Status Instruments DM3600U User manual

SECTION CONTENTS PAGE NO.
1.0 DESCRIPTION 1
2.0 UNPACKING 1
3.0 INSTALLATION 2-3
4.0 OPTION PODS 4-5
5.0 CONFIGURATION OPTIONS 5
6.0 MECHANICAL 6-7
7.0 SPECIFICATION 7-10
8.0 INSTRUMENT CONFIGURATION 10-11
9.0 MENU MODE 11-12
10.0 MENU MAP 13
11.0 RESETTING THE DEVICE 13
12.0 INPUT MENU STRUCTURE 14-17
13.0 OUTPUT MENU STRUCTURE 18-20
14.0 SYSTEM MENU STRUCTURE 21-22
15.0 FAULT FINDING 23
Status Instruments Ltd, Status Business Park, Tewkesbury, Glos. GL20 8FD
Tel: +44 (0)1684 296818 Fax: +44 (0)1684 293746
52-314-2367-02Issue: Web 4
DM3600U
INDEX
Single Channel Universal Input 6 Digit Indicator
Important‐Pleasereadthisdocument
beforeanyinstalling.

The DM3600 is a highly accurate and stable digital process indicator that accepts all commonly used process
signals. The unit can be used "stand alone" or with the Modbus serial communications option, as part of a
larger system. The case design enables Option Pods to be easily installed without the need for dismantling
or re-calibration. A range of Pods are available for:
Relay outputs
Isolated (4 to 20) mA re-transmission
The diagram below shows the rear panel positions for all electrical connections.
Please inspect the instrument carefully for any signs of shipping damage. The packaging has been designed
to provide maximum protection, however, we cannot guarantee that mishandling will not have damaged
the instrument. In the case of this unlikely event, please contact your supplier immediately and retain the
packaging for subsequent inspection.
Page 1
(Read the following safety information before installation)
WARNING !
INSTALLER - This section must be used by competent personnel only. If this equipment is not installed
in accordance with these instructions, protection against electrical hazards may be impaired. It is the
responsibility of the person installing this equipment to implement this procedure in accordance with the
relevant code of practice (for the installation of instrumentation used in process control systems), issued
by a recognised local body.
MOUNTING - This equipment is classed as PERMANENTLY CONNECTED EQUIPMENT. Hazardous voltages
may be present on the terminals of this equipment. The equipment must be panel mounted into a suitable
enclosure which provides at least IP20 protection behind the panel.
SUPPLY - The supply terminals and associated internal circuitry are isolated from all other parts of the
equipment in accordance with BS EN61010-1, for connection to an installation over-voltage Category II
supply, (pollution degree 2). The supply voltage and frequency must remain within the limits stated on the
product label. The mains supply to the unit must be protected by an external 1 A fuse and a suitable switch
or circuit breaker must be located close to the equipment, in order to isolate the supply.
SIGNAL INPUT/OUTPUTS - All signal input, and communication terminals and associated internal circuitry
are intended for operation at voltages less than 40 VDC. These circuits, which may become accessible
during NORMAL OPERATION, must ONLY be connected to signals complying with the requirements for Safety
Extra Low Voltage (SELV) circuits.
RELAYS - The relay terminals and associated internal circuitry are isolated from all other parts of the
equipment in accordance with BS EN 61010-1, for connection to an installation over-voltage Category II supply,
(pollution degree 2). The relay operating voltage and current must remain within the limits stated. (Refer
to Section 7.0).
SERVICE - This equipment contains no user serviceable parts and must be returned to supplier for repair.
The maximum panel thickness is 10 mm. The instrument case has an integral gasket which forms a seal
when the instrument is tightened against the panel. The panel should be clean, smooth and at least 1.6 mm
thick for the seal to be effective.
All connections are made to sockets which are removable for ease of maintenance.
NOTE: CABLE SIZE (0.5 to 1.5) mm²
Page 2
1.0 DESCRIPTION 3.0 INSTALLATION
Tag No.
°C
1A 1B 2A 2B
DISCRETE LED
ALARM
INDICATORS
BRIGHT SIX
DIGIT
DISPLAY
FRONT PANEL
SEALED
TO IP66
CYCLE
KEY
SHIFT
KEY
INCREMENT
KEY
LEGEND
WINDOW
PROCESS
INPUTS
OPTION POD
SLOT 2
(NOT SHOWN)
OPTION
POD SLOT 1
POWER
CONNECTOR
RJ45 COMMS
+ DIGITALS
2.0 UNPACKING
3.1 INSTALLING INTO A PANEL
WARNING
Use only the retaining screws provided to clamp the instrument to the panel (screws
must be tightened sufficiently to effect a seal but must never be over tightened).
3.2 WIRING

Page 3
The Power supply rating will be indicated on the top of the instrument, ENSURE IT IS CORRECT FOR THE
APPLICATION.
THE MAINS SUPPLY TO THE EQUIPMENT MUST BE PROTECTED BY AN EXTERNAL 1 A FUSE AND A
SUITABLE SWITCH OR CIRCUIT BREAKER WHICH SHOULD BE NEAR THE EQUIPMENT.
NOTE: USE 600 VRMS CABLE (0.5 TO 1.5) mm².
Wires are retained by screws. Ensure that the exposed section of the wire is fully inserted and that no
loose strands are exposed.
All sensor connections are made via the five way "fast wiring" socket at the rear of the unit (wire size
(0.5 to 1.5) mm²).
NOTE: THERMOCOUPLE, RTD AND VOLTAGE INPUT A SCREENED CABLE IS RECOMMENDED FOR RUNS
GREATER THAN 10 m.
To make a connection: Insert small screwdriver blade into tension clamp orifice (1), push and twist to
deflect clamp into open position. Do not lever screwdriver thus forcing connector body sideways. Insert
conductor tail sufficiently into (2) then release screwdriver. Ensure no loose wire strands protrude.
Page 4
Power must be removed from unit before adding/removing a pod. Slot 1 (alarm 1A and 1B) should be
positioned on the left side of the unit looking from the front to correspond to front panel alarm indicator,
Slot 2 (alarm 2A and 2B) is positioned on the right.
To install an Option Pod, slide back the cover to its next engaging position and push the pod connection
within the mating connector. To remove an Option Pod, disengage the supporting latch situated beneath
the pod by pushing the back cover forward, the pod can then be lifted away from the instrument connector.
The relay pod has two "change over"relays with a common wiper.
NOTE: USE 600 VRMS CABLE (0.5 TO 1.5) mm²
NOTE: ANY CIRCUIT WITH AN AC POTENTIAL GREATER THAN 33 VRMS AND 46.7 V PEAK MUST BE
PROTECTED WITH A 5 A(T) FUSE WHEN CONNECTED TO THIS POD.
