Fike Quadnet User manual

26-0582 Issue 15
Fire Detection & Alarm System Control Panel V3
(Suitable for Quadnet control panels from V2.00)
Control Panel Engineering and
Commissioning Manual
(TO BE RETAINED BY THE COMMISSIONING ENGINEER)

Quadnet Control Panel Engineering and Commissioning Manual
2
Fike’s policy is one of continual improvement and the right to change a specification at any time without notice is reserved. Whilst every care has
been taken to ensure that the contents of this document are correct at time of publication, Fike shall be under no liability whatsoever in respect of
such contents.
Due to the complexity and inherent importance of a life risk type system, then training on this equipment is essential, and commissioning should
only be carried out by competent persons.
Fike cannot guarantee the operation of any equipment unless all documented instructions are complied with, without variation.
E&OE.
© 2008 Fike Safety Technology Ltd. All rights reserved. Document revised January 2012.

Quadnet Control Panel Engineering and Commissioning Manual
3
Contents
Introduction..........................................................................................................................5
System Design .........................................................................................................5
Equipment Guarantee ..............................................................................................5
Anti Static Handling Guidelines................................................................................5
Warning ....................................................................................................................5
EMC..........................................................................................................................5
The Quadnet System...........................................................................................................6
Advantages of Addressable Systems.......................................................................6
Control Panel .......................................................................................................................7
Mounting the Control Panel......................................................................................7
The General Assembly.............................................................................................7
Control Panel Disassembly ......................................................................................8
Left Hand Side Door (CIE Door) Removal ...............................................................9
Physical Dimensions ................................................................................................9
Cabinet Installation...................................................................................................10
Control Panel Assembly...........................................................................................10
Topology and Cabling...............................................................................................11
Cable Specification...................................................................................................11
Addressable Circuit Wiring.......................................................................................11
Loop Loading............................................................................................................12
General System Schematic......................................................................................13
Control Panel Main PCB...........................................................................................14
Control Panel Terminals...........................................................................................16
Network.................................................................................................................................22
Network Topology and Cabling ................................................................................22
Network Cable Specification.....................................................................................22
Network Connection Schematic ...............................................................................23
Network Terminals....................................................................................................23
General Operation of Control Panel ..................................................................................25
Control Panel Front .................................................................................................25
LED Indication ..........................................................................................................26
Fire Alarm Controls...................................................................................................28
System Controls .......................................................................................................28
Access Levels and Codes........................................................................................29
Access Level 1 (Normal) ..........................................................................................29
Access Level 2A (User)............................................................................................29
Access Level 2B (Supervisor) ..................................................................................30
Access Level 3 (Engineer)........................................................................................34
Printer.......................................................................................................................40
Alarm Confirmation.............................................................................................................41
Alarm Confirmation Delay ........................................................................................42
Selecting the Devices...............................................................................................42
Commissioning....................................................................................................................43
Installation 1st Stage ................................................................................................43
Installation 2nd Stage...............................................................................................43
Initialisation...............................................................................................................43
Commissioning.........................................................................................................44
Configuration Example.............................................................................................45
End User Training.....................................................................................................45

Quadnet Control Panel Engineering and Commissioning Manual
4
Good Practice.......................................................................................................................46
Number of Devices ..................................................................................................46
Label the Loop Ends.................................................................................................46
Note the Loop Readings...........................................................................................46
Configuration Printout and Drawings........................................................................47
Initialisation..........................................................................................................................48
Normal Readings......................................................................................................48
Initialisation Process.................................................................................................48
Initialisation Faults ....................................................................................................49
Earth Faults...............................................................................................................51
General Fault Finding..........................................................................................................53
Common Faults ........................................................................................................53
Intermittent and Recurring Faults .............................................................................54
Summary of Messages.............................................................................................56
Advanced Connections.......................................................................................................59
Monitored Relays......................................................................................................59
Technical Data......................................................................................................................60
Control Panel............................................................................................................60
Power Supply Unit ....................................................................................................61
System Version Compatibility...................................................................................61
OSP Version Compatibility .......................................................................................61
Resistor Colour Codes..............................................................................................62
Battery Calculations..................................................................................................63
Installation Checklist.................................................................................................64
Commissioning Checklist..........................................................................................65
Loop Continuity and Insulation Test Results............................................................66
Network Continuity and Insulation Test Results.......................................................67
Fire Alarm System Notice.........................................................................................68
Device Details...........................................................................................................70
Your Notes................................................................................................................71
Important Points ..................................................................................................................74 – Back Page

Quadnet Control Panel Engineering and Commissioning Manual
5
Introduction
This Manual is intended as a guide to the engineering and commissioning principles of the Quadnet
Addressable Intelligent Fire Alarm and Detection system, and covers the system hardware information only.
Due to the complexity and inherent importance of a system covering a ‘Life Protection Risk’, training on this
equipment is essential, and commissioning should only be carried out by competent and approved persons.
For further details of the availability of commissioning services contact your supplier.
System Design
This document does not cover Fire Alarm system design, and a basic understanding is
assumed.
A knowledge of BS5839: Pt 1: 2002 +A2: 2008 : Fire Detection and Alarm Systems for
Buildings is essential.
It is strongly recommended that a suitably qualified and competent person is consulted in
connection with the Fire Alarm System design and that the entire system is commissioned in
accordance with the current national standards and specifications.
Equipment Guarantee
The equipment carries no warranty unless the system is installed, commissioned and serviced
in accordance with this manual and the relevant standards by a suitably qualified and
competent person or organisation
Anti Static Handling Guidelines
Immediately prior to handling any PCBs or other static sensitive devices, it is essential to
ensure that a personal connection to earth is made with an anti-static wrist-strap or similar
apparatus.
Always handle PCBs by their sides and avoid touching any components. PCBs should also be
stored in a clean dry place, which is free from vibration, dust and excessive heat, and protected
from mechanical damage.
Warning
Do not attempt to install this equipment until you have fully read and understood this
manual.
Failure to do so may result in damage to the equipment and could invalidate the warranty.
Technical support will not be available if the instruction manual has not been read and
understood. Please have this instruction manual available whenever you call for technical
support.
For further technical support please contact your distributor. Do not call the Fike Safety
Technology support department unless your distributor has first given their advice and
attempted to rectify the issue.
EMC This equipment when installed is subject to the EMC directive 2004/108/EC. It is also subject
to UK Statutory Instrument 2006 No. 3418.
To maintain EMC compliance this system must be installed as defined within this manual. Any
deviation from this renders the installer liable for any EMC problems that may occur either to
the equipment or to any other equipment affected by the installation.
!
!
!
!
!

