The Handy THLS-6-PLUS User manual

OPERATOR’S MANUAL & PARTSLIST
MODEL –THLS-6-PLUS
6 TON ELECTRIC LOGSPLITTER WITH STAND
SPARES & SUPPORT: 01793 333212
Please read & understand this manual, paying particular attention to the safety
instructions, before use.
The manufacturer reserves the right to change the product specification and
livery according to continued product improvements.
Due to the weight of this machine, we recommend a two-person lift from the carton
193894001 25/02/2016


CONTENTS
SPECIFICATIONS
IMPORTANT INFORMATION
GENERAL SAFETY INSTRUCTIONS
SET UP & PREPARATION FOR OPERATION
WIRING & HYDRAULIC DIAGRAMS
OPERATION
CHECKING & REPLACING HYDRAULIC OIL
TROUBLE SHOOTING
MAINTENANCE & STORAGE
PARTS LISTS & DIAGRAM
WARRANTY
EC DECLARATION OF CONFORMITY
If you require any assistance with regards to the contents or operation of
your machine, please contact us:
Tel: 01793 333212 (Mon to Friday 8.30am to 5.30pm)
Email: customerservi[email protected]

SPECIFICATIONS
The manufacturer reserves the right to change the product specification and livery according to
continued product improvements.
Model Number
THLS-6
Product Number
193893001
Motor
230V~ 50Hz 2200W S6 (40%)
IP54
Splitting Force
6 Ton
Forward Speed
3.4cm/s
Retract Speed
5.1cm/s
Hydraulic Pressure
20Mpa
Hydraulic Oil Tank Capacity
3.5L
Overall Size (mm)
(L)940 –(W)270 –(H)510
Stroke Length (mm)
370
Log Capacity Diameter (mm)*
Min 50 –250 Max
Log Capacity Length (mm)
Min 160 –520 Max
Weight (kg)
45
* The diameter of the log is not the only factor that determines how easy it will be to split. A small
log can be difficult to split when it has knots or is a particularly hard wood.
IMPORTANT INFORMATION
HYDRAULIC OIL
This machine is supplied with Hydraulic oil from the factory, to allow the machine to be used straight from
the carton. Do check the oil level (instructions available in the manual) prior to the first use and
periodically thereafter.
ELECTRICAL REQUIREMENTS
Connect the main leads to a standard 230V+10% (50Hz+1Hz) electrical supply which has protection
devices for under-voltage, over-voltage, over-current as well as a residual current device (RCD) with
maximum residual current rated at 0.03A.
EXTENSIONS LEADS
Improper use of extension leads may cause inefficient operation of the log splitter which can result in
overheating. Be sure the extension lead is no longer than 10m and its cross-section is no less than 2.5mm²
to allow sufficient current flow to the motor. Avoid use of loose or inadequately insulated connections.
Connections must be made with a protected material suitable for outdoor use.
WORKING CONDITIONS
This log splitter is a domestic use model. It is designed for operating under ambient temperatures between
+5oC and 40oC and for installation at altitudes no more than 1000m above M.S.L. The surrounding
humidity should be less than 50% at 40oC. It can be stored or transported under ambient temperatures
between -25oC and 55oC.
INSPECT YOUR LOG
Make sure there are no nails or foreign objects in logs to be split. The ends of the logs must be cut
square. Branches must be cut off entirely so that the trunk is relatively smooth.

GENERAL SAFETY INSTRUCTIONS
It is important that you read and understand the owner’s manual and labels affixed to the
machine. Learn its application and limitations as well as the specific potential hazards. Retain
these instructions for future reference. The operator is responsible for following the warnings &
instructions in this manual and on the product.
Read & understand operator’s manual
before using the machine. Failure to
follow instructions could result in death
or serious injury.
Always pay full attention to the
movement of the log pusher.
Do not attempt to load the log on
until the log pusher has stopped.
Keep hands out of the way of all
moving parts.
Wear gloves to protect your hands
Keep your hands away from splits
and cracks which open in the log.
They may close suddenly and
crush your hands.
Do not remove jammed logs with
your hands
Whenever the machine is in use, safety
glasses must be worn to safeguard
against flying objects.
Hearing protection must also be used to
protect the operators hearing.
If the operator is working in an area
where there is a risk of falling objects, a
safety helmet must also be worn.
Unplug when not in use, before
making adjustments, changing
parts, cleaning, or working on the
log splitter. Consult the technical
manual before servicing.
Wear foot protection
Take used oil to an authorized
collection point or follow the
local stipulations that apply
where the log splitter is being
used.
Do not discharge into drains, soil
or water.
Check your log splitter before turning it
on. Keep guards in place and in working
order. Frequently check to see that keys
and adjusting wrenches are removed
from the tool area before turning it on.
Replace damaged, missing or failed parts
before using it.
10m
Keep all bystanders & animals at
least 10 metres away from the
machine during operation.
If approached, stop the machine
immediately.
Safety alert symbol. Used to alert you to potential personal injury hazards. Obey all safety messages that
follow this symbol to avoid possible injury.
DANGER
Indicates an imminently hazardous situation which, if not avoided, will result in serious injury.
WARNING
Indicates a potentially hazardous situation which, if not avoided, could result in serious injury
CAUTION
Indicates a potentially hazardous situation which, if not avoided, may result in minor or moderate injury.
CAUTION
Used without the safety alert symbol indicates a potentially hazardous situation which, if not avoided,
may result in property damage.