3.3 POWER SUPPLY
3.4 SENSOR CONNECTIONS
4.0 OPTION PODS
(+) L N (-)
1
2
12345
NO
NC
WIPER
NO
NC
4.1 INSTALLING PODS
4.2 DUAL RELAY POD. POD-3000/02000000

The re-transmission pod (when fitted) is designed to provide (0 to 10) mA, (0 to 20) mA or (4 to 20) mA output
in active or passive modes. The output can be any portion of the display. The pod can be used in two
modes:
Active (Source) Passive (Sink)
Configuration can be performed in two ways. The first configuration method is to use the menu structure
interface, standard on every DM3600 unit. The second configuration method is to use the optional factory
fitted MODBUS RS485 communications option. To enable easy configuration via comms, the user can
download M-Config from www.status.co.uk. This is a free Windows application to allow the user to easily
and intuitively configure DM3600 devices. For more information regarding the DM3600 MODBUS implementation,
please contact your supplier.
When fitted this option provides the user with either 4 or 2 wire RS485 serial communications together two
digital inputs. Connections are made via a RJ45 connector. A 0.5 m interface is supplied with this.
Page 5 Page 6
Material ABS/PC
Flammability IEC707 FV0, UL 94VO
Weight 230 g
Panel cut out (92 x 45) mm
12345
R Load
12345
V
R Load
-+
Max RLoad = 1 K
4.3 ISOLATED (4 TO 20) mA RE-TRANSMISSION POD. POD-3000/03
5.0 CONFIGURATION OPTIONS
5.1 COMMUNICATION/DIGITAL INPUT OPTION
(5 to 24) V
DIS 1
DIS 2
DIS Com
+
-
DISCRETE INPUT CONNECTION
To activate, apply voltage (5 to 24) V
Max Current = V A
Per Channel 1600
Reverse connection and over voltage protected.
DIS COM
DIS1
COMS COM
DIS2
+TX
-RX
-TX
+RX
RJ45
Tag No.
48.0
96.0
VAC
1A 1B 2A 2B
11.0 131.0 BEHIND BEZEL
IP65 SEAL TO PANEL
6.0 MECHANICAL DETAILS
10 mm MAXIMUM PANEL THICKNESS
140.0
PANEL CLAMP
OPTION POD
CLAMPING SCREW
RLoad < (V-2) KΩ
22
And Vmax = 30 V
All dimensions are in mm

Page 7 Page 8
UNIVERSAL INPUT TYPES
SENSOR RANGE AND LINEARISATION
mA 4 to 20, ± 20, ± 10
RTD Pt100, Ni120, Custom*¹
T/C K, J, T, R, S, E, L, N, B, Custom*¹
mV ± 100 mVDC
Volts ± 10 V, ± 5 V, (1 to 5) V, ± 1 VDC
Minimum Span Any span within the range can be selected, but the recommended span is
> 10 % of range
CURRENT INPUT
Basic Accuracy 0.05 % FS ± 0.05 % of reading*²
Thermal Drift 0.02 %/°C
Input Impedance 20 Ω
Linearity Linear, X½, X3/2, X5/2, Custom*¹
A 19.5 V ± 0.5 V @ 25 mA isolated power supply is available to power the current loop. (Short circuit
protected)
RTD
Sensor Range (-200 to 850) °C (18 to 390) Ω
Linearisation BS EN60751/JISC1604/Custom*¹
Basic Accuracy 0.1 °C ± 0.05 % of reading*²
Thermal Drift Zero 0.004 Ω1 °C
Span 0.01 %/°C
Excitation Current 1 mA
Lead Resistance Effect 0.002 °C/Ω
Max Lead Resistance 50 Ω/leg
*NOTES
1. Custom can be up to 60 co-ordinate pairs or up to 7 segments of 15th order polynominal
2. Full accuracy for any span > 10 % of range.
THERMOCOUPLE
TYPE RANGE (°C)
K -200 to 1370
J -200 to 1200
T -210 to 400
R*³ -10 to 1760
B*40 to 1700
S*³ -10 to 1760
E -200 to 1000
L -100 to 600
N -180 to 1300
Custom -999 to 9999
Accuracy
Linearisation
Cold Junction Error
Cold Junction Tracking
Cold Junction Range
± 0.04 % FS ± 0.04 % reading or ±
0.5 °C, whichever is greater*² BS
4937/IEC 584-3/Custom*¹
± 0.5 °C
0.05 °C/°C
(-20 to 60) °C
Thermal Drift Zero 4 uV/°C
Span 0.02 %/°C
VOLTAGE INPUT
Basic Accuracy 0.04 % FS ± 0.04 % of reading*²
Thermal Drift 0.01 %/°C
Input Impedance 1 MΩ
Linearity Linear, X½, X3/2, X5/2, Custom*¹
Range ± 100 mV, ± 1 V, ± 5 V, ± 10 V,
(1 to 5) V
*Notes
1. Custom can be up to 60 co-ordinate pairs or up to 7
segments of 15th order polynominal
2. Full accuracy for any span > 10 % of range
3. Accuracy true for (500 to 1760) °C
4. Accuracy true for (400 to 1650 °C
GENERAL
Filter (Seconds)
Power Supply S1
S2
Power Consumption
Breakdown Isolation
None, Programmable (fixed), Adaptive
(90 to 264) VAC 50/60 Hz
(for LVD Compliance)
(20 to 35) VDC
10 VA (worst case) 6 VA typical
I/O Ports 500 V
ENVIRONMENTAL
Sealing to Panel IP65
Ambient Operating Range (-30 to 60) °C
Ambient Storage (-50 to 85)°C
Ambient Humidity (10 to 90) % RH
EMC
Emissions BS EN61326 Class A
Immunity BS EN61326 Annex A
Safety BS EN61010-1
6.2 OPTION POD
53.5 16.019.5 13.5
43.5
7.0 SPECIFICATIONS @ 20°C
All dimensions in mm
134 52
+-
12345
12345
V
12345
+-
+
-
12345
TX +
-
RTD
T/C
VOLTAGE
CURRENT
ACTIVE
CURRENT
PASSIVE
DM3600 5 WAY I/P CONNECTION

Page 9 Page 10
REMOTE DIGITALS OPTION
Two isolated digital inputs are available to reset latched alarms, clear peak/valley readings, or for
customised use with TFML.
Simple plug in pre-calibrated units, no dismantling or re-calibration.
POD-3000/02 DUAL RELAY ALARM
Two independent mains rated relay outputs
Contacts 2 x changeover relays with common wiper
Ratings AC, DC
Maximum Load 5 A @ 250 V, 5 A @ 30 V
Min Load 100 mA
Maximum Power 1250 VA, 150 W
Maximum Switching 253 V, 125 V
Electrical Life 1 M operations at rated load
Mechanical Life 50 M operations
Termination Standard 5 way tension clamp connector
Optional Screw terminals
Pulse Mode Pulse period 100 ms
POD-3000/03 ISOLATED RE-TRANSMISSION
Ranges (0 to 10) mA (Active or Passive)
(0 to 20) mA (Active or Passive)
(4 to 20) mA (Active or Passive)
Minimum Current Output 0 mA
Maximum Current Output 23 mA
Accuracy 0.07 % F.S.
Resolution 1 part in 30 000
Max. Output load See Section 4.3
Max. Ext. Supply Voltage 30 V (Passive mode)
Voltage Effect 0.2 µA/V
Ripple Current < 3 µA
Isolation 500 VAC
Stability 1 µA/°C
Termination Standard 5 way tension clamp connector
Optional Screw terminals
Voltage Outputs Voltage Outputs may be obtained by connecting a external resistor and
selecting the appropriate current range, as shown in the table below.
