wide
sealing surfaces and a groove disk, all of which tend to
produce leakage.
Lapping may be done using a socket wrench to rotate
the stem and disk assembly back and forth against the
seat for 30 seconds or so. After the sealing surfaces
are lapped in, disassemble and clean all parts.
Seat, Disk and Stem Replacement
1. Clean the body threads of old sealing compound
using a wire brush.
Figure 3. Travel Setting
5
D Series

2. Apply new sealing compound (High-pressure,
high-temperature sealant) to the shoulder of the
seat ring (key 11). Let stand until tacky before
installing in pilot body (key 12).
3. Secure disk (key 21) to stem (key 19) with a stem
nut (key 22). Apply lapping compound to the disk
and insert this assembly into the pilot body (omit
the valve spring C).
4. Use a socket and extender to lap in the disk
(key 21) to seat joint. See Lapping Operations for
more information.
5. Screw pusher plate (key 8) onto the stem. Holding
the disk firmly against its seat, adjust the pusher
plate so that dimension C = 11/64 in. / 4.37 mm. A
gage (part number 05-02416-00) is supplied with
each repair kit. Be careful not to disturb the pusher
plate adjustment, use a prick punch to notch the
stem threads above the pusher plate so that the
pusher plate will not rotate freely. Work carefully
to avoid bending the stem. The valve travel is
now set.
6. Remove the stem nut and lift the stem assembly
(keys 19 and 8) out of the top of the pilot. Grind off
the stem Projection B flush with the upper surface
of the pusher plate. This can be done at the bench
without removing the stem from the body as long
as the grinder does not make contact with the
mating surfaces of the pilot body.
7. Reinsert the stem into the pilot body. Install disk
(key 21) and a stem nut (key 22).
8. Check that the valve travel A = 3/64 in. / 1.19 mm.
This need not be exact. Stem (key 19) should
move smoothly. Binding indicates a bent stem.
9. Remove the stem nut (key 22) and disk (key 21);
withdraw stem (key 19). Install stem with valve
spring (key 19), disk and both stem nuts.
Reassembly
1. If the seat ring (key 11), disk (key 21) and stem
(key 19) were not replaced, reinstall the seat ring
first, then slide the valve spring (key 9) over the
bushing (key 10) and slide the stem back into
place. If they were replaced, skip to step 3.
2. Install the seat ring (key 11) and stem nuts
(key 22) one at a time while holding the pusher
plate (key 8) with a socket.
3. Install the screen (key 20) and gasket (key 13).
Using the blind flange bolts (key 23), reinstall blind
flange (key 14).
Note
When replacing gaskets, be sure that
any serrated sealing surfaces are
cleaned of old gasket material.
4. Assemble the diaphragm assembly (keys 7, 16
and 17) by sandwiching the diaphragms (key 17)
between the pressure plate (key 16) (flat side
against diaphragm) and the diaphragm screw
(key 7). The number of diaphragm disks depends
on the adjusting spring range. See Table 2.
5. Apply sealing compound (High-pressure, high-
temperature sealant) to the shoulder of the
diaphragm screw. Apply sealing compound to the
diaphragm flange of the pilot body for steel body
pilots only.
6. Put the diaphragm assembly into place (pressure
plate up). Center the assembly and install the
cowl (key 6). Install four diaphragm bolts or
studs (key 18) and diaphragm nuts (key 15)
equally around the cowl to ensure the diaphragm
assembly is centered. Install the rest of the
diaphragm nuts, bolts and/or studs and tighten in
an opposing pattern.
7. Install the spring button (key 5), adjusting spring
(key 4), spring yoke (key 2) and adjusting nuts
(key 1).
Parts Ordering
When ordering parts, it is essential that the pilot type,
service and serial number be stated.
Select part by item number, but order by part number.
Specify complete part number when ordering.
