Hunter TC39 Series User manual

Copyright 2018 Hunter Engineering Company
OPERATION INSTRUCTIONS 7108-M010-3_H Rev. 3 (02/2020)
TC39 Series Tire Changer

OWNER INFORMATION
Model Number _____________________________________________________________________
Serial Number _____________________________________________________________________
Date Installed______________________________________________________________________
Service and Parts Representative ______________________________________________________
Phone Number_____________________________________________________________________
Sales Representative________________________________________________________________
Phone Number_____________________________________________________________________
Concept and Procedure Explanation
Safety Precautions Trained Declined
Warning and Caution Labels
Bead Roller
Maintenance and Performance Checks Trained Declined
Air Pressure Check
Checking Arm Calibration to Rims
Adjustment and Filling of Oiler
Wheel Clamping Trained Declined
Drop Center Identification
Standard Wheel
Reverse Drop Center Wheel
Large Pilot Hole Wheel
Bead Loosening Trained Declined
Standard Procedure
Tire Lubrication
Demounting Trained Declined
Standard Procedure
Mounting Trained Declined
Low Profile Wheels
Mounting of High Profile
Inflation Trained Declined
Adjustment of Pre-Set Pressures
Lubrication and Removal of Valve Core

Individuals and Date Trained
___________________________________ ___________________________________
___________________________________ ___________________________________
___________________________________ ___________________________________
___________________________________ ___________________________________
___________________________________ ___________________________________
___________________________________ ___________________________________
___________________________________ ___________________________________
___________________________________ ___________________________________
___________________________________ ___________________________________
___________________________________ ___________________________________
___________________________________ ___________________________________
___________________________________ ___________________________________
___________________________________ ___________________________________

TC39 Series Changer Operation Instructions Contents •
••
•i
CONTENTS
1. GETTING STARTED.......................................................................................1
1.1 Introduction.............................................................................................................1
1.2 For Your Safety.......................................................................................................1
Hazard Definitions................................................................................................1
IMPORTANT SAFETY INSTRUCTIONS.............................................................2
Decal Placement ..................................................................................................3
Electrical...............................................................................................................4
Specific Precautions/Power Source.....................................................................5
Equipment Installation and Service......................................................................5
Equipment Specifications.....................................................................................5
Safety Summary...................................................................................................6
1.3 Tire Bead Loosening with PowerOut......................................................................6
1.4 Wheel Lift Pedal .....................................................................................................6
1.5 Wheel Rotation Pedal.............................................................................................6
1.6 Air Inflation Pedal....................................................................................................7
1.7 Inflator and Pressure Limiter ..................................................................................7
1.8 Bead Press Arm .....................................................................................................7
1.9 Command unit........................................................................................................7
1.10 Equipment Components.......................................................................................9
1.11 Tool Head...........................................................................................................10
Tool Head Damage Prevention..........................................................................10
2. BASIC PROCEDURES.................................................................................12
2.1 Side Shovel Bead Loosening................................................................................12
2.2 Placing Wheel on TC............................................................................................13
Wheel Support Plate Height Adjustment............................................................13
Standard and High Offset Wheels......................................................................14
Reverse Drop Center Wheels ............................................................................15
Large Pilot Hole Wheels.....................................................................................17
2.3 Bead Loosening....................................................................................................18
2.4 Demounting Tires from Rim .................................................................................19
2.5 Mounting Tire to Rim ............................................................................................21
2.6 Mounting Tough, Low Profile Tires.......................................................................25
2.7 Matching/Optimizing of Tire to Rim ......................................................................26
2.8 Tire Inflation..........................................................................................................27
2.9 Removal of Wheel from TC..................................................................................28
3. MAINTENANCE AND CALIBRATION..........................................................29
3.1 Maintenance Schedule.........................................................................................29
3.2 Maintenance Replacement Parts .........................................................................30
3.3 Checking the Bead Rollers...................................................................................31
3.4 Tool Head Adjustment..........................................................................................32

TC39 Series Changer Operation Instructions Getting Started •
••
•1
1. GETTING STARTED
1.1 Introduction
This manual provides operation instructions and information required to maintain the
TC series tire changer.
The owner of the TC is solely responsible for arranging technical training. The TC is
to be operated only by qualified trained technicians. Maintaining records of personnel
trained is solely the responsibility of the owner and management.
This manual assumes the technician has already been trained in basic tire changing
procedures.
“References”
This manual assumes that you are already familiar with the basics of tire changing.
The first section provides the basic information to operate the TC. The following
sections contain detailed information about equipment, procedures, and
maintenance. “Italics” are used to refer to specific parts of this manual that provide
additional information or explanation. For example, refer to “Equipment Components,”
page 9. These references should be read for additional information to the instructions
being presented.
The owner of the TC is solely responsible for arranging technical training. The TC is
to be operated only by a qualified trained technician. Maintaining records of personnel
trained is solely the responsibility of the owner or management.
1.2 For Your Safety
Hazard Definitions
Watch for these symbols:
CAUTION: Hazards or unsafe practices, which could result in minor
personal injury, or product or property damage.
WARNING: Hazards or unsafe practices, which could result in
severe personal injury or death.
DANGER: Immediate hazards, which will result in severe personal
injury or death.
These symbols identify situations that could be detrimental to your safety and/or
cause equipment damage.

