Advantage Sentra SR Series User manual

This reference guide covers standard Advantage temperature
control units with the G Instrument. This guide may be used for
customized units using the G Instrument even when the unit may
not be physically the same as the units depicted in the included
photos.
1. A manual is available at www.advantageengineering.com/Sentra-SRG or by scanning the QR
code on the back of this document. Download and read the manual before starting installation.
2. This unit is designed to be used with water as the circulating fluid. The quality of fluid used in
your temperature control unit will greatly effect its short and long-term operation. Lack of as
well as improper water treatment can damage the temperature control unit by causing scale
build-up, excessive corrosion and/or bacterial contamination. It is the equipment owner’s
responsibility to prevent damage caused by poor water quality. The services of a water
treatment professional is recommended.
3. Before installing and operating the unit, be aware of and follow any local laws and codes that
apply to the installation.
4. When contacting the Service Department always have the unit Model and Serial number from
the data tag located on the side of the unit.
SERVICE DEPARTMENT
317-887-0729
*Reference the manual for requirements for 250°F set point.
Maximum Setpoint : 250°F*
Installation
Before Installing or Operating
Refer to the Manual for complete details on Installation.
1. Electrical: Be certain all electrical connections are tight in the unit. Install unit power cord
(when supplied) to power disconnect switch. Applied power must be equal to the unit voltage
and amps listed on the unit data tag. Follow all applicable local and national electrical codes.
2. Plumbing: Care should be taken to use materials (hose, rigid piping, valves or filters) rated
for the temperature and pressure duty of your unit. Most units have a maximum operating
temperature of 300°F or less and a maximum pressure of 150 PSI. The unit is most efficient
when full size plumbing is run from the unit connections to and from the process. If necessary,
reduce the plumbing size at your process, not at the unit.
Sentra SR Series with GControl Instrument
REFERENCE GUIDE
INSTALLATION • OPERATION • TROUBLESHOOTING

Standby
Status
Not Ready
Setpoint
250°F
Standby
Status
Ready
Setpoint
250°F
Standby
Status
Ready
Setpoint
250°F
Operating Temperature
Water Supply Pressure
180°F
20 PSI
190°F
25 PSI
200°F
30 PSI
210°F
35 PSI
220°F
40 PSI
230°F
45 PSI
250°F
50 PSI
75°F
Setpoint : 250°F
Autovent
To Process
3. Connect the unit’s To Process port to the Water In port on
the process manifold.
4. Connect the unit’s From Process port to the Water Out port
on the process manifold.
5. Note: Circuitry should avoid an excessive use of elbows
and/or lengths of pipe or hose. If hose is the material of
choice, avoid tight twists or curls and excessive lengths.
6. Valves and lters may be installed in the process water
piping circuitry to facilitate service and maintenance,
provided that such devices maintain the full inside diameter
of the process connection. If installed, all such devices must
be open and clean during unit operation.
Drain
From
Process
To
Process
Water
Supply
Typical unit shown.
Installation Continued
7. Connect Unit drain to plant’s open drain, tower water system return or chilled water system
return. The factory recommends a minimum of 20 psi pressure differential between the water
supply and drain line. A larger differential may be required for larger cooling needs.
8. Connect Unit water supply to plant’s city water or well water source or tower water supply or
chilled water supply. Water supply pressure requirements vary with operating temperatures as
shown in the chart below.
Start Unit Refer to the Manual for complete details on start up and operation information.
1. Fill unit with water. Apply power. When Standby screen is
displayed, the unit is not running.
• Status : Ready. Indicates the unit is ready to start.
• Status : Not Ready. Indicates the presence of a
sensor probe, pressure switch or motor overload fault.
See the troubleshooting and maintenance portions
of the manual for Information. The fault must be
corrected in order to continue operation of the unit.
2. This unit features an LCD screen. Use the five soft touch
buttons to navigate the available screens and select
parameters.
3. Determine that the pump is rotating in a clockwise direction
when viewed from the rear of the motor. Follow the
instructions in Section 3.2 of the factory operations manual.
WARNING: proper care should be employed when checking pump
rotation as power is applied to the unit at this point.
