H3C BT1004E User manual

i
Contents
1 Safety ···················································································································································1-1
1.1 Safety Information·····························································································································1-1
1.1.1 General Operating Safety·······································································································1-1
1.1.2 Electrical Safety······················································································································1-1
1.2 Safety Precautions····························································································································1-1
1.3 ESD Prevention·································································································································1-1
1.3.1 Preventing Electrostatic Discharge ························································································1-1
1.3.2 Grounding Methods to Prevent Electrostatic Discharge ························································1-2
2 Overview of the BT1004E Ethernet Cascading Module······································································2-1
Product Overview····································································································································2-1
2.2 Specifications····································································································································2-2
2.3 Port····················································································································································2-2
2.3.1 Port Description······················································································································2-2
2.3.2 Port Numbering Rules············································································································2-3
2.4 Indicators···········································································································································2-4
2.5 Internal Connection···························································································································2-6
2.5.1 Connections Between Cascading Modules and Mezz NICs of the Blade Server··················2-6
2.5.2 Connections Between Cascading Modules and Mezz NIC Ports of the Blade Server ··········2-8
2.5.3 Connections Between Cascading Module Ports and Blade Servers·····································2-8
2.6 Logical Structure·····························································································································2-13
2.7 Installation Guidelines·····················································································································2-14
3 Hardware Compatibility························································································································3-1
3.1 Compatibility Between Cascading Modules and Mezz NICs····························································3-1
3.2 Compatibility Between Cascading Modules and Optical Modules····················································3-1
3.3 External Networking Connection·······································································································3-2
4 Replacing the Cascading Module········································································································4-1
4.1 Scenario············································································································································4-1
4.2 Installation Tools·······························································································································4-1
4.3 Preparations······································································································································4-2
4.4 Replacement Procedure ···················································································································4-2
5 Powering On and Powering Off············································································································5-1
5.1 Powering On the Straight-Through Module ······················································································5-1

ii
5.2 Powering Off the Straight-Through Module ······················································································5-1
6 Checking the Cascading Module·········································································································6-1
6.1 Checking the State of the Cascading Module Port Through OM······················································6-1
6.1.2 Viewing through the OM CLI ··································································································6-2
7 Configuring the Cascading Module······································································································7-1
7.1 Port Rate Switching···························································································································7-1
7.1.1 Changing Through the OM Web UI························································································7-1
7.1.2 Changing Through the OM CLI······························································································7-1
7.2 Common Operations·························································································································7-2
7.2.1 Logging into the OM Web·······································································································7-2
7.2.2 Logging In to the CLI of OM Module ······················································································7-4
8 Firmware Upgrade································································································································8-1

1-1
1 Safety
1.1 Safety Information
To avoid personal injury or damage to the device, read the following information carefully before
you operate the device. Safety precautions in actual operation include but are not limited to safety
information mentioned in this document.
1.1.1 General Operating Safety
•
Only H3C authorized or professional engineers are allowed to operate the device.
•
Keep the device clean and dust-free. Do not place it in a humid place or allow liquids to enter
it.
•
Before powering on the device, ensure that the blade enclosure is securely grounded.
•
To maintain sufficient heat dissipation, use filler panels on idle slots.
1.1.2 Electrical Safety
•
Carefully check any potential hazards in the work area, for example, whether the ground is
wet and whether the blade enclosure is grounded or reliably grounded.
•
Do not work alone when performing live-line maintenance.
•
Do not touch the power supply directly or indirectly through conductive objects to prevent
electric shock.
1.2 Safety Precautions
•
When maintaining the device, place the device on a clean, stable table or floor.
•
To avoid personal injury from hot surfaces or internal components, allow the device and its
internal components to cool before touching them.
•
When using tools to maintain the device, follow the correct operation methods to avoid
damage to the personnel or device.
•
When connecting, testing or replacing optical fibers, do not look directly into the optical fiber
outlet to prevent the laser beam from hurting your eyes.
•
Gently and slowly transport or place the device with force evenly distributed.
1.3 ESD Prevention
1.3.1 Preventing Electrostatic Discharge
Electrostatic charges that build up on people and conductorsdamage or shorten the lifespan of the
main board and electrostatic-sensitive components.
To prevent electrostatic damage, follow these guidelines:

1-2
•
Transport or store the device in an ESD bag.
•
Place the device on a grounded table before taking it out of the ESD bag.
•
Avoid touching pins or circuitry of the device without taking any ESD prevention measures.
1.3.2 Grounding Methods to Prevent Electrostatic Discharge
When removing or installing the device, you can use one or multiple of the following grounding
methods to prevent electrostatic discharge:
•
Wear an ESD wrist strap and ensure that it is reliably grounded. Ensure that the ESD wrist
strap makes good skin contact and can be flexibly stretched out and draw back.
•
In the work areas, wear the ESD clothing and shoes.
•
Use conductive field service tools.
•
Use a portable field service kit with a folding ESD tool mat.

2-1
2 Overview of the BT1004E Ethernet Cascading
Module
Note
•Hardware images shown in this manual are for illustration purposes only. The actual product
may vary.
•The software UI may be updated from time to time. Please refer to the actual product UI.
•ICMs supported by the chassis are classified into switching modules and straight-through
modules (also known as cascading modules in some manuals). BT1004E is a type of
cascading module. The ICM module, straight-through module, and cascading module
mentioned in this document refer to the BT1004E Ethernet cascading module.
Product Overview
H3C UniServer BT1004E is an Ethernet cascading module for the H3C UniServer B16000 blade
chassis (4*(4*25 GE)). It provides an external data interface, which enables direct connection of
parallel cables to the Ethernet Mezz NIC port of the blade server. BT1004E is applicable to the
high-density scale-out networking solution for B16000. By cascading to ToR switches, BT1004E
provides unified multi-frame deployment management. For details, see Deployment Guide for the
H3C UniServer B16000 High-density Scale-out Networking.
Note
Unlike switching modules, cascading modules only transmit data between blade servers and
external networks without the need to process the data.
•The cascading module has four QSFP28 ports, each of which can be split into four logical
ports. The port speed is 10 Gb or 25 Gb, which can be switched through the OM management
software.
Figure 2-1 shows the appearance of the BT1004E.

