MICROENER MG30 User manual

MG30
Doc. N° MO-0084-ING
Rev. 1
Date 28.04.2003
Copyright 2010 - Microener
Firmware:
2.0X
Pag
1
of
43
MULTIFUNCTION GENERATOR
PROTECTION RELAY
TYPE
MG30
OPERATION MANUAL
MULTIFUNCTION
GENERATOR
PROTECTION
RELAY TYPE
MG30
ENTER/RESET
MODE
SELECT
+
-
PROG.
I2>,T>
Zc<,>
PROG/
I.R.F.
MICROELETTRICA SCIENTIFICA
MILANO ITALY
I>,Z<,Uo>
U,f
W<,Ir>
IC
60FL
B.I./
B.F.

MG30
Doc. N° MO-0084-ING
Rev. 1
Date 28.04.2003
Copyright 2010 - Microener
Firmware:
2.0X
Pag
2
of
43
INDEX
1 General utilization and commissioning directions __________________________________________4
1.1 Storage and transportation__________________________________________________________ 4
1.2 Installation_______________________________________________________________________ 4
1.3 Electrical connection_______________________________________________________________ 4
1.4 Measuring inputs and power supply___________________________________________________ 4
1.5 Outputs loading___________________________________________________________________ 4
1.6 Protection earthing_________________________________________________________________4
1.7 Setting and calibration______________________________________________________________ 4
1.8 Safety protection__________________________________________________________________ 4
1.9 Handling_________________________________________________________________________4
1.10 Maintenance_____________________________________________________________________ 5
1.11 Fault detection and repair___________________________________________________________ 5
2 General characteristics and operation____________________________________________________ 5
2.1 Power supply_____________________________________________________________________ 5
2.2 Measuring input___________________________________________________________________ 6
2.3 Algorithms of the different functions___________________________________________________ 7
2.3.1 Setting range of the reference input quantities______________________________________ 7
2.3.2 F50/51 Dual level 3-phase overcurrent with or without________________________________ 7
2.3.3 Voltage controlled overcurrent___________________________________________________8
2.3.4 F46 Current unbalance________________________________________________________ 9
2.3.5 F32 Reverse Power___________________________________________________________9
2.3.6 F40 Loss of excitation: capacitive underimpedance Zc<_______________________________10
2.3.7 F27-59 Dual level 3-phase over/under voltage______________________________________ 11
2.3.8 F81 Dual level over/under frequency______________________________________________12
2.3.9 F49 Thermal overload_________________________________________________________ 13
2.3.10 F37 Underpower W<__________________________________________________________ 13
2.3.11 F21 Dual level under impedance_________________________________________________14
2.3.12 F24 Dual level overfluxing______________________________________________________ 14
2.3.13 F64S 95% Stator earth fault element_____________________________________________ 15
2.3.14 F64S 95% Stator earth fault element _____________________________________________ 15
2.3.15 F60FL PT Fuse Failure________________________________________________________ 16
2.3.16 F50/27 Inadvertent generator energization_________________________________________ 16
2.3.17 F50BF Breaker failure protection___ _____________________________________________ 16
2.4 Clock and Calendar________________________________________________________________ 17
2.4.1 Clock synchronization__________________________________________________________ 17
2.4.2 Date and time setting__________________________________________________________ 17
2.4.3 Time resolution_______________________________________________________________ 17
2.4.4 Operation during power off______________________________________________________ 17
2.4.5 Time tolerance_______________________________________________________________ 17
3 Controls and measurements____________________________________________________________ 18
4 Signalization_________________________________________________________________________ 19
5 Output relays_________________________________________________________________________20
6 Serial communication__________________________________________________________________21
7 Digital inputs_________________________________________________________________________22
8 Test________________________________________________________________________________ 22
9 Keyboard and display operation_________________________________________________________ 23
10 Reading of measurements and recorded parameters________________________________________24
10.1 ACT. MEAS (Actual measure)___________________________________________________ 24
10.2 MAX VAL (Max values)_______________________________________________________24
10.3 LASTTRIP (Last trip)_________________________________________________________ 25
10.4 TRIP NUM (Trip number)______________________________________________________ 26
11 Reading of programmed settings and relay’s configuration__________________________________ 26

MG30
Doc. N° MO-0084-ING
Rev. 1
Date 28.04.2003
Copyright 2010 - Microener
Firmware:
2.0X
Pag
3
of
43
12 Programming_________________________________________________________________________27
12.1 Programming of functions settings________________________________________________ 27
12.2 Programming the configuration of output relay_______________________________________ 29
13 Manual and automatic test operation_____________________________________________________ 31
13.1 Mode “ TESTPROG “ subprogram “ W/O TRIP “____________________________________ 31
13.2 Mode “ TESTPROG “ subprogram “ With TRIP “____________________________________ 31
14 Maintenance_________________________________________________________________________ 31
16 Power frequency insulation test_________________________________________________________ 31
15 Electrical characteristics_______________________________________________________________ 32
17 Connection diagram (Standard Output)____________________________________________________ 33
17.1 Connection Diagram (Double Output)_________________________________________________33
18 Wiring the serial communication bus_____________________________________________________34
19 Change phase rated input 1A or 5A______________________________________________________ 35
20 Time current curves F51_______________________________________________________________ 35
21 Time current curves F46_______________________________________________________________ 36
22 Thermal image curves_________________________________________________________________ 37
23 Time current curve V/Hz________________________________________________________________38
24 Direction for pcb’s draw-out and plug-in__________________________________________________ 39
24.1 Draw-out____________________________________________________________________ 39
24.2 Plug-in______________________________________________________________________39
25 Overall dimensions____________________________________________________________________40
26 Keyboard operational diagram__________________________________________________________ 41
27 Setting’s form________________________________________________________________________ 42

MG30
Doc. N° MO-0084-ING
Rev. 1
Date 28.04.2003
Copyright 2010 - Microener
Firmware:
2.0X
Pag
4
of
43
1. General utilization and commissioning directions
Always make reference to the specific description of the product and to the Manufacturer's instruction.
Carefully observe the following warnings.
1.1 - STORAGE AND TRANSPORTATION,
must comply with the environmental conditions stated on the product's instruction or by the applicable
IEC standards.
1.2 - INSTALLATION,
must be properly made and in compliance with the operational ambient conditions stated by the
Manufacturer.
1.3 - ELECTRICAL CONNECTION,
must be made strictly according to the wiring diagram supplied with the Product, to its electrical
characteristics and in compliance with the applicable standards particularly with reference to human
safety.
1.4 - MEASURING INPUTS AND POWER SUPPLY,
carefully check that the value of input quantities and power supply voltage are proper and within the
permissible variation limits.
1.5 - OUTPUTS LOADING,
must be compatible with their declared performance.
1.6 - PROTECTION EARTHING
When earthing is required, carefully check its efficiency.
1.7 - SETTING AND CALIBRATION
Carefully check the proper setting of the different functions according to the configuration of the
protected system, the safety regulations and the co-ordination with other equipment.
1.8 - SAFETY PROTECTION
Carefully check that all safety means are correctly mounted, apply proper seals where required and
periodically check their integrity.
1.9 - HANDLING
Notwithstanding the highest practicable protection means used in designing M.S. electronic circuits,
the electronic components and semiconductor devices mounted on the modules can be seriously
damaged by electrostatic voltage discharge which can be experienced when handling the modules.
The damage caused by electrostatic discharge may not be immediately apparent but the design
reliability and the long life of the product will have been reduced. The electronic circuits produced by
M.S. are completely safe from electrostatic discharge (8 KV IEC 255.22.2) when housed in their case;
withdrawing the modules without proper cautions expose them to the risk of damage.

