Jet JSMS-10L User manual

JSMS-10L SLIDE MITRE SAW
GB
Operating Instructions
D
Gebrauchsanleitung
F
Mode d´emploi
DK
Brugsanvisning
FIN
Käyttöohje
NL
Gebruiksaanwijzing
WMH Tool Group AG
Bahnstrasse 24, CH - 8603 Schwerzenbach
Tel +41 (0) 44 806 47 48
Fax +41 (0) 44 806 47 58
M-10000826M/U 06/06

JSMS-10L
Declaration of conformity
On our own responsibility we hereby declare that this product complies
with the regulations
* 98/37/EC, 98/79EC, 89/336/EC, 93/68EC, 73/23/EC, 2002/95/EC
designed with consideration of the standards
** EN 61029-1, EN 61029-2-9, EN 55014-1, EN 55014-2, EN 61000-3-2, EN 61000-3-3
05.06.2006 Marcel Baumgartner, managing director
WMH Tool Group AG, Bahnstrasse 24, CH - 8603 Schwerzenbach
2

GB - ENGLISH
Operating Instructions
Dear Customer,
Many thanks for the confidence you have shown in us with the purchase of your new JET-machine. This manual has been
prepared for the owner and operators of a JET JSMS-10L slide mitre saw to promote safety during installation, operation and
maintenance procedures. Please read and understand the information contained in these operating instructions and the
accompanying documents. To obtain maximum life and efficiency from your machine, and to use the machine safely, read
this manual thoroughly and follow instructions carefully.
…Table of Contents
1. Declaration of conformity
2. JET Warranty
3. Safety
Authorized use
General safety notes
Remaining hazards
4. Machine specifications
Technical data
Noise emission
Contents of delivery
5. Transport and start up
Transport and installation
Assembly
Mains connection
Starting operation
6. Machine operation
7. Setup and adjustments
Changing the sawblade
Laser adjustment
Bevel stop adjustment
Cutting depth adjustment
8. Maintenance and inspection
9. Troubleshooting
10. Available accessories
1. Declaration of conformity
On our own responsibility we hereby
declare that this product complies
with the regulations* listed on page 2.
Designed in consideration with the
standards**.
2. JET Group Warranty
The JET Group makes every effort to
assure that its products meet high
quality and durability standards and
warrants to the original retail
consumer/purchaser of our products
that each product be free from
defects in materials and workmanship
as follows:
2 YEARS ON ALL MECHANICAL
PARTS
1 YEAR ON ALL ELECTRICAL
PARTS
This Warranty does not apply to
defects due to directly or indirectly
misuse, abuse, negligence or
accidents, normal wear-and-tear,
repair or alterations outside our
facilities, or to a lack of maintenance.
The Jet group limits all implied
warranties to the period specified
above, from the date the product was
purchased at retail.
To take advantage of this warranty,
the product or part must be returned
for examination, postage prepaid, to
an authorized repair station
designated by our office.
Proof of purchase date and an
explanation of the complaint must
accompany the merchandise.
If our inspection discloses a defect,
we will either repair or replace the
product, or refund the purchase price
if we cannot readily and quickly
provide a repair or replacement, if
you are willing to accept a refund.
We will return repaired product or
replacement at JET’S expense, but if
it is determined there is no defect, or
that the defect resulted from causes
not within the scope of JET’S
warranty, then the user must bear the
cost of storing and returning the
product.
The JET Group reserves the right to
make alterations to parts, fittings, and
accessory equipment which they may
deem necessary for any reason
whatsoever.
3. Safety
3.1 Authorized use
This machine is designed for sawing
wood, wood derived materials as well
as similar to be machined hard
plastics only.
Machining of other materials is not
permitted and may be carried out in
specific cases only after consulting
with the manufacturer.
No metal workpieces may be
machined.
The proper use also includes
compliance with the operating and
maintenance instructions given in this
manual.
The machine must be operated only
by persons familiar with its operation
and maintenance and who are
familiar with its hazards.
The required minimum age must be
observed
The machine must only be used in a
technically perfect condition
When working on the machine, all
safety mechanisms and covers must
be mounted.
In addition to the safety requirements
contained in these operating
instructions and your country’s
applicable regulations, you should
observe the generally recognized
technical rules concerning the
operation of woodworking machines.
Any other use exceeds authorization.
In the event of unauthorized use of
the machine, the manufacturer
renounces all liability and the
responsibility is transferred
exclusively to the operator.
3.2 General safety notes
Woodworking machines can be
dangerous if not used properly.
Therefore the appropriate general
technical rules as well as the
following notes must be observed.

