MICROENER IM30-GLF User manual

IM30-GLF
Doc. N° MO-0062-ING
Rev. 3
Date 14.02.2005
Copyright 2010 - Microener
Pag
1
of
31
MULTIFUNCTION MICROPROCESSOR
PROTECTION RELAY
TYPE
IM30-GLF
OPERATION MANUAL
GENERATOR
PROTECTION
RELAY TYPE
IM30-G
ENTER/RESET
MODE
SELECT
+
-
PROG.
I2>
Ir
PROGR/
I.R.F.
MICROELETTRICA SCIENTIFICA
MILANO ITALY
I>->>
O>
Z<
BR.
FAIL.
B.I/
F.D.

IM30-GLF
Doc. N° MO-0062-ING
Rev. 3
Date 14.02.2005
Copyright 2010 - Microener
Firmware:
2.0X
Pag
2
of
31
INDEX
1. General utilization and commissioning directions_______________________________________________________ 3
1.1 - Storage and Transportation _______________________________________________________________________ 3
1.2 - Installation ____________________________________________________________________________________ 3
1.3 - Electrical Connection ____________________________________________________________________________ 3
1.4 - Measuring Inputs and Power Supply ________________________________________________________________ 3
1.5 - Outputs Loading________________________________________________________________________________ 3
1.6 - Protection Earthing _____________________________________________________________________________ 3
1.7 - Setting and Calibration___________________________________________________________________________ 3
1.8 - Safety Protection _______________________________________________________________________________ 3
1.9 - Handling______________________________________________________________________________________ 3
1.10 - Maintenance__________________________________________________________________________________ 4
1.11 - Fault Detection And Repair ______________________________________________________________________ 4
2. GENERAL ________________________________________________________________________________________ 4
2.1 - Power Supply__________________________________________________________________________________ 5
2.2 - Measuring input ________________________________________________________________________________ 6
2.2.1 –Phase and ground _______________________________________________________________________________________ 6
2.2.2 –Phase-to-Phase voltage___________________________________________________________________________________ 6
2.2.3 - Phase displacement ______________________________________________________________________________________ 6
2.3 - Algorithms of the different functions_________________________________________________________________7
2.3.1 - Setting range of the reference input quantities__________________________________________________________________ 7
2.3.2 - F50/51 - Dual level 3-phase overcurrent ______________________________________________________________________ 7
2.3.3 - F50/51G - Stator Ground Fault______________________________________________________________________________ 7
2.3.4 - F46 - Current unbalance : Measurement of RMS Negative Sequence Current I2_______________________________________ 8
2.3.5 - F32 - Reverse active power ________________________________________________________________________________ 8
2.3.6 - F21/40 - Directional Underimpedance / Loss of excitation_________________________________________________________ 9
2.4 - Configuration of the output relays (see § 5)__________________________________________________________ 11
3. CONTROLS AND MEASUREMENTS __________________________________________________________________ 12
4. SIGNALIZATIONS _________________________________________________________________________________ 13
5. OUTPUT RELAYS _________________________________________________________________________________ 14
6. SERIAL COMMUNICATION _________________________________________________________________________ 14
7. DIGITAL INPUTS __________________________________________________________________________________ 15
8. TEST ___________________________________________________________________________________________ 15
9. KEYBOARD AND DISPLAY OPERATION ______________________________________________________________ 16
10. READING OF MEASUREMENTS AND RECORDED PARAMETERS ________________________________________ 17
10.1 - ACT.MEAS__________________________________________________________________________________ 17
10.2 - MAX VAL ___________________________________________________________________________________ 17
10.3 - LASTTRIP __________________________________________________________________________________ 18
10.4 - TRIP NUM __________________________________________________________________________________ 18
11. READING OF PROGRAMMED SETTINGS AND RELAY'S CONFIGURATION_________________________________ 18
12. PROGRAMMING _________________________________________________________________________________ 19
12.1 - Programming of Functions Settings_______________________________________________________________ 19
12.2 - Programming the Configuration of Output Relays ____________________________________________________ 20
13. MANUAL TEST OPERATION _______________________________________________________________________ 21
13.1 - Mode "TESTPROG" subprogram "W/O TRIP"_______________________________________________________ 21
13.2 - Mode "TESTPROG" subprogram "WithTRIP" _______________________________________________________ 21
14. MAINTENANCE __________________________________________________________________________________ 21
15. POWER FREQUENCY INSULATION TEST ____________________________________________________________ 21
16. ELECTRICAL CHARACTERISTICS __________________________________________________________________ 22
17. CONNECTION DIAGRAM (SCE1395 Rev.5 - Standard Output)____________________________________________ 23
17.1 - CONNECTION DIAGRAM (SCE1468 Rev.2 - Double Output) __________________________________________ 23
18. WIRING THE SERIAL COMMUNICATION BUS (SCE1309 Rev.0) __________________________________________ 24
19. TIME CURRENT CURVES F51 - IM30-G (TU0311 Rev.0) _________________________________________________ 25
20. I2t = constant element F46 - IM30-G (TU0312 Rev.0) ____________________________________________________ 26
21. DIRECTION FOR PCB'S DRAW-OUT AND PLUG-IN_____________________________________________________ 27
21.1 - Draw-out____________________________________________________________________________________ 27
21.2 - Plug-in _____________________________________________________________________________________ 27
22. MOUNTING _____________________________________________________________________________________ 28
23. KEYBOARD OPERATIONAL DIAGRAM ______________________________________________________________ 29
24. SETTING’S FORM ________________________________________________________________________________ 30

IM30-GLF
Doc. N° MO-0062-ING
Rev. 3
Date 14.02.2005
Copyright 2010 - Microener
Firmware:
2.0X
Pag
3
of
31
1. General utilization and commissioning directions
Always make reference to the specific description of the product and to the Manufacturer's instruction.
Carefully observe the following warnings.
1.1 - Storage and Transportation
must comply with the environmental conditions stated on the product's instruction or by the applicable
IEC standards.
1.2 - Installation
must be properly made and in compliance with the operational ambient conditions stated by the
Manufacturer.
1.3 - Electrical Connection
must be made strictly according to the wiring diagram supplied with the Product, to its electrical
characteristics and in compliance with the applicable standards particularly with reference to human
safety.
1.4 - Measuring Inputs and Power Supply
carefully check that the value of input quantities and power supply voltage are proper and within the
permissible variation limits.
1.5 - Outputs Loading
must be compatible with their declared performance.
1.6 - Protection Earthing
When earthing is required, carefully check its effectiveness.
1.7 - Setting and Calibration
Carefully check the proper setting of the different functions according to the configuration of the
protected system, the safety regulations and the co-ordination with other equipment.
1.8 - Safety Protection
Carefully check that all safety means are correctly mounted, apply proper seals where required and
periodically check their integrity.
1.9 - Handling
Notwithstanding the highest practicable protection means used in designing M.S. electronic circuits,
the electronic components and semiconductor devices mounted on the modules can be seriously
damaged by electrostatic voltage discharge which can be experienced when handling the modules.
The damage caused by electrostatic discharge may not be immediately apparent but the design
reliability and the long life of the product will have been reduced. The electronic circuits reduced by
M.S. are completely safe from electrostatic discharge (8 KV IEC 255.22.2) when housed in their case;
withdrawing the modules without proper cautions expose them to the risk of damage.

