LG G3F-AD4A User manual

User’s Manual
LG Programmable Logic Controller
LG Industrial Systems
G3F-AD4A
G3F-AD4B
G4F-AD2A

Be sure to read carefully the safety precautions given in data sheet and user’s manual before operating the module
and follow them.
The precautions explained here only apply to the G3F-AD4A , G3F-AD4B and G4F-AD2A.
For safety precautions on the PLC system, see the GLOFA GM3/4 CPU User’s Manuals and MASTER-
K200S/300S/1000S CPU User’s Manuals.
A precaution is given with a hazard alert triangular symbol to call your attention, and precautions are represented
as follows according to the degree of hazard.
However, a precaution followed with can also result in serious conditions.
Both of two symbols indicate that an important content is mentioned, therefore, be sure to observe it.
Keepthismanualhandyforyourquick reference in necessary.
SAFETY PRECAUTIONS
WARNING
!
If not provided with proper prevention, it can cause death or fatal
injury or considerable loss of property.
CAUTION
!
If not properly observed, it can cause a hazard situation to result
in severe or slight injury or a loss of property.
CAUTION
!
CAUTION
!
Design Precautions
▶Do not run I/O signal lines near to
high voltage line or power line.
Separate them as 100 mm or
more as possible. Oth
erwise,
noise can cause module ma
l-
function.
CAUTION
!
Installation Precautions
▶
Operate the PLC in the environ-
ment conditions given in the
generalspecifications.
▶If operated in other envi
ronment
not specified in the general
specifications, it can cause an
electric shock, a fire, malfunction
or damage or degradation of the
module
▶Make sure the module fixing pro-
jections is inserted into the mo
d-
ule fixing hole and fixed.
▶Improper installation of the mo
d-
ule can cause malfunction, di
s-
order or falling.

CAUTION
!
WiringPrecautions
▶When grounding a FG terminal, be sure to provide class 3 grounding which is dedicated to
the PLC.
▶Before the PLC wiring, be sure to check the rated voltage and terminal arrangement for
the module and observe them correctly.
If a different power, not of the rated voltage, is applied or wrong wiring is provided, it can
cause a fire or disorder of the nodule.
▶
Drive the terminal screws firmly to the defined torque.
If loosely driven, it can cause short circuit, a fire or ma
lfunction.
▶
Be careful that any foreign matter like wire scraps should not enter into the module.
It can cause a fire, disorder or malfunction.
WARNING
!
Test Run and Maintenance
Precautions
▶Do not contact the terminals
while the power is applied.
It can cause malfunction.
▶
When cleaning or driving a term
i-
nal screw, perform them after the
power has been turned off
▶Do not perform works while the
power is applied, which can
cause disorder or malfunction.
CAUTION
!
▶
Do not separate the module from
the printed circuit board(PCB), or
do not remodel the module.
They can cause disorder, mal-
function, damage of the module
ora fire.
When mounting or dismounting
the module, perform them after
the power has been turned off.
▶
Do not perform works while the
power is applied, which can
cause disorder or malfunction.
CAUTION
!
Waste Disposal Precautions
▶When disposing the module, do it as an industrial waste.

◎
CONTENTS
◎
Chapter1. INTRODUCTION
1.1 Features·································································································································································1-1
1.1.1 G3F-AD4A/G3F-AD4B ··································································· 1-1
1.1.2 G4F-AD2A ············································································ 1-1
1.2 Glossary·································································································································································1-2
1.2.1 A-Analog Value ········································································ 1-2
1.2.2 D-DigitalValue ········································································· 1-2
1.2.3 Analog / DigitalConversion Characteristics ·················································· 1-3
Chapter2. SPECIFICATIONS
2.1 General Specifications ··································································································································2-1
2.2 Performance Specifications ·······················································································································2-2
2.3 Names of Parts and Functions ··················································································································2-3
2.3.1 G3F-AD4A ············································································ 2-3
2.3.2 G4F-AD2A ············································································ 2-5
2.3.3 G3F-AD4B ············································································ 2-6
2.4 I/O Conversion Characteristics ·················································································································2-7
2.4.1 G3F-AD4A I/OCharacteristics ··························································· 2-8
1) Voltage Input Characteristics ······························································ 2-9
2) Current Input Characteristics ····························································· 2-10
3) Simultaneous Voltage andCurrent Input Characteristics ········································2-11
2.4.2 G4F-AD2A I/OCharacteristics ··························································· 2-12
1) Voltage Input Characteristics ····························································· 2-12
2) Current Input Characteristics······························································ 2-14
3) Simultaneous Voltage andCurrent Input Characteristics ······································· 2-15
2.4.3 G3F-AD4B I/OCharacteristics ··························································· 2-16
1) Voltage Input Characteristics ····························································· 2-17
2) Current Input Characteristics······························································ 2-17
3) Simultaneous Voltage andCurrent Input Characteristics ······································· 2-18
4)The connection between Analog input and Digital output ······································· 2-18

