macromatic PMP Series User manual

Installation and Wiring
1. Mount the appropriate 8 pin octal socket in a suitable enclosure. NOTE: a 600V-rated socket such as the Macromatic 70169-D or
Custom Connector OT08-PC must be used with these products on applications greater than 300V. When making connections
to the socket, make sure to match the terminal numbers on the socket to the ones shown on the wiring diagram (the wiring
diagram on the relay is the view looking towards the bottom of the relay vs. the top of the socket). Use one or two #12-22 solid
or stranded copper or copper-clad aluminum conductors with terminals on the above Macromatic or Custom Connector sockets—a
terminal tightening torque of 12 in-lbs should be used.
2. Set the VOLTAGE LINE-LINE knob to the actual three-phase line-to-line voltage. The
Voltage Line-Line knob on the PMPU & the PMPU-FA8 has two ranges (see right): 190-
250V on the low voltage scale and 380-500V on the high voltage scale. The unit auto
senses the three-phase line-line voltage when applied and automatically selects one of
the two ranges. The PMP120 has a single adjustable range of 102-138V and the PMP575
has a single adjustable range of 460-600V.
3.(For PMPU-FA8, skip to Step 4) Set initial settings on the UNDERVOLTAGE TRIP, TRIP
DELAY and RESTART DELAY knobs to minimum. Set initial setting on the UNBALANCE
knob to maximum.
4. Connect the three-phase line-line voltage to terminals 3, 4 and 5 (see Wiring Diagram on
the side of the relay or on the back of this sheet). A connection to the neutral or ground
is not required in Wye systems. DO NOT connect output wires to terminals 1, 2 and 8
until later (Step 13).
5. RESET: As standard, the PMP Series relays are in the Automatic Reset mode, which means they will automatically reset once the fault has
been corrected. However, they can be set up in the Manual Reset mode by connecting an external N.C. switch across terminals 6 and 7.
Upon application of three-phase voltage, the PMP Series will go into Manual Reset mode if it recognizes a closure across terminals 6 and
7. After a fault clears, the relay will not reset until the N.C. switch is opened. NOTE: this unit can only be set back to Automatic Reset
mode from Manual Reset mode by removing three-phase voltage, removing the N.C. switch across terminals 6 and 7, and reapplying the
three-phase voltage.
6. Plug the three-phase monitor relay into the socket, making sure the key on the center post is in the
proper orientation before insertion. If the relay must be removed from the socket, do NOT rock
the relay back and forth excessively—the center post could be damaged.
7. Apply three-phase voltage. The LED indicator should initially flash GREEN if in the Automatic Reset
mode while the relay goes through its start-up delay or waiting for an external switch to be operated
if in the Manual Reset mode and then illuminate solid GREEN. If the LED turns RED solid or
flashing, a fault condition exists and must be corrected. Use the LED Status Table at right or the
Troubleshooting Guide on back to determine exact cause of fault. Make required corrections.
Settings
8. REMOVE THREE-PHASE VOLTAGE for Steps 9-13. (For PMPU-FA8, REMOVE THREE-PHASE VOLTAGE and skip to Step 13)
9. Set the RESTART DELAY knob. This setting should be the time period required after a fault has been cleared before the relay should
automatically energize. NOTE: this value is ignored when in the Manual Reset mode (see Step 5).
10. Set the UNDERVOLTAGE TRIP knob between 80 and 95% of the line-line voltage setting. This value should be the same as the minimum
operating voltage for the equipment to be adequately protected.
11. Set the TRIP DELAY knob. This is the maximum time period that an unbalance, undervoltage or overvoltage condition should be allowed to
last. Too short a setting will cause nuisance tripping if there are momentary changes in the three-phase voltage. Too long a setting could
cause damage to the equipment. Note that the setting should be at least slightly longer than the time a three-phase motor is drawing its
inrush or startup current. This will avoid nuisance tripping caused by the starting current.
12. Set the UNBALANCE knob. This setting should be the maximum allowable unbalance in phase voltage that the three-phase system can
tolerate. Too low of a setting can cause nuisance tripping. Too high of a setting may not adequately protect the system.