4. The unit is ready to start when Status
Ready is shown on the screen and
pump rotation is correct. Press the green
start button. The unit will auto vent if the
fluid temperature is below 100°F or as
programmed in the features menu.

78°F
Setpoint : 250°F
Autovent
To Process
Standby
Status
Ready
Setpoint
250°F
85°F
Setpoint : 250°F
Heating : 100%
To Process
85°F
Setpoint : 85°F
Autovent
To Process
Standby
Status
Ready
Setpoint
85°F
300°F
Setpoint : 250°F
Heating : 10%
To Process
85°F
Setpoint : 85°F
Heating : 0%
To Process
250°F
Setpoint : 85°F
Cooling : 100%
To Process
Pump Seal Cool
Wait - Shutting Down
Push Stop again to abort
85°F
Setpoint : 85°F
Heating : 0%
To Process
Pump Seal Cool
Wait - Shutting Down
Push Stop again to abort
85°F
Setpoint : 250°F
Autovent
To Process
85°F
Setpoint : 250°F
Heating : 100%
To Process
250°F
Setpoint : 85°F
Cooling : 100%
To Process
If the Pump Seal Cooling feature is NOT enabled ...
If the Pump Seal Cooling feature IS enabled ...
Setpoints
Utilites
Network
Features
Flow
Main Menu
Back Go
Pick
WARNING: When the pump seal cooling
feature is activated, pressing the stop button
will not turn off the unit. To completely shut
down the unit, press the Stop button twice.
Start Unit Continued.
The instrument has 5 soft keyed buttons.
1. The Home button shows the Home screen.
2. The Up button will add one unit of value or will scroll up through a
menu.
3. The Down button will subtract one unit of value or will scroll down
through a menu.
4. The Go button will advanced through a series of screens or save a
value.
5. The Back button will go backwards through a series of screens.
Operating Screens ... these show the To Process temperature, the
selected Setpoint temperature and status of Autovent, Heating and
Cooling. When enabled, the Pump Seal Cool screen appears when the
unit is stopped. The pump will continue to run and the cooling valve will
open 100% to reduce process temperature prior to shutdown.
Stop Unit Refer to the Manual for complete details on shut down information.
1. Decrease the setpoint temperature lower
than 85°F and allow the unit to cool to the
temperature.
2. Press the Stop Button to disengage the pump.
3. Caution. Dissipate static pressure before
disconnecting hoses.
4. A pump seal cooling feature can be selected
from the Features menu to automatically cool
the unit once the stop button is pressed.
Controller Basic Controller use is presented.
Refer to the Manual for full information.
6. Adjust the setpoint to the desired value by
pressing the Up or Down button until the
value is displayed.
7. The unit will heat or cool to
maintain the setpoint temperature.
75°F
Setpoint : 250°F
Autovent
To Process
Setpoints
Utilites
Network
Features
Flow
Main Menu
Back Go
Pick
Process Setpoint
Hi Deviation
Lo Deviation
Setpoints
Back Go
Pick Cancel OK
Adjust
Autovent Time
Autovent Temp
Pump Seal Cool
Pump Seal Time
Pump Seal Temp
Features
Back Go
Pick
Mold Purge
Manual Vent
Software Version
Display Test
Utilites
Back Go
Pick
Protocol
Baud Rate
Address
Network
Back Go
Pick
Enable
Offset
Calibration
Flow
Back Go
Pick
Mold Purge
Remote Start
Options
Back Go
Pick
Valve Size
Max Setpoint
Units
Machine
Back Go
Pick
FAULT
System Safety
Check water supply
Check pump overload
FAULT
High Temp Limit
Check for cause and allow
unit to cool before
restart
FAULT
High Temp Limit