Quadnet Control Panel Engineering and Commissioning Manual
6
The Quadnet System
The Quadnet system is an addressable intelligent detector system, with many advantages over traditional
addressable analogue detector systems. In order to understand the benefits, let us look more closely at the
terms Fire Detector and Fire Sensor. These terms are often used interchangeably but actually have quite
different meanings. A fire detector is the device (component as defined in EN54) which automatically
detects a fire. In the majority of addressable fire detection systems, the fire devices are in fact fire sensors
which only transfer data relating to smoke and heat levels to the control panel, and the fire decision is made
by the panel.
Nearly all current addressable systems are Addressable Analogue Detector Systems where the control
panel continually scans the fire sensors, processes the returned data, and makes decisions about fires and
faults.
The Quadnet system is defined as an Addressable Intelligent Detector System or an Addressable Fire
Detection and Alarm System with Independent Distributed Intelligence. Distributed intelligence
signifies that the signal processing is spread throughout the system, in order that the decisions about fires
and faults are taken within the detector itself. The detector is capable of being remotely programmed for
different modes of detection.
Thus the Quadnet system is an analogue addressable system, but with the processing power distributed
across the entire system. This dramatically reduces the complexity of the control panel and the data traffic,
and improves the efficiency of the system.
The system addressing is carried automatically upon initialisation from the control panel, and does not need
to be programmed manually at each device.
Advantages of Addressable Systems
The nature of a microprocessor control system with individually identified devices means that the precise
location of fires and faults may be indicated, more complex actions may be implemented, system flexibility
is improved and installation and cabling costs are reduced.
In the Quadnet system, very efficient communications mean that very low quiescent power consumption
maximises the standby capacity, high power transfer capabilities allow more sounders to be connected to
the loop, and a very fast response to events is achieved as the control panel does not have to poll every
device for status data.
IMPORTANT NOTE:
The Quadnet Panel is a 2 box solution comprising a Control Panel (as per this manual) and a matching
Power Supply Unit. This manual describes the Quadnet Control Panel. Please refer to the Quadnet Power
Supply Unit Installation Instructions for details of how to install the Power Supply Unit and connect it to the
Quadnet Control Panel.

Quadnet Control Panel Engineering and Commissioning Manual
7
Control Panel
Mounting the Control Panel
First identify the proposed location for the control panel. Ensure that the control panel will be easily
accessible, and that account is taken of any subsequent work that may affect access. It should be located
at the most likely point of access for the fire services.
The control panel should be mounted on a flat, vertical wall at a height where the indicators may be seen
without difficulty.
Like all electronic equipment, the control panel may be affected by extreme environmental conditions. The
position selected for its installation should therefore be clean and dry, not subjected to high levels of
vibration or shock and at least 2 metres away from any pager or radio transmitting equipment. Ambient
temperatures should be within the range given within the Technical Data section, i.e. not directly over a
radiator or heater or in direct sunlight.
In common with all microprocessor-controlled panels, the control panel may operate erratically or may be
damaged if subjected to lightning induced transients. Proper earth/ground connections will greatly reduce
susceptibility to this problem.
The General Assembly
DOCUMENT POCKET
OPTIONAL PRINTER
CIE / CONTROL DOOR
TERMINATION PCB
(BACKPLANE)

Quadnet Control Panel Engineering and Commissioning Manual
8
Control Panel Disassembly
The panel is normally supplied disassembled to make first fix easier. If the panel is already assembled it
must be disassembled in order to fix the backbox to the wall.
The front left hand door (CIE door) which houses the panel controls must be opened and the ribbon cables
unplugged from the main backplane.
Remove the collar / flange assembly complete with doors. Loosen the 4 screws in the keyhole slots (2 per
side). Remove the retaining screws (2) one at the top and one at the bottom. Lift off the collar / flange
assembly complete with doors and set aside.
The backplane is mounted on a chassis which is fixed into the box by 1 screw at the top. There are two
metal retainers at the bottom.
The screw must be loosened then the chassis plate can be lifted up and out of the box.
BACKPLANE
LOOP CARDS

Quadnet Control Panel Engineering and Commissioning Manual
9
Left Hand Side Door (CIE Door) Removal (if required)
If the panel is assembled and it is necessary to remove the left hand door that houses the CIE in order to
replace the CIE, the door must be opened to its full extent and the ribbon cables unplugged from the main
backplane.
Then it must be gently taken beyond its fully opened extent. This will cause the hinge pins to pop out of the
door. The door can then be completely removed.
Note: a minimum gap of 320mm must be left between the back box and any wall or projection to allow the
door to be gently taken beyond its full extent and removed
Physical Dimensions
50mm
50mm
420mm
420mm
FLUSH MOUNT HOLE IN WALL

Quadnet Control Panel Engineering and Commissioning Manual
10
Cabinet Installation
This backbox is compatible with the Quadnet range of Fire Alarm Control
Equipment and is common to the range of control panels, repeater panels and
power supply units.
Surface Mounting
At least four of the five mounting holes should be used to secure the cabinet to a
solid wall using suitable screws of at least 50mm in length. Ensure that a minimum
gap of 50mm is left between the sides of the backbox and any wall or projection
(such as another box). On the left hand side, a larger gap of 320mm must be left to
allow future removal of the CIE door in situ.
Cable Entry
The cable entry locations available will depend on the type of unit that is intended, and it is important to note
which cable entry areas are suitable for each derivative.
Quadnet Control Panel
The two rows of knockouts at the top are suitable.
The two rows of knockouts in the rear at the top
are suitable.
The main rear face must be kept clear for
mounting the electronics.
The two rows of knockouts at the bottom are
suitable.
Technical Data
Dimensions: Width x Height (excluding flange) 415mm x 415mm
Width x Height (including flange) 445mm x 445mm
Depth 75mm
Flush Mount Hole Size Backbox only 420mm x 420mm
Control Panel Assembly
This is the reverse of the disassembly process above.
To refit the front left hand door, which houses the panel controls, the right hand door must be opened. The
left hand door should then be lined up with the hinge pins and then gently closed. Closing the door will
cause the hinge pins to pop back into the door.
The ribbon cables are labelled Ribbon A, Ribbon B, Ribbon C and Ribbon D on both the front door PCB and
the backplane. These cables must be reconnected as follows: Ribbon A on the front panel PCB to Ribbon A
on the backplane, Ribbon B on the front panel PCB to Ribbon B on the backplane and so on.