MG30
Doc. N° MO-0084-ING
Rev. 1
Date 28.04.2003
Copyright 2010 - Microener
Firmware:
2.0X
Pag
5
of
43
a. Before removing a module, ensure that you are at the same electrostatic potential
as the equipment by touching the case.
b. Handle the module by its front-plate, frame, or edges of the printed circuit board.
Avoid touching the electronic components, printed circuit tracks or connectors.
c. Do not pass the module to any person without first ensuring that you are both at
the same electrostatic potential. Shaking hands achieves equipotential.
d. Place the module on an antistatic surface, or on a conducting surface which is at
the same potential as yourself.
e. Store or transport the module in a conductive bag.
More information on safe working procedures for all electronic equipment can be found
in BS5783 and IEC 147-OF.
1.10 - MAINTENANCE
Make reference to the instruction manual of the Manufacturer ; maintenance must be carried-out by
specially trained people and in strict conformity with the safety regulations.
1.11 - FAULT DETECTION AND REPAIR
Internal calibrations and components should not be alterated or replaced.
For repair please ask the Manufacturer or its authorised Dealers.
Misapplication of the above warnings and instruction relieves the Manufacturer of any liability.
2. GENERAL CHARACTERISTICS AND OPERATION
Input signals are supplied to 3 current transformers and 3 potential transformers respectively measuring
phase currents and phase-to-neutral voltages plus one voltage transformer for measurement of zero
sequence voltage. Phase current input can be 1 or 5A (movable jumpers on relay’s card). Rated voltage
input can be programmed from 50 to 125V (phase-to-phase) 50 or 60Hz.
Make electric connection in conformity with the diagram reported on relay's enclosure.
Check that input quantities are same as reported on the diagram and on the test certificate.
The auxiliary power is supplied by a built-in interchangeable module fully isolated an self protected
2.1 - POWER SUPPLY
The relay can be fitted with two different types of power supply module:
24V(-20%) / 110V(+15%) a.c. 80V(-20%) / 220V(+15%) a.c.
a) - b) -
24V(-20%) / 125V(+20%) d.c. 90V(-20%) / 250V(+20%) d.c.
Before energizing the unit check that supply voltage is within the allowed limits.

MG30
Doc. N° MO-0084-ING
Rev. 1
Date 28.04.2003
Copyright 2010 - Microener
Firmware:
2.0X
Pag
6
of
43
2.2 - Measuring Inputs
For each phase the relay computes the RMS value of current and voltage and the relevant phase
displacement. It also computes the RMS value of the fundamental and the third harmonic
components of the Zero Sequence Voltage.
2.2.1 Phase currents are supplied to three current transformers with 5A rated primary. By movable
jumpers on the relay card, the secondary can be switched-on to two different taps to obtain a
relay rated input current In = 5 or 1 Amp (different values can be provided on request).
The measuring dynamics of the C.Ts. runs from 0.001 through 50 times In.
For the phase current the measuring range of the A/D Converters runs from 0 to 12In
automatically switched to two channels one measuring from 0 to 1.1In and the second from
0 to 12In.
The resolution of the A/D converter is 12 bits.
2.2.2 Phase-to-neutral voltages are supplied to three Potential transformers rated 220V.
Relay’s rated phase-to-phase input voltage (Un) can be matched with the System’s PTs by
setting their ratio kV
The ADC converter measuring range runs up to 2 x Un.
The A/D converter resolution is 12 bits.
2.2.3 Zero Sequence Voltage is supplied to a dedicated input transformer rated 220V.
Relay’s rated input voltage On is adjustable from 50 to 125V and the measuring range runs from
o to 130V with A/D converter’s resolution of 12 bits.
The relay computes the RMS of fundamental and the third harmonic components of the Zero
Sequence Voltage.
2.2.4 Phase displacement
The relay detects the displacement between the input voltage of phase C and each phase
current IA, IB, IC. The displacement angles are therefore :
A= A-C -120° ; B= B-C + 120° ; C= C-C
This means that the voltage system is considered to be
balanced as it is normally, whereas the currents can be
however unbalanced. (see figure)
Angles are measured anticlockwise from 0° to 360° with
accuracy 2°.
Displacement is not measured if current or voltage are null.

MG30
Doc. N° MO-0084-ING
Rev. 1
Date 28.04.2003
Copyright 2010 - Microener
Firmware:
2.0X
Pag
7
of
43
2.3 - Algorithms of the different functions
2.3.1 - Setting range of the reference input quantities
System frequency
:
Fn = (50-60)Hz
Rated primary current of phase C.Ts.
:
In = (0-9999)A, step 1A
Ratio of System’s PTs.
:
Kv = (2-655), step 0.1
P.Ts secondary phase-to-phase voltage
:
Uns = (50-125)V, step 1V
Relay basic current (Generator’s rated current)
:
Ib = (0.5-1.1)In, step 0.1In
Rated primary current of neutral CT
:
On = (50-125)On, step 1V
2.3.2 - F50/51 - Dual level 3-phase overcurrent with or without voltage control
1F 50/51 : Low set overcurrent
-
Voltage control activated / non activated
:
I>/U = ON-OFF
-
Pick-up (operation) level
:
I> = (1-2.5)Ib, step 0.01Ib
Setting I> = Dis blocks function’s operation
-
Drop-out ratio
:
0.95
-
Minimum operation time of instantaneous output
:
30ms
-
Trip time delay in the definite time operation
mode F(I>) = D
:
t = tI> = (0.05-30)s, step 0.01s
- Trip time delay in the inverse time operation mode F(I>) = SI :
1)(I/I tI0.033
t0.02
; (tI> = trip time delay at I/Ib = 5)
(see curves TU0311 §19)
2F 50/51 : High set overcurrent
-
Voltage control activated / non activated
:
I>>/U = ON-OFF
-
Pick-up (operation) level
:
I>> = (1-9.9)Ib, step 0.1Ib
Setting I>> = Dis blocks function’s operation
-
Drop-out ratio
:
0.95
-
Minimum operation time
:
30ms
-
Independent trip time delay
:
t = tI>> = (0.05-3)s, step 0.01s

MG30
Doc. N° MO-0084-ING
Rev. 1
Date 28.04.2003
Copyright 2010 - Microener
Firmware:
2.0X
Pag
8
of
43
2.3.3 - Voltage controlled overcurrent
If the parameters I>/U and/or I>>/U are set to “ON” the voltage control is active respectively for the
level I> and/or I>>. The actual pick-up levels (I>,I>>) vary from the programmed levels ([I>] , [I>>])
proportionally to the voltage variation according to the curve herebelow
The voltage ratio is measured on each phase and the smallest among the values is used
in the algorithm.
Practically when the input voltage drops below 0.8 [Un] the minimum pick-up level of the overcurrent
elements is decreased as follow
Below 0.2 [Un]
Above 0.8 [Un]
level]up-pick[Set levelup-pickActual
][I
I
,
][I
I
voltage]input[Rated voltageActual
[Un]
U
[Un]3Ex
10.8
Un
U
0.6
0.8
I
I
I
I
0.2
I
I
I
I
1
I
I
I
I