2.4.4 The connection between Offset/ Gain Setting andDigital OutputValue ··························· 2-19
1) Resolution ··········································································· 2-19
2) Relations between Maximum Resolution and Digital Output Value ······························· 2-19
3) Offset/ Gain Setting ··································································· 2-20
(1) Offset/G ain Setting of the G3F-AD4A ················································· 2-20
(2) Offset/G ain Setting of the G4F-AD2A ·················································· 2-22
2.5 A/D Conversion Characteristics················································································································2-24
2.5.1 FilterProcessing ······································································ 2-24
2.5.2 Sampling Processing (Instantaneous Value) ················································ 2-25
2.5.3 Average Processing ··································································· 2-25
Chapter3. INSTALLATIONANDWIRING
3.1 Installation ··························································································································································3-1
3.1.1 Installation Ambience ···································································· 3-1
3.1.2 Handling Precautions ··································································· 3-1
3.2 Wiring ···································································································································································3-2
3.2.1 Wiring Precautions ····································································· 3-2
3.2.2 Wiring Examples ······································································· 3-2
1) G3F-AD4A ············································································ 3-2
2) G4F-AD2A ············································································ 3-3
3)G3F-AD4B ············································································ 3-4
Chapter4.FUNCTIONBLOCK
4.1 Insertion of theFunctionBlock for the A/D Conversion ModuleontheGMWIN ················4-1
4.2 LocalFunction Block ·····································································································································4-2
4.2.1 Module Initializ ation(G3F-AD4A: AD4INI, G4F-AD2A: AD2INI, G3F-AD4B: AD4BINI) ················ 4-2
4.2.2 Module Reading -Array Type (G3F-AD4A:AD4ARD,G4F-AD2A:AD2ARD, G3F-AD4B:AD4BARD) ····· 4-3
4.2.3 Module Reading -Single Type (G3F-AD4A:AD4RD,G4F-AD2A:AD2RD, G3F-AD4B:AD4BRD) ········ 4-3
4.3 Remote Function Block ································································································································4-4
4.3.1 Module Initialization (G3F-AD4A: AD4RINI, G4F-AD2A: ADR2INI, G3F-AD4B: ADR4BINI) ············ 4-4
4.3.2 Module Reading (G3F-AD4A: ADR4RD, G4F-AD2A: ADR2RD, G3F-AD4B: ADR4BRD) ·············· 4-5
4.4 Errors onFunction Block ····························································································································4-6
Chapter5. GM PROGRAMMING

5.1 Programming for Distinction of A/DConversion Value····································································5-1
5.2 Programming for Display of A/DConversion Value and Error Code on BCD Display ········5-7
5.3 Programming for Loading the A/DConversion Module onRemoteI/O Station ················5-10
Chapter6. BUFFER MEMORYCONFIGURATIONANDFUNCTION
6.1 Buffer Memory Configuration ····················································································································6-1
6.1.1 G3F-AD4A ············································································ 6-1
6.1.2 G 3F-AD4B ············································································ 6-2
6.1.3 G4F-AD2A ············································································· 6-4
6.2 Buffer Memory Functions·······························································································································6-5
6.2.1 Available ChannelSpecificationArea ······················································· 6-5
6.2.2 Input Used Type Specification Area ························································· 6-5
6.2.3 DataOutput Type SpecificationArea ······················································· 6-6
6.2.4 Filter Processing Enable/Disable SpecificationArea ··········································· 6-6
6.2.5 Filter ConstantSetting Area ······························································ 6-7
6.2.6 Average Processing Enable/Disable SpecificationArea ········································ 6-8
6.2.7 Number/Time Average Processing Area ···················································· 6-9
6.2.8 AverageNumber/Time ConstantSetting Area ··············································· 6-10
6.2.9 SET Data Specification Area ···························································· 6-10
6.2.10 Digital Value O utput Area ·······························································6-11
6.2.11 Channel Operation Data Storage Area ·····················································6-11
6.2.12 ErrorCode Display Area ································································6-11
Chapter7.SPECIAL MODULE COMMAND (Buffer Memory READ / WRITE)
7.1 Local Command ···············································································································································7-1
7.1.1 Internal Memory Read -GET,GETP ························································ 7-1
7.1.2 Internal memory Write -PUT, PUTP ························································· 7-2
7.2 Remote Command ··········································································································································7-3
7.2.1 BufferM emory Read –RGET ····························································· 7-3
7.2.2 BufferM emory Write –RPUT ····························································· 7-4
Chapter8.MK PROGRAMMING

