Ansul SharpEye 20/20MI-32-S-F Operating instructions

SharpEye 20/20MI-32-S-F
TRIPLE IR (IR3)
FLAME DETECTION SYSTEM
User and Maintenance Manual
006848

REVISION RECORD
7-1-07 REV. 1
6-30-05 15 1
7-1-07 1 1
7-1-07 2 2
7-1-07 4 1
7-1-07 5 2
7-1-07 6 1
7-1-07 7 1
7-1-07 8 2
7-1-07 9 2
7-1-07 10 1
7-1-07 11 1
7-1-07 12 1
7-1-07 13 1
7-1-07 14 1
DATE PAGE REV. NO. DATE PAGE REV. NO.
Indicates revised information.

Section Page
______ ____
Introduction 1
Technical Features 2 – 3
Performance 4 – 6
Operation 7 – 8
Electrical Specifications 9
Mechanical Specifications 10
Environmental Specifications 11
Installation Instructions 12
Operating Instructions 13
Maintenance Instructions 14
TABLE OF CONTENTS

CAUTION
This manual should be carefully read by all individuals who have or will have responsibility for using, maintaining or servicing the product.
The Detector is not field-repairable due to the meticulous alignment and calibration of the sensors and the respective circuits. Do not
attempt to modify or repair the internal circuits or change their settings, as this will impair the system's performance and void the Ansul
Incorporated product warranty.
INTRODUCTION
The Model 20/20MI-32-S-F is a Triple IR spectrum flame detector designed to provide maximum fire protection. It uses innovative tech-
nology of advanced digital signal processing to analyze the dynamic characteristics of fire. Three sensitive IR channels process the
signals. Detection performance is controlled by a microprocessor and easily adapted to all environments, applications and requirements.
The result is a unique and superior flame detector, which provides excellent detection sensitivity with extreme immunity to false alarm.
Although there are more than one basic model of the 20/20MI Triple IR flame detector and each has numerous features, only the models
20/20MI-32-A-F* and 20/20MI-32-S-F features are applicable to vehicle fire protection using the CHECKFIRE SC-N detection module.
Only the 20/20MI-32-S-F features are addressed in this manual.
APPROVALS
20/20MI-32-A-F: Aluminum housing, FM Approved
20/20MI-32-S-F: Stainless steel housing; FM Approved
* 20/20MI is the base detector model number. Additional numbers and letters represent options:
20/20MI-3 =Short Range (8.2-33 ft.) (2.5-10m)
20/20MI-32 =Plug Outlet
20/20MI-32-S =Stainless Steel Housing
20/20MI-32-S-F =FM Approved
INTRODUCTION
7-1-07 Page 1
REV. 1

TECHNICAL FEATURES
7-1-07 Page 2
REV. 2
1 TECHNICAL FEATURES
• DETECTION RANGE: up to 33.0 ft (10 m) for a 1 ft2(0.1 m2)fire.
• ULTRA HIGH IMMUNITY TO FALSE ALARMS: (see para. 2.3).
• ADVANCED DIGITAL PROCESSING OF THE DYNAMIC CHARACTERISTICS OF FIRE: Flickering, Threshold correlation and
Ratio.
•THREE SEPARATE IR CHANNELS: Between 3-5 microns.
• TWO RESPONSE LEVELS: Warning & Detection.
• SOLAR BLIND
• MICROPROCESSOR BASED: Digital signal processing.
• BUILT IN TEST: Manual BIT
• CERTIFICATION: FM Approved with CHECKFIRE SC-N Electric Detection and Actuation System
1.1 PRINCIPLES OF OPERATION
1.1.1 Hydrocarbon fire detection
The triple IR flame detector detects all conceivable types of hydrocarbon fires, i.e. any fire, which emits CO2.
1.1.2 Identifying the CO2peak
The hydrocarbon fire is characterized by a typical radiation emission. The CO2peak emits intense radiation in the spectral
band between 4.2 µ – 4.5 µ and weaker radiation intensity outside this spectral band.
1.1.3 The limitations of IR-IR flame detectors
CO2in the atmosphere attenuates the radiation in this spectral band. (Absorption and emission of radiation always occur in
the same band.) As a result, the greater the distance between the detector and the fire, the weaker the intensity of the radia-
tion reaching the detector (the CO2attenuation increases). This phenomenon explains the limitations of the existing IR-IR
flame detectors in the market:
• Detection distance is restricted to 10 meters (33 ft) only.
• Their immunity to false alarm sources is limited.
1.1.4 The advantages of IR3technology
IR3technology overcomes these limitations by an innovative concept of utilizing an additional detection channel. Three chan-
nels collect more data from the environment, permitting more accurate analysis and better performance. After careful investi-
gation, three channels were selected which, when operating jointly,provide optimal fire detection characteristics:
Channel 1: 4.2 µ – 4.6 µ
Fire – the CO2peak.
Channel 2: 4.0 µ – 4.2 µ
Eliminates false alarms from high temperature sources.
Channel 3: 4.8 µ – 5.2 µ
Eliminates false alarms from flickering of background radiation.
Most IR sources, which create misleading IR alarm stimuli, including the sun, incandescent and halogen lamps, electric arc
discharges, electrical heaters, etc., do not possess this unique spectral signature of fire. The IR sensors of the detector
respond only to flickering of radiation signals. The signals are compared to a predetermined threshold. Processing of the
results from the three IR channels is performed by the board microprocessor.The result is a much greater detection distance
and a highly increased ability to distinguish between fire and false alarms. This sophisticated technology surpasses all other
existing flame detection techniques on the market today. Further enhancement of this triple IR analysis enables the accurate
detection of a hidden or smoldering fire where the radiating flames are not visible, but the emitted hot mass of CO2gases is
detected.
This unique flame analysis capability (patent pending) has been incorporated into the Triple IR fire detector.The
result is a unique flame detector, which does not produce false alarms and provides at the same time detection over
greatly increased distances.
1.1.5 Model
The model, 20/20MI-32-S-F, is a short range, fast detection type with a range up to 33.0 ft (10 m).
The 20/20MI-32-S-F has a stainless steel housing.