(Continued on Back)
INSTALLATION
INSTRUCTIONS
PMP SERIES
THREE-PHASE MONITOR RELAYS
901-0000-140
April, 2014 (Replaces November, 2008)
DANGER!
Potentially hazardous voltages are present. Electrical shock can cause death or serious injury.
Installation should be done by qualified personnel following all National, State & Local Codes.
BE SURE TO REMOVE ALL POWER SUPPLYING THIS EQUIPMENT BEFORE CONNECTING OR DISCONNECTING WIRING.
READ INSTRUCTIONS BEFORE INSTALLING OR OPERATING THIS DEVICE. KEEP FOR FUTURE REFERENCE.
IMPORTANT: READ THIS FIRST IF REPLACING A PMP SERIES PRODUCT WITH DATE CODE OF 1414 OR EARLIER
Macromatic made several product design enhancements on all PMP Series products manufactured with Date Code of 1415 or later (2nd week of April
2014). These include a dial-in-dial line-line voltage scale on the PMPU with an increased 190-500V range, new LED fault codes & the ability to set the Line-
Line Voltage with power applied. Basic functionality & protection has been retained.
PMPU-FA8
190-500V
PMPU
190-500V

Operation
13. Connect the output terminal wires to terminals 1, 2 and 8 (see Wiring Diagram on the side of the relay or below).
14. When all connections are made, apply three-phase line-line voltage. The LED indicator should initially flash GREEN while the relay goes
through its restart delay or waiting for an external switch to be operated if in the Manual Reset mode and then illuminate solid GREEN when
all voltage conditions are correct.
15. If the LED does not illuminate solid GREEN during regular operation, a fault condition has occurred. REMOVE THREE-PHASE
VOLTAGE, and check for proper phase rotation, presence of all three phases, and low or high voltage conditions. Use the LED Status
Table on the first page or the Troubleshooting Guide below to determine exact cause of fault. Correct if necessary. Re-
energization is automatic upon correction of the fault condition unless using MANUAL RESET, which requires opening the N.C. switch
across terminals 6 and 7 to reset the unit (see Step 5).
INSTALLATION
INSTRUCTIONS
PMP SERIES
3-PHASE MONITOR RELAYS
Warranty
All catalog-listed PMP Series products manufactured by Macromatic are warranted to be free from defects in workmanship or
material under normal service and use for a period of five (5) years from date of manufacture.
Troubleshooting Guide Typical Connections
(For Load Side connection, contact Macromatic)
Diagram 104
LED STATUS SITUATION SOLUTION
GREEN Motor is not starting Either (a) the relay is going through its
POWER-UP/RESTART delay and will energize
the output contacts when completed; or (b) the
relayis in the Manual Reset mode and waiting
for an external switch to be operated before
energizing the output contacts.
GREEN Motor is not starting The relay is in the run mode and working
properly. Either another control device is
preventing the motor from starting or all wiring
should be checked.
NO INDICATION Relay is not
energized and/or
motor is not running
VerifyL1, L2 and L3 (A, B & C) are connected
to terminals 3, 4 and 5. Measure the three line-
to-line voltages. If anyof the voltages are
below the specified minimum operation
voltage, the relay does not have enough power
to operate. Check to see whyoperating
voltage is low and correct.
RED On power-up or with
motor running The relay is sensing a phase reversal or phase
out-of-sequence (rotation) condition. REMOVE
THREE-PHASE VOLTAGE and switch any two
of the three line connections to ensure the
phase sequence (rotation) is correct.
RED Either a phase loss
or voltage
unbalance condition
Make sure all three phases are present.
Check for a blownfuse or a loose or broken
wire. Measure all three line-line voltages and
calculate the percent unbalance—compare to
UNBALANCE knob setting. Determine why
unbalanced condition exists and correct it.
RED Low voltage Measure the three line-to-line voltages. If the
average of these three voltages is below the
UNDERVOLTAGE TRIP knob setting, the relay
has tripped due to a low voltage condition.
Check for low voltage condition and correct it.
RED High voltage Measure the three line-to-line voltages. If the
average of these three voltages is > 10% of the
VOLTAGE LINE-LINE knob setting, the relay
has tripped due to a over voltage condition.
Check for high voltage condition and correct it.