Read and understand the entire
instruction manual before attempting
assembly or operation.
Keep this operating instruction close
by the machine, protected from dirt
and humidity, and pass it over to the
new owner if you part with the tool.
No changes to the machine may be
made.
Daily inspect the function and
existence of the safety appliances
before you start the machine.
Do not attempt operation in this case,
protect the machine by unplugging
the mains cord.
Do not lock the moving guard in the
open position. Ensure that the
movable guards operate freely
without jamming.
Remove all loose clothing and
confine long hair.
Before operating the machine,
remove tie, rings, watches, other
jewellery, and roll up sleeves above
the elbows.
Wear safety shoes; never wear
leisure shoes or sandals.
Always wear the approved working
outfit
Do not wear gloves while operating
this machine.
For the safe handling of saw blades
wear work gloves.
Observe the chapter “save operation”
in this manual.
Control the stopping time of the
machine, it may not be longer than 10
seconds.
Do NOT stop the blade by forcing the
machine or by using sideways
pressure.
Insure that the workpiece does not
roll when cutting round pieces.
Use suitable table extensions and
supporting aids for difficult to handle
workpieces.
Never use just your hands for
sawing
Always hold and guide the
workpieces safely during machining.
Never cut pieces that are too small.
For safety reasons this machine
requires the use of two hands and
should not be operated standing on a
staircase or leather.
Make sure that the motor ventilation
holes are clean and open.
Install the machine so that there is
sufficient space for safe operation
and workpiece handling.
Keep work area well lighted.
The machine is designed to operate
in closed rooms and must be placed
stable on firm and levelled ground.
Make sure that the power cord does
not impede work and cause people to
trip.
Keep the floor around the machine
clean and free of scrap material, oil
and grease.
Stay alert!
Give your work undivided attention.
Use common sense.
Do not operate the machine when
you are tired.
Do not operate the machine under
the influence of drugs, alcohol or any
medication. Be aware that medication
can change your behaviour.
Keep children and visitors a safe
distance from the work area.
Never reach into the machine while it
is operating or running down.
Never leave a running machine
unattended. Before you leave the
workplace switch off the machine.
Do not operate the electric tool near
inflammable liquids or gases.
Normal brushfire might ignite.
Observe the fire fighting and fire alert
options, for example the fire
extinguisher operation and place.
Do not use the machine in a dump
environment and do not expose it to
rain.
Wood dust is explosive and can also
represent a risk to health.
Dust form some tropical woods in
particular, and from hardwoods like
beach and oak, is classified as a
carcinogenic substance.
Always use a suitable dust extraction
device
Before machining, remove any nails
and other foreign bodies from the
workpiece.
Specifications regarding the
maximum or minimum size of the
workpiece must be observed.
Do not force the power tool. It will do
a better and safer job and give you
much better service if it is used at the
rate for which it was designed.
Do not remove chips and workpiece
parts until the machine is at a
complete standstill.
Never operate with the guards not in
place – serious risk of injury!
Connection and repair work on the
electrical system may be carried out
by a qualified electrician only
Always unwind any extension cords
fully.
Damaged extension cords replace
immediately.
Do not use the power tool if the
ON/OFF switch does not turn the
power tool ON and OFF.
Make all machine adjustments or
maintenance with the machine
unplugged from the power source.
Do not use blades made from High
Speed Steel (HSS).
Remove defective saw blades
immediately.
Use carbide-tipped sawblades with a
negative chip angle only.
Never attempt to use ripping or
combination blades with this saw.
When cutting thin walled stock, it is
essential that you use a fine tooth
blade of at least 80 teeth.
A coarse blade may hook into the
stock and eject it.
This machine is not suitable for
cutting steel and other metals.
Never attempt to cut round or
irregular cross-section stock without
using a suitable jig.
If the blade stalls, switch off
immediately.
When using machine on a workstand,
always clamp it down.
Always listen to the machine and
switch off immediately if abnormal
sounds are heard.
Keep the slide lock tight unless slide
action is needed.
Ensure that the blade guard opens
and closes smoothly.
Always support long pieces with an
additional supporting stand of
appropriate height.
Never carry tool by operating handle.
Always use the carry handle or use
two hands to carry by the base.
Always use approved eye and ear
protection.
Keep hands away from blad at all
times.
Always unplug machine after use.

