Edwards Barocel 7045 User manual

W603200880_A Original Instructions
Barocel 7045 Gauge
INSTRUCTION MANUAL
edwardsvacuum.com

W603200880_A - Copyright notice
Page 2
Copyright notice
©Edwards Limited 2019. All rights reserved.
Trademark credits
Edwards and the Edwards logo are trademarks of Edwards Limited, Innovation Drive,
Burgess Hill, West Sussex RH15 9TW.
VCR® Swagelok Marketing Co.
Disclaimer
The content of this manual may change from time to time without notice. Edwards accepts no
liability for any errors that may appear in this manual nor does it make any expressed or
implied warranties regarding the content. So far as is reasonably practicable Edwards has
ensured that its products have been designed and constructed so as to be safe and without
risks when properly installed and used in accordance with Edwards operating instructions.
Edwards accepts no liability for loss of profit, loss of market or any other indirect or
consequential loss whatsoever.
Product warranty and limit of liability are dealt with in Edwards standard terms and conditions
of sale or negotiated contract under which this document is supplied.
You must use the Barocel 7045 as described in this manual. Read this manual before you
install, operate and maintain the Barocel 7045.

P20010230A
CE Declaration of Conformity
The following product
List products here including –
•Barocel 7025m Series Capacitance Manometer W6011*
•Barocel 7025 Series Capacitance Manometer W6021*
•Barocel 7045 Series Capacitance Manometer W6032*
•Barocel 7100 Series Capacitance Manometer W6033*
Is in conformity with the relevant requirements of European CE legislation:
2014/30/EU
Electromagnetic compatibility (EMC) directive
2011/65/EU
Restriction of certain hazardous substances (RoHS) directive
as amended by Delegated Directive (EU) 2015/863
Based on the relevant requirements of harmonised standards:
EN 61010-1:2010
Safety requirements for electrical equipment for measurement, control and laboratory
use. General requirements
EN 60529:1991 +
A2:2013
Specification for degree of protection provided by enclosures (IP code)
– IP code 30
EN 61326-1:2013
Electrical equipment for measurement, control and laboratory use. EMC requirements.
General requirements
Class B Emissions, Industrial Immunity
This declaration, based on the requirements of the listed Directives and EN ISO/IEC 17050-1, covers all product
serial numbers from this date on: 6th June 2019.
Larry Marini – Senior Technical Manager
Eastbourne
Andy Marsh – General Manager
Eastbourne
Edwards Ltd
Innovation Drive
Burgess Hill
West Sussex
RH15 9TW
UK

This product has been manufactured under a quality management system certified to ISO 9001:2015
Additional Legislation and Compliance Information
EU RoHS Directive: Material Exemption Information
This product is compliant with no Annex III or IV Exemptions
EU REACH Regulation Compliance
This product is a complex article which is not designed for intentional substance release. To the best of our knowledge
the materials used comply with the requirements of REACH. The product manual provides information and instruction to
ensure the safe storage, use, maintenance and disposal of the product including any substance-based requirements.
Article 33 Declaration
This product does not knowingly or intentionally contain Candidate List Substances of Very High Concern above 0.1%ww
by article as clarified under the 2015 European Court of Justice ruling in case C-106/14.
ADDITIONAL INFORMATION
材料成分声明
China Material Content Declaration
表示该有害物质在该部件的所有均质材料中的含量低于 GB/T 26572 标准规定的限量要求。
Indicates that the hazardous substance contained in all of the homogeneous materials for this part is
below the limit requirement in GB/T 26572.

Page 3
W603200880_A - Contents
Introduction 7
Product identification .................................................................................................... 7
Intended use .................................................................................................................. 7
Function ......................................................................................................................... 7
Before using this gauge .................................................................................................. 7
Safety symbols ............................................................................................................... 8
Safety precautions .........................................................................................................8
Liability and warranty .................................................................................................... 8
Technical data 9
Dimensions ................................................................................................................... 11
Analogue measurement signal versus pressure .......................................................... 12
Installation 13
Vacuum connection ..................................................................................................... 13
Electrical connection .................................................................................................... 14
D-Sub, 15-pin connector .................................................................................... 15
Operation 16
Status indication .......................................................................................................... 16
To zero the gauge ........................................................................................................ 16
<ZERO> Adjustment ........................................................................................... 17
<ZERO> Adjustment with ramp function ........................................................... 18
Switching functions ...................................................................................................... 19
Adjusting the setpoints ...................................................................................... 20
To activate the factory setpoint (factory reset) ........................................................... 21
Uninstallation 22
Maintenance and repair 23
Return the equipment for service 24
Disposal 25
Separating the components ......................................................................................... 25
Contents

This page has been intentionally left blank.
Page 4
W603200880_A - Contents

Page 5
W603200880_A - List of Figures
Figure 1: Dimensions .............................................................................................................. 11
Figure 2: Analogue measurement signal versus pressure ...................................................... 12
Figure 3: Connect the gauge to the system ............................................................................ 14
Figure 4: D-Sub 15-pin sensor cable ....................................................................................... 15
Figure 5: Measurement signal (pressure p) ...........................................................................20
List of Figures

Page 6
W603200880_A - List of Tables
Table 1: General ....................................................................................................................... 9
Table 2: Output signal .............................................................................................................. 9
Table 3: Gauge identification ................................................................................................... 9
Table 4: Switching functions .................................................................................................... 9
Table 5: Status relay ............................................................................................................... 10
Table 6: Diagnostic port .........................................................................................................10
Table 7: Electrical ................................................................................................................... 10
Table 8: Materials exposed to vacuum .................................................................................. 11
Table 9: Environmental .......................................................................................................... 11
List of Tables