STAY ALERT
Do not operate the machine while under the influence of drugs, alcohol, or any medication that
could affect your ability to use it properly. Do not use this machine when you are tired or distracted
from the job at hand. Be aware of what you are doing at all times. Use common sense.
AVOID DANGEROUS CONDITIONS
Make sure there is adequate surrounding workspace. Cluttered areas invite injuries.
Keep your work area clean with sufficient light. Keep the area around the machine clear of
obstructions, grease, oil, rubbish and other debris which could cause persons to fall onto moving
parts.
INSPECT YOUR MACHINE
Check all bolts, nuts, and screws for tightness before each use, especially those securing guards and
drive mechanisms. Vibration during use, may cause these to loosen.
Form a habit of checking to see that all other tools/equipment are removed from the working area
before turning it on.
Replace damaged, missing or failed parts before using it. Warning labels carry important
information. Replace any missing or damaged warning labels.
DRESS PROPERLY
Do not wear loose clothing, gloves, scarfs, neckties or jewelry (rings, wrist watches), which can be
caught in moving parts. Protective electrically non-conductive gloves and non-skid heavy duty
footwear are highly recommended when working. Wear a face or dust mask if the operation is dusty.
Always wear safety glasses/goggles and/or face shields. Everyday eyeglasses have only impact
resistant lenses; they are not safety glasses/goggles. Wear protective hair covering to contain long
hair, preventing it from getting caught in machinery.
AVOID ELECTRICAL SHOCK
Check that the electric circuit is adequately protected and that it corresponds with the power,
voltage and frequency of the motor. Check that there is a ground connection, and a regulation
differential switch further up the circuit. Ground the log splitter. Prevent body contact with
grounded surfaces: pipes, radiators, ranges, and refrigerator enclosures. Never open the pushbutton
box on the motor. Should this be necessary, contact a qualified electrician. Make sure your fingers
do not touch the plug’s metal prongs when plugging or unplugging the log splitter.
KEEP BYSTANDERS AND CHILDREN AWAY
Keep unauthorised persons a minimum distance of 10 metres away from the machine. If
approached, stop the machine immediately. Do not allow children to handle, climb on or in the
mixer.
DO NOT OVERREACH
Keep proper footing and balance at all times when using the machine. Never stand on the
machine. Serious injury could occur if the machine is tipped or if the moving parts are
unintentionally contacted. Do not store anything above or near the machine, where anyone might
stand on the machine to reach them.
AVOID INJURY FROM UNEXPECTED ACCIDENT
Keep hands & feet out of the way of all moving parts. Do not place any part of your body or any
tool e.g. in the machine during operation.
DO NOT FORCE TOOL
Always work within the rated capacity. Do not use the machine for a purpose for which it was not
intended.
NEVER LEAVE MACHINE RUNNING UNATTENDED
Do not leave the machine unattended until it has come to a complete stop.
MAINTAIN YOUR MACHINE WITH CARE
Clean the machine immediately after use. Keep the machine clean to ensure it operates to its full &
safest performance. When maintaining this machine, only the manufacturer’s original replacement
parts should be used. The use of non-original manufacturer parts may invalidate your warranty.

PROTECT THE ENVIRONMENT
Take left over materials to an authorised collection point or follow the stipulations in the country
where the mixer is used. Do not discharge into drains, soil or water.
STORE IDLE EQUIPMENT
When not in use, the machine should be stored in a dry location. Keep the machine away from
children and others not qualified to use it.
This symbol on the product or on its packaging indicates that this product may not be treated as
household waste. Instead it shall be handed over to the applicable collection point for the recycling
of electrical and electronic equipment.
For more detailed information about recycling of this product, please contact your local council
office, your household waste disposal service or shop where you purchased the product.

SET UP & PREPARATION FOR OPERATION
Bolt the Support Leg to the Log Splitter, lift the log splitter by the Log Pusher & Handle & place it
on a 60 –75cm high, stable, flat and level work surface.
Familiarise yourself with the controls and features of this log splitter in the illustrations.
1. Log Pusher
2. Work Table
3. Wedge
4. Handle
5. Support Leg
6. Log Retaining Plates
7. Switch
8. Motor
9. Electric Motor Switch Case
10. Wheels (short distances
ONLY).
11. Hydraulic Control Lever
12. Control Lever Guard
13. Bleed Screw
14. Oil Drain Bolt w/ Dipstick
15. Max Pressure Limiting
Screw

ATTACHING THE LOGSPLITTER TO THE STAND
1. Ensure the machine is disconnected from the electrical source.
2. Remove the front support leg and the wheels. The wheels are secured by a circlip behind the wheel
cap. Circlip pliers are required to remove.
3. Place the wheels on the stand axle bar, with the circlip pliers. Attach the centre horizontal bar to the
wheel axle and front support leg and tighten the securing bolts.
4. Attach the rear support legs to your log splitter, with the wheel axles of the log splitter being placed
through the top fixing holes of the rear support legs. With the help of a second person, lift the log
splitter onto the stand, by positioning the front of the log splitter into the front support leg cup. Now
place the rear support legs into the stand axle bar. Now tighten the fixing bolts on the stand