2-2
Figure 2-1 Appearance of BT716F
2.2 Specifications
Table 2-1 describes the specifications of the cascading module.
Table 2-1 Specifications
Category Item Description
Physical
specifications
Dimensions
(H × W × D) 27 mm x 491.6 mm x 296.5 mm
Maximum weight 3.32 kg
Power
consumption Maximum power
consumption 25 W
Environment
specifications
Temperature •Operating temperature: 5°C to 45°C
•Storage temperature: -40°C to 70°C
Humidity •Operating humidity: 8% to 90% (non-condensing)
•Storage humidity: 5% to 95% (non-condensing)
Altitude
•Operating altitude: -60 m to +5000 m (The allowed maximum
temperature decreases by 0.33 °C as the altitude increases by 100
m from 900 m)
•Storage altitude: –60 m to +5000 m
2.3 Port
This section describes positions, quantity, numbering rules about the ports of the cascading
module and the mapping between these ports and slots of blade servers.
2.3.1 Port Description
Figure 2-3 shows the external ports provided by the cascading module. Table 2-2 describes
specific functions of the external ports.
Figure 2-2 External ports

2-3
(1): AMC serial port
(2): 4*25 GE optical ports
Table 2-2 Description of external ports
SN Port
Name Type Quantity Port
No. Description
1 AMC
serial port RJ-45 1 -
Serial port used to enter
the AMC CLI. The baud
rate is 115200 bit/s. It is
only used by technical
support engineers to
display the states of the
optical ports and to
perform subsequent
maintenance.
2
4*25
GE
optical
ports
QSF
P28 4
Four physical
ports ranging
from 1 to 4.
16 logical
ports ranging
from 1 to 16.
•Each QSFP28 port can be split into four logical ports. Four
QSFP28 ports can be split into 16 logical ports ranging from 1
to 16. The port speed is 10 Gb or 25 Gb, which can be
switched through the OM management software.
•For the mapping between the cascading module ports and the
blade servers, see 2.5.3 Connections Between Cascading
Module Ports and Blade Servers.
•For the optical modules supported by each port, see 3.2
Compatibility Between Cascading Modules and Optical
Modules.
For the method of changing port rate, see 7.1 Port Rate Switching.
2.3.2 Port Numbering Rules
As shown in Figure 2-3, the numbering rules for the cascading module ports are defined as "A/B/C"
on the OM Web page.

2-4
•
A: Defaults to 1; cannot be edited.
•
B: Indicates an internal or external port. 0 indicates an internal port, and 1 indicates an
external port. The cascadingmodule does not have an internal port, so this item number is 1.
•
C: Indicates the sequence number of the cascading module ports. Every four ports constitute
a group, which corresponds to one external QSFP28 port.
Figure 2-3 Port Numbering Rules
2.4 Indicators
Table 2-3 shows information relating to indicators on the cascading module.

2-5
Figure 2-4 Indicators
The 16 logical ports of the cascading module correspond to 16 service port indicators. The service port indicator
whose silkscreen is 1 corresponds to Port 1 and the service port indicator whose silkscreen is 2 corresponds to
Port 2, and so on. The appearance and meaning of 16 indicators are identical. The figure takes one port
indicator for illustration.
Table 2-3 Description of indicators
SN Name Color Status
1 UID indicator Blue
•Steady on blue: The UID indicator is activated (through the OM
module).
•Off: The UID indicator is not activated.
2 RUN indicator
(RUN) Green
•Steady on green/off: The system is faulty.
•Blinking green (at a frequency of 4 Hz): The system is loading
data.
•Blinking green (at a frequency of 1 Hz): The system is running
normally.
3 Health indicator
( ) Red/Gre
en
•Steady on green: The cascading module is running normally.
•Blinking red (1 Hz): The cascading module generates an
alarm.
•Off: The cascading module is not powered on or in position.
4 Service port 1
indicator Yellow/G
reen
•Steady on green: The high-speed port link is connected, but no
data is received and sent.
•Blinking green (1 Hz): The high-speed port link is connected,
and data is being received or sent.
•Steady on yellow: The low-speed port linkis connected, but no
data is received and sent.

2-6
SN Name Color Status
•
Blinking yellow (1 Hz): The low-speed port link is connected,
and data is being received or sent.
•Off: The port link is not connected.
2.5 Internal Connection
To ensure access to the target blade server through the external ports of the cascading module,
the user needs to obtain the following information:
•
Slots where the cascading module or Mezz NICs should be placed before installing the
cascading module or Mezz NICs of the blade server. For details, see 2.5.1 Connections
Between Cascading Modules and Mezz NICs of the Blade Server;
•
Mapping between Mezz NIC ports and the cascading module before configuring Mezz NICs
of the blade server. For details, see 2.5.2 Connections Between Cascading Modules and
Mezz NIC Ports of the Blade Server;
•
Connection between the cascading module ports and the target blade server before
accessing the blade server through the cascading module. For details, see 2.5.3
Connections Between Cascading Module Ports and Blade Servers.
2.5.1 Connections Between Cascading Modules and Mezz NICs of the Blade Server
Table 2-4 describes connections between cascading modules and Mezz NICs, helping you
accurately choose slots for installing the cascading modules.
Table 2-4 Connections between cascading modules and Mezz NICs of the blade server
Model of Blade Server Maximum Number of
Supported Mezz NICs Connections between cascading modules and
Mezz NICs of the blade server
H3C UniServer B5700 G5 3 See 2.5.1 1. Mode 1.
H3C UniServer B5700 G3 3 See 2.5.1 1. Mode 1.
H3C UniServer B7800 G3 6 See 2.5.1 2. Mode 2.
H3C UniServer B5800 G3 3 See 2.5.1 1. Mode 1.
1. Mode 1
For blade servers that support up to three Mezz NICs, the connections between cascading
modules and Mezz NICs of the blade server are shown in Figure 2-5. Where:
•
The onboard NIC is connected to the active and standby OM modules.
•
Mezz NIC 1 is connected to cascading modules in slot 1 and slot 4.
•
Mezz NIC 2 is connected to cascading modules in slot 2 and slot 5.
•
Mezz NIC 3 is connected to cascading modules in slot 3 and slot 6.

