EG&G ORTEC 552 Service manual

n
Model
552
Pulse-Shape
Analyzer
and
Timing
Single-Channel
Analyzer
Operating
and
Service
Manual

Model
552
Pulse-Shape
Analyzer
and
Timing
Single-Channel
Analyzer
Operating
and
Service
Manual
This
manual
applies
to
instruments
marked
"Rev
27"
on
rear
panel
2845
0.5C
0485

standard
Warranty
for
EG&G
ORTEC
Nuclear
Electronic
Instruments
EG&G
ORTEC
warrants
that
the
items
will
be
delivered
free
from
defects
in
material
or
workmanship.
EG&G
ORTEC
makes
no
other
warranties,
express
or
implied,
and
specifically
NO
WARRANTY
OF
MERCHANTABILITY
OR
FITNESS
FOR
A
PARTICULAR
PURPOSE.
EG&G
ORTEC's
exclusive
liability
is
limited
to
repairing
or
replacing
at
EG&G
ORTEC's
option,
items
found
by
EG&G
ORTEC
to
be
defective
in
workmanship
or
materials
within
two
years
from
the
date
of
delivery.
EG&G
ORTEC's
liability
on
any
claim
of
any
kind,
including
negligence,
loss
or
damages
arising
out
of,
connected
with,
or
from
the
performance
or
breach
thereof,
or
from
the
manufacture,
sale,
delivery,
resale,
repair,
or
use
of
any
item
or
services
covered
by
this
agree
ment
or
purchase
order,
shall
in
no
case
exceed
the
price
allocable
to
the
item
or
service
furnished
or
any
part
thereof
that
gives
rise
to
the
claim.
In
the
event
EG&G
ORTEC
fails
to
manufacture
or
deliver
items
called
for
in
this
agreement
or
pur
chase
order,
EG&G
ORTEC's
exclusive
liability
and
buyer's
exclusive
remedy
shall
be
release
of
the
buyer
from
the
obliga
tion
to
pay
the
purchase
price.
In
no
event
shall
EG&G
ORTEC
be
liable
for
special
or
consequential
damages.
Quality
Control
Before
being
approved
for
shipment,
each
EG&G
ORTEC
nuclear
electronic
instrument
must
pass
a
stringent
set
of
quality
controt
tests
designed
to
expose
any
flaws
in
materials
or
workmanship.
Permanent
records
of
these
tests
are
maintained
for
use
in
warrany
repair
and
as
a
source
of
statistical
information
for
design
improvements.
Repair
Service
If
it
becomes
necessary
to
return
this
instrument
for
repair,
it
is
essential
that
Customer
Services
be
contacted
in
advance
of
its
return
so
that
a
Return
Authorization
Number
can
be
assigned
to
the
unit.
Also,
EG&G
ORTEC
must
be
informed,
either
in
writing,
by
telephone
[(615)
482-4411]
or
by
telex
(55-7450)
of
the
nature
of
the
fault
of
the
instrument
being
re
turned
and
of
the
model,
serial,
and
revision
("Rev"
on
rear
panel)
numbers.
Failure
to
do
so
may
cause
unnecessary
delays
in
getting
the
unit
repaired.
The
EG&G
ORTEC
standard
procedure
requires
that
instruments
returned
for
repair
pass
the
same
quality
control
tests
that
are
used
for
new-production
instruments.
Instruments
that
are
returned
should
be
packed
so
that
they
will
withstand
normal
transit
handling
and
must
be
shipped
PREPAID
via
Air
Parcel
Post
or
United
Parcel
Service
to
the
nearest
EG&G
ORTEC
repair
center.
(In
the
case
where
the
instrument
did
not
function
upon
pur
chase,
EG&G
ORTEC
will
pay
shipment
costs
both
ways.)
The
address
label
and
the
package
should
include
the
Return
Authorization
Number
assigned.
Instruments
being
returned
that
are
damaged
in
transit
due
to
inadequate
packing
will
be
repaired
at
the
sender's
expense,
and
it
will
be
the
sender's
responsibility
to
make
claim
with
the
shipper.
Instruments
not
in
warranty
will
be
repaired
at
the
standard
charge
unless
they
have
been
grossly
misused
or
mishandled,
in
which
case
the
user
will
be
notified
prior
to
the
repair
being
done.
A
quotation
will
be
sent
with
the
notification.
Damage
in
Transit
Shipments
should
be
examined
immediately
upon
receipt
for
evidence
of
external
or
concealed
damage.
The
carrier
making
delivery
should
be
notified
immediately
of
any
such
damage,
since
the
carrier
is
normally
liable
for
damage
in
shipment.
Packing
materials,
waybills,
and
other
such
documentation
should
be
preserved
in
order
to
establish
claims.
After
such
notification
to
the
carrier,
please
notify
EG&G
ORTEC
of
the
circumstances
so
that
assistance
can
be
provided
in
making
damage
claims
and
in
providing
replacement
equipment
if
necessary.

Ill
CONTENTS
Page
WARRANTY
|j
PHOTOGRAPHS
jv
1.
DESCRIPTION
1
1.1.
Purpose
.|
1.2.
Lower-Level
Reference
''
"
|
2
1.3.
Output
Strobe
!!
!
'
!
2
1.4.
Constant-Fraction
Technique
2
2.
SPECIFICATIONS
2
2.1.
Performance
2
2.2.
Controls
!!!! !
2
2.3.
Inputs
. . .
3
2.4.
Outputs
3
2.5.
Related
Equipment
!
'
'
!
!
3
2.6.
Electrical
and
Mechanical
!
!!
"
'
!
3
3.
INSTALLATION
3
3.1.
General
3
3.2.
Connection
to
Power
3
3.3.
Connection
from
Linear
Amplifier
3
3.4.
Output
Connections
^
4
3.5.
Lower-Level
Reference
Input
4
4.
OPERATING
INSTRUCTIONS
4
5.
CIRCUIT
DESCRIPTION
5
5.1.
General
^
.
5
5.2.
Integrated
Circuits
!
^
!
6
5.3.
Lower-Level
Bias
6
5.4.
Upper-Level
Bias
7
5.5.
Input
Circuit
!
'
.
! !
7
5.6.
Lower-Level
Discriminator
''
7
5.7.
Upper-Level
Discriminator
^
7
5.8.
Channel
A
Discriminator
'
^
7
5.9.
Channel
B
Discriminator
! !!
!
8
5.10.
Reset
Circuit
^
^
g
5.11.
DC
Power
g
6.
MAINTENANCE
AND
CALIBRATION
9
6.1.
General
!
!
^
9
6.2.
Stretcher
Calibration
9
6.3.
Walk
Calibration
!
.
'
!!
9
6.4.
Lower-Level
Calibration
9
6.5.
Factory
Repair
'
g
Schematic
552-0201-S1
ILLUSTRATIONS
Fig.
1.1.
Typical
Walk
vs
Dynamic
Range
.|
Fig.
4.1.
Timing
Relationships
for
Input
and
Output
Pulses
for
Operation
with
Internal
Strobe
5
Fig.
5.1.
Simplified
Block
Diagram
of
the
552
PSA/T-SCA
'
^
6

IV
■
,-
■
••
.
■
^
■
■
'
..
s:.::i
"'t
^
•
C^
§
,
-A
^
;
^l:
-.1:
"•V
>."1'-\'
.,
/^-^c
J::,
/:'
v
'
'
-
<
-
•^-'
.
..
ipiiiiiiPiii^
■S>
-inr.-'
'l'"
'
-
«,,*■
iSIS^
liiiiiii
WSKUk:
m
k€l
'LL
*»
REF
5TR0BE
T
ihtT
J-
W
r-r
^
IN
IN
^
t
SCA
OUT
O
LL
OUT
UL
OUT
©
©
•i>
...
-
WSSSSmSMS
T-
^
s,-
4
-
•
■
■■■S-;
;
<
.--•
r.-
-
-.j
f/'
-J
liiliMi
.
t
•
-
:
;
:sS!pmvim€mm
»
.
4
''
*1-
>■
^'~
,
.
'
■
i
t:g
-■
"V,,
_■
;
J'-'C
4;4Lv'5-v--
>«si^.v!5i,':-«
;imm4iMmismmm
sms^MmS£MMeMSSe

