Bray 70-003-113-536 Series User manual

SERIES 70 Metric
2ND GENERATION ELECTRIC ACTUATOR
METRIC VERSION - OPERATION AND MAINTENANCE MANUAL


BRAY Series 70 Metric Electric Actuator
Operation and Maintenance Manual
1
Table of Contents
Safety Instructions - Definition of Terms . . . . . . . . . . . . . . . . . . . . . . . . . . . . .2
Hazard-Free Use . . . . . . . . . . . . . . . . . . . . . . . . . . . . . . . . . . . . . . . . . .2
Qualified Personnel . . . . . . . . . . . . . . . . . . . . . . . . . . . . . . . . . . . . . . . . 2
Part Numbering System Reference Chart . . . . . . . . . . . . . . . . . . . . . . . . . . . . 3
Introduction . . . . . . . . . . . . . . . . . . . . . . . . . . . . . . . . . . . . . . . . . . . . 3
Principle of Operation . . . . . . . . . . . . . . . . . . . . . . . . . . . . . . . . . . . . 3
Electrical Operation. . . . . . . . . . . . . . . . . . . . . . . . . . . . . . . . . . . . . .3
General Electrical Schematic . . . . . . . . . . . . . . . . . . . . . . . . . . . . . . . . . 3
Mechanical Operation . . . . . . . . . . . . . . . . . . . . . . . . . . . . . . . . . . . . 3
Manual Override Operation (Declutchable) . . . . . . . . . . . . . . . . . . . . . . . . .4
Pre-Installation Storage. . . . . . . . . . . . . . . . . . . . . . . . . . . . . . . . . . . .4
Installation. . . . . . . . . . . . . . . . . . . . . . . . . . . . . . . . . . . . . . . . . . . . .4
Mounting to a Valve . . . . . . . . . . . . . . . . . . . . . . . . . . . . . . . . . . . . . 4
Field Wiring . . . . . . . . . . . . . . . . . . . . . . . . . . . . . . . . . . . . . . . . . . 4
Multiple Actuator (Parallel) Wiring . . . . . . . . . . . . . . . . . . . . . . . . . . . . . 5
Actuator Diagram without I.R.B. . . . . . . . . . . . . . . . . . . . . . . . . . . . . . . .5
Travel Limit Switch and Mechanical Travel Stop Adjustment . . . . . . . . . . . . . . . . 5
S70 On/Off Actuator with Interposing Relay Board (I.R.B.) . . . . . . . . . . . . . . . . .5
Close Travel Switch Adjustment . . . . . . . . . . . . . . . . . . . . . . . . . . . . . . . 6
Open Travel Switch Adjustment . . . . . . . . . . . . . . . . . . . . . . . . . . . . . . . 6
Disassembly and Assembly . . . . . . . . . . . . . . . . . . . . . . . . . . . . . . . . . . . . 7
Procedure . . . . . . . . . . . . . . . . . . . . . . . . . . . . . . . . . . . . . . . . . . . 7
Field or Factory Installable Options . . . . . . . . . . . . . . . . . . . . . . . . . . . . . . . 8
Torque Switches . . . . . . . . . . . . . . . . . . . . . . . . . . . . . . . . . . . . . . . . 8
Torque Switch Mechanism . . . . . . . . . . . . . . . . . . . . . . . . . . . . . . . . . . 8
Heater . . . . . . . . . . . . . . . . . . . . . . . . . . . . . . . . . . . . . . . . . . . . . 9
Installation Procedure . . . . . . . . . . . . . . . . . . . . . . . . . . . . . . . . . . 9
Servo-Pro Module . . . . . . . . . . . . . . . . . . . . . . . . . . . . . . . . . . . . . . .9
Installation Procedure . . . . . . . . . . . . . . . . . . . . . . . . . . . . . . . . . 10
Servo Calibration . . . . . . . . . . . . . . . . . . . . . . . . . . . . . . . . . . . . 10
External Signal Feedback Potentiometer . . . . . . . . . . . . . . . . . . . . . . . . . 11
Installation Procedure . . . . . . . . . . . . . . . . . . . . . . . . . . . . . . . . . 11
Set the Potentiometer . . . . . . . . . . . . . . . . . . . . . . . . . . . . . . . . . 11
Auxiliary Switches . . . . . . . . . . . . . . . . . . . . . . . . . . . . . . . . . . . . . 11
Installation Procedure . . . . . . . . . . . . . . . . . . . . . . . . . . . . . . . . . 11
Auxiliary Switch Configuration Chart . . . . . . . . . . . . . . . . . . . . . . . . . . . 12
Typical Wiring Diagram: On/Off Service . . . . . . . . . . . . . . . . . . . . . . . . . . 13
Typical Wiring Diagram: Modulating Service . . . . . . . . . . . . . . . . . . . . . . . 14
Adjustments, Calibration and Status LED of Servo Pro . . . . . . . . . . . . . . . . . . 15
Receptacles (Quick Connectors) . . . . . . . . . . . . . . . . . . . . . . . . . . . . . . 16
Spinner . . . . . . . . . . . . . . . . . . . . . . . . . . . . . . . . . . . . . . . . . . . 17
Local Control Station (Single Phase Powered Actuators) . . . . . . . . . . . . . . . . . 17
Appendix A . . . . . . . . . . . . . . . . . . . . . . . . . . . . . . . . . . . . . . . . . . . 18
Basic Tools . . . . . . . . . . . . . . . . . . . . . . . . . . . . . . . . . . . . . . . . . . 18
Appendix B . . . . . . . . . . . . . . . . . . . . . . . . . . . . . . . . . . . . . . . . . . . 19
Actuator Troubleshooting Chart . . . . . . . . . . . . . . . . . . . . . . . . . . . . . . 19
S70 Servo Pro Troubleshooting Chart . . . . . . . . . . . . . . . . . . . . . . . . . . . 20
Appendix C - Exploded Views. . . . . . . . . . . . . . . . . . . . . . . . . . . . . . . . . . 21
Series 70 - Housing Size 6. . . . . . . . . . . . . . . . . . . . . . . . . . . . . . . . . . 21
Series 70 - Housing Size 12 . . . . . . . . . . . . . . . . . . . . . . . . . . . . . . . . . 22
Series 70 - Housing Size 30 . . . . . . . . . . . . . . . . . . . . . . . . . . . . . . . . . 23
Series 70 - Housing Size 180 for 3:1 Gear Box . . . . . . . . . . . . . . . . . . . . . . . 24
Series 70 - 3:1 Gear Box . . . . . . . . . . . . . . . . . . . . . . . . . . . . . . . . . . . 25
For information on this product and other Bray products
please visit us at our web page - www.bray.com

BRAY Series 70 Metric Electric Actuator
Operation and Maintenance Manual
2
HAZARD-FREE USE
This device left the factory in proper condition to be
safely installed and operated in a hazard-free manner. The
notes and warnings in this document must be observed
by the user if this safe condition is to be maintained and
hazard-free operation of the device assured.
Take all necessary precautions to prevent damage to
the actuator due to rough handling, impact, or improper
storage. Do not use abrasive compounds to clean the
actuator, or scrape metal surfaces with any objects.
The control systems in which the actuator is installed must
have proper safeguards to prevent injury to personnel, or
damage to equipment, should failure of system components
occur.
QUALIFIED PERSONNEL
• A qualified person in terms of this document is one
who is familiar with the installation, commissioning
and operation of the device and who has appropriate
qualifications, such as:
• Is trained in the operation and maintenance of
electric equipment and systems in accordance with
established safety practices
• Is trained or authorized to energize, de-energize,
ground, tag and lock electrical circuits and equipment
in accordance with established safety practices
• Is trained in the proper use and care of personal
protective equipment (PPE) in accordance with
established safety practices
• Is trained in first aid
• In cases where the device is installed in a potentially
explosive (hazardous) location – is trained in
the operation, commissioning, operation and
maintenance of equipment in hazardous locations
!
WARNING
The actuator must only be installed, commissioned,
operated and repaired by qualied personnel.
The device generates large mechanical force during
normal operation.
All installation, commissioning, operation and maintenance
must be performed under strict observation of all applicable
codes, standards and safety regulations.
Reference is specically made here to observe all
applicable safety regulations for actuators installed in
potentially explosive (hazardous) locations.
Safety Instructions - Definition of Terms
READ AND FOLLOW THESE INSTRUCTIONS
SAVE THESE INSTRUCTIONS
WARNING indicates a potentially hazardous situation which, if not avoided, could result in death
or serious injury.
CAUTION indicates a potentially hazardous situation which, if not avoided, may result in minor
or moderate injury.
!
NOTICE
used without the safety alert symbol indicates a potential situation which, if not
avoided, may result in an undesirable result or state, including property damage.
!
!