2 •
••
•Getting Started TC39 Series Changer Operation Instructions
IMPORTANT SAFETY INSTRUCTIONS
WARNING: This machine stores and uses significant volumes of compressed air.
Disconnect compressed air at the source and drain all compressedair
before servicing. Severe injury or death can occur if service is
attempted on a compressed air chamberwhile it is charged.
WARNING: This machine useshigh voltage electrical power. Shut down and
unplug the machine at the source before servicing. Severe injury or
death can occur if service is attempted on a live electrical circuit.
Read and follow all caution and warning labels affixed to equipment and tools.
Read and understand all instructions before operating this machine.
Misuse of this equipment can cause personal injury and shorten the life of the TC.
To prevent accidents or damage to the TC, use only Hunter recommended procedures and
accessories.
Wear OSHA approved eye protection while operating the TC.
Wear non-slip safety footwear when operating the TC.
Do not wear jewelry or loose clothing when operating the TC.
Wear proper back support when lifting or removing wheel from the TC.
Never stand on the TC.
WARNING: Keep hands and clothing clear of moving parts. Keep hands clear
of upper roller when bead loosening or rotating clamped wheel.
Do not lean or reach over tire when inflating.
WARNING: Do not exceed these pressure limitations:
SUPPLY LINE PRESSURE (from compressor) 175 PSI.
OPERATING PRESSURE (gauge on regulator) 145 PSI.
BEAD SEATING PRESSURE (gauge on hose) 40 PSI.
WARNING: Never mount a tire to a rim that is not the same diameter (e.g., 16
1/2 inch tire mounting on a 16 inch rim).
WARNING: After loss of air line pressure ALWAYS raise the wheel lift pedal
to prevent the wheel lift from rising quickly during first operation.
DANGER: Activate blast inflation nozzle only when seating bead.
CAUTION: Do not hose down or power wash electric tire changers.
Bleed air pressure from system before disconnecting supply line or other pneumatic
components. Air is stored in a reservoir for operation of the blast inflation nozzle. Air
pressure can be bled from the system by pulling up on the knob located on top of the
regulator, and then turning it counterclockwise.
Do not activate the blast inflation nozzle if the tire is not properly clamped.

TC39 Series Changer Operation Instructions Getting Started •
••
•3
Do not operate TC with worn rubber or plastic parts.
Wheels equipped with low tire pressure sensors or special tire and rim design may
require certain procedures. Consult manufacturer’s service manuals.
SAVE THESE INSTRUCTIONS
Service and maintain machine regularly as outlined in “Maintenance and Calibration,”
on page 29. For further information contact:
Hunter Engineering Company
11250 Hunter Drive
Bridgeton, Missouri 63044
(314) 731-3020
http://www.hunter.com
Decal Placement

4 •
••
•Getting Started TC39 Series Changer Operation Instructions
1 128-284-2 DECAL-SAFETY INSTRUCTIONS
2 128-323-2 DECAL-EYE PROTECTION
3 128-1213-2 DECAL-TCA TPMS SENSOR
4 128-286-2 DECAL-DANGER AIR BLAST
5 128-1149-2 DECAL-WARNING AIR BLAST
6 128-489-2 DECAL-MOUNTING ARM INCLINATION
7 128-435-2 DECAL-REMOVE CLIP-ON WEIGHTS
8 128-287-2 DECAL-WARNING INFLATION
9 128-285-2 DECAL-WARNING PRESSURE LIMITATIONS
10 128-504-2 DECAL-DO NOT BREAK BEAD WITH AIR
PRESSURE IN TIRE
11 128-505-2 DECAL-KEEP ARMS AND LEGS CLEAR OF BEAD
BREAKER
12 RP6-3691 DECAL-INFLATION
13 RP6-710211210 DECAL-ROTATION DIRECTION
14 RP6-99990758 DECAL-ELECTRICITY DANGER
15 RP6-4244 DECAL-ROTATING PARTS DANGER INDICATING
16 128-1241-2 DECAL-KEEP CLEAR
17 RP6-999916311 DECAL-RUBBISH SKIP
18 RP6-999915200 SERIAL NUMBER PLATE
19 RP6-1594 DECAL-INSTALLATION DATE
20 128-1748-2 TC LOGO PLATE
21 128-1750-2 TC39 PLATE
22 RP6-999923160 DECAL-WARNING PROP 65
23
24 999923960
RP6-4221 BEAD PRESS ARM PLUS PLATE
GROUNDING PLATE
25 RP6-999923950 DECAL-INDENT
26 RP6-999923990 DECAL-ROLLER
27 RP6-999923940 DECAL-TOOL HEAD
Electrical
The TC is manufactured to operate at a specific voltage and amperage rating.
Make sure that the appropriate electrical supply circuit is of the same voltage and
amperage ratings as marked on the TC.
WARNING: DO NOT ALTER THE ELECTRICAL PLUG. Plugging the
electrical plug into an unsuitable supply circuit will
damage the equipment.
Make sure that the electrical supply circuit and the appropriate receptacle is installed
with proper grounding.
To prevent the possibility of electrical shock injury or damage to the equipment when
servicing the TC, power must be disconnected by removing the power cord from the
electrical power outlet.

TC39 Series Changer Operation Instructions Getting Started •
••
•5
Specific Precautions/Power Source
The TC is intended to operate from a power source that will apply 208-230VAC, 1
phase, 15 amp 50/60 Hz, power cable includes NEMA 20 amp plug, L6-20P, between
the supply conductors of the power cord. The power cord supplied utilizes a twist lock
connector, NEMA L6-20P. This machine must be connected to a 20 amp branch
circuit. Please refer all power source issues to a certified electrician. Refer to
“Installation Instructions for TC Tire Changer.
CAUTION: A protective ground connection, through the grounding
conductor in the power cord, is essential for safe operation.
Use only a power cord that is in good condition.
Equipment Installation and Service
A factory-authorized representative should perform installation.
This equipment contains no user serviceable parts. All repairs must be referred to a
qualified Hunter Service Representative.
Equipment Specifications
Electrical
Voltage: 208-230VAC, 1 phase, 50/60 Hz, power cable includes
NEMA 20 amp plug, L6-20P
Amperage: 15 amperes
Wattage: 3450 watts (peak)
Air
Air Pressure Requirements: 115-175 PSI (7.9-12.0 bar)
Approximate Air Consumption: 4 CFM (110 Liters/Minute)
Mechanical
Clamping System Rotating
Speed: CW – variable up to 14 rpm
CCW – 7rpm
Torque: 867 ft-lbs
Max. Tire Diameter: 46 in.
Max Bead Roller Opening Width:
15 in.
Diameter Range: 10-26 in.
Bead Roller Power; Each Roller: 2645 lbs.

