ESD CAN-PCIe/200 User manual

CAN-PCIe/200 Hardware Manual • Doc. No.: C.2042.21 / Rev. 1.2 Seite 1 von 22
esd electronic system design gmbh
Vahrenwalder Str. 207 • 30165 Hannover • Germany
www.esd-electronics.com • Fax: 0511/37 29 8-68
Phone: 0511/37 29 80 • International: +49-5 11-37 29 80
CAN-PCIe/200
Passive CAN-Interface Board
for PCI Express
Hardware Manual
to Product C.2042.xx

Hardware Manual • Doc. No.: C.2042.21 / Rev. 1.2 CAN-PCIe/200
Seite 2 von 22
N O T E
The information in this document has been carefully checked and is believed to be entirely reliable. esd
makes no warranty of any kind with regard to the material in this document, and assumes no
responsibility for any errors that may appear in this document. esd reserves the right to make changes
without notice to this, or any of its products, to improve reliability, performance or design.
esd assumes no responsibility for the use of any circuitry other than circuitry which is part of a product
of esd gmbh.
esd does not convey to the purchaser of the product described herein any license under the patent rights
of esd gmbh nor the rights of others.
esd electronic system design gmbh
Vahrenwalder Str. 207
30165 Hannover
Germany
Phone: +49-511-372 98-0
Fax: +49-511-372 98-68
E-mail: [email protected]
Internet: www.esd-electronics.com
USA / Canada:
esd electronics Inc.
525 Bernardston Road
Suite 1
Greenfield, MA 01301
USA
Phone: +1-800-732-8006
Fax: +1-800-732-8093
E-mail: [email protected]
Internet: www.esd-electronics.us

CAN-PCIe/200 Hardware Manual • Doc. No.: C.2042.21 / Rev. 1.2 Seite 3 von 22
Document-File: I:\texte\Doku\MANUALS\CAN\PCI\PCIe200\english\PCIe-200_12H.ma9
Date of print: 2007-06-14
PCB version: from PEX266 Rev. 1.0
Changes in the chapters
The changes in the user’s manual listed below affect changes in the firmware as well as changes in the
description of the facts only.
Chapter Changes versus previous version
- Product name changed from CAN-PCIe/2000 to CAN-PCIe/200.
- Footer and page numbers changed.
Technical details are subject to change without notice.

Hardware Manual • Doc. No.: C.2042.21 / Rev. 1.2 CAN-PCIe/200
Seite 4 von 22
This page is intentionally left blank.

CAN-PCIe/200 Hardware Manual • Doc. No.: C.2042.21 / Rev. 1.2 Seite 5 von 22
Table of Contents
1. Overview .................................................................... 7
1.1 Description of the Module .................................................... 7
1.2 PCB View with Position of the Connectors ...................................... 8
2. Hardware-Installation ......................................................... 9
3. Technical Data .............................................................. 11
3.1 General Technical Data ..................................................... 11
3.2 PCI Express Interface ...................................................... 11
3.3 CAN Interface ............................................................ 12
3.4 Software Support .......................................................... 12
3.5 Order Information ......................................................... 13
4. Front Panel View with LED Display ............................................ 14
5. Connector Assignment of the CAN Bus Interface ................................. 15
5.1 CAN Interface on DSUB9 Connector .......................................... 15
6. Correctly Wiring Electrically Isolated CAN Networks ............................. 16
7. CAN-Bus Troubleshooting Guide .............................................. 20
7.1 Termination ............................................................. 20
7.2 CAN_H/CAN_L Voltage ................................................... 21
7.3 Ground ................................................................. 21
7.4 CAN Transceiver Resistance Test ............................................ 22

Hardware Manual • Doc. No.: C.2042.21 / Rev. 1.2 CAN-PCIe/200
Seite 6 von 22
This page is intentionally left blank.

Overview
CAN-PCIe/200 Hardware Manual • Doc. No.: C.2042.21 / Rev. 1.2 Seite 7 von 22
+12 V=
+5 V=
+12 V=
+5 V=
C
A
N
B
U
S
CAN
CAN
LEDs
PLD
Physical
CAN
Layer
C
A
N
B
U
S
Electrical Isolation
DC/DC
Converter
DSUB9
CiA pinning
CAN Controller
SJA1000
PCI Express
Endpoint
PEX8311
Electrical Isolation
PCI Express Card Connector
CAN Controller
SJA1000
Physical
CAN
Layer
DSUB9
CiA pinning
2nd CAN Interface
only
CAN-PCIe/200-2
DC/DC
Converter
1. Overview
1.1 Description of the Module
Fig. 1.1: Block circuit diagram of CAN-PCIe/200
The CAN-PCIe/200 is a passive CAN interface board for PCI Express with one, or optionally two CAN
interfaces.
The ISO 11898-2 CAN interface allows a maximum data transfer rate of 1 Mbit/s. Among many other
features of the CAN interfaces, the baud rate can be set by software.
The maximum effective CAN bit rate value may be limited by the performance of the host CPU,
because this is a passive CAN module without a microcontroller on board.
The CAN interface is electrically isolated from the other potentials by optocouplers and DC/DC-
converters.
The CAN-PCIe/200 is equipped with four LEDs in the front panel.

Overview
Hardware Manual • Doc. No.: C.2042.21 / Rev. 1.2 CAN-PCIe/200
Seite 8 von 22
1.2 PCB View with Position of the Connectors
Fig. 1.2: PCB view of CAN-PCIe/200-2 with 2 CAN interfaces

Installation
CAN-PCIe/200 Hardware Manual • Doc. No.: C.2042.21 / Rev. 1.2 Seite 9 von 22
2. Hardware-Installation
Attention!
Electrostatic discharge may cause damage to electronic devices. In order to avoid this, please follow
the instructions below before you touch the CAN module to discharge your personal static
electricity:
@Switch off the power supply of your PC but leave the connector plug in the socket.
@Then touch the metal case of the PC to discharge the static electricity.
@Furthermore you must avoid contact between your clothes and the CAN module.
Procedure:
1. Switch off the PC and all connected peripheral devices (monitor, printer, etc.). Switch off the
CAN devices of the net to which the CAN module is to be connected.
2. Discharge yourself as described above.
3. Disconnect the power supply of the PC from the mains.
4. Remove the PC cover.
Unfasten the mounting screws at the back of the PC and remove the cover.
5. Select an open PCIe slot and remove the slot cover at the back of the PC. Unfasten the screw
which fixes the slot cover and retain it for fixing the module afterwards.
The CAN module can be inserted into every PCI slot. Be careful not to insert the board into an
ISA slot, because this can damage the PC and the board!
6. Insert the CAN module into the selected PCIe slot.
Carefully push the board down until it snaps into place.
7. Attach the board.
Use the screw you removed from the slot cover in step 5.
8. Replace the PC cover.
Secure the cover with the screws you removed in step 4.
@@

Installation
Hardware Manual • Doc. No.: C.2042.21 / Rev. 1.2 CAN-PCIe/200
Seite 10 von 22
9. Connect the CAN wire.
Please note that the CAN bus has to be terminated at both ends!
esd offers special T- connectors and terminator connectors. Additionally the CAN_GND signal
has to be connected to earth at exactly one point. For easier wiring the termination connectors are
equipped with an earth connector (4.8 mm fast-on, male).
A CAN participant without an electrically isolated interface acts as an earth connection.
The first CAN interface (CAN net 0) has to be connected via the lower DSUB connector (X400)
and the second CAN interface (net 1) has to be connected via the upper DSUB connector (X410).
10. Reconnect the power supply of the PC.
11. Switch on the PC, the peripheral devices and the other CAN participants in any order.
12. End of hardware installation.
Continue with the software installation as described in the manual “CAN-API, Part 2: Installation
Guide".