7.1 PLUG AND PLAY OPTION PODS
RS485 MODBUS Communications
DM3600 is available with RS485 serial communications using MODBUS RTU protocol, and can be used with
Status’ own M-Config software.
Physical Layer 4 wire or 2 wire half duplex RS485
Protocol MODBUS RTU format
Breakdown Isolation 500 VAC
Maximum Fan out 32 units (can be increased with repeaters)
Termination Standard RS485
The DM3600 is configured using the three keys on the front panel. The unit has two modes of operation:
The first is ‘Run’ mode. This will automatically be entered 5 s after power up. This is the principle mode
of operation. There are 6 possible key press combinations, as shown in the ‘Key Press Definitions’ diagram
below. The ‘Run Mode Options’ diagram shows the key presses required to access various states from the
run mode. (See diagram in Section 8.2 overleaf).
The other principle mode of operation is ‘Menu Mode’. The menu navigation method is shown diagrammatically
in the ‘General Menu Structure’ (see Section 9.1).
Once the menu mode has been accessed, the user can use the large ‘Menu Map’ (see Section 10.0) to
navigate through the menu structure.
All programming is done using the three front panel keys, A, B and C.
ESCAPE (A & B), ENTER (B & C) and CLEAR (A & C) are obtained by simultaneously pressing the two keys.
CYCLE (A), SHIFT (B) and INC (C) keys are pressed singularly.
7.2 COMMUNICATIONS OPTION
RESISTOR CURRENT RANGE OUTPUT
1 K
Ω(0 to 10) mA (0 to 10) V
500 Ω(0 to 20) mA (0 to 10) V
250 Ω(4 to 20) mA (1 to 5) V
8.0 INSTRUMENT CONFIGURATION
8.1 KEY PRESS DEFINITIONS
CYCLE
SHIFT
INC
ESCAPE
ENTER
CLEAR
B
C
AB
BC
AC
A
CONNECTIONS
Input
Comms + Digitals
5 way tension clamp connector (2 part)
8 way RJ45 (Supplied with matching plug and 1 m cable)
Communications option fitted

The diagram below describes how to move around the menu structure and enter data. More specifically it
details:
1. How to enter a real number
2. How to choose an option from a list
3. How to enter and navigate around a submenu
Using these three procedures the user can enter all applicable data to configure the unit to suit the application.
The options displayed depends on whether the short menu or full menu option is enabled (This can be
selected in the SYStEn submenu).
This menu configures the unit to suit the application. The menu covered in this section is the menu structure
for all applications.
The ‘Menu’ mode is protected by a passcode and the user is asked for this when the ‘Menu’ mode is
accessed from the run mode. The passcode is set to the default of 0 and can be changed to any value
between 0 and 65535, setting the value to zero (default) removes the passcode prompt and the passcode
function is disabled.
If enabled this
gives access to
the relevant
alarm setpoints
To revert to ‘Run’
mode, press these
keys up to 4 times
Show electrical
value e.g.
(4 to 20) mA input
Shows secondary
value i.e.
total or rate
If enabled this will
clear total, and/or
latched alarms
Perform clear
function
Show upper 6
digits of Total
RUN MODE
(RATE OR TOTAL DISPLAYED)
Edit setpoints
menu shortcut
Followed by
Enter menu mode
8.2 RUN MODE OPTIONS
9.0 MENU MODE
9.1 GENERAL MENU NAVIGATION
Cycle around menu items
IIttEEnn11
Description
IIttEEnn22
Description
IIttEEnn33
Description
1. Entering
a number
2. Choosing
from
option list
3. Entering
a submenu
Enter Value 112233445566
ooPPttAAooPPttBB
Description A Description B
IIttEEnn33AA
Description 3a
IIttEEnn33BB
Description 3b
Shift into
editable values
Shift into
editable values
Shift into
editable values
Escape to reject
change
Cycle around menu
items
Shift into
editable values
Escape to reject
change
Escape to reject
change
Inc to increment
digit
Inc to increment
choice
Enter to
accept change
OR
Enter to
accept change
OR
Page 12Page 11

Holding down the Cycle key whilst applying power to the unit will cause all settings to revert to factory
default.
USE THIS FUNCTION WITH CAUTION as there is no way of reversing it.
NOTE that this function will also clear any TFML module loaded.
The input submenu is where the input to the unit is
selected and configured.
Output configures the outputs of the unit. The format of
the output submenu varies according to the Output Pod
fitted. The two possible output types are:
1. Current transmission
2. Twin Relay
This submenu configures the units characteristics e.g.
communications and passcode.
If a TFML is loaded, this submenu gives access to the 8
TFML configuration registers.
tFnL
SyStEn
OUt 2
OUt 1
InPUt
FROM
RUN MODE
10.0 MENU MAP
11.0 RESETTING THE DEVICE
12.0 INPUT MENU STRUCTURE
Page 13 Page 14
tYPE
Input type
uOLt
Voltage
rtd
RTD
tc
Thermocouple
CUrEnt
Current
rAnge
Range
10
± 10 V
1
± 1 V
5
± 5 V
1.5
(±1 to 5) V
4-220
(4 to 20) mA
20
(0 to 20) mA
10
(0 to 10) mA
0.1
± 100 mV Displayed if VOLTAGE input is selected
Displayed if CURRENT input is selected
Lin
Linearisation type
nOnE
None Linear
S9rOOt
Square root
rOOt32
Power 3/2
rOOt52
Power 5/2
USEr
User defined
Pt100
Pt100 European
Ni 120
Ni120
CA
K
Current/Voltage
JISC
Pt100 USA/Japanese
USEr
User defined RTD
J
J
t
T
r
R
S
S
E
E
L
L
n
N
b
B
USEr
User defined Thermocouple
SE9ntS
Segments
EntEr
Enter
Enter Value
Enter value
Enter value
etc. etc.
In 1
Electrical co-ordinate 1
OUt 1
PV co-ordinate 1
Stndrd
Standard manual scaling applies
Auto
Auto scaling applies
En9 LO
Engineering low Enter value
En9 HI
Engineering high Enter value
APPLy
Apply auto scale Enter value
Enter value
Enter value
Enter value
bUrn
Burnout
Hi
High
FILtEr
Filter Enter value
APL Lo
Apply electrical input low
HI UAL
ScALE
Scaling method
Lo UAL
lo
Low
USEr L
User linearisation
InPUt
units
Temperature unit
deg c
Degrees C
deg f
Degrees F
88888.8
1 DP
...Etc... 8.88888
5 DP
APL HI
Apply electrical input high
dec pl
Decimal places

TYPE
This allows the type of input on the unit to be selected. The DM3600 accepts a Voltage, RTD, Thermocouple
or Current Input.
RANGE
Depending on the input type selected the DM3600 will either show the voltage ranges or current ranges
available. Select the range which is applicable to the input device.
LINEARISATION TYPE
The input type selected will determine the linearisation options available. Current/Voltage, RTD or
Thermocouple.
USER LINEARISATION
When the user selects user linearisation, up to 60 co-ordinate pairs of interpolation data can be entered
via the front panel keys. The ‘SE9ntS’ value defines the number of segments.