6 •
••
•Getting Started TC39 Series Changer Operation Instructions
Safety Summary
Explanation of Symbols
These symbols may appear on the equipment.
Alternating current.
Earth ground terminal.
Protective conductor terminal.
l ON (supply) condition.
OFF (supply) condition.
Risk of electrical shock.
Stand-by switch.
1.3 Tire Bead Loosening with PowerOut
WARNING: Keep arms and legs from between the bead breaker arm
and the side of the housing.
The bead loosener shovel is controlled by a handle on the shovel itself. Pulling
upward on the handle will insert push the shovel into the tire for bead loosening.
Pushing downward on the handle will pull the shovel back outward under power.
Repeat as necessary to loosen entire bead on both sides of wheel. Use care around
TPMS sensors.
1.4 Wheel Lift Pedal
Press down on the wheel lift pedal to raise wheel lift. PULL UP THE WHEEL LIFT
PEDAL TO LOWER THE LIFT. When the pedal is released the wheel lift WILL
REMAIN IN POSITION.
1.5 Wheel Rotation Pedal
The right pedal on the front of TC base controls the rotation of the wheel. Refer to
“Equipment Components,” on page 9.
Step down on the pedal to rotate the wheel clockwise (variable speed).
Lift the pedal to rotate the wheel counterclockwise (fixed speed).
CAUTION: Keep hands clear of wheel, tire, and rollers during bead
loosening.

TC39 Series Changer Operation Instructions Getting Started •
••
•7
1.6 Air Inflation Pedal
The left or the central pedal on the front of TC base is a two-stage design. Refer to
“Equipment Components,” on page 9. The pedal controls the air going to the inflation
hose and the blast inflation nozzle.
CAUTION: Keep hands clear of wheel during sealing and seating of
bead.
CAUTION: When operating air inflation hose, do not lean over the tire.
Step down partially on the pedal to inflate tires through inflation hose.
Step down completely on the pedal to activate the blast inflator nozzle to seal tire
beads.
Refer to “2.6” on page 25 for complete inflation operation instructions.
1.7 Inflator and Pressure Limiter
As a safety device, the pressure limiter prevents the operator from using excessive
air pressure to seat the tire bead during tire inflation. Bead seating pressure should
never exceed 40 psi. If tires being mounted require more than 40 psi for inflation
pressure, the tire/wheel assembly should be removed from the tire changer, placed in
an inflation cage, and inflated per manufacturer’s instructions.
While inflating the tire, the pressure gauge will read zero until the inflation pedal is
released. At that time, the gauge will give the correct air pressure reading in the tire.
Refer to “2.6” on page 25 for complete inflation operation instructions.
1.8 Bead Press Arm
The bead press arm assists with tire mounting. The bead press arm moves in tandem
with the mount / demount head.
The controls on the bead press arm move the bead press up or down.
Refer to “Equipment Components,” on page 9.
1.9 Command unit
The command unit governs all the movements necessary for complete bead roller
operation. Refer to “Equipment Components,” on page 9.
The command unit is used to position the bead roller and the tool into working
position.
Press the positioning push-buttons in order to press and pull the bead breaker rollers,
or the tool, on the correct rim diameter.
For proper operation of the command unit, place your hand over controller with index
finger and middle finger over lever buttons.
The command unit consists of 2 levers (pos. A) and of 2 push buttons (pos. B).
The left lever and push button control the lower bead breaker roller. The right lever
and push button control the upper bead breaker roller.
Each lever has 4 positions:
- Position 1 (rest position) stops the operated bead breaker roller in its current
position;
- Position 2 (held position) lowers the upper bead breaker roller or lifts the lower
bead breaker roller;

8 •
••
•Getting Started TC39 Series Changer Operation Instructions
- Position 3 (held position) lifts the upper bead breaker roller or lowers the lower
bead breaker roller;
- Position 4 (lock position) brings automatically the arms to their high / low stroke
limit.
When the corresponding push button is pressed (pos. B) the cam for the introduction
of the bead breaker roller between tire and rim is operated.
Tool command unit consists of two push buttons. The upper push button controls the
rising, while the lower push button controls tool descent.

TC39 Series Changer Operation Instructions Getting Started •
••
•9
1.10 Equipment Components

10 •
••
•Getting Started TC39 Series Changer Operation Instructions
1.11 Tool Head
Tool Head Damage Prevention
NOTE: Always generously lubricate all
sides, including the bottom, of new
tool heads with tire lube paste
before first use.
If the tool head breaks near the middle the user was rotating the wheel and tire
assembly while pressing the “Tool Head Raise” button.
Demounting
=
+

TC39 Series Changer Operation Instructions Getting Started •
••
•11
Use the following tips to prevent this type of tool head damage:
•DO NOT ROTATE while pressing the “Tool Head Raise” button.
•Ensure tool head cradles the rim edge before rotating during demount of
upper bead.
TOOL HEAD NOT CRADLED ON RIM TOOL HEAD CORRECTLY POSITIONED
If the tool head breaks at the mount/demount end the tire bead was not in the drop
center when mounting the upper bead.
Use the following tips to prevent this type of tool head damage:
•The bead MUST be in the drop center when mounting the upper bead.
•Use the bead press device and the upper roller to guide the bead into the
drop center.
•Ensure the bead is completely in the drop center on wheels where the
drop center is far from the bead seat.
BEAD NOT IN DROP CENTER
BEAD FULLY IN DROP CENTER
Mounting
Bead not drop center.