8.1 Basic Programming ········································································································································8-1
8.1.1 G3F-AD4A ············································································ 8-1
8.1.2 G4F-AD2A ············································································ 8-2
8.2 Application Programming ···························································································································8-3
8.2.1 Programming for Distinction of A/DConversion Value ·········································· 8-3
8.2.2 Programming for Display of A/DConversion Value and Error Code on BCD Display ·················· 8-5
8.2.3 Programming for Loadin g the A/DConversion Module on Remote I/OStation ······················· 8-7
Chapter9. TROUBLESHOOTING
9.1 Error Code ··························································································································································9-1
9.1.1 ErrorCode Indicated by RUN LEDFlickering ················································ 9-1
9.2 Troubleshooting·················································································································································9-2
9.2.1 RUN LEDFlickering ···································································· 9-2
9.2.2 RUN LEDOff ·········································································· 9-2
9.2.3 Digital ValueUnreadable from the CPU Module ·············································· 9-3
9.2.4 Sudden DigitalValue Change ····························································· 9-3
9.2.5 Analog and Digital ValueMismatch························································· 9-4
9.2.6 A/D Conversion Module Hardware F ault ···················································· 9-4
Chapter10. DIMENSIONS
10.1 G3F-AD4A, G3F-AD4B Dimensions ····································································································10-1
10.2 G4F-AD2A Dimensions ·····························································································································10-2

Chapter 1. INTRODUCTION
1 -1
Chapter1.INTRODUCTION
The G4F-AD2A, G3F-AD4A and G3F-AD4B are analog/digital conversion modules for use with the GLOFA PLC GM 1/2/3/4
series CPU module and the MASTER-K PLC K300S/1000S Series CPU module. The G4F-AD2A is used on GM4 series
moduleand the K300S series module, and the G3F-AD4A and G3F-AD4B is used on the GM1/2/3 series module and the
K1000S series module. (Hereafter the G4F-AD2A, G3F-AD4A and G3F-AD4B are called the A/D conversion module) The
A/D conversion module is to convert an analog input signal (voltage or current) from external sensors into a 14-bit binary
digitalvalue.
1.1.1 G3F-AD4A/ G3F-AD4B
1)16-Channel analog to digital conversion is possible with a single module.
The G3F-AD4A and G3F-AD4B hav e 16-Channel A/D conversion capacity, with each channel selectable for
voltage or current input.
2) High resolution of 1/16000
High-resolution digital values can be obtained. Resolution setting applies to all channels.
4) The number of the G3F-AD4A used on one base is unlimited.
1.1.2 G4F-AD2A
1)4-Channel analog to digital conversion is possible with a single module.
The G3F-AD2A has 4-Channel A/D conversion capacity, with each channel selectable for voltage or current
input.
2)Highresolutionof1/16000
High-resolution digital values can be obtained. Resolution setting applies to all channels.
3) The number of the G4F-AD2A used on one base is unlimited.
1.1 Features

Chapter 1. INTRODUCTION
1 -2
[Fig 1.1] AnalogValue [Fig 1.2] Transducer
1.2.1 A-AnalogValue
Analog value is a sequentially changing value such as voltage, current, temperature, speed, pressure, flux, etc.
Temperature, for example, is sequentially changing according to the time. Because this temperature is not input
on the PLC through transducer, the same analog value of DC voltage (0 to ±10V) or current (4 to 20 mA) in
accordance with the temperature should be inputted on the PLC.
1.2.2 D-DigitalValue
Digitalvalue is non-sequentially changing value written as the number like 0,
1, 2, 3. The signal of on or off iswritten as digital value of 0 or 1.
There are BCD value and binary value in the range of digital value.
Analog value isn't written directly onto the CPU. For analog input to the
CPU operation, analog converted to digital value has to be inputted onto
the CPU and for analog output, the digital value of the CPU should be
converted toanalog value.
1.2 Glossary
Transducer
Analog input
0 to±10 V or
0 to±20 mA
Analog output
0 to±10 V or
0 to±20 mA
[Fig 1.3] Digital Value
[Fig 1.4] PLC Processing
Time

Chapter 1. INTRODUCTION
1 -3
1.2.3 Analog/ Digital Conversion Characteristics
1)Voltage input
[Fig 1.5] A/D Conversion Characteristics(VoltageInput)
Analog/digital conversion module allows external analog input to be converted to digital value and to be operated
in the CPU. On voltage input, input of –10Vleads to digital value of 0 and 10 Vto 16000.
Input of 1.25 mV is equal to digital value of 1. Therefore, input less than 1.25 mV shouldn't be converted but
ignored.
2)Current input
[Fig 1.6] A/D Conversion Characteristics(Currentinput)
On current input, input of -20mAleads to digital value of 8000 and 20mA to 16000. Input of 2.5㎂is equal to
digital value of 1. Therefore, input less than 2.5㎂shouldn't be converted but ignored.
Analoginputcurrent Current input
Input Voltage
Input Current
Input Voltage

