Vivace VVP10 Operating manual

1
CALIBRATION AND MAINTENANCE GUIDE
VVP10
VALVE POSITIONER
1 FUNCTION DETAILS
VVP10 positioner controls the air outlets for the actuator/valve assembly using the nozzle-vane system with magnetic
coil, where the supply pressure passes through an internal pressure regulator, supplying pressure to the coil, which
generates the pilot for controlling a directional spool valve. See the schematic of this system in Figure 1.1, below.
Figure 1.1 – Diagram for pneumatic control.
The regulator for supply pressure (between 20 and 140 psi) limits the pressure in the coil to the range of 18 to 22 psi.
After passing through the nozzle-vane, which contains a magnetic coil and a metallic blade, the pilot pressure varies
between 3 and 12 psi (ideally), for currents in the coil between 0 and 1.6 mA, according to the desired control signal,
modulating the spool valve.
Figure 1.2 – Spool valve positioning.

2
Figure 1.2 shows three positions of the spool valve: the upper figure shows its equilibrium position, that is, controlling
in intermediate positions, when PV = SP. Note that both outputs are closed, stabilizing the pneumatic control. In the
figure on the left, the positioning of the spool valve feeds output 1 (OUT1), caused by an increase in the electrical
current of the coil, causing the blade to approach the nozzle and, consequently, an increase in the pilot pressure. So,
the force of the spring is overcome, and the spool moves to the left.
Similarly, in the figure on the right, the positioning of the spool valve feeds output 2 (OUT2), caused by a decrease in
the electrical current of the coil, causing the blade to move away from the nozzle and, consequently, a decrease in the
pilot pressure. So, the force of the spring overcomes the pressure, and the spool moves to the right. This is actually
the positioner's safety position in the case of an electrical failure, since there will be no current in the coil and the pilot
pressure will be minimal and insufficient to overcome the force of the spring, sending all the supply air to output 2
(OUT2).
2 REGULATOR CALIBRATION
For the calibration of the internal pressure regulator, we must mount the calibration device with pressure gauge (sold
separately). To do this, simply remove the cap screw on the left and insert the device, as shown in Figure 2.1. Then,
apply 40 psi of pressure at the positioner inlet and, with the aid of an allen wrench, adjust the regulator screw, after
loosening the lock nut, until the device pressure gauge shows a pressure between 18 and 22 psi – Figure 2.2.
Figure 2.1 – Calibration orifices location.
Figure 2.2 – Regulator pressure adjustment – around 20 psi.

3
Next, we must increase the positioner supply pressure to 100 psi, verifying that the pressure in the regulator pressure
gauge does not vary significantly (below 3 psi). After confirmation, simply lock the lock nut to fix the screw position,
without changing the regulated pressure. Finally, we remove the calibration device and replace the cap screw..
3 COIL CALIBRATION
For the positioner coil calibration, we must use the coil control parameter (CWR), read with a HART configurator such
as the DTM, for example. As a reference, the CWR parameter will indicate 100% when the coil has maximum electrical
current (1.6 mA) and 0% when it has minimum current (0 mA). Therefore, in the positioner control (PV = SP), the ideal
is that the CWR value is close to 50% (current at 0.8 mA).
In a similar way to the pressure regulator calibration, we must remove the
calibration cap screw from the coil, on the right – Figure 2.1. Then, simply
insert the gauge calibration device and apply supply pressure to the
positioner between 40 and 100 psi.
With the positioner turned off (no power supply), we must adjust the
pressure on the device's gauge between 3 and 4 psi. To do this, just
loosen the coil lock nut and adjust the screw with the help of an allen
wrench.
Figure 3.1 – VVP10 magnetic coil location.
Figure 3.2 – Coil current adjustment using DTM.
To manually vary the current in the coil using the positioner DTM, access the Maintenance and Coil Control menu –
see Figure 3.2.
To generate manual control of coil current, we must disable PID control. Next, when generating 0% on the CWR, we
must verify that the pilot pressure generated is between 3 and 4 psi. Next, generate 100% on the CWR (1.6 mA) and
confirm that the pressure generated is greater than 12 psi. Note in Figure 3.3 that the pilot pressure is below 10 psi
with the coil generating 100% on the CWR, requiring adjustment.
Figure 3.3 – Pilot pressures for CWR 0% and 100%, respectively.

