LG GLOFA G3F - RD3A User manual

User’s Manual
LG Programmable Logic Controller
G3F –RD3A
G4F –RD2A
GLOFA
LG
Industrial Systems

◎
CONTENTS
◎
Chapter 1. INTRODUCTION
1.1 Features
⋯⋯⋯⋯⋯⋯⋯⋯⋯⋯⋯⋯⋯⋯⋯⋯⋯⋯⋯⋯⋯⋯⋯⋯⋯⋯⋯⋯⋯⋯⋯⋯
1 –1
1.2 Glossary
⋯⋯⋯⋯⋯⋯⋯⋯⋯⋯⋯⋯⋯⋯⋯⋯⋯⋯⋯⋯⋯⋯⋯⋯⋯⋯⋯ ⋯⋯⋯⋯⋯
1 –2
1.2.1 A –Analog Value ⋯⋯⋯⋯⋯⋯⋯⋯⋯⋯⋯⋯⋯⋯⋯⋯⋯⋯⋯⋯⋯⋯⋯⋯⋯⋯⋯ 1 –2
1.2.2 D –Digital Value ⋯⋯⋯⋯⋯⋯⋯⋯⋯⋯⋯⋯⋯⋯⋯⋯⋯⋯⋯⋯⋯⋯⋯⋯⋯⋯⋯ 1 –2
1.2.3 PT ⋯⋯⋯⋯⋯⋯⋯⋯⋯⋯⋯⋯⋯⋯⋯⋯⋯⋯⋯⋯⋯⋯⋯⋯⋯⋯⋯⋯⋯⋯⋯⋯ 1 –2
1.2.4 Burn-out function ⋯⋯⋯⋯⋯⋯⋯⋯⋯⋯⋯⋯⋯⋯⋯⋯⋯⋯⋯⋯⋯⋯⋯⋯⋯⋯⋯ 1 –2
Chapter 2. SPECIFICATIONS
2.1 General Specifications
⋯⋯⋯⋯⋯⋯⋯⋯⋯⋯⋯⋯⋯⋯⋯⋯⋯⋯⋯⋯⋯⋯⋯⋯⋯⋯⋯
2 –1
2.2 Performance Specifications
⋯⋯⋯⋯⋯⋯⋯⋯⋯⋯⋯⋯⋯⋯⋯⋯⋯⋯⋯⋯⋯⋯⋯⋯⋯
2 –2
2.3 Names of Parts and Functions
⋯⋯⋯⋯⋯⋯⋯⋯⋯⋯⋯⋯⋯⋯⋯⋯⋯⋯⋯⋯⋯⋯⋯⋯
2 –3
2.3.1 G3F-RD3A ⋯⋯⋯⋯⋯⋯⋯⋯⋯⋯⋯⋯⋯⋯⋯⋯⋯⋯⋯⋯⋯⋯⋯⋯⋯⋯⋯⋯⋯⋯⋯ 2 –3
2.3.2 G4F-RD2A ⋯⋯⋯⋯⋯⋯⋯⋯⋯⋯⋯⋯⋯⋯⋯⋯⋯⋯⋯⋯⋯⋯⋯⋯⋯⋯⋯⋯⋯⋯⋯ 2 –4
2.4 RTD Input Module Characteristics
⋯⋯ ⋯⋯⋯⋯⋯⋯⋯⋯⋯⋯⋯⋯⋯⋯⋯⋯⋯⋯⋯
2 –5
2.4.1 Temperature Conversion Characteristics ⋯⋯⋯⋯⋯⋯⋯⋯⋯⋯⋯⋯⋯⋯⋯⋯⋯⋯⋯ 2 –5
2.4.2 Conversion Speed ⋯⋯⋯⋯⋯⋯⋯⋯⋯⋯⋯⋯⋯⋯⋯⋯⋯⋯⋯⋯⋯⋯⋯⋯⋯⋯⋯ 2 –5
2.4.3 Accuracy ⋯⋯⋯⋯⋯⋯⋯⋯⋯⋯⋯⋯⋯⋯⋯⋯⋯⋯⋯⋯⋯⋯⋯⋯⋯⋯⋯⋯⋯⋯⋯ 2 –5
2.4.4 Burn-out Function ⋯⋯⋯⋯⋯⋯⋯⋯⋯⋯⋯⋯⋯⋯⋯⋯⋯⋯⋯⋯⋯⋯⋯⋯⋯⋯⋯ 2 –6
2.5 Connection between a Pt and RTD Input Module
⋯⋯⋯⋯⋯⋯⋯⋯⋯⋯⋯⋯⋯⋯⋯
2 –7
Chapter 3. INSTALLATION AND WIRING
3.1 Installation
⋯⋯⋯⋯⋯⋯⋯⋯⋯⋯⋯⋯⋯⋯⋯⋯⋯⋯⋯⋯⋯⋯⋯⋯⋯⋯⋯⋯⋯⋯⋯
3 –1
3.1.1 Installation Ambience ⋯⋯⋯⋯⋯⋯⋯⋯⋯⋯⋯⋯⋯⋯⋯⋯⋯⋯⋯⋯⋯⋯⋯⋯⋯⋯ 3 –1
3.1.2 Handling Precautions ⋯⋯⋯⋯⋯⋯⋯⋯⋯⋯⋯⋯⋯⋯⋯⋯⋯⋯⋯⋯⋯⋯⋯⋯⋯⋯⋯ 3 –1
3.2 Wiring Precautions
⋯⋯⋯⋯⋯⋯⋯⋯⋯⋯⋯⋯⋯⋯⋯⋯⋯⋯⋯⋯⋯⋯⋯⋯⋯⋯⋯⋯
3 –2