MG30
Doc. N° MO-0084-ING
Rev. 1
Date 28.04.2003
Copyright 2010 - Microener
Firmware:
2.0X
Pag
9
of
43
2.3.4 - F46 - Current unbalance : Measurement of RMS Negative Sequence Current I2
1F 46 : I22 t = K (adiabatic heating)
- Generator’s continuous I2rating : 1Is = (0.05-0.5)Ib, step 0.01Ib
Setting 1Is = Dis blocks function’s operation
- Time multiplier : Ks = (5-80)s, step 1s ; Ks = Trip time when I2= Ib
- Trip time delay
tKs
(I / I )
h2 b 2
; Heat accumulation only operates if I2 [1Is]
- Cooling time from trip level to the state corresponding to the continuous operation at I2 = [1Is] :
tcs = (10-1800)s, step 1s
Cooling time
t[tcs]
Ks I
It
l2
b
2
; t1= [tcs] when
I
ItKs
2
b
2
Cooling only takes places if
I
I1Is
2
b
(see curves TU0312 §20)
2F 46 : Unbalance Alarm
-
Alarm level
:
2Is = (0.03-0.5)Ib, step 0.01Ib
Setting 2Is = Dis blocks function’s operation
-
Independent trip time delay
:
t2Is = (1-100)s, step 1s
2.3.5 - F32 - Reverse power
-
Current setting range
:
Ir = (0.02-0.2)Ib, step 0.01Ib
Setting Ir = Dis blocks function’s operation
-
Operation level
:
I [Ir]
-
Independent trip time delay
:
tIr = (0.1-60)s, step 0.01s (0.1 to 0.99),
step 0.1s (1.0 to 60)
-
Operation zone
:
90°<c<270°
I2/Ib
[1Is]/Ib
th
Ks

MG30
Doc. N° MO-0084-ING
Rev. 1
Date 28.04.2003
Copyright 2010 - Microener
Firmware:
2.0X
Pag
10
of
43
2.3.6 - F40 - Loss of excitation : capacitive underimpedance Zc<
- For each phase the relay computes the impedance
Zc E
Icos( 90 )
xx
x x
- Characteristics angle of the impedance Z= 270°
N.B. By definition the relation between current displacement and impedance displacement
is : = 360°-
Angles are counted anticlockwise from 0° (real axis = direction of phase-to-neutral
voltage E) through 360°.
For example : the displacement of a totally capacitive current is = 90°;
the angle of a totally capacitive impedance is = 270°.
- Operation zone is that included in the circle having (see figure) :
Center on the axis Jx at distance from the axes origin and Diameter= K1
- Circle offset : K2 = (5-50)%Zb, step 1%
- Circle diameter : K1 = (50-300)%Zb, step 1%
Setting K1 = Dis blocks the function operation
- rated generator’s impedance :
[Ib]3
[Un]
Zb
- Independent trip time delay : tz = (0.2-60)s, step 0.1s
- Integration time : ti = (0-10)s, step 0.1s
In case of impedance oscillation,reset of the timer tz only takes place if Z remains outside the trip
area for at least [ti].
- Undervoltage inhibition level : Ex < 0.3
3
[Un]
- Undercurrent inhibition level : Ix < 0.2 [In]
- Operation taxes place only if all the 3 impedances of phase A, B, C are within the trip zone
- The following setting are normally used:
K2 1/2 X’d
(X’d = transient direct axis reactance)
K1 + K2 Xd
(Xd = synchronous reactance)
=
1
for salient-pole alternators and for synchronous motors
=
1, 2
for turbo alternators
tz
=
2s
(1s for synch. motors)
ti
=
1/4tz
2
K1
K2