2-7
Figure 2-5 Connections between cascading modules and Mezz NICs of the blade server
enclosure (1)
2. Mode 2
For blade servers that support up to six Mezz NICs, the connections between cascading modules
and Mezz NICs of the blade server are shown in Figure 2-6. Where:
•
The onboard NIC is connected to the active and standby OM modules.
•
Mezz NIC 1 and Mezz NIC 4 are connected to cascading modules in slot 1 and slot 4.
•
Mezz NIC 2 and Mezz NIC 5 are connected to cascading modules in slot 2 and slot 5.
•
Mezz NIC 3 and Mezz NIC 6 are connected to cascading modules in slot 3 and slot 6.
Mezz1
Mezz2
Mezz3
12
LOM P1
LOM P2
2
3
1
6
5
4
Blade ICM
Mid-plane
Embedded
OM

2-8
Figure 2-6 Connections between cascading modules and Mezz NICs of the blade server
enclosure (2)
2.5.2 Connections Between Cascading Modules and Mezz NIC Ports of the Blade Server
For connections between cascading modules and Mezz NIC ports, check through the Networking
query tool.
2.5.3 Connections Between Cascading Module Ports and Blade Servers
Table 2-5 shows the connections between external ports of cascading modules and blade servers.
Table 2-5 Connections between external ports of cascading modules and blade servers
Model of Blade Server Maximum Number of
Supported Mezz NICs Connections between external ports of
cascading modules and blade servers
Half-width single-height blade
server 3 See 2.5.3 1. Connections between external
ports of cascading modules and half-width
single height blade servers.
Full-width single-height blade
server 6
For details, see 2.5.3 2. Connections
between external ports of cascading
modules and full-width single height blade
servers (supporting up to six Mezz NICs).
3 For details, see 2.5.3 3. Connections
Mezz1
Mezz2
Mezz3
Mezz4
Mezz5
Mezz6
1
4
2
3
5
6
12
LOM P1
LOM P2
Blade ICM
Mid-plane
OM
Embedded

2-9
Model of Blade Server Maximum Number of
Supported Mezz NICs Connections between external ports of
cascading modules and blade servers
between external ports of cascading
modules and full-width single height blade
servers (supporting up to three Mezz NICs).
When the full-width single height blade server and the half-width single height blade server exist together in the
same enclosure, check the external ports of cascading modules according to the type of the blade server
configured for each slot.
1. Connections between external ports of cascading modules and half-width single height blade
servers
Figure 2-3 shows ports on the panel of the cascading module. Four QSFP28 ports can provide 16
ports ranging from 1 to 16. Figure 2-7 shows the 16 slots of the half-width single-height blade
server installed in the front slots of the blade server chassis. The slots are numbered 1 to 16.
Figure 2-7 Numbering of slots for the half-width single-height blade server
As shown in Figure 2-8, when the half-width single height blade servers are configured in the front
of the enclosure, the external ports of the cascading module correspond to the 16 blade servers
respectively. Specifically, Port 1 is connected to the blade server 1, which allows users to access
the blade server 1 through Port 1. Port 2 is connected to the blade server 2, which allows users to
access the blade server 2 through Port 2, and so on.
Note
•For the connections between cascading modules and Mezz NICs of the blade server, see
2.5.1 Connections Between Cascading Modules and Mezz NICs of the Blade Server.

2-10
•For the specific Mezz NIC port on the blade server connected to the cascadingmodule, check
through the Networking query tool.
Figure 2-8 Logical diagram for connections between external ports of cascading modules and
half-width single height blade servers
2. Connections between external ports of cascading modules and full-width single height blade
servers (supporting up to six Mezz NICs)
Figure 2-3 shows ports on the panel of the cascading module. Four QSFP28 ports can provide 16
ports ranging from 1 to 16. Figure 2-9 shows the slots for the 8 full-width single-height blade
servers installed in the front slots of the blade server chassis. They are numbered 1, 3, 5, 7, 9, 11,
13, and 15.
ICM
Front
Port 4
Port 16
Port 15
Port 14
Port 13
Blade1
Blade3
Blade2
Blade4
Blade13
Blade15
Blade14
Blade16
……
Mid-plane Enclosure
……
……
Port 3
Port 2
Port 1
QSFP28-1
QSFP28-4

2-11
Figure 2-9 Numbering of slots for the full-width single-height blade server
As shown in Figure 2-10, when the full-width single height blade servers (supporting up to six Mezz
NICs) are configured in the front of the enclosure, every two external ports of the cascading
module correspond to one full-width single height blade server. Specifically, Port 1 and Port 2 are
connected to the blade server 1, which allows users to access the blade server 1 through Port 1 or
Port 2. Port 3 and Port 4 are connected to the blade server 3, which allows users to access the
blade server 3 through Port 3 or Port 4, and so on.
Note
•For the connections between cascading modules and Mezz NICs of the blade server, see
2.5.1 Connections Between Cascading Modules and Mezz NICs of the Blade Server.
For the specific Mezz NIC port on the blade server connected to the cascading module, check
through the Networking query tool.

