Taylor 1200E User manual

V-21A
OPERATING GUIDE
FOR TYPE
1200E & 1600E
MULTI GUN DRAWN ARC
CONTROLLERS
2, 3 & 4 GUN MODELS
TAYLOR STUDWELDING
SYSTEMS LIMITED
A TAYLORMADE DRAWN ARC STUDWELDING SYSTEM TO WELD UP TO 16mm REDUCED BASE STUDS

V-21A
INDEX
2
PAGE No. CONTENT
3USEFUL INFORMATION.
5IMPORTANT SAFETY INFORMATION.
7INTRODUCTION TO STUDWELDING.
8GUIDE TO EXTERNAL FEATURES.
11 SETTING UP AND WELDING.
15 WELDING TIME AND CURRENT SETTINGS.
16 VISUAL WELD INSPECTION.
18 WELD TESTING.
21 STUDWELDING TECHNIQUES.
24 PARTS LIST & EXPLODED DIAGRAMS.
34 PCB’s - LED GUIDE
35 CIRCUIT SCHEMATICS
42 ACCESSORIES.
43 EC DECLARATION OF CONFORMITY.

V-21A
USEFUL INFORMATION
3
MANUFACTURERS DETAILS
TAYLOR STUDWELDING SYSTEMS LIMITED
COMMERCIAL ROAD
DEWSBURY
WEST YORKSHIRE
WF13 2BD
ENGLAND
TELEPHONE :+44 (0)1924 452123
FACSIMILE :+44 (0)1924 430059
email :sales@taylor-studwelding.com
WEB :www.taylor-studwelding.com
SALES DIRECT TEL :+44 (0)1924 487703
TECHNICAL HELPLINE :+44 (0)1924 487701
You may wish to record the details of your controller below as this informaon will help
with any technical assistance you may require:
PURPOSE AND CONTENT OF THIS GUIDE
This guide has been wrien for :
• The personnel of the end-user responsible for the installaon and maintenance of the
controller.
• The operator of the welding controller.
This guide contains informaon relang to :
• Installaon and connecon.
• Operaon.
• Technical specicaons and parameters.
• Spare parts.
CONTROLLER SERIAL No.
DATE PURCHASED.

V-21A
USEFUL INFORMATION
4
FURTHER INFORMATION
Should you require addional technical informaon, please contact us directly (details
on previous page) or our local agent / distributor (details of agents etc. can be obtained
from us).
This guide contains important informaon which is a pre-requisite for safe operaon
of the equipment. The operang personnel must be able to consult this guide when
necessary. In the interests of safety, make this guide available to your personnel in good
me.
If the equipment is sold / passed on, please pass this manual to the new owner and if
possible please inform us of the name and address of the new owner, in case we need to
contact them regarding the safety of the machine.
PLEASE READ THIS GUIDE CAREFULLY BEFORE INSTALLING OR OPERATING THE
CONTROLLER.
PLEASE OBSERVE CAREFULLY ALL SAFETY PROCEDURES/INSTRUCTIONS.
DUE TO THE POWER REQUIREMENTS AND ELECTROMAGNETIC EMISSIONS
PRODUCED DURING NORMAL USE, THIS MACHINE MUST ONLY BE OPERATED IN
AN INDUSTRIAL ENVIRONMENT.
THIS MACHINE OPERATES FROM A MAINS SUPPLY OF 380/415V AC @ 50/60 Hz
NEVER REMOVE ANY PORTION OF THE UNIT HOUSING WITHOUT FIRST
ISOLATING THE CONTROLLER FROM THE MAINS ELECTRICAL SUPPLY.
NEVER OBSTRUCT THE UNDERSIDE, FRONT OR REAR PANELS AS THIS MAY
CAUSE THE UNIT TO OVERHEAT DURING OPERATION.
Taylor Studwelding Systems Limited reserves the right to amend the contents of this guide without nocaon.

V-21A
IMPORTANT SAFETY INFORMATION !
5
PROTECT YOURSELF AND OTHERS !
Read and understand these safety notes.
1. ELECTRICAL
No poron of the outer cover of the welding controller should be removed by anyone other
than suitably qualied personnel and never whilst mains power is connected.
ALWAYS DISCONNECT THE MAINS LEAD BEFORE ATTEMPTING ANY
MAINTENANCE.
BEWARE - RISK OF ELECTRIC SHOCK !
Do not use any uids to clean electrical components as these may penetrate into the
electrical system.
Installaon must be according to the seng up procedure detailed on page 11 of this guide
and must be in line with naonal, regional and local safety codes.
2. FIRE
During welding small parcles of very hot metal are expelled. Ensure that no combusble
materials can be ignited by these.
3. PERSONNEL SAFETY
Arc rays can burn your eyes and skin and noise can damage your hearing. Operators and
personnel working in close proximity must wear suitable eye, ear and body protecon.
Fumes and gases can seriously harm your health. Use this equipment only in a suitably
venlated area. If venlaon is inadequate, then appropriate fume extracon equipment
must be used.
Hot metal spaer can cause re and burns. Appropriate clothing must be worn. Clothing
made from, or soiled with, combusble materials must NOT be worn.
Have a re exnguisher nearby and know how to use it.
Magnec elds from high currents can aect heart pacemakers or other electronically
controlled medical devices. It is imperave that all personnel likely to come into the vicinity
of any welding plant are warned of the possible risks before entering the area.
4. MAINTENANCE
All cables must be inspected regularly to ensure that no danger exists from worn or
damaged insulaon or from unsound electrical connecons. Special note should be made
of the cables close to the pistol, where maximum wear occurs. As well as producing
inconsistent welds, worn cables can overheat or spark, giving rise to the risk of re.