ORTEC
552
PULSE-SHAPE
ANALYZER
AND
TIMING
SINGLE-CHANNEL
ANALYZER
DESCRIPTION
1.1.
PURPOSE
The
ORTEC
552
PSA/T-SCA
provides
a
versatile
group
of
signal
derivation
functions.
It
can
be
used
as
either
a
single-channel
analyzer
or
as
an
integral
discriminator;
by
comparing
the
time
relationships
between
its
two
sets
of
outputs,
information
can
be
interpreted
for
pulse-
shape
analysis.
Each
input
signal
that
is
accepted
by
the
adjusted
amplitude
criteria
generates
two
separate
outputs,
each
precisely
time-related
to
the
input
signal.
For
reference
in
the
instrument,
one
output
signal
is
generated
through
channel
A
and
the
other
through
channel
B.
The
input
logic
circuits
can
be
used
in
any
of
three
modes,
selected
by
a
front
panel
switch.
The
Integral
mode
uses
the
adjusted
lower-level
discriminator
as
the
only
logic
reference
and
generates
an
output
if
the
input
signal
amplitude
exceeds
the
lower
level.
The
Normal
mode
uses
both
lower-level
and
upper-level
discriminators
and
generates
an
output
if
the
input
amplitude
exceeds
the
lower-level
bias
but
does
not
exceed
the
upper
level;
the
front
panel
Upper-Level
control
is
adjusted
within
a
range
of
0
to
10
V
with
ground
as
the
zero
reference
point.
The
Window
mode
operates
the
same
as
the
Normal
mode
except
that
the
zero
reference
point
for
the
Upper-Level
control
is
equal
to
the
adjusted
lower
level
and
the
range
of
the
Upper-Level
control
is
0
to
1
V.
The
lower
level
for
any
mode
can
be
furnished
from
the
front
panel
control
or
by
a
dc
input
signal
through
a
rear
panel
connector.
An
output
signal
through
channel
A
is
generated
by
the
constant-fraction
method
on
the
trailing
edge
of
the
input
signal,
after
the
logic
for
acceptance
has
been
completed.
The
fraction
is
selectable
at
10%,
20%,
or
50%
measured
down
from
the
peak
pulse
height,
using
a
jumper
on
the
printed
circuit
board
to
select
the
fraction.
The
output
occurs
promptly
at
the
constant-fraction
point
on
the
trailing
edge
and
is
a
NIM-standard
fast
negative
output
pulse
with
excellent
timing
characteristics.
An
output
signal
through
channel
B
is
also
generated
by
the
constant-fraction
method
on
the
trailing
edge
of
the
input
signal.
The
fraction
for
channel
B
is
selected
by
a
front
panel
switch
that
can
be
set
for
any
level
from
10%
through
100%
(bipolar
crossover)
in
10%
increments
of
the
peak
pulse
height.
The
unit
must
be
strobed,
either
internally
or
externally,
for
an
output
pulse
to
be
provided.
When
the
rear
panel
switch
selects
internal
strobe,
the
channel
B
outputs
are
generated
after
an
adjusted
delay
following
the
constant-fraction
trigger
point;
the
delay
is
adjusted
on
the
front
panel
within
the
range
of
0.1
to
1.1
/iS,
permitting
normalization
for
specific
applications.
When
the
rear
panel
switch
selects
external
strobe,
the
channel
B
outputs
are
generated
promptly
when
a
NIM-
standard
positive
strobe
is
furnished
through
the
rear
panel
connector:
the
strobe
signal
must
be
furnished
within
10
MS
after
the
channel
B
constant-fraction
trigger
point.
There
are
two
channel
B
outputs;
one
is
a
NIM-
standard
fast
negative
pulse
and
the
other
is
a
NIM-
standard
slow
positive
pulse.
By
using
an
internally-strobed
channel
B
output,
the
timing
differentials
between
channels
A
and
B
can
be
used
to
measure
the
decay
characteristics
of
an
input
pulse
as
the
constant-fraction
points
of
the
two
channels
are
changed.
For
example,
using
a
50%
fraction
for
channel
A
and
10%
for
channel
B,
the
time
difference
on
the
decaying
waveform
can
be
measured
by
sub
tracting
the
channel
B
delay.
In
many
applications,
the
decay
time
of
the
pulse
is
significant
for
the
type
of
par
ticle
that
is
detected
so
the
pulse
shape
can
be
used
to
identify
the
nature
of
the
source.
The
552
accepts
either
unipolar
or
bipolar
input
pulses
having
either
RC
or
delay-line
pulse-shaped
waveforms.
It
includes
an
input
attenuator
so
that
an
input
amplitude
can
be
reduced
by
a
factor
of
1,
10,
or
100,
selected
by
a
front
panel
toggle
switch.
The
walk
of
the
attenuator
is
typically
less
than
1
ns.
This
feature
can
be
used
to
optimize
the
timing
accuracy
of
both
output
channels.
The
walk
characteristics
can
be
optimized
individually
in
each
channel,
using
a
front
panel
screwdriver
adjust
ment
for
each
channel.
When
these
controls
are
adjusted
properly,
the
walk
characteristics
for
a
bipolar
delay-line
shaped
input
are
less
than
2.5
ns
over
a
200:1
dynamic
range
of
input
amplitudes
(see
Fig.
1.1).
The
instrument
is
designed
to
meet
the
interchangeability
standards
recommended
by
USAEC
Report
TID-28093
(Rev).
An
ORTEC
401/402
Series
Bin
and
Power
Supply
provides
all
the
necessary
power
through
the
rear
panel
module
connector.
All
signal
levels
and
impedances
are
compatible
with
other
ORTEC
NIM
modules.
5
1,0
!
1 1 1 1
552
f
=
0,5
Mi
l
460
Amp
Bipolar
Output
Tektronix
Attenuator
Channel
8
-
—
Channel
A
i
1
1 1 1
1
1
1 1
40:1
60.1
80:1
100:1
200:1
Dynamic
Range
Fig.
1.1.
Typical
Walk
vs
Dynamic
Range.