12 •
••
•Basic Procedures TC39 Series Changer Operation Instructions
2. BASIC PROCEDURES
2.1 Side Shovel Bead Loosening
For bead loosening with rollers, refer to “Bead Loosening,” page 18.
Remove valve stem core and deflate tire completely.
WARNING: All air pressure inside the tire must be removed before
proceeding. Never attempt to loosen the bead until all air
is removed from the tire. Failure to remove all air from
tire may result in injury to operator, or damage to
equipment, tire, or wheel.
Remove all weights from the rim to protect the rim and to extend life of the
mount/demount head.
The lever (pos. 1) allows to operate the bead breaker arm cylinder/side shovel. This
lever has two stable positions with hold control: when the handle is lifted, the side
shovel is pushed into the tire for bead loosening (pos. 2); when the handle is pressed
downward the side shovel opens outwards.
Press the lever downward to make the side shovel open outwards.
Position the wheel against the side of the TC, between the bead breaker arm and the
housing.
Lift the lever. The bead breaker arm will be pulled toward the TC to loosen the bead.
Press the lever downward again to swing the arm to the open position. Once the arm
has been swung to the open position, release the lever.
If the bead has not completely loosened, rotate the wheel and repeat the bead
loosening procedure at a different area on the tire.
Turn the wheel and loosen the opposite bead using the same procedure.

TC39 Series Changer Operation Instructions Basic Procedures •
••
•13
2.2 Placing Wheel on TC
Wheel Support Plate Height Adjustment
The wheel support plate on the TC is height adjustable to allow a wide range of
wheels to be serviced.
Use the highest setting for most high offset wheels.
Standard wheels typically use the middle height.
Use the lowest height for most reverse drop-center wheels.
To adjust center support height, pull the knob outwards on center support and raise or
lower center support table to desired height.

14 •
••
•Basic Procedures TC39 Series Changer Operation Instructions
Standard and High Offset Wheels
Adjust center support position to appropriate settings for the tire and wheel
combination to be serviced. This is typically the middle or highest setting.
Place the wheel, face up, on the center support. Ensure the anti-rotation pin enters a
lug hole in the wheel.
Insert wheel clamp, press down and twist clockwise 1/4 turn to lock into center
support.

TC39 Series Changer Operation Instructions Basic Procedures •
••
•15
The clamping shaft is equipped with a quick clamp cone to speed clamping. Simply
activate the Quick Clamp, drop the cone into place then hand tighten.
Reverse Drop Center Wheels
Adjust center support position to appropriate settings for the tire and wheel
combination to be serviced. This is typically the lowest setting.
Place anti-rotation pin protector and wheel protector pad on center support
Anti/Rotation Pin with Extensions

