Winget 500R Instruction manual

ISSUE 10 2016
WORKSHOP MANUAL
500R
WINGET LIMITED
PO BOX 41
EDGEFOLD INDUSTRIAL ESTATE
PLODER LANE
BOLTON
LANCS
BL4 0LR
Tel:-++ 44 (0) 1204 854650
Fax:- ++ 44 (0) 1204 854663
service@winget.co.uk
part[email protected].uk
www.winget.co.uk

WORKSHOP MANUAL
500R
WINGET REVERSING DRUM CONCRETE MIXERS
ISSUE 10 2016
CONTENTS
Section 1 Introduction
Section 2 Repair and Service Procedures
Section 3 General Arrangement Dimensions
Section 4 Service Schedules
Lubrication Diagram
Section 5 Hydraulic Circuit Diagrams
Section 6 Wiring Diagrams
Section 7 Noise Levels
Section 8 Special Tools
Section 9 Hydraulic Control Valve
Service Manual (Where available)
Section 10 Parts Listings
Section 11 Batchweigher Maintenance Instructions
Section 12 Reversing Gearbox Manual
Section 13-18 Blank
IMPORTANT Engine Change
From mid 2004 the Lister Petter TS2 and TS3 engines were replaced by the Lister Petter
TR2 and TR3 engines. The TR range of engines is completely interchangeable with the
TS range and consumable items such as filter elements are identical. There are some
internal component differences and when ordering spares it is important to state whether
it is a TS or TR engine.
Instructions and notes found throughout this manual which refer to TS engines are also
applicable to the TR engine

WORKSHOP MANUAL
500R
SECTION 1
INTRODUCTION

WORKSHOP MANUAL
500R
WINGET REVERSING DRUM CONCRETE MIXERS
ISSUE 10 2016
Introduction
The following procedures should enable experienced service personnel to strip, repair
and rebuild Winget 500R Reversing Drum Concrete Mixers in a safe and competent
manner. The procedures are not intended to be used by personnel who are unfamiliar
with the product nor mechanically inexperienced.
It is assumed that personnel are aware of Health and Safety Regulations which should
be applied to all working practices, but the following should act as a reminder.
Ensure all work tools are in good condition.
Always wear Safety Spectacles when using Soft or Hard Faced Hammers, Chisels or
when using Air Tools. Wear Safety Spectacles when cleaning hardened concrete or
mortar off components.
Do not misuse Air Lines and be aware of the damage Compressed Air can cause if
misused.
Always make sure lifting equipment is in good condition and the Safe Working load
exceeds the weight of the components to be lifted.
Oils, Fuels, Silicone Sealers and Open Gear Lubricants can cause skin diseases if
allowed to contaminate the skin. Always apply barrier creams, wear suitable protective
clothing, or when contamination is unavoidable clean the area with soap and water as
soon as possible. Do not use thinners or other solvents to clean skin.
Health and Safety is a matter of common sense. If common sense is applied correctly
Health and Safety can be improved and the risk of accidents reduced.
Refer to the Parts Listings in Section 10 or the Parts & Operators Manual for a guide to
the correct sequence for assembling components and sub assemblies.
It is assumed for the purposes of this manual that the machine is standing on firm level
ground and is horizontal in both planes.
Left hand and Right Hand views are taken when looking directly at the Feed Hopper.
Whilst every effort is made to ensure the contents of this manual are accurate Winget
Limited accept no responsibility for errors or omissions and reserve the right to alter
specification without prior notification in which case certain sections may then no longer
apply.

WORKSHOP MANUAL
500R
SECTION 2
REPAIR & SERVICE
PROCEDURES

WORKSHOP MANUAL
500R
WINGET REVERSING DRUM CONCRETE MIXERS
ISSUE 10 2016
Lifting Points
Lifting Points capable of supporting the weight of the Mixer are incorporated in both of
the Water Tank Supports just below the height of the Drum Top Guard.
The Lifting Points are highlighted with an ISO ‘Hook’ symbol adjacent to each Point.
On Military/Nato mixers the Lifting Points are also painted white.
The Hopper also incorporates Lifting Points to assist in removing the Hopper. The L/H
Point is used to secure the Hopper Safety Chain which is attached to the raised Hopper
during maintenance work. The Hopper Lifting Points are not highlighted to avoid
confusion with the main lifting points. On no account must the Hopper Lifting Points be
used to support the weight of the mixer.
Drawbars – Standard & Military/Nato
The Drawbars are retained to the Front axle by two ‘L’ shaped retaining pins which are in
turn secured by two lynch pins c/w chains which are inserted through the retaining pins
once the drawbar is in position. To remove the drawbar first remove the lynch pins,
withdraw the retaining pins and lift the drawbar clear, refit the retaining pins and prevent
their loss by refitting the lynch pins. Reverse the procedure to refit the drawbar.
Military/Nato Towing Eye (Used with Military/Nato Drawbars)
Remove the split pin, castle nut and flat washer retaining the eye in the drawbar.
Remove the eye. To refit reverse the above procedure, do not fully tighten the nut, allow
the eye to rotate in the drawbar. New eyes will require drilling for the split pin when fitted
in place.
Jack Legs
To remove a Jack Leg either jack up and support the machine or using suitable lifting
equipment lift the machine. Pull out the retaining pin remove the leg. Refit in the
reverse order.
Military/Nato machines have an additional security measure in the form of a lynch pin
through the jack leg retaining pin to prevent the jack leg dropping unintentionally.
Anti-Bounce Bracket
An Anti-Bounce Bracket is fitted between the L/H side of the Hopper Cradle and
Mainframe whilst transporting the mixer to prevent the Hopper bouncing and causing
damage to the Batchweigher Loadcell and other components.
One end of the Hopper Anti-Bounce Bracket is bolted to the Hopper Cradle, the other
end is retained by the Jack Leg retaining pin.