1.2.
LOWER-LEVEL
REFERENCE
A
rear
panel
toggle
switch
selects
either
the
front
panel
Lower-Level
control
or
the
voltage
signal
furnished
through
the
rear
panel
LL
Ref
connector
as
the
reference
for
the
lower-level
discriminator.
This
permits
flexibility
in
operation,
where
an
external
reference
source
can
furnish
the
lower-level
threshold
from
a
stepped-
or
sliding-voltage
source
to
automatically
sweep
the
SCA
response
through
a
spectral
range.
The
selected
source
for
the
lower-level
reference
is
effective
for
all
three
operating
modes.
1.3.
OUTPUT
STROBE
A
rear
panel
toggle
switch
selects
either
an
internal
strobe,
based
on
a
delayed
trigger
derived
from
the
input
signal,
or
a
strobe
pulse
that
is
furnished
through
the
rear
panel
Strobe
In
connector
to
determine
when
the
channel
B
outputs
are
to
be
generated.
This
has
no
effect
on
the
channel
A
output,
which
is
generated
promptly
at
the
constant-fraction
trigger.
When
external
strobe
is
used,
the
input
signal
must
be
received
within
10
yus
after
the
trigger
time
or
the
channel
B
outputs
will
not
be
generated.
When
the
internal
strobe
is
used,
the
Delay
control
on
the
front
panel
can
be
adjusted
to
set
the
de
lay
time
from
the
trigger
point
to
the
channel
B
output
in
the
range
of
0.1
through
1.1
^s.
1.4.
CONSTANT-FRACTION
TECHNIQUE
Both
output
channels
derive
information
that
uses
the
constant-fraction
technique,
which
is
an
ORTEC
devel
opment.
It
consists
of
comparing
the
amplitude
along
the
decay
of
a
pulse
to
a
selected
fraction
of
the
peak
amplitude
of
the
same
pulse.
Thus,
through
a
wide
range
of
input
pulse
peak
amplitudes,
the
timing
information
is
obtained
with
precision.
The
reference
fractions
that
are
available
in
both
output
channels
indicate
the
percentage
of
amplitude
decay
from
the
peak
toward
the
ground
reference
level.
Thus
a
setting
of
10%
in
either
channel
selects
a
trigger
point
at
90%
of
the
peak
amplitude
for
that
channel,
or
a
setting
of
20%
selects
a
trigger
point
at
80%
of
the
peak
ampli
tude.
2.
SPECIFICATIONS
2.1.
PERFORMANCE
INPUT
DYNAMIC
RANGE
200:1.
PULSE-PAIR
RESOLVING
TIME
Output
pulse
width
plus
Delay
(selected
by
front
panel
Delay
control
or
by
external
strobe
input)
plus
200
ns
for
NIM-standard
fast
negative
output
or
plus
740
ns
for
NIM-standard
slow
positive
output.
Minimum
resolving
time
for
negative
output,
260
ns;
for
positive
output,
800
ns.
THRESHOLD
TEMPERATURE
INSTABILITY
^0.005%/
°C
of
full
scale,
0
to
50°
0.
DISCRIMINATOR
NONLINEARITY
^±0.25%
of
full
scale
(Integral)
for
each
discriminator.
DELAY
TEMPERATURE
INSTABILITY
^±0.01
%/°C
of
full
scale,
0
to
50°C,
measured
at
full
scale.
DELAY
NONLINEARITY
^±2%
of
delay
range.
WINDOW
WIDTH
INCONSISTENCY
<±0.1%
variation
of
full-scale
window
width
over
the
0-to
10-V
linear
range.
MINIMUM
INPUT
THRESHOLD
40
mV,
TIME
SHIFT
vs
PULSE
HEIGHT
(Walk)
(Specified
for
Channels
A
and
B
at
50%
fraction.)
Walk
(ps)
Input
Oynamic
Range
System
1*
System
II**
10:1
±500
±2000
50:1
±1500 ±2500
100:1
±2000 ±3000
200:1
±2500 ±8000
*Uslng
the
bipolar
output
of
an
ORTEC
460
Amplifier,
single
delay-line
mode,
integrate
<0.1
with
delay
line
1
^s.
**Using
an
ORTEC
472A
Amplifier,
unipolar
output,
0.5
mS
shaping.
2.2.
CONTROLS
UPPER
LEVEL
Front
panel
10-turn
potentiometer
deter
mines
the
window
width
(0
to
+1
V)
in
the
Window
mode
or
the
Upper
Level
(0
to
+10
V)
in
the
Normal
and
Integral
modes
(not
used
to
determine
SCA
outputs
during
Inte
gral
mode
operation).
LOWER
LEVEL
Front
panel
10-turn
potentiometer
ad
justable
from
40
mV
to
10
V;
when
the
rear
panel
LL
Ref
switch
is
set
for
Int,
determines
the
threshold
setting
for
the
Lower-Level
discriminator;
when
the
LL
Ref
switch
is
set
at
Ext,
this
control
is
ineffective.
MODE
Front
panel
3-position
locking
toggle
switch
selects
one
of
three
operating
modes:
INT
(Integral)
LL
sets
a
single
discriminator
threshold
(40
mV
to
10
V)
and
UL
is
not
used
to
determine
an
SCA
response.
NORM
(Normal)
UL
and
LL
are
independently
adjust
able
levels;
UL
range
0
to
+10
V;
LL
range
40
mV
to
10
V.
WIN
(Window)
LL
sets
the
baseline
level
(40
mV
to
10
V)
and
UL
sets
the
window
width
(LL
to
LL+1
V).
ATTN
Front
panel
3-position
locking
toggle
switch
selects
an
attenuation
factor
for
the
input
signals:
XI
Input
signals
not
attenuated.
X10
Input
signals
are
attenuated
by
a
factor
of
1/10.
X100
Input
signals
are
attenuated
by
a
factor
of
1/100.
DELAY
Front
panel
10-turn
potentiometer
for
continu
ously
adjustable
delay
for
channel
B
output,
using
inter
nal
strobe;
range
0.1
to
1.1
ms.
WALK
ADJ
(A
and
B)
Independent
front
panel
screw
driver
adjustments
on
front
panel
for
precise
setting
of
walk
compensation
in
each
output
channel.
The
Walk
Adj
B
control
is
ineffective
when
the
B
Fraction
switch
is
set
at
its
Bl
position.
LL
REF
MODE
Rear
panel
2-position
locking
toggle
switch
selects
either
the
front
panel
LL
control
or
the

voltage
signal
applied
to
the
rear
panel
LL
Ref
Ext
con
nector
for
the
lower-level
discriminator
reference
thresh
old.
STROBE
MODE
Rear
panel
2-position
locking
toggle
switch
selects
either
an
internal
strobe,
derived
from
the
input
signal,
or
an
external
strobe,
furnished
through
the
adjacent
connector,
to
generate
a
channel
B
output.
The
automatic
reset
time
is
»10
/jls.
B-FRACTION
Front
panel
switch
selects
the
constant
fraction
that
will
be
used
for
the
channel
B
response
point:
marked
.1
through
.9
and
Bl
for
10%
through
90%
and
bipolar
crossover
(100%),
referring
to
the
decay
after
the
peak
of
the
input
waveform.
A-FRACTION
An
internal
jumper
selects
the
constant
fraction
that
will
be
used
for
the
channel
A
response
point;
jumper
positions
are
10%,
20%,
and
50%,
referring
to
the
decay
from
the
peak
of
the
input
waveform.
2.3.
INPUTS
INPUT
Front
panel
dc-coupied
BNC
connector
accepts
positive
unipolar
or
bipolar
signals,
0
to
+10
V
linear
range,
±12
V
maximum;
width,
^100
ns;
lOOOfl
input
im
pedance.
LL
REF
IN
Rear
panel
BNC
accepts
lower-level
bias
when
the
LL
Ref
mode
switch
selects
Ext.
An
input
of
0
to
-10
V
on
this
connector corresponds
to
a
range
of
0
to
+10
V
for
the
front
panel
Lower-Level
control.
Input
pro
tected
to
±24
V.
EXT
STROBE
IN
Rear
panel
BNC
accepts
a
NIM-stand-
ard
slow
positive
pulse,
nominally
+5
V,
500
ns
wide,
to
cause
an
output
to
occur
from
the
channel
B
circuits
when
the
Strobe
switch
is
set
at
Ext.
The
external
strobe
must
be
provided
within
10
/is
after
the
linear
input.
At
the
end
of
this
period,
the
552
resets
its
internal
logic
without
producing
a
channel
B
output.
2.4.
OUTPUTS
SCA
NEG
OUT
A
Front
panel
BNC
connector
provides
NIM-standard
fast
negative
output
pulses
from
channel
A
only;
nominally
-16
mA
(-800
mV
on
50n
load),
^20
ns
wide,
^5
ns
rise
time.
Output
occurs
promptly
at
the
channel
A
constant
fraction
trigger
point.
SCA
NEG
OUT
B
Front
panel
BNC
connector
provides
NIM-standard
fast
negative
output
pulses
from
channel
B
only;
nominally
-16
mA
(-800
mV
on
50n
load),
^20
ns
wide,
^5
ns
rise
time.
Output
occurs
promptly
at
strobe
time.
SCA
POS
OUT
B
Front
and
rear
panel
BNC
connectors
provide
NIM-standard
slow
positive
output
pulses
from
channel
B
only;
nominally
+5
V,
500
ns
wide,
^20
ns
rise
time.
Output
occurs
promptly
at
strobe
time.
Zo
^lOn.
LL
OUT
Rear
panel
BNC
connector
provides
positive
NIM-standard
output,
nominally
+5
V,
500
ns
wide.
Out
put
occurs
as
leading
edge
of
the
linear
input
crosses
the
LL
threshold,
Zo
^lOfl.
UL
OUT
Rear
panel
BNC
connector
provides
positive
NIM-standard
output,
nominally
+5
V,
500
ns
wide.
Out
put
occurs
as
leading
edge
of
the
linear
input
crosses
the
UL
threshold.
Zo
<10n.
2.5.
RELATED
EQUIPMENT
The
552
is
compatible
with
all
ORTEC
amplifiers
and
other
amplifiers
having
a
0-
to
+10-V
linear
output
range.
2.6.
ELECTRICAL
AND
MECHANICAL
POWER
REQUIRED
+24
V,
83
mA;
-24
V,
83
mA;
+12
V,
166
mA;
-12
V,
166
mA.
DIMENSIONS
NIM-standard
single-width
module
(1.35
by
8.714
inches)
per
TID-20893
(Rev).
3.
INSTALLATION
3.1.
GENERAL
The
552
must
be
used
in
conjunction
with
an
ORTEC
401/
402
Series
Bin
and
Power
Supply,
or
equivalent,
which
is
intended
for
rack
mounting.
If
any
source
of
heat
is
oper
ating
in
the
same
rack,
there
must
be
sufficient
cooling
air
circulating
to
prevent
any
localized
heating
of
the
transis
torized
and
integrated
circuits
used
throughout
the
552.
The
temperature
of
equipment
mounted
in
racks
can
easily
exceed
the
maximum
unless
precautions
are
taken;
the
552
should
not
be
subjected
to
temperatures
in
excess
of
120°F
(50°
C).
3.2.
CONNECTION
TO
POWER
Turn
off
the
Bin
Power
Supply
when
inserting
or
removing
modules.
The
ORTEC
NIM
modules
are
designed
so
that
it
is
not
possible
to
overload
a
properly
operating
power
supply
with
a
full
complement
of
modules
in
the
bin.
Since,
however,
this
may
not
be
true
when
the
bin
con
tains
modules
other
than
those
of
ORTEC
design,
power
supply
voltages
should
be
checked
after
the
modules
have
been
inserted.
The
401/402
has
test
points
on
the
power
supply
control
panel
to
monitor
the
do
voltage
levels.
When
using
the
552
outside
the
401/402
Bin
and
Power
Supply,
be
sure
that
the
power
extension
cord
or
cable
that
is
used
properly
accounts
for
the
power
supply
grounding
circuits
that
are
provided
according
to
the
recommended
AEC
standards
outlined
in
TID-20893
(Rev).
Both
high-quality
and
power-return
ground
con
nections
are
provided
to
ensure
proper
reference
voltage
feedback
into
the
power
supply,
and
these
must
be
pre
served
in
remote
cable
installations.
Be
careful
also
to
avoid
ground
loops
when
the
module
is
operated
outside
the
bin.
3.3.
CONNECTION
FROM
LINEAR
AMPLIFIER
The
Input
BNC
connector
on
the
front
panel
accepts
posi
tive
unipolar
or
bipolar
signals
through
a
dc-coupied
input
path.
For
bipolar
input
pulses,
the
positive
lobe
will
be
analyzed.
The
amplifier
output
should
be
adjusted
so
that
there
is
no
dc
offset,
and
the
poie-zero
networks
are
adjusted
properly.