16 •
••
•Basic Procedures TC39 Series Changer Operation Instructions
Place wheel, face-down, on center support ensuring anti-rotation pin inserts one lug
hole.
Insert wheel clamp, press down and twist clockwise 1/4 turn to lock into center
support.
The clamping shaft is equipped with a quick clamp cone to speed clamping. Simply
activate the Quick Clamp, drop the cone into place then hand tighten.
Table of contents
Other Hunter Tyre Changer manuals
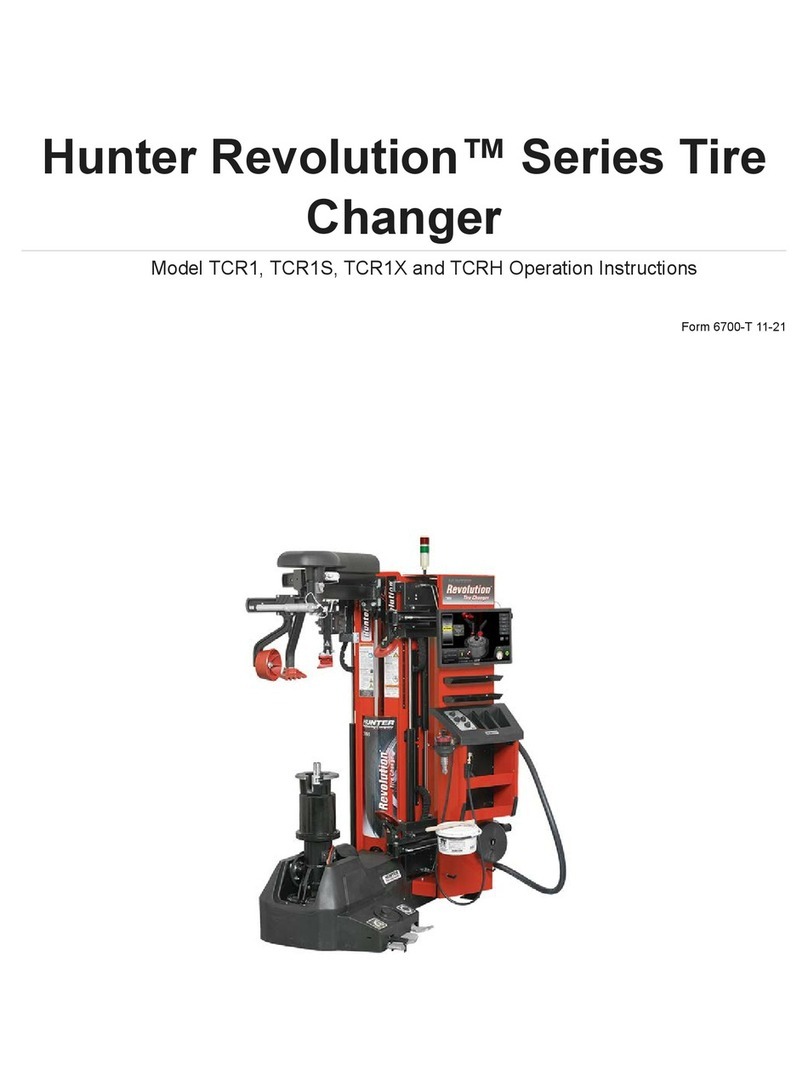
Hunter
Hunter Revolution Series User manual
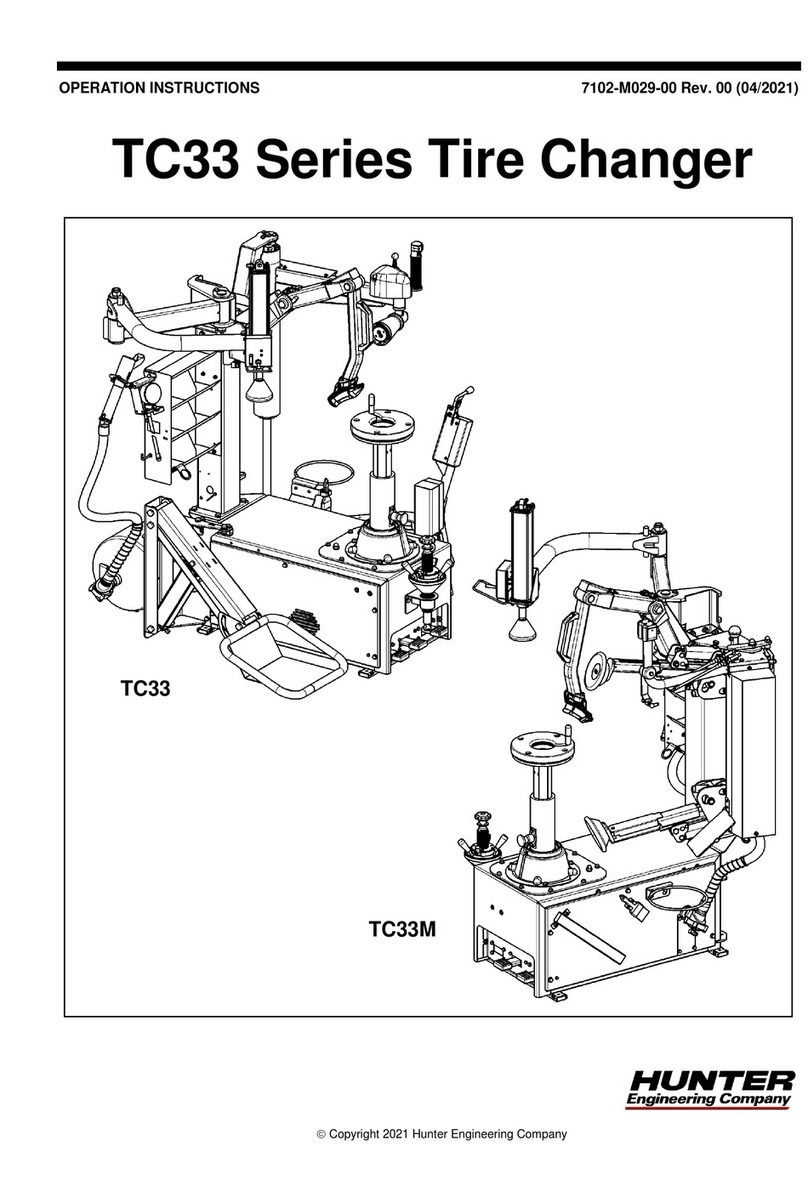
Hunter
Hunter TC33 Series User manual
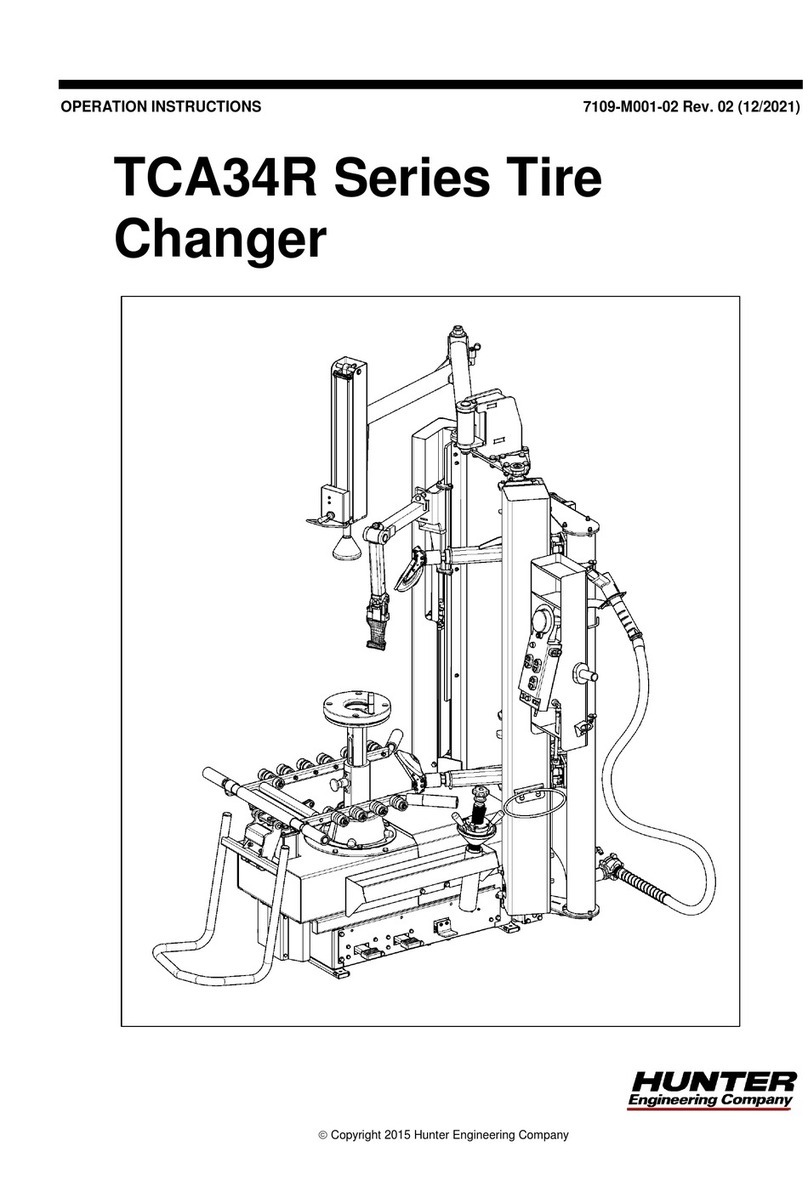
Hunter
Hunter TCA34R Series User manual