Parts List
Repair Parts Kit (See Table 3)
D Series and Options Parts List (See Tables 4 to 7)
ADJUSTING SPRING RANGE DIAPHRAGM DISK
psig bar
0 to 8 0 to 0.55 1
3 to 20 0.21 to 1.38 2
5 to 50 0.35 to 3.45 2
10 to 100 0.69 to 6.89 2
20 to 150 1.38 to 10.3 3
Table 2. Number of Diaphragm Disk
6
D Series

KEY PART NAME MATERIAL PART NUMBER QUANTITY REMARKS
1 Adjusting Nut Steel WAL05-02874-00 2 - - - -
2Spring Yoke Iron WAL05-06183-00 1 - - - -
3 Standard Steel WAL04-05219-00 2 - - - -
4 Adjusting Spring Steel See Table 1 1 - - - -
5 Spring Button Steel WAL04-01040-00 1 - - - -
6 Cowl Cast Iron WAL04-01508-00 1 Cast Iron Body
Cowl Steel WAL04-1592-00 1 Steel Body
7* Diaphragm Screw Steel WAL04-04822-00 1 - - - -
8* Pusher Plate Steel WAL04-03718-00 1 - - - -
9* Valve Spring Inconel®WAL05-04985-00 1 - - - -
10 Bushing Stainless steel WAL04-01080-00 1 - - - -
11* Seat Ring Seco Metal WAL04-04057-90 1 - - - -
12 Body, Bushing, Plug Cast Iron WAL07-03514-00 1 - - - -
Body, Bushing, Plug Steel WAL07-04267-02 1 - - - -
13* Gasket Blugard WAL05-02378-01 1 Cast Iron Body
Gasket Flexitalic WAL05-11718-00 1 Steel Body
14 Blind Flange Cast Iron WAL04-02151-00 1 - - - -
Blind Flange Steel WAL04-11678-00 1 - - - -
15 Diaphragm Nut Steel WAL05-02871-00 12 Cast Iron Body
Diaphragm Nut Steel WAL05-02845-00 24 Steel Body
16* Pressure Plate Steel WAL04-06979-00 1 - - - -
17* Diaphragm Stainless steel WAL04-01623-00 3 - - - -
18 Diaphragm Bolt Steel WAL05-04764-00 12 Cast Iron Body
Diaphragm Stud Steel WAL05-05490-00 12 Steel Body
19* Stem Stainless steel WAL04-05229-00 1 - - - -
20* Screen Stainless steel WAL04-04700-00 1 Steam Service
Screen Stainless steel WAL04-04701-00 1 Water Service
21* Disk Seco Metal WAL04-01772-90 1 - - - -
22* Stem Nut Steel WAL05-02888-00 2 Steam Service
Stem Nut Brass WAL05-02886-00 2 Water Service
23 Blind Flange Bolt Steel WAL05-04803-00 4 Cast Iron Body
Blind Flange Bolt Steel WAL05-11719-00 4 Steel Body
* These parts furnished in Repair Kit.
REPAIR KIT MATERIAL PART NUMBER
Repair Kit - Hard Cast Iron Pilot WAL07-04164-00
Repair Kit - Hard Steel Pilot WAL08-10375-00
Repair Kit - Soft Cast Iron Pilot WAL08-08556-00
Repair Kit - Soft Steel Pilot WAL08-10379-00
Table 3. Repair Parts Kit
Table 4. Types D and D5 Series Parts List
Inconel®is a mark owned by Special Metals Corporation.