MG30
Doc. N° MO-0084-ING
Rev. 1
Date 28.04.2003
Copyright 2010 - Microener
Firmware:
2.0X
Pag
11
of
43
2.3.7 - F27/59 : Dual level 3-phase over-under voltage
1F 27-59 : First voltage element 1U
- Minimum Pick-up of voltage difference : 1u = (5-50)%Un, step 1%
- Independent trip time delay : t1u = (0.1-60)s, step 0.1s
- Operation mode : (Un +/-1u)
The function can be programmed to operate as :
- Overvoltage (Un +1u) : operates when any phase voltage Exrises above the rated value
3
[Un]
by more than [1u]%.
- Undervoltage (Un -1u): operates when any phase voltage Exdrops below the rated value
3
[Un]
by more than [1u]%.
- Voltage balance (Un +/-1u) : operates when any phase voltage differs from the rated value
more then [1u]%
- Operation blocked : (Un = Dis)
2F 27-59 : Second voltage element 2U
It operates same as the first element; the programmable parameter are :
-
Pick-up level
:
2u = (5-50)%Un, step 1%
-
Independent trip time delay
:
t2u = (0.1-60)s, step 0.1s
-
Operation mode
:
(Un +/- 2u)
[1u])%(100100
[Un]
Ex3
[1u])%(100100
[Un]
Ex3
[1u])%(100100
[Un]
Ex3
%1u100
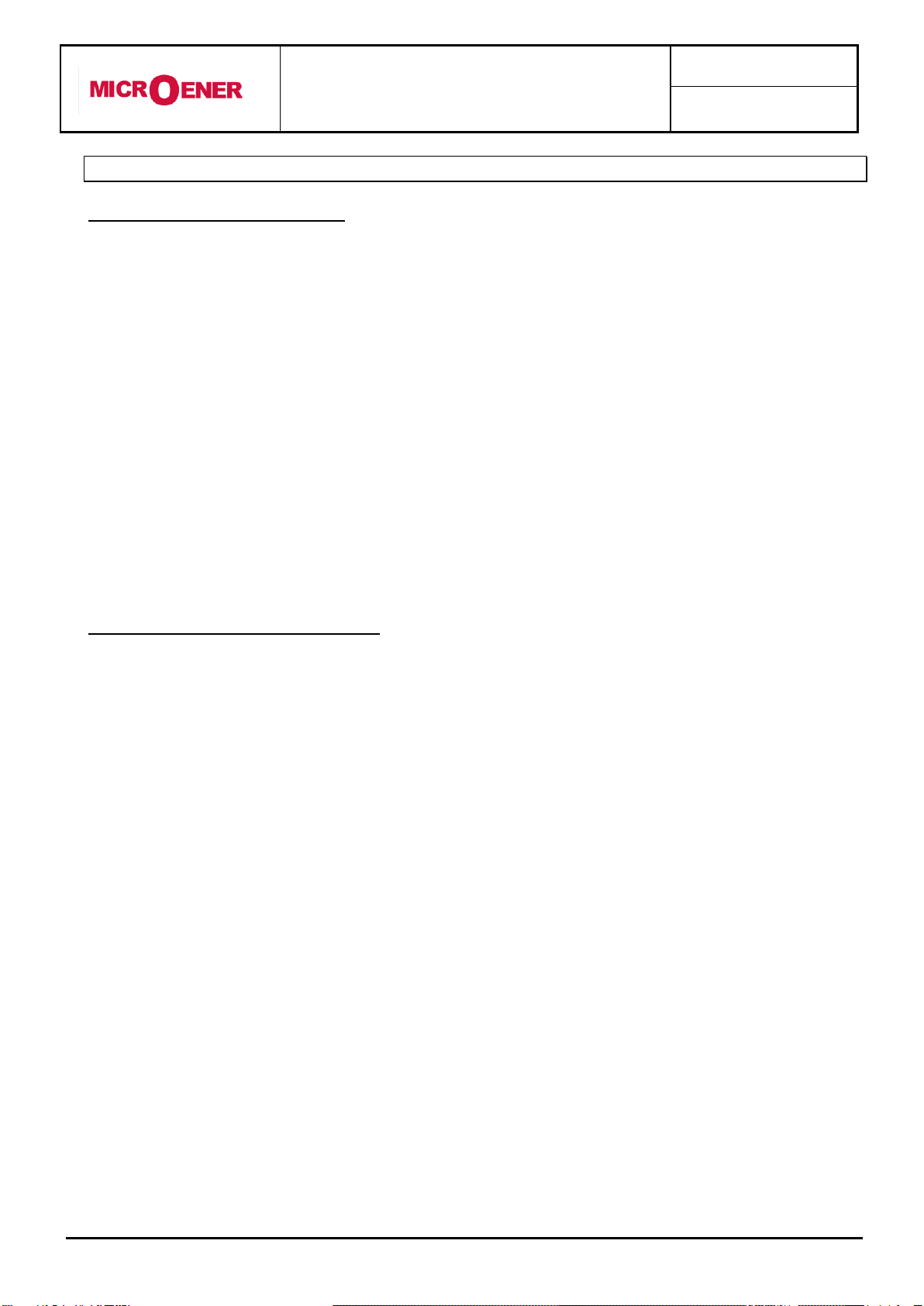
MG30
Doc. N° MO-0084-ING
Rev. 1
Date 28.04.2003
Copyright 2010 - Microener
Firmware:
2.0X
Pag
12
of
43
2.3.8 - F81 : Dual level over/under frequency
1F 81 : First frequency element 1f
-
Minimum Pick-up of frequency difference
:
1f = (0.05-9.99)Hz, step 0.01Hz
-
Independent trip time delay
:
t1f = (0.1-60)s, step 0.1s
-
Operation mode
:
(Fn +/- 1f)
The function can be programmed to operate as
:
-
Overfrequency (Fn +1f)
operates when the frequency rises above the rated
value [Fn] by more than 1f Hz. f (Fn+[1f])Hz
-
Underfrequency (Fn - 1f)
operates when the frequency drops below the rated
value [Fn] by more than [1f]Hz. f (Fn-[1f])Hz
-
Frequency balance (Fn +/-1f)
operates when frequency differs from rated value by
more than [1f]Hz. (Fn-[1f])Hz f (Fn+[1f])Hz
-
Operation blocked
:
(Fn = Dis)
-
Undervoltage inhibition
:
U < 0.1Un
-
Undercurrent inhibition
:
I < 0.01In
2F F81 : Second frequency element 2f
It operates same as the first element ; the programmable parameters are :
-
Pick-up level
:
2f = (0.05-9.99)Hz, step 0.01Hz
-
Independent trip time delay
:
t2f = (0.1-60)s, step 0.1s
-
Operation mode
:
(Fn +/-2f)

MG30
Doc. N° MO-0084-ING
Rev. 1
Date 28.04.2003
Copyright 2010 - Microener
Firmware:
2.0X
Pag
13
of
43
2.3.9 - F49 - Thermal overload
The relay computes a thermal image of the machine based on the ratio I/[Ib] of the RMS of the
current flowing in each phase to the rated full load current of the generator :
-
Warming-up time constant
:
Tc = (1 - 400)m, step 1m
-
Maximum continuous overload
:
Ic = 1.05Ib (110%Tn)
-
Rated full load (I=Ib) temperature rise
:
Tn
-
Overtemperature prealarm level
:
Ta = (50-110)% Tn, step 1%
- Current corresponding to machine temperature before the overload :
- Time to warm-up from Tp to trip temperature (110%Tn) in function of the current overload
22
22
(Ib/[Ib])(I/[Ib]) (Ip/[Ib])(I/[Ib])
[Tc]ln
(Tb/Tn)(Tx/Tn) (Tp/Tn)(Tx/Tn)
[Tc]lnt
(see curves TU0325 §20)
Cooling is computed with the same time constant (Tc) as heating.
2.3.10 - F37 - Underpower W<
The element measures the 3-phase active power and trips when the power generated (forward)
drops below the set level [W<]
-
Pick-up (operation) level
:
W< = (0.05-1.00)Wb, step 0.05Wb
Setting W< = Dis blocks function’s operation
-
Independent trip time delay
:
tW< = (0.1-60)s, step 0.1s
-
Undervoltage inhibition level
:
U < 0.5Un
-
Undercurrent inhibition level
:
I < 0.01In
-
Overcurrent inhibition level
:
I> 2In
TpIp

MG30
Doc. N° MO-0084-ING
Rev. 1
Date 28.04.2003
Copyright 2010 - Microener
Firmware:
2.0X
Pag
14
of
43
2.3.11 - F21 - Dual Level Under Impedance
The relay computes the modulus of the Impedance of each phase and compares it to
the relay rated input impedance
1F 21 : Low-set element
-
Maximum pick-up level
:
1Z = (0.1 –1.00)Zn, step 0.01Zn
-
Independent trip time delay
:
t1Z = (0.05 –9.99)s, step 0.01s
-
Setting
t1Z = inst no intentional delay
-
Undercurrent inhibition
:
I < 0.2In
-
Operation blocked
:
(1Z = Dis)
2F 21 : High-set element
-
Maximum pick-up level
:
2Z = (0.1 –1.00)Zn, step 0.01Zn
-
Independent trip time delay
:
t2Z = (0.05 –9.99)s, step 0.01s
-
Setting
t2Z = inst no intentional delay
-
Undercurrent inhibition
:
I < 0.5In
-
Operation blocked
:
(2Z = Dis)
2.3.12 - F24 –Dual level Overfluxing
The relay computes the ratio of the input voltage to input frequency and compares it to
the relay rated value
1F 24 : Inverse Time element
- Minimum pick-up level : 1>= (1 –2) , step 0.1pU
- Time multiplier: K= (0.5 –5), step 0.1
- Trip time delay : (see curve §22)
- Operation blocked : (1= Dis)
2F 24 : Definite Time element
-
Minimum pick-up level
:
2>= (1 –2) , step 0.1pU - Un/Fn
-
Independent time delay
:
t2= (0.1 –60), step 0.1s
-
Operation blocked
:
(2= Dis)
For both levels:
-
Underfrequency inhibition
:
f < Fn -10Hz
-
Undervoltage inhibition
:
U < 0.5Un
Ix
Ex
Zx
In3
Un
Zn
Hz
V
Fn
Un
Fn
Un
0.5
1
Hz
VK
t
Trip when
Zx [1Z], [2Z]