Quadnet Control Panel Engineering and Commissioning Manual
11
Topology & Cabling
All system wiring should be installed to comply with BS 5839: Pt 1: 2002: Amendment 2: 2008 and BS 7671
(wiring regulations) and any other standards relevant to the area or type of installation. A cable complying
with the BS 5839: Pt 1: 2002 Category 1 (cables required to operate for prolonged periods during fire
conditions) is required. This must be a 2-core 1.5mm2screened fire resistant cable (ie. MICC, FP200,
Firetuff, Firecell, Lifeline or equivalent). Ventcroft No-Burn multicore cable was utilised during the LPCB
approval testing.
Cable Specification
Max Capacitance Core to Screen...................................................180pF / m
Max Capacitance Core to Core ......................................................100pF / m
Max Inductance............................................................................... 1.0mH / km
Max Resistance Two Core Screened 1.5mm²................................ 12.1Ω / km
Fire Proof........................................................................................ BS5839: Pt1: 2002 Category 1
Example.......................................................................................... Datwyler 8700
Addressable Circuit Wiring
The addressable circuit must be installed as a loop with a maximum length of up to 2 km.
Addressable spur circuits are NOT permitted with this system.
In order to protect against possible data corruption it is important ensure the following points are adhered
to:
1. The addressable circuit cable screen must be connected to the loop SCRN terminal at the
control panel.Both ends must be connected using the terminals provided.
2. The addressable circuit cable screen must not be connected to earth/ground at any point other
than the control panel (at the SCRN terminal provided, not at any earthing point). Do not
connect the screen to a device back box.
3. The addressable circuit cable screen continuity must be maintained at every point of the
loop, using the terminals provided or a suitable connection block.
4. Do not use a 4-core cable as a loop feed & return due to the possibility of data corruption. It is
essential that two 2-core cables are used if this is required.
5. Excess cable lengths must not be coiled as coiling will increase the inductance and cause
communication problems.

Quadnet Control Panel Engineering and Commissioning Manual
12
Loop Loading
In order to allow a method of calculating the maximum loop loading that the system will support, each
device has a rating assigned in Device Loading Units (DLUs). This relates to the load presented in alarm. A
maximum of 450 DLUs are permissible on each loop (subject also to a maximum of 200 addressable
devices, whichever limit is reached first).
The DLUs of the current models of devices as at October 2011 are as follows:
PRODUCT DESCRIPTION
DLU RATING
Type Product
Code Subtype SP0-Off Low Medium High
MP
203 0003
Multipoint Mk3
1
-
-
-
205 0003
ASD Mk3
1
-
-
-
MPS
203 0001
Multipoint with Sounder Mk3
1
1.5
4.5
6
205 0001
ASD with Sounder Mk3
1
1.5
4.5
6
205 0012
ASD with Sounder/Strobe Mk3
4.5
5
8
10
MCP
403 0006
403 0007
Manual Call Point Mk3 3 - - -
SOUNDER
313 0001
313 0002
Soundpoint Mk3 1.5 2 4 5.5
323 0001
Hipoint Mk3
1.5
2
4
5.5
303 0013
Bell Mk2
2
22
22
22
303 0012
303 0022
Flashpoint 1.5 4.5 6.5 8
326 0021
326 0023
Sounder/Strobe 9 9.5 11.5 13
326 0001
326 0003
Sounder 1.5 2 4 5.5
326 0015
Strobe
9
-
-
-
I/O
803 0006
Loop I/O Module Mk2
10.5
-
-
-
CZM 803 0010
Conventional Zone Module
(Loop Powered)
23.5 - - -
803 0010
Conventional Zone Module
(Ext PSU)
3.5 - - -
ANCILLARY 803 0003
803 0005
Multipoint I/O Module (in Relay
Base)
Multipoint I/O Module (in Box)
3 - - -
600 0092
Remote Indicator
0.5
-
-
-
The Quadnet OSP programming software v2.02 or later (v2.04 or later required for the latest devices)
automatically keeps control of the quantities and DLU ratings of devices on the loop and will warn the
engineer if the limit is reached. It will not allow a system to be programmed to exceed the maximum DLU
rating. It can detect the type of the device and, in the case of devices manufactured from March 2010, the
subtype from the above list as well. For devices manufactured prior to this date, the Quadnet OSP will
attempt to detect the subtype and use the appropriate DLUs. The engineer can override the automatically
detected subtype if required ie. if the OSP cannot correctly identify an older device, the engineer can tell the
system that the device is a different subtype to the one OSP has selected (eg. Soundpoint instead of
Flashpoint) within the same main type.
Note: 1) An Excel spreadsheet (document no. 26-1049) is also available to automatically work out
both standby battery calculations and loop loading calculations based on the quantities
entered. This includes ratings for legacy devices as well as the above current models.
2) Whilst the system will operate a maximum of 800 devices per control panel, for compliance
with EN54-2, it is recommended that a limit of a maximum of 512 detection devices is
adhered to. This includes detectors and manual call points, but does not affect the number of
sounders or other alarm devices on the system.