Hunter
Hunter TCX50 User manual
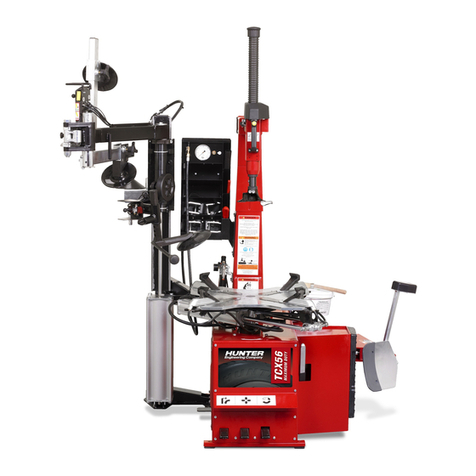
Hunter
Hunter TCX56 User manual
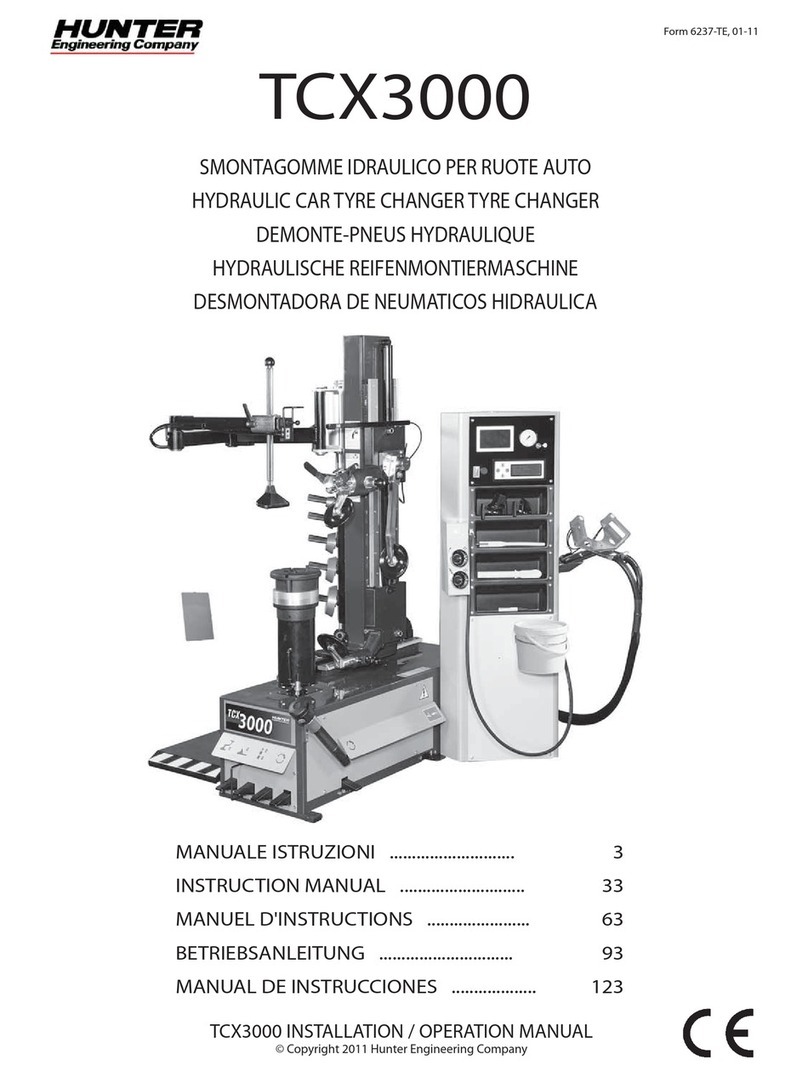
Hunter
Hunter TCX3000 User manual
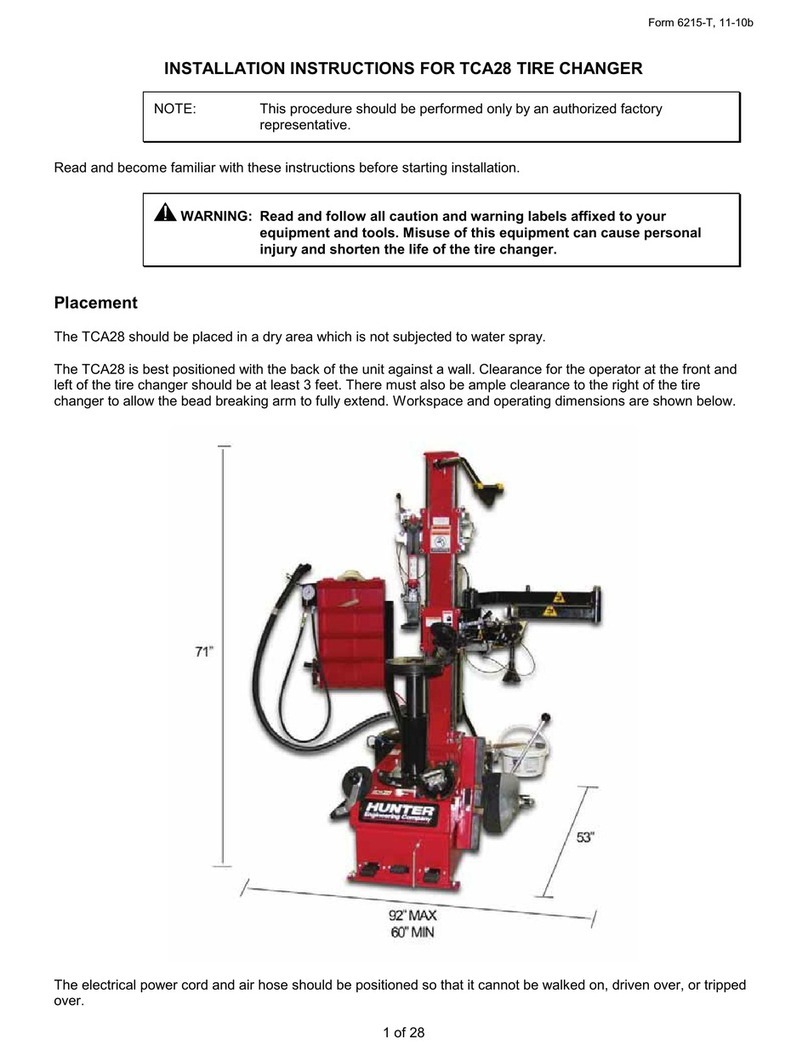