Page 7
W603200880_A - Introduction
Introduction
Product identification
Specify the information given on the gauge nameplate in all communications with Edwards.
Intended use
The Barocel 7045 gauge is intended for absolute pressure measurement of gases in their
respective pressure ranges, see Technical data on page 9.
The gauges belong to the Barocel 7000 series and can be operated in connection with an
Edwards vacuum gauge controller or another applicable unit.
Function
A ceramic diaphragm is deflected by pressure. The deflection is measured capacitively and
converted into an analogue linear output signal by the digital electronics.
The output signal is independent of the gas type.
Very accurate pressure measurement is achieved by the sensor being heated to a constant
temperature of 45 °C which results in a compensation of changes in the ambient conditions
and a reduced deposition of process products and by-products in process applications.
Before using this gauge
Make sure that the model is the same as you ordered and there was no damage during
shipment.
Read this instruction manual before you install, operate, inspect, or service this gauge to
familiarize yourself with safety precautions, specifications and operations.

Page 8
W603200880_A - Introduction
Safety symbols
Important safety information is highlighted as WARNING and CAUTION instructions. Obey the
safety instructions.
The use of warnings and cautions is defined as:
Safety precautions
Obey the applicable regulations and follow the necessary precautions for the process
media used. Reactions with the gauge materials are possible.
Obey the applicable regulations and follow the necessary precautions for the work
you do. Obey the safety instructions in this document.
Before you start work, find out if any vacuum components are contaminated. Obey
the applicable regulations and the necessary precautions when you handle
contaminated parts.
Ensure all other users are aware of the safety instructions.
Liability and warranty
Edwards accepts no liability and the warranty becomes non applicable if the end user or third
parties:
Ignore the information in this document
Use the gauge in a non-agreeable manner
Make any kind of interventions (modifications, alterations, etc.) on the gauge
Use the gauge with accessories not listed in this instruction manual.
The customer assumes the responsibility along with the process media used.
Gauge failures because of contamination are not included in the warranty.
WARNING:
Warnings are given where failure to obey the instruction could result in injury or death to
people. The symbol shown will change and refer to the applicable hazard.
CAUTION:
Cautions are given where failure to obey the instruction could result in minor injury or
damage to the equipment, associated equipment or process.

Page 9
W603200880_A - Technical data
Technical data
Table 1 General
Measurement range "Validity"
Accuracy*
*Non linearity, hysteresis, repeatability at 25 °C ambient operating temperature without
temperature effects after operation of 2 hours.
0.15% of reading
Temperature effect on zero
0.1 F.S. 0.0050% F.S./ °C
1.0 to 1100 F.S. 0.0025% F.S.
Temperature effect on span 0.01% of reading /°C
Resolution 0.003% F.S.
Gas type dependence None
Mass 837 to 897 grams
Table 2 Output signal
Output signal analogue (measurement
signal)
Voltage range -5 to +10.24 V (limited to +10.24 V)
Measurement range 0 to +10 V
Relationship voltage-pressure Linear
Output impedance 0 (short-circuit proof)
Loaded impedance > 10 k
Response time*
*Increase 10 to 90% F.S.R.
0.25 Torr/mbar (F.S.) 30 ms
0.1 Torr/mbar (F.S.) 130 ms
Table 3 Gauge identification
Resistance Rident
Voltage
Resistance 13.2 k referenced to supply
common 5 V
Table 4 Switching functions
Switching functions SP1, SP2
Setting range 0 to 99% F.S. (0 to 9.9 volts)
Hysteresis 1% F.S.
Relay contact 30 V d.c. /0.5 A (d.c.)
floating (n.o.)
Closed p psp (LED is illuminated)
Open p psp (LED is not illuminated)
Switching time 50 ms

Page 10
W603200880_A - Technical data
Table 5 Status relay
Status relay
Relay contact 30 V (d.c.) / 0.5 A (d.c.)
connected to supply common (pin 5)
Closed Measurement mode
Warning
Open
No supply voltage
Warming up
Error
Table 6 Diagnostic port
Diagnostic port Jack connector, 2.5 mm, 3-pin
. WARNING: HIGH VOLTAGE
Risk of electrical shock. The gauge can only be connected to power supplies, instruments
or control devices that comply with the requirements of a grounded Protective Extra-Low
Voltage (PELV) and Limited Power Source (LPS), Class 2. The connection to the gauge has
to be fused*.
*Edwards controllers meet this requirement.
Table 7 Electrical
Supply voltage Class 2 / LPS
at the gauge +14 to +30 V d.c. or
15 V (5%)
ripple 1 Vpp
Power consumption
while being heated 12 W
at operating temperature 8 W
Electrical connection*
*The gauge is protected against reverse polarity of the supply voltage and overload.
15-pin D-Sub, male
Sensor cable 15-pin plus shielding
Cable length§
§For longer cables, larger conductor cross-sections are required (Rcable
1.0
).
Supply voltage 15 V 8 m (0.14 mm²/conductor)
15 m (0.25 mm²/conductor)
Supply voltage 24 V 43 m (0.14 mm²/conductor)
75 m (0.25 mm²/conductor)
Supply voltage 30 V 88 m (0.14 mm²/conductor)
135 m (0.25 mm²/conductor)
Grounding concept See Electrical connection on page 14