WORKSHOP MANUAL
500R
WINGET REVERSING DRUM CONCRETE MIXERS
ISSUE 10 2016
To remove the Hopper Anti-Bounce Bracket, start the engine and raise the Hopper very
slightly to release its weight off the bolt and jack leg retaining pin (it is normal for the
Hopper to settle slightly during transportation).
Remove the bolt, pull out the pin and lift the Anti-Bounce Bracket clear. Refit in the
reverse order.
On no account must attempts be made to fully raise the Hopper whilst the Anti-Bounce
Bracket is in place.
Pneumatic Wheels, Stub Axles, Hubs
The complete Wheel, Stub axle and Hub assemblies are retained to the axles by four
bolts, two positioned vertically and two horizontally. To remove the assemblies, support
the machine on the jack legs, remove the bolts and lift the assemblies clear. If fitted take
care not to lose the tapered washers. Reverse the procedure to refit.
Wheels – Pneumatic
To change a wheel, first slacken the five nyloc nuts, jack up the machine supporting the
weight on a jack leg. Remove the nuts and wheel. To refit, reverse the procedure.
Hubs
Remove the wheel as described previously. Knock off the dust cap. Remove the split
pin and nut, pull off the hub assembly complete with bearings and oil seal. Knock out
the bearings and oil seal clean the hub and shaft. Pack the new bearings with grease.
Fit the new bearings and oil seal into the hub. Coat the shaft with copperslip, push the
hub complete with bearings onto the shaft. Fit the flat washer and castle nut and tighten
the nut. Back off until the wheel spins freely with no end float. Align the nut with the
cross drillings in the shaft, fit the split pin. Refit the wheel as described previously.
Steel Wheels, Stub Axles and Hubs
To remove the complete assembly refer to Pneumatic Wheels, Stub axles and Hubs.
Wheels – Steel
Steel wheels are retained to simple stub axles using a collar retained by a single cross
bolt. To remove the wheel, jack up the machine, remove the bolt, remove the collar and
lift the steel wheel clear. Reverse the procedure to refit coating the shaft, bore of he
steel wheel and collar with copperslip.

WORKSHOP MANUAL
500R
WINGET REVERSING DRUM CONCRETE MIXERS
ISSUE 10 2016
Front Axle and Pivot Bracket
To remove the axle or pivot bracket, support the front of the machine and fully raise the
jack legs. Remove the drawbar, stub axles, hubs and wheel assemblies as described
previously. Remove the split pins and washers retaining the tie bar between the axle and
mainframe, support the axle and remove the tie bar, remove the split pins, and washers
though the pivot pin, knock out the pin. Remove the supports and lift the axle clear of
the pivot bracket. The pivot bracket may be held in place by either a split pin and
washer or nut and bolt. Reassemble in the reverse order coating pins etc. with
copperslip, replacing damaged split pins.
Water Tank Removal (Where fitted)
Turn off and disconnect the water supply. Remove the split pin and disconnect the
operating rod. Unbolt and remove the outlet pipe. Unbolt the tank and using suitable
lifting equipment lift the tank clear of the mainframe. Refit in the reverse order.
For an explanation of the Water Tank operation and repair instructions see pages 25- 29.
Flowmeter Removal (Where fitted)
The Flowmeter is mounted on a bracket on the L/H side of the mainframe and is
connected to the inlet pipe at the drum charge mouth by a 1.5 bore rubber hose. The
meter is a mechanical device featuring a reset facility and includes a water on/off valve
and an inline strainer which is removable for cleaning. To Remove the Meter disconnect
the rubber hose by either slackening one of the hose clamps or removing one of the
threaded connectors, remove the two ‘U’ bolts securing the meter in place and lift the
meter clear. Reverse the procedure to refit. Note:- the meter itself contains no user
serviceable components.
Drum Edge Rollers
Where fitted remove the water tank as previously described. Support the front of the
drum to prevent it falling forward suddenly when the Edge Roller assembly is removed.
Release the adjusting screw then unbolt and remove the edge roller assembly taking
care not to lose the shim packers. Remove the setscrews holding the rollers into the
housing and remove the rollers. Support the rollers in a soft jawed vice remove the
circlips and using a suitable drift, knock the shafts through the bearings and out of the
rollers. Drift the bearings out of the rollers.
Using a sharp instrument remove the seals from the new bearings and pack with a good
quality grease, refit the seals.

WORKSHOP MANUAL
500R
WINGET REVERSING DRUM CONCRETE MIXERS
ISSUE 10 2016
Reassemble in reverse order taking care not to forget the ‘V’ seals. When assembling
the rollers back into the housing do not fully tighten the setscrews until the assembly has
been refitted and final adjustment carried out.
Refit the assembly onto the drum housing. Adjust the height of the assembly using the
shims so the rollers do not foul the drum circumference and the drum gear ring will not
foul the assembly.
Adjust the rollers against the track ring so that a total 1.5mm clearance exists between
the rollers and ring. Tighten the setscrews. Lock the adjusting screws with locking wire.
Note:
Incorrectly setting the rollers in relation to the track ring will result in premature bearing
failure and/or excessive wear of the track ring and idler rollers.
As a final check that all adjustments are correct remove the support from below the
drum, engage either forward or reverse drive and crank the engine rotating the drum
checking visually that neither a foul condition nor tight rollers exist.
If removed refit the water tank assembly.
Drum Removal
It is necessary to remove the Drum for replacement of the Drum Gear Ring it is also
strongly recommended that the Drum is removed if repair or replacement of the Idler
Rollers is necessary.
Remove either the Water Tank or Flowmeter and Water Inlet Pipe and Drum Edge
Rollers as described previously.
On machines fitted with a Dragline remove the Mast and Cable. Disconnect the Wire
Rope from the Shovel and wind back onto the Winch Motor. Mark for identification
purposes the hoses to the Winch Motor and disconnect both the hoses from the Motor.
Fit blanking caps and plugs to both the hoses and Winch motor adaptors to prevent the
ingress of foreign matter. Disconnect the Electrical Cable and using suitable lifting
equipment support the Dragline Winch Motor Bracket, remove the retaining setscrews
and nuts and lift the assembly clear. Where a Batchweigher is fitted unbolt the Gauge
from the left hand Water Tank Support and stow in the Mainframe (Do not disconnect
the small bore pipe).
Release the Engine/Fuel Tank Cover from the Right Hand Water Tank Support, if a UK
step is fitted, separate the top step from the rest of the step assembly.
Unbolt both Water Tank Supports and lift clear using suitable lifting equipment.
Unbolt and lift off the Drum Top Guard.