Chapter 2. SPECIFICATIONS
2 - 1
Chapter 2 . SPECIFICATIONS
Table 2.1 shows the general specifications of GLOFA GM series and MASTER-K series.
No Item Specifications Standard
1 Operating ambient
tem
p
erature 0 ~ 55℃
2 Storage ambient
tem
p
erature -25 ~ 70℃
3 Operating ambient
humidit
y
5 ~ 95%RH, non-condensing
4 Storage ambient
humidity 5 ~ 95%RH, non-condensing
Occasional vibration
Frequency Acceleration Amplitude Sweep count
10≤f∠57 Hz - 0.075 mm
57 ≤f≤150 Hz 9.8㎨
{
1G
}
-
Continuos vibration
Frequency Acceleration Amplitude
10≤f∠57 Hz - 0.035 mm
5 Vibration
57≤f≤150 Hz 4.9㎨
{
0.5G
}
-
10 times in each
direction for
X, Y, Z
IEC 61131-2
6 Shocks
*Maximum shock acceleration: 147㎨{15G}
*Duration time :11 ms
*Pulse wave: half sine wave pulse( 3 times in each of X, Y and Z directions )
IEC 61131-2
Square wave impulse noise ±1,500 V
Electrostatic discharge Voltage :4kV(contact discharge) IEC 61131-2
IEC 1000-4-2
Radiated electromagnetic field 27 ~ 500 MHz, 10 V/m IEC 61131-2
IEC 1000-4-3
Severity
Level All power
modules
Digital
I/Os
( Ue
≥
24 V)
Digital I/Os
(Ue <24 V)
Analog I/Os
communication
I/Os
7 Noise immunity
Fast transient burst noise
Voltage 2 kV 1 kV 0.25 kV
IEC 61131-2
IEC 1000-4-4
8 Operating atmosphere
Free from corrosive gases and excessive dust
9 Altitude for use Up to 2,000m
10 Pollution degree 2 or lower
11 Cooling method Self-cooling
[Table 2.1 ] General specifications
REMARK
1) IEC(International Electrotechnical Commission)
: The international civilian organization which produces standards for electrical and electronics industry.
2) Pollution degree
: It indicates a standard of operating ambient pollution level.
The pollution degree 2 means the condition in which normally, only non-conductive pollution occurs.
Occasionally, however, a temporary conductivity caused by condensation shall be expected.
2.1 General Specifications

Chapter 2. SPECIFICATIONS
2 - 2
Table 2-2 shows performance specifications of A/D conversion module.
Specifications
Items G3F-AD4A G4F-AD2A G3F-AD4B
I/O points 16 points
Voltage –5 ~ 5 VDC (input resistance 560㏀)
–10 ~ 10 VDC (input resistance 560㏀) 1 ~ 5 VDC
(input resistance 560㏀)
Current DC –20 ~ 20 mA (input resistance 250Ω) 4 ~ 20 mA
(input resistance 250Ω)
Analog input
Voltage/Current
selection
*. Select with the Input conversion
switch on the side of the module
(on: current, off: voltage)
*. When current input is used, set the
Input range switch to V1 / I.
*. Select in accordance with the
Input terminals.
*. Connect the V terminal with the
I terminal on the use of
current input.
*. Select with the Input conversion
switch on the side of the module
(on: current, off: voltage)
*. Select with program initial F/B
(input variable:IN_SEL, 0:current,
1:voltage)
Digital output *. 16-bit (data: 14bit)signed binary
*. May be set per channel by setting output data
("0": -192 to 16191, "1": -8192 to 8191)
*. 16-bit (data: 14bit)signed binary
("0": 0 to 16000, "1": -8000
to 8000)
1 ~ 5 VDC - 0.25 mV (1/16000)
-5 ~ 5 VDC 0.625 mV (1/16000) -
-10 ~ 10 VDC 1.25 mV (1/16000) -
DC 4 ~20 mA - 1.0 ㎂(1/16000)
Maximum
resolution
DC -20 ~20 mA 0.0025 mA (1/16000) -
Overall Accuracy(%) ±0.5% or lower
(accuracy to full scale)
(±0.3% at ambient temperature 25℃)
±0.2% or lower
(accuracy to full scale)
±0.5% or lower
(accuracy to full scale)
(±0.3% at ambient temperature 25℃
Maximum conversion speed
(
ms/channel
)
3.0 5.0 3.0
Maximum absolute input Voltage(V):±12, Current (mA):±25
Number of analog input point 16 channels/module 4 channels/module 16 channels/module
Isolation Between input terminals and PLC: Photo coupler isolation
(Between channels : Non-isolated)
Terminals connected 38-point terminal block 20-point terminal block 38-point terminal block
Internal current
consumption(A)
0.67 A 0.4 A 0.54 A
Weight (g) 630 360 560
[Table 2.2] Performance Specifications
CAUTION
The offset / gain value of G3F-AD4B A/D conversion module at factory has been fixed. Therfore it is not
Changed.
2.2 Performance Specifications
!