IM30-GLF
Doc. N° MO-0062-ING
Rev. 3
Date 14.02.2005
Copyright 2010 - Microener
Firmware:
2.0X
Pag
4
of
31
f
fn
ttf
5t
10
50
tt10
a. Before removing a module, ensure that you are at the same electrostatic potential
as the equipment by touching the case.
b. Handle the module by its front-plate, frame, or edges of the printed circuit board.
Avoid touching the electronic components, printed circuit tracks or connectors.
c. Do not pass the module to any person without first ensuring that you are both at
the same electrostatic potential. Shaking hands achieves equipotential.
d. Place the module on an antistatic surface, or on a conducting surface which is at
the same potential as yourself.
e. Store or transport the module in a conductive bag.
More information on safe working procedures for all electronic equipment can be found
in BS5783 and IEC 147-OF.
1.10 - Maintenance
Make reference to the instruction manual of the Manufacturer; maintenance must be carried-
out by specially trained people and in strict conformity with the safety regulations.
1.11 - Fault Detection And Repair
Internal calibrations and components should not be altered or replaced.
For repair please ask the Manufacturer or its authorised Dealers.
Misapplication of the above warnings and instruction relieves the Manufacturer of any liability.
2. GENERAL
Input currents are supplied to 4 current transformers: - three measuring phase current - one measuring
the earth fault zero-sequence current. Phase current input can be 1 or 5A
For zero-sequence current, taps for 1A and 5A input are provided on relay’s terminal board.
Input phase to phase voltage is supplied to one voltage transformer with rated input
programmable 100-125V.
The Time/current Curves, the algorithms and the ratings are herebelow reported.
This relay is derived from the version IM30-G with the addition of the possibility to work with input
frequency in the range from 5 to 70 Hz taking into account the following limitation:
During the transient operation with frequency “f” different from the nominal one “fn” the functions
programmed with dependent inverse time delay will compute a trip time “tf” different than that “t”
corresponding to the operation at the nominal frequency :
Example : the trip time delay at 10Hz will be five times that corresponding to 50Hz
There fore for low-frequency operation the function I> has to be programmed in the
independent definite time mode F(I>)=D (see § 12).
On the contrary the current unbalance element F46 operates properly even at low-frequency because
the heating of the rotor produced by the negative sequence component is by itself inversely proportional
to the frequency.

IM30-GLF
Doc. N° MO-0062-ING
Rev. 3
Date 14.02.2005
Copyright 2010 - Microener
Firmware:
2.0X
Pag
5
of
31
The Stator Earth Fault element F64S does not work when the frequency differs from the nominal
value by more than 10% due to the action of its pass-band filter.
The functions F40 (underimpedance = loss of excitation) and F32 (Reverse Power) are
automatically disactivated when frequency is less than 25Hz.
The trip level of the overcurrent element of this version has a different setting range :
I>=(0.2-2.5)Ib. At the end of the generator/motor start-up period, this element is normally
disactivated via the digital input 2 (terminals 1-2 shorted) by programming “ 2=I1..... (see § 12 :
Output relay’s programming).
If has to be taken into account than that the relay computes the RMS values of the input
quantities on each half-cycle whereas the frequency is detected on each full cycle. It is then clear
that the computing time of the RMS values is inversely proportional to the frequency. Any trip time
delay is started as soon as at least one RMS value above the set level has been detected. As
already remarked the dependent time delay are affected by the frequency whereas the
independent time delays are not.
Make electric connection in conformity with the diagram reported on relay's enclosure.
Check that input currents are same as reported on the diagram and on the test certificate.
The auxiliary power is supplied by a built-in interchangeable module fully isolated an self protected.
2.1 - Power Supply
The auxiliary power is supplied by a built-in interchangeable module fully isolated an self protected.
The relay can be fitted with two different types of power supply module :
24V(-20%) / 110V(+15%) a.c.
80V(-20%) / 220V(+15%) a.c.
a)
-
b)
-
24V(-20%) / 125V(+20%) d.c.
90V(-20%) / 250V(+20%) d.c.
Before energising the unit check that supply voltage is within the allowed limits.

IM30-GLF
Doc. N° MO-0062-ING
Rev. 3
Date 14.02.2005
Copyright 2010 - Microener
Firmware:
2.0X
Pag
6
of
31
2.2 - Measuring input
The relay computes the RMS value of current and voltage and the relevant phase displacement.
2.2.1 –Phase and ground
Phase and ground currents are supplied to four current transformers with 5A rated primary.
By movable jumpers on the relay card, the secondary can be switched-on to two different taps to
obtain a relay rated input current In = 5 or 1 Amp (different values can be provided on request).
The measuring dynamics of the C.Ts. runs from 0.001 through 50 times In.
For the phase current the measuring range of the A/D Converters runs from 0 to 13In
automatically switched to two channels one measuring from 0 to 1.3In and the second from 0.1 to
13In. The theoretical accuracy of the measurement is 0.12%In from 0 to 1.3In and 1.3%In from
through 13In.
- 1 = 0.02 M 0.002 In from 0 to 1.2 In
- 2 = 0.02 M 0.02 In from 1.2 to 12 In
For ground current the measuring range of the A/D converter runs from 0 to 2On
The actual absolute error on each measurement M can be:
- 0= 0.02 M 0.004 On
2.2.2 –Phase-to-Phase voltage
Phase-to-phase voltage UAB is supplied to one Potential transformers rated 220V.
Relay’s rated phase-to-phase input voltage (Uns) can be adjusted from 100 through 125V.
The ADC converter measuring range runs up to 2 x Uns.
The theoretical accuracy is 0.2%Uns.
The actual absolute error can be :
- v = 0.02 M 0.003 Uns
2.2.3 - Phase displacement
The relay detects the displacement between the input voltage of phase C and each phase current IA,
IB, IC. The displacement angle are therefore :
A= (IAUAB)+30°; B= (IBUAB)+150°; C= (ICUAB)-90°;
This means that the voltage system is considered to be balanced
as it is normally, where as the currents can be however
unbalanced. (see figure)
Angles are measured anticlockwise from 0° to 360° with
accuracy 2°.
Displacement is not measured if current or voltage are null.
Ec
IB
B
EB
C
VAB
IC
IA
EA
A

IM30-GLF
Doc. N° MO-0062-ING
Rev. 3
Date 14.02.2005
Copyright 2010 - Microener
Firmware:
2.0X
Pag
7
of
31
2.3 - Algorithms of the different functions
2.3.1 - Setting range of the reference input quantities
System frequency
:
Fn = (50-60)Hz
Rated primary current of phase C.Ts.
:
In = (0-9999)A, step 1A
Rated primary current of ground C:T.
:
On = (0-9999)A, step 1A
Rated secondary phase-to-phase voltage of P.Ts.
:
Uns = (100-125)V, step 1V
Relay basic current (Generator’s rated current)
:
Ib = (0.5-1.1)In, step 0.1In
2.3.2 - F50/51 - Dual level 3-phase overcurrent
F1 - 50/51 : Low set overcurrent
Pick-up (operation) level
Setting I> = Dis blocks function’s operation
:
I> = (1-2.5)Ib, step 0.01Ib
Drop-out ratio
:
0.95
Minimum operation time of instantaneous output
:
30ms
Trip time delay in the definite time operation mode F(I>) = D
:
t = tI> = (0.05-30)s, step 0.01s
Trip time delay in the inverse time operation mode F(I>) = SI
1)(I/I tI0.033
t0.02
(tI> = trip time delay at I/I> = 5)
(see curves TU0311 Attachment. B)
F2 50/51 : High set overcurrent
Pick-up (operation) level
Setting I>> = Dis blocks function’s operation
:
I>> = (1-12)Ib, step 0.1Ib
Drop-out ratio
:
0.95
Minimum operation time of the instantaneous element
:
30ms
Independent trip time delay
:
t = tI>> = (0.05-3)s, step 0.01s
2.3.3 - F50/51G - Stator Ground Fault
Pick-up (operation) level
Setting O> = Dis. blocks function’s operation
:
O> = (0.02-0.4)On, step 0.01On
Drop-out ratio
:
0.95
Minimum operation time of the instantaneous element
:
30ms
Independent trips time delay
:
t = tO> = (0.05-30)s, step 0.01s