BLEED SCREW
IMPORTANT
Before operating the log splitter, the Bleed Screw should be loosened a few rotations until air can go in and
out of the oil tank smoothly. Air flow through the Bleed Screw hole should be noticeable while the log
splitter is working. Before moving the log splitter, make sure the Bleed Screw is tightened to avoid oil leaks.
FAILURE TO LOOSEN THE BLEED SCREW WILL KEEP THE SEALED AIR IN HYDRAULIC
SYSTEM COMPRESSED. SUCH CONTINUOUS AIR COMPRESSION WILL BLOW OUT THE
SEALS OF THE HYDRAULIC SYSTEM AND CAN CAUSE PERMANENT DAMAGE TO THE LOG
SPLITTER, WHICH IS NOT COVERED UNDER THE TERMS & CONDITIONS OF THE
MANUFACTURERS WARRANTY.
MAX PRESSURE LIMITING SCREW
DO NOT ADJUST
The max pressure was set by the manufacturer. The max pressure limiting screw is sealed
with glue to ensure the log splitter works under pressure no more than is listed in the specifications.
The setting was made by a qualified mechanic with professional instruments. Unauthorised resetting
will reduce the performance of the hydraulic pump or RESULT IN SERIOUS INJURY AS WELL AS
DAMAGE TO THE MACHINE.

WIRING DIAGRAM
HYDRAULIC DIAGRAM

OPERATION
This log splitter is equipped with “ZHB” control system that must be operated with both hands – the
left hand controls the hydraulic control lever while right hand controls the pushbutton switch. The
log splitter will freeze if either hand is removed. The log pusher will only start to return backward to
the starting position after both hands release the controls. During use the log pusher will move
towards the splitting wedge putting pressure on the log.
The trigger type lockout device is used to avoid accidental Hydraulic Control Lever activation. To
operate the Hydraulic Control Lever, draw the Trigger backward with your index finger before
pushing the Hydraulic Control Lever forward.
Never force the log splitter for more than 5 seconds. Do not keep pressure on it to split
excessively hard wood.
After 5 seconds of constant use, the oil under pressure will be overheated and the machine could be
damaged. For such extremely hard logs, rotate it by 90oto see whether it can be split in a different
direction (the log should still be split with the grain as shown in the diagrams in this manual). In any
case, if you are not able to split the log, this means that its hardness exceeds the capacity of the
machine and thus that log should be discarded to protect the log splitter.
Always set logs firmly on the log retaining
plates and work table. Make sure that the
log will not twist, rock or slip while being
split. Do not force the blade by splitting the
log on the upper part of the wedge (as
shown in the diagram). This will break the
blade or damage the machine.
Break the log in the direction of its growing grain. Do not place log across the log splitter for splitting.
It may be dangerous and may seriously damage the machine.
Do not attempt to split 2 pieces of logs at the same time. One of them may be thrown by the
machine which could cause serious injuries to the user.

FREEING A JAMMED LOG
Release both controls.
After the log pusher moves back and
completely stops at its starting position,
insert a wedge of wood under the
jammed log.
Start the log splitter to push the wedge
wood to go completely under the
jammed one.
Repeat above procedure with sharper
sloped wedges of wood until the log is
completely freed.
DANGER
Do not try to knock the jammed log off.
This will damage the machine or may
launch the log and cause serious injuries.
SHARPENING THE SPLITTING WEDGE
After using the log splitter for some time, sharpen the splitting wedge using a fine-toothed file and
smooth any burrs or crushed areas along the cutting edge.

RAM ADJUSTMENT
The Handy Log Splitters are fitted with a Ram Adjustment Knob which reduces any unnecessary
movement of the ram, allowing for quicker and more efficient use of the tool.
Warning: When adjusting the ram movement do not put your hands between the hand knob
and the log splitter, as accidental release of the Control Handle would cause the returning hand
knob and handle to trap and crush your hand against the splitter.
To adjust the ram movement, first undo the hand knob.
Then without a log on the work table depress the Control Handle and the start button.
When the gap between the ram and the splitting wedge is the intended size, release the start
button, but continue to hold the Control Handle to keep the ram in place.
Slide the hand knob along the pipe to set the gap size. The closer you move the Ram Adjustment
Knob towards the Log Splitter, and the more you slide it down the pipe, the smaller the gap will
be left between the ram and the splitting wedge.
If the gap is correct you should place the hand knob against the log splitter.
If the gap is too small you can leave an equivalent space between the knob and the log splitter
so that the ram returns further back.
If the gap is too small you will have to press the start button to reduce it before setting the Ram
Adjustment Knob.
Once you have set the hand knob at the desired
position, retighten it to adjust the movement of the
ram.
Make sure that your hand is clear of the hand knob
area. You can now release the Control Handle. The
ram should now return to the desired position
whenever you release the start button and Control
Handle. You can repeat these steps if further
adjustment is required.
Ram
Adjustment
Knob