Chapter 4. FUNCTION BLOCKS
4.1 Inserting Function Blocks for RTD Input Modulein GMWIN
⋯⋯⋯⋯⋯⋯⋯⋯⋯⋯⋯⋯⋯
4 –1
4.2 Local Function Blocks
⋯⋯⋯⋯⋯⋯⋯⋯⋯⋯⋯⋯⋯⋯⋯⋯⋯⋯⋯⋯⋯⋯⋯⋯⋯⋯⋯
4 –2
4.2.1 ModuleInitialization (G3F-RD3A:RTD3INI, G4F-RD2A:RTD2INI)⋯⋯⋯⋯⋯⋯⋯⋯⋯⋯⋯ 4 –2
4.2.2 ReadingtheDetected Temperature Valueof the Module(ArrayType)
(G3F-RD3A:RTD3ARD, G4F-RD2A:RTD2ARD) ⋯⋯⋯⋯⋯⋯⋯⋯⋯⋯⋯⋯⋯⋯⋯⋯ 4 –3
4.2.3 ReadingtheDetected Temperature Value of the Module (Single Type)
(G3F-RD3A : RTD3RD, G4F-RD2A : RTD2RD) ⋯⋯⋯⋯⋯⋯⋯⋯⋯⋯⋯⋯⋯⋯⋯⋯⋯ 4–4
4.3Remote Function Blocks
⋯⋯⋯⋯⋯⋯⋯⋯⋯⋯⋯⋯⋯⋯⋯⋯⋯⋯⋯⋯⋯⋯⋯⋯⋯⋯⋯
4 –5
4.3.1 Module Initialization (G3F-RD3A:RTDR3INI, G4F-RD2A:RTDR2INI)⋯⋯⋯⋯⋯⋯⋯⋯⋯ 4 –5
4.3.2 Reading the Detected Temperature Value of the Module ⋯⋯⋯⋯⋯⋯⋯⋯⋯⋯⋯⋯⋯⋯ 4 –6
(G3F-RD3A:RTDR3ARD, G4F-RD2A:RTDR2ARD)
4.4 Errors on Function Block
⋯⋯⋯⋯⋯⋯⋯⋯⋯⋯⋯⋯⋯⋯⋯⋯⋯⋯⋯⋯⋯⋯⋯⋯⋯⋯
4 –7
4.4.1 Errors Indicated by the Output Variable STAT ⋯⋯⋯⋯⋯⋯⋯⋯⋯⋯⋯⋯⋯⋯⋯⋯⋯ 4 –7
4.4.2 Error Indicated by the Output Variable ALM_CODE in the Array Type
Detected Temperature Value Reading Function Block ⋯⋯⋯⋯⋯⋯⋯⋯⋯⋯⋯⋯⋯⋯ 4 –7
Chapter 5. PROGRAMMING
5.1 A Program for Output of the Detected Temperature Value as a BCD Value
⋯⋯⋯⋯⋯⋯⋯
5 –1
5.2 AProgram for Conversing the Detected Temperature Value(
°
C) into Fahrenheit(
°
F)
and Output as a BCD Value
⋯⋯⋯⋯⋯⋯⋯⋯⋯⋯⋯⋯⋯⋯⋯⋯⋯⋯⋯⋯⋯⋯⋯⋯⋯
5 –6
5.3 A Program when Loading the RTD Input Module onto the Remote I/O Station
⋯⋯⋯⋯⋯⋯
5 –9
Chapter 6. BUFFER MEMORY CONFIGURATIONAND FUNCTIONS
6.1 Buffer MemoryConfiguration
⋯⋯⋯⋯⋯⋯⋯⋯⋯⋯⋯⋯⋯⋯⋯⋯⋯⋯⋯⋯⋯⋯⋯⋯
6 –1
6.1.1 G3F-RD3A Buffer Memory ⋯⋯⋯⋯⋯⋯⋯⋯⋯⋯⋯⋯⋯⋯⋯⋯⋯⋯⋯⋯⋯⋯⋯⋯ 6 –1
6.1.2 G4F-RD2A Buffer Memory ⋯⋯⋯⋯⋯⋯⋯⋯⋯⋯⋯⋯⋯⋯⋯⋯⋯⋯⋯⋯⋯⋯⋯⋯ 6 –2
6.2 Functions of Buffer Memory
⋯⋯⋯⋯⋯⋯⋯⋯⋯⋯⋯⋯⋯⋯⋯⋯⋯⋯⋯⋯⋯⋯⋯⋯
6 –3
6.2.1 Specifying Channel Enable/Disable ⋯⋯⋯⋯⋯⋯⋯⋯⋯⋯⋯⋯⋯⋯⋯⋯⋯⋯⋯⋯⋯ 6 –3
(G3F-RD3A :Address 0,G4F-RD2A :Address 0)
6.2.2 Specifying the Type of the RTD ⋯⋯⋯⋯⋯⋯⋯⋯⋯⋯⋯⋯⋯⋯⋯⋯⋯⋯⋯⋯⋯⋯ 6 –3
(G3F-RD3A :Addresses 1 to 8, G4F-RD2A :Addresses 1 to 4)
6.2.3 Detected Temperature Value ⋯⋯⋯⋯⋯⋯⋯⋯⋯⋯⋯⋯⋯⋯⋯⋯⋯⋯⋯⋯⋯⋯⋯ 6 –4
(G3F-RD3A :Addresses 9,12,15,18,21,24,27and30, G4F-RD2A :Addresses 5, 8, 11 and 14)

6.2.4 Digital Conversion Value ⋯⋯⋯⋯⋯⋯⋯⋯⋯⋯⋯⋯⋯⋯⋯⋯⋯⋯⋯⋯⋯⋯⋯⋯ 6 –4
(G3F-RD3A :Addresses 10, 13, 16, 19, 22, 25, 28 and 31, G4F-RD2A :Addresses6, 9, 12 and 15)
6.2.5 Error Code ⋯⋯⋯⋯⋯⋯⋯⋯⋯⋯⋯⋯⋯⋯⋯⋯⋯⋯⋯⋯⋯⋯⋯⋯⋯⋯⋯⋯⋯ 6 –4
(G3F-RD3A :Addresses 11, 14, 17, 20, 23, 26, 29 and 32, G4F-RD2A :Addresses 7,10,13and16)
6.2.6 Specifying SETData ⋯⋯⋯⋯⋯⋯⋯⋯⋯⋯⋯⋯⋯⋯⋯⋯⋯⋯⋯⋯⋯⋯⋯⋯⋯⋯ 6 –5
(G3F-RD3A :Address 33, G4F-RD2A :Address 17)
6.2.7 Information on Run Channel ⋯⋯⋯⋯⋯⋯⋯⋯⋯⋯⋯⋯⋯⋯⋯⋯⋯⋯⋯⋯⋯⋯⋯ 6 –5
(G3F-RD3A :Address 34, G4F-RD2A :Address 18)
6.2.8 Information on RTD Specification Error ⋯⋯⋯⋯⋯⋯⋯⋯⋯⋯⋯⋯⋯⋯⋯⋯⋯⋯⋯ 6–6
(G3F-RD3A :Address 35,G4F-RD2A :Address 19)
Chapter 7. DEDICATED INSTRUCTIONSFOR SPECIAL MODULES
(Readfrom/WritetoBufferMemory)
7.1 Local
⋯⋯⋯⋯⋯⋯⋯⋯⋯⋯⋯⋯⋯⋯⋯⋯⋯⋯⋯⋯⋯⋯⋯⋯⋯⋯⋯⋯⋯⋯⋯⋯⋯
7–1
7.1.1 Read from Buffer Memory⋯GET, GETP⋯⋯⋯⋯⋯⋯⋯⋯⋯⋯⋯⋯⋯⋯⋯⋯⋯⋯⋯7–1
7.1.2 Write to Buffer Memory⋯PUT, PUTP⋯⋯⋯⋯⋯⋯⋯⋯⋯⋯⋯⋯⋯⋯⋯⋯⋯⋯⋯⋯7–2
7.2 Remote
⋯⋯⋯⋯⋯⋯⋯⋯⋯⋯⋯⋯⋯⋯⋯⋯⋯⋯⋯⋯⋯⋯⋯⋯⋯⋯⋯⋯⋯⋯⋯⋯
7–3
7.2.1 Read from Buffer Memory⋯RGET ⋯⋯⋯⋯⋯⋯⋯⋯⋯⋯⋯⋯⋯⋯⋯⋯⋯⋯⋯⋯ 7 –3
7.2.2 Write to Buffer Memory⋯RPUT ⋯⋯⋯⋯⋯⋯⋯⋯⋯⋯⋯⋯⋯⋯⋯⋯⋯⋯⋯⋯ 7–4
Chapter 8. PROGRAMMING
8.1 Basic Programming
⋯⋯⋯⋯⋯⋯⋯⋯⋯⋯⋯⋯⋯⋯⋯⋯⋯⋯⋯⋯⋯⋯⋯⋯⋯⋯⋯
8–1
8.1.1 G3F-RD3A ⋯⋯⋯⋯⋯⋯⋯⋯⋯⋯⋯⋯⋯⋯⋯⋯⋯⋯⋯⋯⋯⋯⋯⋯⋯⋯⋯⋯⋯
8 –1
8.1.2 G4F-RD2A ⋯⋯⋯⋯⋯⋯⋯⋯⋯⋯⋯⋯⋯⋯⋯⋯⋯⋯⋯⋯⋯⋯⋯⋯⋯⋯⋯⋯⋯ 8 –2
8.2 Application Programming
⋯⋯⋯⋯⋯⋯⋯⋯⋯⋯⋯⋯⋯⋯⋯⋯⋯⋯⋯⋯⋯⋯⋯⋯⋯
8 –3
8.2.1 A Program for Output of the Detected Temperature Value as a BCD Value ⋯⋯⋯⋯⋯⋯ 8 –3
8.2.2 AProgram for Conversing the Detected Temperature Value(°C) into Fahrenheit(°F)
and Output as a BCD Value ⋯⋯⋯⋯⋯⋯⋯⋯⋯⋯⋯⋯⋯⋯⋯⋯⋯⋯⋯⋯⋯⋯ 8 –4
8.2.3 A Program when Loading the RTD Input Module onto the Remote I/O Station ⋯⋯⋯⋯⋯8–6
Chapter 9. TROUBLESHOOTING
9.1 ErrorsIndicated by RUN LED Flickering
⋯⋯⋯⋯⋯⋯⋯⋯⋯⋯⋯⋯⋯⋯⋯⋯⋯⋯⋯⋯
9–1
9.2 Troubleshooting Procedure
⋯⋯⋯⋯⋯⋯⋯⋯⋯⋯⋯⋯⋯⋯⋯⋯⋯⋯⋯⋯⋯⋯⋯⋯⋯
9–2
9.2.1 RUN LED Flickering ⋯⋯⋯⋯⋯⋯⋯⋯⋯⋯⋯⋯⋯⋯⋯⋯⋯⋯⋯⋯⋯⋯⋯⋯⋯⋯ 9 –2
9.2.2 RUN LED Off ⋯⋯⋯⋯⋯⋯⋯⋯⋯⋯⋯⋯⋯⋯⋯⋯⋯⋯⋯⋯⋯⋯⋯⋯⋯⋯⋯⋯ 9–2
9.2.3 Detected Temperature Value Unreadable from the CPU Module ⋯⋯⋯⋯⋯⋯⋯⋯⋯⋯⋯ 9 –3