Chapter 2. SPECIFICATIONS
2 - 3
The names of parts and functions of the A/D conversion module are shown as below.
2.3.1 G3F-AD4A
The names of parts and functions of the A/D conversion module are shown
2.3 Names of Parts and Functions
②
③
④
⑤

Chapter 2. SPECIFICATIONS
2 - 4
No Descriptions
RUN LED
①
Indicates the operating status of the G3F-AD4A
(1) On : Normal operation
(2) Flicker : An error has occurred. (For moreinformation, see the General Section 4.1)
(3) Off : DC 5 V power-off or G3F-AD4A module fault.
Offset Trimmer
②
Used to make micro adjustment of an offset value.
Gain Trimmer
③
Used to make micro adjustment of a gain value.
Input range switch
④
- On factory set, the voltage range has to be set to from -10 to 10 VDC.
(1) Set to voltage
(2) Set to current
Input select switch
⑤
(1) Used to select the analog input(voltage or current input) of each channel
-Set to OFF to use voltage input. -Set to ON to uses current input.
(2) On factory set, it has to be set to voltage input condition. (Every Dip Switch is off.)
V1 : Voltage range -5 ~ 5 VDC
V2 : Voltage range -10 ~ 10 VDC
: Unusable
I : Current range -20 ~ 20 mA

Chapter 2. SPECIFICATIONS
2 - 5
2.3.2 G4F-AD2A
This section shows the names of parts and functions of G4F-AD2A module.
No Descriptions No
Descriptions
←RUN LED ↓GAIN switch
A
d
j
ust upward, and the analo
g
input value o
f
corresponding channels is stored as a gain value.
Input range select switch
Indicates the operating status of the G4F-AD2A.
Normal mode: channel switch's setting range: 4 to F
- ON : Normal operation.
- Flicker : An error hasoccurred.
- OFF : DC5V power-off or G3F-AD4A module fault.
Test mode: channel switch's range: 0 to 3
- Flicker(per 1.0sec) : No operation of offset/gain switch.
-ON :Offset/
g
ain switch ad
j
usted upward.
- Flicker(per 0.2sec) : offset/gain setting error.
Offset switch
↑
A
d
j
ust upward, and the analo
g
input value of correspondin
g
channels is stored as an offset value.
Channel switch for the test mode
→
Correspondin
g
channels will be selected in the ad
j
ustment o
f
offset/gain value. (Valid range: 0 to 3 )
°
* Don’t put the input switch on or
* It leads to malfunction.
Analog input Switch
-10 ~ 10 VDC
Voltage -5 ~ 5 VDC
Current -20 ~ 20 mA

Chapter 2. SPECIFICATIONS
2 - 6
2.3.3 G3F-AD4B
Description
←
RUN LED
Indicates the operating status of G3F-AD4B
↑
Selection switch of voltage/current
1) The switch status at voltage selection
TheswitchlocatesOFFstatus.
2) The switch status at current selection
TheswitchlocatesONstatus.
G3F-AD4B
On
1 2 3 4 5 6 7 8
On
1 2 3 4 5 6 7 8
On
1 2 3 4 5 6 7 8
On
1 2 3 4 5 6 7 8
②
1~5V
4~20mA

Chapter 2. SPECIFICATIONS
2 - 7
Input / Output (hereafter I/O) conversion characteristics are expressed by the angle of the line connecting the
offset value and gain value used to convert the analog signals, input to the PLC into digital values.
The I/O conversion characteristics of the A/D conversion module are shown as below.
[Fig 2.1] I/O Conversion Characteristics
2.4 I/O Conversion Characteristics
G3F-AD4A
G4F-AD2A
Practical analog input range
Gain value
Offset value
Ran
g
e: - 10 ~ 10 VDC
Ran
g
e: - 5 ~ 5 VDC
Ran
g
e: - 20 ~ 20 mA
Practical analog input range
Gain value
Offset value
Ran
g
e: - 10 ~ 10 VDC
Ran
g
e: - 5 ~ 5 VDC
Ran
g
e: - 20 ~ 20 mA
A
nalo
g
Input
A
nalo
g
Input
Di
g
ital
Output
Value
Di
g
ital
Output
Value