7
D Series

KEY PART NAME MATERIAL PART NUMBER QUANTITY REMARKS
Locking Device
35 Padlock Brass WAL05-03204-00 1 - - - -
36 Lock Bar Steel WAL04-00436-00 1 - - - -
37 Spring Yoke Assembly Iron WAL07-43507-00 1 - - - -
Wall Bracket
15 Diaphragm Nut Steel WAL05-02871-00 1 Iron Body
Diaphragm Nut Steel WAL05-02845-00 4 Steel Body
38 Wall Bracket Cast Iron WAL04-01029-00 4 - - - -
39 Diaphragm Bolt Steel WAL05-04766-00 4 Iron Body
Diaphragm Stud Steel WAL05-05462-00 8 Steel Body
Composition Disk
25* Disk Assembly Brass WAL07-53512-00 1 - - - -
26* Stem Stainless steel WAL04-05381-00 1 - - - -
27* Seat Ring Stainless steel WAL04-04060-00 1 - - - -
Enclosed Spring Chamber
28 Adjusting Screw Steel WAL05-04860-00 1 - - - -
29 Locknut Steel WAL05-02942-00 1 - - - -
30
Spring Chamber Iron WAL04-01393-00 1 - - - -
Spring Chamber Bronze WAL04-01395-00 1 - - - -
Spring Chamber Steel WAL04-01394-00 1 - - - -
Enclosed Spring Chamber Kit Cast Iron WAL08-01868-00 - - - -
Adjusting Wheel
31 Handwheel Aluminum WAL04-12985-01 1 - - - -
32 Adjusting Screw Steel WAL04-04752-02 1 - - - -
33 Locknut Steel WAL05-02942-00 1 - - - -
34 Yoke Cast Iron WAL04-06170-00 1 Iron Body
Yoke Ductile Iron WAL04-06167-02 1 Steel Body
Handwheel Kit Cast Iron WAL08-01867-00 - - - -
Vacuum Spring Assembly
40 Floating Plate Iron WAL04-03710-00 1 - - - -
41 Vacuum Spring 302 Stainless steel WAL05-05055-00 1 - - - -
42 Valve Spring Inconel®WAL05-09353-00 1 - - - -
*These parts furnished in Repair Kit.
Table 5. D Series Options Parts List
Inconel®is a mark owned by Special Metals Corporation.
8
D Series

KEY PART NAME MATERIAL PART NUMBER REMARKS
1 Adjusting Screw Steel WAL4-04760-0 - - - -
2 Locknut Steel WAL5-02877-0 - - - -
3 Standard Nut Steel WAL5-02877-0 - - - -
4Spring Yoke Cast iron WAL4-06177-0 - - - -
5 Guide Stud Stainless steel WAL4-05419-0 - - - -
6 Upper Spring Button Steel WAL4-01078-0 - - - -
7 Adjustment Spring, 5 to 25 psi / 0.35 to 1.72 bar Steel WAL5-05016-0 Use 2 Diaphragm
Adjustment Spring, 10 to 75 psi / 0.69 to 5.17 bar Steel WAL5-05028-0 Use 2 Diaphragm
Adjustment Spring, 40 to 150 psi / 2.76 to 10.3 bar Alloy steel WAL5-05030-0 Use 3 Diaphragm
8 Standard Steel WAL5-05200-0 - - - -
9 Lower Spring Button Steel WAL4-01041-0 - - - -
10 Diaphragm Nut Steel WAL5-02872-0 Note 1
Diaphragm Nut Steel WAL5-02848-0 Note 2
11 Cowl Cast iron WAL4-01513-0 - - - -
Cowl Steel WAL4-01514-0 - - - -
12 Diaphragm Stainless steel WAL4-01659-0 A, B See item 7
13 Diaphragm Bolt Steel WAL5-04770-0 Note 1
Diaphragm Stud Steel WAL5-05480-0 Note 2
14 Bushing Stainless steel WAL4-01132-0 See item 16
15 Stem Stainless steel WAL4-05305-1 B
16 Body and Bushing Cast iron WAL8-09159-0 - - - -
Body and Bushing Steel WAL8-09160-1 - - - -
17 Screen - Steam Monel®WAL4-04700-0 B
18 Pressure Plate Cast iron WAL4-03599-0 B
19 Diaphragm Screw Steel WAL4-04822-0 B
20 Pusher Plate Steel WAL4-03717-0 B
21 Valve Spring Inconel®WAL5-04985-0 A, B
22 Seat Ring Stainless steel WAL4-04062-0 B
23 Disk Stainless steel WAL4-07283-1 B
24 Stem Nut Steel WAL5-02891-0 B
25 Gasket Asbestos WAL5-02378-0 A, B Note 1
Gasket Flexitalic WAL5-11718-0 A, B Note 2
26 Blind Flange Cast iron WAL4-02151-0 - - - -
Blind Flange Steel WAL4-11678-0 - - - -
27 Blind Flange Bolt Steel WAL5-04803-0 Note 1
Blind Flange Bolt Steel WAL5-11719-0 Note 2
28 Pipe Plug, 1/4 NPT Steel WAL4-03772-0 Not shown
Wall Bracket
29 Wall Bracket Iron WAL4-01028-0 - - - -
30 Diaphragm Bolt Steel WAL5-04781-0 - - - -
10 Diaphragm Nut Steel WAL5-02872-0 - - - -
A - Recommended Spare Parts
B - Furnished in Repair Kit:
WAL8-09154-0 Note 1
WAL8-10356-0 Note 2
Note 1: Applies to Iron Body Pilots
Note 2: Applies to Steel Body Pilots
Table 6. Type D120 Pilot (Figure 6)
Inconel®and Monel®are marks owned by Special Metals Corporation.
