StepperOnline BLD-530S User manual

©2023 All Rights Reserved
User Manual
BLD-530S
Brushless DC Motor Driver
Address: 15-4, #799 Hushan Road, Jiangning, Nanjing, China
Tel: 0086-2587156578
Web: www.omc-stepperonline.com
Sales: [email protected]
Support: [email protected]
Read the operating instructions carefully before putting the driver into operation with power

BLD-530S BLDC
B
r
u
s
h
l
e
ss
Dr
i
v
e
r
1
Introduction
BLD-530S brushless motor driver is a small power driver independently developed by STEPPERONLINE to archive the modern
industrial automatic control. It mainly uses high-performance dedicated brushless DC motor driver chips, which have a series
of advantages such as high integration, small size, comprehensive protection, simple and clear wiring, and high reliability. The
driver is suitable for driving medium and small brushless DC motors with a rated power of 600W or below. It uses a new type
of PWM technology, which enables the brushless motor to run at high speed, with low vibration, low noise, good stability, and
high reliability.
1. Specifications
1.1 Electric Specification
Parameters
BLD-530S
Min
Typical
Max
Unit
Input voltage
24
36
48
VDC
Continuous Output Current
11
14
20
A
Max. Output Power
-
-
500
W
Peak Output Current
-
-
30
A
1.2 Environment
Cooling
Radiator
Control Signal I/O
Full Isolation
Working Temperature
0~+45°C
Storage Temperature
-20~+85°C
Working & Storage Humidity
<85% (No Frosting)
Protection Functions
Over-current, overheat, over-speed, over-voltage,
under-voltage, power supply abnormality control
1.3 Safety Precautions
*Do not measuring or touch any components without housing while operating
* Board inspection or fuse replacement can only be carried out after 1 minute of power off
* Operating without housing is forbidden
* Make sure to connect the ground well, otherwise the brushless motor will working unsteadily
* Should the driver be accidentally damaged during operation, our company is only responsible for the repair and
replacement of the driver within the warranty scope. Our company does not assume any liability for compensation for motor
damage, personal injury, property damage, or any other losses caused by the accidental failure of the driver

BLD-530S BLDC
B
r
u
s
h
l
e
ss
Dr
i
v
e
r
2
1.4 Mechanical Specification
(Unit: mm [1inch=25.4mm])
2. Terminal and Signal
2.1 Control Interface
No.
Terminal Name
Description
8
COM
COM terminal
7
F/R
CW/CCW terminal
6
EN
Stop/Start terminal
5
BK
Brake terminal
4
SV
Analogy signal input terminal
3
PG
Speed output terminal
2
ALARM
Alarm output terminal
1
+5V
+5V power output terminal
2.2 Hall Signal Terminal
No.
Name
Description
1
GND
Hall sensor Negative
2
HA
Hall sensor A phase
3
HB
Hall sensor B phase
4
HC
Hall sensor C phase
5
+5V
Hall sensor Positive

BLD-530S BLDC
B
r
u
s
h
l
e
ss
Dr
i
v
e
r
3
2.3 Motor Connection Terminal
No.
Name
Description
1
DC+
DC+
2
DC-
DC-
3
FG
For the Ground
4
U
BLDC winding U phase(A)
5
V
BLDC winding U phase(B)
6
W
BLDC winding U phase(C)
3. Function and Usage
3.1 Speed Control Modes
This driver offers two speed control modes that the user can choose from:
Internal Potentiometer Speed Control: Counterclockwise rotation of the potentiometer on the driver panel decreases the
motor speed, while clockwise rotation increases the speed. When using external input speed control, the potentiometer must
be set to the minimum position.
External input speed control can be achieved by connecting the two fixed ends of an external potentiometer (5K100K) to the
C0M and +5v terminals of the driver, and connecting the adjustable end to the SV terminal. Alternatively, analog voltage
can be input to the SV terminal (relative to C0M) through other control units such as PLC or microcontroller to
achieve speed control. The input range for SV is DC OV+5V, corresponding to a motor speed range of 0~rated speed。
Digital signal speed control can also be used by applying a pulse-width modulated (PWM) signal with an amplitude of 5V and
a frequency of 1kHz~2kHz between SV and C0M. The motor speed is linearly adjusted by the duty cycle of the PWM signal.