V-21A
IMPORTANT SAFETY INFORMATION !
6
5. TRAINING
Use of the equipment must limited to authorised personnel only who must be suitably
trained and must have read and understood this manual. This manual must be made
available to all operators at all mes. Further copies of this manual may be purchased from
the manufacturer. Measures must be taken to prevent the use of this equipment by
unauthorised personnel.
6. INSTALLATION
Ensure that the site chosen for the equipment is able to support the weight of the
equipment and that it will not fall or cause a danger in the course of its normal operaon.
Do not hang connecng cables over sharp edges and do not install connecng cables near
heat sources or via trac routes where people may trip over them or they may be
damaged by the passage of vehicles (forklis etc).
7. INTERFERENCE
During welding operaons, intense magnec and electrical elds are unavoidably produced
which may interfere with other sensive Electronic equipment.
All Taylor Studwelding equipment is designed, manufactured and tested to conform the
current appropriate European standards and direcves regarding electromagnec
emissions and immunity and as such is safe to use in any normal industrial environment.
8. DISPOSAL
The equipment either wholly or any of its component parts may be disposed of as part of
general industrial waste or passed to a scrap merchant. None of the components used in
the manufacture are known to be toxic, carcinogenic or harmful to health in their “as
supplied” condion.

V-21A
INTRODUCTION TO STUDWELDING
7
The Taylor Studwelding 1200E/1600E Drawn Arc Mul Gun controller when matched with
up to 4 appropriate pistols and earth cables is intended for precision stud welding up to
16/20 mm diameter reduced base studs. The controller is easily transportable and has been
designed to operate with a minimum amount of maintenance.
The energy required to carry out the welding operaon is derived from a fully micro-
processor controlled transformer-recer inside the controller.
Taylor Studwelding Systems Ltd pistols are modern, ergonomically designed and oer
maximum comfort in handling with minimum operator fague.
THE PROCESS
The process of drawn arc studwelding is long established and well proven. The basic steps
are as follows :
• A measured amount of weld stud protrusion is set at the welding pistol.
• Once in posion, the pistol lis the stud away from the work-piece, simultaneously
striking an arc between the two.
• Both the p of the weld stud and the surface of the work-piece melt as the arc is
sustained for a pre-determined interval.
• At the compleon of the pre-determined interval, the pistol returns the weld stud to
the molten pool on the work-piece, thus forming a weld.
The most common and tradional drawn arc welds have a weld duraon greater than
100ms and employ the use of a single use ceramic arc shield, commonly referred to as a
ferrule. This ferrule helps to protect the arc during the weld and assists in formaon of the
nal llet. Post welding the ferrule is removed and disposed of.
It is possible to stud weld without a ferrule. This method is more commonly employed with
welds having a duraon of less than 100 ms and this type of weld is referred to as short
cycle stud welding. Although no ferrule is employed, it is recommended pracce in short
cycle welding to employ a suitable shielding gas to reduce the amount of porosity in the
completed weld and improve weld quality.

V-21A
GUIDE TO EXTERNAL FEATURES
8
1
2
3
4
5
6
7
8
9
10
FRONT PANEL
1. GUIDING HANDLE - ! NOT FOR LIFTING !
2. MAINS ON/OFF SWITCH
3. PISTOL WELDING CONNECTION SOCKET (MODEL DEPENDENT, UP TO 4)
4. PISTOL CONTROL CONNECTION SOCKET (MODEL DEPENDENT, UP TO 4)
5. WELDING EARTH CONNECTION SOCKET (MODEL DEPENDENT, UP TO 4)
6. ADVISORY STICKER (NOT FOR LIFTING)
7. CONTROL PANEL (SEE PAGE 9)
8. SHIELDING GAS OUTLET SOCKET
9. VENTILLATION HOLES - ! DO NOT OBSTRUCT !
10. FRONT CASTOR (SWIVEL & BRAKE TYPE)

V-21A
GUIDE TO EXTERNAL FEATURES
9
CONTROL PANEL
1. WELD COUNTER (NON-RESETTABLE)
2. PUSHBUTTON (WELD CURRENT SETTING/CURRENT READBACK)
3. PUSHBUTTON (WELD TIME SETTING/ERROR CODE READBACK)
4. DISPLAY WINDOW (WELD CURRENT SET/CURRENT READBACK)
5. DISPLAY WINDOW (WELD TIME SET/SHIELDING GAS PURGE TIME SET/ERROR CODE
READBACK)
6. ADJUSTER KNOB
7. PUSHBUTTON (SHIELDING GAS PURGE SETTING/PARAMETER READBACK)
8. INDICATOR (SHIELDING GAS PURGE ACTIVATED)
9. INDICATOR (STUD TO PLATE CONTACT)
10. INDICATOR (PISTOL TRIGGER ACTIVATED (1 TO 4, MODEL DEPENDENT))
11. INDICATOR (PISTOL LIFT COIL ACTIVATED (1 TO 4, MODEL DEPENDENT))
12. INDICATOR (WELD CONTROLLER OVER TEMPERATURE)
13. INDICATOR (WELD CONTROLLER MAINS SUPPLY FAULT)
123456
78910 11 12 13

V-21A
GUIDE TO EXTERNAL FEATURES
10
BACK PANEL
1. LIFTING EYEBOLTS
2. VENTILLATION GRILLES - ! DO NOT OBSTRUCT !
3. RATING/SERIAL PLATE
4. REAR CASTORS (FIXED TYPE. NO BRAKE)
5. SHIELDING GAS INLET SOCKET
6. 3 PHASE MAINS CABLE INLET GLAND (CABLE NOT SHOWN).
1
2
3
4
5
6