Table of contents
Other macromatic Relay manuals
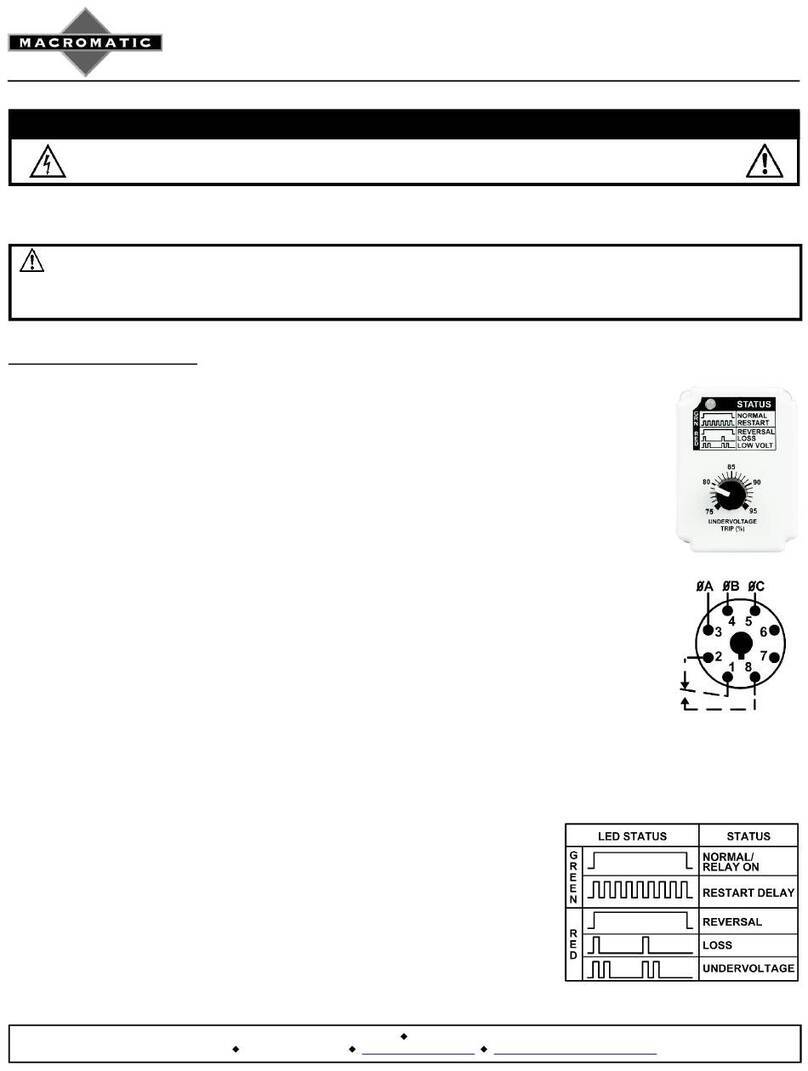
macromatic
macromatic PAP Series User manual