The R-SV potentiometer can be adjusted to attenuate the SV digital signal amplitude in a 01.0 ratio. Generally, R-SV
is set to 1.0, and no attenuation is applied to the SV input digital signal.
3.2 Motor Operate/Stop Control (EN)
Motor on/off control (EN) can be achieved by controlling the on/off state of the EN terminal relative to C0M. When the
terminal is connected, the motor runs, and when it is disconnected, the motor stops. When using the on/off control
terminal to stop the motor, the motor will naturally come to a stop, which depends on the load inertia.
3.3 Motor Rotation Direction Control (F/R)
Motor forward/reverse control (F/R) can be achieved by controlling the on/off state of the F/R terminal relative to C0M. When
F/R is not connected to C0M, the motor rotates clockwise (facing the motor shaft), otherwise the motor rotates
counterclockwise.
Attention: To avoid damaging the driver when changing the motor direction, the motor should be stopped before
operating the change direction function.
3.4 Brake the Motor to Stop (BREAK)
By controlling the connection and disconnection of terminals BK and C0M, the motor can be controlled to brake and stop.

BLD-530S BLDC
B
r
u
s
h
l
e
ss
Dr
i
v
e
r
4
When terminals BK and C0M are disconnected, the motor runs, and when they are connected, the motor quickly brakes to a
stop. The braking time is dependent on the load inertia of the user system. However, because braking has an impact on both
electrical and mechanical systems, natural stopping should be used unless special stopping requirements are needed.
3.5 Speed Signal Output (PG)
The port is an OC output (30V/10mA max) that outputs a speed pulse. You can connect with a resistance (3K ohm~10K ohm)
between signal and input power to get the pulse signal. The port will output a fixed pulse width (50 us) negative pulse string
that is proportional to the frequency of the motor's rotation. The number of output pulses per revolution of the motor is 3 x
N, where N is the number of poles of the motor. For example, a four-pole motor with two pairs of poles
will output six pulses per revolution. When the motor speed is 500 rpm, the output pulse of the PG terminal is 3000.。
3.6 Alarm Output (ALM)
The driver alarm output is an OC output (30V/10mA max). You can connect a resistance (3K ohm ~10K ohm) with the input
power to get the alarm signal. When the alarm is triggered, the port is connected to C0M (low level), and the driver stops
working and enters an alarm state.
3.7 Driver Failure
When over-voltage or over-current occurs inside the driver, the driver will enter protection mode, automatically stop working,
and the motor will stop. The digital display on the driver will show Err-×. To clear the alarm, the enable terminal (EN) needs to
be reset (i.e., disconnected from C0M) or power needs to be disconnected. If this fault occurs, please check the motor wiring.
3.8 Sensorless control mode
STEPPERONLINE drivers can be used for sensorless brushless motors.
But it should be noted that since our brushless driver is mainly used for our brushless motor with sensors, its built-in program
is also used for motors with sensors.
Although our brushless driver can be used for sensorless brushless motors, the program of the driver is not fully compatible
and can only be used in simple scenarios. Our brushless drives are not recommended if the motor needs to be started and
stopped frequently.
When using a brushless driver to drive a sensorless motor, it is necessary to use software to set the sensorless starting torque
according to the parameters of the motor.

BLD-530S BLDC
B
r
u
s
h
l
e
ss
Dr
i
v
e
r
5
4. Display and Keyboard Operation
Remark: "SET": Start/stop, (backspace)
"△": "+", Plus 1
"▽": "+", Minus 1
"ENT": "ENTER" (call out setting parameter)
4.1 System Parameter Setting
Please ensure that the motor is under the stop situation when setting the parameter. That is, in the case of panel mode, the
motor is in the stop state or an external port mode, the motor is enabled to disconnect.
4.1.1 In standby mode, press the "ENTER" key to call up the system parameters, and then press ENTER again to call up the
setting value of the system parameters.