FIGURE 1: IR3FLAME DETECTOR
TECHNICAL FEATURES
7-1-03 Page 3

PERFORMANCE
7-1-07 Page 4
REV. 1
FIGURE 2: FLAME DETECTOR ASSEMBLY–OUTLINE DRAWING
WITH CONNECTOR OUTPUT
2PERFORMANCE
2.1 DETECTION SENSITIVITY
Detection sensitivity is the detection distance for a specified size of fire and type of fuel ("Standard Fire") within a given time from
the ignition of the fire.
Standard Fire:
A1ft2/(0.1 m2)Gasoline pan fire with max. wind speed of 6.5 ft/sec/(2 m/sec).
Sensitivity Range:
The sensitivity is factory set at 10 (33 ft. (10 m)) with a response time of 3 seconds.
VIEW A
006849
NO. 6-32UNC-2B
FOR GROUND CONNECTION
NO. 10-32UNF-2B
4PL.
DIA .275 IN. (7 mm)
2PL.
IR SENSOR
REFLECTOR
STATUS LED
IR SENSOR
IR SENSOR
A
4.3 IN.
(110 mm)
2.5 IN.
(63.5 mm)
2.6 IN.
(65.5 mm)
3.9 IN.
(98.6 mm)
3.9 IN.
(98.6
mm)

Other fuels
The detector will react to other types of fires as follows:
PAN FIRE SIZE: 1 ft2/(0.1 m2)
MAXIMUM WIND SPEED: 6.5 ft/sec (2 m/sec)
MAXIMUM RESPONSE TIME: 10 sec
Table 2.1.2: Sensitivity to other fuel types
2.2 CONE OF VISION
Horizontal: 100°
Vertical: 100°
Relative Range as a Function of the Incidence Angle
FIGURE 3: HORIZONTAL AND VERTICAL FIELDS OF VIEW
PERFORMANCE
7-1-07 Page 5
REV. 2
TYPE OF FUEL % OF MAX. DISTANCE AT EACH SENSITIVITY RANGE
GASOLINE 100%
N-HEPTANE 100%
ALCOHOL 75%
JET FUELS 75%
KEROSENE 75%
DIESEL FUEL 70%
HYDRAULIC FLUID 70%
METHANE* 30%
PROPANE* 30%
*0.5 m plume fire
006850
RELATIVE RANGE
100%
90%
80%
70%
60%
50%
10 DEG
20 DEG
30 DEG
35 DEG
40 DEG
45 DEG
60 DEG
–10 DEG
–20 DEG
–30 DEG
–35 DEG
–40 DEG
–45 DEG
–50 DEG
–60 DEG
50 DEG

PERFORMANCE
7-1-07 Page 6
REV. 1
2.3 FALSE ALARM PREVENTION
The detector will not provide an alarm or a warning signal as a reaction to the radiation sources specified below.
NOTES:
IAD = Immune at Any Distance
All sources are chopped from 0 to 20 Hz.
Table 2-3.1: Immunity to False Alarm Sources
Table 2-3.2: Welding Immunity Distance – 20/20MI-32-S-F
RADIATION SOURCE IMMUNITY DISTANCE FT (M)
Sunlight IAD
Indirect or reflected sunlight IAD
Incandescent frosted glass light, 100 W IAD
Incandescent clear glass light, rough service, 100 W IAD
Fluorescent light with white enamel reflector, standard office or shop, 40 W (or two 20 W) IAD
Electric arc [12mm (15/32 in) gap at 4000 V alternating current, 60 Hz] IAD
Arc welding [4 mm (5/32 in) rod; 240 A] See Table 2-3.2
Ambient light extremes (darkness to bright light with snow,water, rain, desert glare and fog) IAD
Bright colored clothing, including red and safety orange. IAD
Electronic flash (180 watt-seconds minimum output) IAD
Movie light, 625 W quartz DWY lamp (Sylvania S.G.-55 or equivalent) 6.5 (2)
Flashlight (MX 991/U) IAD
Radiation heater,1500 W IAD
Radiation heater,1000 W with fan IAD
Quartz lamp (1000 W) 10 (3)
Mercury vapor lamp IAD
Grinding metal IAD
Lit cigar 1(0.3)
Lit cigarette 1(0.3)
Match, wood, stick including flare up 10 (3)
SENSITIVITY DETECTION RANGE IMMUNITY DISTANCE
10 33 ft (10 m) >10 ft (3 m)