WORKSHOP MANUAL
500R
WINGET REVERSING DRUM CONCRETE MIXERS
ISSUE 10 2016
Attach suitable lifting gear to the Drum Assembly (The Drum weighs approximately ¾
tonne when clean) and lift out of the Mainframe. It may be necessary to remove the
Drum Mouth Extension to allow attachment of the lifting equipment.
Reassemble in reverse order, following the instructions for adjusting the Drum Edge
Rollers.
Drum Gear
Remove the Drum as described previously. Stand the Drum Assembly on the charge
mouth. Remove the Socket Headed Capscrews securing the Gear to the Drum. Using
suitable lifting equipment lift the Gear clear of the Drum.
Drum Cone Extensions
The various mouth extensions either Standard Steel Cone, Steel Extension Cone or
Rubber Extension Cone bolt to the Drum mouth. Removal is simply a matter of
removing the ring of bolts and lifting off the mouth extensions.
Drum Blades
Drum Blades can be changed with the Drum in Situ. The Blades are bolted in place and
if the Drum interior is clean replacement is fairly straightforward although two pairs of
hands are necessary. Unbolt and discard the old Blades and bolt the new Blades in
their place using new bolts.
Take care if using oxyacetylene cutting equipment to remove corroded bolts for the
concrete can “explode” violently spitting pieces of concrete. Wear suitable safety
goggles or spectacles. Do not breathe in the fumes generated by the cutting and burning
process ensure the drum is adequately ventilated and wear suitable air fed breathing
apparatus.
Idler Roller Non Drive R/H
Whilst it is recommended that the Drum is removed to enable the Rollers Assemblies to
be replaced It is possible to remove the Rollers with the Drum in situ provided great care
is taken.
Remove the Water Tank or Flowmeter and the Edge Rollers as described previously.
Remove the Inspection Covers from each side of the Drum Housing. Block up the Drum
taking the weight off the Roller Assemblies or support the weight of the Drum using
suitable lifting equipment.
Remove the Stop Bracket secured with two M10 bolts, unbolt the Rear Carrier Bracket,
remove the nuts and washers from the bolts securing the Front Carrier Bracket but do

WORKSHOP MANUAL
500R
WINGET REVERSING DRUM CONCRETE MIXERS
ISSUE 10 2016
not remove the bolts which are supporting the Front Bracket and preventing the
complete assembly dropping into the Drum Housing.
Carefully manoeuvre the Roller Assembly through the access hole, the assembly is quite
heavy and extra hands or suitable lifting equipment are recommended. Take care not to
lose the Shim Pack below the rear carrier bracket.
Remove the bolt securing the Rear Carrier and the grubscrew securing the Front Carrier
remove both from the shaft.
Remove the setscrews holding the Oil Seal Housing/Bearing Retainer to each side
of the Roller, take care not to lose or mix up the shims.
Support the Roller and using a suitable soft faced hammer knock the shaft and Bearings
out of the Roller, remove the Outer Bearing Cones from within the Seal
housings/Bearing Retainers. Secure the shaft in a soft jawed vice and remove the Taper
Roller Bearing Cages from the Shaft.
Fit the new Inner Bearing Cages to the shaft (tapering outwards) and the Outer Cones
into the Seal Housings. Fit the Shaft and bearings into the Roller. Slip a 0.60 thou thick
shim (usually cream in colour) onto the front Bearing Retainer and secure in place on the
Front of the Roller. Turn the roller over, slip the remainder of the shim pack onto the rear
Seal Housing/Bearing Retainer and secure to the Roller, adjust the shimming behind the
rear Housing to give a bearing pre-load of between 0.000” to 0.002” thou. Check the
shaft rotates freely within the bearings.
Charge the roller with grease until it can be seen to squeeze out through both bearings,
carefully fit the new Oil Seals into both Bearing Retainers. Refit the Front and Rear
Carrier Brackets. Using suitable lifting equipment, lift the Roller Assembly back into the
Mainframe, loosely secure the front Carrier to the Mainframe with the four nuts, bolts and
washers. Insert the Shim pack under the Rear Carrier and Shim the Roller and Shaft
until it is horizontal.
Place a straight edge across the rear face of the Roller and ensure it is square with the
opposite roller. Tighten the retaining bolts. Refit the stop bracket. Remove the Drum
supports and lower the Drum back onto the rollers.
Refit the Edge Rollers and Water Tank or Flowmeter as described previously. Run the
mixer, checking operation of the Drum. Coat the Rollers/Gear with open gear lubricant.
Stop the engine. Replace the inspection covers.
Idler Roller/Drum Drive Pinion L/H
Whilst it is recommended that the Drum is removed to enable the Roller Assemblies to
be replaced it is possible to remove the Rollers and Drum Drive Shaft with the Drum in
situ provided great care is taken.