4.1.2 Use the "△" or "▽" keys to navigate to the parameter you want to modify. If you do not want to modify it, press the
"SET" key to exit the setting and return to standby mode.
4.1.3 Press "ENTER" to see the parameter content. If you do not want to modify it, press the "SET" key to exit the setting and
return to standby mode.
4.1.4 Use the "△" or "▽" keys to adjust the parameter value you want to modify.
4.1.5 Press the "ENTER" key to store the parameters and press the SET key to return to standby mode.
Note: In the setting state, if no key is pressed for one minute, it will automatically jump to the speed display interface.
4.2 Working Mode
There are two working modes for the driver, which can be set through the panel. One is the panel working mode, and the
other is the external port working mode. The motor operates according to the set mode, and the digital display shows the
motor's rotational speed. In panel working mode, press the SET key to start or stop the motor. Press and hold the △and
▽keys to increase or decrease the motor speed, and press the ENTER key to confirm the motor speed. The motor runs at
the set speed.

BLD-530S BLDC
B
r
u
s
h
l
e
ss
Dr
i
v
e
r
6
4.3 Protect Mode
While Motor operates abnormally, display will show Err×:
Err-01
Stall
Err-02
Over Current
Err-04
Hall Fault
Err-05
Stall and Hall Fault
Err-08
Under-Voltage
Err-10
Over-Voltage
Err-20
Peak Current Alarm
Err-40
Temperature Alarm
4.4 Drives Parameter Setting
P00X:Operating Parameter
Code
Name
Setting Range
Unit
Default Value
Change
P000
Control Mode
00 External port mode
18 Panel control mode
485 communication control mode
External Port
Control Mode
P001
Pair of Pole
1~255
Pair
2
o
P002
Rated Speed
1~65535 (external port mode effective)
RPM
3000
o
P003
Display mode
00: Speed Display
00
o
01: PWM Speed Adjustment
02: Segmented speed control mode
(when parameter P000 is set to 10)
80: Current Display
P004
No sense Starting
torque
1~255
16
o

BLD-530S BLDC
B
r
u
s
h
l
e
ss
Dr
i
v
e
r
7
P005
Initial Speed w/o
Sensor Start
1~255
04
o
P006
Acceleration Time
1~255
0.1S
0
o
P007
Deceleration
Time
1~255
0.1S
0
o
P008
Current Setting
1~255
44
P009
Temperature
Alarm
1~255
34
P010
Panel Speed
Setting
0~65535
Only external port mode effective
RPM
2000
P011
Brake Force
0~1023
1023
P012
Site Address
0~250
1
P013
Reserved
P014
Current Adjusting
Parameter
0~FF
Hexadec
imal
3A
P015
Reserved
P016
Velocity 1
0~65535
Hexadec
imal
500
P017
Velocity 2
0~65535
Hexadec
imal
1000
P018
Velocity 3
0~65535
Hexadec
imal
2000
P019
Velocity 4
0~65535
Hexadec
imal
3000
P020
Velocity 5
0~65535
Hexadec
imal
4000
P021
Velocity 6
0~65535
Hexadec
imal
5000
P022
Velocity 7
0~65535
Hexadec
imal
6000
P023
Velocity 8
0~65535
Hexadec
imal
7000
P024-
P031
Reserved

BLD-530S BLDC
B
r
u
s
h
l
e
ss
Dr
i
v
e
r
8
4.5 Explanation of Segmented Speed Control
4.5.1 Set the segmented speed control mode: Change the P-000 parameter to 10, change P-003 to 02, and connect EN to
0V.
4.5.2 DBLS-02S segmented speed control gear table: 0 represents 0V, 1 represents 5V, SV is suspended at 0V, and pins 1
and 2 are suspended at 5V.