Page 11
W603200880_A - Technical data
Dimensions
Figure 1 Dimensions (mm)
Table 8 Materials exposed to vacuum
Materials exposed to vacuum Ceramics (Al2O3 99.5%),
Stainless steel AISI 316L
Internal volume 4.2 cm3
Admissible pressure (absolute)
1000/1100 F.S. 4 bar | 400 kPa
1/10/100 F.S. 2.6 bar | 260 kPa
0.1 F.S. 1.3 bar | 130 kPa
Bursting pressure (absolute) 6 bar | 600 kPa
Table 9 Environmental
Admissible temperatures
Storage -40 °C to +65 °C
Operation +10 °C to +40 °C
Bake-out 110 °C at the flange
Relative humidity 80% at temperatures
+31 °C decreasing to 50% at +40 °C
Use Indoors only, altitude up to 2000 metres NN
Degree of protection IP 40

Page 12
W603200880_A - Technical data
Analogue measurement signal versus pressure
Figure 2 Analogue measurement signal versus pressure
p = (Uout / 10 V) × p (F.S.)
Conversion Torr to Pascal
Torr mbar Pa
1.00 1013.25 / 760 = 1.3332… 101325 / 760 = 133.3224…
Example: Gauge with 10 Torr F.S.
Measurement signal Uout = 6 V
p = (6 V / 10 V) × 10 Torr
= 0.6 × 10 Torr = 6 Torr

Page 13
W603200880_A - Installation
Installation
Vacuum connection
WARNING: NOT FAIL-SAFE DESIGNED
Risk of death. Do not use the Barocel 7045 for safety critical applications. The gauge is not
intended to be fail-safe.
CAUTION: IMPACT DAMAGE
Risk of damage to equipment. The ceramic sensor can be damaged by impacts. Do not
drop the gauge.
WARNING: PRESSURIZED CONTAINER
Risk of injury or death. A release of parts and process gases because of system
overpressure greater than 1 bar causes a hazard. Do not open any clamps while the
vacuum system is pressurized. Use clamps designed for overpressure conditions.
WARNING: PRESSURIZED CONTAINER
Risk of injury or death. A release of process gases because of system overpressure greater
than 2.5 bar causes a hazard. KF flange connections with elastomer seals cannot resist
such pressures. Use O-rings with an outer centring ring.
WARNING: HIGH VOLTAGE
Risk of electric shock. Make sure that the pump and electrical cables are correctly
protected against earth (ground) faults. A protective earth (ground) conductor
(equivalent or larger than the incoming supply power cable conductor) must be attached
to the protective earth (ground) stud.
CAUTION: DIRT CONTAMINATION
Risk of damage to equipment. Dirt and damage will cause the gauge to operate
incorrectly. When you handle the gauge, prevent dirt and damage to the vacuum
components.
CAUTION: DIRT SENSITIVE AREA
Dirt sensitive area. Do not touch the components with bare hands as it increases the
desorption rate. Wear clean, lint-free gloves and use clean tools when you work in this
area.

Page 14
W603200880_A - Installation
1. Position the gauge to prevent vibrations.
Note:
The gauge can be installed in any orientation. We recommend you install the gauge in a
horizontal to upright position and use a seal with a centring ring and filter to prevent the influx
of condensates and particles in the measurement chamber.
2. Install the gauge so that the buttons can be accessed with a pin for future
adjustments.
3. Remove the protective lid and connect the gauge to the vacuum system.
4. Keep the protective lid.
Figure 3 Connect the gauge to the system
Electrical connection
Make sure that the vacuum connection is correct.
1. Clamp
2. Seal with centring ring
3. Protective lid
WARNING: HIGH VOLTAGE
Risk of electric shock. The gauge can only be connected to power supplies, instruments or
control devices that agree to the requirements of a grounded Protective Extra-Low
Voltage (PELV) and Limited Power Source (LPS), Class 2. The connection to the gauge has
to be fused.*
*Edwards controllers meet this requirement.

Page 15
W603200880_A - Installation
Ground loops, differences of potential, or EMC problems can affect the measurement signal.
For optimum signal quality:
Use an overall metal braided shielded cable. The connector must have a metal case.
Connect the cable shield to ground on one side through the chassis ground. Do not
connect the other side of the shield.
Connect the supply common with protective ground directly at the power supply.
Use differential measurement input (signal common and supply common wired
separately).
Potential difference between the supply common and the housing 18 V (over-
voltage protection).
D-Sub, 15-pin connector
If a sensor cable is not available, one can be made. Refer to Figure 4 on page 15. Connect the
sensor cable.
Figure 4 D-Sub 15-pin sensor cable
1, 4 Relay SP1, closing contact 10 Gauge identification or
remote zero adjust
2 Signal output (measurement
signal) or thresholds SP1/2
12 Signal common
3 Status 13 Reserved
5 Supply common 14 Reserved
6 Supply (-15 V) 15 Housing (chassis ground)
7, 11 Supply (+14 to +30 V or +15 V) case Connector case
8, 9 Relay SP2, closing contact

Page 16
W603200880_A - Operation
Operation
Put the gauge into operation. If you use an Edwards controller, specify the measurement
range and the unit of measurement.
Warm-up time:
For general purpose reading (within specifications) > 0.50 hours
For zero adjustment and precision measurement > 2.00 hours
Note:
If the gauge is used for fast downstream pressure control, we recommend setting the signal
filter to "fast".
The filter can be set via the diagnostic port.
Status indication
To zero the gauge
The gauge is factory calibrated in an upright orientation.
Note:
Do a zero adjustment when the gauge is operated for the first time.
LED Status Meaning
<STATUS>
off No supply voltage
Illuminated Measurement mode
Flashing green
Short blinks Warning, over/under range
Long blinks Warming up
Illuminated solid red Error
<SP1>
Illuminated solid green p setpoint 1
Flashing green Waiting for setpoint 1 input
Off p > setpoint 1
<SP2>
Illuminated solid green p setpoint 2
Flashing green Waiting for setpoint 2 input
Off p > setpoint 2