The
input
Impedance
of
the
552
is
lOOOfi.
When
long
cables
are
used
to
connect
the
amplifier
output
to
the
552
Input,
cable
termination
may
be
necessary
in
orderto
pre
vent
reflections:
match
the
cable
impedance
with
a
term
inator
at
the
552
Input
in
such
cases.
Normally,
the
ATTN
switch
on
the
552
front
panel
will
be
left
at
its
XI
setting
for
operation
in
a
system.
The
main
purpose
for
the
X10
and
X100
attenuator
settings
are
to
aid
in
precise
walk
adjustments.
3.4.
OUTPUT
CONNECTIONS
Outputs
are
furnished
through
both
channel
A
and
channel
B
connectors.
Each
channel
is
considered
sepa
rately
because
of
the
differences
in
timing
characteristics
of
the
two
channels.
The
channel
A
output
on
the
front
panel
is
dependent
only
on
satisfaction
of
the
input
logic
of
the
single-channel
analyzer
and
it
occurs
at
the
se
lected
trigger
level
on
the
trailing
edge
of
the
linear
input.
The
channel
B
outputs
are
dependent
on
satisfaction
of
input
logic
and
of
a
strobe,
which
can
be
either
internally
generated
or
furnished
from
an
external
source.
The
channel
A
output
is
available
as
a
NIM-standard
fast
negative
pulse
from
a
front
panel
BNC
connector.
It
is
intended
for
transmission
to
the
driven
unit
through
50n
cable
with
50fl
termination.
When
the
552
is
set
for
either
the
Normal
or
Window
mode,
a
channei
A
output
means
that
an
input
pulse
amplitude
is
sufficient
to
trigger
the
lower-level
discriminator
without
also
triggering
the
upper-levei
discriminator.
When
the
552
is
set
for
the
Integral
mode
of
operation,
the
channel
A
output
means
that
the
input
pulse
amplitude
is
sufficient
to
trigger
the
lower-level
discriminator;
triggering
of
the
upper-level
discriminator
does
not
affect
the
output
for
this
mode.
The
time
when
a
channel
A
output
is
made
available
is
promptly
at
a
trigger
point
on
the
decay
of
the
input
wave
form.
The
decay
level
is
selected
by
an
internal
jumper
on
the
printed
circuit
board,
which
can
be
set
for
10%,
20%,
or
50%,
referring
to
the
decay
from
the
peak
amplitude
of
the
pulse.
Three
channel
B
outputs
are
available.
A
NIM-standard
fast
negative
pulse
is
furnished
through
a
front
panel
con
nector
and
a
NIM-standard
slow
positive
puise
is
fur
nished
through
both
front
and
rear
panel
connectors.
The
negative
output
is
intended
for
transmission
to
the
driven
unit
through
50n
cable
with
50fl
termination.
The
positive
outputs
can
be
furnished
through
50n
or
93n
cable
to
the
driven
unit.
A
channei
B
output
means
that
the
logic
for
the
channel
A
output
has
been
satisfied
and
that
an
output
strobe
is
furnished.
The
output
strobe
can
be
generated
internally
or
furnished
from
an
external
source,
depend
ing
on
the
setting
of
the
rear
panel
switch.
The
time
when
the
channel
B
outputs
are
generated,
using
the
internal
strobe,
is
at
a
fixed
delay
after
the
trig
ger
point
on
the
decay
of
the
input
waveform.
The
decay
level
is
selected
by
a
front
panel
switch
that
can
be
set
at
any
multiple
of
10%
from
10%
through
100%
(baseline
crossover
of
a
bipolar
input),
referring
to
the
decay
from
the
peak
amplitude
of
the
pulse.
The
range
of
the
front
panel
Delay
control
is
about
0.1
through
1.1
fiS.
The
channel
B
output
time,
using
an
external
strobe,
is
promptly
at
the
strobe
pulse;
this
strobe
pulse
must
be
furnished
within
10
ns
after
the
trigger
point
or
the
in
ternal
logic
is
reset
without
generating
a
channel
B
out
put.
Separate
logic
outputs
are
available
through
the
rear
panel
to
indicate
when,
on
the
leading
edge
of
an
input
pulse,
each
of
the
two
discriminators
is
triggered.
These
responses
can
be
used
to
monitor
the
discriminator
levels
during
adjustment,
to
be
counted
in
external
sealers,
to
provide
subgroup
routing
to
a
multichannei
analyzer,
or
for
any
other
applications
desired.
Each
logic
output
for
LL
Out
and
UL
Out
is
a
NIM-standard
slow
positive
pulse
that
is
compatible
with
ORTEC
counters,
ratemeters,
and
other
Instruments.
The
output
impedance
through
each
output
path
is
sufficiently
low
to
drive
as
many
as
ten
paralleled
lOOOfl
inputs.
3.5.
LOWER-LEVEL
REFERENCE
INPUT
If
the
LL
Ref
toggle
switch
on
the
rear
panel
of
the
552
is
set
at
Ext,
the
reference
level
for
the
lower-level
discrim
inator
must
be
furnished
through
the
adjacent
In
BNC
connector;
the
10-turn
Lower-Level
control
on
the
front
panel
is
disconnected.
An
input
of
0
to
-10
V
through
this
connector
corresponds
directly
to
a
range
of
0
to
+10
V
for
the
lower-level
discriminator
threshold.
The
signal
through
the
LL
Ref
In
connector
is
not
used
unless
the
toggle
switch
is
set
at
Ext.
4.
OPERATING
INSTRUCTIONS
After
the
552
has
been
connected
into
a
system
according
to
the
installation
information
in
Section
3,
the
operating
and
strobe
modes
can
be
selected
and
the
discriminator
thresholds
can
be
adjusted
as
required
for
each
appli
cation.
Figure
4.1
illustrates
the
timing
relationships
that
will
be
effective
in
the
552,
operating
with
an
internal
strobe,
for
each
of
three
possible
input
pulse
ampitudes.
The
first
two
pulses
exceed
the
lower-level
threshold
without
also
exceeding
the
upper
level,
and
the
third
pulse
exceeds
both
threshold
levels.
Superimposed
on
each
of
these
input
pulses
in
Fig.
4.1
are
two
internally
stretched
con
stant-fraction
reference
levels;
the
upper
stretched
level
is
at
the
50%
point
on
the
input
pulse
decay,
which
can
be
set
in
channel
A;
the
lower
stretched
level
is
at
the
70%
point
on
the
input
pulse
decay,
which
can
be
set
in
channel
B.
When
the
input
pulse
decays
through
the
50%
level,
the
channel
A
CF
discriminator
is
fired
and
triggers
a
prompt
channel
A
output.
When
the
input
pulse
decays
through
the
70%
level,
the
channel
B
CF
discriminator
is
fired
and
triggers
an
internal
delay,
which
then
generates
both
negative
and
positive
channel
B
outputs
at
the
end
of
the
delay.
The
delay
is
fron^anel
adjusted
in
the
range
of
0.1
through
1.1
ixs.
If
the
552
is
set
for
Normal
or
Window
mode,
time-significant
pulses
would
be
generated
for