V-21A
SETTING UP AND WELDING
11
Set up the control unit at the place of work,
ensuring that the mains switch is in the OFF
posion.
Plug the controller into a suitable three phase AC supply with a
63A motor rated fuse/breaker.
Plug the welding earth cables into the controller. Note that
the cable end weld plug has a peg which mates with the key
slot in the panel mounted socket.
IMPORTANT! Secure the connectors with a clockwise turn
unl they lock. Failure to do this may result in damage to the
connectors during welding.
Aach the welding earth clamps to the work piece at
approximately 180° to each other; this will help prevent "arc-
blow" when welding takes place. Prior to ng the clamps,
ensure that the contact area of the work piece is free from rust,
paint, grease etc., as this will result in a poor welding
connecon.
Plug the pistol control cable into the controller. Note that the
cable end plug and panel-mounng socket are keyed to prevent
incorrect ng. Push the plug rmly home and twist the locking
ring to secure the plug in posion.
Plug the welding pistol cable into the controller. Note that the
cable end weld plug has a peg which mates with the key slot in
the panel mounted socket.
IMPORTANT! Secure the connector with a clockwise turn unl it
locks. Failure to do this may result in damage to the connector
during welding.
Push the pistol shielding gas connecon plug into the
appropriate panel socket unl the socket outer sleeve snaps into
posion (only if the pistol is ed for use with shielding gas).
Set up the welding pistol according to the instrucons in the
operang guide supplied with the pistol.

V-21A
SETTING UP AND WELDING
12
Switch the controller ON by turning the mains
switch clockwise through 90°. The venlaon
fans will start, the display will illuminate and
carry out a start up diagnosc roune. This will
take approx’ 6 seconds at the end of which the
display will indicate the current sengs of the
last pistol used.
A guide to the recommended me and current sengs can be found on page 15 of this
handbook.
Referring back to the control panel guide on page 9, set the controller by following these
simple steps :-
SELECT THE PISTOL TO SET UP.
Having previously connected one or more (up to
4, dependent on controller model) pistols to the
controller. Firstly select the pistol to be set. To do
this, pick up the pistol you want to set up and
acvate the trigger. The display window (4) will
briey display an idener for the pistol. From
this point, unl a trigger is acvated on another
connected pistol, any seng entered will be for
this pistol connected to this port.
SET WELD CURRENT
1. Press and hold the current seng
pushbuon (2). The display window (4) will
display the last set current for this pistol
and display window (5) will display the
pistol idener.
2. Turn the adjuster knob (6) unl the
required current is displayed in the welding
current display window (4). The current is
adjustable between 200 and 1200/1600A*
in increments of 10A.
3. Release the pushbuon (2). The current is now set.
NOTE! If the pushbuon (2) is held for more than 3 seconds before turning the adjuster
knob (6), the display (4) will change to last weld current readback mode and will need to be
released and re-pressed.
* Depending on controller model

V-21A
SETTING UP AND WELDING
13
SET WELD TIME
1. Press and hold the weld me seng
pushbuon (3).
2. Turn the adjuster knob (6) unl the
required me is displayed in the display
window (5). The me is adjustable
between 20 and 2000ms in 5ms
increments up to 100ms and 10ms
increments thereaer.
3. Release the pushbuon (3). The weld
me is now set.
NOTE! If the pushbuon (3) is held for more than 3 seconds before turning the adjuster
knob (6), the display (5) will change to last system error code display mode and will need to
be released and re-pressed.
SETTING THE GAS PURGE TIME
1. Press and hold the shielding gas purge
me seng pushbuon (7).
2. Turn the adjuster knob (6) unl the
required me is displayed in the me
display window (5). The me is
adjustable between 0 and 5000ms in
100ms increments.
3. Release the pushbuon (7). The
shielding gas purge me is now set.
4. If no gas purge is required, this me
parameter must be set to 0 (zero).
NOTE! If the pushbuon (7) is held for more than 3 seconds before turning the adjuster
knob (6), the display (5) will change to display feedback system parameters (not operator
adjustable) and will need to be released and re-pressed.
Repeat these steps from “SELECT THE PISTOL TO SET UP” on the previous page for any
addional pistols connected to the controller.
NOTE! Changing pistols over from one port to another will not carry the sengs over and
the pistol will require re-seng in-line with these steps.

V-21A
SETTING UP AND WELDING
14
Place the pistol perpendicular to the work piece with
the stud touching down at the desired locaon to be
welded. Press down on the pistol unl the ceramic
ferrule rests rmly on the work piece. Press the
trigger to iniate the weld sequence.
See the secon on Studwelding Techniques for
further advice.
The welding process is as follows: -
1. Start.
2. Pistol lis stud.
3. Pilot Arc strikes.
4. Main Arc strikes melng both stud and workpiece.
5. Arc stops. Pistol plunges stud into molten pool.
6. Weld complete.
Having welded the stud, draw the pistol vercally o
the stud. Failure to do this may cause the split nes
of the chuck to splay out. This will result in the chuck
and stud arcing together during subsequent welds.
Finally, remove the ferrule by lightly tapping unl it shaers. Visually
inspect the weld.
For a guide to the inspecon of the welded stud see the secons on
inspecng and tesng welded studs.
1 2 3
4 5 6