2-12
Figure 2-10 Logical diagram for connections between external ports of cascading modules and
full-width single height blade servers (supporting up to six Mezz NICs)
3. Connections between external ports of cascading modules and full-width single height blade
servers (supporting up to three Mezz NICs)
Figure 2-3 shows ports on the panel of the cascading module. Four QSFP28 ports can provide 16
ports ranging from 1 to 16. Figure 2-9 shows the slots for the 8 full-width single-height blade
servers installed in the front slots of the blade server chassis. They are numbered 1, 3, 5, 7, 9, 11,
13, and 15.
When the full-width single-height blade server that supports up to 3 Mezz NICs is installed in the
front slots of the chassis:
•
As shown in Figure 2-11, cascading modules in slots 1, 3, 4, and 6 are connected to blade
servers through odd-numbered ports. Specifically, Port 1 is connected to the blade server 1,
which allows users to access the blade server 1 through Port 1. Port 3 is connected to the
blade server 3, which allows users to access the blade server 3 through Port 3, and so on.
•
As shown in Figure 2-12, cascading modules in slots 2 and 5 are connected to blade servers
through even-numbered ports. Specifically, Port 2 is connected to the blade server 1, which
allows users to access the blade server 1 through Port 2. Port 4 is connected to the blade
server 3, which allows users to access the blade server 3 through Port 4, and so on.
Note
•For the connections between cascading modules and Mezz NICs of the blade server, see
2.5.1 Connections Between Cascading Modules and Mezz NICs of the Blade Server.
•For the specific Mezz NIC port on the blade server connected to the cascadingmodule, check
through the Networking query tool.
ICM
Front
Port 4
Port 3
Port 2
Port 1
……
Blade1
Blade3
Blade13
Blade15
……
Mid-plane Enclosure
Port 16
Port 15
Port 14
Port 13
QSFP28-1
QSFP28-4

2-13
Figure 2-11 Logical diagram for connections between external ports of cascading modules in slots
1, 3, 4, and 6 and full-width single height blade servers (supporting up to three Mezz NICs)
Figure 2-12 Logical diagram for connections between external ports of cascading modules in slots
2 and 5 and full-width single height blade servers (supporting up to three Mezz NICs)
2.6 Logical Structure
Figure 2-13 shows two modules in the logical structure of the cascading module.
•
AMC unit:As the management unit of the cascading module, theAMC unit is mainly
responsible for board data collection and reporting, board power-on/off control, and system
monitoring.
•
PHY unit: As the data transmission unit of the cascading module, the PHY unit provides a
connection channel between the NIC ports of the blade server and the external ports of the
ICM 1/3/4/6
Front
……
Blade1
Blade3
Blade13
Blade15
……
Mid-plane Enclosure
Port 4
Port 3
Port 2
Port 1
Port 16
Port 15
Port 14
Port 13
QSFP28-1
QSFP28-4
ICM 2/5
Front
……
Blade1
Blade3
Blade13
Blade15
……
Mid-plane Enclosure
Port 4
Port 3
Port 2
Port 1
Port 16
Port 15
Port 14
Port 13
QSFP28-1
QSFP28-4

2-14
cascadingmodule to implementtransparent transmission between theNIC ports of the blade
server and the external network.
Figure 2-13 Logical structure
2.7 Installation Guidelines
•
As shown in Figure 2-14, up to six cascading modules can be installed in the blade enclosure.
The slots to install those modules are ICM1 – ICM6.
•
The cascading module supports hot swapping.
•
Figure 2-5 and Figure 2-6 describe connections between cascading modules and Mezz NICs,
helping you accurately choose slots for installing the cascading modules.
2*PHY
AMC
Mid-plan
ICM
2*GE
...
4*(4*25GE)
...
16*25GE
RJ45

2-15
Figure 2-14 Guidelines for installing the cascading module
(1): ICM1 slot
(2): ICM2 slot
(3): ICM3 slot
(4): ICM4 slot
(5): ICM5 slot
(6): ICM6 slot