9.2.4 Input Value of the RTD Is Not Consistent with
The Detected Temperature Value ⋯⋯⋯⋯⋯⋯⋯⋯⋯⋯⋯⋯⋯⋯⋯⋯⋯⋯⋯⋯⋯ 9–4
9.2.5 RTD Input Module Hardware Defect ⋯⋯⋯⋯⋯⋯⋯⋯⋯⋯⋯⋯⋯⋯⋯⋯⋯⋯⋯⋯ 9 –4
Chapter 10.DIMENSIONS.
10.1 G3F-RD3A Dimensions
⋯⋯⋯⋯⋯⋯⋯⋯⋯⋯⋯⋯⋯⋯⋯⋯⋯⋯⋯⋯⋯⋯⋯⋯⋯⋯
10 –1
10.2 G4F-RD2A Dimensions
⋯⋯⋯⋯⋯⋯⋯⋯⋯⋯⋯⋯⋯⋯⋯⋯⋯⋯⋯⋯⋯⋯⋯⋯⋯⋯
10 –2
Appendix1. Standard Resistance Value of Pt/RTD
⋯⋯⋯⋯⋯⋯⋯⋯⋯⋯⋯⋯⋯⋯⋯
A –1

Chapter 1. INTRODUCTION
1 -1
Chapter 1. INTRODUCTION
These two units are called G3F-RD3A and G4F-RD2A. The G3F-RD3A is an Pt input module used with the
CPU of GLOFA GM1/2/3 series and MASTER-K1000S series, and the G4F-RD2A is used with the CPU of
GM4 series and K 300S series Hereafter, the two units are called the RTD input module
The RTD input module is a module that converts the temperature data(°C) input by the Pt (Pt100 or JPt100)
into a signed 16 bit digital binary data and outputs it.
1.1 Features
1) With direct connection of the RTD input module, the temperature data(°C) can be converted into a digital
value to be processed in the PLC.
2) The temperature data(°C) input can be processed to one digit after the point asa digital value.
3) One module can be connected to G3F-RD3A 8-point or G4F-RD2A 4-point Pt100 or JPt100.
4) The RTD input module has Pt100, Jpt100 or cable burn-out function at their every channel.
5) The RTD input module detects the out-of-rangetemperaturethat is input by Pt100 or JPt100.

Chapter 1. INTRODUCTION
1 -2
1.2 Glossary
1.2.1 A-Analog Value
The continuous changeable value such as voltage, current, temperature, velocity, pressure and flow is
called analog value. For example, temperature changes continuously with time as shown in Fig. 1.1. The
PLC can process that continuous changeable temperature by use of the RTD input module.
1.2.2 D -Digital Value
In Fig.1.2, the number of man can be counted as 0, 1, 2, 3. The non-continuous changeable value as such
iscalled a digital value. On and Off signals can be denoted as a digital value 0 and 1, respectively.
Analog value cannot be directly input to the CPU
module for digital processing. Therefore, analog value
should be converted into a digital value to be input to
the CPU module. In addition, for external output of
analog value, digital value of the CPU module should
beconverted into analogvalue.
1.2.3 Pt
This is a sensor that detects temperature as the type of resistance.
The Pt 100 outputsthe resistance valueof 100.00 Ωfor the temperature of 0 °C
1.2.4 Burn-out Function
If a part of the connected RTD or cable is disconnected, the out-of-range voltage is input by the internal
burn-outcircuit and theconnection or disconnection is detected.
A/D
Conversion
CPU
(Digital
processing)
D/A
Conversion
Analog
-200~-600℃
Analog
0~±10Vor
4~20mA
[Fig 1.3] Processing in the PLC
0
Temperature
time time
Numberofman
[Fig 1.1] Analog Value [Fig 1.2] Digital Value
0

Chapter 2. SPECIFICATIONS
2-1
REMARK
Chapter 2. SPECIFICATIONS
2.1 General Specifications
Table 2.1 shows general specifications of the GLOFA GM series and MASTER-Kseries
No Item Specifications Reference
specification
1Operating
ambient
temperature 0 ~ 55 °C
2Storage
ambient
temperature -25 ~ +75 °C
3Operating
humidity 5 ~ 95%RH, non-condensing.
4Storage
humidity 5 ~ 95%RH, non-condensing.
Occasional vibration
Frequency Acceleration Amplitude Sweep
Count
10≤f<57 Hz -0.075mm
57≤f≤150 Hz 9.8 m/s2{1G} -
Continuous vibration
Frequency Acceleration Amplitude
10≤f <57 Hz -0.035mm
5
Vibration
57≤f≤150 Hz 4.9 m/s2{0.5G} -
10 times in
each
direction
for X,Y,Z
IEC 61131-2
6Shocks lMaximum shock acceleration: 147 m/s2{15G}
lDuration time : 11ms
lPulse wave: half sine pulse (3 times in each of X, Y and Z directions)
IEC 61131-2
Square wave impulse
noise ±1,500 V LGIS
Standard
Electrostaticdischarge Voltage : 4 kV (contact discharge) IEC 61131-2,
IEC1000-4-2
Radiated electromagnetic
field 27 ~ 500 MHz, 10 V/m IEC 61131-2,
IEC 1000-4-3
Severity
Level
All
Power
modules
Digital
I/Os (Ue
> 24 V)
DigitalI/Os
(Ue < 24 V)
Analog I/Os
interface
communication
I/Os
7Noise
Immunity
Fast transient/burst noise
Voltage 2 kV 1 kV 0.25 kV
IEC 61131-2,
IEC 1000-4-4
8Operating
Atmosphere Free from corrosive gases and excessive dust.
9Operation
Altitude Up to 2,000m
10 Pollution
degree 2
11 Cooling
method Self-cooling
[Table 2.1] General Specifications
1) IEC(International Electromechanical Commission) : The international civilian organization which produces standards
for electrical and electronic industry.
2) Pollution degree : It indicates a standard of operating ambient pollution level The pollution degree 2 means the condition
in which normally, only con-conductive pollution occurs. Occasionally, however, a temporary conductivity caused by
condensation shall be expected.