CHECKING & REPLACING HYDRAULIC OIL
The log splitter is supplied with a full hydraulic oil tank,
however you should check if hydraulic oil needs to be added,
in case of leakage during transit.
You should also replace the hydraulic oil in the log splitter
after every 150 hours of use.
Periodically check the oil level to ensure it is between the 2
rooves around the Dipstick. To check the oil.
Stand the machine up at the wheel end.
Release the Dipstick located on the end of the machine
with an 8mm Allen Key.
If the oil level is lower than the bottom mark on the
Dipstick and refill the oil.
The oil level should be between the 2 grooves.
Follow the steps below to check and replace it.
Make sure all moving parts stop and the log splitter is
unplugged.
Using an Allen key, unscrew the Oil Drain Bolt with
Dipstick and remove it.
Tip the log splitter onto the Support Leg side over a 4
litre capacity container to drain the hydraulic oil off.
Tip the log splitter on the motor side.
Refill with fresh hydraulic oil as per the hydraulic oil
capacity indicated in the specifications.
Clean the Dipstick and put it back into the oil tank while
keeping the log splitter held upright.
Make sure the level of the refilled oil is just between the
2 grooves around the Dipstick.
Clean the Oil Drain Bolt before replacing it. Make sure
they are tightened to avoid leaks before lowering the
log splitter back to a horizontal position.
The following hydraulic oils or equivalent are recommend for the log splitter’s hydraulic
transmission system:
HANDY PARTS Logsplitter Oil WPL110 (1 Litre), WPL113 (5 Litre)
SHELL Tellus 22
MOBIL DTE 11
ARAL Vitam GF 22
BP Energol HLP-HM 22

TROUBLE SHOOTING
PROBLEM
PROBABLE CAUSE
REMEDY SUGGESTED
Motor running, ram
not moving
Incorrect specification
extension lead
Be sure the extension lead is no longer
than 10m and its cross-section is no
less than 2.5mm² to allow sufficient
current flow to the motor.
Fails to split logs
Log is improperly positioned
Refer to the “Operation” section for
log loading instructions.
The sizes or hardness of the log
exceeds the capacity of the
machine
Reduce the log size before splitting it
Splitting wedge is blunt
Refer to “Sharpening Splitting Wedge“
section to sharpen the cutting edge.
Oil leak
Locate leak & contact local Approved
Dealer
Unauthorised adjustment was
made on Max. Pressure Limiting
Screw. Lower max pressure
rating was set.
Contact local Approved Dealer.
The log pusher
moves jerkily, making
unfamiliar noises or
vibrating excessively
Lack of hydraulic oil
Check oil level for possible oil refilling.
Excessive air in the hydraulic
system.
Remove the bleed screw. Operate the
ram 5 or 6 times without a log in place.
Return the bleed screw to open
position and split the log. If the
problem continues contact the local
Approved Dealer.
Oil leaks around the
cylinder ram or from
other points.
Air sealed in the hydraulic
system while operating.
Loosen the Bleed Screw by 2 - 3
rotations to open position, do not
remove, before operating the log
splitter
Bleed Screw was not tightened
before moving the log splitter.
Tighten the Bleed Screw after use and
before moving.
The Oil Drain Bolt with Dipstick
is not tight.
Tighten the Oil Drain Bolt with Dipstick
with 8mm Allen Key.
The Hydraulic Control Valve
Assembly and / or seal(s) are
worn
Contact the local Approved Dealer
MAINTENANCE & STORAGE
Always ensure the Bleed Screw is fully tightened when the machine is not in use.
When not in use, the machine should be stored in a dry location. Keep the machine away from
children and others not qualified to use it. Avoid direct sunlight.
Do not store anything above or near the machine, where anyone might stand on the machine to
reach them.

PARTS DIAGRAM –THLS-6 (193893001)