A
Fraction
50%
,._ri
JT
Channel
B
Trigger
"T"
"T
Delay
-
Channel
B
Neg
Out
Channel
8
Pos
Out,
y
J~L
1
y
y
jy
y,
n
I
/»
1/
I
Int
mode
only
Fig.
4.1.
Timing
Relationships
for
Input
and
Output
Pulses
for
Operation
with
Internal
Strobe.
each
of
the
first
two
input
pulses
but
none
would
be
gen
erated
for
the
third
pulse
because
it
is
too
large
to
satisfy
the
single-channel
criteria.
If
the
552
is
set
for
Integral
mode,
the
responses
would
be
generated
for
the
third
input
pulse,
as
shown
by
the
broken
line
output
pulses.
For
any
mode
of
operation,
the
LL
Out
and
UL
Out
pulses
are
generated
when
the
input
pulse
amplitude
exceeds
the
related
discriminator
level.
The
adjusted
lower-level
threshold
is
furnished
from
either
the
front
panel
Lower-Level
control
or
an
external
source
that
is
furnished
through
the
rear
panel
LL
Ref
connector;
selection
of
the
source
is
made
with
the
rear
panel
LL
Ref
toggle
switch.
In
either
case,
the
range
(for
an
unattenuated
input
signal)
is
from
Oto+IO
V,
measured
from
chassis
ground.
The
adjusted
upper-level
threshold
is
determined
by
the
setting
of
the
front
panel
Upper-Level
control
and
by
the
mode
selector
toggle
switch.
When
the
switch
is
set
at
either
Int
or
Norm,
the
range
of
the
variable
control
is
from
0
to
+10
V,
measured
from
chassis
ground.
When
the
switch
is
set
at
Win,
the
range
of
the
variable
control
is
0
to
+1
V,
measured
above
the
adjusted
lower-level
threshold.
When
the
rear
panel
Strobe
switch
selects
Ext,
operation
of
the
552
is
the
same
as
it
is
for
Int
except
for
the
time
at
which
a
channel
B
output
is
made
available.
For
this
mode
of
operation,
an
external
strobe
pulse
must
be
furnished
after
the
channel
B
CF
trigger
time
and
before
an
auto
matic
reset,
and
the
channel
B
outputs
are
furnished
promptly
at
the
strobe
time.
The
time
window,
during
which
the
strobe
can
be
effective,
is
from
the
trigger
time
to
10
ms
after
the
trigger.
If
no
strobe
is
furnished
within
the
time
window,
the
internal
logic
is
reset
without
gen
erating
an
output
through
channel
B.
For
optimum
time-significant
outputs,
each
front
panel
Walk
Adj
control
must
be
trimmed
for
the
combined
effects
of
the
input
shaping
and
its
time
constants,
and
of
the
expected
dynamic
range
of
operation.
Using
a
dupli
cate
of
the
minimum
and
maximum
amplitudes
for
shaped
input
pulses,
set
each
control
to
provide
the
minimum
walk
for
its
respective
channel;
walk
is
the
variation
of
time
of
occurrence
vs
input
pulse
amplitude.
Using
internal
strobe,
the
decay
shape
of
an
input
pulse
can
be
reconstructed.
Use
the
following
steps.
1.
Select
the
same
fraction
for
both
channels
of
outputs,
and
adjust
the
Delay
control
as
desired.
2.
Connect
the
channel
A
output
to
the
Start
input
of
a
time-to-pulse-height
converter
(TPHC).
3.
Connect
the
channel
B
Neg
output
to
the
Stop
input
of
the
TPHC.
4.
Furnish
the
shaped
input
pulses
to
the
552
and
meas
ure
the
time
difference
between
the
channel
A
and
channel
B
outputs.
This
is
an
accurate
measurement
of
the
Delay
time
adjustment.
5.
Switch
the
B-Fraction
selector
to
each
of
its
active
settings,
10%
through
90%,
and
measure
the
time
differ
ences
at
each
level;
use
the
adjusted
Delay
time
to
correct
each
measurement.
Note;
Do
not
use
the
Bl
setting
of
the
B-Fraction
se
lector
unless
the
input
pulse
is
bipolar,
since
a
zero
crossover
is
necessary
to
obtain
a
channel
B
output
when
this
selection
has
been
made.
6.
Plot
the
decay
curve
for
the
input
pulses,
using
the
set
of
data
obtained
in
step
5.
5.
CIRCUIT
DESCRIPTION
5.1.
GENERAL
Refer
to
block
diagram
552-0101-B1
and
schematic
dia
gram
552-0201-S1,
both
included
at
the
back
of
the
manual.
Figure
5.1
is
a
simplified
block
diagram
of
the
552
Pulse-
Shape
Analyzer
and
Timing
SCA.
It
shows
that
each
input
pulse
is
furnished
through
an
attenuator
(attenuation
factors
XI,
X10,
and
X100).
The
resulting
input
pulse
is
applied
to
each
of
four
discriminators
and
its
peak
is
also
stretched
and
attenuated
for
each
of
the
two
CF
(con
stant-fraction)
discriminators.
The
UL
(upper-level)
and
LL
(lower-level)
discriminators
form
the
single-channel
analyzer.
When
the
SCA
logic
is
satisfied,
it
gates
the
timing
outputs
of
the
two
channels
for
their
respective
outputs.
Each
of
the
four
discriminators
independently
triggers
a
response
when
the
amplitude
of
its
noninverted
input
exceeds
the
amplitude
of
its
inverted
input.
The
response
of
the
UL
and
LL
discriminators
is
latched
until
an
internal
reset
occurs.
The
stretcher
for
the
constant-
fraction
discriminators
is
also
reset
internally.
Reference
levels
for
the
UL
and
LL
discriminators
are
set
independently
for
either
Normal
or
Integral
mode
opera
tion.
For
Window
operation,
the
threshold
for
the
UL
dis
criminator
is
based
on
the
LL
setting
instead
of
ground.

Input
OUTPUT
GENERATOR
UL
DISC
Int
Norm/Win'
Int/Norm
A
Win
OUTPUT
GENERATOR
IL
DISC
ATTN
A
SCA
CURRENT
SWITCH
CHANNEL
A
GATE
CHANNE
CP
DISC
.2
A
Jumper
tor
Fraction
Select
CURRENT
SWITCH
CHANNEL
B
B-SCA
CHANNEL
DELAY
CP
DISC
PEAK
STRETCHER
Strobe
B-Praction
Switch
Strobe
OUTPUT
GENERATOR
@
UL
Out
LL
Out
A
Neg
Out
B
Neg
Out
-0(FP)
Fig.
5.1.
Simplified
Block
Diagram
of
the
552
PSA/T-SCA.
The
CF
discriminators
are
both
triggered
at
the
onset
of
each
input
pulse,
whether
its
amplitude
is
sufficient
to
trigger
either
of
the
other
two
discriminators
or
not.
Then
each
CF
discriminator
is
reset
when
the
input
pulse
decays
through
its
attenuated
peak-reference
level
be
cause
the
stretch
and
attenuate
circuit
has
generated
and
maintained
this
reference
level
by
that
time
and
has
fur
nished
it
as
the
reference
level
of
its
corresponding
discriminator.
The
stretched
input
to
the
attenuator
for
channel
A
can
be
used
to
set
the
reference
level
at
10%,
20%,
or
50%
of
the
decay
from
the
peak,
selected
by
a
jumper
location
on
the
printed
circuit
board,
J2.
The
same
stretched
input
is
supplied
to
the
channel
B
attenuator
which
can
select
a
reference
level
of
10%,
20%,
30%,
40%,
50%,
60%,
70%,
80%,
90%,
or
100%
of
the
decay
from
the
peak,
selected
by
a
front
panel
switch.
The
logic
gate
is
triggered
when
the
LL
discriminator
has
been
set
and
when
there
is
no
signal
from
the
UL
discrim
inator.
This
enables
a
gate
for
the
channel
A
discriminator
and
a
current
switch
generates
a
NIM-standard
fast
negative
output
promptly
at
the
discriminator
reset.
The
logic
gate
output
also
enables
a
gate
for
the
channel
8
discriminator
that
can
be
used
to
generate
channel
B
out
puts.
A
rear
panel
Strobe
switch
selects
either
an
internal
or
an
external
strobe
signal
for
the
delay
circuit.
If
the
external
strobe
.node
is
used,
the
circuits
are
reset
with
out
generating
a
channel
B
output
if
no
strobe
is
furnished
within
10
ns.
5.2.
INTEGRATED
CIRCUITS
The
nomenclature
used
to
identify
integrated
circuit
packages
in
this
manual
is
defined
below
for
the
example
IC1-7
where
and
10
=
integrated
circuit,
1
=
reference
designation,
7
=
pin
number.
Any
portion
of
an
10
package
can
be
designated
by
its
output
pin
number.
Thus
the
example
specifies
the
por
tion
of
101
that
includes
pin
7
as
an
output.
5.3.
LOWER-LEVEL
BIAS
The
threshold
for
the
lower-level
discriminator
is
adjusted
with
the
front
panel
Lower-Level
control,
R53,
or
is
furnished
as
a
dc
level
through
0N2
on
the
rear
panel.
Switch
82
on
the
rear
panel
selects
which
source
is
effec
tive
for
the
lower-level
bias
reference.
For
the
internal
bias
circuit,
the
minimum
level
of
the
front
panel
control
is
normalized
with
potentiometer
R54,
mounted
on
the
printed
circuit.
The
actual
range
of
R53
Is
from
a
few
millivolts,
adjusted
by
R54,
to
-5
V.
The
ad
justed
level
is
buffered
through
IC1-1
and
inverted
without
being
amplified
through
IC1-7
to
be
furnished
as
the
reference
level
to
the
noninverting
input
of
discrim
inator
IC3.