Do not stare into beam of laser
Do not point the laser beam at people
or animals.
Do not use the laser beam on highly
reflective materials. Reflected light is
dangerous.
Repair work on the laser beam may
only be carried out by a specialist.
3.3 Remaining hazards
When using the machine according to
regulations some remaining hazards
may still exist
The moving saw blade in the work
area can cause injury.
Broken saw blades can cause
injuries.
Thrown workpieces can lead to injury
Wood chips and sawdust can be
health hazards. Be sure to wear
personal protection gear such as
safety goggles ear- and dust
protection.
Use a suitable dust exhaust system.
The use of incorrect mains supply or
a damaged power cord can lead to
injuries caused by electricity.
Avoid body contact with earthed or
grounded surfaces (e.g. pipes,
radiators, ranges and refrigerators).
There is no substitute for a careful
attentive operator. Conversely
there is no safety device that can
protect a careless operator in all
situations.
4. Machine specifications
4.1 Technical data
Saw blade size 254x 2,8x 30mm
No load speed 4500 rpm
Max cutting height 90°/45° 90/42mm
Max. cutting length 90°/45° 305/215mm
Bevel capacity left 0°-45°
Mitre capacity left/right 45°/45°
Dust extraction port d/D 30/40mm
Weight 18 kg
Mains 230V ~1L/N 50-60Hz
Motor input power 1500W
Reference current 6,5 A
Extension cord (H05VV-F) 2x1,0mm²
Installation fuse protection 10A
The machine has double insulation
in accordance with EN61029.
Laser class 2 <1mW, 400-700nm
Laser power supply 3V by transformer
4.2 Noise emission
Determined according to EN
1807:1999 (Inspection tolerance 4 dB)
Acoustic power level (acc. EN 3746):
Idling 101,5 dB (A)
Acoustic pressure level (EN 11202):
Idling 88,7 dB (A)
The specified values are emission
levels and are not necessarily to be
seen as safe operating levels.
This information is intended to allow
the user to make a better estimation
of the hazards and risks involved.
4.3 Content of delivery
1 slide mitre saw
1 dust extraction bag
1 workpiece clamp
2 table extension pieces
1 length gauge
1 spanner 13mm
1 sawblade
Operating manual
Spare parts list
4.4 Mitre saw description
Fig 1
A….Laser ON/OFF switch
B….Handgrip with switch button
C….Protective cover for blade
D….Cutting head lock button
E…..Workpiece clamp
F….Miter lock knob
G….Length gauge
H….Machine table
I….Workpiece fence
J….Sawblade
K…..Dust bag
L…...Slide lock knob
M….Line laser
N….bevel lock knob
O….Table extensions
P…..Unlock botton
Q….Cutting depth adjustment
U….Spindle lock button
Fig 2
Fig 3
5. Transport and start up
5.1 Transport and installation
The machine is designed to operate
in closed rooms and must be placed
stable on firm and levelled surface.
The machine can be bolted down if
required.
For packing reasons the machine is
not completely assembled.
5.2 Assembly
If you notice any transport damage
while unpacking, notify your supplier
immediately. Do not operate the
machine!
Dispose of the packing in an
environmentally friendly manner.
Clean all rust protected surfaces with
a mild solvent.
Mounting the table extensions
Mount the length gauge (B, Fig 4) to
the left or right table extension.