Check for cause and allow
unit to cool before
restart
FAULT
AVT Cooling Valve
Check position switch
Replace valve
FAULT
To Process Sensor
Check sensor is connected
Check connector is dry
FAULT
Phase
SRG
250°F
Process Setpoint
Acknowledge
Process Setpoint
Success
Change Setting

75°F
Setpoint : 250°F
Autovent
To Process
Setpoints
Utilites
Network
Features
Flow
Main Menu
Back Go
Pick
Process Setpoint
Hi Deviation
Lo Deviation
Setpoints
Back Go
Pick Cancel OK
Adjust
Autovent Time
Autovent Temp
Pump Seal Cool
Pump Seal Time
Pump Seal Temp
Features
Back Go
Pick
Mold Purge
Manual Vent
Software Version
Display Test
Utilites
Back Go
Pick
Protocol
Baud Rate
Address
Network
Back Go
Pick
Enable
Offset
Calibration
Flow
Back Go
Pick
Mold Purge
Remote Start
Options
Back Go
Pick
Valve Size
Max Setpoint
Units
Machine
Back Go
Pick
FAULT
System Safety
Check water supply
Check pump overload
FAULT
High Temp Limit
Check for cause and allow
unit to cool before
restart
FAULT
High Temp Limit
Check for cause and allow
unit to cool before
restart
FAULT
AVT Cooling Valve
Check position switch
Replace valve
FAULT
To Process Sensor
Check sensor is connected
Check connector is dry
FAULT
Phase
SRG
250°F
Process Setpoint
Acknowledge
Process Setpoint
Success
Change Setting
For Current Factory Operations Manual Scan this QR code to download an PDF copy to a
smart phone or tablet. Download the PDF copy to a desktop computer for view or print by this
link: www.advantageengineering.com/Sentra-SRG.
Unit Will Not Start
(Display Blank & Off)
1. Fuse open at disconnect switch.
2. Transformer fuse open
Unit Will Not Start (Display On)
1. Error or alert indicator
displayed.
2. Follow instructions on screen
to troubleshoot and refer to
manual or contact the service
department.
Unit Overheats
1. Low water supply pressure.
2. Cooling solenoid valve
defective.
3. Drain line obstructed.
4. Instrument defective.
5. Cooling requirement exceeds
cooling valve capacity.
Unit Underheats
1. Process water leakage -
defective cooling solenoid valve.
2. Heater element failure.
3. Process heating requirement
exceeds unit heating capability.
4. Control instrument defective and
not calling for heat.
Pressure Relief Valve Leaks
1. Water supply pressure too high.
See manual.
2. Pressure relief valve
contamination.
525 East Stop 18 Road, Greenwood, IN 46143 phone: 317-887-0729 fax: 317-881-1277
Form #ADV-1083 updated 03/22/2023 ©2023 Advantage Engineering, Inc.
Controller Continued.
Troubleshooting Basic Troubleshooting is shown here. Refer to the Manual for full information.
If you have any questions regarding this Reference Guide, the Sentra G Series Operations Manual,
installation, operation or servicing of the unit, please call the Advantage Service Department.
317-887-0729
Main Menu ... from the Operating Screen,
press the Go button to advance to the
Main Menu.
Setpoint ... use the Go button to advance
to the Setpoint select
screen. Use the Up and
Down buttons to select
the setpoint. Save the
setting by pressing the
Go button.
Screens ... there are six
screens to set and view machine
operating parameters. Use the
Go button to advance screens
from the Main Menu. Please
note, the Flow menu requires
optional components that may
not be installed on your machine.
Fault Screens indicate what issue
is present on the unit. See the
Operations Manual for detailed
explaination.