IM30-GLF
Doc. N° MO-0062-ING
Rev. 3
Date 14.02.2005
Copyright 2010 - Microener
Firmware:
2.0X
Pag
8
of
31
2.3.4 - F46 - Current unbalance : Measurement of RMS Negative Sequence Current I2
F1 46 : I22 t = K (adiabatic heating)
Generator’s continuous I2rating
Setting 1Is = Dis blocks function’s operation
:
1Is = (0.05-0.5)Ib, step 0.01Ib
Time multiplier
:
Ks = (5-80)s, step 1s
Trip time when I2= Ib
Trip time delay
2
b2
h)/I(IKs
t
Heat accumulation only operates if I2[1Is]
Cooling time from trip level to the status corresponding to
the operation at I2=[1Is]
:
tc = (10-1800)s, step 1s
Cooling time
t
I
I
Ks
[tc]
t2
b
2
l
: tl= [tc] when
Kst
I
I
2
b
2
Cooling only takes places if
1Is
I
I
b
2
(see curves TU0312 Attachment. B)
F2 46 : Alarm
Alarm level
Setting 2Is = Dis blocks function’s operation
:
2Is = (0.03-1)Ib, step 0.01Ib
Independent trip time delay
:
t2Is = (1-100)s, step 1s
2.3.5 - F32 - Reverse active power
Active current setting range
Setting Ir> = Dis blocks function’s operation
:
Ir> = (0.02-0.2)In, step 0.01In
Operation level
:
= Ic cos (c-180°) [Ir]
Independent trip time delay
:
tIr> = (0.1-60)s, step 0.1s
Operation zone
:
(-90°+180°)<c<(90°+180°)

IM30-GLF
Doc. N° MO-0062-ING
Rev. 3
Date 14.02.2005
Copyright 2010 - Microener
Firmware:
2.0X
Pag
9
of
31
2.3.6 - F21/40 - Directional Underimpedance / Loss of excitation
The relay computes the impedance
)cos(I E
Z
Characteristics angle of the impedance = (0°-330°), step 30°
Setting of impedance
angle
Max sensitivity current
angle
Current components
=
0°
R
=
0°
(360°)
Forward Resistive
=
330°
R+C
=
+30°
Forward Resistive + Forward Capacitive
=
300°
R+C
=
+60°
Forward Resistive + Forward Capacitive
=
270°
C
=
+90°
Forward Capacitive (Loss of Field)
=
240°
C-R
=
+120°
Forward Capacitive + Reverse Resistive
=
210°
C-R
=
+150°
Forward Capacitive + Reverse Resistive
=
180°
-R
=
+180°
Reverse Resistive
=
150°
R-R
=
+210°
(-150°)
Forward Inductive + Reverse Resistive
=
120°
L-R
=
+240°
(-120°)
Forward Inductive + Reverse Resistive
=
90°
L
=
+270°
(-90°)
Forward Inductive
=
60°
L+R
=
+300°
(-60°)
Forward Inductive + Forward Resistive
=
30°
L+R
=
+330°
(-30°)
Forward Inductive + Forward Resistive
The direction is that of the axle where the center of the circle is located.
N.B. By definition the relation between current displacement and impedance displacement is :
= 360°-
Angles are counted anticlockwise from 0° (real axis = direction of phase-to-neutral voltage E)
through 360°.
For example : the displacement of a totally capacitive current is = 90°; the angle of a totally
capacitive impedance is = 270°. (see figure)
Operation zone is that included in the circle having (see figure) :
Center on the axle displaced by at distance
2
K1
K2
from the origin Diameter = K1
Circle offset : K2 = (5-50)%Zb, step 1%
Circle diameter : K1 = (50-300)%Zb, step 1%
Setting K1 = Dis blocks the function’s operation
Ib3
Uns
Zb

IM30-GLF
Doc. N° MO-0062-ING
Rev. 3
Date 14.02.2005
Copyright 2010 - Microener
Firmware:
2.0X
Pag
10
of
31
Independent trip time delay : tz = (0.2-60)s, step 0.1s
Integration time : ti = (0-10)s, step 0.1s
In case of impedance oscillation reset of the timer tz only takes place if Z remains outside
the trip area for at least [ti].
Undervoltage inhibition level : Ex<0.3
3
Uns
Undercurrent inhibition level : Ix<0.2Ib
Testing :
For testing the Field loss protection operate as follows :
Impedance characteristic angle set to Z= 270° capacitive
(this corresponds to current leading voltage by 90°).
Circle off-set to any value (recommended value for testing K2 = 50%)
Circle diameter to any value (recommended value for testing K1 = 200%)
Time delay tz to any value (recommended value for testing tz = 0.2s)
Using a single phase apparatus
Voltage input at rated value to terminals 32-33
Current input to phase A terminals 25-26
Phase displacement of input current on input voltage = 90° (current leading voltage)
See attached table.
The trip area is that inside the circle
b
ns
nI3
U
Z
we can individuate the two intersection
point between circle and the impedance axle when the impedance values are :
ZA = K2%Zb; ZB = (K1+K2)%Zb
If input = Uns the currents corresponding to ZA and ZB are :
2
AK100Ib3
I
;
21
BK+K 100Ib3
I
with Ib = 2A, K1 = 200%, K2 = 50% currents are
6,93A2)3(2IA
;
1,39A2)3(0,4IB
Trip must take place for : 1,39A<I<6,93A

IM30-GLF
Doc. N° MO-0062-ING
Rev. 3
Date 14.02.2005
Copyright 2010 - Microener
Firmware:
2.0X
Pag
11
of
31
2.4 - Configuration of the output relays (see § 5)
The different functions of the relay can be programmed to operate any of the output relays as
explained in § 5.
The functions are more than the available output relays but some of then can be grouped to operate
the same relay according to the protection system.
For generator protection the different functions normally operate the trippings shown in the tabel here
below.
PROTEC.
DEVICE
OPERATED
OUTPUT RELAY
CONTROLLED
FUNCTION
EMERG.
MACHINE
FIELD
SIGNALS OR
TRIP
C/B
C/B
OTHER
R1
R2
R3
R4
32
=
Ir>
X
X
X
X
40
=
Zc<
X
X
46-1
=
1Is
X
X
X
46-2
=
2Is
(X)
X
50-1
=
I>
(X)
(X)
50-2
=
I>>
(X)
(X)
51-1
=
tI>
X
X
X
X
51-2
=
tI>>
X
X
X
X
50G
=
O>
(X)
51G
=
tO>
(X)
X
X
(X)
(X)
X
X
(X)
(X) = if required ; X = needed