Quadnet Control Panel Engineering and Commissioning Manual
13
General System Schematic
Sita Multipoint Sita MP I/O
Sita MCP Remote Indicator
Sita Loop I/O Module
ADDRESSABLE
LOOPS
ALL 2-CORE
1.5mm
2
MAX 2km
QUADNET
CONTROL
PANEL
QUADNET
PSU
1 X 2C1.5
2 X 2C2.5
QUADNET
PSU
(OPTIONAL
UP TO 4 MAX
PER PANEL)
1 X 2C1.5
2 X 2C2.5

Quadnet Control Panel Engineering and Commissioning Manual
14
Control Panel Main PCB Located on the inside of the front left hand inner door.
LED PCB
Display
Main Control Panel
CIE PCB
Ribbon connectors
to Termination PCB
USER FUNCTION
BUTTON
LED PANEL
ZONE LEDS
CONTRAST
LCD BACKLIGHT
LCD
RIBBON
RIBBON A
TO TERMINATION PCB
RIBBON B
TO TERMINATION PCB
RIBBON C
TO TERMINATION PCB
RIBBON D
TO TERMINATION PCB
PRIINTER PORT
NETWORK CARD
KEY SWITCH
REMOVE LINKS
TO PROGRAM
EXTERNAL FLASH
PRINTER
CONTROL
PROCESSOR
COMMS
CONTROLLER
BUZZER
KEYSWITCH
MAIN
CIE
PROCESSOR
10-0049
PSU CONTROL ISP
DO NOT CONNECT
CIE PCB
POWER
TEST
DISABLED
FAULT
FIRE
10-0050
LED PCB
LCD
LCD BACKLIGHT CONNECTION
LCD RIBBON
LED RIBBON
NETWORK I/F

Quadnet Control Panel Engineering and Commissioning Manual
15
Control Panel Firmware Upgrade Link Pins
The control panel firmware may be upgraded on site if required using the External Flash Upgrade software.
The two link pins located to the right of the key switch connector MUST be left in position for correct field
operation and only removed when performing the flash upgrade.
Before undertaking any upgrades, it is important to make sure that the proposed new software is
compatible with the system hardware version and with the other panels and components in the system.
Note that firmware upgrades are only permitted to be carried out by Fike engineers or trained installation
engineers operating under specific instructions from Fike Technical Support.
LCD Contrast
The LCD contrast may be adjusted by rotating the screw on the variable resistor located in the upper left
hand corner of the main PCB. This may require many (10 to 20) rotations if the contrast is particularly out of
adjustment.
LCD CONTRAST
VR1
Rotate anticlockwise
to reduce the
contrast (lighten text)
Rotate clockwise to
increase the contrast
(darken text)

Quadnet Control Panel Engineering and Commissioning Manual
16
Control Panel Terminals
The Termination and PSU PCB (also known as the backplane) is located at the rear of the main control
panel back box.
The Loop cards may be plugged into the loop card slots on the backplane. To avoid damage, ensure that
the panel is powered down whilst connecting and removing the loop cards. When connecting, do not
press down on the loop card other than where indicated. Similarly, when removing, do not pull the centre of
the card but pull from both ends at the same time so that the PCB does not get flexed.
o o o o o o o o o o o
o o o o o o o o o o
o o o o o
o o o o
BUFFER
MICRO
PROC
BUFFER
POWER
FET
POWER
FET
FIRMWARE UPGRADE
ONLY
SERIAL PORT
BOTTOM EDGE
PRESS HERE ONLY
PRESS HERE ONLY
TOP EDGE
LOOP CARD
RIBBON CABLE CONNECTIONS TO MAIN CONTROL PCB MOUNTED ON DOOR
SW 1
BACK PLANE CONNECTION PCB
2
3
SERIAL
10k EOL
10k EOL
3k3 EOL
680R
N/O
3k3 EOL
680R
N/O
3k3 EOL
680R
N/O
3k3 EOL
680R
N/O
SCRN
B
A
SCRN
0V
+24V
SCRN
0V
+24V
N
O
T
U
S
E
D
RIBBON D
RIBBON C
RIBBON B
RIBBON A

Quadnet Control Panel Engineering and Commissioning Manual
17
Loop Card Serial Port
The serial port may be used for connection to a computer running the Diagnostic software in order to
interrogate the loop communications; it is also used to upgrade the firmware of the loop card.
Loop Card Firmware Upgrade Link Pins
The loop card firmware may be upgraded on site using the external flash utility. The link pin should be left
connected for correct field operation and removed for firmware upgrade.
Note that firmware upgrades are only permitted to be carried out by Fike engineers or trained installation
engineers operating under specific instructions from Fike Technical Support.
Outputs 1 and 2: SPR, COM, NC, NO, SCRN
Outputs 1 and 2 are derived from single pole change over ‘volt-free’ relay contacts which are not fault
monitored. The relay contacts are rated at 30V DC / 1A max. All inductive loads should be diode protected
to prevent back EMF. However, if this is not done, the load should be limited to 200mA to reduce the
likelihood of back EMF causing damage to the relay contacts.
The default setting for Output 1 causes the relay to operate as a Common Fire output where the relay is
energised in the fire condition. The default setting for output 2 causes the relay to operate as a Common
Fault output where the relay is de-energised in the fault condition. Various other modes may also be set
using the Quadnet OSP programming software. However, to meet the requirements of EN54-2, Output 1
must be left as a fire output (Common Fire or Zonal Fire) and Output 2 must be left as Common Fault.
On later versions of the panel hardware, Output 2 is optimised for Common Fault use and has an additional
safety feature (which cannot be disabled) to turn off the output in the unlikely event of the operating
software stopping, even if not specifically configured as Common Fault.
Terminal
Description
SPR
Spare terminal for general use. Not connected internally.
COM
Common contact
NC
Normally closed contact
NO
Normally open contact
SCRN
Field cable screen connection
Outputs 3 and 4: COM, NC, NO, SCRN
Outputs 3 and 4 are single pole change over ‘volt-free’ relay contacts which are not fault monitored. The
relay contacts are rated at 30V DC / 1A max. All inductive loads should be diode protected to prevent back
EMF. However, if this is not done, the load should be limited to 200mA to reduce the likelihood of back EMF
causing damage to the relay contacts.
The default setting for Output 3 and Output 4 is “not configured”. Various modes may be set using the
Quadnet OSP programming software.
NOTCONNECTED
SPARE
COM
NO
NC
SCRN
ON BOARD PCB
FIELD CONNECTIONS
COM
NO
NC
SCRN
ON BOARD PCB
FIELD CONNECTIONS