Chapter 2. SPECIFICATIONS
2 - 8
2.4.1 G3F-AD4A I/O Characteristics
The G3F-AD4A allows voltage or current input to be selected per channel by the input select switch.
Offset / gain setting is performed for 16 channels in block.
1) Voltage Input Characteristics
For voltage input, the input select switch of each channel is set to "off".
a) Range : -10 ~ 10 VDC
-The analog input range switch has to be set to downward (V2).
-The digital output value according to voltage input characteristics will be shown as below.
Analog input voltage
Digital output
range -10.24V -10 V 0 V 1 V 5 V 10V 10.24V
-192~16191 -192 0 8000 8800 12000 16000 16191
-8192~8191 -8192 -8000 0 800 4000 8000 8191
Position of Input select switch
- Off : Voltage
(On the left side of the Module)
Position of Analog input range switch
<On the front side of the module>
V1/ I (–5~5 VDC select)
V2
(
–
10~10 VDC select
)
A
nalo
g
in
p
ut
(
volta
g
e
)
Analog Input (Voltage)
Digital
Output
Value
-10.24 V -10 V 0 V 1 V 5 V 10 V 10.24 V
Channel number

Chapter 2. SPECIFICATIONS
2 - 9
b) Range: -5 ~ 5 VDC
-The analog input range switch has to be set upward (V1/ I)
The wa
y
to set analo
g
in
p
ut
r
an
g
e switch
<
The front side of the module
>
-The digital output value according to voltage input characteristics will be shown as below.
Analog input voltage
Digital output
range -5.12 V -5 V 0 V 1 V 3 V 5 V 5.12 V
-192~16191 -192 0 8000 9600 12800 16000 16191
-8192~8191 -8192 -8000 0 1600 4800 8000 8191
V1/ I (–5~5 VDC select)
V2 (–10~10 VDC select)
Digital
Output
Value
Analog Input Value (Voltage)
-5.12 V –5 V 0 V 1 V 3 V 5 V 5.12 V