BRAY Series 70 Metric Electric Actuator
Operation and Maintenance Manual
3
INTRODUCTION
The Bray Series 70 is a quarter turn electric actuator
with manual override for use on any quarter turn valve
requiring up to 2034 Nm of torque. Operating speeds
vary between 6 to 110 seconds.
PRINCIPLE OF OPERATION
The Series 70 actuator is divided into two internal
sections; the power center below the switchplate, and
the control center above the switchplate. Below the
switchplate the capacitor and gearmotor with its spur
geartrain drive a non-backdriveable worm gear output. The
override mechanism for manual operation is also housed
here. Above the switchplate is where user required,
readily accessible components are placed. The camshaft
assembly, limit switches, terminal strips, torque switches,
heater, and servo are all placed here for easy access.
External to the unit are adjustable mechanical travel
stops, a large easy to read indicator, the unique manual
override handwheel and dual conduit entry ports. The
external coating is a high quality polyester powder coat
which has exceptional UV as well as chemical resistance.
ELECTRICAL OPERATION
The motors used in the Bray Series 70 are either
permanent induction split capacitor design (single
phase AC power), SCI (Three Phase AC Power) or PM
(DC Power). Travel limit switches are mechanical form
(SPDT) with contacts rated at 10 amp (0.8 PF), 1/2 HP
125/250 VAC. In cases where the torque capacity of the
unit is exceeded to the point where the motor stalls and
overheats, a thermal protector switch built into the motor
windings will automatically disconnect the motor power.
Once the motor cools sufficiently the thermal protector
switch will reset. Optional torque switches are available
in all units to prevent the possibility of stalling the motor,
thus reducing the necessity for an inoperable thermal
cooldown period. Torque switches installed by Bray are
factory adjusted to the output torque rating of the unit
using electronic torque testing equipment.
!
NOTICE
Torque switches are not eld adjustable. Adjustment of torque
switches in the eld will void warranty.
GENERAL ELECTRICAL SCHEMATIC
NEUTRAL
LIVE
OPEN
CLOSE
DOUBLE
OVERRIDE
SWITCHES
THERMAL PROTECTOR
OPEN
CLOSE
CAPACITOR
TORQUE
SWITCHES
(OPTIONAL)
TRAVEL
LIMIT
SWITCHES
SINGLE
PHASE
POWER
SUPPLY
FIELD WIRING
COM
N.C.
N.O.
CAMS
MOTOR
COM
N.C.
N.O.
COM
N.C.
N.O.
COM
N.C.
N.O.
COM
N.C.
N.O.
COM
N.C.
N.O.
1
2
3
NOTE: this is only a reference. For the actual wiring diagram refer to
the diagram placed inside the actuator cover.
MECHANICAL OPERATION
Mechanically, the ratio of the gearmotor determines the
speed of the unit. The gearmotor utilizes high efficiency
spur gears with various ratios for the different speeds.
Initial gear reduction through the spur gears is then
transferred to the worm shaft. The final gear reduction
and output is through a non-backdriveable worm gear
set. Positioning is determined by an indicator-cam shaft
linked to the output shaft. In the declutchable condition
the manual override drives the worm shaft when engaged.
PART NUMBERING SYSTEM REFERENCE CHART
SerieS Torque Code Speed produCT STyle VolTage Trim
70 AAA X 113 Y Z 536
HouSing
Size parT number Torque
(Nm)
Speed, ¼Turn
(Seconds)
Supply
(Z Voltage)
6 70-003X-113YZ-536 34 30/15 0/2/4
6 70-006X-113YZ-536 68 30 0/3/4
12 70-008X-113YZ-536 90 30/15/6 0/4/8
12 70-012X-113YZ-536 136 30/15/6 0/4/9
12 70-020X-113YZ-536 226 30/15 0/2/3/4/5/6/7/8
30 70-030X-113YZ-536 339 30/18 0/2/4/5/6/7/8
30 70-050X-113YZ-536 565 30/18 0/2/3/4/5/6/7/8
30 70-065X-113YZ-536 735 30 0/2/4/5/6/7/8
180 70-13WX-113YZ-536 1469 110 0/4
180 70-18WX-113YZ-536 2034 110 0/4
Use this chart as a guide to interpret the S70 electric actuator part number.
Note: Not all combinations are possible.
W - DESIGNATES THE OUTPUT BORE DIAMETER
02.5 Inches
11.97 Inches
X - DESIGNATES THE SPEED
X: 0 1 2 3 4 5 6
Sec: 60 30 15/18 10 6 8 110
Y - DESIGNATES STYLE
MBasic Unit - Declutchable
NWith Interposing Relay Board*
P24VAC Unit with 24VAC Servo
*Only available for 120VAC or 220VAC On/Off units
Z - DESIGNATES THE VOLTAGE
Z: 0123456789
Voltage:
120VAC
12VDC
24VDC
24VAC
220VAC
380V
3-PH
400V
3-PH
440V
3-PH
480V
3-PH
208V
3-PH

BRAY Series 70 Metric Electric Actuator
Operation and Maintenance Manual
4
MANUAL OVERRIDE OPERATION (DECLUTCHABLE)
The manual override operates similar to a watch
adjusting knob. To engage the manual override, simply
pull the handwheel to its outermost position. A yellow
stripe is revealed for visual indication that the unit
cannot run electrically. The two handwheel positions,
engaged and disengaged, are held in place with the use
of spring plungers. The handwheel remains in position
until physically moved. Rotating the handwheel in the
clockwise direction will rotate the output shaft in the same
clockwise (closed) direction and vice-versa.
!
CAUTION
A label on the handwheel hub warns users not to exceed
a specic rim pull force, for each size of actuator. If the rim
pull force is exceeded, the roll pin securing the handwheel
onto the manual override shaft is designed to shear, thus
preventing more serious internal gearing damage.
PRE-INSTALLATION STORAGE
Actuators are not weatherproof until properly installed
on the valve or prepared for storage. Bray cannot accept
responsibility for deterioration caused on-site once the
cover is removed.
!
NOTICE
Units are shipped with two metal screw-in plugs to prevent
foreign matter from entering the unit. To prevent condensation
from forming inside these units, maintain a near constant
external temperature and store in a well-ventilated, clean,
dry room away from vibration.
For units with an internal heater, power should be supplied
to the heater via conduit entry and appropriate sealing gland.
Store units on a shelf or wooden pallet in order to protect
against oor dampness.
Keep units covered to protect against dust and dirt.
INSTALLATION
MOUNTING TO A VALVE
All Bray Series 70 electric actuators are suitable for direct
mounting on Bray butterfly valves. With proper mounting
hardware, the S70 actuator can be installed onto other
quarter-turn valves or devices.
!
NOTICE
The standard mounting position for the actuator is to orient
the unit with its handwheel in a vertical plane and parallel to
the pipeline. If the actuator is to be mounted on a vertical pipe,
it is recommended that the unit be positioned with the conduit
entries on the bottom to prevent condensation from entering
the actuator by way of the conduit. In all cases, the conduit
should be positioned to prevent drainage into the actuator.
The actuator should be mounted to the valve as follows:
1. Manually operate the actuator until the output shaft of
the actuator is in line with the valve stem. If possible,
select an intermediate position (i.e. valve disc/stem
and actuator both half open).
2. Place the proper adapter, if required, onto the valve
stem. It is recommended that a small amount of
grease be applied to the adapter to ease assembly.
3. Mount the actuator onto the valve stem. It may be
necessary to swing or manually override the actuator
to align the bolt patterns.
4. Install the furnished mounting studs by threading
them all the way into the actuator base.
5. Fasten in place with the furnished hex nuts and
lock washers.
FIELD WIRING
!
WARNING
Turn off all power and lock out service panel before installing
or modifying any electrical wiring.
Each actuator is provided with two (2) conduit entries
(one for power and one for control).
1. The motor full load current is noted on the nameplate
of the actuator. The terminal strip will accept wire
sizes ranging from 14 to 22 AWG (14 to 24 AWG
for the servo).
!
NOTICE
18 AWG minimum wire is recommended for all eld wiring.
Note that the optional heaters use approximately 0.5
amps at 110 volts.
2. All actuators have their applicable wiring diagram
attached to the inside of the cover. Field wiring
should be terminated at the actuator terminal strip
in accordance with this wiring diagram.
!
NOTICE
The conduit connections must be properly sealed to maintain
the weatherproof integrity of the actuator enclosure.

BRAY Series 70 Metric Electric Actuator
Operation and Maintenance Manual
5
The back feeding of one actuator by another one wired
in parallel is eliminated by using the I.R.B.
If actuator is running Open and customer switches
“instantaneously” to run Closed, the Open relay will take
time to ‘drop-out’ and the Close relay will take time to
‘pull-in’ this time lapse is ~ 40ms. The time delay provided
by the I.R.B. will protect the switches and gears from
the controller’s instantaneous command signal reversal.
Current draws and field wirings are not affected by
adding I.R.B.
S70 120VAC I.R.B., auxiliary switch, heater, and torque
switch option are UL certified units.
MULTIPLE ACTUATOR (PARALLEL) WIRING
!
CAUTION
Do not connect more than one S70 actuator which do not
have I.R.B. installed to a single SPDT switch. A voltage is
present on the opposite winding to the powered one. If this
winding is connected to another as shown in the INCORRECT
diagram it will interfere with the motor performance. Use a
multiple pole switch as shown in the CORRECT diagram.
ACTUATOR DIAGRAM WITHOUT I.R.B.
!
CAUTION
Do not reverse motor instantaneously when it is still running.
Reversing direction to actuator motor when it is running can
cause damage to motor, switches and gearing. Directional
control switching can be done by PLC in 20ms or by a small
relay in 46ms. Therefore time delay of 1s has to be incorporated
into the control scheme to avoid damage.
TRAVEL LIMIT SWITCH AND MECHANICAL TRAVEL
STOP ADJUSTMENT
!
CAUTION
The electrical travel switches must be set to activate
(depress) prior to reaching the mechanical travel stops.
The cams are color coded (green for open, red for closed).
NOTE: Manual travel stops are designed to prevent
manual overtravel from turning the handwheel, not to stop
the electric motor. The travel stops have an adjustment
range of approximately 10-degrees.
S70 ON/OFF ACTUATOR WITH INTERPOSING RELAY BOARD (I.R.B.)