In Production
This manual suits for next models
10
Other Advantage Control Unit manuals
Popular Control Unit manuals by other brands
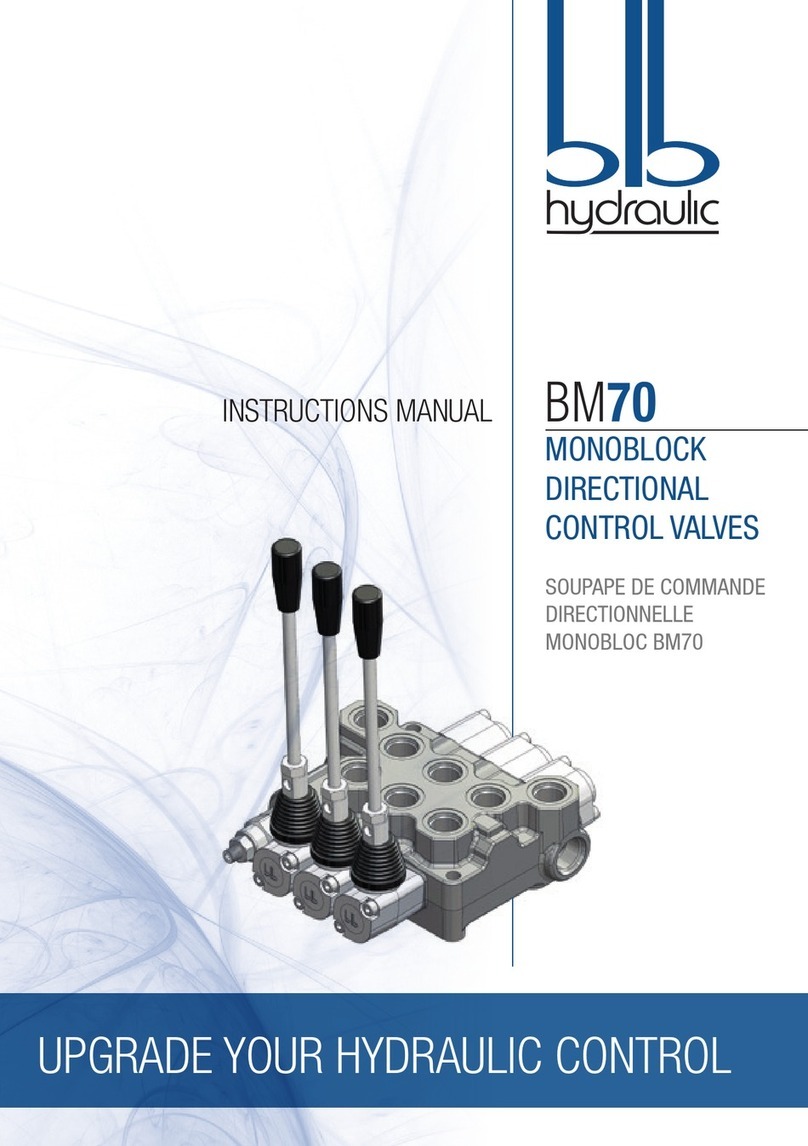
BLB hydraulic
BLB hydraulic BM70 instruction manual