= Number of interpolated segments = Number of co-ordinate pairs -1
= Electrical input co-ordinate 1
= Process variable (PV) co-ordinate 1
= Electrical input co-ordinate 2
= PV co-ordinate 2
etc......
For n segments there are n + 1 co-ordinate pairs.
If the electrical input goes below electrical input co-ordinate 1, or above electrical input co-ordinate
(n+1), the input is flagged as being under or over-range, respectively.
TEMPERATURE UNITS
This is only available if a Thermocouple or RTD input is selected.
DECIMAL PLACES
The number of decimal places shown on the display can be selected using this option.
INPUT SCALING FUNCTIONALLY
The primary function of a DM3600 is to take an electrical input, and convert it to a displayable Process
Variable (PV, also referred to as an engineering value, e.g. temperature or flow). The DM3600 input signal
can be scaled in one of many ways. For ‘rtd’ or ‘tC’ inputs, the user is simply required to choose the
‘tyPE’ and ‘Lin’ (linearity type). For ‘CurEnt’ or ‘uOLt’ input types, the user can choose STndrd or
AUtO scaling (from the ‘ScALE’ sub-menu).
ENGINEERING LOW / HIGH
If ‘Stndrd’ scaling is chosen, the user will encounter ‘En9LO’ and ‘En9HI’ entries, in order to manually
scale the input to the relevant input_lo and input_hi values (see table overleaf for input_lo/hi values). The
PV_lo & PV_hi values shown overleaf equate to the ‘En9LO’ and ‘En9Hi’ entries). Scaling is subsequently
applied according to the graph overleaf. (The straight line illustrated overleaf will change if a non linear
linearity type is selected. If the user requires strict control over out of range limits, user linearisation
should be chosen).
12.1 INPUT MENU BLOCKS
SE9ntS
In1
OUt1
In2
OUt2
APPLY AUTO SCALE
If ‘AUtO’ scaling is selected, the ‘APPLy’ submenu appears (in place of ‘En9LO’ and ‘En9HI’ entries). The
‘APPLy’ submenu procedure must be carried out as follows.
1. Shift into ‘APPLy’ submenu.
2. Edit & Enter the ‘LOuAL’ engineering value required for low scaling (This will equate to PV_lo).
3. The display will flash ‘APLLO’ to prompt the user to apply the electrical signal corresponding to PV_lo.
If the electrical signal goes out of range, the display signifies this, and the input signal won't be accepted
by the DM3600. This applied electrical signal equates to input_lo, in the graph and table below.
4. Repeat Steps 2 & 3 for ‘HIuAL’, and the corresponding high electrical/engineering values.
OUT OF RANGE ALARM
When an input goes out of range, the following occurs:
If fitted, any relays go into alarm state
If fitted, the re-transmission current derived from the out of range alarm input goes to 3.8 mA or
21.12 mA, depending on whether the burnout setting is set to low or high, respectively.
Once scaling is complete, and the menu structure is exited, if the electrical input is under/over range,
the display shows or
Electrical under
range
limit_lo input_lo input_hi
1.25 % of
(input_hi-input_lo)
7% of
(input_hi-input_lo)
Electrical input
(mV, V, mA)
PV_lo
PV_hi
PV (e.g. level)
Electrical over
range
INPUT TYPE RANGE limit_lo input_lo input_hi
VOLTAGE ± 100 mV -100 mV 0 mV 100 mV
± 10V -10 V 0 V 10 V
± 1V -1 V 0 V 1 V
± 5V -5 V 0 V 5 V
(1 to 5) V 1 V 1 V 5 V
CURRENT (4 to 20) mA 4 mA 4 mA 20 mA
± 20 mA -20 mA 0 mA 20 mA
± 10 mA -10 mA 0 mA 10 mA
Page 15 Page 16

FILTER
The user can choose one of three filter types by editing this configuration;
1. Entering a value of > 0.3. A fixed first order recursive filter is applied to the input processing, with a
time constant (TC) equating to the actual value entered, in seconds.
2. Entering a value = 0.0. An adaptive first order recursive filter is applied to the input processing, with
the time constant adapting to the dynamic behaviour of the input signal.
3. Entering a value x, where 0 < x < 0.3. No filter is applied to the input processing.
BURNOUT
This defines whether, in the event of a sensor failure (burnout), the output current goes high (21.5 mA) or
low (3.6 mA). This is only available if the thermocouple or RTD input type is chosen.
13.0 OUTPUT MENU STRUCTURE
Page 17 Page 18
DELAyA
Alarm delay
dEUA
Deviation
Enter value
Enter value
Enter value in seconds
Enter value
HI
High
dEUIAt
Deviation
tESt
Test
dISAbL
Disable
nonInU
Non inverting
InUErt
Inverting
RELAY OUTPUT MENU
OUt 1
Output 1
OUt 2
Output 2 off
Off
lo
Low
enable
Enable
SEtPA
Setpoint
RE-TRANSMISSION (mA)
OUTPUT MENU
rEtrAn
mA Output scaled to re-transmit
output source
PrESEt
mA output fixed to
LEVEL value
4-220
(4 to 20) mA
0-220
(0 to 20) mA
0-110
(0 to 10) mA
Enter value
(in engineering units)
Enter value
(in engineering units)
Only available if PrESEt
option is chosen Enter value mA
OUt 1
Output 1
OUt 2
Output 2
ACtn A
Alarm action
LAtChA
Latch
InUrtA
Relay sense
hySt A
Hysteresis
tyPE
Retran (mA) output type
SPAn
Output span
rEt LO
Re-transmission scale low
rEt Hi
Re-transmission scale high
LEuEL
Preset mA output level

RELAY SENSE
The ‘Inurt’ setting refers to the relay sense during powered operation. All other relay output menu settings
refer to the alarm state. When in alarm, the relevant front panel LED is lit.
DEVIATION
If the ‘dEu’ action is chosen in the alarm action option, this value determines the amount by which the
PV may change before the alarm is triggered. The value should be in the engineering units.
This menu is only displayed if a current re-transmission output pod is fitted. If ‘PrESEt’ is chosen, the output
current can be edited in ‘LEuEL’. Otherwise, the re-transmitted current is derived linearly from the
process variable, using ‘rEtLO’ and ‘rEtHI’.
RE-TRANSMISSION OUTPUT TYPE
The re-transmission can be set to represent rate or total.
OUTPUT SPAN
(4 to 20) mA, (0 to 20) mA or (0 to 10) mA can be selected as the span of the re-transmission.
RE-TRANSMISSION SCALE LOW / HIGH
By entering these values, the user can scale the mA output (selected in SPAn) to the PV. Default values
will be equal to the engineering low and engineering high values entered in the input menu.
PRESET mA OUTPUT LEVEL
This is only available if ‘PrESEt’ output is chosen.
The relay menu shown is for alarm A. There are two alarms A and B so the menu will be duplicated for
alarm B. The relay menu will only be displayed if a twin relay pod is fitted to the DM3600.
SETPOINT A
The setpoint value defines the engineering value associated with an alarm. For example if an alarm is
required when the flow exceeds 10 000 kg/h, the setpoint will be set to 10 000.
ALARM ACTION
This defines the behaviour of the alarm when the setpoint is reached.