3-1
3 Hardware Compatibility
This section describes the compatibility between cascading modules and Mezz NICs and the
compatibility between cascading modules and optical modules.
3.1 Compatibility Between Cascading Modules and Mezz NICs
Table 3-1 describes the compatibility between the cascading module and the Mezz NIC.
Table 3-1 Mezz NIC compatible with BT1004E
Mezz NIC Model Port Quantity Description
NIC-ETH522i-Mb-2*10G 2 2-Port 10Gb CNA Mezz NIC
NIC-ETH640i-Mb-2*25G 2 2-Port 25Gb Ethernet Mezz NIC
NIC-ETH681i-Mb-2*25G 2 2-Port 25Gb Ethernet Mezz NIC
NIC-ETH682i-Mb-2*25G 2 2-Port 25Gb CNA Mezz NIC
3.2 Compatibility Between Cascading Modules and Optical Modules
Table 3-2 describes the compatibility between the cascading module and the optical module.
Table 3-2 Optical modules/cables compatible with BT1004E
Module/
Cable Type Module/Cable Name Center
Wavelength
Module
Port
Connector
Type
Cable
Specifications
Maximum
Transmission
Distance
QSFP+
optical
module
QSFP-40G-SR4-MM850-C
M
850 nm MPO
50/125µm
multi-mode fiber 150 m
QSFP-40G-SR4-MM850 50/125µm
multi-mode fiber 150 m
QSFP-40G-CSR4-MM850-
CM 50/125µm
multi-mode fiber 400 m
QSFP-40G-CSR4-MM850 50/125µm
multi-mode fiber 400 m
QSFP28
optical
module
QSFP-100G-SR4-MM850-
CM 850 nm MPO
50/125µm
multi-mode fiber 100 m
QSFP-100G-SR4-MM850 50/125µm
multi-mode fiber 100 m
QSFP+ cable QSFP-40G-3M-CM - - QSFP+ cable 3 m
QSFP-40G-5M-CM 5 m
QSFP+
optical cable QSFP-40G-D-AOC-7M-C
M - - QSFP+ optical cable 7 m
QSFP-40G-D-AOC-7M 7 m
Table of contents
Other H3C Computer Hardware manuals
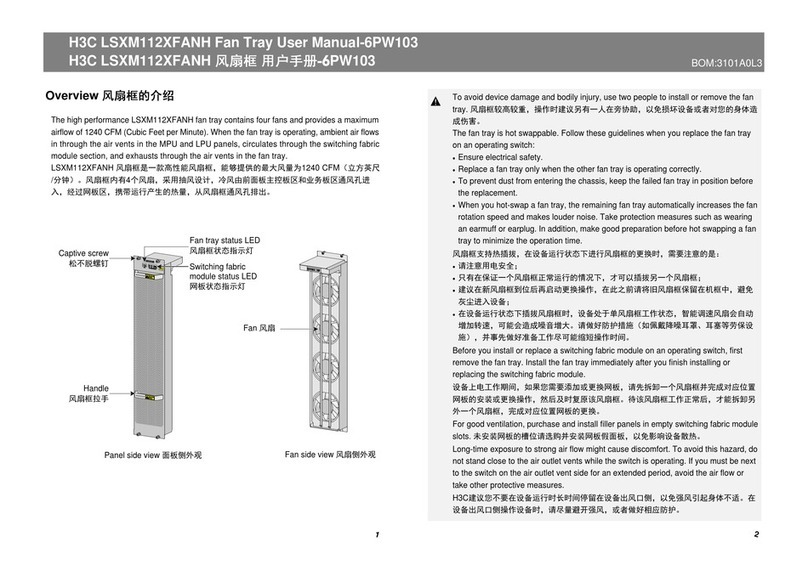
H3C
H3C LSXM112XFANH User manual
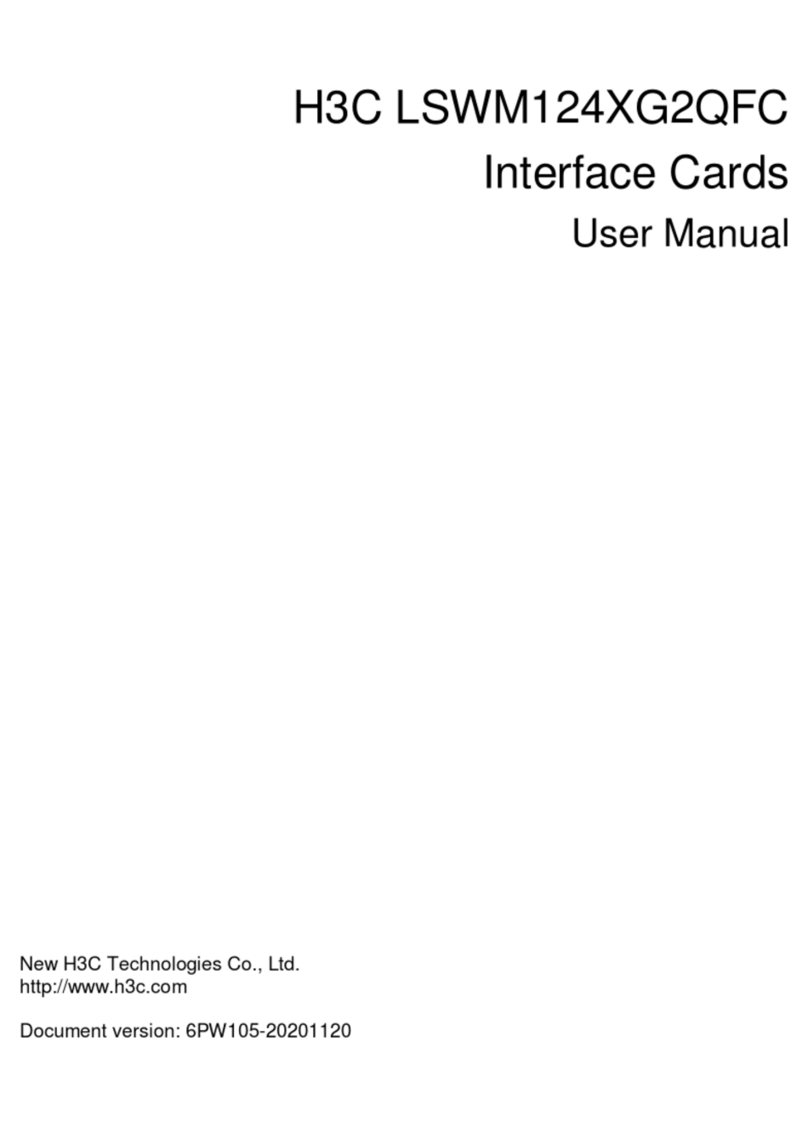
H3C
H3C LSWM124XG2QFC User manual
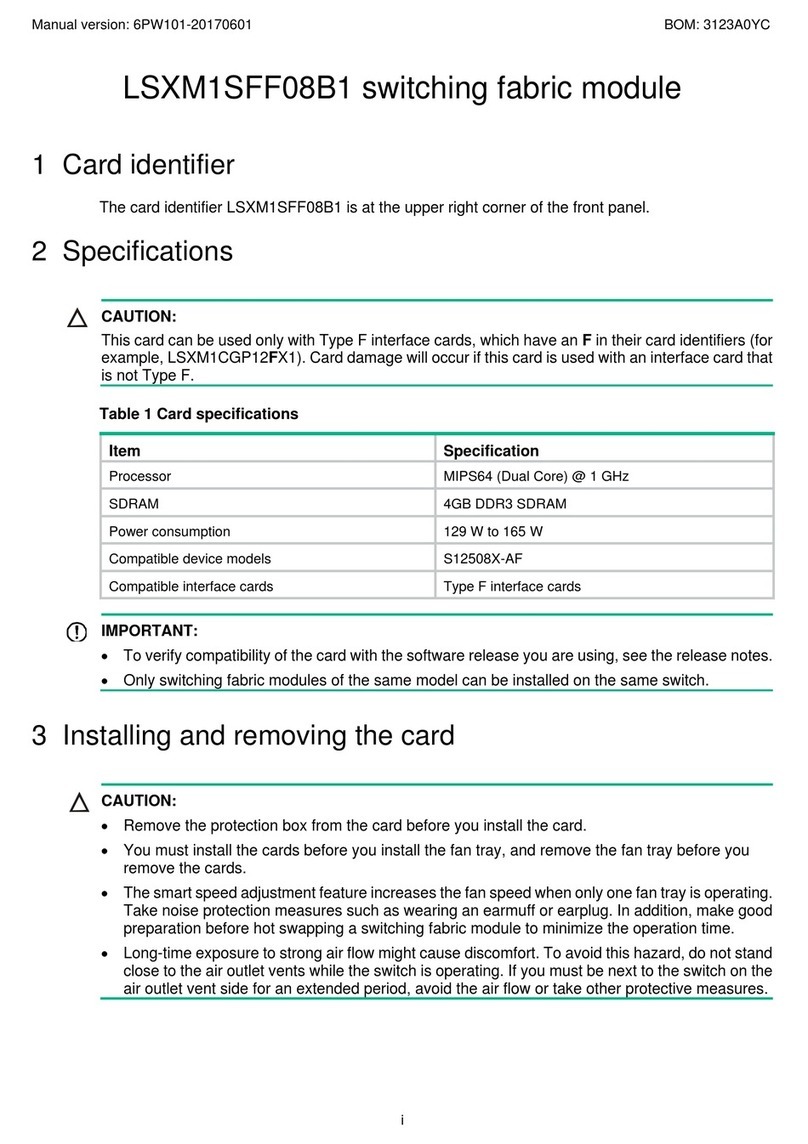
H3C
H3C LSXM1SFF08B1 Instruction Manual
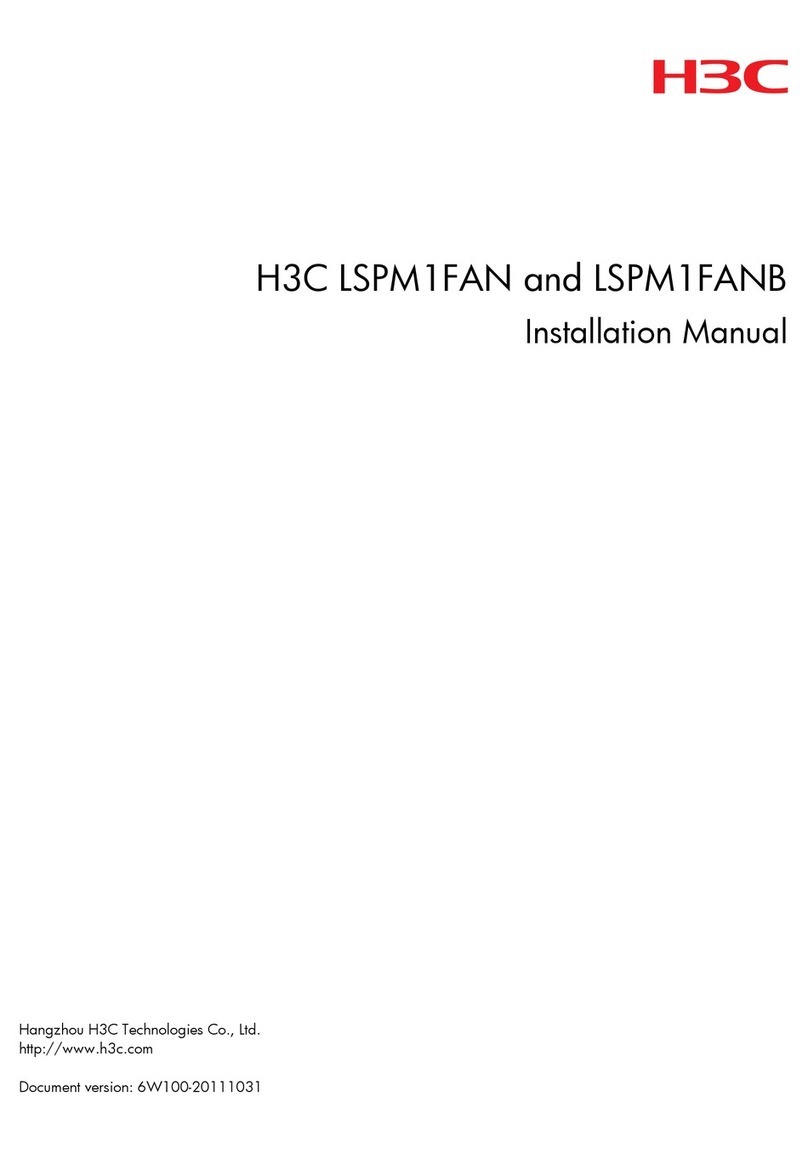
H3C
H3C LSPM1FAN User manual