IM30-GLF
Doc. N° MO-0062-ING
Rev. 3
Date 14.02.2005
Copyright 2010 - Microener
Firmware:
2.0X
Pag
12
of
31
3. CONTROLS AND MEASUREMENTS
Five key buttons allow for local management of all relay's functions.
A 8-digit high brightness alphanumerical display shows the relevant readings (xxxxxxxx)
(see synoptic table fig.1)
Fig. 1
ENTER/RESET
MODE
SELECT
+
-
PROG.
The SELECT button chooses
which category of values within the
chosen mode to display
Pressing this button progressively
selects between
Measurements Display,
Setting Display, Programming,
and Test modes
When in Program mode, this
button stores the newly selected
value. If not in Program mode and
the relay has tripped, this button
resets the relay and all output
contacts. If not tripped, this button
restores the default display.
The + and - buttons are used to
select the actual measurement or
display desired when in
Measurements Display or Settings
Display modes. When in Program
mode, these buttons increase or
decrease the value of the
displayed setting.
When in Program mode, and when
all input currents are zero,
pressing this recessed button
places the relay into active
programming mode, allowing any
or all of the relay’s settings to be
altered.

IM30-GLF
Doc. N° MO-0062-ING
Rev. 3
Date 14.02.2005
Copyright 2010 - Microener
Firmware:
2.0X
Pag
13
of
31
4. SIGNALIZATIONS
Eight signal leds (normally off) are provided:
a)
Red LED
I>->>
Flashing when measured current overcomes the set trip level
[I>],[I>>]
Illuminated on trip after expiry of the set trip time delay [tI>],[tI>>].
b)
Red LED
I2>->>
same as above related to [1Is], [2Is].
c)
Red LED
Ir
same as above related to [Ir>], [tIr>].
d)
Red LED
O>
same as above related to [O>], [tO>].
e)
Yellow LED
PROG/
I.R.F.
Flashing during the programming of the parameters or in case of
Internal Relay Fault.
f)
Red LED
Z<
same as above related to [Z<], [tz].
g)
Red LED
BR.
FAIL.
Lit-on when the BREAKER FAILURE function is activated.
h)
Yellow LED
B.I./
F.D.
Lit-on when the operation of one or more of the relay functions has
been disactivated in the programming
Flashing when a blocking signal is present at the relevant input
terminals.
The reset of the leds takes place as follows:
Leds
a,b,c,d,e
:
From flashing to off, automatically when the lit-on cause disappears.
From ON to OFF, by "ENTER/RESET" push button only if the tripping
cause has disappeared.
Leds
f,g,h
:
From ON to OFF, automatically when the lit-on cause disappears.
In case of auxiliary power supply failure the status of the leds is recorded and reproduced when power
supply is restored.

IM30-GLF
Doc. N° MO-0062-ING
Rev. 3
Date 14.02.2005
Copyright 2010 - Microener
Firmware:
2.0X
Pag
14
of
31
5. OUTPUT RELAYS
Five output relays are available (R1, R2, R3, R4, R5)
a) - The relays R1,R2,R3,R4 are normally deenergized (energised on trip): these output relays are user
programmable and any of them can be associated to one of the IM30-GLF's functions.
One relay eventually associated to the instantaneous element of one of the functions, after pick-up
normally drops-out as soon as the tripping cause disappears (current below the set trip level).
If the current remains above the trip level longer than the time delay programmed for the relevant
function, the drop-out of the instantaneous relay is anyhow forced after an adjustable waiting time
[tBF].(Diasactivation of the blocking output eventually used to block a relay upstream in the
distribution system). Moreover any of the relays R1,R2,R3,R4, can be programmed to be energised
at the end of the delay tBF(Breaker Failure function)
Reset of the output relays associated to any time delayed function can be programmed to take
place “Automatically” (tFRES= A) as soon as the tripping cause has disappeared, or “Manually”
(tFRES= M) only by operating the ENTER/RESET key on relay’s front or via the serial bus.
It has to be remarked that the programming structure does not allow to associate the same relay at
the same time to instantaneous and delayed elements. Therefore any relay already associated to
any time delayed element cannot be associated to any instantaneous element and viceversa.
b) - The relay R5, normally energised, is not programmable and it is deenergized on:
internal fault
power supply failure
during the programming
6. SERIAL COMMUNICATION
The relays fitted with the serial communication option can be connected via a cable bus a fiber optic bus
for interfacing with a Personal Computer (type IBM or compatible).
All the functionalities that can be operated locally (for example reading of input measurement and
changing of relay’s settings) are also possible via the serial communication interface.
Furthermore the serial port allows the user to read event recording and stored data.
The unit has a RS232 / RS485 interface and can be connected either directly to a P.C. via a dedicated
cable or to a RS485 serial bus, allowing having many relays to exchange data with a single master P.C.
using the same physical serial line. A RS485/232 converter is available on request.
The communication protocol is MODBUS RTU (only functions 3, 4 and 16 are implemented).
Each relay is identified by its programmable address code (NodeAd) and can be called from the P.C.
A dedicated communication software (MSCOM) for Windows 95/98/NT4 SP3 (or later) is available.
Please refer to the MSCOM instruction manual for more information Microelettrica Scientifica.

IM30-GLF
Doc. N° MO-0062-ING
Rev. 3
Date 14.02.2005
Copyright 2010 - Microener
Firmware:
2.0X
Pag
15
of
31
7. DIGITAL INPUTS
Two inputs are provided: they are active when the relevant terminals are shorted
2
(terminals 1 - 2)
:
it blocks the operation of the time delayed elements relevant to phase or
ground fault protection; programming allows to block the operation of the
functions I>(Il) or I>>(Ih) or O>(Io).
3
(terminals 1 - 3)
:
it blocks the operation of the time delayed elements relevant to Under
Impedance or Reverse Power protection; programming allows to block
the operation of the function (Z<) only or (Ir) only or both.
When a function is blocked the pick-up of its output is inhibited. For input -2- programming allows to
have the inhibition either permanent as long as the blocking input is active (t2=OFF) or automatically
removed after the expiry of the set trip time delay of the function involved plus additional time 2tBF
(t2=2tBF). By proper interconnection of the blocking inputs and blocking outputs of different relays it is
possible to configurate very efficient arrangements of logic fault discrimination as well as to feature a
safe and quick breaker back-up protection.
8. TEST
Besides the normal "WATCHDOG" and "POWERFAIL" functions, a comprehensive program of self-test
and self-diagnostic provides:
Diagnostic and functional test, with checking of program routines and memory's content, run every
time the aux. power is switched-on: the display shows the type of relay and its version number.
Dynamic functional test run during normal operation every 15 min. (relay's operation is suspended
for less than 4 ms). If any internal fault is detected, the display shows a fault message, the Led
"PROG/IRF" illuminates and the relay R5 is deenergized.
Complete test activated by the keyboard or via the communication bus either with or without tripping
of the output relays.