BRAY Series 70 Metric Electric Actuator
Operation and Maintenance Manual
6
CLOSE TRAVEL SWITCH ADJUSTMENT
1. Loosen the mechanical stop for the closed position
and back it off so that it does not interfere with
actuator travel (closed stop located on right when
viewed from travel stop side of actuator).
2. Remove the indicator rotor by pulling up it straight
up away from the indicator shaft. This will expose
the machined groove on the end of the cam shaft,
which is the reference to the valve disc position.
NOTE: For Housing Size 180, ignore steps 2 and 6. The
valve position indicator plate on the lower gearbox is the
reference to the valve position.
3. Manually operate the actuator handwheel clockwise
until the valve reaches the desired fully closed
position.
4. Rotate the red adjusting knob by hand or with a flat
head screwdriver until the cam lobe just activates
(depresses) the switch from a clockwise direction.
5. With the travel switch in the closed position, rotate
the handwheel clockwise ½ turn for Housing Size
6, 1 turn for Housing Size 12, ½ turn for Housing
Size 30, and 2 turns for Housing Size180.Adjust the
closed travel stop bolt until it bottoms against the
output gear and lock it in position with the locknut.
6. After all travel switch adjustments have been
completed, replace the indicator rotor and secure
the actuator cover.
OPEN TRAVEL SWITCH ADJUSTMENT
1. Loosen the mechanical stop for the open position and
back it off, so that it does not interfere with actuator
travel. The open stop is located on the left, when
viewed from travel stop side of actuator.
2. Remove the indicator rotor by pulling it straight up
away from the indicator shaft. This will expose the
machined groove on the end of the cam shaft, which
is the reference to the valve disc position.
NOTE: For Housing Size180, ignore steps 2 and 6. The
valve position indicator plate on the lower gearbox is the
reference to the valve position.
3. Manually operate the actuator handwheel
counterclockwise until the valve reaches the desired
open position.
4. Rotate the green adjusting knob until the cam
lobe just activates (depresses) the switch from a
counterclockwise direction.
NOTICE: All continuous duty actuators have a cam locking
screw. Cam locking screw must be slackened before cam
adjustments and re-rightened after cam adjustments.
NOTE: It is possible that the rotation of one cam will
move the other cam. If this occurs, hold the other knobs
or cams during adjustment.
5. With the travel switch in the open position, rotate the
handwheel counterclockwise ½ turn for Housing Size
6, 1 turn for Housing Size 12, ½ turn for Housing
Size 30, and 2 turns for Housing Size 180. Adjust
the open travel stop bolt until it bottoms against the
output gear and lock in position with the locknut.
6. After all travel stop adjustments have been
completed, replace indicator rotor and secure the
actuator cover.
NOTICE: All continuous duty actuators have a cam locking
screw. Cam locking screw must be slackened before cam
adjustments and re-tightened after cam adjustments.
UPPER GREEN
“OPEN” CAM
LOWER RED
“CLOSE” CAM
POT DRIVE GEAR
“BLACK” NOT SHOWN
FOR CLARITY REASONS
CAM ADJUSTMENT KNOB
(ONLY ADJUST IF LOCKING
SCREW IS SLACKENED)
CAM
LOCKING
SCREW
NOTE: It is possible that the rotation of one cam will move
the other cam. If this occurs, hold the other knobs or cams
during

BRAY Series 70 Metric Electric Actuator
Operation and Maintenance Manual
7
DISASSEMBLY AND ASSEMBLY
Tools required:
See Appendix A for a complete list of basic tools.
PROCEDURE
!
WARNING
Turn off all power and lock out service panel before installing
or modifying any electrical wiring.
1. Disconnect motor wires from the main terminal strip
(motor neutral, open, and close).
2. Remove the switchplate by unscrewing the seven
Phillips head mounting screws. The switchplate
should lift out as an assembly with the camshaft
attached.
3. The switchplate can be independently disassembled.
4. To remove the Gearmotor, first disconnect the motor
leads which run to the capacitor, and unscrew the
mounting screws for Housing Size 6 (two lower,
one upper) for other Housing Sizes (four lower, one
upper). The motor can now be removed vertically out
of the unit. Note: do not misplace the alignment pin.
5. To remove the worm shaft spur gear, remove the
spring pin using a 2.5 mm punch, then slide the gear
off the end of the worm shaft for Housing Sizes 6
and 12. Remove bowed E-clip retainer for Housing
Size 30-180.
6. To remove the output drive worm gear, back off both
mechanical travel stops. Remove the retaining ring
and thrust washer, then lift the output drive worm
gear out of its base.
7. The handwheel is held by a spring pin.
!
CAUTION
Further disassembly of the unit requires special tools and
procedures, and thus will not be covered in this manual.
NOTE 1: Assembly is the opposite of removal
NOTE 2: Pictures shown for Housing Size 6 are typical
for all sizes

BRAY Series 70 Metric Electric Actuator
Operation and Maintenance Manual
8
FIELD OR FACTORY INSTALLABLE OPTIONS
TORQUE SWITCHES
Torque switches are a factory installed and calibrated
option available for all Series 70 units. Installation is
simple, but due to the requirement for special calibration
equipment, it is not recommended for field installation.
In fact, modifying the factory torque setting voids the
actuator warranty. Removal of the switchplate invalidates
factory calibration
The unique mechanism is extremely accurate and has
excellent repeatability. The worm is pinned to the worm
shaft, which is held in position with a stack of disc springs
at both ends. The torque transmitted through the worm
to the output worm gear acts directly against the disc
springs, which compress proportionately. The worm and
worm shaft shift longitudinally as a result.
A specially designed drive lever and pin is incorporated
into the worm, providing the profile for the torque switching
mechanism. A drive lever & pin rides in the worm gear
torque sensor groove, and in turn drives a cam. The
cam then actuates
its electrical switch,
which interrupts the
power to the motor
winding when the
torque exceeds
the setting. The
motor can still be
powered to run in the
opposite direction,
the switch will release
automatically.
TORQUE SWITCH MECHANISM
Switching Mechanism

BRAY Series 70 Metric Electric Actuator
Operation and Maintenance Manual
9
HEATER
To prevent condensation from forming inside the
actuator, Bray offers an optional heater. The heater is a
PTC (Positive Temperature Coefficient) style which has
a unique temperature - resistance characteristic. The
heater self-regulates by increasing its electrical resistance
relative to its temperature. The heater does not require
external thermostats or switches to control its heat output.
It is constructed of a polycrystalline ceramic, sandwiched
between two conductors, and wrapped inside a thermally
conductive electrical insulator.
Connect the heater wires to the terminal strip as indicated
on the wiring diagram.
NOTE: The heater must have a constant power supply
to be effective.
!
WARNING
The heater surface can reach temperatures in excess
of 200 degrees Celsius
Heater Kit Consists of:
1. Heater with flying leads
2. Heater Mounting Bracket
3. #10 pan head screw, Phillips drive
Tools required:
• For terminal wiring: Screwdriver, 5mm tip flat blade
• For heater mounting screw: Screwdriver, No.1
Phillips
INSTALLATION PROCEDURE
The heater is mounted through a hole provided in the
switchplate.
Before servicing unit, switch all power off at the service
panel and lock the service disconnecting means to prevent
power from being switched on accidentally. When the
service disconnecting means cannot be locked, securely
fasten a prominent warning device, such as a tag, to the
service panel.
Disconnect all power to the unit.
1. Place the heater snugly into its mounting bracket
until approx. 10 to 20mm is left above the bracket
as shown in diagram.
2. Slip the heater into its mounting hole.
3. Align the fastening hole in the bracket with the
threaded screw hole in the plate. Fasten the heater
to the switchplate.
4. Connect the heater wires to the terminal strip as
indicated on the wiring diagram.
SERVO-PRO MODULE
Servo kits can be field installed on any continuous duty
actuator (30, 60, or 110 sec. operation speed) to provide
proportional positioning in response to a control signal.
Intermittent duty actuators are not adaptable for servo
control.
Servo Kit Consists of:
1. One servo module
2. Four #6 cross drive pan head screw (two for servo,
two for feedback potentiometer)
3. One potentiometer assembly
4. Two #6 type A internal lockwashers (for pot)
5. One wiring diagram sticker for attaching to inside
of actuator’s cover
6. One wiring diagram sticker for servo units with
torque switches
Tools required:
• For actuator terminals wiring Screwdriver, 5mm
flatblade
• For servo terminals: Screwdriver, No.1 Phillips
• For servo and pot mounting screws: Screwdriver,
No.2 Phillips