Page 17
W603200880_A - Operation
Continuous operation or contamination can lead to zero drift and the gauge will need zero
adjustment.
To adjust the zero, operate the gauge under the same constant ambient conditions and in the
same mounting orientation as normal.
The output signal is dependent on the mounting orientation. The signal difference between
the vertical and horizontal mounting orientation is:
Note:
If the gauge is operated through a controller, the zero of the whole measurement system has
to be adjusted on the controller. Adjust the zero on the gauge first and then on the controller.
<ZERO> Adjustment
The zero can be adjusted by:
The <ZERO> button on the gauge
The digital input “Remote Zero”: Apply the supply voltage to pin 10 (15-pin) or to
pin 7 (9-pin) pulse.
An Edwards vacuum gauge controller.
Note:
While the gauge is being heated and/or under atmospheric pressure, the zero adjustment
function is disabled to prevent operational errors.
To adjust the zero:
1. Evacuate the gauge to a pressure according to the table below:
Note:
If the final pressure in the gauge is too high for the zero adjustment (> 25% of the F.S.), the zero
cannot be reached and the <STATUS> flashes green. If this happens, start the factory setting
and adjust the zero again.
2. Operate the gauge for a minimum of 0.25 hours (until the signal is stable).
F.S. U/90°
1000 Torr/mbar approximately 2 mV
100 Torr/mbar approximately 10 mV
10 Torr/mbar approximately 50 mV
1 Torr/mbar approximately 300 mV
0.1 Torr/mbar approximately 1.8 V
F.S. Recommended final pressure for zero adjustment
1100 mbar - < 6.65 × 100 Pa < 6.65 × 10-2 mbar
1000 Torr < 5.0 × 10-2 Torr < 6.65 × 100 Pa -
100 Torr/mbar < 5.0 × 10-3 Torr < 6.65 × 10-1 Pa < 6.65 × 10-3 mbar
10 Torr/mbar < 5.0 × 10-4 Torr < 6.65 × 10-2 Pa < 6.65 × 10-4 mbar
1 Torr/mbar < 5.0 × 10-5 Torr < 6.65 × 10-3 Pa < 6.65 × 10-5 mbar
0.1 Torr/mbar < 5.0 × 10-6 Torr < 6.65 × 10-4 Pa < 6.65 × 10-6 mbar