For
the
external
bias
circuit,
a
dc
level
between
0
and
-10
V
can
be
furnished
through
CN2and
is
divided
by
R56
and
R57.
The
result
that
is
selected
by
switch
S2
is
then
furnished
through
the
same
buffering
and
coupling
net
work
to
the
lower-level
discriminator.
5.4.
UPPER-LEVEL
BIAS
The
threshold
for
the
upper-level
discriminator
is
ad
justed
with
the
front
panel
Upper-Level
control,
R48.
The
range
for
this
control
is
0
to
-5
V.
The
adjusted
level
is
buffered
through
IC1-14
and
furnished
through
either
R60
or
R61,
through
operational
amplifier
IC1-8,
and
to
the
noninverting
input
of
the
upper-level
discriminator,
IC2.
When
switch
S3
is
set
at
either
Integral
or
Normal,
the
gain
of
this
adjusted
bias
is
1.0;
when
the
switch
selects
Window,
the
gain
is
reduced
to
0.1
and
the
effec
tive
range
of
the
control
is
thus
reduced
by
a
factor
of
10.
Also,
when
the
switch
selects
Window,
the
level
that
is
furnished
from
IC1-1
for
the
lower-level
discriminator
is
also
furnished
through
R62
to
IC1-8.
Thus
the
adjusted
lower
level
becomes,
effectively,
the
base
to
which
the
upper
level
is
added
and
the
result
is
a
window
of
0
to
1
V
based
on
the
lower-level
threshold.
5.5.
INPUT
CIRCUIT
The
analog
input
signal
to
be
analyzed
is
furnished
through
CN1
on
the
front
panel
and
through
an
attenuator
network.
The
ATTN
switch,
SI,
on
the
front
panel
can
be
set
at
XI,
X10,
or
X100.
When
it
is
set
at
XI,
the
full
am
plitude
input
signal
is
furnished
to
a
peak
stretcher
and
through
a
divide-by-two
network
into
each
of
the
four
discriminator
circuits.
The
output
of
the
peak
stretcher
is
divided
by
two
so
that
the
original
input
amplitude
range
of
0
to
10
V
corresponds
to
a
0
to
5
V
range
at
the
input
to
each
discriminator
and
this
corresponds
directly
to
the
0
to
5
V
range
that
is
provided
for
each
comparator.
If
the
switch
is
set
at
X10
attenuation,
the
input
signal
is
divided
through
R1
and
R5
so
that
1/10
of
the
input
signal
amplitude
is
available
for
the
internal
circuits.
If
the
switch
is
set
at
X100,
the
signal
is
attenuated
to
1%
of
its
original
amplitude
by
division
through
R1
in
series
with
the
par
allel
network
of
R5
and
R3.
The
attenuator
output
is
applied
to
a
stretcher
circuit
that
stores
the
peak
amplitude
of
its
input
as
a
stretched
level
until
it
is
discharged.
The
discharge
signal
is
furnished
from
106-12
and
occurs
only
after
a
trigger
has
occurred
in
both
the
channel
A
and
channel
B
discriminator
out
puts
and
the
lower-level
discriminator
has
been
reset.
Because
of
this
logic,
if
the
channel
B-Fraction
selector
switch
on
the
front
panel
is
set
at
Bl
and
the
input
does
not
cross
zero,
the
channel
B
discriminator
will
not
be
triggered
and
the
module
will
lock
up
since
its
logic
can
not
be
reset.
Jumper
J1,
shown
on
the
schematic,
is
installed
during
a
test
adjustment
of
the
dc
zero
level
of
the
stretcher
and
is
removed
for
normal
operation.
See
Section
6.2
for
cali
bration
information.
5.6.
LOWER-LEVEL
DISCRIMINATOR
Integrated
circuit
package
IC3
is
the
lower-level
discrim
inator.
As
long
as
the
input
level
at
its
pin
4
is
lower
than
the
reference
level
at
pin
3,
the
output
at
pin
9
is
high.
When
the
input
amplitude
rises
through
the
reference
level,
the
output
at
pin
9
switches
to
the
low
state.
Then
when
the
input
amplitude
decays
back
through
the
refer
ence
level,
the
pin
9
output
switches
back
to
high
again.
When
the
pin
9
output
goes
low,
this
sets
flip
flop
IC4-6
and
IC4-3
high
to
identify
the
lower-level
trigger
point.
The
switch
to
high
at
IC4-3
is
furnished
through
an
output
generator,
Q18
through
Q22,
to
generate
a
NIM-standard
slow
positive
pulse
through
LL
Out
connector
CN6.
It
is
also
furnished
as
one
input
to
105-11,
where
a
decision
is
made
for
the
single-channel
logic.
With
both
inputs
high,
105-11
switches
to
low
to
identify
that
the
logic
is
satis
fied.
Unless
this
condition
is
cancelled
by
a
response
from
the
upper-level
discriminator
before
the
constant-fraction
circuits
are
triggered,
the
output
of
103-11
enables
the
gates
for
the
SCA
outputs.
To
prevent
multiple
firings
of
the
discriminator
near
the
threshold
level,
a
hysteresis
of
about
5
mV
is
furnished
to
the
lower-level
discriminator
by
R220
and
R219.
5.7.
UPPER-LEVEL
DISCRIMINATOR
Integrated
circuit
package
102
is
the
upper-level
discrimi
nator.
As
long
as
the
input
level
at
its
pin
4
is
lower
than
the
reference
level
at
pin
3,
the
output
at
pin
9
is
high.
When
the
input
amplitude
rises
through
the
reference
level,
the
output
at
pin
9
switches
to
low
and
sets
flip
flop
104-11
and
104-8,
with
104-11
going
high.
If
switch
S3
is
set
at
Normal
or
Window,
the
upper-level
discriminator
response
provides
a
low
from
105-8
to
cancel
the
logic
at
105-11
and
to
prevent
any
SCA
output
from
being
gener
ated.
If
switch
S3
is
set
at
Integral,
the
upper-level
re
sponse
is
not
used
at
103-11.
When
104-11
goes
high,
an
output
generator,
013
through
017,
triggers
and
generates
a
NIM-standard
slow
positive
pulse
through
UL
Out
connector
0N4.
A
5
mV
hysteresis
is
used
to
prevent
multiple
firings
near
the
threshold
for
102.
This
is
generated
by
R218and
R124.
5.8.
CHANNEL
A
DISCRIMINATOR
The
channel
A
discriminator
is
107.
The
input
signal
is
furnished
through
pin
3
and
the
reference
level
is
fur
nished
through
pin
4.
At
the
onset
of
the
input
pulse,
the
level
at
pin
3
rises
faster
than
the
level
through
pin
4
and
this
generates
a
low
output
at
pin
9
and
a
high
at
pin
11.
The
level
at
pin
4
is
furnished
from
the
peak
stretcher
so
it
will
remain
at
a
fixed
level,
which
is
a
proportional
amplitude
with
reference
to
the
input
peak,
while
the
input
pulse
decays.
When
the
input
pulse
decay
crosses
the
reference
level,
107
is
reset
to
generate
the
channel
A
trigger.
Jumper
J3
on
the
printed
circuit
board
selects
which
of
the
three
fractions
is
effective
for
the
reference
level;
this
can
be
set
at
10%,
20%,
or
50%
down
from
the
peak
amplitude
(90%,
80%,
or
50%
respectively
of
the
peak
amplitude).
When
107
is
reset
and
its
pin
11
goes
to
ground,
a
10-ns
negative
pulse
is
generated
from
108-15
through
Q23,
108-6,
and
DL1.
If
the
A
SOA
gate,
108-2,
has
been
en
abled
by
a
low
from
Q27A
(logic
is
satisfied)
the
output