3 OPERATION
3.1 VISUAL INDICATIONS
One 3-color LED-indication is located in the detector front window:
FIGURE 4: INDICATION LEDS
3.2 OUTPUT SIGNALS
The detector controls the following outputs:
• Alarm relay
• Fault relay
The detector can be in one of the following states.
In each state, the detector will activate different outputs as specified in table 3-2.1.
OPERATION
7-1-07 Page 7
REV. 1
DETECTOR STATUS LED COLOR LED MODE
Fault, BIT Fault Yellow 4 Hz flashing
Normal Green 1 Hz flashing
Warning Red 2 Hz flashing
Alarm Red Steady
NORMAL: The detector is functioning normally.
MANUAL/
AUTOMATIC BIT: The detector performs a Built In Test.
WARNING: Fire detected – warming alarm (prealarm) state
ALARM: Fire detected – fire alarm state
MANUAL/
AUTOMATIC BIT
FAULT: A fault is detected during BIT sequence.
FAULT: A fault is detected when the power supply is too low or during a software
fault.
STATUS LED
006851

OPERATION
7-1-07 Page 8
REV. 2
Table 3-2.1: Output Signals versus Detector State
Note:
(1) The detector will be in its BIT FAULT state until it has passed a successful BIT.
(2) The alarm outputs will be activated as long as the alarm conditions are present and will stop approximately 3 seconds after
the fire is no longer detected.
3.3 ALARM DELAY
When an alarm (detection) condition is encountered, detection activation will be delayed for 3 seconds while evaluating the
condition. If the alarm condition is still present, a signal will be sent to the CHECKFIRE controller.If this condition no longer
exists, the detector will return to its standby state. The LED will indicate warning level during the delay time only if the fire
condition exists.
3.4 MANUAL/AUTOMATIC BUILT-IN TEST (BIT)
The detectors’ Built In Test (BIT) checks the following:
• Electronics circuitry
•Sensors
• Window cleanliness
Note: Manual/automatic BIT operation will require disconnecting power to each detector to be tested.
An unsuccessful BIT sequence activates the following:
• A FAULT condition at the CHECKFIRE controller.
• The LED flashes (4 Hz) at yellow.
•BIT procedure will be performed every 1 minute until successful BIT has been encountered.
Asuccessful BIT does not activate any indicator.
The LED flashes (1 Hz) at green (normal condition).
DETECTOR COLOR FLASHING ALARM FAULT
STATE LED LED RELAY RELAY
NORMAL Green 1 Hz Off On
WARNING Red 2 Hz Off On
ALARM (3) Red Steady On On
MANUAL/AUTOMATIC
BIT FAULT (2) Yellow 4 Hz Off Off
WARNING AT BIT FAULT Red 2 Hz Off Off
ALARM AT BIT FAULT Red Steady On Off
FAULT Yellow 4 Hz Off Off

4 ELECTRICAL SPECIFICATIONS
4.1 OPERATING VOLTAGE: 18-32 VDC
4.2 POWER CONSUMPTION:
Max. 25 mA in Stand-by
Max. 50 mA in Alarm
4.3 ELECTRIC INPUT PROTECTION:
The input circuit is protected against voltage-reversed polarity, voltage transients, surges and spikes according to MIL-STD-1275.
FIGURE 5: CONNECTOR INTERFACE
ELECTRICAL SPECIFICATIONS
7-1-07 Page 9
REV. 2
006852
1
2
3
4
5
6
7
8
9
10
11
12
SHIELD GROUND
FAULT RELAY
CONTACT
(NC)
ALARM RELAY
CONTACT
(NO)
POWER (18-32VDC)
RETURN (–)
4-20mA IN – NOT USED WITH
CHECKFIRE SC-N SYSTEM
4-20mA OUT – NOT USED WITH
CHECKFIRE SC-N SYSTEM
RS 485 (–) – USED ONLY FOR DETECTOR
PROGRAM SET-UP COMMUNICATION
RS 485 (+) – USED ONLY FOR DETECTOR
PROGRAM SET-UP COMMUNICATION
MANUAL BIT ACTIVATION – NOT USED
WITH CHECKFIRE SC-N SYSTEM
GROUND

MECHANICAL SPECIFICATIONS
7-1-07 Page 10
REV. 1
5 MECHANICAL SPECIFICATIONS
1. Enclosure
Stainless steel 316L electro chemical and passivation coating.
2. Water and dust tight
NEMA 250 type 6p.
IP 66 and IP 67 per EN60529
3. Electronic Modules
Conformable coated
4. Electrical Connection
Connector Interface
5. Dimensions
Base: 4.3 in (110mm) x 3.9 in (100 mm)
Height: 2.6 in (65.5mm)
6. Weight
2.4 lb. (1.2 kg) stainless steel 316L housing
7. Functional Test
FM functional test per 3620