Page 18
W603200880_A - Operation
3. Briefly press the <ZERO> button with a pin (maximum ø1.1 mm). The zero
adjustment runs automatically. The <STATUS> LED flashes until the adjustment
(duration 8 seconds) is completed.
Note:
After zero adjustment, the gauge automatically returns to measurement mode.
The <STATUS> LED flashes if:
At final pressure, the signal output is negative (< -20 mV)
The zero adjustment has failed.
<ZERO> Adjustment with ramp function
The ramp function allows to adjust the zero at a known reference pressure within the
measurement range of the gauge.
It also permits to adjust an offset of the characteristic curve to:
Compensate for the offset of the measurement system, or
Obtain a slightly positive zero for a 0 to 10 V AD converter.
The offset should not be more than 2% of the F.S. (+200 mV). The measurement range is more
than the upper limit if there is a higher positive offset.
Note:
Zero adjustment using the ramp function can be done by the <ZERO> button on the gauge.
The recommended procedure for adjusting the offset of a measurement system is:
1. Operate the gauge for at least 1.0 hour (until the signal is stable).
2. Push the <ZERO> button with a pin (maximum ø1.1 mm) and keep it depressed. The
<STATUS> LED starts flashing. After 5 seconds, the zero adjustment value, starting at
the current output value, keeps continually changing (ramp) until the button is
released or until the setting limit (maximum 25% F.S.) is reached. The corresponding
output signal is delayed by about 1 second.
1. Press the button briefly
Table of contents
Other Edwards Measuring Instrument manuals
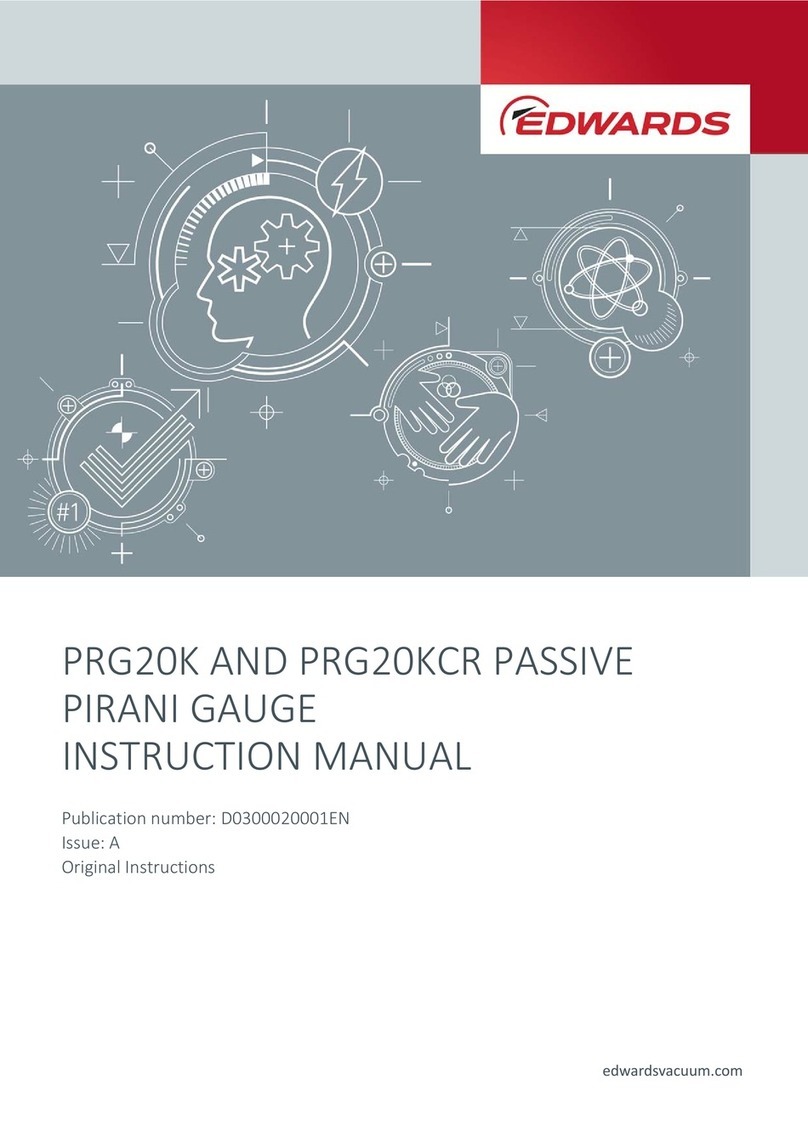
Edwards
Edwards PRG20K User manual
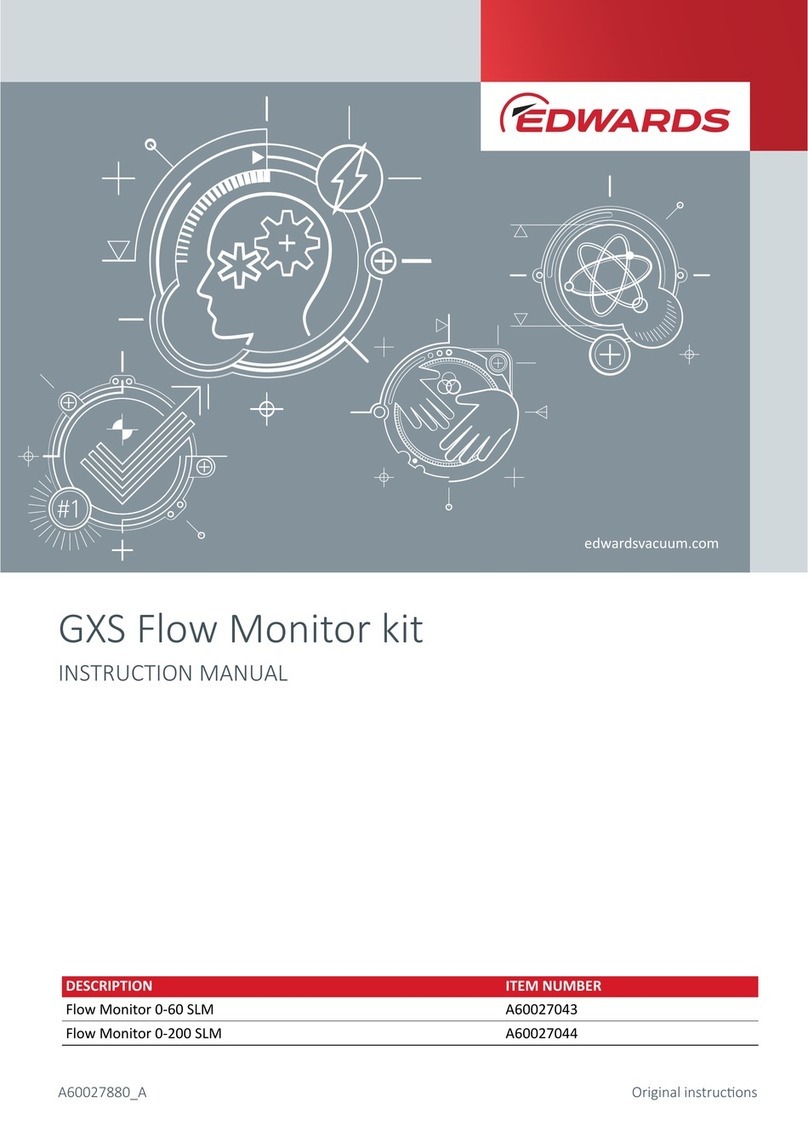
Edwards
Edwards GXS 0-60 SLM User manual
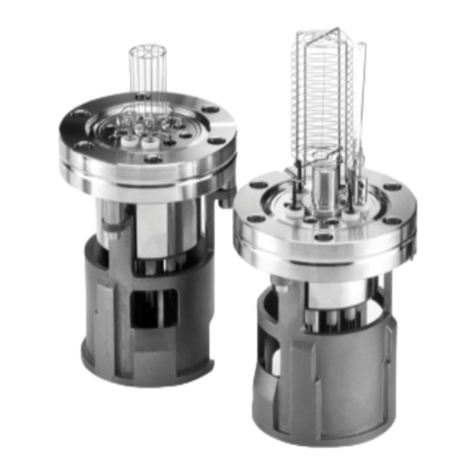
Edwards
Edwards IG40 BA User manual
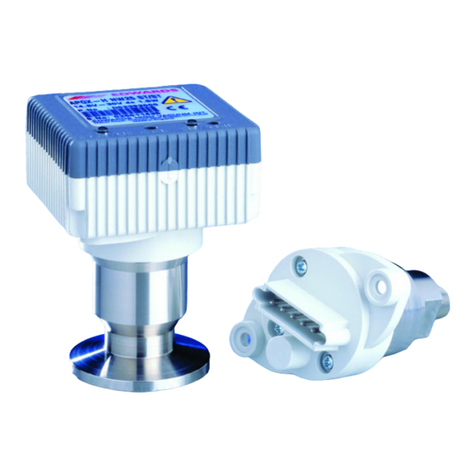
Edwards
Edwards APGX-H User manual