IM30-GLF
Doc. N° MO-0062-ING
Rev. 3
Date 14.02.2005
Copyright 2010 - Microener
Firmware:
2.0X
Pag
16
of
31
9. KEYBOARD AND DISPLAY OPERATION
All controls can be operated from relay's front or via serial communication bus.
The keyboard includes five hand operable buttons (MODE) - (SELECT) - (+) - (-) - (ENTER/RESET)
plus one indirect operable key (PROG) (see synoptic table a fig.1):
a)
-
White key
MODE
:
when operated it enters one of the following operation modes
indicated on the display :
MEASURES
=
Reading of all the parameters measured and of those recorded
in the memory
SET DISP
=
Reading of the settings and of the configuration of the output
relays as programmed.
PROG
=
Access to the programming of the settings and of relay
configuration.
TEST PROG
=
Access to the manual test routines.
b)
-
Green key
SELECT
:
When operated it selects one of the menus available in the
actual operation MODE
c)
-
Red key
“+”AND “-“
:
When operated they allow to scroll the different information
available in the menu entered by the key SELECT
d)
-
Yellow key
ENTER/RESET
:
It allows the validation of the programmed settings
- the actuation of test programs
- the forcing of the default display indication
- the reset of signal Leds.
e)
-
Indirect key
:
Enables access to the programming.
ENTER/RESET
MODE
SELECT
+
-
PROG.

IM30-GLF
Doc. N° MO-0062-ING
Rev. 3
Date 14.02.2005
Copyright 2010 - Microener
Firmware:
2.0X
Pag
17
of
31
10. READING OF MEASUREMENTS AND RECORDED PARAMETERS
Enter the MODE "MEASURE", SELECT the menus "ACT.MEAS"-"MAX VAL"-"LASTTRIP"-
-"TRIP NUM", scroll available information by key "+" or "-" .
10.1 - ACT.MEAS
Actual values as measured during the normal operation.
The values displayed are continuously refreshed.
Display
Description
IA
xxxxx
A
True R.M.S. value of the current of phase A displayed as primary Amps. (0 - 99999)
IB
xxxxx
A
As above, phase B
IC
xxxxx
A
As above, phase C.
Io
xxxxx
A
As above, earth fault current
Us
xxxxx
%
R.M.S. voltage as % of rated VTs secondary
I2
xxx
%Ib
R.M.S. Negative sequence current as % of basic setting Ib
xxxxx
°
Symmetric phase displacement (IE).
N.B:If no key is operated within 60 sec. the display is automatically switched to the default indication
(IAxxxxxA)
10.2 - MAX VAL
Maximum demand values recorded starting from 100ms after closing of main Circuit Breaker plus
highest inrush values recorded within the first 100ms from Breaker closing, (updated any time the
breaker closes).
Display
Description
IA
xxxx
In
Max. value of phase A current after the first 100ms, displayed as p.u. of C.Ts rated current
IB
xxxx
In
As above, phase B
IC
xxxx
In
As above, phase C.
Io
xxxx
On
As above, earth fault current
I2
xxx
%Ib
As above, negative sequence current
Us
xxxx
%
Max. val. of input voltage after the first 100ms, as % of rated input.
SA
xxxx
In
Max. current of phase A during the first 100ms.
SB
xxxx
In
As above, phase B.
SC
xxxx
In
As above, phase C.
So
xxxx
On
As above, earth fault current.
SU
xxxx
%
Max. input voltage during the first 100ms

IM30-GLF
Doc. N° MO-0062-ING
Rev. 3
Date 14.02.2005
Copyright 2010 - Microener
Firmware:
2.0X
Pag
18
of
31
10.3 - LASTTRIP
Display of the function which caused the tripping of the relay plus values of the parameters at the
moment of tripping.
Display
Description
F:xxxxxx
Function which produced the last event being displayed and faulty phase in case of phase
current element’s trip I>, I>>, Io>, 1Is, 2Is, Ir>, Z<.
IA
xxxx
In
Current of phase A. (value recorded at the moment of tipping)
IB
xxxx
In
Current of phase B. (as above)
IC
xxxx
In
Current of phase C. (as above)
Io
xxxx
On
Earth fault current. (as above)
I2
xxxx
%Ib
Negative sequence current. (as above)
Us
xxxx
%
Input voltage. (as above)
10.4 - TRIP NUM
Counters of the number of operations for each of the relay functions.
The memory is non-volatile and can be cancelled only with a secret procedure.
Display
Description
I>
xxxx
Trip number of Low set overcurrent time delayed element [tI>].
I>>
xxxx
Trip number of High set overcurrent time delayed element [tI>>].
Io>
xxxx
Trip number of earth fault time delayed element [tO>].
1Is
xxxx
Trip number of Low set unbalance time delayed element.
2Is
xxxx
Trip number of High set unbalance time delayed element.
Ir>
xxxx
Trip number of Reverse Power time delayed element.
Z<
xxxx
Trip number of Under Impedance time delayed element.
11. READING OF PROGRAMMED SETTINGS AND RELAY'S CONFIGURATION
Enter the mode "SET DISP", select the menu "SETTINGS" or "FRELAY", scroll information available
in the menu by keys "+" or "-".
SETTING= values of relay's operation parameters as programmed; the setting program actually active is
displayed with steady light whereas the stand-by program is displayed with flashing light.
FRELAY= output relay associated to the different functions as programmed.

IM30-GLF
Doc. N° MO-0062-ING
Rev. 3
Date 14.02.2005
Copyright 2010 - Microener
Firmware:
2.0X
Pag
19
of
31
12. PROGRAMMING
The relay is supplied with the standard default programming used for factory test. [ Values here below
reported in the “ Display “ column ].
All parameters can be modified as needed in the mode PROG and displayed in the mode SET DISP
Local Programming by the front face key board is enabled only if no input current is detected
(main switch open). Programming via the serial port is always enabled but a password is
required to access the programming mode. The default password is the null string; in the
standard application program for communication “MS-COM” it is also provided an emergency
password which can be disclosed on request only.
As soon as programming is enabled, the Led PRG/IRF flashes and the alarm relay R5 is deenergized..
Enter MODE "PROG" and SELECT either "SETTING1" or "SETTING2" for programming of
parameters or "FRELAY" for programming of output relays configuration; enable programming by the
indirect operation key PROG.
The key SELECT now scrolls the available parameters. By the key (+) , (-) the displayed values can be
modified; to speed up parameter's variation press the key SELECT while "+" or "-" are pressed.
Press key "ENTER/RESET" to validate the set values.
12.1 - Programming of Functions Settings
Mode PROG menu SETTINGS. (Production standard settings here under shown).
Display
Description
Setting Range
Step
Unit
NodAd
1
-
Identification number for connection on serial communication bus
1 - 250
1
-
Fn
50
Hz
Mains frequency: setting range
50 - 60
Hz
In
500
Ap
Rated primary current of the phase C.Ts.
1 - 9999
1
A
On
500
Ap
Rated primary current of the C.Ts. or of the tore C.T. supplying
the zero sequence current
1 - 9999
1
A
Uns
100
V
Rated secondary voltage of V.Ts (phase to phase)
100 - 125
1
V
Ib
0.5
In
Generator’s rated current as p.u. of C.Ts rated current
0.5 - 1.1
0.1
In
F(I>)
D
Operation characteristic of the low-set overcurrent element
(D) = Independent definite time.
(SI) = Dependent normal inverse time.
D
SI
D
SI
-
I>
1.0
Ib
Trip level of low-set overcurrent element (p.u. of Ib)
1 - 2.5 - Dis
0.01
Ib
tI>
0.05
s
Trip time delay of the low-set overcurrent element. In the inverse
time operation [tI>] is the trip time delay at I = 5x[I>].
0.05 - 30
0.01
s
I>>
1
Ib
Trip level of high-set overcurrent element (p.u. of Ib)
1 –12 - Dis
0.1
Ib
tI>>
0.05
s
Trip time delay of the high-set overcurrent element
0.05 - 3
0.01
s
O>
0.02
On
Trip level of earth fault element (p.u. of the rated current of the
C.Ts. for zero sequence detection)
The Earth Fault element does not work when frequency is
outside the range 45-65Hz due to the action of the input
band-pass filter
0.02 - 0.4 - Dis
0.01
On
tO>
0.05
s
Trip time delay of low-set earth fault element
0.05 - 30
0.01
s
1Is
0.05
Ib
Generator’s max. continuous negative sequence current rating
(p.u. of Ib)
0.05 - 0.5 - Dis
0.01
Ib
Ks
5
s
Time multiplier of the I2t time-current curve
5 - 80
1
s
tc
10
s
Cooling time from trip level to cold state
10 - 1800
1
s
2Is
0.03
Ib
Negative sequence current alarm level
0.03 - 1 - Dis
0.01
Ib
t2Is
1
s
Independent trip time delay of alarm element
1 - 100
1
s
Ir>
0.02
In
Trip level of the reverse power element (Active component of
current as p.u. of In). The Reverse Power function
disactivated when frequency 36Hz
0.02 - 0.2 - Dis
0.01
In
In 500 Ap
Ap is the unit of measure,
Amps primary.
500 is the
setting default
In is the name
of the variable