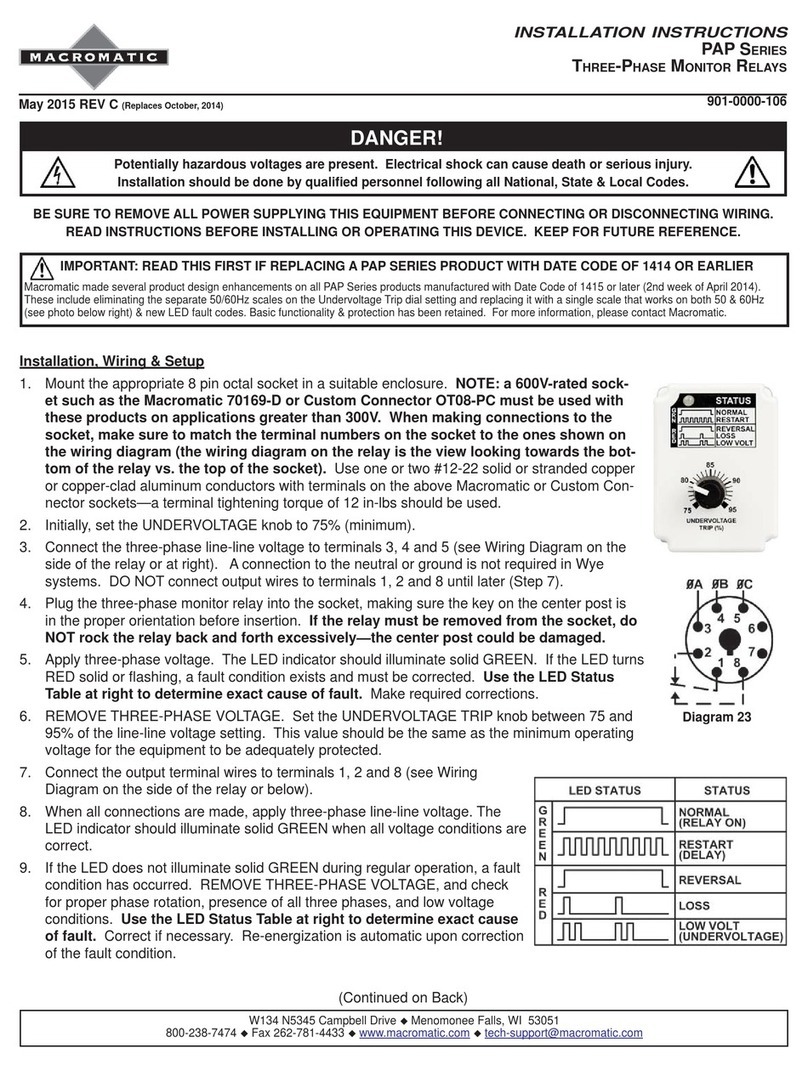
macromatic
macromatic PAP Series User manual
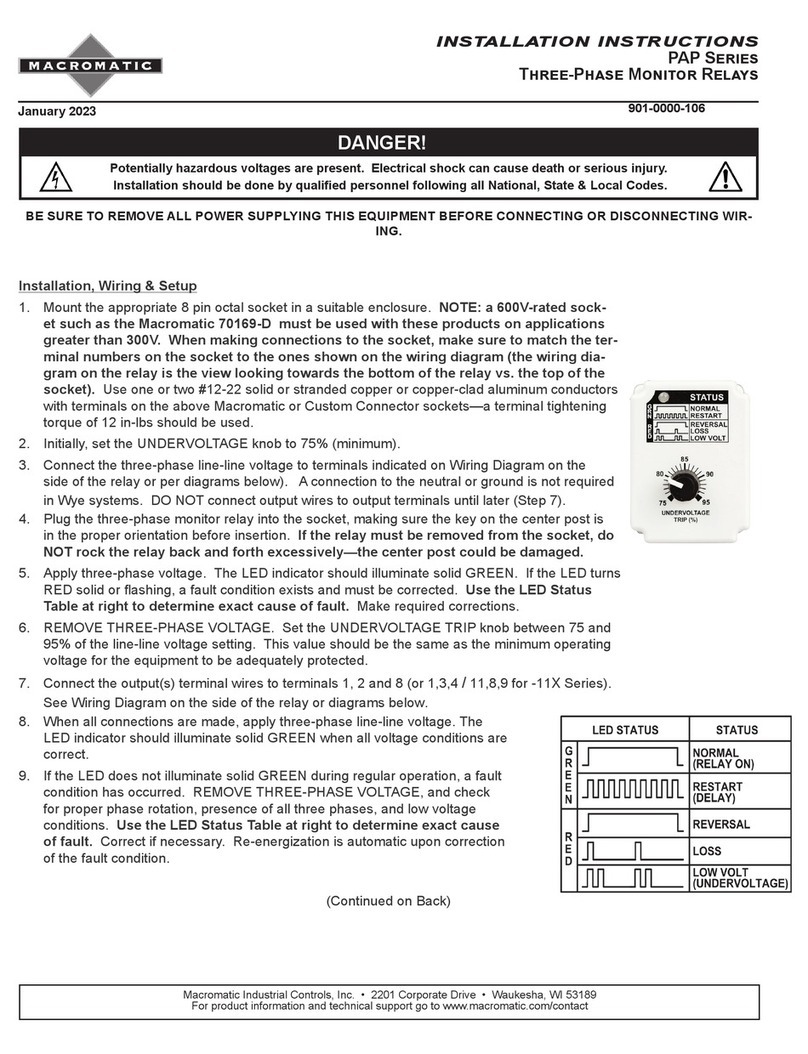
macromatic
macromatic PAP Series User manual