WORKSHOP MANUAL
500R
WINGET REVERSING DRUM CONCRETE MIXERS
ISSUE 10 2016
Remove the Water Tank or Flowmeter and the Drum Edge Rollers as described
previously. Remove the Inspection Covers from each side of the Drum Housing. Block
up the Drum taking the weight off the Roller Assemblies or support the weight of the
Drum using suitable lifting equipment.
Remove the Chain Cover, Drive Chain and Upper Sprocket as described on page 11.
Remove the Stop Bracket secured by two M10 bolts, unbolt the Plummer Block and
Bearing Assembly, remove the nuts securing the front Bearing Carrier/Housing but do
not remove the bolts which are supporting this housing and preventing the complete
assembly dropping into the Drum Housing.
Carefully manoeuvre the Roller Assembly through the access hole, the assembly is very
heavy and it is recommended that either an additional pair of hands or suitable lifting
equipment are used. Take care not to lose the shimpack.
Release the Grub Screw and remove the Plummer Block and Bearing off the rear of the
Shaft. Remove the Front Bearing Carrier/Housing off the shaft and retrieve the spacer.
Using a soft faced hammer knock the cast Drive Pinion off the shaft, remove the Parallel
Key and ‘V’ Seal.
Following the procedure for the R/H Idler Roller, strip and rebuild the Roller Shaft and
Bearing.
Refit the Plummer Block and Bearing to the rear of the Shaft and lock the Grubscrew.
Smear the ‘V’ Seal with grease and fit both the ‘V’ Seal and Parallel Key to the shaft.
Slide home the cast Drive Pinion and spacer. Clean all traces of silicone sealer from the
front Bearing Housing/Carrier and Mainframe mating surfaces. Refit the Housing to the
Shaft, note the grease nipple is located on the top face. Apply a bead of silicone to the
housing face.
Lift the Roller Assembly back into the Mainframe loosely securing the front
Carrier/Housing. Insert the Shim Pack below the Plummer Block and Bearing shim the
Roller and Shaft until it is horizontal.
Place a straight edge across the rear face of the Roller and ensure it is square with the
opposite roller. Tighten the retaining bolts. Refit the Stop Bracket.
Refit the Upper Drive Sprocket, Drive Chain and Chain Cover as described previously.
Remove the Drum supports and lower the Drum back onto the Rollers.
Refit the Edge Rollers and Water Tank or Flowmeter as described previously. Run the
mixer, check the operation of the Drum coating the Rollers/Gear with open gear
lubricant. Stop the engine and replace the inspection covers.

WORKSHOP MANUAL
500R
WINGET REVERSING DRUM CONCRETE MIXERS
ISSUE 10 2016
Drive Chain Adjustment
The Drive Chain is located behind the cast cover on the front of the Mainframe. The
cover contains an inspection aperture through which the Chain Tension can be checked.
The Tension is correct when the chain deflects 8mm-12mm mid way between the
sprockets.
To adjust the chain, remove the Inspection cover on the L/H side of the Drum Housing.
Slacken the three nuts on the lower Bearing Bracket, do not slacken the nuts too much
to avoid oil leaks following chain adjustment. Using the adjusting screw above the
Bearing Bracket increase or decrease tension on the chain as necessary. Lock up the
nuts. Replace the Inspection Covers.
Drive Chain/Sprocket Replacement
Drain the oil from the Chain case. Remove the setscrews and lift the Cast Chain Cover
from the Mainframe. The joint between the Chain Cover and Backplate/Mainframe is
made with Silicone Sealer and the Cover may require gently prising from the Mainframe.
Slacken the Adjustable Bearing Bracket as previously described to release the Chain
Tension. Disconnect the Chain split link and remove the Chain.
To remove the upper sprocket cut the locking wire, remove the special screws and
retaining washer, pull off the sprocket. Take care not to lose the key. In some cases it
may be necessary to use a suitable two legged puller.
To remove the Lower Sprocket remove the Circlip and Grubscrew. Pull off the sprocket
taking care not to lose the key. In some cases it may be necessary to use a suitable two
legged puller.
Reassemble in the reverse order.
Re-tension the Chain as previously described on page 10.
Ensure the joint faces on the Cover and Backplate are clean. Apply a generous bead of
Silicone Sealer to the Cover, allow the sealer to cure for a few minutes then refit the
Covers.
Top up the oil through the inspection aperture and refit the cover plate.
Start the engine, running the drive train checking for unusual noises.
Adjustable Bearing Bracket/Lower Drive Shaft
Remove the Chain Cover, Drive Chain and Lower Sprocket as described above.
Remove the L/H inspection cover, disconnect the Propshaft between the Gearbox and
Lower Drive Shaft. Release the adjusting screw above the Bearing Bracket remove the

WORKSHOP MANUAL
500R
WINGET REVERSING DRUM CONCRETE MIXERS
ISSUE 10 2016
nuts from the three studs securing the Bracket and carefully pull off the Bearing Bracket
taking care not to damage the gasket. If damaged the gasket must be replaced.
The Bearing Bracket is sealed to the Mainframe using a thick gasket which is coated
with silicone sealer on assembly. Clean all traces of jointing materials from the
Mainframe and Bearing Bracket.
Remove the ‘Binx’ nut securing the Drive Flange to the Drive Shaft, remove the
Retaining Washer and Shim Pack and pull off the Flange, remove the Seal Protector
from the shaft. Using a suitable Bearing tube and a soft faced hammer knock the Drive
Shaft and Taper Roller Bearing out of the Bracket from the sprocket end. Remove the
Outer Bearing Cones from within the Bracket and the remaining Inner Bearing Cage off
the shaft.
Reassemble the Bearing Bracket assembly fitting the new Outer Bearing Cones into the
Bracket using a suitable bearing tube. Fit one of the Inner Bearing Cages to the
Sprocket end of the Shaft with the taper inwards i.e away from the Sprocket. Pass the
Shaft complete with the Bearing through the housing from the flanged end until the Cage
is located into the Outer Cone.
Support the Bracket and using a suitable bearing tube fit the second Inner Bearing Cage
over the Shaft and down into the Cone. Fit the parallel key and Drive Flange, (but not the
Seal or Seal Protector so as not to increase the drag on the Shaft and Bearings) install
the Shim Pack, Washer and Binx nut and adjust the shimming to give a bearing pre-load
of 0.000” to 0.002” thou. Check the Shaft turns freely within the Bearings.
Slacken and remove the Binx nut, Washer, Shim Pack and Flange, fit the Seal Protector
over the Flange smearing the lip with a little grease, coat the lip of the Oil Seal with
grease and using a suitable tool install the Oil Seal into the Bracket. Note that item No3
on the illustration, the ‘V’ Seal, is not required.
Refit the Flange, sized Shim Pack, Washer and Binx nut to the shaft. Ensure the mating
surfaces of the Bracket and Mainframe are clean and apply Silicone Sealer to both
surfaces, allow the Silicone to cure for a short time then apply the gasket to the Bracket
and apply a bead of Silicone Sealer to the gasket. Take care when fitting the Bracket not
to damage the gasket. Refit the Propshaft.
Following the procedures described previously fit the Lower Sprocket, Drive Chain and
Chain Cover. Take care when adjusting the chain not to damage the gasket. Top up the
Chain Case oil and refit the inspection cover.