from
IC8-15
triggers
a
current
switch
to
generate
a
NIM-
standard
fast
negative
output
pulse
through
CN3
on
the
front
panel.
5.9.
CHANNEL
B
DISCRIMINATOR
The
channel
B
discriminator
Is
109.
The
Input
signal
Is
furnished
through
pin
3
and
the
reference
level
Is
fur
nished
through
pin
4.
At
the
onset
of
the
Input
pulse,
the
level
at
pin
3
rises
faster
than
the
level
at
pin
4
and
this
sets
the
discriminator
with
a
low
at
pin
9
and
a
high
at
pin
11.
The
level
at
pin
4
Is
furnished
from
the
peak
stretcher
so
It
will
remain
at
a
fixed
level,
which
Is
an
amplitude
pro
portional
to
the
Input
peak,
while
the
Input
pulse
decays.
When
the
Input
pulse
decay
crosses
the
reference
level,
109
Is
reset
to
generate
the
channel
B
trigger.
Switch
34
on
the
front
panel
selects
the
fractional
level
that
Is
effec
tive
for
the
pin
4
reference
level;
this
level
can
be
set
at
10%
through
90%,
In
10%
Increments,
or
at
Bl
(equivalent
to
100%),
where
each
fraction
Is
measured
down
from
the
peak
amplitude.
When
109
Is
reset,
the
level
at
Its
pin
11
goes
to
ground
to
Indicate
recognition
of
the
constant-fraction
point
on
the
decay
of
the
Input
pulse.
This
output
Is
furnished
to
an
EOL
gate,
Q27B
through
Q47.
This
serves
as
both
the
SOA
logic
gate
and
the
constant-fraction
trigger
gate,
and
must
be
enabled
from
105-11
In
order
to
respond
to
the
OF
trigger.
With
the
logic
satisfied,
the
trigger
forces
the
collector
of
Q41
high
and
It
will
remain
high
until
It
Is
reset.
The
high
transition
at
Q410
Is
furnished
through
the
delay
circuitry
that
Includes
Q28,
Q29,
Q42,Q33,
Q32,Q30,
and
Q31.
The
Input
pair,
Q28
and
Q29,
Is
biased
from
Q290
and
Q29D
operating
as
a
temperature
compensated
cur
rent
source.
Normally
028
Is
off
and
its
collector
Is
In
the
high
state.
At
the
Input
pulse,
028
turns
on
and
029
turns
off.
The
low
transition
at
the
collector
of
028
Is
fed
through
O30
to
storage
capacitor
076.
Thus
the
029
base
voltage
Is
stepped
In
a
negative
direction
through
076.
Oapacltor
076
Is
charged
by
temperature
compensated
source
032
and
033,
and
the
rate
Is
determined
(for
In
ternal
strobe
operation)
by
front
panel
Delay
control
R189.
When
the
storage
capacitor
has
charged
back
to
the
point
where
the
base
of
029
Is
at
the
same
level
as
the
base
of
028,
029
turns
on
again
to
switch
the
collector
of
029
to
the
low
state.
When
the
collector
of
029
switches
to
the
low
state,
an
output
for
channel
B
will
be
generated.
For
internal
strobe
operation,
1010-15
Is
enabled
by
+5
V
through
D17.
When
0290
goes
high
at
the
trigger
Input,
IC10-15
Is
high
and
IC10-9
Is
low,
so
IC10-3
Is
low.
At
the
end
of
the
delay,
when
0290
goes
low,
this
switches
IO10-9
to
high
and
IO10-15
to
low.
For
10
ns,
both
Inputs
to
1010-3
are
high
so
there
Is
a
10-ns
positive
pulse
gen
erated
at
1010-3.
This
pulse
triggers
output
generator
046,045,
036,037,
and
038
through
066
to
furnish
a
NlM-standard
slow
positive
pulse
through
0N7
on
the
rear
panel
and
0N8
on
the
front
panel.
The
1010-3
output
Is
also
Inverted
through
044
to
trigger
the
current
switch
that
generates
the
NlM-standard
fast
negative
output
through
0N9.
For
external
strobe
operation,
the
charge
circuit
for
076
Is
through
R188,
so
029
Is
turned
on
after
10
If
It
has
not
already
been
turned
on
by
an
external
strobe
pulse.
While
029
Is
turned
off,
gate
IO10-15
Is
enabled
at
Its
pin
13and
will
trigger
an
output
pulse
If
a
NlM-standard
slow
posi
tive
pulse
Is
furnished
through
0N3
on
the
rear
panel.
The
strobe
Input
Is
coupled
through
025
and
026
to
start
the
output
pulse
generation
through
1010-15
In
the
same
manner
as
described
for
Internal
strobe
operation.
At
the
leading
edge
of
the
strobe
Input,
the
signal
through
033
and
034
will
quickly
charge
076
and
turn
off
029
to
reset
the
system.
If
029
Is
turned
on
by
076
before
a
strobe
Is
furnished,
gate
IO10-15
will
be
disabled
so
that
the
strobe
will
have
no
effect.
5.10.
RESET
CIRCUIT
An
Internal
reset
Is
generated
at
106-12
when
all
three
Inputs
are
high.
The
Input
at
pin
2
goes
high
when
both
channel
A
and
channel
B
discriminators
are
reset
(the
trigger
point).
The
Input
at
pin
13
goes
high
when
the
lower-level
discriminator
Is
reset
by
having
the
Input
pulse
amplitude
fall
back
through
the
reference
level.
The
104-3
level
stays
high,
latched,
until
the
flip
flop
Is
reset,
so
the
Input
to
pin
1
of
106-12
Is
also
high.
Thus,
after
all
three
events
have
taken
place
(lower-level
dis
criminator
reset
and
both
channels
triggered)
the
Inputs
to
106-12
are
all
high
to
generate
reset.
The
reset
signal
Is
furnished
to
104-6
and
104-8
to
reset
both
discriminator
latches
and
to
the
Input
stretcher
circuit
to
discharge
Its
stretched
peak
level.
5.11.
DC
POWER
Input
power
from
the
bin
and
power
supply
Is
accepted
through
the
module
connector
on
the
rear
panel.
The
552
operates
on
166
mA
through
the
+12
V
circuit,
166
mA
through
tne
-12
V
circuit,
83
mA
from
+24
V,
and
83
mA
from
-24
V.
Internally
the
+12-V
source
Is
used
to
generate
a
regu
lated
+5
V
by
1011
and
-12
V
Is
used
to
generate
a
reg
ulated
-5
V
by
1012.