Quadnet Control Panel Engineering and Commissioning Manual
18
Terminal
Description
COM
Common contact
NC
Normally closed contact
NO
Normally open contact
SCRN
Field cable screen connection
Outputs 5 and 6: MO+, MO-, SCRN
Outputs 5 and 6 are monitored circuits which may be configured to monitor for open and short circuit faults
with a 10K EOL resistor, and to be activated with a stage 3 alarm.
The default setting for outputs 5 and 6 causes the circuits to operate as Common Fire Sounder Circuits,
where the outputs turn on in the alarm condition. Various other states may also be set using the Quadnet
OSP programming software.
The maximum output current for each output is 200mA. These outputs are protected by the 315mA T
fuses labelled FUSE 1 and FUSE 2.
Terminal
Description
MO+
Monitored Output positive connection
MO-
Monitored Output 0V connection
SCRN
Field cable screen connection
Auxiliary Power: +24V, 0V, SCRN
An auxiliary nominal 24V DC power supply is available to power ancillary devices requiring up to 30V DC.
The maximum output current is 200mA. The Auxiliary Power is protected by a F315mA fuse labelled FUSE
3. It is suggested that additional Power Supply Units be installed to provide power for additional loads.
Note: The auxiliary nominal 24V power supply output will be approximately 30 – 31V DC when the
panel is running from a mains supply and between 20 and 27V DC when running from the batteries
in a mains failure condition. Please ensure that the equipment to be powered from this output is
capable of operating from between 19V and 32V DC.
Terminal
Description
+24V
Aux power positive connection
0V
Aux Power 0V connection
SCRN
Field cable screen connection
MO-
MO+
SCRN
ON BOARD PCB
FIELD CONNECTIONS
+
-
+
-
10K EOL
SCREEN
SCREEN
OV
+24V
SCRN
ON BOARD PCB
FIELD CONNECTIONS
SCREEN
DC LOAD

Quadnet Control Panel Engineering and Commissioning Manual
19
Inputs 1- 4: MI+, MI-, SCRN
Inputs 1-4 may be configured to monitor for open and short circuit faults using a 3k3 EOL resistor, and to
activate an alarm link using a 680R ‘firing’ resistor.
Terminal
Description
MI+
Monitored Input positive connection
MI-
Monitored Input 0V connection
SCRN
Field cable screen connection
Fuses 1-3: FUSE 1, FUSE 2, FUSE 3
The fuses are located towards the top of the back plane PCB.
Blown fuses are easy to spot using the LED adjacent to each fuse. This will switch on if the output is
switched on (even in the passive state) and the fuse is blown.
Label
Description
Fuse
FUSE 1
Output 5
F315 mA
FUSE 2
Output 6
F315 mA
FUSE 3
Auxiliary Power
F315 mA
Addressable Circuit Loops 1- 4: END1+, END 1-, SCRN, END2+, END2-, SCRN
Each loop 1-4 addressable circuits must be connected to its
appropriate End 1 and End 2 terminals.
Communications normally run from Loop End 1 but, in the event of
a continuity fault, both ends of the circuit will operate.
It is important that the cable screen is only connected at the control panel (using the SCRN terminal
provided, not at any earthing point), and that the screen continuity is maintained at all times. 4-core cable
must not be used as a loop ‘feed & return’ due to the possibility of data corruption.
Terminal
Description
LOOP END1+
Circuit End 1 positive connection:
+VE OUT
LOOP END 1 -
Circuit End 1 0V connection :
0V OUT
SCRN
Field cable screen connection:
SCRN OUT
LOOP END2+
Circuit End 2 positive connection:
+VE IN
LOOP END 2 -
Circuit End 2 0V connection :
OV IN
SCRN
Field cable screen connection:
SCRN IN
MI-
MI+
SCRN
ON BOARD PCB
FIELD CONNECTIONS
3K3 EOL
SCREEN
680R
N/O CONTACT
FIRE RESISTOR
END1-
END1+
SCRN
MAIN PCB
FIELD CONNECTIONS
SCREEN
END2+
END2-
SCRN
SCREEN