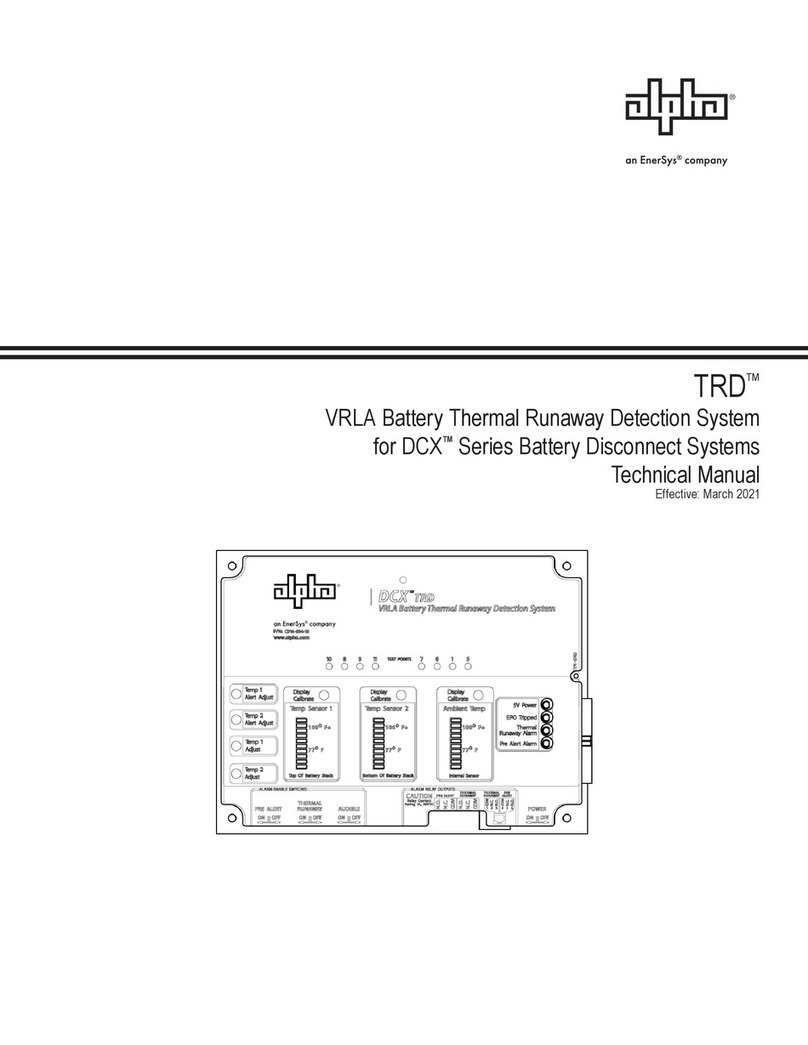
EnerSys
EnerSys Alpha TRD Technical manual
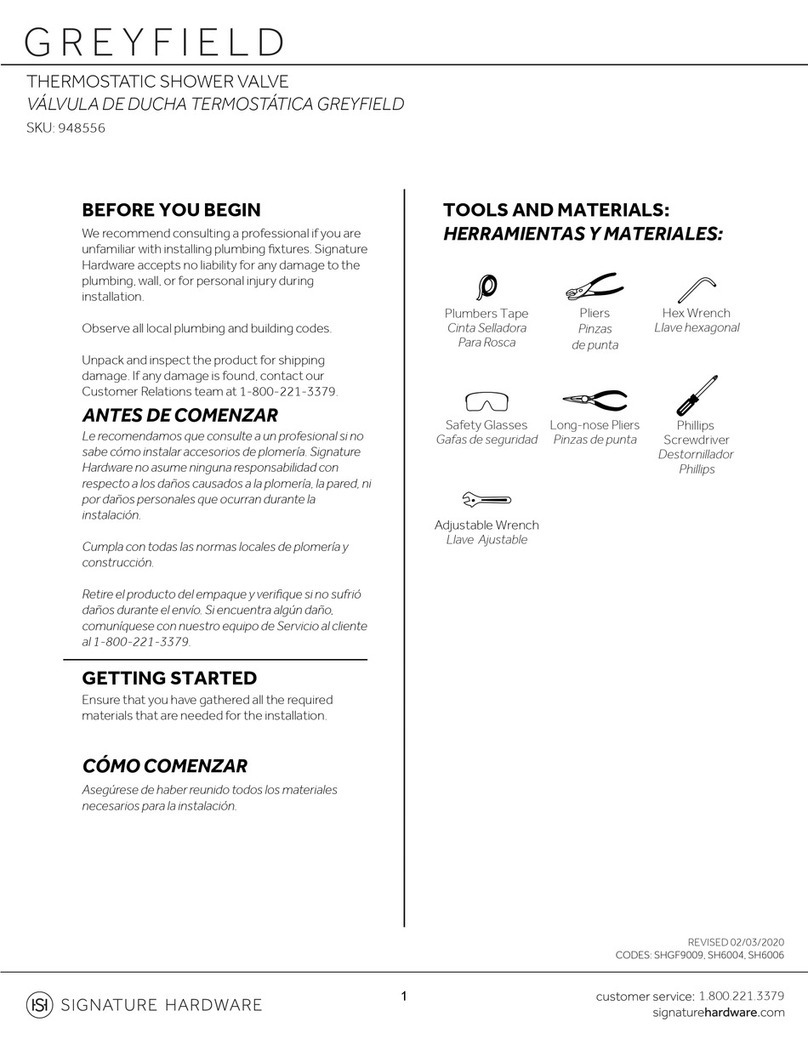
Signature Hardware
Signature Hardware GREYFIELD 948556 quick start guide
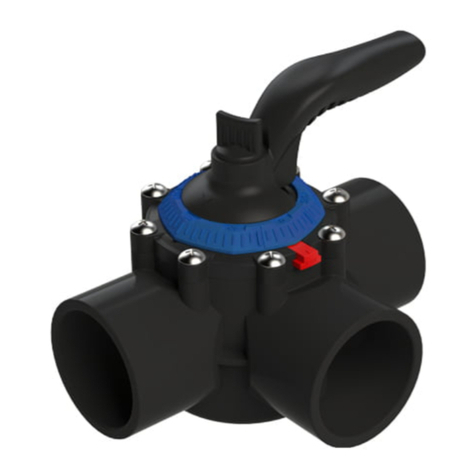
emaux