4
If the pilot pressure variation is low, it will be necessary to open the coil to clean the blade and nozzle, repeating the
calibration process. When the pilot pressure variation is satisfactory, simply remove the calibration device and reinsert
the cap screw.
To successfully complete the coil calibration process and fine tune the calibration, we must validate the CWR
measurement during positioner control. So, with the positioner mounted on a small actuator, run the complete
automatic calibration (Full Setup) and set SP = 50% (or any value different from 0% and 100%), waiting for the control
(PV = SP).
Figure 3.4 – Monitoring of CWR with DTM on VVP10 HART.
The CWR value in this condition should preferably be close to 50%, but the limits of 30% and 70% can be used as
acceptable. If it is necessary to decrease the CWR (lower the coil control current), we must turn the screw clockwise,
bringing the blade closer to the nozzle. To increase the CWR (increase the control current of the coil) we must turn the
screw counterclockwise, moving the blade away from the nozzle. For this fine adjustment, the CWR parameter can be
monitored via DTM (Figure 3.4) or by the positioner display itself, in the “CONTROL VALUE” parameter. At the end of
the process, lock the counter nut of the coil screw carefully so that there is no variation in the fine adjustment of the
CWR, performed above.
4 OTHER MAINTENANCES
In addition to regulator and coil calibrations, positioner filter elements
and silencers may require cleaning or replacement over time.
Consider your exchanges in cases of degradation.
In addition, the restriction screw can also be clogged by dirt as it has
a hole of only 0.3 mm.
In this case, the air passage from the regulator to the coil will be
compromised. To remove it, simply unscrew it and remove it with the
help of a pair of needle-nose pliers. After cleaning, for reassembly,
pay attention to the correct positioning of the sealing rings
Figure 4.1 – Other maintenance elements.
Figure 4.2 – Restriction screw with sealing rings.
Table of contents
Popular Valve Positioner manuals by other brands
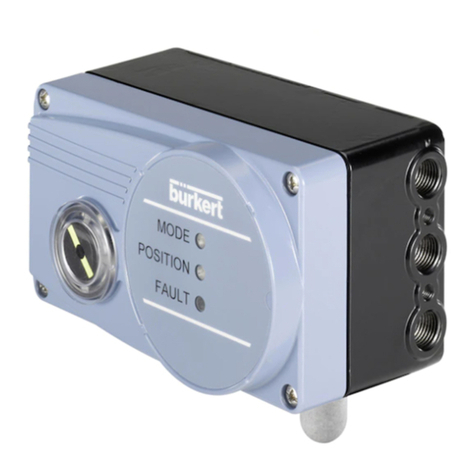
Burkert
Burkert 8791 operating instructions
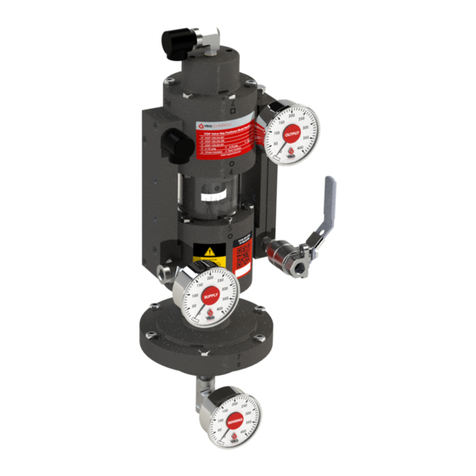
VRG Controls
VRG Controls VGP Series instruction manual
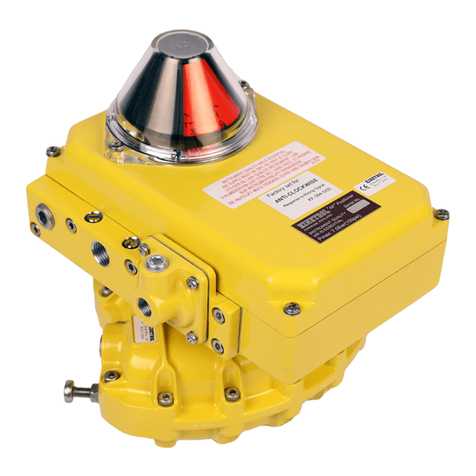
Kinetrol
Kinetrol AP Installation & maintenance
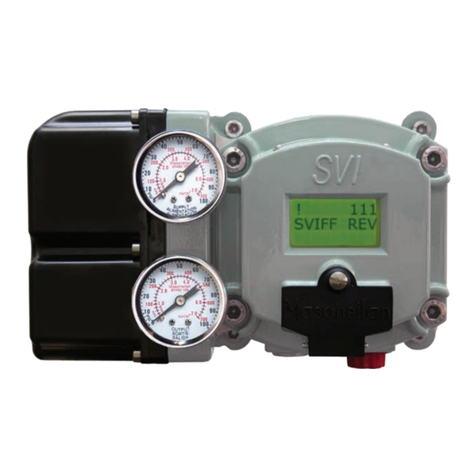
Baker Hughes
Baker Hughes Masoneilan SVI FF quick start guide
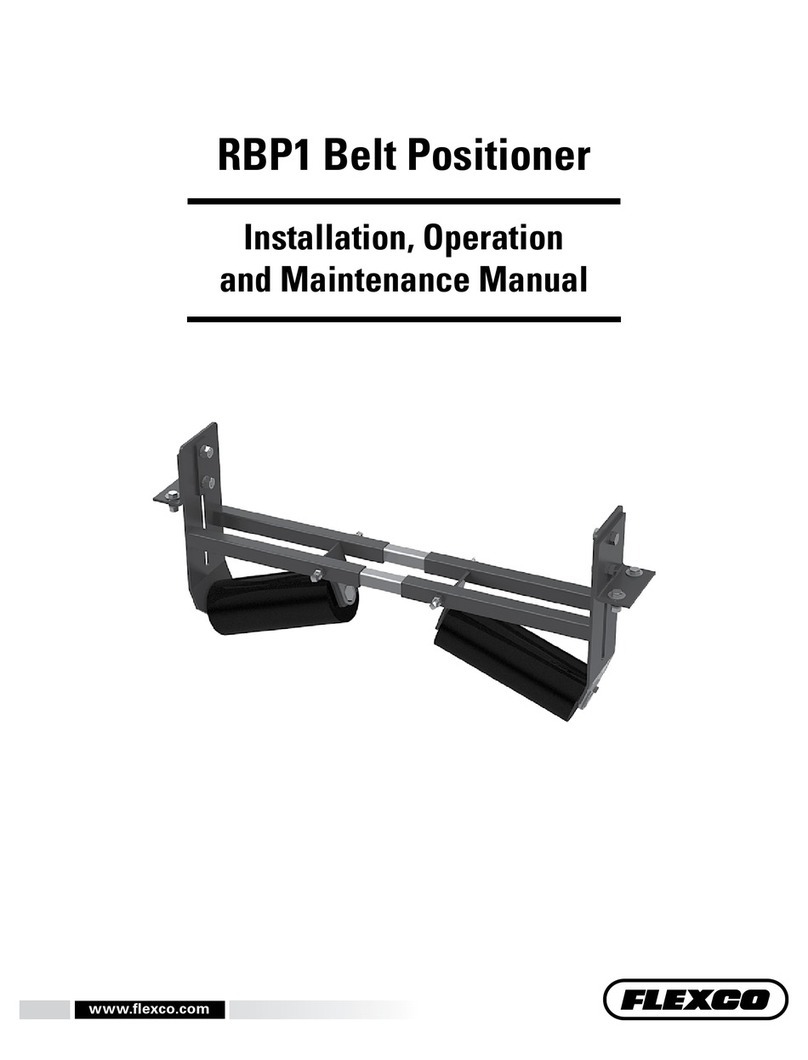
Flexco
Flexco RBP1 Installation, operation and maintenance guide
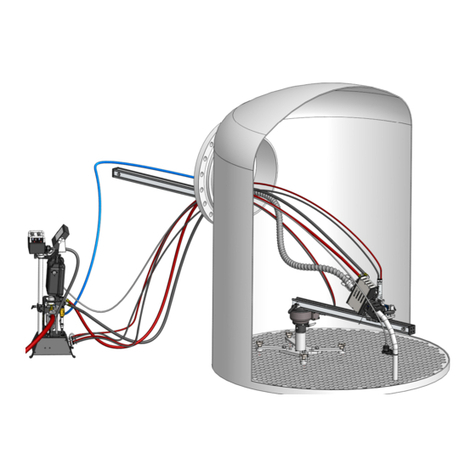
StoneAge
StoneAge PROPOSITIONER PROP-DBP user manual