Chapter 2. SPECIFICATIONS
2-2
2.2 Performance Specifications
Table 2.2 shows performance specifications of the RTD input module.
Specifications
Item G3F-RD3A G4F-RD2A
Connectable RTD Pt 100 (JIS C1640-1989,DIN 43760-1980)
JPt100 (KS C1603-1991,JIS C1604-1981)
Temperatureinput range Pt100
JPt100 : -200.0°Cto 600°C (18.48 to 313.59Ω)
: -200.0°Cto 600°C (17.14 to 317.28Ω)
Digital output
Digital conversion value : 0 to 16,000
Detected temperature value : -2000 to 6000 (one digit after
point 510)
Buffermemory Each of three wires at every channel has detection
function.
Accuracy ±0.5 %(full scale)
Maximum conversion speed 50msperchannel
Number of temperature input device points 8 channels per module 4 channels per module
Insulationmethod Photo-coupler insulation between the input terminal and
the PLC power supply (non-insulationbetween channels)
Connection terminal block 38-pointterminal block 20-point terminalblock
Internal current consumption 0.5 A 0.45A
Weight 630 g 350 g
[Table. 2.2 Performance Specifications]

Chapter 2. SPECIFICATIONS
2-3
2.3 Names of Parts and Functions
The following gives names of parts.
2.3.1 G3F-RD3A
The following gives the names and functions of each part of the G3F-RD3A.
No. Descriptions
RUNLED
ℵIt displays the operating status of G3F-RD3A module
lOn : Normal Operation
lFlickering : Error occurred (For more information,
see Chapter 4.1
lOff : DC 5V disconnection or the G3F-RD3A
module error

Chapter 2. SPECIFICATIONS
2-4
2.3.2 G4F-RD2A
The following gives the names and functions of each part of the G4F-RD2A.
RUNLED
G4F-RD2A module operating status Indication
-On : Normal operation
-Flickering: Error occurred(For more information,see
Section Common 4.1)
-Off : 5 VDC disconnection or G4F-RD2A module error

Chapter 2. SPECIFICATIONS
2-5
2.4 RTD Input Module Characteristics
2.4.1 Temperature Conversion Characteristics
The RTD input module, as shown in the Fig. 2.1, linearlizes the non-linearcharacteristicresistance
input of the RTD.
[Fig. 2.1] Temperature conversion characteristics( Pt100)
2.4.2 Conversionspeed
The conversion speed of the RTD input module is 50 ms per channel and its processing is
processed sequentially, that is, one channel is processed and then another channel is
processed.
Processing time = 50 ms 5the number of the used channels
Example) When three channels are used
Processing time = 50 ms 53 = 150 ms
2.4.3 Accuracy
The accuracy of RTD input module is within ±0.5 % of all of the measurable temperature range.
Example) When the RTD Pt100 is used, the conversion valuesof –100°C and 400°Care as
below.
-Measurable temperature full range : 800°C(-200.0°Cto 600.0°C)
-Accuracy : 800 5(±0.5%) = 8005(±0.005) = ±4°C
-Temperature conversion range : -104°Cto –96 °Cwhen –100°C
396°Cto 404°Cwhen 400°C
Resistance
temperature
detection value

Chapter 2. SPECIFICATIONS
2-6
2.4.4 Burn-out Detection Function
The RTD input module has the function of burn-out detection on the Pt100, JPt100 or cable.
1)As shown in the Fig. 2.2, if disconnection occurs in the RTD or cable then a voltage outside the
measurable range voltage is inputted by the internal burn-out detection circuit and burn-outdetection
error code is generated.
2)The RTD input module can detect disconnection for each channel. But, burn-out detection is possible
only in the channels enabled.
3)Ifdisconnection is detected in two or more wires, first, disconnection error code is generated by‘b’and
then disconnection error code is generated by ‘A’or‘b’sequentially. If disconnection is detected
simultaneouslyin ‘A’and ‘B’, only disconnection error code is generated by ‘b’.
Connection
Method Connection Example Burn-out Detection
Function Remark
2-wire
type
3-wire
type
4-wire
type
No wiring
-When specified as the
enabled channel
: The burn-out detection
function is enabled.
-When not specified as
the enabled channel
: The burn-out detection
function is disabled
-In 4-wire type, only all
wires marked '2'
connected to the
terminal block A are
all detected as
disconnection then
the A disconnection
error can be
detected.
*1 : Pt
*2: Shield wire
[Fig. 2.2] Burn-out Detection Area
burn-outdetectionarea
burn-outdetectionarea
burn-outdetectionarea

Chapter 2. SPECIFICATIONS
2-7
2.5 Connection between a Pt and RTD input module
-Number of method of connection between Pt and RTD input module are three, that is, 2-wired type, 3-
wired type and 4-wiredtype.
-The resistance of the wires used to connect Pt to RTD input module should be 10 Ωor less per wire.
The same wire (in thickness, length, and kind, etc.) should be used for each channel.
REMARK
ΣThe difference between the resistance values of the wires used should be 1 Ωor less, or the accuracy
shown in the Table 2.2 could not be satisfied.
Connection
Method Connection Example Wire Conditions
2-wiredtype
3-wiredtype
4-wiredtype
ℵwire resistance≤10Ω
ℑwire resistance≤10Ω
ℜwire resistance≤10Ω
The difference between the
resistance values of the wires ℵand
ℑ: 1Ωor less
The difference between the
resistance values of the wires ℑand
ℜ: 1Ωor less
The difference between the
resistance values of the wires ℜand
ℵ: 1Ωor less
[Fig. 2.3] Method of Connectionbetween Pt and RTD Input Module
*1: RTD (Pt100 or JPt1000)
*:2: Shielded wire
-The shields of the RTD and shields of wire should be connected to the FG of the RTD input
module.

Chapter 3. INSTALLATION AND WIRING
3 -1
Chapter 3. INSTALLATION AND WIRING
3.1 Installation
3.1.1 InstallationAmbience
This module has high reliability regardless of its installation environment, but be sure to check the
following for system reliability and stability.
1)Ambience requirements
Avoid installing this unit in locations which are subjected or exposed to :
-Water leakage and dust.
-Continuousshocksor vibrations.
-Direct sunlight.
-Dew condensation due to rapid temperature change.
-Higher or lower temperatures outside the rangeof0to55 °C
2) Precautions during installing and wiring.
-During drilling or wiring, do not allow any wire scraps to enter into the PLC.
-Install it on locations that are convenient for operation.
-Make sure that it is not located on the same panel that high voltage equipment located.
-Make sure that the distance from the walls of duct and external equipment be 50 mm or more.
-Be sure to be grounded to locations that have good ambient noise immunity.
3.1.2 Handling Precautions
From unpacking to installing the RTD input module, be sure to check the following:
1) Do not drop it off, and make sure that strong shock should not be applied.
2) Do not unload the PCB from its case. It can cause faults.
3) During wiring, be sure to check any foreign matter like wire scraps should not enter into the upper side
of the PLC. If any foreign matter has entered into it, always eliminate it.
4) Do not load or unload the module while the power supply is being connected.

Chapter 3. INSTALLATION AND WIRING
3 -2
3.2 WringPrecautions
1) Whenconnecting Pt with the RTD input module, refer to the Chapter 2.5 for wiring.
2) Be sure to separate the external input signal of the RTD input module from an alternating current so
that surge or induction noise generated from the alternating current could not effect.
3) Whenwiring, locatingthis unit toonear from high temperature generatingdevices or materials or
contacting it with the material like oil can cause short-circuitand occur damageor disorder.
4) Whenwiring to theterminal block, wiringwith high-pressure wire or power supply wire can occur flow
inhibition and cause disorder or malfunction.