Chapter 2. SPECIFICATIONS
2 - 10
2) Current Input Characteristics
- For current input, the input select switch of each channel is set to "on".
Analog input range switch has to be set upward (V1/ I).
Input select switch position Analog input range switch position
- The digital output value according to current input characteristics will be shown as below.
Analog input current
Digital output
range -20.48 mA -20 mA 0 mA 4 mA 12 20 20.48 mA
-192~16191 -192 0 8000 9600 12800 16000 16191
-8192~8191 -8192 -8000 0 1600 4800 8000 8191
V1/ I (DC –20~20mA)
V2 (Current input disable)
Digital
Output
Value
Analog Input Value (Voltage)
-20.48 m-20mA 0mA 4mA 12mA 20mA20.48mA
9600
This manual suits for next models
2
Table of contents
Other LG Controllers manuals
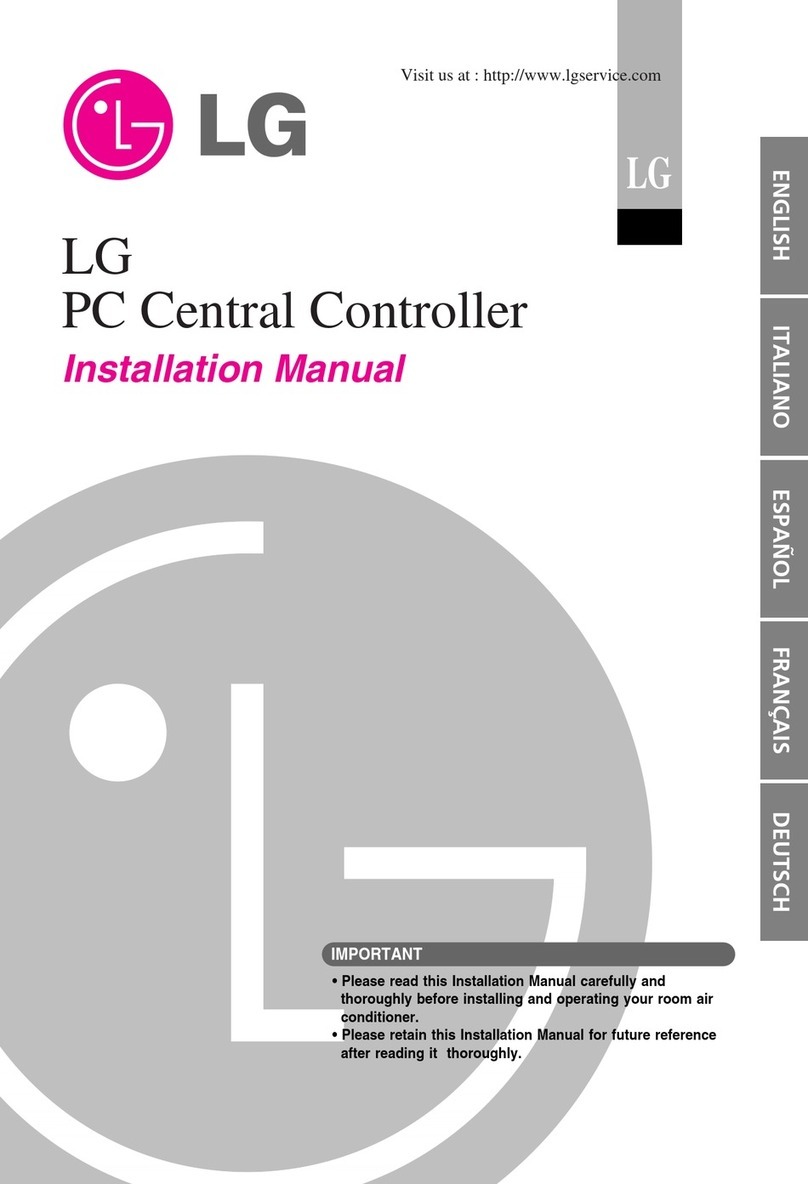
LG
LG PC Central Controller User manual
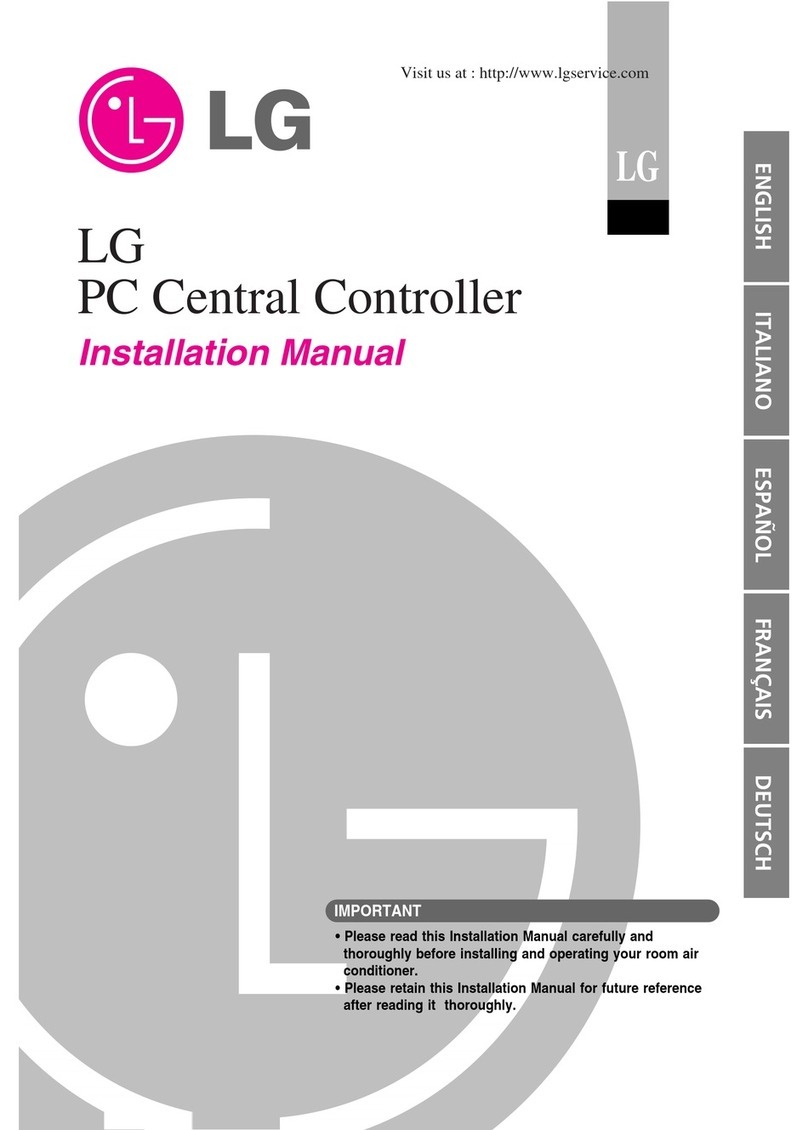
LG
LG PC Central Controller User manual

LG
LG PQCSA001T0 Quick start guide
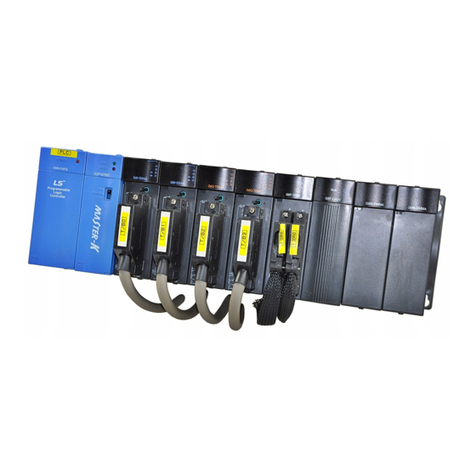
LG
LG MASTER-K200S User manual