PARTS LIST –THLS-6 (193893001)
Item No Part No Description Qty Item No Part No Description Qty Item No Part No Description Qty
1 TH114-38 Lever Mount Nut 1 37 TH114-11 Nut 2 73 TH114-71 Motor Cover 1
2 TH114-33 Nut Cap 3 38 TH114-8 Flat Wahser 2 74 TH114-57 Seal 1
3 TH114-36 Lever 1 39 TH114-7 Nut 2 75 TH114-54 Nut 1
4 TH114-37 Lever Knob 1 40 TH114-51 Valve Plug 1 76 TH114-55 Screw 1
5 TH114-34 Guard Plate 1 41 TH114-50 Washer 1 77 TH114-65 Motor 1
6 TH114-35 Nut 2 42 TH155-42 Valve Sleeve 1 78 TH155-78 Fan 1
7 TH114-28 Copper Gasket 4 43 TH155-43 Spring 5 79 TH155-79 Block turn 1
8 TH155-8 Screw 1 44 TH155-44 Adjusting Screw 1 80 TH155-80 Shroud 1
9 TH155-9 O-ring 1 45 TH114-40 Steel Ball 1 81 TH155-81 Flat Washer 2
10 TH155-10 Snap Washer – Shaft 146 TH114-29 Pressure Valve Spring 1 82 TH155-82 Spring Washer 3
11 TH155-11 Valve Retract Spring 1 47 TH114-30 Adjusting Screw 1 83 TH155-83 Screw 2
12 TH114-32 O-ring 1 48 TH114-53 Log Pusher Weldment 1 84 TH114-59 Support Leg 1
13 TH114-43 Valve Core Rod 1 49 TH114-52 Plastic Inserts1 1 85 TH155-85 Nut 5
14 TH155-14 Sliding Pressure Sensor Sleeve 1 50 TH114-23 Plastic Insert 2 1 86 TH114-60 Bolt 5
15 TH155-15 Sliding Pressure Sensor Sleeve Spring 1 51 TH114-24 Log Pusher 1 87 TH114-65 Cable & plug 1
16 TH114-27 Alumium Cover ( Rear ) 1 52 TH114-25 Nut 4 88 TH114-66 Motor Foot Nut 3
17 TH114-26 O-ring 1 53 TH114-22 Flat Wahser 5 89 TH114-67 Motor Foot 1
18 TH114-3 Piston 1 54 TH114-21 Screw 4 90 TH114-90 Electrical cable Housing 1
19 TH114-2 Piston Ring 1 55 TH114-88 Wheel cover 2 91 TH114-91 Screw 11
20 TH114-4 O-ring 1 56 TH114-89 Block turn 2 92 TH114-92 Switch Box cover 1
21 TH114-5 Spring 1 57 TH114-90 Wheel 2 93 TH114-93 Airproof underlay 1
22 TH114-15 Stud 4 58 TH155-58 Washer 2 94 TH114-94 Switch 1
23 TH114-1 Hydraulic Cylinder 1 59 TH114-39 Wheel shelf 1 95 TH114-95 Connection Terminal 1
24 TH114-61 Alumium Cover ( Front) 1 60 TH114-87 Bolt 6 96 TH114-96 Capacitor 1
25 TH114-12 Piston Rod Seal 1 61 TH155-61 Spring Washer 9 97 TH114-97 Switch Box 1
26 TH114-14 O-ring 1 62 TH155-62 Washer 9 98 TH114-98 Waterproof underlay 1
27 TH114-13 Bleed Screw 1 63 TH114-83 Gear Pump Cover 1 99 TH114-73 Motor Support Left Shoe 1
28 TH114-62 wahser groupware 1 64 TH144-64 Spring 2 100 TH114-72 Motor Support Right Shoe 1
29 TH114-63 Dipstick 1 65 TH114-76 Gear Housing Plate 1 101 TH114-75 Pin 2
30 TH114-6 Piston Rod 1 66 TH114-79 Circlip 2 102 TH114-82 Sping 2
31 TH114-9 Lift Handle 1 67 TH114-80 Gear Shaft 1 103 TH114-81 Sliding Sleeve 4
32 TH114-10 Screw 2 68 TH114-78 Steel Ball 1 104 TH114-84 Bolt 3
33 TH114-20 Frame Tube 1 69 TH114-77 Gear 2 105 TH114-105 Ram Stopper 1
34 TH114-19 Lead plank 2 70 TH155-70 Pin 1 106 TH114-106 Ram Stopper 3-star screw 1
35 TH114-17 Spring Washer 4 71 TH114-69 Washer 6
36 TH114-16 Screw 6 72 TH114-70 Bolt 3

PARTS DIAGRAM & LIST –THLSS-6 STAND
No.
Parts No.
Description
Specification
Qty
1
TH202-01
Bolt 8.8
M8*25
6
2
TH202-02
Nut
M8
6
3
TH202-03
Washer
8
6
4
TH202-04
Spring Washer
8
6
5
TH202-05
Support Leg - Front
CAA39011
1
6
TH202-06
Bolt 8.8
M10*25
4
7
TH202-07
Connector
CBA39107-A-1
1
8
TH202-08
Rear Axle
CBA39011
1
9
TH202-09
Support Leg - Rear
CAA39012
2

GJ HANDY & CO LTD USER WARRANTY POLICY
1. Users Statement of Warranty
Each new machine is warranted against defective material or assembly of material under normal
usage. The warranty applies to the original purchaser and covers faulty parts and the labour involved
in replacing and repairing those parts, which are of original manufacture.
2. Period of Warranty
All Webb, Handy Pro (Brushcutter & Long Handle Hedgecutter only) and Sanli domestic products
2 years from the original date of sale to the first domestic user.
90 days from the original date of sale to the professional/commercial user.
90 days from the original date of sale when used for hire.
Engines as per the manufacturer’s warranty statement which will be supplied with the machine.
1 year from the original date of purchase for Replacement Spare Parts (unless normal wear & tear
component, which are covered for 90 days).
All machines’ must be serviced within the first 12 months from the original date of purchase to
comply with the warranty, failure to do so will invalidate the 2nd year of the warranty.
A reduced warranty period of ninety days applies to those items which are subject to normal wear
and tear (e.g. wheels, tyres, cutter bars, cylinders, bottom blades, belts, cables, grass bags, spark
plugs).
All Handy, Handy Pro (All others), Mowerland and Q-Garden domestic products
1 year from the original date of sale to the first domestic user.
90 days from the original date of sale to the professional/commercial user.
90 days from the original date of sale when used for hire.
Engines as per the manufacturer’s warranty statement which will be supplied with the machine.
1 year from the original date of purchase for Replacement Spare Parts (unless normal wear & tear
component, which are covered for 90 days).
A reduced warranty period of ninety days applies to those items which are subject to normal wear
and tear (e.g. wheels, tyres, cutter bars, cylinders, bottom blades, belts, cables, collection bags,
spark plugs).
All warranty repairs must be undertaken by an authorised service dealer.
These dealers have been accredited by GJ Handy & Co Ltd and agree to only use genuine parts and
follow our repair procedures.
Version 2 06-15
Table of contents
Other The Handy Log Splitter manuals