Technical Data
CAN-PCIe/200 Hardware Manual • Doc. No.: C.2042.21 / Rev. 1.2 Seite 11 von 22
3. Technical Data
3.1 General Technical Data
Ambient temperature 0...50 /C
Humidity 90 %, non-condensing
Power supply voltage
via PCIe-bus,
nominal voltage / current consumption (typ. at 20 /C):
3.3 V ±5% / 200 mA
and
+12 V ±5% / 80 mA
Connectors
X400 (DSUB9/male) - CAN net 0
X410 (DSUB9/male) - optional CAN net 1
X100 (Card Edge) - PCIe bus
LEDs 4 LEDs
Dimensions height: 111.15 mm (standard PCI Express Add-In Card Size)
lenght: 80 mm
Link width x1
Weight approx. 85 g (module with 2 x CAN)
Table 3.1: General data of the module
3.2 PCI Express Interface
PCIe Endpoint PEX8311
PCIe port compliant with PCI Express Specification R1.0a
Connector x1 PCI Express card edge socket
Table 3.2: PCI Express data

Technical Data
Hardware Manual • Doc. No.: C.2042.21 / Rev. 1.2 CAN-PCIe/200
Seite 12 von 22
3.3 CAN Interface
Number 1,
optional 2 CAN interfaces
CAN controller SJA1000, ISO 11898-1 (Basic-CAN 2.0)
Physical Layer Physical Layer ISO 11898-2 accordant, transmission rate up to
1 Mbit/s
Termination has to be set externally
Electrical isolation of the CAN
interface against other units
both CAN interfaces are electrically isolated via optocouplers
and DC/DC-converters against each other and against the PCI
bus potentials.
Table 3.3: Data of the CAN interfaces
3.4 Software Support
Software drivers are available for Windows, Linux and QNX. Drivers for other operating systems are
available on request. For detailed information about drivers for other operating systems, please contact
The CAN-API is described in the manual:
"CAN-API, Part 1: Function description"
Order No.: C.2001.21

Technical Data
CAN-PCIe/200 Hardware Manual • Doc. No.: C.2042.21 / Rev. 1.2 Seite 13 von 22
3.5 Order Information
Type Description Order No.
CAN-PCIe/200-1 1 x CAN, ISO11898-1, ISO11898-2 C.2042.02
CAN-PCIe/200-2 2 x CAN, ISO11898-1, ISO11898-2 C.2042.04
CAN-DRV-LCD Object licence for Windows and Linux incl. CD-ROM C.1101.02
CAN-PCIe/200-Vx VxWorks object licence C.2042.55
CAN-PCIe/200-ME Hardware manual in English 1*)
(this manual) C.2042.21
CAN-PCIe/200-ENG
Engineering manual in English 2*)
Contents: Circuit diagrams, PCB top overlay drawing,
data sheets of significant components
C.2042.25
CAN-API-MD Software manual of the CAN-API in English 1*) C.2001.21
1*) If ordered together with the product, the manual will be delivered free of charge.
2*) This manual is liable for costs, please contact our support.
Table 3.5: Order information

LED Display
Hardware Manual • Doc. No.: C.2042.21 / Rev. 1.2 CAN-PCIe/200
Seite 14 von 22
4. Front Panel View with LED Display
The CAN-PCIe/200 is equipped with four green LEDs located in the front panel.
Fig. 4.1: Front panel view
LED
Display function (LED on)
Name Function Colour
A ADU-CS green reserved
B CAN1-IRQ green Interrupt in CAN Net 1 -
CAN frames are received or transmitted
C CAN0-IRQ green Interrupt in CAN Net 0 -
CAN frames are received or transmitted
D Power green 5 V-power supply voltage is on
Table 4.1: LEDs

CAN-PCIe/200 Hardware Manual • Doc. No.: C.2042.21 / Rev. 1.2 Seite 15 von 22
Connector Assignment
5. Connector Assignment of the CAN Bus Interface
5.1 CAN Interface on DSUB9 Connector
The assignment of the signals to the connector pins of CAN net 0 (X400) is equal to the assignment of
the optional second CAN net 1 (X410). The connectors are 9-pin DSUB connectors (male).
Pin Position:
Pin Assignment:
Signal Pin Signal
1 reserved
(CAN_GND) 6 2 CAN_L
CAN_H 7 3 CAN_GND
reserved 8 4 reserved
reserved 9 5 Shield
9-pin DSUB connector
Signal description:
CAN_L, CAN_H... CAN signal lines
CAN_GND ... reference potential of the local physical CAN layer
(CAN_GND) ... optional reference potential of the local physical CAN layer
reserved ... reserved for future applications
Shield... shielding

Wiring
Hardware Manual • Doc. No.: C.2042.21 / Rev. 1.2 CAN-PCIe/200
Seite 16 von 22
9
1
4
5
6
7
9
2
3
8
1
4
5
6
7
2
3
8
CAN_L
CAN_H
CAN_GND
Shielded wire with
transposed wires
CAN_L
CAN_H
CAN_GND
(at wire shield)
120 Ohm
120 Ohm
earth (PE)
Wire structure Signal assignment of wire and connection of earthing and terminator
n.c.
n.c.
n.c.
n.c.
n.c.
n.c.
n.c.
n.c.
n.c.
n.c.
n.c.
n.c.
n.c.
n.c.
n.c. = not connected
DSUB9 connector
(female or male)
pin designation
connector case connector case
DSUB9 connector
(female or male)
pin designation
CAN wire with connectors
6. Correctly Wiring Electrically Isolated CAN Networks
Generally all instructions applying for wiring regarding an electromagnetic compatible installation,
wiring, cross sections of wires, material to be used, minimum distances, lightning protection, etc. have
to be followed.
The following general rules for the CAN wiring must be followed:
1.
A CAN net must not branch (exception: short dead-end feeders) and has to be terminated
by the wave impedance of the wire (generally 120 W ±10%) at both ends (between the
signals CAN_L and CAN_H and not at GND)!
2.
A CAN data wire requires two twisted wires and a wire to conduct the reference potential
(CAN_GND)!
For this the shield of the wire should be used!
3. The reference potential CAN_GND has to be connected to the earth potential (PE) at one
point. Exactly one connection to earth has to be established!
4. The bit rate has to be adapted to the wire length.
5. Dead-end feeders have to kept as short as possible (l < 0.3 m)!
6. When using double shielded wires the external shield has to be connected to the earth
potential (PE) at one point. There must be not more than one connection to earth.
7. A suitable type of wire (wave impedance ca. 120 Ω±10%) has to be used and the voltage
loss in the wire has to be considered!
8. CAN wires should not be laid directly next to disturbing sources. If this cannot be avoided,
double shielded wires are preferable.
Figure: Structure and connection of wire