WORKSHOP MANUAL
500R
WINGET REVERSING DRUM CONCRETE MIXERS
ISSUE 10 2016
Drum and Gearbox Controls
Hand Lever
The Hand lever pivot is retained on the inside of the Drum Housing with a split pin and
washer, removal of the Hand lever will allow replacement of the pivot bushes, (which
should be reamed to size following replacement) and the Roller and Bush.
Slotted Operating Lever
The Slotted Lever is retained to its pivot via a circlip and flat washer. To renew either
the Lever or its Bushing remove the Handlever as previously described, disconnect the
Connecting Rod, remove the Circlip and Washer, pull off the Lever. If the Bushing is
renewed it will require reaming to size.
Reassemble in reverse order.
Connecting Rod
Disconnect the Spherical Bearing at the end of the Connecting Rod from the Slotted
Lever, remove the locknut and adjusting nut from the other end of the rod. Carefully pull
the Rod through the Long Sliding Gland, Clevis Block, Spring, Sleeve and Short Sliding
Gland. Remove the second adjusting nut and locknut. Remove the Spherical Bearing.
Reassemble in the reverse order.
Drum Clutch Adjustment
Set the Handlever in the Mix/Charge position and rotate the nut on the Connecting rod to
allow 3mm of the Short Sliding gland to protrude beyond the end of the Clevis Assembly,
lock up the locking nut.
Repeat this operation in the Discharge position and rotate the nut on the Connecting
Rod to allow 3mm of the Long Sliding gland to protrude beyond the end of the Clevis
Assembly, lock up the locking nut.
Gearbox Removal
Disconnect the Connecting Rod as previously described.
Disconnect and plug the pipework and fittings at the Hydraulic Pump. Split the
Driveshaft between the Engine and Gearbox at the Nylon Splined Coupling.Unbolt the
Gearbox from the Mainframe, using suitable slings and lifting equipment lift the Gearbox
clear of the Mainframe.
Reassemble in reverse order ensuring the centreline of the Engine and Gearbox are in
line by shimming as necessary to avoid straining the Couplings and Flanges.

WORKSHOP MANUAL
500R
WINGET REVERSING DRUM CONCRETE MIXERS
ISSUE 10 2016
Engine Removal
On Electrical Start Diesel and machines fitted with a Dragline and Alternator, isolate the
Battery and disconnect the wiring. Split the Driveshaft between the Engine and Gearbox
at the nylon splined sliding coupling. Unbolt the Engine from the Mainframe, disconnect
the Air Cleaner pipework. Using suitable lifting equipment lift the Engine clear taking
care not to lose the two engine packers. (Later ‘CE’ machines are fitted with guarding
over the propshaft)
Reassemble in the reverse order ensuring the centreline of the Engine and Gearbox are
in line by shimming as necessary to avoid straining the Couplings and Flanges.
Air Filter
The Air Filter is located on the Engine/Fuel Tank Shroud on the R/H side of the mixer.
During operation dust collected the body is ejected through the rubber valve in the side
of the filters cylindrical body. The Element, which should be removed daily for cleaning
and replaced at least once every 300 hours or three months is retained in the main body
by a large wing nut, which when released allows removal of the element for cleaning.
Hydraulic Tank
The Hydraulic Tank contains a Suction Filter suspended below the Tank Lid. To access,
clean any debris from the top of the tank, disconnect the Hydraulic Pipework from the
Tank Lid, plug all hoses and blank off all fittings, remove the screws and carefully lift off
the Lid to avoid damaging the lid seal. Unscrew and clean the filter.
Reassemble in reverse order ensuring the seal between the Lid and Tank Body is in
good condition.
Oil Draining
The oil drain plug is located centrally in the base of the Hydraulic Tank and can be
accessed from below the machine.
To drain the oil run the engine and circulate the oil through the system until warm. Stop
the engine and remove the Tank Lid as described above. Place a collection tray below
the Tank, remove the plug and allow the Tank to drain completely. Clean out the Tank
and refit the drain plug. Refit the Lid. Top up the oil until the oil is level with the tip of the
cone at the base of the oil filler neck. Run the engine, operate the Hopper and Dragline
Controls. Stop the engine and allow the oil in the Tank to settle for approximately two
minutes before rechecking the level. Recheck the oil level in the Header Tank.

WORKSHOP MANUAL
500R
WINGET REVERSING DRUM CONCRETE MIXERS
ISSUE 10 2016
Note:
The Hydraulic Systems holds approximately 22 Litres (5 gallons) of oil.
Located on the top of the tank is the Bleed Valve which allows oil discharged from the
single Acting Hopper Ram (as the Ram lowers the Hopper) to bleed back into the tank.
If replacing the Bleed Valve body, ensure that the Ball in the Body forms a good seat by
driving the Ball down on the seat using a soft faced punch.
The tank is retained in the Mainframe by three M10 setscrews, however it is not possible
to remove the Tank unless the Gearbox is first removed.
Hydraulic Pump
The Hydraulic Pump is located on top of the Gearbox secured by four setscrews and is
driven through the Gearbox Bevel Gears, via a Pump Mounted Bevel Pinion. If replacing
a Bevel Pinion on the pump be aware that many pumps have more than one keyway cut
into the tapered shaft, selecting the wrong keyway will result in premature shearing of
the key.
Hydraulic pumps should be shimmed to give 5-8 Thou (0.02-0.20mm) gear backlash.
Place the Pump Assembly onto the Gearbox without any shims and measure the gap
between the pump body and gearbox casting. Add 5-8 thou (0.02-0.20mm) to the
measurement obtained and select the correct number of shims.
Hydraulic Control Valve
The Hydraulic Control Valve is mounted on the L/H side of the machine below the step
being secured to its bracket by at least two bolts, nits and washers.
Lifting the control lever raises the Hopper whilst lowering the lever lowers the Hopper.
The Control Valve powers the Single Acting Hydraulic Ram and also provides oil for the
Dragline Winch Motor via a High Pressure Carryover located in one of the control valves
ports. The adjustable system relief valve is located in the Control Valve and apart from a
spool seal kit no and handle kit no other user serviceable parts are available.
Hopper Ram & Restrictor
Lift the Hopper and support with the Safety Chain provided.
Disconnect the ¼ bore hose leading from the Header Tank to the Ram cylinder and plug
the hose to prevent oil loss. Remove the bolt retaining the Upper Pivot Pin through the
Hopper Cradle and knock out the pin. Do not lose the Washers placed each side of the
Ram Eye. Allow the ram to drop forward, the upper eye bush is now visible and can be