6 ENVIRONMENTAL SPECIFICATIONS
1. High Temperature
Design to meet MIL-STD-810C, method 501.1 procedure II
Operating temperature: +70 °C (+160 °F)
Storage temperature: +85 °C (+185 °F)
2. Low Temperature
Design to meet MIL-STD-810C, method 502.1, procedure I
Operating temperature: –40 °C (–40 °F)
Storage temperature: –55 °C (–65 °F)
3. Humidity
Design to meet MIL-STD-810C, method 507.1, procedure IV
Relative humidity of up to 95% for the operational temperature range.
4. Salt Fog
Design to meet MIL-STD-810C, method 509.1, procedure I
Exposure to a 5% Salt Solution Fog for 48 hours.
5. Dust
Design to meet MIL-STD-810C, method 510.1, procedure I
Exposure to a dust concentration of 0.3 frames/cubic ft at a velocity of 1750 fpm, for 12 hours
6. Vibration
Design to meet MIL-STD-810C, method 514.2, procedure VIII
Vibration at an acceleration of 1.1g within the frequency range of
5-30 Hz, and an acceleration of 3g within the frequency range of 30-500 Hz
#UL 1254 – Section 43 to meet off-road vehicle protection
7. Mechanical Shock
Design to meet MIL-STD-810C, method 516.2, procedure I
Mechanical Shock of 30g half-sin wave, for 11 msec
#UL 1254 – Section 43 to meet off-road vehicle protection
8. Electromagnetic Compatibility (EMC)
This product is in conformance with EMC directive 89/336/EC
Radiated Emission: EN61000-6-3
Conducted Emission: EN61000-6-3
Radiated Immunity: EN61000-4-3
Conducted Immunity: EN61000-4-6
ESD EN61000-4-2
Burst EN61000-4-4
Surge EN61000-4-5
ENVIRONMENTAL SPECIFICATIONS
7-1-07 Page 11
REV. 1

INSTALLATION INSTRUCTIONS
7-1-07 Page 12
REV. 1
7 INSTALLATION INSTRUCTIONS
7.1 SCOPE
The Model 20/20MI-32-S-F is a self-contained Optical Flame Detector, designed for quick detection response in addition to standard
heat detection options. The Model 20/20MI-32-S-F flame detector is connected to the detection interface module, when used with
the CHECKFIRE automatic fire extinguishing systems for off-road vehicle protection. The detector can be a part of a more complex
system where many detectors and other devices are integrated through a common control unit. This chapter does not attempt to
cover all of the standard practices and codes of installation. Rather, it emphasizes specific points of consideration and provides some
general rules for qualified personnel. Wherever applicable, special safety precautions are stressed.
7.2 GENERAL CONSIDERATIONS
Very Important:
The detector should be aimed toward the center of the detection zone and have a completely unobstructed view of the protected
area. Whenever possible, the detector face should be tilted down at a slight angle to prevent the accumulation of dust and dirt. Do
not start an installation unless all conceivable considerations regarding detector location have been taken into account. To ensure
optimal performance and an efficient installation, the following guidelines should be considered:
A. SPACING AND LOCATION
The number of detectors and their locations in the protected area are affected by:
• Size of the protected area
• Obstructed lines of sight
• Cone of view of the detectors
B. ENVIRONMENT
• Dust, snow or rain can reduce the detectors sensitivity and require more maintenance activities.
• The presence of high intensity flickering of IR sources may affect sensitivity.
7.3 PREPARATIONS FOR INSTALLATION
Tools and equipment required for installation of detectors, brackets, modules, and interconnecting cabling will depend upon the
specific application.
1. Verify the appropriate Purchase Order. Record the Part No. and the Serial No. of the detectors and the installation date in the
appropriate Logbook.
2. Open the container package immediately prior to detector installation and visually inspect the detector.
3. Verify that all components required for the detector installation are readily available before commencing the installation
7.4 DETECTOR MOUNTING
The detector shipping assembly, Part No. 432480, contains a 20/20MI-32-S-F detector, detector bracket, and associated hardware.
See ANSUL CHECKFIRE SC-N Installation Manual, Part No. 432522, for detailed mounting information.
7.5 INSTALLATION
Refer to ANSUL CHECKFIRE SC-N Installation Manual, Part No. 423522, for detailed installation instructions.