HYSTERISIS
The hysterisis value is the difference between the points at which the alarm triggers and releases,
expressed in the relevant engineering units.
ALARM DELAY
The alarm will not trigger until the PV has been in the alarm region for more than the specified number
of seconds.
LATCH
When latch is enabled, an alarm will remain triggered until it is manually cleared.
13.1 OUTPUT MENU FUNCTION BLOCKS
13.2 RELAY OUTPUT MENU
ALARM ACTION ALARM BEHAVIOUR
OFF (Off) The alarm is always off
LO (Low) The alarm triggers when PV < setpoint, i.e. low alarm
HI (High) The alarm triggers when PV > setpoint, i.e. high alarm
dEu (Deviation) The alarm triggers when PV moves out of a deviation band e.g. if the flow drops below
or above the set point by 10 L/m.
tESt (Test) Alarm is on
Not Triggered
Hysteresis
Hysteresis
Setpoint
PV
Alarm Function
Triggered
High Alarm Low
Alarm
Setpoint
Deviation
Deviation
Deviation
Alarm
Alarm
Function Not Triggered
Triggered
Hysteresis
Hysteresis
POWER ALARM STATUS Inurt SETTING RELAY POSITION (A) RELAY POSITION (B)
OFF X X 3 and 5 3 and 2
ON Not in Alarm nOnInu 3 and 4 3 and 1
ON In Alarm nOnInu 3 and 5 3 and 2
ON Not in Alarm InuErt 3 and 5 3 and 2
ON In Alarm InuErt 3 and 4 3 and 1
13.3 RE-TRANSMISSION (mA) OUTPUT MENU
Page 20Page 19

The system menu allows the communications to and from the device to be configured and also allows
various functions to be enabled from the run mode. The passcode can also be changed from within this
menu. (See menu below).
14.0 SYSTEM MENU
MODBUS DEVICE ADDRESS
This sets the address for the RS485 communications. The default is 1 and the maximum is 247.