Quadnet Control Panel Engineering and Commissioning Manual
20
USB Port: USB
The Quadnet control panel may be programmed using the Quadnet OSP programming software using a
USB lead to link to a computer. This allows the site specific data to be customised as required.
NOTE: It is imperative that the correct version of OSP is used to match your version of Quadnet
control panel. The use of an incompatible version may result in incorrect operation of the
control panel. In particular, do not use a V2.xx series OSP with a V3.xx series control
panel and do not use a V3.xx series OSP with a V2.xx series control panel.
Serial Port: SERIAL
SW 1
ON
The Quadnet control panel firmware (control panel operating software stored in external flash memory on
the control panel CIE PCB) may be updated using the Quadnet Firmware programming software using a
serial lead to link to a computer. This allows the control panel software version to be updated on site as
required. To enable the flash upgrade option switch 1 must be in the ON position. During normal operation
switch 1 must be set to OFF.
It is important to ensure that the new version is compatible with your hardware version and with
other software used in the system such as loop cards, PSU and repeaters etc. If not, then all items
would need to be updated.
Note that firmware upgrades are only permitted to be carried out by Fike engineers or trained installation
engineers operating under specific instructions from Fike Technical Support.
Network Ports 1- 2: B, A, SCRN
The network ports allow multiple panels to be connected together, up to a maximum of 4panels (including
both control panels and repeater panels). The 2 network ports (NET1-2) may be connected in any
sequence between panels. Note Network ports 3 + 4 are not currently used.
Note that although the terminals for the network ports are always fitted on the backplane, they may only be
used if the optional Quadnet Network Card has been fitted onto the control panel main PCB (CIE).
Network Port 1
Terminal
Description
SCRN
Field cable screen connection (Connect only at 1 end)
NW1B
Data B connection for Port 1
NW1A
Data A connection for Port 1
NW1B
ON BOARD PCB
FIELD CONNECTIONS
TO NETWORK PORT OF NEXT CONTROL PANEL
NW1A
B
A
SCREEN
ON BOARD PCB
FIELD CONNECTIONS
USB
PC USB PORT
ON BOARD PCB
FIELD CONNECTIONS
SERIAL
PC SERIAL PORT
Other manuals for Quadnet
1
Table of contents
Other Fike Control Panel manuals
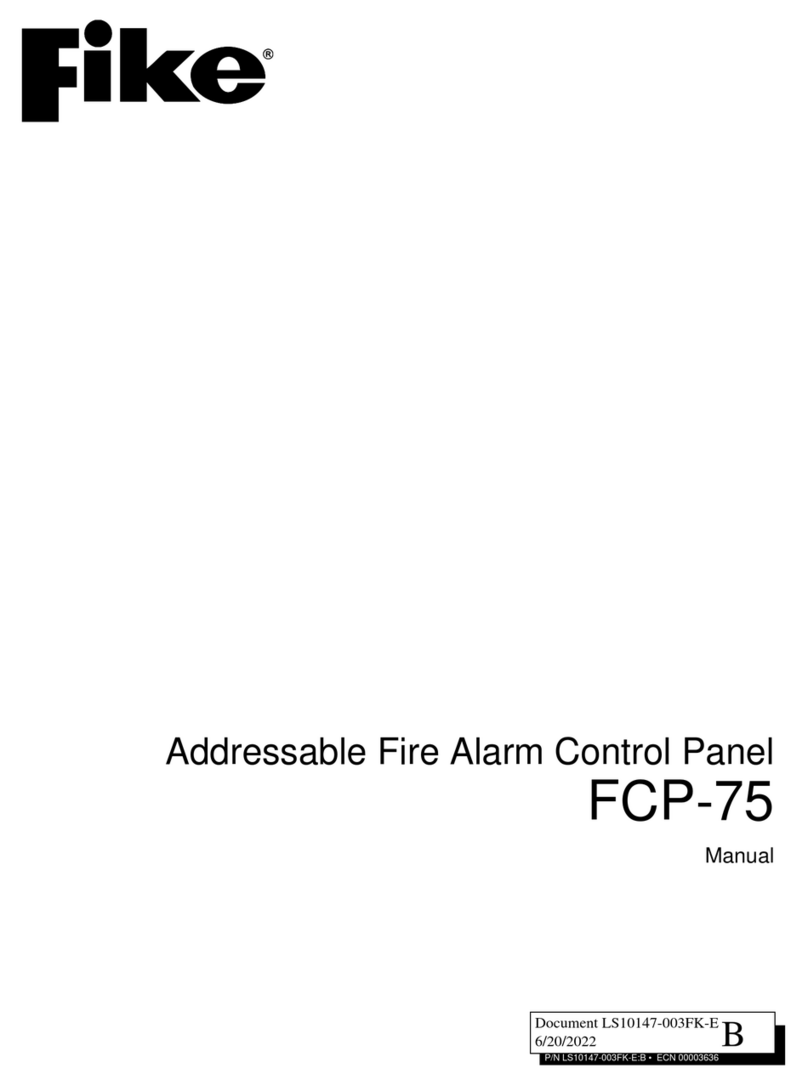
Fike
Fike FCP-75 User manual
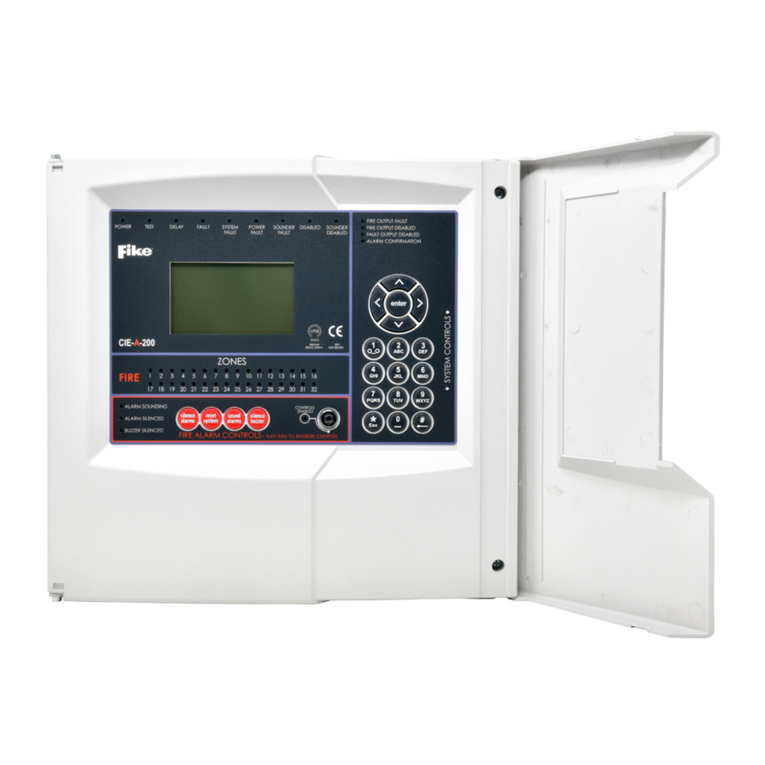
Fike
Fike CIE-A-200 User manual