V-21A
WELDING TIME AND CURRENT SETTINGS
15
This page is intended as a guide to seng your
machine.
A set of basic formulae as dened by the Brish
Standard BS EN ISO 14555:2014 (European
Standard EN ISO 14555:2014) Annex A.2.7.2.2
and Annex A.2.7.2.4 may be used to calculate the
current and me sengs to weld any stud.
These formulae when applied to standard studs
give results shown in the table on this page. A
graphical representaon of the data is also
illustrated below.
The sengs generated in the table are only
intended as a starng point. It is possible that
the sengs will give
sasfactory results
without adjustment, but
in reality the quality of
the welding results is
governed by many
variable factors. These
include, most obviously,
the welding me, current
and arc-gap (pistol li) as
covered in the table, but
can also include factors
such as stud and work-
piece material type and
condion, ambient
temperature, relave
humidity, quality of supply
etc. All of these factors
can act on the weld to
change the outcome. It is
recommended that in all
instances, you need to
carry out sample welds in
your actual condions and
environment. This will
enable you to alter the
sengs, where necessary,
to achieve welds that are
most acceptable to you.
STUD
TYPE
ACTUAL
DIAMETER
(mm)
WELD
CURRENT
(A)
WELD
TIME
(ms)
5FB 5 400 100
6RB 4.7 376 94
6FB 6 480 120
8RB 6.2 496 124
8FB 8 640 160
10RB 7.9 632 158
10FB 10 800 200
12RB 9.5 760 190
12FB 12 960 240
16RB 13.2 1056 528
16FB 16 1440 640
19FB 19 1710 760
20RB 16.5 1485 660
WELD CURRENT - EN ISO 14555
0
200
400
600
800
1000
1200
1400
1600
1800
2000
5FB 6RB 6FB 8RB 8FB 10RB 10FB 12RB 12FB 16RB 16FB 19FB 20RB 20FB
STUD SIZE
CURRENT (A)
WELD TIME - EN ISO 14555
0
0.1
0.2
0.3
0.4
0.5
0.6
0.7
0.8
0.9
5FB 6RB 6FB 8RB 8FB 10RB 10FB 12RB 12FB 16RB 16FB 19FB 20RB 20FB
STUD SIZE
WELD TIME (s)

V-21A
VISUAL WELD INSPECTION
16
This page will help you to recognise a poor weld when you see one and give some of the
possible explanaons as to how it may have occurred. Your test welds should look like the
rst example diagram in the series and once you transfer to the actual job, periodic checks
should be made to ensure that your welding is consistently good.
POINTS TO LOOK FOR IRRESPECTIVE OF PROCESS USED.
• L.A.W. (Length Aer Welding). This should be correct to within the tolerances
specied for the type of stud being welded.
• The base llet of the welded stud is complete.
• The welded stud is perpendicular to the work-piece.
WHEN USING A CERAMIC FERRULE.
This diagram is a representaon of a good normal weld, fullling the criteria
above i.e. The LAW is correct, the stud has a complete, well formed and even
llet and is also perpendicular to the work-piece. The following examples will
help you to recognise the most common types of poor weld, explain the
possible causes of these problems and make suggesons as to how to remedy
them.
EXAMPLE 1
PROBLEM : Insucient heat and/or me causing the LAW to be too long
and the llet to be underdeveloped and/or incomplete.
REMEDY : Increase the welding current/me (see page 13).
EXAMPLE 2
PROBLEM : Excessive heat and/or me causing the LAW to be too short
and the llet to be too large and messy, spreading out under
the ferrule and/or splashing up the threads.
REMEDY : Reduce the welding current/me (see page 13).
EXAMPLE 3
PROBLEM : The ferrule is not being held rmly against the work-piece
and/or the stud is binding against the ferrule.
REMEDY : Hold the pistol rmly down to the work-piece (see page 14)
and reset the alignment of the stud and ferrule (refer to your
pistol setup guide).
✓

V-21A
VISUAL WELD INSPECTION
17
EXAMPLE 4
PROBLEM : Insucient stud protrusion set on the pistol.
REMEDY : Adjust stud protrusion to correct seng (refer to your pistol
setup guide).
EXAMPLE 5
PROBLEM : Poor alignment i.e. stud is not perpendicular to the workpiece.
REMEDY : Hold the pistol perpendicular to the work-piece (see page 14).
NOTE : If the misalignment is only slight and in all other aspects the
weld is good, then the weld may be salvaged by tapping
straight with a so mallet.
A broader set of examples may be found in the standard BS EN ISO 14555:2014 Annex 5,
Tables A5, A6 & A7