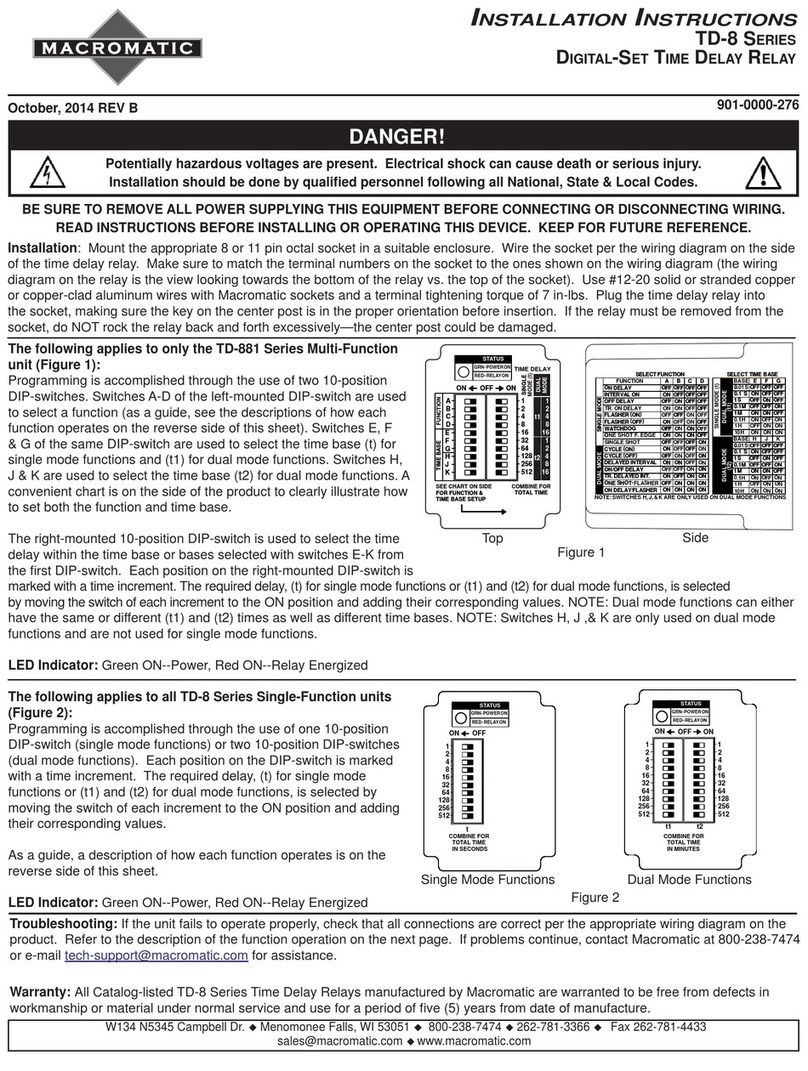
macromatic
macromatic TD-8 Series User manual
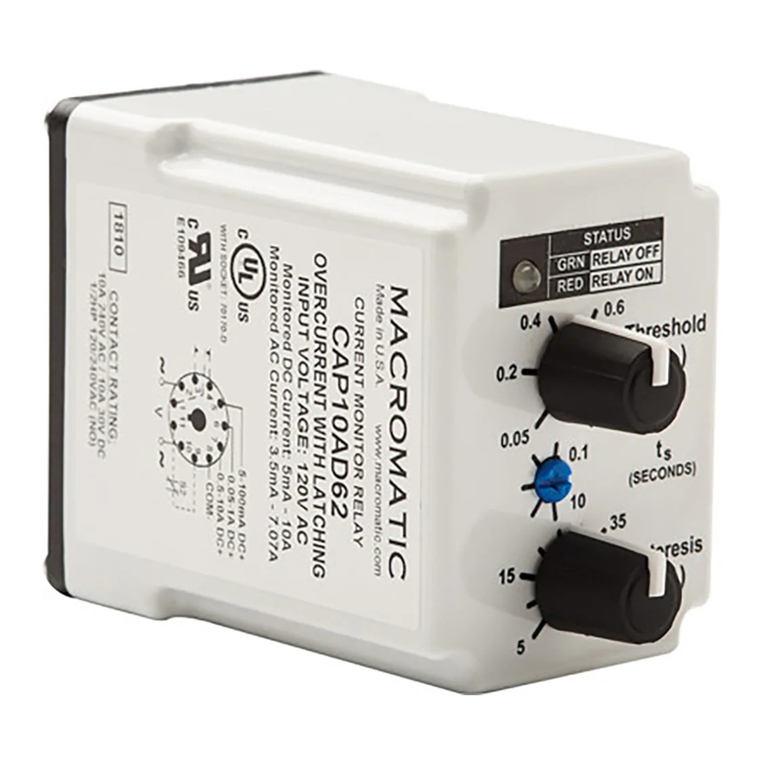
macromatic