Fig 4
Use the clamping pieces (A) to lock
the table extensions (C) in place.
Mounting the dust bag.
Use the dust bag (K, Fig 1) to collect
the dust emissions. You can slide the
dust bag onto the dust port on the
rear of the machine.
The dust port is also suitable for the
connecting to a dust collector.
Unlocking the cutting head.
The mitre saw is supplied with the
cutting head in locked position. The
cutting head lock button (D, Fig 2)
can be pulled out by pushing the
cutting head down at the same time.
Allow the cutting head to slowly rise.
The cutting head should be relocked
for transportation.
5.3 Mains connection
Mains connection and any extension
cords used must comply with
applicable regulations.
The mains voltage and frequency
must comply with the information on
the machine licence plate.
The mains connection must have a
10A surge-proof fuse.
Only use power cords marked
H05VV-F
Connections and repairs to the
electrical equipment may only be
carried out by qualified electricians.
5.4 Starting operation
You can start the machine by
pressing the trigger (B, Fig 1) on the
handle with your fingers.
To stop the saw release the trigger.
6. Machine operation
Correct working position:
In front of the machine standing in the
direction of cutting (Fig 5)
Fig 5
Keep your face and body to one side
of the blade, out of line with a
possible debris throwback.
Never cross your arms or place your
hands near the cutting area.
Don’t overreach; keep good footing
and balance.
Do not cut short workpieces.
You cannot properly hold a short
workpiece.
Workpiece handling:
Support long workpieces with helping
roller stands.
During cutting operation the
workpiece must be locked down to
the table with the workpiece clamp.
Do not perform any operation
freehand.
Operating hints:
Always observe the safety
instructions and adhere to the
current regulations.
Set up mitre and bevel cut as desired.
Plug in (connect to mains).
Ensure that the saw blade protective
cover is in the correct position before
you start sawing.
The mitre saw is switched on by
means of the trigger button that is
situated on the inside of the handgrip
(B, Fig 1).
The cutting blade must first reach the
maximum rpm before cutting may
begin.
Cutting without slide:
(slide locked)
Slide the unlock button (P, Fig 2) to
the side and by using the handgrip,
push the cutting head slowly and
evenly downwards.
The cutting head must be returned
carefully to its starting position after
cutting.
Cutting with slide:
For cutting wider stock slide action is
necessary.
Loosen slide lock knob (L, Fig 1).
Pull the motor head towards you.
Slide the unlock button (P, Fig 2) to
the side and by using the handgrip,
push the cutting head slowly and
evenly downwards.
Push the motor head forward in a
slow steady motion to complete the
cut.
Release trigger to stop the motor.
The cutting head must be returned
carefully to its starting position after
cutting.
Attention:
The condition of the blade should be
checked before each machining
process.
Work only with a sharp and flawless
sawblade.
Use the workpiece clamp (E, Fig 1).
Use a suitable fixture to prevent
round and irregular shaped timber
from turning under the pressure of the
cut.
Cutting wrapped material:
Wrapped or bowed material should
be positioned so that the workpiece is
supported near the cutting point by
the workpiece fence (Fig 6).
Fig 6
This operation is potentially
dangerous (Fig 7).

Fig 7
Bevel cutting:
Bevel angle can be adjusted between
0° and 45°.
The bevel lock knob (N, Fig 8) on the
rear of the machine must be loosened
for bevel setting.
Fig 8
Tilt the cutting head to the left until
the desired angle on the scale has
been reached.
Retighten the cutting head lock knob
before machine operation.
Mitre cutting:
The mitre angle can be adjusted
between -45° and +45°.
The 2 miter lock knobs (F, Fig 1)
behind the fence must be loosened.
Rotate the cutting head until the
desired angle on the table scale has
been reached.
Retighten the table locking knobs
before machine operation.
Mitre bevel cutting:
Select the correct bevel and mitre
angles.
7. Setup and adjustments
General note:
Setup and adjustment work may
only be carried out after the
machine is protected against
accidental starting by pulling the
mains plug.
7.1 Changing the sawblade
The sawblade has to meet the
technical specification.
Check sawblade for flaws (cracks,
broken teeth, bending) before
installation. Do not use faulty
sawblades.
The sawblade teeth must point in
cutting direction (down)
Always wear suitable gloves when
handling sawblades.
The sawblades may only be
changed when the mains plug is
pulled!
Remove the blade’s protective cover
by unscrewing the two screws (R, Fig
9) on the side and flip up the
protective cover (S).
Fig 9
Press the spindle lock button (U,Fig
3) and loosen the sawblade clamping
screw with the supplied spanner (T).
Attention: Left hand tread
Remove the outer clamping flange.
Replace the sawblade (J, Fig 1).
The teeth of the blade must point in
the same direction as the arrow on
the protective cover.
The flanges should be cleaned before
the new blade is fitted.
Fit the outer clamping flange back
into position and tighten the clamping
screw.
Reposition the plastic protective
cover and tighten the two screws (R,
Fig 9).
7.2 Laser Adjustment
The line laser (V, Fig 10) must be
adjusted so that the beam meets the
cutting line.
Use the screws (W) for adjustment
Fig.10
Attention:
Class 2 laser product, do not stare
into beam of laser.
7.3 Bevel Stop Adjustment
The 90° and 45° bevel stops are
adjusted ex works.
In case of need they can be adjusted
with the screws (X, Fig 8)
7.4 Cutting Depth Adjustment
The cutting depth can be adjusted
with the screw (Q, Fig2).
This allows a halve cut of the
workpiece when cutting with slide.
Attention:
After each adjustment check the free
movement of the sawblade before
switching on the machine.
8. Maintenance and inspection
General notes:
Maintenance, cleaning and repair
work may only be carried out after
the machine is protected against
accidental starting by pulling the
mains plug.
Repair and maintenance work on the
electrical system may only be carried
out by a qualified electrician.
Repair work on the laser beam may
only be carried out by a specialist.
Clean the machine regularly.
Inspect the proper function of the dust
extraction daily.