Hunter
Hunter TCA28 User manual
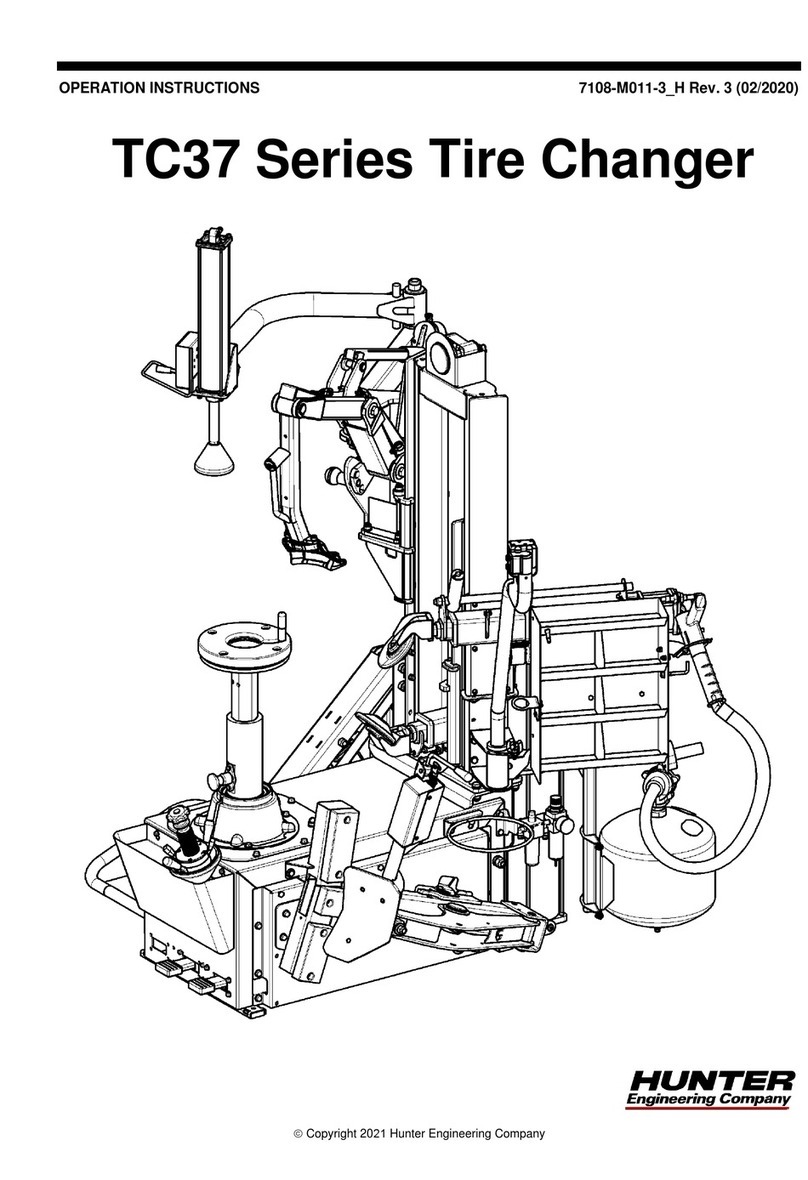
Hunter
Hunter TC37 Series User manual
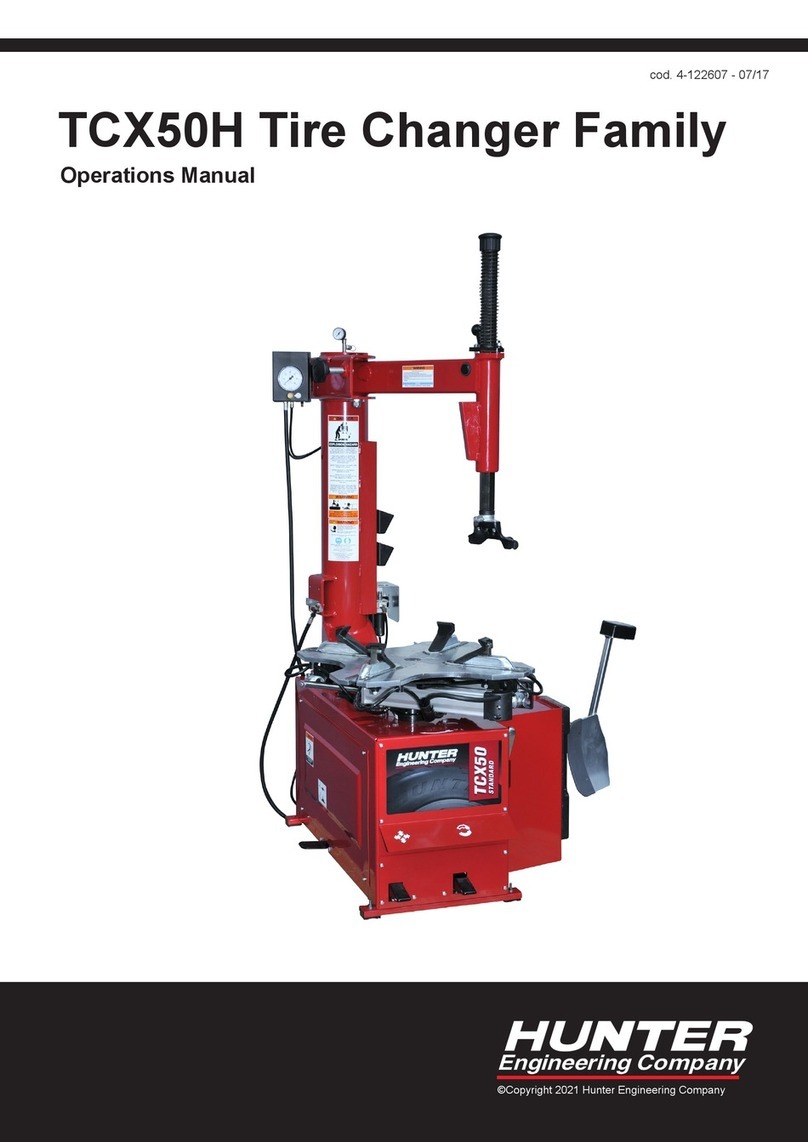
Hunter
Hunter TCX50H Series User manual