V-21A
WELD TESTING
18
There are two factors which should receive special aenon in establishing visually whether or not
a stud weld is sound. These are :
• The length aer weld (L.A.W.) of the stud should be correct. That is to say that a stud which is
intended to be 50 mm long aer welding, should be correct within the tolerances specied
for that parcular stud. A word of explanaon is perhaps needed on this point. All studs
produced include a "weld allowance". This allowance is so arranged for the dierent
diameters of stud, that it will be completely melted during the welding process, provided of
course that the correct condions have been established and the correct values of current
and me are used.
• The llet of metal formed around the base of the stud should be well formed, reasonably
evenly distributed, completely free from blow holes and of a silver blue colour.
These two factors combined form the basis of all visual stud weld examinaon. It should be the aim
of every operator to produce these results.
Under normal condions a stud welded to clean mild steel plate of adequate thickness having the
correct LAW and llet formaon as described above, will be a sasfactory weld.
It should be remembered, however, that dierent applicaons or condions will produce slightly
dierent visual results, parcularly in the appearance of the llet, i.e. Slightly rusty, dirty or oily
plate will produce blow holes in the llet, in proporon to the degree of plate contaminaon.
Welding close to some magnec obstrucon may produce uneven llet distribuon. Too much
power will produce a llet that ows too easily and is lost either up in the threads of the stud or out
through the ferrule vents, while too lile power may not melt sucient material to form a complete
llet.
It is important, therefore, to judge the degree to which these possible variaons will aect the weld
strength, but in general, provided that the LAW is correct and the llet formaon is not unsightly, a
visual examinaon is all that is required.
Further tesng may be carried out on a "percentage of producon" basis, and the methods used fall
into the classes outlined below.
1. DESTRUCTIVE TESTING.
Should only be used on studs welded to samples and test pieces.
• Hammering a stud over may look spectacular, but it is not a sasfactory test, as the direcon
and force behind the blows is uncontrolled, as also is the point at which the impact takes
place. The length, diameter and type of stud also have an eect on the results obtained.
• Bending the stud over by using a tube of approximately the same bore as the stud diameter.
This method is preferred to hammering, but again no conclusive evidence as to the strength
of the weld is obtained.
• Loading the stud by the use of washers / spacer and a nut unl the stud breaks. This method
is much more conclusive and should show that the weld is in fact stronger than the stud. Use
of a suitably calibrated torque wrench for this test will give an indicaon of the U.T.S.
developed by the stud material under test.
A broader explanaon of these methods may be found in standard BS EN ISO 14555:2014, Secon
11 (Examinaon and Tesng).

V-21A
WELD TESTING
19
2. NON DESTRUCTIVE TESTING.
Generally the most praccal way of tesng threaded stud welds, without destroying the
stud, is with the use of proof tests. A torque wrench is parcularly useful for this purpose.
Below and overleaf are some tables which you may nd useful. However, it must be noted
that :
• Formulas & data shown are intended for guidance only.
• In applicaons where control of preload is important, the torque - tension
relaonship should be determined experimentally on the actual parts involved
including any lubricants.
• The coecient of fricon (k) varies with material, surface nish and lubricity of
threads and bearing areas of fastened parts.
• For standard steel screws it is 0.19 to 0.25 and 0.13 to 0.17 for plated screws. An-
seize materials and lubricants can lower k to 0.05. For some stainless steel threads
and parts not coated or lubricated k may be as high as 0.33
• All the gures are approximate and do not form part of any specicaon.
• Designers and speciers must sasfy themselves that the studs and materials chosen
are suitable for their parcular applicaon.
All torque gures are calculated by the formula : T = kDP
Where :T = Torque (Nm)
D = Eecve Stud Diameter (m)
k = Coecient of Fricon (0.2 used for calculaons)
A broader explanaon of these methods may be found in standard BS EN ISO 14555:2014, Secon
11 (Examinaon and Tesng).
Material properes: (N/mm²) (N/mm²) (N/mm²)
UTS Yield Safe
Mild Steel (4.8) 420 340 272
Stainless Steel (1.4301) 540 350 280
Note: safe loads are 80% of the yield