Wiring
CAN-PCIe/200 Hardware Manual • Doc. No.: C.2042.21 / Rev. 1.2 Seite 17 von 22
l< 0,3 m
CAN_L
CAN_GND
CAN_H
PE
l< 0,3 m
CAN-CBM-
AI4
CAN-CBM-
COM1
CAN-CBM-
DIO8
l< 0,3 m
l< 0,3 m
l< 0,3 m
Female Connector
Male Connector
e.g.
CAN-SPS Interface
CSC595/2
or
CAN-PC Board
Terminator
Male Terminator
(Order-no.: C.1302.01)
Connecting
CAN_GND to
Protective Conductor PE
Terminator
with PE Connector
Female Terminator
(Order-no.: C.1301.01)
T-Connector
C.1311.03
CAN-Cable
Order-no.: C.1323.03
Net 2
Net 1
e.g. PCI/405,
CAN-USB,
VME-CAN2, etc.
CAN-Cable
Order-no.: C.1323.03
CAN-Cable
Order-no.: C.1323.03
T-Connector
C.1311.03
T-Connector
C.1311.03
T-Connector
C.1311.03
CAN-Board
T-Connector
Order-no.: C.1311.03
Cabling
for devices which have only one CAN connector per net use T-connector and dead-end feeder
(shorter than 0.3 m) (available as accessory)
Figure: Example for correct wiring (when using single shielded wires)
Terminal Resistance
use external terminator, because this can later be found again more easily!
9-pin DSUB-terminator with male and female contacts and earth terminal are available as
accessories
Earthing
CAN_GND has to be conducted in the CAN wire, because the individual esd modules are
electrically isolated from each other!
CAN_GND has to be connected to the earth potential (PE) at exactly one point in the net!
each CAN user without electrically isolated interface works as an earthing, therefore: do not
connect more than one user without potential separation!
Earthing CAN e.g. be made at a connector

Wiring
Hardware Manual • Doc. No.: C.2042.21 / Rev. 1.2 CAN-PCIe/200
Seite 18 von 22
Wire Length
Optical couplers are delaying the CAN signals. By using fast optical couplers and testing each
board at 1 Mbit/s, however, esd CAN guarantee a reachable length of 37 m at 1 Mbit/s for most
esd CAN modules within a closed net without impedance disturbances like e.g. longer dead-end
feeders. (Exception: CAN-CBM-DIO8, -AI4 and AO4 (these modules work only up to 10 m with
1 Mbit/s))
Bit rate
[Kbit/s]
Typical values of reachable
wire length with esd
interface lmax [m]
CiA recommendations
(07/95) for reachable wire
lengths lmin [m]
1000
800
666.6
500
333.3
250
166
125
100
66.6
50
33.3
20
12.5
10
37
59
80
130
180
270
420
570
710
1000
1400
2000
3600
5400
7300
25
50
-
100
-
250
-
500
650
-
1000
-
2500
-
5000
Table: Reachable wire lengths depending on the bit rate when using esd-CAN interfaces

Wiring
CAN-PCIe/200 Hardware Manual • Doc. No.: C.2042.21 / Rev. 1.2 Seite 19 von 22
Examples for CAN Wires
Manufacturer Type of wire
U.I. LAPP GmbH
Schulze-Delitzsch-Straße 25
70565 Stuttgart
Germany
www.lappkabel.de
e.g.
UNITRONIC ®-BUS CAN UL/CSA (UL/CSA approved)
UNITRONIC ®-BUS-FD P CAN UL/CSA (UL/CSA approved)
ConCab GmbH
Äußerer Eichwald
74535 Mainhardt
Germany
www.concab.de
e.g.
BUS-PVC-C (1 x 2 x 0.22 mm²) Order No.: 93 022 016 (UL appr.)
BUS-Schleppflex-PUR-C (1 x 2 x 0.25 mm²) Order No.: 94 025 016 (UL appr.)
SAB Bröckskes GmbH&Co. KG
Grefrather Straße 204-212b
41749 Viersen
Germany
www.sab-brockskes.de
e.g.
SABIX® CB 620 (1 x 2 x 0.25 mm²) Order No.: 56202251
CB 627 (1 x 2 x 0.25 mm²) Order No.: 06272251 (UL appr.)
Note: Completely configured CAN wires can be ordered from esd.