H3C
H3C H3C S7500E-X User manual
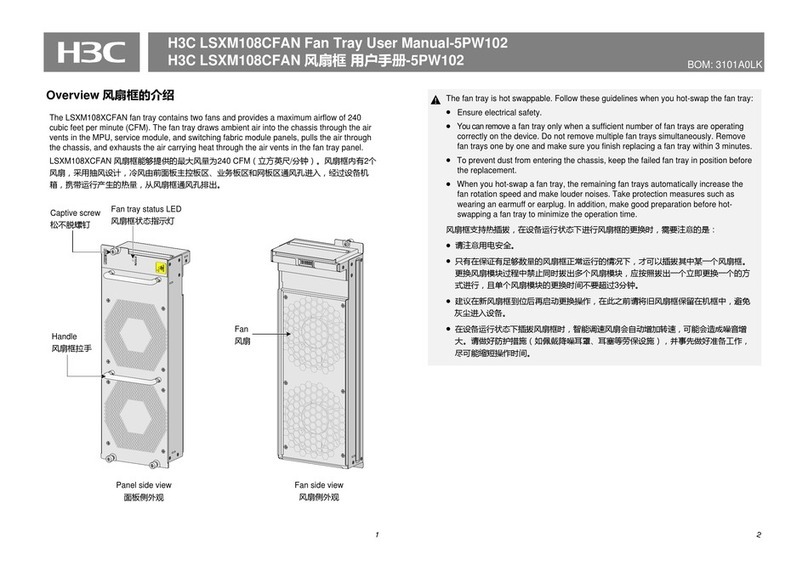
H3C
H3C LSXM108CFAN User manual
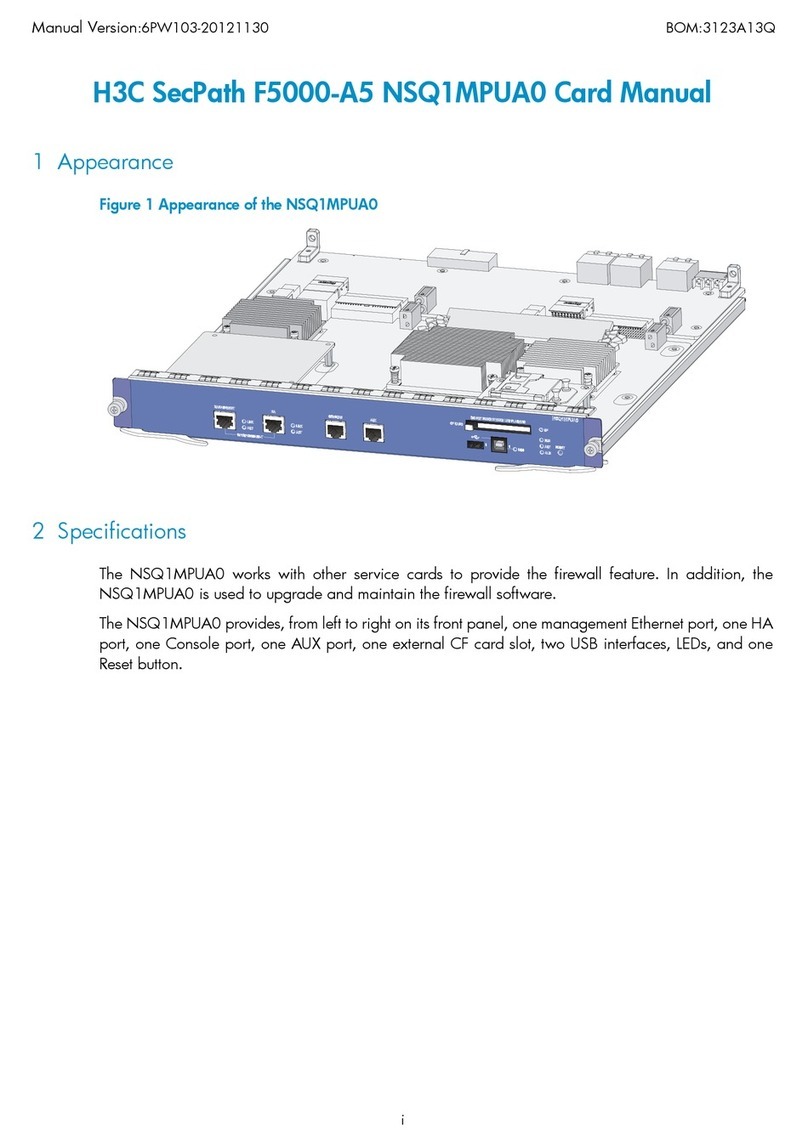
H3C
H3C SecPath F5000-A5 NSQ1MPUA0 User manual
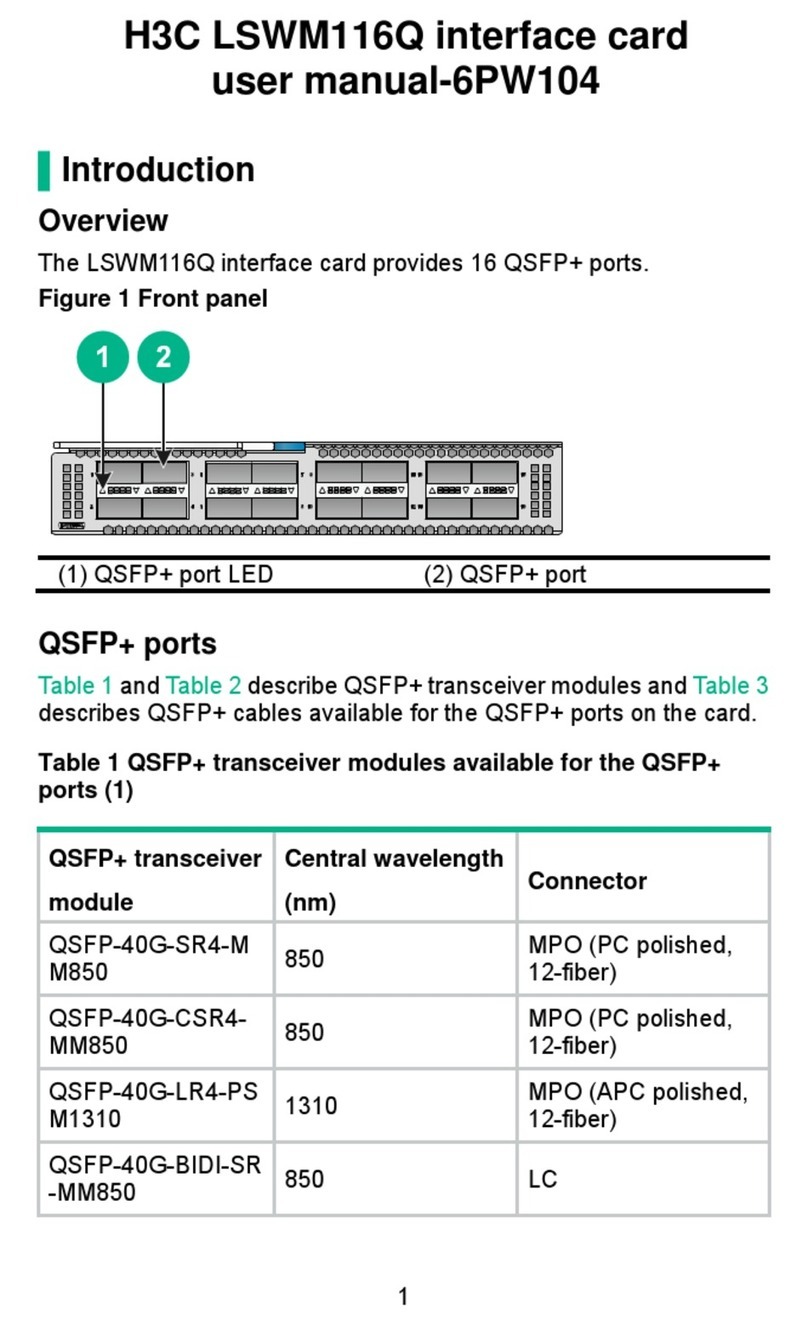
H3C
H3C LSWM116Q User manual