Hunter
Hunter Maverick Series User manual
Popular Tyre Changer manuals by other brands

Bosch
Bosch TCE 60 Original instructions
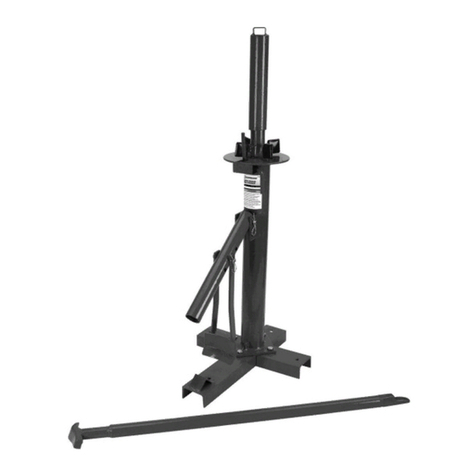
Strongway
Strongway 54413 owner's manual
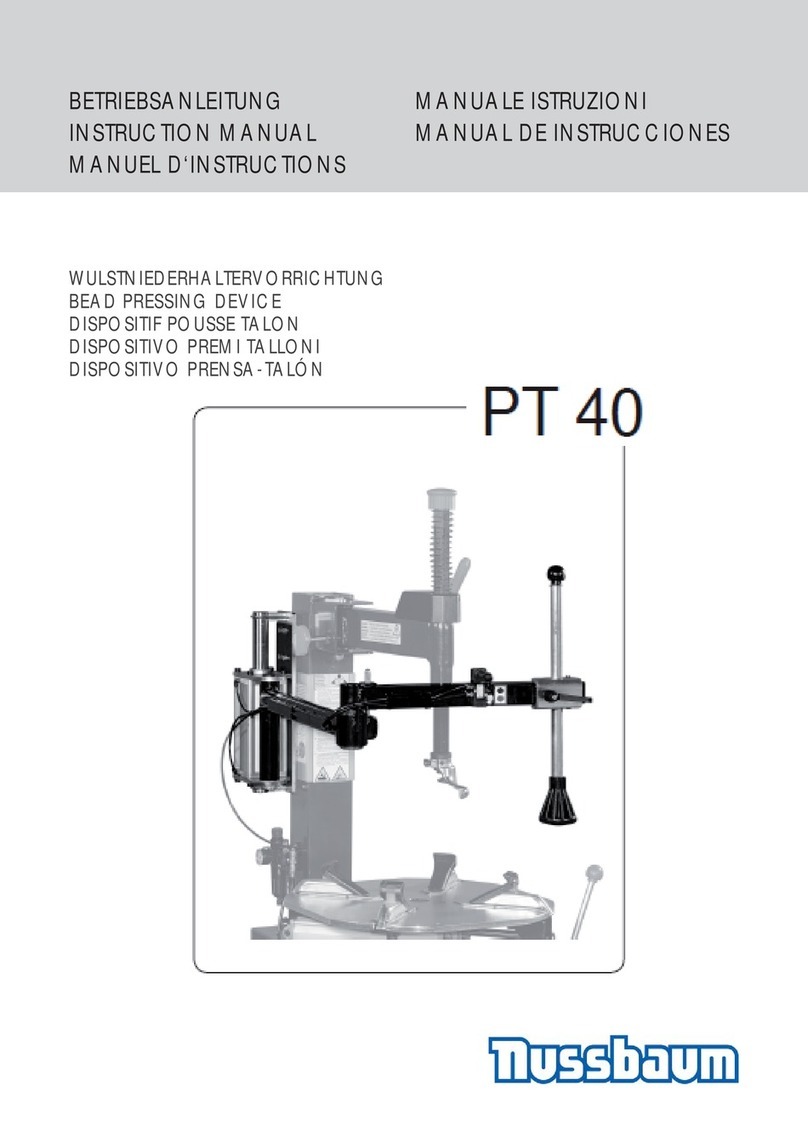
Nussbaum
Nussbaum PT 40 instruction manual

Hofmann Megaplan
Hofmann Megaplan megamount 601 Installation, operation and maintenance guide

Coats
Coats CHD-4730W Operating and maintenance instructions

Zipper Mowers
Zipper Mowers ZI-RMM95 user manual