WORKSHOP MANUAL
500R
WINGET REVERSING DRUM CONCRETE MIXERS
ISSUE 10 2016
replaced if necessary. When replacing the upper bush with the ram in situ it is important
that the ram is prevented from moving from side to side. When fitting a new bush ensure
the lubrication hole in the bush is aligned with the grease nipple.
To remove the Ram Assembly, disconnect and plug the Hydraulic Hose and the
Restrictor on the Ram port. Remove the bolt retaining the lower pivot pin through the
Mainframe. Support the Ram with suitable lifting equipment and knock out the lower pin.
Lift the Ram Assembly clear drain out any oil and support in a suitable soft jawed vice.
Clean the area around the end cap and attaching a suitable tool unscrew the end cap,
carefully remove the rod and piston assembly and secure in a soft jawed vice.
Examine the cylinder bore carefully for signs of scoring or corrosion and the piston rod
for signs of pitting or peeling, it is pointless attempting to reseal a ram which has a
damaged bore or rod.
Remove the split pin securing the Piston Nut and remove the Nut, Piston Assembly and
End Cap. Remove and discard the old seals, new seals should be soaked in clean
hydraulic oil before fitment. Ensure all components are clean. Fit the new seals, rebuild
the Ram in reverse order fitting a new split pin through the piston retaining nut.
The Restrictor screwed into the Ram Inlet/Outlet port restricts the flow of oil out of the
Ram as the Ram is closed ensuring a more controlled descent.
The Restrictor contains a spring and Poppet valve and does not usually cause problems
in service.
Note:
The Hydraulic Ram is single Acting and in operation when the Ram is closed the
majority of the Hydraulic Oil is discharged from the full bore side of the Ram. To avoid
condensation forming in the annulus (upper) side of the cylinder as the Ram is closed,
oil is drawn into the annulus side from the Header Tank to fill the void with oil, this oil is
expelled back into the Header Tank as the Piston raises extending the Ram and lifting
the Hopper.
The Header Tank contains a sight glass and it is important that the oil level within the
Tank is checked on a daily basis. The oil level is correct if it is just visible in the sight
glass when the ram is fully closed.
Hose Failure Valve
Machines bearing the “CE” mark indicating compliance with the EC Machinery Safety
Directive have a Hose Failure Valve fitted to the Ram Inlet/Outlet port in addition to the
restrictor.

WORKSHOP MANUAL
500R
WINGET REVERSING DRUM CONCRETE MIXERS
ISSUE 10 2016
In service it is not unusual for violent operation of the Control Valve (In order to shake
material free from the Hopper when the Ram is at the full extent of its stroke) to blow off
the relief valve activating the Hose Failure Valve. Which then prevents closing of the
Ram and lowering of the Hopper.
Should this occur, slowly lift the Hopper slightly by extending the Ram without blowing
off the relief valve, then slowly close the Ram lowering the Hopper. Once the Hopper
has lowered by approximately 300mm normal operation can be resumed.
If a new hose failure valve is to be fitted the valve should first be unscrewed from the
body, and the gap between the valve baffles adjusted to 2mm by means of the small
capscrew and nut. Following adjustment, the valve should be screwed fully home into
the body and operation of the machine checked when it is fitted.
Hopper, Cradle, Link Arms and Pivot Shaft
Link Arms
The Hopper Cradle pivots on Needle Bearings contained within the “L” shaped Link
Arms.
To remove the Arms lower the Hopper Cradle and block up the Hopper to prevent the
assembly dropping when a Link Arm is removed.
Remove the Bearing Caps, each secured with three setscrews which pass through the
Caps and Arms into the Bearing Housings. Remove the Nut and Flat Washer retaining
the Link Arm to the Shaft, pull off the Arm, retrieve the Housings and “O” Rings from the
Pivot Shafts.
Remove the Inner Bearing of the Shafts, using a suitable bearing tube and soft faced
hammer remove the Outer Bearings from the Link Arm.
Reassemble in the reverse order greasing the Needle Bearings on Assembly.
Hopper Cradle and Hopper
Removal
Raise the Hopper slightly to allow access to the Hopper retaining bolts and nuts, attach
suitable lifting equipment to the Hopper, remove the bolts and carefully lift the Hopper
clear.
Attach the lifting equipment to the Hopper Cradle, raise the Cradle to allow removal of
the upper Ram pivot pin, lower the Cradle. Remove both Link Arms and the Link Shaft
which passes through the Cradle, lift the Hopper Cradle clear.
Reassemble in reverse order.