NUMBER OF WIRES
This defines the type of RS485 communication mode. It can either be 4 (full duplex) or 2 (half duplex).
BAUD RATE
This defines the comms baud rate i.e. the speed of communication between the unit and interrogating
device. The Baud rate is displayed in bps.
MENU TYPE
When ‘SHort’ type is chosen, access to the greyed out menu items is restricted. To allow access to these
items the ‘FULL’ menu type should be chosen.
START UP DELAY TIME
The outputs of the unit will not operate until the start up delay time (measured in seconds) has expired.
The minimum delay is 5 s and the maximum 3 600 s.
DISCRETE ACTIVE LEVEL SELECT
The function of the discrete input ‘dISc’ is to operate as a remote clear button press, i.e. you can use this
to reset the totals remotely. This menu item selects whether the clear function is executed when the
discrete is high (24 V) ‘ACtHI’ or low (0 V) ‘ACtLO’.
MENU ACCESS PASSCODE
When accessing the menus from ‘Run’ mode, the user is prompted for this passcode. If it is zero (default),
then there is no prompt and the password function is disabled. If the password is forgotten please contact
your supplier.
USER OFFSET
This value is used to offset the scaled process variable by a fixed amount.
MENU TIME OUT
This sets the amount of time after which the display will revert to the ’Run’ mode if no key is pressed.
ENABLE
Enables the following sub-menu:
CLEAR LATCH
When set to ‘On’ latched alarms can be cleared by pressing the clear button on the front panel, or
applying discrete input 1.
CLEAR TOTAL