CAN-Bus Troubleshooting Guide
Hardware Manual • Doc. No.: C.2042.21 / Rev. 1.2 CAN-PCIe/200
Seite 20 von 22
120 Ω
CAN_H
CAN_GND
CAN_L
CAN_L
CAN_H
CAN_GND
V
Ω
120 Ω
23
1
V
1
7. CAN-Bus Troubleshooting Guide
The CAN-Bus Troubleshooting Guide is a guide to find and eliminate the most frequent hardware-error
causes in the wiring of CAN-networks.
Figure: Simplified diagram of a CAN network
7.1 Termination
The termination is used to match impedance of a node to the impedance of the transmission line being
used. When impedance is mismatched, the transmitted signal is not completely absorbed by the load
and a portion is reflected back into the transmission line. If the source, transmission line and load
impedance are equal these reflections are eliminated. This test measures the series resistance of the
CAN data pair conductors and the attached terminating resistors.
To test it, please
1. Turn off all power supplies of the attached CAN nodes.
2. Measure the DC resistance between CAN_H and CAN_L at the middle and ends of
the network (see figure above).
The measured value should be between 50 and 70 S. The measured value should be nearly the same
at each point of the network.
If the value is below 50 S, please make sure that:
- there is no short circuit between CAN_H and CAN_L wiring
- there are not more than two terminating resistors
- the nodes do not have faulty transceivers.
If the value is higher than 70 S, please make sure that:
- there are no open circuits in CAN_H or CAN_L wiring
- your bus system has two terminating resistors (one at each end) and that they are 120 Seach.
Other manuals for CAN-PCIe/200
1
Table of contents
Other ESD Computer Hardware manuals
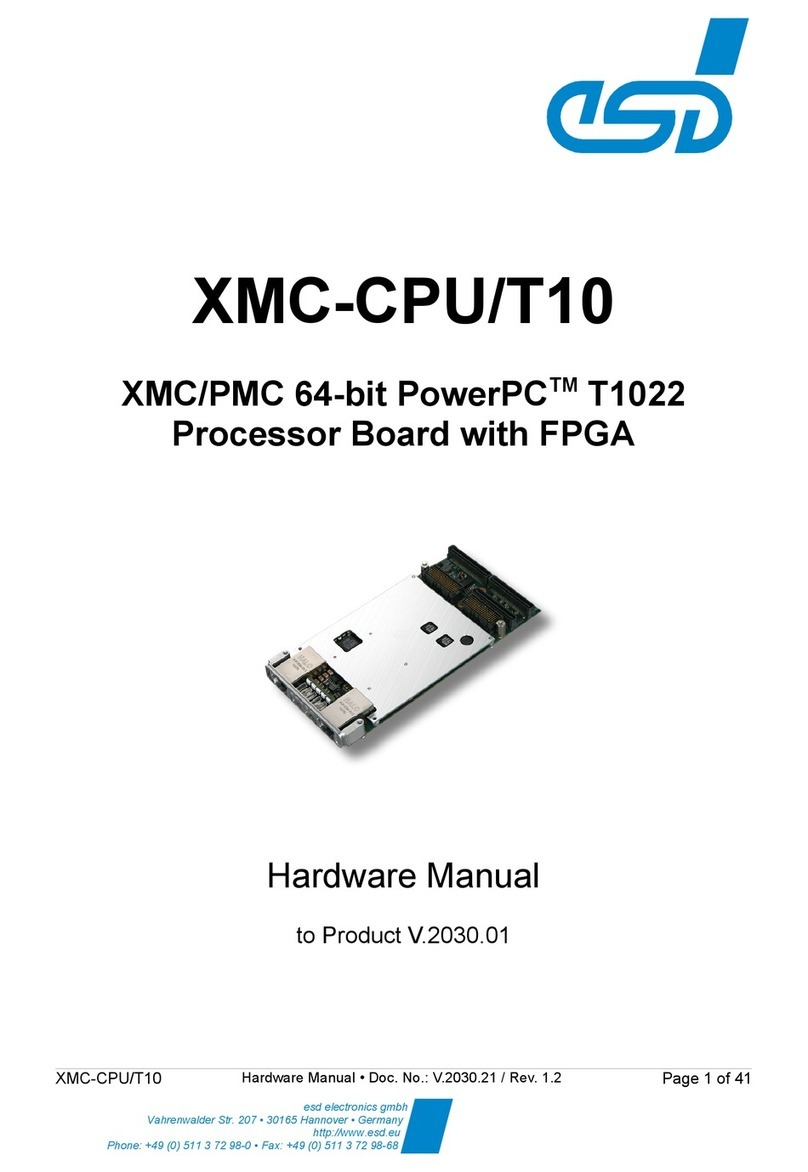
ESD
ESD XMC-CPU/T10 User manual
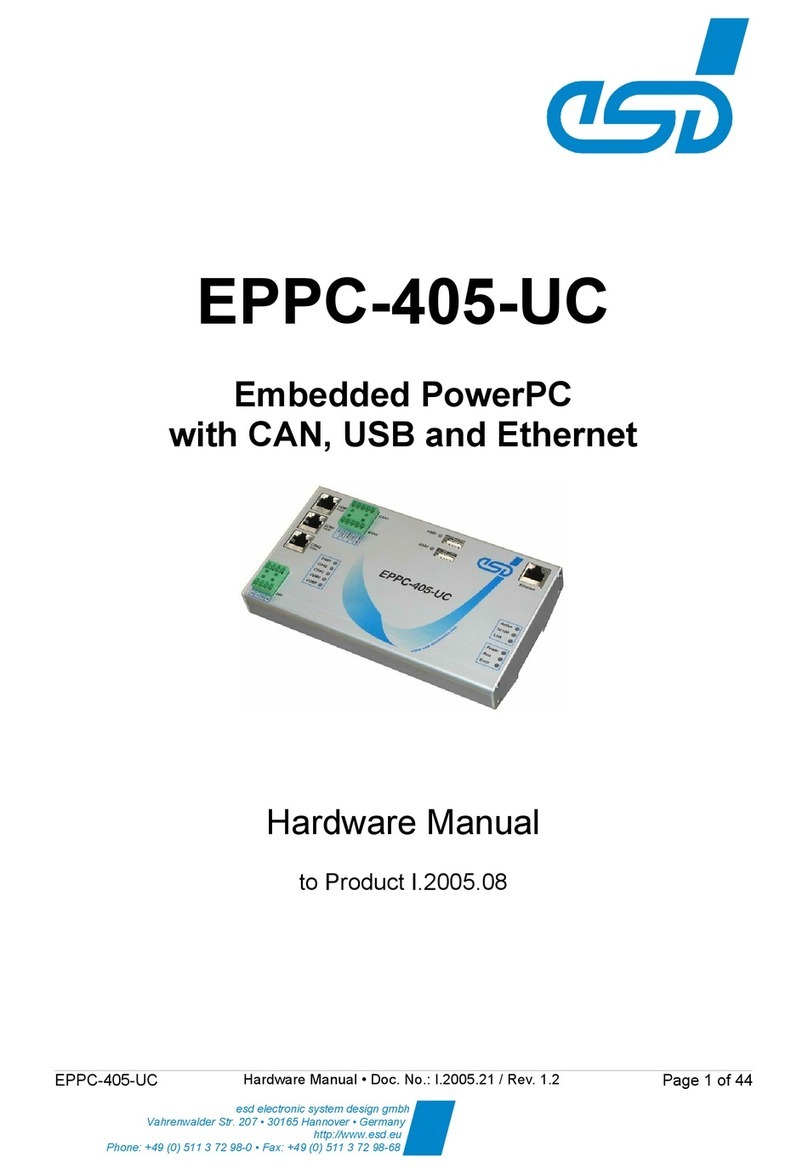
ESD
ESD EPPC-405-UC User manual
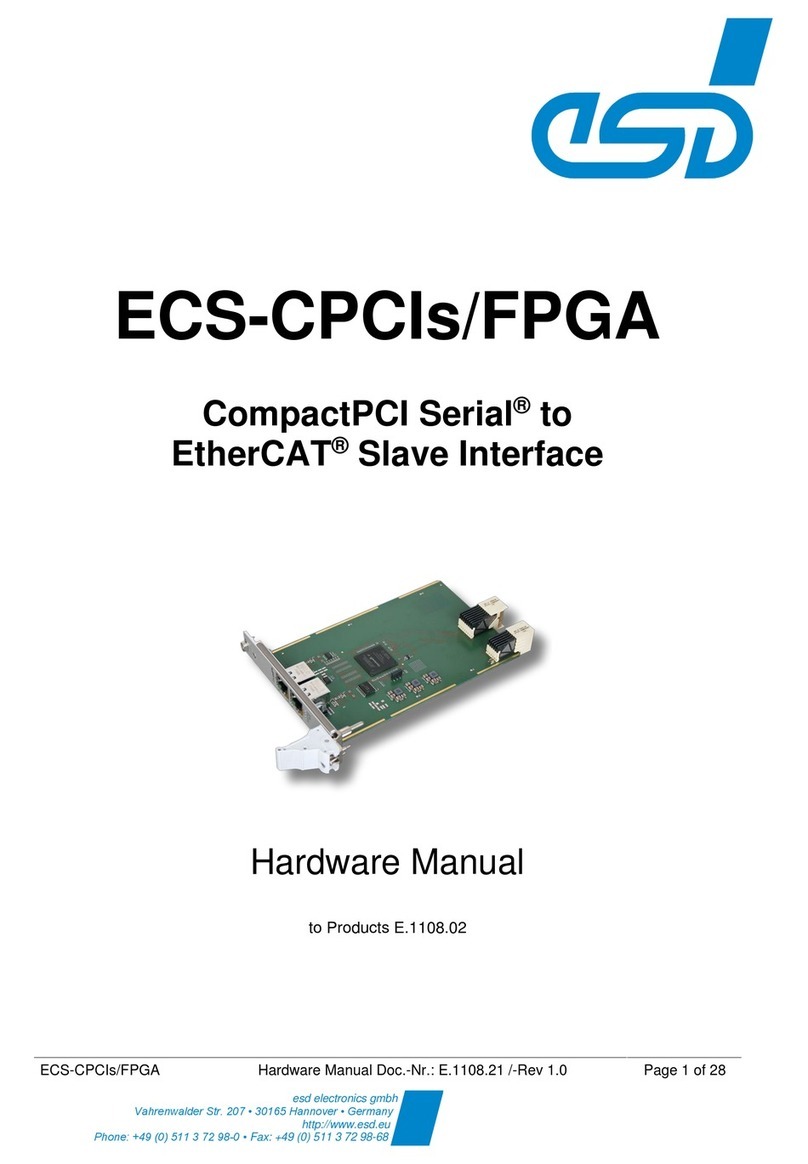
ESD
ESD ECS-CPCIs/FPGA User manual
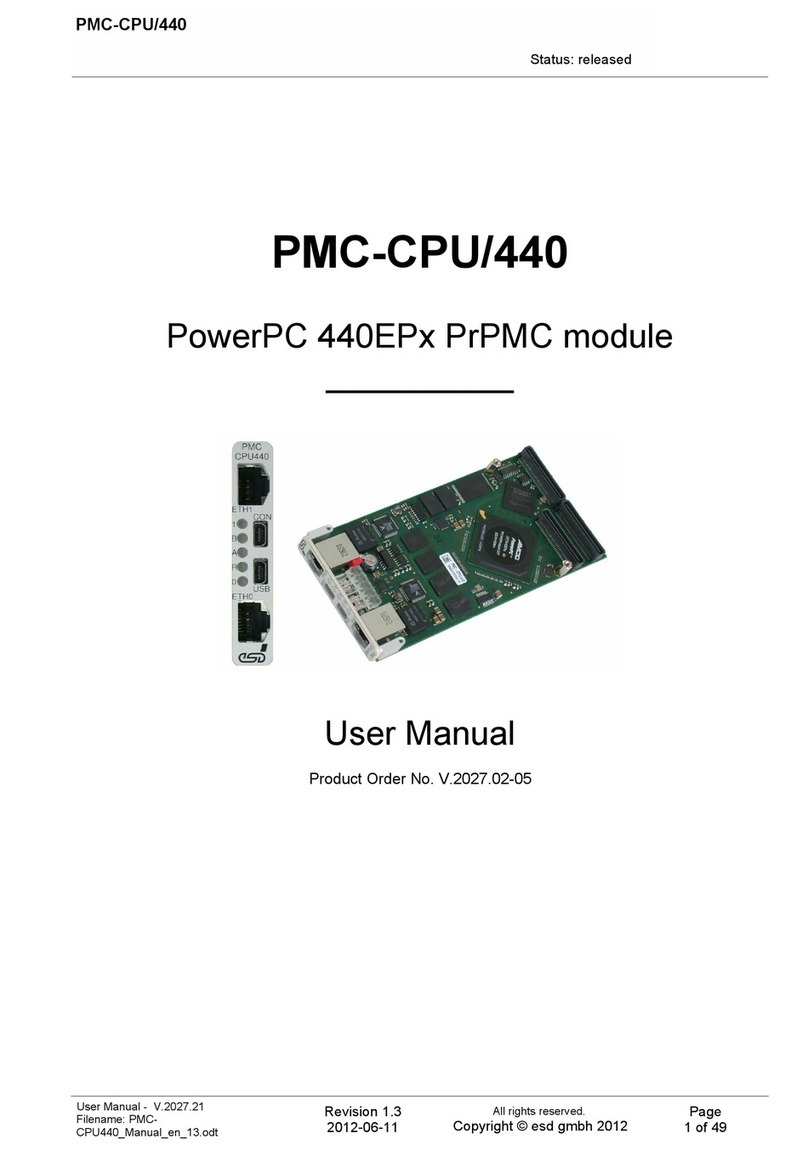
ESD
ESD PMC-CPU/440 User manual