9
D Series

KEY PART NAME MATERIAL PART NUMBER REMARKS
1 Adjusting Screw Steel WAL4-04760-0
2 Adjusting Screw Locknut Steel WAL5-02953-0
3 Guide Stud Stainless steel WAL4-05419-0
4 Standard Nut Steel WAL5-02874-0
5Spring Yoke Cast iron WAL4-06179-0
6 Upper Spring Button Steel WAL4-01078-0
7 Standard Steel WAL4-05213-0
8 Adjusting Spring Aluminum steel WAL5-04990-0
9 Lower Spring Button Steel WAL4-01041-0
10 Diaphragm Nut Steel WAL5-02871-0 Note 1
Diaphragm Nut Steel WAL5-02845-0 Note 2
11 Pressure Plate Steel WAL4-03679-0 B
12 Body and Bushing Iron WAL7-03514-0 - - - -
Body and Bushing Bronze WAL8-04265-0 - - - -
Body and Bushing Steel WAL7-04267-2 Screwed
Body and Bushing Steel WAL8-09518-2 Flanged Inlet
Body and Bushing Steel WAL8-09517-2 Secoweld Screwed
Body and Bushing Steel WAL8-07124-2 Secoweld Flanged Inlet
13 Diaphragm Bolt Steel WAL5-04764-0 Note 1
Diaphragm Stud Steel WAL5-05490-0 Note 2
14 Diaphragm Stainless steel WAL4-01623-0 A, B 3 per set
15 Valve Spring Inconel®WAL5-04985-0 A, B
16 Bushing Stainless steel WAL4-01080-0 See item 12
17 Gasket Asbestos WAL5-02378-0 A, B Note 1
Gasket Flexitalic WAL5-11718-0 A, B Note 2
18 Blind Flange Iron WAL4-02151-0 - - - -
Blind Flange Bronze WAL4-02153-0 - - - -
Blind Flange Steel WAL4-11678-0 - - - -
19 Blind Flange Bolt Steel WAL5-04803-0 Note 1
Blind Flange Bolt Steel WAL5-11719-0 Note 2
20 Cowl Iron WAL4-01505-0 - - - -
Cowl Steel WAL4-01591-0 - - - -
21 Diaphragm Screw Steel WAL4-04822-0 B
22 Pusher Plate Steel WAL4-03718-0 B
23 Stem Stainless steel WAL4-05229-0 B
24 Seat Ring Stainless steel WAL4-04057-0 B
25 Disk Stainless steel WAL4-01772-0 B
26 Stem Nut Steel WAL5-02888-0 B
27 Screen - Water Monel®WAL4-04701-0 - - - -
Screen - Steam Monel®WAL4-04700-0 B
28 Pipe Plug, 1/8 NPT Steel WAL4-03769-0 Not Shown
Pipe Plug, 1/8 NPT Brass WAL4-03770-0 Not Shown
A - Recommended Spare Parts
B - These parts furnished in Repair Kit (Steam screen):
Stainless steel Disk: Cast iron and Bronze (WAL8-09157-0), Carbon steel (WAL8-10357-0)
Composite Disk: Cast iron and Bronze (WAL8-09158-0), Carbon steel (WAL8-10380-0)
Note 1: Applies to Iron and Bronze Body Pilots
Note 2: Applies to Steel Body Pilots
Use Pilot Setting instructions WAL9-98165-0
Table 7. Type D2 Pilot Parts List (Figure 7)
- continued -
Inconel®and Monel®are marks owned by Special Metals Corporation.