V-21A
WELD TESTING
Stud loads - Full Base Drawn Arc Studs (kN)
Torque required to reach the loads above (Nm)
Stud loads - Reduced Base drawn Arc Studs (kN)
Torque required to reach the loads above (Nm)
Mild Steel Mild Steel Mild Steel Stainless
Steel
Stainless
Steel
Stainless
Steel
Thread UTS Yield Safe UTS Yield Safe
M5 x 0.8 5.8 4.7 3.7 7.4 4.8 3.8
M6 x 1.0 8.2 6.6 5.3 10.6 6.8 5.4
M8 x 1.25 15.2 12.3 9.8 19.6 12.7 10.1
M10 x 1.5 23.8 19.2 15.4 30.6 19.8 15.8
M12 x 1.75 34.6 28.0 22.4 44.5 28.8 23.1
M16 x 2.0 64.6 52.3 41.8 83.1 53.8 43.1
Mild Steel Mild Steel Mild Steel Stainless
Steel
Stainless
Steel
Stainless
Steel
Thread UTS Yield Safe UTS Yield Safe
M5 x 0.8 4.9 4.0 3.2 6.3 4.1 3.3
M6 x 1.0 8.2 6.7 5.3 10.6 6.9 5.5
M8 x 1.25 20.7 16.8 13.4 26.7 17.3 13.8