macromatic CAP Series User manual
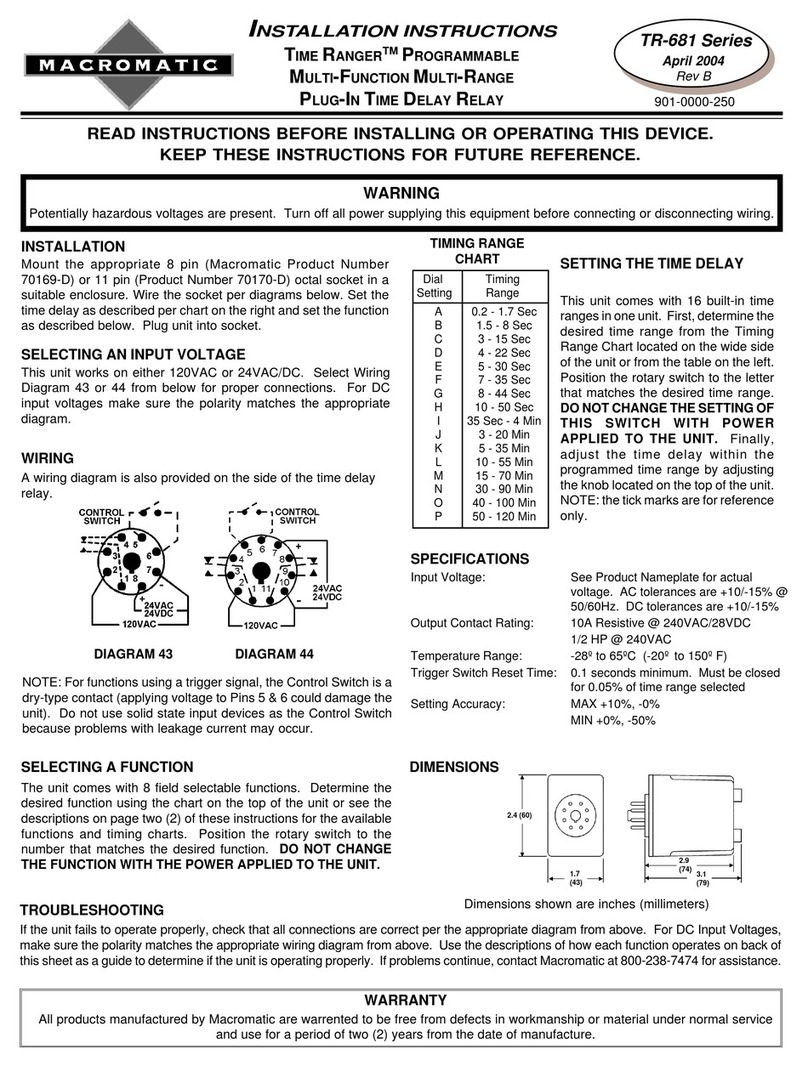
macromatic
macromatic Time Ranger TR-681 Series User manual
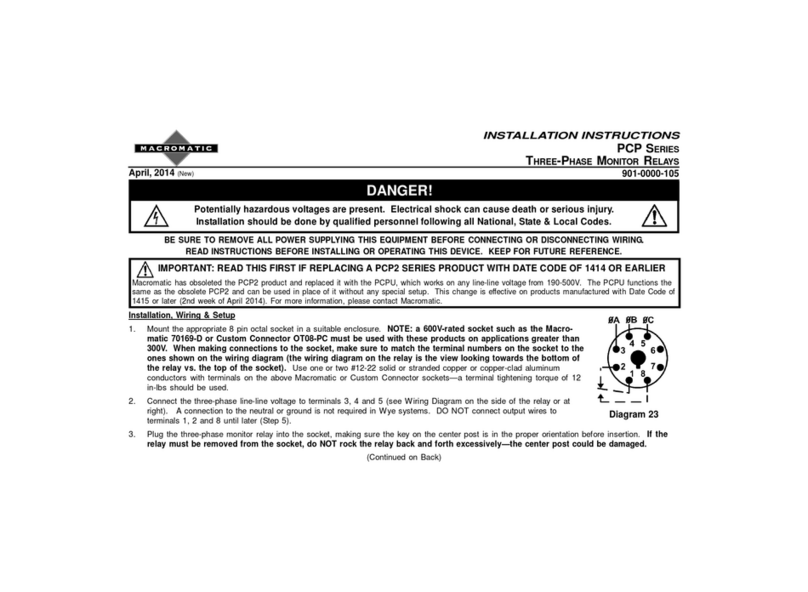