BRAY Series 70 Metric Electric Actuator
Operation and Maintenance Manual
10
INSTALLATION PROCEDURE
• Disconnect all power to the unit.
• Remove the on/off duty, 9 point terminal strip and
its marker
1. Disconnect all wiring to the terminal strip.
2. All wiring in the actuator is color coded to facilitate
wiring, and does not need to be tagged or marked.
3. Field wiring should be marked if it is not already
color coded.
Mount the servo module
4. Secure the servo card module onto switchplate with
the 2X #6 screws.
Install the potentiometer assembly
5. The potentiometer installs next to the camshaft where
there are two threaded holes provided.
6. The potentiometer assembly must be mounted in
the correct orientation, with the actuator in its fully
open (counter clockwise) position, the indicator shaft
should be in-line with raised green rib on pot gear.
7. Push the assembly towards the cam to mesh the
pot gears. Then tighten the mounting screws.
Note: On Housing Size 180, the raised green rib on pot
gear should be aligned with arrow on lower gear box’s
position indicator plate.
8. Rotate the actuator handwheel so that the red cam
lobe is facing the body of the potentiometer. Make
sure that the cam is not touching the potentiometer
assembly. Readjust the assembly position if
necessary.
Wire the potentiometer to the servo
9. Connect the potentiometer wires into the terminal
strip on the servo module.
10. Wire according to the wiring diagram provided.
Wire the servo to the actuator
11. Wire according to the wiring diagram provided.
12. See the servo calibration instructions.
SERVO CALIBRATION
The calibration procedure defines the limits of operation
of the Series 70 Actuator between the fully open valve
position and the fully closed valve position. The cams on
the Series 70 Actuator define the fully open and closed
positions of the valve and may be set at any degree of
opening. The only requirement is that the open cam
limit setting must set at a higher degree of opening than
the closed cam limit setting. In other words, the “Open”
position must be more open than the “Closed” position.
Calibration is performed as follows:
1. Adjust the Open and Closed limit switch cams on
the Series 70 Actuator to the desired position.
2. Engage the handwheel and move the Series 70
Actuator to its mid position.
NOTE: An analog signal source is not required for
calibration. Press and hold the “Calibrate” Set pushbutton
for a minimum of 2 seconds. When the servo status LED
begins to flag rapidly, release the button. The servo will
now seek both travel limits and record these values to its
nonvolatile memory. Following a successful calibration,
the status LED will begin to flash a slow single green
flash. If the calibration is unsuccessful, the status LED
will alternately flash red and green. If this occurs, make
sure the cams and the potentiometer are set correctly.
This completes the “Self Calibration” procedure.
After completing the calibration procedure, it is good
practice to apply the fully closed and fully open Command
Signals, and verify that the S70 Actuator moves to the
proper positions.
* Refer to Servo Pro Version 3.0 Operation & Maintenance
Manual for more details
MOTOR
OPEN
1
ON
MOTOR
CLOSE
FUSE
NEUTRAL
NEUTRAL
LINE
Power
OUTPUT (+)
OUTPUT (-)
+5 VDC
INPUT (+)
INPUT (-)
OPEN
LIMIT
CLOSE
LIMIT
COMMON
COMMON
HANDWHEEL
CALIBRATE STATUS
+5 VDC
COMMON
FB POT
HIGH
VOLTAGE
SERVO
210987
6543
PRO
HEATER
DEAD BAND
CLOSE
SPEED
OPEN
SPEED
CLOSE
OPEN
COMMON
TORQUE LIMIT
CLOSE
OPEN
COMMON
CONTROL BOX
S10
S9
S8
S7
S6
S5
S4
S3
S2
S1
Green Rib

BRAY Series 70 Metric Electric Actuator
Operation and Maintenance Manual
11
EXTERNAL SIGNAL FEEDBACK POTENTIOMETER
Potentiometers for external feedback can be field
installed on all continuous duty actuators.Actuators which
are not continuous duty do not have a pot gear fitted on
their indicator shafts & must be fitted with a new shaft
which has a pot drive gear for feedback pot (see Options:
Auxiliary Switches).
Feedback Potentiometer Kit consists of:
• One potentiometer assembly
• Two #6 cross drive pan head screws
• Two #6 internal lockwashers
• One 4 point terminal strip
• One terminal strip marker for feedback pot
• One small wiring diagram sticker for the additional
potentiometer
Tools Required:
• For terminal wiring Screwdriver, 5mm tip flat blade
• For pot mounting screws Screwdriver, No.2 Phillips
INSTALLATION PROCEDURE
1. The potentiometer installs next to the camshaft
where there are two threaded holes provided for it.
2. The potentiometer
assembly must
be mounted in the
correct orientation,
with the actuator in
its fully open (counter
clockwise) position,
the indicator shaft
should be in-line with
raised green rib on
pot gear.
3. Push the assembly
towards the cam to
mesh the pot gears.
Then tighten the mounting screws.
4. Rotate the actuator handwheel so that the red cam
lobe is facing the body of the potentiometer. Make
sure that the cam is not touching the potentiometer
assembly. Readjust the assembly position if
necessary.
5. Fit the 4 point terminal strip and marker in the kit.
Before laying down the marker, cut it to obtain a
marker as illustrated: opposite
6. Wire the pot to the terminal strip using the small
stick-on wiring diagram provided.
7. Adhere the wiring diagram sticker to the inside of
the cover.
SET THE POTENTIOMETER
1. Manually operate the actuator handwheel until the
unit is in the fully closed position.
2. Rotate the black potentiometer drive gear adjustment
knob, to engage the potentiometer gear at the
closed position.
3. Manually operate the actuator to the fully open position.
AUXILIARY SWITCHES
Auxiliary switches are available, refer to chart on next
page.
NOTES:
1. All auxiliary switches have voltage -free contacts.
2. Housing Sizes 6, 12, and 30 have double lobe cams.
Housing Size 180 has single lobe cams.
3. Main limit switches are one OPEN and one CLOSE
switch.
4. Auxiliary switches are one OPEN and one CLOSE
switch, which are fixed to activate 3°before the
main switches.
5. Adjustable auxiliary switches are adjustable to any
position.
INSTALLATION PROCEDURE
1. Cut terminal strip marker to length needed with
letters facing up.
2. Mount terminal strip and marker to switchplate using
two #4-40 screws.
Green Rib
178 9
2 3 4 5 6
D
C
B
A
Cut marker as needed
(4-way shown as example)
and mount to switchplate as shown.
Aux Terminal Strip

BRAY Series 70 Metric Electric Actuator
Operation and Maintenance Manual
12
CONFIGURATION HOUSING SIZE 6 HOUSING SIZES 12 & 30 HOUSING SIZE 180
1. ON/OFF (Intermittent Duty Motor) with
Main Switches (Standard OPEN and
CLOSE switches)
2 Switch
2 Cams
Standard Assembly P/N
2 Switch
2 Cams
Standard Assembly P/N
N/A
2. ON/OFF (Continuous Duty Motor) with
Main Switches (Standard OPEN and
CLOSE Switches
2 Switch
2 Cams
& Pot Gear
Standard Assembly P/N
2 Switch
2 Cams
& Pot Gear
Standard Assembly P/N
N/A
3. ON/OFF (Intermittent Duty Motor) with
Main and 1 set of Auxiliary Switches
4 Switch
2 Cams
Kit PN/ 70-0006-22980-536
4 Switch
2 Cams
Kit PN/ 70-0012-22960-536
4 Switch
2 Cams
& Pot Gear
Standard Assembly P/N
4. ON/OFF (Continuous Duty Motor) with
Main and 1 set of Auxiliary Switches
4 Switch
2 Cams
& Pot Gear
Kit P/N 70-0006-22980-536
4 Switch
2 Cams
& Pot Gear
Kit P/N 70-0012-22960-536
4 Switch
2 Cams
& Pot Gear
Standard Assembly P/N
5. ON/OFF with Main, 1 set of Auxiliary,
and 1 Adjustable Auxiliary Switches
5 Switch
3 Cams
Kit P/N 70-0006-22983-536
5 Switch
3 Cams
Kit P/N 70-0012-22963-536
N/A
6. ON/OFF with Main, 1 set of Auxil-
iary, and 1 set of Adjustable Auxiliary
Switches
6 Switch
3 Cams
Kit P/N 70-0006-22984-536
6 Switch
3 Cams
Kit P/N 70-0012-22964-536
N/A
7. ON/OFF with Main, 1 set of Auxiliary,
and 2 adjustable Auxiliary Switches
For use with control station
only. See Factory
6 Switch
4 Cams
Kit P/N 70-0012-22961-536
6 Switch
4 Cams
& Pot Gear
8. ON/OFF with Main, 1 set of Auxil-
iary, and 2 sets of adjustable Auxiliary
Switches
N/A
8 Switch
4 Cams
Kit P/N 70-0012-22962-536
N/A
9. Servo with Main, 1 set of Auxiliary, and
1 adjustable Auxiliary Switches N/A
5 Switch
3 Cams & 1 Pot Gear
Kit P/N 70-0012-22966-536
5 Switch
3 Cams & 1 Pot Gear
10. Servo with Main, 1 set of Auxiliary, and
2 Adjustable Auxiliary Switches N/A N/A
6 Switch
4 Cams
& Pot Gear
11. ON/OFF with Main and 1 Adjustable
Auxiliary Switch
3 Switches
3 Cams
Kit P/N 70-0006-22988-536
3 Switch
3 Cams
Kit P/N 70-0012-22968-536
N/A
12. Servo with Main and 1 Adjustable
Auxiliary Switch N/A
3 Switch
3 Cams & 1 Pot Gear
Kit P/N 70-0012-22971-536
N/A
AUXILIARY SWITCH CONFIGURATION CHART