6.
MAINTENANCE
AND
CALIBRATION
6.1.
GENERAL
The
basic
performance
of
the
552
Pulse-Shape
Analyzer
and
Timing
SCA
can
be
inferred
from
its
operating
responses.
If
the
unit
fails
to
respond
properly
at
any
time,
use
the
information
in
Section
5
to
identify
the
probable
fault.
The
block
diagrams
of
Fig.
5.1
and
552-
0101-B1
and
the
schematic,
552-0201-S1,
identify
all
of
the
circuits
in
the
instrument.
6.2.
STRETCHER
CALIBRATION
There
is
a
provision
for
calibration
of
the
stretcher
cir
cuit.
Potentiometers
RISand
R29,
mounted
on
the
printed
circuit,
provide
this
calibration.
Use
the
following
pro
cedure:
1.
Remove
jumper
at
location
J1
from
A
to
B
and
insert
In
B
to
C.
2.
Set
potentiometer
R18
fully
counterclockwise,
as
viewed
from
the
top.
3.
With
no
input
signals
into
the
552,
adjust
R27
to
obtain
0
V
±
1
mV
at
TP1.
4.
Remove
jumper
at
location
J1
from
B
to
0
and
insert
in
A
to.B.
.5.
With
no
inputsignalsintothe552,adjustR18toobtain
D
V
±
1
mV
at
TP1.
Leave
jumper
in
position
A
to
B
for
normal
operation.
6.3.
WALK
CALIBRATION
A
Walk
Adj
control
is
furnished
separately
for
each
of
the
two
output
channels.
R86
serves
channel
A
and
R100
serves
channel
B.
Use
the
following
procedure
after
the
stretcher
has
been
calibrated
as
described
in
Section
6.2.
1.
With
the
552
turned
on
and
with
no
input
signal,
adjust
R86
to
a
point
where
the
dc
levels
at
pins
3
and
4
of
107
have
a
difference
of
0
V.
Adjust
R100
so
the
dc
levels
at
pins
3
and
4
of
109
have
a
difference
of
0
V.
2.
Set
the
front
panel
ATTN
switch
at
XI,
the
Mode
switch
at
Int,
and
use
Internal
Strobe.
Adjust
the
Lower-
Level
control
to
its
minimum
setting.
3.
Furnish
a
10-V
shaped
pulse
into
the
552
Input
con
nector.
Use
whatever
shaping
will
be
used
for
subsequent
operation.
4.
Examine
the
response
time
for
each
channel.
5.
Switch
the
ATTN
to
XI0,
and
check
the
response
time
for
walk.
If
any
is
noted,
adjust
R86
carefully
for
channel
A
or
R100
for
channel
B.
6.
Switch
the
ATTN
to
XI00
and
check
for
walk.
If
necessary,
adjust
R86
for
channel
A
and
R100
for
chan
nel
B.
7.
Use
all
three
settings
of
the
ATTN
switch
and
com
pare
the
timing
responses.
The
final
adjustment
of
R86
and
R100
should
provide
minimum
walk.
The
input
attenuator
is
a
high-quality
circuit
for
this
application
and
contributes
nominally
less
than
1
ns
to
the
walk.
8.
Return
the
ATTN
switch
to
X1
for
normal
operation.
6.4.
LOWER-LEVEL
CALIBRATION
The
minimum
level
to
which
the
Lower-Level
front
panel
control
can
be
set
is
40
mV.
This
can
be
calibrated
by
adjusting
R54
on
the
printed
circuit
board
as
follows:
1.
Set
the
Lower-Level
control
at
004/1000
dial
divisions.
2.
Set
the
ATTN
switch
at
XI.
3.
Furnish
a
40
mV
input
pulse
into
the
552.
4.
Adjust
R54
as
required
to
half-trigger
under
these
conditions.
6.5.
FACTORY
REPAIR
This
instrument
can
be
returned
to
the
ORTEC
factory
for
service
and
repair
at
a
nominal
cost.
Our
standard
procedure
for
repair
ensures
the
same
quality
control
and
checkout
that
are
used
for
a
new
instrument.
Always
contact
Customer
Services
at
ORTEC,
(615)
482-4411,
before
sending
in
an
instrument
for
repair
to
obtain
shipping
instructions
and
so
that
the
required
Return
Authorization
Number
can
be
assigned
to
the
unit.
Write
this
number
on
the
address
label
and
on
the
package
to
ensure
prompt
attention
when
the
shipment
reaches
the
ORTEC
factory.

BIN/MODULE
CONNECTOR
PIN
ASSIGNMENTS
FOR
AEC
STANDARD
NUCLEAR
INSTRUMENT
MODULES
PER
TID-20893
(Rev
4)
(adopted
by
DOE)
Pin
Function
Pin
Function
1
+3
volts
23
Reserved
2
-3
volts
24
Reserved
3
Spare
Bus
25
Reserved
4
Reserved
Bus
26
Spare
5
Coaxial
27
Spare
6
Coaxial
*28
+24
volts
7
Coaxial
*29
-24
volts
8
200
volts
dc
30
Spare
Bus
9
Spare
31
Spare
*10
+6
volts
32
Spare
*11
-6
volts
*33
117
volts
ac
(Hot)
12
Reserved
Bus
*34
Power
Return
Ground
13
Spare
**35
Reset
(Sealer)
14
Spare
**36
Gate
15
Reserved
**37
Reset
(Auxiliary)
*16
+12
volts
38
Coaxial
*17
-12
volts
39
Coaxial
18
Spare
Bus
40
Coaxial
19
Reserved
Bus
*41
117
volts
ac
(Neut.)
20
Spare
*42
High
Quality
Ground
21
Spare
G
Ground
Guide
Pin
22
Reserved
Pins
marked
(")
are
installed
and
wired
in
EG&G
ORTEC's
4001A,
40018,
4001C.
401A,
and
4018
Modular
System
8ins.
Pins
marked
(*)
and
(**)
are
installed
in
EG&G
ORTEC-HEP
M250/N
and
M350/N
NIM8INS.

Id
♦
sai3did333d
auHidiNiu
H
l020-2Se
331U0
1
^OZB
I
ini-
-{ins-
-411^
-f^rsh-
,
H9etd|-
Hs^tm-
'—'
/—
6SIU
¥013
96IU
OCZU
OcT::^
0013
HOUdt—
■o
Cto
h-
¥113
icol
v«oj
j«a-
™
OOd
—
CIlJ
-OO-
H^ZZdH
-{corg-
diV{m>
±MD^
^
(i«
C
3
W
(
Z23
)
-zzia-fezaUzal
HcTTa
■/£]♦
4s3[-
^nm
(HID
-mni
110
ZIQ
<JQ>
ZI31
saooid
c
san3vid333d
aunidiNiM
Table of contents
Other EG&G Measuring Instrument manuals
Popular Measuring Instrument manuals by other brands
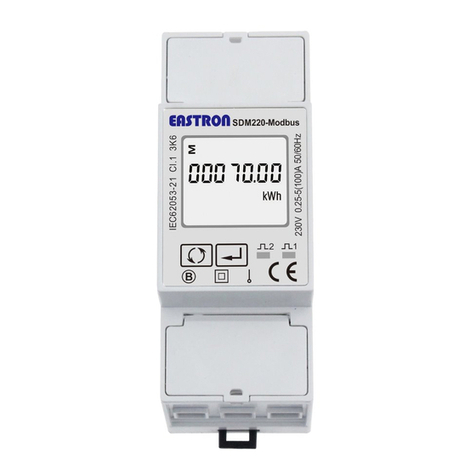
Eastron
Eastron SDM220-Modbus user manual
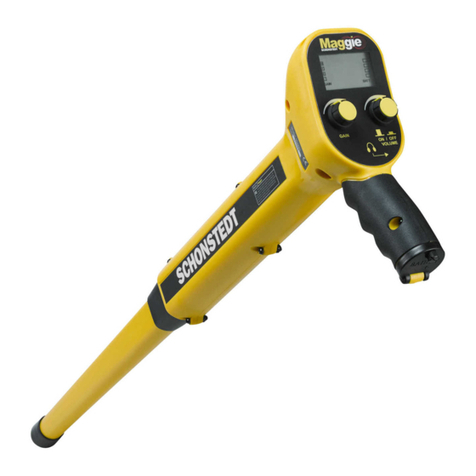
Schonstedt Instrument
Schonstedt Instrument MAGGIE instruction manual
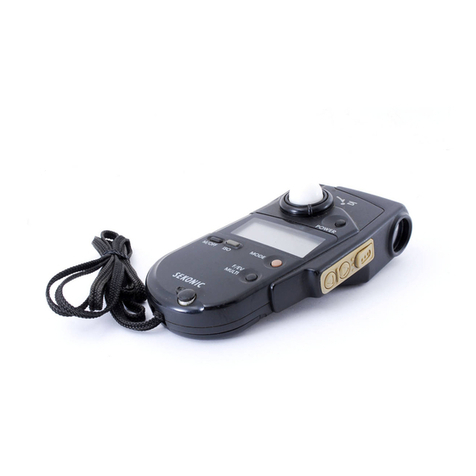
Sekonic
Sekonic MULTIMASTER L-408 operating instructions

NVision
NVision 30100VA owner's manual
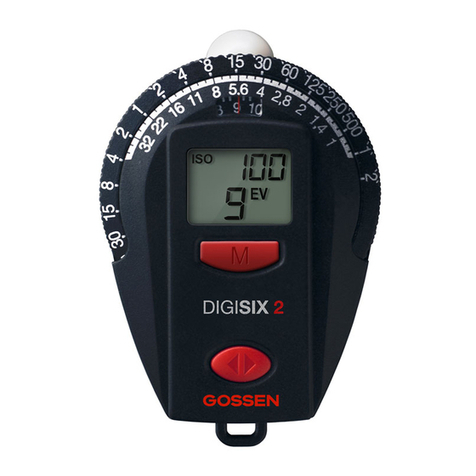
Gossen MetraWatt
Gossen MetraWatt DIGISIX 2 operating instructions

GASTRON
GASTRON GIR-3000 instruction manual