IM30-GLF
Doc. N° MO-0062-ING
Rev. 3
Date 14.02.2005
Copyright 2010 - Microener
Firmware:
2.0X
Pag
20
of
31
Display
Description
Setting Range
Step
Unit
tIr>
0.1
s
Independent trip time delay of reverse power element
0.1 - 60
0.01
s
=
270
C
Impedance characteristic angle (Max. sensitivity direction)
0 - 330
30
°
K1
300
%Zb
Diameter of the circle
50 - 300
1
%
K2
50
%Zb
Offset of the circle including the underimpedance tripping zone
(% of Zb=Vn/(3 Ib)
Underimpedance trip is inhibited on undervoltage U<0,3Un
and undercurrent I<0,2Ib and frequency 36Hz
5 - 50
1
%
tz
0.2
s
Trip time delay of the underimpedance element
0.2 - 60
0,1
s
ti
0
s
Integration time of underimpedance element. To avoid non
operation in case of impedance swinging the reset of the trip time
delay “tz” only takes place if the measured impedance remains
outside the tripping zone for at least “ti”.
N.B. “ti” must be always shorter than “tz”
0 - 10
0.1
s
tBF
0.05
s
Max. reset time delay of the instantaneous elements after tripping
of the time delayed elements and time delay for activation of the
output relay associated to the Breaker Failure function
0.05 - 0.5
0.01
s
The setting Dis indicates that the function is disactivated.
12.2 - Programming the Configuration of Output Relays
Mode PROG menu FRELAY (Production standard settings here under shown).
The key "+" operates as cursor; it moves through the digits corresponding to the four programmable
relays in the sequence 1,2,3,4,(1= relay R1, etc.) and makes start flashing the information actually
present in the digit. The information present in the digit can be either the number of the relay (if this was
already associated to the function actually on programming) or a dot (-) if the relay was not yet
addressed. The key "-" changes the existing status from the dot to the relay number or viceversa.
Display
Description
I>
-
-
3
-
Instantaneous element of low-set overcurrent
(only one or more, whatever combination)
operates relays R1,R2,R3,R4.
tI>
1
-
-
-
As above, time delayed element
operates relay R1,R2,R3,R4
I>>
-
-
3
-
Instantaneous element of high-set overcurrent
operates relay R1,R2,R3,R4
tI>>
1
-
-
-
As above, time delayed element
operates relay R1,R2,R3,R4
O>
-
-
3
-
Instantaneous element of low-set earth fault element
operates relay R1,R2,R3,R4.
tO>
1
-
-
-
As above, time delayed element
operates relay R1,R2,R3,R4
1Is
1
-
-
-
First unbalance element (time delayed)
operates relay R1,R2,R3,R4
2Is
-
2
-
-
As above, second unbalance element
operates relay R1,R2,R3,R4
Ir>
1
-
-
-
Reverse power time delayed element
operates relay R1,R2,R3,R4
Z<
1
-
-
-
Underimpedance time delayed element
operates relay R1,R2,R3,R4
tBF
-
-
-
4
Breaker Failure function operates
output relay R1,R2,R3,R4.
tFRes:
A
The reset after tripping of the relays associated to the time delayed elements can take place:
(A) automatically when current drops below the trip level.
(M) manually by the operation of the "ENTER/RESET" key.
2:
--Ih--
The input (2) for blocking the time delayed elements relevant to phase and ground
faults operate on I>(Il) or I>>(Ih) or O>(Io) as programmed
t2
OFF
The operation of the blocking input (2) can be programmed so that it lasts as long the blocking input
signal is present (t2=OFF) or so that, even with the blocking input still present, it only lasts for the set trip
time delay of the function plus an additional time 2xtBF (t2=2xtBF).
3:
--Ir
The blocking input (3) operate on function Z< or IR> as programmed
tI> -2 - 4
This dash means
that output relay
number 1 is not
assigned to this
element
This is the name of
protective element
The number 2
means that
output relay 2 will
operate when
this element trips
This dash means
that output relay
number 3 is not
assigned to this
element
The number 4 means
that output relay 4 will
operate when this
element trips
Table of contents
Other MICROENER Relay manuals
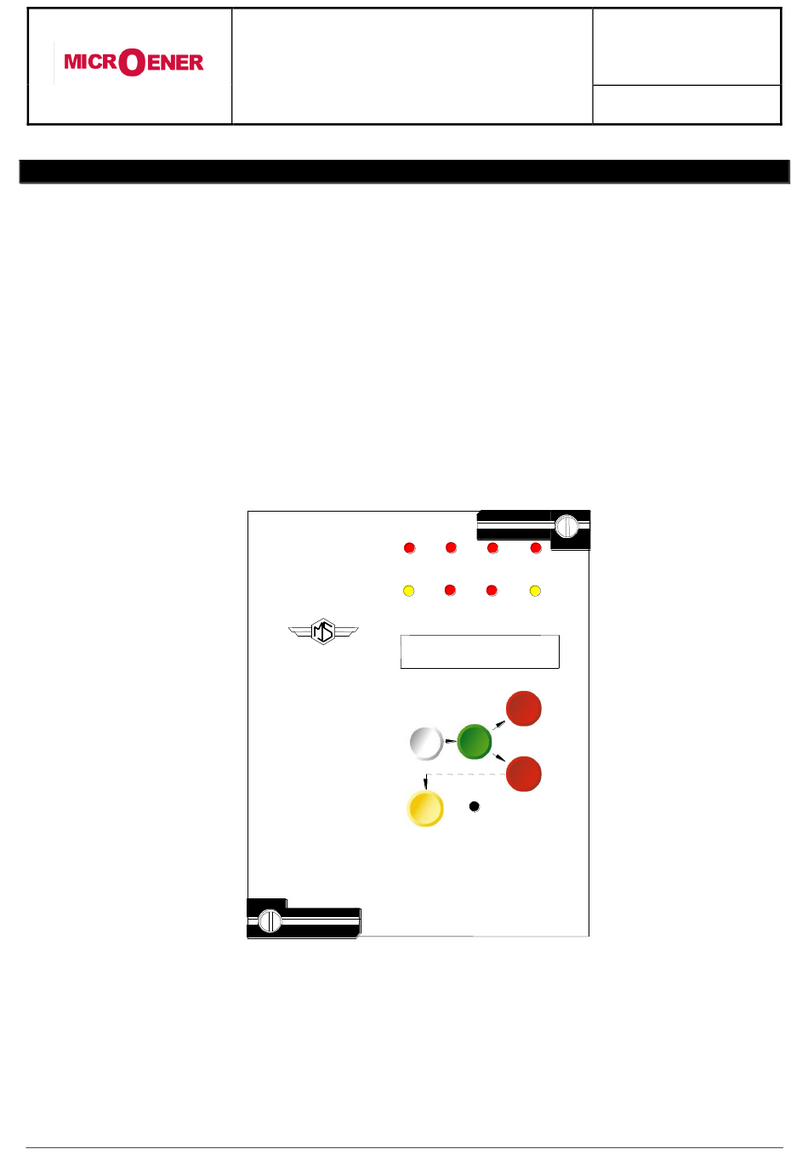
MICROENER
MICROENER M-LIB3 User manual