BRAY Series 70 Metric Electric Actuator
Operation and Maintenance Manual
13
Wiring diagram for basic unit with Form-C (SPDT) travel limit switches, I.R.B., and double override switches.
(Drawn for actuator in its fully closed condition.)
Wiring diagram for unit with Form-C (SPDT) travel limit switches, “Voltage Free” Auxiliary open/close switches, I.R.B.,
double override switches and torque switches. (Drawn for actuator in its fully closed condition.)
Actuator Form-C Switches, SPDT
Housing Size: 6
V3-Sw
Housing Size:12, 30 & 180
V3-Sw with Lever
TYPICAL WIRING DIAGRAM: ON/OFF SERVICE
N.C.
N.O.
COM.
N.C.
N.O.
COM.

BRAY Series 70 Metric Electric Actuator
Operation and Maintenance Manual
14
Warning: Turn ALL Power Off prior to adjusting DIP switches.
SWITCH COMMAND INPUT
4-20 mA DC 0-5 VdC * 0-10 VdC 2-10 VdC
1Off On On On
2Off Off On On
3Off Off Off On
OUTPUT
4-20 mA DC 0-5 VDC 0-10 VDC 2-10 VDC
4Off On On N/A
5 On Off Off N/A
6Off On Off N/A
Forward Acting Reverse Acting
7Off On
Fail in Last Position Fail Enable **
8Off On
Fail Close Fail Open
9Off On
Torque Torque
Switch Enable Switch Disable
10 Off On
*To control servo with a remote potentiometer, set the Command Input to 0-5VDC (see Command Signal Connector section; page 8 Servo
Pro Manual).
**Fail position is the position that the servo will travel to when the control signal is removed. It does not apply to 0-5VDC or 0-10VDC
Command Signals.
TYPICAL WIRING DIAGRAM: MODULATING SERVICE
Wiring diagram for unit with Form-C (SPDT) travel limit switches, “Voltage Free” Auxiliary open/close switches,
Servo and double override switches. (Drawn for actuator in its full closed position.)

BRAY Series 70 Metric Electric Actuator
Operation and Maintenance Manual
15
A. Adjust the open and close speed of your actuator
(The fastest closing speed of your actuator is
printed on the label of the unit):
1. Use the Close Speed trim pot to adjust the closing
speed of your actuator (pot in the fully CCW position
equals fastest close speed).
2. Use the Open Speed trim pot to adjust the opening
speed of your actuator (pot in the fully CCW position
equals fastest open speed).
B. Calibrate the Servo:
1. Manually position your actuator somewhere in mid
position; away from the travel limits.
2. Disengage your handwheel (push it back in towards
the actuator), hold down the Calibration push button
for two seconds and release, the servo will begin
to drive the actuator in the close direction and then
in the open direction in order to save these limits
to memory.
3. Following a successful calibration the servo’s Status
LED will begin to flash the normal operation code, an
unsuccessful calibration will yield a Red-Green-Red-
Green flash immediately following the attempted
calibration (for more information on the Status LED
flash codes see the Status LED Flash Code Table).
Table 2: Status LED Flash Codes
Green Status LED warning and information Flash Codes:
#Indication Reason Solution
1 Steady Green Flash Normal Operation Servo Functioning Ok
2 2 Green Flashes Calibration Defaults Loaded Adjust travel limits, push autocalibration PB
3 3 Green Flashes Reverse Acting Mode If you would like your servo to not operate in reverse acting mode,
set DIP switch 7 accordingly
4 4 Green Flashes 2-10VDC Input Command Signal Selected If you require a different conguration, set DIP switches 1, 2, and 3 accordingly
5 1 Red Flashes Handwheel engaged Push the Handwheel in towards the actuator
6 2 Red Flashes Command Signal Failure Set DIP switches accordingly, send servo appropriate signal
7 3 Red Flashes Feedback Pot Fault Position the feedback Pot correctly, see Feedback Pot calibration
8 4 Red Flashes Limit Switch Fault Check wiring of limit switches, ensure that both switches are not tripped
simultaneously
9 5 Red Flashes Torque Switch Fault Ensure that DIP switch 10 is positioned correct, check wiring of torque switches,
reverse direction of actuator, correct over torque condition
10 6 Red Flashes Feedback Pot Wired In Reverse Correctly wire the Feedback Pot
Note: A ashing green LED provides status and warning information. The servo will operate normally in this state. Some ash
codes indicate a warning, where the servo has recovered automatically such as the detection of an invalid calibration. In this case,
a default calibration is automatically loaded that will allow the Servo to operate, but may not be a perfect match to the actuator.
The servo should be re-calibrated as soon as possible.
ADJUSTMENTS, CALIBRATION AND STATUS LED OF SERVO PRO
Status LED
The “Status LED” is a bi-color LED which provides detailed information regarding the operation of the S70 Servo Pro.
Table 2 below illustrates the different combinations of LED flash codes and their corresponding conditions. Following
the table is a more descriptive explanation of the Flash Code. Whenever the LED is flashing green, regardless of
the flash code, the servo will operate, but not necessarily optimally. Whenever the LED flash codes are RED, the
servo will not operate. An example is an engaged handwheel, the Status LED will flash a single red flash code and
will not operate.

BRAY Series 70 Metric Electric Actuator
Operation and Maintenance Manual
16
RECEPTACLES (QUICK CONNECTORS)
Unless otherwise specified, power receptacles will be
5-pin mini style standard duty with a black anodized
aluminum finish. They conform to ANSI B93.55M except
in wire color. Euro receptacles will be used for low power
instrument and signal cable since they can be supplied
shielded. Wiring diagrams for plug-in receptacles for
either the Bray Series 70 or the local control station will
be provided as a separate diagram. Units ordered with
pin connector receptacles factory installed are wired
and tested. Cordsets which fit these receptacles may be
ordered in several lengths.
Receptacle Kit consists of:
1. Receptacle(s), male pin and male thread M20, in the
quantity, style, and number of pins ordered
2. Reducing bushing M25 to M20 for installation in
Housing Sizes 12 - 180 and control stations
3. Wiring diagram (SK-# below)
Tools required:
• For terminal wiring: Screwdriver, 5mm tip flat blade
• For Mini or Euro receptacle: Wrench, 25mm
Installation procedure:
1. Screw the receptacle into the actuator conduit entry
using Teflon tape or similar.
2. Wire to the terminal strip according to the wiring
diagram or the field wiring requirements.
Wiring Schematic for Optional Pin Connector Receptacles
no l.C.S.1WiTH l.C.S.1
requiremenTS reCepTaCleS req’d diagram diagram
on - oFF uniTS (inTermiTTenT or ConTinuouS)
poWer one mini SK-960517 SK-960515
poWer poSiTion indiCaTion2one mini one euro SK-960717 SK-960513
poWer poSiTion indiCaTion3one mini one euro SK-960516 SK-9607165
poWer FeedbaCK poTenTiomeTer one mini one euro SK-960718 SK-960720
poWer poSiTion indiCaTion3FeedbaCK poTenTiomeTer one mini 6-pin euro4SK-960719 N/A
Custom configurations are possible - consult the factory.
1L.C.S.: Local Control Station , WHICH implies mounted to
the actuator
2Travel indication is wired to the supply voltage
3 Travel indication wiring is voltage free
4
A 6-pin EURO connector is required for this application,
consult factory for price and availability.
5The Local Control Station comes standard with 120 Volt
lamp bulbs, for other voltages consult factory.
Note: the Control Station lights must be wired to the same
voltage as the remote end of travel indication.
Euro receptacles use 22 AWG wire rated at 250V, 4 Amp.
Pin conguration interfaces with European standards.
Mini receptacles use 18 AWG wire rated at 300 V, 9 Amp.
Pin conguration conforms to ANSI B93.55M.
* For requirements beyond these ratings consult the factory.