MG30
Doc. N° MO-0084-ING
Rev. 1
Date 28.04.2003
Copyright 2010 - Microener
Firmware:
2.0X
Pag
15
of
43
2.3.13 - F64S –95% Stator Earth Fault element
The relay computes the fundamental (system frequency) component of the Neutral-to-Ground input
voltage and compares it to the rated input voltage On of the element
1F 64 : First element
-
Minimum pick-up level
:
1Uo = (5 –99)%On, step 1%On
-
Independent trip time delay
:
t1O = (0.05 –9.99)s, step 0.01s
Setting t1O = inst no intentional delay
-
Operation blocked
:
(1Uo = Dis)
2F 64 : Second element
-
Minimum pick-up level
:
2Uo = (5 –99)%On, step 1%On
-
Independent trip time delay
:
t2O = (0.05 –9.99)s, step 0.01s
Setting t2O = inst no intentional delay
-
Operation blocked
:
(2Uo = Dis)
2.3.14 - F64S –100% Stator Earth Fault element
The relay computes the third harmonic component of the Neutral-to-Ground input voltage of the
element and compares it to the rated input voltage of the element.
When a fault close to the generator neutral is experienced, the 3rd harmonic voltage between neutral
and ground will reduce nearly to zero.
In high resistance earthed generators, the measurement of this voltage discriminates the fault
condition the more clearly the closer the fault is to the neural point.
Protection against faults occurring at points of the winding farther a-way from the neutral is performed
by the 95% protection elements.
-
Maximum pick-up level
:
Uo3 = (1 –30)%On, step 1%On
Pick-up takes place if Uo3 [Uo3]
-
Independent trip time delay
:
to3 = (0.05 –9.99)s, step 0.01s
Setting tO3 = inst no intentional delay
-
Undervoltage inhibition
:
U < 0.5Un
-
Undercurrent inhibition
:
I < 0.01In
-
Operation blocked
:
(Uo3 = Dis)

MG30
Doc. N° MO-0084-ING
Rev. 1
Date 28.04.2003
Copyright 2010 - Microener
Firmware:
2.0X
Pag
16
of
43
2.3.15 - F60FL –PT Fuse Failure
-
Setting
:
60FL = ON or OFF
When set to “ ON “, the element operates as follows:
E2/E1 > 0.3 and I2/I1 < 0.8
If the ratio of the negative sequence voltage to the positive sequence voltage exceeds 0.3 and the
ratio of the negative sequence current to the positive sequence current is below 0.8, the fuse failure
is detected and the operation of the functions involving any voltage measurement is instantaneously
blocked.
After 3 sec delay one output relay is energized for fuse failure alarm signalization.
2.3.16 - F50/27 –Inadvertent generator energization
-
Setting
:
IC = ON or OFF
When set to “ ON “, the element operates as follows:
If all voltages are below 0.2Un for longer than 20s an overcurrent element is enabled; this element
trips when current of any phase excees 0.2Ib for longer than 0.2s.
2.3.17 - F50BF –Breaker Failure Protection
-
Setting
:
tBF = (0.05 –0.5)s, step 0.01s
The element operates as follows:
After tripping of the output relay R1 the time tBF starts.
If at the end of tBF the current in any phase is still present the output relay associated to the Breaker
Failure protection is energized.

MG30
Doc. N° MO-0084-ING
Rev. 1
Date 28.04.2003
Copyright 2010 - Microener
Firmware:
2.0X
Pag
17
of
43
2.4 CLOCK AND CALENDAR
The unit features a built in clock calendar with Years, Months, Days, Hours, Minutes, Seconds,
Tenths of seconds and Hundredths of seconds.
2.4.1 Clock synchronization.
The clock can be synchronized via the serial communication interface. The following
synchronization periods can be set: 5, 10, 15, 30, 60 minutes.
Synchronization can also be disabled, in which case the only way to modify the current date and
time is via the front panel keyboard (SETTINGS menu) or the serial communication interface.
In case synchronization is enabled, the unit expects to receive a sync signal at the beginning of
every hour and once every Tsyn minutes. When a sync signal is received, the clock is
automatically set to the nearest expected synchronization time.
For example: if Tsyn is 10min and a sync signal is received at 20:03:10 January the 10th, 98, then
the clock is set to 20:00:00 January the 10th, 1998.
On the other hand, if the same sync signal were received at 20:06:34, the clock would be set to
20:10:00, January the 10th 98.
Note that if a sync signal is received exactly in the middle of a Tsyn period, the clock is set to the
previous expected synchronization time.
2.4.2 Date and time setting.
When the PROG/SETTINGS menu is entered, the current date is displayed with one of the
groups of digits (YY, MMM or DD) blinking.
The DOWN key operates as a cursor. It moves through the groups of digits in the sequence
YY => MMM => DD => YY => …
The UP key allows the user to modify the currently blinking group of digits.
If the ENTER button is pressed the currently displayed date is captured.
On the other hand pressing the SELECT button leaves the current date unchanged and scrolls
the SETTINGS menu. Current time can now be modified using the same procedure described
above. If synchronization is enabled and the date (or time) is modified, the clock is stopped until
a sync signal is received (via digital input or the serial port). This allows the user to manually set
many units and have them to start their clocks in a synchronized fashion.
On the other hand if synchronization is disabled the clock is never stopped.
Note that the setting of a new time always clears 10ths and 100ths of sec.
2.4.3 Time resolution.
The clock has a 10ms resolution. This means that any event can be time-stamped with a 10ms
resolution, although the information concerning 10ths and 100ths of sec. can be accessed only
via the serial communication interface.
2.4.4 Operation during power off.
The unit has an on board Real Time Clock which maintains time information for at least 1 hour in
case of power supply failure.
2.4.5 Time tolerance.
During power on, time tolerance depends on the on board crystal (+/-50ppm typ, +/-100ppm
max. over full temperature range).
During power off, time tolerance depends on the RTC’s oscillator (+65 –270 ppm max over full
temperature range).

MG30
Doc. N° MO-0084-ING
Rev. 1
Date 28.04.2003
Copyright 2010 - Microener
Firmware:
2.0X
Pag
18
of
43
3. CONTROLS AND MEASUREMENTS
Five key buttons allow for local management of all relay's functions.
A 8-digit high brightness alphanumerical display shows the relevant readings (xxxxxxx)
(see synoptic table fig.1)
Fig.1
MEASURES
MAX VAL.
LASTTRIP
TRIP NUM
ACT MEAS
Actual measuremant values
Max. values measured
Values measured at last
tripping
N° of tripping for each
function
Measurements
display
SET DISP
SETTINGS
FRELAY
Display of setting
Display of configuration of output
relay
Setting Program
display
PROGR
SETTINGS
FRELAY
Setting of parameters
Configuration of output
relays
Set Programming
PRO
G
TEST PRG
W/O TRIP
WithTRIP
Functional Test
Test with operation of signals and output
relays
Test with operation of signals
only
Test activation
by the key ENTER
Paramater scanning
by the key
SELECT
Parameter modification
by the key “+” “-”
Set validation
by the key ENTER
Scanning of
the menus by
the key
“+” “-”
MODE
SELECT
ENTER
+ -
(*) Enabled only if input current is
zero
(*)
(*)
ENTER/RESET
MODE
SELECT
+
-
PROG.
The SELECT button chooses
which category of values within the
chosen mode to display
Pressing this button progressively
selects between
Measurements Display,
Setting Display, Programming,
and Test modes
When in Program mode, this
button stores the newly selected
value. If not in Program mode and
the relay has tripped, this button
resets the relay and all output
contacts. If not tripped, this button
restores the default display.
The + and - buttons are used to
select the actual measurement or
display desired when in
Measurements Display or Settings
Display modes. When in Program
mode, these buttons increase or
decrease the value of the
displayed setting.
When in Program mode, and when
all input currents are zero,
pressing this recessed button
places the relay into active
programming mode, allowing any
or all of the relay’s settings to be
altered.