ESD
ESD PMC-CAN/402-4-FD User manual
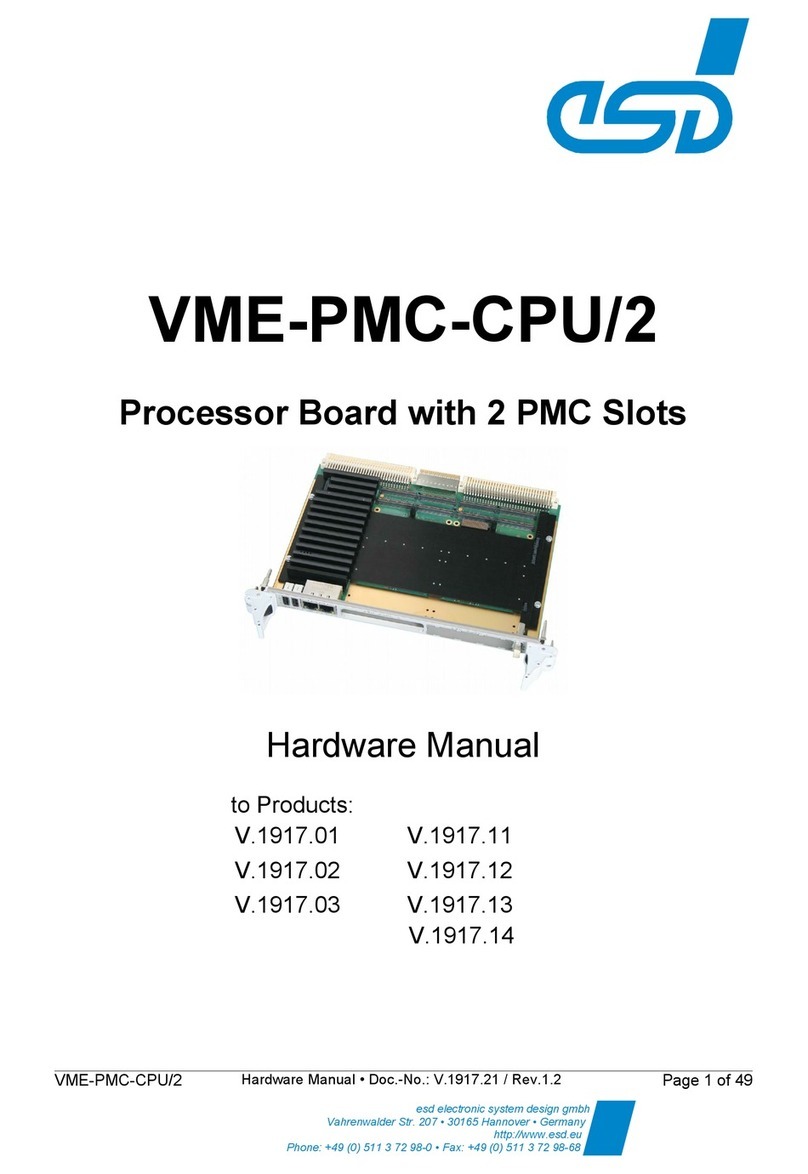
ESD
ESD VME-PMC-CPU/2 User manual
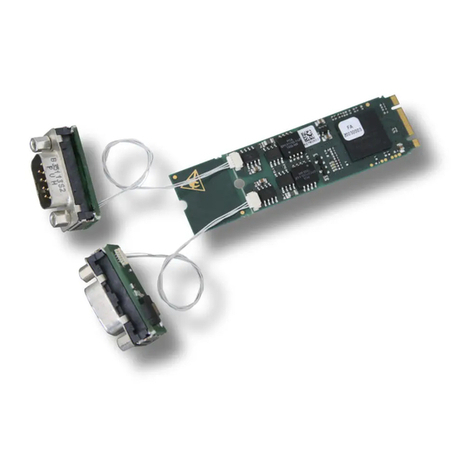
ESD
ESD CAN-M.2/402-2-FD User manual
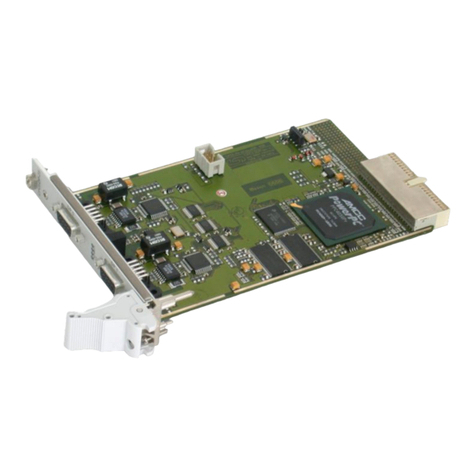
ESD
ESD CPCI-DP-2S User manual
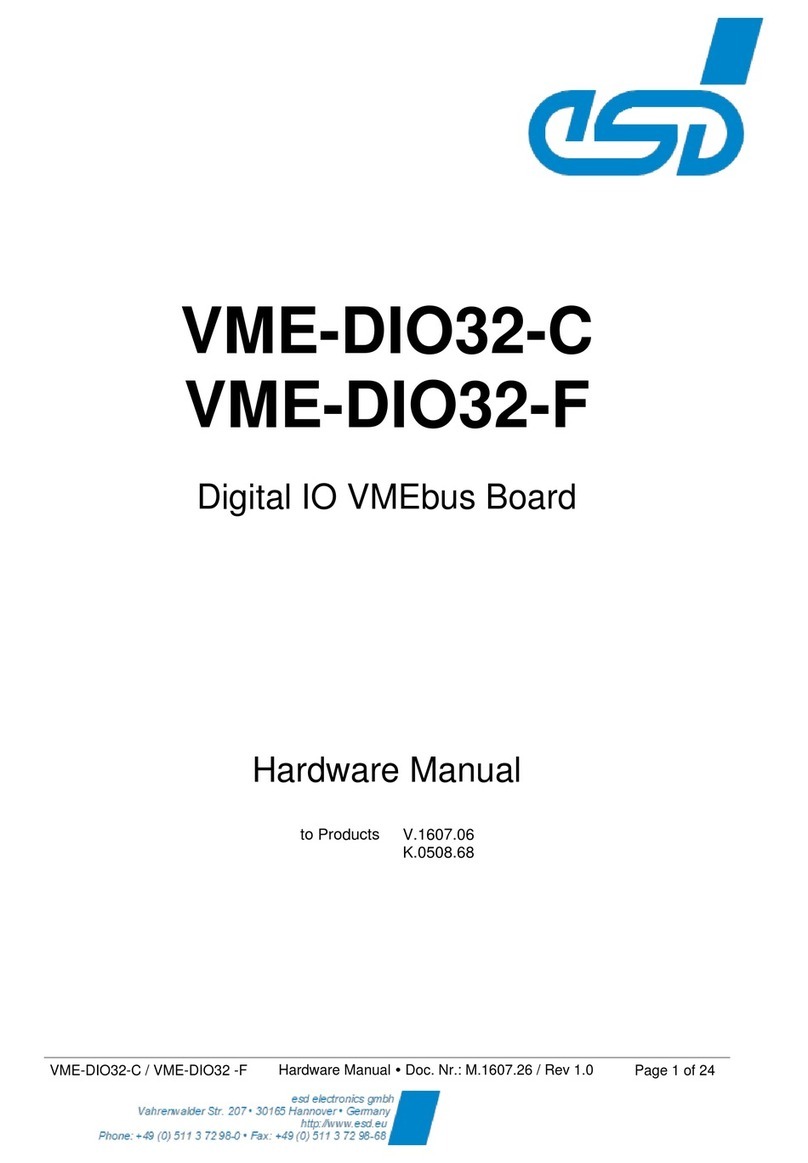
ESD
ESD VME-DIO32-C User manual
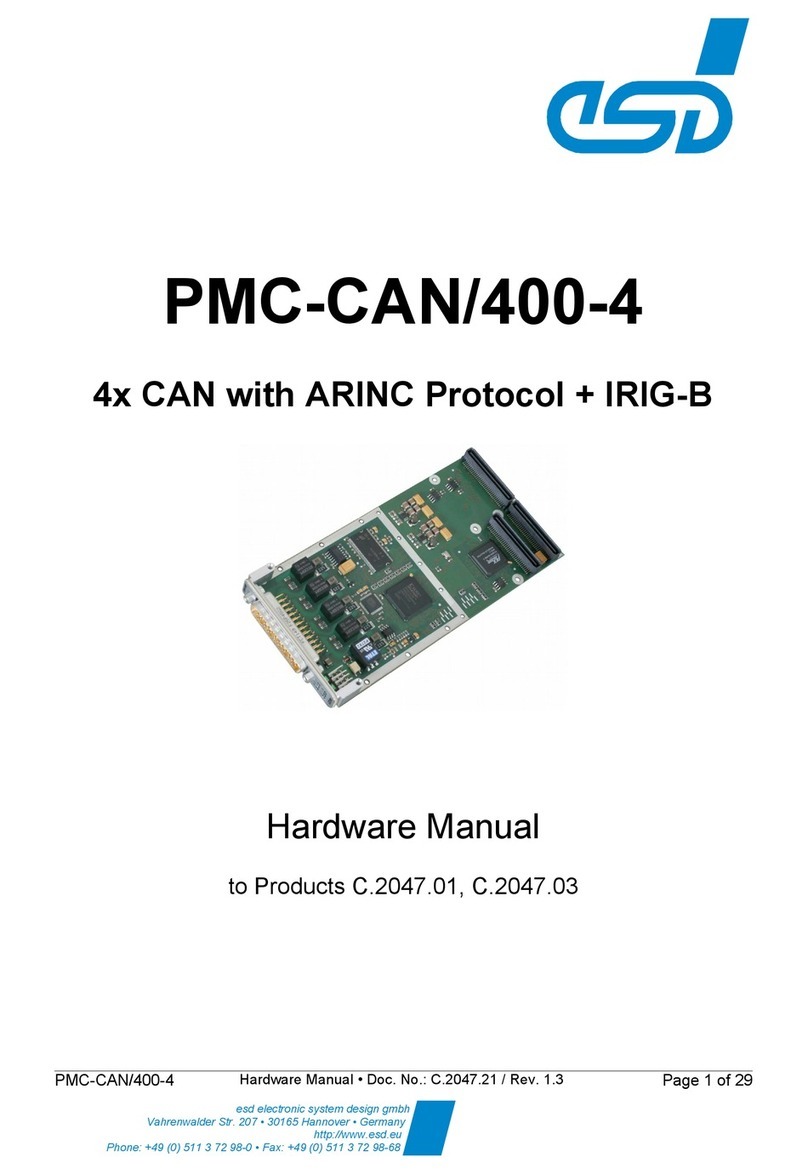
ESD
ESD PMC-CAN/400-4 User manual
Popular Computer Hardware manuals by other brands