Chapter 4. FUNCTION BLOCKS
4 -1
Chapter 4. FUNCTION BLOCKS
The followings explain the function blocks for the RTD input module used in GMWIN
The types of function block are given here.
G3F-RD3A G4F-RD2A
No. Local Remote Local Remote Function
1RTD3INI RTDR3INI RTD2INI RTDR2INI ModuleInitialization
2RTD3ARD RTDR3RD RTD2ARD RTDR2RD Reading the detected temperature value
(Array type)
3RTD3RD -RTD2RD -Reading the detected temperature value
(Single type)
4.1 Inserting Function Blocks for the RTD Input Module in GMWIN.
Function blocks can be registered with the following procedure while the GMWIN is running.
Registering function blocks is only possible when a project is open.
G4F-RD2A
1.Special.4fb
•RTD2INI
•RTD2ARD
•RTD2RD
2.Remote4.4fb
•RTDR2INI
•RTDR2RD
3.Remote3.4fb
•RTDR3INI
•RTDR3RD
Project(P)
Library Insert(I)
G3F-RD3A
1.Special.3fb
•RTD3INI
•RTD3ARD
•RTD3RD
2.Remote3.3fb
•RTDR3INI
•RTDR3RD
3.Remote4.3fb
•RTDR3INI
•RTDR2RD
Insertinglocal
function block
InsertingGM3remote
function block
InsertingGM4remote
function block
Insertinglocal
functionblock
InsertingGM4remote
function block
InsertingGM3remote
function block
Selection

Chapter 4. FUNCTION BLOCKS
4 -2
4.2 Local Function Blocks
4.2.1 Module Initialization (G3F-RD3A: RTD3INI, G4F-RD2A:RTD2INI)
Module initialization function block specifies RTD input module base location, slot location, run channel
enable/disable and the type of RTD for use in program.
Function
Block I/O Variable Data
Type Descriptions
REQ BOOL
Functionblockexecutionrequestarea
-Usedto requestanexecutionoftheinitializationfunctionblock
-If the conditions connected with this area are established while program is
running and input condition changes from low to high, the initialization function
blockisexecuted
BASE USINT
BaselocationNo.
-Used to write the number of the base where the RTD input module is loaded.
-Settingrange:GM1series(0~31),GM2series(0~7), GM3/4series(0-3)
SLOT USINT
SlotlocationNo.
-Usedtowritethe number oftheslotwheretheRTDinput module isloaded.
-Settingrange:0~7
CH BOOL
[Array]
*Note1
Runchannelenable/disablespecification
-Usedtoenable ordisableachannelforrun.
-Specify“1”for enabling, and“0”for disabling
I
TYPE BOOL
[Array]
*Note1
SpecifyingthetypeofRTDfor use
-Usedtospecifythetypeof“0”for Pt100 and“1”forJPt100foreachchannel
"0":Pt100
"1":JPt100
DONE BOOL
Functionblockexecutioncompletestatus
-“1”
is output when the initialization function block is finished with no error and
“1”remains until next execution. If an error occur, ‘0’is displayed and the
operationentersintothestopstate.
STAT USINT
Errorstatusindicationarea
-Usedtooutputthe number ofanerrorwhenitoccursduring initialization function
blockexecution.
-Fordescriptionoferrors,seeGMSection7.4
O
ACT BOOL
[Array]
*Note1
Run channelstatusindicationarea
-After the initialization function block is finished with no error, “1”is output if the
channelis innormalstate.But“0”isoutputforthedisabledchannels.
REMARK
Note 1: The numbers of Array are 8 in G3F-RD3A, 4in G4F-RD2A.

Chapter 4. FUNCTION BLOCKS
4 -3
4.2.2 Reading the Detected Temperature Value of the Module (Array Type)
(G3F-RD3A : RTD3ARD, G4F-RD2A : RTD2ARD)
The Array type temperature conversion value reading function block executes all channels of the RTD
input module in a batch processing. If a channel is enabled then the function block outputs the detected
temperature value and its digital conversion value that is usable as a PV in the PID control module.
Function
Block I/O Variable Data
Type Descriptions
REQ BOOL Functionblockexecutionrequestarea
-Usedtorequestanexecutionofthereadingfunctionblock
-If the conditions connected with this area are established while the program is
running and“0”changes into“1”, the readingfunctionblockisexecuted.
BASE USINT BaselocationNo.
-Used to write the number of the base where the RTD input module is loaded.
-Settingrange:GM1series(0~31), GM2 series(0~7), GM3/4 series(0-3)
SLOT USINT SlotlocationNo.
-Usedtowritethe number oftheslotwheretheRTDinput module isloaded.
-Settingrange:0~7
I
CH BOOL
[Array]
*Note1
Runchannel enable/disable specification
-UsedtoenableordisableachanneIforrun.
-Specify“1”for enabling, and“0”for disabling
DONE BOOL Functionblockexecutioncompletestatus
-“1”is output when the reading function block is finished with no error and “1”
remainsuntil nextexecution.Ifanerroroccur,‘0’is displayed and the operation
entersintothestopstate.
STAT USINT
Errorstatusindicationarea
-Used to output the number of an error when it occurs during reading function
blockexecution.
-Fordescriptionoferrors,seeGMSection7.4
ACT BOOL
[Array]
*Note1
Runchannelstatusindicationarea
-After the reading function block is finished with no error, “1”is output if the
channelis innormalstate.But“0”isoutputforthedisabledchannels.
ALM BOOL
[Array]
*Note1
Run channelerrorindicationarea
-“1”isoutputtedwhen erroroccursforeachrunchannel.
ALM_
CODE USINT
[Array]
*Note1
Runchannelerrorcodearea
-Usedtooutput thecodeoferror occurred during run for each channel.
-For error description, seeGMSection7.4.
TEMP INT
[Array]
*Note1
Detectedtemperaturevalueoutputarea
-The CPU module reads the detected temperature value(-200.0°Cto+600.0°C) of
thecorrespondingchannelfromtheRTD inputmoduleandoutputsittothis area.
-The detected temperature value of each channel is 10 times than the real
temperaturevalue.
-(Example:Detected temperaturevalue1234 →realtemperaturevalue123.4°C)
O
SCAL INT
[Array]
*Note1
Digitalconversionvalueoutputarea
-TheCPUmodulereadsthedigitalconversionofthecorrespondingchannelfrom
theRTDinput moduleandoutputsitto thisarea.
-The detected temperature value (-200.0°C to +600.0°C) of each channel is
convertedintothea digital valuewithin0to16000andit is outputtothisarea.
-Valuetobe readfromtheoutput variable.
•SCAL =(the value to be read from the output variable TEMP + 2000)52
•Example: Where a temperature is 234.5°C.
The value to be read from the TEMP is (temperature 510),then
2345 is the detected temperature value.
The value to be read from the SCAL is (2345 + 2000) 52, i.e.,
8690.
-Theoutputvalue converted into a digitalvaluecan be used as the PVof the PID
control module.
REMARK
Note 1: The numbers of Array are 8 in G3F-RD3A, 4 in G4F-RD2A.