When set to ‘On’, the total is reset by pressing the clear button on the front panel.
EDIT SETPOINTS
When set to ‘On’ the edit setpoints submenu can be accessed directly from the ‘Run’ mode.
14.1 SYSTEM MENU FUNCTION BLOCKS
Page 21 Page 22
LinES
Number of wires
SyStEn
System
Enter value
(0 to 247) default 1
4
4 wire RS485
2
2 wire RS485
bAUd
BAUD rate 19 200 9600
1200
tyPE
Menu type
SHort
Short menu
FULL
Full menu
StArt
Start up delay time Enter value in seconds
ACt HI
Active high
ACt LO
Active low
PASS
Menu access passcode
Enter value
0 to 65535 default:0
OFFSEt
User offset Enter offset
tOut
Menu time out
60 SEC
60 seconds
EnAbLE
Enable submenu
OFf ON
OFF ON
OFF ON
1hour
1 hour
CL LAt
Clear latch
CL tot
Clear total
EditSP
Edit setpoints
diSC
Discrete activity level select
AddrES
Address

15.0 FAULT FINDING
Smart In Head Temperature Transmitters
DIN Rail Mounted Temperature Transmitters
Panel & Field Temperature Indicators
Temperature Probes
Trip Amplifiers
Signal Conditioners
And many other products
For further information on all products:
Status Instruments Ltd, Status Business Park, Tewkesbury, Glos. GL20 8FD
Tel: +44 (0)1684 296818 Fax: +44 (0)1684 293746
ALSO AVAILABLE:
Page 23 Page 24
SYMPTOM
DISPLAY IS BLANK
DISPLAY SHOWS
DISPLAY SHOWS
‘DP Err’ IS DISPLAYED
‘OP CAL’ IS DISPLAYED
‘IP CAL’ IS DISPLAYED
POSSIBLE CAUSE
No power
Input is out of range
(above maximum)
Input is out of range
(below minimum)
The displayed value (excluding
total) is greater than 6 digits
(i.e. 999999)
The output pod has been corrupted
The input calibrated data has been
corrupted
ACTION
Check power supply connections