Fike
Fike GB2426367 User manual
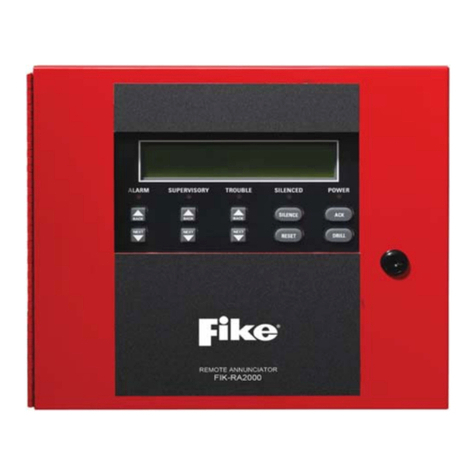
Fike
Fike FIK-RA2000 Technical manual
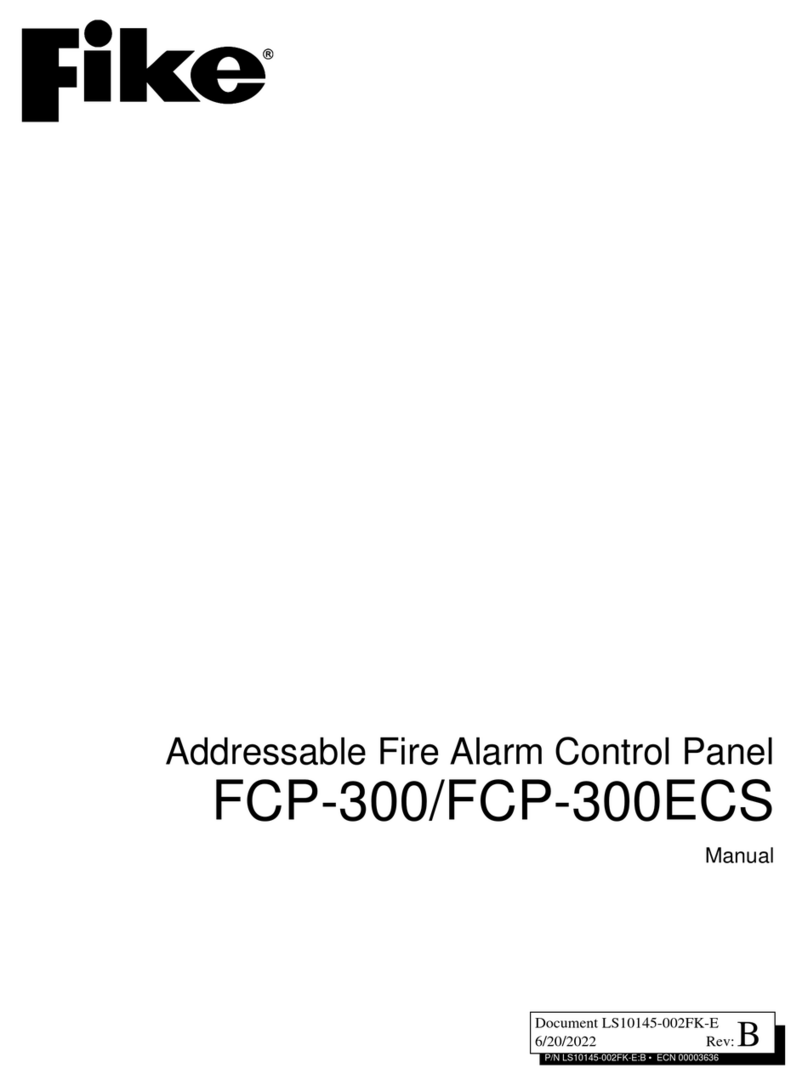
Fike
Fike FCP-300 User manual
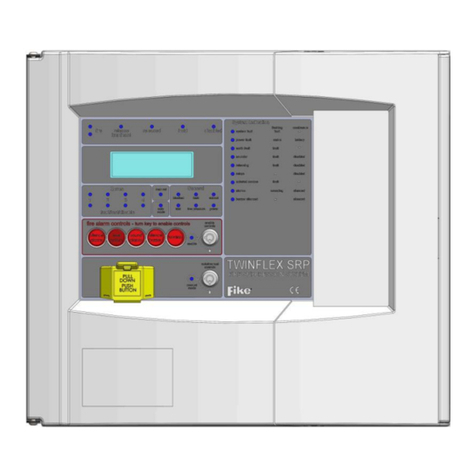
Fike
Fike TWINFLEX SRP 100-0001 User manual
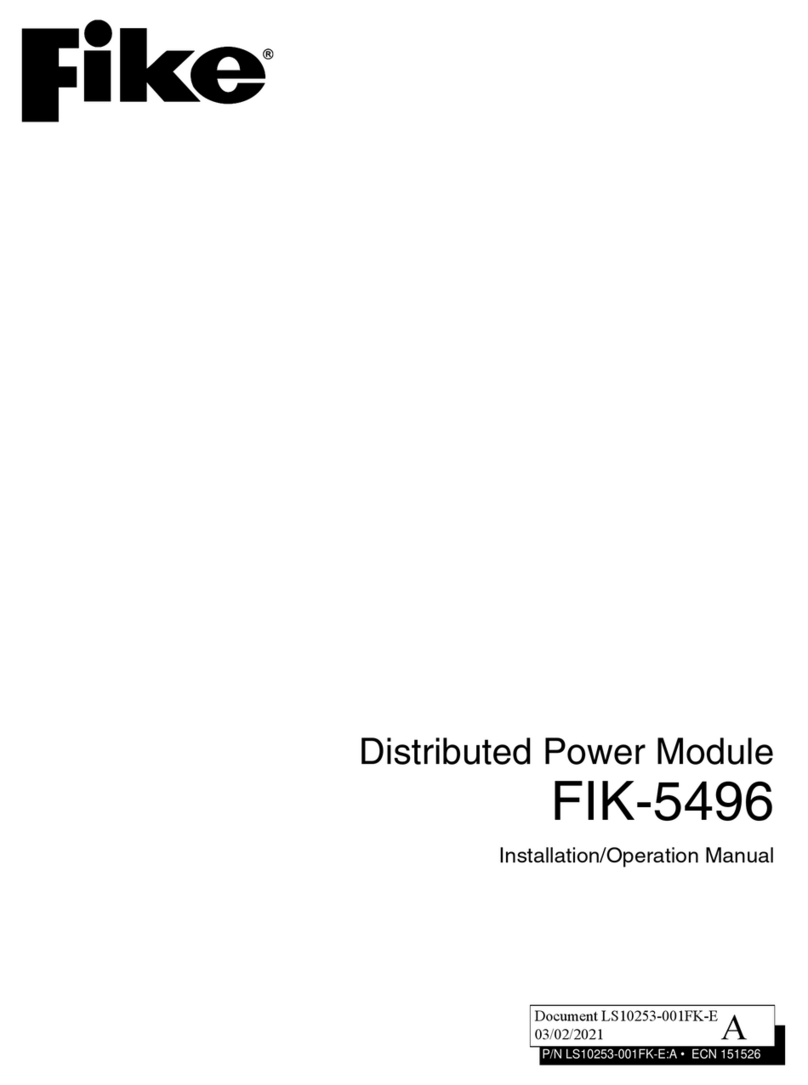
Fike
Fike FIK-5496 User manual
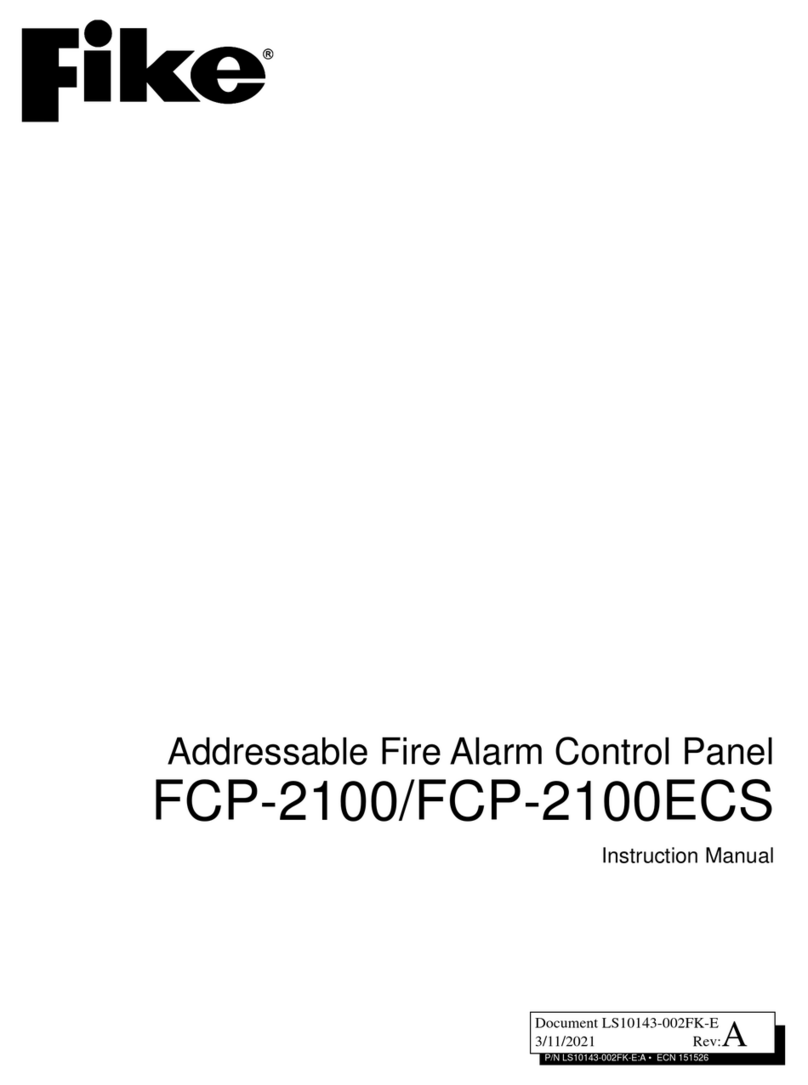
Fike
Fike FCP-2100 User manual