BRAY Series 70 Metric Electric Actuator
Operation and Maintenance Manual
17
SPINNER
A spinner is available to ease and speed the manual
override of the Bray Series 70 actuator. The Housing Size
6 units mount the spinner on a lever which screws onto
the back of the handwheel. The Housing Size 12-180
units mount the spinner on the rim of the handwheel.
Note that care should be exercised in the use of spinner
equipped handwheels. Rapid operation of the handwheel
to close the valve may cause water hammer. Also, rapid
travel into a travel stop may cause damage.
Spinner Kit Consists of:
For Housing Size 6 For Housing
Sizes 12-180
Spinner and lever
assembly Spinner handle
Flat head socket cap
screw, #10-32UNF x 3/8
Socket head
shoulder bolt,
1/4-20UNC x .75
Tools required:
• For socket head shoulder bolt and flat head capscrew
• Hex key, 1/8” for Housing Size 6
• Hex key, 3/16” for Housing Sizes 12-180
Installation procedure:
• For Housing Size 6 units simply position the lever
onto the back of the handwheel then screw the flat
head cap screw in to place from behind.
• For Housing Size 12-180 units, put the socket head
shoulder bolt through the spinner handle and screw
it firmly into the handwheel rim.
LOCAL CONTROL STATION (SINGLE PHASE POW-
ERED ACTUATORS)
Bray’s local control station gives the user the ability to
locally override the actuator electrically. The station is
open / stop / close operation in the local control mode.
Red and green end of travel indication lights are also
provided. Depending on how it is wired the control station
can be used on the on - off units and the servo controlled
modulating units. Optional key operated locking switches
are available.
Note: The control station used with On - Off S70 and that
used with modulating S70 have different contact blocks
internally, the correct part number must be used to ensure
you order the correct unit (see price sheet).
Local Control Station Kit consists of:
1. Local control station assembly
2. Four socket head cap screws, #10-24UNC x 4.50
long, for mounting the station to the actuator
3. A gasket for sealing the station to the actuator
4. Wiring diagram
Tools required:
• For tapping control station mounting holes on
actuator, #10-24UNC Tap.
• For wiring Screwdriver, 3/16” flat blade.
• For mounting and cover screws Hex key, 5/32”
Installation procedure:
1. Tap #10-24UNC
holes using the
cored holes on the
side of actuator.
2. Adhere the gasket
to the control box.
3. Mount the control
box to the actuator
using the 4 long
socket head
capscrews.
4. Wire the control box to the actuator in accordance
to the wiring diagram provided. The local control
station contains
no terminal
strips, and all
wiring is direct
to the switches
and lights via
2” x 3/4” NPT