Chapter 4. FUNCTION BLOCKS
4 -4
4.2.3 Reading the Detected Temperature Value of the Module (Single Type)
(G3F-RD3A : RTD3RD, G4FRD2A : RTD2RD)
The stand-alone type Temperature conversion value reading function block processes only one channel
of the RTD input module. If a channel is enabled then the function block outputs the detected
temperature value and its digital conversion value that is usable as a PV in the PID control module.
Function
Block I/O Variable Data
Type Descriptions
REQ BOOL Function block execution request area
-Used to request an execution of the reading function block
-If the conditions connected with this area are established while the
program is running and “0”changes into “1”, the reading function block
isexecuted.
BASE USINT Base location No.
-Used to write the number of the base where the RTD input module is
loaded.
-Setting range: GM1 series(0~31), GM2 series(0~7), GM3/4 series(0-3)
SLOT USINT Slot location No.
-Used to write the number of the slot where the RTD input module is
loaded.
-Setting range: 0~7
I
CH USINT
Area for specifying the used channel.
Settings : G3F-RD3A: 0 to 7, G4F-RD2A: 0 to 3
DONE BOOL Function block execution complete status
-“1”
is output when the reading function block is finished with no error and
“1”remains until next execution. If an error occur, ‘0’is displayed and the
operation enters into the stop state.
STAT USINT
Error status indication area
-Used to output the number of an error when it occurs during reading
function block execution.
-For description of errors, see GM Section 7.4
ALM BOOL
Run channel error indication area
-“1”is output if error occurs for each run channel.
TEMP IN T Detected temperature value output area
-The CPU module reads the detected temperature value(-200.0°C to
+600.0°C) of the corresponding channel from the RTD input module and
outputs it to this area.
-The detected temperature value of each channel is 10 times than the real
temperature value.
(Example: Detected temperature value 1234 →real temperature value
123.4°C)
O
SCAL INT
Digital conversion value output area
-The CPU module reads the digital conversion of the corresponding
channel from the RTD input module and outputs it to this area.
-The detected temperature value (-200.0°C to +600.0°C) of each channel
is converted into a digital value within 0 to 16000 and it is output to this
area.
-Value to be read from the output variable.
•SCAL =(the value to be read from the output variable TEMP + 2000)
52
•Example: Where a temperature is 234.5°C.
The value to be read from the TEMP is (temperature 510),
then
2345 is the detected temperature value.
The value to be read from the SCAL is (2345 + 2000) 52,
i.e., 8690.
-The output value converted into a digital value can be used as the PV of
the PID control module.
This manual suits for next models
1
Table of contents
Other LG Controllers manuals
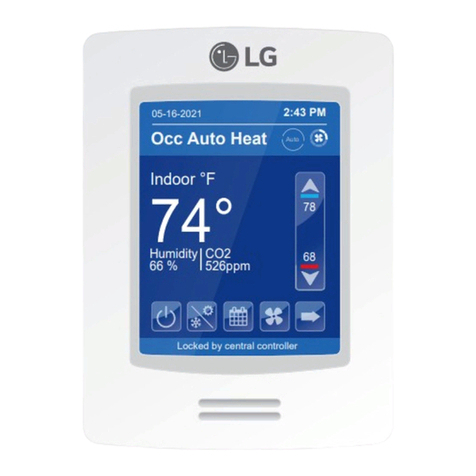
LG
LG MultiSITE CRC2 Series User manual
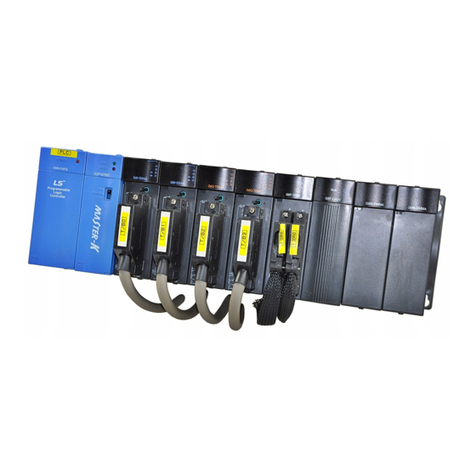
LG
LG MASTER-K200S User manual
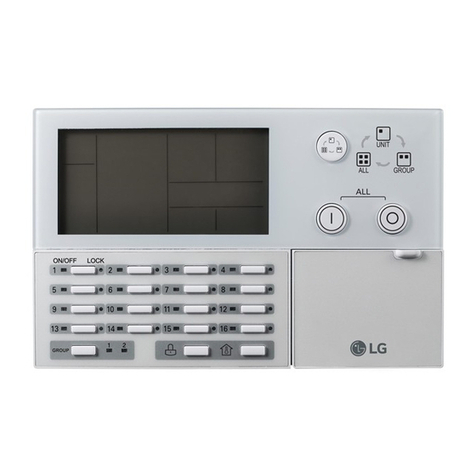
LG
LG AC Ez Operating instructions
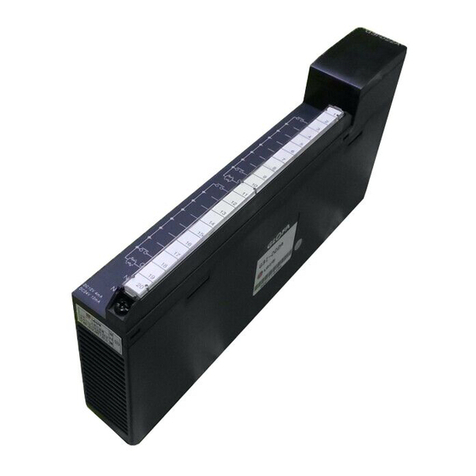
LG
LG G3F-TC4A User manual
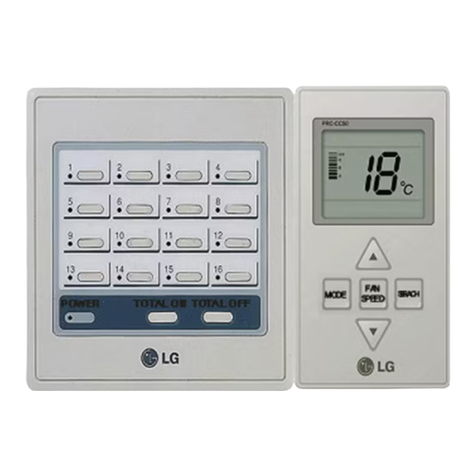
LG
LG PQCSB101S0 User manual