All protective and safety devices must
be re-attached immediately after
completed cleaning, repair and
maintenance work.
Defective safety devices must be
replaced immediately.
Cleaning:
Regularly clean the machine housing
with a soft cloth preferably after each
use.
Keep the ventilation slots free from
dust and dirt.
If the dirt does not come off use a soft
cloth moistened with soapy water.
Never use solvents such as petrol,
alcohol, ammoniac water, etc. These
solvents may damage the plastic
parts.
Motor brushes:
The collector brushes are due to wear
and may need replacement.
- Disconnect the machine from the
power source, pull mains plug.
-remove the brush covers (A, Fig 11).
Fig 11
-Replace the collector brushes (B)
(Jet Article Number: JSMS10L-109
2 pieces needed).
-reattach the brush covers.
Saw blades:
Only use sharp saw blades.
Use carbide-tipped sawblades with a
negative chip angle only.
Never attempt to use ripping or
combination blades with this saw.
When cutting thin walled stock, it is
essential that you use a fine tooth
blade of at least 80 teeth.
The servicing of saw blades should
only be performed by a trained
person.
Replace a defective sawblade
immediately.
9. Trouble shooting
Motor doesn’t start
*No electricity-
check mains and fuse.
*Defective switch, motor or cord-
consult an electrician.
*Motor brushes worn-
Replace brushes.
Laser doesn’t work
*Defective line laser or power supply-
consult an electrician
Machine vibrates excessively
*Stand on uneven surface-
adjust base for even support.
*sawblade damaged-
replace sawblade immediately
Cut is not square
*Bevel stop setting is bad.
*Workpiece fence setting is bad
Cutting surfaces is bad
*Wrong sawblade used
*resin collection on sawblade
*sawblade is dull
*workpiece inhomogeneous
*Feed pressure too high-
Do not force the workpiece.
10. Available accessories
Refer to the JET-Pricelist
for various saw blades.

JSMS-10L
Slide miter saw
10000826M/U
230/50-60/1
PARTS LIST
ERSATZTEILLISTE
LISTE DE PIECES
WMH Tool Group AG
Bahnstrasse 24, CH – 8603 Schwerzenbach
Tel +41 (0) 44 806 47 48
Fax +41 (0) 44 806 47 58
P-10000826M/U 05/06


Parts List For JSMS-10L Slide Miter Saw
Index
No.
Part No.
Description
Size
Qty.
1
JSMS10L -001
Base
1
2
JSMS10L -002
Rubber feet
5
3
JSMS10L -003
Position shaft
1
4
JSMS10L -004
Screw
M10×10
1
5
JSMS10L -005
Indicator
1
6
JSMS10L -006
Flat washer
4
10
7
JSMS10L -007
Screw
M4×15
6
8
JSMS10L -008
Compress spring
1
9
JSMS10L -009
Miter knob
1
10
JSMS10L -010
Screw
M5×15
4
11
JSMS10L -011
Flat washer
5
15
12
JSMS10L -012
Sleeve
1
13
JSMS10L -013
Spring pin
5×10
4
14
JSMS10L -014
Screw
M4×10
11
15
JSMS10L -015
Body support
1
16
JSMS10L -016
Knob
2
17
JSMS10L -017
Fence
1
18
JSMS10L -018
Flat washer
8
4
19
JSMS10L -019
Spring washer
8
4
20
JSMS10L -020
Hex bolt
M8×30
4
21
JSMS10L -021
Adjustable knob
1
22
JSMS10L -022
Pin
1
23
JSMS10L -023
Compression spring
1
24
JSMS10L -024
Pin cap
1
25
JSMS10L -025
Spring pin
3×15
1
26
JSMS10L -026
Laser
1
27
JSMS10L -027
Laser holder
1
28
JSMS10L -028
Screw
M5×10
2
29
JSMS10L -029
Hex nut
M6
6
30
JSMS10L -030
Hex bolt
M6×40
1
31
JSMS10L -031
Torque spring
1
32
JSMS10L -032
Sleeve
1
33
JSMS10L -033
Screw
M5×10
2
34
JSMS10L -034
Pin shaft
1
35
JSMS10L -035
Hex bolt
M8×25
1
36
JSMS10L -036
Washer
1
37
JSMS10L -037
Out flange
1
38
JSMS10L -038
Spring washer
4
3
39
JSMS10L -039
Guard
1
40
JSMS10L -040
Saw blade
1
41
JSMS10L -041
Inner flange
1
42
JSMS10L -042
Power cord
1
43
JSMS10L -043
Fix plate
1
44
JSMS10L -044
Torque spring
1
45
JSMS10L -045
Safety plate
1
46
JSMS10L -046
Cover
1
47
JSMS10L -047
Spring washer
5
6
48
JSMS10L -048
Spring
1
49
JSMS10L -049
Shaft lock cap
1
50
JSMS10L -050
Shaft lock
1
51
JSMS10L -051
Screw
M5×30
8
52
JSMS10L -052
Screw
M4X14
1
53
JSMS10L -053
Handle
1