H3C
H3C LSVM1FANSC User manual
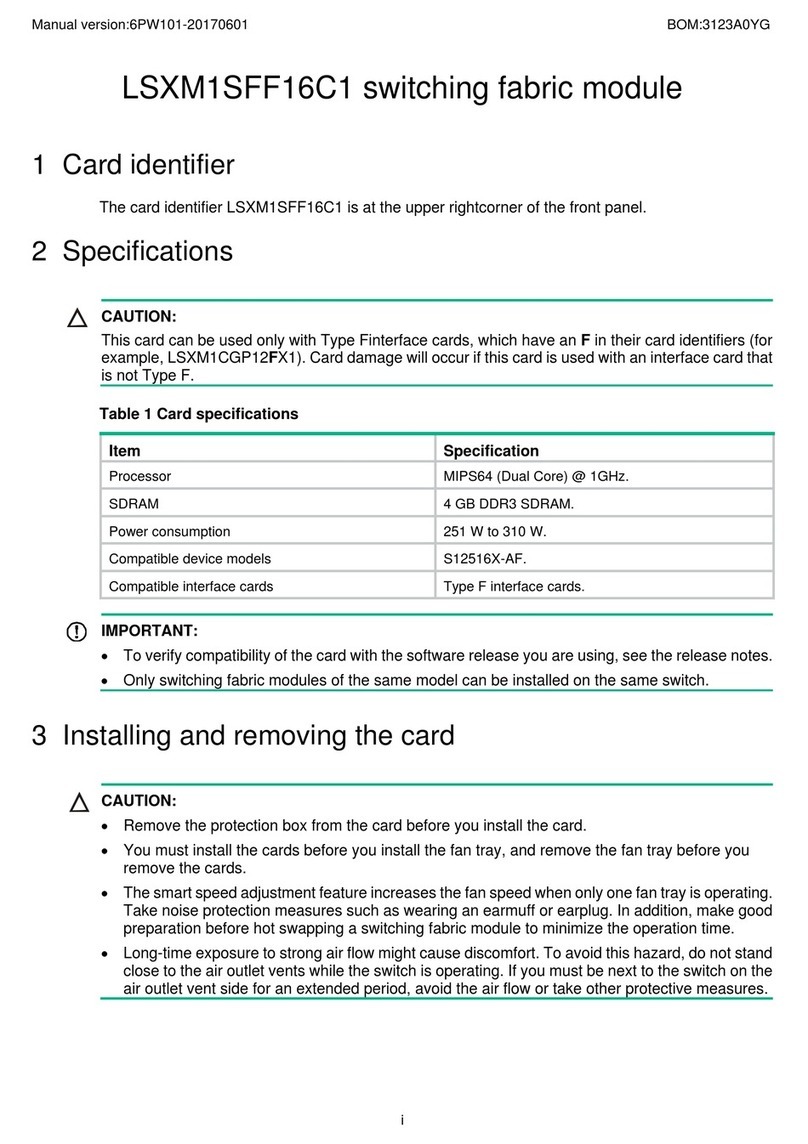
H3C
H3C LSXM1SFF16C1 Instruction Manual