8 OPERATING INSTRUCTIONS
8.1 SCOPE
The following instructions are designed to obtain optimal performance from the detector over its life cycle.
CAUTION
Disconnect automatic extinguishing system actuator(s) from system before powering up
detector(s). Failure to do so may result in unwanted discharge.
8.2 POWER-UP/FUNCTIONAL TESTING
1. Apply power and wait approximately 60 seconds for the manual/automatic BIT (self-test) of the detector. Note: Applying power
initiates the following sequence: The LED will flash (4Hz) yellow. Manual/automatic BIT is executed; if successful then: The LED
will flash (1Hz) green.
2. Wiring Inspection: If an open detection circuit condition exists,a fault indication will appear on the CHECKFIRE control unit display
panel. Review your wiring.
3. The detector goes into its FAULT state when supply voltage drops below 16.5V. The detector status goes back to NORMAL when
the supply voltage is above 17.5V.
4. Detector Inspection: Visually inspect the viewing window of the detector. It should be clean and clear. The LED should flash (1 Hz)
green.
5. If any of the outputs or indications is different from the description in step 4, see paragraph 9.6 for troubleshooting.
8.3 SAFETY PRECAUTIONS
After powering-up, the detector requires minimal attention in order to function properly, but the following should be noted:
1. Follow the instructions in the manual and refer to the drawings and specifications issued by the manufacturer.
2. Do not expose the detector to radiation of any kind unless required for testing purposes.
3. Do not open the detector housing.
4. Disconnect external devices, such as automatic extinguishing systems, before carrying out any maintenance.
OPERATING INSTRUCTIONS
7-1-07 Page 13
REV. 1

MAINTENANCE INSTRUCTIONS
7-1-07 Page 14
REV. 1
9 MAINTENANCE INSTRUCTIONS
9.1 SCOPE
This chapter deals with preventive maintenance, describes possible faults in detector operation and indicates corrective measures.
Ignoring these instructions may cause problems with the detector and may invalidate the warranty. Whenever a unit requires service,
please contact the manufacturer or its authorized distributor for assistance.
9.2 MAINTENANCE INSTRUMENTATION AND PERSONNEL
The detectors’ maintenance requires ordinary tools and qualified personnel who should be familiar with local codes and practices.
9.3 PREVENTIVE MAINTENANCE PROCEDURES
The detector must be kept as clean as possible. The viewing window and the reflector of the Model 20/20MI-32-S-F Flame Detector
must be cleaned on a periodic basis. The frequency of cleaning operations depends upon the environmental conditions and specific
applications. The fire detection system designer will give recommendations.
1. Disconnect power to the detector before proceeding with any maintenance including lens cleaning.
2. To clean the detector viewing window and reflector, use water and detergent, rinse with clean water. NOTE: Do not use high
pressure wash to clean detectors and connectors of cabling system.
3. Where dust, dirt, or moisture accumulate on the window, clean first with a soft optical cloth and detergent, then rinse with clean
water.
9.4 PERIODIC MAINTENANCE PROCEDURES
9.4.1 Disconnect detector and interconnect cable connections and inspect for any debris such as dirt, moisture, other contaminents,
or corrosion inside the connectors. If there is any debris present, clean with electrical contact cleaner and re-apply electrical
insulating paste (such as Dow Corning #4) to the connections. If corrosion is present, replace effected components. Before
reconnecting cables, make certain insulating paste is present. If not, re-apply.
9.4.2 Reconnect all detection and cable interconnections. Then perform a manual/automatic built-in test for each optical flame
detector in the system. Refer to Manual/Automatic Built-In Test (BIT) Instructions, 3.4, Page 8, and Power-Up/Functional
Testing Procedure, 8.2, Page 13.
Note: The power-up/functional testing procedure will initiate the manual/automatic BIT in the detectors. Disconnect power and
re-apply power for each detector to be checked.
9.5 MAINTENANCE RECORDS
It is recommended that maintenance operations performed on a detector be recorded in the system Logbook. The record should
include information which identifies the unit, the installation date, contractor, and entries including the description of the operation,
date and personnel ID for each maintenance operation performed. If a unit is sent to the manufacturer or distributor for service, a
copy of the Maintenance records should accompany it.
9.6 TROUBLESHOOTING
9.6.1 Fault Indication
1. Check power supply for correct voltage, polarity and wiring.
2. Check detector window and reflector for cleanliness. If necessary, clean the window as indicated in paragraph 9.3 above
and repeat the test.
9.6.2 False Alarm or Warning Indication
1. Disconnect the power supply from the system and check wiring.
2. Reconnect power supply and wait approximately 60 seconds. If indication remains, the unit requires service.