holes in bottom
of housing.
Ordering the
control station
with optional pin
connector receptacles will eliminate the necessity
of field wiring. The units will be completely factory
wired and tested.
Note: The inclined cover of the local control station can
be mounted in any of its four symmetrical positions. If field
wiring is required , first mount the base to the actuator,
then remove the cover to gain access for wiring.
*Local Control Station requires a dedicated set of auxiliary
switches for control station use only. Two additional
adjustable auxiliary switches are needed for remote
indication of open/close position in ON/OFF configurations

BRAY Series 70 Metric Electric Actuator
Operation and Maintenance Manual
18
APPENDIX A
BASIC TOOLS
Common To All Units
Terminal connections, cam adjustment Screwdriver, 6 mm tip at tip blade
All switches, terminal strip, torque switch plate Screwdriver, No.1 Phillips
Switchplate screws, capacitor Screwdriver, No.2 Phillips
Servo trimmer pots Screwdriver, 3 mm at tip for trim pots
34-68 Nm Units
Mounting nuts Wrench, M8
Cover captivated capscrews Hex Key, M8
Travel stop adjusting bolts Wrench, M6
Travel stop jam nuts Wrench, M6
Motor mount socket at head capscrew Hex Key, 3⁄32"
Motor mount socket head capscrew Hex Key, 9⁄64"
Conduit Entry Plug Hex Key, M20
90-136 Nm Units
Mounting nuts (small pattern) Wrench, M8
Mounting nuts (large pattern) Wrench, M12
Cover captivated capscrews Hex Key, M10
Travel stop adjusting bolts Wrench, M10
Travel stop nuts Wrench, M10
Motor mount socket head capscrew Hex Key, 5⁄32"
Conduit Entry Plug Hex Key, M25
339-735 Nm Units
Mounting nuts (Small pattern) Wrench, M12
Mounting nuts (Large pattern) Wrench, M20
Travel stop jam nuts Wrench, M12
Cover captivated capscrews Hex Key, M20
Travel stop adjusting studs Wrench, M12
Motor mount socket head shoulder bolt Hex Key, M12
Motor mount socket head cap screws Hex Key, 3⁄16"
Conduit Entry Plug Hex Key, M25
1469-2034 Nm Units
Mounting nuts (Small pattern) Wrench, M12
Mounting nuts (Large pattern) Wrench, M20
Travel stop jam nuts Wrench, M16
Cover captivated capscrews Hex Key, M12
Travel stop adjusting studs Wrench, M25
Motor mount socket head shoulder bolt Hex Key, 5⁄32"
Motor mount socket head cap screws Hex Key, 3⁄16"
Conduit Entry Plug Hex Key, M25
This manual suits for next models
10
Table of contents
Other Bray Controllers manuals
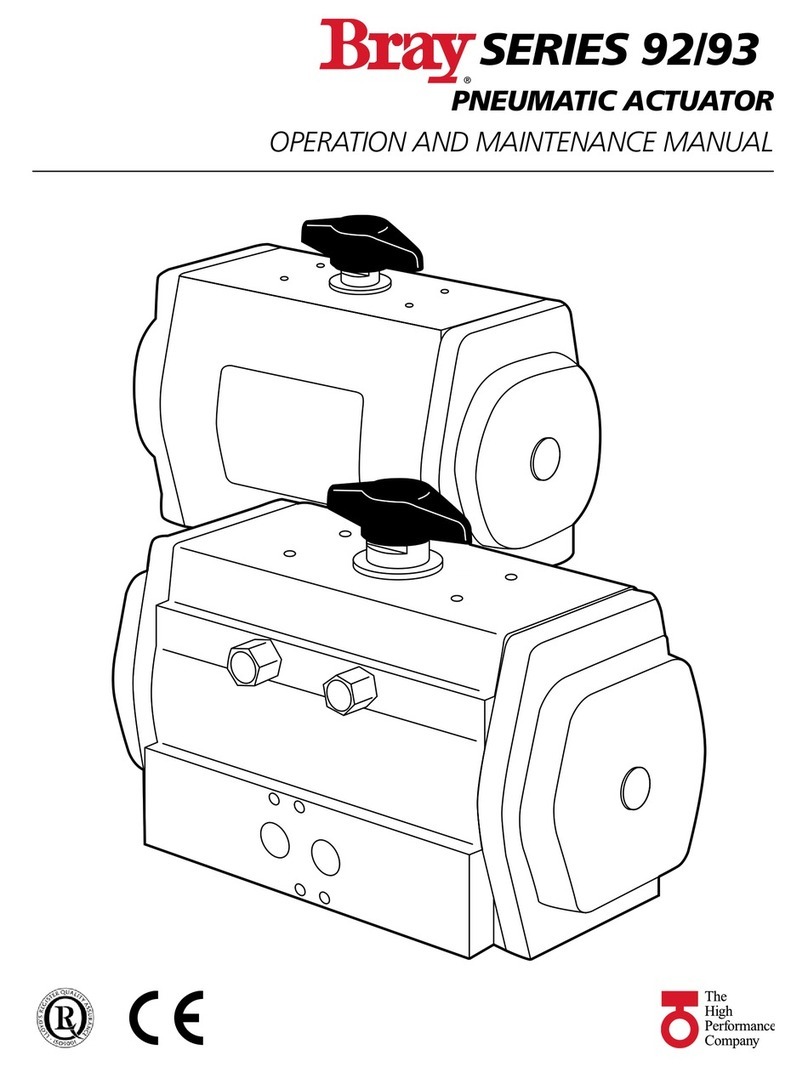
Bray
Bray 92 Series User manual
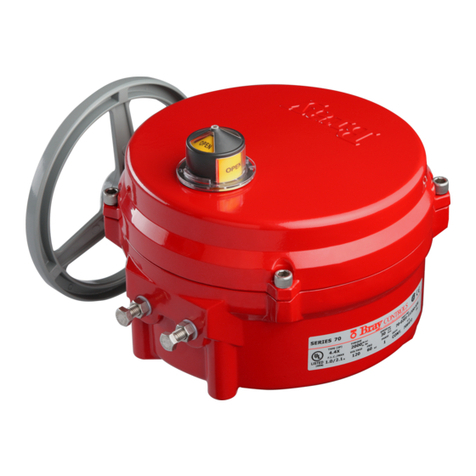
Bray
Bray Series 70 User manual
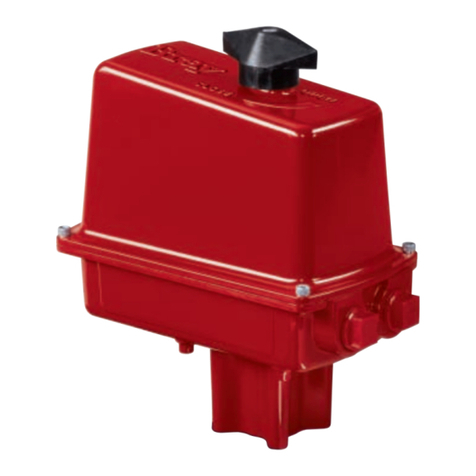
Bray
Bray 73 Series User manual
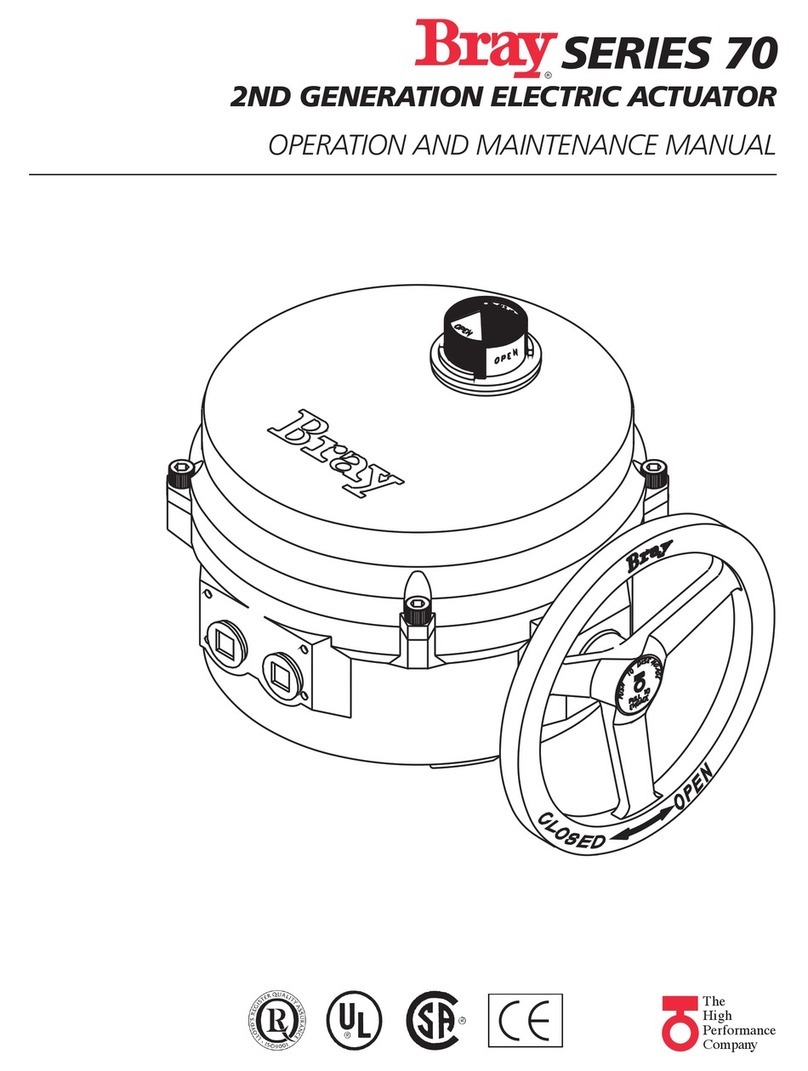
Bray
Bray Series 70 User manual
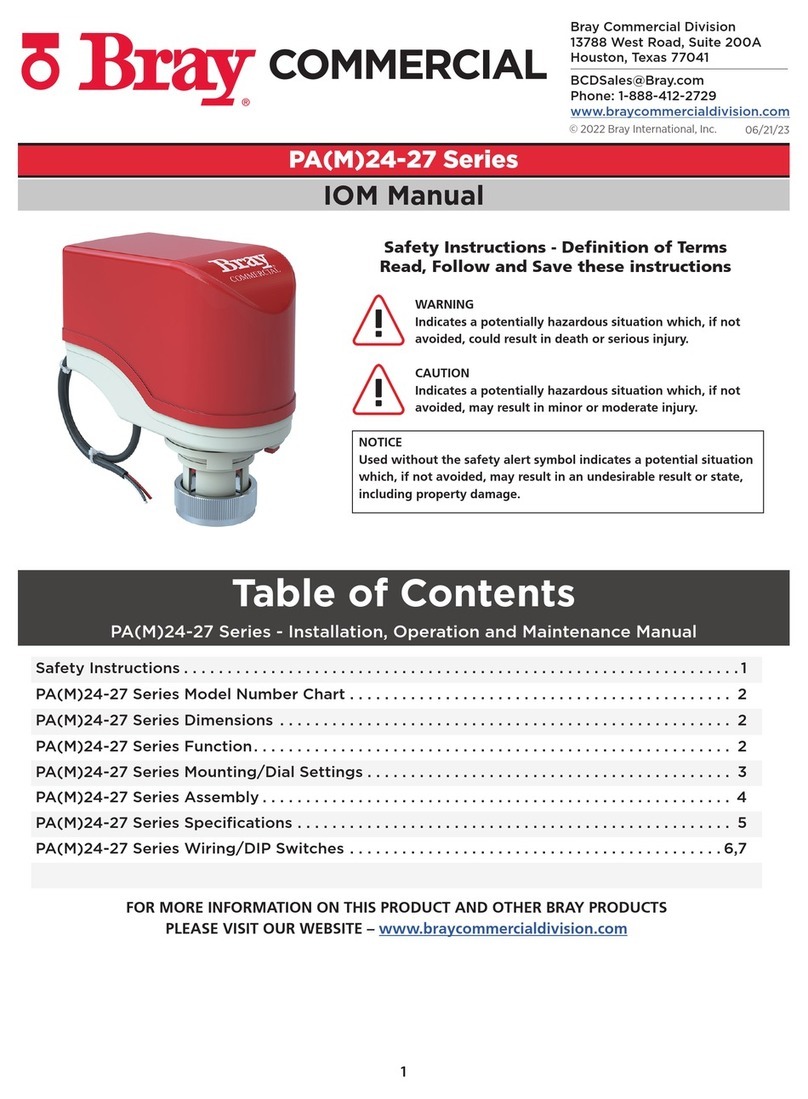
Bray
Bray PA(M)24-27 Series User manual