WORKSHOP MANUAL
500R
WINGET REVERSING DRUM CONCRETE MIXERS
ISSUE 10 2016
Pivot Shaft
The Pivot Shaft is retained in the “A” frame by two grubscrews one each end of the
Shaft.
To remove the Shaft carry out the procedures describing removal of the Hopper, Link
Arms and Cradle. Remove the Inner Bearings from the ends of the Shaft. Remove the
grubscrews and using a soft faced hammer knock out the Shaft.
Reassemble in reverse order coating the Shaft with copperslip and ensuring the Shaft is
central in the “A” frame before tightening the Grubscrews.
Batchweigher
The Batch Weigher Gauge is located on the L/H Water Tank Support and is mounted on
rubbers to dampen vibrations. The Gauge is connected to the Loadcell which is located
in the Mainframe below the Hopper Cradle via a hydraulic pipe.
The Loadcell and Gauge must be considered a sealed unit and on no account must the
hydraulic pipe be removed.
Damage to the Gauge or Loadcell is most commonly caused by dropping a loaded
Hopper onto the Loadcell, allowing an empty Hopper to free fall directly onto the
Loadcell or filling the Hopper directly from a Site Dumper, Skid Steer Loader, Tipping
Lorry or other similar equipment.
These cause high shock loadings which can loosen the Needle Pointer in the Gauge,
damage the Loadcell seals, or cause the top half of the Loadcell to turn over at an angle.
Although the both Workshop Manual and the Operators Manual contains instructions for
overhauling the unit, it is recommended that the Loadcell and Gauge Assembly are
returned to Winget Limited whenever possible for repairs. Field service and repairs can
often cause complications and accurate calibration of the Assembly cannot be
guaranteed. Winget Limited can accept no responsibility should attempts be made to
overhaul or repair the units.
Assuming the Loadcell and Gauge are in good condition the most common causes of
inaccurate weighing are:-
1) Mixer not level
2) Hopper resting on ground or build up of waste material below Hopper. Ensure at
least 50mm (2”) clearance between the ground and Hopper.
3) Build up of material around the Hopper Cradle Link Shaft.
4) Worn Hopper Cradle Pivot Bearings.
5) Loadcell Striker guide fouling Mainframe or failing to rotate freely.
This manual suits for next models
2
Table of contents
Other Winget Mixer manuals
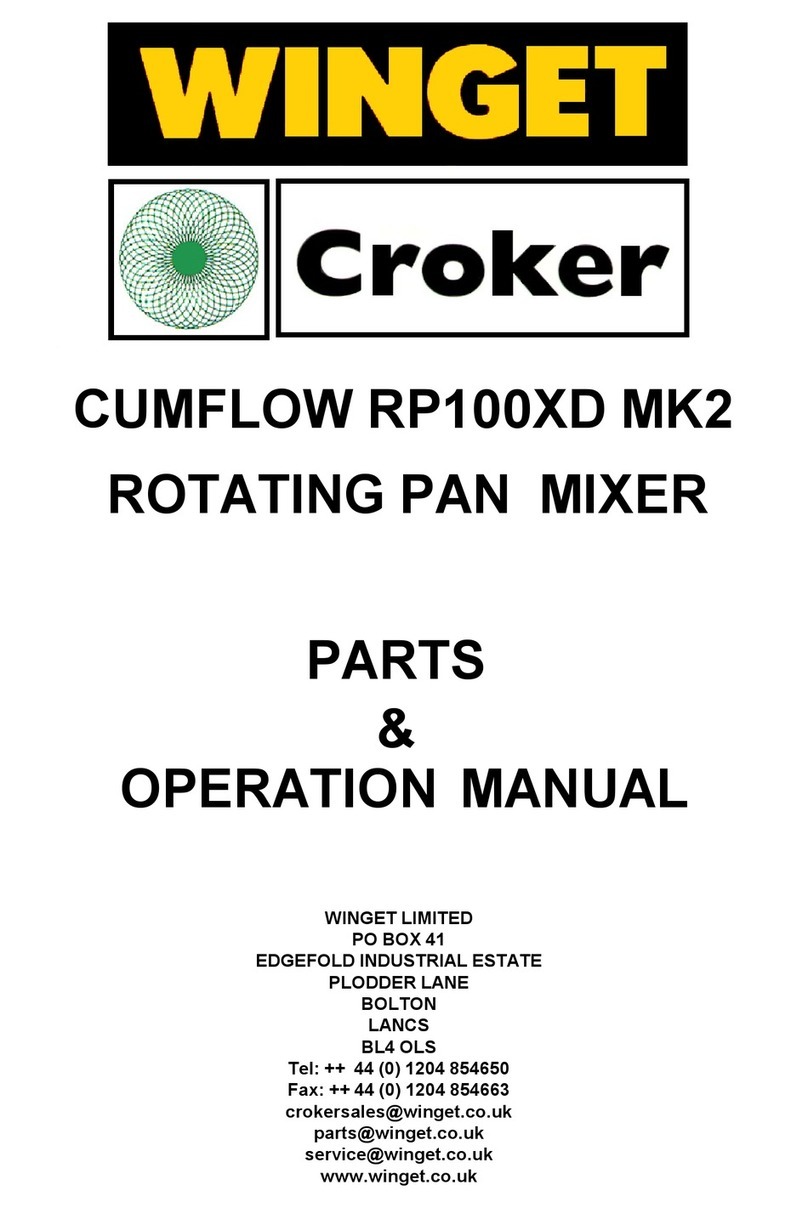
Winget
Winget CUMFLOW RP100XD MK2 User manual

Winget
Winget CUMFLOW RP150XD MK2 User manual
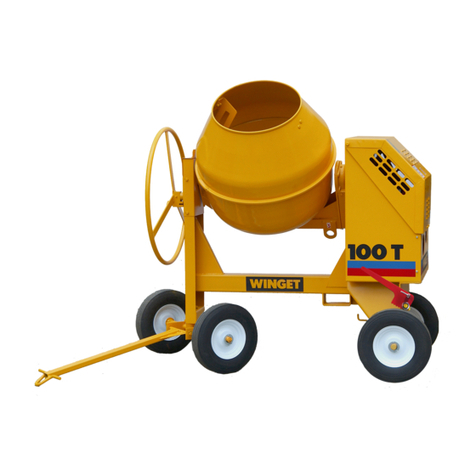
Winget
Winget 100T Service manual