MG30
Doc. N° MO-0084-ING
Rev. 1
Date 28.04.2003
Copyright 2010 - Microener
Firmware:
2.0X
Pag
19
of
43
4. SIGNALIZATIONS
Eight signal leds (normally off) are provided:
a)
Red LED
I>,Z<,Uo>
Flashing during the trip time delay of any of the following elements:
I>, I>>,1Z, 2Z, 1Uo, 2Uo, Uo3.
Illuminated on trip after expiry of the set trip time delay of any of the
above elements: tI>, tI>>, t1Z, t2Z, t1Uo, t2Uo, tUo3
b)
Red LED
I2>, T>
Flashing during the trip time delay of the 1Is, 2Is elements or when the
thermal image’s temperature exceeds the prealarm temperature [Ta].
Illuminated on trip after expiry of the set trip time delay of the 1Is, 2Is
elements or when temperature exceeds the trip level.
c)
Red LED
Zc<, >
Flashing during the trip time delay of any of the following elements:
Zc, 1>, 2>.
Illuminated on trip after expiry of the set trip time delay of any of the
above elements: tZc, t1>, t2>.
d)
Red LED
U,f
Flashing during the trip time delay of any over/under voltage elements
1U, 2U or over/under frequency elements 1f,2f.
Illuminated on trip at the end of time delay.
e)
Yellow LED
PROG/
I.R.F.
Flashing during the programming of the parameters.
Illuminated in case of Internal Relay Fault.
f)
Red LED
W<, Ir>
Same as d), related to W<, Ir>.
g)
Red LED
IC
60FL
Illuminated in case of trip of the I>/V< or 60FL functions.
h)
Yellow LED
B.I./B.F.
Lit-on when the Breaker Failure function operateds
Flashing when a blocking signal is present at the relevant input
terminals.
The reset of the leds takes place as follows:
- From flashing to off, automatically when the lit-on cause disappears.
- From ON to OFF, by "ENTER/RESET" push button via serial bus command only if the
tripping cause has disappeared.
In case of auxiliary power supply failure the status of the leds is recorded and reproduced when power
supply is restored.
I>,Z<,Uo>
I2>,T>
Zc<,>
U,f
B.I/
B.F.
PROG/
I.R.F.
W<, Ir>
a
b
c
d
e
f
g
h
IC
60FL

MG30
Doc. N° MO-0084-ING
Rev. 1
Date 28.04.2003
Copyright 2010 - Microener
Firmware:
2.0X
Pag
20
of
43
5. OUTPUT RELAYS
The unit MG30-X includes four (R1, R2, R3, R4) user programmable plus one diagnostic (R5) output
relays.
The number of output relays can be increased by the addition of one or two optional Relay Expansion
modules REX-8.
The modules REX-8 are for protruding mounting and are controlled by the master module MG30-X via a
screened twisted pairs of cables connecting dedicated RS485 serial ports (see diagram herebelow).
The module REX-8 includes eight (RA, RB, RC, RD, RE, RF, RG, RH) user programmable plus one
(R-Diag) diagnostic output relays
The master module MG30-X can control all-together up to sixteen output relays
- 4 internal R1 –R2 –R3 –R4
- 8 from the first optional REX-8 module RA –RB –RC –RD –RE –RF –RG –RH
- 4 from a second optional REX-8 module RI(RA+RB) –RJ(RC+RD) –RK(RE+RF) –RL(RG+RH)
This second unit REX-8 is configured (by internal Dip-Switch) to operate the eight relays two by two in
parallel (only four user programmable outputs with double number of available contacts)
Any of the functions featured by the MG30-X can be programmed to control up to four out of the sixteen
user programmable output relays
MASTER
RELAY
Table of contents
Other MICROENER Relay manuals
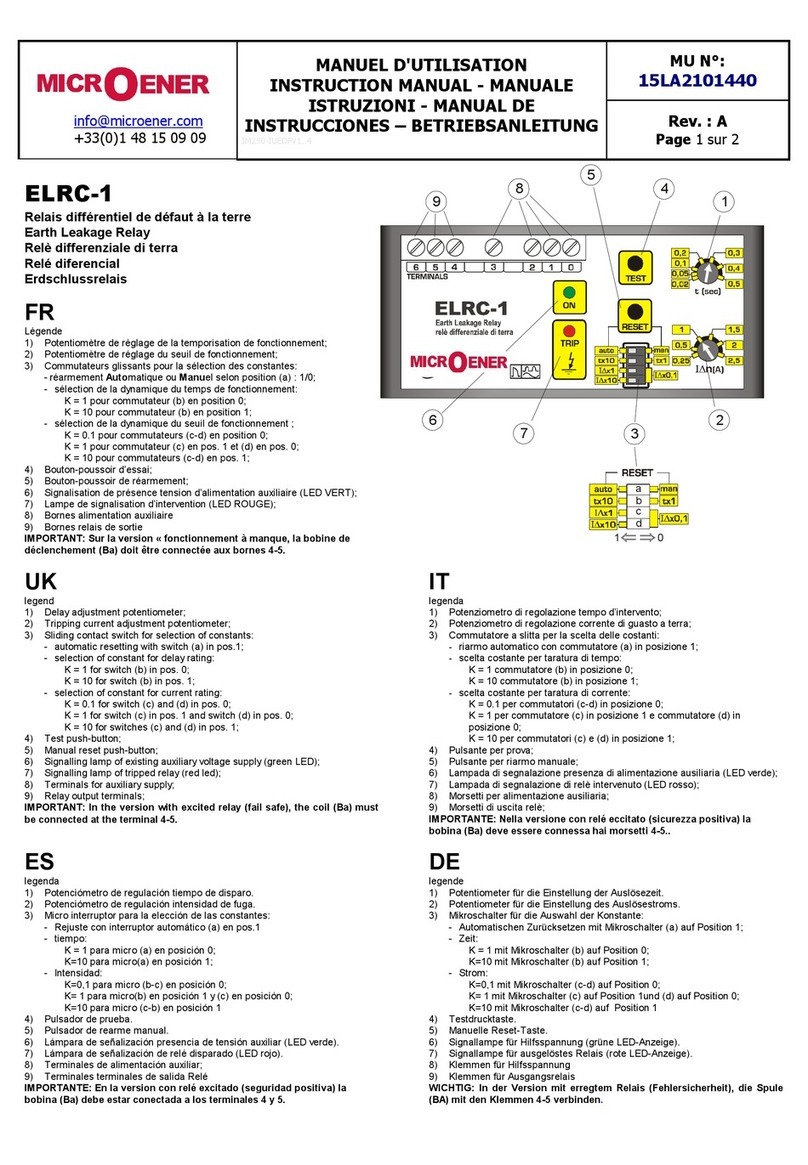
MICROENER
MICROENER ELRC-1 User manual