Part No. 432485-2 Copyright ©2007 Ansul Incorporated
ANSUL INCORPORATED
ONE STANTON STREET
MARINETTE, WI 54143-2542
Table of contents
Other Ansul Security Sensor manuals
Popular Security Sensor manuals by other brands
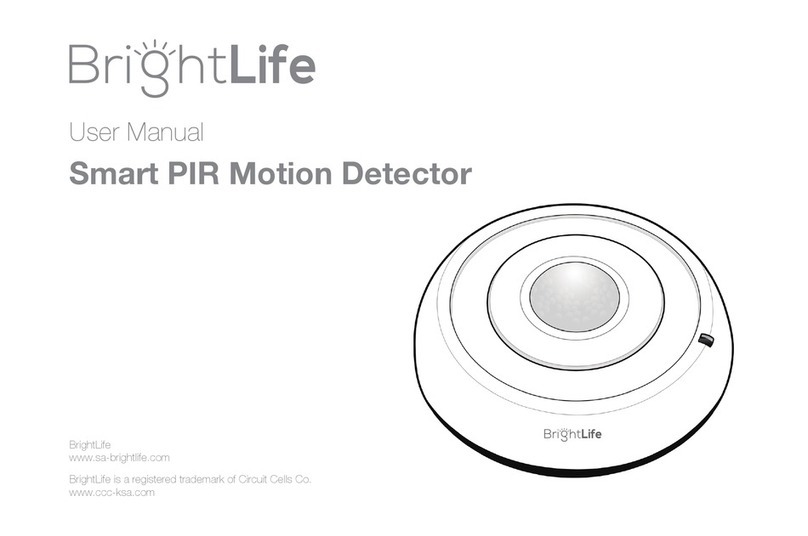