Edwards
Edwards AIM-S-NW25 User manual
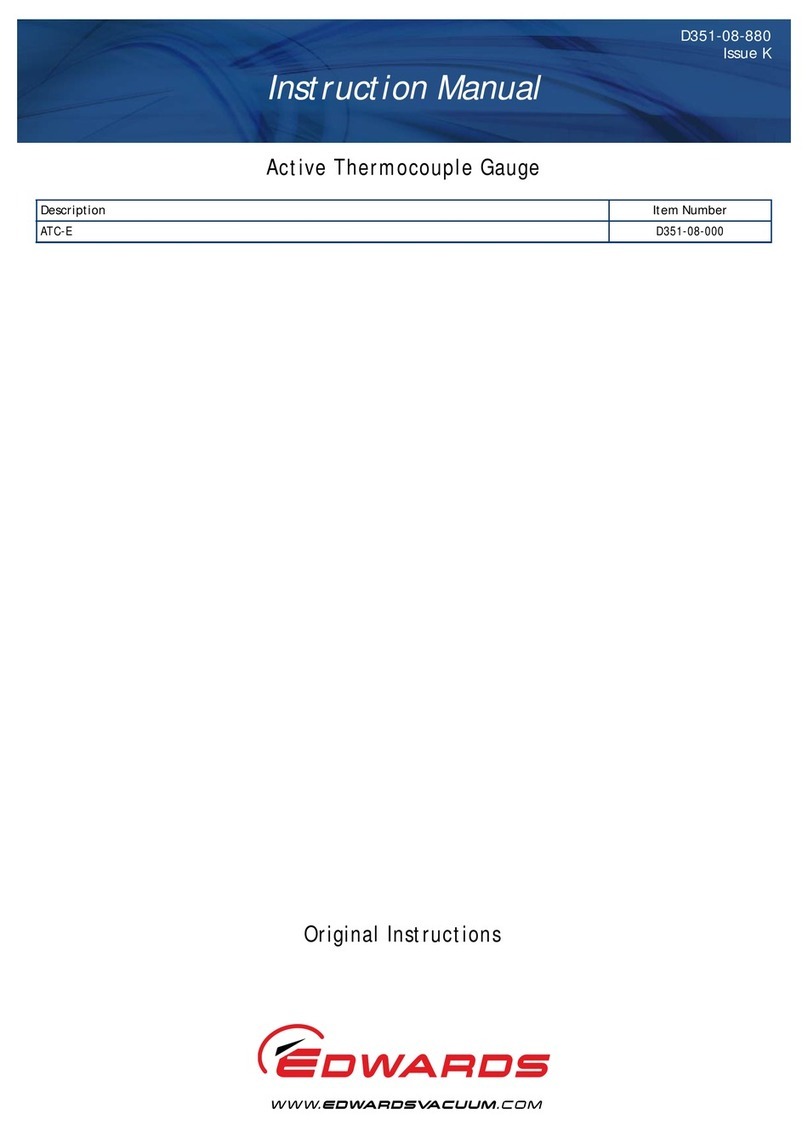
Edwards
Edwards ATC-E User manual
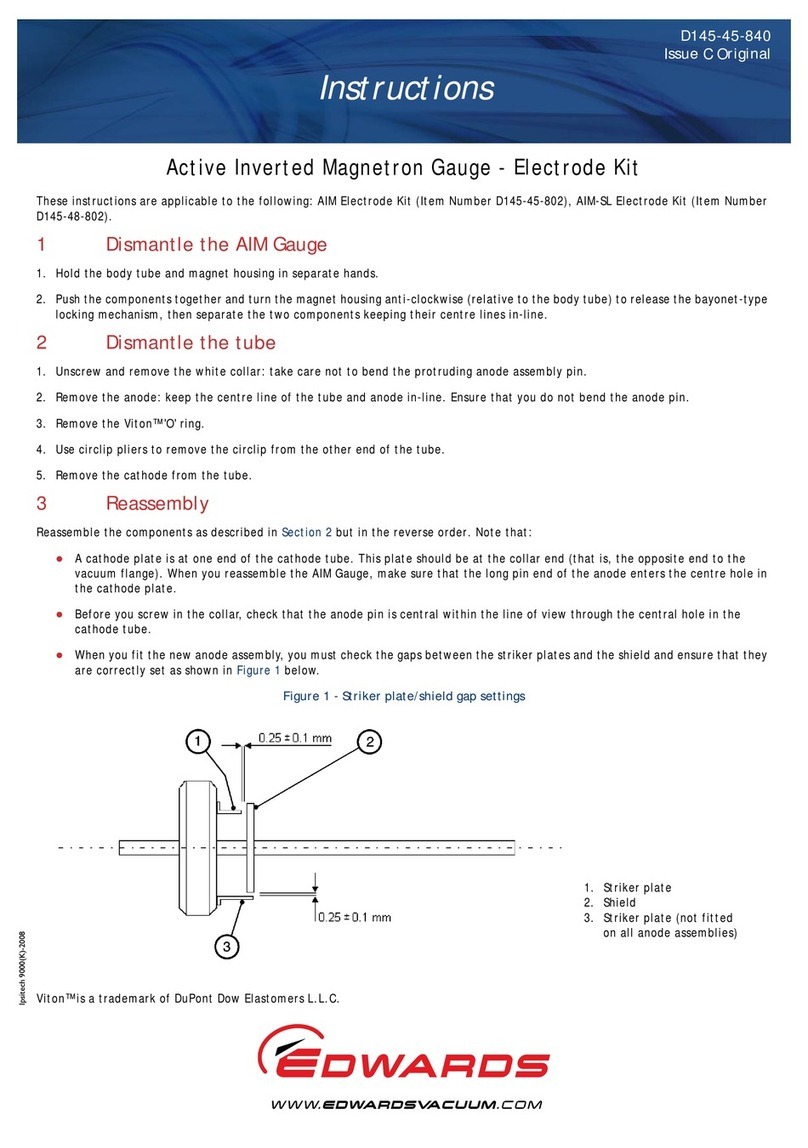
Edwards
Edwards AIM User manual
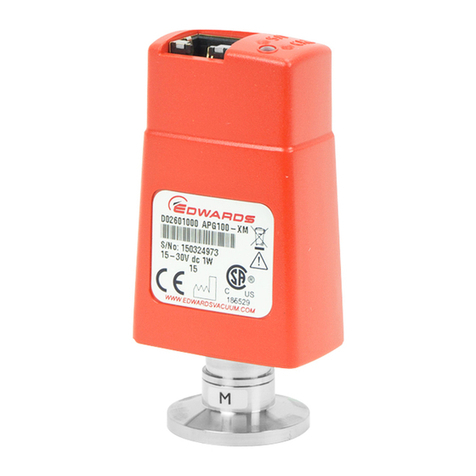
Edwards
Edwards APG100 User manual
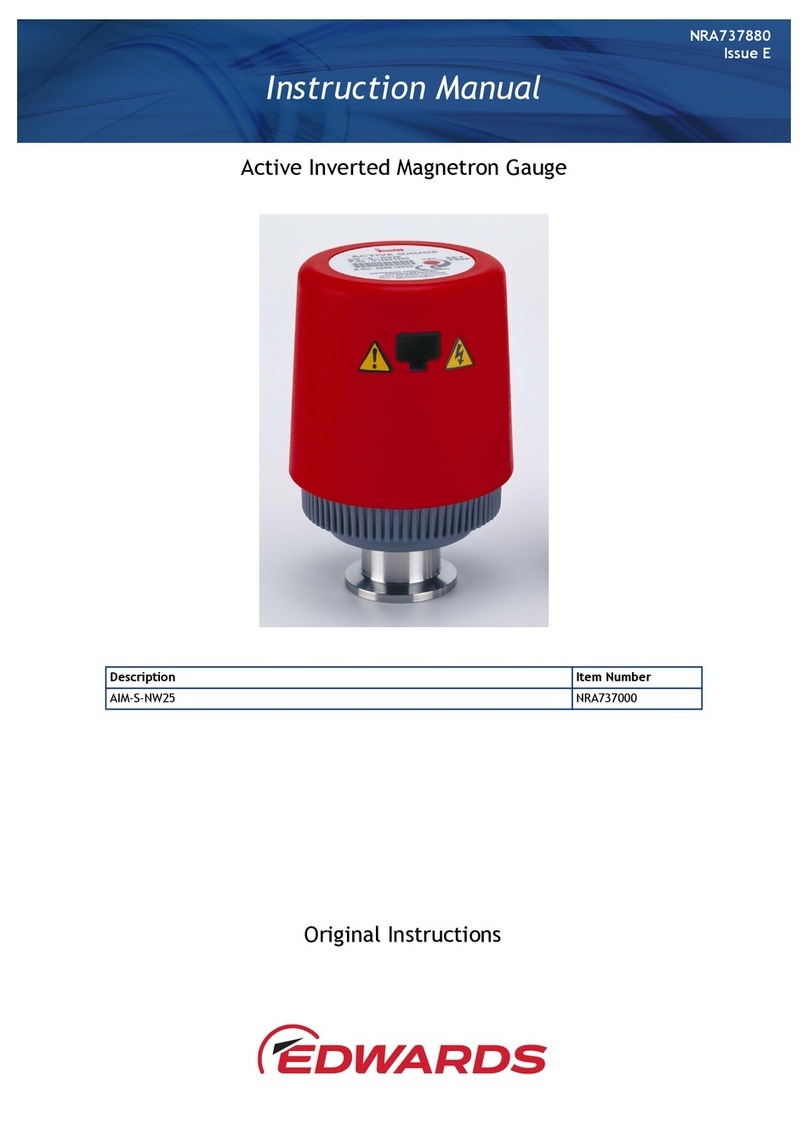
Edwards
Edwards AIM-S-NW25 User manual