Sony Ericsson
Sony Ericsson GC89 - Ericsson EDGE/Wireless LAN PC Card user guide
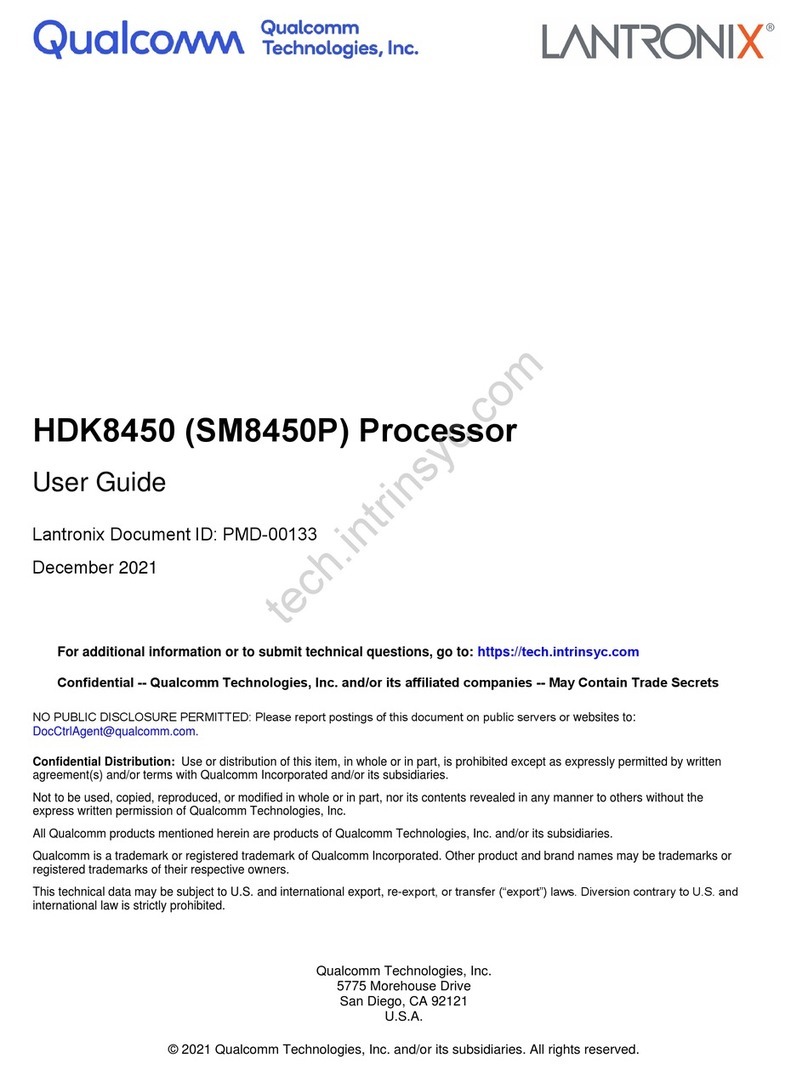
Lantronix
Lantronix Qualcomm HDK8450 user guide
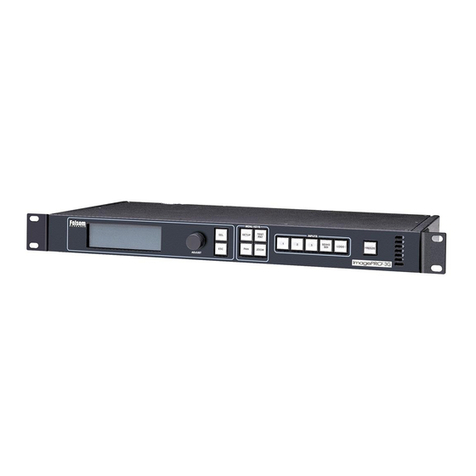
Barco
Barco ImagePRO-3G Specifications