4
54
JSMS10L -054
Blade case
1
55
JSMS10L -055
Dust port
1
56
JSMS10L -056
Spring washer
6
3
57
JSMS10L -057
Screw
M6×20
3
58
JSMS10L -058
Tapping screw
M4×52
1
59
JSMS10L -059
Nut
M5
1
60
JSMS10L -060
Fix plate
1
61
JSMS10L -061
Screw
1
62
JSMS10L -062
Torque spring
1
63
JSMS10L -063
Screw
1
64
JSMS10L -064
Movable guard
1
65
JSMS10L -065
Center plate
1
66
JSMS10L -066
Washer
1
67
JSMS10L -067
Rod
1
68
JSMS10L -068
Screw
2
69
JSMS10L -069
Knob
1
70
JSMS10L -070
Screw
M4×10
2
71
JSMS10L -071
Screw
M6×15
4
72
JSMS10L-072
---072-072
Screw
M5×15
1
73
JSMS10L -073
Linear bearing
LM25UU
2
74
JSMS10L -074
Cushion
4
75
JSMS10L -075
Wool felt
4
76
JSMS10L -076
Plate
2
77
JSMS10L -077
Pin
2
78
JSMS10L -078
Sliding bar
2
79
JSMS10L -079
Joint holder
1
80
JSMS10L -080
Pivot
1
81
JSMS10L -081
Nut
M16
1
82
JSMS10L -082
Bevel knob
1
83
JSMS10L -083
Flat washer
16
1
84
JSMS10L -084
Flat washer
10
1
85
JSMS10L -085
Washer
6
1
86
JSMS10L -086
Screw
M6
1
87
JSMS10L -087
Steel ball
φ8
1
88
JSMS10L -088
Screw
M6×35
2
89
JSMS10L -089
Indicator
1
90
JSMS10L -090
Shaft
1
91
JSMS10L -091
Work table
1
92
JSMS10L -092
Screw
M6×15
1
93
JSMS10L -093
Steel C-washer
3
94
JSMS10L -094
Screw
1
95
JSMS10L -095
Support
1
96
JSMS10L -096
Nut
M4
2
97
JSMS10L -097
Laser guard
1
98
JSMS10L -098
Pole
1
99
JSMS10L -099
Knob
1
100
JSMS10L -100
Butterfly knob
2
101
JSMS10L -101
Pole holder
1
102
JSMS10L -102
Clamp plate
1
103
JSMS10L -103
Extension wing
2
104
JSMS10L -104
Knob
2
105
JSMS10L -105
Fence
1
106
JSMS10L -106
Laser switch
1
107
JSMS10L -107
Carbon brush cap
2
108
JSMS10L -108
Brush holder
2