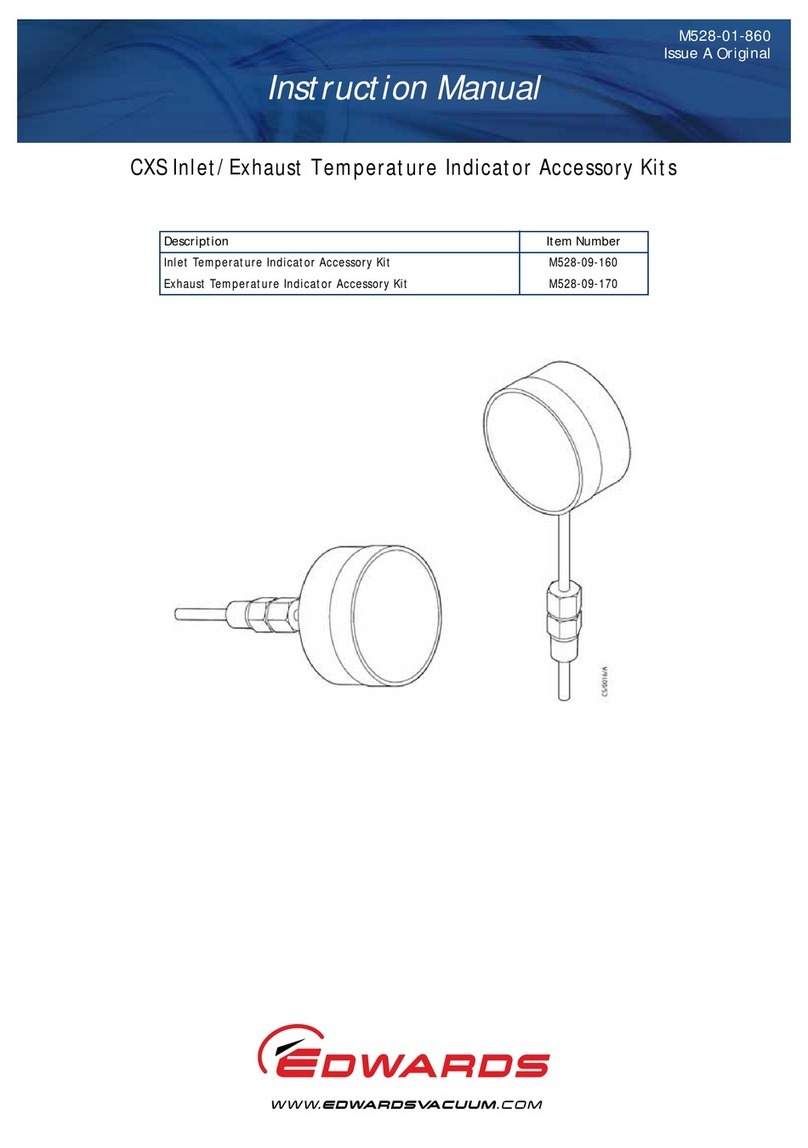
Edwards
Edwards M528-09-160 User manual
Popular Measuring Instrument manuals by other brands
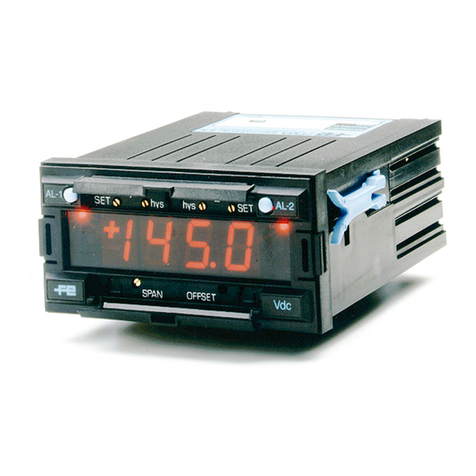
Fema Electronica
Fema Electronica Series MAG-35 user manual
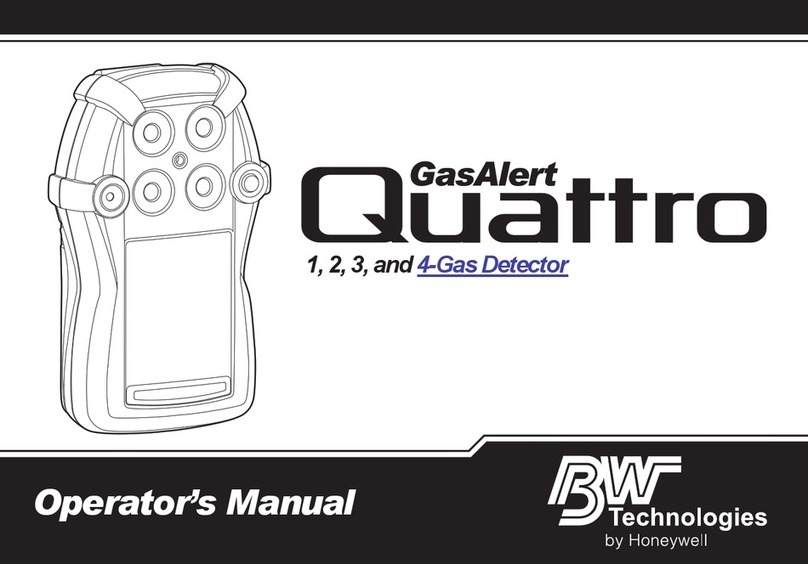
BW Technologies