The Handy
The Handy THFLS User manual
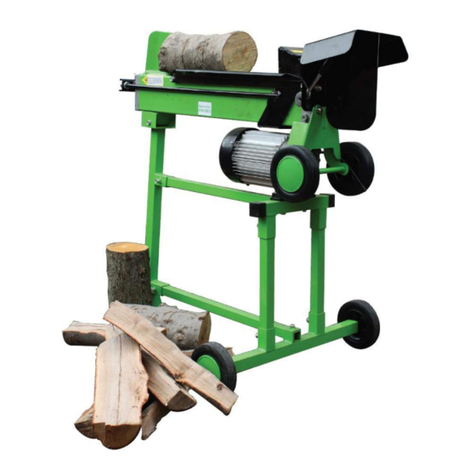
The Handy
The Handy THLSS-B Installation and maintenance instructions

The Handy
The Handy THMLS Installation and maintenance instructions
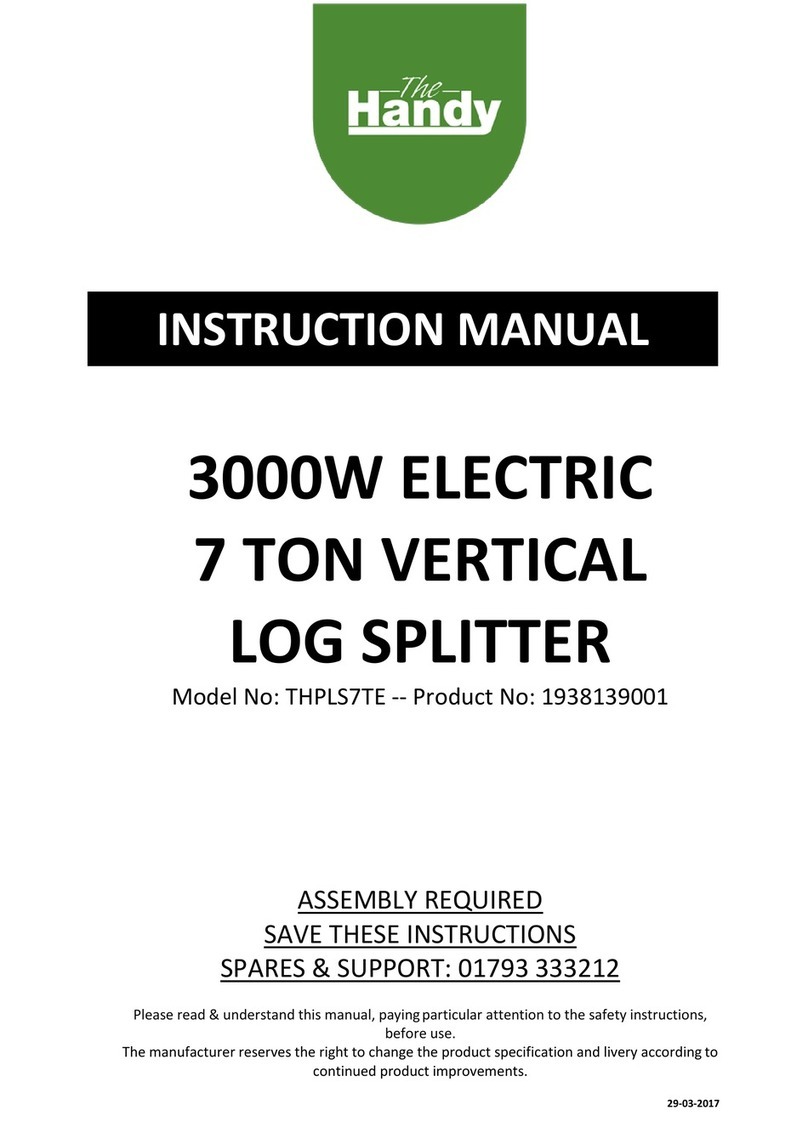
The Handy
The Handy THPLS7TE User manual