LG
LG PQCSA001T0 Quick start guide
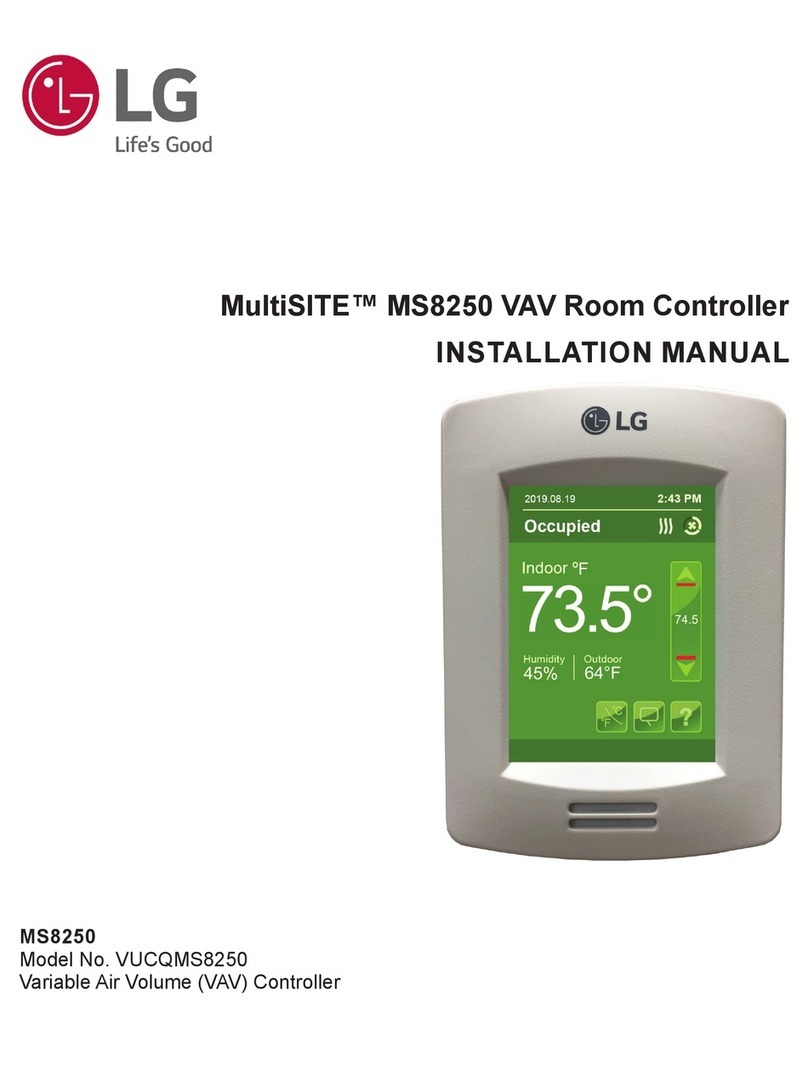
LG
LG MultiSITE MS8250 User manual
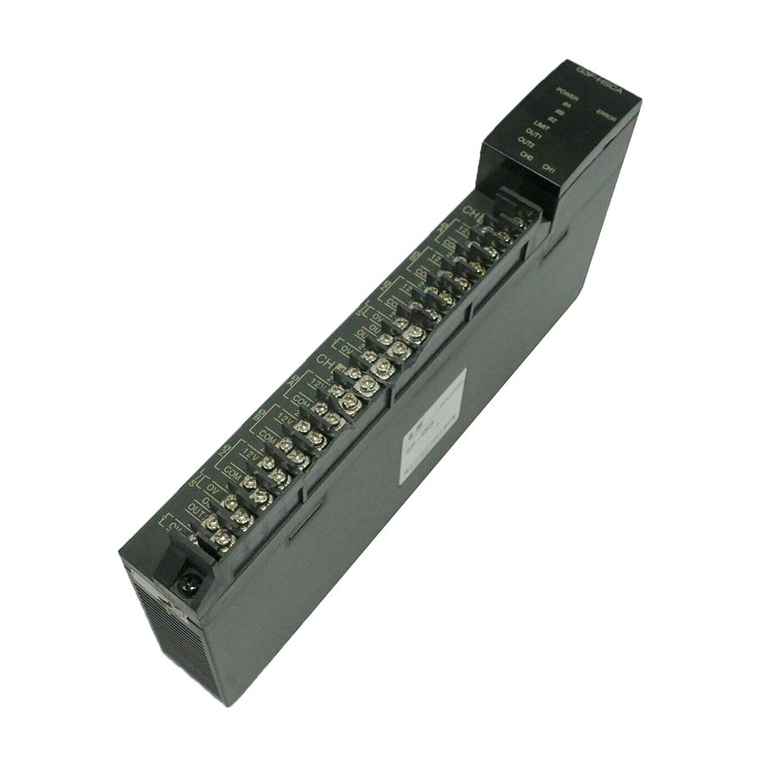
LG
LG MASTER-K Series User manual
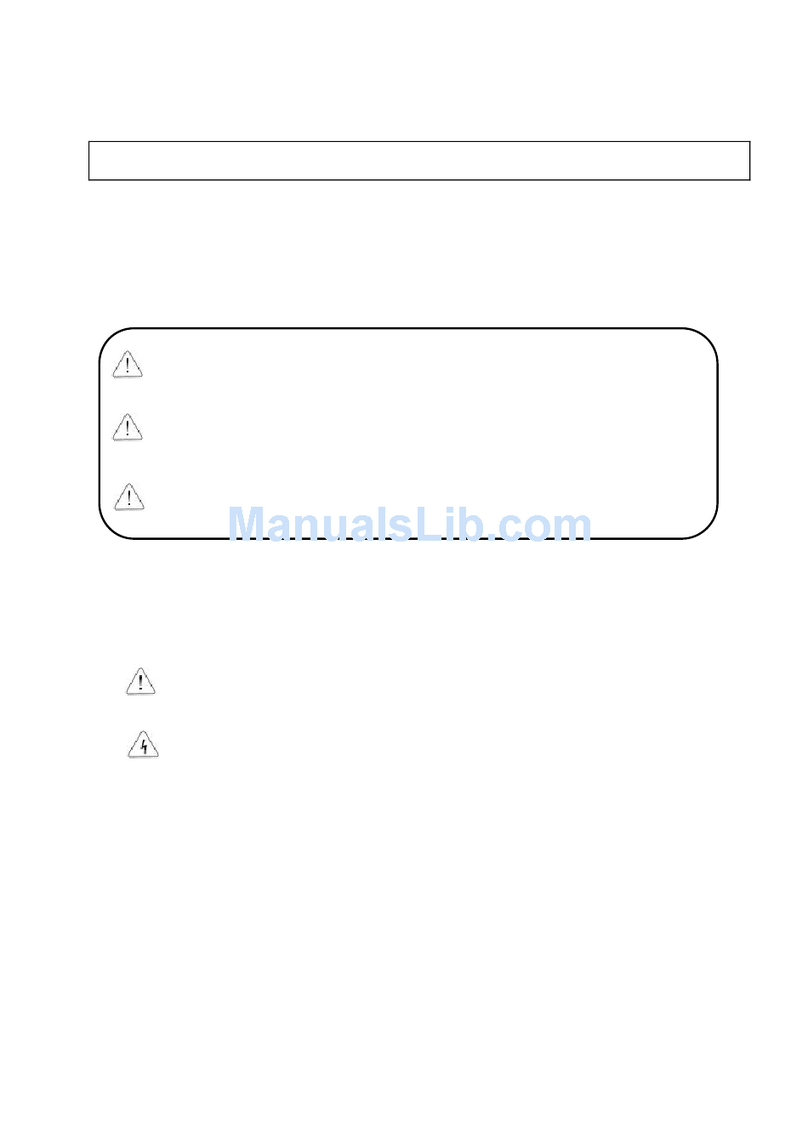
LG
LG SV-iS5 Series User manual
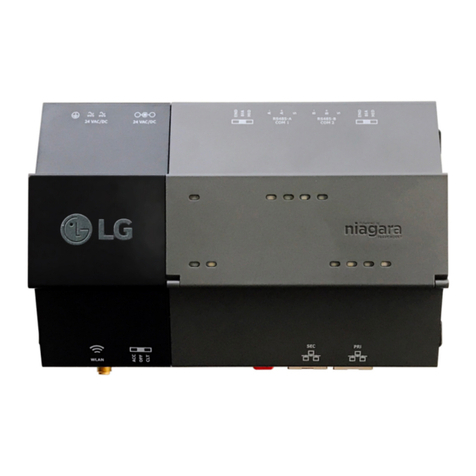
LG
LG PBACNBTR0 User manual
Popular Controllers manuals by other brands
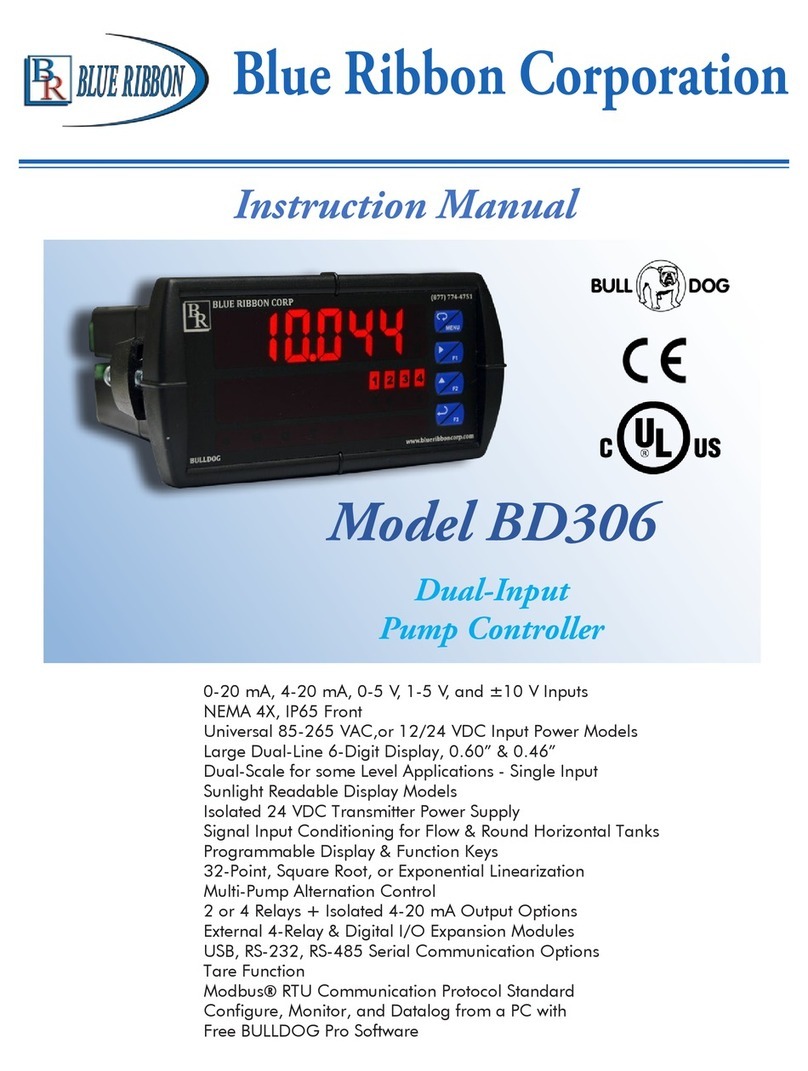
Blue Ribbon
Blue Ribbon BD306 instruction manual
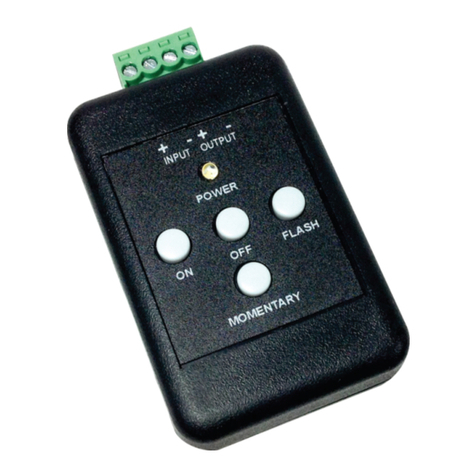
American Recorder
American Recorder OAS-CON-4B manual
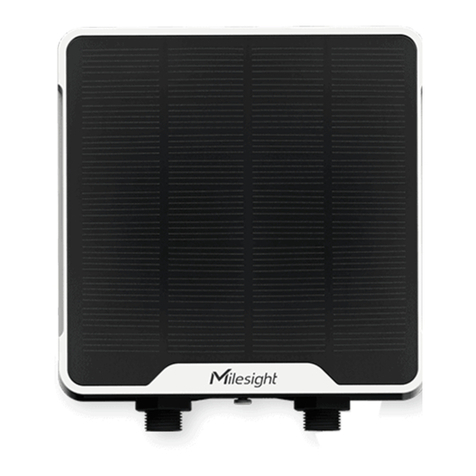
Milesight
Milesight UC50 Series user guide
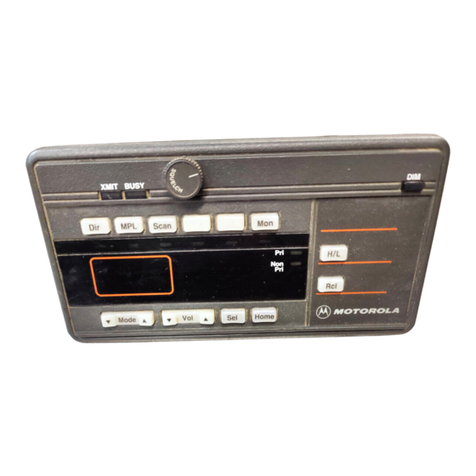
Motorola
Motorola MaraTrac Advanced Control Head operating instructions