LG
LG PRCKA0 User manual
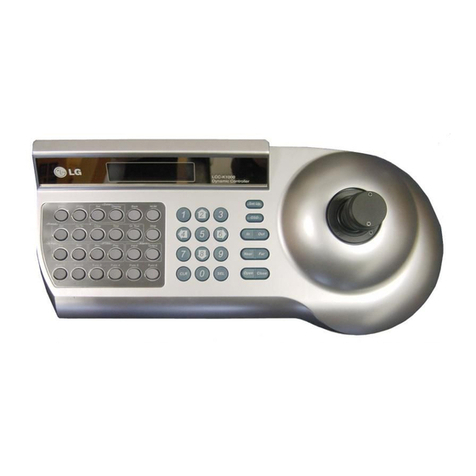
LG
LG LCC-K1000 User manual
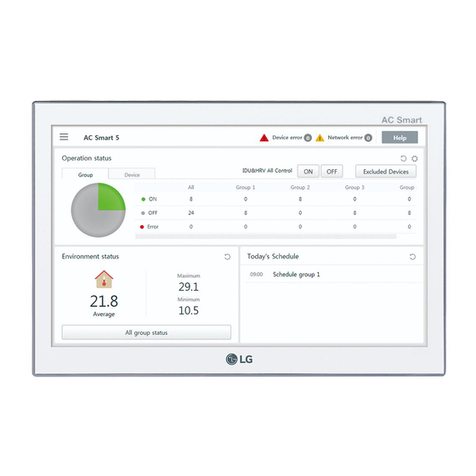
LG
LG AC Smart 5 User manual
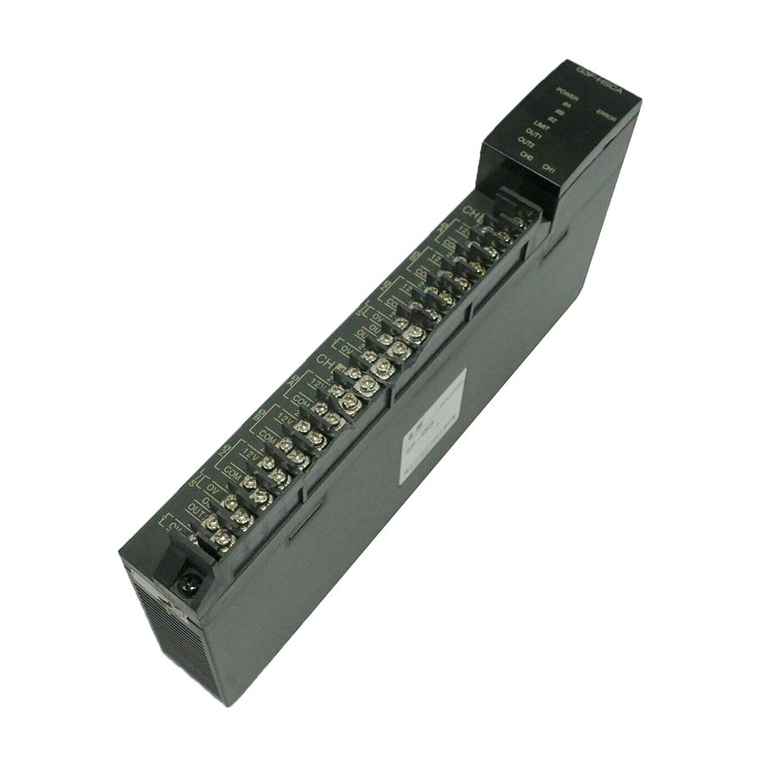
LG
LG MASTER-K Series User manual
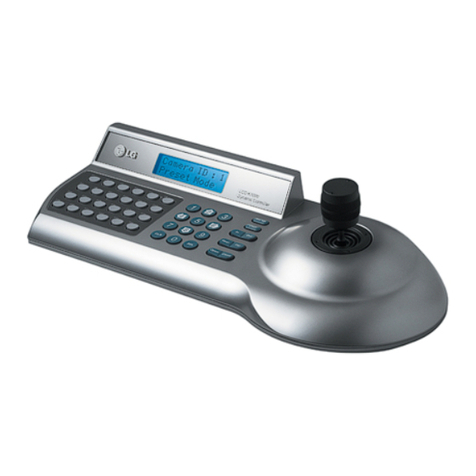
LG
LG LKD1000 User manual
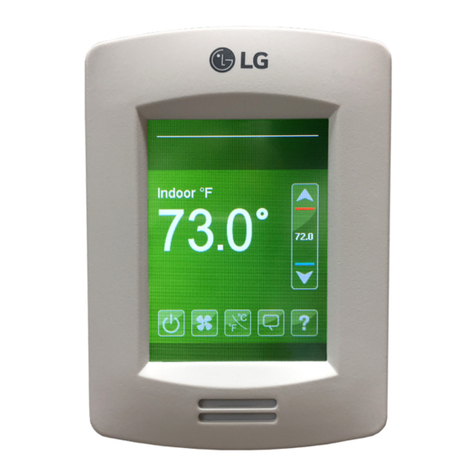
LG
LG MultiSITE MS8000 Series User manual