5
109
JSMS10L -109
Carbon brush
2
110
JSMS10L -110
Motor rear cover
1
111
JSMS10L -111
Motor housing
1
112
JSMS10L -112
Tapping screw
ST4.2×10
2
113
JSMS10L -113
Dust bag
1
114
JSMS10L -114
Roller
1
115
JSMS10L -115
Clip
1
116
JSMS10L -116
Bearing
6304-2RZ
1
117
JSMS10L -117
Retainer
φ20
1
118
JSMS10L -118
Spindle
1
119
JSMS10L -119
Key
5×10
1
120
JSMS10L -120
Retainer
φ16
1
121
JSMS10L -121
Gear
1
122
JSMS10L -122
Bearing
6200
1
123
JSMS10L -123
Rotor
1
124
JSMS10L -124
Bearing
6201
1
125
JSMS10L -125
Tapping screw
ST4.2×18
6
126
JSMS10L -126
Handle upper cover
1
127
JSMS10L -127
Handle lower cover
1
128
JSMS10L -128
Screw
M5×10
4
129
JSMS10L -129
Nut
M5
4
130
JSMS10L -130
Power cord sleeve
1
131
JSMS10L -131
Transformer
1
132
JSMS10L -132
Switch
1
133
JSMS10L -133
Gear box
1
134
JSMS10L -134
Screw
M5×70
2
135
JSMS10L -135
Screw
1
136
JSMS10L -136
Anti-vibration cover
1
137
JSMS10L -137
Stator
1
138
JSMS10L -138
Left table insert
1
139
JSMS10L -139
Right table insert
1
140
JSMS10L -140
Base assembly
1
141
JSMS10L -141
Body support assembly
1
142
JSMS10L -142
Movable guard assembly
1
143
JSMS10L -143
Motor complete assembly 230V
1
144
JSMS10L -144
Spindle assembly
1
145
JSMS10L -145
Rotor assembly
1
146
JSMS10L -146
Handle assembly
1
147
JSMS10L -147
Bevel scale
1
148
JSMS10L -148
Length scale
1
149
JSMS10L -149
Miter scale
1
150
JSMS10L -150
Rivet
Ø2×3
2
151
JSMS10L -151
Screw
M4×10
3
152
JSMS10L -152
Clip
1
153
JSMS10L -153
Big washer
4
1
154
JSMS10L -154
Tapping screw
ST4.2×12
6
155
JSMS10L -155
Cover
1
156
JSMS10L -156
Clamp assembly
1
157
JSMS10L -157
Extension wing assembly
1
158
JSMS10L -158
Wrench
6
1
159
JSMS10L -159
Wrench
1
160
JSMS10L -160
Capacitor
CB244-B
1
161
JSMS10L -161
Strain relief
1
162
JSMS10L -162
Wire clip(A) assembly
1
163
JSMS10L -163
Tapping screw
ST2.9×8
2
164
JSMS10L -164
Baffle plate
1
165
JSMS10L -165
Magnet ring Assembly
Ø8
4
166
JSMS10L -166
Screw
M5×10
2
167
JSMS10L -167
Wire clip(B) assembly
1
168
JSMS10L -168
Warning label
3
Other manuals for JSMS-10L
1
Table of contents
Other Jet Saw manuals
Popular Saw manuals by other brands

Milwaukee
Milwaukee Super Sawzall 6537-22 Operator's manual
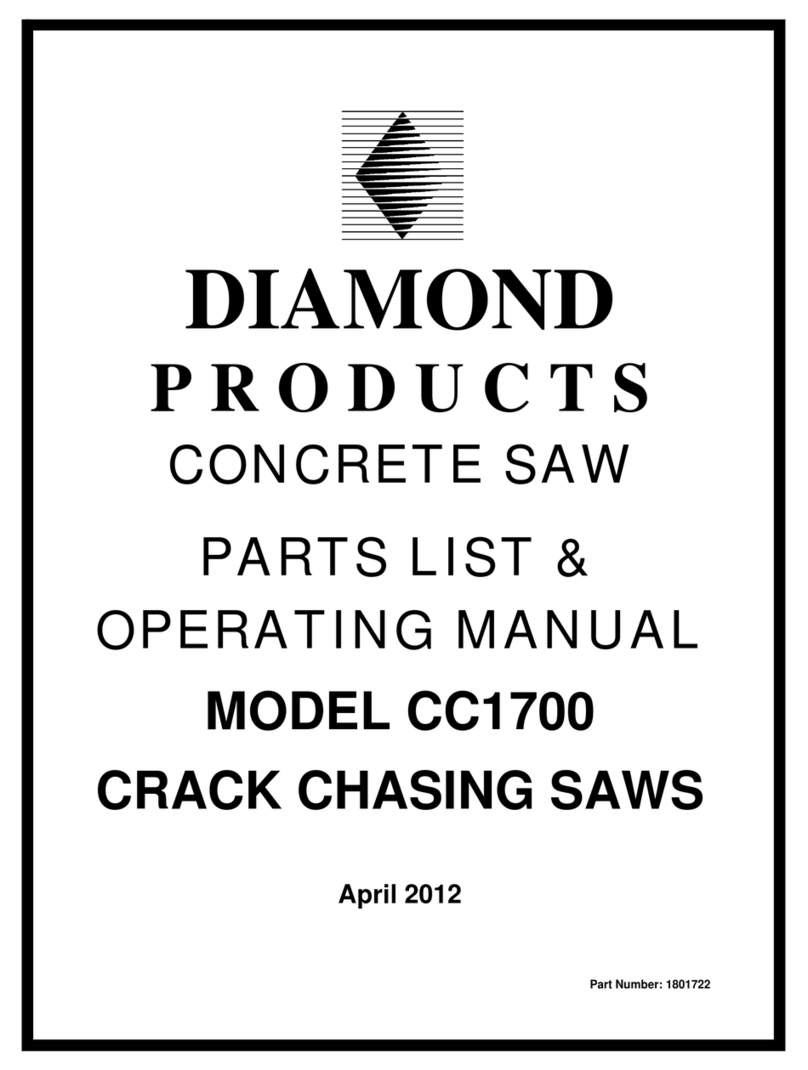
Diamond Products
Diamond Products CC1700 Parts list & operating manual
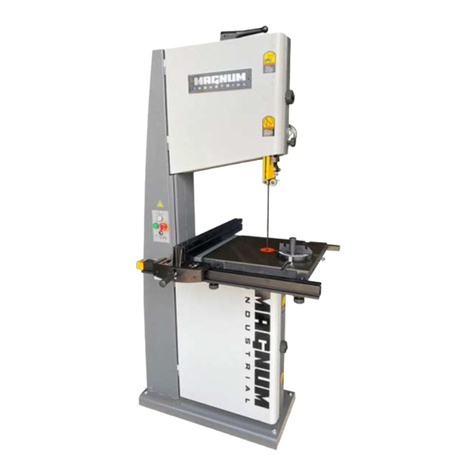
Magnum Industrial
Magnum Industrial MI-91600 operating manual