BrightLife
BrightLife Smart PIR Motion Detector user manual
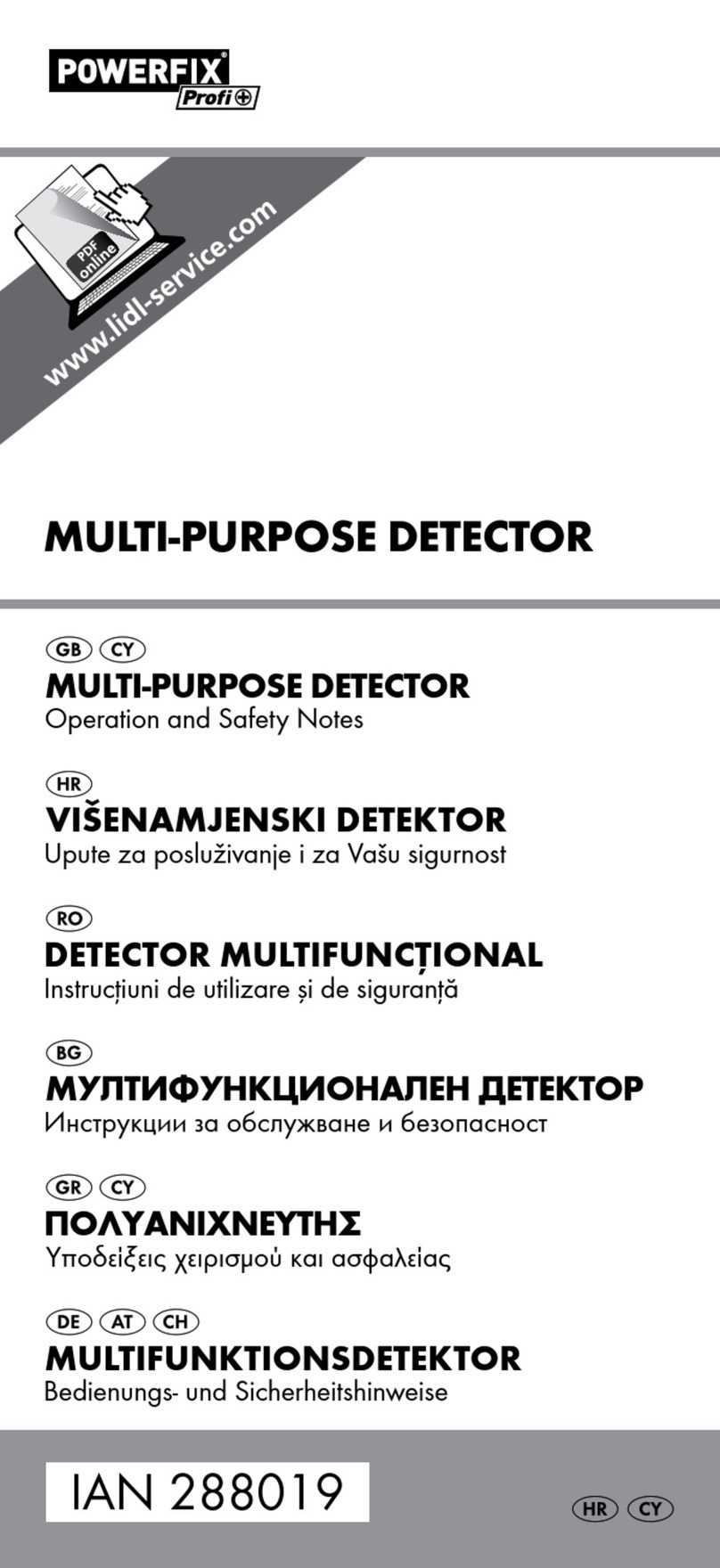
Powerfix Profi
Powerfix Profi 288019 Operation and safety notes
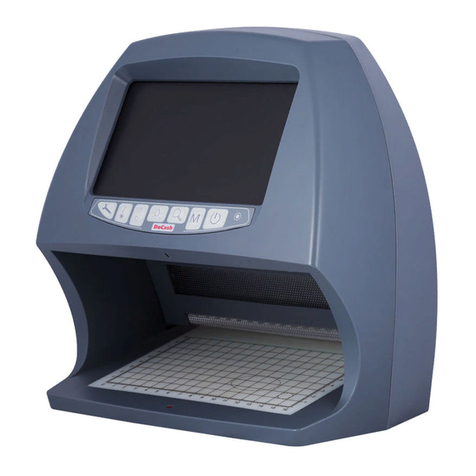
DoCash
DoCash BIG D user manual
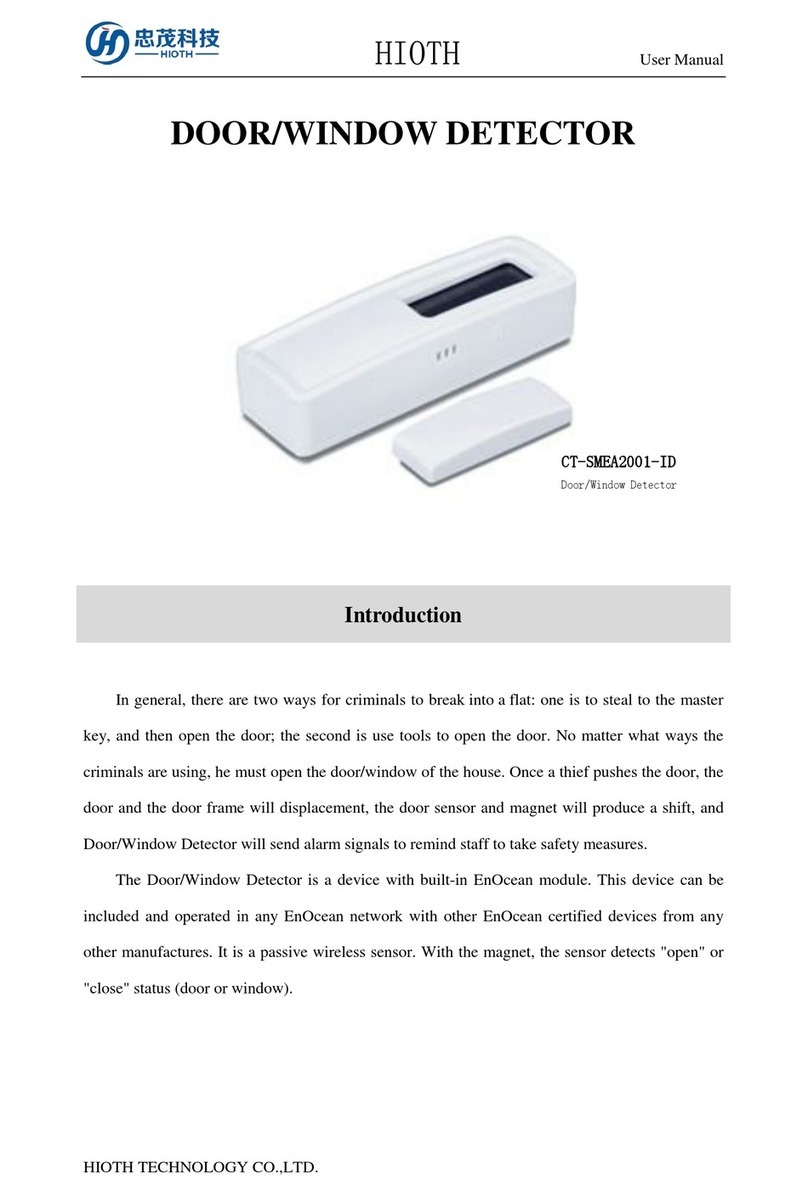