MICROENER
MICROENER IM30-B00 User manual
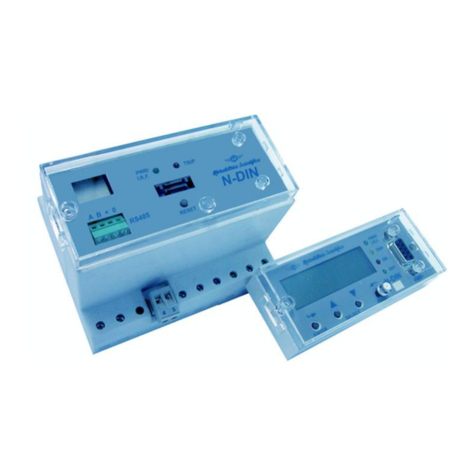
MICROENER
MICROENER N-DIN-MSG User manual
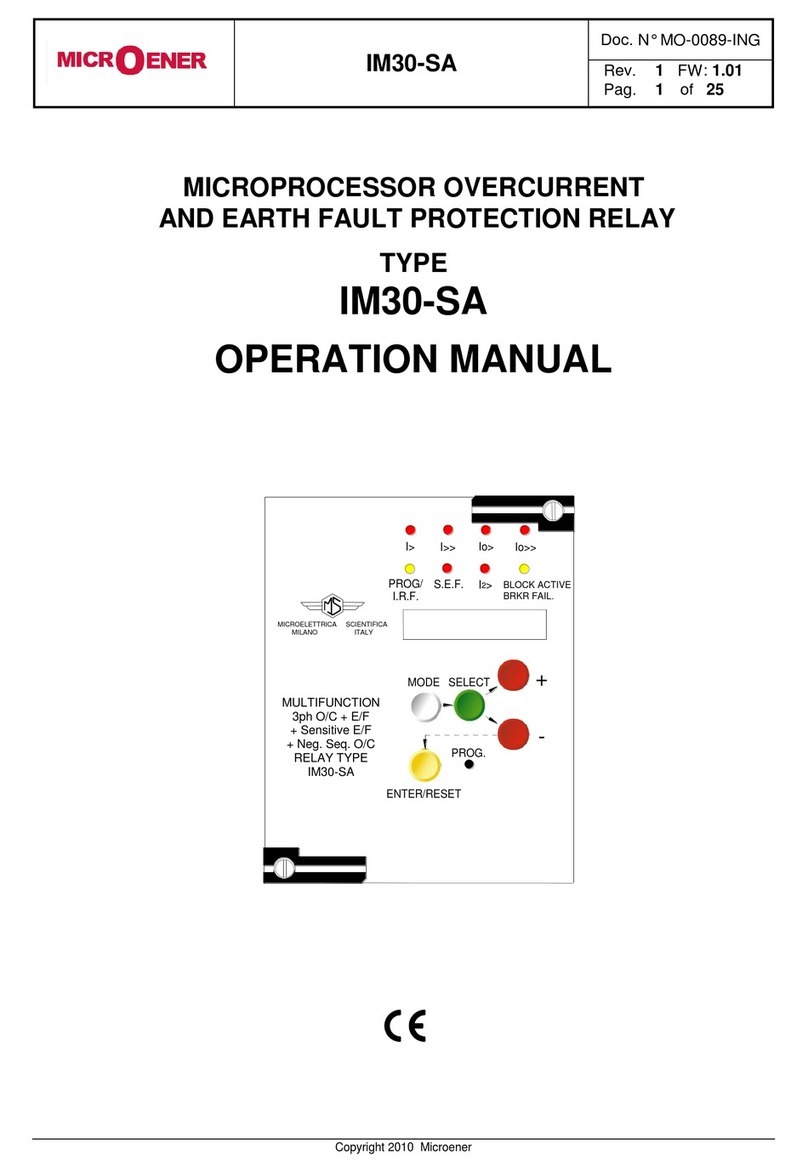
MICROENER
MICROENER IM30-SA User manual

MICROENER
MICROENER IM30-DK User manual

MICROENER
MICROENER IM3G-VX User manual
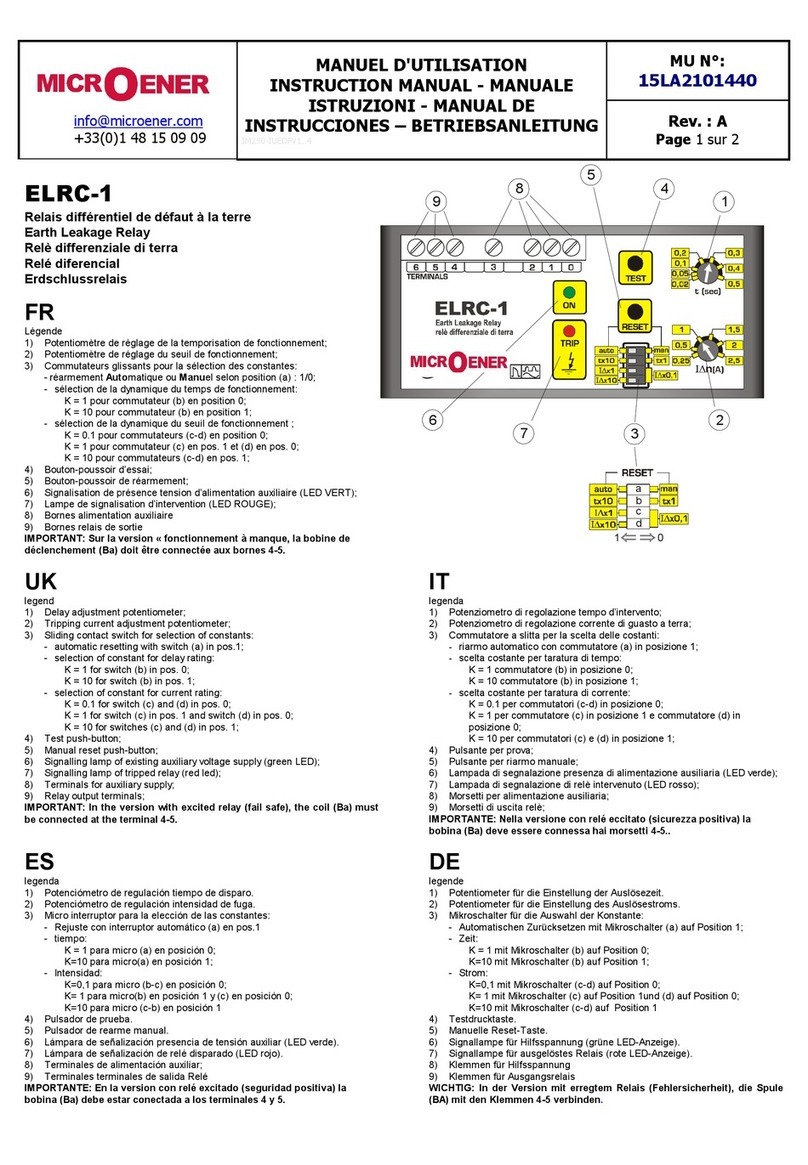
MICROENER
MICROENER ELRC-1 User manual