jcb
jcb JCB-20RS Instructions & user's manual

Woodtec
Woodtec XW054 instruction manual
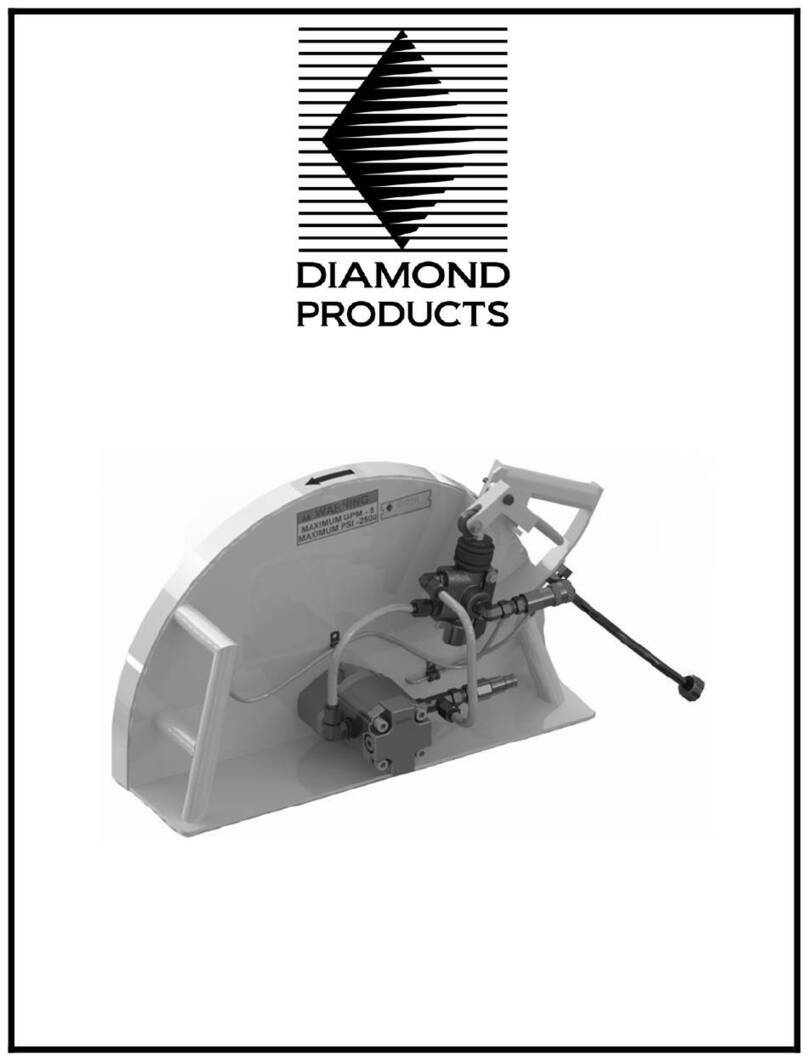
Diamond Products
Diamond Products HS-24-F-8 parts manual