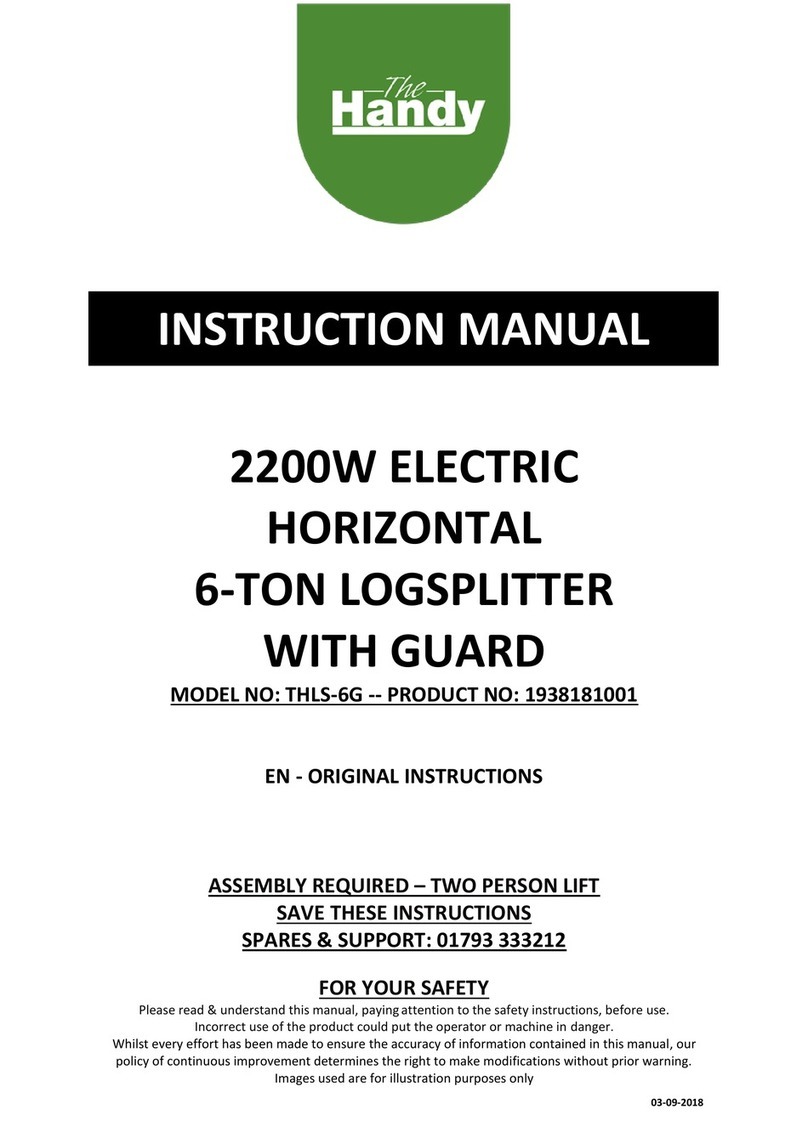
The Handy
The Handy THLS-6G User manual
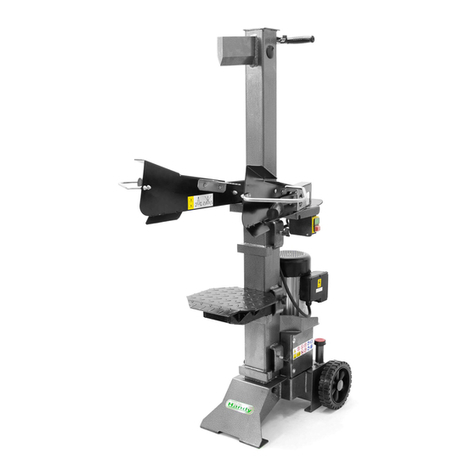
The Handy
The Handy THLSV6 User manual
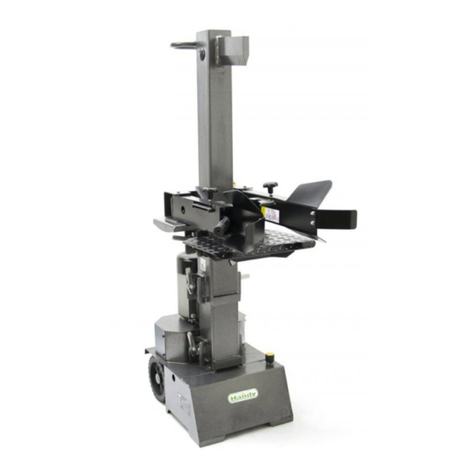
The Handy
The Handy THPLS7TE Installation and maintenance instructions