C0M
SV
1Pin K1
2Pin K2
RPM
0
0
0
0
500
0
0
0
1
1000
0
0
1
0
2000
0
0
1
1
3000
0
1
0
0
4000
0
1
0
1
5000
0
1
1
0
6000
0
1
1
1
7000
5. System Usage
First, connect the motor and driver wires (motor winding wires, Hall signal wires, and power wires) strictly according to the
requirements. Brushless motors cannot achieve forward and reverse rotation by changing the wiring like asynchronous
motors. Incorrect wiring can cause abnormal motor operation or no operation at all. The main manifestations are that the
brushless motor vibrates or heats up quickly (within tens of seconds to two minutes, and the temperature rises to 80
degrees), and it can damage the motor and driver.
After connecting the motor winding wires, Hall wires, and driver power wires, you can try to run it. First, adjust the
potentiometer to the minimum, then press the start switch and slightly increase the motor potentiometer. The motor
should run. If the motor does not run or vibrates, it may be due to the wrong phase sequence of the motor wires. Please
recheck the order of the brushless motor leads until the motor can run normally. Then, stop the motor.
6. Communication Mode
The communication mode adopts the standard Modbus protocol, which complies with the national standard GB/T
19582.1-2008. It uses RS484 dual-line serial communication and the physical interface adopts two 3.81mm spaced 3-core
Phoenix terminals, which is very convenient for serial connection. The transmission mode is RTU, the verification mode is
CRC, and the CRC starting word is FFFFH. The data mode is 8-bit asynchronous serial, 2 stop bits, no parity, and supports
multiple communication speeds (see parameter table for details).
Note: If communication mode is required to control the motor, it must be in internal speed control mode.

BLD-530S BLDC
B
r
u
s
h
l
e
ss
Dr
i
v
e
r
9
6.1 ModBus Communication Control Register Definition
No
Addres
Name
Setting Range
Default
Unit
00
$8000
First byte: control bit state
Second byte: Hall angle and
motor poles
First byte:
Bit0: EN
Bit1: FR
Bit2: BK
Bit3: NW1
Bit4: NW
Bit5: KHX
Bit6: HR60
Bit7: KH Second byte:
Bit0-7: Poles 1-255
00H
02H
01
$8001
Max. Speed in analog adjustment
0-65535
3000
Rpm
02
$8002
First byte: start torque
Second byte: start speed without
sense start
1-255
10H
03
$8003
First byte: accelerate time
Second byte: decelerate time
1-255
0
0.1s
04
$8004
First byte: Max. current
Second byte: temp alarm point
38H
30H
05
$8005
External Speed Setting
0-65535
2000
RPM
06
$8006
Brake Force
0-1023
1023
07
$8007
First Byte: Site address
Second byte: reserved
1-250
1
0
08-0F
$8008-$800F
Segmental speed value
10-17
$8010-$8017
Reserved
18
$8018
Real Speed
19
$8019
First byte: bus voltage
Second byte: bus current
1A
$801A
First byte: Control port state
Second byte: Analog port value
Bit0: SW1
Bit1: SW2
Bit2: SW3
Bit3: SW4
1B
$801B
First byte: Fault State
Second byte: Motor running state
Bit0: Stall
Bit1: Over-current
Bit2: Hall Abnormality
Bit3: Low Bus Voltage
Bit4: High Bus Voltage
Bit5: Peak Current Alarm
Bit6: Temperature Alarm
Bit7: Reserved
1C
$801C-$801F
Reserved
20
$8020 Above Illegal

BLD-530S BLDC
B
r
u
s
h
l
e
ss
Dr
i
v
e
r
10
Site address 8000H-8017H Read-write register
Site address 8018H-801FH Read-only register
Other address is illegal
8000: first byte:
EN: when NW=0, 0: external EN low level effective 1: external EN high level effective
when NW=1, 0: EN ineffective 1: EN effective
FR: when NW=0, 0: External FR low level effective 1: External FR high level effective
when NW=1, 0: FR ineffective 1: FR effective
BK: when NW=0, 0: external BK low level effective 1: external BK high level effective
when NW=1, 0: BK ineffective 1: BK effective
NW1: 0: Control terminal external effective(EN,FR,BK) 1: Internal effective
NW: 0: Speed external effective 1: Speed internal effective (under panel speed
adjusting mode, PWN speed adjusting mode and segmental speed adjusting mode, it must set to1)
KH: 0: Closed loop control 1: Open loop control
KHX: 0: Stall alarm 1: No alarm
Stall alarm under the open loop w/ sense mode.