macromatic
macromatic PCP series User manual
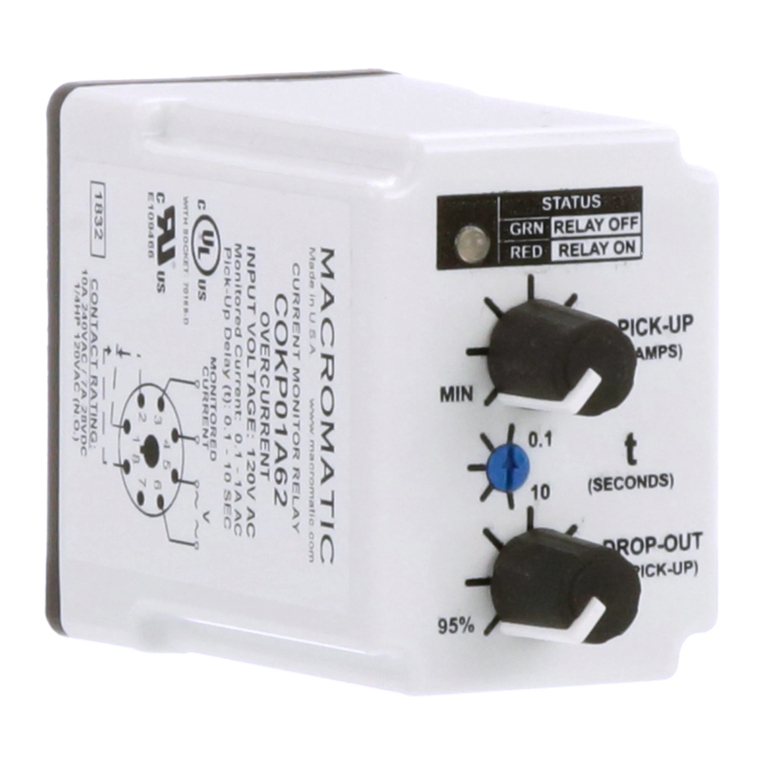
macromatic
macromatic COKP Series User manual