MICROENER
MICROENER ULTRA Series User manual
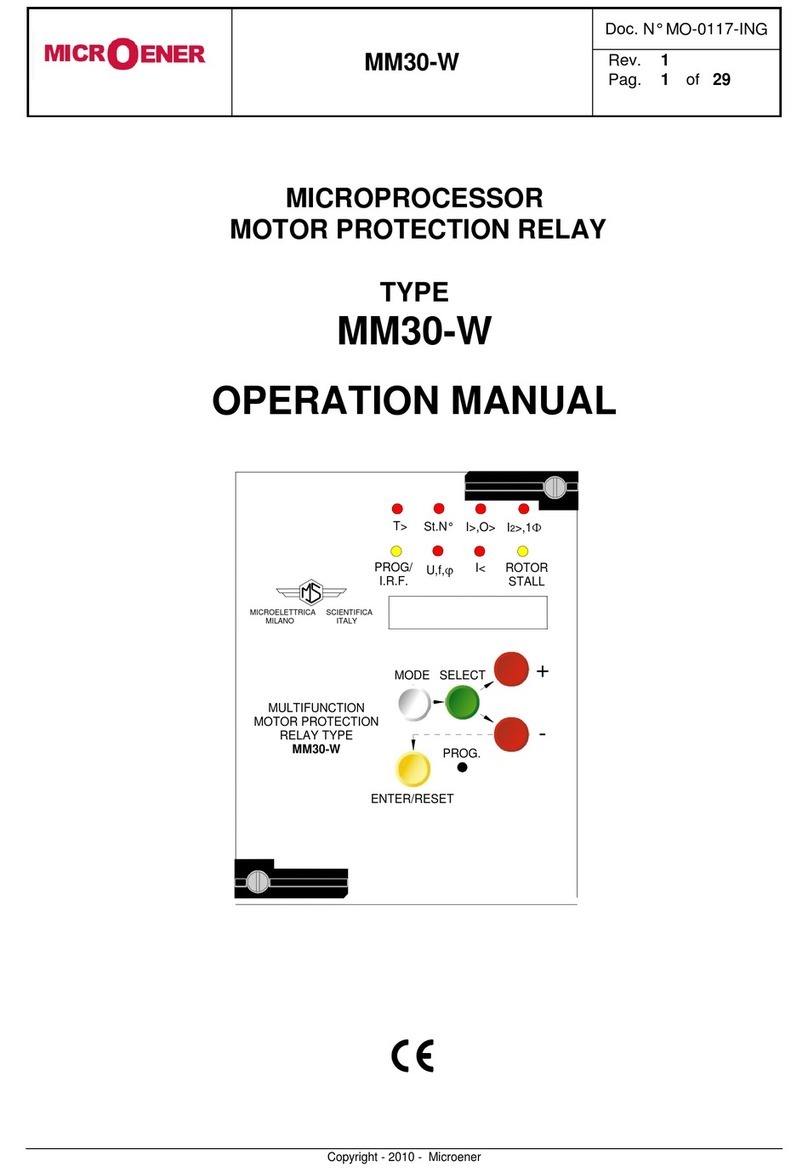
MICROENER
MICROENER MM30-W User manual
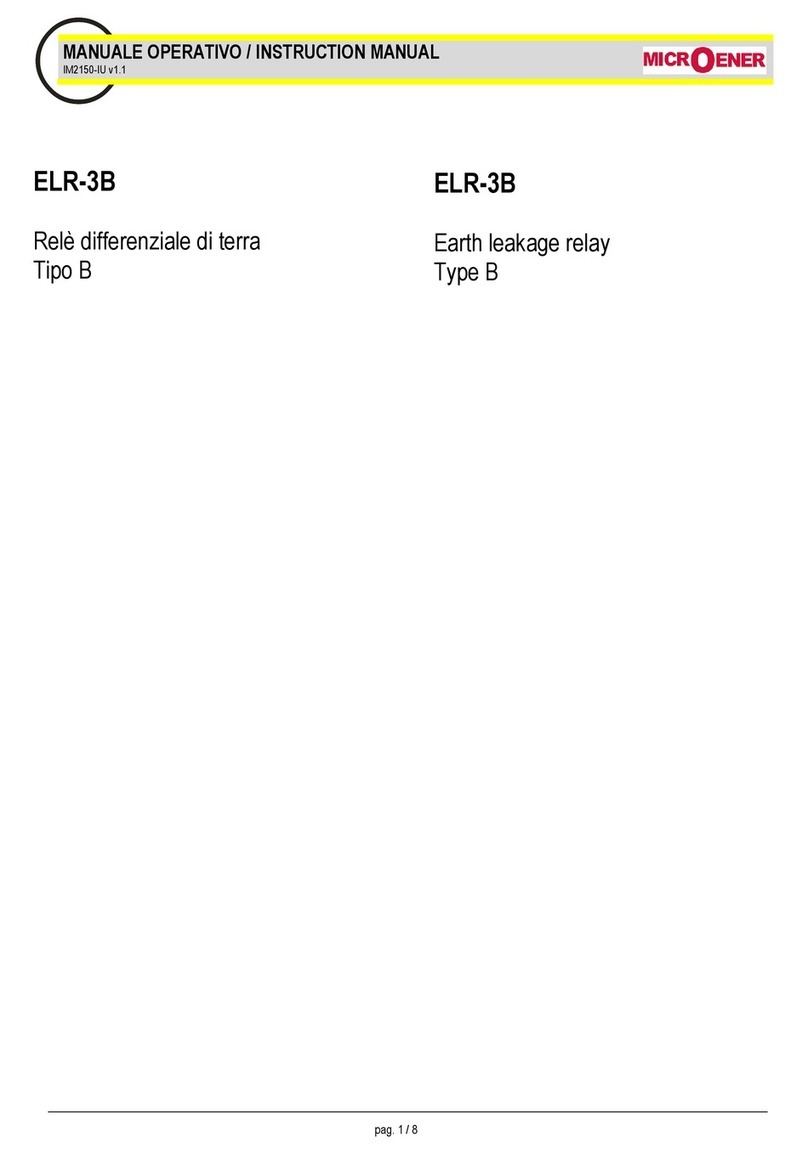
MICROENER
MICROENER ELR-3B User manual