M10 x 1.5 40.5 32.8 26.2 52.1 33.8 27.0
M12 x 1.75 71.0 57.5 46.0 91.3 59.2 47.4
M16 x 2.0 181.0 146.5 117.2 232.8 150.9 120.7
20
Mild Steel Mild Steel Mild Steel Stainless
Steel
Stainless
Steel
Stainless
Steel
Thread UTS Yield Safe UTS Yield Safe
M6 x 1.0 7.2 5.8 4.7 9.3 6.0 4.8
M8 x 1.25 12.6 10.2 8.2 16.3 10.5 8.4
M10 x 1.5 20.5 16.6 13.3 26.4 17.1 13.7
M12 x 1.75 29.7 24.0 19.2 38.2 24.8 19.8
M16 x 2.0 57.4 46.5 37.2 73.8 47.8 38.3
M20 x 2.5 89.8 72.7 58.1 115.4 74.8 59.8
Mild Steel Mild Steel Mild Steel Stainless
Steel
Stainless
Steel
Stainless
Steel
Thread UTS Yield Safe UTS Yield Safe
M6 x 1.0 6.8 5.5 4.4 8.8 5.7 4.6
M8 x 1.25 15.7 12.7 10.2 20.2 13.1 10.5
M10 x 1.5 32.5 26.3 21.1 41.8 27.1 21.7
M12 x 1.75 56.6 45.8 36.6 72.7 47.1 37.7