Winget
Winget Croker CUMFLOW RP100XD User manual

Winget
Winget 200T User manual
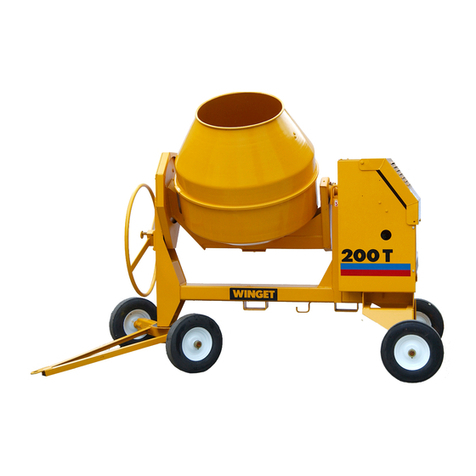
Winget
Winget 200T Instruction manual
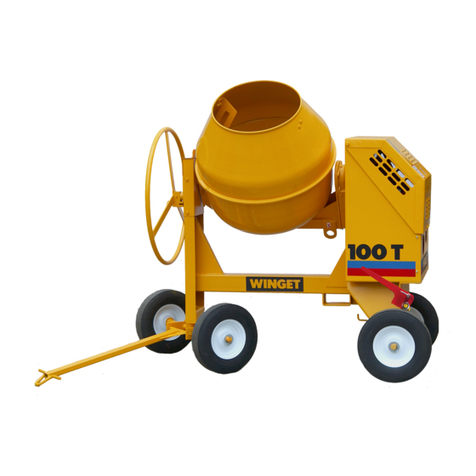
Winget
Winget 100T Service manual
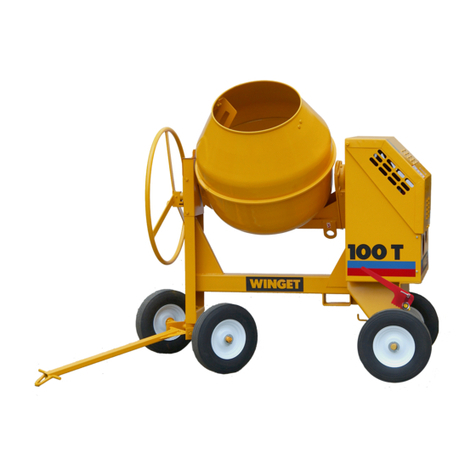
Winget
Winget 100T Instruction manual
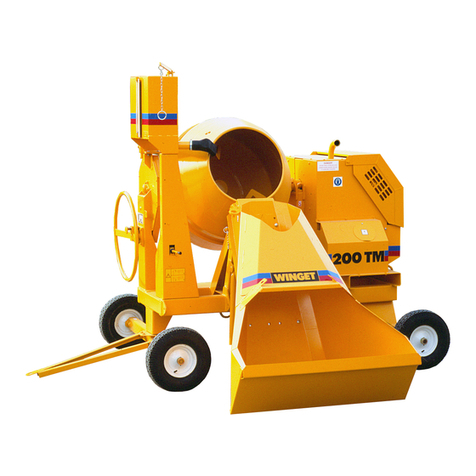
Winget
Winget 200TM Instruction manual
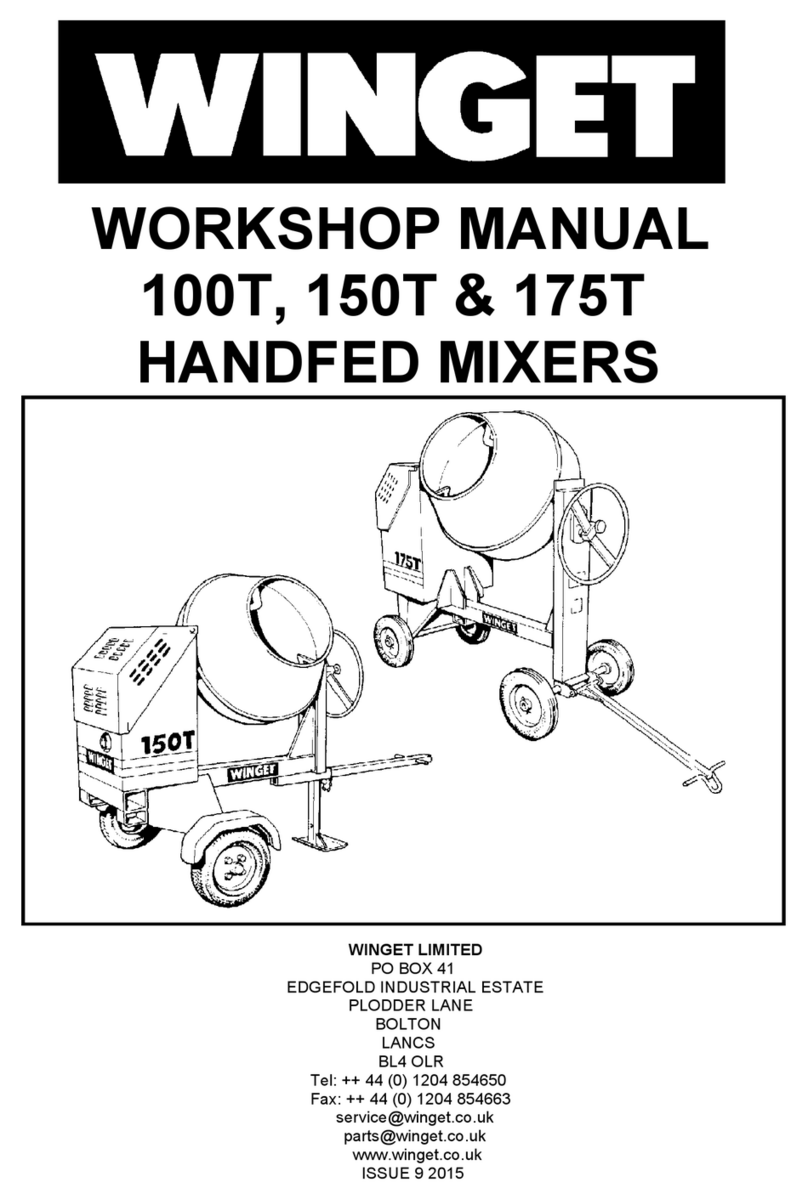
Winget
Winget 100T Instruction manual