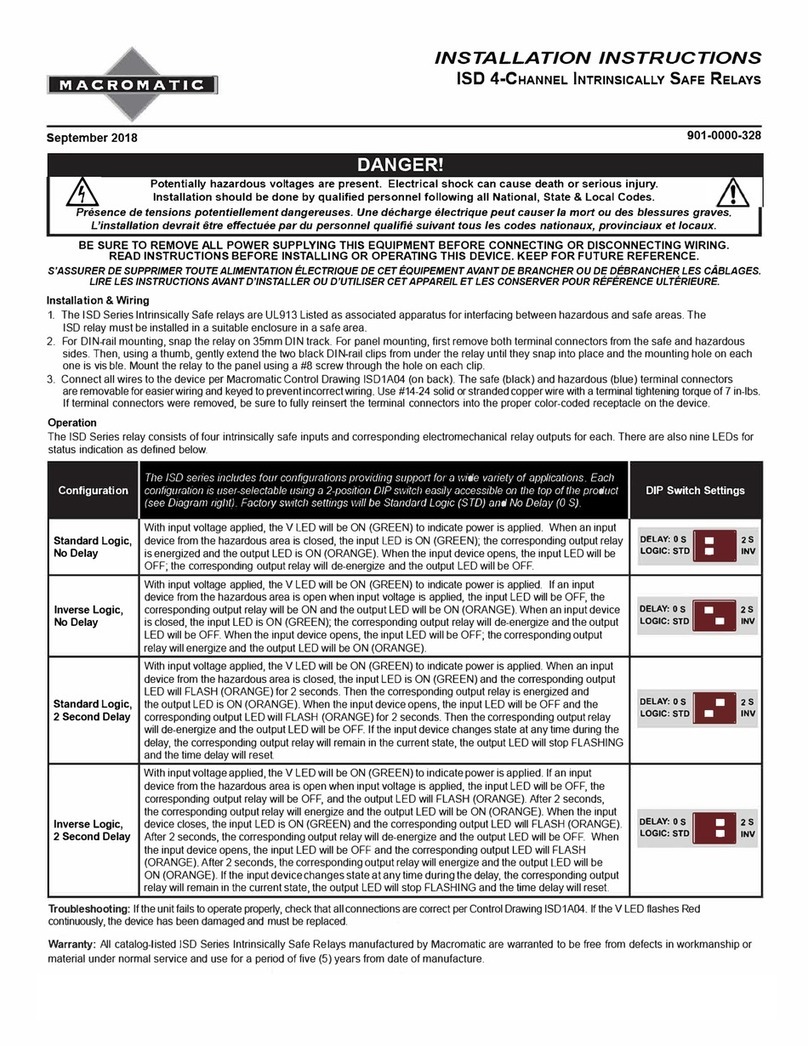
macromatic
macromatic MDB Series User manual
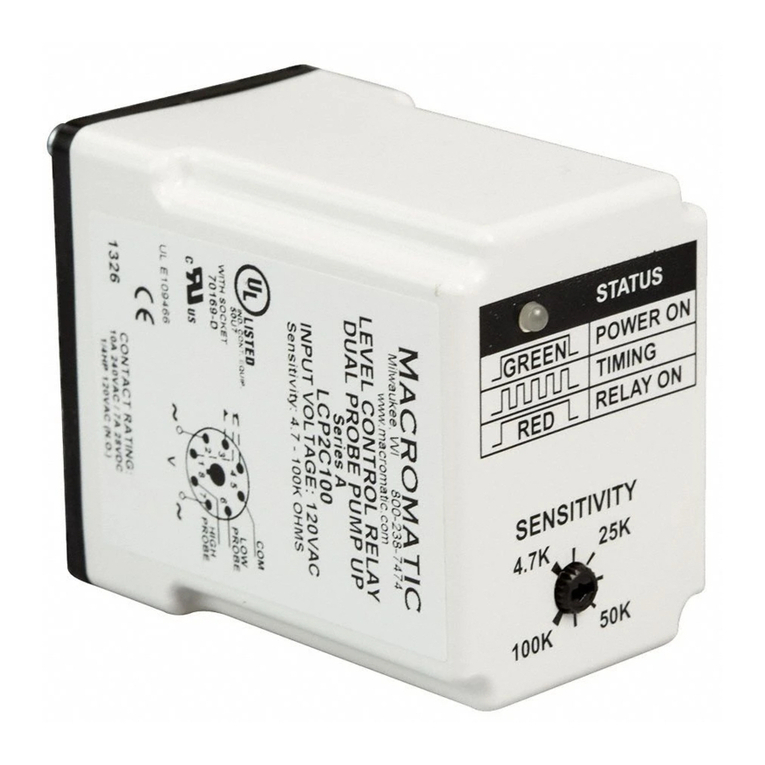
macromatic
macromatic LCP Series User manual