HR60: 0: 120° hall control 1: 60° hall control (temporarily not supported)
1. Write 1500 Speed:
01 06 80 05 DC 05 28 C8
2. Write 2 pair of poles EN start:
01 06 80 00 19 02 2A 5B
3. Write EN stop:
01 06 80 00 18 02 2B CB
4. Write brake:
01 06 80 00 1D 02 28 9B
5. Checking the fault state:
01 03 80 1b 00 01 DD CD
6. 01 06 80 00 19 02 2A 5B EN start 2 pair of poles
7. 01 06 80 05 D0 07 AC 09 Write 2000
8. 01 06 80 05 E8 03 BE 0A Write 1000
9. 01 06 80 00 18 02 2B CB EN stop
10. 01 06 80 00 19 01 6A 5A 1 pair of poles EN start
The write message is explained as follows:
Message
Explain
01
Address
10
Function code
00 1B
Start address register
00 05
The numbers of register
0A
Total byte digits
02 58
Write the first register data
02 58
Write the second register data

BLD-530S BLDC
B
r
u
s
h
l
e
ss
Dr
i
v
e
r
11
00 F0
Write the third register data
00 03
Write the fourth register data
0D 40
Write the fifth register data
CD 83
CRC testing (from the address to the fifth register data)
The successful feedback message is explained as follows:
Message
01
10
11 1B
00 05
70 0D
Explain
Address
Function Code
The start register