10
D Series

KEY PART NAME MATERIAL PART NUMBER REMARKS
Enclosed Spring Chamber
29 Spring Chamber Steel WAL7-40529-0 - - - -
Adjusting Handle
30 Handle and Hub Assembly Steel WAL8-09774-0 - - - -
31 Adjusting Stud Spacer Brass WAL4-05600-0 - - - -
32 Thrust Bearing Steel WAL5-00552-0 - - - -
33 Guide Standard Locknut Steel WAL5-03016-0 - - - -
34 Cross Bar Steel WAL4-00434-0 - - - -
35 Guide Standard Spacer Brass WAL4-04936-0 - - - -
36 Support Standard Nut Steel WAL5-02942-0 - - - -
37 Adjusting Stud Assembly - - - - WAL7-40550-0 - - - -
38 Spring Yoke Cast iron WAL4-06173-0 - - - -
39 Support Standard Steel WAL4-05223-0 - - - -
40 Guide Standards Steel WAL4-05221-0 - - - -
Wall Bracket
41 Wall Bracket Cast iron WAL4-01029-0 - - - -
42 Diaphragm Bolt Steel WAL5-04766-0 Note 1
Diaphragm Stud Steel WAL5-05462-0 Note 2
10 Diaphragm Nut Steel WAL5-02871-0 Note 1
Diaphragm Nut Steel WAL5-02845-0 Note 2
Flanged Inlet
44 Gasket Steel Asbestos WAL5-02370-0 - - - -
45 Flange Assembly - Female Steel WAL7-43516-0 See item 12
46 Flange Assembly - Male Steel WAL7-40535-0 - - - -
13 Stud Steel WAL5-05490-0 - - - -
10 Nut Steel WAL5-02845-0 - - - -
Composition Disk
47 Stem Stainless steel WAL4-05381-0 B
48 Seat Ring Stainless steel WAL4-04060-0 B
49 Composite Disk Assembly Brass WAL7-53512-0 B
A - Recommended Spare Parts
B - These parts furnished in Repair Kit (Steam screen):
Stainless steel Disk: Cast iron and Bronze (WAL8-09157-0), Carbon steel (WAL8-10357-0)
Composite Disk: Cast iron and Bronze (WAL8-09158-0), Carbon steel (WAL8-10380-0)
Note 1: Applies to Iron and Bronze Body Pilots
Note 2: Applies to Steel Body Pilots
Use Pilot Setting instructions WAL9-98165-0
Table 7. Type D2 Pilot Parts List (Figure 7) (continued)
11
D Series

Figure 4. Type D Pilot Assembly
12
D Series

LOCKING DEVICE WALL BRACKET ENCLOSED SPRING
CHAMBER
ADJUSTING HANDWHEEL
COMPOSITION DISK VACUUM SPRING ASSEMBLY
Figure 5. D Series Options Assembly
13
D Series

Figure 6. Type D120 Pilot Assembly
1/4 NPT
SERIAL NUMBER PLATE
1/4 NPT
WALL BRACKET
14
D Series

Figure 7. Type D2 Pilot Assembly
ADJUSTING HANDLE
ENCLOSED SPRING CHAMBER
WALL BRACKET
FLANGED INLET
ALTERNATE:
SECOWELD CONSTRUCTIONS
15
D Series

SD4111C
Emerson Automation Solutions
SpenceValve.com
VCIMD-14966 © 2021, 2022 Emerson Electric Co. All rights reserved 08/22.