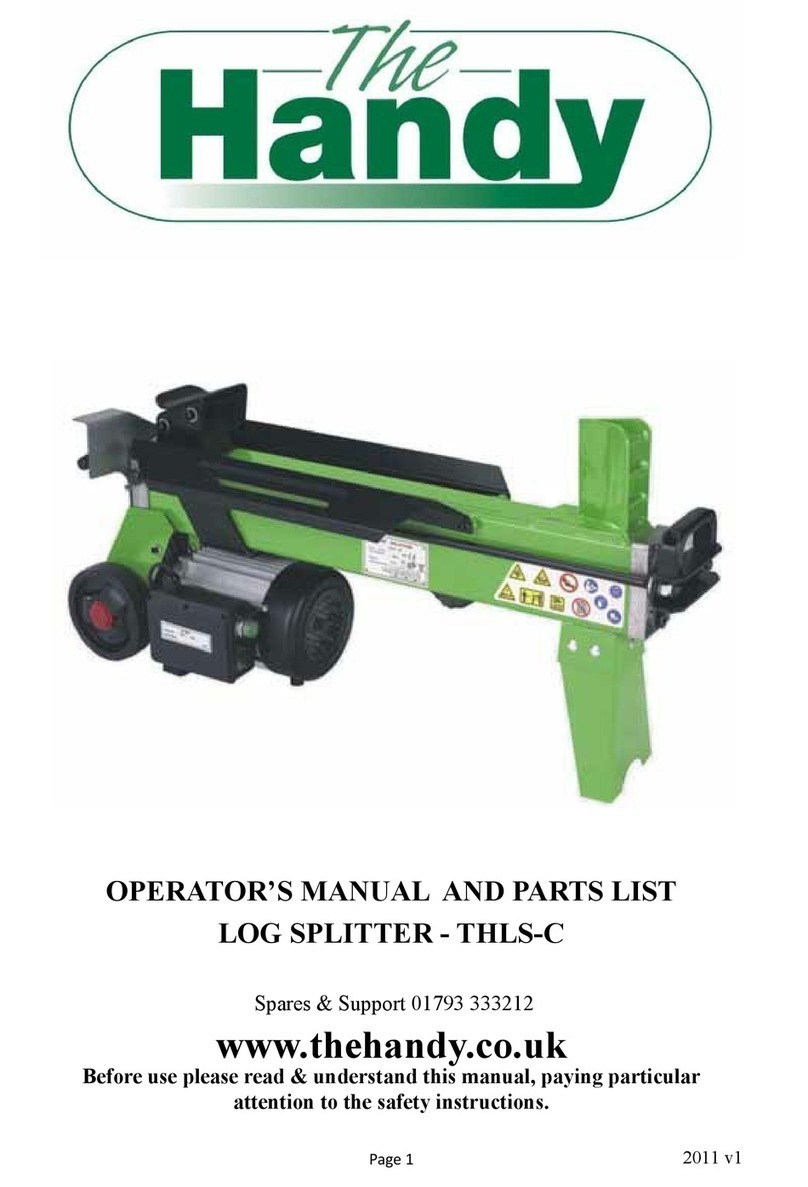
The Handy
The Handy THLS-C Installation and maintenance instructions
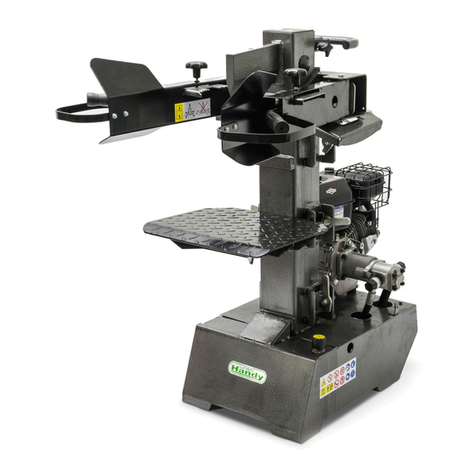
The Handy
The Handy THPLS7TP Installation and maintenance instructions
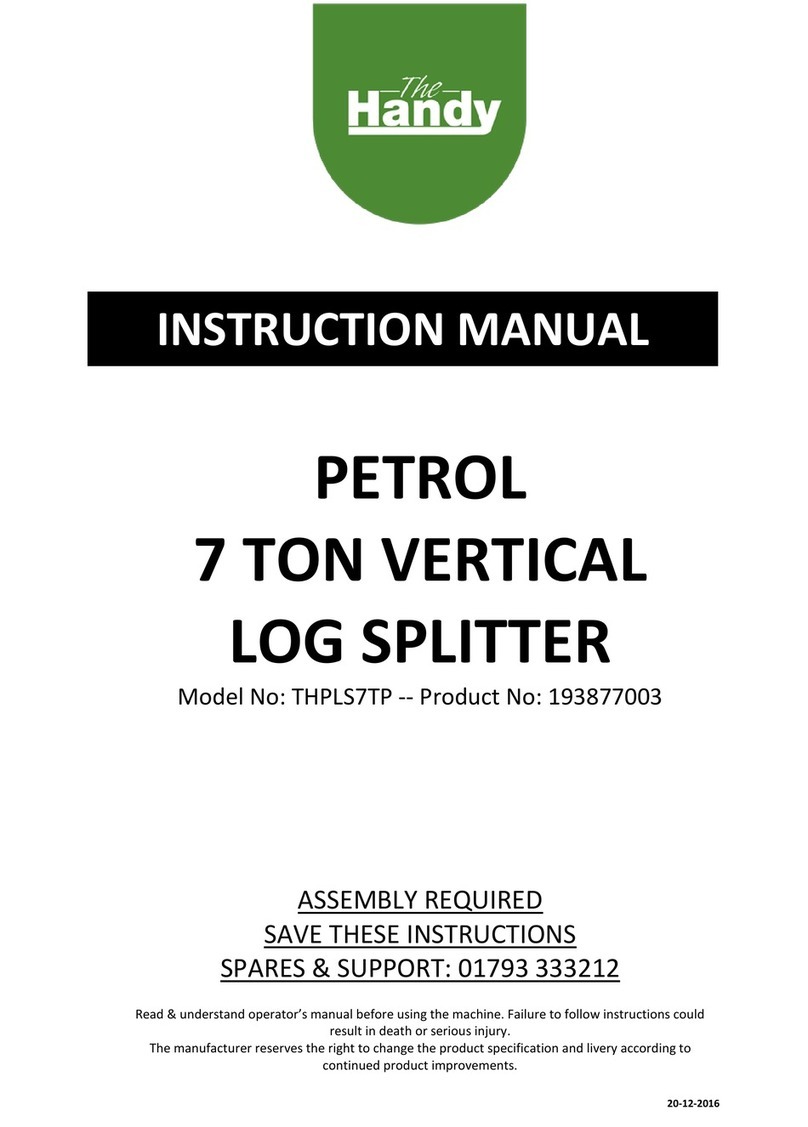
The Handy
The Handy THPLS7TP User manual