M16 x 2.0 151.7 122.8 98.3 195.1 126.4 101.2
M20 x 2.5 296.4 239.9 191.9 381.0 247.0 197.6
This manual suits for next models
4
Table of contents
Other Taylor Controllers manuals
Popular Controllers manuals by other brands
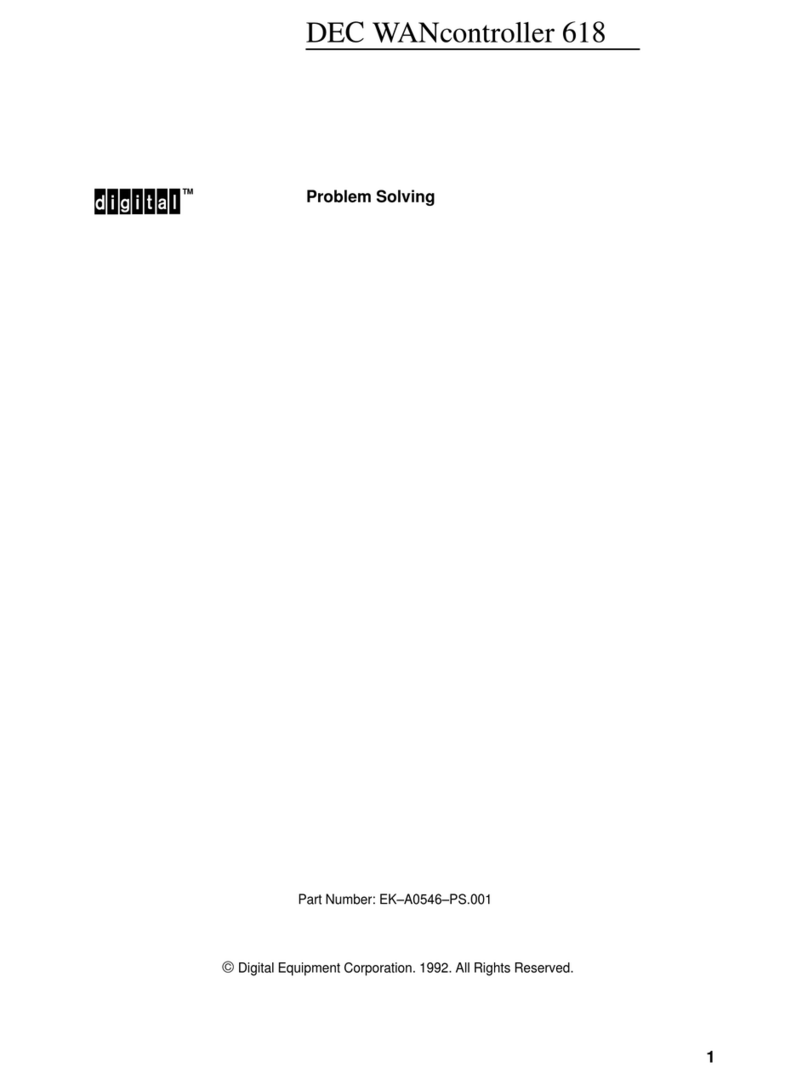
Digital Equipment
Digital Equipment DEC WANcontroller 618 Problem Solving
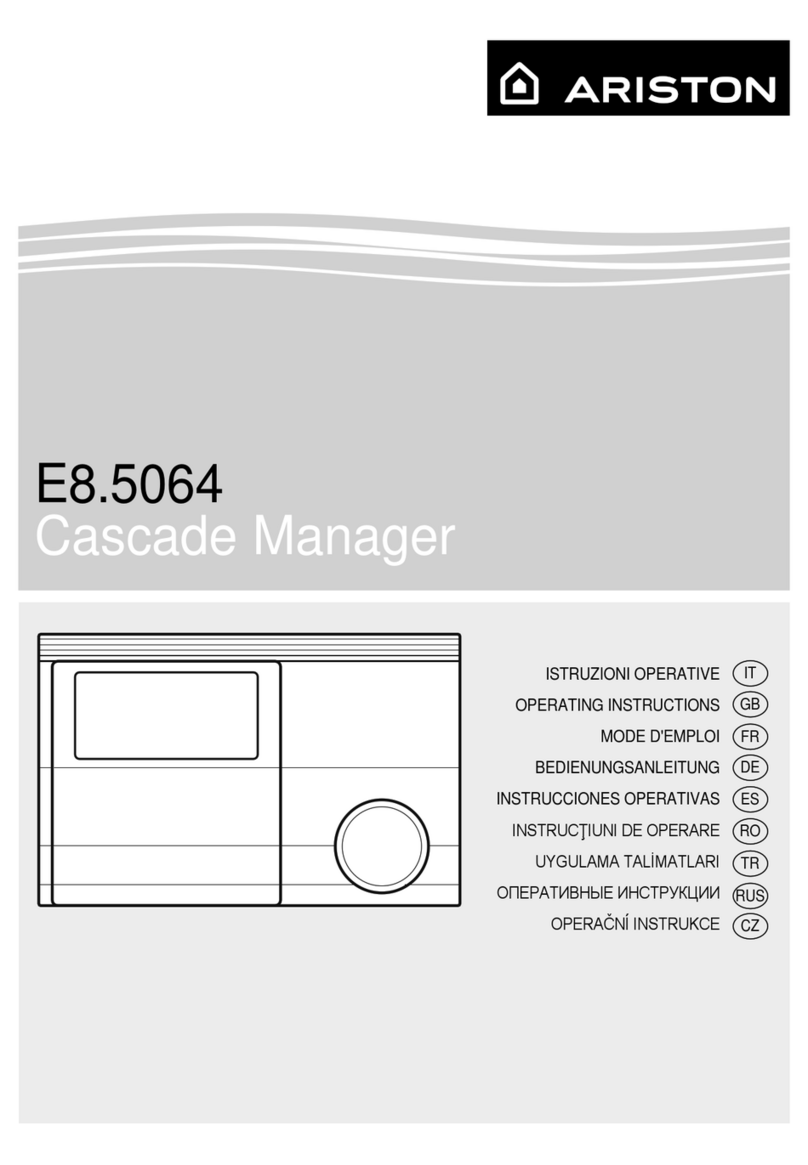
Ariston
Ariston E8.5064 operating instructions
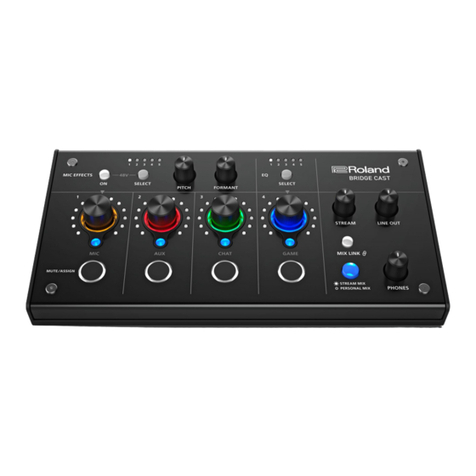
Roland
Roland BRIDGE CAST owner's manual
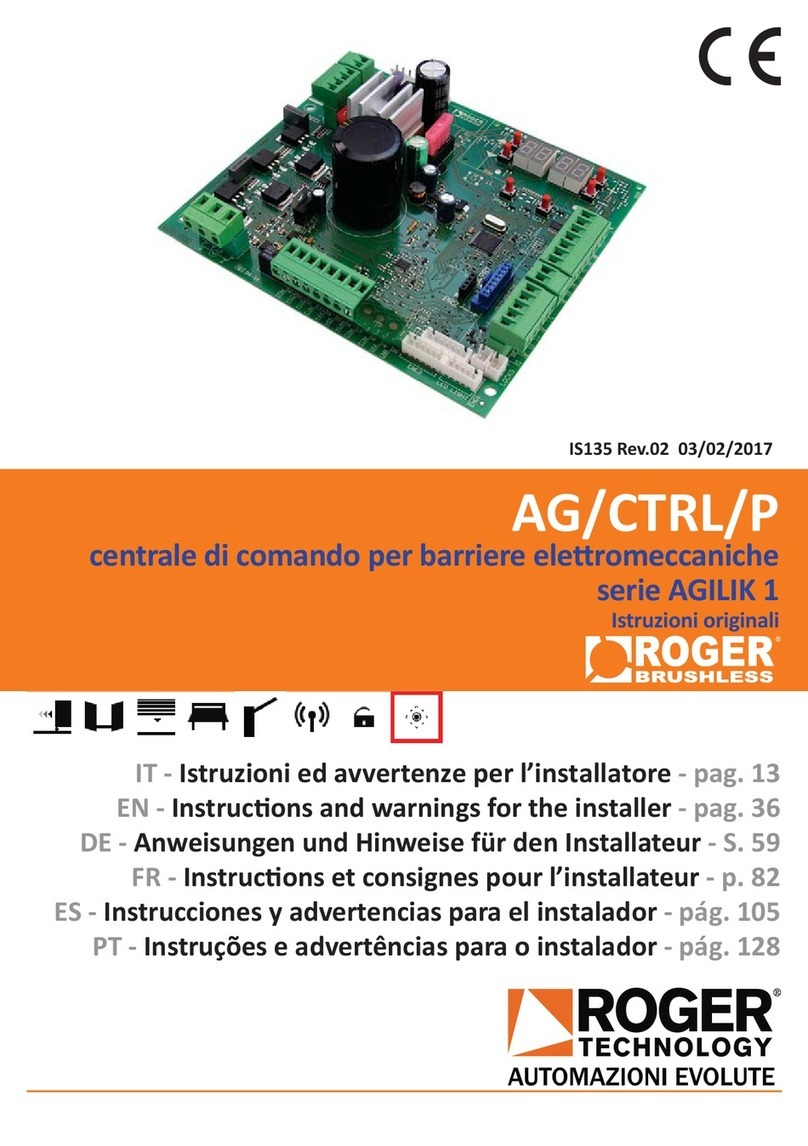
Roger
Roger AG/CTRL/P Instruction and warnings for the installer
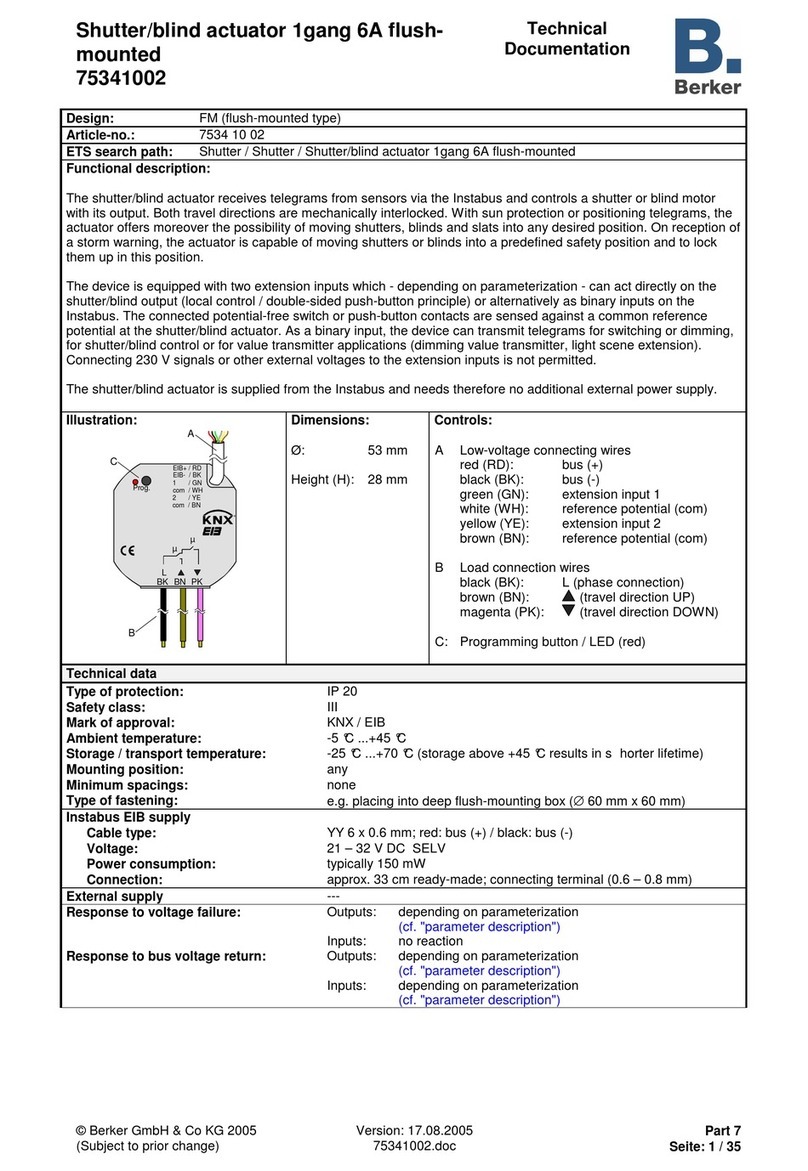
Berker
Berker 75341002 Technical documentation
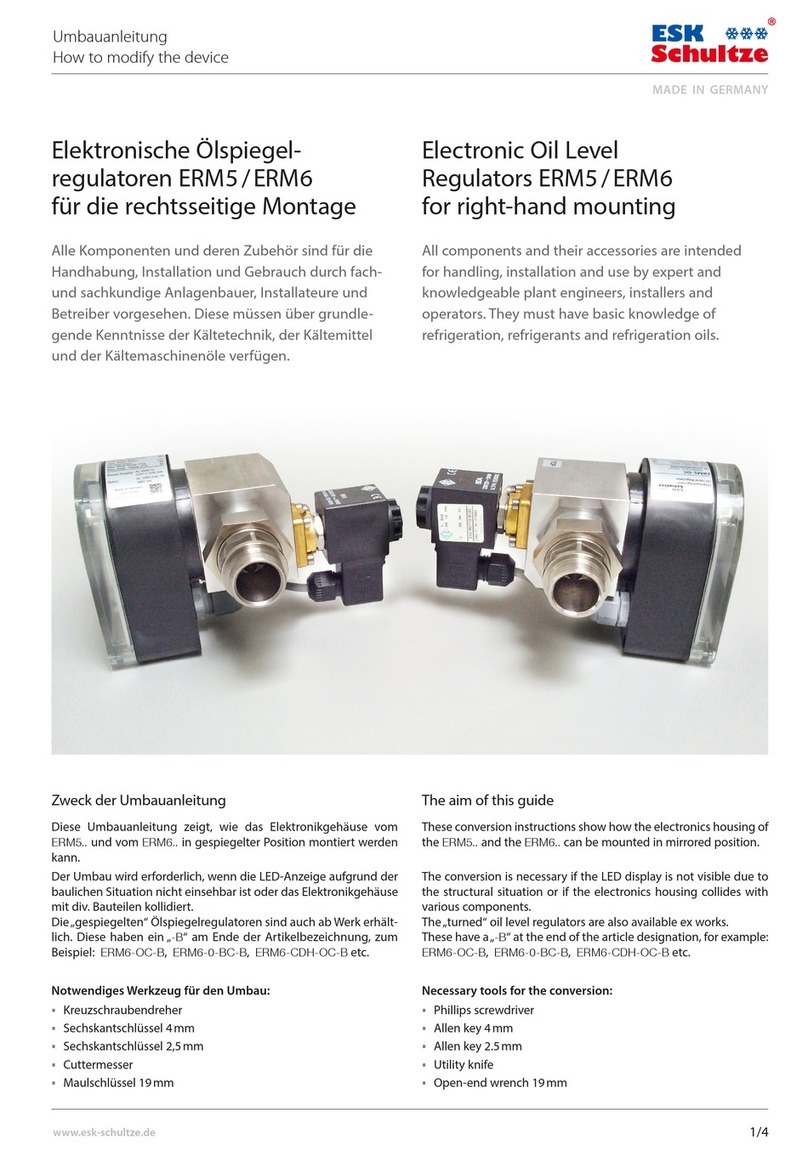
ESK Schultze
ESK Schultze ERM5 How-to