MICROENER
MICROENER IM30-B00 User manual
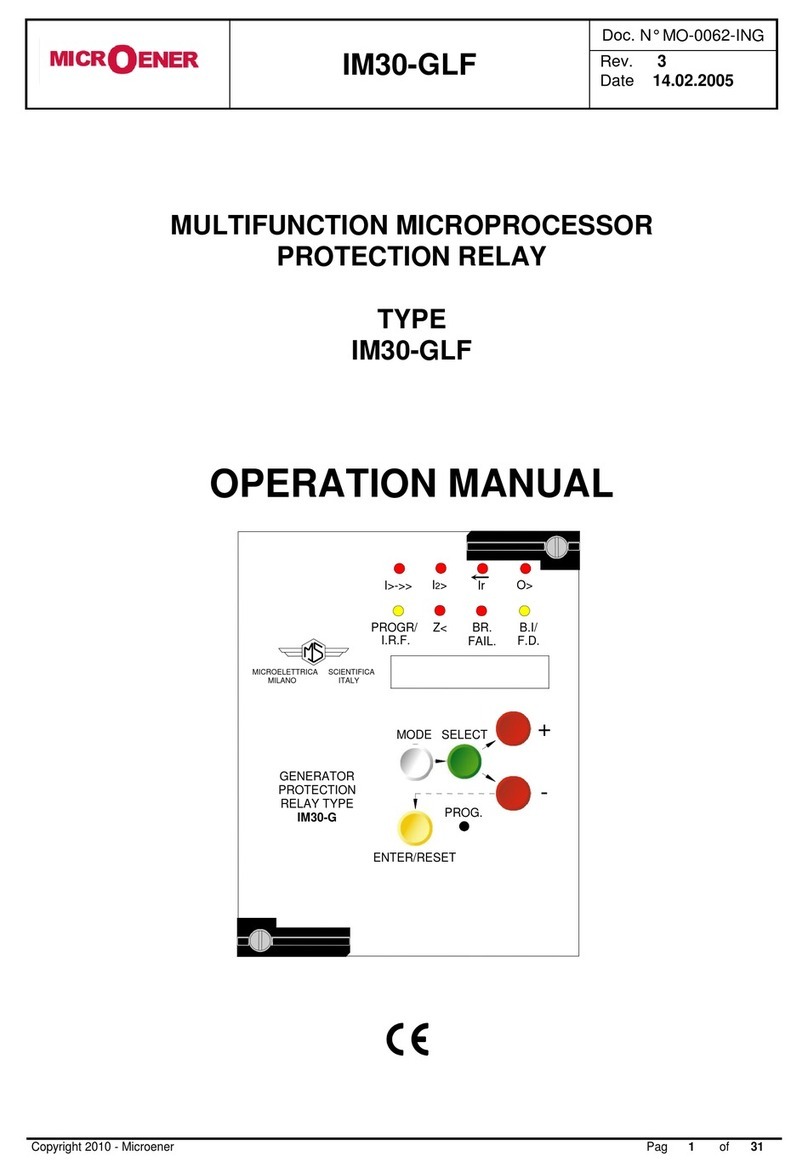
MICROENER
MICROENER IM30-GLF User manual
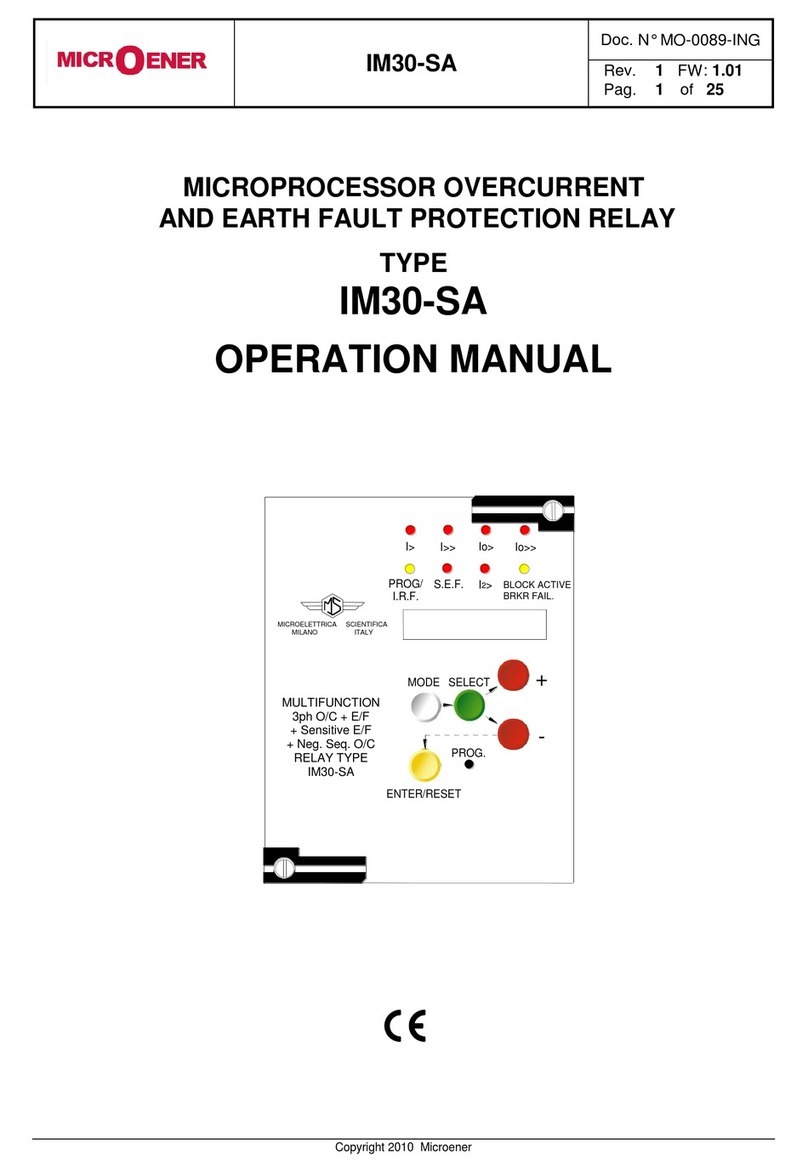
MICROENER
MICROENER IM30-SA User manual