address
The wrote
Register number
CRC testing code
7. Communication Wires Connection
RS-485 communication can be carried out by using the RJ45 cable connector.
The RJ45 connector pins are defined as follows:
Pin
Function
8
COM
6
A
3
B
Table of contents
Other StepperOnline DC Drive manuals
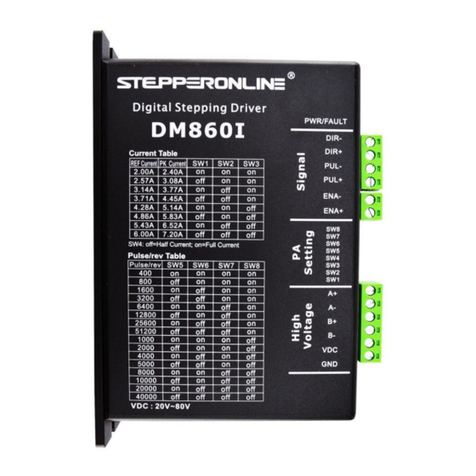
StepperOnline
StepperOnline DM860I User manual
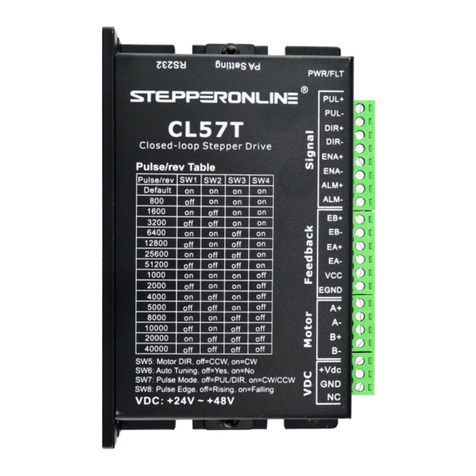
StepperOnline
StepperOnline CL57T User manual
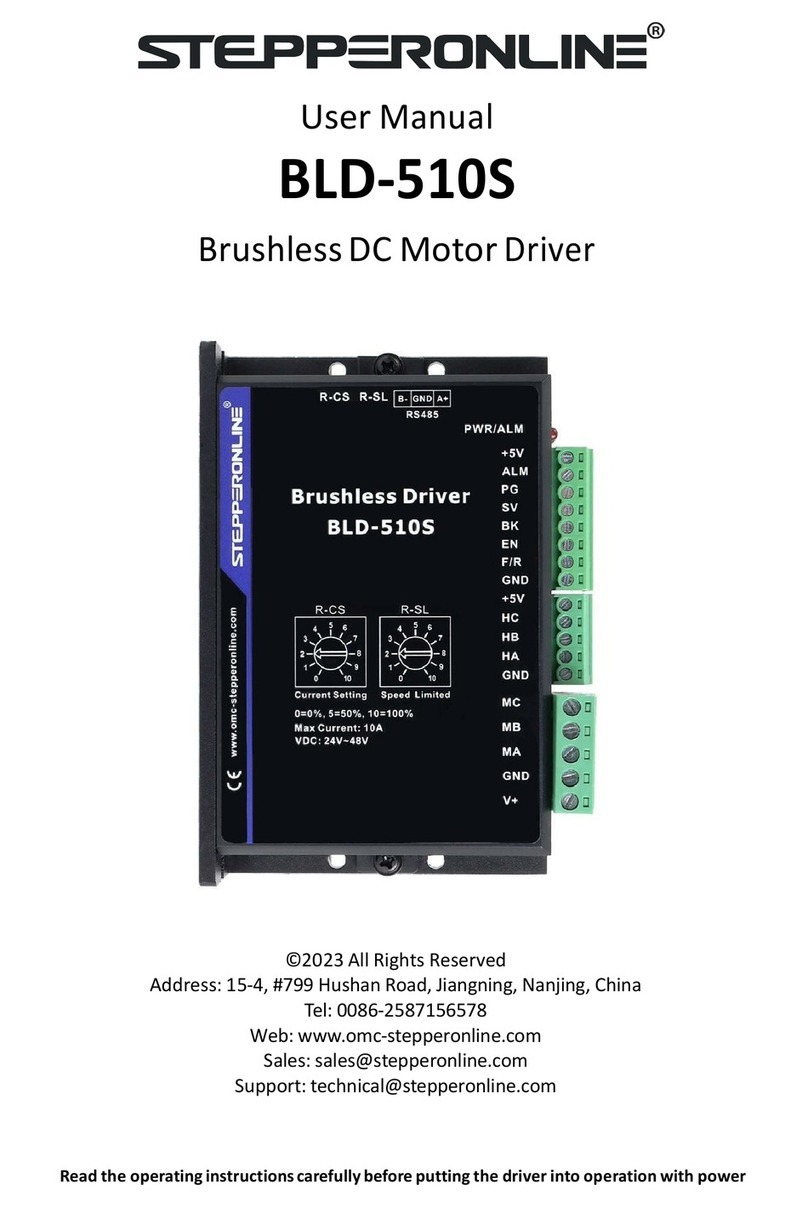
StepperOnline
StepperOnline BLD-510S User manual