Mitsubishi Electric
Mitsubishi Electric MELSEC iQ-F FX5 user manual
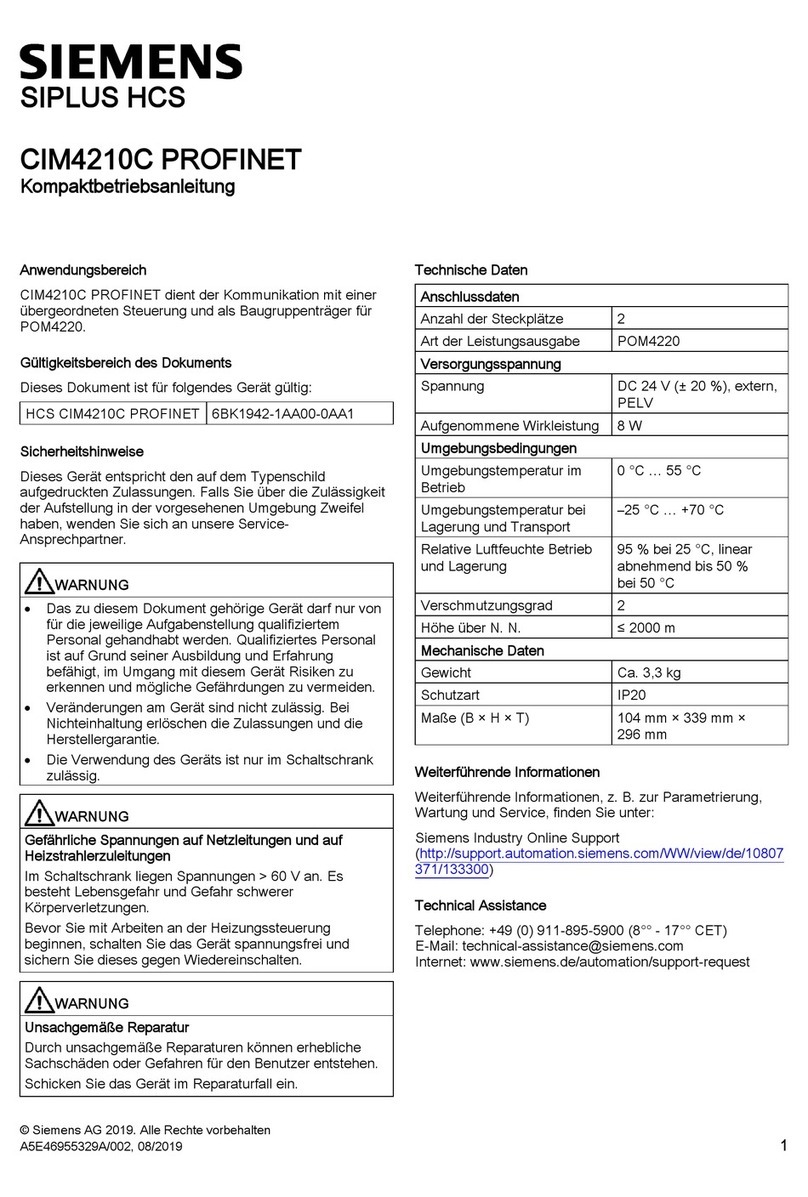
Siemens
Siemens SIPLUS HCS CIM4210C PROFINET Compact operating instructions