Spence is a mark owned by one of the companies in the Emerson Automation
Solutions business unit of Emerson Electric Co. The Emerson logo is a
trademark and service mark of Emerson Electric Co. All other marks are
property of their prospective owners.
The contents of this publication are presented for informational purposes only,
and while every eort has been made to ensure their accuracy, they are not to
be construed as warranties or guarantees, express or implied, regarding the
products or services described herein or their use or applicability. All sales are
governed by our terms and conditions, which are available upon request. We
reserve the right to modify or improve the designs or specications of such
products at any time without notice.
Emerson Electric Co. does not assume responsibility for the selection, use
or maintenance of any product. Responsibility for proper selection, use
and maintenance of any Emerson Electric Co. product remains solely with
the purchaser.
D Series
Americas
McKinney, Texas 75070 USA
T +1 800 558 5853
+1 972 548 3574
Europe
Bologna 40013, Italy
T +39 051 419 0611
Asia Pacic
Singapore 128461, Singapore
T +65 6777 8211
Middle East and Africa
Dubai, United Arab Emirates
T +971 4 811 8100
This manual suits for next models
4
Table of contents
Other SPENCE Controllers manuals
Popular Controllers manuals by other brands
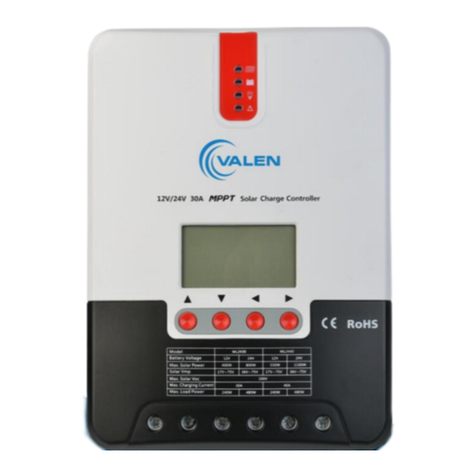
Valen
Valen MPPT 30A Operation manual

ADTRAN
ADTRAN BlueSecure Controller Setup and administration guide
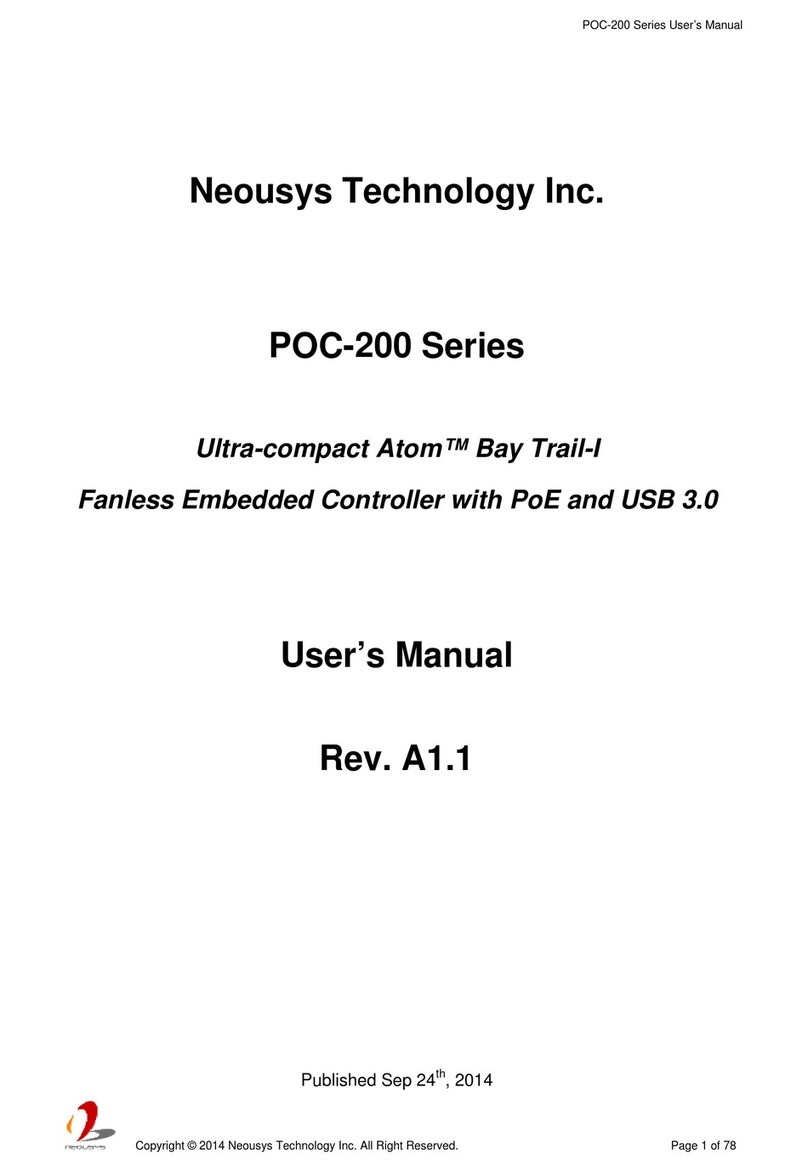
Neousys Technology
Neousys Technology POC-200 user manual
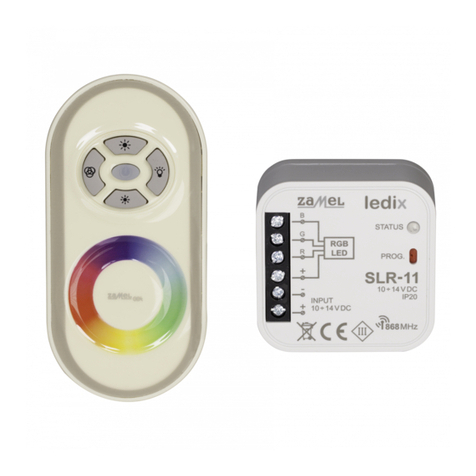
Zamel
Zamel Cet LediX SLR-11P manual
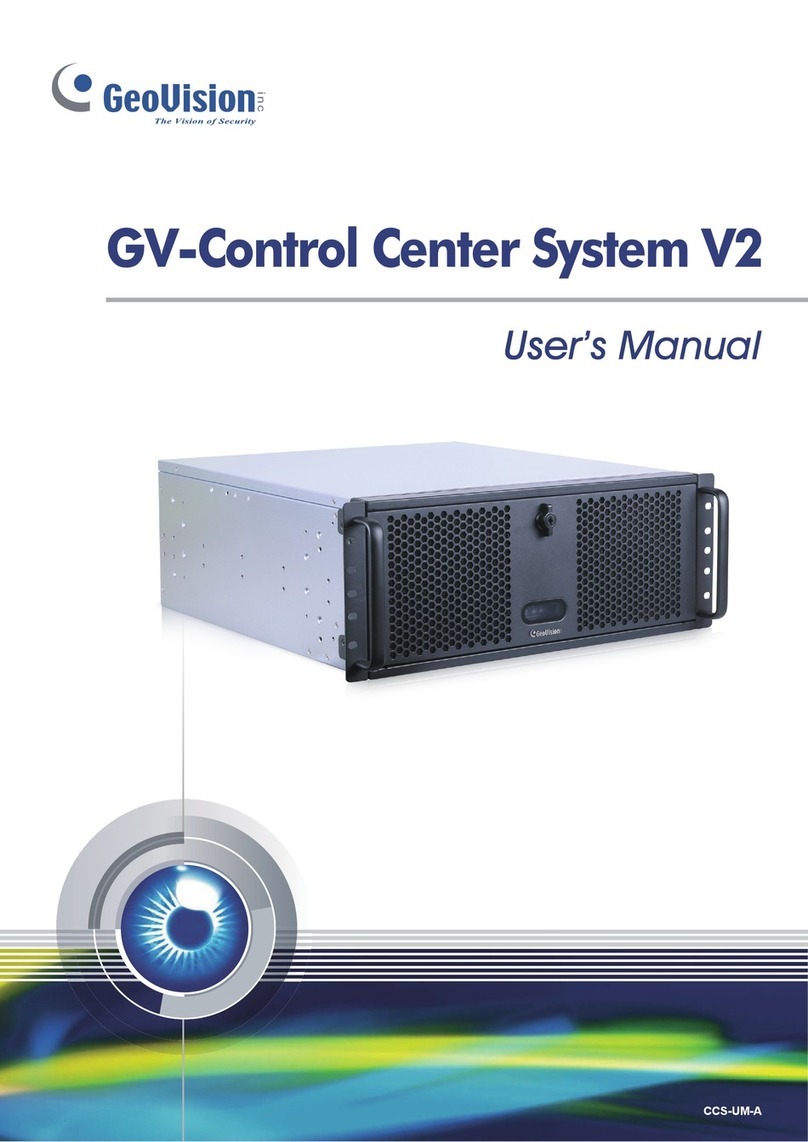
GeoVision
GeoVision GV-Control Center System V2 user manual
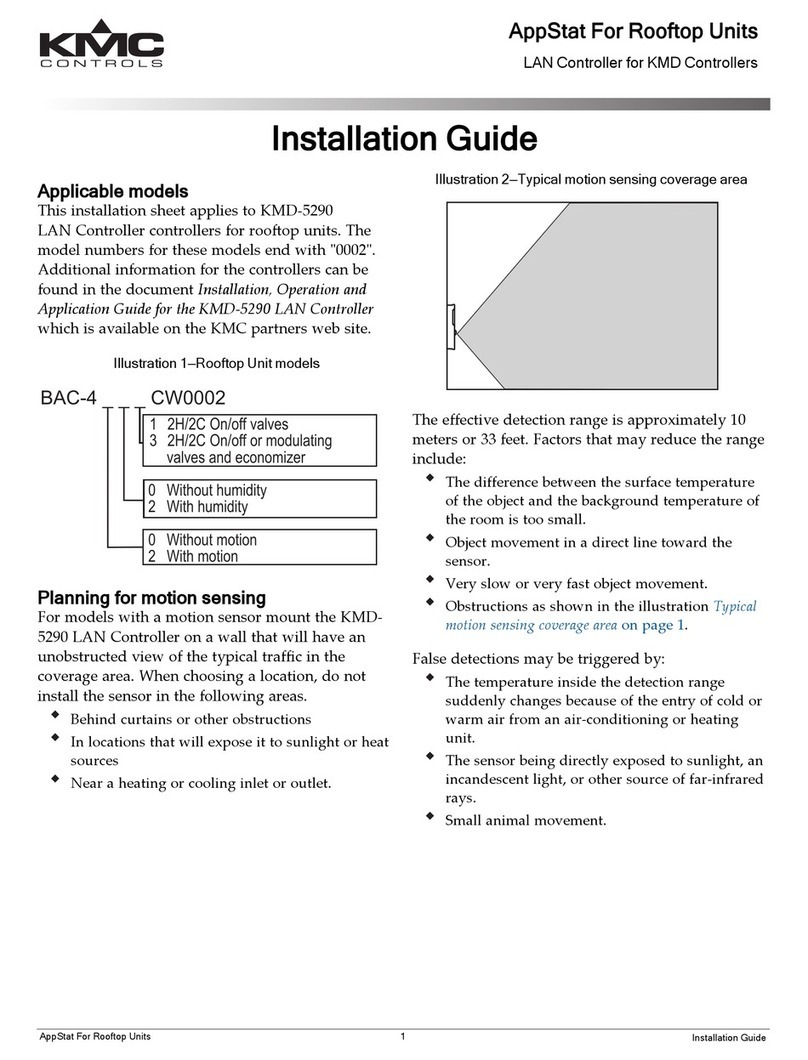
KMC Controls
KMC Controls KMD-5290 installation guide