BW Technologies GasAlertQuattro 3 Operator's manual
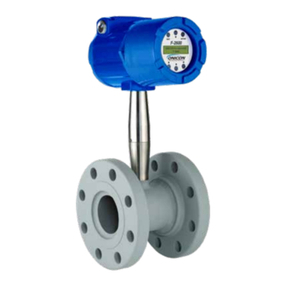
Onicon
Onicon F-2600 Series Installation and operation guide
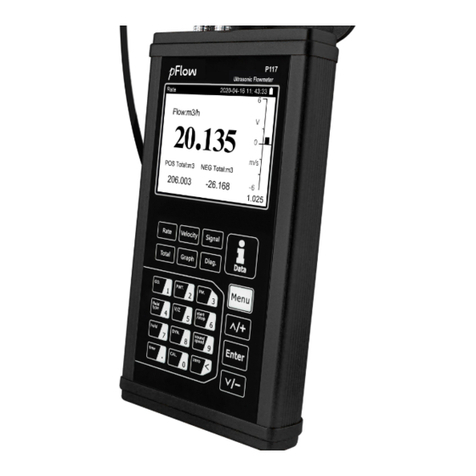
PFlow Industries
PFlow Industries P117 instruction manual

sauermann
sauermann Si-CA 8500 quick start guide

Velleman Modules
Velleman Modules VM112 user manual