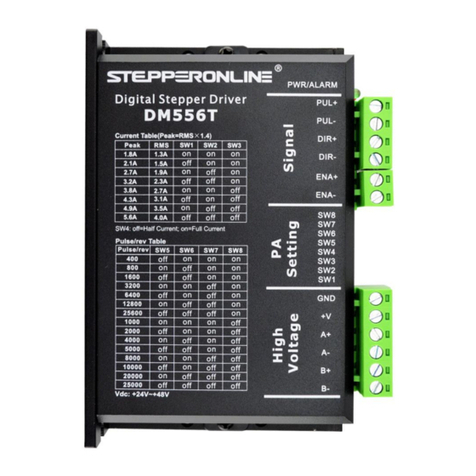
StepperOnline
StepperOnline DM556T User manual
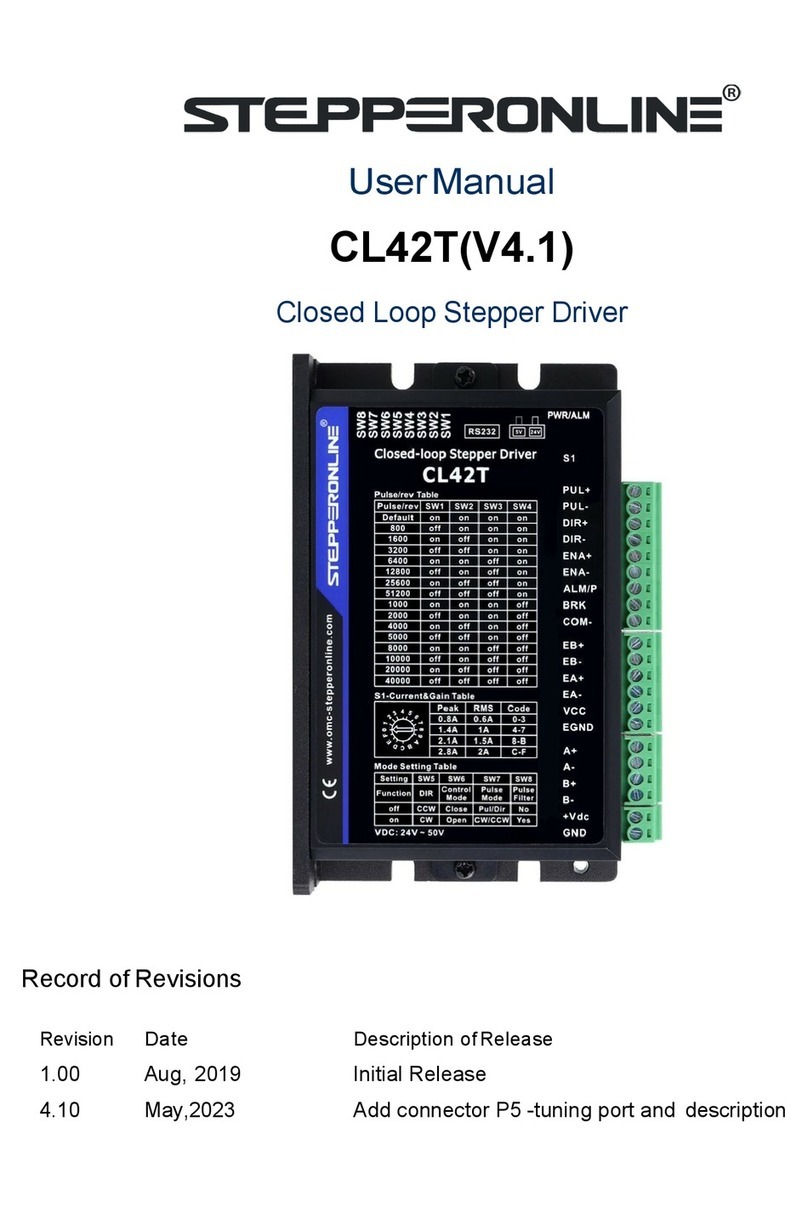
StepperOnline
StepperOnline CL42T User manual
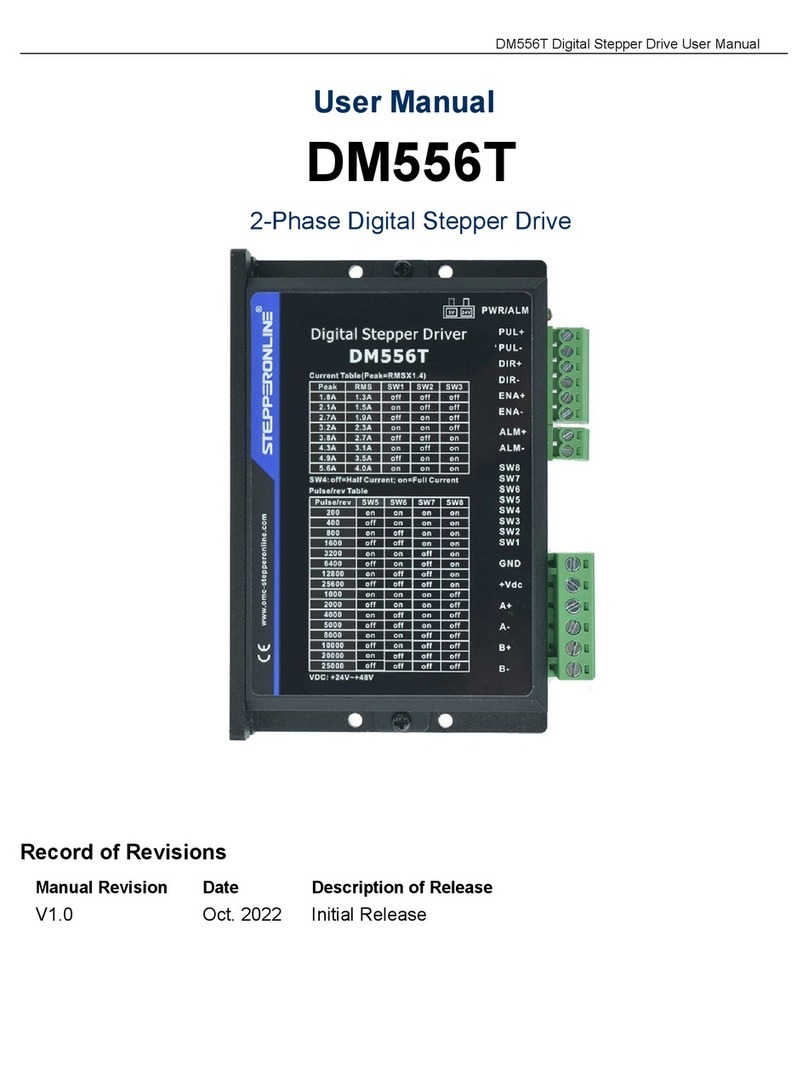
StepperOnline
StepperOnline DM556T User manual
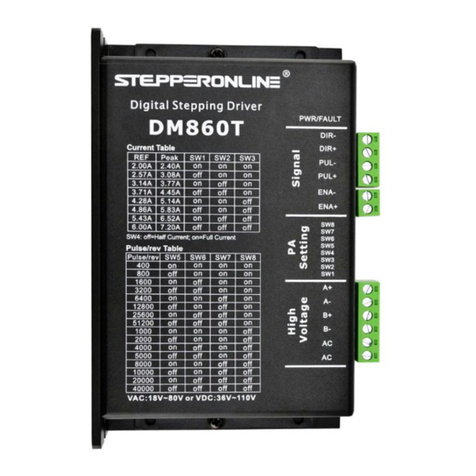
StepperOnline
StepperOnline DM860T User manual
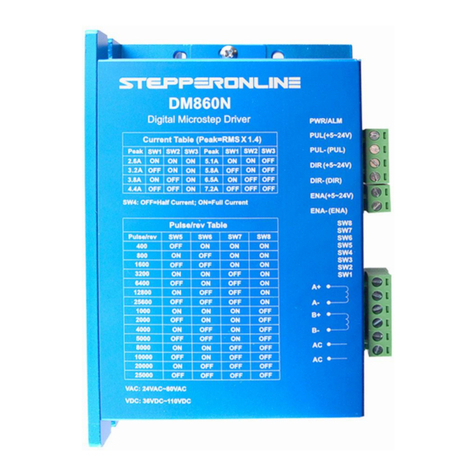
StepperOnline
StepperOnline DM860N User manual
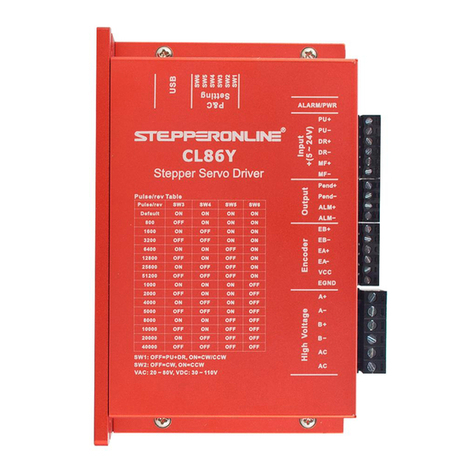
StepperOnline
StepperOnline Y Series User manual

StepperOnline
StepperOnline DMT556T User manual