MICROENER
MICROENER IM3G-VX User manual
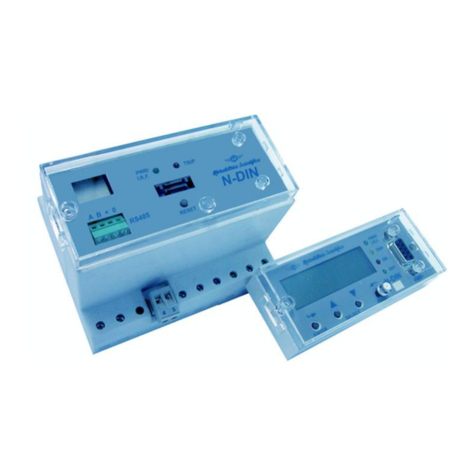
MICROENER
MICROENER N-DIN-MSG User manual
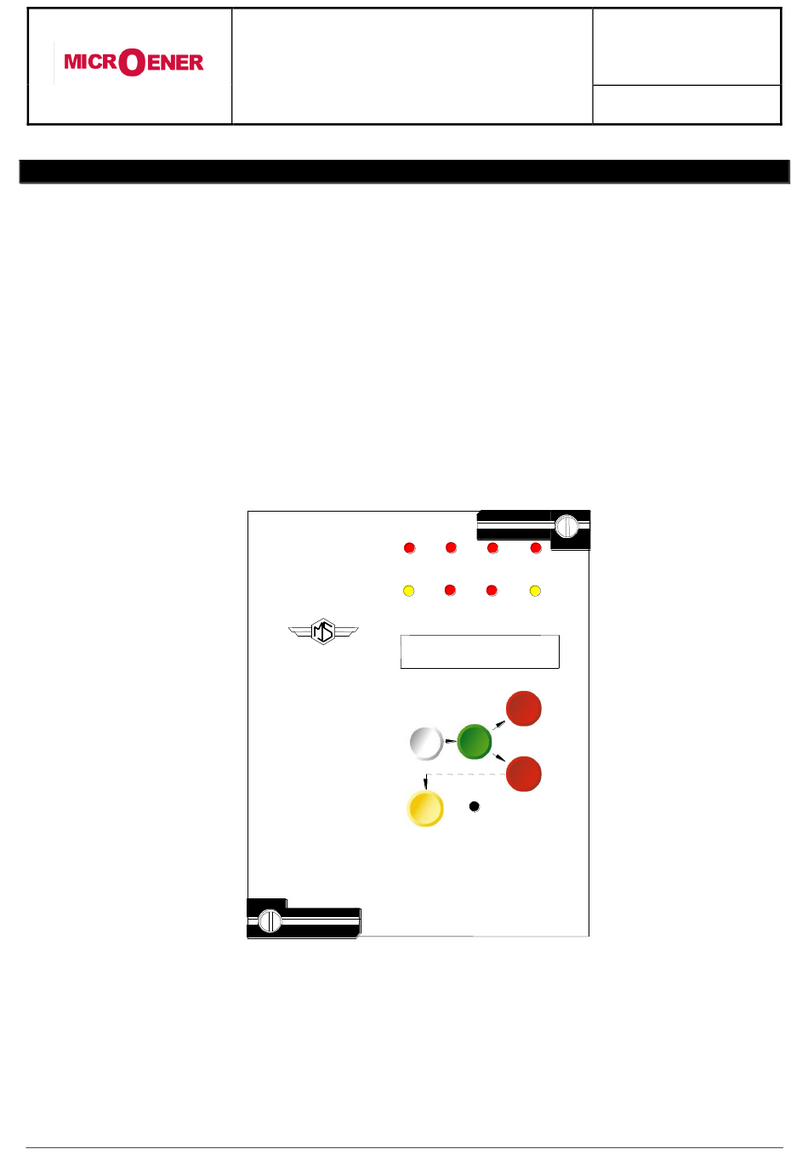
MICROENER
MICROENER M-LIB3 User manual

MICROENER
MICROENER IM30-DK User manual
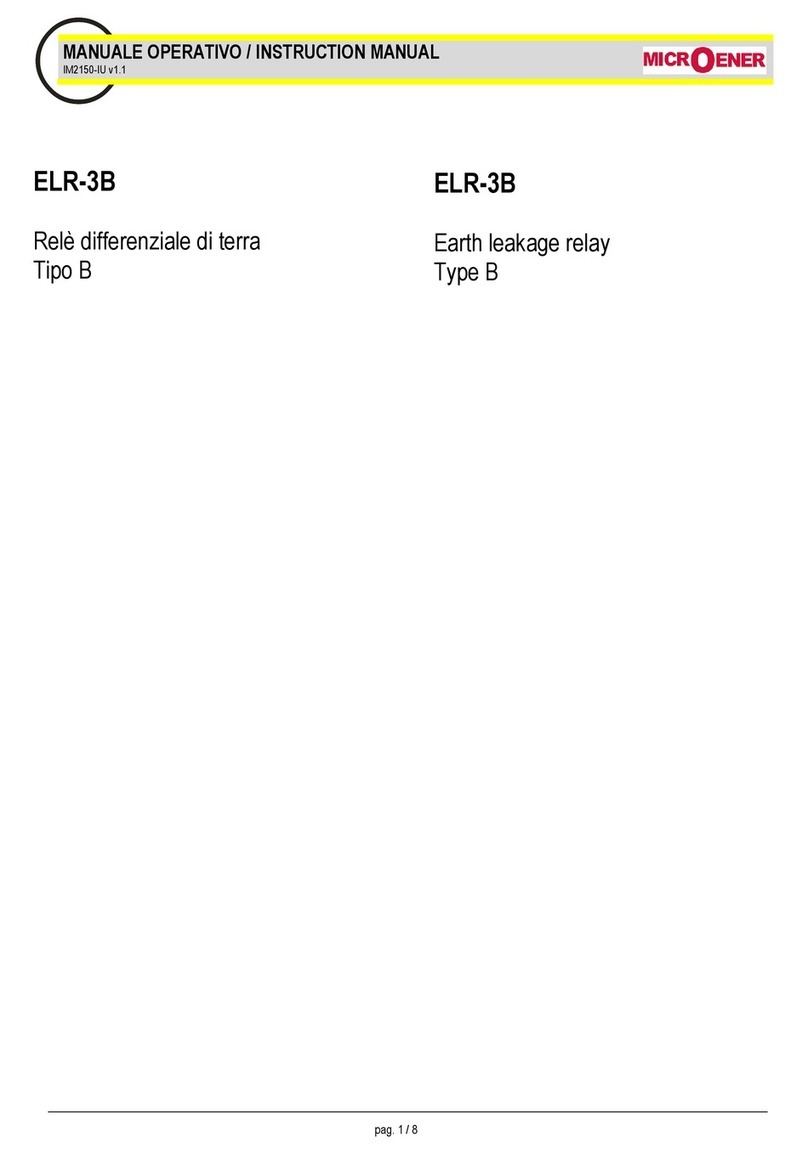
MICROENER
MICROENER ELR-3B User manual
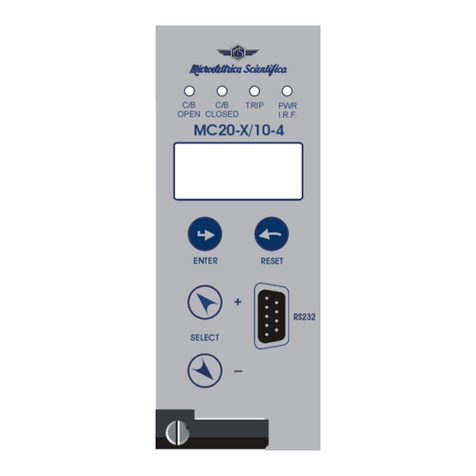
MICROENER
MICROENER MC20-X/10-4 User manual