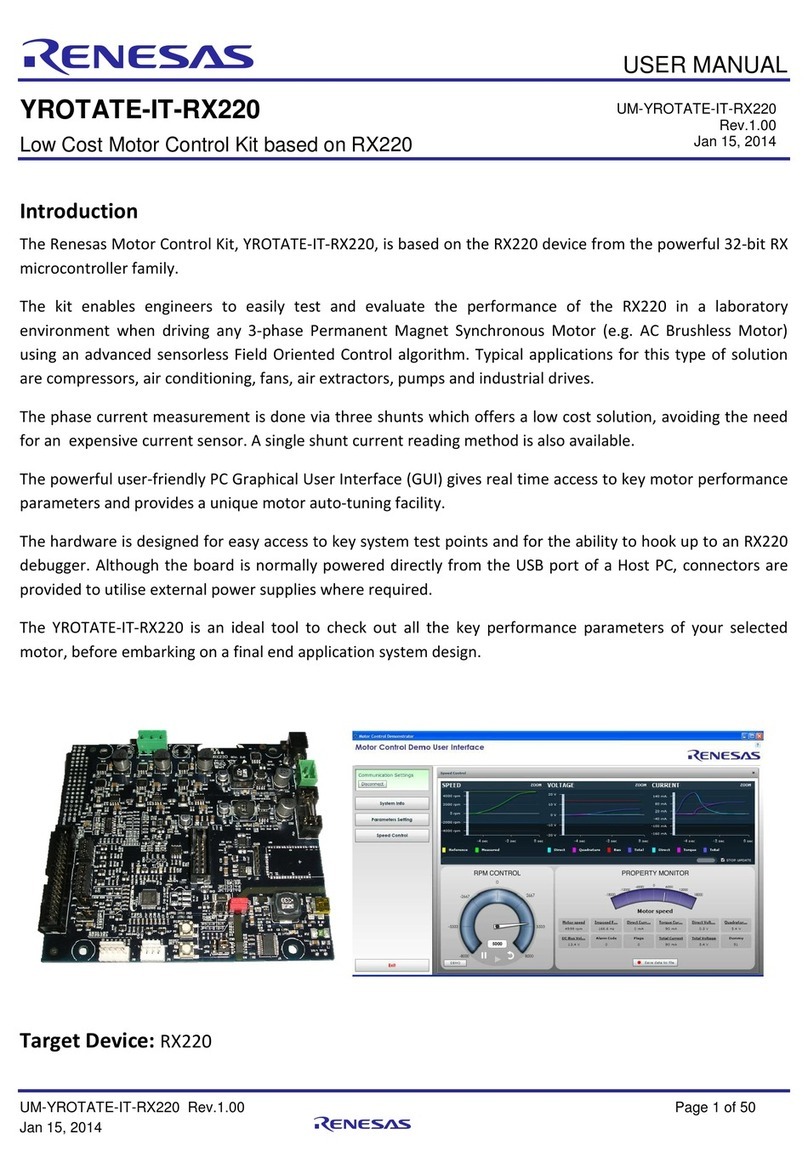
Renesas
Renesas YROTATE-IT-RX220 user manual
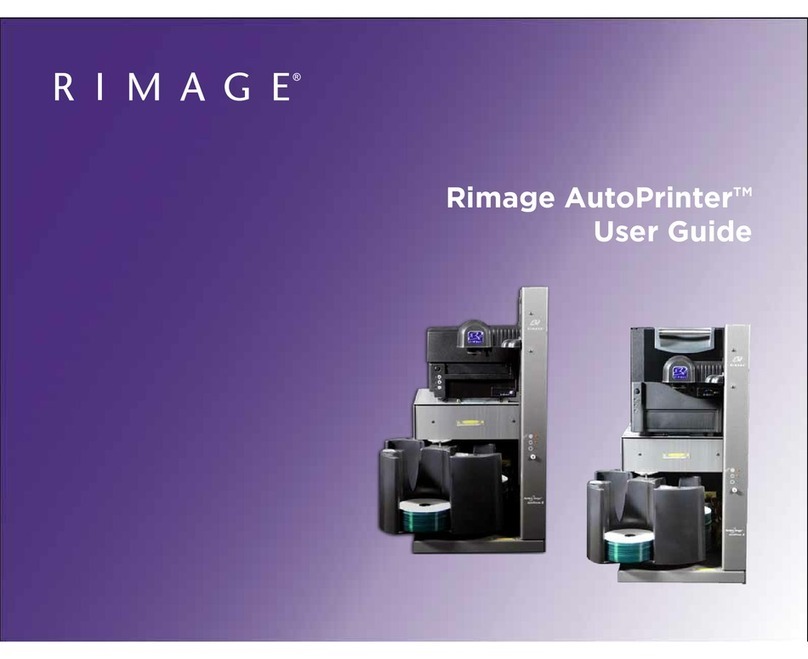
Rimage
Rimage AutoPrinter user guide
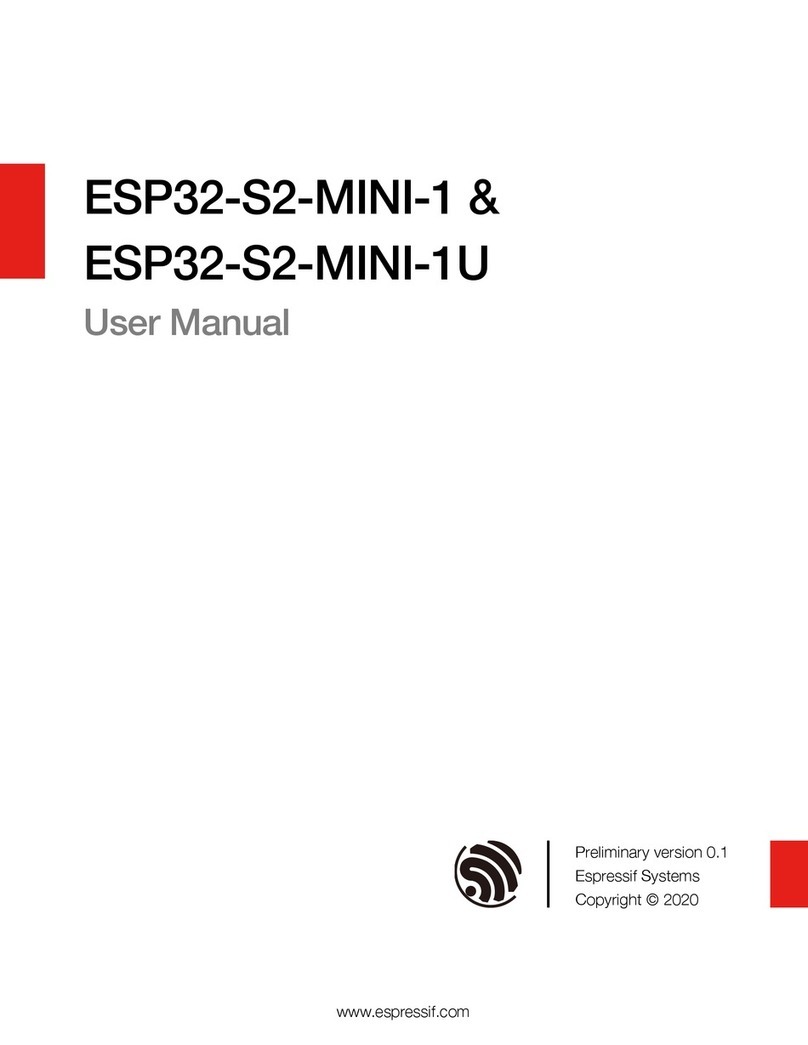
Espressif Systems
Espressif Systems ESP32-S2-MINI-1 user manual