Fike
Fike SITA200plus User manual
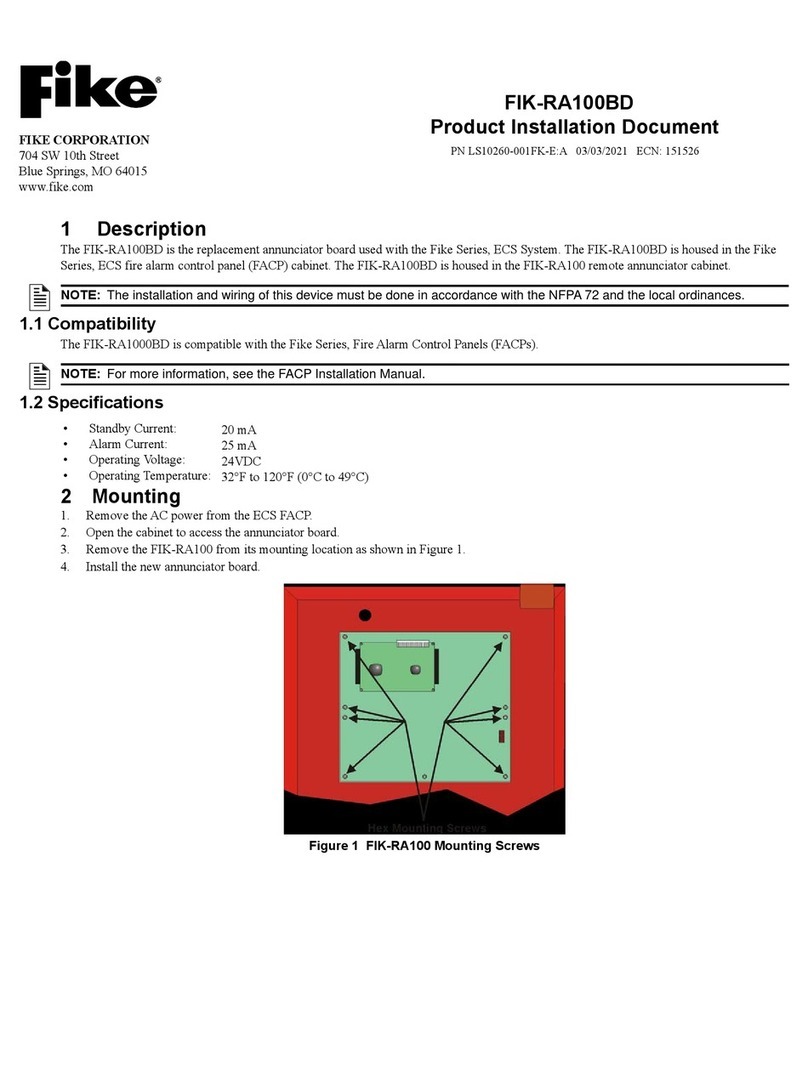
Fike
Fike FIK-RA100BD Technical manual