HIOTH TECHNOLOGY CO., LTD
HIOTH TECHNOLOGY CO., LTD CT-SMEA2001-ID user manual
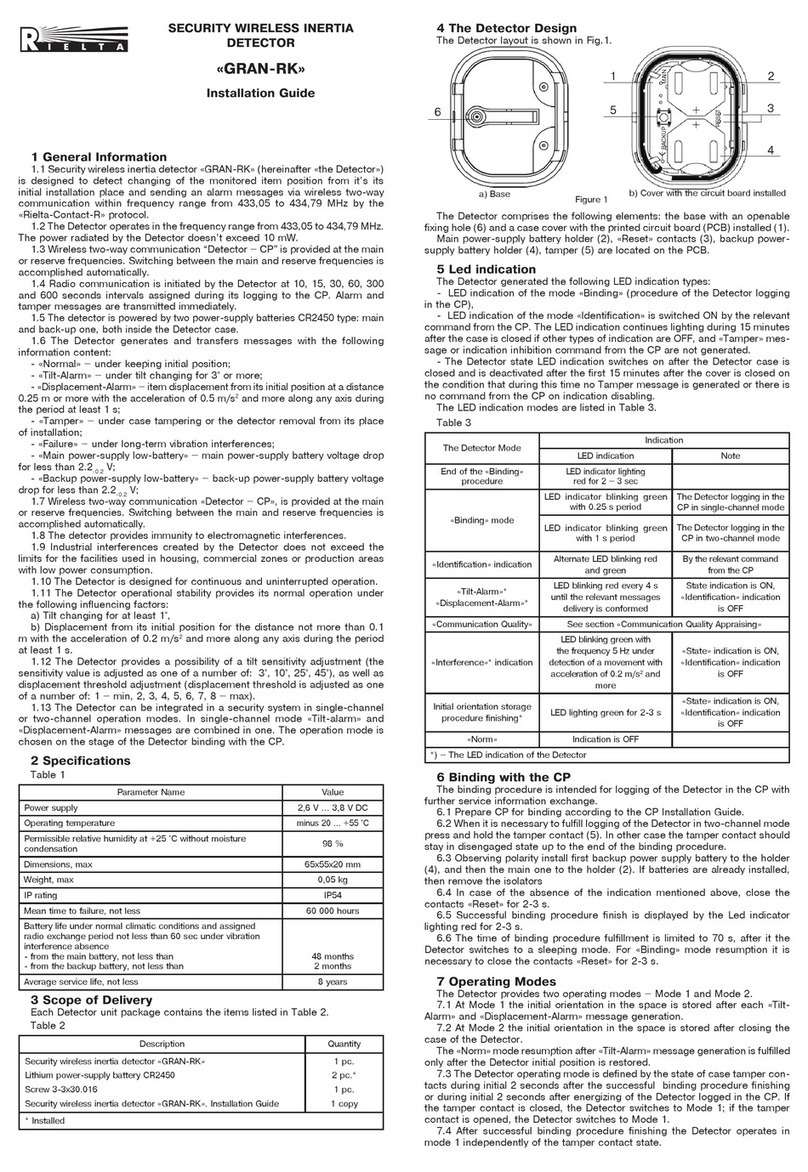
Rielta
Rielta GRAN-RK installation guide
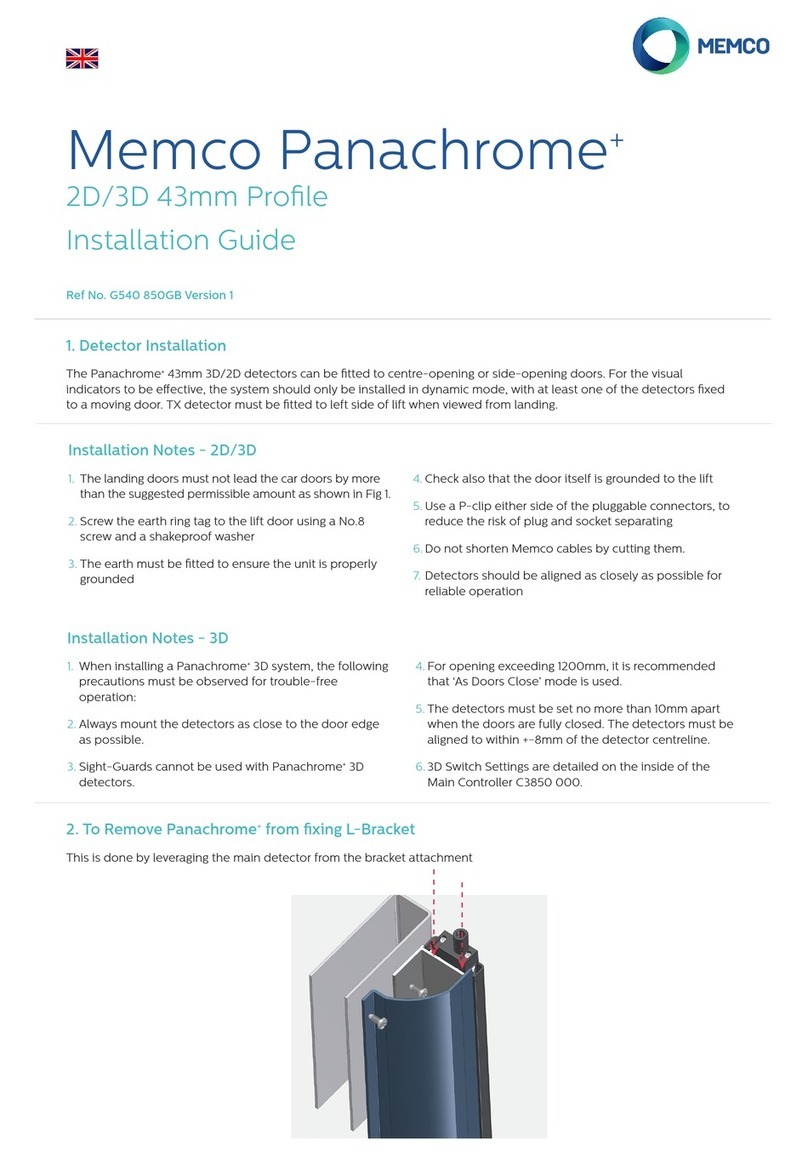
Memco
Memco Panachrome+ installation guide