Bray
Bray Series 70 User manual
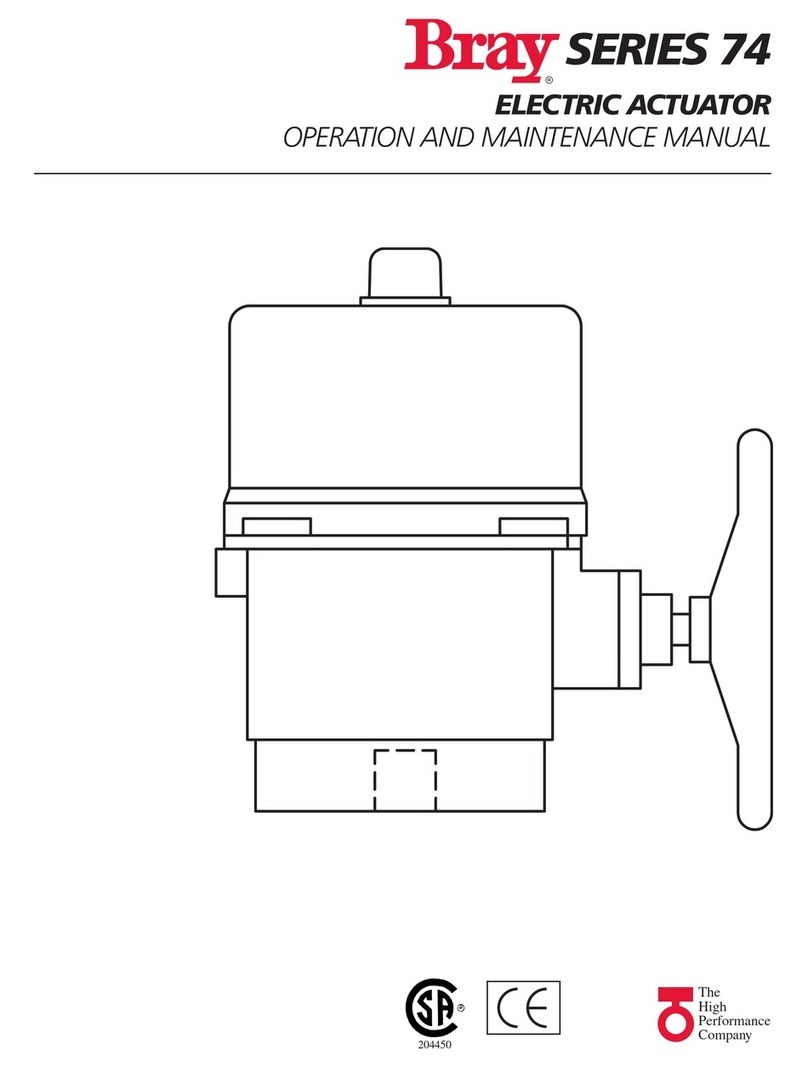
Bray
Bray 75 Series User manual
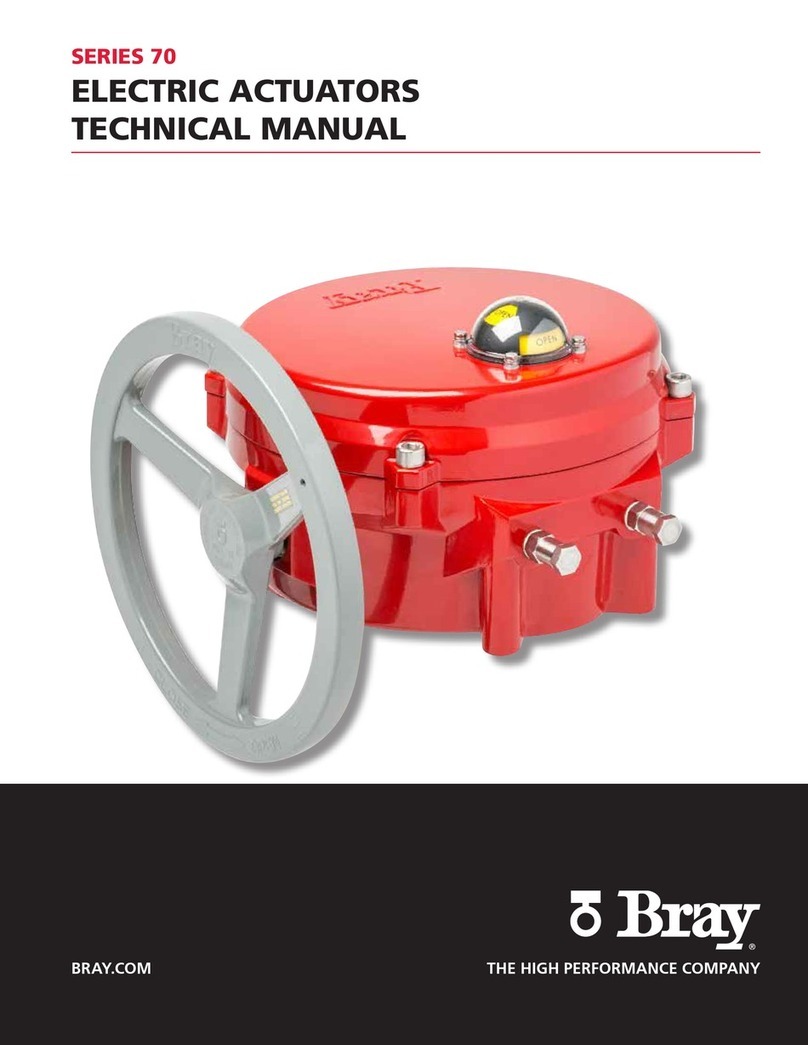
Bray
Bray Series 70 User manual
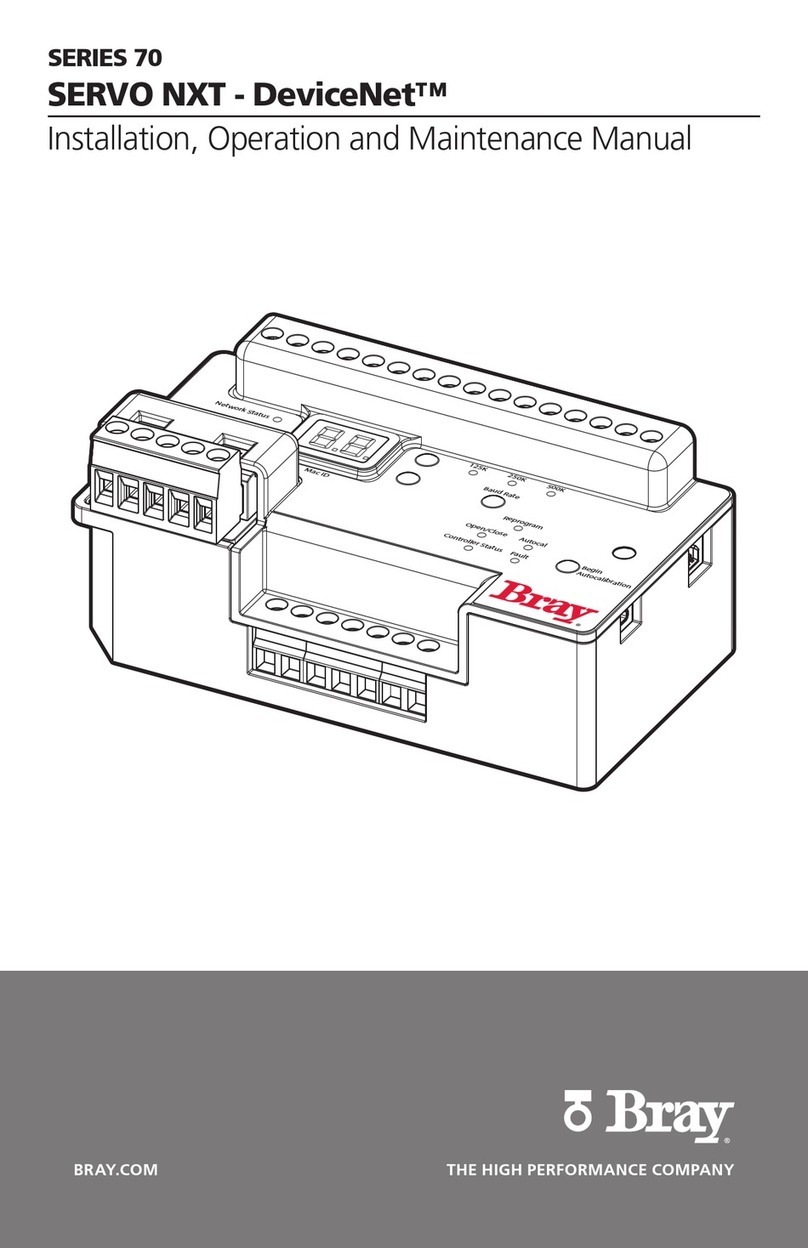
Bray
Bray Series 70 User manual
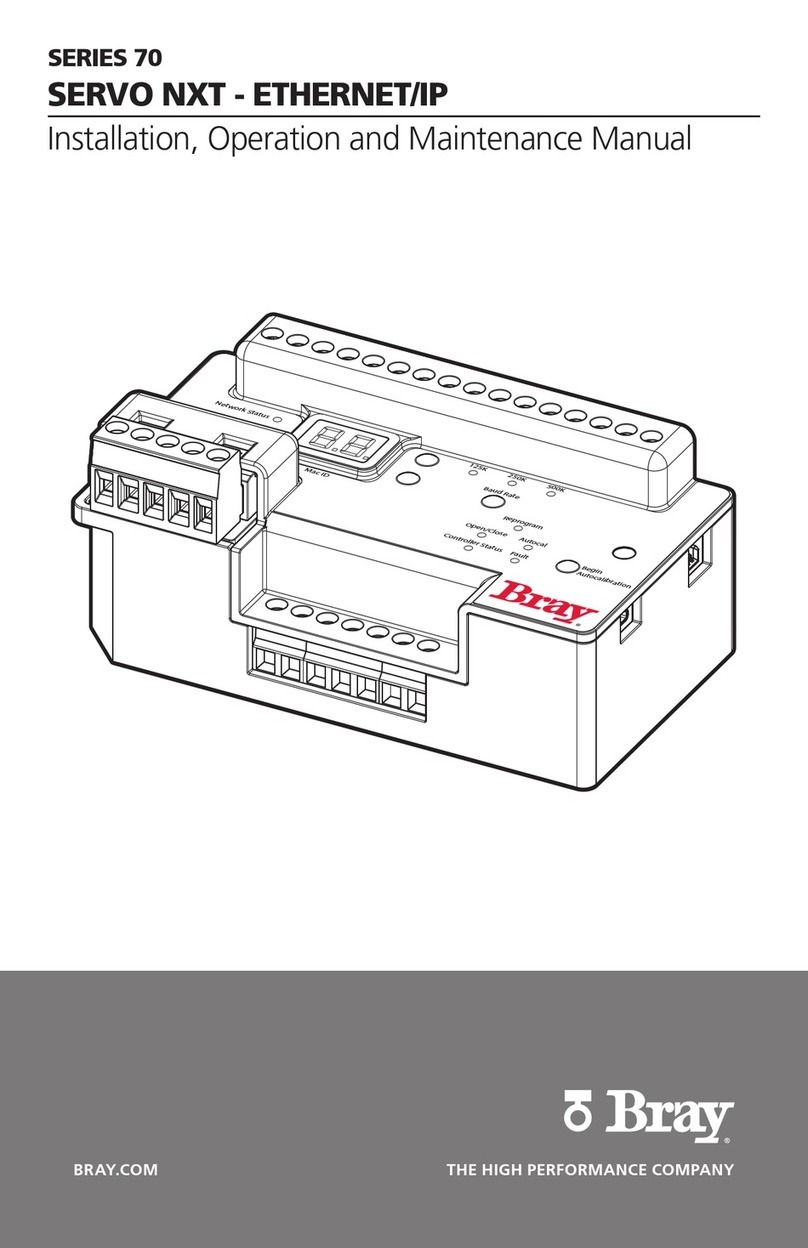
Bray
Bray Series 70 User manual