Check that the engineering high value is
correct
Check that the engineering low value is
correct
This can occur if the PV is configured
outside of the displayable range
Re-configure output. If the error is still
present replace the output pod
Re-input calibration data. If the error is
still present replace the unit
Table of contents
Other Status Instruments Measuring Instrument manuals
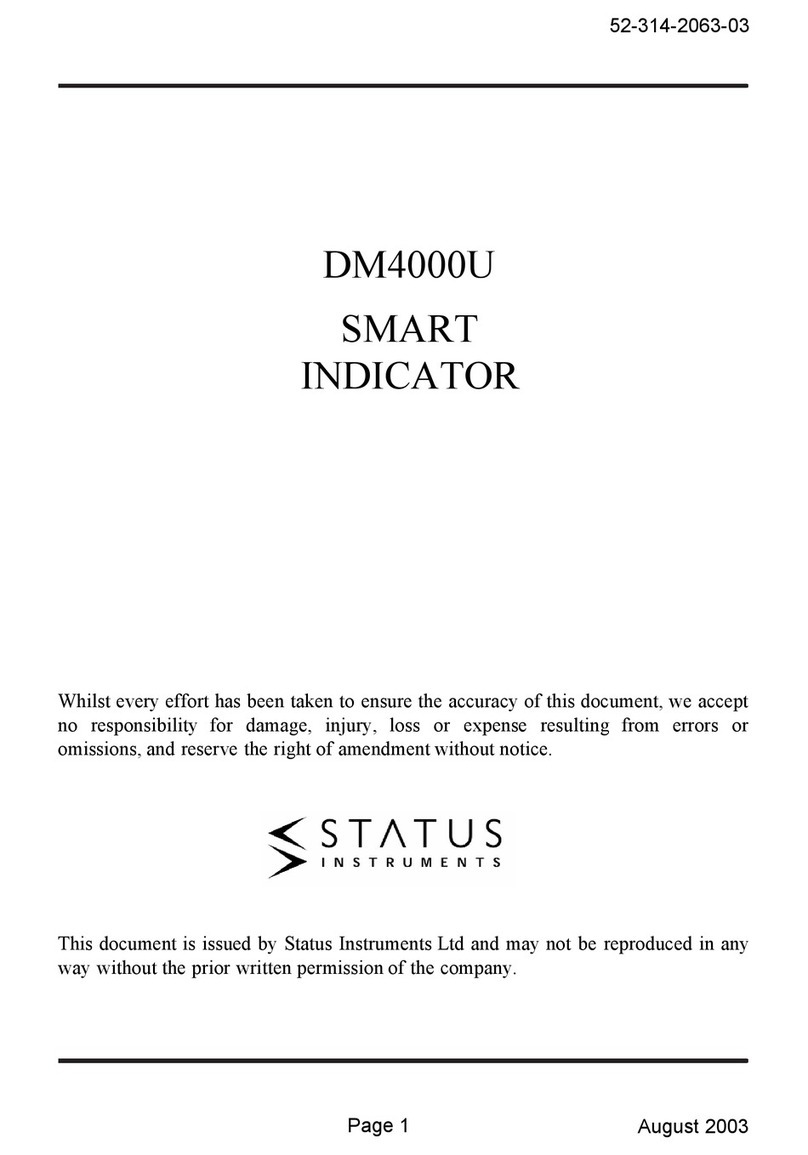
Status Instruments
Status Instruments DM4000U User manual
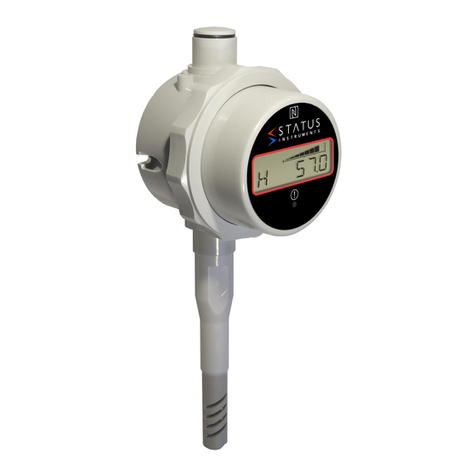
Status Instruments
Status Instruments DM650HM User manual
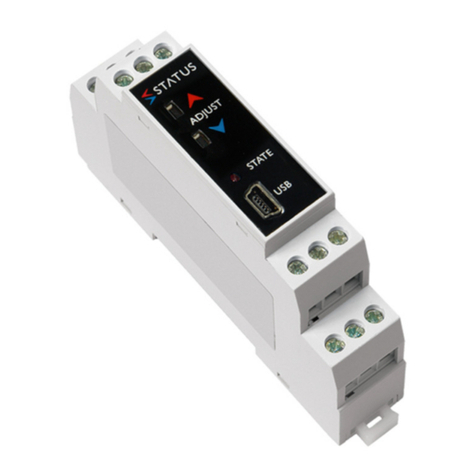
Status Instruments
Status Instruments SEM1620 User manual
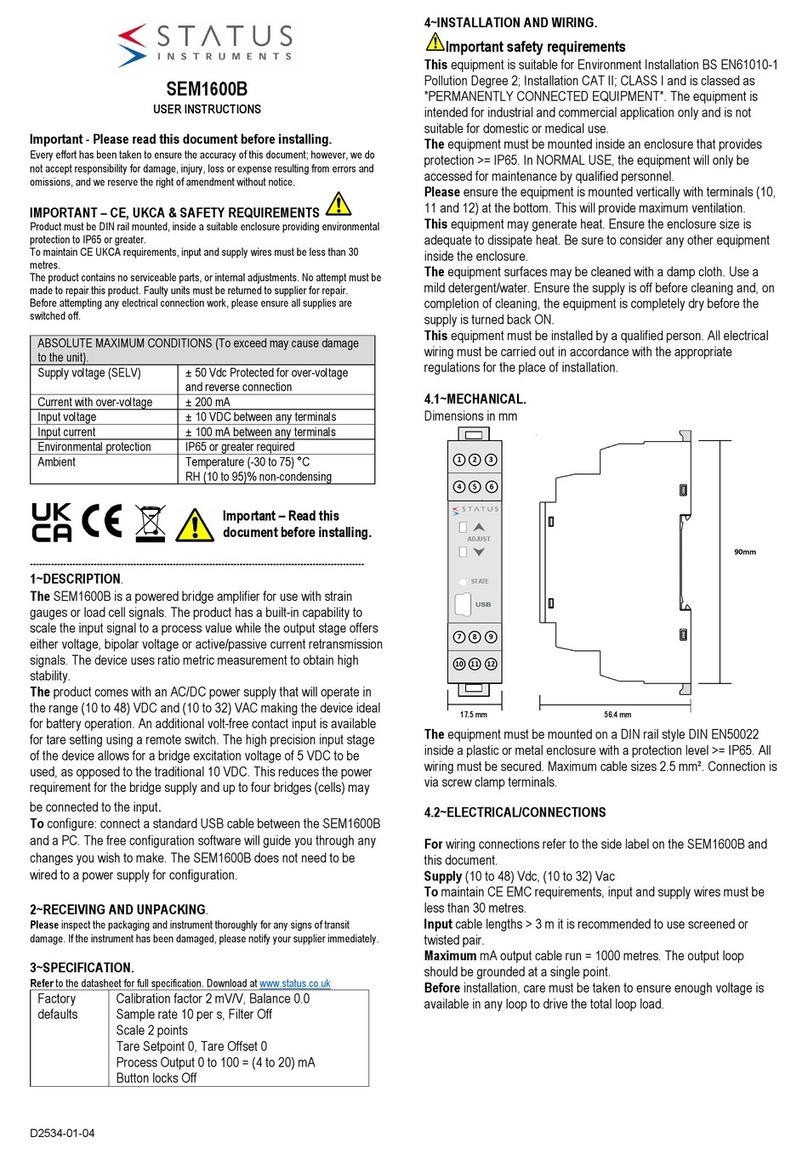
Status Instruments
Status Instruments SEM1600B User manual
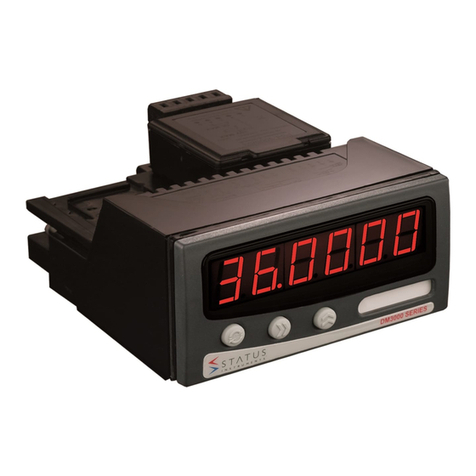
Status Instruments
Status Instruments DM3600A User manual
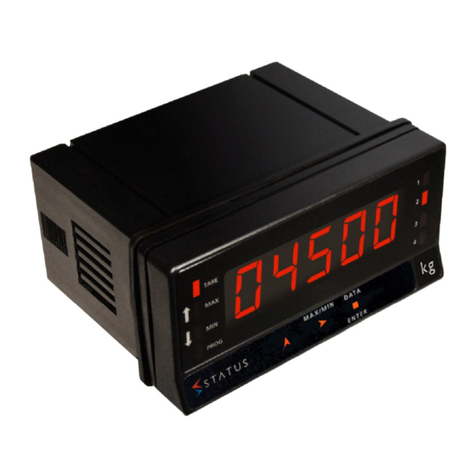
Status Instruments
Status Instruments DM4500U User manual
Popular Measuring Instrument manuals by other brands
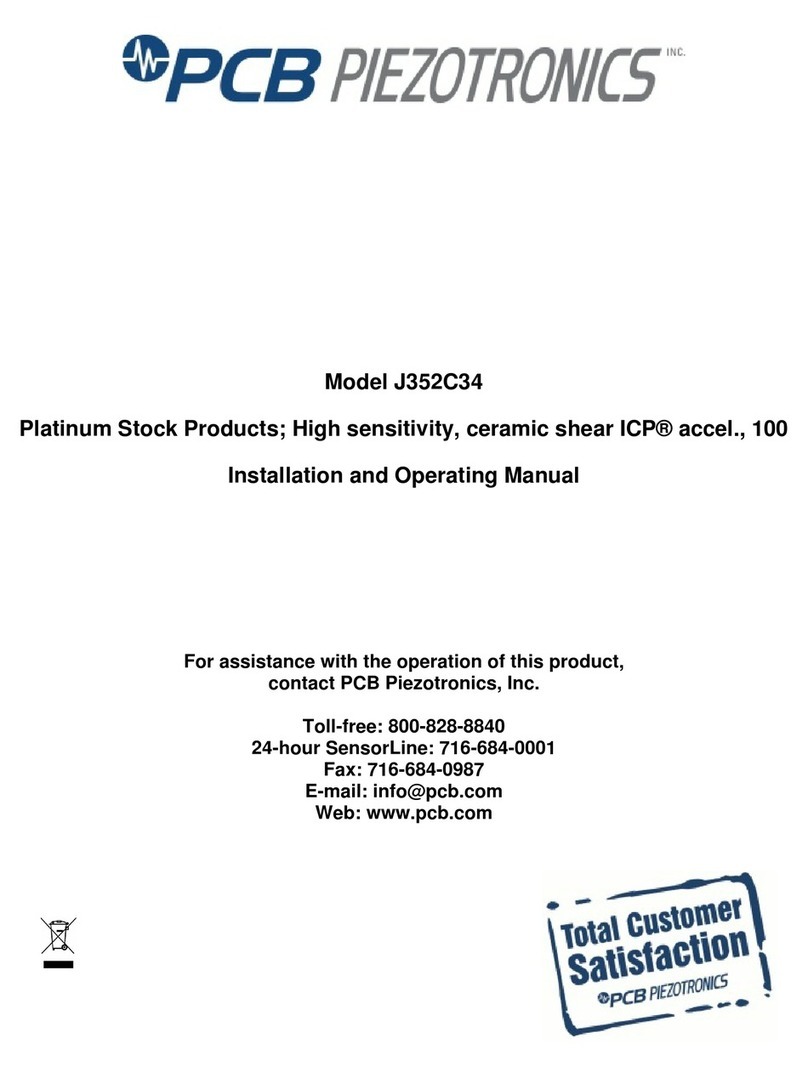
PCB Piezotronics
PCB Piezotronics ICP J352C34 Installation and operating manual
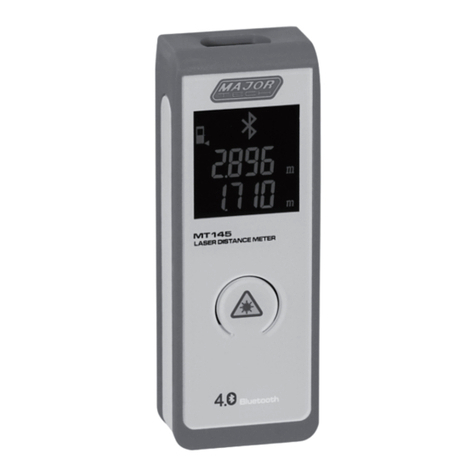
Major tech
Major tech MT145 instruction manual
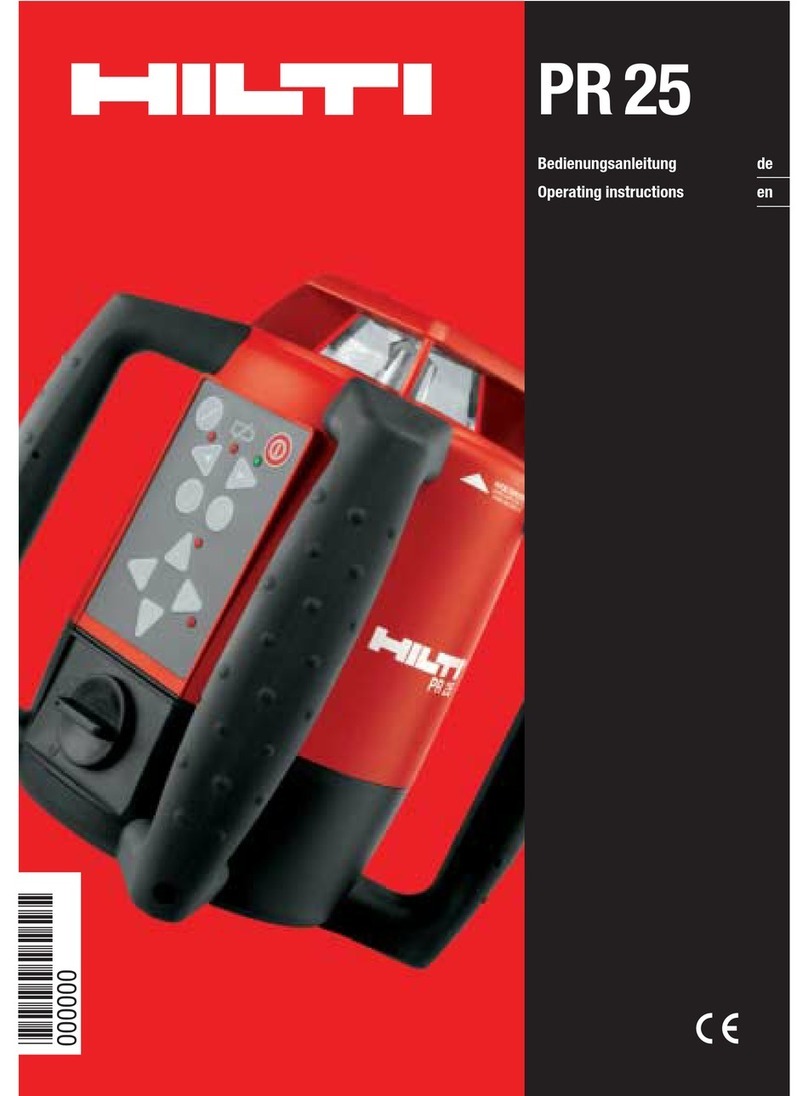
Hilti
Hilti PR 25 operating instructions
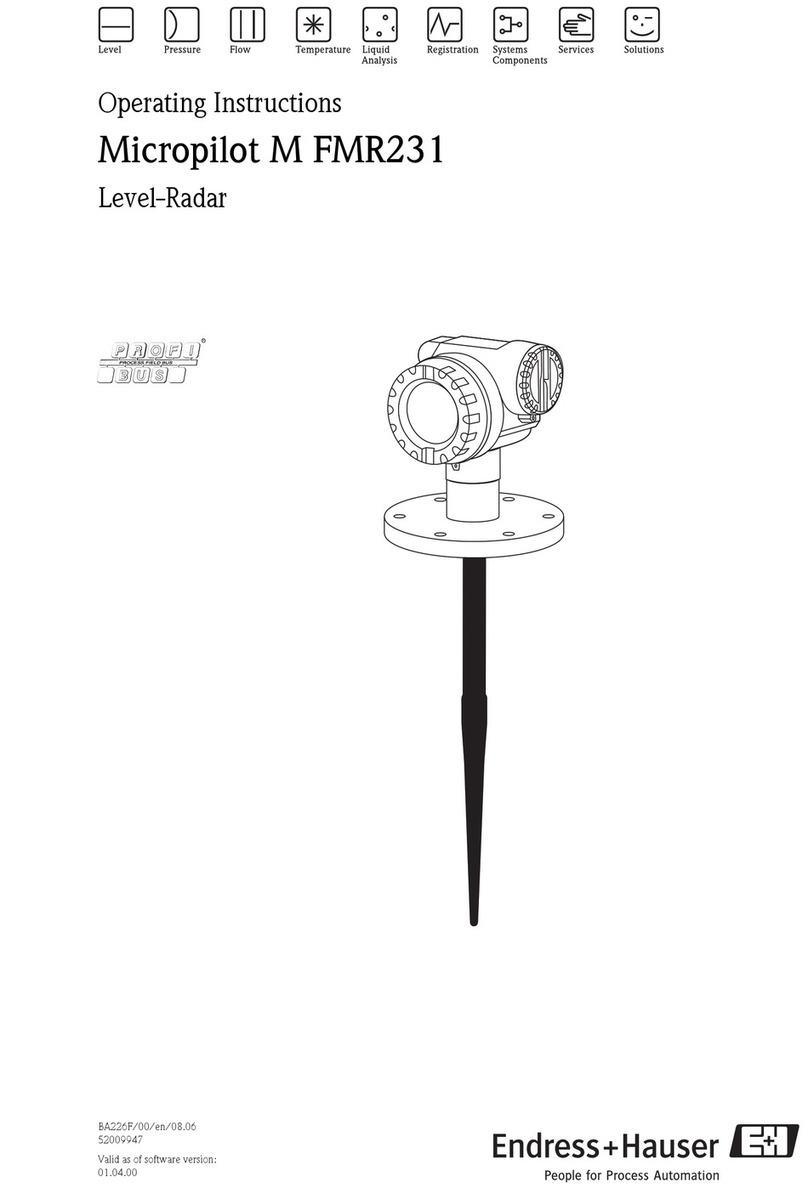
Endress+Hauser
Endress+Hauser Micropilot M FMR231 operating instructions
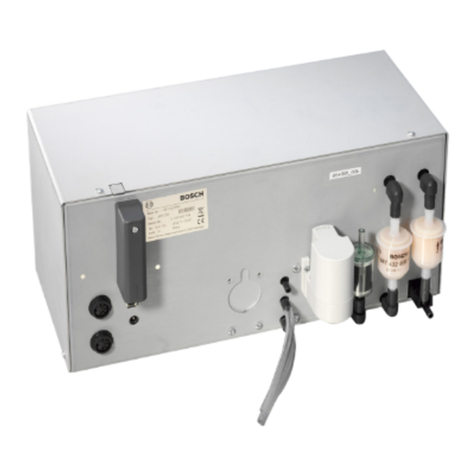
Bosch
Bosch BEA 055 Original instructions
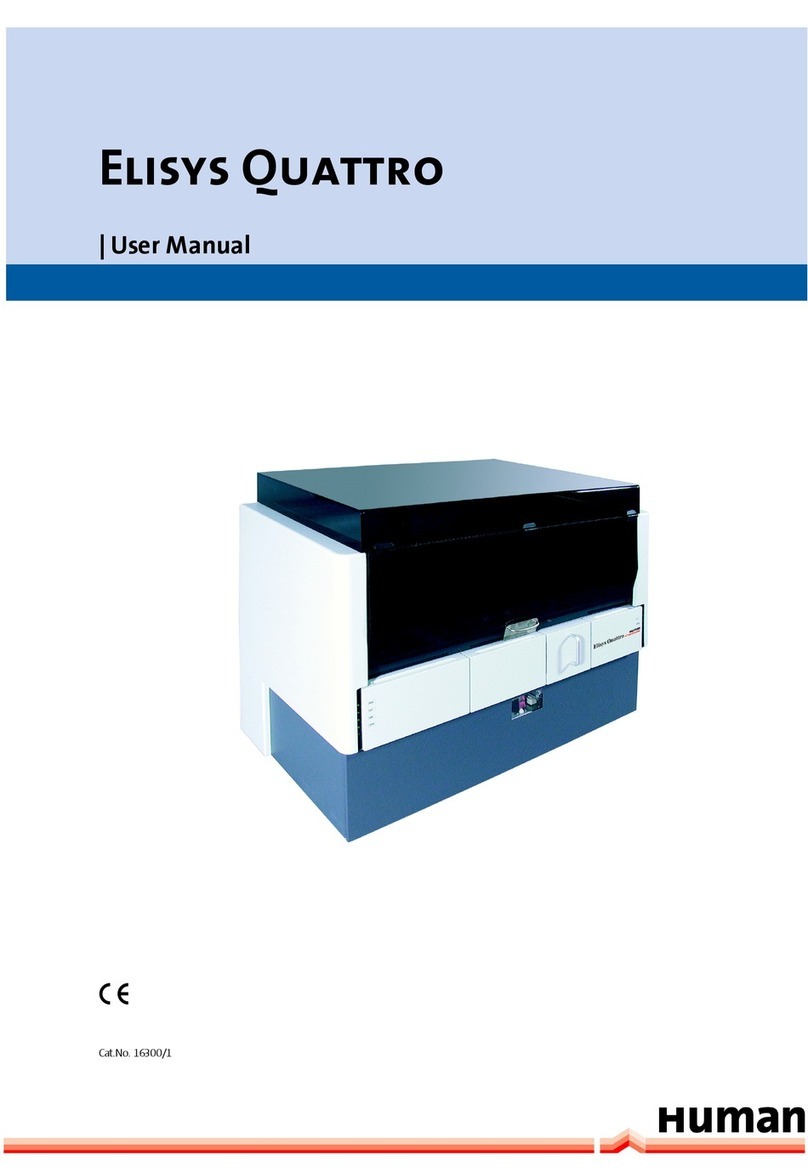
Human
Human Elisys Quattro user manual