emaux FLEX Series Installation and operation manual
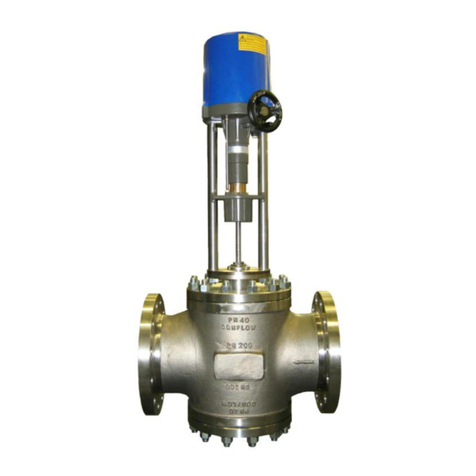
CONFLOW
CONFLOW 20VT EP Installation and maintenance manual
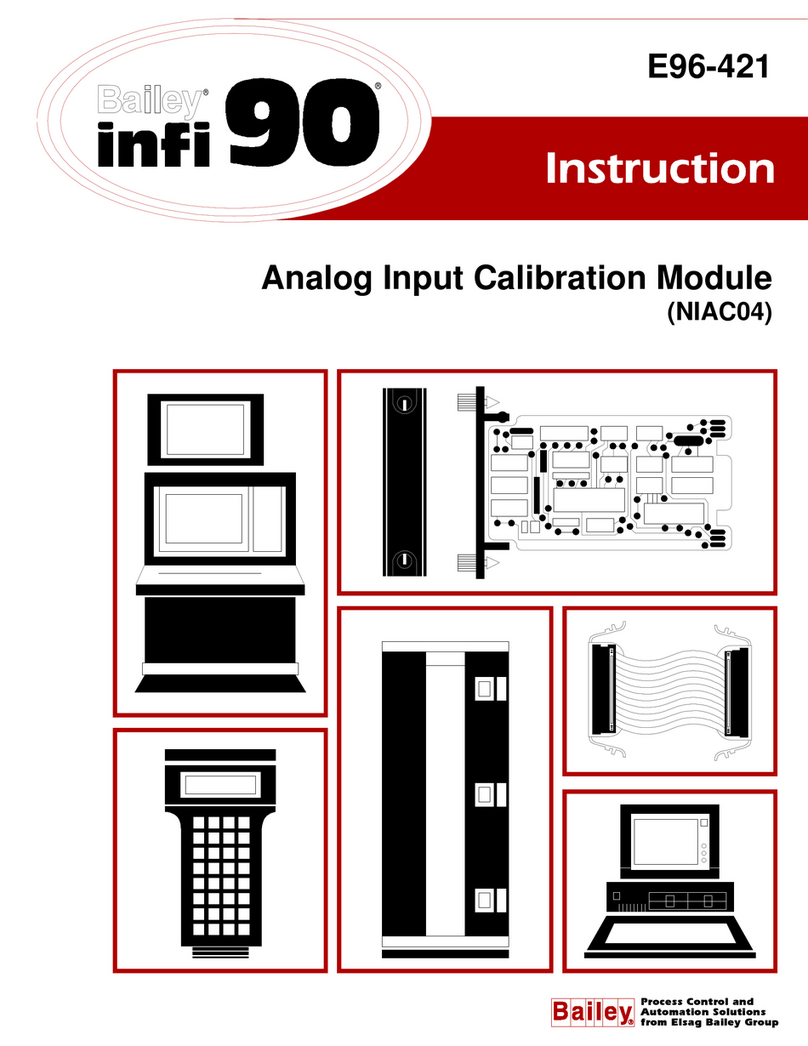
Bailey
Bailey Infi 90 NIAC04 Instruction